热轧带钢轧辊破坏原因分析
热轧轧辊剥落或断裂的原因及预防方法探究

热轧轧辊剥落或断裂的原因及预防方法探究热轧轧辊在钢铁生产中起着至关重要的作用,是完成金属板材加工的重要设备之一。
在使用过程中,热轧轧辊剥落或断裂的现象时有发生,给生产带来了严重的影响。
针对这一问题,本文将从热轧轧辊剥落或断裂的原因及预防方法进行探究,以期为相关企业提供参考。
一、热轧轧辊剥落或断裂的原因1. 设备质量不达标热轧轧辊作为重要的设备之一,其质量必须达到相应的标准。
如果生产厂家在生产过程中使用了劣质的材料或者工艺不合格,就会导致轧辊的质量不达标,容易出现剥落或断裂的现象。
2. 设备磨损严重长时间的使用会造成轧辊表面的磨损,特别是在高温、高压力的环境下,磨损会更加严重。
一旦轧辊表面磨损过度,就会影响其正常的工作状态,进而产生剥落或断裂的风险。
3. 工艺参数设置不当热轧轧辊在使用过程中,需要根据所加工金属的性质和厚度等因素设置相应的工艺参数,如温度、压力等。
如果工艺参数设置不当,就会导致轧辊在工作过程中承受过大的压力或温度,从而容易出现剥落或断裂的情况。
4. 操作不当操作人员在使用热轧轧辊的过程中,如果操作不当,容易对设备造成损坏。
比如在装卸轧辊时使用不当的工具或方法,会导致轧辊受力不均,从而产生损坏的可能性。
5. 周期性检修不足热轧轧辊作为重要设备,需要定期进行检修和维护工作。
如果企业在这方面投入不足,就会导致轧辊出现各种问题,包括剥落或断裂现象。
二、预防方法探究1. 选购正规厂家生产的轧辊企业在选购热轧轧辊时,应该选择质量可靠的正规厂家生产的产品,避免使用劣质轧辊。
2. 定期维护检修企业应该对热轧轧辊进行定期的维护检修工作,包括表面磨损的修复、工艺参数的调整和润滑等工作,以确保轧辊处于最佳的工作状态。
3. 合理设置工艺参数在使用热轧轧辊时,企业应该合理设置工艺参数,根据加工的金属材料性质和厚度等因素进行调整,避免出现过大的压力或温度对轧辊造成损坏。
4. 加强操作培训企业应该加强对操作人员的培训,提高其对热轧轧辊设备的操作技能和安全意识,避免因为操作不当对轧辊造成损坏。
轧辊破坏常见原因分析及对策
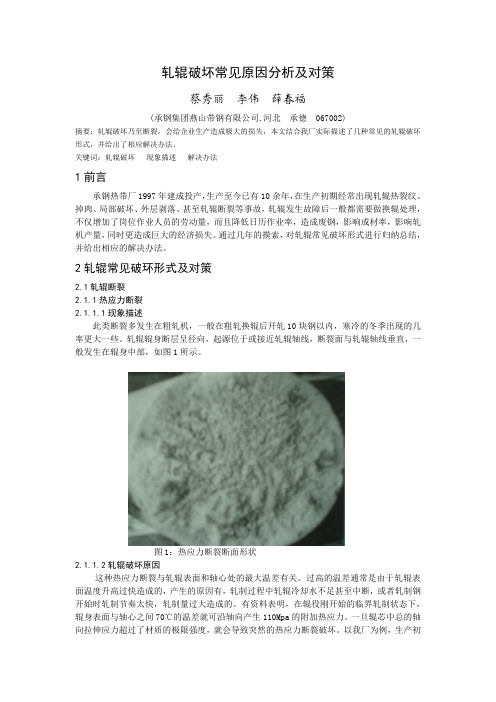
轧辊破坏常见原因分析及对策蔡秀丽李伟薛春福(承钢集团燕山带钢有限公司,河北承德 067002)摘要:轧辊破坏乃至断裂,会给企业生产造成极大的损失,本文结合我厂实际描述了几种常见的轧辊破坏形式,并给出了相应解决办法。
关键词:轧辊破坏现象描述解决办法1前言承钢热带厂1997年建成投产,生产至今已有10余年,在生产初期经常出现轧辊热裂纹、掉肉、局部破坏、外层剥落、甚至轧辊断裂等事故,轧辊发生故障后一般都需要做换辊处理,不仅增加了岗位作业人员的劳动量,而且降低日历作业率,造成废钢,影响成材率,影响轧机产量,同时更造成巨大的经济损失。
通过几年的摸索,对轧辊常见破坏形式进行归纳总结,并给出相应的解决办法。
2轧辊常见破环形式及对策2.1轧辊断裂2.1.1热应力断裂2.1.1.1现象描述此类断裂多发生在粗轧机,一般在粗轧换辊后开轧10块钢以内,寒冷的冬季出现的几率更大一些。
轧辊辊身断层呈径向,起源位于或接近轧辊轴线,断裂面与轧辊轴线垂直,一般发生在辊身中部,如图1所示。
图1:热应力断裂断面形状2.1.1.2轧辊破坏原因这种热应力断裂与轧辊表面和轴心处的最大温差有关。
过高的温差通常是由于轧辊表面温度升高过快造成的,产生的原因有,轧制过程中轧辊冷却水不足甚至中断,或者轧制钢开始时轧制节奏太快,轧制量过大造成的。
有资料表明,在辊役刚开始的临界轧制状态下,辊身表面与轴心之间70℃的温差就可沿轴向产生110Mpa的附加热应力。
一旦辊芯中总的轴向拉伸应力超过了材质的极限强度,就会导致突然的热应力断裂破坏。
以我厂为例,生产初期,有一次正值寒冬腊月,室外温度-20℃,厂房内温度较低,备辊正处在风口上,轧辊上线前没有预热,仅烫辊4块,在烫辊效果不好的前提下,温度较低的冷却水很快浇凉辊面,在轧制中与红钢接触,轧辊处于冷热交替中,内外表面温差大。
断辊后约10分钟,用手摸断辊边缘,触觉为凉辊,带钢轧制部位的轧辊表面微温,轧辊断口内触觉发凉。
热轧轧辊剥落或断裂的原因及预防方法探究

热轧轧辊剥落或断裂的原因及预防方法探究热轧轧辊作为热轧设备中重要的组成部分,其质量直接影响到产品质量和生产效率。
在生产中,往往会出现轧辊剥落或断裂的情况,造成了生产效率低下和安全隐患,因此研究热轧轧辊剥落或断裂的原因及预防方法具有重要的实际意义。
1. 轧辊表面损伤导致轧辊剥落或断裂在轧辊使用过程中,出现轧辊表面损伤容易导致轧辊剥落或断裂。
这种损伤包括表面裂纹、划痕、磨损、腐蚀等,这些损伤会进一步扩大,最终导致轧辊剥落或断裂。
轧辊材质好坏直接影响到轧辊的使用寿命和质量。
如果轧辊的材质不够坚固耐用,那么在热轧过程中会出现轧辊变形、疲劳、裂纹等问题,将极大影响热轧产品质量。
热轧设备的操作不规范也容易导致轧辊剥落或断裂。
例如温度控制不当、轧辊调整不到位等等,都会在热轧过程中产生不同程度的影响,最终导致轧辊剥落或断裂。
热轧工艺参数是热轧过程中必须严格控制的参数,如果热轧工艺参数不合适将会直接影响到轧辊的寿命和使用效果。
例如,轧制过程中的拉伸率、轧制力、速度等参数不合适,都将导致轧辊剥落或断裂。
1. 轧辊材质的优化优化轧辊材质可以提高轧辊的抗拉、抗压、抗疲劳等性能。
特别是在硬度和韧性之间的平衡上,选择合适的轧辊材料可大大提高轧辊的使用寿命。
2. 加强对轧辊的检测热轧轧辊在使用过程中应每隔一些周期对轧辊进行检测,及时发现轧辊损伤和裂纹等问题并进行处理,避免因轧辊的损坏而影响到生产和产品质量。
3. 热轧设备的维护针对热轧设备操作不规范等问题,应加强设备维护,保持轧辊的良好状态。
定期做好轧辊的维护与更新,及时清理轧辊附着的物质,避免附着物进一步侵蚀轧辊表面。
4. 控制热轧工艺参数对于热轧工艺参数不合适问题,应严格控制热轧温度、轧制力、速度等参数。
调整工艺参数能够有效避免轧辊的剥落或断裂。
总之,对于热轧轧辊剥落或断裂问题,合理地选择轧辊材质,加强轧辊的检测和维护,规范热轧设备操作,严格控制热轧工艺参数,是预防轧辊剥落或断裂的有效方法。
热轧轧辊剥落或断裂的原因及预防方法探究
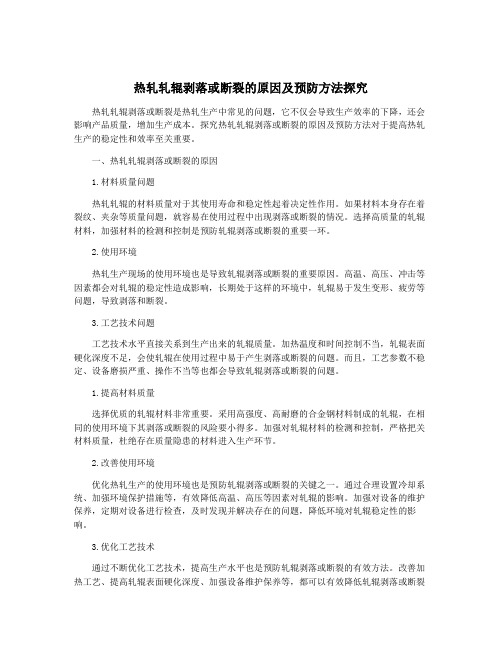
热轧轧辊剥落或断裂的原因及预防方法探究热轧轧辊剥落或断裂是热轧生产中常见的问题,它不仅会导致生产效率的下降,还会影响产品质量,增加生产成本。
探究热轧轧辊剥落或断裂的原因及预防方法对于提高热轧生产的稳定性和效率至关重要。
一、热轧轧辊剥落或断裂的原因1.材料质量问题热轧轧辊的材料质量对于其使用寿命和稳定性起着决定性作用。
如果材料本身存在着裂纹、夹杂等质量问题,就容易在使用过程中出现剥落或断裂的情况。
选择高质量的轧辊材料,加强材料的检测和控制是预防轧辊剥落或断裂的重要一环。
2.使用环境热轧生产现场的使用环境也是导致轧辊剥落或断裂的重要原因。
高温、高压、冲击等因素都会对轧辊的稳定性造成影响,长期处于这样的环境中,轧辊易于发生变形、疲劳等问题,导致剥落和断裂。
3.工艺技术问题工艺技术水平直接关系到生产出来的轧辊质量。
加热温度和时间控制不当,轧辊表面硬化深度不足,会使轧辊在使用过程中易于产生剥落或断裂的问题。
而且,工艺参数不稳定、设备磨损严重、操作不当等也都会导致轧辊剥落或断裂的问题。
1.提高材料质量选择优质的轧辊材料非常重要。
采用高强度、高耐磨的合金钢材料制成的轧辊,在相同的使用环境下其剥落或断裂的风险要小得多。
加强对轧辊材料的检测和控制,严格把关材料质量,杜绝存在质量隐患的材料进入生产环节。
2.改善使用环境优化热轧生产的使用环境也是预防轧辊剥落或断裂的关键之一。
通过合理设置冷却系统、加强环境保护措施等,有效降低高温、高压等因素对轧辊的影响。
加强对设备的维护保养,定期对设备进行检查,及时发现并解决存在的问题,降低环境对轧辊稳定性的影响。
3.优化工艺技术通过不断优化工艺技术,提高生产水平也是预防轧辊剥落或断裂的有效方法。
改善加热工艺、提高轧辊表面硬化深度、加强设备维护保养等,都可以有效降低轧辊剥落或断裂的风险。
培训操作人员,提高其技术水平,增强操作规范性,也是有效预防轧辊剥落或断裂的方法之一。
4.加强监控和管理加强对生产过程的监控和管理,及时发现并处理存在的问题也是预防轧辊剥落或断裂的关键。
轧辊失效方式及其原因分析

轧辊失效方式及其原因分析轧机在轧制生产过程中,轧辊处于复杂的应力状态。
热轧机轧辊的工作环境更为恶劣:轧辊与轧件接触加热、轧辊水冷引起的周期性热应力,轧制负荷引起的接触应力、剪切应力以及残余应力等。
如轧辊的选材、设计、制作工艺等不合理,或轧制时卡钢等造成局部发热引起热冲击等,都易使轧辊失效。
轧辊失效主要有剥落、断裂、裂纹等形式。
任何一种失效形式都会直接导致轧辊使用寿命缩短。
因此有必要结合轧辊的失效形式,探究其产生的原因,找出延长轧辊使用寿命的有效途径。
1 、轧辊剥落(掉肉)轧辊剥落为首要的损坏形式,现场调查亦表明,剥落是轧辊损坏,甚至早期报废的主要原因。
轧制中局部过载和升温,使带钢焊合在轧辊表面,产生于次表层的裂纹沿径向扩展进入硬化层并多方向分枝扩展,该裂纹在逆向轧制条件下即造成剥落。
1.1 支撑辊辊面剥落支撑辊剥落大多位于轧辊两端,沿圆周方向扩展,在宽度上呈块状或大块片状剥落,剥落坑表面较平整。
支撑辊和工作辊接触可看作两平行圆柱体的接触,在纯滚动情况下,接触处的接触应力为三向压应力。
在离接触表面深度为 0.786b 处 ( b 为接触面宽度之半 ) 剪切应力最大,随着表层摩擦力的增大而移向表层。
疲劳裂纹并不是发生在剪应力最大处,而是更接近于表面,即在 Z 为 0.5b 的交变剪应力层处。
该处剪应力平行于轧辊表面,据剪应力互等定理,与表面垂直的方向同样存在大小相等的剪应力。
此力随轧辊的转动而发生大小和方向的改变,是造成接触疲劳的根源。
周期交变的剪切应力是轧辊损坏最常见的致因。
在交变剪切应力作用下,反复变形使材料局部弱化,达到疲劳极限时,出现裂纹。
另外,轧辊制造工艺造成的材质不均匀和微型缺陷的存在,亦有助于裂纹的产生。
若表面冷硬层厚度不均,芯部强度过低,过渡区组织性能变化太大,在接触应力的作用下,疲劳裂纹就可能在硬化过渡层起源并沿表面向平行方向扩展,而形成表层压碎剥落。
支撑辊剥落只是位于辊身边部两端,而非沿辊身全长,这是由支撑辊的磨损型式决定的。
热轧带钢精轧辊破坏原因分析
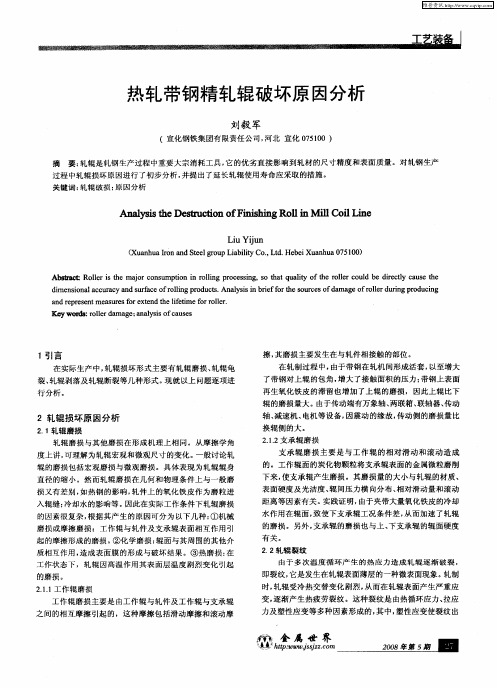
入辊缝 : 冷却水 的影 响等 。 因此在实际工 作条件下 轧辊磨损 的因素很复杂 , 根据 其产 生的原因可分为 以下几种 : ①机械
磨 损 或 摩 擦 磨 损 :工 作 辊 与轧 件及 支 承 辊 表 面 相 互 作 用 引
距离等因素有关。 实践证 明, 由于夹带大量氧化铁皮的冷却 水作用在辊面, 致使 下支 承辊工况条件差, 从而加速 了轧辊 的磨损 。另外 , 支承辊的磨损也与上、 支承辊 的辊面硬度 下
Luvi n i j u
( a h aI na dSe l ru iblyCo, d He e a h a0 5 0 ) Xu n u o n te o pLa it .Lt. b i r g i Xu n u 7 1 0
A s atR lr stema r o smpini ol gpoes g S a q ai f erl r o l edrcycuete bt c ol j nu t rln rc s n , Ot t ul o l udb i t a s r : ei h oc o n i i h y t h t oec el h
d me s n l c u a y a d s ra eo r l n r d c An l s r f o es u c s f a g f o lrd r gp o u i g i n i a c r c n f c f o l gp o u m. ay i i b i f rt o r e d ma e o r l u n r d cn o a u i sn e h o e i a dr p e e t a u e r x e d t el ei o l r n rsn e me s r s o t n f t f e h i mef r o l . r e
热轧轧辊剥落或断裂的原因及预防方法探究
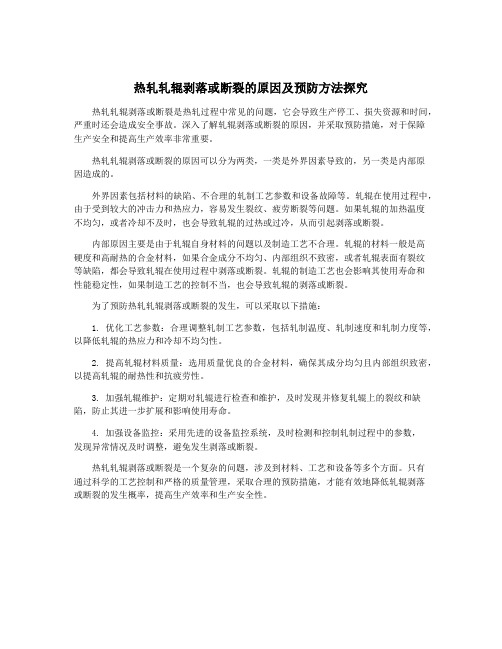
热轧轧辊剥落或断裂的原因及预防方法探究热轧轧辊剥落或断裂是热轧过程中常见的问题,它会导致生产停工、损失资源和时间,严重时还会造成安全事故。
深入了解轧辊剥落或断裂的原因,并采取预防措施,对于保障生产安全和提高生产效率非常重要。
热轧轧辊剥落或断裂的原因可以分为两类,一类是外界因素导致的,另一类是内部原因造成的。
外界因素包括材料的缺陷、不合理的轧制工艺参数和设备故障等。
轧辊在使用过程中,由于受到较大的冲击力和热应力,容易发生裂纹、疲劳断裂等问题。
如果轧辊的加热温度不均匀,或者冷却不及时,也会导致轧辊的过热或过冷,从而引起剥落或断裂。
内部原因主要是由于轧辊自身材料的问题以及制造工艺不合理。
轧辊的材料一般是高硬度和高耐热的合金材料,如果合金成分不均匀、内部组织不致密,或者轧辊表面有裂纹等缺陷,都会导致轧辊在使用过程中剥落或断裂。
轧辊的制造工艺也会影响其使用寿命和性能稳定性,如果制造工艺的控制不当,也会导致轧辊的剥落或断裂。
为了预防热轧轧辊剥落或断裂的发生,可以采取以下措施:1. 优化工艺参数:合理调整轧制工艺参数,包括轧制温度、轧制速度和轧制力度等,以降低轧辊的热应力和冷却不均匀性。
2. 提高轧辊材料质量:选用质量优良的合金材料,确保其成分均匀且内部组织致密,以提高轧辊的耐热性和抗疲劳性。
3. 加强轧辊维护:定期对轧辊进行检查和维护,及时发现并修复轧辊上的裂纹和缺陷,防止其进一步扩展和影响使用寿命。
4. 加强设备监控:采用先进的设备监控系统,及时检测和控制轧制过程中的参数,发现异常情况及时调整,避免发生剥落或断裂。
热轧轧辊剥落或断裂是一个复杂的问题,涉及到材料、工艺和设备等多个方面。
只有通过科学的工艺控制和严格的质量管理,采取合理的预防措施,才能有效地降低轧辊剥落或断裂的发生概率,提高生产效率和生产安全性。
热轧轧辊的失效原因及科学预防

热轧轧辊的失效原因及科学预防摘要轧辊的失效形式主要包括剥落、断裂、裂纹等,无论哪种失效都会影响轧辊的使用寿命。
因此,为延长轧辊使用寿命、降低轧辊消耗,必须要针对不同的失效原因,采取科学性、针对性的预防措施。
基于此,本文对轧辊失效的原因进行了阐述,并分析了科学的预防措施,旨在为提高轧辊的使用寿命,提升轧辊质量,提供参考借鉴。
关键词轧辊失效;应力;剥落;裂纹;预防1 轧辊常见失效形式及原因1.1 剥落剥落的发生不是瞬间的,而是需要一个疲劳的过程,轧辊的非正常失效形式中剥落占比达60%~70%,属于较为严重的生产事故,严重时会导致轧辊报废。
其主要形式及原因为:首先,马鞍形剥落。
在对薄而硬的带钢进行轧制时,由于压下比大,使得在承受较大负荷的作用下而产生交变应力、残留应力及热应力,会使拉应力变大,一旦超过轧辊芯部材质的疲劳极限,就会导致出现微裂纹。
裂纹的进一步蔓延,就会表现在辊身表面,致使产生马鞍形剥落。
其次,带状疲劳剥落。
轧辊局部过大超负荷运转时,当大于轧辊外层的抗剪切强度极限时,就会出现裂纹,在进行轧制过程中,持续的疲劳状态会引发裂纹的增多,致使辊身局部出现大面积剥落。
另外,对于服役期较长的工作辊和支承辊,中间磨损量大于两端磨损量,致使辊身两端交变剪应力不断增大,加速了疲劳破坏,从而产生带状疲劳剥落。
另外,表层/芯部结合层处脱落。
在发生轧制事故时,局部出现过大负荷,导致外部与芯部材质出现脱落,随着这一分割面的逐渐延伸,一旦达到临界尺寸,就会出现二次脱落。
这种形式的剥落出现通常有以下几种情况,表层和芯部间有氧化层残留,结合层留有杂质、碳化物或是气孔等。
1.2 断裂轧制过程中的断辊事故时有发生,断裂通常发生在辊身、辊颈及轴头部位。
当钢种以及生产工艺存在差异時,断裂的部位也会出现差异。
通常,断辊是由于疲劳裂纹所致,也可能会出现一次性脆断,具体分析如下:(1)内因在轧辊的材质内部存在缺陷时,引发轧辊断裂的可能性也会增大,例如,钢材球化率低、渗碳体数量过高、局部晶粒不均匀以及结构疏松等缺陷,非正常情况下的芯部组织致使机械性能降低,在承受的热应力大于材料抗拉强度时,轧辊内部的材质出现局部裂纹,裂纹逐步蔓延最终导致轧辊断裂。
热轧轧辊剥落或断裂的原因及预防方法探究
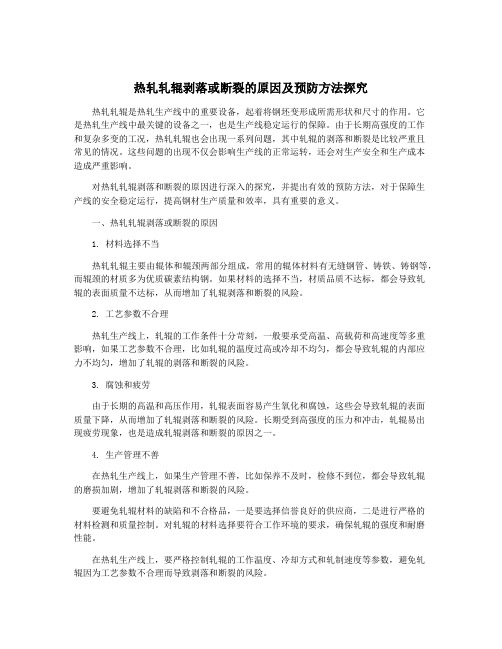
热轧轧辊剥落或断裂的原因及预防方法探究热轧轧辊是热轧生产线中的重要设备,起着将钢坯变形成所需形状和尺寸的作用。
它是热轧生产线中最关键的设备之一,也是生产线稳定运行的保障。
由于长期高强度的工作和复杂多变的工况,热轧轧辊也会出现一系列问题,其中轧辊的剥落和断裂是比较严重且常见的情况。
这些问题的出现不仅会影响生产线的正常运转,还会对生产安全和生产成本造成严重影响。
对热轧轧辊剥落和断裂的原因进行深入的探究,并提出有效的预防方法,对于保障生产线的安全稳定运行,提高钢材生产质量和效率,具有重要的意义。
一、热轧轧辊剥落或断裂的原因1. 材料选择不当热轧轧辊主要由辊体和辊颈两部分组成,常用的辊体材料有无缝钢管、铸铁、铸钢等,而辊颈的材质多为优质碳素结构钢。
如果材料的选择不当,材质品质不达标,都会导致轧辊的表面质量不达标,从而增加了轧辊剥落和断裂的风险。
2. 工艺参数不合理热轧生产线上,轧辊的工作条件十分苛刻,一般要承受高温、高载荷和高速度等多重影响,如果工艺参数不合理,比如轧辊的温度过高或冷却不均匀,都会导致轧辊的内部应力不均匀,增加了轧辊的剥落和断裂的风险。
3. 腐蚀和疲劳由于长期的高温和高压作用,轧辊表面容易产生氧化和腐蚀,这些会导致轧辊的表面质量下降,从而增加了轧辊剥落和断裂的风险。
长期受到高强度的压力和冲击,轧辊易出现疲劳现象,也是造成轧辊剥落和断裂的原因之一。
4. 生产管理不善在热轧生产线上,如果生产管理不善,比如保养不及时,检修不到位,都会导致轧辊的磨损加剧,增加了轧辊剥落和断裂的风险。
要避免轧辊材料的缺陷和不合格品,一是要选择信誉良好的供应商,二是进行严格的材料检测和质量控制。
对轧辊的材料选择要符合工作环境的要求,确保轧辊的强度和耐磨性能。
在热轧生产线上,要严格控制轧辊的工作温度、冷却方式和轧制速度等参数,避免轧辊因为工艺参数不合理而导致剥落和断裂的风险。
要对轧辊的表面进行防腐处理,避免氧化和腐蚀的发生;并对轧辊进行定期的疲劳检测和预防性维护,延长轧辊的使用寿命。
热轧轧辊剥落或断裂的原因及预防方法探究
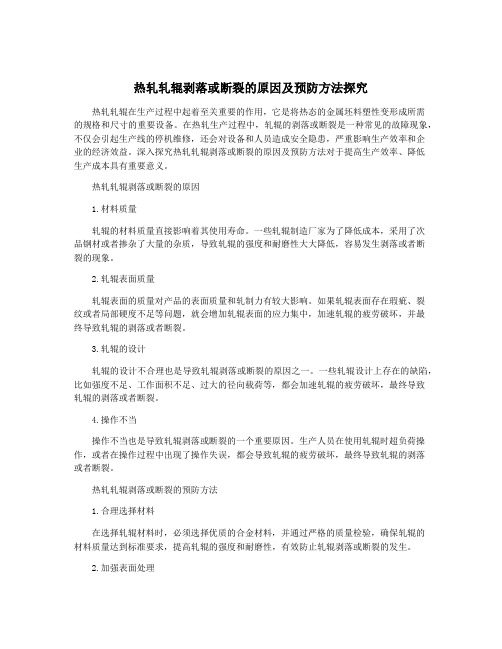
热轧轧辊剥落或断裂的原因及预防方法探究热轧轧辊在生产过程中起着至关重要的作用,它是将热态的金属坯料塑性变形成所需的规格和尺寸的重要设备。
在热轧生产过程中,轧辊的剥落或断裂是一种常见的故障现象,不仅会引起生产线的停机维修,还会对设备和人员造成安全隐患,严重影响生产效率和企业的经济效益。
深入探究热轧轧辊剥落或断裂的原因及预防方法对于提高生产效率、降低生产成本具有重要意义。
热轧轧辊剥落或断裂的原因1.材料质量轧辊的材料质量直接影响着其使用寿命。
一些轧辊制造厂家为了降低成本,采用了次品钢材或者掺杂了大量的杂质,导致轧辊的强度和耐磨性大大降低,容易发生剥落或者断裂的现象。
2.轧辊表面质量轧辊表面的质量对产品的表面质量和轧制力有较大影响。
如果轧辊表面存在瑕疵、裂纹或者局部硬度不足等问题,就会增加轧辊表面的应力集中,加速轧辊的疲劳破坏,并最终导致轧辊的剥落或者断裂。
3.轧辊的设计轧辊的设计不合理也是导致轧辊剥落或断裂的原因之一。
一些轧辊设计上存在的缺陷,比如强度不足、工作面积不足、过大的径向载荷等,都会加速轧辊的疲劳破坏,最终导致轧辊的剥落或者断裂。
4.操作不当操作不当也是导致轧辊剥落或断裂的一个重要原因。
生产人员在使用轧辊时超负荷操作,或者在操作过程中出现了操作失误,都会导致轧辊的疲劳破坏,最终导致轧辊的剥落或者断裂。
热轧轧辊剥落或断裂的预防方法1.合理选择材料在选择轧辊材料时,必须选择优质的合金材料,并通过严格的质量检验,确保轧辊的材料质量达到标准要求,提高轧辊的强度和耐磨性,有效防止轧辊剥落或断裂的发生。
2.加强表面处理对轧辊表面进行加强处理,提高轧辊的表面质量和强度,有效减少轧辊表面的裂纹和瑕疵,降低轧辊的疲劳破坏,延长轧辊的使用寿命,减少剥落或断裂的发生。
3.改善轧辊设计改善轧辊的设计,提高轧辊的强度和刚性,增加轧辊工作面积,合理分配径向载荷,减小轧辊的应力集中,降低轧辊的疲劳损伤,有效预防轧辊剥落或断裂。
轧辊破坏常见原因分析及对策

轧辊破坏常见原因分析及对策蔡秀丽李伟薛春福(承钢集团燕山带钢有限公司,河北承德 067002)摘要:轧辊破坏乃至断裂,会给企业生产造成极大的损失,本文结合我厂实际描述了几种常见的轧辊破坏形式,并给出了相应解决办法。
关键词:轧辊破坏现象描述解决办法1前言承钢热带厂1997年建成投产,生产至今已有10余年,在生产初期经常出现轧辊热裂纹、掉肉、局部破坏、外层剥落、甚至轧辊断裂等事故,轧辊发生故障后一般都需要做换辊处理,不仅增加了岗位作业人员的劳动量,而且降低日历作业率,造成废钢,影响成材率,影响轧机产量,同时更造成巨大的经济损失。
通过几年的摸索,对轧辊常见破坏形式进行归纳总结,并给出相应的解决办法。
2轧辊常见破环形式及对策2.1轧辊断裂2.1.1热应力断裂2.1.1.1现象描述此类断裂多发生在粗轧机,一般在粗轧换辊后开轧10块钢以内,寒冷的冬季出现的几率更大一些。
轧辊辊身断层呈径向,起源位于或接近轧辊轴线,断裂面与轧辊轴线垂直,一般发生在辊身中部,如图1所示。
图1:热应力断裂断面形状2.1.1.2轧辊破坏原因这种热应力断裂与轧辊表面和轴心处的最大温差有关。
过高的温差通常是由于轧辊表面温度升高过快造成的,产生的原因有,轧制过程中轧辊冷却水不足甚至中断,或者轧制钢开始时轧制节奏太快,轧制量过大造成的。
有资料表明,在辊役刚开始的临界轧制状态下,辊身表面与轴心之间70℃的温差就可沿轴向产生110Mpa的附加热应力。
一旦辊芯中总的轴向拉伸应力超过了材质的极限强度,就会导致突然的热应力断裂破坏。
以我厂为例,生产初期,有一次正值寒冬腊月,室外温度-20℃,厂房内温度较低,备辊正处在风口上,轧辊上线前没有预热,仅烫辊4块,在烫辊效果不好的前提下,温度较低的冷却水很快浇凉辊面,在轧制中与红钢接触,轧辊处于冷热交替中,内外表面温差大。
断辊后约10分钟,用手摸断辊边缘,触觉为凉辊,带钢轧制部位的轧辊表面微温,轧辊断口内触觉发凉。
热轧轧辊剥落或断裂的原因及预防方法探究

热轧轧辊剥落或断裂的原因及预防方法探究【摘要】热轧轧辊剥落或断裂是热轧生产中常见的问题,严重影响生产效率和产品质量。
本文从热轧轧辊剥落或断裂现象引起注意和研究目的和意义两个方面展开,然后深入探讨了造成这一问题的原因,包括金属材料的质量问题、外部环境因素和工艺参数设置不当等。
针对这些原因,提出了一些有效的预防方法,如加强材料检验、保持良好的生产环境和合理设置工艺参数。
在研究成果总结和未来研究展望两个方面进行总结,指出今后需要深入研究轧辊剥落或断裂的原因及预防方法,以提高热轧生产的效率和质量。
通过本文的研究,有望为解决热轧轧辊剥落或断裂问题提供一定的参考和借鉴。
【关键词】热轧轧辊、剥落、断裂、金属材料、质量问题、外部环境、工艺参数、预防方法、研究成果、展望。
1. 引言1.1 热轧轧辊剥落或断裂现象引起注意热轧轧辊剥落或断裂是热轧生产中常见的问题,一旦发生会给生产带来严重的影响。
轧辊是热轧生产中不可或缺的重要设备之一,承担着对金属带材进行塑性加工的重要任务。
由于受到多种因素的影响,轧辊往往会出现剥落或断裂的现象,如果不及时处理和预防,将导致生产事故的发生,影响生产效率和产品质量。
热轧轧辊剥落或断裂现象需要引起注意,因为其主要危害包括:一是轧辊剥落或断裂会导致生产线停机,给企业带来直接的经济损失;二是剥落或断裂的轧辊会造成产品表面质量不达标,影响产品的销售和企业的声誉;三是轧辊剥落或断裂会增加生产中的安全隐患,可能导致事故发生,影响员工的生命安全。
对热轧轧辊剥落或断裂现象引起足够的重视,研究其发生的原因以及预防方法,对于提高生产效率、保证产品质量和保障人员安全具有重要意义。
本文旨在探究热轧轧辊剥落或断裂的原因及预防方法,为热轧生产提供一定的参考和指导。
1.2 研究目的和意义研究的目的在于深入探究热轧轧辊剥落或断裂的原因,分析其中可能存在的金属材料质量问题、外部环境因素以及工艺参数设置不当等方面的因素。
通过研究分析,可以为预防热轧轧辊剥落或断裂提供理论依据和技术支持,提高轧辊的使用寿命和生产效率。
热轧轧辊剥落或断裂的原因及预防方法探究

热轧轧辊剥落或断裂的原因及预防方法探究热轧轧辊在钢铁生产中扮演着非常重要的角色,它直接影响到板材的成型质量和生产效率。
在实际生产中,经常会发生热轧轧辊剥落或断裂的情况,给生产带来严重的影响。
探究热轧轧辊剥落或断裂的原因及预防方法对于提高生产效率,降低生产成本具有非常重要的意义。
一、热轧轧辊剥落或断裂的原因1. 轧辊质量问题热轧轧辊的质量直接关系到其使用寿命和稳定性。
如果轧辊材料的硬度和强度不达标,就容易在生产过程中发生剥落或断裂的问题。
如果轧辊的表面光洁度不够,也容易导致板材表面出现瑕疵,甚至剥落。
2. 过热或过冷的板坯温度在热轧生产过程中,如果板坯的温度不稳定,容易导致热轧轧辊受到过大的冲击力,从而加速其磨损和断裂的过程。
特别是过冷的板坯容易导致轧辊的温度骤然下降,从而造成轧辊的变形和断裂。
3. 辊缝调整不当热轧轧辊的辊缝调整不当也是导致剥落或断裂的重要原因之一。
如果辊缝太小,就容易造成辊缝夹板,从而导致轧辊的断裂;如果辊缝太大,就会导致轧辊的挤压能力下降,磨损加剧,最终也会导致轧辊的剥落或断裂。
4. 轧辊表面磨损随着生产的不断进行,轧辊表面会发生磨损,磨损过多会导致轧辊的表面粗糙,从而造成板材表面质量的下降。
轧辊表面的磨损也会加速轧辊的断裂。
5. 运行参数不合理一些运行参数不合理也是导致热轧轧辊剥落或断裂的原因之一。
轧辊的进给速度过快,就容易导致轧辊受到过大的冲击力,从而加速其磨损和断裂;轧辊的冷却水量不足,也会导致轧辊温度过高,从而破坏轧辊的结构。
1. 选择优质的轧辊材料为了防止热轧轧辊的剥落或断裂,首先要选择优质的轧辊材料。
要选择具有高硬度和高强度的轧辊材料,以及表面光洁度好、抗磨损性能好的轧辊材料。
2. 严格控制板坯温度在热轧生产过程中,要严格控制板坯的温度,确保其稳定在适宜的温度范围内。
尤其是在板坯的预热和送入轧机的过程中,要确保板坯温度的稳定性。
为了防止轧辊的剥落或断裂,辊缝的调整非常重要。
浅析南钢带钢四辊轧机轴承损坏原因及改进

浅析南钢带钢四辊轧机轴承损坏原因及改进南钢热轧带钢四辊轧机轴承损坏的主要原因是它们在工作中所受的径向及轴向载荷过大造成。
工作辊与支承辊轴线的不平行引起其接触面的轴向相对滑动,由此产生较大的轴向滑动摩擦力,轧件在轧制过程中偏离轧制中心线,造成各列轴承径向载荷不均匀,往往会发生某一列轴承径向载荷超载,从而导致整列轴承损坏。
因此要研究四辊轧机轴承的受力分析、轧机机架的稳定性等方面,对轴承进行改型、机架进行修复提高设备精度,来提高轧机轴承寿命,减少异常损坏。
标签:四辊轧机;径向力;轴向力;轴承失效;改进南钢带钢厂精轧四辊轧机共6架,每台轧机工作辊轴承采用2097938四列圆锥滚子轴承,支承辊轴承采用6890250四列短圆柱轴承和1060深沟球止推轴承组合。
持续对生产现场轧制规格及钢种以及机械、液压系统传动稳定性跟踪,持续对轧辊轴承寿命跟踪统计分析,持续对每一支烧损的轴承进行解体检查分析,发现工作辊2097938轴承损坏主要发生在靠近轧机操作侧轧辊辊径侧的这一列轴承先损坏造成整列轴承损坏,支承辊6890250轴承主要是四列短圆柱轴承外圈及滚动体碎裂。
1 轧辊轴承损坏原因分析1.1 工作辊2097938轴承损坏原因分析持续对每一支烧损的轴承进行解体检查分析,结合烧损轴承寿命跟踪统计以及轧制的钢种及规格,以及轧机设备、液压系统运行稳定性分析,发现工作辊2097938轴承烧损的主要发生在是轧机操作侧固定端某一列轴承,而传动侧自由端轴承烧损很少发生,而且从烧损现象上看轴承润滑良好,但是轴承外圈和保持架断裂,部分损坏的轴承滚动体断裂。
图1所示为四辊轧机工作辊与支承辊的受力分析简图,从受力情况分析来看,带钢产品在轧制过程中,轧件的变形抗力主要是通过工作辊向支承辊传递,轧制轴向力主要是轧件与工作辊间之间的摩擦力向工作辊传递。
也就是说工作辊2097938轴承在轧制过程中受到轧制轴向力较多,而支承辊6890250轴承在轧制过程中受到轧制径向力较多。
热轧带钢轧辊破坏原因分析

热轧带钢轧辊破坏原因分析轧辊包括工作辊和支承辊,是轧机的关键零件之一,装在轧机牌坊窗口当中。
在热轧带钢生产中,轧辊的消耗量很大,尤其是工作辊,它始终与红热钢坯直接接触。
因此,找出轧辊的损坏原因并做出相应的解决措施,提高轧辊寿命,降低辊耗,是轧机制造商和用户都十分关注的问题。
在实际生产过程中,轧辊的破坏形式主要有轧辊磨损、轧辊裂纹、轧辊剥落及轧辊断裂等。
轧辊磨损轧辊磨损与其他磨损在形成机理上相同。
从摩擦学角度来讲,可理解为轧辊宏观和微观尺寸的变化。
一般讨论的轧辊磨损,包括宏观磨损和微观磨损,具体表现为轧辊直径的缩小。
然而,轧辊磨损在几何和物理条件上与一般磨损又有差别,如轧辊上的某点与轧件周期性接触;轧件上的氧化铁皮作为磨粒进入辊缝;冷却液和润滑液的作用以及热的影响等。
因此,在实际工作条件下轧辊磨损的因素很复杂,根据其产生的原因可分为以下几种:(1)机械磨损或摩擦磨损。
工作辊与轧件及支撑辊表面相互作用引起的摩擦形成的磨损。
(2)化学磨损。
辊面与周围其他介质相互作用,造成表面膜的形成与破坏的结果。
(3)热磨损。
在工作状态下,轧辊因高温作用其表面层温度剧烈变化引起的磨损。
1 工作辊磨损工作辊磨损主要是由工作辊与轧件及工作辊与支撑辊之间的相互摩擦引起的,这种摩擦包括滑动摩擦和滚动摩擦,其磨损主要发生在与轧件相接触的部位。
在生产过程中,由于带钢在轧机间形成活套,以致增大了带钢对上辊的包角,增加了接触面积的压力;带钢上表面再生氧化铁皮的滞留也增加了上辊的磨损,因此,上辊比下辊的磨损量大。
由于传动端与电机连接,因振动之故,传动侧的磨损量比换辊侧的大。
2 支承辊磨损支撑辊磨损主要是与工作辊的相对滑动和滚动造成的。
工作辊表面的炭化物颗粒将支撑辊表面的金属微粒磨削下来,使支撑辊产生磨损。
其磨损量的大小与轧辊的材质、表面硬度及光洁度、辊间压力横向分布、相对滑动量和滚动距离等因素有关。
实践证明,由于夹带大量氧化铁皮的冷却水作用在辊面,致使下支撑辊工况条件差,从而加速了轧辊的磨损。
热轧轧辊剥落或断裂的原因及预防方法探究
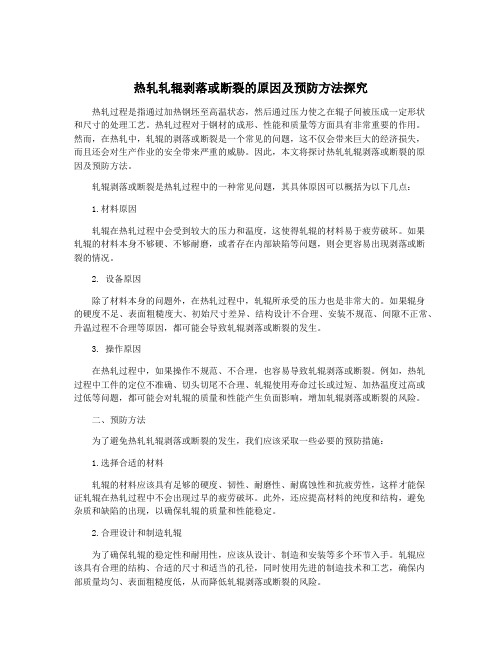
热轧轧辊剥落或断裂的原因及预防方法探究热轧过程是指通过加热钢坯至高温状态,然后通过压力使之在辊子间被压成一定形状和尺寸的处理工艺。
热轧过程对于钢材的成形、性能和质量等方面具有非常重要的作用。
然而,在热轧中,轧辊的剥落或断裂是一个常见的问题,这不仅会带来巨大的经济损失,而且还会对生产作业的安全带来严重的威胁。
因此,本文将探讨热轧轧辊剥落或断裂的原因及预防方法。
轧辊剥落或断裂是热轧过程中的一种常见问题,其具体原因可以概括为以下几点:1.材料原因轧辊在热轧过程中会受到较大的压力和温度,这使得轧辊的材料易于疲劳破坏。
如果轧辊的材料本身不够硬、不够耐磨,或者存在内部缺陷等问题,则会更容易出现剥落或断裂的情况。
2. 设备原因除了材料本身的问题外,在热轧过程中,轧辊所承受的压力也是非常大的。
如果辊身的硬度不足、表面粗糙度大、初始尺寸差异、结构设计不合理、安装不规范、间隙不正常、升温过程不合理等原因,都可能会导致轧辊剥落或断裂的发生。
3. 操作原因在热轧过程中,如果操作不规范、不合理,也容易导致轧辊剥落或断裂。
例如,热轧过程中工件的定位不准确、切头切尾不合理、轧辊使用寿命过长或过短、加热温度过高或过低等问题,都可能会对轧辊的质量和性能产生负面影响,增加轧辊剥落或断裂的风险。
二、预防方法为了避免热轧轧辊剥落或断裂的发生,我们应该采取一些必要的预防措施:1.选择合适的材料轧辊的材料应该具有足够的硬度、韧性、耐磨性、耐腐蚀性和抗疲劳性,这样才能保证轧辊在热轧过程中不会出现过早的疲劳破坏。
此外,还应提高材料的纯度和结构,避免杂质和缺陷的出现,以确保轧辊的质量和性能稳定。
2.合理设计和制造轧辊为了确保轧辊的稳定性和耐用性,应该从设计、制造和安装等多个环节入手。
轧辊应该具有合理的结构、合适的尺寸和适当的孔径,同时使用先进的制造技术和工艺,确保内部质量均匀、表面粗糙度低,从而降低轧辊剥落或断裂的风险。
3.规范操作和维护在热轧过程中,必须确保操作规范严谨。
轧辊失效的原因及防治措施

轧辑失效的原因及防治措施轧辐的损坏形式多种多样,典型形式及失效原因如下:1、轧辑磨损分三类:机械磨损是由轧辐表面与轧件摩擦引起的;热磨损是由高温作用使其表层软化、熔化或蒸发引起的;腐蚀磨损是由轧辐表面水分的化学作用、电化学作用、氧化作用等引起表面材料损失和迁移。
2、轧辐裂纹轧制中发生堆钢、卡钢、追尾等事故,致使其局部温度急剧升高,产生的热应力和组织应力超过极限,形成热裂纹;轧制延伸形成舌头,其温度低于中部轧件,会产生热应力以及轧制应力突变,形成冲击裂纹;轧制中,由于氧化铁皮叠轧,导卫划痕等原因也会形成裂纹。
3、轧辐剥落裂纹的形成和扩展加快,到达一定长度和深度后,会导致剥落。
4、轧辑断裂1)辐轴铸造缺陷轧辐离心铸造中,因离心震动产生成分和组织层状偏析,形成裂纹迅速扩展,造成轧辐断裂。
2)轧辐组织缺陷化学成分不合格、冷却速度不当会导致成分偏析、渗碳体过高等缺陷,只是机械性能下降,最终导致断裂。
3)加工工艺轧辐在锻造时压力过小或变形不合理造成轧辐芯部未锻透,形成穿晶裂纹。
其防治措施为:1、轧辐选用耐磨又抗热裂纹的材质,采取相应的热处理及物流化学处理措施,使组织均化,表面耐磨性增加。
2、轧辑在上轧机前进行硬度、超声波等综合检验,确保其无裂纹等缺陷。
3、轧辐车削时,将残留氧化层及裂纹彻底清除,以减少轧辐表面裂纹及剥落产生。
4、合理安排换辐周期,选配轧辐,制定详细的轧辐车修方案,将车修量控制在要求范围内。
5、合理布置冷却水喷射范围和控制冷却水量,确保轧辐冷却温度控制在正常范围内。
6、加强设备点检,预防轧钢设备事故,减少导致卡钢、堆钢、追尾等事故发生。
严格控制轧制温度,杜绝低温钢通过轧机,避免轧制力过载。
轧辊破坏常见原因分析及对策.doc

CL0501-轧辊破坏常见原因分析及对策案例简要说明:依据国家职业标准和金属材料及热处理技术、材料成型与控制技术专业教学要求,归纳提炼出所包含的知识和技能点,弱化与教学目标无关的内容,使之与课程学习目标、学习内容一致,成为一个承载了教学目标所要求知识和技能的教学案例。
该案例是轧钢设备使用与维护事故案例,体现了轧辊材质及其力学性能等知识点和轧钢工、设备点检工的岗位操作技能,与本专业轧钢机械设备课程中轧辊部分、金属材料与热处理课程中金属材料的性能部分单元的教学目标对应。
轧辊破坏常见原因分析及对策天津冶金职业技术学院王磊该案例发生在承钢热带厂,该厂自1997年建成投产,生产至今已有10多年,在生产初期经常出现轧辊热裂纹、掉肉、局部破坏、外层剥落、甚至轧辊断裂等事故,轧辊发生故障后一般都需要做换辊处理,不仅增加了岗位作业人员的劳动量,而且降低日历作业率,造成废钢,影响成材率,影响轧机产量,同时更造成巨大的经济损失。
通过几年的摸索,对轧辊常见破坏形式进行归纳总结,并给出相应的解决办法。
该案例在教学过程中辅以图片等多媒体资源对学生进行讲解,让学生能够更好地掌握轧制过程中如何更好地延长轧辊的寿命。
1.背景介绍某厂自1997年建成投产,生产至今已有10多年,在生产初期经常出现轧辊热裂纹、掉肉、局部破坏、外层剥落、甚至轧辊断裂等事故,轧辊发生故障后一般都需要做换辊处理,不仅增加了岗位作业人员的劳动量,而且降低日历作业率,造成废钢,影响成材率,影响轧机产量,同时更造成巨大的经济损失。
通过几年的摸索,对轧辊常见破坏形式进行归纳总结,并给出相应的解决办法。
2.主要内容2.1.热应力断裂一、现象描述此类断裂多发生在粗轧机,一般在粗轧换辊后开轧10块钢以内,寒冷的冬季出现的几率更大一些。
轧辊辊身断层呈径向,起源位于或接近轧辊轴线,断裂面与轧辊轴线垂直,一般发生在辊身中部,如图1所示。
图1 热应力断裂断面形状二、轧辊破坏原因这种热应力断裂与轧辊表面和轴心处的最大温差有关。
粗轧辊断裂原因分析
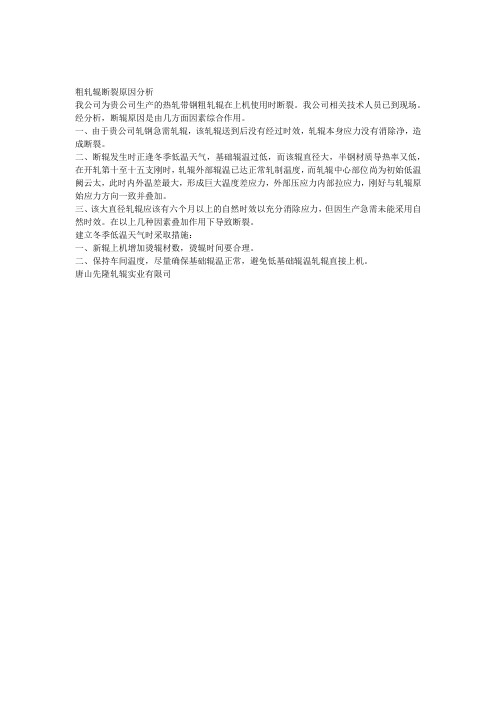
粗轧辊断裂原因分析
我公司为贵公司生产的热轧带钢粗轧辊在上机使用时断裂。
我公司相关技术人员已到现场。
经分析,断辊原因是由几方面因素综合作用。
一、由于贵公司轧钢急需轧辊,该轧辊送到后没有经过时效,轧辊本身应力没有消除净,造成断裂。
二、断辊发生时正逢冬季低温天气,基础辊温过低,而该辊直径大,半钢材质导热率又低,在开轧第十至十五支刚时,轧辊外部辊温已达正常轧制温度,而轧辊中心部位尚为初始低温阙云太,此时内外温差最大,形成巨大温度差应力,外部压应力内部拉应力,刚好与轧辊原始应力方向一致并叠加。
三、该大直径轧辊应该有六个月以上的自然时效以充分消除应力,但因生产急需未能采用自然时效。
在以上几种因素叠加作用下导致断裂。
建立冬季低温天气时采取措施:
一、新辊上机增加烫辊材数,烫辊时间要合理。
二、保持车间温度,尽量确保基础辊温正常,避免低基础辊温轧辊直接上机。
唐山先隆轧辊实业有限司。
热轧轧辊剥落或断裂的原因及预防方法探究
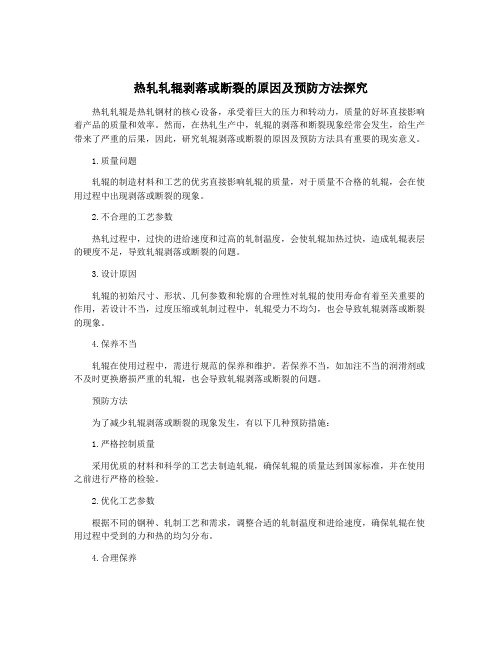
热轧轧辊剥落或断裂的原因及预防方法探究热轧轧辊是热轧钢材的核心设备,承受着巨大的压力和转动力,质量的好坏直接影响着产品的质量和效率。
然而,在热轧生产中,轧辊的剥落和断裂现象经常会发生,给生产带来了严重的后果,因此,研究轧辊剥落或断裂的原因及预防方法具有重要的现实意义。
1.质量问题轧辊的制造材料和工艺的优劣直接影响轧辊的质量,对于质量不合格的轧辊,会在使用过程中出现剥落或断裂的现象。
2.不合理的工艺参数热轧过程中,过快的进给速度和过高的轧制温度,会使轧辊加热过快,造成轧辊表层的硬度不足,导致轧辊剥落或断裂的问题。
3.设计原因轧辊的初始尺寸、形状、几何参数和轮廓的合理性对轧辊的使用寿命有着至关重要的作用,若设计不当,过度压缩或轧制过程中,轧辊受力不均匀,也会导致轧辊剥落或断裂的现象。
4.保养不当轧辊在使用过程中,需进行规范的保养和维护。
若保养不当,如加注不当的润滑剂或不及时更换磨损严重的轧辊,也会导致轧辊剥落或断裂的问题。
预防方法为了减少轧辊剥落或断裂的现象发生,有以下几种预防措施:1.严格控制质量采用优质的材料和科学的工艺去制造轧辊,确保轧辊的质量达到国家标准,并在使用之前进行严格的检验。
2.优化工艺参数根据不同的钢种、轧制工艺和需求,调整合适的轧制温度和进给速度,确保轧辊在使用过程中受到的力和热的均匀分布。
4.合理保养轧辊在使用过程中,应定期进行润滑和维护,并根据实际情况进行轧辊更换和修理,以保证轧辊使用寿命的延长。
总之,热轧轧辊的剥落或断裂问题的解决需要多方面的努力,除了以上预防措施之外,还需要提高工作人员的素质,严格执行操作规程,保证生产环境安全、清洁、整洁,以及进行适当的科技创新和技术改进,以确保轧辊质量及生产效率的提高。
- 1、下载文档前请自行甄别文档内容的完整性,平台不提供额外的编辑、内容补充、找答案等附加服务。
- 2、"仅部分预览"的文档,不可在线预览部分如存在完整性等问题,可反馈申请退款(可完整预览的文档不适用该条件!)。
- 3、如文档侵犯您的权益,请联系客服反馈,我们会尽快为您处理(人工客服工作时间:9:00-18:30)。
热轧带钢轧辊破坏原因分析
轧辊包括工作辊和支承辊,是轧机的关键零件之一,装在轧机牌坊窗口当中。
在热轧带钢生产中,轧辊的消耗量很大,尤其是工作辊,它始终与红热钢坯直接接触。
因此,找出轧辊的损坏原因并做出相应的解决措施,提高轧辊寿命,降低辊耗,是轧机制造商和用户都十分关注的问题。
在实际生产过程中,轧辊的破坏形式主要有轧辊磨损、轧辊裂纹、轧辊剥落及轧辊断裂等。
轧辊磨损
轧辊磨损与其他磨损在形成机理上相同。
从摩擦学角度来讲,可理解为轧辊宏观和微观尺寸的变化。
一般讨论的轧辊磨损,包括宏观磨损和微观磨损,具体表现为轧辊直径的缩小。
然而,轧辊磨损在几何和物理条件上与一般磨损又有差别,如轧辊上的某点与轧件周期性接触;轧件上的氧化铁皮作为磨粒进入辊缝;冷却液和润滑液的作用以及热的影响等。
因此,在实际工作条件下轧辊磨损的因素很复杂,根据其产生的原因可分为以下几种:
(1)机械磨损或摩擦磨损。
工作辊与轧件及支撑辊表面相互作用引起的摩擦形成的磨损。
(2)化学磨损。
辊面与周围其他介质相互作用,造成表面膜的形成与破坏的结果。
(3)热磨损。
在工作状态下,轧辊因高温作用其表面层温度剧烈变化引起的磨损。
1 工作辊磨损
工作辊磨损主要是由工作辊与轧件及工作辊与支撑辊之间的相互摩擦引起的,这种摩擦包括滑动摩擦和滚动摩擦,其磨损主要发生在与轧件相接触的部位。
在生产过程中,由于带钢在轧机间形成活套,以致增大了带钢对上辊的包角,增加了接触面积的压力;带钢上表面再生氧化铁皮的滞留也增加了上辊的磨损,因此,上辊比下辊的磨损量大。
由于传动端与电机连接,因振动之故,传动侧的磨损量比换辊侧的大。
2 支承辊磨损
支撑辊磨损主要是与工作辊的相对滑动和滚动造成的。
工作辊表面的炭化物颗粒将支撑辊表面的金属微粒磨削下来,使支撑辊产生磨损。
其磨损量的大小与轧辊的材质、表面硬度及光洁度、辊间压力横向分布、相对滑动量和滚动距离等因素有关。
实践证明,由于夹带大量氧化铁皮的冷却水作用在辊面,致使下支撑辊工况条件差,从而加速了轧辊的磨损。
另外,支承辊的磨损也与上、下支撑辊的辊面硬度有关。
轧辊裂纹
由于多次温度循环产生的热应力造成轧辊逐渐破裂,即裂纹,它是发生在轧辊表面薄层的一种微表面现象。
轧制时,轧辊受冷热交替变化剧烈,从而在轧辊表面产生严重应变,逐
渐产生热疲劳裂纹。
这种裂纹是由热循环应力、拉应力及塑性应变等多种因素形成的,其中,塑性应变使裂纹出现,拉应力使其扩展。
轧辊剥落
轧辊剥落通常是由显微裂纹引起的轧辊破坏,热轧带钢的支撑辊和工作辊由于力学因素、工作条件及服役周期不同,其剥落方式及轻重也不同。
1 工作辊剥落
热轧工作辊剥落是由接触疲劳造成的,生产中出现的剥落多数为辊面裂纹所致。
工作辊与支撑辊接触,产生接触应力及相应的交变剪应力,通常工作辊服役约8小时就下机进行磨削,因此不易产生疲劳裂纹。
由于支撑辊与工作辊接触宽度不足20mm,即使在冷却水的作用下,支承辊也无明显的温差,工作辊则不然。
当工作辊与高温带钢接触时,其辊面温度可升高到500~600℃;当其接触到冷却水时,工作辊的温度又迅速降到100~15 0℃以下。
这种周期性的加热和冷却使工作辊辊面产生了变化的温度场,因而产生了明显的周期应力,当热应力超过材料的疲劳极限时,轧辊表面便产生细小的网状热裂纹,即龟裂。
另外,在轧制过程中,当带钢出现甩尾,叠轧时,轧件将划伤轧辊,这样就形成了新的裂纹源。
轧辊表面的龟裂、表层裂纹等,在工作应力、残余应力和冷却作用下引起的氧化,使裂纹尖端的应力急剧增加并超过材料的允许应力而向轧辊内部扩展。
当裂纹发展成与辊面呈一定的角度甚至沿着辊面平行的方向扩展时,就造成了剥落。
2 支撑辊剥落
支撑辊剥落主要是由距辊面一定深度的交变剪切应力造成的,其剥落部位主要发生在支撑辊两端。
支撑辊由于服役周期较长,普遍存在磨损量大,磨损严重且不均匀等现象。
由于支撑辊的中间磨损量大,两端磨损量小,所以辊身两端产生局部的接触应力尖峰,造成两端交变剪应力的增大,因而加快了疲劳破坏。
同时辊身中部的剪应力点,在轧辊磨损的推动作用下,逐渐往辊身内部移动至少0.5mm,不易形成疲劳裂纹;而轧辊边部的最大剪应力点,由于该边部磨损较少,基本保持不变,故其在交变应力的反复作用下,局部材料弱化,出现裂纹。
在轧制过程中,辊面以下为接触疲劳引起的裂纹源,由于尖端存在应力集中现象,因而自尖端开始沿辊面垂直方向向辊面扩展,或与辊面成小角度以致呈平行的方向扩展,两者相互作用,随着裂纹扩展,最终造成剥落。
轧辊断裂
轧辊断裂的因素很多,其中包括本身的因素,即辊身内部存在大量裂纹及轧辊组织缺陷和轧辊的铸造缺陷。
在生产过程中,如辊身内部存在大量裂纹,则该裂纹尖端产生应力集中而快速扩展并连接形成一个较大的裂纹,这种裂纹在交变应力的作用下,由内向外逐渐扩大,当裂纹扩大到一定程度时就会发生断裂;轧辊组织缺陷和轧辊的铸造缺陷也都会造成断辊。
轧辊设计所受的局限性及设计的不合理也会造成轧辊断裂,由此引起的断裂主要发生在轧辊的辊颈或辊颈与辊身的过渡处。
辊颈直径受轧辊轴承径向尺寸的影响,辊颈直径比辊身直径小得多;在辊颈与辊身的连接处,由于直径突然变化,以致当轧辊受载时产生明显的应力集中现象。
在轧制过程中,过大的轧制力会使工作辊辊颈从根部和辊颈受力处断裂。
因此,在工作辊设计过程中,应尽量加大轧辊的辊颈直径及辊颈和辊身的过渡圆角,同时,一定要校核工作辊辊颈所能承受的扭转力矩。
提高轧辊使用寿命的相应措施
(1)热轧辊长期在700~800℃环境中工作,与热钢坯直接接触,承受强大的轧制力,同时表面还要承受轧材的强力磨损,且反复被热轧材加热和冷却水冷却,经受温度变化较大的热疲劳作用。
因此,要求热辊轧材具有淬透性高,热膨胀系数低,热传导能力高和高的高温屈服强度及抗氧化性高等特点。
(2)出现裂纹的轧辊应及时更换进行磨削,保证其适度的磨削量,以消除残余裂纹。
(3)为减小或者消除内应力,工作辊在使用一个周期后要进行一次消除应力退火,或将磨削后的轧辊浸入具有一定温度的油剂中保存。
(4)合理的轧辊辊型配置,均匀辊间接触应力,保持适量均匀的磨损,利用磨损的推动作用以有效消除轧辊剥落。
(5)从轧制工艺方面出发。
要确保冷却水的正常投入,在使用过程中必须加强对轧辊冷却喷嘴的管理,保证喷嘴和过滤网不堵塞,水量足够,确保轧辊的温度控制在正常范围之内;在热轧带钢生产中还可应用轧制润滑技术,实践证明,轧制润滑可以减少轧辊的磨损,降低轧制力及轧制扭矩,缓解轧辊的热疲劳,改善轧制时的应力状态;应用在线磨辊技术和工作辊横移以降低轧辊磨损,延长带钢的轧制公里数,减少换辊次数。
轧辊的破坏是由多种因素相互作用和相互影响引起的,它的损坏形式多种多样。
虽然在实际工作中轧辊破损还不能完全避免,但我们可以针对具体的损坏形式,提出相应的解决办法;还可根据轧辊的使用环境来考虑轧辊的选材,保证轧辊可以经受温度变化较大的热疲劳作用;也可以通过合理安排换辊周期、合理布置冷却水和轧制润滑等工艺手段及应用在线磨辊技术减少轧辊的磨损。