DEFORM在金属热处理工艺设计中的应用
Deform-3d热处理模拟操作全解
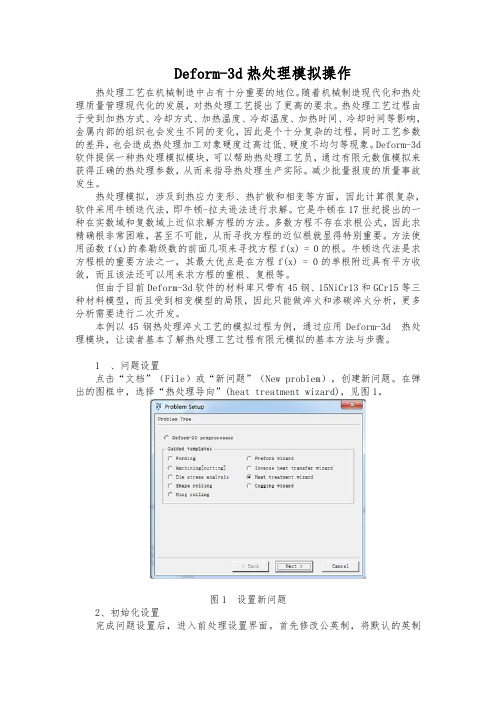
Deform-3d热处理模拟操作热处理工艺在机械制造中占有十分重要的地位。
随着机械制造现代化和热处理质量管理现代化的发展,对热处理工艺提出了更高的要求。
热处理工艺过程由于受到加热方式、冷却方式、加热温度、冷却温度、加热时间、冷却时间等影响,金属内部的组织也会发生不同的变化,因此是个十分复杂的过程,同时工艺参数的差异,也会造成热处理加工对象硬度过高过低、硬度不均匀等现象。
Deform-3d 软件提供一种热处理模拟模块,可以帮助热处理工艺员,通过有限元数值模拟来获得正确的热处理参数,从而来指导热处理生产实际。
减少批量报废的质量事故发生。
热处理模拟,涉及到热应力变形、热扩散和相变等方面,因此计算很复杂,软件采用牛顿迭代法,即牛顿-拉夫逊法进行求解。
它是牛顿在17世纪提出的一种在实数域和复数域上近似求解方程的方法。
多数方程不存在求根公式,因此求精确根非常困难,甚至不可能,从而寻找方程的近似根就显得特别重要。
方法使用函数f(x)的泰勒级数的前面几项来寻找方程f(x) = 0的根。
牛顿迭代法是求方程根的重要方法之一,其最大优点是在方程f(x) = 0的单根附近具有平方收敛,而且该法还可以用来求方程的重根、复根等。
但由于目前Deform-3d软件的材料库只带有45钢、15NiCr13和GCr15等三种材料模型,而且受到相变模型的局限,因此只能做淬火和渗碳淬火分析,更多分析需要进行二次开发。
本例以45钢热处理淬火工艺的模拟过程为例,通过应用Deform-3d 热处理模块,让读者基本了解热处理工艺过程有限元模拟的基本方法与步骤。
1 、问题设置点击“文档”(File)或“新问题”(New problem),创建新问题。
在弹出的图框中,选择“热处理导向”(heat treatment wizard),见图1。
图1 设置新问题2、初始化设置完成问题设置后,进入前处理设置界面。
首先修改公英制,将默认的英制(English)修改成公制(SI),同时选中“形变”(Deformation)、“扩散”(Diffusion)和“相变”(Phase transformation),见图2。
DEFORM-3D基本操作指南

3、设置模拟类型
1)、deformation:变形模拟 2)、heat transfer:传热模拟 3)、transfmation:相变模拟 4)、diffusion:扩散模拟 5)、grain:晶粒度模拟 6)、heating:热处理模拟
二、导入毛坯几何文件
1.在前处理的物体操作窗口中点击按钮 (Geometry) ,然后再选 择 (Import Geometry),选择在CAD中或其他CAE软 件中的造型文件。(本例中选择安装目录下DEFORM3D\V6.1\Labs 的Block_Billet.STL。) 2.在DEFORM3D v6.1的版 本中,默认第一个物体是 工件(毛坯),所以物体 属性默认为Rigid-plastic。
四、导入模具文件
1. 导入上下模具的几何文件。在前处理控制窗口中点击增加物体按钮 Inter Objects…进入物体窗口。可以看到在Objects列表中增加了 一个名为Top Die的物体。 2.在当前选择默认Top Die 物体的情况下,直接 选择 然后选 3.本例中选择安装目录下 DEFORM3D\V6.1\ Labs的 Block_Top Die .STL
DEFORM-3D可以应用于金属成形的冷加工、热加工 等工 艺。 DEFORM-3D的典型应用:拉深、锻造、挤压、压塑、 冷 镦、机加工、轧制、开坯、镦锻等。
(更多相关应用请见)
说明:
1、 DEFORM-3D软件不支持中文,因此文件夹及其模 型文件中不能出现中文,否则无法读取。 2、 DEFORM-3D不具备三维造型功能,所以该软件所 用模型均在其它三维软件中建立。 3、 DEFORM-3D软件操作环境的坐标与Pore、UG软件 中默认的坐标系相同。所以在创建模型的时候最好把位臵 关系安排好,这样调进来的模型比较容易调整。 4、使用有限元软件时,要养成分析每个问题创建新 的文件夹的习惯。因为打开DEFORM-3D软件,其默认安装 目录下会自动生成一文件夹,所作模拟都会放臵在该文件 夹下,不便于管理。
deform 热处理报告

材料成型专业综合性实验报告热处理工艺对45#钢组织性能的影响学生专业: 材料成型与控制工程学生班级:学生学号: 1学生姓名:指导老师:报告日期: 2016年7月目录一、综述、、、、、、、、、、、、、、、、、、、、、、、、、、、、、、、、、、、、、、3二、实验目的、、、、、、、、、、、、、、、、、、、、、、、、、、、、、、、、、、、7三、材料及仪器、、、、、、、、、、、、、、、、、、、、、、、、、、、、、、、、、8四、实验过程及热处理模拟操作、、、、、、、、、、、、、、、、、、、8五、实验结果及热处理模拟对比分析、、、、、、、、、、、、、、、、9六、结果分析、、、、、、、、、、、、、、、、、、、、、、、、、、、、、、、、、、、、、、16七、结论、、、、、、、、、、、、、、、、、、、、、、、、、、、、、、、、、、、、、、16参考文献、、、、、、、、、、、、、、、、、、、、、、、、、、、、、、、、、、、17一、综述1、钢的热处理钢的热处理就就是把钢在固态下加热到一定的温度进行必要的保温,并以适当的速度冷却到室温,以改变钢的内部组织,从而得到所需性能的工艺方法。
热处理与其她加工方法(铸造、锻压、焊接、切削加工等)不同,它只改变金属材料的组织与性能,而不改变其形状与大小,所以用它来处理零件、工具等制成品,处理各种工具、刀具、齿轮与转轴等。
钢在热处理条件下所得到的组织与钢的平衡组织有很大的差别,钢加热到临界点(A)以上时发生奥氏体转变,奥氏体在非常缓1慢冷却时才能得到平衡组织状态的珠光体或珠光体+铁素体(或渗碳体),但大部分热处理工艺,如退火、正火、淬火、(回火或时效例外)都就是将钢加热到奥氏体状态,然后以不同的冷却速度(或冷却方式)冷却到室温。
退火、正火、淬火的冷却速度的不同,则会得到不同的组织,其力学性能或物理性能也不同。
2.45#钢的综述45号钢就是GB中的叫法,JIS中称为:S45C,ASTM中称为1045,080M46,DIN为:C45。
Deform-3d热处理模拟操作全解
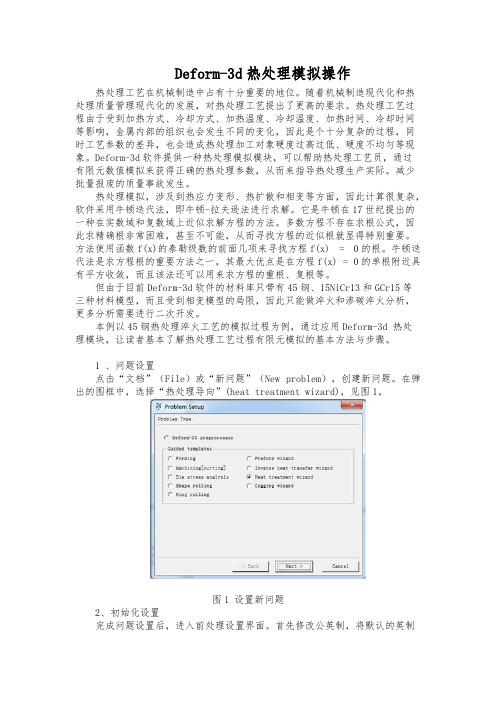
Deform-3d热处理模拟操作热处理工艺在机械制造中占有十分重要的地位。
随着机械制造现代化和热处理质量管理现代化的发展,对热处理工艺提出了更高的要求。
热处理工艺过程由于受到加热方式、冷却方式、加热温度、冷却温度、加热时间、冷却时间等影响,金属内部的组织也会发生不同的变化,因此是个十分复杂的过程,同时工艺参数的差异,也会造成热处理加工对象硬度过高过低、硬度不均匀等现象。
Deform-3d软件提供一种热处理模拟模块,可以帮助热处理工艺员,通过有限元数值模拟来获得正确的热处理参数,从而来指导热处理生产实际。
减少批量报废的质量事故发生。
热处理模拟,涉及到热应力变形、热扩散和相变等方面,因此计算很复杂,软件采用牛顿迭代法,即牛顿-拉夫逊法进行求解。
它是牛顿在17世纪提出的一种在实数域和复数域上近似求解方程的方法。
多数方程不存在求根公式,因此求精确根非常困难,甚至不可能,从而寻找方程的近似根就显得特别重要。
方法使用函数f(x)的泰勒级数的前面几项来寻找方程f(x) = 0的根。
牛顿迭代法是求方程根的重要方法之一,其最大优点是在方程f(x) = 0的单根附近具有平方收敛,而且该法还可以用来求方程的重根、复根等。
但由于目前Deform-3d软件的材料库只带有45钢、15NiCr13和GCr15等三种材料模型,而且受到相变模型的局限,因此只能做淬火和渗碳淬火分析,更多分析需要进行二次开发。
本例以45钢热处理淬火工艺的模拟过程为例,通过应用Deform-3d 热处理模块,让读者基本了解热处理工艺过程有限元模拟的基本方法与步骤。
1 、问题设置点击“文档”(File)或“新问题”(New problem),创建新问题。
在弹出的图框中,选择“热处理导向”(heat treatment wizard),见图1。
sgniht图1 设置新问题2、初始化设置完成问题设置后,进入前处理设置界面。
首先修改公英制,将默认的英制t h i ng si nt he i rb ei n ga re go od fo rs (English )修改成公制(SI ),同时选中“形变”(Deformation )、“扩散”(Diffusion)和“相变”(Phase transformation),见图2。
运用Deform有限元分析优化锻造模具设计

软件介绍D eform 是一套基于有限元的工艺仿真系统,用于分析金属成形及其相关工艺的各种成形和热处理工艺。
通过在计算机上模拟整个加工过程,帮助工程师和设计人员设计工具和产品工艺过程,减少昂贵的现场实验成本。
提高模具的设计效率,降低生产的材料成本,缩短产品的研究开发周期。
案例分析以下就通过一个案例阐述在实际设计中如何运用D eform 有限元分析来优化锻造工艺及其锻造模具的设计。
图1产品是水龙头的一个重要零件,材质为铅黄铜(C uZn40Pb2),产品重量419克。
锻造工艺有两种方案:①开式模锻,如图2,②闭式挤压,如图3。
运用Deform 有限元分析优化锻造模具设计刘名水图1水龙头重要零件图2开式模锻图3闭式挤压!!!!!!!!!!!对两种方案分别运用DEFROM 进行模拟分析。
DEFROM 软件操作过程:因DEFROM -3D 本身建立几何模型功能较差,难以建立复杂几何模型,且模具设计是用P roe设计,所以就用P roe 建立几何模型。
上模,下模,以及锻造原材料(铜棒)。
用P roe 建好几何模型后,把上模,下模,原材料分别导成.stl 文件。
打开DEFROM -3D 中的DEFROM -F3模块,建立模拟文件,首先进行前处理。
导入之前建立的几何模型(.stl 文件),为了简化计算,不考虑热量在原材料与模具之间的传递,原材料进行网格划分,设定锻造参数:锻造温度700℃,模具温度150℃,摩擦系数0.3,上模移动速度400mm/sec ,上模移动距离等,原材料选择DE -FROM-3D 软件自带材料库里的DI N -CuZn40Pb2。
其中最重要的是注意原材料的网格划分,网格划分越粗,即网格数量越少,模拟计算就越不准确。
相反,网格划分越细,即网格数量越多,模拟计算就越准确,但计算量就越大。
需根据计算机硬件条件及分析需求,合理划分网格数。
前处理设定好,检测数据OK 后,生成待模拟计算数据。
然后进行模拟计算。
DEFORM软件应用实例2

3 -11 锻件有限元网格图
3 -12 锻件终锻截面图
3 -13 不同飞边的 锻件图
分析上面的模拟结果图可以知道, φ78×228mm的坯料足以充满型
腔,锻件没有产生任何缺陷。图3-13中的第一个锻件采用φ75×228mm
的坯料,第二个锻件采用的是φ78×228mm的坯料,从图中两个锻件的
飞边比较来看,第一个锻件的飞边较薄,而第二个锻件的飞边大而且厚,
数设定为0.25,假定模具为刚体,不发生变形。
3.1.2.2 有限元模拟
3.1.2.2.1 坯料优化 模拟首先选用了φ72×223mm的坯料,并经压扁工步压扁30mm,模拟
结果如图3 -18~3-21所示。
图3 -18 坯料压扁状态
图3 -19 锻件终锻状态
图3-20 锻件有限元网格图
图3-21 锻件终锻截面图
件的侧面与飞边的连接处出现了折叠。采用压扁工步合理地分配了坯料的
体积,使坯料更符合金属的变形规律,变形比较均匀,因此锻件质量较好。
3.1.1.2.3 温度场模拟 温度场模拟结果如图3 -15所示。
(a) 锻件温度场
图3 -15 温度场模拟图
(b) 锻模温度场
3.1.2 084锻件
084锻件的锻件图和模具图如图3 -16和3 -17所示。
2、精化坯料尺寸,减少产品和材料的费用;
3、优化锻造工艺、优化锻模设计
4、降低产品成本,缩短新产品研制周期,提高企业的市场竞争力。
DEFORM不同于一般目的的通用有限元模拟软件,其被设计成
适合用于对锻造过程中金属变形的模拟。DEFORM提供了友好的用
户界面,为前处理的数据准备工作以及分析过程提供了方便,该软件
第二部分 UG软件及其与DEFORM间数据交换
DEFORM金属成形及热处理模拟解决方案

DEFORM金属成形及热处理模拟解决方案1DEFORM锻造、拉拔模拟方案DEFORM锻压数值模拟可实现适热、冷、温状态下的自由锻、模锻、开坯、墩粗、拉拔、挤压等成形工艺的仿真分析,提供极有价值的工艺分析数据:➢通过锻造、拉拔全过程模拟,获得成形产品形状及尺寸,有助于分析锻件、管材、棒材等横向缺陷发生的原因;多工步成形过程模拟➢获得成形过程工件应力场、应变场及速度场分布;➢提高模内金属流动现象,分析材料流动规律;➢预测成形缺陷,包括裂纹、拉痕、凹坑、缩径、折叠、填充不足等;裂纹折叠➢可优化工艺参数,包括成形吨位、拉拔力、拉拔速度、润滑方案、锻造温度、拉坯截面形状等;➢分析及优化模具结构,包括模具内腔、模具孔径、孔型,入模锥角等;不同孔径及毛坯的优化➢获得模具应力场数据,分析模具强度,模具磨损。
模具主应力和等效应力2DEFORM轧制模拟方案DEFORM轧制模拟可以实现有色金属及钢等的管材、板材及其他型材的连轧、滚轧、扩孔等工艺,预测成形尺寸、成形缺陷等结果,提供快速全面的工艺优化模拟方案:➢根据工艺流程,实现冷轧、热轧的成形过程,预测成形产品形状及尺寸、有助于分析缺陷的产生。
➢预测轧制过程中出现的折叠、塔型卷曲、壁厚不均、变形扭曲、流线紊乱等轧制缺陷。
➢获得成形过程金属应力、应变、速度、损伤、温度等场变量数据。
应力云图及板型尺寸变化➢分析轧制过程金属流动规律,有助于成形方式的控制。
➢优化工艺参数,包括轧制速度、轧制道次、轧制厚度等。
➢耦合模具应力分析,可判断轧辊发生弹性变形对轧制效果的影响。
➢可模拟复合材料的轧制过程,研究复合材料的成形特型。
3DEFORM微观组织模拟方案DEFORM采用元胞自动机及蒙特卡洛法实现微观组织相图及演变过程的可视化模拟,通过耦合结构及温度,获得成形过程及热处理过程中微观组织的模拟分析,提供多方面的分析方案:➢模拟微观组织在锻造、轧制、自由锻等成形过程、热处理过程及加热、冷却过程的演变;自由锻过程晶粒细化分布(红色为细化部分)➢ 模拟晶粒生长,分析整个过程的晶粒尺寸变化;➢ 计算成形及热处理过程中的回复再结晶现象,包括动态再结晶、中间动态再结晶及静态再结晶;➢ 通过微观演变预测总体性能,避免缺陷;➢ 模拟微观组织相的转变,提供转变时间、转变温度及任一时刻的微观演变结果;马氏体转变率分布云图及残余应力云图 ➢ 用户可二次开发自己的晶粒演变模型用于微观组织计算,验证新的演变模型的可行性;➢ 具有元胞自动机法、蒙特卡洛法等计算方法,可现实微观组织相图、晶粒尺寸、晶界及晶向,实现微观组织演变的可视化观测;➢ 分析成形过程中晶粒织构的变化情况,有助于优化成形工艺;ε =0 ε = 0.01 ε = 0.3 ε = 1.24 DEFORM 热处理模拟方案金属的热处理工艺,主要包括钢的奥氏体化,渗碳,淬火,回火,有色金属的金相固溶沉淀、应力松弛。
Ansys金属成形及热处理专业仿真环境:DEFORM介绍

Ansys金属成形及热处理专业仿真环境:DEFORM介绍DEFORM是一套基于有限元的工艺仿真系统,用于分析金属成形及其相关的各种成形工艺和热处理工艺。
二十多年来的工业实践证实了基于有限元法的DEFORM有着卓越的准确性和稳定性,模拟引擎在大流动、行程载荷和产品缺陷预测等方面同实际生产相符,保持着令人叹为观止的精度。
DEFORM通过在计算机上模拟整个加工过程,帮助工程师和设计人员:∙设计工具和产品工艺流程,减少昂贵的现场试验成本;∙提高工模具设计效率,降低生产和材料成本;∙缩短新产品的研究开发周期;∙DEFORM 不同于一般的有限元程序,是专为金属成形而设计、为工艺设计师量身定做的软件。
DEFORM具有非常友好的图形用户界面,可帮助用户方便地进行数据准备和成形分析。
这样,工程师们便可把精力主要集中在工艺分析上,而不是去学习烦琐的计算机软件系统。
<特色功能∙友好的图形界面;∙高度模块化、集成化的有限元模拟系统;∙有限元网格自动生成器以及网格重分自动触发系统;∙集成金属合金材料库;∙集成多种成形设备模型;∙用户自定义子程序。
客户价值∙完善的IGES、STL、IDEAS、PATRAN、NASTRAN等CAD和CAE接口,方便用户导入模型;∙提供多达230种材料数据的材料库,几乎包含了所有常用材料的弹性变形数据、塑性变形数据、热能数据、热交换数据、晶体长大数据、材料硬化数据和破坏数据,方便用户计算过程中使用;∙系统集成了在任何必要时能够自行触发自动网格重划生成器,生成优化的网格模型。
在精度要求较高的区域,可以划分较细密的网格,从而降低题目的规模,并显著提高计算效率;∙提供三种迭代计算方法:Newton-Raphson、Direct和Explicit,用户可根据不同工况、不同材料性能选择不同计算方法;∙多种控制选项和用户子程序使得用户在定义和分析问题时有很大的灵活性;∙并行求解显著提高求解速度;∙获得金属成形过程中的速度场、静水压力场、应力应变、温度场结果,以分析型材成形中波浪、扭拧、折叠、裂纹等缺陷;∙设计工具和产品工艺流程,减少昂贵的现场试验成本;∙提高工模具设计效率,降低生产和材料成本;∙为用户优化模具结构及工艺参数;∙缩短新产品的研发周期。
DEFORM基本操作指南(行业信息)
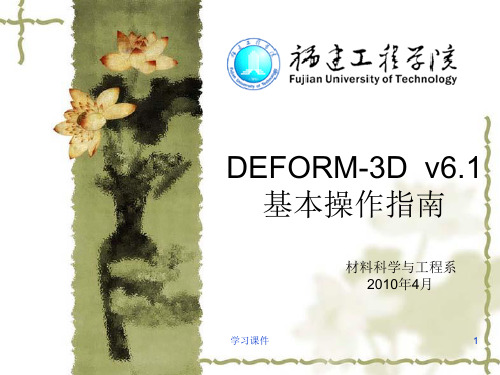
指向对象外。如果方
向反了,点击按钮
。
学习课件
21
三、划分网格
对于那些非刚性材料和考虑传热影响的刚体(Rigid)材料,需要划分有 限元网格:
1.点击按钮进入网格划分窗口; 2.可以在网格数量输入框中输入单元数或用滑动条来设定。在本例 中,默认为8000(在DEFORM3D中只能划分四面体网格,如果你想用六 面体网格可以点击按钮Import,输入IDEAS或PATRAN的网格) 3.点击下面的按钮Preview可 以预览,如果满意,可以点击按 钮Generate Mesh来生成网格。 注:1)preview只划分元件表面; 2)generate mesh即划分表
学习课件
29
九、定义物间关系
1.在前处理控制窗口的右上角点击 Yes弹出Inter Object窗口。
按钮,会出现一个提示,选择
2.定义物间从属关系:在v6.1中,系统会自动将物体1和后面的物体定
为从属关系(Slave-Master),即软的物体为Slave,硬的物体设为
Master。
学习课件
30
1.点击按钮
,进入新的窗口
2.选择剪切摩擦方式Shear,输入常摩擦系数constant,如果你对具体 的摩擦系数没有概念,可以选择工艺种类,例如,本例中的冷Cold Forming用的是Steel Die,摩擦系数系统会设为0.12,点击Close按 钮,关闭窗口。
面单元又划分体单元。
(具体网格划分总类见后面)
学习课件
22ห้องสมุดไป่ตู้
四、导入模具文件
1. 导入上下模具的几何文件。在前处理控制窗口中点击增加物体按钮
Inter Objects…进入物体窗口。可以看到在Objects列表中增加了
DEFORM软件简介

• 1.14后处理 1)状态变量的读取
等效应变显示图
等高线显示的等效应变显示图
• 2)工件上的点追踪
经过变形后三点的坐标值
三点的Z方向应变曲线
三点的X方向应变曲线
• 3)对象剖面的选择
curve
plane
curve+plane
剖切面上等效应力的分布
2.方环镦粗模拟实例
• 2.1创建新项目 • 2.2加载模拟对象数据 1)建立几何模型 2)划分网格 3) 设置材料属性
• 2.3添加上模 • 2.4设置模具的运动
• 2.5设定对称边界条件
• 2.6模拟信息的设定控制
ቤተ መጻሕፍቲ ባይዱ
• 2.9后处理
• 模拟处理器:DEFORM 运行时,首先通过有限元离散化 将平衡方程、本构关系和边界条件转化为非线形方程组, 然后通过直接迭代法和Newton—Rapson法进行求解,求 解的结果以二进制的形式进行保存,用户可在后处理器中 获取所需要的结果。 • 后处理器:用于显示计算结果,结果可以是图形形式,也 可以是数字、文字混编的形式。可获取的结果可为每一步 的(1)有限元网格;(2)等效应力、等效应变以及破坏程度 的等高线和等色图;(3)速度场;(4)温度场;(5)压力行程 曲线等。此外用户还可以列点进行跟踪,对个别点的轨迹、 应力、应变、破坏程度进行跟踪观察,并可根据需要抽取 数据。
DEFORM软件简介
DEFORM是一套基于有限元的工艺仿真系统, 用于分析金属成形及其相关工业的各种成形工 艺和热处理工艺。通过在计算机上模拟整个加 工过程,帮助工程师和设计人员: 设计工具和 产品工艺流程,减少昂贵的现场试验成本。 提 高工模具设计效率,降低生产和材料成本。缩 短新产品的研究开发周期。 典型应用于:锻造、机加工、轧制、挤压、冷 镦、拉伸等
[整理版]基于deform在金属塑性成形中的应用
![[整理版]基于deform在金属塑性成形中的应用](https://img.taocdn.com/s3/m/944826076d175f0e7cd184254b35eefdc8d3158a.png)
基于deform 在金属塑性成形中的应用铜陵学院09材控一班陈军 0910121117摘要:由于deform-3D不具有三维造型功能,所以要实现塑性模拟过程所需要的物理模型均在其他三维软件中建立。
然后利用deform软件所具备的重新划分网格后,原节点的信息不会丢失。
设定变形物体的网格重划分网格标准,有两种选择:一个是绝对值,一个是相对值。
在deform软件的材料库中,各种材料都被分成易于选择的类别。
材料可以通过单位制或加工工艺类型进行检索。
这里主要介绍deform图形文件的生成及其相关功能键使用方法。
正文:一,deform软件的操作流程:(1)、定义几何特征。
Deform中对象的几何数据具有多种格式可供选择。
(2)、网格划分。
Deform网格划分生成四面体单元,这种四面体表面适合于表面成型。
(3)、初始条件。
如轧制时设置变形体、模具与周围介质间的热交换,变形体内部大变形生成热量及其传导都对产品的成形质量造成很大影响,对此问题的仿真模拟分析应按瞬间热-机耦合处理。
Deform软件可提供多种温度下的材料特性。
(4)、材料模型。
这里只研究钢塑性材料。
设定材料变形前,变形时,变形终了的温度和变形率下材料流动应力应变曲线和热膨胀系数、弹性模量、泊松比、热导率等随温度变化的曲线。
(5)、接触定义。
定义变形体与模具之间以及模具之间可能产生的接触关系。
变形的的温度、变形是待求量,变形体为接触体,刚性接触时只具有常温,起主动传递位移或合力作用。
如果需要模具的温度变化,可将模具上要关心的部分离散成单元,定义成允许热传递的刚性接触体,可以与外界催在热交换。
(6)、网格自动重划分。
模拟分析过程中,单元附着在材料上,材料流动中极易造成相应的单元格畸变,单元格畸变后会中断计算过程。
因此保证仿真过程中材料经大量流动后仍然可以继续,获得的结果仍然具有足够的精度。
Deform在网格畸变到一定程度后会自动进行网格重划分,生成搞质量的网格。
DEFORM 热冲压成形工艺数值模拟技术应用

DEFORM热冲压成形工艺数值模拟技术应用安世亚太公司工艺产品部1 前言热冲压成形工艺可使超高强度钢具有极好的可塑性、良好的成形性能及热加工性能,钣金热冲压成形技术作为钣金件冲压强化的有效途径,已在汽车等领域得到了越来越广泛的应用。
热冲压件可应用于汽车A柱、B柱、边梁、保险杠、顶盖纵梁、门梁、侧栏等重要结构件。
DEFORM金属热冲压成形模拟技术可实现高强度钣金热冲压成形过程的分析,预测冲压缺陷及热冲过程淬火现象,优化热冲工艺参数及热冲模设计。
2 热冲压成形工艺技术及特点热冲压成形是一项专门用来成形超高强度钢板冲压件的新型工艺和技术,是获得超高强度冲压件的有效途径。
热冲压成形部件的抗拉强度可达1500MPa以上,抗疲劳极限可达800MPa,因此硼钢等超高强度钢以其高强度特性已成为汽车重要保护部件用钢的最佳选择。
热冲压成形具有很多优点,如可得到超高强度的车身覆盖件;在保证汽车安全性能得条件下,优化设计以减薄车身零部件,可减轻车身重量,提高车身安全性、舒适性;改善冲压成形性,降低钣金出现易拉伸失稳性,克服传统工艺回弹严重、成形困难容易开裂等诸多难题。
热冲工艺成形技术是将钢板(如硼钢)加热至奥氏体状态,然后进行冲压并同时以20-30摄氏度/秒的冷却速度进行淬火处理,通过一定时间的保压以获得具有均匀马氏体组织的高强度钢钣金件的成形方式。
热冲压工艺包括直接成形(图1)和间接成形(图2),间接成形工艺因增加了设备成本,故现在的热冲压主要以直接热冲压工艺为主。
图1 直接热冲压成形工艺图2 间接热冲压成形工艺3 DEFORM热冲压成形工艺方案的工业应用热冲压成形技术虽具有很多优点,但因较普通冷冲压成形存在热成形及淬火冷却热处理的诸多因素影响,使得如何进行热冲压工艺参数优化及模具冷却结构设计成为需要解决的问题。
影响热冲成形的因素包括板料拉伸性能参数、冲压温度、冲压速度、润滑方案、保压时间、冷却速度及模具冷却水管的结构分布设计等,因此如何在工艺及模具设计阶段优化工艺设计参数,是提高热冲成形效率,降低研发成本的重点。
Deform-3d热处理模拟操作全解
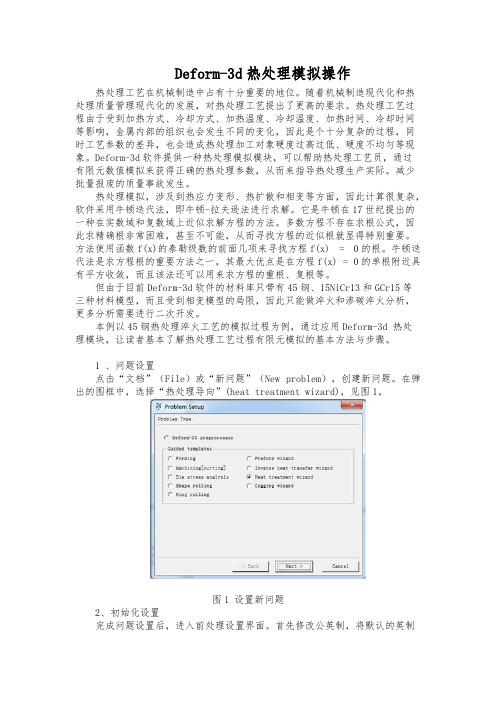
Deform-3d热处理模拟操作热处理工艺在机械制造中占有十分重要的地位。
随着机械制造现代化和热处理质量管理现代化的发展,对热处理工艺提出了更高的要求。
热处理工艺过程由于受到加热方式、冷却方式、加热温度、冷却温度、加热时间、冷却时间等影响,金属内部的组织也会发生不同的变化,因此是个十分复杂的过程,同时工艺参数的差异,也会造成热处理加工对象硬度过高过低、硬度不均匀等现象。
Deform-3d软件提供一种热处理模拟模块,可以帮助热处理工艺员,通过有限元数值模拟来获得正确的热处理参数,从而来指导热处理生产实际。
减少批量报废的质量事故发生。
热处理模拟,涉及到热应力变形、热扩散和相变等方面,因此计算很复杂,软件采用牛顿迭代法,即牛顿-拉夫逊法进行求解。
它是牛顿在17世纪提出的一种在实数域和复数域上近似求解方程的方法。
多数方程不存在求根公式,因此求精确根非常困难,甚至不可能,从而寻找方程的近似根就显得特别重要。
方法使用函数f(x)的泰勒级数的前面几项来寻找方程f(x) = 0的根。
牛顿迭代法是求方程根的重要方法之一,其最大优点是在方程f(x) = 0的单根附近具有平方收敛,而且该法还可以用来求方程的重根、复根等。
但由于目前Deform-3d软件的材料库只带有45钢、15NiCr13和GCr15等三种材料模型,而且受到相变模型的局限,因此只能做淬火和渗碳淬火分析,更多分析需要进行二次开发。
本例以45钢热处理淬火工艺的模拟过程为例,通过应用Deform-3d 热处理模块,让读者基本了解热处理工艺过程有限元模拟的基本方法与步骤。
1 、问题设置点击“文档”(File)或“新问题”(New problem),创建新问题。
在弹出的图框中,选择“热处理导向”(heat treatment wizard),见图1。
sgniht图1 设置新问题2、初始化设置完成问题设置后,进入前处理设置界面。
首先修改公英制,将默认的英制t h i ng si nt he i rb ei n ga re go od fo rs (English )修改成公制(SI ),同时选中“形变”(Deformation )、“扩散”(Diffusion)和“相变”(Phase transformation),见图2。
DEFORM自由锻模拟与应用

DEFORM自由锻模拟与应用CAE仿真是当前比较流行的工艺研发工具,尤其对于新材料、新工艺开发方面发挥了重要的指导作用。
对于金属成形过程的仿真,国内应用已经非常普遍,很多工艺人员在做模锻成形仿真时通常是观察金属流动情况,分析是否完全充满模具、是否有折叠缺陷,以及设备吨位是否过载等缺陷,而自由锻成形,是比较传统的锻造工艺,工艺过程及模具都相对简单,因此很多人都困惑除了模拟形状尺寸变化以外,自由锻仿真分析什么呢?DEFORM是世界上最著名的金属成形及热处理仿真分析软件,美国SFTC公司经过三十多年的研发和改进,DEFORM软件具有各类典型的成形工艺向导式模块,这些向导式模块也融合了世界顶尖的成形工艺专家对工艺仿真的价值的理解,我们可以从DEFORM自由锻向导式模块来学习和分析自由锻模拟仿真能够带来的价值和意义。
自适应再加热模拟——温度控制不管是坯料的翻转多次锻打(Multi blow forging)或轴拔长的开坯锻造(cogging或swagging),DEFORM都增加了再加热模拟控制,如下图。
Multi blow forging中的自适应再加热cogging中的自适应再加热使用当前功能工艺人员可进行温度控制及自动优化功能,也就是自由锻过程中强调温度的重要性。
我们都知道自由锻过程由于锻打时间长,工件的温度变化也较大,锻打频率不同,温度变化差异也大,因此为了保证锻打过程中,锻件温度需要一直保持高于最低锻造温度(再结晶温度以上),并且低于最高锻造温度(防止粗大晶粒产生),这样才能生产出高质量的锻件。
在模拟过程中如果锻件温度过低,或变形后锻件芯部温度过高,将自动触发加热或与空气传热模拟。
另外,加热多久能够达到我们需要的温度范围内,30分钟?3个小时?比如下面这个例子的停止判据:每个节点温度都在935~975℃之间 ,需要约花费9540秒。
自适应在加热过程工艺流程优化自由锻模拟中,DEFORM向导式模块的第二个界面提供了工艺流程列表的输入,在自由锻复杂的多次锻打过程中如何安排锻打顺序,以及将锻打过程输入给设备的自动化程序,需要一目了然的方式。
基于deform_在金属塑性成形中的应用

基于deform 在金属塑性成形中的应用铜陵学院09材控一班陈军 0910121117摘要:由于deform-3D不具有三维造型功能,所以要实现塑性模拟过程所需要的物理模型均在其他三维软件中建立。
然后利用deform软件所具备的重新划分网格后,原节点的信息不会丢失。
设定变形物体的网格重划分网格标准,有两种选择:一个是绝对值,一个是相对值。
在deform软件的材料库中,各种材料都被分成易于选择的类别。
材料可以通过单位制或加工工艺类型进行检索。
这里主要介绍deform图形文件的生成及其相关功能键使用方法。
正文:一,deform软件的操作流程:(1)、定义几何特征。
Deform中对象的几何数据具有多种格式可供选择。
(2)、网格划分。
Deform网格划分生成四面体单元,这种四面体表面适合于表面成型。
(3)、初始条件。
如轧制时设置变形体、模具与周围介质间的热交换,变形体内部大变形生成热量及其传导都对产品的成形质量造成很大影响,对此问题的仿真模拟分析应按瞬间热-机耦合处理。
Deform软件可提供多种温度下的材料特性。
(4)、材料模型。
这里只研究钢塑性材料。
设定材料变形前,变形时,变形终了的温度和变形率下材料流动应力应变曲线和热膨胀系数、弹性模量、泊松比、热导率等随温度变化的曲线。
(5)、接触定义。
定义变形体与模具之间以及模具之间可能产生的接触关系。
变形的的温度、变形是待求量,变形体为接触体,刚性接触时只具有常温,起主动传递位移或合力作用。
如果需要模具的温度变化,可将模具上要关心的部分离散成单元,定义成允许热传递的刚性接触体,可以与外界催在热交换。
(6)、网格自动重划分。
模拟分析过程中,单元附着在材料上,材料流动中极易造成相应的单元格畸变,单元格畸变后会中断计算过程。
因此保证仿真过程中材料经大量流动后仍然可以继续,获得的结果仍然具有足够的精度。
Deform在网格畸变到一定程度后会自动进行网格重划分,生成搞质量的网格。
DEFORM综述

DEFORM-3D是一套基于工艺模拟系统的有限元系统(FEM),专门设计用于分析各种金属成形过程中的三维 (3D) 流动,提供极有价值的工艺分析数据,有关成形过程中的材料和温度流动。
DEFORM. -3D强大的模拟引擎能够分析金属成形过程中多个关联对象耦合作用的大变形和热特性。
系统中集成了在任何必要时能够自行触发自动网格重划生成器,生成优化的网格系统。
典型的DEFORM-3D应用包括锻造、挤压、镦头、轧制,自由锻、弯曲和其他成形加工手段。
在要求精度较高的区域,可以划分较细密的网格,从而降低题目的规模,并显著提高计算效率。
DEFORM-3D 图形界面,既强大又灵活。
为用户准备输入数据和观察结果数据提供了有效工具。
DEFORM系统简介: DEFORM(Design environment for forming) 是由美国Battelle Columbus 实验室在八十年代早期着手开发的一套有限元分析软件。
早期的DEFORM - 2D 软件只能局限于分析等温变形的平面问题或者轴对称问题。
随着有限元技术的日益成熟,DEFORM 软件也在不断发展完善,目前,DEFORM软件已经能够成功用于分析考虑热力耦和的非等温变形问题和三维变形(DE2FORM- 3D) ,此外,DEFORM软件可视化的操作界面以及强大而完善的网格自动再划分技术,都使DEFORM这一商业化软件在现代工业生产中变得愈来愈实用而可靠。
DEFORM 软件的模块结构: DEFORM- 2D 和DEFORM- 3D 的模块结构基本相同,都由前处理器、模拟处理器和后处理器三大模块组成,不同的是DEFORM - 2D 自身可以制作简易的线框模具,DEFORM - 3D 不具备实体造型能力,但它提供一些通用的CAD 数据接口,如IGES 和STL 接口。
前处理器包括三个子模块(1) 数据输入模块,便于数据的交互式输入,如:初始速度场、温度场、边界条件、冲头行程以及摩擦系数等初始条件。
DEFORM软件简介

• 模拟处理器:DEFORM 运行时,首先通过有限元离散化 将平衡方程、本构关系和边界条件转化为非线形方程组, 然后通过直接迭代法和Newton—Rapson法进行求解,求 解的结果以二进制的形式进行保存,用户可在后处理器中 获取所需要的结果。
• 后处理器:用于显示计算结果,结果可以是图形形式,也 可以是数字、文字混编的形式。可获取的结果可为每一步 的(1)有限元网格;(2)等效应力、等效应变以及破坏程度 的等高线和等色图;(3)速度场;(4)温度场;(5)压力行程 曲线等。此外用户还可以列点进行跟踪,对个别点的轨迹、 应力、应变、破坏程度进行跟踪观察,并可根据需要抽取 数据。
-
• 网格划分 :DEFORM网格划分命令可以生成四面体单元, 这种四面体单元适合于表面成型
• 初始条件:有些加工过程是在变温条件下进行的,比如热 轧,在轧制过程中,工件、模具与环境介质之间存在热交 换,工件内部因大变形生成的热量及其传导都对产品的形 成质量产生重要的影响,对此问题的仿真分析应按瞬态热 -机耦合处理
DEFORM软件简介
DEFORM是一套基于有限元的工艺仿真系统, 用于分析金属成形及其相关工业的各种成形工 艺和热处理工艺。通过在计算机上模拟整个加 工过程,帮助工程师和设计人员: 设计工具和 产品工艺流程,减少昂贵的现场试验成本。 提 高工模具设计效率,降低生产和材料成本。缩 短新产品的研究开发周期。 典型应用于:锻造、机加工、轧制、挤压、冷 镦、拉伸等
-
• 2.5设定对称边界条件
-
-
• 2.6模拟信息的设定控制
-
• 2.9后处理
-
-
-
三点的Z方向应变曲线 -
三点的X方向应变曲线
• 3)对象剖面的选择
- 1、下载文档前请自行甄别文档内容的完整性,平台不提供额外的编辑、内容补充、找答案等附加服务。
- 2、"仅部分预览"的文档,不可在线预览部分如存在完整性等问题,可反馈申请退款(可完整预览的文档不适用该条件!)。
- 3、如文档侵犯您的权益,请联系客服反馈,我们会尽快为您处理(人工客服工作时间:9:00-18:30)。
硬件 平 台 -HPD 3 30
系
统:Wid ws P C SS 2 no H P X
图 1 热处理 工艺示意图
模拟结果
一
低碳钢锥齿轮渗碳后油冷 而后再进行调 质处理。
图2 的云 图清 晰地 表明了经过调 质处理后的锥齿轮 的马 氏 体含量由原来的 8 %下降到现在 的2 %左右 ,其综合机 0 5 械性能和疲劳强度都得到相应 的提升 , 这和 已有的 实际经
的 1 0 s。 3 ki
3 樊东黎 论我 国热处理 生产的技 术改追 . 金属 热处
理 . I 9 ,7 8 ():2 9 8~2 9
4 Koh y s i . hS I Al n r a ah O . t M e a F r i ga h S a tl o m n ndt e Fii lm el eho N e Yo k O x o d Un v r t rs, nt Ee l M t d e f w r : f r i es y P es i
( 提高工模具 设计效率 ,降低生产和材料成本 2)
f 缩短新产 品的研 究开发周期。 J 3
温度、保温时间、冷却速度 3个主要 因素 的有机 配合,使 其发生金属相的转变 , 形成 各种 各样的组织结构 . 而获得 所需要的使用性能的一种热加工工艺 。 为保证机械产 品的质量和使 用寿命 , 通常都要将重要 的机械 零件进 行热 处理 ,例 如机床 制造业 中有 6 0% ~ 7 % 的零件 耍进行 热处理 ,汽车 和拖拉 机制造业 中有 0 7 % ~8 % 的零件 要进行 热处理 ,工模具制 造业中则 0 0 1 0 要进行热处理。而旦 ,只 要选 择的金属材料合适 , 0% 热处理工艺得 当, 就能使机械零件 的使用寿命成倍 、 甚至 十几倍地提高 , 收到事半功倍 的效果。因此 , 热处理是机 械零件和工模具 制造过程 中的关键 工序 , 电是机械工业 的
一
在众 多的模拟软 件中 ,由美 国 S T ( c e t c C S ln… F
F r n e h o ge op rt n) 发的D f r o mi T c n l isC r oa i 研 g o o e om是一
套 基于 有限单元法的工艺仿真软件 系统 , 用于分析金属成 形 及其相关工业的各种成形工 艺和热 处理工 艺。 其中的热 处理 模块 ( e t ra me t 可以模 拟正火、 火、 H a e t n ) T 退 淬火、 回火、渗碳等工艺过程 ,能够 预测硬度、晶粒组织成分 、 扭曲和含碳量 ,并且有 专门的材料模型用于蠕变、相变 、 硬度 和扩散分析 同时可以分析材料晶相 , 以及每种晶相 的弹- 生、塑性、热和硬度属 ’ 生等。 多年 以来 由于热 处理 工艺的复杂性和对此认识的局 限, 使得对于热 处理 的计 算机模拟这一领域的研究一直都 是各国学者和专 家们 所致力的热点和重点。 目前 , e om D fr 对所能进行 分析 的材 料和工艺类型见表 1 其 中绿 色表示 , 此模型功 能已实现,黄色代表该模型 尚处在研 发状态 。
验是完全一致构。
经过无数学者和专家 的努 力, 今天已成为了工厂产品设计 与开发的重要工具。由于我国的工业化起步较 晚, 发展水
平远远低于西 方工业 发达 国家,在材料模型、设备模型 、
数据挖掘等方面 的技 术积 累明显不足 , 技术人 员在发展高
科技 , 工艺的同时也不能放松对材料成形工业 的基础性 新
的最关键 因素。
数值模 拟技术 数值模拟 技术 的出现改变了我们传
艺设计方法 , 通过计 算机 软件技 可以无需试模就能够预测工业实 中的金属流动情况 , 是降低制造
Hale Waihona Puke 维普资讯 专题
报
道
Fa ue e trs
工艺实例
为了更为形象地说 明D f r eo m软件 在金属热处理工艺 设计 中的应用 , 本文 以 齿轮锻 件的热处理工艺设计为例 进行 阐述 ,其渗碳工艺 方案如 图 1 所示 。
研究。
参考文献
1 崔忠沂, 刘北兴编 金属学与热处理原理 哈 尔滨: 尔 哈 滨工业 大学出版社 .19 98 2谭家骏 主编 金属材料厦热处理专业知识解答. 北京
国防 i 业 版 社 . 1 9 97
图3是对锥齿 轮在调质前后其硬度的对 比, 通过计算
机模拟 , 我们可 以清楚地知道通过调质处理 , 齿轮的耐磨 性 得到了提升, 向应 力也从原来的1 0 s降低到处理后 径 6 ki
18 : 9 9 1~ 3 f 7)
Deo m 不仅仅是对应 力应变 以及金属相进 行分析 , f r
气
而且还能够对产品的机械性 能进行 预测 和模拟。图4 就显
示 了经过调质处理后 ,产品 的硬度 变化情况。 结束语
5 顾剑峰 .潘健生等 淬冷过程计算机模拟的若干进
展 金属 热处理 ,19 . 2 0 1 9 8( )3 —3 1
表 1 卜T模块分析 I
项重要基础技 术, 对于提高和控制材 料的性能 . 分发 充
挥材料 的性能潜 力, 节约材料 , 减少能耗并增加产 品的可 靠 ’, 性 延长产品 的使用寿命 , 提高生产单位经济效 益等都 具有十分重要的意义。因此 ,国际 工业
界公认 热处理技术的先进程度是 保证 机械制造技术先进与否和保证产品质嚣
( 设计工具和 产品工艺流程 , 少昂贵 的现场 试验 1j 减
成 本
形与改性的生产方式 , 是从属于材 料和 制造两大工
业领域 的交叉学 科与技术。 中, 其 金属材 料的热处理工艺
是在 固态条件下将金属或合金加热到一定 的温度 . 保持一
定的时间, 然后用 不同的冷却 方法冷却下来。通过对加热
维普资讯
专
题
报
道
F a ur s e t e
Fo M R
理工艺设计 中的应用
国家模具 C D工程研究中心 A 濮伸佳 马月青 董万鹏 胡广洪
全
成本 , 缩短 研发周期高效而 实用 的工具 。 通过在计算机上
模拟整个产品 的加工 过程,帮助工程师和设计人 员:
t
’'
芒
数值模 拟技 术在中国的发展与应用 已有二十 多年 了.
5 8