固定床式渣油加氢脱硫技术的简介
VRDS渣油加氢装置技术特点

VRDS渣油加氢装置技术特点1.1 装置特点①UFR/VRDS加工的是高硫、高残炭的常减压减四线和减低渣油,通过加氢脱硫、加氢脱残炭、加氢脱金属等反应,生产适合催化裂化的原料。
②UFR是有三个催化剂床层的上流式反应器,其主要的工艺目的是在稳定状态下操作UFR,大幅度地降低进料中的金属含量,以防止固定床反应器内催化剂过早失活。
加热后的UFR进料(油氢混合物)进入反应器底部,向上流动通过球型催化剂颗粒填充床层。
因为是上流方向,所以UFR 催化剂床层轻微悬浮。
③优化的换热网络系统,设置原料、常渣、柴油、反应产物等的换热器,利用系统热能加热原料、反应进料、轻烃等,提高了热利用率。
加热炉采用余热回收,空气与烟气进行换热,回收烟气中的热量,提高加热炉热效率。
④重油加氢装置的DCS控制系统于2009年由原来的ABB公司的Advance 500更新为Honeywell公司PKS R310系统,先进控制系统的平台更新为EAS NODE,先进控制软件最近升级为技术更为先进的Profit suite R320控制器软件。
VRDS装置使用了先进控制应用的意义在于,希望通过先进控制的应用可以帮助操作人员实现最大的高附加值产品产率、最小的产品指标富裕量、最小的能量消耗从而获得最大的经济效益。
⑤UFR/VRDS装置反应器和循环气体系统分为A、B 两列。
2007年停工后,通过新加流程,使VRDS装置具备单列停开工能力,依靠单系列流程,VRDS装置已经成功实现4次单系列停开工。
充分利用催化剂活性,实现渣油处理最大效益。
1.2 技术改造1.2.1 烟气余热回收系统1、项目实施的背景进入21世纪后,为了适应节能降耗的大趋势,重油加氢装置进行了多项重大节能改造项目,其中就包括加热炉余热回收系统改造。
重油加氢装置原有一套加热炉余热回收系统,加热炉高温烟气排入到集合烟道去往废锅做热源产0.8MPa蒸汽,由于燃料中的硫含量较高,废锅的省煤器段难以避免烟气低温露点腐蚀,所以废锅投用很短时间就因省煤器段破坏而停用,5台加热炉的烟气直接排放大气,排烟平均温度340℃,能量损失严重。
渣油加氢技术

渣油加氢技术
渣油加氢可以处理不易轻质化并难于加工的高含硫含氮以及胶质、沥青质含量高、粘度大、残炭高、重金属含量高的劣质渣油原料;
如果采用一般的延迟焦化或重油催化裂化等重油加工工艺,不但产品液收低,而且质量差,加工难度大;
不仅提高了轻油收率,改善产品质量,而且减轻了环境污染.
渣油加氢的原料(常渣或减渣)依次经过脱金属、脱硫和脱氢以及裂解三段串联加氢处理过程。
经过加氢处理后,未转化渣油中的重金属和残炭含量明显降低,且粘度大大下降,有利于下游装置的进一步加工;
渣油加氢脱硫率一般可达90%以上,脱氮率达70%左右,镍和钒的脱除率达85%左右,残炭脱除率达60%以上.
产品质量好。
低凝柴油产品的十六烷值可达50,安定性好;VGO的氮含量和金属含量较低,有助于提高催化裂化的转化率.
灵活性大。
生产轻质油品,VGO做催化裂化料,未转化渣油是低硫燃料油或掺渣催化裂化料;
固定床加氢过程是应用最多,技术最成熟的工艺,原料适用范围为金属含量<200PPm,残碳<20%,转化率<50%
( 3号白矿油、3号白油、2731油墨溶剂油、150号溶剂油、6号抽提溶剂油)。
浅谈悬浮床与固定床渣油加氢改质技术区别

浅谈悬浮床与固定床渣油加氢改质技术区别发布时间:2021-10-14T07:10:35.993Z 来源:《科学与技术》2021年17期作者:刘圆元[导读] 固定床渣油加氢钙质技术出现的时间比较早,工艺相对较为成熟,悬浮床渣油加氢技术则是一种比较新的技术手段。
刘圆元中国石油四川石化有限责任公司 611930摘要:固定床渣油加氢钙质技术出现的时间比较早,工艺相对较为成熟,悬浮床渣油加氢技术则是一种比较新的技术手段。
本文详细对比了两种技术性质上和工艺过程的不同,可以根据实际情况选择相应的工艺手段,以便实现更大的经济价值。
关键词:悬浮床;固定床;渣油;加氢引言由于现代化社会发展对于环保的高度要求,工业生产对于油品质量的要求也越来越高,因此,渣油轻质化技术得到了行业内高度重视并不断发展成熟,悬浮床和固定床加氢技术作为渣油改质的主要技术手段,得到了迅速发展。
悬浮床和固定床渣油加氢技术在性质和工艺上都有明显的不同,下面就两种技术的不同方面进行对比。
一、催化剂的区别1.悬浮床渣油加氢处理催化剂按照催化剂的溶解性特点来分,悬浮床渣油加氢催化剂主要可以分为两种,一种是固体粉末催化剂,另一种是没有载体的均相催化剂。
因为在工艺中加入催化剂的剂量非常小,再加上原料自身就含有一定比例的硫,所以也就可以进行在线硫化来参与反应。
影响悬浮床催化剂加氢性能的主要原因有催化剂在原料油中的分散情况和金属活动组分。
通常情况下,固定粉末催化剂的活动要稍低于均相催化剂,因为均相催化剂在渣油原料中的接触面积比较大,加氢反应也就更加迅速。
2.固定床渣油加氢处理催化剂因为渣油原料的组成成分复杂较高,其中包含着比较多的金属成分,因此使用的催化剂类型也比较多。
固定床渣油加氢催化剂的物理性质诸如孔体积、空隙率等因素密切关系这催化剂的活性和使用时间。
二、反应机理的区别渣油加氢改质工艺较为复杂,因为渣油原料中含有大量的重金属以及其他化合物。
悬浮床和固定床渣油加氢工艺过程均会发生加氢和热裂化反应,但其中也存在些许区别。
渣油加氢技术

(第十章第四、五节)
渣油加氢工艺反应器类型
固定床 渣油+H2
移动床
生成油+H2 催化剂
沸腾床
浆液床
生成油+H2
生成油+H2油 催化剂 +H2
渣油 催化剂 +H2
渣油+H2+催化剂
几种渣油加氢工艺技术特点
工艺类型
可加工原料油: Ni+V, ppm 残炭值,%
反应压力, MPa 反应温度, ℃ 体积空速, h-1 主要反应类别 渣油转化率, %
H HH
H2(+H2S) NixSy
Ni-X
催化剂使用寿命(t)与MOC的关系
催化剂使用寿命(t) ≈催化剂容金属能力(MOC)
催化剂级配的作用
渣油Ni+V含量与催化剂耗量的关系
14.00 7.00 3.50 m3原料油/kg催化剂 1.75
0.35 脱硫率/%
催化剂活性与寿命的平衡
催化剂级配
Ⅰ
最高温度
1
25 10 13 10 14 100
装置套数
12 5
1
16 5 7 5
7
58
沸腾床
500 600 1230 125 0 0 0 145 2600
所占比例,% 19 23 47
500
0
6 100
装置套数
44
6
100
0
1
16
占世界渣油加氢总能力:固定床=82%;沸腾床=18%
固定床渣油加氢在炼厂中的作用
复杂 成熟
较复杂 开发中
中等
较高
中等
不同渣油加氢工艺产品性质比较
渣油加氢文档

渣油加氢概述渣油加氢是一种炼油过程,通过将重质渣油与氢气反应,以降低硫、氮等杂质含量,提高产品质量。
这一技术在炼油行业中被广泛应用,能够将低质量的渣油转化为高价值的燃料油、润滑油和化工原料。
加氢工艺渣油加氢的关键是加氢反应,通过将渣油与氢气在催化剂的催化下进行反应,使其中的硫、氮等杂质得以去除。
加氢工艺主要包括以下几个步骤:1.加氢反应器:渣油与氢气首先进入加氢反应器,在适宜的温度和压力条件下进行反应。
加氢反应器内通常包含多层催化剂床,以实现高效的反应转化。
2.催化剂:催化剂在渣油加氢过程中起到了关键的作用。
常用的催化剂材料包括镍钼、镍钨、铜锌等,它们能够促进反应的进行,并降低反应的活化能,提高反应的选择性和转化率。
3.去硫:渣油中的硫是一种主要的杂质,会影响产品的质量和环境效应。
通过加氢反应,硫化物会与氢气反应生成硫化氢,然后通过各种设备去除硫化氢,从而实现去硫的效果。
4.去氮:渣油中的氮也是一种重要的杂质,它会影响产品的稳定性和可加工性。
加氢反应可以将氮化物转化为氨气,然后通过适当的方法去除氨气,以实现去氮的效果。
产品及应用渣油加氢可以生产出多种高价值产品,主要包括以下几类:1.燃料油:通过渣油加氢处理后的产品可以作为燃料油使用,具有较高的热值和较低的硫含量,可以用于发电、加热等领域。
2.润滑油:渣油加氢处理后的产品可以进一步提炼,得到纯净的润滑油,用于各种机械设备的润滑,提高设备的使用寿命。
3.化工原料:渣油加氢产生的一些中间产物可以作为化工原料使用,用于生产塑料、橡胶、合成纤维等产品。
优势和应用前景渣油加氢作为一种先进的炼油技术,具有以下几个优势:1.降低环境污染:渣油中的硫、氮等杂质会在燃烧过程中生成有害气体,通过渣油加氢处理,可以显著降低产品中的硫、氮含量,减少环境污染。
2.资源回收利用:渣油通常被认为是炼油过程中的副产品,通过渣油加氢处理,可以将这些低价值的渣油转化为高价值产品,实现资源的回收利用。
渣油加氢工艺说明

第一节工艺技术路线及特点一、工艺技术路线300×104t/a渣油加氢脱硫装置采用CLG公司的固定床渣油加氢脱硫工艺技术,该工艺技术满足操作周期8000h、柴油产品硫含量不大于500ppm、加氢常渣产品硫含量不大于0.35w%、残炭不大于5.5w%、Ni+V不大于15ppm的要求;二、工艺技术特点1、反应部分设置两个系列,每个系列可以单开单停单开单停是指装置内二个系列分别进行正常生产和停工更换催化剂;由于渣油加氢脱硫装置的设计操作周期与其它主要生产装置不一致,从全厂生产安排的角度,单开单停可以有效解决原料储存、催化裂化装置进料量等问题,并使全厂油品调配更灵活;2、反应部分采用热高分工艺流程,减少反应流出物冷却负荷;优化换热流程,充分回收热量,降低能耗;3、反应部分高压换热器采用双壳、双弓型式,强化传热效果,提高传热效率;4、反应器为单床层设置,易于催化剂装卸,尤其是便于卸催化剂;5、采用原料油自动反冲洗过滤器系统,滤除大于25μm以上杂质,减缓反应器压降增大速度,延长装置操作周期;6、原料油换热系统设置注阻垢剂设施,延长操作周期,降低能耗,而且在停工换剂期间可减少换热器和其它设备的检修工作;7、原料油缓冲罐采用氮气覆盖措施,以防止原料油与空气接触从而减轻高温部位的结焦程度;8、采用炉前混氢流程,避免进料加热炉炉管结焦;9、第一台反应器入口温度通过调节加热炉燃料和高压换热器旁路量来控制,其他反应器入口温度通过调节急冷氢量来控制;10、在热高分气空冷器入口处设注水设施,避免铵盐在低温部位的沉积;11、循环氢脱硫塔前设高压离心式分离器除去携带的液体烃类,减少循环氢脱硫塔的起泡倾向,有利于循环氢脱硫的正常操作;12、设置高压膜分离系统,保证反应氢分压;13、冷低压闪蒸罐的富氢气体去加氢裂化装置脱硫后去PSA回收氢气;14、新氢压缩机采用二开一备,每台50%负荷,单机负荷较小,方便制造,且装置有备机;15、分馏部分采用主汽提塔+分馏塔流程,在汽提塔除去轻烃和硫化氢,降低分馏塔材质要求;分馏塔设侧线柴油汽提塔及中段回流加热原料油,降低塔顶冷却负荷,提高能量利用率,减小分馏塔塔径;16、利用常渣产品发生部分低压蒸汽;通过对装置换热流程的优化,把富裕热量集中在温位较高的常渣产品,发生低压蒸汽;17、考虑到全厂能量综合利用,正常生产时常渣在150℃送至催化裂化装置;在催化裂化装置事故状态下,将常渣冷却至90℃送至工厂罐区;18、催化剂预硫化按液相预硫化方式设置;三、工艺流程说明一工艺流程简述1、反应部分原料油自进装置后至冷低压分离器V-1812前的流程分为两个系列,以下是一个系列的流程叙述:原料油在液位和流量的串级控制下进入滤前原料油缓冲罐V-1801;原料从V-1801底部出来由原料油增压泵P1801/S升压,经中段回流油/原料油换热器E-1801AB、常渣/原料油换热器E-1802AB、E-1803AB分别与中段回流油和常渣换热,然后进入原料油过滤器S-1801以除去原料油中大于25μm的杂质;过滤后的原料油进入滤后原料油缓冲罐V-1802,原料油从V-1802底部出来后由加氢进料泵P1802/S升压,升压后的原料油在流量控制下进入反应系统;原料油和经热高分气/混合氢换热器E-1805AB预热后的混合氢混合,混合进料经反应流出物/反应进料换热器E-1804预热后进入反应进料加热炉F-1801加热至反应所需温度进入第一台加氢反应器R-1801,R-1801的入口温度通过调节F-1801的燃料量和E-1804的副线量来控制,R-1801底部物流依次通过其它三台反应器R-1802、R-1803、R-1804,各反应器的入口温度通过调节反应器入口管线上注入的冷氢量来控制;从R-1804出来的反应产物经过E-1804换热后进入热高压分离器V-1803进行气液分离,V-1803底部出来的热高分液分别在液位控制下减压后,进入热低压分离器V-1804进行气液分离,V-1803顶部出来的热高分气分别经热高分气/混合氢换热器、热高分气蒸汽发生器E-1806换热后进入热高分气空冷器E-1807,冷却到52℃进入冷高压分离器V-1806进行气、油、水三相分离;为了防止铵盐在低温位析出堵塞管路,在热高分气空冷器前注入经注水泵P-1803/S升压后的脱硫净化水等以溶解铵盐;从V-1806顶部出来的冷高分气体循环氢进入高压离心分离器V-1807除去携带的液体烃类,减少循环氢脱硫塔C-1801的起泡倾向;自V-1807顶部出来的气体进入C-1801底部,与贫胺液在塔内逆向接触,脱除H2S,脱硫溶剂采用甲基二乙醇胺MDEA,贫胺液从贫胺液缓冲罐V-1809抽出经贫溶剂泵P-1804/S升压后进入C-1801顶部,从塔底部出来的富胺液降压后进入富胺液闪蒸罐V-1810脱气;富液脱气后出装置去溶剂再生,气体去硫磺回收;自C-1801顶不出来的循环氢进入循环氢压缩机入口分液罐V-1808除去携带的胺液,V-1808顶部出来的循环氢分成两路,一路去氢提浓ME-1801部分,提浓后的氢气经提浓氢压缩机K-1804升压后与新氢压缩机K-1802A.B.C出口新氢汇合,释放气去轻烃回收装置;另一路进入循环氢压缩机K-1801升压,升压后的循环氢分为三部分,第一部分与新氢压缩机来的新氢混合,混合氢去反应部分;第二部分作为急冷氢去控制反应器入口温度;第三部分至E-1807前作为备用冷氢和K-1801反飞动用;循环氢压缩机选用背压蒸汽透平驱动的离心式压缩机;从两个反应系列的冷高压分离器底部出来的冷高分液分别在液位控制下减压混合后,进入冷低压分离器V-1812进行气液分离,冷低分液体在液位控制下从罐底排出并进入热低分气/冷低分液换热器E-1809、柴油/冷低分油换热器E-1811、常渣/冷低分油换热器E-1812换热后进入汽提塔C-1803;V-1812顶部出来的冷低分气去轻烃回收装置脱硫;冷高压分离器底部的含H2S、NH3的酸性水进入酸性水脱气罐V-1823集中脱气后送出装置;两个反应系列的热低分油在液位控制下从V-1803底部排出去分馏部分;热低分气体经E-1809换热后进入热低分气空冷器E-1810冷却到54℃,然后进入冷低压闪蒸罐V-1811进行气液分离,为了防止在低温位的地方有铵盐析出堵塞管路,在E-1810前注水以溶解铵盐;V-1811顶部出来的富氢气体直接送至加氢裂化装置进行脱硫,然后去PSA装置回收氢气;从下部出来的冷低压闪蒸液进入到冷低压分离器;新氢从全厂氢网送入,进入新氢压缩机经三段压缩升压后分两路分别与两个系列循环氢压缩机出口的循环氢混合,混合氢气分别返回到各自的反应部分;新氢压缩机设三台,二开一备,每一台均为三级压缩,每台的一级入口设入口分液罐,级间设冷却器和分液罐;2、分馏部分来自反应部分的热低分油与经加热后的冷低分液一起进入汽提塔C-1803;塔底采用水蒸汽汽提;塔顶部气相经汽提塔顶空冷器E-1814冷凝冷却后进入汽提塔顶回流罐V-1814进行气液分离,V-1814气体与冷低分气一起出装置送至轻烃回收统一脱硫;V-1814底部出来的液体经汽提塔顶回流泵P-1805/S升压后分成两部分,一部分作为回流返回到塔顶部,另一部分去石脑油加氢;V-1814底部分水包排出的酸性水进入V-1823脱气后出装置;为减轻塔顶管道和设备的腐蚀,在汽提塔的顶部管道注入缓蚀剂;汽提塔底油经分馏塔进料加热炉F-1802加热至合适温度进入分馏塔C-1804,分馏塔设一个柴油抽出侧线和一个中段回流,塔底采用水蒸汽汽提,塔顶气相经分馏塔顶空冷器E-1815冷凝冷却后进入分馏塔顶回流罐V-1815进行气液分离;V-1815底部出来的液体经分馏塔顶回流泵P-1806/S 升压后分成两部分,一部分作为塔顶回流返回到塔顶部,另一部分在V-1815液位控制下与C-1803塔顶油一道送出装置;V-1815底部分水包排出的含油污水经含油污水泵P-1807/S升压后送注水罐回用;未汽提柴油从分馏塔抽出进入柴油汽提塔C-1805,柴油汽提塔底设重沸器,以分馏塔底油为热源,C-1805顶气体返回到分馏塔;柴油从塔底部抽出经柴油泵P-1811/S升压后再经柴油/低分油换热器、柴油空冷器E-1816冷却到50℃出装置;中段回流油从分馏塔集油箱用分馏塔中段回流泵P-1809/S抽出,进入E-1801A.B换热后返回分馏塔;分馏塔底油加氢常渣经分馏塔底泵P-1810/S加压后依次经柴油汽提塔重沸器E-1818、常渣/原料油换热器、常渣蒸汽发生器E-1817等换热至168℃作为热供料去催化裂化装置,或再经常渣空冷器E-1819冷却至90℃出装置至罐区;3、催化剂预硫化为了使催化剂具有活性,新鲜的或再生后的催化剂在使用前均必须进行预硫化,设计采用液相硫化法,硫化剂为二甲基二硫化物DMDS;两个系列催化剂可以分别独立进行预硫化,以下是一个系列硫化的流程叙述:硫化时,系统内氢气经循环氢压缩机按正常操作路线进行循环,冷高压分离器压力为正常操作压力;DMDS自硫化剂罐V-1831来,至加氢进料泵入口管线,硫化油采用蜡油;自R-1804来的流出物经E-1804、V-1803、E-1805A.B、E-1806、E-1807冷却后进入冷高压分离器V1806进行分离,冷高分气体经循环氢压缩机K-1801循环,催化剂预硫化过程中产生的水从V4004底部间断排出;二主要操作条件如下:1反应部分反应器液时空速,h-10.20总气油比,SOR/EOR1132/1232反应器入口压力,SOR/EORMPag19.45/19.88平均反应温度,SOR/EOR℃391/402 2热高压分离器温度℃SOR/EOR371/374压力MPaG17.8 3冷高压分离器温度℃52压力MPaG17.5 4反应进料加热炉入口/出口温度℃337/365SOR350/378EOR压力MPaG20.6 5循环氢压缩机入口温度℃61入口/出口压力MPaG17.46/21.43循环氢压缩机设计能力m3n/h224315单台6新氢压缩机入口温度℃40入口/出口压力MPaG 2.4/21.2新氢压缩机设计能力m3n/h51400单台7提浓氢压缩机入口温度℃60入口/出口压力MPaG 4.18/21.37提浓氢压缩机设计能力m3n/h31800 8循环氢脱硫塔塔顶温度℃61塔顶压力MPaG17.59汽提塔进料温度℃364/366SOR/EOR塔顶温度℃189/172SOR/EOR塔顶压力MPaG 1.1塔底温度℃350/344SOR/EOR10分馏塔进料温度℃371塔顶温度℃124/129SOR/EOR塔顶压力MPaG0.14塔底温度℃354/322SOR/EOR10柴油汽提塔进料温度℃226/231塔顶温度℃227/247塔顶压力MPaG0.17塔底温度℃293第二节副产品的回收、利用及“三废”处理方案一、副产品的回收和利用该装置副产品富氢气体和含硫燃料气;富氢气体约为2422Kg/hEOR,其中H2含量为83.02%V,H2S含量为2.99%V,C1含量为7.13%V,C2含量为3.34%V,富氢气体送至加氢裂化装置进行脱硫,然后去PSA装置回收氢气;含硫燃料气由低分气、汽提塔顶气、氢提浓单元尾气、酸性水罐闪蒸气及富胺液闪蒸气总量约为7969Kg/hEOR,其中H2含量为32.67%V,H2S含量为10.32%V,C1含量为6.63%V,C2含量为11.94%V,含硫燃料气送轻烃回收装置脱硫;二、“三废”处理方案一废水处理废水按其性质主要可分为四类含硫污水:主要由冷高压分离器、冷低压分离器、汽提塔顶回流罐等排出,含有较高浓度的H2S和NH3,送酸性水处理装置进行处理;含油污水:分馏塔顶回流罐产生的含油污水经含油污水升压后送注水罐作为装置注水回收利用;机泵和地面冲洗等产生的含油污水,送至污水处理场;装置界区内的初期雨水并入含油污水,后期雨水排入清净废水系统,以减轻工厂污水处理的负荷;生活污水:装置间断排出职工生活污水,排入生活污水系统;废水见表2-1;表2-1废水排放量和污染物浓度一览表二废气处理1 废气燃烧废气:反应进料加热炉、分馏塔进料加热炉排出的燃烧烟气,充分回收能量后,经烟囱高空排放;放空气体:安全阀及放空系统包括紧急放空排放的含烃气体排入密闭的火炬系统;废气排放情况见表2-2表2-2主要废气污染源表三固液体废物正常生产时无固液体废物排放,仅在停工检修时,排出废保护剂、废催化剂和废碱液等;废保护剂、催化剂:由加氢反应器排出,约1年一次,送废催化剂回收工厂或桶装深埋;废碱液:反应部分中和清洗排放的废碱液由工厂系统统一处理;固体废弃物列于表2-3;表2-3固体废物分类汇总表四噪声源及处理1空冷器选用低转速、低噪声风机,单台噪声控制在85分贝以下;2机泵选用低噪声增安型电机;3蒸汽放空装有消音器;4加热炉采用低噪声燃烧器,风道部分采用保温隔音材料;5凡易产生噪声的排放点均设置消音器;6加氢进料泵、新氢压缩机配用的大型电机设置消音罩;采用上述措施后,噪声指标符合石油化工企业职业安全卫生设计规范SH3047-93;表2-4噪声特征表第三节安全卫生一、装置危险、危害性分析1 火灾、爆炸危害因素分析所用原料、中间产品、产品的火灾理化特性见表3-1;表3-1生产中主要原料、中间产品、产品火灾危险性分类表2 危害因素较大设备及场所主要危险设备包括:加氢反应器、循环氢脱硫塔、新氢压缩机、循环氢压缩机、高压换热器等;主要危险岗位见表3-2:表3-2主要危险岗位表3 生产中使用、产生的部分物料为有毒物质,对人体有一定程度的危害作用,其危害及危害程度见表3-3;表3-3主要有毒、有害物质及其特性表4 危险等级所用原料、中间产品、产品各物料在加工过程中处于高温、高压、含氢环境中,当环境温度超过其自燃点时,发生泄漏就可能引发火灾;火灾危险性属于甲类;二安全卫生措施1 安全卫生设施依托情况该装置所需的劳动安全卫生措施,按现行有关劳动安全卫生标准、规范的要求,在依托现有系统劳动安全卫生设施的基础上补充完善,以确保该装置的劳动安全卫生达到标准和规范的要求;2 主要安全卫生防范措施⑴工艺设计①采用先进可靠的工艺技术和合理的工艺流程,设计考虑必要的裕度及操作弹性,以适应加工负荷上下波动的需要;②装置内设有1.05/2.1MPa/min紧急泄压系统;当出现反应器床层温度过高或发生严重火灾时,使用紧急泄压系统手动启动,使反应系统迅速降压,以避免催化剂和设备严重损坏;③为确保安全操作,保障设备、人身安全,设置下述自动联锁保护系统;当1.05/2.1MPa/min放空系统启动时,反应进料加热炉将自动停运;当燃料气压力过低,反应器入口温度过高,反应进料加热炉流率过低时,反应进料加热炉停炉;当燃料油压力过低,加热炉出口温度过高,加热炉流率过低时,分馏塔进料加热炉停运;当循环氢压缩机入口分液罐高高液位时,循环氢压缩机停机;④所有带压设备及管道均设安全阀,所有安全阀均设备阀;⑤各部分设置的安全阀泄压时,其排放物分别由火炬线或液体放空线排至密闭的放空罐,然后气体去工厂火炬,液体去工厂污油罐;⑥关健转动设备,均设有备机,以确保安全生产;⑵平面布置设计①平面布置在满足有关防火、防爆及安全卫生标准和规范要求的前提下,尽量采用露天化、集中化和流程式布置,并考虑同类设备相对集中,以达到减少占地、节约投资、降低能耗、便于安全生产操作和检修管理,实现本质安全的目的;②四周设绿化带和环形消防通道,并确保与周围装置的防火间距满足有关规范的要求;设置检修及消防通道,保证消防车和急救车能顺利通往可能出现事故的地方;③加热炉布置在全年最小风频的下风向;④所有框架、管架均按GB50160-921999版的有关规定设有防火层;界区内设有消火栓、水炮、蒸汽灭火设施、软管站及灭火器等消防设施用于火灾扑救;⑤对于表面温度高于60℃管线,在操作人员可触摸到的部位均采用隔热层防烫保护;在管带区、框架区、塔区等地方均设蒸汽灭火系统;⑥设计中选用优质垫片,加强管道、设备密封,防止介质泄漏;⑦设置移动式小型灭火设备;包括推车式泡沫灭火器,手提式干粉灭火器以及手提式泡沫灭火器;⑶自控设计①装置的仪表自动控制采用DCS,由控制室进行统一管理,并根据工艺特点和安全要求,对关键部位,设置必要的报警、自动控制及自动联锁等控制措施;②为保证装置停电时仪表用电,设置UPS不间断电源;③对有可能泄露可燃气体和H2S等有毒气体的地方,设置固定式的可燃气体报警仪和H2S气体报警仪;可能有H2S气体泄漏和聚积岗位上的操作人员配备便携式H2S气体报警器;④为了保护设备和生产安全,在设计中选用风开、风关调节阀,以便停风时,调节阀能处于安全位置;同时为防止仪表管道的冻凝和阻塞,在必要部位设置仪表蒸汽伴热系统和冲洗油系统;⑤监测、控制仪表除按工艺生产要求选型时,还考虑了仪表安装地点的防爆等级,并按爆炸和火灾危险环境电力装置设计规范GB50058-92进行选型;⑥生产仪表及其它电气设备按所处区域的防爆等级选用防爆型号;在中控室、变配电室内设置可燃气体报警仪、火灾检测报警器;并设置事故通风设施;⑷电气设计①装置内爆炸危险区域内的电力设备设置严格按照爆炸和火灾危险环境电力装置设计规范GB50058-92的要求进行设计;②在爆炸危险场所的电器设备均选用相应等级的防爆电器,如防爆电钮、防爆照明灯、防爆电机等;③电力配电电缆均选用阻燃铠装电缆;④设防爆检修动力箱,供停工时检修用电;⑤平台、过道及其它需要的地方均设置照明设施,照明亮度符合规范要求;为了便于事故抢救,局部重要的操作通道及操作点配备事故照明设施;⑥为确保人身安全,在有关建构筑物、工艺设备及管道上均设置防雷防静电的可靠接地装置,并依照工业与民用电力装置接地设计规范GBJ65-83的要求,接地电阻<4Ω,接地线均采用镀锌扁钢;⑦设防爆对讲电话以及火灾报警装置,以便发生火灾时及时报警;⑸工艺配管工程设计①各部分均设有固定的消防蒸汽管线和足够的软管站,使可能出现的泄漏点均在消防蒸汽软管范围之内;②按标准、规范规定选用管道、管件、法兰、垫片、阀门;③对安装管道采取必要的保温、保冷措施:a 工艺过程的需要;b 减少散热或冷量散失的需要c 保证操作人员安全、改善劳动条件的需要;④工艺管道安全的措施a 热补偿安全b 适应高温、高压及腐蚀介质的管道材质;c 防泄漏措施;⑹土建设计①各建筑物、构筑物的抗震性能均按建筑抗震设计规范GB50011-2001的规定进行设计;建筑物的耐火性能满足2级耐火等级的要求;②钢结构框架、管带及其它梁柱均满足设计规范所要求的强度、耐火、防爆等性能,并加设厚型无机外防火层,以防止火灾伤害及火势蔓延;③抗震、防雷措施:建构筑物及大型框架设备采取相应的抗震、防雷措施;⑺设备机械工业炉设计①根据有关规定,设备设计中充分考虑当地的风压、地震烈度及场地等因素,对反应器等主要设备基础按7度近震地震烈度设计;②主要设备的裙座均设置防火层,对高温设备和管道均进行隔热保温;③根据设备内介质操作温度、压力和腐蚀情况,分别选用相适应的材质,以减少腐蚀,延长设备寿命;加热炉设置长明灯,以防瞬间熄火而引起炉内瓦斯爆炸,同时在炉体安装防爆门,并设置灭火蒸汽管;④对必须在高空操作的设备,根据规范要求在必要的位置均设置平台、梯子、扶手、围栏等,以保证操作人员的人身安全;⑤加热炉的燃料气管线上设置阻火器,防止回火发生事故;三防毒与职业病防治1、生产过程中会产生有毒气体硫化氢,在操作和检修过程中少量的硫化氢气体可能从密闭系统中泄漏到大气中;因此,装置中除设置硫化氢报警仪外,还配备防毒面具和空气呼吸器,以便在事故时进行自救、抢救,防止硫化氢中毒;2、据国内外炼油厂调查资料表明,在同类装置工作的操作人员及管理人员至今尚未发现患有国家规定的职业病及其他特殊病症;但为确保操作人员的身体健康,对该装置的操作人员应定期进行体检,以防患于未然;四设置安全色、安全标志1、按GB2894规定,凡容易发生事故的场所和设备设置安全警示标志,并在生产场所、作业场所的紧急通道和出入口,设置醒目的标志和指示箭头;2、按GB2893规定,对需要迅速发现并引起注意,以防发生事故的场所、部位涂有安全色;对阀门布置比较集中,易因误操作而引发事故的地方,在阀门的附近设标明输送介质的名称、符号等标志;五消防措施的设置1 压缩机、反应器、加热炉等需要重点保护的设备附近,设置箱式消火栓,其保护半径为30m;2 反应器附近设置固定式消防水炮保护;3 按照石油化工企业设计防火规范GB50160—921999年局部修订的要求在装置危险设备区设置蒸汽灭火软管;4 框架、平台上每层设置半固定式蒸汽接头;5 在高于15米的框架处,沿梯子平台敷设半固定式消防竖管;6 装置内设置的固定式露天消防设施如箱式消火栓、消防水炮等采取防冻措施;7 装置内按照石油化工企业设计防火规范GB50160—921999年版设置手提式灭火器;8 装置内报警采用电话报警,报警报至厂消防站;六劳动保护措施1、设置密闭式采样器,以减少可燃有害介质的扩散;2、有毒有害物质的装卸人员应配戴防毒面具;采取以上防范措施后,该装置的职业安全卫生设计可以满足有关标准规范的要求;。
固定床加氢工艺_概述说明以及解释

固定床加氢工艺概述说明以及解释1. 引言1.1 概述:固定床加氢工艺是一种在化学工业中广泛应用的重要技术,通过引入氢气来催化加氢反应,将有机物质转化为更有价值或更稳定的产物。
该工艺具有高效、低成本、环保等优势,在石油加工、化工合成、食品加工等领域得到了广泛应用。
1.2 文章结构:本文将分为五个部分进行阐述。
首先是引言部分,对固定床加氢工艺进行概述和说明。
接下来是固定床加氢工艺的概述,包括其基本原理、应用领域以及存在的问题和挑战。
然后是详细的固定床加氢工艺说明,包括相关的工艺步骤、设备与材料要求以及反应条件与控制策略。
紧接着是固定床加氢工艺的解释部分,包括催化剂选择与活性控制、反应机理与动力学分析以及优缺点和发展前景。
最后是结论部分,总结文章主要观点和结果,并对固定床加氢工艺的展望提出建议。
1.3 目的:本文旨在全面了解固定床加氢工艺,介绍其工艺原理、应用领域以及存在的问题和挑战,详细说明该工艺的步骤、设备要求、反应条件与控制策略,并解释相关的催化剂选择与活性控制、反应机理与动力学分析等内容。
同时,本文还将总结固定床加氢工艺的优缺点并展望其未来的发展前景,为相关领域研究人员提供参考和借鉴。
2. 固定床加氢工艺概述:2.1 工艺原理:固定床加氢工艺是一种常用的催化加氢方法,用于将有机化合物或气体通过与催化剂接触进行加氢反应,将其转化为相应的加氢产物。
该工艺基于固体催化剂的活性和选择性,在适当的温度、压力和反应条件下进行。
2.2 应用领域:固定床加氢工艺广泛应用于石油炼制、化学工业和环境保护等领域。
在石油炼制中,固定床加氢工艺可用于重质油的脱硫、裂解轻质烃的饱和、芳香族烃的脱芳等反应。
在化学工业中,该工艺可用于合成各种有机化合物,如醇类、酮类和羧酸类。
此外,固定床加氢还可以用于处理废水中的有机污染物和净化大气中的有害气体。
2.3 存在问题及挑战:尽管固定床加氢工艺具有许多优点,如操作灵活、反应效果稳定等,但也存在着一些问题和挑战。
固定床与流化床、悬浮床渣油加氢处理技术研究

固定床与流化床、悬浮床渣油加氢处理技术研究摘要:随着石油资源的日益减少和原油重质、劣化趋势的加剧,渣油加氢工艺是实现渣油清洁高效转化的关键技术,固定床渣油加氢工艺已成为渣油加工的重要手段。
根据渣油加氢工艺的反应原理,分析了固定床与流化床、悬浮床渣油加氢技术的应用,最后提出了固定床渣油加氢装置高效运行的保障措施。
关键词:炼油;固定床;流化床;悬浮床;渣油加氢工艺技术前言:渣油是原油蒸馏后其中的不理想组分、不理想杂质组成物,渣油的二次加工难度较大,多应用于炼油厂锅炉燃料,也可作为催化裂化装置的原料。
渣油内有较高的硫、氮、残碳和重金属,如果不做处理,燃烧后会产生大量的含硫气体以及温室气体,污染周围环境,威胁生态平衡,也会给下游装置造成较大影响。
渣油加氢技术能脱出渣油中大部分硫、氮、残碳以及重金属,能够大大的降低渣油燃烧后所产生的污染气体,减少废气处理量,增加了重质原油的加工量,减低了企业的加工成本,增加了企业的经济收入。
目前,渣油处理工艺多为固定床渣油加氢处理技术,其他形式的工艺技术也具有相同的效果,但是各有优缺点,本文主要对此进行研讨。
1.固定床渣油加氢工艺反应原理1.1脱硫反应作为脱硫反应沸腾床-固定床组合渣油加氢处理最为重要的化学反应,脱硫反应参与硫化物类型复杂、结构复杂,涉及流程较为复杂。
通常情况下,硫化物脱硫反应可认为是渣油借助硫化物催化作用,促使碳硫反应断裂,属于氢解反应,可释放硫化氢气体、无硫饱和烃,这类化学反应比较强烈,为不可逆反应。
加氢脱硫反应中,催化剂颗粒尺寸、催化剂孔径分布、催化剂颗粒工艺条件为三大主要影响因素。
1.2脱金属反应加氢脱金属反应主要是去除金属杂质,比如:镍、铁,金属杂质会影响残渣二次反应性能。
脱金属与脱硫反应类似,属于沸腾床-固定床组合渣油加氢处理的关键化学反应,属于一个或多个可逆反应。
该反应影响因素为催化剂颗粒尺寸、催化剂孔径分布、反应物分子扩散率。
1.3反硝化反应残渣内的氮元素存在形式为氮杂环化合物,杂环饱和后加氢,能够促进碳氮裂解,并形成气产物。
VRDS渣油加氢装置概况

VRDS渣油加氢装置概况1.1 装置简介为适应原油逐年重质化、劣质化的趋势,提高轻油收率和减少环境污染,胜利炼油厂于1989年10月份从美国雪弗隆(Chevron)公司引进了设计能力为84×104t/a的固定床减压渣油加氢脱硫装置(简称VRDS)。
该装置由华鲁工程公司设计,中石化十化建承建,1992年5月21日建成投产。
1998年,根据中石化公司整体原油加工方案的安排,胜利炼油厂需要掺炼75%(6.0 Mt/a)的进口中东高硫原油,胜利炼油厂原有以加工胜利原油为主的加工流程难以适应劣质高硫原油的加工,为此,1999年10月份装置进行了扩能改造,增加了Chevron公司的最新专利—上流式反应器(Up Flow Reactor,简称UFR),因此,装置又简称为UFR/VRDS。
2000年1月7日完成并投产。
装置改造后的设计处理能力150×104t/a(其中包括120×104t/a减压渣油及30×104t/a减压蜡油),主要对中东减压渣油进行脱硫、脱氮、脱金属并部分裂解为石脑油、柴油和蜡油。
设计运转初期,349℃产品馏份的MCR为<8.5%,S<0.5%,末期MCR<9.2%、S<0.8%,生产的石脑油可作为乙烯原料,柴油是优质的低硫轻柴油产品,常压渣油是优质的催化裂化原料。
2005年,随着VRDS—FCC组合工艺的投用,常压和减压渣油混合做为催化原料,催化回炼油改进本装置处理,优化了FCC装置原料性质,提高了FCC装置轻油收率。
2006年10月份,利用第五周期停工检修时机,进行了装置节能改造,主要改造内容是停开减压塔,对原料/产品换热网络进行优化和流程动改,及对加热炉烟气余热回收系统进行改造。
2006年11月14日装置开工正常。
目前随着催化剂级配及操作的不断优化,装置运行周期已延长到480天。
图3-1 渣油加氢装置方块流程图1.2 工艺原理1.2.1 工艺过程渣油加氢作为重油加工的重要手段,在整个炼厂的加工工艺中有着十分重要的地位。
浅析国内外渣油加氢处理技术发展现状及分析
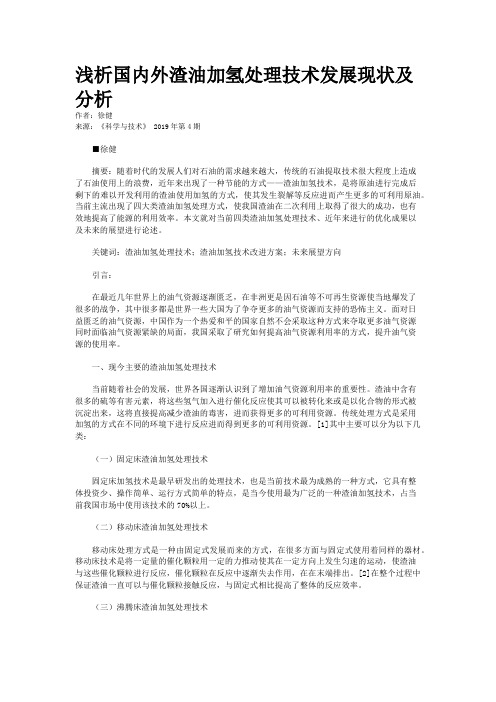
浅析国内外渣油加氢处理技术发展现状及分析作者:徐健来源:《科学与技术》 2019年第4期■徐健摘要:随着时代的发展人们对石油的需求越来越大,传统的石油提取技术很大程度上造成了石油使用上的浪费,近年来出现了一种节能的方式——渣油加氢技术,是将原油进行完成后剩下的难以开发利用的渣油使用加氢的方式,使其发生裂解等反应进而产生更多的可利用原油。
当前主流出现了四大类渣油加氢处理方式,使我国渣油在二次利用上取得了很大的成功,也有效地提高了能源的利用效率。
本文就对当前四类渣油加氢处理技术、近年来进行的优化成果以及未来的展望进行论述。
关键词:渣油加氢处理技术;渣油加氢技术改进方案;未来展望方向引言:在最近几年世界上的油气资源逐渐匮乏,在非洲更是因石油等不可再生资源使当地爆发了很多的战争,其中很多都是世界一些大国为了争夺更多的油气资源而支持的恐怖主义。
面对日益匮乏的油气资源,中国作为一个热爱和平的国家自然不会采取这种方式来夺取更多油气资源同时面临油气资源紧缺的局面,我国采取了研究如何提高油气资源利用率的方式,提升油气资源的使用率。
一、现今主要的渣油加氢处理技术当前随着社会的发展,世界各国逐渐认识到了增加油气资源利用率的重要性。
渣油中含有很多的硫等有害元素,将这些氢气加入进行催化反应使其可以被转化来或是以化合物的形式被沉淀出来,这将直接提高减少渣油的毒害,进而获得更多的可利用资源。
传统处理方式是采用加氢的方式在不同的环境下进行反应进而得到更多的可利用资源。
[1]其中主要可以分为以下几类:(一)固定床渣油加氢处理技术固定床加氢技术是最早研发出的处理技术,也是当前技术最为成熟的一种方式,它具有整体投资少、操作简单、运行方式简单的特点,是当今使用最为广泛的一种渣油加氢技术,占当前我国市场中使用该技术的70%以上。
(二)移动床渣油加氢处理技术移动床处理方式是一种由固定式发展而来的方式,在很多方面与固定式使用着同样的器材。
移动床技术是将一定量的催化颗粒用一定的力推动使其在一定方向上发生匀速的运动,使渣油与这些催化颗粒进行反应,催化颗粒在反应中逐渐失去作用,在在末端排出。
渣油加氢工艺流程

第一节工艺技术路线及特点工艺技术路线300X10*“渣油加範脱硫装置采用CLG公司的固定床渣油加氮脱硫匚艺技术.该匸艺技术満足操作删期SOOOh.柴油产骷硫含址不大于500ppm.加氢常渣产品硫含畫不大于0.35硫、残炭不大于5・5w& Ni+V不大于15pp■的要求。
二、工艺技术特点1、反瓯部分设置两个系列.每个系列可以单开单停(单开单停定指装置二个系列分别进行正常生产和停工更换供化剂)O由于渣油加氫脱硫装逆的设计操作用期与其它主耍生产装亀不一致.从全厂生产安排的角度.单开单停可以有效解决原料储存、催化裂化装迸进料址等何题.并便全厂油品调配更灵活.2.反应部分釆用热窩分工艺涼程.减少反咸潦出物冷却负荷:优化换热涼程.充分回收热址.降低能耗,3.反应部分高压换热器采用双壳.双弓型式.强化传热效果.提高传热效率。
4.反应器为单床层设置.易于催化剂装卸.尤其是便于卸催化剂.5.采用原料油自动反冲洗过滤器系统.滤除大于25心以上朵质.减缓反应器压降增大速度.延长装置操作周期;6.原料油换热系统设置注阻垢剂设施.延长操作周期.降低能耗.而且在停1:换剂期间可减少换热器和其它设备的检修匸作•7.原料油缓冲確采用氮气覆盖措施.以防止原料油与空气接触从而减轻高温部位的结焦程度:8.采用炉前混氮流程.避免进料加热炉炉管结焦.9.第一台反应器入口温度通过调节加热炉燃料和高压换热器旁路址来控剑.其他反应器入口温度通过调节急冷氮虽來控制,10.在热商分气空冷器入口处设注水设施.避免钱盐在低鮎部位的沉枳。
11,循环氫脱硫塔前设高压离心式分离器除去携带的液体婭类.域少循坏氮脱硫塔的起泡倾向.有利丁•循环氮脱硫的正常操作。
12.设赳离压膜分离系统.保证反腹氮分压。
13.冷低压闪蒸谜的富氮气体去加氮裂化装魁脱硫后去PSA回收包气,14.新宜压缩机釆用二开一备•每台50%负荷.单机负荷校小.方便制造.且装置有备机,15.分憎部分采用主汽提塔+分懈塔流程.在汽提塔除去轻烧和硫化氮.降低分他塔材质耍求.分懈塔设侧线柴油汽提塔及中段回流加热原料油.降低塔顶冷却负荷.捉高能虽利用率.减小分懈塔塔径。
沸腾床-固定床组合渣油加氢处理技术研究

沸腾床-固定床组合渣油加氢处理技术研究杨涛;刘建锟;耿新国【摘要】沸腾床渣油加氢技术与固定床渣油加氢技术组合可以明显改善固定床进料性质,大幅度降低杂质含量,大大改善固定床操作;同时可以扩大可加工的原料范围,延长操作周期.中试数据表明,加工金属质量分数分别为118,233μg/g、残炭质量分数分别为15.7%,21.1%的劣质渣油,沸腾床与固定床组合工艺均可稳定操作,所得加氢渣油金属质量分数分别为10.6,7.8μg/g,残炭质量分数分别为5.6%,5.2%,可以直接作为催化裂化装置原料,从而实现劣质渣油的高效转化.通过技术特点和技术经济分析,并与单独的固定床方案对比,发现沸腾床与固定床组合渣油加氢处理新技术具有更好的盈利能力,并可实现3 a稳定运转,从而与下游装置相匹配,实现同步开停工.【期刊名称】《炼油技术与工程》【年(卷),期】2015(045)005【总页数】4页(P24-27)【关键词】沸腾床;固定床;渣油;加氢;组合工艺【作者】杨涛;刘建锟;耿新国【作者单位】中国石油化工股份有限公司抚顺石油化工研究院,辽宁省抚顺市113001;中国石油化工股份有限公司抚顺石油化工研究院,辽宁省抚顺市113001;中国石油化工股份有限公司抚顺石油化工研究院,辽宁省抚顺市113001【正文语种】中文在世界原油劣质化和产品清洁化要求的交互推动下,渣油加工技术的开发和选择需要应对新的形势。
相较于其他类型的渣油加氢技术,固定床渣油加氢技术的投资和操作费用最低、反应器利用率高、运行安全简单,是目前渣油加氢技术的首选技术,装置的总加工能力占渣油加氢总加工能力的四分之三以上[1]。
但其原料适应性差,运行周期短,限制了炼油企业原油采购和生产调度的灵活性,进而影响其经济效益。
沸腾床渣油加氢其反应器内温度均匀、运转周期长、装置操作灵活,是加工高硫、高残炭、高金属重质原油、劣质渣油的重要技术,在工业应用中受到越来越多的关注。
渣油加氢技术工艺原理

渣油加氢技术工艺原理由于石油资源有限、原油变重变劣、中间馏分油的需求量增加及环保法规越来越严格等因素,渣油轻质化技术不断发展,通过渣油加氢处理后的渣油,送到催化裂化装置处理,生产出大量的合格轻质油。
减压渣油是原油经过加工后密度最大、杂质组分含量最高的油品,含有相当多的金属、硫、氮、及残炭等物质,杂质金属、氮会使下游装置催化剂失去活性,严重影响下游装置的生产周期;硫化物会腐蚀生产装置的设备及管线;残炭在下游装置催化裂化装置深加工过程中,极不稳定,很容易结焦,影响催化裂化装置的长周期运行;在装置原料中掺入减压重蜡油与焦化蜡油,有效降低渣油进料的粘度与杂质含量,利于催化加氢反应的进行,利于装置的操作与长周期运行。
本装置采用固定床加氢工艺,在适当的温度、压力、氢油比和空速条件下,原料油和氢气在催化剂的作用下进行反应,使油品中的杂质,即硫、氮、氧化物转化成为相应的易于除去的H2S、NH3和H2O而脱除,重金属杂质与H2S反应生成金属硫化物沉积在催化剂上,稠环芳烃及一部分不饱和烃得到加氢饱和,为下游装置生产出合格的原料油,同时副产出部分柴油及石脑油。
在渣油加氢处理过程中,所发生的化学反应很多,也非常复杂,但主要有以下几种反应发生:1)加氢脱硫反应2)加氢脱金属反应3)加氢脱氮反应4)加氢脱残碳反应5)加氢脱氧反应6)芳烃饱和反应7)烯烃饱和反应8)加氢裂化反应9)缩合生焦反应2.1加氢脱硫反应(HDS)渣油加氢脱硫反应是渣油加氢处理过程中所发生的最主要的化学反应,在催化剂和氢气的作用下,通过加氢脱硫反应,各种含硫化合物转化为不含硫的烃类和H 2S 。
烃类留在产品中,而H 2S 从反应物中脱除。
原油中大部分的硫存在于渣油中,渣油中的硫主要分布在芳烃、胶质和沥青质中,其中绝大部分的硫以噻吩和噻吩衍生物的形式存在。
通过氢解反应将这种大分子的C -S 键断开,使S 转化为H 2S 。
以噻吩和苯并噻吩为例,加氢脱硫反应式为:存在于非沥青质中的硫,在加氢条件下较容易脱除,可达到较高的转化深度,但存在于沥青质中的硫,由于沥青质的大分子结构,则很难脱除,因此,渣油加氢脱硫过程的脱硫率是有一定限度的。
关于对渣油加氢脱硫技术的研究

关于对渣油加氢脱硫技术的研究【摘要】自七十年代以来,石油开采出来的原油质量开始变差,原油中的重质油含量尤其是渣油收率出现增加的趋势,而渣油和燃料油在燃烧过程中,渣油中所含的硫化物会与氧气结合形成二氧化硫、三氧化硫等气体排放到空气中,进而形成酸雨,影响人类正常的生活。
为了改善渣油的燃烧性能,降低有毒气体的排放,需要对渣油进行脱硫处理,来去除硫化物,并使渣油转化为易以加工处理的原料油。
对渣油进行脱硫处理的方式有加氢和不加氢两种,本文针对渣油的加氢脱硫处理技术,介绍了几种渣油脱硫装置,以及雪佛龙专利、ifp专利及联合油专利等三种固定床式渣油脱硫技术工艺。
【关键词】渣油加氢脱硫雪佛龙专利 ifp专利联合油专利1 几种渣油加氢脱硫装置的介绍为了进行渣油的脱硫处理,首先就要选择合适合理的加氢脱硫装置,本文主要介绍三套用于渣油加氢脱硫的装置:(1)中石化齐鲁分公司胜利炼油厂减压渣油加氢脱硫处理装置(简称vrds)是引进美国雪弗隆(chevron)公司的固定床渣油加氢专利技术,由华鲁工程公司设计,原设计规模为0.84 mt/a,用于处理孤岛减压渣油,并于1992年5月21日一次投料试车成功;1999年采用了chevron公司的最新专利—上流式反应器(up flowreactor,简称ufr)技术对装置进行扩能改造,以满足原料性质、处理量及产品质量等大幅度变化的要求。
ufr-vrds装置于2000年1月7日顺利投产,成为世界上首套采用ufr-vrds 联合技术的装置。
(2)西太平洋石油化工有限公司的200万t/a加氢脱硫装置,该装置以处理进口的沙特轻、重混合原油(50:50)的常压渣油为主,该装置是联合油公司的专利,并有该公司提供工艺包,由中国石油化工总公司北京设计院完成最初设计和最终设计;(3)茂名石油化工公司2.0mt/a渣油加氢脱硫装置,该装置以减压渣油和减压蜡油的混合油为原料,其主要产品加氢脱硫渣油能满足重油催化裂化进料的性质要求,而最终实现了渣油的完全催化转化。