A182-F51喷焊Ni55工艺指导书
球体硬密封喷焊、堆焊常用材料

球体硬密封喷焊、堆焊常用材料1、司太立钴基1号焊丝相当AWS ERCoCr-C主要特征及用途:高碳Co-Cr-W合金堆焊焊丝,耐磨性、耐蚀性好,但抗冲击韧度差。
工艺方法:对焊涂成厚度(um):2500-3000适用介质:煤化工、酸性流体工况温度:<450使用基体:A105、304、316L、F51堆焊层硬度:48-50HRC2、司太立钴基6号焊丝相当AWS ERCoCr-A主要特征及用途:Co106钴基堆焊焊丝是Co-Cr-W堆焊合金中C及W含量最低、韧性最好的一种,能承受冷热条件下的冲击,产生裂纹的倾向小,具有良好的耐蚀、耐热和耐磨性能。
工艺方法:对焊涂成厚度(um):2500-3000适用介质:通用流体、无硬质颗粒工况温度:<650使用基体:A105、304、316L、F51堆焊层硬度:38-40HRC3、司太立钴基20号焊丝主要特征及用途:Co120钴基堆焊焊丝,硬度高,耐磨性非常好,但抗冲击性较差,堆焊时产生裂纹倾向大,具有良好的耐蚀、耐热、耐磨性能,在650℃左右仍可保持这些性能。
工艺方法:HVOF热喷涂涂成厚度(um):120-150适用介质:空气分体工况温度:<300使用基体:inconel625、316L堆焊层硬度:55-60HRC4、NiCrBSi镍基合金Ni60主要特征及用途:自熔性、润湿性和喷焊性优良,而且熔点比较低,喷焊层具有硬度高、耐蚀、耐磨、耐热特点,难以切削,以湿式磨削为宜。
工艺方法:喷焊、喷涂重溶涂成厚度(um):500-800适用介质:煤化工、酸性流体工况温度:<300使用基体:A105、304、316L堆焊层硬度:55-60HRC4、NiCrBSi镍基合金Ni55主要特征及用途:自熔性、润湿性和喷焊性优良,而且熔点比较低,喷焊层具有硬度高、耐蚀、耐磨、耐热特点,难以切削,以湿式磨削为宜。
工艺方法:喷焊、喷涂重溶涂成厚度(um):500-800适用介质:煤化工、酸性流体工况温度:<300使用基体:A105、304、316L堆焊层硬度:50-55HRC。
铝及铝合金焊接作业指导书
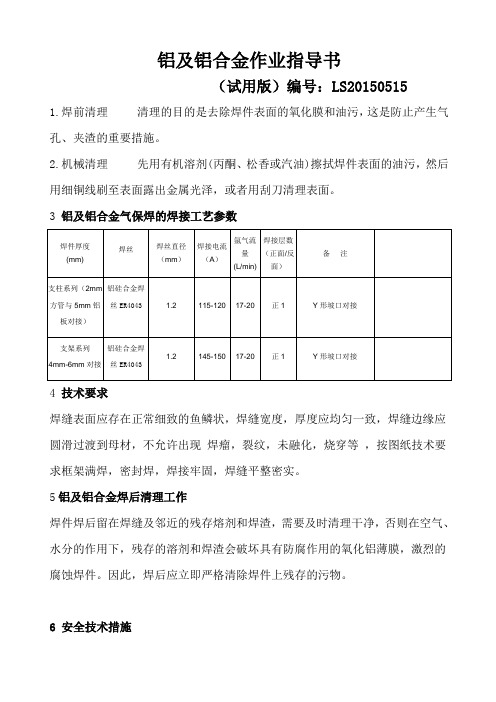
铝及铝合金作业指导书
(试用版)编号:LS20150515
1.焊前清理清理的目的是去除焊件表面的氧化膜和油污,这是防止产生气
4 技术要求
焊缝表面应存在正常细致的鱼鳞状,焊缝宽度,厚度应均匀一致,焊缝边缘应圆滑过渡到母材,不允许出现焊瘤,裂纹,未融化,烧穿等,按图纸技术要求框架满焊,密封焊,焊接牢固,焊缝平整密实。
5铝及铝合金焊后清理工作
焊件焊后留在焊缝及邻近的残存熔剂和焊渣,需要及时清理干净,否则在空气、水分的作用下,残存的溶剂和焊渣会破坏具有防腐作用的氧化铝薄膜,激烈的腐蚀焊件。
因此,焊后应立即严格清除焊件上残存的污物。
6 安全技术措施
6.1 焊工工作时必须穿工作服,戴绝缘手套,穿绝缘鞋。
6.2 焊工必须遵守安全、文明施工的规定。
6.3 焊工在使用电磨工具时采取防护措施。
使用前检查电磨工具砂轮片是否松动,是否需要更换砂轮片。
6.4 应避免电焊线与带有感应线圈的设备相连,电焊线与焊钳连接部分应放置可靠,避免工作时电弧击伤管子或设备。
6.5 焊接时应注意避免飞溅或电弧损伤设备、飞溅或焊渣落入已清洁干净的产品表面。
编制:
技术:
质量:
生产:
批准:。
焊接(喷焊)作业指导书
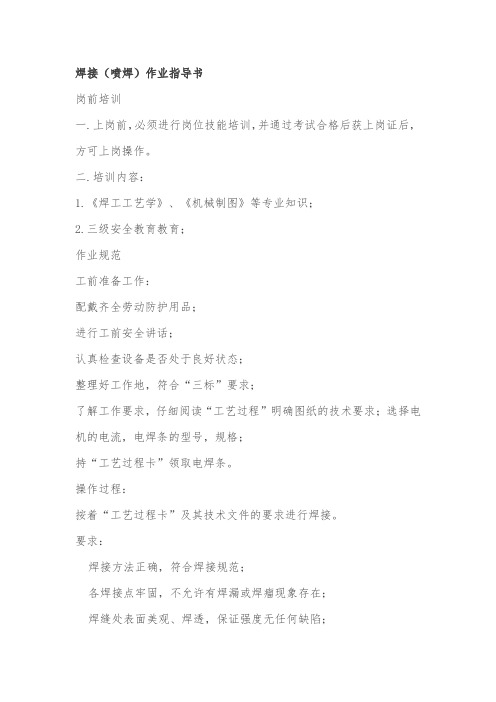
焊接(喷焊)作业指导书岗前培训一.上岗前,必须进行岗位技能培训,并通过考试合格后获上岗证后,方可上岗操作。
二.培训内容:1.《焊工工艺学》、《机械制图》等专业知识;2.三级安全教育教育;作业规范工前准备工作:配戴齐全劳动防护用品;进行工前安全讲话;认真检查设备是否处于良好状态;整理好工作地,符合“三标”要求;了解工作要求,仔细阅读“工艺过程”明确图纸的技术要求;选择电机的电流,电焊条的型号,规格;持“工艺过程卡”领取电焊条。
操作过程:按着“工艺过程卡”及其技术文件的要求进行焊接。
要求:焊接方法正确,符合焊接规范;各焊接点牢固,不允许有焊漏或焊瘤现象存在;焊缝处表面美观、焊透,保证强度无任何缺陷;出现技术、质量问题及时向车间领导反映情况提出纠正措施。
3) 操作规范①、平焊A平对接焊ⅰ、不开坡口平对接焊:当焊件厚度小于6mm时采用不开坡口对接(重要构件除外)焊接正面焊缝时,用3—4mm焊条,采用短弧焊接,并应使熔深达到板厚的2/3焊缝宽度为5—8mm加强高应小于1.5mm。
焊接反面的封底焊前,应将正面焊缝下面的焊缝时运条速度应慢些,以获得较大的熔深和宽度。
焊反面封底焊缝时则运条速度要稍快些,以获得较小的焊缝宽度。
ⅱ、开坡口的平对接焊当焊件厚度等于或大于6㎜时,应开坡口,开坡口对接接头的焊接可采用多层焊法或多层多道焊法。
多层焊时,对第一层的打底焊道应选用直径较小的焊条,运条方法应以间隙大小而定。
当间隙小时可用直线形,间隙较大时,则采用直线往返形,以免烧穿。
B平角接焊平角接焊主要是指T字头焊和搭接接头平焊.a B-1单层焊:ⅰ、焊脚尺寸小于8㎜的焊缝,通常用单层焊来完成,焊条直径根据钢板厚度不同在3-5㎜范围内选择.ⅱ、焊脚小于5㎜的焊缝,可采用直线形运条法和短弧进行焊接,焊接速度要均匀,焊条与水平板成45°,与焊接方向成规65—80°的尖角。
ⅲ、焊角尺寸在5—8mm时可采用圆形或反锯齿形运条法进行焊接。
氧乙炔焰喷焊(镍基)合金粉末通用工艺规程
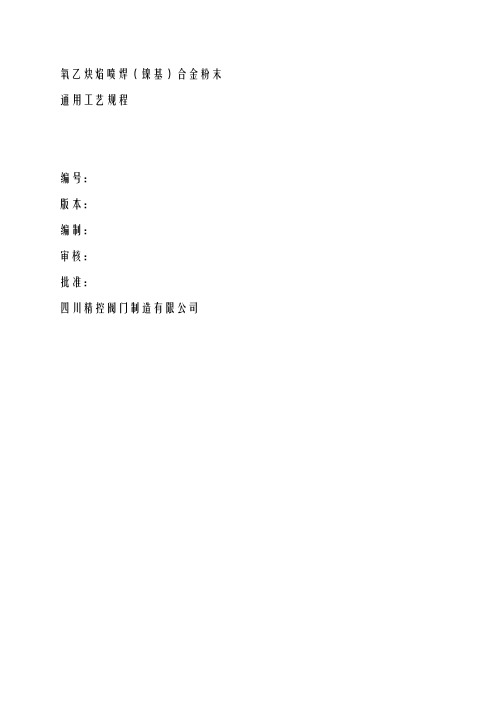
氧乙炔焰喷焊(镍基)合金粉末通用工艺规程编号:版本:编制:审核:批准:四川精控阀门制造有限公司1、目的合金粉末喷焊技术是金属表面强化的新技术之一,氧乙炔焰喷焊是利用氧乙炔焰所产生的热能,通过特制喷枪将合金粉末加热到熔融状态,高速地喷敷到经清洁粗糙化的工件表面上,使其形成一致密的金属合金焊层,达到表面强化之目的。
为了正确指导喷焊技术的实施,有效地控制喷焊质量,本工艺规程规定了氧乙炔焰喷焊(镍基粉末)工艺的粉末选择,基材要求,操作规范以及缺陷预防措施等。
2、适用范围本工艺规程适用于采油(气)井口装置中闸板、阀座的镍基喷焊,其它零件的喷焊可参照进行。
3、喷焊操作人员要求旋焊人员应有相应的焊接技术水平合格证书,并应遵守焊接工艺规程中确定的各种焊接参数,达到焊接工艺规程的要求。
4、合金粉末喷焊用合金粉末一般称为“自熔性合金粉末”。
4.1、镍基粉末选用原则:根据零件技术要求的硬度值来选择粉末。
4.2、粉末化学成份4.3、粉末的主要性能4.4、喷焊层性能A-优B-良5、粉末质量检查为保证喷焊质量,每批粉末在批量喷焊前应作好《质量跟踪表》的填写;并应作试件喷焊检查,试件合格后方可批量喷焊,试件按下表进行:6、喷焊工具及设备6.1、喷枪喷枪选用一般应根据工件喷涂面积大小、几何形状和合金粉末熔点以及喷焊工艺与方法选择。
一般采用中压射吸式喷枪。
根据井口装置中喷焊零件,喷焊阀座时,采用型号SPH-2/h;喷焊闸板时,选用型号为SPH-4/h。
6.2、设备及其它装置喷焊需要设备及装置有:氧气瓶、乙炔瓶以及减压器、流量计、过滤器、安全装置、可转单台、电动砂轮、粉末恒温干燥箱、箱形电阻炉以及无油污的钢丝刷、毛刷、刀等工具。
7、工作环境喷焊应在清洁明亮的场地进行。
施焊时空气干燥,温度不大。
8、火焰要求喷焊时在工件预热喷敷合金粉末过程中均须采用中性焰或微碳化焰,禁止使用氧化焰和碳化焰,同时应控制好火焰强度。
9、基体要求喷焊的阀座、闸板均应为锻件,基体锻后经调质处理,调质硬度如下:10、操作规程喷焊工艺流程一般为:焊前准备→工件表面预热处理→工件预热→喷敷底粉→重熔底粉工件加热升温→喷敷合金粉末→重熔→工件冷却→机加工10.1、焊前准备10.1.1、了解零件基本材料,以确定喷焊工艺参数。
焊接工艺评定指导书

序号
项目名称
编号
页数
1
焊接工艺指导书
HP02-021
2
焊接工艺评定报告(PQR)
HP02
3
材料质量证明书
4
焊接材料质量证明书
5
焊接工艺评定施焊及焊缝外观检查记录
6
无损探伤报告
7
焊接工艺评定试件试验报告
8
化学分析试验报告
9
热处理报告
备注
编制:存档日期:年月日
保护气体:
气体种类混合比 流量(L/min)
保 护 气Ar//
尾气保护气Ar//
背面保护气///
填充金属:焊丝、焊条
焊材标准:GB/T5117-1995
焊条牌号:E4315 J427
焊丝牌号:H08Mn2SiA
电特性:
电流种类:直流
极性:DC-
钨极尺寸:__Wce-20Ф2.5__
焊接电流(A):80--130
J427
φ3.2
DC+
110-125
20-22
适当
1/3
DS
J427
φ3.2
DC+
110-125
20-22
适当
钨极类别及直径/喷嘴直径(mm):/
熔滴过渡形式/焊丝送进速度(cm/min):/
技术措施:
摆动焊及不摆动焊:摆动摆动参数:适当
焊前清理和层间清理:清理坡口附近30mm油、锈、水份等
焊接中间清理:角向磨光机
分析表面或取样开始表面至熔合线的距离(mm):
附加说明:
结论:本评定按JB4708-2000《钢制压力容器焊接工艺评定》规定焊接试件、检验试样,测定性能,确认试验记录正确。
喷涂工艺指导书
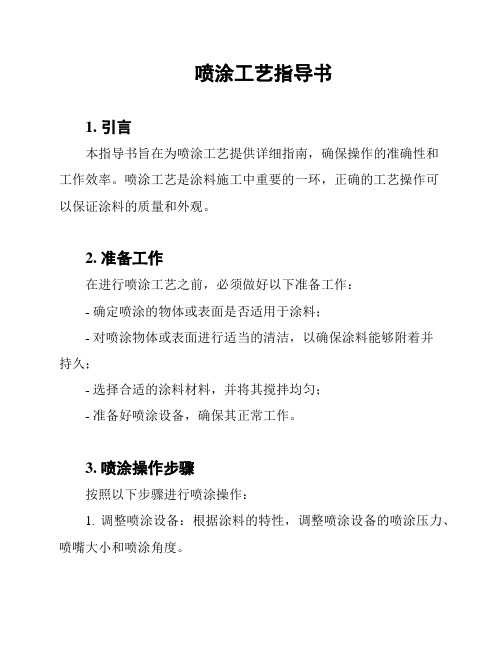
喷涂工艺指导书1. 引言本指导书旨在为喷涂工艺提供详细指南,确保操作的准确性和工作效率。
喷涂工艺是涂料施工中重要的一环,正确的工艺操作可以保证涂料的质量和外观。
2. 准备工作在进行喷涂工艺之前,必须做好以下准备工作:- 确定喷涂的物体或表面是否适用于涂料;- 对喷涂物体或表面进行适当的清洁,以确保涂料能够附着并持久;- 选择合适的涂料材料,并将其搅拌均匀;- 准备好喷涂设备,确保其正常工作。
3. 喷涂操作步骤按照以下步骤进行喷涂操作:1. 调整喷涂设备:根据涂料的特性,调整喷涂设备的喷涂压力、喷嘴大小和喷涂角度。
2. 进行底漆涂层:首先,喷涂一层底漆涂料,以提高涂料的附着性和光滑度。
注意要均匀涂抹并尽量避免起皱。
3. 进行面漆涂层:在底漆涂层干燥后,进行面漆喷涂。
根据需要,可以喷涂多层面漆,确保涂层的厚度和质量。
4. 检查和修复:在喷涂完成后,检查涂层是否均匀、光滑,是否有漏涂或起皱现象。
如有问题,及时进行修复。
4. 安全事项在进行喷涂工艺时,务必注意以下安全事项:- 使用防护设备:佩戴适当的口罩、手套和防护服,以保护皮肤和呼吸系统。
- 通风良好:确保喷涂作业区域有足够的通风,以避免吸入有害气体。
- 避免火源:禁止在喷涂作业区域内吸烟或使用明火等火源。
- 存储和处理涂料:将涂料储存在安全的地方,并按照相关规定进行处理。
5. 维护保养定期进行喷涂设备的保养和维护,以确保其正常工作。
清洗喷嘴和喷涂设备,避免涂料残留堵塞设备。
6. 结论本指导书详细介绍了喷涂工艺的操作步骤和注意事项,旨在帮助喷涂工作者进行准确和高效的工作。
请在使用本指导书时遵循相关的安全规定,并保持设备的维护保养。
以上为喷涂工艺指导书内容,祝您操作顺利!。
5ni钢的焊接工艺要求

5ni钢的焊接工艺要求5ni钢是一种高强度、耐腐蚀、耐高温的合金钢材料,广泛用于航空航天、船舶、核电站等领域。
然而,由于其特殊的成分和特性,其焊接过程中存在一些特殊的工艺要求。
本文将详细介绍5ni钢的焊接工艺要求。
一、焊接工艺选择1. 焊接方法: 对于5ni钢的焊接,常用的方法有手工电弧焊、氩弧焊和埋弧焊。
其中,氩弧焊和埋弧焊是较为常用的焊接方法,能够满足5ni钢的焊接要求。
2. 焊接工艺: 在选择焊接工艺时,需要考虑焊材、焊接位置和功能要求等因素。
常用的焊接工艺有垂直焊、水平焊、横向焊和角焊等。
二、焊接设备要求1. 焊机选择: 对于5ni钢的焊接,一般选择直流焊机或交直流焊机,具备良好的电弧稳定性和调节性能。
2. 焊接电流和电压: 根据焊接材料的厚度和类型,选择合适的焊接参数进行调节,以确保焊缝的均匀性和质量。
三、预热和焊缝处理1. 预热要求: 5ni钢的焊接前需要进行预热处理,以消除材料内部的应力和冷裂纹的产生。
一般预热温度为200℃至300℃。
焊接区域的温度要达到预热温度并保持一段时间,预热结束后进行焊接。
2. 焊缝处理: 在焊接完成后,需要对焊缝进行后续处理,如去除焊渣、打磨和平整等,以保证焊缝的质量和外观。
四、焊接材料选择和处理1. 焊接电极选择: 对于5ni钢的焊接,常用的焊接电极有石墨电极、钼合金电极和铁合金电极等。
根据具体需求选择合适的电极。
2. 焊接材料前处理: 在焊接前,需要对焊接材料进行除油、除锈和清洁等处理,以保证焊接质量和连接强度。
5ni钢的焊接工艺要求是确保焊接质量和连接强度的重要环节。
在焊接过程中,选择适当的焊接方法和工艺,合理使用焊接设备和电流电压,注意预热和焊缝处理,选择合适的焊接材料并进行前处理都是不可忽视的步骤。
通过遵循这些工艺要求,可以提高焊接质量,确保5ni钢的焊接效果达到设计标准。
化学工艺与工程所学课程化学工艺与工程是一门涉及化学原理、工程设计和技术操作等方面的综合学科。
涂装作业各工序作业指导书
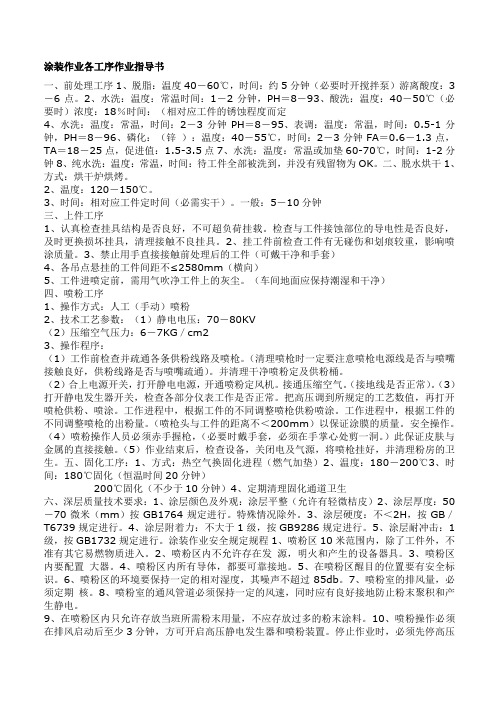
涂装作业各工序作业指导书一、前处理工序1、脱脂:温度40-60℃,时间:约5分钟(必要时开搅拌泵)游离酸度:3-6点。
2、水洗:温度:常温时间:1-2分钟,PH=8-93、酸洗:温度:40-50℃(必要时)浓度:18%时间:(相对应工件的锈蚀程度而定4、水洗:温度:常温,时间:2-3分钟PH=8-95、表调:温度:常温,时间:0.5-1分钟,PH=8-96、磷化:(锌):温度:40-55℃,时间:2-3分钟FA=0.6-1.3点,TA=18-25点,促进值:1.5-3.5点7、水洗:温度:常温或加垫60-70℃,时间:1-2分钟8、纯水洗:温度:常温,时间:待工件全部被洗到,并没有残留物为OK。
二、脱水烘干1、方式:烘干炉烘烤。
2、温度:120-150℃。
3、时间:相对应工件定时间(必需实干)。
一般:5-10分钟三、上件工序1、认真检查挂具结构是否良好,不可超负荷挂载。
检查与工件接蚀部位的导电性是否良好,及时更换损坏挂具,清理接触不良挂具。
2、挂工件前检查工件有无碰伤和划痕较重,影响喷涂质量。
3、禁止用手直接接触前处理后的工件(可戴干净和手套)4、各吊点悬挂的工件间距不≤2580mm(横向)5、工件进喷定前,需用气吹净工件上的灰尘。
(车间地面应保持潮湿和干净)四、喷粉工序1、操作方式:人工(手动)喷粉2、技术工艺参数:(1)静电电压:70-80KV(2)压缩空气压力:6-7KG/cm23、操作程序:(1)工作前检查并疏通各条供粉线路及喷枪。
(清理喷枪时一定要注意喷枪电源线是否与喷嘴接触良好,供粉线路是否与喷嘴疏通)。
并清理干净喷粉定及供粉桶。
(2)合上电源开关,打开静电电源,开通喷粉定风机。
接通压缩空气。
(接地线是否正常)。
(3)打开静电发生器开关,检查各部分仪表工作是否正常。
把高压调到所规定的工艺数值,再打开喷枪供粉、喷涂。
工作进程中,根据工件的不同调整喷枪供粉喷涂。
工作进程中,根据工件的不同调整喷枪的出粉量。
铝焊工序操作指导书
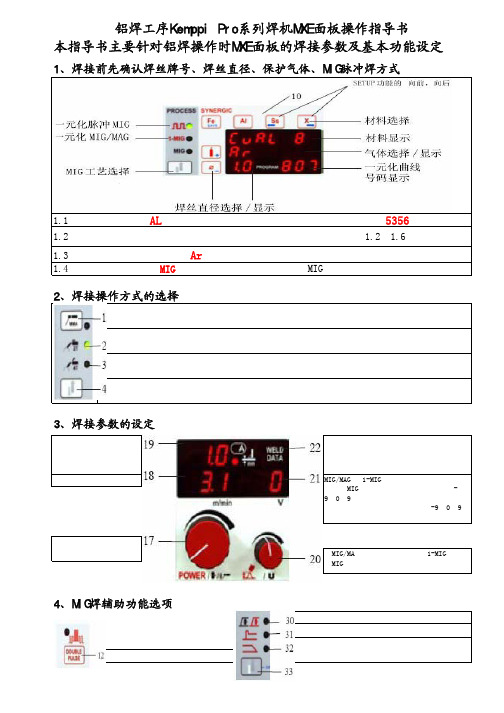
本指导书主要针对铝焊操作时MXE 面板的焊接参数及基本功能设定 送丝速度的显示。
4、MIG 焊辅助功能选项铝焊工序Kemppi Pro 系列焊机MXE 面板操作指导书1、焊接前先确认焊丝牌号、焊丝直径、保护气体、MIG脉冲焊方式1.1、可循环按上图中AL 按键选择相应的铝焊接材料,铝焊工序现用材料:5356将显示。
1.2、可循环按上图中Φ按键选择实际使用的铝焊丝直径,焊丝直径:1.2或1.6将显示。
1.3、铝焊的保护气体标准使用Ar 气,将自动显示在屏幕。
1.4、焊接方式选择:按MIG 工艺选择键,选择一元化脉冲MIG 焊接方式,此时绿灯应亮。
2、焊接操作方式的选择手工电弧焊按键:当使用焊条时,请按此键。
焊接两步操作方式,绿灯亮表示已选择此方式操作。
焊接四步操作方式,绿灯亮未亮表示未选择此方式操作。
两步、四步操作方式选择按键,按此键可选择需要的操作方式,选择后绿灯会亮。
3、焊接参数的设定按此键可以显示焊接停止前最后使用的送丝速度, 焊接电流和焊接电压参数值。
工件厚度显示,在焊接过程中,实时显示焊接电流。
目前工位设定是直接显示焊接电流!MIG/MAG 和1-MIG 焊接电压设定参数的显示。
脉冲MIG 弧长设定参数的设定范围为-9…0…9。
焊接时, 显示极间电压, 此显示也可表示焊接动态特性控制,-9…0…9。
送丝速度、焊接电流调节旋钮对MIG/MA 为焊接电压的控制,1-MIG 和脉冲MIG 为弧长控制的调节旋钮。
功能选择键,功能选择后绿灯亮,功能开启。
双脉冲功能选择键,选择后绿灯亮。
慢送丝功能:有利于铝焊时起弧稳定,建议开启。
热起弧功能:有利于减少铝焊起弧点未熔合缺陷。
收弧功能:有利于填满弧坑,减少收弧缺陷。
涂装通用指导书

涂装通用指导书一、涂装流程1.去毛刺、杂物。
清除飞溅、焊道气孔、粗糙的焊道、钢板表面尖锐的凹凸、翘皮、焊道裂缝、深的咬口、超过0.3mm的气割边、自由边倒角等打磨光滑,直到获得一个无棱角及无尖锐凸起的均匀表面。
2.清洗。
先用抹布把工件表面的油污、杂物擦去,再把工件吊入油污清洗池,戴上胶手套用刷子或抹布清洗工件,浸泡15分钟后吊起,擦去表面清洗液,将工件吊放入水洗池,用高压清水清洗,吊出工件擦拭干净,然后风干(干燥压缩气、风扇)约15分钟。
3.打砂。
工件打砂Sa2.5级粗糙,气压6—8Kg,打砂后4小时内需进行喷底漆。
无法打砂的工件/表面,用砂轮机在工件要喷漆的表面拉毛。
4.表面检查。
5.除尘。
用干燥压缩气除去工件表面灰尘,再用干净的抹布粘清水、拧干擦拭,风干约15分钟。
6.底漆。
先薄喷一层底漆,能遮住金属表面即可,过10-20分钟再喷一层底漆达到厚度要求。
气压3—5Kg小喷枪距离15-25cm,大喷枪距离25-45cm,喷漆时10米范围内禁止打砂、打磨、电焊、气割或者产生灰尘的作业(中漆、面漆同样要求)。
7.底漆检查。
8.间隔。
底漆间隔6-8小时后,油漆表面若出现气孔、沙粒、斑点、粘灰尘等缺陷,用粗砂纸磨去油漆表层缺陷。
9.除尘。
(同上,略)。
10.中漆。
喷漆过程中,要不时搅拌油漆。
先薄喷一层中漆,能遮住底漆表面即可,过10-20分钟再喷一层中漆达到厚度要求。
11.中漆检查。
12.间隔。
中漆间隔6-8小时后,油漆若出现气孔、沙粒、斑点、粘灰尘等缺陷,用粗砂纸磨去油漆表层缺陷。
13.除尘。
(同上,略)。
14.面漆。
先薄喷一层面漆,能遮住中漆表面即可,过10-20分钟再喷一层面漆达到厚度要求。
15.面漆检查。
16.间隔。
面漆至少间隔8小时后方可吊运。
17.油漆检查。
18.修补。
对装配后的零部件进行修补时,先用抹布擦去零部件表面油污,再放入油污清洗池清洗、浸泡15分钟,(若不可浸泡,吊挂在油污清洗池上方,用油污清洗液多次喷在油漆面上清洗、浸泡约15分钟),(禁止用汽油清洗),擦拭干净后吊出,再放入水洗池清洗,吊出后风干约15分钟,用粗砂纸/砂布在油漆表面进行十字交叉拉毛,用干燥压缩气除去大部分灰尘,用抹布粘清水拧干、擦拭,风干约15分钟后方可修补。
2铝合金型材立式喷涂工艺操作规程

一.主题内容和适用范围1.目的:指导铝合金型材立式喷涂生产线生产工艺及生产操作,实现标准化、规范化作业,确保生产顺利进行和产品品质保证,提高工作效率,有效地降低生产成本。
2. 本规程适用于铝合金型材立式喷涂生产线的工艺操作。
二.生产工艺流程图上架前处理(关键工序)喷涂(关键工序)固化下架检验包装三.工艺条件及操作方法1.上架1.1按车间生产计划安排的先后顺序以及订单号,由跟单员领用相应合金牌号、状态、型号、壁厚、长度、数量的铝合金型材;上架员轻拿轻放,避免人为损伤型材表面,将合格型材挂到运输传送链挂钩上。
1.2上架前,型材需经质检员核对尺寸、壁厚、长度、硬度等都符合订单要求;质检员、上架员检查型材表面是否有毛刺、颗粒、油污、腐蚀斑痕、铝屑及杂物、粘胶等,如有以上缺陷,必须经过处理(打磨或溶剂清洗)合格后才能上架。
有变形、起鼓、气泡、划伤、夹渣等明显严重缺陷的型材不允许上架。
1.3 上架必须确保不掉排和挂具导电性良好,挂具使用1-2次后必须经过硫酸清洗,或经过挂具炉处理后才能继续使用。
1.4 打孔只能在型材的同一方向端头10mm之内打孔,保证大装饰面对准喷枪的同时并在非装饰面打孔,将打孔好的型材逐支摆放在上架平台上,装饰面朝下,型材之间预留适当间距,以方便上架时取料。
1.5 上架时型材与型材之间的间距以型材本身的宽度为准,不同断面、长度的型材必须分开上架,隔开间距不低于1200mm。
1.6 不同色号的型材上架时,跟单员必须通知粉房(以随行卡经粉房确认签字为准),易清理的粉末间隔时间为20分钟,不易清理的粉末间隔时间为40分钟,且必须在上架的第一支型材之前用铝板作好标识,防止喷错颜色。
1.7 上架时,必须把型材大装饰面朝喷枪正面,一般型材使用正挂具,特殊型材使用侧挂具;使用挂具时,必须检查挂具的牢固性,积粉是否清理干净。
1.8 每隔四小时由前处理人员观察一次固化炉、前处理通道是否有掉料现象。
1.9 返工料,存放24小时以上或经过包装过的型材,重新上架时,必须经过打磨或用溶剂清洗后才能上架,且把打孔位朝运输链条方向摆放,避免型材第二次打孔。
2505(A182-F51)双相钢连接焊焊接工艺规程(WPS)
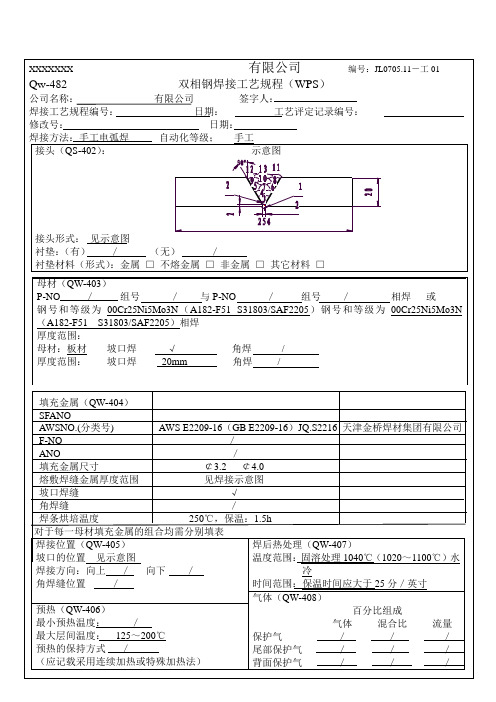
厚度范围:
母材:板材坡口焊√角焊/
厚度范围:坡口焊20mm角焊/
填充金属(QW-404)
SFANO
AWSNO.(分类号) AWS E2209-16(GB E2209-16)JQ.S2216天津金桥焊材集团有限公司
进行x光探伤检验焊层定位焊123顶层编制焊接方法填充金属种类直径极性电流安培a电压焊接速度范围范围vmms252525手工电弧焊s221632直流反接901202530手工电弧焊s221632直流反接901202530手工电弧焊s221640直流反接1301702530日期审核日期
XXXXXXX有限公司编号:JL0705.11-工01
焊接技术(Qw-410)
直进焊或横摆焊:直进焊
嘴孔或喷嘴尺寸/
打底焊道和中间焊道的清理方法(刷理或打磨等):刷理。道、层间彻底清除熔渣后再继续施焊
背面清根方法:/
横摆方法:不摆动
导电嘴至工作距离:/
多道焊或单道焊(每侧):多道焊
多丝焊或单丝焊:单丝焊
焊接速度(范围):3~5mm/s
锤击有无:无
其它:焊前清除焊件油污、水渍、铁锈。多道焊接。采用回弧法、小电流、快焊速、短弧、窄焊道(5-6mm)、直线运条法焊接,根部、接弧处应焊透与溶合。连续焊接直至焊完最后一道焊缝,每一焊层厚2~4mm。收弧时填满弧坑。后段焊缝必须熔化前段焊缝1/3~2/3,焊道重叠1/3~1/4,错开层、段件接头,层、段间焊向向相反。顶层焊缝堆高3 mm。
90~120
25~30
2~5
A182-F51喷焊Ni55工艺指导书
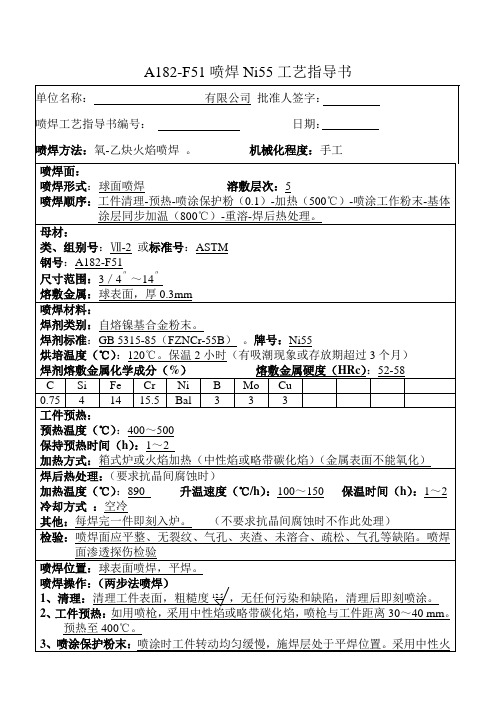
其他:每焊完一件即刻入炉。(不要求抗晶间腐蚀时不作此处理)
检验:喷焊面应平整、无裂纹、气孔、夹渣、未溶合、疏松、气孔等缺陷。喷焊面渗透探伤检验
喷焊位置:球表面喷焊,平焊。
喷焊操作:(两步法喷焊)
1、清理:清理工件表面,粗糙度12.5,无任何污染和缺陷,清理后即刻喷涂。
2、工件预热:如用喷枪,采用中性焰或略带碳化焰,喷枪与工件距离30~40 mm。预热至400℃。
检查氧气、乙炔气压力,不得超压。检查喷枪嘴(1.5~2.5mm)、开关喷粉量等是否正常(不许在工件上试喷)。基体加工的粗糙度12.5,棱、尖角倒圆,不许有氧化层、硬化层、砂眼、气孔、疏松等缺陷。彻底清除工件表面铁锈、氧化物、水渍、油污。可用砂轮打磨或清洗剂清洗,使喷焊面粗、净、新。箱式炉预热的工件出炉后用砂布打磨现清理现喷。
3、喷涂保护粉末:喷涂时工件转动均匀缓慢,施焊层处于平焊位置。采用中性火焰。焰心长度7毫米,喷嘴距工件表面90~100 mm,垂直于工件表面。喷焊第一层(厚0.1 mm)。
4、继续加热:
用喷涂枪或重溶枪用中性火焰,喷嘴至工件表面30~40mm,将工件继续加热至500~600℃(呈暗红色)。
5、喷涂工作粉末:按喷涂保护粉末规定,继续分层均匀喷粉到工件表面(每层0.1~0.2mm),至厚度要求。每层、次的喷粉有1/3的重叠,喷涂中如工件温度降低,即应边喷粉边用另一把喷枪加热。
编制(日期)
审核(日期)
焊层厚度(mm)
氧气
乙炔气
氧气
乙炔气
1~顶层
Ni62
0.4~0.5
0.07~0.08
1200
950
0.1~0.2
重熔参数:
气体压力(Mpa)
140.构件钢印、安装标志及喷涂作业指导书
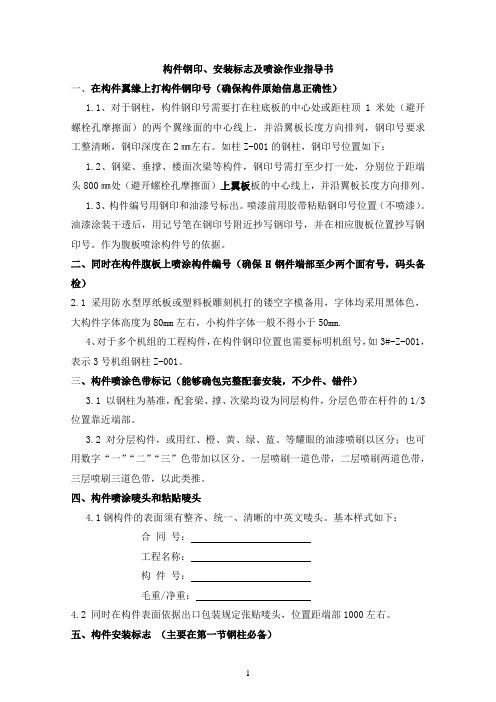
构件钢印、安装标志及喷涂作业指导书一、在构件翼缘上打构件钢印号(确保构件原始信息正确性)1.1、对于钢柱,构件钢印号需要打在柱底板的中心处或距柱顶1米处(避开螺栓孔摩擦面)的两个翼缘面的中心线上,并沿翼板长度方向排列,钢印号要求工整清晰,钢印深度在2㎜左右。
如柱Z-001的钢柱,钢印号位置如下:1.2、钢梁、垂撑、楼面次梁等构件,钢印号需打至少打一处,分别位于距端头800㎜处(避开螺栓孔摩擦面)上翼板板的中心线上,并沿翼板长度方向排列。
1.3、构件编号用钢印和油漆号标出。
喷漆前用胶带粘贴钢印号位置(不喷漆)。
油漆涂装干透后,用记号笔在钢印号附近抄写钢印号,并在相应腹板位置抄写钢印号。
作为腹板喷涂构件号的依据。
二、同时在构件腹板上喷涂构件编号(确保H钢件端部至少两个面有号,码头备检)2.1 采用防水型厚纸板或塑料板雕刻机打的镂空字模备用,字体均采用黑体色,大构件字体高度为80mm左右,小构件字体一般不得小于50mm.4、对于多个机组的工程构件,在构件钢印位置也需要标明机组号,如3#-Z-001,表示3号机组钢柱Z-001。
三、构件喷涂色带标记(能够确包完整配套安装,不少件、错件)3.1 以钢柱为基准,配套梁、撑、次梁均设为同层构件,分层色带在杆件的1/3位置靠近端部。
3.2 对分层构件,或用红、橙、黄、绿、蓝、等耀眼的油漆喷刷以区分;也可用数字“一”“二”“三”色带加以区分。
一层喷刷一道色带,二层喷刷两道色带,三层喷刷三道色带,以此类推。
四、构件喷涂唛头和粘贴唛头4.1钢构件的表面须有整齐、统一、清晰的中英文唛头。
基本样式如下:合同号:工程名称:构件号:毛重/净重:4.2 同时在构件表面依据出口包装规定张贴唛头,位置距端部1000左右。
五、构件安装标志(主要在第一节钢柱必备)根据工程要求以0米标高线为基准制作安装标志(若工程有特殊说明,按工程要求操作)。
样冲点打法如下图所示:在规定标高位置,用红色的油漆醒目地喷涂出立柱中心标记。
【涂装工艺】油漆喷涂作业指导书
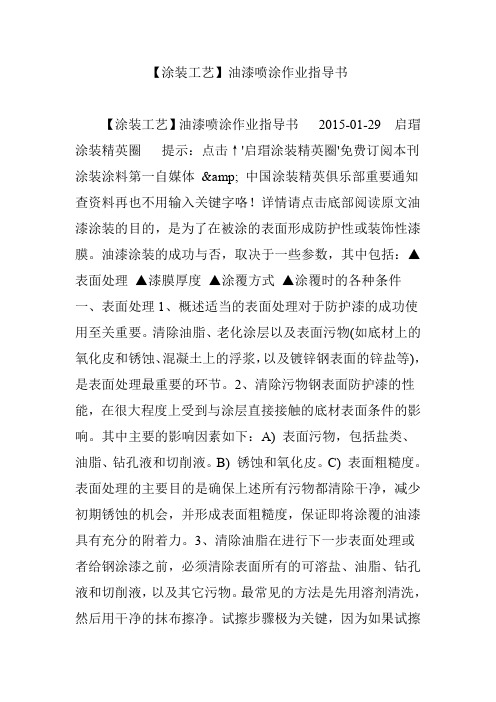
【涂装工艺】油漆喷涂作业指导书【涂装工艺】油漆喷涂作业指导书2015-01-29 启瑁涂装精英圈提示:点击↑'启瑁涂装精英圈'免费订阅本刊涂装涂料第一自媒体& 中国涂装精英俱乐部重要通知查资料再也不用输入关键字咯!详情请点击底部阅读原文油漆涂装的目的,是为了在被涂的表面形成防护性或装饰性漆膜。
油漆涂装的成功与否,取决于一些参数,其中包括:▲表面处理▲漆膜厚度▲涂覆方式▲涂覆时的各种条件一、表面处理1、概述适当的表面处理对于防护漆的成功使用至关重要。
清除油脂、老化涂层以及表面污物(如底材上的氧化皮和锈蚀、混凝土上的浮浆,以及镀锌钢表面的锌盐等),是表面处理最重要的环节。
2、清除污物钢表面防护漆的性能,在很大程度上受到与涂层直接接触的底材表面条件的影响。
其中主要的影响因素如下:A) 表面污物,包括盐类、油脂、钻孔液和切削液。
B) 锈蚀和氧化皮。
C) 表面粗糙度。
表面处理的主要目的是确保上述所有污物都清除干净,减少初期锈蚀的机会,并形成表面粗糙度,保证即将涂覆的油漆具有充分的附着力。
3、清除油脂在进行下一步表面处理或者给钢涂漆之前,必须清除表面所有的可溶盐、油脂、钻孔液和切削液,以及其它污物。
最常见的方法是先用溶剂清洗,然后用干净的抹布擦净。
试擦步骤极为关键,因为如果试擦彻底,那么溶剂清洗反而会将污物扩散。
4、人工处理钢表面上松散的氧化皮、锈蚀和老化涂层可以用钢丝刷刷掉、用砂纸砂去、用手工工具刮掉或铲除。
但是,所有这些方法都不彻底,尤其是紧紧附着在钢表面的薄锈层,更难清除。
5、动力处理一般来说,在清除松散的氧化皮、老化涂层和锈蚀时,用动力工具比用人工效果好,而且省力。
但是动力工具不能除去紧紧附着在钢表面的锈蚀和氧化皮。
通常采用的动力工具,包括动力钢丝刷、冲击工具(如撞针枪)、砂轮机及砂皮磨光机。
但是,必须注意,不要抛光金属表面,尤其是在使用动力钢丝刷时,否则会破坏涂覆所需的表面粗糙度。
高压无气喷涂工艺指导书及工艺评定
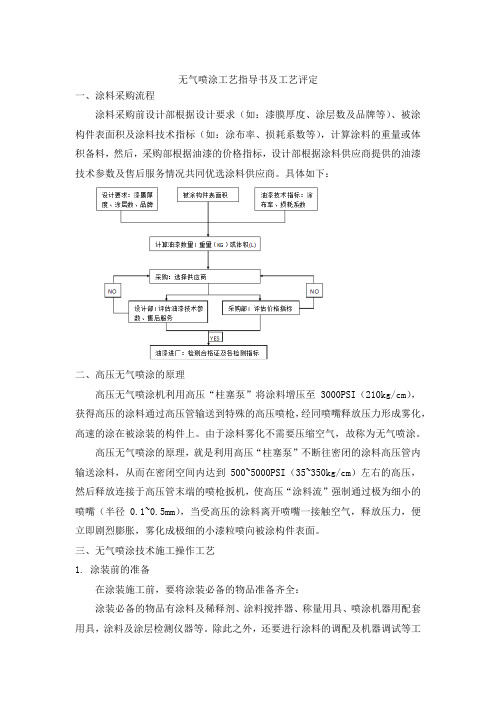
无气喷涂工艺指导书及工艺评定一、涂料采购流程涂料采购前设计部根据设计要求(如:漆膜厚度、涂层数及品牌等)、被涂构件表面积及涂料技术指标(如:涂布率、损耗系数等),计算涂料的重量或体积备料,然后,采购部根据油漆的价格指标,设计部根据涂料供应商提供的油漆技术参数及售后服务情况共同优选涂料供应商。
具体如下:二、高压无气喷涂的原理高压无气喷涂机利用高压“柱塞泵”将涂料增压至3000PSI(210kg/cm),获得高压的涂料通过高压管输送到特殊的高压喷枪,经同喷嘴释放压力形成雾化,高速的涂在被涂装的构件上。
由于涂料雾化不需要压缩空气,故称为无气喷涂。
高压无气喷涂的原理,就是利用高压“柱塞泵”不断往密闭的涂料高压管内输送涂料,从而在密闭空间内达到500~5000PSI(35~350kg/cm)左右的高压,然后释放连接于高压管末端的喷枪扳机,使高压“涂料流”强制通过极为细小的喷嘴(半径0.1~0.5mm),当受高压的涂料离开喷嘴一接触空气,释放压力,便立即剧烈膨胀,雾化成极细的小漆粒喷向被涂构件表面。
三、无气喷涂技术施工操作工艺1. 涂装前的准备在涂装施工前,要将涂装必备的物品准备齐全:涂装必备的物品有涂料及稀释剂、涂料搅拌器、称量用具、喷涂机器用配套用具,涂料及涂层检测仪器等。
除此之外,还要进行涂料的调配及机器调试等工作。
(1)涂料的调配A. 确认涂料根据涂装要求确认涂料的品种及质量,发现问题及时更正。
B. 调整涂料粘度将涂料充分搅拌均匀,测量涂料的粘度,若粘度过高时,应适当加入稀释剂调至合适的粘度。
(2)喷涂机的安装与检查A. 安装:将备好的喷涂机的各部件及辅助配件正确安装、连接。
B. 喷涂机安装连接完毕,进入待喷涂状态,喷涂前要检查动力源是否运转正常,然后吸入涂料,检查高压涂料缸是否增压正常,输料软管有无泄漏,配件间连接是否紧密,喷枪及滤网有无堵塞情况等。
发现故障,及时排除。
C. 涂装环境条件控制:测量喷涂环境的温度及湿度,符合涂装条件,即可进行涂装作业。
- 1、下载文档前请自行甄别文档内容的完整性,平台不提供额外的编辑、内容补充、找答案等附加服务。
- 2、"仅部分预览"的文档,不可在线预览部分如存在完整性等问题,可反馈申请退款(可完整预览的文档不适用该条件!)。
- 3、如文档侵犯您的权益,请联系客服反馈,我们会尽快为您处理(人工客服工作时间:9:00-18:30)。
编制(日期)
审核(日期)
A182-F51喷焊Ni55工艺指导书
单位名称:有限公司批准人签字:
喷焊工艺指导书编号:日期:
喷焊方法:氧-乙炔火焰喷焊。机械化程度:手工
喷焊面:
喷焊形式:球面喷焊溶敷层次:5
喷焊顺序:工件清理-预热-喷涂保护粉(0.1)-加热(500℃)-喷涂工作粉末-基体涂层同步加温(800℃)-重溶-焊后热处理。
冷却方式:空冷
其他:每焊完一件即刻入炉。(不要求抗晶间腐蚀时不作此处理)
检验:喷焊面应平整、无裂纹、气孔、夹渣、未溶合、疏松、气孔等缺陷。喷焊面渗透探伤检验
喷焊位置:球表面喷焊,平焊。
喷焊操作:(两步法喷焊)
1、清理:清理工件表面,粗糙度12.5,无任何污染和缺陷,清理后即刻喷涂。
2、工件预热:如用喷枪,采用中性焰或略带碳化焰,喷枪与工件距离30~40 mm。预热至400℃。
C
Si
Fe
Cr
Ni
B
Mo
Cu
0.75
4
14
15.5
Bal33Fra bibliotek3工件预热:
预热温度(℃):400~500
保持预热时间(h):1~2
加热方式:箱式炉或火焰加热(中性焰或略带碳化焰)(金属表面不能氧化)
焊后热处理:(要求抗晶间腐蚀时)
加热温度(℃):890升温速度(℃/h):100~150保温时间(h):1~2
3、喷涂保护粉末:喷涂时工件转动均匀缓慢,施焊层处于平焊位置。采用中性火焰。焰心长度7毫米,喷嘴距工件表面90~100 mm,垂直于工件表面。喷焊第一层(厚0.1 mm)。
4、继续加热:
用喷涂枪或重溶枪用中性火焰,喷嘴至工件表面30~40mm,将工件继续加热至500~600℃(呈暗红色)。
5、喷涂工作粉末:按喷涂保护粉末规定,继续分层均匀喷粉到工件表面(每层0.1~0.2mm),至厚度要求。每层、次的喷粉有1/3的重叠,喷涂中如工件温度降低,即应边喷粉边用另一把喷枪加热。
6、继续加热:喷涂达到预定厚度后,将喷嘴移至工件表面30~40mm,基体与涂层同时继续加热加热至800℃,升温要快。
7、重溶:当温度达到800℃时,即可重溶,采用中性火焰,将喷嘴移至工件表面20~30mm,应注意不可过热,时间越短越好。
8、焊后处理
喷焊参数:
喷焊层次
填充金属
气体压力(Mpa)
气体流量(升/时)
焊层厚度(mm)
氧气
乙炔气
氧气
乙炔气
1~顶层
Ni62
0.4~0.5
0.07~0.08
1200
950
0.1~0.2
重熔参数:
气体压力(Mpa)
气体流量(升/时)
氧气
乙炔气
氧气
乙炔气
0.4~0.5
0.05
2600
1200
技术措施:
环境条件:
室内、室温,相对湿度小于90%,空气畅通。
多层或单层焊:多层
焊前准备和清理:
母材:
类、组别号:Ⅶ-2或标准号:ASTM
钢号:A182-F51
尺寸范围:3/4″~14″
熔敷金属:球表面,厚0.3mm
喷焊材料:
焊剂类别:自熔镍基合金粉末。
焊剂标准:GB 5315-85(FZNCr-55B)。牌号:Ni55
烘培温度(℃):120℃。保温2小时(有吸潮现象或存放期超过3个月)
焊剂熔敷金属化学成分(%)熔敷金属硬度(HRc):52-58