挤压工艺与模具设计..
第五章冷挤压工艺及模具设计
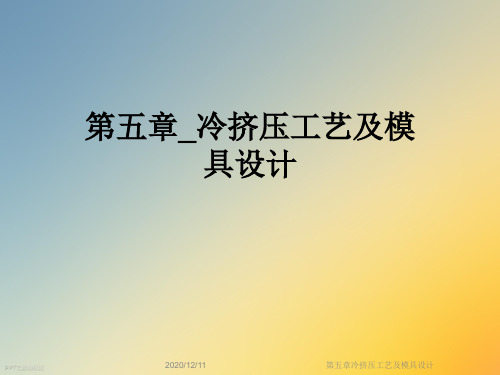
PPT文档演模板
2020/12/11
第五章冷挤压工艺及模具设计
冷挤压工艺及模具设计
•5.1 冷挤压工艺
•5.2 冷挤压模具设计 • •5.3 冷挤压模的典型结构
PPT文档演模板
第五章冷挤压工艺及模具设计
冷挤压工艺及模具设计
•5.1 冷挤压工艺
• 冷挤压是一种先进的少无切削加工工艺之一。它是在 常温下,使固态的金属在巨大压力和一定的速度下,通过模 腔产生塑性变形而获得一定形状零件的一种加工方法。冷挤 压的工艺过程是:先将经处理过的毛坯料放在凹模内,借助 凸模的压力使金属处于三向受压应力状态下产生塑性变形, 通过凹模的下通孔或凸模与凹模的环形间隙将金属挤出。它 是一种在许多行业广泛使用的金属压力加工工艺方法。
• (3) 冷挤压的变形方式 在变形程度相同的条件下, 反挤压的力大于正挤压的力。反挤压的许用变形程度比正挤 压小。
PPT文档演模板
第五章冷挤压工艺及模具设计
冷挤压工艺及模具设计
• (4) 毛坯表面处理与润滑 毛坯表面处理越好,润滑 越好,许用变形程度也就越大。
• (5) 冷挤压模具的几何形状 冷挤压模具工作部分的 几何形状对金属的流动有很大影响。形状合理时,有利于挤 压时的金属流动,单位挤压力降低,许用变形程度可以大些。
第五章冷挤压工艺及模具设计
冷挤压工艺及模具设计
•5.1.4.2 许用变形程度
• 冷挤压时,一次挤压加工所容许的变形程度,称为许 用变形程度。不同材料有不同的许用变形程度。在工艺上, 每道冷挤压工序的变形程度应尽量小于许用值,使模具承受 的单位挤压力不超过模具材料许用应力(目前一般模具材料 的许用应力为2500~3000N/mm2),确定许用变形程度数值 是冷挤压工艺计算的一个重要依据,因为冷挤压许用变形程 度的大小决定了制件所需的挤压次数。若计算出的冷挤压变 形程度超过许用值、则必须用多次挤压完成,以延长模具寿 命,避免损坏模具。
《冷冲压工艺与模具设计》第6章冷挤压工艺与模具设计

6.3.1 冷挤压的应力与应变状态
/webnew/
6.3.2 冷挤压的变形程度
/webnew/
6.3.2 冷挤压的变形程度
2. 冷挤压的极限变形程度 极限变形程度是指冷挤压时,在模具强度允许的条件下一次挤压所能达
(4) 冷挤压时材料在冷态下发生塑性变形,应选用组织致密和杂质少的材料,避免加工过程过多的 中间退火;冷挤压件一般都不进行精加工,所以必须选用精度高的坯料;在冷挤压加工前,毛坯常进行 软化退火和表面磷化等润滑处理。
(5) 冷挤压的适用范围广,既可挤压塑性良好的铜、铝等材料,又可挤压采用锻造等方法较难加工 的一些金属(因金属处于强烈的三向压应力状态,能充分提高金属坯料的塑性);既可以生产截面形状简 单的管、棒等型材,又可生产截面极其复杂的或具有深孔、薄壁以及变截面的零件。
/webnew/
第6章 冷挤压工艺与模具设计简介
案例导入: 下列各图所示零件的工作负荷很大,要求有极高的强度和韧
性,用切削工艺加工会将材料中的纤维组织切断,对材料的 强度和韧性有一定的影响,而且材料利用率较低,改用冷冲 压工艺加工,可以直接制造出高精度的零件或切削量很小的 零件毛坯,在材料的内部还能形成更高强度的纤维组织,大 大提高材料的综合性能,而且能够最大限度地节约原材料和 能源。冷冲压加工是一种少切削或无切削而使金属成形的塑 性加工工艺。
(1) 在冷态下挤压成形,挤压件质量好,精度高,表面粗糙度值小,一般尺寸精度可以达到 IT8~IT9,表面粗糙度可达Ra3.2~0.4μm;冷挤压后材料产生冷作硬化,零件内部的纤维组织连续, 基本沿零件外形分布而不被切断,零件的强度远高于原材料的强度;合理的冷挤压工艺还可使零件表面 形成压应力,从而提高疲劳强度;但冷挤压零件的塑性、冲击韧性变差,而且零件的残余应力大,容易 引起零件变形和耐腐蚀性的降低(产生应力腐蚀)。
挤压工艺及模具课程设计

挤压工艺及模具课程设计一、课程目标知识目标:1. 学生能够理解挤压工艺的基本概念,掌握金属挤压的基本原理;2. 学生能够描述挤压模具的构成、分类及工作原理;3. 学生能够掌握影响挤压工艺的主要因素,如材料性能、挤压温度、挤压速度等;4. 学生能够了解挤压工艺在实际生产中的应用及发展趋势。
技能目标:1. 学生能够运用所学知识,分析并解决挤压工艺中的实际问题;2. 学生能够设计简单的挤压模具,并进行初步的模具分析与优化;3. 学生能够运用计算机辅助设计软件(如CAD)进行挤压模具的设计与仿真。
情感态度价值观目标:1. 学生通过学习挤压工艺及模具课程,培养对制造业的兴趣和热情;2. 学生能够认识到挤压工艺在现代化生产中的重要性,增强对制造业的责任感和使命感;3. 学生在学习过程中,培养团队合作意识,提高沟通与表达能力。
分析课程性质、学生特点和教学要求:1. 课程性质:本课程为机械制造及自动化专业的一门专业课程,具有实践性和应用性;2. 学生特点:学生为高职或中职院校机械制造及自动化专业二年级学生,具备一定的机械基础知识;3. 教学要求:注重理论与实践相结合,强调实际操作能力的培养,提高学生的综合素质。
二、教学内容1. 挤压工艺基本概念与原理- 金属挤压的基本概念与分类- 挤压工艺的优缺点分析- 挤压工艺的基本原理及过程2. 挤压模具设计与分析- 挤压模具的构成与分类- 挤压模具的设计原则与方法- 模具分析与优化- 计算机辅助设计软件在模具设计中的应用3. 影响挤压工艺的因素- 材料性能对挤压工艺的影响- 挤压温度、挤压速度等工艺参数对挤压质量的影响- 挤压润滑对挤压工艺的影响4. 挤压工艺在实际生产中的应用- 挤压工艺在各类产品中的应用实例- 挤压工艺在制造业中的发展趋势- 新型挤压工艺及模具技术的探讨5. 实践教学环节- 挤压模具设计与制作实践- 挤压工艺操作实践- 案例分析与讨论教学大纲安排:第一周:挤压工艺基本概念与原理第二周:挤压模具设计与分析第三周:影响挤压工艺的因素第四周:挤压工艺在实际生产中的应用第五周:实践教学环节(挤压模具设计与制作实践、挤压工艺操作实践、案例分析)教学内容根据课程目标,结合教材章节进行组织,注重理论与实践相结合,旨在培养学生的实际操作能力和创新能力。
挤压工艺与模具设计

挤压工艺及模具设计Extrusion Technology and Mould Design一、挤压工艺分类挤压可分为以下三类:1)冷挤压,又称冷锻,一般指在回复温度以下(室温)的挤压。
2)温挤压,一般指坯料在金属再结晶温度以下、回复温度以上进行的挤压。
对于黑色金属,以600℃为界,划分为低温挤压和高温挤压。
3)热挤压,指坯料在金属再结晶温度以上进行的挤压。
1)冷挤压工艺冷挤压是在冷态下,将金属毛坯放入模具模腔内,在强大的压力和一定的速度作用下,迫使金属从模腔中挤出,从而获得所需形状、尺寸以及一定力学性能的挤压件。
冷挤压与热锻、粉末冶金、铸造及切削加工相比,具有以下主要优点:1)因在冷态下挤压成形,挤压件质量好、精度高、其强度性能也好;2)冷挤压属于少、无切削加工,节省原材料;3)冷挤压是利用模具来成形的,其生产效率很高;4)可以加工其它工艺难于加工的零件。
2)温挤压工艺温挤压成形技术是近年来在冷挤压塑性成形基础上发展起来的一种少无切削新工艺,又称温热挤压。
它与冷、热挤压不同,挤压前已对毛坯进行加热,但其加热温度通常认为是在室温以上、再结晶温度以下的温度范围内。
对温挤压的温度范围目前还没有一个严格的规定。
有时把变温前将毛坯加热,变形后具有冷作硬化的变形,称为温变形。
或者,将加热温度低于热锻终锻温度的变形,称为温变形。
从金属学观点来看,区分冷、热加工可根据金属塑性变形后有无加工硬化现象存在来决定似乎更合理些。
在金属塑性变形后存在加工硬化现象这个过程称为冷变形及温变形。
3)热挤压工艺热挤压是几种挤压工艺中最早采用的挤压成形技术,它是在热锻温度时借助于材料塑性好的特点,对金属进行各种挤压成形。
目前,热挤压主要用于制造普通等截面的长形件、型材、管材、棒料及各种机器零件等。
热挤压不仅可以成形塑性好,强度相对较低的有色金属及其合金,低、中碳钢等,而且还可以成形强度较高的高碳、高合金钢,如结构用特殊钢、不锈钢、高速工具钢和耐热钢等。
铝挤压工艺与模具设计考核试卷

7.下列哪种方法可以降低铝挤压过程中的摩擦力?()
A.提高挤压速度
B.降低挤压温度
C.增加润滑剂用量
D.减小挤压比
8.铝挤压模具在使用过程中,以下哪种磨损形式最为常见?()
A.粘着磨损
B.磨粒磨损
C.氧化磨损
D.腐蚀磨损
9.下列哪个因素会影响铝材的挤压变形程度?()
A.挤压比
A.提高模具的表面光洁度
B.适当降低挤压速度
C.增加挤压过程中的润滑
D.提高挤压温度
4.铝挤压过程中可能导致铝材内部出现裂纹的因素有哪些?()
A.挤压温度过低
B.挤压速度过快
C.挤压比过大
D.模具设计不合理
5.以下哪些措施可以减少铝挤压模具的磨损?()
A.提高模具的预热温度
B.增加挤压过程中的润滑剂用量
( )
2.铝挤压模具设计时,应考虑哪些关键因素以确保模具的性能和使用寿命?
( )
3.描述铝挤压过程中可能出现的常见缺陷,并分析这些缺陷产生的原因。
( )
4.针对一种特定的铝材,设计一个铝挤压工艺流程,包括挤压温度、挤压速度、润滑剂的选择等关键参数的设定,并解释这些参数选择的原因。
( )
标准答案
一、单项选择题
A.模具材料
B.模具结构
C.冷却水的流速
D.模具的表面光洁度
13.下列哪种铝材不适合采用直接挤压工艺?()
A.纯铝
B.铝合金6061
C.铝合金7075
D.铝合金2024
14.在铝挤压过程中,以下哪种现象可能导致铝材表面出现波纹?()
A.模具光洁度低
B.挤压速度过快
C.润滑剂用量不足
课程设计(论文)-铝合金型材挤压工艺及模具计算
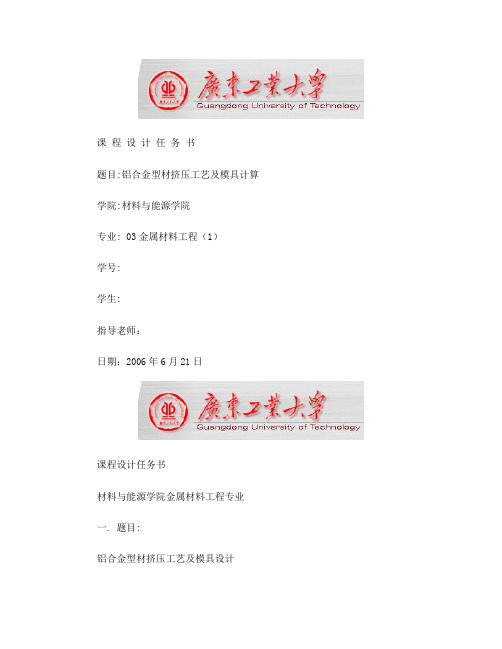
课程设计任务书题目:铝合金型材挤压工艺及模具计算学院:材料与能源学院专业: 03金属材料工程(1)学号:学生:指导老师:日期:2006年6月21日课程设计任务书材料与能源学院金属材料工程专业一. 题目:铝合金型材挤压工艺及模具设计二. 设计基本内容:设计一件实心型材制品和一件空心型材制品的工艺工艺过程及模具设计,包括挤压工艺参数,模具结构,制造工艺等要求三. 完成后应缴的资料:课程设计说明书一份实心型材模AUTOCAD图空心型材模上模AUTOCAD图空心型材模下模AUTOCAD图空心型材模上下模AUTOCAD装配图四. 设计完成期限:2005年6月14日------2005年6月24日指导老师_袁鸽成签发日期___________教研室主任_______批准日期___________课程设计评语:成绩:设计指导教师______________年_____月____日目录一: 绪论 (5)二: 总设计过程概论 (8)三: 实心型材模设计 (10)四: 空心型材模设计 (19)五: 后记 (28)一绪论铝被誉为仅次于钢铁的第二大金属,由于具有密度低、强度适中、加工性能好等一系列优点,被广泛应用于建筑、包装、交通运输等行业,铝及铝材的消费已经成为一个国家工业发展水平的重要标志。
近年来工业铝型材应用于交通行业呈上升趋势。
铝合金在国民经济中起着非常重要的作用。
随着科学技术的进步和现代经济的高速发展,铝合金型材正向着大型整体化、薄壁扁宽化、尺寸高精化、形状复杂化、外廓美观化的方向发展,品种规格不断增多,应用范围不断拓展,已由民用建筑门窗型材为主体推广到了航天航空、汽车船舶、交通运输、电子电力、石油化工、机械制造、家用电器等各行各业和人民生活各个方面。
据不完全统计,目前世界上每年需要的大型铝合金型材约4o万吨,而且增涨势头不减。
为了适应这种市场需求趋势,各国都在加速建设重型挤压机或大型材挤压生产线。
近年来,随着科技的进步和经济的发展,特别是交通运输的现代化、高速化和轻量化,需要大量的大型特种型材。
挤压铸造工艺的模拟与模具设计

挤压铸造工艺的模拟与模具设计铸造工艺一直是金属制造领域中的重要环节之一。
而其中的挤压铸造工艺,同样在不同行业中发挥着重要的作用。
挤压铸造工艺通过将熔融金属材料以高压注入模具中,利用其充填模具的特性,实现金属制品的快速制造。
然而,想要实现高质量的挤压铸造产品,必须进行模拟与模具设计,以确保制造过程的可行性和产品质量的稳定性。
首先,挤压铸造工艺的模拟是一个必不可少的环节。
通过模拟软件,我们可以在计算机上模拟出整个铸造过程中的各个环节,包括模具充填、凝固过程和铸件缺陷等。
通过模拟,我们可以根据模型的几何形状和材料特性,预测铸件的充填情况和凝固过程,并检测出可能存在的缺陷,如气孔、夹杂等。
模拟还可以帮助优化铸件的结构设计,提高产品的性能和质量。
通过不断调整模拟参数,我们可以得到最佳的铸造参数,以确保模具充填完全、凝固均匀,从而生产出理想的挤压铸造产品。
其次,模具设计是挤压铸造工艺中不可或缺的一环。
模具的设计直接影响到挤压铸造产品的质量和生产效率。
在模具设计中,首先需要根据产品的几何形状和尺寸要求,确定模具的整体结构和尺寸。
模具的结构应该合理,以便于材料的注入和冷却,并保证充填的均匀性。
模具的尺寸应根据产品的缩脱率和凝固收缩率来确定,以确保产品的尺寸稳定性。
其次,还需要考虑模具的材料选择和表面处理。
模具应具备足够的强度和刚度,以承受挤压铸造过程中的高压和剧烈变形。
模具表面应进行适当的处理,以提高产品的表面质量和降低摩擦阻力。
最后,还需要考虑模具的制造工艺和使用寿命。
模具应通过适当的制造工艺和材料热处理,以确保其具有足够的耐磨性和使用寿命。
除了模拟和模具设计外,挤压铸造工艺中还需要考虑其他一些因素。
例如,熔融金属的温度和物性参数对于铸件的质量有重要影响。
通过调整熔融金属的温度和成分,可以改变其流动性和凝固过程,从而影响铸件的充填性和凝固缩孔的形成。
此外,还需要选择合适的润滑剂和涂料,以减少金属与模具的摩擦和氧化反应。
挤压工艺与模具课程设计
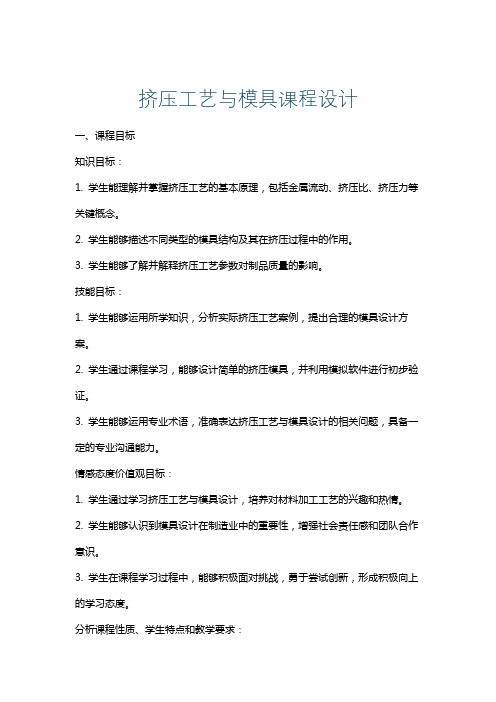
挤压工艺与模具课程设计一、课程目标知识目标:1. 学生能理解并掌握挤压工艺的基本原理,包括金属流动、挤压比、挤压力等关键概念。
2. 学生能够描述不同类型的模具结构及其在挤压过程中的作用。
3. 学生能够了解并解释挤压工艺参数对制品质量的影响。
技能目标:1. 学生能够运用所学知识,分析实际挤压工艺案例,提出合理的模具设计方案。
2. 学生通过课程学习,能够设计简单的挤压模具,并利用模拟软件进行初步验证。
3. 学生能够运用专业术语,准确表达挤压工艺与模具设计的相关问题,具备一定的专业沟通能力。
情感态度价值观目标:1. 学生通过学习挤压工艺与模具设计,培养对材料加工工艺的兴趣和热情。
2. 学生能够认识到模具设计在制造业中的重要性,增强社会责任感和团队合作意识。
3. 学生在课程学习过程中,能够积极面对挑战,勇于尝试创新,形成积极向上的学习态度。
分析课程性质、学生特点和教学要求:本课程为专业实践课程,以模具设计与制造为核心内容,结合学生已掌握的机械基础知识,培养其实践操作能力。
课程针对高中年级学生,具备一定的基础知识和动手能力,注重理论与实践相结合。
教学要求强调学生的主动参与,通过项目式学习,激发学生的创新思维,培养解决实际问题的能力。
课程目标旨在使学生能够将理论知识应用于实际生产,提高综合素养。
二、教学内容1. 挤压工艺原理:包括金属塑性变形原理、挤压比、挤压力的计算、挤压过程中的温度控制等。
相关教材章节:第1章 挤压工艺基础2. 模具结构与设计:介绍不同类型的挤压模具结构、工作原理、设计要点及材料选择。
相关教材章节:第2章 模具结构与设计3. 挤压工艺参数对制品质量的影响:分析挤压速度、温度、润滑等工艺参数对制品表面质量、尺寸精度等方面的影响。
相关教材章节:第3章 挤压工艺参数优化4. 模具设计实例分析:通过实际案例,分析模具设计的全过程,包括市场需求、模具结构设计、参数选择等。
相关教材章节:第4章 模具设计实例5. 模拟软件应用:介绍挤压模具设计模拟软件的使用方法,使学生能够利用软件进行模具设计的初步验证。
铝型材(散热型)挤压工艺与模具设计毕业设计

摘要铝合金因质轻、美观、良好的导热性和易加工成复杂的形状,而被广泛地用于生产散热器材。
铝合金散热器型材主要有三种类型:扁宽形,梳子形或鱼刺形;圆形或椭圆形以及树枝形。
与其他铝型材比,散热器有其自身的特点:散热片之间距离短,相邻两散热片之间形成一个槽形,其深宽比很大;壁厚差大,散热片的齿部很薄,而其根部的底板厚度大。
散热器复杂的截面形状给模具设计、制造和生产带来很大的难度。
本文以两种常用散热器为实例,在总结大量散热器模具设计制造经验的基础上,论述了散热片挤压模具设计的步骤和关键点。
散热器型材挤压模具设计既要保证模具有足够的强度又要平衡金属在模具中的流速。
根据散热器的产品图,将梳子型散热器挤压模具设计成平摸,与导流模配合使用。
把太阳花散热器挤压模具设计成分假流模,以保证在挤压时的金属流动比平模更均匀,这也是太阳花散热器模具设计的关键点。
文中选用4Cr5MoSiV1模具钢作为模具材料,讨论了散热器挤压模具的热处理工艺和散热器的挤压工艺特点。
关键词:散热器挤压模具设计挤压工艺铝型材Extrusion Process and Die Design for Radiator Aluminum Extruded SectionsABSTRACTAluminum alloy, for its light weight, beautiful, good thermal conductivity and easy processing into complex shapes,is widely used to produce cooling equipment. Aluminum radiator profiles are mainly three typesg: flat wide shape, or a fishbone-shaped comb-shaped; round or oval-shaped;and branching shape. Compared with the other aluminum extruded sections radiator has its own characteristics: the distance between the heat sink is short, between two adjacent heat sink to form a trough, and its large aspect ratio; differential wall thickness, heat sink teeth thin, and its roots in the bottom thick. The mold design, manufacturing and production are very difficulty for the complexity of the shape of radiator extruded sections.In this paper, the extruded die design of two common heat sink radiators are discussed in detail on the basis of a lot of experiences in mold design and manufacture for the radiator. Extruded die design has two key parts,the first is sufficient strength to ensure that mold; the second is to balance the flow of metal in the mold. Based on the Product plans of radiators, the radiator comb flat extrusion die are designed to touch, used in conjunction with the diversion mode. The extrusion die is designed radiator sunflowers streaming mode, split mode when the metal flow in the extrusion die is more complex than flat, so how to balance the flow rate of the metal mold is key points for the design of radiator sunflowers. 4Cr5MoSiV1 die steel is usedand also the radiator heat treatment process and extruded process are discussed.Keywords:Radiator Extrude mold design Extrusion processAluminum extruded sections目录摘要 (I)Extrusion Process and Die Design for Radiator Aluminum Extruded Sections (II)ABSTRACT (II)第一章绪论 (1)1.1引言 (1)1.2挤压模具在铝型材挤压生产中的重要性 (1)1.3铝型材挤压模具技术发展概况 (3)1.4论文的主要研究内容 (5)第二章型材挤压模具设计技术 (6)2.1型材模具的设计原则及步骤 (6)2.1.1挤压模具设计时应考虑的因素 (6)2.1.2模具设计的原则与步骤 (6)2.1.3模具设计的技术条件及基本要求 (9)2.2挤压模典型结构要素的设计 (9)2.2.1模角 (9)2.2.2定径带长度和直径 (10)2.2.3出口直径或出口喇叭锥 (10)2.2.4入口圆角 (11)2.3确定采用平面和分流模的原则 (11)2.4平面分流组合模的特点与结构 (12)2.4.1工作原理与特点 (12)2.4.2分流组合模的结构 (13)2.5模具外形尺寸的确定原则 (14)第三章典型散热器挤压模具设计 (16)3.1太阳花散热器的模具设计 (16)3.1.1太阳花散热器产品结构分析 (16)3.1.2太阳花散热器挤压模具整体结构设计方案 (17)3.1.3太阳花散热器分流组合模结构设计 (18)3.2梳子型散热器模具设计 (30)3.2.1梳子型散热器产品结构分析 (30)3.2.2梳子型散热器挤压模具整体结构设计方案 (32)3.2.3梳子型散热器结构设计 (32)第四章模具的选材与热处理及维护与保养 (45)4.1模具材料的选择 (45)4.1.1模具材料的使用条件 (45)4.1.2模具材料的性能要求 (45)4.1.3挤压工模具选材的特点 (46)4.1.4模具材料的选择 (48)4.2模具材料的热处理 (50)4.2.1退火工艺 (50)4.2.2淬火工艺 (50)4.2.3回火工艺 (51)4.2.4 4Cr5MoSiV1钢的热处理工艺 (52)4.3模具的维护与保养 (53)4.3.1模具的修正 (53)4.3.2模具的合理使用 (54)第五章型材挤压工艺 (55)5.1铝及铝合金材料挤压生产工艺流程 (55)5.2挤压工艺的制定 (56)5.2.1挤压方法的选择 (56)5.2.2坯料形状尺寸的确定 (56)5.2.3挤压温度范围 (57)5.2.4流动速度和挤压速度 (58)5.2.5挤压工具的结构 (58)第六章结论 (59)参考文献 (60)致谢 (62)第一章绪论1.1引言挤压工模具设计与制造是铝合金挤压材,特别是铝合金型材生产的关键技术,不仅影响产品的质量、生产效率和交货周期,而且也是决定产品成本的重要因素之一。
铝型材挤压工艺及模具设计

铝型材挤压工艺及模具设计1. 挤压工艺铝型材挤压是一种利用压力对铝型材进行塑性变形的加工工艺。
其基本工艺是:铝棒坯料通过加热软化后,被压入模头,通过模头出口挤出成需要的截面形状。
铝型材挤压工艺的优点包括:高成形精度、高表面质量、操作简便,高生产效率等等。
2. 模具设计铝型材挤压的模具主要包括模头、辅助金属件、固定板、滑动板、胚料夹持装置等组成。
其中,模头是铝型材挤出的关键装置,包括卡箍板、模板、模板底部垫片、模座、模膜等部分。
模头的最重要的特点是不同形状的铝型材需要不同形状的模头;其次需要各个部位的设计匹配度高,精度要求高。
滑动板和固定板是模具的基础结构,他们需要耐压、耐磨,同时需要精度高、边缘无毛刺。
辅助金属件在滑动板、固定板及模头之间起到了加强固定的作用,除此之外还需要具有良好的导向功能。
2.2. 理论参数的确定合理的选择合适的挤压荷载能够很好的保证挤压过程中的质量,同时也能够最大限度的提高生产效率。
因此,在模具设计阶段,应尽可能的确定相应的理论参数。
此外,应还需根据压力、速度、保压时间等因素来确定合适的机器配置,以及最优的辅助系统。
为了达到最优的效果,这些参数需要经过实验验证。
2.3. 模具材料的选择对于铝型材挤压模具来说,常见的材料包括H13钢、特种合金钢、定向硅钢、硬质合金等材料。
如:H13钢:具有高的耐磨性、硬度和强度,适用于铝型材的大批量生产。
特种合金钢:高抗氧化性、高强度、高磨损性,这些特性使其适用于生产高性能和高质量的铝型材。
硬质合金:它具有高硬度和强度、高耐磨性和高耐蚀性,是生产大规模、高复杂度的模具的首选。
2.4. 设计注意事项在模具设计过程中还需要注意以下问题:1)要防止铝材在挤压过程中发生撕裂断裂,因此要注意模具底部的角度把控2)要避免孔洞过大过小,且要容易拆卸,之所以拆卸是为了清洁铝型材上残余物。
3)在设计过程中,要考虑铝型材的变形,保证材料截面和尺寸的均匀性。
4)在滑动板部位,还需要考虑降低铝型材与模具接触时所产生的不良效果,例如顶出口和顶料等问题。
冷挤压工艺及模具设计课件

对修复后的模具进行全面检测 和调试,确保其性能达到要求 。
05
冷挤压工艺与模具 设计的未来发展
新材料的应用
高强度轻质材料
随着新材料技术的不断发展,高强度轻质材料如钛合金、铝合金等在冷挤压工 艺中的应用将更加广泛,能够满足产品轻量化、高性能的要求。
复合材料
复合材料的出现为冷挤压工艺提供了更多的可能性,通过将不同材料组合在一 起,可以实现单一材料无法达到的性能,提高产品性能和降低成本。
合理布局
根据产品特点和工艺要求,合 理布置模具结构,确保产品成
型和出模顺利。
优化流道设计
优化模具流道设计,减少流动 阻力,降低成型难度和压力。
增强刚性和稳定性
为确保模具在使用过程中不易 变形和损坏,应加强模具的刚 性和稳定性设计。
易于维修和更换
模具结构应便于维修和更换损 坏或磨损的部件,降低维护成
本。
冷挤压特点
冷挤压工艺具有高效率、高精度、低 成本等优点,能够加工出形状复杂、 精度要求高的零件,广泛应用于汽车 、家电、电子、航空航天等领域。
冷挤压的应用范围
汽车零件制造
家用电器制造
冷挤压工艺可以用于制造汽车发动机、底 盘、电气系统等零部件,如活塞、连杆、 气瓶等。
家用电器中的金属零部件,如空调压缩机 、冰箱压缩机、洗衣机电机等,也广泛采 用冷挤压工艺制造。
模具的制造工艺
选择合适的加工方法
根据模具材料和结构特点,选择合适的加工方法,确保模具精度 和表面质量。
控制加工参数
合理控制加工参数,如切削速度、进给量等,以提高加工效率和模 具质量。
热处理和表面处理
根据需要,对模具进行热处理和表面处理,提高其硬度和耐久性。
03
铝型材挤压工艺和模具设计的仿真分析和优化

Altair HyperXtrude铝型材挤压工艺和模具设计的仿真分析和优化Altair工程软件(上海)有限公司动机–更早的设计决策解决个问题的成本使用CAE= 解决一个问题的成本题数传统方法出的问# 找模具设计模具制造试模量产HyperXtrude 唯一专业的铝型材挤压仿真软件稳态变形分析模具变形/强度分析瞬态变形分析工作带长度分析焊合长度预测压余长度预测正向/反向挤压虚拟试模材料库快捷的图形用户界面挤压模具优化中文菜单型材料头变形分析——稳态法TemperatureTemperatureVelocityProfile Deflection瞬态分析——型材变形型材变形比较模具变形分析和强度校核耦合的材料流动、热和变形分析依据挤压载荷和热载计算模具的变形和强度模具和材料的网格单元的自动更新位于模具和材料的接触表面网格单元不需要完全匹配保险杠横梁——模具几何Mandrel Die Plate模具上的温度分布模具表面上的法向力分布模具的变形模具上的应力分布——强度校核虚拟试模实例初始模具设计方案结果建议改进方案ObjectiveUniform exitvelocity=6m/min=1m/s•Uniform exit velocity = 6m/min = 0.1m/s Design IterationsFi t It ti R d th th l A d B b 10•First Iteration –Reduce the portholes A and B by 10 mm •Second Iteration –Increase C & D by 5 mm2nd IterationCAD1st IterationBABCD AB案例分析——汽车保险杠横梁Problem DefinitionProblem Definition¾Alloy:AA 6082¾Container Diameter:7.375 in (187.325 mm)¾Billet Length: 25 in (635 mm)¾Press Capacity: 1800 T (16 MN)¾Unit Pressure:580 MPa¾Max. Ram Speed: 41 ipm (17.357 mm/s)¾Container Temperature 441 °CProfile Type:Hollow¾Profile Type:¾Extrusion Ratio:21.93¾Extrusion Speed: 6.87 m/minRam Speed:523mm/s¾Ram Speed: 5.23 mm/s¾Part Exit Speed: 6.87 m/min¾Billet Preheat:518 °C创建有限元模型PortholesDie Plate MandrelAluminum + Tool模芯的变形模芯变形(靠近棒料一侧)下模变形Weld Chamber Bolster Side温度分布(模芯和分流孔)Mandrel Portholes, Bearing and Profile速度分布Original Bearing After 1st Modification Velocity Contours –After 2nd ModificationDecrease by 2mm Decrease by 2 mmIncrease by 3 mm棒料表皮杂质材料跟踪--压余长度预测•棒料表皮包含氧化杂质•表皮挤进型材将影响质量•最佳的压余长度预测停止挤压的时刻——棒料焊合长度计算•材料进入分流孔和导流室•不能停车清理模具•循环棒料的加载挤压•如何预测型材完全是新材料挤出?棒料的接口计算After 5 secAfter 60 sec初始工作带——出口流速不平衡初始设计——型材变形修改工作带长度工作带修改后计算结果——速度分布工作带修改后的计算结果——型材变形正向/反向挤压快捷的图形用户界面 1.Import Geometry 2.Create Project Directory 3.Select Units 4.Set Analysis Requirements Process DataAnalysis DataSelect Components5Select Materials 5.Select Materials6.Set Process Conditions 7.Define Bearing 8S l 8.Solve9.Check Results材料性能数据Workpiece and Tool MaterialsCommon AlloysPlots of Flowstress Curves U M difi blUser Modifiable挤压模具的优化统一的平台,无缝调用集成在HyperWorks统的平台,无缝调用•HyperXtrude, HyperStudy, HyperMorph 工作带长度的优化•平衡材料流动•减少修模分流孔的优化•平衡材料流动•确保模具在挤压过程中没有损坏•减少修模优化原理优化实例——工作带长度的优化型材截面的区域划分工作带优化过程——优化目标出口流速均匀优化前后的出口流速比较支持中文菜单建立挤压工艺数据库•挤压工艺数据•型材数据•棒料数据•挤压设备数据•可挤压合金材料HyperXtrude任务管理器一个桌面应用工具,能够实现在远程机器上提交任务。
挤压工艺与模具设计---复习宝典
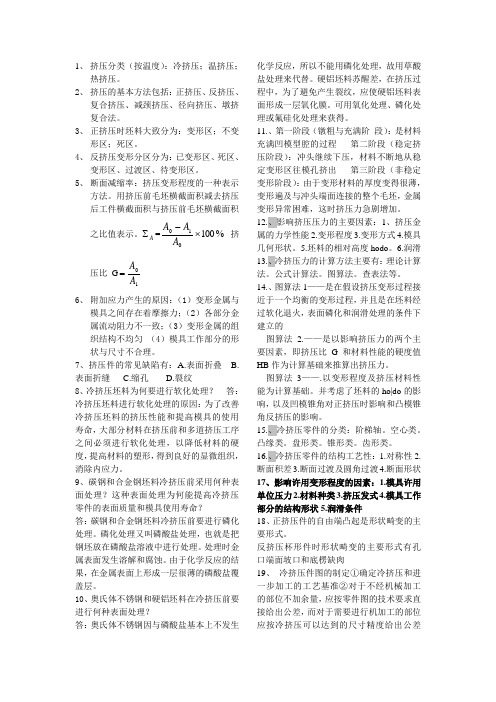
1、 挤压分类(按温度):冷挤压;温挤压;热挤压。
2、 挤压的基本方法包括:正挤压、反挤压、复合挤压、减颈挤压、径向挤压、墩挤复合法。
3、 正挤压时坯料大致分为:变形区;不变形区;死区。
4、 反挤压变形分区分为:已变形区、死区、变形区、过渡区、待变形区。
5、 断面减缩率:挤压变形程度的一种表示方法。
用挤压前毛坯横截面积减去挤压后工件横截面积与挤压前毛坯横截面积之比值表示。
A ∑=%100010⨯-A A A 挤压比 G 1A A =6、 附加应力产生的原因:(1)变形金属与模具之间存在着摩擦力;(2)各部分金属流动阻力不一致;(3)变形金属的组织结构不均匀 (4)模具工作部分的形状与尺寸不合理。
7、挤压件的常见缺陷有:A.表面折叠 B.表面折缝 C.缩孔 D.裂纹8、冷挤压坯料为何要进行软化处理? 答:冷挤压坯料进行软化处理的原因:为了改善冷挤压坯料的挤压性能和提高模具的使用寿命,大部分材料在挤压前和多道挤压工序之间必须进行软化处理,以降低材料的硬度,提高材料的塑形,得到良好的显微组织,消除内应力。
9、碳钢和合金钢坯料冷挤压前采用何种表面处理?这种表面处理为何能提高冷挤压零件的表面质量和模具使用寿命? 答:碳钢和合金钢坯料冷挤压前要进行磷化处理。
磷化处理又叫磷酸盐处理,也就是把钢坯放在磷酸盐溶液中进行处理。
处理时金属表面发生溶解和腐蚀。
由于化学反应的结果,在金属表面上形成一层很薄的磷酸盐覆盖层。
10、奥氏体不锈钢和硬铝坯料在冷挤压前要进行何种表面处理? 答:奥氏体不锈钢因与磷酸盐基本上不发生化学反应,所以不能用磷化处理,故用草酸盐处理来代替。
硬铝坯料苏醒差,在挤压过程中,为了避免产生裂纹,应使硬铝坯料表面形成一层氧化膜。
可用氧化处理、磷化处理或氟硅化处理来获得。
11.、第一阶段(镦粗与充满阶 段):是材料充满凹模型腔的过程 第二阶段(稳定挤压阶段):冲头继续下压,材料不断地从稳定变形区往模孔挤出 第三阶段(非稳定变形阶段):由于变形材料的厚度变得很薄,变形遍及与冲头端面连接的整个毛坯,金属变形异常困难,这时挤压力急剧增加。
冲压工艺与模具设计第 6章 冷挤压工艺与模具 设计

A0 挤压变形前毛坯的横断 面积( mm 2 ) A1 挤压变形后毛坯的横断 面积( mm 2 )
2)挤压比:
A0 G A1 A0 0 Ln A1
3)对数变形程度:
2.冷挤压许用变形程度 挤压的许用变形程度:模具强度允许的条件下一次挤 压的变形程度. 影响因素: 挤压材料的力学性能、模具强度、挤压变形方式、毛 坯表面处理、润滑等。 挤压(如图6.1.10) 、反挤压(如图6.1.11)分别表 达了毛坯材料硬度与许用变形程度的关系。曲线由实验测 得,其试验条件是: 毛坯的相对高度 h0 / d0 1 毛坯经退火软化、表面 磷皂化处理 .
第 6 章 冷挤压工艺与模具 设计
6.1
冷挤压工艺的分类及挤压金属的变形特点
6.2
冷挤压原材料与毛坯的制备 冷挤压力的确定 冷挤压的工艺设计
6.3
6.4
6.5
冷挤压模具设计
冷挤压是在室温将毛坯放入模具型腔,在强大压力和 一定速度作用下,迫使金属从形腔中挤出而获得一定形状、 尺寸和力学性能的制件。 主要的优点: 1)因在冷态下挤压成形,挤压件质量好、精度高、其 强度性能也好; 2)冷挤压属于少、无切削加工,节省原材料; 3)冷挤压是利用模具来成形的,其生产效率很高; 4)可以加工其它工艺难于加工的零件
6.1.2
冷挤压金属的变形分析
1. 正挤压变形分析 正挤压实心件的金属流动网格图(如图6.1.5) 正挤压时坯料大致分为: 变形区、不变形区(又分为待变形区、已变形区) 和死角区。(如图6.1.6a) 变形区的应力应变关系(如图6.1.6b)单元体所示。 挤压时变形区的应力状态是三向受压。其变形是两向 收缩、一向伸长的应变状态.
特殊要求: 1)要求设备吨位较大 冷挤压的变形抗力大,单位挤 压力可能高达 2)对模具要求高 冷挤压力时常接近甚至超过现有模 具材料的抗压强度,所以对模具材料要求很高.
铝合金挤压工艺及模具毕业设计

一、绪论1.1 挤压加工方法挤压是有色金属、钢铁材料生产与零件成型加工的主要方法之一,也是各种复合材料、粉末材料等先进材料制备与加工的重要方法。
从大尺寸金属铸锭的热挤压开坯、大型管棒型材的热挤压加工至小型精密零件的冷挤压成型,从粉末、颗粒料为原料的复合材料直接固化成型到金属间化合物、超导材料等难加工材料,现代挤压技术得以广泛的应用。
挤压加工的方法主要有正挤压,反挤压,侧向挤压,玻璃润滑挤压,静液挤压,连续挤压。
挤压加工特点是处于强烈的三向压应力状态,这有利于提高金属的塑性变形能力,提高制品的质量,改善制品内部微观组织和性能。
除此以外,挤压加工还具有应用范围广,生产灵活性大,工艺流程简单和设备投资少的特点。
应用挤压加工工艺最多的材料是低熔点的有色合金,如铝及铝合金。
1.2 铝加工行业的分布中国的铝加工企业主要集中于沿海(广东、福建、浙江、上海、江苏、山东、河北、天津、北京、辽宁)地区,即珠江三角洲(广州一深圳为中心的经济圈)、长江三角洲(上海为中心的经济圈)、环渤海湾地区(京津经济圈)所占比例较大,许多铝加工企业都云集于此三大经济圈。
在珠三角地区,主要集中在佛山地区,其中大沥更是全国,甚至世界地区铝加工业的佼佼者。
1.3铝及铝合金的特点与应用铝及铝合金具有一系列特性,在金属材料的应用中仅次于钢材而居第二位。
目前全世界铝材的消费量在1800万吨以上,其中用于交通运输(包括铁道车辆、汽车、摩托车、自行车、汽艇、快艇、飞机等)的铝材约占27%,用于建筑装修的铝材约23%,用于包装工业的铝材约占20%。
随着中国经济建设的高速发展,人民生活水平的不断提高,中国的建筑行业发展迅速,包括铝型材在内的建筑装饰材料不断增加。
铝型材的应用已经扩展到了国民经济的各个领域和人民生活的各个层面。
根据铝合金的成分和生产工艺特点,通常分为变形铝合金与铸造铝合金两大类。
变形铝合金也叫熟铝合金,根据据其成分和性能特点又分为防锈铝,硬铝,超硬铝,锻铝和特殊铝等五种。
挤压成型工艺及模具设计
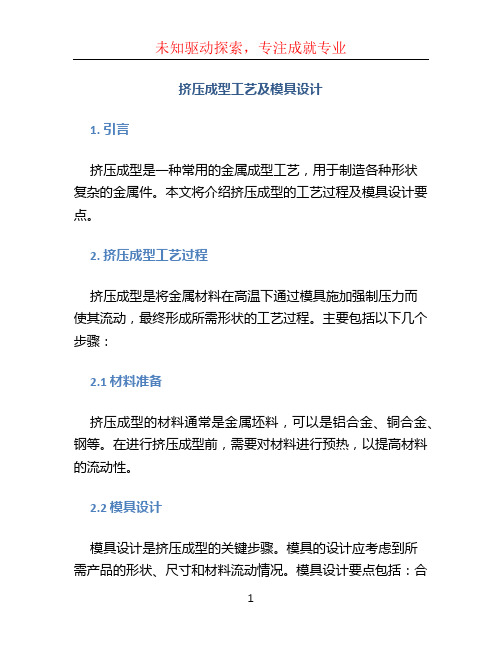
挤压成型工艺及模具设计1. 引言挤压成型是一种常用的金属成型工艺,用于制造各种形状复杂的金属件。
本文将介绍挤压成型的工艺过程及模具设计要点。
2. 挤压成型工艺过程挤压成型是将金属材料在高温下通过模具施加强制压力而使其流动,最终形成所需形状的工艺过程。
主要包括以下几个步骤:2.1 材料准备挤压成型的材料通常是金属坯料,可以是铝合金、铜合金、钢等。
在进行挤压成型前,需要对材料进行预热,以提高材料的流动性。
2.2 模具设计模具设计是挤压成型的关键步骤。
模具的设计应考虑到所需产品的形状、尺寸和材料流动情况。
模具设计要点包括:合理确定模具结构、开发合适的模具材料、考虑模具的冷却方式等。
2.3 加热加热是为了提高金属材料的流动性。
通常使用感应加热、火焰加热等方式进行加热。
2.4 挤压在加热后,将预热的金属材料放入挤压机的料斗中,并施加一定的压力将材料挤出模具。
挤压过程中,材料会与模具表面摩擦产生热量,增加金属的塑性变形。
2.5 修整挤压成型后,需要对成品进行修整,去除多余的材料、毛刺等。
2.6 退火挤压成型后的产品通常需要进行退火处理,以消除内部应力,提高产品的力学性能和稳定性。
3. 模具设计要点模具设计是挤压成型的重要环节,对产品的质量和生产效率有着重要影响。
以下是一些模具设计的要点:3.1 模具结构模具结构应根据产品的形状和尺寸合理设计,包括上模、下模、模具腔等。
模具结构的设计应确保产品形状的准确性和一致性。
3.2 模具材料模具材料应具有足够的硬度、耐磨性和热稳定性。
常用的模具材料有工具钢、硬质合金等。
3.3 模具冷却模具冷却是保证挤压成型过程中正确进行的关键。
合理的模具冷却设计可以提高生产效率、延长模具使用寿命。
常用的模具冷却方式有冷却水循环系统、气体冷却等。
3.4 模具润滑模具润滑是减少模具与材料之间摩擦、降低能量消耗的重要方法。
常用的模具润滑方式有润滑油、润滑脂等。
4. 结论挤压成型是一种常用的金属成型工艺,通过对金属材料的高温加热和施加压力,可以制造各种形状复杂的金属件。
- 1、下载文档前请自行甄别文档内容的完整性,平台不提供额外的编辑、内容补充、找答案等附加服务。
- 2、"仅部分预览"的文档,不可在线预览部分如存在完整性等问题,可反馈申请退款(可完整预览的文档不适用该条件!)。
- 3、如文档侵犯您的权益,请联系客服反馈,我们会尽快为您处理(人工客服工作时间:9:00-18:30)。
目录一、挤压相关知识及发展状况 (2)二、总设计过程概论 (5)三、实心型材模设计 (7)四、总结与体会 (19)1.1 挤压加工方法挤压是有色金属、钢铁材料生产与零件成型加工的主要方法之一,也是各种复合材料、粉末材料等先进材料制备与加工的重要方法。
从大尺寸金属铸锭的热挤压开坯、大型管棒型材的热挤压加工至小型精密零件的冷挤压成型,从粉末、颗粒料为原料的复合材料直接固化成型到金属间化合物、超导材料等难加工材料,现代挤压技术得以广泛的应用。
挤压加工的方法主要有正挤压,反挤压,侧向挤压,玻璃润滑挤压,静液挤压,连续挤压。
挤压加工特点是处于强烈的三向压应力状态,这有利于提高金属的塑性变形能力,提高制品的质量,改善制品内部微观组织和性能。
除此以外,挤压加工还具有应用范围广,生产灵活性大,工艺流程简单和设备投资少的特点。
应用挤压加工工艺最多的材料是低熔点的有色合金,如铝及铝合金。
1.2 铝加工行业的分布中国的铝加工企业主要集中于沿海(广东、福建、浙江、上海、江苏、山东、河北、天津、北京、辽宁)地区,即珠江三角洲(广州一深圳为中心的经济圈)、长江三角洲(上海为中心的经济圈)、环渤海湾地区(京津经济圈)所占比例较大,许多铝加工企业都云集于此三大经济圈。
在珠三角地区,主要集中在佛山地区,其中大沥更是全国,甚至世界地区铝加工业的佼佼者。
1.3铝及铝合金的特点与应用铝及铝合金具有一系列特性,在金属材料的应用中仅次于钢材而居第二位。
目前全世界铝材的消费量在1800万吨以上,其中用于交通运输(包括铁道车辆、汽车、摩托车、自行车、汽艇、快艇、飞机等)的铝材约占27%,用于建筑装修的铝材约23%,用于包装工业的铝材约占20%。
随着中国经济建设的高速发展,人民生活水平的不断提高,中国的建筑行业发展迅速,包括铝型材在内的建筑装饰材料不断增加。
铝型材的应用已经扩展到了国民经济的各个领域和人民生活的各个层面。
根据铝合金的成分和生产工艺特点,通常分为变形铝合金与铸造铝合金两大类。
变形铝合金也叫熟铝合金,根据据其成分和性能特点又分为防锈铝,硬铝,超硬铝,锻铝和特殊铝等五种。
铝合金比纯铝具有更好的物理力学性能:易加工、耐久性高、适用范围广、装饰效果好、花色丰富。
铝合金分为防锈铝、硬铝、超硬铝等种类,各种类均有各自的使用范围,并有各自的代号,以供使用者选用。
铝合金型材具有强度高、重量轻、稳定性强、耐腐蚀性强、可塑性好、变形量小、无污染、无毒、防火性强,使用寿命长(可达50—100年),回收性好,可回炉重炼。
1.4挤压工模具的材料常用挤压工具钢化学成分本设计选用模具材料为4Cr5MoSiV1,又称H13钢。
钢中碳化物类型有623C M 、C M 6。
钒在钢中起回火时二次硬化作用;Cr 、Mo 、W 、V 能提高钢抗回火软化能力,保持高温下的强度、韧度;硅提高钢的回火稳定性和抗热疲劳能力。
铬和硅还能提高抗氧化和抗烧蚀性。
常用挤压工具钢及其机械性能:二、总设计过程概论2.1 挤压工艺流程金属制品是经若干个工序制作出来的,每个工序按一定顺序连接起来,就形成了工艺。
工艺要在一定条件下完成,有特定的工艺参数。
挤压工艺流程:铸锭加热→挤压→切压余→淬火→冷却→切头尾→切定尺→时效→表面处理→包装入库2.2挤压工艺及工艺参数条件的确定应考虑挤压温度、挤压速度、润滑、模具(种类形状、形状等)、切压余、切头尾、淬火、冷却、等多方面的因素,合理地选择工艺或参数。
1)铸锭的加热温度3003铝的最高允许加热温度为550℃,下限温度为320℃,为了保证制品的组织,性能,表面质量,为了降低变形抗力,挤压时锭坯的加热温度不宜过高,应尽量降低挤压温度。
一般取490~530℃。
2)挤压筒预热模具的成分多为合金钢,由于导热性差,为避免产生热应力,挤压前挤压筒要预热,为保证挤压制品的质量,并且具有良好的挤压效应,挤压筒温度可取400℃~450℃。
可采用通电自行预热。
3)模子预热避免急热,延长模具寿命,应对模具进行预热。
4)挤压温度热挤压时,加热温度一般是合金熔点绝对温度的0.75~0.95倍,挤压过程中温度最好控制在500℃左右。
6)挤压速度考虑金属与合金的可挤压性,制品质量要求及设备的能力限制,本设计的挤压速度取m in /0.2~8.0m V =锭,m in /80~60m V ≤流出。
7)工模具的润滑因本设计采用热挤压,故不采用润滑。
8)模具模具应具有足够的耐高温疲劳强度和硬度,较高的耐回火性及耐热性,足够的韧性,低的热膨胀系数和良好的导热性,可加工性,及经济性,本设计采用4Cr5MoSiV1作为模具的材料,热处理的硬度为HRC48~52。
9)切压余本设计视挤压设备而定,一般20~30mm ,要控制质量,切去缩尾等缺陷。
10)淬火本工艺过程中,制品挤出后可通过设置风扇对制品进行吹风来达到风淬(固溶强化)的目的,或采用喷水雾的方法。
11)冷却直接露置在空气中冷却,达到自然时效的目的。
12)切头尾一般挤压制品的头部和尾部都存在缺陷,为了不影响制品的性能,需要进行切头尾的工作。
切头尾的量可以是300~500mm 或500~1000mm ,本次设计头尾各切300mm 。
13)切定尺本次设计取每根制品6m 长作为切定尺的标准。
14)时效时效处理可以分为两种:自然时效和人工时效。
自然时效即让挤压制品在空气中停放;人工时效对3xxx系铝合金可在180~240℃下保温6~8h。
15)表面处理为了提高制品的耐蚀性和抗疲劳性等,可以对其进行表面处理。
表面处理一般有:阳极氧化、着色、喷粉、喷涂、电泳、抛光等。
16)包装入库将铝合金成品进行包装入库。
三、实心型材模设计3.1所要设计的实心型材制品图1 v型材截面(1)已知:要求本制品的形状和尺寸及公差如下牌号XC311-5(v 型) 制品的截面积263mmF =制制品材料为3003,制品挤一米的重量m kg G /171.0= 模孔外接圆直径mm D 97.16121222=+=外(2)现有设备表63.2选坯和选设备选择挤压筒直径D0是一个最核心的问题,有以下的选择原则:1)保证产品表面质量原则C'≥1K(C'为模孔距筒内表面的距离,1K为经验数据,可取15、20、30)2)保证挤压模强度的原则3)保证产品内在质量的原则4)经济上的优化原则-生产成本最低;成材率最大;产量最高可用500T,按成才率最高的原则,进一步优化,计算如下表所示:最后选择成才率最高的81.8%方案1即:选择500T的挤压机设备,挤压筒内径D0=Φ95mm锭坯尺寸为:Dd×Ld=Φ90×270mmλ=62.483.3挤压力的计算根据挤压力经验系数公式,b D dDP σ2)8.0(775.11-= P ——挤压力, N D ——挤压筒内直径,mmd ——制品的当量直径,mm ;(π制F d 4=)b σ——材料在挤压温度下的变形抗力,MPa ;查表3,并由外推法得出500℃时的变形抗力为10MPa 。
所以d=π制F 4=π634⨯=8.96mmP=b D dDσ2)8.0(775.11- =1095)8.096.895(775.112⨯⨯-⨯ =2610162N换算成吨位:约266TP=266T <额定吨位500T ,设备选择符合要求,即理论技术可行 3.4实心型材模具体结构设计 模组的结构如下图图2 模组的结构1.模子2.模垫3.前环4.后环5.保护垫板6.前机架7.模座8.模套 9.剪刀 10.挤压筒对于不同吨位的挤压机,下图中的主要结构尺寸都是配套设置的,可以从有关资料中查得。
模组的主要结构尺寸如图3模组尺寸如下表表7模组尺寸挤压模具的尺寸如下表表8挤压模具的尺寸3.5 实心模尺寸数据设计(1)选坯和选择设备根据前面的计算选500T挤压机挤压筒内直径D=95㎜锭坯尺寸:Dd×Ld=Φ90×320mm挤压比λ=62.48(2)模组及模子尺寸外形的计算图3模组主要结构尺寸标注模组主要结构尺寸确定根据前面计算,从表7选取H=190mmH=20mm2H=80mm3H=55mm1∅=Φ160mm1∅=Φ180mm 1模子外形尺寸的确定(如下图4)图4模子外形尺寸依据表8的数据可以确定d=Φ135㎜2d=Φ145㎜1h=12㎜2h=25㎜1(3)模孔几何尺寸的确定挤压比λ=62.48<λ,故不需要多孔挤压。
max①模孔的外形尺寸(指型材的宽与高)A K :由公式11(1)k m A A C =++∆式中:m A ——型材的名义尺寸,mm1C ——裕量系数,见《金属塑性加工学》,冶金工业出版社,P67表5-1锻铝取0.007~0.010,本设计取0.0101∆——型材外形尺寸的正偏差,mm②型材的壁厚的尺寸S K 由公式22k m S S C =++∆式中:m S ——型材壁厚的名义尺寸,mm2∆——型材壁厚的正偏差,mm2C ——裕量系数,对铝合金取0.05~0.15,其中壁薄的取下限,厚壁取上限。
本设计取0.1③计算得出几何尺寸:模孔外型尺寸: 长度方向25±0.45mm 尺寸k B =m B (1+ 1C )+1∆=32×(1+0.01)+0.45=12.57mm宽度方向13±0.45mm 尺寸k H =m H (1+1C )+1∆=13×(1+0.01)+0.45=12.57mm壁厚的尺寸 22k m S S C =++∆=2.4+0.1+0.2 =3.4㎜型材的圆角及圆弧没有偏差要求,故可按名义尺寸设计 由于这种型材在挤压的过程中有并口现象,角度取91° 制造偏差为 45.0±㎜,主要尺寸如下图图5 模孔几何尺寸(4)孔形在模子端面位置的确定由于本型材为等壁厚的型材,故型材的重心与模子的中心重合。
模孔重心的计算,如下图建立坐标系:图6模孔几何中心确定设压力中心为(0x ,0y )由于v 型截面具有一条对称轴,如图6关于Y 轴称 所以0x =0 ,则压力中心为(0,0y ) 各边中心坐标为:()()23,23,111-=y x l ,()()275.6,225.4,222-=y x l ,()()275.6,25.4,333-=y x l ,()()275.6,25.4,444=y x l ,()()275.6,225.4,555=y x l ,()()23,23,666=y x l各边长分别为:1l =12mm ,2l =3mm ,3l =9mm ,4l =9mm ,5l =3mm,126=l mm0y =876543218877665544332211l l l l l l l l l y l y l y l y l y l y l y l y ++++++++++++++=4.24mm由于制品对称,所以(0x ,0y )=(0,4.24)(5)工作带长度的确定工作带又称定径带,是用以稳定制品尺寸和保证制品质量的关键部分。