金属切削工艺中冷却液的选择与性能分析
金属切削原理与刀具内冷却设计的综述
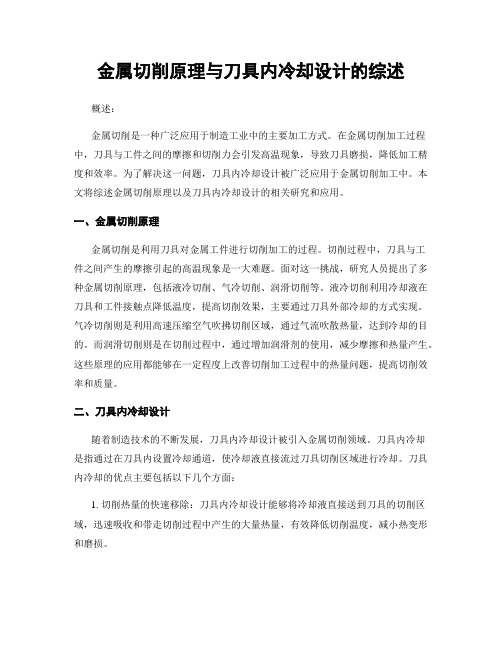
金属切削原理与刀具内冷却设计的综述概述:金属切削是一种广泛应用于制造工业中的主要加工方式。
在金属切削加工过程中,刀具与工件之间的摩擦和切削力会引发高温现象,导致刀具磨损,降低加工精度和效率。
为了解决这一问题,刀具内冷却设计被广泛应用于金属切削加工中。
本文将综述金属切削原理以及刀具内冷却设计的相关研究和应用。
一、金属切削原理金属切削是利用刀具对金属工件进行切削加工的过程。
切削过程中,刀具与工件之间产生的摩擦引起的高温现象是一大难题。
面对这一挑战,研究人员提出了多种金属切削原理,包括液冷切削、气冷切削、润滑切削等。
液冷切削利用冷却液在刀具和工件接触点降低温度,提高切削效果,主要通过刀具外部冷却的方式实现。
气冷切削则是利用高速压缩空气吹拂切削区域,通过气流吹散热量,达到冷却的目的。
而润滑切削则是在切削过程中,通过增加润滑剂的使用,减少摩擦和热量产生。
这些原理的应用都能够在一定程度上改善切削加工过程中的热量问题,提高切削效率和质量。
二、刀具内冷却设计随着制造技术的不断发展,刀具内冷却设计被引入金属切削领域。
刀具内冷却是指通过在刀具内设置冷却通道,使冷却液直接流过刀具切削区域进行冷却。
刀具内冷却的优点主要包括以下几个方面:1. 切削热量的快速移除:刀具内冷却设计能够将冷却液直接送到刀具的切削区域,迅速吸收和带走切削过程中产生的大量热量,有效降低切削温度,减小热变形和磨损。
2. 增加切削速度:刀具内冷却可以使切削温度下降,降低了刀具的磨损速度和损伤程度,从而允许更高的切削速度,提高加工效率。
3. 改善切削质量:通过刀具内冷却设计,可以减少切削过程中产生的切削热影响区,降低切削温度梯度,减小切削应力分布的不均匀性,提高加工表面质量和尺寸精度。
刀具内冷却设计的关键问题包括冷却液的供应方式、冷却通道的布置和尺寸优化以及冷却液的流动特性等。
目前,研究人员通过数值模拟和实验研究,不断改进刀具内冷却系统的设计,并提出了一系列优化方案,以提高刀具内冷却的效果。
mql的冷却标准
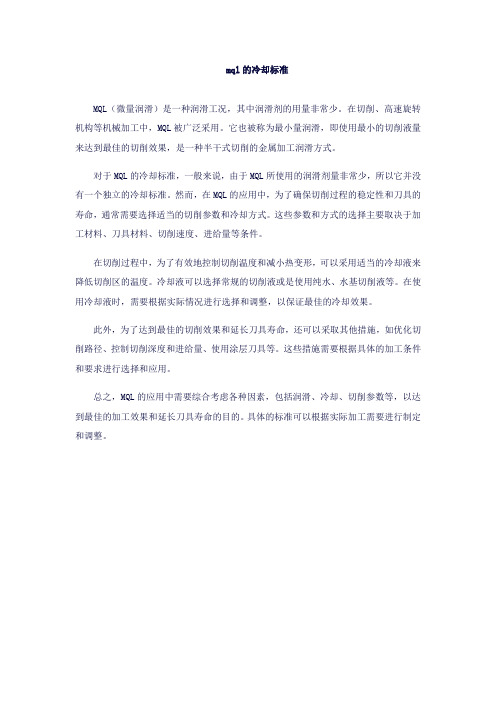
mql的冷却标准
MQL(微量润滑)是一种润滑工况,其中润滑剂的用量非常少。
在切削、高速旋转机构等机械加工中,MQL被广泛采用。
它也被称为最小量润滑,即使用最小的切削液量来达到最佳的切削效果,是一种半干式切削的金属加工润滑方式。
对于MQL的冷却标准,一般来说,由于MQL所使用的润滑剂量非常少,所以它并没有一个独立的冷却标准。
然而,在MQL的应用中,为了确保切削过程的稳定性和刀具的寿命,通常需要选择适当的切削参数和冷却方式。
这些参数和方式的选择主要取决于加工材料、刀具材料、切削速度、进给量等条件。
在切削过程中,为了有效地控制切削温度和减小热变形,可以采用适当的冷却液来降低切削区的温度。
冷却液可以选择常规的切削液或是使用纯水、水基切削液等。
在使用冷却液时,需要根据实际情况进行选择和调整,以保证最佳的冷却效果。
此外,为了达到最佳的切削效果和延长刀具寿命,还可以采取其他措施,如优化切削路径、控制切削深度和进给量、使用涂层刀具等。
这些措施需要根据具体的加工条件和要求进行选择和应用。
总之,MQL的应用中需要综合考虑各种因素,包括润滑、冷却、切削参数等,以达到最佳的加工效果和延长刀具寿命的目的。
具体的标准可以根据实际加工需要进行制定和调整。
机加工冷却液主要成分

机加工冷却液主要成分机加工冷却液是一种广泛应用于机械加工过程中的液体,它能够有效地降低加工过程中的摩擦、热量以及切削工具的磨损,从而提高加工的效率和质量。
机加工冷却液的主要成分在很大程度上决定了其性能和适用范围。
本文将讨论机加工冷却液的主要成分,并解释它们在加工过程中的作用。
1. 水水是机加工冷却液中最主要的成分。
它具有良好的导热性和热容量,能够吸收和分散加工过程中产生的热量。
此外,水还能够冲洗加工区域,清除切屑和废料,确保加工的顺利进行。
但水的使用也存在一些问题,比如腐蚀性较强,容易导致金属零件生锈,因此需要添加其他成分来改善其性能。
2. 润滑剂润滑剂是机加工冷却液中的重要成分之一。
它能够减少切削工具和工件之间的摩擦,降低切削力和磨损,延长工具的使用寿命。
常见的润滑剂有油脂、酯类和聚合物等。
润滑剂的选择应根据加工材料和加工方式来确定,以确保最佳的润滑效果。
3. 防锈剂防锈剂是为了防止机加工冷却液中的金属零件生锈而添加的成分。
它能够在金属表面形成一层保护膜,防止氧气和水的接触,从而减缓金属的腐蚀速度。
常见的防锈剂有有机酸、磷酸盐和硝酸盐等。
4. 抗菌剂机加工冷却液中的水分和有机成分为微生物的生长提供了良好的条件,因此需要添加抗菌剂来防止细菌和真菌的滋生。
常见的抗菌剂有甲醛、苯胺和二氧化氯等。
抗菌剂的添加量应根据冷却液的使用环境和寿命来确定,以保证冷却液的稳定性和安全性。
5. pH调节剂机加工冷却液的pH值对其性能和稳定性有着重要影响。
过高或过低的pH值都会导致冷却液的腐蚀性增强或增加其对金属的刺激性。
因此,需要添加pH调节剂来维持冷却液的稳定性。
常见的pH调节剂有磷酸盐、碱性物质和有机酸等。
6. 抗氧化剂机加工冷却液中的氧气会导致液体的氧化和降解,影响其使用寿命和性能。
抗氧化剂的添加可以有效地延长冷却液的使用寿命,并保持其稳定性。
常见的抗氧化剂有苯酚、硫醇和硝酸盐等。
7. 乳化剂机加工冷却液中的水和润滑剂通常不易混合,需要添加乳化剂来促使两者充分混合,并形成稳定的乳化液。
CNC机床加工中的冷却液应用与优化

CNC机床加工中的冷却液应用与优化冷却液在CNC(数控)机床加工中起着至关重要的作用。
它不仅可以有效降低温度,还能减少摩擦、延长工具寿命,并且改善加工表面质量。
本文将探讨CNC机床加工中冷却液的应用和优化方法,以提高加工效率和降低成本。
一、冷却液的选择与应用在CNC机床加工中,冷却液的选择是至关重要的。
首先,要根据加工材料和工艺要求选择合适的冷却液。
对于不同材料和不同加工方式,冷却液的性能要求也会有所不同。
例如,对于高速切削加工,需要选择具有良好热稳定性和抗泡性的冷却液。
其次,冷却液的应用方式也需要考虑。
常见的冷却液应用方式有湿式加工和干式加工。
湿式加工是指在加工过程中,冷却液与切削区直接接触,起到冷却和润滑的作用。
而干式加工则是在加工过程中不使用冷却液,主要依靠干燥气体吹扫切削区域的碎屑。
不同的加工方式决定了冷却液的使用与否,需要根据具体情况选择合适的方式。
二、冷却液的优化方法为了最大程度地发挥冷却液的功效,需要对冷却液进行优化。
以下是几个常见的优化方法:1. 控制冷却液的浓度和温度冷却液的浓度和温度对加工效果有重要影响。
如果冷却液浓度过高,会导致切削液黏度增大,加工过程中的冷却和润滑效果下降;而浓度过低则会增加切削液消耗量。
因此,要控制好冷却液的浓度。
同时,也要控制冷却液的温度,过高的温度会降低冷却液的散热性能,影响加工效果。
2. 定期更换冷却液冷却液在使用过程中会受到切削液和金属杂质的污染,会影响其性能。
因此,定期更换冷却液是必要的。
一般来说,根据冷却液的使用寿命和加工量来确定更换周期,确保冷却液始终保持良好的性能。
3. 提高冷却液的过滤效果冷却液中的杂质会阻碍切削液的正常流动,影响冷却和润滑效果。
为了减少杂质对冷却液性能的影响,可以加装过滤设备,提高冷却液的过滤效果。
4. 合理使用添加剂适量添加一些合适的添加剂可以提高冷却液的性能。
常见的添加剂包括抗菌剂、抗锈剂、乳化剂等。
根据加工材料和工艺要求,选择合适的添加剂进行添加,以提高冷却液的性能和稳定性。
切削冷却液管理制度范文

切削冷却液管理制度范文切削冷却液是在机械加工过程中经常使用的一种润滑剂,它可以有效地减少切削温度、延长刀具寿命、提高加工质量。
然而,如果切削冷却液管理不当,不仅会浪费资源,还可能对环境造成污染,影响生产效率和员工健康。
因此,建立一套科学的切削冷却液管理制度是非常必要的。
一、制度目的1.规范切削冷却液的使用,减少浪费。
2.保护环境,预防废弃切削冷却液对环境造成的污染。
3.提高切削冷却液的使用效果,延长刀具寿命,提高生产质量。
二、管理责任1.生产部门负责切削冷却液的采购、使用和管理。
2.设立切削冷却液管理专职人员,负责切削冷却液的监督与检查。
三、购买与验证1.采购部门应根据生产需要购买合适的切削冷却液,并确保供应商具有合法的环境保护资质。
2.在收到切削冷却液之前,进行必要的验证,包括检查润滑性能、防锈性能和稳定性等。
四、存储与搬运1.切削冷却液应放置在干燥、通风、阴凉的地方,远离火源和酸碱物质。
2.切削冷却液的存放容器应标明名称、型号、批号、生产日期和有效期限,并进行定期检查。
3.搬运时应使用专用工具,并做好防护措施,避免切削冷却液的泄漏和损坏。
五、使用与循环1.按照规定的浓度使用切削冷却液,不得随意稀释或浓缩。
2.定期检查切削冷却液的浓度和清洁度,必要时进行补充和清洁。
3.使用过的切削冷却液应进行循环利用,经过处理后方可再次使用,尽量减少废弃切削冷却液的排放。
六、清洁与维护1.定期对切削冷却液的设备进行清洗和检修,确保设备的正常运转。
2.清洁时应使用清洁剂,避免使用酸碱物质,以免对设备和切削冷却液造成损伤。
3.定期更换切削冷却液过滤器和精滤器,保持切削冷却液的清洁度和稳定性。
七、废弃处理1.废弃切削冷却液应分类存放,并委托合法的废物处置单位进行处理。
2.废弃切削冷却液的处理应符合环保法律法规的要求,严禁随意倾倒或排放。
3.定期对废弃切削冷却液进行监测,确保废物处理过程符合环保标准。
八、培训与宣传1.组织切削冷却液管理培训,提高员工的管理和运用切削冷却液的意识。
切削液的作业及如何合理的选用切削液

切削液的作业及如何合理的选用切削液正确的选用切削液,可以提高金属切削的生产率,保证被加工材料的加工精度。
每种切削液都有各自的优缺点,各有各的用途。
因此在加工不同的金属材料时需要选用不同的切削液,这样才能使切削液和刀具有效地结合到金属切削加工中。
今天,金属切削行业已进入了系统解决方案的年代。
过去那种镶嵌法选用的工艺现已被简化,如果还不能称为“科学”的话,至少可称为“技术”。
各种等级的刀具、涂层及断屑装置等因素都应结合在一起统筹考虑和设计,使其适应更大的应用范围和工件材料,更有效地进行加工。
然而有时候,金属切削加工中有一个问题往往容易忽略,那就是如何适当地选用切削液。
将今天的系统方法应用于金属切削加工,需要正确地使用合适于金属加工的切削液,这与其它因素一样,已成为解决方案中的同样重要部分。
实际上,现在至少有一家公司正在将切削液和刀具有效地结合到金属切削系统之中。
当你选用以后的切削液时,应考虑到以下一些因素:第一个问题,你在切削加工的是什么材料?你在切削加工中加工的是什么材料?回答这个问题往往是最困难的,因为在正常的情况下,大多数车间内所加工的工件材料是各种各样的。
如果答案毫不含糊的说是“铝”或“不锈钢”或“铸铁”,切削液的选用就可能相当简单和直截了当。
可惜在大批量生产的工厂,这样的情况极少。
如果所切削加工的绝大部分零件为铝或有色金属,那末切削加工时就必须采用非污染型切削液。
一般来说,所使用的切削液为加有特殊成分的半合成液体,可防止有色金属工件的双金属腐蚀和污染。
如果有色金属占绝大部分,选用通用的半合成或混合切削液比较经济。
第二个问题,在你的切削液中含有哪些化学成分?在你的切削液中含有哪些化学成分?这个问题可能涉及到切削液使用的成败原因。
很少有工厂会花费必要的资金,去投资安装采用等离子技术或逆向渗透技术的有效水净化系统。
可惜在重新配制切削液的过程中,所使用水中的化学成分对切削液的性能和油箱的使用寿命会产生相当大的差别。
数控机床技术中的冷却液使用与维护
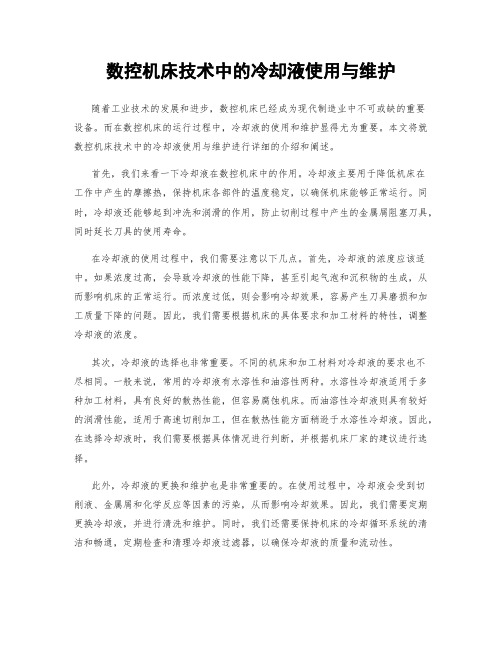
数控机床技术中的冷却液使用与维护随着工业技术的发展和进步,数控机床已经成为现代制造业中不可或缺的重要设备。
而在数控机床的运行过程中,冷却液的使用和维护显得尤为重要。
本文将就数控机床技术中的冷却液使用与维护进行详细的介绍和阐述。
首先,我们来看一下冷却液在数控机床中的作用。
冷却液主要用于降低机床在工作中产生的摩擦热,保持机床各部件的温度稳定,以确保机床能够正常运行。
同时,冷却液还能够起到冲洗和润滑的作用,防止切削过程中产生的金属屑阻塞刀具,同时延长刀具的使用寿命。
在冷却液的使用过程中,我们需要注意以下几点。
首先,冷却液的浓度应该适中。
如果浓度过高,会导致冷却液的性能下降,甚至引起气泡和沉积物的生成,从而影响机床的正常运行。
而浓度过低,则会影响冷却效果,容易产生刀具磨损和加工质量下降的问题。
因此,我们需要根据机床的具体要求和加工材料的特性,调整冷却液的浓度。
其次,冷却液的选择也非常重要。
不同的机床和加工材料对冷却液的要求也不尽相同。
一般来说,常用的冷却液有水溶性和油溶性两种。
水溶性冷却液适用于多种加工材料,具有良好的散热性能,但容易腐蚀机床。
而油溶性冷却液则具有较好的润滑性能,适用于高速切削加工,但在散热性能方面稍逊于水溶性冷却液。
因此,在选择冷却液时,我们需要根据具体情况进行判断,并根据机床厂家的建议进行选择。
此外,冷却液的更换和维护也是非常重要的。
在使用过程中,冷却液会受到切削液、金属屑和化学反应等因素的污染,从而影响冷却效果。
因此,我们需要定期更换冷却液,并进行清洗和维护。
同时,我们还需要保持机床的冷却循环系统的清洁和畅通,定期检查和清理冷却液过滤器,以确保冷却液的质量和流动性。
最后,关于冷却液的使用和维护,还有一些注意事项。
首先,我们需要遵循相关的操作规程和安全操作规范,正确使用冷却液,避免对人体和环境造成危害。
同时,我们还需要避免雨水和杂物等杂质进入冷却液中,以免影响其正常工作。
此外,当机床长时间停工时,应该及时清空冷却液,以防止冷却液长时间积聚而产生异味和腐蚀机床的问题。
机床冷却液的成分

机床冷却液的成分机床冷却液是用于机床加工过程中对切削热量进行吸收和传导的液体。
它的成分是由多种物质组成的,下面将详细介绍机床冷却液的成分。
1. 水机床冷却液的主要成分之一是水。
水具有良好的吸热性能,能够迅速吸收机床加工过程中产生的热量,并通过循环进行传导和散热。
同时,水还能稀释其他添加剂,提高冷却液的流动性和散热效果。
2. 抗菌剂机床冷却液中添加的抗菌剂能够有效抑制细菌和霉菌的生长繁殖,防止冷却液被污染和产生异味。
抗菌剂还能延长冷却液的使用寿命,提高冷却液的稳定性和可靠性。
3. 抗腐蚀剂机床冷却液中的抗腐蚀剂能够防止冷却液与机床中的金属接触产生电化学反应,减少金属腐蚀的发生。
抗腐蚀剂还能保护机床零部件的表面,延长机床的使用寿命。
4. 渗透剂机床冷却液中加入的渗透剂能够改善冷却液在切削过程中的润滑性能,减少切削工具与工件表面的摩擦和磨损。
渗透剂还能提高切削液的附着性,防止切削液在切削过程中被喷溅和挥发。
5. pH调节剂机床冷却液中的pH调节剂能够控制冷却液的酸碱度,保持冷却液的稳定性和性能。
pH调节剂还能中和切削过程中产生的酸性物质,防止对机床和工件产生腐蚀。
6. 润滑剂机床冷却液中的润滑剂能够减少切削工具和工件表面的摩擦系数,提高切削过程的效率和精度。
润滑剂还能降低机床零部件的磨损和噪音,延长机床的使用寿命。
7. 悬浮剂机床冷却液中添加的悬浮剂能够使冷却液中的杂质和金属屑悬浮在液体中,减少对机床和切削过程的影响。
悬浮剂还能方便冷却液的过滤和清洁,提高冷却液的再生利用率。
8. 表面活性剂机床冷却液中的表面活性剂能够降低冷却液的表面张力,提高液体的润湿性和渗透性。
表面活性剂还能改善冷却液的稳定性和分散性,防止冷却液产生泡沫和沉积。
机床冷却液的成分主要包括水、抗菌剂、抗腐蚀剂、渗透剂、pH调节剂、润滑剂、悬浮剂和表面活性剂。
这些成分相互配合,能够有效地吸收和传导机床加工过程中产生的热量,保持机床和切削工具的稳定性和性能,延长机床的使用寿命。
金属切削液
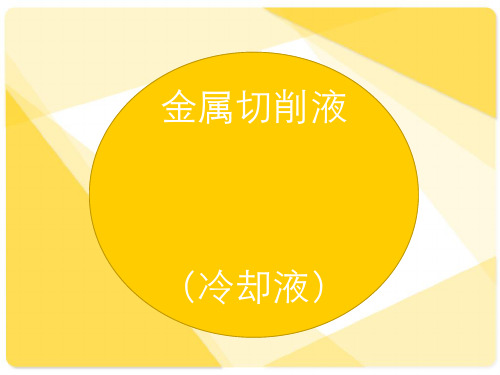
问题,保养和措施
问题
腐蚀
常规保养
液体浓度 低 高
正确措施
加入浓缩液以修正稀释度 加入稀释液以修正浓度 加入杀菌剂 更换切削液
气味
杀菌剂用量
低 高
水的硬度
皮肤过敏 PH值
高
低
提高切削液浓度以防止腐蚀
加入水硬化剂,使用低起泡产品
>9.5 检查碱性物质来源 <8.0 检查细菌数量,加入稀释液/ 杀菌剂或更换切削液
细菌检测
一
常规测试在现场进行,采用
菌条 PH/乳化液稳定性 产品气味
微乳化液(包括生物稳定型的)-细菌侵蚀 合成产品-真菌侵蚀 生物稳定型和含菌剂的产品
细菌数量<105个/ml-正常 1)检查浓度和ph 2)添加杀菌剂 3)更换切削液
二
使用菌条较为简易地检测细菌/真菌
过滤 容易分离
过低
细菌性的降级 腐蚀 降低刀具寿命
表面粗糙度降低
黏性沉淀 产品消耗低
浓度是水溶性切削液最重要的指标!
现场浓度检测
折射仪测量浓度
折射仪读数*折射系数=实际浓度 折射系数
对乳化液通常是<1 对半合成或合成产品通常>1
新配的切削液易于读数 使用一段时间后变得较难读数(含有杂油,细菌, 乳化液不稳定)
其它成分 – 脂肪酸盐, 硫酸盐, 非离子式乳化剂, 防腐剂, 防锈剂, 缓冲剂和防泡沫剂 这种产品有良好的防锈和润滑性能,符合环保 要求和良好的稳定性
可溶于水的乳化油可能包含:
防腐剂
消毒剂和/或杀菌剂
防泡沫添加剂
EP 添加剂
乳剂 – 要和水混合
乳状 因为乳化剂使油滴分散在水中,象
不锈钢的车削参数

不锈钢的车削参数不锈钢是一种耐腐蚀、耐高温的金属材料,常用于制造机械零件、压力容器、航空航天器械等领域。
在进行车削加工时,需要根据不锈钢的特性和要求选择合适的车削参数,以达到理想的加工效果。
一、切削速度(vc)切削速度是车刀在工件表面移动的速度,也是车削过程中最基本的参数。
不锈钢的切削速度较低,一般在30-60m/min之间。
过高的切削速度会导致刀具过热、磨损加剧,影响切削质量和加工效率;过低的切削速度则会造成切削力增大,刀具负荷过大,甚至造成刀具断裂。
二、进给速度(f)进给速度是指车刀在单位时间内向工件进给的量。
在车削不锈钢时,进给速度一般在0.05-0.15mm/r之间。
进给速度过高会造成刀具磨损加剧、表面质量下降;进给速度过低则会导致车削效率低下。
需要根据具体材料硬度和刀具的质量要求来确定合适的进给速度。
三、切削深度(ap)切削深度是指车刀在一次切削过程中,刀尖与工件表面的距离。
不锈钢的切削深度一般在0.5-4mm之间,具体取决于工件的硬度和刀具的强度。
切削深度过大会增加切削力,容易造成刀具断裂;切削深度过小则会导致车削效率低下。
四、切削角度(γ)切削角度是指车刀主切削刃与工件表面的切削角。
在车削不锈钢时,一般选择切削角较小的刀具,如30度左右。
切削角较小的刀具可以减小切削力,提高刀具的切削性能和寿命。
五、冷却液由于不锈钢的切削过程会产生较高的温度,因此在车削不锈钢时需要使用冷却液进行冷却和润滑。
冷却液的选择应根据不锈钢的材质和车削过程的具体要求来确定,以保证切削效果和刀具的使用寿命。
六、切削工具选择不锈钢的切削难度较大,对切削工具的要求也比较高。
一般采用硬质合金或散热钨钢制成的切削工具。
此外,还可以通过涂覆刀具和刀具几何形状的优化来提高不锈钢的切削效果。
总结起来,车削不锈钢需要根据不锈钢的特性和要求选择适当的车削参数,包括切削速度、进给速度、切削深度、切削角度等。
同时还需要选择合适的切削工具和冷却液,以保证切削效果和刀具的使用寿命。
冷却液选用要求

冷却液选用要求
汽车冷却液的种类较多,包括防冻液、水箱宝、水等。
不同种类的冷却液具有不同的性能和特点,因此需要根据车辆的使用环境和需求选择合适的冷却液。
在选用冷却液时,需要注意以下几点:
- 冷却液质量:冷却液的质量直接影响着发动机的性能和寿命,需要选择质量可靠的冷却液。
一般来说,正规品牌的冷却液质量较好,而假冒伪劣产品则可能存在质量问题。
此外,还需要注意冷却液的有效期,过期的冷却液可能会失效或变质,影响发动机的正常工作。
- 冷却液浓度:冷却液的浓度是指冷却液中防冻液的含量。
一般来说,冷却液的浓度越高,防冻性能越好,但过高的浓度可能会影响发动机的散热效果。
因此,需要根据车辆的使用环境和需求选择合适的冷却液浓度。
一般来说,在寒冷的冬季,建议使用浓度较高的防冻液,而在夏季则可以使用浓度较低的水箱宝或水。
- 使用方法:在使用冷却液之前,需要先将发动机和散热器中的水放干净,然后再加入冷却液。
在加入冷却液时,需要注意不要混入其他液体,以免影响冷却液的性能。
此外,还需要定期检查冷却液的水位和浓度,及时补充和更换冷却液。
总之,在选用冷却液时,需要综合考虑车辆的使用环境、需求以及冷却液的质量、浓度和使用方法等因素,以确保车辆发动机能够正常运转。
机械加工中切削液冷却液润滑液的选用
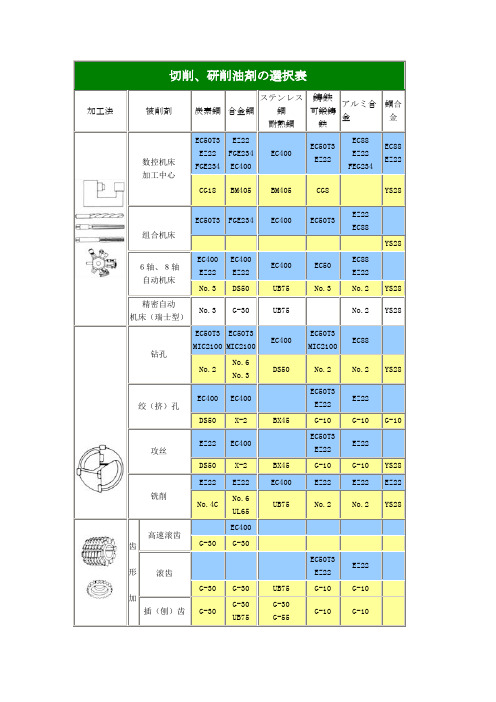
切削、研削油剤の選択表加工法被削剤炭素鋼合金鋼ステンレス鋼耐熱鋼鋳鉄可鍛鋳鉄アルミ合金銅合金数控机床加工中心EC50T3EZ22FGE234EZ22FGE234EC400EC400EC50T3EZ22EC88EZ22FEG234EC88EZ22 CG18BM405BM405CG8YS28组合机床EC50T3FGE234EC400EC50T3EZ22EC88YS286轴、8轴自动机床EC400EZ22EC400EZ22EC400EC50EC88EZ22No.3DS50UB75No.3No.2YS28精密自动机床(瑞士型)No.3G-30UB75No.2YS28钻孔EC50T3MIC2100EC50T3MIC2100EC400EC50T3MIC2100EC88No.2No.6No.3DS50No.2No.2YS28绞(挤)孔EC400EC400EC50T3EZ22EZ22DS50X-2BX45G-10G-10G-10攻丝EZ22EC400EC50T3EZ22EZ22DS50X-2BX45G-10G-10YS28铣削EZ22EZ22EC400EZ22EZ22EZ22 No.4CNo.6UL65UB75No.2No.2YS28齿形加高速滚齿EC400G-30G-30滚齿EC50T3EZ22EZ22 G-30G-30UB75G-10G-10插(刨)齿G-30G-30UB75G-30G-55G-10G-10工格里森固盘G-30G-30 BX1545剃齿DS50UB75通用拉削EC400EZ22 UB75BX45BX1545G-10链式拉削B50B50BX45圣诞树型拉削BX45螺纹重整EC400EC400EZ22EZ22 DS50DS50UB75G-10单点攻丝EC400EC400EZ22EZ22 No.3DS50UB75UB100No.3No.2滚压No.7UB75UB75研磨H-35H-35G-55H-35齿轮研磨螺纹研磨G-55G-55超精研磨加工SF33SF33SF33SF33外面磨削SC46KSC630SC46KSC630MIC2100EZ22SC46KEZ22EE66平面磨削SC46KSC630SC46KSC630MIC2100EZ22SC46KEZ22EE66内面磨削S90S90MIC2100SC46K EZ22 EE66无心磨削SC46KSC630SC46KSC630S90SC46KEZ22EE66精抛光SC46K SC46K No.2No.2以上选型仅供参考,用户在选用产品时以我公司实际推荐为准金属切削加工油◆ 非水溶性产品系列◆ 金属成型加工油◆ 金属清洗剂◆ 金属防锈油。
金属切削加工中切削液的选用和维护
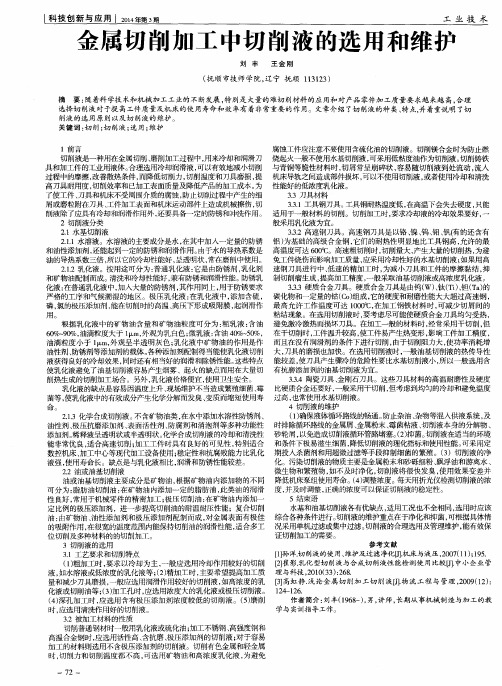
工 业 技 术
金属切 削加工 中切 削液 的选 用 和维 护
刘 丰 王 金 刚
( 抚顺 市技师学院 , 辽宁 抚顺 1 1 3 1 2 3 ) 摘 要: 随着科学技术和机械加工工业的不断发展 , 特别是大量的难切削材料的应用和对产品零件k_ v - 质量要 求越来越 高, 合理 选择切削液对于提 高工件质量及机床的使 用寿命和效率有着非常重要的作用。文章介绍 了切削液的种 类、 特点, 并着重说 明了切
命。
3 . 3 . 1工具钢刀 具 。 工具钢 耐热温度低 , 在高温下 会失去硬 度 , 只能 适用于一般 材料 的切削 。切 削加工时 , 要 求冷却液 的冷却 效果要 好 , 一 般采用乳 化液为 宜。 3 . 3 . 2 高速 钢刀具 。高速钢 刀具 是 以铬 、 镍、 钨、 钼、 钒隋 的还含 有 铝) 为基 础 的高级合 金钢 , 它们 的耐热 性 明显 地 比工具 钢高 , 允许 的最 高温度 可达 6 0 0  ̄ ( 2 。高速粗切 削时 , 切削量 大 , 产生 大量的切削 热 , 为避 免工件烧 伤而影 响加工 质量 , 应采用冷却 性好 的水基切削 液 ; 如果 用高 速钢 刀具进 行 中 、 低 速 的精加工 时 , 为减小 刀具 和工 件 的摩 擦 黏结 , 抑 制切 削瘤生成 , 提高加工精 度 , 一般采取 油基切 削液或高 浓度乳化 液 。 3 . 3 - 3硬 质合金 刀具 。硬 质合金 刀具是 由钨 ( w) 、 钛( T i ) 、 钽( T a ) 的 碳化 物和一 定量 的钴 ( c o ) 组成 , 它 的硬度和耐 磨 胜能 大大超过 高 速钢 , 最 高允 许 工作 温度 可达 1 0 0 0 %, 在加 工钢 铁材 料 时 , 可 减少 切 屑 间的 粘结 现象 。在选 用切 削液时 , 要考虑尽 可能使 硬质合 金刀具均 匀受 热 , 避免激冷激热而损坏刀具。在加工一般的材料时 , 经常采用干切削, 但 在 干切削 时 , 工件温 升较 高 , 使工件 易产生热 变形 , 影 响工件 加工 精度 , 而且在没 有润滑剂 的条件下进 行切削 , 由于切削 阻力大 , 使功 率消耗 增 大, 刀具 的磨 损也加快 。在选用切 削液时 , 一般 油基切 削液 的热传 导性 能较差 , 使 刀具产生 骤冷 的危 险 } 生 要 比水 基切 削液小 , 所 以一 般选 用含 有抗磨添 加剂 的油基切削液 为宜 。 3 . 3 . 4陶瓷 刀具 、 金刚石刀 具 。这些 刀具材 料 的高温耐磨 性及 硬度 比硬 质合金还要 好 , 一般采 用干切削 , 但 考虑到均 匀的冷却 和避免 温度 过高 , 也 常使用水基 切削液 。
钨钢钻头加工参数

钨钢钻头加工参数引言钨钢钻头是一种常用于金属加工中的切削工具,其具有高硬度、耐磨性强等特点,因此在机械制造、航空航天等领域得到广泛应用。
为了确保钨钢钻头的加工效果和寿命,合理选择和设置加工参数至关重要。
本文将详细介绍钨钢钻头的加工参数,包括转速、进给量、冷却液等方面。
转速转速是指主轴每分钟旋转的圈数,它对于钨钢钻头的加工效果有着重要影响。
转速过高会导致刀具过热、磨损严重甚至断裂,而转速过低则会降低加工效率,并可能引起切削不稳定。
选择合适的转速需要考虑以下几个因素: 1. 材料:不同材料对应不同的最佳转速范围。
一般来说,对于硬度较高的材料如不锈钢、合金等,需要较低的转速;而对于较软的材料如铝合金,则可以选择较高的转速。
2. 直径:钻头直径越大,转速应越低。
这是因为大直径钻头在加工时受力较大,转速过高容易造成刀具振动、破损等问题。
3. 切削深度:切削深度越大,转速应越低。
较大的切削深度会增加刀具的负荷,因此需要适当降低转速。
一般来说,在选择转速时可以参考钻头制造商提供的建议值,并根据具体情况进行微调。
进给量进给量是指在单位时间内工件相对于钻头的移动距离,它对于加工效率和加工质量有着重要影响。
进给量过大容易导致切削过快、表面粗糙甚至断钻;而进给量过小则会降低加工效率。
选择合适的进给量需要考虑以下几个因素: 1. 材料:不同材料对应不同的最佳进给量范围。
一般来说,对于硬度较高的材料如不锈钢、合金等,需要较小的进给量;而对于较软的材料如铝合金,则可以选择较大的进给量。
2. 切削深度:切削深度越大,进给量应越大。
较大的切削深度需要更多的切屑空间,因此需要较大的进给量。
3. 钻头类型:不同类型的钻头对应不同的最佳进给量。
例如,中心钻和螺旋钻在加工参数上有所区别。
一般来说,在选择进给量时可以参考钻头制造商提供的建议值,并根据具体情况进行微调。
冷却液冷却液在钨钢钻头加工过程中起到降温、润滑、清洁等作用,能够有效延长刀具寿命、提高加工质量。
CNC机床加工中的刀具冷却与切削液选择

CNC机床加工中的刀具冷却与切削液选择刀具冷却与切削液选择在CNC机床加工过程中,刀具冷却和切削液的选择是非常重要的环节。
刀具冷却可以提高切削质量和加工效率,而合适的切削液则可以延长刀具寿命和改善加工表面质量。
本文将探讨CNC机床加工中的刀具冷却与切削液选择问题,并提供一些建议。
一、刀具冷却刀具冷却在CNC机床加工中起着重要作用。
刀具冷却的主要目的是降低切削区的温度,防止切削过程中过热引起的磨损和变形。
刀具冷却还可以降低加工过程中产生的热变形和应力,提高加工的稳定性和精度。
常见的刀具冷却方法有以下几种:1. 冷却液浸泡法:将刀具浸泡在冷却液中,通过冷却液的传导和吸收热量的方式来降低刀具的温度。
这种方法简单易行,但需要选择合适的切削液。
2. 冷却液喷洒法:使用喷嘴将切削液喷洒到刀具上,形成冷却效果。
这种方法可以根据加工需求和材料选择不同的喷洒方式和角度。
3. 气体冷却法:通过吹气或喷气的方式将冷空气或液化气体喷射到刀具上,达到刀具冷却的目的。
这种方法适用于高速加工和对切削液有特殊要求的场景。
在选择刀具冷却方式时,需要考虑加工材料、加工方式、切削速度和切削深度等因素。
不同的材料和加工要求可能需要不同的刀具冷却方式,因此在实际应用中需要根据具体情况进行选择。
二、切削液选择切削液是CNC机床加工过程中不可或缺的一部分。
切削液的主要功能包括冷却、润滑、防锈和清洗等。
合适的切削液可以有效提高加工效率和切削质量,延长刀具的使用寿命。
常见的切削液类型有以下几种:1. 液压油:主要用于金属切削加工中,可以提供良好的润滑和冷却效果。
液压油具有良好的温度稳定性和抗氧化性,可以在高温和重负荷情况下保持稳定的性能。
2. 水溶性切削液:将切削液与水混合而成,适用于各种金属加工。
水溶性切削液具有良好的冷却效果和润滑性能,可以减少切削表面的热变形和摩擦。
3. 纯油切削液:一般采用合成油或矿物油作为基础油,在金属切削中提供良好的润滑性能和稳定性。
加工中如何选择切削液【干货技巧】
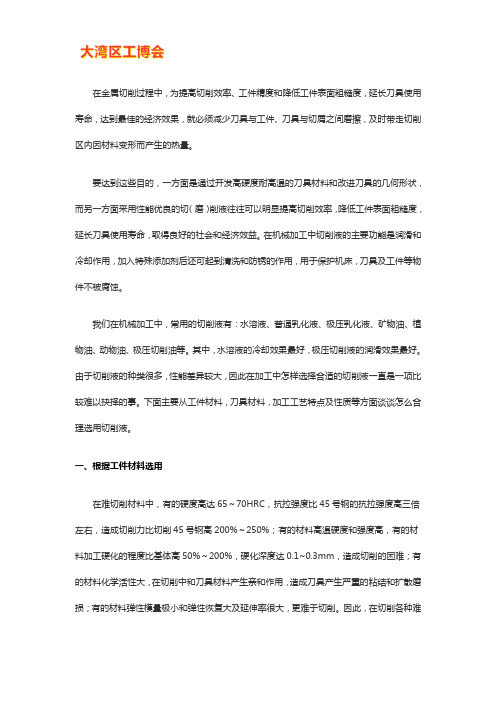
在金属切削过程中,为提高切削效率、工件精度和降低工件表面粗糙度,延长刀具使用寿命,达到最佳的经济效果,就必须减少刀具与工件、刀具与切屑之间磨擦,及时带走切削区内因材料变形而产生的热量。
要达到这些目的,一方面是通过开发高硬度耐高温的刀具材料和改进刀具的几何形状,而另一方面采用性能优良的切(磨)削液往往可以明显提高切削效率,降低工件表面粗糙度,延长刀具使用寿命,取得良好的社会和经济效益。
在机械加工中切削液的主要功能是润滑和冷却作用,加入特殊添加剂后还可起到清洗和防锈的作用,用于保护机床,刀具及工件等物件不被腐蚀。
我们在机械加工中,常用的切削液有:水溶液、普通乳化液、极压乳化液、矿物油、植物油、动物油、极压切削油等。
其中,水溶液的冷却效果最好,极压切削液的润滑效果最好。
由于切削液的种类很多,性能差异较大,因此在加工中怎样选择合适的切削液一直是一项比较难以抉择的事。
下面主要从工件材料,刀具材料,加工工艺特点及性质等方面谈谈怎么合理选用切削液。
一、根据工件材料选用在难切削材料中,有的硬度高达65~70HRC,抗拉强度比45号钢的抗拉强度高三倍左右,造成切削力比切削45号钢高200%~250%;有的材料高温硬度和强度高,有的材料加工硬化的程度比基体高50%~200%,硬化深度达0.1~0.3mm,造成切削的困难;有的材料化学活性大,在切削中和刀具材料产生亲和作用,造成刀具产生严重的粘结和扩散磨损;有的材料弹性模量极小和弹性恢复大及延伸率很大,更难于切削。
因此,在切削各种难切削材料时,要根据所切材料各自的性能与切削特点与加工阶段,选择相宜的切削液,以改善难切削材料的切削加工性,而达到加工的目的。
一般而言:加工铸铁,铸铝等脆性金属,为避免切屑堵塞冷却系统或粘附在机床上难以清除,一般不用切削液。
但精加工时为了提高表面质量,可用润滑好,黏度小的煤油或7%~10%的乳化液。
加工一般钢件,粗加工选用乳化液,精加工选用硫化乳化液。
电火花机工作液冷却技术参数
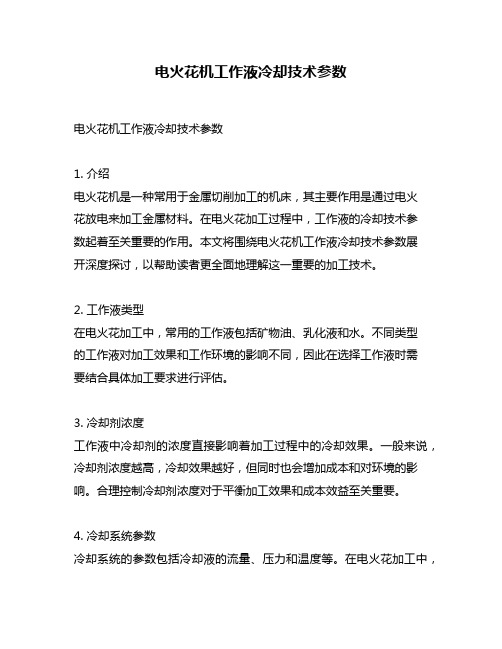
电火花机工作液冷却技术参数电火花机工作液冷却技术参数1. 介绍电火花机是一种常用于金属切削加工的机床,其主要作用是通过电火花放电来加工金属材料。
在电火花加工过程中,工作液的冷却技术参数起着至关重要的作用。
本文将围绕电火花机工作液冷却技术参数展开深度探讨,以帮助读者更全面地理解这一重要的加工技术。
2. 工作液类型在电火花加工中,常用的工作液包括矿物油、乳化液和水。
不同类型的工作液对加工效果和工作环境的影响不同,因此在选择工作液时需要结合具体加工要求进行评估。
3. 冷却剂浓度工作液中冷却剂的浓度直接影响着加工过程中的冷却效果。
一般来说,冷却剂浓度越高,冷却效果越好,但同时也会增加成本和对环境的影响。
合理控制冷却剂浓度对于平衡加工效果和成本效益至关重要。
4. 冷却系统参数冷却系统的参数包括冷却液的流量、压力和温度等。
在电火花加工中,需要根据加工材料的特性和加工过程中产生的热量来合理设置冷却系统参数,以保证加工质量和加工效率。
5. 润滑剂选择除了冷却效果之外,工作液还需要具备良好的润滑性能,以减小摩擦、延长刀具寿命。
在选择工作液时需要考虑润滑剂的类型和含量。
6. 个人观点作为一种关键的加工技术,电火花机工作液冷却技术参数的选择对于加工效果和设备寿命都有着重要作用。
在实际应用中,需要根据具体情况对工作液的类型、冷却剂浓度、冷却系统参数和润滑剂进行综合考量,以取得最佳的加工效果。
7. 总结本文围绕电火花机工作液冷却技术参数展开了深度探讨,从工作液类型、冷却剂浓度、冷却系统参数和润滑剂选择等多个方面对这一重要的加工技术进行了细致分析。
通过本文的阅读,读者可全面了解电火花机工作液冷却技术参数的重要性,并在实际应用中更灵活地进行参数选择。
8. 参考来源:- 电火花机加工工艺参数设置与选择研究. 刘娜, 张三.《机械设计与制造》, 2018.- 加工液中冷却剂的影响及性能研究. 李四, 王五.《现代加工技术》, 2016.电火花机是一种广泛应用于金属切削加工领域的机床,其主要原理是利用电火花放电来加工金属材料,包括精密模具、高硬度材料和金属合金等。
机械加工中的冷却技术
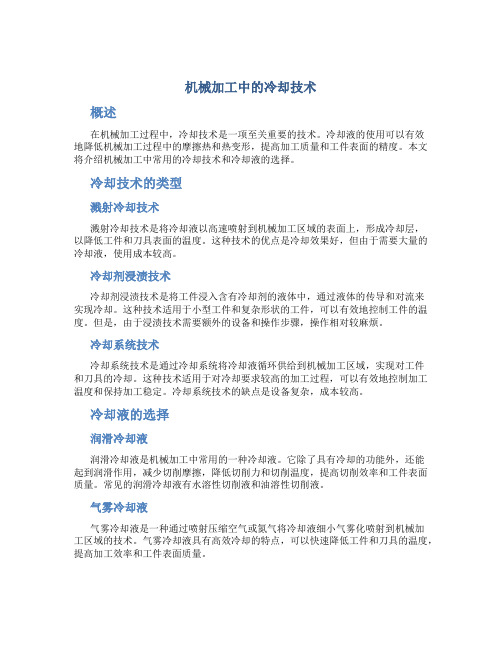
机械加工中的冷却技术概述在机械加工过程中,冷却技术是一项至关重要的技术。
冷却液的使用可以有效地降低机械加工过程中的摩擦热和热变形,提高加工质量和工件表面的精度。
本文将介绍机械加工中常用的冷却技术和冷却液的选择。
冷却技术的类型溅射冷却技术溅射冷却技术是将冷却液以高速喷射到机械加工区域的表面上,形成冷却层,以降低工件和刀具表面的温度。
这种技术的优点是冷却效果好,但由于需要大量的冷却液,使用成本较高。
冷却剂浸渍技术冷却剂浸渍技术是将工件浸入含有冷却剂的液体中,通过液体的传导和对流来实现冷却。
这种技术适用于小型工件和复杂形状的工件,可以有效地控制工件的温度。
但是,由于浸渍技术需要额外的设备和操作步骤,操作相对较麻烦。
冷却系统技术冷却系统技术是通过冷却系统将冷却液循环供给到机械加工区域,实现对工件和刀具的冷却。
这种技术适用于对冷却要求较高的加工过程,可以有效地控制加工温度和保持加工稳定。
冷却系统技术的缺点是设备复杂,成本较高。
冷却液的选择润滑冷却液润滑冷却液是机械加工中常用的一种冷却液。
它除了具有冷却的功能外,还能起到润滑作用,减少切削摩擦,降低切削力和切削温度,提高切削效率和工件表面质量。
常见的润滑冷却液有水溶性切削液和油溶性切削液。
气雾冷却液气雾冷却液是一种通过喷射压缩空气或氮气将冷却液细小气雾化喷射到机械加工区域的技术。
气雾冷却液具有高效冷却的特点,可以快速降低工件和刀具的温度,提高加工效率和工件表面质量。
油性冷却液油性冷却液是一种以矿物油、合成油或液晶等为基础油的冷却液。
它具有优良的抗切削性能和高温稳定性,适用于高速切削和重负荷加工。
油性冷却液也常被用于金属加工,如钢铁加工、铝合金加工等。
高温冷却液高温冷却液是一种专门用于高温加工的冷却液。
它具有较高的沸点和稳定性,可以在高温条件下保持冷却效果,有效地控制加工温度和保护工件表面。
高温冷却液常用于高温合金加工和熔融金属加工。
冷却技术的应用•机械加工中的冷却技术广泛应用于铣削、切削、钻孔、磨削等加工过程中,可以提高加工效率和工件表面质量。
冷却液 冷却焊接电极

冷却液冷却焊接电极
冷却液是一种用于冷却设备或机械的液体,通常是通过循环系统流动以吸收热量并保持设备在适宜的工作温度范围内。
在焊接过程中,冷却液通常用于冷却焊接电极,以确保电极不过热并保持其稳定的工作状态。
冷却液的作用包括但不限于以下几个方面:
1. 热量吸收,冷却液通过循环流动,能够吸收焊接过程中产生的热量,防止焊接电极过热。
2. 稳定温度,通过控制冷却液的流动速度和温度,可以保持焊接电极在适宜的工作温度范围内,提高焊接质量和效率。
3. 防腐抑菌,一些冷却液还具有防腐和抑菌的功能,可以延长设备的使用寿命并保持焊接电极的清洁。
在选择冷却液时,需要考虑以下几个因素:
1. 导热性能,冷却液的导热性能直接影响着其对焊接电极的冷
却效果,需要选择具有良好导热性能的冷却液。
2. 腐蚀性,冷却液对设备材料的腐蚀性是需要考虑的因素,需要选择对设备材料无腐蚀作用的冷却液。
3. 环保性,在选择冷却液时,需要考虑其对环境的影响,选择环保型的冷却液。
总的来说,冷却液在焊接过程中扮演着重要的角色,能够有效地保护焊接电极并提高焊接质量和效率。
选择合适的冷却液并合理使用,能够为焊接工作提供良好的保障。
- 1、下载文档前请自行甄别文档内容的完整性,平台不提供额外的编辑、内容补充、找答案等附加服务。
- 2、"仅部分预览"的文档,不可在线预览部分如存在完整性等问题,可反馈申请退款(可完整预览的文档不适用该条件!)。
- 3、如文档侵犯您的权益,请联系客服反馈,我们会尽快为您处理(人工客服工作时间:9:00-18:30)。
金属切削工艺中冷却液的选择与性能分析
在金属切削工艺中,冷却液的选择和性能分析对于提高切削加工效率和工件质
量至关重要。
本文将介绍金属切削工艺中冷却液的选择原则和常见类型,并分析其对切削过程中的影响。
一、冷却液的选择原则
在金属切削工艺中,冷却液的选择应考虑以下几个方面:
1. 热传导性能:冷却液应具有良好的热传导性能,能够迅速带走切削过程中产
生的热量,防止工件和刀具的温度过高,从而延长刀具寿命。
2. 冷却性能:冷却液应具有良好的冷却性能,能够有效降低切削区域的温度,
减少切削过程中的热变形和热裂纹的产生。
3. 润滑性能:冷却液应具有良好的润滑性能,能够减少金属与刀具之间的摩擦,降低切削力和切削工具磨损。
4. 清洁性:冷却液应具有良好的清洁性,能够有效清除切削过程中产生的切屑
和金属粉末,防止切削区堵塞和二次划伤。
5. 环保性:冷却液应具有良好的环保性能,不含有害物质,能够符合环保要求。
二、常见冷却液类型
根据成分和用途的不同,冷却液可以分为以下几种类型:
1. 水溶性切削液:水溶性切削液是一种以水为基础的液体切削介质,主要由水、抗锈剂、润滑剂和添加剂等组成。
它具有良好的冷却性能和润滑性能,适用于大多数金属切削加工,尤其适用于铸铁、碳钢和不锈钢等材料的切削.
2. 非水溶性切削液:非水溶性切削液由有机溶剂和添加剂组成,不含水分。
它可以有效减少金属与刀具之间的摩擦,提高切削效率。
非水溶性切削液适用于高速切削和切削困难材料,如合金钢、高硬度合金等。
3. 高分子切削液:高分子切削液由聚合物和添加剂组成,具有极佳的润滑性能和极高的抗热性能,适用于高温、高速切削加工。
4. 气雾切削液:气雾切削液是一种以气雾形式喷射到切削区域的切削液,具有良好的冷却和润滑效果。
它适用于高速切削、硬质合金切削和有高表面粗糙度要求的切削加工。
三、冷却液性能的分析
冷却液的性能对金属切削过程中的加工效果有着直接的影响。
下面将对冷却液的性能进行分析:
1. 冷却效果:合适的冷却液能够带走切削时产生的大量热量,降低切削区域的温度,减少工件和刀具的热变形,并提高刀具寿命。
2. 润滑效果:良好的润滑性能能够减少切削时金属与刀具之间的摩擦,降低切削力和刀具磨损,提高加工效率和表面质量。
3. 抗菌性能:冷却液中的添加剂具有一定的抗菌性能,可以防止切削区域的细菌滋生,延长冷却液的使用寿命。
4. 稳定性:优质的冷却液具有较好的稳定性,能够长时间保持其良好的性能,不易发生变质和酸败。
5. 环保性:冷却液在使用过程中应尽量减少对环境的污染,具有良好的生物降解性。
综上所述,冷却液的选择和性能分析在金属切削工艺中具有重要意义。
根据切削材料、工艺要求和经济效益等方面的考虑,可以选择合适的冷却液类型,并且根据具体情况对其性能进行分析,以确保切削工艺的顺利进行。