如何解决压片机发生片剂脱落现象
压片机常见问题及解决办法
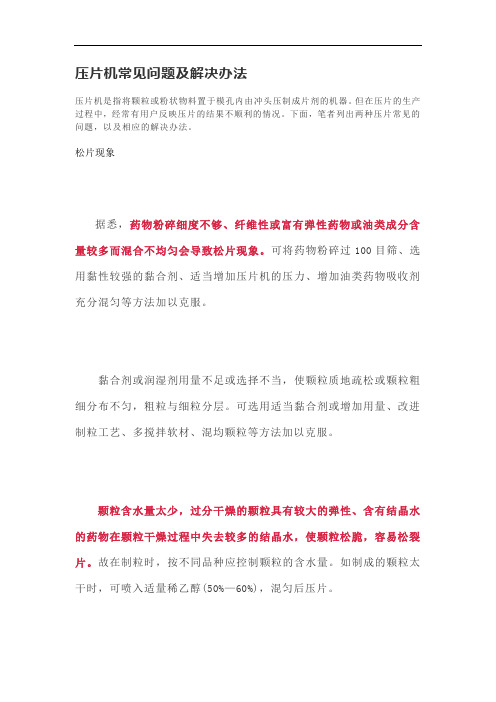
压片机常见问题及解决办法压片机是指将颗粒或粉状物料置于模孔内由冲头压制成片剂的机器。
但在压片的生产过程中,经常有用户反映压片的结果不顺利的情况。
下面,笔者列出两种压片常见的问题,以及相应的解决办法。
松片现象据悉,药物粉碎细度不够、纤维性或富有弹性药物或油类成分含量较多而混合不均匀会导致松片现象。
可将药物粉碎过100目筛、选用黏性较强的黏合剂、适当增加压片机的压力、增加油类药物吸收剂充分混匀等方法加以克服。
黏合剂或润湿剂用量不足或选择不当,使颗粒质地疏松或颗粒粗细分布不匀,粗粒与细粒分层。
可选用适当黏合剂或增加用量、改进制粒工艺、多搅拌软材、混均颗粒等方法加以克服。
颗粒含水量太少,过分干燥的颗粒具有较大的弹性、含有结晶水的药物在颗粒干燥过程中失去较多的结晶水,使颗粒松脆,容易松裂片。
故在制粒时,按不同品种应控制颗粒的含水量。
如制成的颗粒太干时,可喷入适量稀乙醇(50%—60%),混匀后压片。
业内表示,压片过程中发生松片现象可能还与药物本身的性质有关。
例如,密度大压出的片剂虽有一定的硬度,但经不起碰撞和震摇;颗粒的流动性差,填入模孔的颗粒不均匀;或者有较大块或颗粒、碎片堵塞刮粒器及下料口时,影响填充量。
此外,压片机械也会影响压片的效果。
如果压力过小,多冲压片机冲头长短不齐,车速过快或加料斗中颗粒时多时少。
可通过调节压力、检查冲模是否配套完整、调整车速、勤加颗粒使料斗内保持一定的存量等方法克服。
裂片现象片剂受到震动或经放置时,有从腰间裂开的称为腰裂;从顶部裂开的称为顶裂,腰裂和顶裂总称为裂片。
药物本身弹性较强、纤维性药物或因含油类成分较多。
可加入糖粉以减少纤维弹性,加强黏合作用或增加油类药物的吸收剂,充分混匀后压片。
黏合剂或润湿剂不当或用量不够,颗粒在压片时粘着力差。
颗粒太干、含结晶水药物失去过多造成裂片,解决方法与松片相同。
有些结晶型药物,未经过充分的粉碎。
可将此类药物充分粉碎后制粒。
细粉过多、润滑剂过量引起的裂片,粉末中部分空气不能及时逸出而被压在片剂内,当解除压力后,片剂内部空气膨胀造成裂片,可筛去部分细粉与适当减少润滑剂用量加以克服。
压片过程中易出现的问题及解决方法
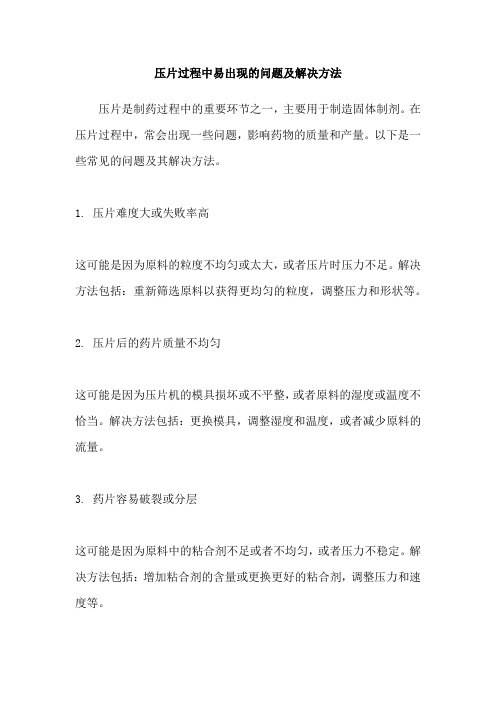
压片过程中易出现的问题及解决方法
压片是制药过程中的重要环节之一,主要用于制造固体制剂。
在压片过程中,常会出现一些问题,影响药物的质量和产量。
以下是一些常见的问题及其解决方法。
1. 压片难度大或失败率高
这可能是因为原料的粒度不均匀或太大,或者压片时压力不足。
解决方法包括:重新筛选原料以获得更均匀的粒度,调整压力和形状等。
2. 压片后的药片质量不均匀
这可能是因为压片机的模具损坏或不平整,或者原料的湿度或温度不恰当。
解决方法包括:更换模具,调整湿度和温度,或者减少原料的流量。
3. 药片容易破裂或分层
这可能是因为原料中的粘合剂不足或者不均匀,或者压力不稳定。
解决方法包括:增加粘合剂的含量或更换更好的粘合剂,调整压力和速度等。
4. 药片的重量或尺寸不符合规格
这可能是因为原料的流量不稳定,或者模具的尺寸不正确。
解决方法包括:调整原料的流量和压力,或者更换正确尺寸的模具。
5. 压片机噪音过大或发生故障
这可能是因为机器的部件损坏,或者机器清洗和维护不当。
解决方法包括:定期检查机器的各个部件,及时更换损坏的部件,遵循正确的机器清洗和维护程序等。
总之,在压片过程中,需要注意各种因素,如原料的粒度、湿度和温度,压力和速度的调整,模具的质量和尺寸,以及机器的清洗和维护等。
只有这样,才能保证药物的质量和产量。
生产过程中得压片问题及解决办法
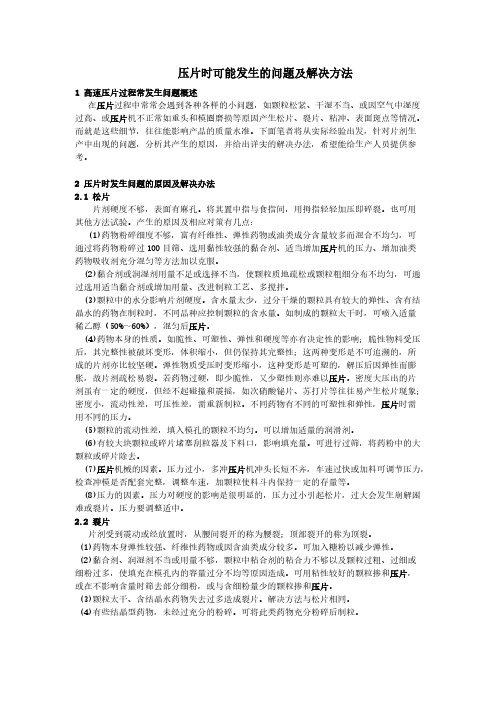
压片时可能发生的问题及解决方法1 高速压片过程常发生问题概述在压片过程中常常会遇到各种各样的小问题,如颗粒松紧、干湿不当、或因空气中湿度过高、或压片机不正常如重头和模圈磨损等原因产生松片、裂片、粘冲、表面斑点等情况。
而就是这些细节,往往能影响产品的质量水准。
下面笔者将从实际经验出发,针对片剂生产中出现的问题,分析其产生的原因,并给出详实的解决办法,希望能给生产人员提供参考。
2 压片时发生问题的原因及解决办法2.1 松片片剂硬度不够,表面有麻孔。
将其置中指与食指间,用拇指轻轻加压即碎裂。
也可用其他方法试验。
产生的原因及相应对策有几点:(1)药物粉碎细度不够,富有纤维性、弹性药物或油类成分含量较多而混合不均匀,可通过将药物粉碎过100目筛、选用黏性较强的黏合剂、适当增加压片机的压力、增加油类药物吸收剂充分混匀等方法加以克服。
(2)黏合剂或润湿剂用量不足或选择不当,使颗粒质地疏松或颗粒粗细分布不均匀,可通过选用适当黏合剂或增加用量、改进制粒工艺、多搅拌。
(3)颗粒中的水分影响片剂硬度。
含水量太少,过分干燥的颗粒具有较大的弹性、含有结晶水的药物在制粒时,不同品种应控制颗粒的含水量。
如制成的颗粒太干时,可喷入适量稀乙醇(50%~60%),混匀后压片。
(4)药物本身的性质。
如脆性、可塑性、弹性和硬度等亦有决定性的影响;脆性物料受压后,其完整性被破坏变形,体积缩小,但仍保持其完整性;这两种变形是不可追溯的,所成的片剂亦比较坚硬。
弹性物质受压时变形缩小,这种变形是可塑的,解压后因弹性而膨胀,故片剂疏松易裂。
若药物过硬,即少脆性,又少塑性则亦难以压片。
密度大压出的片剂虽有一定的硬度,但经不起碰撞和震摇,如次硝酸铋片、苏打片等往往易产生松片现象;密度小,流动性差,可压性差,需重新制粒。
不同药物有不同的可塑性和弹性,压片时需用不同的压力。
(5)颗粒的流动性差,填入模孔的颗粒不均匀。
可以增加适量的润滑剂。
(6)有较大块颗粒或碎片堵塞刮粒器及下料口,影响填充量。
压片过程中可能出现的问题及解决办法
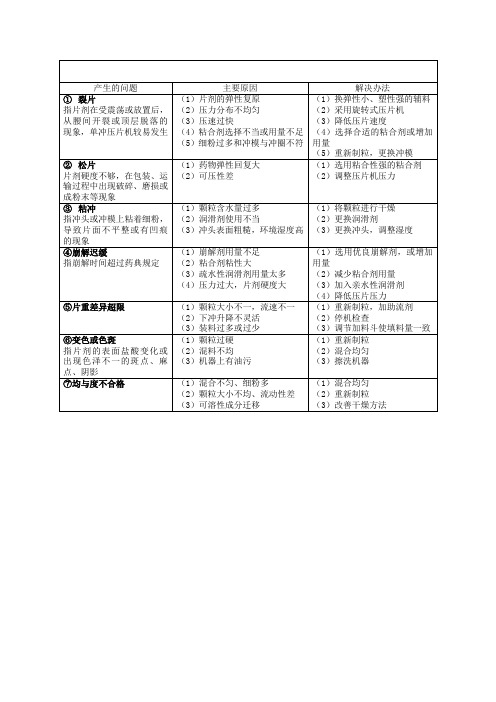
(1)重新制粒,加助流剂
(2)停机检查
(3)调节加料斗使填料量一致
⑥变色或色斑
指片剂的表面盐酸变化或出现色泽不一的斑点、麻点、阴影
(1)颗粒过硬
(2)混料不均
(3)机器上有油污
(1)重新制粒
(2)混合均匀
(3)擦洗机器
⑦均与度不合格
(1)混合不匀、细粉多
(2)颗粒大小不均、流动性差
(5)重新制粒,更换冲模
2松片
片剂硬度不够,在包装、运输过程中出现破碎、磨损或成粉末等现象
(1)药物弹性回复大
(2)可压性差
(1)选用粘合性强的粘合剂
(2)调整压片机压力
3粘冲
指冲头或冲模上粘着细粉,导致片面不平整或有凹痕的现象
(1)颗粒含水量过多
(2)润滑剂使用不当
(3)冲头表面粗糙,环境湿度高
(1)将颗粒进行干燥
(2)更换润滑剂
(3)更换冲头,调整湿度
④崩解迟缓
指崩解时间超过药典规定
(1)崩解剂用量不足
(2)粘合剂粘性大
(3)疏水性润滑剂用量太多
(4)压力过大,片剂硬度大
(1)选用优良崩解剂,或增加用量
(2)减少粘合剂用量
(3)加入亲水性润滑剂
(4)降低压片压力
⑤片重差异超限
(1)颗粒大小不一,流速不一
(2)下冲升降不灵活
产生的问题
主要原因
解决办法
1裂片
指片剂在受震荡或放置后,从腰间开裂或顶层脱落的现象,单冲压片机较易发生
(1)片剂的弹性复原
(2)压力分布不均匀
(3)压速过快
(4)粘合剂选择不当或用量不足
(5)细粉过多和冲模与冲圈不符
压片过程中可能出现的问题及解决办法

(3)降低压片速度
(4)选择合适的粘合剂或增加用量
(5)重新制粒,更换冲模
2松片
片剂硬度不够,在包装、运输过程中出现破碎、磨损或成粉末等现象
(1)药物弹性回复大
(2)可压性差
(1)选用粘合性强的粘合剂
(2)调整压片机压力
3粘冲
指冲头或冲模上粘着细粉,导致片面不平整或有凹痕的现象
压片过程中可能出现的问题及解决办法(总1页)
压片过程中可能出现的问题及解决办法
产生的问题
主要原因
解决办法
1裂片
指片剂在受震荡或放置后,从腰间开裂或顶层脱落的现象,单冲压片机较易发生
(1)片剂的弹性复原
(2)压力分布不均匀
(3)压速过快
(4)粘合剂选择不当或用量不足
(5)细粉过多和冲模与冲圈不符
(1)换弹性小、塑性强的辅料
(1)颗粒含水量过多
(2)润滑剂使用不当
(3)冲头表面粗糙,环境湿度高
(1)将颗粒进行干燥
(2)更换润滑剂
(3)更换冲头,调整湿度
④崩解迟缓
指崩解时间超过药典规定
(1)崩解剂用量不足
(2)粘合剂粘性大
(3)疏水性润滑剂用量太多
良崩解剂,或增加用量
(2)减少粘合剂用量
(3)加入亲水性润滑剂
(4)降低压片压力
⑤片重差异超限
(1)颗粒大小不一,流速不一
(2)下冲升降不灵活
(3)装料过多或过少
(1)重新制粒,加助流剂
(2)停机检查
(3)调节加料斗使填料量一致
⑥变色或色斑
指片剂的表面盐酸变化或出现色泽不一的斑点、麻点、阴影
(1)颗粒过硬
(2)混料不均
压片操作可能出现的质量问题

压⽚操作可能出现的质量问题压⽚操作可能出现的质量问题1、松⽚因压⼒不⾜、冲头长短不齐(多冲机),粘合剂和湿润剂过少引起松⽚的,可⽤调整压⼒,修检冲头,增加粘合剂解决。
⼀般弹性⼤的(如⼲酵母、植物药粉末)需⽤较⼤的压⼒及粘性较强的粘合剂。
含⽔量太⼩(完全⼲燥)的颗粒有较⼤的弹性变形,所压成的⽚剂硬度较差;⽽许多含有结晶⽔的药物,在颗粒烘于时因失去了⼀部分结晶⽔,颗粒松脆,也容易出现松⽚。
这些情况,可在制粒中喷⼊适量的稀⼄醇(%"( &)"(),以恢复其适当的湿度,混合均匀后压⽚。
2、裂⽚(顶裂)即⽚剂受震动或放置时,出现腰间裂开或顶部脱落⼀层的现象。
常因粘合剂不⾜,或颗粒过粗、过细、细粉过多,或车速过快、压⼒过⼤,或冲模磨损、压⼒不均等引起,可酌情克服。
因颗粒中油状成分过多产⽣裂⽚的,则应以药粉来吸收或另加吸收剂,混合均匀后压⽚。
3、粘冲压⽚时冲头或模圈上若有细粉粘着,会使压出的⽚剂带凹痕或边缘不齐整。
常由于颗粒⽔分过多,油滴没有混合均匀,或润滑剂不⾜,或冲模表⾯粗糙、裂损等引起,应查明原因后解决。
制剂室内的空⽓湿度过⾼,也会引起粘冲。
4、崩解迟缓由于崩解剂选择不当或⽤量不⾜,粘合剂⽤量过⼤,或压⽚时压⼒过⼤或颗粒过硬过粗,都会位⽚剂崩解时间延迟。
在地解剂中配⼊少量表⾯活性剂(⼗⼆烷基磺酸钠),可促进⽚剂的崩解。
⽤浸膏类药物压⽚,其⽚剂常常崩解迟缓,如在浸膏中加⼊适量中草药细粉,混合均匀后制粒,便可改善其崩解度。
崩解迟缓影响药物的溶出速度,特别是难溶性药物,可通过药物与辅料的合理混合⽽得到解决。
例如某些难溶性药物可先与⽔溶性辅料(如+,-*""")混合,使迅速溶解⽽呈细⼩微粒分散后再与填充剂混合制⽚,由于溶出表⾯积增⼤,可提⾼药物的溶出速度。
5、花斑带⾊的药物特别是中草药⽚剂,由于颗粒过粗或润滑剂不均匀⽽出现花斑时,应注意调整颗粒粗细并充分混句后压⽚。
压片机出现片剂产生脱落现象了

压片机是指将颗粒或粉状物料置于模孔内由冲头压制成片剂的机器。
在中、西药的制药工艺中,压片机是必不可少的设备之一。
近年来,我国环境污染问题日益突出,GMP 标准也在不断提高,压片机设备在面临升级转型的同时,市场上涌现的压片机机型也越来越多样,如单冲式压片机、花篮式压片机、旋转式压片机等。
这些设备功能各异,可以满足不同行业压片的需求然而在压片机的使用过程中,经常有用户反映压片的结果不顺利的情况。
例如,近日就有药企表示,公司生产片剂的设备不太中用,出现了片剂脱落的现象,这是什么情况呢?某压片机生产制造厂的技术人员表示,片剂从模孔中被推出后,产生了脱落的现象被称之为裂片。
有时候是片剂的中间裂开分为两片,但这种情况很少发生。
对此,技术人员针对裂片现象作了几种原因的分析,笔者对内容进行了整理。
原因一:颗粒中细粉过多据介绍,压片机在压片过程中发生裂片的原因一般都是颗粒中细粉过多,导致压缩的时候空气没有逸出,压缩的速度太快,冲跟模孔之见的间隙比较小,空气被封闭在片剂内,压力过后空气开始膨胀就会导致裂片现象的发生。
遇到这种情况时,应该把颗粒中的细粉去除,这样才可以使片剂里的空气可以逸出。
原因二:压缩行为不当颗粒压缩的行为不当,容易造成压制的时候压力不均匀。
因为颗粒有较强的弹性,所以在压片压制过程当中会产生裂片,压制好后的片剂弹性复原率比较高。
原因三:颗粒过于干燥颗粒过于干燥也会导致裂片,这时我们应该调节含水量来防止裂片。
原因四:压力过大如果压力过大也会导致裂片现象。
在这种情况下发生裂片,我们可以适当的降低压力防止它裂片。
技术人员表示,不同的压片机设备压力都不同。
其中,单冲压片机压制片剂的时候是单方面的压力,旋转压片机压片的时候是上下一起压,弹性复原率跟压力大小是有关系的,片剂上表面受压时间短,所以先从顶部裂片。
知道这点后就可以指导怎么防止裂片现象的发生,例如,可以调整处方设计,增加原料跟辅料的塑性,改善颗粒压缩成型时间等。
压片常见问题及解决方法
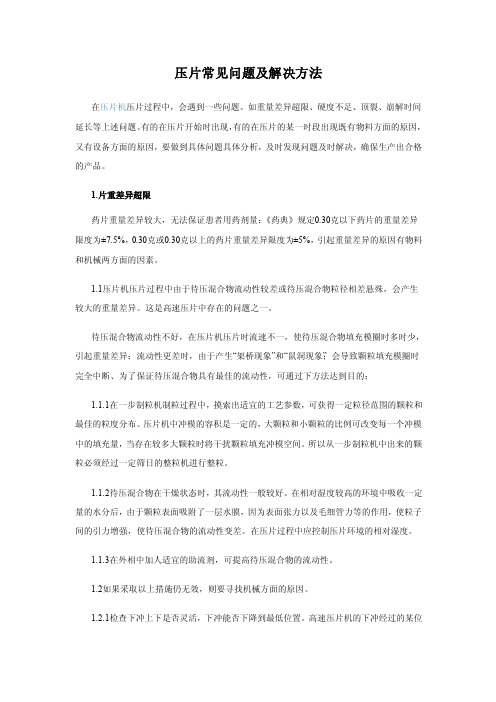
压片常见问题及解决方法在压片机压片过程中,会遇到一些问题。
如重量差异超限、硬度不足、顶裂、崩解时间延长等上述问题。
有的在压片开始时出现,有的在压片的某一时段出现既有物料方面的原因,又有设备方面的原因,要做到具体问题具体分析,及时发现问题及时解决,确保生产出合格的产品。
1.片重差异超限药片重量差异较大,无法保证患者用药剂量:《药典》规定0.30克以下药片的重量差异限度为±7.5%,0.30克或0.30克以上的药片重量差异限度为±5%,引起重量差异的原因有物料和机械两方面的因素。
1.1压片机压片过程中由于待压混合物流动性较差或待压混合物粒径相差悬殊,会产生较大的重量差异。
这是高速压片中存在的问题之一。
待压混合物流动性不好,在压片机压片时流速不一,使待压混合物填充模圈时多时少,引起重量差异:流动性更差时,由于产生“架桥现象”和“鼠洞现象”;会导致颗粒填充模圈时完全中断、为了保证待压混合物具有最佳的流动性,可通过下方法达到目的:1.1.1在一步制粒机制粒过程中,摸索出适宜的工艺参数,可获得一定粒径范围的颗粒和最佳的粒度分布。
压片机中冲模的容积是一定的,大颗粒和小颗粒的比例可改变每一个冲模中的填充量,当存在较多大颗粒时将干扰颗粒填充冲模空间。
所以从一步制粒机中出来的颗粒必须经过一定筛日的整粒机进行整粒。
1.1.2待压混合物在干燥状态时,其流动性一般较好。
在相对湿度较高的环境中吸收一定量的水分后,由于颗粒表面吸附了一层水膜,因为表面张力以及毛细管力等的作用,使粒子间的引力增强,使待压混合物的流动性变差。
在压片过程中应控制压片环境的相对湿度。
1.1.3在外相中加人适宜的助流剂,可提高待压混合物的流动性。
1.2如果采取以上措施仍无效,则要寻找机械方面的原因。
1.2.1检查下冲上下是否灵活,下冲能否下降到最低位置。
高速压片机的下冲经过的某位置,安装有压力感受器,通过一定的反馈系统来自动控制下冲的下降位置,从而控制冲模的填充深度,最终达到自动调节片重的目的。
压片机压片过程可能出现的问题及解决办法
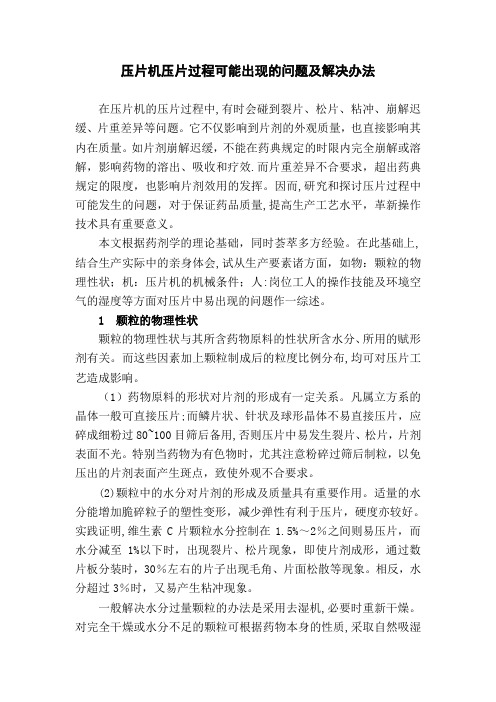
压片机压片过程可能出现的问题及解决办法在压片机的压片过程中,有时会碰到裂片、松片、粘冲、崩解迟缓、片重差异等问题。
它不仅影响到片剂的外观质量,也直接影响其内在质量。
如片剂崩解迟缓,不能在药典规定的时限内完全崩解或溶解,影响药物的溶出、吸收和疗效.而片重差异不合要求,超出药典规定的限度,也影响片剂效用的发挥。
因而,研究和探讨压片过程中可能发生的问题,对于保证药品质量,提高生产工艺水平,革新操作技术具有重要意义。
本文根据药剂学的理论基础,同时荟萃多方经验。
在此基础上,结合生产实际中的亲身体会,试从生产要素诸方面,如物:颗粒的物理性状;机:压片机的机械条件;人:岗位工人的操作技能及环境空气的湿度等方面对压片中易出现的问题作一综述。
1 颗粒的物理性状颗粒的物理性状与其所含药物原料的性状所含水分、所用的赋形剂有关。
而这些因素加上颗粒制成后的粒度比例分布,均可对压片工艺造成影响。
(1)药物原料的形状对片剂的形成有一定关系。
凡属立方系的晶体一般可直接压片;而鳞片状、针状及球形晶体不易直接压片,应碎成细粉过80~100目筛后备用,否则压片中易发生裂片、松片,片剂表面不光。
特别当药物为有色物时,尤其注意粉碎过筛后制粒,以免压出的片剂表面产生斑点,致使外观不合要求。
(2)颗粒中的水分对片剂的形成及质量具有重要作用。
适量的水分能增加脆碎粒子的塑性变形,减少弹性有利于压片,硬度亦较好。
实践证明,维生素C片颗粒水分控制在1.5%~2%之间则易压片,而水分减至1%以下时,出现裂片、松片现象,即使片剂成形,通过数片板分装时,30%左右的片子出现毛角、片面松散等现象。
相反,水分超过3%时,又易产生粘冲现象。
一般解决水分过量颗粒的办法是采用去湿机,必要时重新干燥。
对完全干燥或水分不足的颗粒可根据药物本身的性质,采取自然吸湿或酌喷适宜浓度乙醇,静置或密闭吸湿5小时左右过筛后压片.如含结晶水的药物颗粒,结晶水失去过多时出现的裂片、松片、崩解迟缓等情况则可采用此法解决。
片剂裂片的原因及解决方法
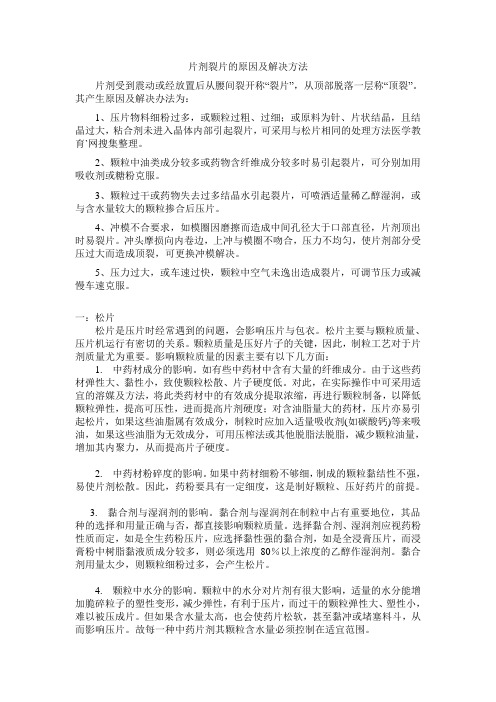
片剂裂片的原因及解决方法片剂受到震动或经放置后从腰间裂开称“裂片”,从顶部脱落一层称“顶裂”。
其产生原因及解决办法为:1、压片物料细粉过多,或颗粒过粗、过细;或原料为针、片状结晶,且结晶过大,粘合剂未进入晶体内部引起裂片,可采用与松片相同的处理方法医学教育`网搜集整理。
2、颗粒中油类成分较多或药物含纤维成分较多时易引起裂片,可分别加用吸收剂或糖粉克服。
3、颗粒过干或药物失去过多结晶水引起裂片,可喷洒适量稀乙醇湿润,或与含水量较大的颗粒掺合后压片。
4、冲模不合要求,如模圈因磨擦而造成中间孔径大于口部直径,片剂顶出时易裂片。
冲头摩损向内卷边,上冲与模圈不吻合,压力不均匀,使片剂部分受压过大而造成顶裂,可更换冲模解决。
5、压力过大,或车速过快,颗粒中空气未逸出造成裂片,可调节压力或减慢车速克服。
一:松片松片是压片时经常遇到的问题,会影响压片与包衣。
松片主要与颗粒质量、压片机运行有密切的关系。
颗粒质量是压好片子的关键,因此,制粒工艺对于片剂质量尤为重要。
影响颗粒质量的因素主要有以下几方面:1. 中药材成分的影响。
如有些中药材中含有大量的纤维成分。
由于这些药材弹性大、黏性小,致使颗粒松散、片子硬度低。
对此,在实际操作中可采用适宜的溶媒及方法,将此类药材中的有效成分提取浓缩,再进行颗粒制备,以降低颗粒弹性,提高可压性,进而提高片剂硬度;对含油脂量大的药材,压片亦易引起松片,如果这些油脂属有效成分,制粒时应加入适量吸收剂(如碳酸钙)等来吸油,如果这些油脂为无效成分,可用压榨法或其他脱脂法脱脂,减少颗粒油量,增加其内聚力,从而提高片子硬度。
2. 中药材粉碎度的影响。
如果中药材细粉不够细,制成的颗粒黏结性不强,易使片剂松散。
因此,药粉要具有一定细度,这是制好颗粒、压好药片的前提。
3. 黏合剂与湿润剂的影响。
黏合剂与湿润剂在制粒中占有重要地位,其品种的选择和用量正确与否,都直接影响颗粒质量。
选择黏合剂、湿润剂应视药粉性质而定,如是全生药粉压片,应选择黏性强的黏合剂,如是全浸膏压片,而浸膏粉中树脂黏液质成分较多,则必须选用80%以上浓度的乙醇作湿润剂。
片剂裂片的原因及解决方法
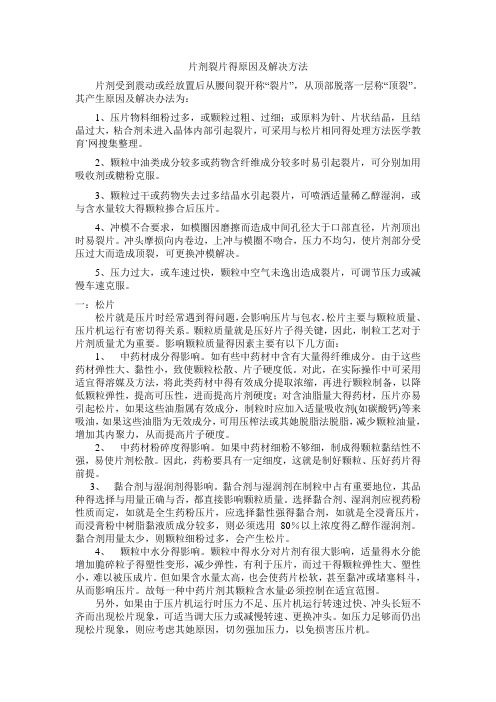
片剂裂片得原因及解决方法片剂受到震动或经放置后从腰间裂开称“裂片”,从顶部脱落一层称“顶裂”。
其产生原因及解决办法为:1、压片物料细粉过多,或颗粒过粗、过细;或原料为针、片状结晶,且结晶过大,粘合剂未进入晶体内部引起裂片,可采用与松片相同得处理方法医学教育`网搜集整理。
2、颗粒中油类成分较多或药物含纤维成分较多时易引起裂片,可分别加用吸收剂或糖粉克服。
3、颗粒过干或药物失去过多结晶水引起裂片,可喷洒适量稀乙醇湿润,或与含水量较大得颗粒掺合后压片。
4、冲模不合要求,如模圈因磨擦而造成中间孔径大于口部直径,片剂顶出时易裂片。
冲头摩损向内卷边,上冲与模圈不吻合,压力不均匀,使片剂部分受压过大而造成顶裂,可更换冲模解决。
5、压力过大,或车速过快,颗粒中空气未逸出造成裂片,可调节压力或减慢车速克服。
一:松片松片就是压片时经常遇到得问题,会影响压片与包衣。
松片主要与颗粒质量、压片机运行有密切得关系。
颗粒质量就是压好片子得关键,因此,制粒工艺对于片剂质量尤为重要。
影响颗粒质量得因素主要有以下几方面:1、中药材成分得影响。
如有些中药材中含有大量得纤维成分。
由于这些药材弹性大、黏性小,致使颗粒松散、片子硬度低。
对此,在实际操作中可采用适宜得溶媒及方法,将此类药材中得有效成分提取浓缩,再进行颗粒制备,以降低颗粒弹性,提高可压性,进而提高片剂硬度;对含油脂量大得药材,压片亦易引起松片,如果这些油脂属有效成分,制粒时应加入适量吸收剂(如碳酸钙)等来吸油,如果这些油脂为无效成分,可用压榨法或其她脱脂法脱脂,减少颗粒油量,增加其内聚力,从而提高片子硬度。
2、中药材粉碎度得影响。
如果中药材细粉不够细,制成得颗粒黏结性不强,易使片剂松散。
因此,药粉要具有一定细度,这就是制好颗粒、压好药片得前提。
3、黏合剂与湿润剂得影响。
黏合剂与湿润剂在制粒中占有重要地位,其品种得选择与用量正确与否,都直接影响颗粒质量。
选择黏合剂、湿润剂应视药粉性质而定,如就是全生药粉压片,应选择黏性强得黏合剂,如就是全浸膏压片,而浸膏粉中树脂黏液质成分较多,则必须选用80%以上浓度得乙醇作湿润剂。
压片过程中可能出现的问题及解决办法
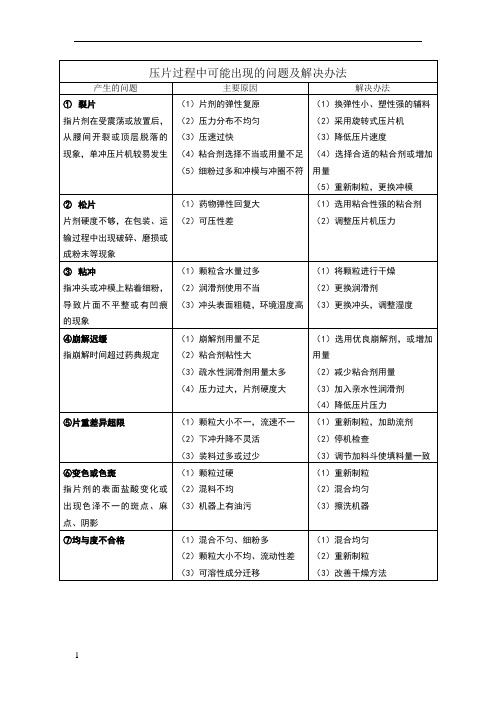
(4)选择合适的粘合剂或增加用量
(5)重新制粒,更换冲模
2松片
片剂硬度不够,在包装、运输过程中出现破碎、磨或成粉末等现象
(1)药物弹性回复大
(2)可压性差
(1)选用粘合性强的粘合剂
(2)调整压片机压力
3粘冲
指冲头或冲模上粘着细粉,导致片面不平整或有凹痕的现象
(1)颗粒含水量过多
(2)润滑剂使用不当
压片过程中可能出现的问题及解决办法
产生的问题
主要原因
解决办法
1裂片
指片剂在受震荡或放置后,从腰间开裂或顶层脱落的现象,单冲压片机较易发生
(1)片剂的弹性复原
(2)压力分布不均匀
(3)压速过快
(4)粘合剂选择不当或用量不足
(5)细粉过多和冲模与冲圈不符
(1)换弹性小、塑性强的辅料
(2)采用旋转式压片机
(3)冲头表面粗糙,环境湿度高
(1)将颗粒进行干燥
(2)更换润滑剂
(3)更换冲头,调整湿度
④崩解迟缓
指崩解时间超过药典规定
(1)崩解剂用量不足
(2)粘合剂粘性大
(3)疏水性润滑剂用量太多
(4)压力过大,片剂硬度大
(1)选用优良崩解剂,或增加用量
(2)减少粘合剂用量
(3)加入亲水性润滑剂
(4)降低压片压力
⑤片重差异超限
(1)颗粒大小不一,流速不一
(2)下冲升降不灵活
(3)装料过多或过少
(1)重新制粒,加助流剂
(2)停机检查
(3)调节加料斗使填料量一致
⑥变色或色斑
指片剂的表面盐酸变化或出现色泽不一的斑点、麻点、阴影
(1)颗粒过硬
(2)混料不均
压片过程中常见的问题及解决方法

腰裂课 堂 导 入松片粘冲色斑顶裂一、松片(一)现象片剂的硬度不够,受压震动后出现散碎或放松片置不久即变松散的现象。
改进制粒工艺干颗粒混合均匀,制软材时多搅拌更换黏合剂或增加其用量一、松片(二)出现的原因和解决方法黏合剂或润湿剂选择不当或用量不足干颗粒质地较松且细粉较多植物药材中含纤维太多,质地疏松调节下冲下降灵活性,使冲模中干颗粒填满。
调换冲头,提高压力在干颗粒中喷入适量稀乙醇(50%~60%),以恢复其适当的湿度,混合均匀。
一、松片(二)出现的原因和解决方法颗粒中含水量不当冲头长短不一,片剂所受压力过小冲模中干颗粒充填量不足含水量太少的颗粒具有较大的弹性,压成的片剂硬度较差。
鳞片状状或针状结晶容易形成层状排列,压制的片剂易碎裂选择适宜粒径大小的颗粒控制好原辅料的熔点尽量选择利于成形的晶体形态选用可压性较好的物料一、松片(二)出现的原因和解决方法可压性越差,物料压出的片剂硬度越小原、辅料的结晶状态原、辅料的熔点原、辅料的粒子大小立方形晶形对称性好、表面积大,易于压缩成形二、裂片(一)现象片剂受到震动或贮存时出现从片剂腰际裂开裂片顶裂腰裂让冲头与模圈相符减少细粉的量,并使粗细合适选择合适的黏合剂与用量调节压力(二)出现的原因和解决方法压力过大黏合剂选择不当或用量不足干颗粒中细粉过多或过粗、过细二、裂片减少颗粒中油类物质颗粒中油类物较多冲头与模圈不符,模圈中模孔中间大两端小给干颗粒保持适当的水分干颗粒中含水量过少或失去结晶水调节合适的车速车速过快三、粘冲(一)现象当冲头或冲模上粘着细粉,导致片面不平有凹痕粘冲黏壁合理使用润滑剂减少引湿性易受潮的药物受潮降低操作环境湿度降低干颗粒中含水量干颗粒中含水量过多操作环境湿度过高含有引湿性易受潮的药物更换辅料调高熔点原辅料熔点低润滑剂使用不当让冲头表面光滑冲头表面粗糙或有刻字、冲模表面粗糙检修压片机压片机异常发热三、粘冲(二)出现的原因和解决方法四、色斑(一)现象色斑系指片剂表面的颜色变化或出现色泽不一的色斑斑点,导致外观不符合要求通过加强清洁卫生将其粉碎或重新整粒,并检查筛网是否破裂。
压片过程中易出现的问题及解决方法

压片过程中易出现的问题及解决方法一、前言压片是制药过程中的重要环节之一,它能够将粉末状药物转化为易于贮存、运输和使用的片剂形态。
然而,在压片过程中,常常会出现一系列问题,如片剂硬度不足、断裂、表面不光滑等等。
这些问题不仅会影响片剂的质量,还会影响生产效率和成本。
因此,本文将介绍压片过程中易出现的问题及解决方法。
二、压片过程中易出现的问题及解决方法1. 片剂硬度不足问题原因:可能是粉末状药物颗粒大小分布范围较大或者含水量较高,也可能是机器参数设置不当。
解决方法:(1)优化原料:选择颗粒大小分布范围小、含水量低的原料,并进行预处理。
(2)调整机器参数:调整机器参数,如加大压力或延长保持时间等。
(3)添加助剂:添加助剂可以增加片剂硬度。
常用的助剂有结晶纤维素、微晶纤维素等。
2. 片剂断裂问题原因:可能是机器参数设置不当或原料中含有较多的空气或异物。
解决方法:(1)调整机器参数:调整机器参数,如减小压力或缩短保持时间等。
(2)优化原料:避免原料中含有较多的空气或异物,可以通过筛选、除尘等方法进行处理。
3. 片剂表面不光滑问题原因:可能是原料中含有较多的粘合剂或者机器参数设置不当。
解决方法:(1)优化原料:减少粘合剂的使用量,或选择颗粒大小分布范围小、形状规则的原料。
(2)调整机器参数:调整机器参数,如加大压力或延长保持时间等。
4. 片剂重量不一致问题原因:可能是药物颗粒大小分布范围大,也可能是药物颗粒密度不均匀。
解决方法:(1)优化原料:选择颗粒大小分布范围小、密度均匀的原料,并进行预处理。
(2)调整机器参数:调整机器参数,如加大挤出量或增加挤出次数等。
5. 片剂容易产生静电问题原因:可能是环境湿度低、温度高或者使用了带电材料。
解决方法:(1)调整环境:增加环境湿度或降低温度。
(2)更换材料:使用不带电材料。
三、总结压片是制药过程中的重要环节之一,但在实际生产中,常常会出现一系列问题。
本文介绍了压片过程中易出现的问题及解决方法,如片剂硬度不足、断裂、表面不光滑等等。
压片机的常见问题及解决方法

压片机的常见问题及解决方法(总4页)--本页仅作为文档封面,使用时请直接删除即可----内页可以根据需求调整合适字体及大小--压片机的常见问题及解决方法(一)关于未来的设想、新的技术我们说了太多,现在或许是我们回归本源的时候了,万变不离其宗,对于未来的改变,都是基于对现行的流程,现在所使用的设备足够了解,才有可能谈创新和改变,那今天我们就来简单谈谈两个关于压片机的一些常见问题以及解决的办法。
01class片重超差:指片重差异超过药典规定的限度1.颗粒粗细分布不匀,压片时颗粒流速不同,导致充填到中模孔内的颗粒粗细不均匀,如粗颗粒量多则片轻,细颗粒多则片重。
解决方法:应将颗粒混匀或筛去过多细粉。
2.如有细粉粘附冲头而造成吊冲时可使片重差异幅度较大。
此时下冲转动不灵活。
解决方法:检查,拆下冲模,清理干净下冲与中模孔。
3.颗粒流动性不好,流入中模孔的颗粒量时多时少,引起片重差异过大而超限。
解决方法:应重新制粒或加入适宜的助流剂如微粉硅胶等,改善颗粒流动性。
4.颗粒分层。
解决颗粒分层,减小粒度差。
5.较小的药片选用较大颗粒的物料。
解决方法:选择适当大小的颗粒。
6.加料斗被堵塞,此种现象常发生于黏性或引湿性较强的药物。
应疏通加料斗、保持压片环境干燥,并适当加入助流剂解决。
7.物料内物料存储量差异大,控制在50%以内。
8.加料器不平衡或未安装到位,造成填料不均。
解决方法:安装到位。
9.刮粉板不平或安装不良。
解决方法:调平。
10.带强迫加料器的,强迫加料器拨轮转速与转台转速不匹配。
解决方法:调一致。
11.冲头与中模孔吻合性不好,例如下冲外周与模孔壁之间漏下较多药粉,致使下冲发生“涩冲”现象,造成物料填充不足。
解决方法:更换冲头、中模。
12.下冲长短不一,超差,造成充填量不均。
解决办法:修差,差±5μm以内。
13.下冲带阻尼的,阻尼螺钉调整的阻尼力不佳。
解决方法:重新调整。
14.充填轨道磨损或充填机构不稳定。
- 1、下载文档前请自行甄别文档内容的完整性,平台不提供额外的编辑、内容补充、找答案等附加服务。
- 2、"仅部分预览"的文档,不可在线预览部分如存在完整性等问题,可反馈申请退款(可完整预览的文档不适用该条件!)。
- 3、如文档侵犯您的权益,请联系客服反馈,我们会尽快为您处理(人工客服工作时间:9:00-18:30)。
本文摘自再生资源回收-变宝网()如何解决压片机发生片剂脱落现象
压片机是指将颗粒或粉状物料置于模孔内由冲头压制成片剂的机器。
在中、西药的制药工艺中,压片机是必不可少的设备之一。
近年来,我国环境污染问题日益突出,GMP标准也在不断提高,压片机设备在面临升级转型的同时,市场上涌现的压片机机型也越来越多样,如单冲式压片机、花篮式压片机、旋转式压片机等。
这些设备功能各异,可以满足不同行业压片的需求。
然而在压片机的使用过程中,经常有用户反映压片的结果不顺利的情况。
例如,近日就有药企表示,公司生产片剂的设备不太中用,出现了片剂脱落的现象,这是什么情况呢?
某压片机生产制造厂的技术人员表示,片剂从模孔中被推出后,产生了脱落的现象被称之为裂片。
有时候是片剂的中间裂开分为两片,但这种情况很少发生。
对此,技术人员针对裂片现象作了几种原因的分析,对内容进行了整理。
原因一:颗粒中细粉过多
据介绍,压片机在压片过程中发生裂片的原因一般都是颗粒中细粉过多,导致压缩的时候空气没有逸出,压缩的速度太快,冲跟模孔之见的间隙比较小,空气被封闭在片剂内,压力过后空
气开始膨胀就会导致裂片现象的发生。
遇到这种情况时,应该把颗粒中的细粉去除,这样才可以使片剂里的空气可以逸出。
原因二:压缩行为不当
颗粒压缩的行为不当,容易造成压制的时候压力不均匀。
因为颗粒有较强的弹性,所以在压片压制过程当中会产生裂片,压制好后的片剂弹性复原率比较高。
原因三:颗粒过于干燥
颗粒过于干燥也会导致裂片,这时我们应该调节含水量来防止裂片。
原因四:压力过大
如果压力过大也会导致裂片现象。
在这种情况下发生裂片,我们可以适当的降低压力防止它裂片。
技术人员表示,不同的压片机设备压力都不同。
其中,单冲压片机压制片剂的时候是单方面的压力,旋转压片机压片的时候是上下一起压,弹性复原率跟压力大小是有关系的,片剂上表面受压时间短,所以先从顶部裂片。
知道这点后就可以指导怎么防止裂片现象的发生,例如,可以调整处方设计,增加原料跟辅料的塑性,改善颗粒压缩成型时间等。
降低压缩时的压力也能防止裂片。
因为压力小弹性复原率就随之变小,颗粒中的含水量适当会增加颗粒的塑性改善压力分布防止裂片。
此外,技术人员建议,还可以适当的加入润滑剂或者助流剂。
除了以上几种原因以外,或许还存在其他的原因导致裂片,比如模孔变形,机器磨损也会导致片剂裂片。
技术人员表示,如果逐一对常见故障进行排除后还得不到解决,建议联系压片机厂家售后服务,请专业人士进行维修。
本文摘自变宝网-废金属_废塑料_废纸_废品回收_再生资源B2B交易平台网站;
变宝网官网:/?cj
买卖废品废料,再生料就上变宝网,什么废料都有!。