CNC坐标磨床全干式切削加工性能的分析
CNC机床加工中的切削参数调优与控制
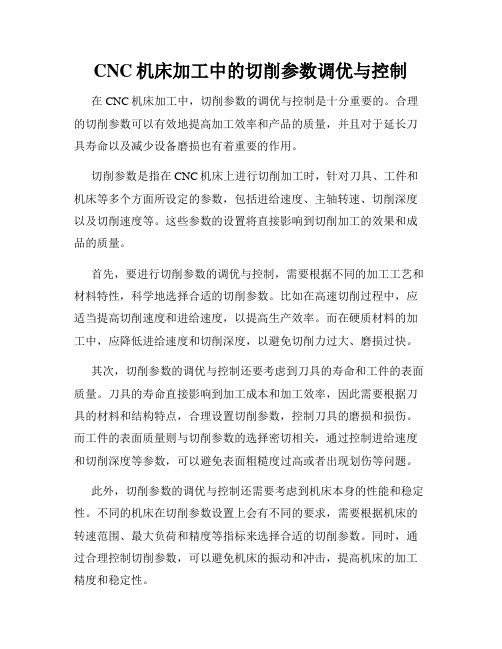
CNC机床加工中的切削参数调优与控制在CNC机床加工中,切削参数的调优与控制是十分重要的。
合理的切削参数可以有效地提高加工效率和产品的质量,并且对于延长刀具寿命以及减少设备磨损也有着重要的作用。
切削参数是指在CNC机床上进行切削加工时,针对刀具、工件和机床等多个方面所设定的参数,包括进给速度、主轴转速、切削深度以及切削速度等。
这些参数的设置将直接影响到切削加工的效果和成品的质量。
首先,要进行切削参数的调优与控制,需要根据不同的加工工艺和材料特性,科学地选择合适的切削参数。
比如在高速切削过程中,应适当提高切削速度和进给速度,以提高生产效率。
而在硬质材料的加工中,应降低进给速度和切削深度,以避免切削力过大、磨损过快。
其次,切削参数的调优与控制还要考虑到刀具的寿命和工件的表面质量。
刀具的寿命直接影响到加工成本和加工效率,因此需要根据刀具的材料和结构特点,合理设置切削参数,控制刀具的磨损和损伤。
而工件的表面质量则与切削参数的选择密切相关,通过控制进给速度和切削深度等参数,可以避免表面粗糙度过高或者出现划伤等问题。
此外,切削参数的调优与控制还需要考虑到机床本身的性能和稳定性。
不同的机床在切削参数设置上会有不同的要求,需要根据机床的转速范围、最大负荷和精度等指标来选择合适的切削参数。
同时,通过合理控制切削参数,可以避免机床的振动和冲击,提高机床的加工精度和稳定性。
在实际的CNC机床加工过程中,切削参数的调优与控制是一个不断优化和改进的过程。
随着刀具和材料的不断研发和改良,切削参数的选择也需要与时俱进。
因此,需要进行充分的实验研究和数据分析,结合工程实践经验,不断调整和改进切削参数,以求达到最佳的加工效果和成品质量。
总之,CNC机床加工中的切削参数调优与控制对于提高加工效率、保证产品质量以及延长设备和刀具的使用寿命都具有重要的意义。
通过合理选择和控制切削参数,可以实现更高效、更稳定的加工过程,为工业生产的发展做出积极的贡献。
CNC机床加工中的磨削工艺参数优化与控制

CNC机床加工中的磨削工艺参数优化与控制随着现代制造技术的发展,CNC(Computer Numerical Control,数控)机床已成为工业生产中重要的加工设备之一。
在CNC机床的加工过程中,磨削技术广泛用于零件表面的加工与修整。
为了实现更高的加工精度和效率,磨削工艺参数的优化与控制变得至关重要。
本文将探讨CNC机床加工中的磨削工艺参数优化与控制的相关问题。
1. 磨削工艺参数的意义与影响磨削工艺参数是指在磨削过程中对磨削操作进行调节的各项参数。
这些参数包括磨削速度、进给速度、切削深度、磨削负荷等。
正确的磨削工艺参数可以显著提高零件的加工质量和生产效率,而错误的参数选择则可能导致零件的表面质量下降、寿命减短甚至设备受损。
2. 磨削工艺参数优化与控制方法为了实现磨削工艺参数的优化与控制,可以采用以下几种方法:2.1 实验法通过设计并进行一系列实验,结合不同磨削工艺参数的组合,测量和分析加工结果,可以找到最佳参数组合。
然而,实验法需要大量的时间和成本,并且对设备和材料的要求较高。
2.2 统计分析法利用统计学方法对历史数据进行分析,找出磨削工艺参数与加工质量之间的关联性,并基于此建立统计模型。
通过优化模型参数,可以达到磨削工艺参数的最优选择。
然而,统计分析法需要大量的数据支持,且对参数的选择和模型的准确性要求较高。
2.3 数值模拟法利用计算机软件对磨削过程进行数值模拟,通过设置不同的参数值,模拟并预测加工结果。
通过反复优化参数值,可以找到最佳的磨削工艺参数。
数值模拟法相对于实验法和统计分析法具有成本低、效率高的特点,但对模拟模型的准确性和精度要求较高。
3. 磨削工艺参数的实际应用与控制在实际的CNC机床加工中,除了确定最佳的磨削工艺参数外,还需要进行参数的实时监控和控制,以保持加工过程的稳定性和一致性。
3.1 在线监测与反馈控制通过在加工过程中实时监测和获取关键参数的数据,如加工速度、磨削力等,可以及时发现工艺异常和问题,并采取相应的措施进行调整和修正,以保证加工质量的稳定性和一致性。
CNC机床加工中的切削参数选择与优化

CNC机床加工中的切削参数选择与优化在CNC机床加工中,切削参数选择与优化是至关重要的一步。
正确的切削参数可以保证工件的质量,提高加工效率,同时还可以延长刀具的使用寿命。
本文将探讨CNC机床加工中的切削参数选择与优化的要点。
一、切削参数的选择在选择切削参数时,需要考虑以下几个方面:1.工件材料不同的工件材料对切削参数有着不同的要求。
一般来说,硬度较高的材料需要选择较大的进给量和切削速度,以保证切削效果。
而对于较软的材料,则需要选择较小的进给量和切削速度。
2.刀具材料和形状刀具的材料和形状也会影响切削参数的选择。
硬质合金刀具通常适用于高速切削,而高速钢刀具则适用于低速切削。
此外,刀具的形状也会对切削参数产生影响。
例如,球头刀具适合进行曲面加工,而平头刀具适合进行平面加工。
3.加工精度要求不同的加工精度要求也会对切削参数产生影响。
如果要求加工精度较高,就需要选择较小的进给量和切削速度,以提高加工的精度。
而如果加工精度要求较低,可以适当增大切削参数,以提高加工的效率。
二、切削参数的优化切削参数的优化可以通过试切试验和仿真模拟两种方法来进行。
1.试切试验试切试验是一种直接测量和比较不同切削参数效果的方法。
通过试切试验,可以找出切削参数与加工表面粗糙度、切削力等因素的关系。
根据试切试验的结果,可以调整切削参数,从而达到优化加工效果的目的。
2.仿真模拟仿真模拟是通过计算机软件对切削过程进行模拟和分析的方法。
通过仿真模拟,可以在不进行实际加工的情况下对不同的切削参数进行比较和优化。
仿真模拟可以节省时间和成本,并且可以预测加工结果,为切削参数的选择和优化提供依据。
三、切削参数的优化策略在进行切削参数的选择和优化时,可以采用以下几种常用的策略:1.保证切削稳定性切削过程中的稳定性对于保证加工质量和提高加工效率至关重要。
因此,在选择和优化切削参数时,要避免过大或过小的切削速度和进给量,以保证切削过程的稳定性。
2.控制切削温度切削过程中会产生大量的切削热量,如果温度过高,可能会导致刀具磨损加剧和工件变形。
CNC机床加工中的切削力与振动控制技术研究与应用案例分析
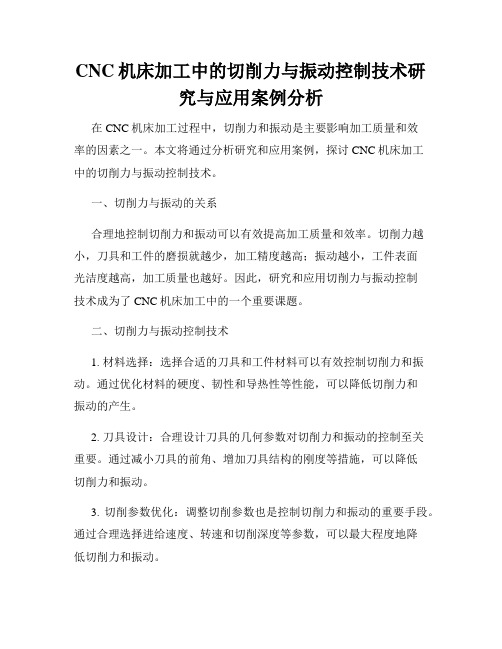
CNC机床加工中的切削力与振动控制技术研究与应用案例分析在CNC机床加工过程中,切削力和振动是主要影响加工质量和效率的因素之一。
本文将通过分析研究和应用案例,探讨CNC机床加工中的切削力与振动控制技术。
一、切削力与振动的关系合理地控制切削力和振动可以有效提高加工质量和效率。
切削力越小,刀具和工件的磨损就越少,加工精度越高;振动越小,工件表面光洁度越高,加工质量也越好。
因此,研究和应用切削力与振动控制技术成为了CNC机床加工中的一个重要课题。
二、切削力与振动控制技术1. 材料选择:选择合适的刀具和工件材料可以有效控制切削力和振动。
通过优化材料的硬度、韧性和导热性等性能,可以降低切削力和振动的产生。
2. 刀具设计:合理设计刀具的几何参数对切削力和振动的控制至关重要。
通过减小刀具的前角、增加刀具结构的刚度等措施,可以降低切削力和振动。
3. 切削参数优化:调整切削参数也是控制切削力和振动的重要手段。
通过合理选择进给速度、转速和切削深度等参数,可以最大程度地降低切削力和振动。
4. 切削液的应用:正确选择和使用切削液可以有效降低切削力和振动。
切削液可以起到冷却、润滑和减小摩擦的作用,从而降低切削力和振动。
三、案例分析以某公司的数控车床加工中心为例进行案例分析。
该公司在加工特定零件时经常遇到切削力和振动过大的问题,导致加工质量不稳定。
为了解决这个问题,该公司采取了以下措施:1. 调整刀具几何参数:根据工件材料和加工要求,优化刀具的前角和后角,增加刀具的主偏角,提高刀具的刚度,以减小切削力和振动的产生。
2. 优化切削参数:通过试切试验和实际加工情况分析,调整切削速度、进给速度和切削深度等参数,找到最佳的切削参数组合,以降低切削力和振动。
3. 应用合适的切削液:根据切削材料的特性和切削过程的要求,选择了一种高效的切削液。
该切削液具有良好的冷却性能和润滑性能,可以有效降低切削力和振动。
通过上述措施的应用,该公司成功地控制了切削力和振动,提高了加工质量和效率。
CNC机床加工中的加工力学性能分析与优化
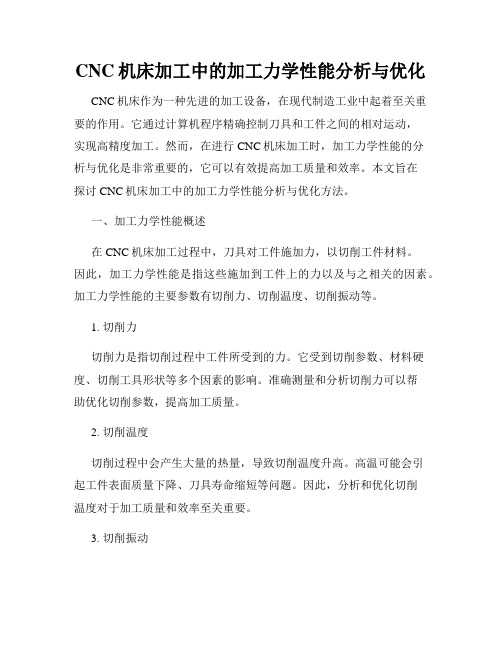
CNC机床加工中的加工力学性能分析与优化CNC机床作为一种先进的加工设备,在现代制造工业中起着至关重要的作用。
它通过计算机程序精确控制刀具和工件之间的相对运动,实现高精度加工。
然而,在进行CNC机床加工时,加工力学性能的分析与优化是非常重要的,它可以有效提高加工质量和效率。
本文旨在探讨CNC机床加工中的加工力学性能分析与优化方法。
一、加工力学性能概述在CNC机床加工过程中,刀具对工件施加力,以切削工件材料。
因此,加工力学性能是指这些施加到工件上的力以及与之相关的因素。
加工力学性能的主要参数有切削力、切削温度、切削振动等。
1. 切削力切削力是指切削过程中工件所受到的力。
它受到切削参数、材料硬度、切削工具形状等多个因素的影响。
准确测量和分析切削力可以帮助优化切削参数,提高加工质量。
2. 切削温度切削过程中会产生大量的热量,导致切削温度升高。
高温可能会引起工件表面质量下降、刀具寿命缩短等问题。
因此,分析和优化切削温度对于加工质量和效率至关重要。
3. 切削振动切削振动是指在切削过程中刀具和工件之间发生的振动。
这种振动可能导致刀具的不稳定、工件表面质量下降等问题。
因此,减小切削振动是提高加工质量的重要措施之一。
二、加工力学性能分析方法为了准确地分析CNC机床加工中的加工力学性能,下面介绍几种常用的分析方法。
1. 实验方法实验方法是通过在实际加工过程中测量和记录相关的力学参数来获得加工力学性能的信息。
这种方法可以提供直接的数据支持,但需要实际操作,并且时间和成本较高。
2. 数值模拟方法数值模拟方法是利用计算机模拟技术对CNC机床加工过程进行仿真。
通过将加工参数和切削条件输入计算模型中,可以得到各种加工力学性能参数的预测结果。
这种方法具有快速、高效、低成本的特点,可以对不同工况下的加工力学性能进行分析。
3. 理论分析方法理论分析方法是通过建立数学模型和公式,对切削力和切削温度等加工力学性能参数进行推导和计算。
CNC机床加工中的切削参数对加工质量的影响

CNC机床加工中的切削参数对加工质量的影响CNC(数控)机床是一种利用计算机程序控制的机床,能够通过控制切削参数来进行高精度的加工。
在CNC机床加工中,切削参数的选择和设定对加工质量有着重要的影响。
本文将从几个重要的切削参数入手,分析它们对加工质量的具体影响。
切削速度是CNC机床中最基本的切削参数之一。
它指的是加工过程中刀具在工件上运动的速度。
切削速度的选择直接影响着加工表面的粗糙度和切削温度。
当切削速度过高时,刀具与工件之间的摩擦会增加,导致加工表面粗糙度增加。
同时,过高的切削速度会产生过多的热量,容易导致刀具磨损和工件变形。
相反,切削速度过低则会导致加工效率低下。
因此,在选择切削速度时,需要综合考虑加工要求和刀具材料的特性,寻找最佳的速度范围。
进给速度是指在切削速度确定的情况下,刀具在单位时间内切削的长度。
进给速度决定了加工的效率和加工表面的粗糙度。
过高的进给速度会导致切削力过大,加工表面粗糙度增加,甚至会引起刀具折断等问题。
而进给速度过低则会降低加工效率。
因此,在选择进给速度时,需要根据工件材料、切削工艺和刀具性能等因素进行合理搭配,以获得高效的切削效果。
切削深度是指刀具在一次下刀过程中切削的厚度。
它是影响切削力和切削温度的重要参数。
切削深度过大会增加切削力,容易导致刀具振动和加工表面的粗糙度增加。
切削深度过小则会增加进给次数,导致加工效率降低。
因此,在确定切削深度时,需要考虑刀具和工件的刚性,并结合加工要求和刀具磨损情况进行合理选择。
切削角度是指刀具切削部分与工件表面法线之间的夹角。
切削角度的选择直接影响切削力的大小和切屑的排出。
合适的切削角度可以减小切削力,降低切削过程中的振动和声音,同时利于切削液和切屑的顺利排出。
因此,在选择切削角度时,需要考虑工件材料、切削工艺和刀具结构等因素,以保证加工过程的稳定和加工质量的提高。
除了以上几个重要的切削参数外,切削液的选择也对加工质量有着重要影响。
CNC机床加工中的加工精度与加工速度研究

CNC机床加工中的加工精度与加工速度研究加工精度和加工速度在CNC机床加工中起着重要作用。
本文将探讨这两个因素的相互关系,并介绍相关的研究成果。
1. 引言在制造业发展中,CNC机床已经成为加工的重要工具。
CNC机床通过精确的控制系统,可以实现高精度和高效率的加工过程。
然而,加工精度和加工速度在实际应用中往往存在着一定的制约关系。
因此,研究如何在保证加工精度的同时提高加工速度,成为了当前CNC机床加工领域亟待解决的问题。
2. 加工精度的影响因素加工精度受到多个因素的影响,包括机床本身的精度、刀具的选择、工件材料等。
首先,机床的几何精度和运动控制精度直接影响着加工的精确度。
其次,刀具的选择也具有重要作用。
优良的刀具材料和设计能够减少刀具的振动和磨损,从而提高加工的精度。
此外,工件材料的选择、工件的夹持方式以及切削参数的设置也会对加工精度产生影响。
3. 加工速度的影响因素在加工速度方面,切削速度、进给速度和切削深度是三个主要的影响因素。
切削速度是刀具相对于工件表面的速度,进给速度是工件上切削道的线速度,切削深度则表示每个切削道的切削深度。
这三者的合理协调是实现高速加工的关键。
此外,也需要考虑刀具的材料和刃口的形状,以及切削润滑和冷却等因素。
4. 加工精度与加工速度的关系通常情况下,加工精度和加工速度存在一定的权衡关系。
提高加工速度可能会导致加工精度的下降,而追求更高的精度则可能限制了加工的速度。
这是因为高速切削时,由于刀具与工件之间的热量和力的作用,可能会引起刀具的振动和变形,进而影响加工精度。
因此,在实际应用中需要根据具体情况来调整加工精度和加工速度的平衡。
5. 研究成果为了探索加工精度和加工速度之间的关系,许多研究人员进行了相关的实验和理论探索。
例如,一些研究表明,通过优化刀具的设计和选择合适的切削参数,可以在一定程度上提高加工精度和加工速度。
另外,一些研究还介绍了采用精密测量设备和先进的控制系统来提高加工精度的方法。
CNC机床切削参数优化分析

CNC机床切削参数优化分析CNC机床是现代机械制造行业中不可或缺的设备,它的发展给制造行业带来了巨大的便利。
而CNC机床的切削参数优化是影响加工效率和产品质量的重要因素之一。
本文将对CNC机床切削参数进行分析和优化。
一、CNC机床切削参数的分类及影响因素CNC机床的切削参数包括进给速度、转速、切削深度和切削速度等。
根据其影响因素可以将其分为工件材料、刀具材料和加工工艺参数三类。
1.工件材料的影响工件材料是影响CNC机床切削参数的重要因素之一,其特性直接关系到切削力、表面质量和切削温度等。
在选择切削参数时,必须考虑工件材料的硬度、强度、粘着性等特性。
2.刀具材料的影响刀具材料也是影响CNC机床切削参数的重要因素之一。
刀具材料的硬度和抗磨性能直接关系到切削功率、表面质量和切削寿命等。
在选择刀具时,必须考虑刀具材料的硬度、抗磨性、导热性等特性。
3.加工工艺参数的影响加工工艺参数是影响CNC机床切削参数的关键因素之一。
加工工艺参数的选择直接影响切削力、表面粗糙度和工件成形等。
在选择加工工艺参数时,必须考虑切削速度、进给速度、切削深度和转速等参数的综合影响。
二、CNC机床切削参数的优化方法CNC机床切削参数的优化方法可以分为经验法和理论法两种。
1.经验法优化方法经验法是基于经验或试验数据来确定最优切削参数的方法。
其优点是操作简单、迅速,但其缺点是不够准确、不能用于不同工件材料和刀具材料的切削参数优化。
2.理论法优化方法理论法是基于数学模型和实验数据来确定最优切削参数的方法。
其优点是准确性高、可适用于不同的工件材料和刀具材料的切削参数优化。
常用的理论法优化方法有神经网络法、遗传算法和模拟退火算法等。
三、CNC机床切削参数优化实例以某企业的CNC机床为例,其加工工件是一种高强度的合金钢。
通过理论研究和实验数据的分析,得出如下优化方案:1.刀具选择选用耐磨钢材料制成的PCD刀具,其硬度和抗磨性能均优于其他刀具,能够提高加工效率和切削寿命。
CNC机床加工中的加工参数调整与优化

CNC机床加工中的加工参数调整与优化随着科技的不断进步和制造业的发展,计算机数控(CNC)机床在工业生产中扮演着越来越重要的角色。
CNC机床通过预先编程的方式控制工具和工件的相对运动,实现复杂零件的加工。
在CNC机床加工中,加工参数的调整和优化是提高加工质量和效率的关键。
一、加工参数的定义和影响因素CNC机床的加工参数包括切削速度、进给速度、进给量和切削深度等。
这些参数的选择和调整直接影响到加工效果和工件质量。
1. 切削速度切削速度是指刀具在工件上接触面上相对于工件表面的移动速度。
切削速度的选择与刀具材料、被加工材料和加工方式等因素有关。
合适的切削速度能够保持刀具寿命、提高加工效率和保证加工质量。
2. 进给速度进给速度是指工件在刀具上运动的速度。
进给速度的选择与刀具直径、被加工材料和切削深度等因素相关。
适当的进给速度能够保持刀具的寿命、减小加工周期并提高加工精度。
3. 进给量进给量是指刀具在过程中每一次接触工件的移动距离。
合适的进给量可以控制切削力和切削温度,从而影响加工的质量和效率。
4. 切削深度切削深度是指刀具在一次切削过程中切削轮廓的垂直距离。
切削深度的选择应该考虑到刀具的强度和创伤力等因素。
切削深度过大会增加切削力、温度和振动,降低切削质量。
二、加工参数调整的方法1. 经验法在实际生产中,经验法是最为常用和简便的调整加工参数的方法之一。
通过工人的经验和实践,根据不同的工件和加工要求,逐渐调整各个加工参数的数值,找到最佳的加工参数组合。
2. 实验法利用实验方法进行加工参数调整是一种科学且系统的方法。
通过合理设计实验方案,对不同参数组合进行实际加工,然后评估加工结果和质量,从而找到最优加工参数。
3. 仿真模拟法借助计算机软件进行CNC机床加工仿真模拟是一种高效且经济的方法。
在模拟软件中,可以根据加工要求和工件特点,调整各个加工参数的数值,然后模拟加工过程,评估加工效果并优化加工参数。
三、加工参数优化的技术手段1. 供应链优化加工参数优化不仅仅局限于CNC机床自身的加工参数调整,还包括整个供应链的优化。
CNC机床加工中的材料切削性能评估与选择

CNC机床加工中的材料切削性能评估与选择CNC机床在现代制造业中扮演着重要角色,它能够精确地进行复杂的切削加工。
然而,不同的材料对于CNC机床的切削性能有着不同的要求和表现。
因此,在选择CNC机床加工材料时,对材料的切削性能进行评估与选择是至关重要的。
本文将探讨CNC机床加工中的材料切削性能评估与选择的相关内容。
一、材料切削性能评估的指标1. 切削力:切削力是衡量材料在加工过程中所受到的力的大小。
切削力的大小直接影响到机床的切削效率和工具的寿命,并且会对加工表面质量产生一定影响。
2. 切削温度:材料在切削过程中会产生高温,高温会引起材料的塑性变形和软化,从而影响加工质量。
因此,切削温度是评估切削性能的重要指标之一。
3. 切削表面质量:切削表面质量是评估材料切削性能的重要指标,它直接关系到加工零件的质量和精度。
好的切削表面质量应是光滑、无毛刺和无裂纹的。
二、材料切削性能的选择原则1. 材料的物理性质:不同的材料具有不同的物理性质,如硬度、韧性和热导率等。
在选择材料时,需要根据具体的加工要求和机床的性能来确定合适的材料。
2. 加工条件的要求:不同的加工条件对材料的切削性能有着不同的要求。
例如,高速切削要求材料具有良好的热导率和高的软化温度,而硬质切削要求材料具有较高的硬度。
3. 加工表面质量的要求:加工表面质量要求高的零件需要选择具有良好切削性能的材料,以确保能够获得光滑无瑕疵的表面。
三、常用材料的切削性能评估与选择1. 黄铜:黄铜是一种常用的切削材料,具有良好的切削性能。
它的硬度适中,易于加工,并且具有较好的热导率和机械性能,适用于大多数的CNC机床切削工艺。
2. 不锈钢:不锈钢具有良好的耐腐蚀性和机械性能,但其切削性能相对较差。
由于不锈钢的硬度较高,切削时易产生较高的切削力和温度,因此需要选择适当的工艺参数和工具材料来保证切削表面质量。
3. 铝合金:铝合金具有较低的密度和良好的切削性能,是一种常用的切削材料。
CNC机床加工中的加工参数灵敏度分析与优化

CNC机床加工中的加工参数灵敏度分析与优化CNC机床是一种自动化加工设备,广泛应用于各个工业领域。
在CNC机床加工过程中,加工参数的设定对成品的质量和效率起着至关重要的作用。
本文将针对CNC机床加工中的加工参数进行灵敏度分析与优化,以提高加工过程的效能和产品质量。
一、加工参数的定义在CNC机床加工过程中,加工参数主要包括进给速度、切削速度、切削深度、刀具半径等。
这些参数的设定直接影响到加工过程中的切削力、刀具磨损、加工表面质量等因素。
二、加工参数的灵敏度分析加工参数的灵敏度是指在一定范围内改变一个加工参数,对加工结果的影响程度。
通过对加工参数的灵敏度进行分析,可以了解到不同参数的重要性和敏感性。
1. 进给速度的灵敏度分析进给速度是指工件在单位时间内的相对移动速度。
通过改变进给速度,可以调整加工过程中的切削速度和切削深度。
进给速度的灵敏度分析可以帮助我们确定最佳的进给速度范围,以提高加工效率和产品质量。
2. 切削速度的灵敏度分析切削速度是指刀具在单位时间内切削工件的线速度。
切削速度的大小直接影响切削力和刀具磨损。
通过对切削速度的灵敏度分析,可以确定最佳的切削速度范围,以实现最佳的切削效果。
3. 切削深度的灵敏度分析切削深度是指刀具每次切削进入工件的深度。
切削深度的改变会直接影响切削力和切削热量的分布,进而影响加工表面的质量与精度。
通过对切削深度的灵敏度分析,可以确定最佳的切削深度范围,以提高加工的效率和表面质量。
4. 刀具半径的灵敏度分析刀具半径是指刀具切削部分的半径值。
刀具半径的改变会导致切削力和切削面的形状发生变化,进而影响加工表面的粗糙度和尺寸精度。
通过对刀具半径的灵敏度分析,可以确定最佳的刀具半径范围,以提高加工表面的质量和精度。
三、加工参数的优化通过对加工参数的灵敏度分析,我们可以确定各个参数的重要性和敏感性。
基于此,我们可以进行加工参数的优化,以获得最佳的加工效果。
1. 基于优先级的参数优化根据加工参数的灵敏度分析结果,我们可以评估各个参数对加工结果的影响程度。
CNC机床加工中的加工精度与表面质量控制技术研究进展与应用实例分析
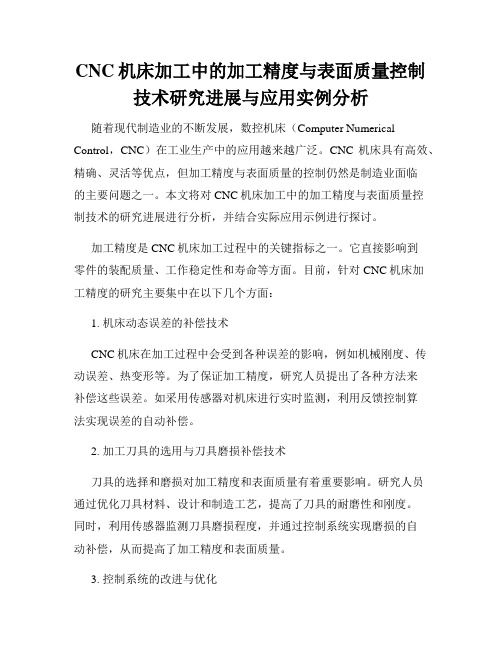
CNC机床加工中的加工精度与表面质量控制技术研究进展与应用实例分析随着现代制造业的不断发展,数控机床(Computer Numerical Control,CNC)在工业生产中的应用越来越广泛。
CNC机床具有高效、精确、灵活等优点,但加工精度与表面质量的控制仍然是制造业面临的主要问题之一。
本文将对CNC机床加工中的加工精度与表面质量控制技术的研究进展进行分析,并结合实际应用示例进行探讨。
加工精度是CNC机床加工过程中的关键指标之一。
它直接影响到零件的装配质量、工作稳定性和寿命等方面。
目前,针对CNC机床加工精度的研究主要集中在以下几个方面:1. 机床动态误差的补偿技术CNC机床在加工过程中会受到各种误差的影响,例如机械刚度、传动误差、热变形等。
为了保证加工精度,研究人员提出了各种方法来补偿这些误差。
如采用传感器对机床进行实时监测,利用反馈控制算法实现误差的自动补偿。
2. 加工刀具的选用与刀具磨损补偿技术刀具的选择和磨损对加工精度和表面质量有着重要影响。
研究人员通过优化刀具材料、设计和制造工艺,提高了刀具的耐磨性和刚度。
同时,利用传感器监测刀具磨损程度,并通过控制系统实现磨损的自动补偿,从而提高了加工精度和表面质量。
3. 控制系统的改进与优化CNC机床的控制系统是实现加工精度和表面质量控制的关键。
研究人员通过改进控制算法、提高控制系统的响应速度等手段,不断优化控制系统的性能。
同时,引入先进的传感器和测量技术,实时监测和调整加工过程中的参数,提高了加工精度和表面质量。
表面质量是衡量零件加工质量的重要指标。
在CNC机床加工中,表面质量的控制主要包括以下方面:1. 加工参数的优化加工参数对于表面质量有着重要影响,例如进给速度、切削速度、进给深度等。
通过优化加工参数,可以降低表面粗糙度和提高加工质量。
2. 先进的切削工具与润滑技术选择合适的切削工具和润滑技术对于提高表面质量非常重要。
现代切削工具采用先进的涂层技术和设计,使得切削过程更加稳定、光滑。
CNC机床加工中的切削力分析与优化
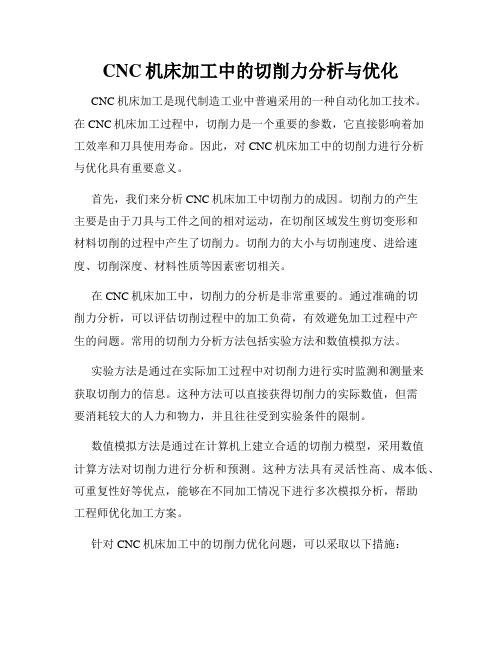
CNC机床加工中的切削力分析与优化CNC机床加工是现代制造工业中普遍采用的一种自动化加工技术。
在CNC机床加工过程中,切削力是一个重要的参数,它直接影响着加工效率和刀具使用寿命。
因此,对CNC机床加工中的切削力进行分析与优化具有重要意义。
首先,我们来分析CNC机床加工中切削力的成因。
切削力的产生主要是由于刀具与工件之间的相对运动,在切削区域发生剪切变形和材料切削的过程中产生了切削力。
切削力的大小与切削速度、进给速度、切削深度、材料性质等因素密切相关。
在CNC机床加工中,切削力的分析是非常重要的。
通过准确的切削力分析,可以评估切削过程中的加工负荷,有效避免加工过程中产生的问题。
常用的切削力分析方法包括实验方法和数值模拟方法。
实验方法是通过在实际加工过程中对切削力进行实时监测和测量来获取切削力的信息。
这种方法可以直接获得切削力的实际数值,但需要消耗较大的人力和物力,并且往往受到实验条件的限制。
数值模拟方法是通过在计算机上建立合适的切削力模型,采用数值计算方法对切削力进行分析和预测。
这种方法具有灵活性高、成本低、可重复性好等优点,能够在不同加工情况下进行多次模拟分析,帮助工程师优化加工方案。
针对CNC机床加工中的切削力优化问题,可以采取以下措施:1. 优化切削参数。
切削参数是影响切削力的重要因素,通过合理调整切削速度、进给速度、切削深度等参数,可以减小切削力的大小,提高加工效率。
在实际加工中,可以根据不同材料和刀具的特性进行切削参数的优化选择。
2. 选择合适的刀具形状和材料。
刀具的形状和材料也会对切削力产生影响。
合理选择刀具形状和材料,可以降低切削力的大小,提高切削效果。
此外,刀具的磨损情况也需要及时检测和更换,以保证切削力的有效控制。
3. 采用液体冷却剂。
在切削过程中,液体冷却剂的使用可以有效降低切削区域的温度,减小变形和磨损,从而降低切削力的大小。
选用适当的冷却液,并合理控制冷却液的供给,可以达到优化切削力的效果。
CNC机床加工中的切削力分析与控制
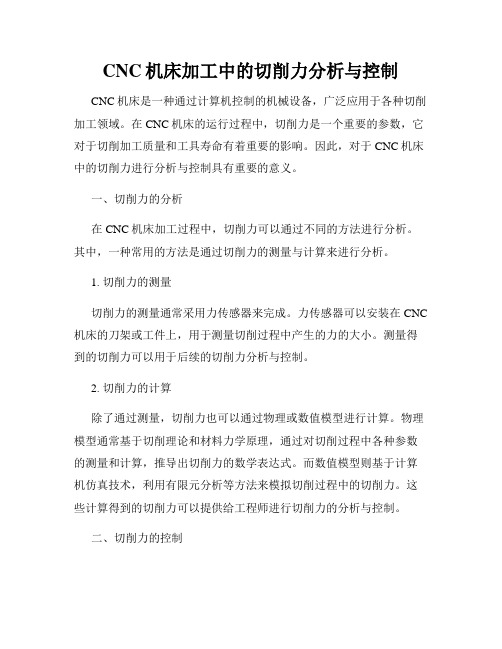
CNC机床加工中的切削力分析与控制CNC机床是一种通过计算机控制的机械设备,广泛应用于各种切削加工领域。
在CNC机床的运行过程中,切削力是一个重要的参数,它对于切削加工质量和工具寿命有着重要的影响。
因此,对于CNC机床中的切削力进行分析与控制具有重要的意义。
一、切削力的分析在CNC机床加工过程中,切削力可以通过不同的方法进行分析。
其中,一种常用的方法是通过切削力的测量与计算来进行分析。
1. 切削力的测量切削力的测量通常采用力传感器来完成。
力传感器可以安装在CNC 机床的刀架或工件上,用于测量切削过程中产生的力的大小。
测量得到的切削力可以用于后续的切削力分析与控制。
2. 切削力的计算除了通过测量,切削力也可以通过物理或数值模型进行计算。
物理模型通常基于切削理论和材料力学原理,通过对切削过程中各种参数的测量和计算,推导出切削力的数学表达式。
而数值模型则基于计算机仿真技术,利用有限元分析等方法来模拟切削过程中的切削力。
这些计算得到的切削力可以提供给工程师进行切削力的分析与控制。
二、切削力的控制在CNC机床加工中,切削力的控制是非常重要的。
通过合理控制切削力的大小,可以提高切削加工的精度和效率,同时也能够延长刀具和设备的使用寿命。
1. 选择合适的切削参数切削参数是切削加工中影响切削力的重要因素之一。
通过选择合适的切削参数,如进给速度、切削深度和切削速度等,可以有效地控制切削力的大小。
例如,减小切削深度和提高进给速度可以降低切削力的大小。
2. 优化刀具设计刀具是进行切削加工的重要工具。
通过优化刀具的设计,可以降低切削力的产生与传递。
例如,采用合适的刀具几何形状和刀具材料,可以减小切削面积和切削力的大小。
3. 应用切削力反馈控制切削力反馈控制是一种先进的切削力控制方法。
它通过实时测量切削力,并将测量值与设定值进行比较,然后通过调整切削参数来控制切削力的大小。
这种方法可以实现对切削力的精确控制,提高切削加工的稳定性和精度。
CNC机床加工中的加工力学与切削理论
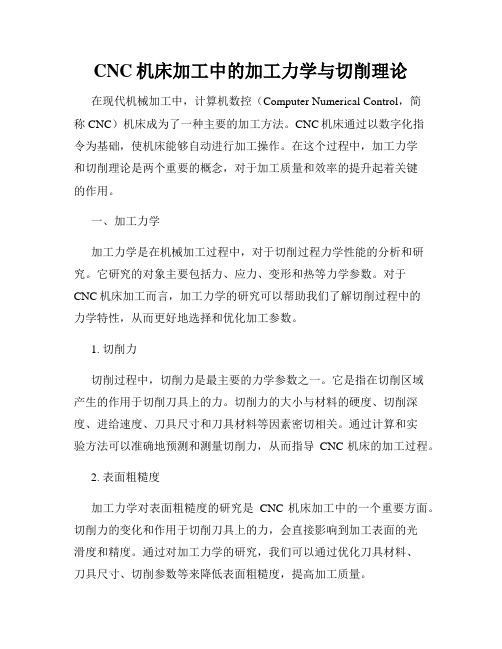
CNC机床加工中的加工力学与切削理论在现代机械加工中,计算机数控(Computer Numerical Control,简称CNC)机床成为了一种主要的加工方法。
CNC机床通过以数字化指令为基础,使机床能够自动进行加工操作。
在这个过程中,加工力学和切削理论是两个重要的概念,对于加工质量和效率的提升起着关键的作用。
一、加工力学加工力学是在机械加工过程中,对于切削过程力学性能的分析和研究。
它研究的对象主要包括力、应力、变形和热等力学参数。
对于CNC机床加工而言,加工力学的研究可以帮助我们了解切削过程中的力学特性,从而更好地选择和优化加工参数。
1. 切削力切削过程中,切削力是最主要的力学参数之一。
它是指在切削区域产生的作用于切削刀具上的力。
切削力的大小与材料的硬度、切削深度、进给速度、刀具尺寸和刀具材料等因素密切相关。
通过计算和实验方法可以准确地预测和测量切削力,从而指导CNC机床的加工过程。
2. 表面粗糙度加工力学对表面粗糙度的研究是CNC机床加工中的一个重要方面。
切削力的变化和作用于切削刀具上的力,会直接影响到加工表面的光滑度和精度。
通过对加工力学的研究,我们可以通过优化刀具材料、刀具尺寸、切削参数等来降低表面粗糙度,提高加工质量。
二、切削理论切削理论是关于切削加工中刀具与工件间相互作用的研究。
它是基于切削力学原理的理论体系,可以帮助我们深入理解CNC机床加工中刀具与工件的相互作用过程。
1. 切削速度切削速度是切削理论中的一个重要参数。
它是指切削刀具与工件间相对运动的速度。
切削速度的选择与加工材料的硬度、切削力的大小以及刀具材料等有关。
通过合理选择切削速度,我们可以提高加工效率,同时保证加工质量。
2. 切削力分析切削力分析是切削理论中的另一个重要方面。
通过对切削力的分析,我们可以了解切削过程中发生的力学变化,包括切削力的大小、方向和变化规律等。
切削力分析可以帮助我们改进刀具设计和优化切削参数,提高加工的稳定性和精度。
CNC机床加工中的切削力模拟与优化
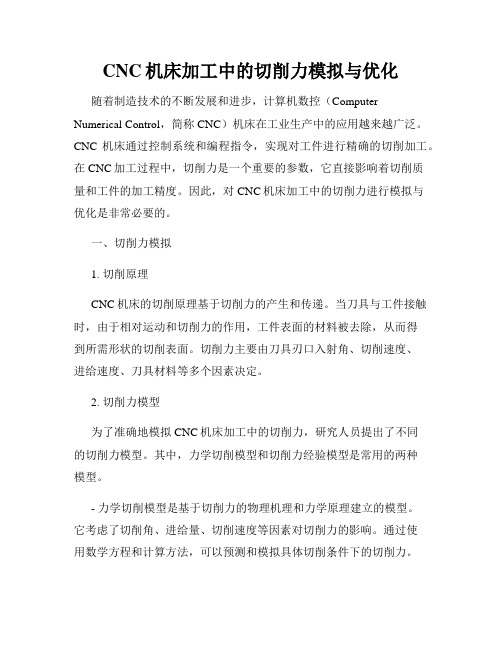
CNC机床加工中的切削力模拟与优化随着制造技术的不断发展和进步,计算机数控(Computer Numerical Control,简称CNC)机床在工业生产中的应用越来越广泛。
CNC机床通过控制系统和编程指令,实现对工件进行精确的切削加工。
在CNC加工过程中,切削力是一个重要的参数,它直接影响着切削质量和工件的加工精度。
因此,对CNC机床加工中的切削力进行模拟与优化是非常必要的。
一、切削力模拟1. 切削原理CNC机床的切削原理基于切削力的产生和传递。
当刀具与工件接触时,由于相对运动和切削力的作用,工件表面的材料被去除,从而得到所需形状的切削表面。
切削力主要由刀具刃口入射角、切削速度、进给速度、刀具材料等多个因素决定。
2. 切削力模型为了准确地模拟CNC机床加工中的切削力,研究人员提出了不同的切削力模型。
其中,力学切削模型和切削力经验模型是常用的两种模型。
- 力学切削模型是基于切削力的物理机理和力学原理建立的模型。
它考虑了切削角、进给量、切削速度等因素对切削力的影响。
通过使用数学方程和计算方法,可以预测和模拟具体切削条件下的切削力。
- 切削力经验模型则是基于实验数据和经验规律得出的模型。
它通过对大量实验数据的分析和统计,建立了与切削参数相关的经验公式,从而可以在实际加工中推算出切削力的大小。
3. 切削力模拟软件为了更加方便地进行切削力模拟和优化设计,研究人员开发了各种切削力模拟软件。
这些软件基于先进的建模和仿真技术,结合丰富的切削力模型库,可以对不同类型的CNC机床加工过程进行精确的切削力模拟,为工艺优化提供依据。
二、切削力优化1. 刀具选择和切削参数优化切削力的大小很大程度上取决于刀具的选择和切削参数的设置。
在CNC机床加工中,选择合适的刀具材料、刀具形状和刀具涂层对降低切削力非常重要。
此外,合理控制切削速度、进给速度和切削深度等切削参数,也是优化切削力的关键。
2. 机床结构优化CNC机床的结构特性也会对切削力产生影响。
CNC机床加工中的加工强度分析与优化

CNC机床加工中的加工强度分析与优化在现代工业制造中,CNC机床被广泛应用于各个领域的零件加工和生产中。
在CNC机床的运行过程中,加工强度是一个至关重要的因素。
本文将分析CNC机床加工中的加工强度,并提出相应的优化方法。
一、CNC机床加工中的加工强度CNC机床加工中的加工强度指的是在加工过程中所需的切削力和切削热以及相应的应力和温度等参数。
加工强度的大小直接影响着零件加工质量和机床的寿命等因素。
1. 切削力的分析在CNC机床的切削过程中,刀具对工件的切削力是一个重要的参数。
切削力的大小与切削液的使用、刀具状况、切削速度和进给速度等因素有关。
通过对切削力的分析,可以评估加工强度的大小,并在加工过程中进行相应的优化。
2. 切削热的分析在CNC机床的切削过程中,会产生大量的切削热。
切削热的积累不仅会影响加工精度,还会导致零件表面质量的下降,甚至引起刀具的热破坏。
因此,对切削热的分析与控制是非常必要的。
二、加工强度优化方法为了提高CNC机床加工的效率和质量,需要对加工强度进行优化。
下面将介绍几种常用的加工强度优化方法。
1. 材料选择和切削参数优化首先,材料的选择对于加工强度的优化非常重要。
合理选择加工材料可以降低切削力和切削热的产生,减轻机床负荷,提高加工效率和质量。
同时,对切削参数进行优化也是必不可少的。
合理的切削速度和进给速度可以有效控制切削力和切削热的产生,并减少切削过程中的应力和温度。
2. 刀具的选择和刀具磨损的监测选择合适的刀具也是加工强度优化的关键。
优质的刀具可以降低切削力和切削热的产生,提高零件加工的精度和表面质量。
另外,刀具磨损的监测也是非常重要的。
及时更换磨损严重的刀具可以避免刀具断裂和加工质量下降的问题。
3. 加工液的使用和冷却系统的改进合适的加工液对于降低切削力和切削热的产生起着重要的作用。
加工液的使用可以有效冷却切削区域,降低切削温度,减轻切削应力,保证加工质量。
同时,改进冷却系统的设计和布置也是加工强度优化的一项重要工作。
CNC机床加工中的加工力与工具磨损关系分析
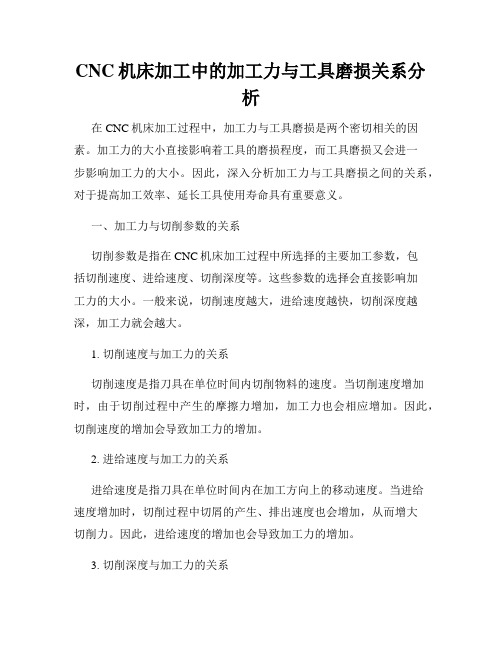
CNC机床加工中的加工力与工具磨损关系分析在CNC机床加工过程中,加工力与工具磨损是两个密切相关的因素。
加工力的大小直接影响着工具的磨损程度,而工具磨损又会进一步影响加工力的大小。
因此,深入分析加工力与工具磨损之间的关系,对于提高加工效率、延长工具使用寿命具有重要意义。
一、加工力与切削参数的关系切削参数是指在CNC机床加工过程中所选择的主要加工参数,包括切削速度、进给速度、切削深度等。
这些参数的选择会直接影响加工力的大小。
一般来说,切削速度越大,进给速度越快,切削深度越深,加工力就会越大。
1. 切削速度与加工力的关系切削速度是指刀具在单位时间内切削物料的速度。
当切削速度增加时,由于切削过程中产生的摩擦力增加,加工力也会相应增加。
因此,切削速度的增加会导致加工力的增加。
2. 进给速度与加工力的关系进给速度是指刀具在单位时间内在加工方向上的移动速度。
当进给速度增加时,切削过程中切屑的产生、排出速度也会增加,从而增大切削力。
因此,进给速度的增加也会导致加工力的增加。
3. 切削深度与加工力的关系切削深度是指每次切削中刀具与工件之间的距离。
切削深度的增加会导致切削削面积的增加,从而增大切削力。
因此,切削深度的增加也会导致加工力的增加。
二、加工力与工具磨损的关系工具磨损是指在CNC机床加工过程中由于与工件的相互作用而导致的刀具表面的磨损现象。
加工力的大小对工具磨损具有直接影响。
1. 加工力的增大与工具磨损的关系加工力的增大会导致刀具受到更大的应力,从而加速刀具的磨损。
特别是在高切削速度、进给速度和深度等情况下,由于加工力的增大,工具磨损会更加明显。
2. 工具磨损对加工力的影响工具磨损会改变刀具的几何特征和切削能力,从而影响加工力的大小。
当工具磨损严重时,刀具几何特征的变化会导致加工力的增加。
因此,及时检测和处理工具磨损对于控制加工力具有重要意义。
三、加工力与工艺优化的关系加工力的大小直接影响着加工质量和工具使用寿命。
CNC坐标磨床全干式切削加工性能的分析
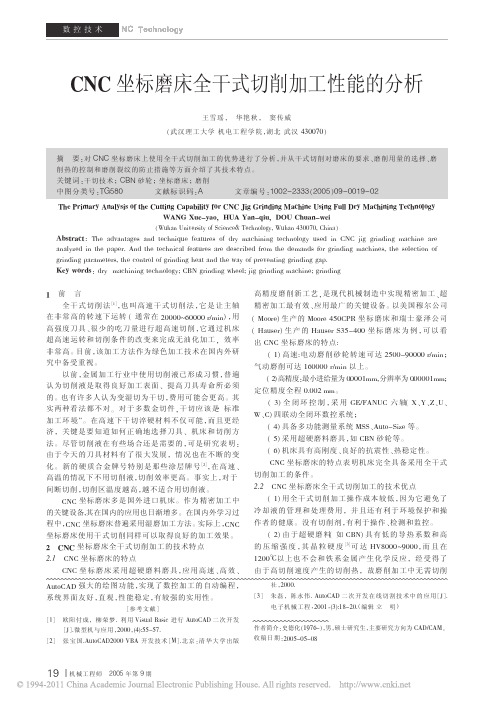
#< $
!!!!!!!!!! 作者简介%史德化&=A;B%’!男!硕士研究生!主要研究方向为 %12C%1D "
收稿日期 %3449:49:4>
!"
机械工程师
(%%+ 年第 $ 期
!" #$%&’()(*+
数控技术
液对砂轮进行冷却 ! 相反 " 由于干切产生的高温使工件材 料硬度降低较多 " 较高的温度使工件材料软化 " 刀具工件 间硬度差增大使切削加工更易进行 "切削效率更高 ! # !$ 一般 所 采 用 的 湿 磨 法 " 无 论 如 何 注 入 切 削 液 " 切 削液都不可能在磨削的同时进入磨削面 " 因而无法降低 磨削点位置的磨削热 % 切削液只能使砂轮和零件的磨削 点在磨削走过后瞬时受到冷却 " 同时切削液对零件的磨 削点起淬火作用 " 因而事实上加大了磨削裂纹的产生 ! 在
2由于超硬磨料如cbn具有低的导热系数和高的压缩强度其晶粒硬度口1可达hv80009000而且在1200以上也不会和铁系金属产生化学反应经受得了由于高切削速度产生的切削热故磨削加工中无需切削autocad强大的绘图功能实现了数控加工的自动编程系统界面友好直观性能稳定有较强的实用性
数控技术
!" #$%&’()(*+
& =’ 用全干式切削加工操作成本较低 ! 因为它避免了
%H% 坐标磨床多是国外进口机床 " 作为精密加工中 的关键设备I其在国内的应用也日渐增多" 在国内外学习过 程中 !%H% 坐标磨床普遍采用湿磨加工方法 " 实际上 !%H%
坐标磨床使用干式切削同样可以取得良好的加工效果 "
CNC坐标磨床全干式切削加工性能的分析

CNC坐标磨床全干式切削加工性能的分析
王雪瑶;华艳秋;窦传威
【期刊名称】《机械工程师》
【年(卷),期】2005(000)009
【摘要】对CNC坐标磨床上使用全干式切削加工的优势进行了分析,并从干式切削对磨床的要求、磨削用量的选择、磨削热的控制和磨削裂纹的防止措施等方面介绍了其技术特点.
【总页数】2页(P19-20)
【作者】王雪瑶;华艳秋;窦传威
【作者单位】武汉理工大学,机电工程学院,湖北,武汉,430070;武汉理工大学,机电工程学院,湖北,武汉,430070;武汉理工大学,机电工程学院,湖北,武汉,430070
【正文语种】中文
【中图分类】TG580
【相关文献】
1.基于全干式的CNC坐标磨床切削加工 [J], 焦红卫
2.六坐标CNC工具磨床的上位机与多位置环的握手通信 [J], 周宏甫;张立三
C坐标磨床Z轴的开发 [J], 蔡廷宇
4.五坐标联动CNC砂带磨床的研制 [J], 全荣;陈尔昌
5.用CNC坐标磨床制造模具的实例 [J], 傅信国
因版权原因,仅展示原文概要,查看原文内容请购买。
- 1、下载文档前请自行甄别文档内容的完整性,平台不提供额外的编辑、内容补充、找答案等附加服务。
- 2、"仅部分预览"的文档,不可在线预览部分如存在完整性等问题,可反馈申请退款(可完整预览的文档不适用该条件!)。
- 3、如文档侵犯您的权益,请联系客服反馈,我们会尽快为您处理(人工客服工作时间:9:00-18:30)。
数控技术
!" #$%&’()(*+
!"! 坐标磨床全干式切削加工性能的分析
王雪瑶 ! 华艳秋 ! 窦传威 & 武汉理工大学 机电工程学院 ! 湖北 武汉 6<44;4 ’
摘
要 %对 !"! 坐标磨床上使用全干式切削加工的优势进行了分析 ! 并从干式切削对磨床的要求 ( 磨削用量的选择 ( 磨
削热的控制和磨削裂纹的防止措施等方面介绍了其技术特点 "
面的温度 )<*可能高达 @(6%&@56% 或更高 % 淬火钢中的残 余奥氏体 " 在磨削时受磨削热的影响即发生分解 " 逐渐转 变为马氏体 " 这种新生的马氏体集中于表面 " 引起零件局 部 体 积 膨 胀 " 加 大了 零 件 表 面 应 力 " 导 致 磨 削 应 力 集 中 " 继续磨削则容易加速磨削裂纹的产生 ’ 此外 " 新生的马氏 体脆性较大 " 磨削也容易加速磨削裂纹的产生 % 另一方 面 " 在磨床上磨削工件时 " 对工件既是压力 " 又是拉力 " 助 长了磨削裂纹的形成 % 所以降低磨削热是解决磨削裂纹 的关键 % 如下措施可有效防止磨削裂纹的产生 ( # *$ 产生 磨 削 裂 纹 的 根 本 原 因 在 于 淬 火 件 的 马 氏 体 组织是一种膨胀状态 " 有应力存在 " 要减少和消除这种应 力 " 工件应进行去应力回火即淬火后应马上进行回火处 理 % 有时经过一次回火后仍可能产生磨削裂纹 " 这时可 以进行二次回火或人工时效 " 这个方法非常有效 % 如果零 件硬度要求不高 " 而零件外观表面要求较高时 " 可以将回 火温度 提 高 到 566% 以 上 " 即 调 质 处 理 " 这 时 零 件 表 面 将 不会再出现磨削裂纹现象 % # ($ 刚 出 炉 的 工 件 " 必 须 待 工 件 自 然 冷 却 至 常 温 后 才能进行磨削 % 在时间允许的情况下 " 最好让工件自然时 效一段时间 " 消除应力后再进行磨削 " 这也会收到很好的 效果 % # 2$ 干磨时 " 选用粒度较大 & 锋利的砂轮 " 增加磨削次 数"减少背吃刀量"减小工作台移动速度"可减少磨削裂纹 %
"&# 砂轮高的磨削效率 " 使磨削比降低 " 而磨削比降低意
味着磨削加工成本大幅地提高 ! 磨床刚度低易产生严重 的 粘 屑 " 而 使 "&# 砂 轮 不 能 进 行 正 常 磨 削 " 需 修 整 后 才 能进行磨削工作 ! 磨床刚度低易发生振动 % 尤其是磨屑粘 附时 % 振动会更加严重 " 对加工表面产生振纹和烧伤 % 使表 面粗糙度急剧增加 " 工件表面质量严重恶化 !
全干式切削法 #=$! 也叫高速干式切 削 法 ! 它是 让 主 轴 在非常高的转速下运转 & 通常在 34444&B4444 ECF)G’ ! 用 高强度刀具 ( 很少的吃刀量进行超高速切削 ! 它通过机床 超高速运转和切削条件的改变来完成无油化加工 ! 效率 非常高 " 目前 ! 该加工方法作为绿色加工技术在国内外研 究中备受重视 " 以前 ! 金属加工行业中使用切削液已形成习惯 ! 普遍 认为切削液是取得良好加工表面 ( 提高刀具寿命所必须 的 " 也有许多人认为变湿切为干切 ! 费用可能会更高 " 其 实两种看法都不对 " 对于多数金切件 ! 干切应该是 ) 标准 加工环境 *" 在高速下干切淬硬材料不仅可能 ! 而且更经 济 ! 关键是要知道如何正确地选择刀具 ( 机床和切削方 法 " 尽管切削液在有些场合还是需要的 ! 可是研究表明 % 由于今天的刀具材料有了很大发展 ! 情况也在不断的变 化 " 新的硬质合金牌号特别是那些涂层牌号 #3$! 在 高 速 ( 高温的情况下不用切削液 ! 切削效率更高 " 事实上 !对于 间断切削 ! 切削区温度越高 ! 越不适合用切削液 "
#< $
!!!!!!!!!! 作者简介%史德化&=A;B%’!男!硕士研究生!主要研究方向为 %12C%1D "
收稿日期 %3449:49:4>
!"
机械工程师
(%%+ 年第 $ 期
!" #$%&’()(*&冷却 ! 相反 " 由于干切产生的高温使工件材 料硬度降低较多 " 较高的温度使工件材料软化 " 刀具工件 间硬度差增大使切削加工更易进行 "切削效率更高 ! # !$ 一般 所 采 用 的 湿 磨 法 " 无 论 如 何 注 入 切 削 液 " 切 削液都不可能在磨削的同时进入磨削面 " 因而无法降低 磨削点位置的磨削热 % 切削液只能使砂轮和零件的磨削 点在磨削走过后瞬时受到冷却 " 同时切削液对零件的磨 削点起淬火作用 " 因而事实上加大了磨削裂纹的产生 ! 在
&W"[+G SG)\JE*)0] $^ O.)JG.J_ ‘J.[G$,$a]I W"[+G 6<??;?I %[)G+ ’
!"#$%&’$% ‘[J +b\NG0NaJ* NGb 0J.[G)c"J ^JN0"EJ* $^ bE] FN.[)G)Ga 0J.[G$,$a] "*Jb )G %H% def fEeGg)Gf FNh[)Gi NEi NGN,]Zig )G 0[i jNjiE@ 1Gg 0[i 0ih[G)hN, kiN0"Ei* NEi gi*hE)lig kE$F 0[i giFNGg* k$E aE)Gg)Ga FNh[)Gi*I 0[i *i,ih0)$G $k aE)Gg)Ga jNENFi0iE*I 0[i h$G0E$, $k aE)Gg)Ga [iN0 NGg 0[i mN] $k jEi\iG0)Ga aE)Gg)Ga aNj@ ()* +,%-# % gE] FNh[)G)Ga 0ih[G$,$a]n %-H aE)Gg)Ga m[ii,n d)a aE)Gg)Ga FNh[)Gin aE)Gg)Ga
"#" 坐标磨床上使用全干式切削 " 利用砂轮的高速运转
可 以 减 少 刀 具 与 工 件 发热 区 的 接 触 时 间 和 接 触 面 积 " 撕 裂下来的切屑以极快的速度脱离工件 & 把热量带走 " 能有 效控制热传导 "防止磨削裂纹产生 "提高砂轮的使用寿命 !
!!%
磨削裂纹的防止措施 磨削裂纹的产生是因为磨削热所致 " 磨削时 " 零件表
关键词 %干切技术 + !#" 砂轮 + 坐标磨床 + 磨削 中图分类号 %!"#$% 文献标识码 %&
文章编号 %’%%()(*** &(%%+ ’%$)%%,-)%(
%&’ ()*+,)- ./,0-1*1 23 4&’ !544*/6 !,7,8*0*4- 32) !"! 9*6 :)*/;*/6 <,=&*/’ >1*/6 ?500 @)- <,=&*/*/6 %’=&/2026A.": B5’C-,2D E>. F,/CG*5D @H> !&5,/CI’*
!!# 磨削用量的选择 !’()* "$# 砂轮速度
在 "#" 坐标 磨 床 上 使 用 "$# 砂 轮 进 行 全 干 式 切削 加 工 时 " 要 选 用 高 的 砂 轮 速 度 " 以 充 分 发 挥 "$# 砂 轮 的 切削能力 ! 在较高的砂轮速度下 " 不仅能显著提高 "$# 的 磨 削 效率 " 提 高 磨 削 比 " 而 且 能 降 低 磨 削 力 " 减少 功 率 消耗 " 改善工件磨削表面的粗糙度 ! 砂轮速度越高 " 工件 表面粗糙度值越小 " 使切向和法向磨削力下降 " 这样就减 少了单个磨粒上承受的力 " 因而砂轮磨损减少 & 磨削热降 低 ! 在 +,-./0 1234566 坐标磨床上 " 一般取 "&# 砂轮速 度为 *(6 7879: !
!!!!!!!!!!!!!!!!!!!!!!!!!!!!!!!!!!!!!!!!!!!!!!!!!!!!!!!!! 社 !3444’ !"#$%!& 强大的绘图功能 ! 实现了数控加工的自动编程 !
系统界面友好 ! 直观 !性能稳定 !有较强的实用性 "
# 参考文献 $ #!$ #3 $ 欧阳付成 ! 柳荣梦 ’ 利用 ()*"+, -+*). 进行 /"0$%12 二 次开 发 #" $’ 微型机与应用 !3444 !567899:9;’ 张 宝 国 ’1"0$%1&3444 (-1 开 发 技 术 ## $’ 北 京 % 清 华 大 学 出 版
& =’ 用全干式切削加工操作成本较低 ! 因为它避免了
%H% 坐标磨床多是国外进口机床 " 作为精密加工中 的关键设备I其在国内的应用也日渐增多" 在国内外学习过 程中 !%H% 坐标磨床普遍采用湿磨加工方法 " 实际上 !%H%