福特制定FMEA时如何对特性进行分类
FMEA简述

缺陷产品;不需要分拣;需要向供应商提供反馈
触感令人略微感觉不舒服。
1
非常低 没有可觉察到的影响
没有可觉察到的影响或没有影响
没有可觉察到的影响。
注:绿色为公司重点采用的相关评判标准,灰色为不常用标准。
十、第五版FMEA内容——失效原因
· 由小组结合特定的知识和经验来确定 · 失效原因能够直接确定或者通过理解失效的原理来确定
八、第四版FMEA
过程步骤/功能
要求
潜在失效模式
潜在失效影 响
SEV 严重度
分类
潜在失效原因
OCC发生 度
现行过程控制 预防
Plasma清洗
芯片背面 无污染
D/B 焊胶层 芯片背面污染 脱落,电参
失效
8
Plasma能量&时间参 数不恰当 Plasma工艺气压值偏 小或偏大
气体流量偏小
1.限制参数编辑权限,仅工程部负责人有
· 描述失效模式对客户的影响:
- 内部客户(下一个操作/后续操作/操作目标) - 外部客户(下一级/OEM/经销商)政府法律法规
- 产品或产品最终用户/操作者 - 立法机构
要求 四个螺钉
失效模式
影响
最终顾客:座垫松动,有噪音。
少于四个螺钉 制造和装配:由于受影响的部分,因而停止发
运,并进行额外挑选和返工。
1.要求作业员每班检查气罐接口是否漏气 2.气体流量超出范围时,设备自动报警
DET RP 探测度 N
4 64
4 64 2 32
推荐措施 NONE NONE NONE
Action Results/实施结果
职责和目标完 成日期
采取的措施 和有效日期
SE V 严重 度
DFMEA培训教材

5.1989年:美健康与人类服务部颁布“生产质量保证计划”(FDA90-4236);FMEA被要求用于设施资格认可.
6.1990年:美汽油协会建议将FMEA溶于设计之中(ANSIZ21。64andZ21.47).美铁道业建议用FMEA来提高火车车厢的安全性。ISO9000建议用FMEA作设计检讨。
2发动机零部件潜在失效模式:
·推荐选用表1所给的发动机故障模式,(统一使用这些描述,会避免出现常把失效原因当成了失效模式使用的错误);
·在失效链中“找到倒下的第一块砖”;
·用“潜在失效模式找全了吗?”进行自我检查.
表1发动机故障模式
代号
故障模式
代号
故障模式
代号
故障模式
01
断裂
02
碎裂
03
开裂
04
裂纹
潜在设计失效模式及后果分析
DESIGNFMEA
2009-1-5
一、什么是FMEA?
FMEA是英文“PotentialFailureModeandEffectsAnalysis”的缩写—潜在的失效模式及后果分析
本应写成P-FMEA,但由于企业/公司常用P—FMEA表示“过程FMEA”,D—FMEA表示“设计FMEA”所以省略了“Potential",以免混淆。
八、DFMEA表各栏定义及DFMEA报告编制
A项目功能
1定义:
·项目是指要分析的零件、分总成;
·功能是指零件、分总成的作用.
2功能描述要求:
·用动词+名词简洁语句。
·例如“点火开关”,功能为“接通电源起动汽车”。
·用“设计意图是否表达清楚?”进行自我检查.
产品特性和过程特性分类管理办法
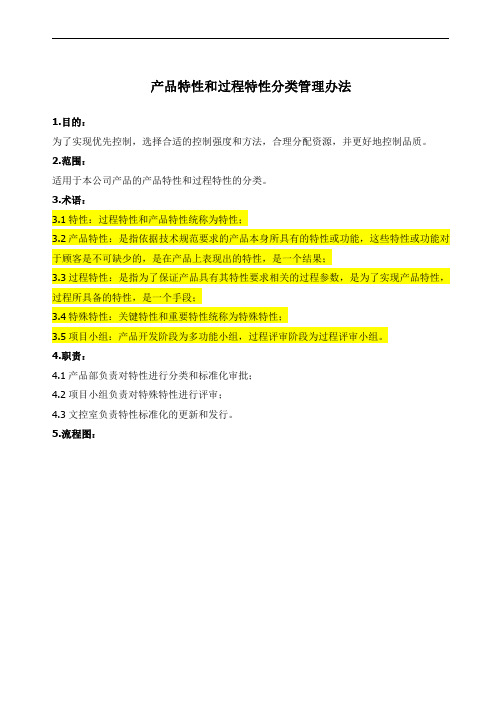
产品特性和过程特性分类管理办法1.目的:为了实现优先控制,选择合适的控制强度和方法,合理分配资源,并更好地控制品质。
2.范围:适用于本公司产品的产品特性和过程特性的分类。
3.术语:3.1特性:过程特性和产品特性统称为特性;3.2产品特性:是指依据技术规范要求的产品本身所具有的特性或功能,这些特性或功能对于顾客是不可缺少的,是在产品上表现出的特性,是一个结果;3.3过程特性:是指为了保证产品具有其特性要求相关的过程参数,是为了实现产品特性,过程所具备的特性,是一个手段;3.4特殊特性:关键特性和重要特性统称为特殊特性;3.5项目小组:产品开发阶段为多功能小组,过程评审阶段为过程评审小组。
4.职责:4.1产品部负责对特性进行分类和标准化审批;4.2项目小组负责对特殊特性进行评审;4.3文控室负责特性标准化的更新和发行。
5.流程图:6.内容:6.1分类规则6.1.1顾客指定6.1.1.1美国三大汽车公司类别项目通用汽车公司北美部福特汽车公司克莱斯勒汽车公司6.1.1.2当顾客要求成为高等级重要性时,那个特性就自动成为高等级的重要特性;6.1.1.3当顾客指定特性符号时,按照顾客指定的特性符号。
6.1.2自己定义:6.1.2.1自己定义的特性可以参照6.1.1.1美国三大汽车公司特性分类规则;6.1.2.2自己定义的产品特性重要性等级分类及符号,如下表:6.2标注方法在产品质量先期策划过程和过程评审中,必须在下列文件中用特性符号标识出“产品特性”或“过程特性”的特性类别(除“QR7-01-09产品/过程重要特性分级表”外的其他文件可只标出特殊特性的类别):6.2.1“QR7-01-09产品/过程重要特性分级表”;6.2.2“QR7-01-10过程流程图”;6.2.3“QR7-01-21过程FMEA表”;6.2.4“QR7-01-22(试)生产控制计划”;6.2.5“QR7-01-24作业指导书”;6.2.6PPAP提交的文件;6.2.7顾客要求提供的其它文件。
基于福特FMEA手册定义特殊特性识别方法整理

以下内容是基于福特FMEA手册定义特殊特性识别方法整理特殊特性的识别管理一直是IATF16949体系及五大工具应用中的重点和难点,今天在这里和大家一起探讨下特殊特性的识别和管理:第一部分:特殊特性定义产品特性是一种可区分的特征,例如尺寸,大小,形状,位置,方向,质地,纹理,硬度,抗拉强度,外观,涂层,或反光率等,这些特征需要得到严格控制从而来保证达到预期的产品功能产品特性的公差范围:每个产品特性必须被定义在一定的公差范围内,才能确保预期的产品功能过程特性-会影响过程输出结果的可度量的过程输入特性以及它们的相互影响。
例如速度,温度,压力以及电压等-过程特性包括方法和流程,这些方法和流程能够确保生产操作的顺利进行从而来满足零部件的质量要求和其他目标,如产能要求等-过程特性包括操作条件和过程参数,比如生产节拍和生产维护要求关键特性(CC)-关键特性CC用倒置的三角形(∇)表示。
是指那些能够影响到是否符合政府法规,整车安全或产品功能的产品要求(比如尺寸,性能要求,材料规范)或者过程参数(比如比率,温度,压强)-关键特性需要包含在控制计划中,并有相应的生产,装配,运输和监控的具体措施-潜在的关键特性:在DFMEA中被划分为YC一类的产品特性。
这些特性与严重度为9或10的潜在失效模式有直接的因果关系(产品特性或过程参数不符合规范或变差较大,并最终导致了某个失效模式的发生,则可以说该特性与该失效模式有因果关系)例如:门锁的横向载荷和纵向载荷国标有要求,为CC特性,主要和门锁的棘轮、棘爪和锁扣强度有关,与之相关的棘轮、棘爪和锁扣的热处理工艺参数需列为CC项重要特性(SC)-重要特性SC是指对客户满意度影响比较大的产品、过程和试验要求-重要特性需要包含在控制计划中进行控制潜在重要特性:当某个产品特性满足如下条件时,在DFMEA中应该将其划为YS类别:该特性与严重度为5-8的潜在失效模式有因果关系。
在严重度小于5时,经各部门一致同意也可归为YS该特性可能会被生产过程影响并且可能需要特殊控制措施来维持所要求的过程能力例如:门锁需要装配到车门上,因此三个安装孔的相对位置尺寸列为SC。
特殊特性及FMEA准则
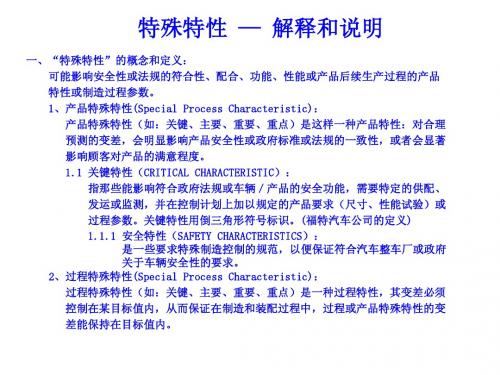
无/没有 需有持续改进计划,以降低成本。
设计 FMEA 严重度评价准则
后 果 评 定 准 则 : 后 果 的 严 重 度 严重度 10 9 8 7 6 5 4 3 2 1 无警告的 这是一种非常严重的失效形式,它是在没有任何失效预兆的情况下影响到行 严重危害 车安全或不符合政府的法规。 有警告的 这是一种非常严重的失效形式,是在具有失效预兆的前提下所发生的,并影 严重危害 响到行车安全或不符合政府的法规。 很高 高 中等 低 很低 轻微 很轻微 无 车辆/项目不能运行(丧失基本功能)。 车辆/项目可运行,但性能下降,顾客非常不满意。 车辆/项目可运行,但舒适性/方便性项目不能运行,顾客不满意。 车辆/项目可运行,但舒适性或方便性项目的性能下降,顾客有些不满意。 配合和外观/尖响和卡嗒响等项目舒服,大多数顾客(75%以上)能感觉到有 缺陷 配合和外观/尖响和卡嗒响等项目不舒服,50%的顾客能感觉到有缺陷 配合和外观/尖响和卡嗒响等项目不舒服,有辩识能力的顾客(25%以下)能 感觉到有缺陷 无可辨别的后果
1、多方论证小组应对评定准则和分级规则达成一致意见,否则由技术部主管和/或管 理者代
备 注 表裁定,尽管个别产品分析可做修改。不推荐/建议修改确定为9和10的严重度数值,
过程 FMEA 严重度评价准则
判定准则:后果的严重度 当潜在失效模式导致最终顾客和/或一个制造/装 后 果 配厂产生缺陷时便得出相应的定级结果。最终顾 客永远是首先考虑的。如果两种可能都存在的, 采用两个严重度值中的较高者。(顾客的后果) 无警告 的严重 危害 有警告 的严重 危害 判定准则:后果的严重度 当潜在失效模式导致最终顾客和/或一个制造/装 严 配厂产生缺陷时便得出相应的定级结果。最终顾 重 客永远是首先考虑的。如果两种可能都存在的, 度 采用两个严重度值中的较高者。(制造/装配的后 果)
五大手册之FMEA介绍
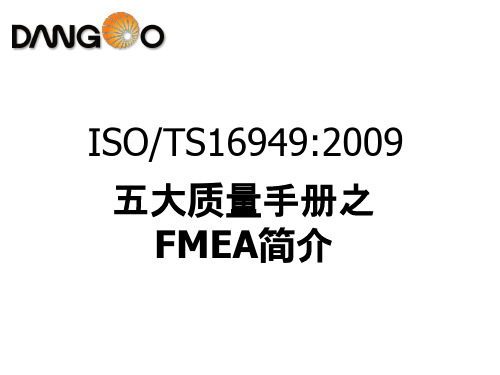
危险(没有征兆的)
危険(有征兆的) 非常高 高 还可以 低 非常低 轻微 非常轻微 没有
导致人身事故(破裂,发火,发热)
导致物品损害事故(破裂,发火,发热) 灯泡不可点亮,客户的产品无法使用. 灯泡可以点亮,但寿命低下。 大部分的顾客感到不满. 灯泡可以点亮,但配光或光通量达不到客户要求。 一部分的顾客感到不满. 安全性、电气特性正常。明显的外观问题。 没有明显外观问题,但是比轻微外观问题严重的 细小伤痕,污点等外观问题. 在工程内可能修正的 没有影响.没有人注意到
FMEA-参考手册
9
由北美三大汽车公司(克莱斯勒、福特和通用)FMEA工 作组编写;是一本设计FMEA和过程FMEA的开发指南; 目的不在于定义要求,而是在于阐明FMEA技术开发中的 问题;
1993年2月发布第一版;1995年2月发布第二版; 2001年7月发布第三版;2008年6月发布第四版; 2001年11月发布《设备和工装潜在失效模式及后果分析 (MFMEA )》第一版; 手册提供了应用 FMEA 技术的总体指南,但并没有给出 如何完成每一 FMEA 项目的具体说明,也不是综合性的 参考资料或培训资料。
A
B
C C C C
基准说明 不能测出结果或不检查 只通过间接或抽查来控制 只通过目视检查来控制
评 分 10 9 8
非常低
低 中等 中高等 高 非常高
控制方法测出的机会少
控制方法可能测出 控制方法可能测出 控制方法测出的机会高 控制方法测出的机会高 肯定能测出 A A A B B B B B
C
C
只通过双重目视检查来控制
DFMEA是产品设计和开发(第二阶段)的输出之一 PFMEA是过程设计和开发(第三阶段)的输出之一 PFMEA是CP的输入及指导依据 文件流程:特殊特性清单、过程流程图、特殊特性矩阵图、 FMEA、CP、PCM(如TRW要求)、SOP
FMEA特殊特性的设定

FMEA 特殊特性的设定APQP(产品质量先期策划和控制计划)→计划(技术和概念开发)→实施(产品过程开发和样件验证)→研究(产品确认和过程确认)→行动(持续改进)→计划(技术和概念开发)1、什么是概念开发:提出和批准,二个过程输出内容:设计目标可靠性和质量目标初始材料清单初始过程流程图产品和过程特殊特性的初始清单产品保证计划管理者的支持2、设计技术开发:大部分为顾客输入的翻版二、产品设计和开发输出内容:1、样件制造——控制计划样件制造过程中的尺寸测量和材料S功能试验的描述①顾客的关注都识别了没有。
②计划中是否使用了SFMEA DFMEA和PFMEA。
DFMEA指的是产品可能会在配合、功能、耐久性、安全、顾客关注有失效可能,在实现产品时克服不了设计中潜在的缺陷,如拔模斜度、表面硬度、装配空间与工具可接近性、过程能力达不到性能要求。
③材料检验规范。
④进货(材料/零件)到制造/装配(包括包装)的全过程。
⑤涉及到工程性能试验要求。
⑥具备如控制计划所要求的量具和试验设备。
⑦如要求顾客批准。
⑧供方和顾客之间的测量方法是否一致2、工程图样(包括数学数据)注意:工程图样中包括必须在控制计划上出现的特殊特性(政府法规和安全性),并决定哪些特性影响配合、功能、耐久性或政府法规中的安全要求,就是特殊特性的设定,由策划小组评审并决定。
3、工程规范:功能、耐久性、外观要求(顾客的特殊要求)4、材料规范:图样、物理特性、性能、环境、搬运、贮存要求的特殊特性也应包括在控制计划中。
5、更改图样和规范:适当的书面形式通知相关部门。
6、新设备、工装和设施的要求:必须在试生产前完工。
7、产品和过程特殊特性:可标识性列入,也可另列控制计划特殊特性工作单,作为控制计划的扩展,产品特殊特性往往和DFMEA密切相关(如JK918干涉自排系统)。
8、量具/试验设备要求:可列入进度图表中。
9、小组可行性承诺和管理者的支持。
三、过程设计和开发(技术开发部的重头戏)输出内容:1、包装标准:包装设计应保证产品在使用时的完整性,通常要批准。
FMEA简介

3. FMEA解释
●失效定义
失效是指系统的组件或某一结构发生任何形状、
尺寸或材料性质的变化,造成这些系统处于无法充
分地执行其特定的功能的状态。
产品在工作范围内,出现零件 破损、断裂、卡死、损坏的现 象
在规定条件下不能完成既定功 能
失效
在规定条件下,产品参数值不能维 持在规定的上下限之间
3. FMEA解释
主要运用在两个方面,设计(DFMEA)和过程( PFMEA)。
在产品设计阶段和过程设计阶段,对构成产品的 子系统、零件,及构成过程的各个工序逐一进行分 析,找出所有潜在失效模式,并分析其可能的结果 ,从而预先采取必要的措施,以提高产品的质量和 可靠性的一种系统化的活动,并将全部过程形成文 件。
3. FMEA解释
4. FMEA填写说明
潜在失效后果说明 ●是指失效模式对顾客产生的影响。
注意: 1.要根据顾客可能发现或经历的情况来描述失效的后果; 2.如果某一失效模式对应多个失效后果,应逐一列出,加以分析。 2.顾客可能是内部客户,也可能是外部最终客户,包括最终使用着、主机厂组装客户或下一道工序操作人员; 3 如果顾客是最终使用者,典型失效后果有:异音、异味、外观不良、触感差、不起作用、不稳定、不符合法规等。
4. FMEA填写说明
●PFMEA编辑逻辑思路:
功能、特征 或要求是什 么?
影响是什么 ?
影响有多严 重?
起因是什么 ?
发生概率有 多大?
可能有何错误?
--功能丧失 --功能降低 --功能过强 --功能间隙性中断 --非预期功能
能否被探测 到?
探测它的方 法有多好?
可以怎样改 进?
--设计变更 --过程变更 --特别的控制 --标准的更改
参考资料2 FMEA简介

F M E A运用计划一.FMEA简介FMEA为Failure Mode and Effect Analysis(失效模式与效能分析)之简称,最早由美国航天工业于六十所代所发展出来的一套信赖度分析的工具.北美福特公司(Automotive Operations)于1972年发展信赖度训练计划时将FMEA包括于内,福特将FMEA分为两个模块:一为设计的FMEA;一为制程的FMEA.而后又陆续出版个别的指导手册,发展使用至今已广为汽车工业所使用,目前亦逐渐用于其它工业之上.福特公司给FMEA所下的定义为,FMEA可视为一系统化的群组活动,其目的在达成:1.辨认及评估与产品设计及制造相关的可失效模式及原因.2.找出可以消除或减少可能失效发生的改正措施,以及3.记录分析的过程.二.实施重点准备FMEA的工作应由负责设计或制造的工程师个人负责,但准备时所须的各种Input则必须为一整体的努力而非负责工程师个人的责任.对复杂的Item,可能要组成一个特定的队伍,队伍成员由其不同专业知识的人员所组成,可能包括设计、制造、装配、服务或品管等人员,或者利用会签的方式,要求以上所提各人员提出意见及反应,以找出负责工程师所不熟悉的可能Failure Mode.另一实施重点是FMEA须适时的实施,FMEA 应该是一个“事件发生前”的行动而非“事实产生后”的练习,要达成FMEA 的最侍佳效果,FMEA一定要在任何未知的设计或制造的Failure产生之前实施,花时间将FMEA做好,则将来的设计或制造程序变更可以较容易及花费较少的执行并减轻设计后期设计变更的危机.FMEA如果能被适当的应用,则FMEA 是一个重复,周期性永不间断的必进程序.三.设计的FMEA(Design FMEA)Design Potential FMEA是一种分析的技巧,提供产品工程师一种手段能尽可能的保证所有的可能Failure Mode及其Cause都已被考虑并加以强调,最终产品及与其相关的所有次组件以至单一零件皆应被评估分析.在整个设计过程中,FMEA提供或协助以下所列的各事项来减少Failure发生的风险:1.协助做设计需求及设计选择方案的客观评估;2.增加可能Failure Mode 及其对系统的Effect,能在产品设计发展阶段被预先考虑的机率;3.提供额外的信息来协助彻底而有效的设计测试及发展的计划;4.因为可能失效模式是依据对“顾客”的影响大小来做优先次序排列,所以可依此而建立一个设计改进及测试的优先系统;5.提供一个开放式的格式来追踪风险降低措施及改进建议;6.针对分析顾客使用考虑,评估设计变更及发展更先进设计提供将来的参考.顾客(Customer)的定义对设计的FMEA来说,顾客的定义应为最终使用者(End User),但是对设计工程师来说,顾客的定义并不只限于此,其顾客也可以是相关制造或装配单位的负责工程师或服务工程师等.注意事项:设计的FMEA并非准备一次就完成的记录,它在设计概念成形后开始,然后在整个产品发展过程中须随着设计变更随时更新来反应现有设计,要一直到最后设计工程图完成后,设计的FMEA才能算基本的告一段落.在制程或装配上会发生的可能失效模式不能包括在设计的FMEA内,而应包括在制程的FMEA内,但是有关这些失效模式的信息,设计工程师必须将它们传递给负责制程FMEA的工程师作为准备制程FMEA的输入.设计的FMEA不能依靠以制程的控制来克服设计上的弱点,但在做设计的FMEA时,必须把一些制程及装配上的技术及实际限制条件列入考虑.例如:1.表面处理的限制;2.钢材硬度的限制;3.制程能力的限制等条件.四.分析方式(Analysis Approach)FMEA有两种不同的分析方式Hardware Approach及Functional Approach,分析方式的选择,依现有资料及设计复杂性的不同而定.Hardware Approach是将设计的每一Hardware Item列出,然后就每一Hardware Item进行分析,将其所有的可能的Failure Mode找出.Functional Approach是将设计的Item所能执行的各种功能分类为不同的Output列出,然后就每一Output进行分析将其所有的Failure Mode找出.当设计为一复杂的系统时,FMEA可使用两者综合的分析方式.FMEA为分析架构可由上至下或由下至上.如果由蓝图,工程或设计资料中能很明确的定义出Hardware Item,则FMEA通常使用Hardware Approach且多使用由下至上的架构.反之若Hardware Item不易定义或系统复杂分析须由Initial Indenture Level 向下层层的分析,则FMEA通常使用Functional Approach,且多使用由上至下的架构.分析方式使用何种分析架构并非绝对,分析可由任一层开始向任一方向进行分析.五.FMEA程序(FMEA Process)FMEA为设计程序的一部份,应在设计初期实施并须随时更新反应所有设计变更.由设计初期至最后完成阶段,每一阶段的设计Review皆应将由FMEA列出主要考虑项目,使用FMEA来考量高风险的Item及其相关活动以订出改正措施,FMEA亦可用来定义特殊测试考虑﹑品质检验点﹑预防保养措施﹑操作条件﹑可用寿命及降低Failure风险至最小的必要信息及活动.FMEA所订出的所有建议措施都必须加以评估,经评估决定不采取行动的措施要有适当的记录建立来做正式处理.以下是实施FMEA的步骤:1.定义要分析的系统,包括内部及接口的功能,所有Indenture Level的预期续效,系统条件及失效的定义;2.建立Block Diagram;3.找出所有可能的失效模式,判定其对邻接的Item或功能,整个系统及所行使命的影响;4.就失效模式评估其可能导致最糟的结果,将结果归类至不同的严重性分类类别内;5.就失效模式订出失效检出方法及补救措施;6.找出消除失效或控制风险的必要改正设计或措施;7.判定改正措施的影响;8.将FMEA记录起来,并将问题汇总,问题包括那些无法由变更设计而解决的问题及降低风险的必要特殊控制.六.FMEA表格内容说明FMEA所使用的表格有两种:一为设计的FMEA,一为制程的FMEA,以下即对两种表格的内容分别介绍.设计FMEA表格内容说明表头各项内容说明1.产品名称:FMEA所分析产品的名称;2.设计责任单位:负责设计该产品的单位名称;3.相关单位:与该产品有关之各单位及组织的名称;4.供货商及制造工厂:自制或外包的厂商或工厂的名称(客户亦须列入)5.产品编号:产品的产品编号(包括自己的编号及客户使用的料号);6.设计定稿日期:填入该产品设计定稿的预期日期;7.负责人:负责制作FMEA表格之人员的姓名﹑职称及分机号码:8.FMEA定稿/更新日期:FMEA表格制作日期及更新日期.表格各项分析内容说明9.零件名称及编号/功能:填入(1)及(5)项之内容并对产品的功能加以叙述,功能定义的愈清楚,愈容易定义出失效模式,如果产品有多种不同的功能及可能的失效模式,各项内容应分开叙述;10.潜在的失效模式:指产品无法达到设计意图﹑续效要求或客户预期的可能产品缺失,针对产品的功能列出所有可能的失效模式,潜在失效模式的假设为有可能发生却非一定发生,建议找出失效模式的方式可参考以前的FMEA﹑测试报告﹑实际使用或信赖度的考量﹑以及对类似产品脑力激荡的结果,在特定的环境或使用状况下可能发生之失效模式亦须列入考虑,描述失效模式应使用技术性的用语,便如龟裂﹑变形﹑腐蚀﹑氧化﹑震动﹑松动﹑开路或短路;11.潜在的失效效应:指如果失效模式发生,失效模式对客户可能造成的影响或效应,描述失效效应应使用客户所经验注意到之用语,例如产品的外观﹑适用性及功能.12.严重度:对失效模式所造成的失效效应严重程度的评估,严重度的大小以1至10的数字来表示,欲降低严重度惟有做设计的变更,评估严重度可参考下列的评估表:严重度指数评估标准1、Negligible(可忽略的),对产品的续效不太可能产生影响,使用者可能不会发觉任何缺失.2﹑3 Mild(轻度的),造成使用者一些轻度的使用不顺,但一般不会感觉到任何续效的变化4﹑5﹑6 Moderate(中度化),使用者使用的不顺仍可忍受,但已感觉到一些续效及外观的变化7﹑8 High(高度的),使用之不顺已达无法忍受的地步,可能有无法达到续效要求的问题发生9﹑10 Very High(极高度的),续效已完全失去或未达到安全规定的要求13.重要产品特性:以,如严重度的指数为9或10且发生及检出率皆大于1时,应判定是否归类为重要产品特性而予以标示.14.潜在的失效原因:导致失效模式产生的原因,就设计的部份来看即为设计上的弱点,一些典型的原因为材料选择错误﹑不好的模具等;15.发生率:对某一特定失效原因发生导致失效模式产生的可能性大小的评估.发生率大小以1至10的数字来表示,欲降低发生率惟有靠设计变更来控制或消除一个或数个失效原因,评估发生率可参考下列的评估表:发生率指数评估标准1、emote(微乎其微),失效原因造成失效模式产生的机会微乎其微2﹑3 Very Low(非常低)失效原因造成失效模式产生的机会非常低4﹑5﹑6 Moderate(很高),失效原因造成失效模式产生的机会较高7﹑8 High(很高),失效原因造成失效模式产生的机会很高9﹑10 Very High(非常高),失效原因造成失效模式产生的机会非常高,几乎一定会发生16.现行的设计确认方式:指防范可能失效原因发生或检出失效原因及模式的各种检查或检测计划:在此栏内须将所有现有的设计确认(DV)列出,DV与防范或检出失效原因直接相关,非现有的DV必须放在议改善方案栏内;17.检出率:指设计确认能检出或防范失效原因发生的能力,检出率大小以1至10的数字来表示,欲增加检出率,DV计划必须加以修改,评估检出率可参考下列的评估表:检出率指数评估标准1﹑2 Very High(非常高),DV几乎一定能找出设计的弱点3﹑4 High(很高),DV能找出设计弱点的可能性很高5﹑6 Moderate(高),DV可能可以找出设计的弱点7﹑8 Low(很低),DV可能不太容易找出设计的弱点9 Very Low(非常低),DV可能找不出设计的弱点10 Min-Detection,DV找不出设计弱点或根本没有DV18.风险指数值(RPN):为严重度﹑发生率及检出率三者指数的乘积,数字本身不具任何意义;表格内改善方案及处臵结果之各项内容说明19.建议改善方案及优先级:经由对严重度﹑发生率及检出率三者指数所做分析的结果订定重要设计弱点的改正措施.改正措施的目的在改善严重度﹑发生率及检出率三者中任一﹑二或全部之指数,依各设计弱点在程度上订定改善措施的优先等级并填入改善优先等级栏内,可能有的等级区分为:A-出货前须改善B-一个月内须改善C-半年至一年内改善D-可能要改善或可能不改善20.执行单位负责人及完成日期:改正措施执行的负责单位,人员姓名及预计的完成日期;21.实际改善措施:实际上执行的改正措施项目,完成的日期及效果;22.处臵结果的风险优先指数:改正措施完成后重新评估三项指数,未列改善措施的项目不需要计算,如有任何项目须进一步的改善措施时,重复(19)至(22)内各项内容.制程FMEA表格内容说明表头各项内容说明1﹑制程﹑制品的名称/编号:被分析的制程﹑制品的名称及编号(包括制程编号或零件编号,产品编号);2.制程责任单位:负责该制品的单位及组织的名称(客户亦须列入);3.相关单位:与该制品有关之各单位及组织的名称;4.供货商及制造工厂:自制或外包的厂商或工厂的名称;5.产品名称/编号:产品的名称及编号(包括自己的编号及客户使用的料号);6.设计定稿日期:填入该产品设计定稿的预计日期;7.负责人:负责制作FMEA表格之人员的姓名﹑职称及分机号码;8.FMEA定稿/更新日期:FMEA表格制作日期及更新日期;9.开始量产日期:量产预定开始日期;表格各项分析内容说明10.制程名称/功能:对被分析之作业或制程目的之描述,如果制程有多种不同的失效模式可能发生则制程应分开叙述;11.潜在的失效模式:指制品无法达到工程或特定要求的可能失效方式.制作制程FMEA时,必须假设进入制程的零件或材料皆为正确的,而且为确保各项考虑的正确性,取得信息的方式应以团队的方式进行,针对每一特定的作业,以零件或制程的特性来表达并列出所有可能的失效模式.建议找出失效模式的方式是比较类似的制程及审查客户对类似零件所做的反应与抱怨.另外,也要具备一些对设计目的了解的知识;12.潜在的失效效应:指如果失效模式发生,失效模式对客户可能造成的影响或效应.在这里所指的客户可为产品使用者或后续的作业,如客户所为使用者,则效应应以使用者所经验或注意到之用语来描述,如指为后作业,则以制程或作业上之续效用语来描述.13.严重度:参考设计FMEA;严重度指数评估标准1、Negligible(可忽略的),对产品的续效不太可能产生影响,使用者可能不会发觉任何缺失,对后续制程可能没有任何影响.2﹑3 Mild(轻度的),造成使用者一些轻度的使用不顺,但一般不会感觉到任何续效的变化,后续制程可能会有一些轻度的重工4﹑5﹑6 Moderate(中度的),使用者使用的不顺仍可忍受,但已感觉到一些续效及外观的变化,后续制程会有不定的重工及修理,机台可能会受损.7﹑8 High(高度的),使用之不顺已达无法忍受的地步,可能有无法达到续效要求的问题发生,后续制程可能会有主要的重工及机台受损.9﹑10 Very High(极高度的),续效已完全失去或未达到安全规定的要求,后续无法进行;14.重要产品特性:参考设计FMEA15.潜在失效原因:对失效模式如何发生的描述,描述的内容必须是能够改善或可控制的事情,针对每一失效模式应尽可能列出所有可能的原因,如果原因只有一个,则找出原因的部分可告一段落,但多数原因皆不只一个,应使用实验设计或其它方式找出主要且易控制的根本原因,在叙述失效原因时,应使用明确的错误或故障用语(例如:机器故障/作业员错误等);16.发生率:指某一特定失效原因而导致失效模式产生之可能性大小加以评估,以1到10的数字为表示,仅有为防范失效原因发生而使用的方法才能列入发生率之评估考虑中,为检出失效原因而做之检测不能列入.评估发生率时,如制程是在管制之内或与其它在统计管制之下之制程相似则须使用这些资料做评估,评估发生率可参考下列评估表:发生率指数评估标准1、emote(微乎其微),失效原因造成失效模式产生的机会微乎其微,或Cpk>=1.672、Evry Low(非常低),失效原因造成失效模式产生的机会非常低,或Cpk>=1.333、Low (很低),失效原因造成失效模式产生的机会很低,或Cpk>1.04﹑5﹑6 Moderate(较高),失效原因造成失效模式产生的机会较高或Cpk<=1.07﹑8 High(很高),失效原因造成失效模式产生的机会很高,或制程未在统计管制之下9﹑10 Very High(非常高),失效原因造成失效模式产生的机会非常高,几乎一定会发生17.现行的管制方式:指防范可能失效原因发生或检出失效原因及模式的各项现行管制方法,这些管制方法可以是防呆夹具或统计制程管制,也可以是制程后的检验或测试,非现有的管制方法必须放在议改善方案栏内;18.检出率:指零件离开生产线前,失效原因能被订出的管制方法检出的机率的大小,检出率大小以1至10的数字来表示,评估检出率可参考下列的评估表: 检出率指数评估标准1﹑2 Very High(非常高),管制方法几乎一定能找出失效的原因3﹑4 High(很高),管制方法能找出失效原因的可能性很高5﹑6 Moderate(高),管制方法可能可以找出失效原因7﹑8 Low(很低),管制方法可能不太容易找出失效原因9 Very Low(非常低),管制方法可能找不出失效原因10、Min-Detection ,管制方法找不出失效原因或根本没有管制方法19.风险指数值(RPN):为严重度﹑发生率及检出率三者指数的乘积,数字本身不具任何意义;表格内改善方案及处臵结果之各项内容说明20.建议改善方案及优先级:参考设计FMEA;欲减少发生率的指数,制程或设计必须加以变更,如欲降低严重度的指数惟有靠设计的变更,而欲改善检出指数,亦须变更制程或设计,但防止不良应较发生不良后再检出更为重要,所以重点应在防止而非检出,例如使用统计制程管制及制程改善而非随机抽样及全检.21.执行单位负责人及完成日期:参考设计FMEA;22.实际改善措施:参考设计FMEA;23.处臵结果的风险优先指数:改正措施完成后重新评估三项指数,未列改善措施的项目不需要计算,如有任何项目须进一步的改善措施时,重复(20)至(23)内各项内容.第11 頁,共11 頁。
福特FMEA评分准则

基本功 能丧失 或功能 降低
7
7
7
6
6
2/1000
6
次要功 能丧失 或功能 降低
一部分产品必须离线返工后 再被接受。
5
0.5/1000
中等
5
在来源处探 测问题
4 中等中 断 3 微小中 断 没有影 响
100%的产品在处理前,必须 在线返工。 一部分产品在处理前,必须 在线返工。 对过程、操作或操作员造成 轻微的不便。 没有可识别的影响
3
2
2
2
错误探测和/ 通过自动控制防止不规范的零件的生产,在 很高 或问题预防 岗位上实施错误(原因)的探测。 探测不适 用;错误预 防 有预防错误(原因)的夹具设计,机械设计 几乎可 或零件设计。由于过程/产品的防错设计, 以确定 不规范零件无法生产。
没有影 响
1
1
1
266357449.xlsx
Date Printed2015-6-13
EN-04-F-VDP0960A (08/13/2002)
STANDARD VEHICLE PFMEA RISK RANKINGS
Severity严重度 标准:对产品影响的严重度 (对顾客的影响) 潜在失效模式影响了汽车的安 全运行;或者包含不符合政府 法规的情形,失效发生时无预 警。 潜在失效模式影响了汽车的安 全运行;或者包含不符合政府 法规的情形,失效发生时有预 警。 基本功能丧失(汽车无法运 行,不影响汽车安全运行)。 基本功能降低(汽车可以运 行,但性能下降)。 次要功能丧失(汽车可以运 行,但舒适/便捷性能不可实 施)。 次要功能降低(汽车可以运 行,但舒适/便捷性能下降)。 有外观、可听噪音、汽车操作 项目上的问题,并且被绝大多 数顾客(75%)察觉到。 等级 影响 标准:对过程影响的严重度 (对制造/装配的影响) 会使操作员身处危险(机械 或装配),失效发生时无预 警。 会使操作员身处危险(机械 或装配),失效发生时有预 警。 产品需要被100%的废弃。生 产线关闭或中止发运。 一部分产品必须废弃。偏离 基本过程,包括降低生产线 速度或增人力。 100%的产品必须离线返工后 再被接受。 中等中 断 5 Occurrence频度 标准:原因 失效 等级 的发生频度 可能 性 10 ≥100/1000 很高 Detection 可探测度 等级 探测几率 没有探测几 率 在任何阶段 都不容易探 测 在后工序探 测问题 在来源处探 测问题 在后工序探 测问题 标准:通过过程控制来探测的可能性 探测可 能性 几乎不 可能4Leabharlann 0.1/10004
特殊特性及FMEA

品管技能提升培训
课程安排:
1、课程目的 2、课程思考 3、基本术语和概念 4、常用工具与方法 5、识别、评价与控制 6、案例分析 7、课程小结
1
课程目的
品管技能提升培训
课程目的:
利用关键的少数2/8原则理论,导入关 键质量特性概念及FMEA分析工具方法, 指导品管人员正确快速掌握识别关键特 性,使品控工作有的放矢,提高品检效 率和效果。
开始
完成 更新和评估
APQP第一阶段(计划和确 在APQP第二 概念变更时
定项目阶段)
阶段前
APQP第二阶段 (产品设用 中失效后
APQP第三阶段(过程设计 在试生产之 生产之后
和开发)
前
在设计阶段的早期,被指 在机器投入 根据故障发 定的设备和零部件可以进 使用之前 生情况 行改变的情况下
头脑风暴法、因 果图、相关性分
析等
潜在的失 效模式
潜在的失 效原因及
评价O
RPN如何?
优
先
PDCA循环
原
现行过程控
则
制及评价D
进一步采取措施
27
过程功 能、特 性或要 求是什 么?
后果怎 有多糟 么样? 糕?
能做什么? -设计更改 -过程更改 -特殊控制
会出现什么问题? -无功能
起因是 发生频 什么? 度如何?
3、特性:可以区分的特征。(A、可以固有的
或赋予的;B、可以定性的或定量的;C、有各种类别的,如物量的、 感官的、时间的、功能的等)
4、质量特性:与要求有关的,产品、 过程或体系的固有特性。
5、产品特性:是指在图纸或其它的工 程技术资料中所描述的零部件或总成的 特点与性能如尺寸、材质、外观、性能 等特性。
FMEA的分类.ppt

(1)~(5) 潛在的失效模式及后果分析(PFMEA)
(1)PFMEA編號:
(2)制程段:
(3)制程責任部門:
頁碼: 第 頁 共 頁
(5)機种名稱:
(6)關鍵日期:
(4)編制者:
(8)核心小組成員:
(7)FMEA日期(編制) (修訂)
(9)制程 功 能/要求
(10)潛 在 失效模 式
FMEA 使用講解
Potential Failure Mode and Effects Analysis
--- FMEA Team
REV: 01
FMEA的分類
FMEA分為兩個不同的部份 - DFMEA---設計FMEA
Design
- PFMEA---制程FMEA
Process
PFMEA
潛在的失效模式及后果分析(PFMEA)
嚴重度 10
9
8 7
6
5 4 3 2 1
(13)~(14)潛在的失效模式及后果分析(PFMEA)
(2)制程段: (5)機种名稱:
(3)制程責任部門: (6)關鍵日期:
(1)PFMEA編號:
頁碼: 第 頁 共 頁 (4)編制者:
(8)核心小組成員:
(7)FMEA日期(編制) (修訂)
(9)制程 功 能/要求
(15) 頻 度
(16)現行制 程控制
(17)探 測 度(D)
(18)風險 順序數
(修訂)
(19) 建 議 (20)責任及目 的 標完成日期 措 施
(21)采 取 的措施
嚴重 度 (S)
(22)措施結果
頻 探測
度
度
(RPN)
(O) (D)
质量管理五大核心工具之FMEA

质量管理五大核心工具之FMEA一、什么是FMEA:潜在的失效模式与后果分析(Potential Failure Mode and Effects Analysis),简称为FMEA,是一种定性的具有工程实用价值的可靠性分析方法。
使用这种方法,可以发现和评价产品/过程中一切潜在的失效模式,及早地指出根据经验判断出的弱点和可能发生的缺陷,并分析导致的失效后果和风险,最后在决策过程中找到能够避免或减少这些潜在失效发生的措施,并将这样一组系统化活动的整个过程文件化。
所有FMEA的重点在于设计,无论是用在设计产品或过程。
1、FMEA的由来:FMEA最早由美国航天工业于上世纪60年代所发展出来的一套信赖度分析工具。
北美福特公司于1972年发展信赖度训练计划时将FMEA包括与内。
发展至今,已被汽车工业界广为采用,并对提高汽车工业产品的可靠性卓有成效。
现在,无论在ISO/TS16949:2002体系标准中,还是在汽车行业顾客对供应商的质量能力评审中,都已明确规定必须采用FMEA。
2、FMEA的优点:由于FMEA是一种定性的分析方法,因此与定量的分析方法相比,FMEA就显得简便易懂,且较直观,易于被人们掌握并运用。
尤其是在一些不能用定量的可靠性数字说明问题的工程关键阶段,FMEA就更为适用。
3、FMEA的实施l 减少减少潜在的隐忧——使用FMEA作为专门的技术应用、以识别并减少潜在的隐患;——全面实施FMEA能够避免许多车辆抱怨事件的发生。
l 适时性是成功实施FMEA的最重要因素之一——是”事发前”的行为,要求FMEA必须在设计或过程失效模式被无意纳入产品或过程之前进行;——事先花时间完成FMEA分析,能更容易并低成本地对产品/过程进行修改,从而减轻事后修改的危机;.—— FMEA能够减少或消除因进行预防/纠正而带来更大损失的机会。
l FMEA适用场合——新设计、新技术或新过程。
该FMEA的领域是完成设计、技术或过程。
基于福特FMEA手册定义特殊特性识别方法整理

基于福特FMEA手册定义特殊特性识别方法整理以下内容是基于福特FMEA手册定义特殊特性识别方法整理特殊特性的识别管理一直是IATF16949体系及五大工具应用中的重点和难点,今天在这里和大家一起探讨下特殊特性的识别和管理:第一部分:特殊特性定义产品特性是一种可区分的特征,例如尺寸,大小,形状,位置,方向,质地,纹理,硬度,抗拉强度,外观,涂层,或反光率等,这些特征需要得到严格控制从而来保证达到预期的产品功能产品特性的公差范围:每个产品特性必须被定义在一定的公差范围内,才能确保预期的产品功能过程特性-会影响过程输出结果的可度量的过程输入特性以及它们的相互影响。
例如速度,温度,压力以及电压等-过程特性包括方法和流程,这些方法和流程能够确保生产操作的顺利进行从而来满足零部件的质量要求和其他目标,如产能要求等-过程特性包括操作条件和过程参数,比如生产节拍和生产维护要求关键特性(CC)-关键特性CC用倒置的三角形(?)表示。
是指那些能够影响到是否符合政府法规,整车安全或产品功能的产品要求(比如尺寸,性能要求,材料规范)或者过程参数(比如比率,温度,压强)-关键特性需要包含在控制计划中,并有相应的生产,装配,运输和监控的具体措施-潜在的关键特性:在DFMEA中被划分为YC一类的产品特性。
这些特性与严重度为9或10的潜在失效模式有直接的因果关系(产品特性或过程参数不符合规范或变差较大,并最终导致了某个失效模式的发生,则可以说该特性与该失效模式有因果关系)例如:门锁的横向载荷和纵向载荷国标有要求,为CC特性,主要和门锁的棘轮、棘爪和锁扣强度有关,与之相关的棘轮、棘爪和锁扣的热处理工艺参数需列为CC项重要特性(SC)-重要特性SC是指对客户满意度影响比较大的产品、过程和试验要求-重要特性需要包含在控制计划中进行控制潜在重要特性:当某个产品特性满足如下条件时,在DFMEA中应该将其划为YS类别:该特性与严重度为5-8的潜在失效模式有因果关系。
FMEA介绍绝对经典版)

Documentation 存档
When can FMEA documents be discarded? 什么时候可以处理掉FMEA文档
FMEA的更新由责任单位负责(产品、制造)。
FMEA 介绍
什么时候做FMEA?
DFMEA: 在设计概念前或决定时起动; 在该项目产品开发的各个阶段进行更新。
PFMEA: 在可行性分析前或开始时起动。
FMEA 介绍
要求何时“阶段性”完成?
FMEA是动态的文档; FMEA阶段性“完成”也针对特定项目的产品或过程
FMEA 可以看作是有系统的一组活动,包括:
a) 辨认并且评估潜在的产品/工艺缺陷及该缺陷可能造成的 影响;
b) 找出可以除去或减少潜在问题发生机会的方法; c) 为整个过程提供文件资料。
FMEA是确定哪些设计或工艺必须要用才能使顾客满意 的补充手段。
FMEA 介绍
FMEA方法应用的要点
这是一套方法,不是一堆制式表格。制式表格是推荐使 用的工具;
P-Diagram P图
Identifies Noise and Control Factors and Error States 识别噪音因素,控制因素和误差状态
FMEA (with Robustness
Linkages) FMEA(有稳健联系的)
Robustness and Reliability Checklist 稳健和可靠的检查清单
Scope incorrectly done: 不正确的范围会: Lengthens analysis 扩大分析 Misses target analysis 偏离目标分析 Identifies wrong team membership 错误地识别小组成员
FMEA百度百科
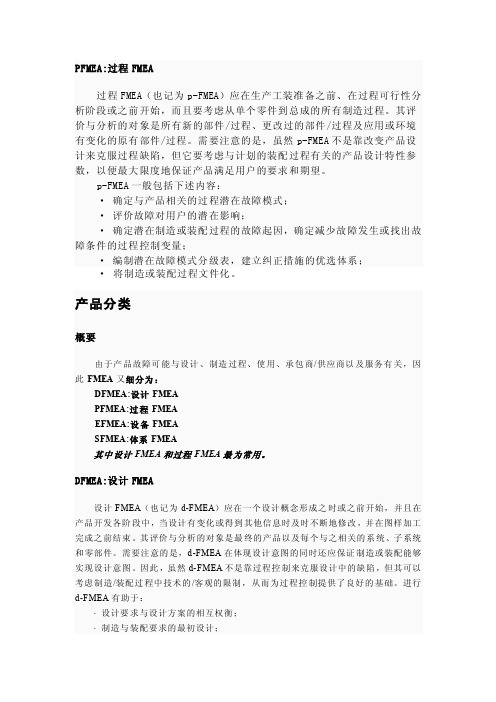
PFMEA:过程FMEA过程FMEA(也记为p-FMEA)应在生产工装准备之前、在过程可行性分析阶段或之前开始,而且要考虑从单个零件到总成的所有制造过程。
其评价与分析的对象是所有新的部件/过程、更改过的部件/过程及应用或环境有变化的原有部件/过程。
需要注意的是,虽然p-FMEA不是靠改变产品设计来克服过程缺陷,但它要考虑与计划的装配过程有关的产品设计特性参数,以便最大限度地保证产品满足用户的要求和期望。
p-FMEA一般包括下述内容:· 确定与产品相关的过程潜在故障模式;· 评价故障对用户的潜在影响;· 确定潜在制造或装配过程的故障起因,确定减少故障发生或找出故障条件的过程控制变量;· 编制潜在故障模式分级表,建立纠正措施的优选体系;· 将制造或装配过程文件化。
产品分类概要由于产品故障可能与设计、制造过程、使用、承包商/供应商以及服务有关,因此FMEA又细分为:DFMEA:设计FMEAPFMEA:过程FMEAEFMEA:设备FMEASFMEA:体系FMEA其中设计FMEA和过程FMEA最为常用。
DFMEA:设计FMEA设计FMEA(也记为d-FMEA)应在一个设计概念形成之时或之前开始,并且在产品开发各阶段中,当设计有变化或得到其他信息时及时不断地修改,并在图样加工完成之前结束。
其评价与分析的对象是最终的产品以及每个与之相关的系统、子系统和零部件。
需要注意的是,d-FMEA在体现设计意图的同时还应保证制造或装配能够实现设计意图。
因此,虽然d-FMEA不是靠过程控制来克服设计中的缺陷,但其可以考虑制造/装配过程中技术的/客观的限制,从而为过程控制提供了良好的基础。
进行d-FMEA有助于:·设计要求与设计方案的相互权衡;·制造与装配要求的最初设计;·提高在设计/开发过程中考虑潜在故障模式及其对系统和产品影响的可能性;·为制定全面、有效的设计试验计划和开发项目提供更多的信息;·建立一套改进设计和开发试验的优先控制系统;·为将来分析研究现场情况、评价设计的更改以及开发更先进的设计提供参考。
FMEA-编制方法
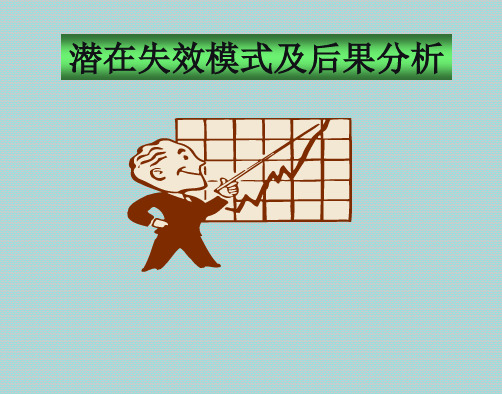
部件FMEA
设计FMEA 过程FMEA
整理课件
21
系统FMEA – 实 施 步 骤
第一步 第二步 第三步 第四步 第五步
系统单元 与
功系能统与结功构 能结构
缺陷分 析
风险评 价
优化
整理课件
分解
输入、输出、 内部功能 失效模式
RPN值
采取措施
22
产 品 系 统 FMEA
确定产品系统的结构 :
底盘系 统
– 确定系统单元并说明其功 能关系(结构树/功能树)。
整车
– 每一系统单元可能的失效
失效
模式。
发动机 驱动轴
失效 – 确定不同系统单元失效模
动力系统 传动器
失效
失效
齿轮
式间的逻辑关系
离合器
失效
整理课件
23
过 程 系 统 FMEA
过程1
整个过程 失效
过程 2 失效
分过程2.1
分过程 2.2失效
分过程2.3
•活塞 尺寸和材料是否 满足间隙的需求?
Herstellung betrachtet
•活塞 活塞销能否 被装错?
•Pleul Ist das Pleul in jeder Lage im Package genügend Freigang
•连杆 Ist die Pleulform den Anforderungen entsprechend konzipiert?
潜在失效模式及后果分析
课程内容
一、FMEA概 述
FMEA的定义、起源 FMEA的实施、跟踪 FMEA的分类
二、设计 FMEA
三、过程 FMEA
设计FMEA简介 设计FMEA的实施
- 1、下载文档前请自行甄别文档内容的完整性,平台不提供额外的编辑、内容补充、找答案等附加服务。
- 2、"仅部分预览"的文档,不可在线预览部分如存在完整性等问题,可反馈申请退款(可完整预览的文档不适用该条件!)。
- 3、如文档侵犯您的权益,请联系客服反馈,我们会尽快为您处理(人工客服工作时间:9:00-18:30)。
福特制定FMEA时如何对特性进行分类
在制定FMEA时如何对产品或过程特性进行分类,经常是一个棘手的问题。
主要在于对各种特性的称谓不一致、没有具体的定义或定义模糊。
这里根据汽车行业的应用,对各种特性的分类做个归纳。
在产品规格中所确定的特性我们称之为“产品特性”(PC: Product Characteristic),在生产过程中需要控制的特性我们称之为“过程特性”或“控制特性”(CC: Control Characteristic)。
针对这两类特性进行重要性分类时,我们经常会碰到“特殊特性”(Special Characteristic)、“关键特性”(Key Characteristic)、“关键特性”(Critical Characteristic)、“重要特性”(Significant Characteristic)等分类术语。
一般来说,“特殊特性”(Special Characteristic)实际上包含了“关键特性”(Critical Characteristic)和“重要特性”(Significant Characteristic)这两类需要重点关注的特性,“关键特性”(Critical Characteristic)主要是与安全和法律法规要求相关的特性(在FMEA 中,其严重度S通常为9或10),而“重要特性”(Significant Characteristic)则是与装配性、性能等密切相关的特性(在FMEA中,其严重度S通常为5至8并且发生度O为4至10)。
“关键特性”(Key Characteristic)则与“特殊特性”(Special Characteristic)具有大致相同的含义,只是汽车行业中不同称谓而已。
于是,我们经常能见到KPC (关键产品特性:Key Product Characteristic)和KCC(关键控制特性: Key Control Characteristic)等术语,产品特性是由过程控制特性保证的,因此往往相应的KPC和KCC是互相关联的。
在福特,其对“特殊特性”(Special Characteristic)规定得比较细致,其规定的“特殊特性”(Special Characteristic)细分得更多,参见下图(需要清晰查看,可点击图片)。
当我们对于特性的分类不甚了解时,建议参考福特的分类方法来明确各类特殊特性。