注塑机性能测试
注塑模具试模报告(最完美)

注塑模具试模报告引言注塑模具试模是一个关键的过程,它对产品的质量和生产效率具有重要影响。
本报告旨在详细介绍注塑模具试模过程中的各个环节,为了实现最完美的结果,我们将从模具设计、材料选择、工艺参数设置、试模测试以及优化改进等方面进行阐述。
概述注塑模具试模是在注塑机上进行的模具性能测试过程,通过对模具进行试模可以评估其性能和功能的可靠性,以确保产品能够满足设计要求。
试模过程中需要考虑模具的定位精度、注塑过程的稳定性、产品的成型质量等因素。
正文内容一、模具设计1. 模具结构设计:模具的结构设计应考虑产品的设计要求和注塑工艺的特点,确保模具能够精确定位并顺利进行注塑过程。
2. 模具材料选择:模具的材料选择应考虑产品的成型要求、生产批量和模具寿命等因素,常用的模具材料有硬质合金、工具钢、不锈钢等。
二、材料选择1. 塑料材料选择:根据产品的用途和要求选择合适的塑料材料,考虑其热稳定性、机械性能、耐化学腐蚀性等。
2. 材料预处理:塑料材料在注塑前需要进行干燥处理,以确保材料的质量和注塑过程的稳定性。
三、工艺参数设置1. 注射压力与速度设置:注射压力和速度的设置应根据产品形状、尺寸和壁厚等因素进行合理调整,以防止产生缺陷,如短射、热裂纹等。
2. 注射温度控制:注射温度的控制对于保证产品的成型质量至关重要,应根据塑料材料的熔融温度进行合理设定。
3. 模具温度控制:模具温度的控制能够影响产品的收缩和表面质量,应根据塑料材料的热性能设定合适的温度。
四、试模测试1. 注塑工艺试模:在试模过程中,通过调整工艺参数进行试模测试,如调整注射速度、温度等,评估产品的造型效果和成型质量。
2. 模具寿命测试:通过连续进行多次试模测试,以评估模具的寿命和性能稳定性,确定模具是否需进行改进或调整。
五、优化改进1. 问题分析和解决:根据试模测试的结果,分析产生的缺陷及其原因,并提出相应的解决方案,如调整工艺参数、优化模具结构等。
2. 模具维护与保养:及时进行模具的维护和保养工作,延长模具的使用寿命,提高生产效率和产品质量。
注塑车间质量控制流程

注塑车间质量控制流程一、原料入库检验核对数量:对采购的原料进行数量清点,确保数量准确。
检查外观:观察原料有无明显的破损、污渍、杂质等不良现象。
性能测试:抽取部分原料进行物理性能测试,如拉伸强度、冲击强度等,确保符合生产要求。
记录存档:对入库原料的检验结果进行详细记录,并存档备查。
不合格处理:对不合格原料进行标识、隔离,并通知采购部门进行处理。
二、生产过程监控工艺参数监控:对注塑机的温度、压力、时间等工艺参数进行实时监控,确保在工艺范围内。
半成品检验:对生产的半成品进行外观、尺寸、性能等方面的检验,防止不良品流入下道工序。
过程记录:对生产过程中的关键参数、检验结果等进行详细记录,以便追溯和改进。
不良品处理:对生产过程中出现的不良品进行标识、隔离,并分析原因,采取措施防止再次发生。
监控结果反馈:定期将生产过程监控的结果反馈给相关部门,以便及时调整和优化生产过程。
三、产品出库检测抽样检验:按照规定的抽样方案对即将出库的产品进行抽样检验。
外观检查:对产品的外观进行详细检查,确保无明显缺陷。
性能测试:对产品的物理性能进行测试,如抗冲击、抗老化等性能。
不合格处理:对不合格产品进行标识、隔离,并进行返工或报废处理。
出库记录:对出库产品的数量、质量等信息进行详细记录,以便追溯。
四、设备维护与保养日常保养:定期对设备进行清洁、润滑、紧固等保养工作,确保设备正常运行。
定期检查:对设备的运行状态、磨损情况进行定期检查,及时发现并处理问题。
维修记录:对设备的维修、保养情况进行详细记录,以便分析设备状况和制定保养计划。
维修流程:制定详细的设备维修流程,确保维修工作顺利进行。
备件管理:对设备备件进行妥善保管,确保备件充足且无损坏。
五、环境与安全卫生环境:保持注塑车间的整洁卫生,防止产品受到污染。
安全防护:确保注塑车间具备完善的安全防护设施,如防爆、防火设施等。
安全生产:制定并执行安全生产规章制度,确保员工的人身安全和企业的财产安全。
注塑机检测报告
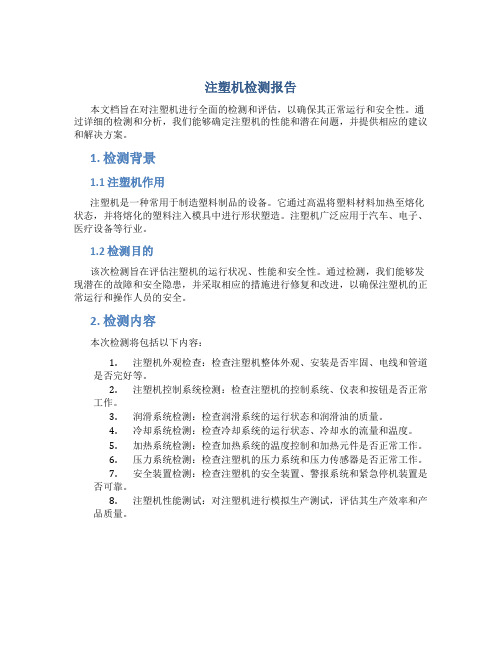
注塑机检测报告本文档旨在对注塑机进行全面的检测和评估,以确保其正常运行和安全性。
通过详细的检测和分析,我们能够确定注塑机的性能和潜在问题,并提供相应的建议和解决方案。
1. 检测背景1.1 注塑机作用注塑机是一种常用于制造塑料制品的设备。
它通过高温将塑料材料加热至熔化状态,并将熔化的塑料注入模具中进行形状塑造。
注塑机广泛应用于汽车、电子、医疗设备等行业。
1.2 检测目的该次检测旨在评估注塑机的运行状况、性能和安全性。
通过检测,我们能够发现潜在的故障和安全隐患,并采取相应的措施进行修复和改进,以确保注塑机的正常运行和操作人员的安全。
2. 检测内容本次检测将包括以下内容:1.注塑机外观检查:检查注塑机整体外观、安装是否牢固、电线和管道是否完好等。
2.注塑机控制系统检测:检查注塑机的控制系统、仪表和按钮是否正常工作。
3.润滑系统检测:检查润滑系统的运行状态和润滑油的质量。
4.冷却系统检测:检查冷却系统的运行状态、冷却水的流量和温度。
5.加热系统检测:检查加热系统的温度控制和加热元件是否正常工作。
6.压力系统检测:检查注塑机的压力系统和压力传感器是否正常工作。
7.安全装置检测:检查注塑机的安全装置、警报系统和紧急停机装置是否可靠。
8.注塑机性能测试:对注塑机进行模拟生产测试,评估其生产效率和产品质量。
3. 检测方法与步骤3.1 注塑机外观检查1.检查注塑机的外观,包括机身、进料口、模具接口等,确保没有明显的损坏或变形。
2.检查注塑机的安装,确保其稳固且无松动现象。
3.检查注塑机的电线和管道,确保其完好且没有漏电现象。
3.2 注塑机控制系统检测1.检查注塑机的控制系统,包括控制面板、仪表和按钮,确保其正常工作。
2.检查注塑机的温度控制系统,验证温度传感器和控制器的准确性和稳定性。
3.3 润滑系统检测1.检查润滑系统的润滑油质量,确保其清洁度和充足度。
2.检查润滑系统的运行状态,包括润滑油泵的工作情况和润滑点的润滑情况。
注塑车间质量控制流程

注塑车间质量控制流程一、背景介绍注塑车间是创造业中常见的生产工序之一,质量控制流程对于保证产品质量和提高生产效率至关重要。
本文将详细介绍注塑车间质量控制流程的各个环节和要求。
二、原材料检验1. 原材料到货时,质检人员应进行外观检查、尺寸检查和物理性能测试,以确保原材料符合要求。
2. 原材料应按照规定的存储条件进行储存,确保不受潮、变质或者受到其他污染。
三、模具检验1. 模具在使用前应进行全面的检查,确保模具无损坏、磨损或者其他缺陷。
2. 模具的尺寸和结构应符合产品要求,可进行模具试模,确保产品质量。
四、注塑工艺参数设定1. 根据产品要求和模具特性,设定合适的注塑工艺参数,包括注射压力、注射速度、保压时间等。
2. 工艺参数设定后,需要进行试模验证,确保产品尺寸、外观和物理性能符合要求。
五、注塑过程控制1. 操作人员应按照工艺参数设定进行注塑操作,确保每一个注塑周期的稳定性和一致性。
2. 注塑过程中,需要定期检查注塑机的运行状态,确保设备正常工作。
六、成品检验1. 从注塑机上取下的成品应进行外观检查、尺寸检查和物理性能测试,以确保产品符合要求。
2. 成品的外包装应符合规定,防止在运输过程中受到损坏。
七、不良品处理1. 如发现不良品,应即将住手生产,并进行不良品分析,找出问题的原因。
2. 对不良品进行分类、记录和处理,防止不良品流入下道工序或者出厂。
八、质量记录和统计1. 每一个注塑周期的工艺参数、注塑过程操纵情况、成品检验结果等应进行记录,以便后续分析和追溯。
2. 根据质量记录,进行质量统计和分析,及时发现问题并采取措施改进。
九、持续改进1. 根据质量记录和统计结果,进行问题分析和改进措施的制定。
2. 定期组织质量改进会议,总结经验教训,推动质量管理的持续改进。
以上是注塑车间质量控制流程的详细介绍,通过严格执行质量控制流程,可以确保产品质量的稳定性和一致性,提高生产效率和客户满意度。
注塑机试模方法及注意事项
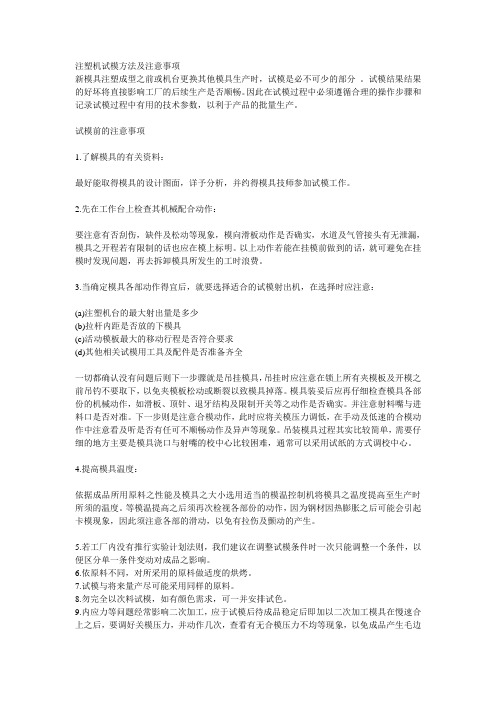
注塑机试模方法及注意事项新模具注塑成型之前或机台更换其他模具生产时,试模是必不可少的部分。
试模结果结果的好坏将直接影响工厂的后续生产是否顺畅。
因此在试模过程中必须遵循合理的操作步骤和记录试模过程中有用的技术参数,以利于产品的批量生产。
试模前的注意事项1.了解模具的有关资料:最好能取得模具的设计图面,详予分析,并约得模具技师参加试模工作。
2.先在工作台上检查其机械配合动作:要注意有否刮伤,缺件及松动等现象,模向滑板动作是否确实,水道及气管接头有无泄漏,模具之开程若有限制的话也应在模上标明。
以上动作若能在挂模前做到的话,就可避免在挂模时发现问题,再去拆卸模具所发生的工时浪费。
3.当确定模具各部动作得宜后,就要选择适合的试模射出机,在选择时应注意:(a)注塑机台的最大射出量是多少(b)拉杆内距是否放的下模具(c)活动模板最大的移动行程是否符合要求(d)其他相关试模用工具及配件是否准备齐全一切都确认没有问题后则下一步骤就是吊挂模具,吊挂时应注意在锁上所有夹模板及开模之前吊钓不要取下,以免夹模板松动或断裂以致模具掉落。
模具装妥后应再仔细检查模具各部份的机械动作,如滑板、顶针、退牙结构及限制开关等之动作是否确实。
并注意射料嘴与进料口是否对准。
下一步则是注意合模动作,此时应将关模压力调低,在手动及低速的合模动作中注意看及听是否有任可不顺畅动作及异声等现象。
吊装模具过程其实比较简单,需要仔细的地方主要是模具浇口与射嘴的校中心比较困难,通常可以采用试纸的方式调校中心。
4.提高模具温度:依据成品所用原料之性能及模具之大小选用适当的模温控制机将模具之温度提高至生产时所须的温度。
等模温提高之后须再次检视各部份的动作,因为钢材因热膨胀之后可能会引起卡模现象,因此须注意各部的滑动,以免有拉伤及颤动的产生。
5.若工厂内没有推行实验计划法则,我们建议在调整试模条件时一次只能调整一个条件,以便区分单一条件变动对成品之影响。
6.依原料不同,对所采用的原枓做适度的烘烤。
注塑机使用率标准

注塑机的使用率标准通常涉及到多个方面的性能评估,包括但不限于机器的效率、合格品率、时间开动率以及节拍时间等。
具体来说,可以从以下几个方面来评估注塑机的使用率:
1. 效率:效率可以通过计算计划节拍数来评估,即开动时间除以标准节拍时间。
这个指标反映了注塑机在规定时间内完成工作的能力。
2. 合格品率:合格品率是指生产出的合格品数量与加工总数量的比例。
这个比例越高,说明注塑机的生产效率和产品质量越好。
3. 时间开动率:时间开动率是指注塑机在计划生产时间内实际运行的时间比例。
一个高的时间开动率意味着机器的利用率高,停机时间少。
4. 节拍时间:节拍时间是指完成一个生产周期所需的时间。
短的节拍时间可以提高生产效率,但也需要确保产品质量不受影响。
此外,注塑机的使用还受到相关标准的规范,例如GB/T 41102-2021《包装PET瓶坯注塑成型模具系统通用技术要求》等,这些标准规定了注塑机的型号、基本参数、要求、检测方法等内容。
综上所述,在选择和使用注塑机时,操作人员应该综合考虑机器的性能指标,并参照相关标准来确保注塑机的高效运行和产品质量。
同时,了解注塑机的工作原理和性能特点也是非常重要的,这有助于更好地维护和优化生产过程。
注塑实验总结报告

注塑实验总结报告注塑实验总结报告注塑实验是材料工程专业学生必修的一门实验课程。
通过这门实验课程,我们学习了注塑技术的原理和操作方法,掌握了塑料材料的特性及其在注塑过程中的变化规律。
本次实验使用了聚丙烯(PP)作为塑料材料,通过调整注塑工艺参数,如温度、压力、注塑时间等,获得了不同的注塑产品,并对其进行了测试分析。
以下是本次注塑实验的总结报告。
一、实验目的本次实验的目的是通过注塑工艺制作出符合要求的聚丙烯产品,并对其进行性能测试,以评估注塑工艺参数对产品性能的影响。
二、实验步骤1. 准备工作:将聚丙烯颗粒加入注塑机的料斗中,根据要求设置好注塑机的温度、压力等参数。
2. 开始注塑:启动注塑机,使其预热到设定温度,然后将熔融状态的聚丙烯注入模具腔内,开始注塑过程。
3. 注塑完毕:注塑时间结束后,等待注塑产品冷却,然后取出注塑产品。
4. 进行性能测试:对注塑产品进行拉伸强度、抗冲击性等性能测试,记录测试结果。
三、实验结果通过调整温度、压力等参数,我们成功制作出了一批聚丙烯注塑产品。
在测试过程中,我们发现不同的工艺参数对注塑产品的性能有着明显的影响。
首先,我们发现调节温度对产品质量有着重要影响。
过高或过低的温度都会导致产品的性能下降。
在合适的温度范围内,产品的拉伸强度、抗冲击性等性能指标较好。
其次,压力的控制也十分关键。
过高的压力会导致产品变形不完整或出现气孔等缺陷,而过低的压力则会影响产品的密实性。
我们通过调整压力,找到了最佳的注塑条件,从而获得了质量较好的产品。
最后,注塑时间的控制也非常重要。
过长的注塑时间会导致产品的热变形,而过短的注塑时间则会使产品缺乏韧性。
我们通过实验发现,适当的注塑时间能够保证产品的良好性能。
四、存在的问题与改进在本次实验中,我们发现了一些问题,需要进行改进。
首先,需要加强对注塑机操作方法的学习,以提高操作的熟练度。
其次,对于工艺参数的调整还需要进一步的研究和实践,以获得更好的产品质量。
注塑试料报告范文

注塑试料报告范文注塑试料报告范文一、试料介绍本次试验的注塑试料是一种高分子材料,主要成分是聚丙烯,外观为白色颗粒状。
该材料具有良好的加工性能、高韧性、耐热性和耐化学腐蚀性能。
该材料被广泛应用于各种塑料制品的生产中,如塑料袋、塑料瓶等。
二、试验目的本次试验的目的是测试注塑试料的物理与力学性能,包括密度、熔指、模塑温度、成型温度、流动性能、拉伸强度、断裂伸长率等参数,以评估该材料的性能指标,并为其应用提供可靠的参考数据。
三、试验设备本次试验使用的主要设备包括:注塑机、热分析仪、拉伸试验机、电子天平、流变仪等。
四、试验方法1.密度测试:按照ISO 1183标准测定,采用水的置换法进行测试。
2.熔指测试:采用热分析仪测量该材料在一定温度下的熔化温度。
3.模塑温度测试:在注塑机上进行测试,采用不同的温度范围进行注塑。
4.成型温度测试:在注塑机上进行测试,采用不同的温度范围进行注塑。
5.流动性能测试:采用流变仪进行测试,测量该材料在不同温度下的流动性能。
6.拉伸强度测试:采用拉伸试验机进行测试,测量该材料在拉伸过程中的强度参数。
7.断裂伸长率测试:采用拉伸试验机进行测试,测量该材料在拉伸过程中的变形程度。
五、试验结果1.密度:该材料的密度为0.95g/cm³。
2.熔指:该材料的熔点为162℃。
3.模塑温度:较理想的模塑温度范围为150℃-175℃。
4.成型温度:较理想的成型温度范围为160℃-180℃。
5.流动性能:该材料在不同温度下的流动性能较好,流动率随温度升高而增加。
6.拉伸强度:该材料拉伸强度较高,达到33MPa左右。
7.断裂伸长率:该材料在拉伸过程中的变形程度较大,断裂伸长率为40%左右。
六、结论综上所述,该注塑试料具有优良的物理与力学性能,密度小、熔点低、流动性好、拉伸强度高、断裂伸长率大等特点,适合用于各种塑料制品的生产。
但是在实际生产中仍需根据具体情况进行温度调整以达到更好的加工效果。
注塑出货检验报告

注塑出货检验报告
一、项目背景
二、出货检验内容和方法
1.物理性能检验:使用拉力试验机对产品进行拉伸强度、断裂伸长率和冲击强度的测试。
2.尺寸精度检验:使用三坐标测量仪对产品进行尺寸精度测量。
3.外观质量检验:对产品进行外观缺陷、色差、划痕等方面的目测检查和电子显微镜观察。
三、出货检验结果
1.物理性能检验结果:
-拉伸强度:根据客户要求,产品的拉伸强度应不低于50MPa,经测试,该产品的拉伸强度为55MPa,符合要求。
-断裂伸长率:根据客户要求,产品的断裂伸长率应不低于20%,经测试,该产品的断裂伸长率为23%,符合要求。
-冲击强度:根据客户要求,产品的冲击强度应不低于5kJ/m²,经测试,该产品的冲击强度为6kJ/m²,符合要求。
2.尺寸精度检验结果:
-经使用三坐标测量仪测量,产品的尺寸精度在允许误差范围内,符合要求。
3.外观质量检验结果:
-目测检查和电子显微镜观察结果显示,产品表面无明显缺陷、色差和划痕等问题。
四、结论与建议
通过注塑出货检验,我们得出以下结论:
1.产品的物理性能符合要求,具有较好的拉伸强度、断裂伸长率和冲击强度。
2.产品的尺寸精度在允许误差范围内,符合要求。
3.产品的外观质量良好,无明显缺陷、色差和划痕等问题。
建议:
1.继续保持生产工艺的稳定性,确保产品的一致性和稳定性。
2.加强员工培训,提高操作技术和质量意识,以确保产品质量不断提升。
3.与客户进行及时沟通,了解其需求变化,并根据客户的反馈持续改进产品质量和服务满意度。
注塑检验成绩报告

注塑检验成绩报告1. 引言注塑检验是在注塑生产过程中对产品进行质量控制的重要环节。
本报告旨在总结和分析最近一次注塑检验的成绩,以便对生产过程进行改进和优化。
2. 检验目的本次注塑检验的主要目的是评估注塑产品的质量,并识别任何潜在的质量问题。
通过分析成绩报告,我们可以及时发现和解决问题,从而提高产品的一致性和可靠性。
3. 检验方法在注塑检验中,我们使用了以下几种常见的检验方法:3.1 外观检验外观检验是通过目视检查产品外观来评估其质量。
我们检查了产品的颜色、表面光滑度和任何可见的缺陷。
这些缺陷可能包括气泡、瘢痕、裂纹等。
3.2 尺寸检验尺寸检验是通过使用测量工具来检查产品的尺寸是否符合规定的要求。
我们测量了产品的长度、宽度、高度和任何其他关键尺寸。
3.3 物理性能测试物理性能测试是通过对产品进行力学测试来评估其强度和耐久性。
我们测试了产品的抗拉强度、抗冲击性能等。
4. 检验结果根据对样品的检验和测试,我们得出了以下结果:4.1 外观检验结果样品的外观无明显缺陷,颜色均匀,表面光滑度良好。
4.2 尺寸检验结果样品的尺寸符合规定的要求,长度、宽度、高度等尺寸均在允许范围内。
4.3 物理性能测试结果样品的抗拉强度达到了预期的要求,能够承受一定的冲击力。
5. 结论根据本次注塑检验的结果,我们可以得出以下结论:1.注塑产品的外观质量良好,没有明显的缺陷。
2.注塑产品的尺寸符合规定的要求,满足设计要求。
3.注塑产品的物理性能良好,能够满足使用要求。
6. 改进措施鉴于本次注塑检验结果良好,我们仍然可以提出一些建议的改进措施,以进一步提高产品质量:1.定期检查注塑机的运行状态,确保其正常工作。
2.加强原材料的质量控制,确保注塑产品的原材料符合要求。
3.提供员工培训,提高其注塑产品检验的技能和水平。
7. 结语本次注塑检验成绩报告总结了注塑产品的质量状况,并提出了一些改进措施。
通过持续的质量控制和改进,我们相信可以进一步提高注塑产品的质量和可靠性。
注塑机验证报告材料的
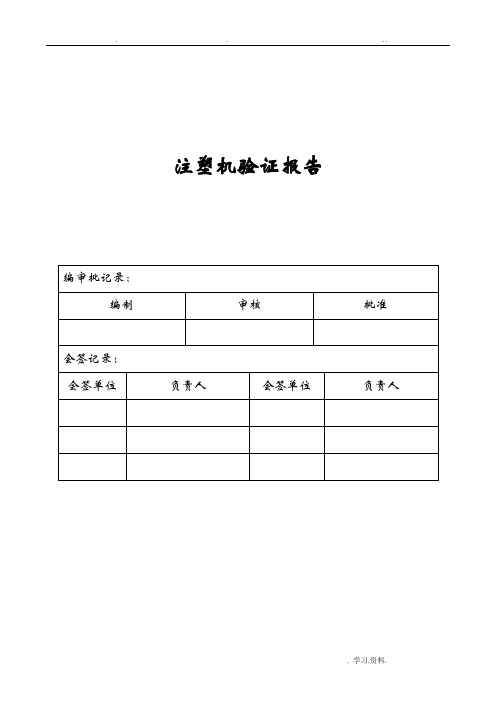
. . . .注塑机验证报告目次1. 概述公司产品为**管医疗器械,属于II类无菌器械,与负压吸引装置配套使用,该产品用于人工流产手术,产品组成有导管和手柄,其中手柄材料为PP材料,型号为5、6、7、8号,其中5号适用于单管,其余适于单管和双管产品,导管手柄采用注塑方法制造,要求手柄外观整齐、无毛刺、无注塑缺陷,为达到此目的,特展开以下确认工作。
2.目的通过验证,证实EH160B注塑机能够实现**管正常生产,并为正常生产和工艺文件编写提供参数依据。
3.围本方案适用于公司生产车间***型注塑机安装、运行和性能验证。
4.职责技术部负责起草验证方案,负责配合设备的安装调试过程,主要参与性能验证。
生产部负责对验证活动的开展实施和过程记录。
质管部负责验证方案的审核,负责对验证过程的监控和检验。
管理者代表负责方案和报告的最后批准。
5.验证小组6.注塑机安装确认(IQ)6.1注塑机基本信息6.2注塑机系统描述设备结构:主要由液压系统、锁模系统和射台系统等部分组成。
技术参数:见操作说明书6.3注塑机资料档案和备件检查6.4 注塑机安装要求确认6.3安装确认小结7.运行确认(OQ)7.1 运行物料确认确认物料名称、批号、模具和检测设备等,并保证与性能确认时一致。
7.2. 验证方法:a)根据厂家提供的模具对温度、注射压力、注射速度、保压时间、冷却时间等数值作为基础设定,初始数据设定为:b)参数调节:样品制出后需对整摸样品进行初检,主要观测其外观和主要尺寸是否符合产品要求,待产品基本符合要求后对工艺进行微调。
工艺调节为温度每次调节差值为 5 ℃,压力和速度调节差值为 5 %,保压时间调节差值为0.5 s,冷却时间调节值为 1 s。
c)取样:手柄模具为16腔,对每组工艺参数下所有样品进行检验,要求符合要求(见技术图纸)。
d)最佳工艺选择、注塑工艺围的确定:根据样品测量的结果对生产工艺参数进行判定,产品尺寸符合图纸要求则该工艺为产品注塑的最佳工艺。
SPC在注塑成型过程中的应用解析

摘要关键词SPC 注塑成型参数分布状态过程能力控制图SPC从问世以来,得到很大的推广。
汽车行业的ISO/TS16949:2000技术规范把SPC作为一项工具要求在产品开发和生产中进行使用。
对SPC在生产过程中运用所带来的好处就是预防控制、获得改进机会,但在与具体的生产结合过程中,就会碰到这些问题,如何选择监控参数并进行测量,这些参数的分布模式是什么样的,如何计算过程能力,如何建立控制图等。
下面就开始探讨在注塑成型过程中这些问题该如何解决。
一、监测参数和测量注塑成型过程的控制水平在很大程度上取绝于测量系统的完善程度。
这就意味着不仅需要合理地选择所要测量的过程参数,而且要正确的使用传感器、转换器,并将其置于正确的位置。
通过对所选的参数进行在线监测,在理想的资源配备状态下,把这些参数值输入计算机,就可以计算出极差、控制限、标准偏差等并得到控制图。
以此为基础的实时SPC对于过程的精密监控是非常有用的。
1、注塑制品的质量参数反映产品质量的参数有尺寸、重量、外观、性能。
1.1尺寸的定义是容易的,在开发产品中,对重要的尺寸基本上需要进行过程能力计算。
根据测量方法,可获得计量型数据,也可转化为计数型数据。
1.2单个外观缺陷及其优劣的定义对外观缺陷分两类,一类是难以明确测量的缺陷如:烧焦、分层剥离、油渍、溢料飞边、蛇形、空洞和熔接痕等,这些缺陷很难给予度的量测,但通过观察可以给出以下区分其优劣的定义。
Yi={ 0(合格)如果缺陷已消除(式 1 )Yi= 1(不合格)如果缺陷未消除{-1 缺陷改进△Yi= 0 缺陷 没 有变化(式 2)+1 缺陷恶化式中 Yi ------- 第i 种缺陷,1=1, 2, 3, • • • m 种缺陷;△Yi ——定性质量的改变。
可以明确测量的缺陷如:色泽、波流痕、光泽不良、萎缩、欠注、 凹陷和翘曲变形等。
对这类数据有两种处理办法,一是直接用计量型 数据进行统计,二是转化为二元判断后的计数型数据,如下转化:Y i 二0 如果 yi W bi =1 如果 yi >bi-1 如果 A yi V O△Yi =0 如 果 △ yi =0 =+1 如果△%> 0式中yi ——第i 种缺陷的测量值;bi ——无缺陷的上限值。
塑料制品检验规范

塑料制品检验规范引言:塑料制品广泛应用于生活和工业领域,质量安全成为社会关注的焦点。
为了确保塑料制品的质量和安全性,制定、实施和遵守规范、规程和标准是非常重要的。
本文将介绍塑料制品检验的规范和标准,从原材料检验、生产工艺控制到成品质量检验等方面进行详细论述,以期提高塑料制品质量标准的制定和执行。
一、原材料检验1.1 物理性能:原材料的物理性能是塑料制品质量的基础,必须进行全面的物理性能测试,如密度、熔融指数、拉伸强度等。
1.2 成分分析:通过化学分析技术,检测原材料中的添加剂含量、杂质等,确保原材料的成分符合标准要求。
1.3 金属杂质:采用金属探测仪进行原材料检验,以排除金属杂质的存在,保证塑料制品的安全性。
二、生产过程控制2.1 加工温度控制:根据不同塑料材料的特性,合理控制加工温度,防止过高或过低的温度对塑料制品的物理性能产生不良影响。
2.2 注塑机参数设置:注塑机的压力、速度、时间等参数的设定要符合标准和工艺要求,以确保注塑成型质量合格。
2.3 成型模具检验:对成型模具进行严格检验,确保其尺寸精度、表面质量等符合要求,防止因模具问题导致的制品质量不良。
2.4 生产环境控制:确保生产车间的温度、湿度、清洁度等符合要求,避免外部环境对生产过程和制品质量的影响。
三、成品质量检验3.1 外观检验:对塑料制品外观质量进行检验,包括表面光洁度、颜色一致性、无划痕、无气泡等。
可以采用目视检查、光学仪器等方法进行检测。
3.2 尺寸检验:对塑料制品的尺寸进行测量,包括长度、宽度、厚度等参数,确保符合设计要求。
3.3 物理性能检验:对塑料制品的物理性能进行测试,包括拉伸强度、弯曲强度、冲击强度等。
3.4 化学性能检验:检测塑料制品的化学性能,如耐酸碱性能、耐热性能等。
3.5 加工性能检验:对塑料制品的加工性能进行测试,包括熔融流动性、收缩率等参数。
3.6 环境适应性检验:对塑料制品在不同环境条件下的稳定性进行测试,如耐候性、耐热性等。
注塑机整机检验测试报告

机器型号
机器出厂编号
1/外观:
实际检验结果
2/尺寸和性能
实际检验结果
油漆有无色差
最大模厚
喷塑有无色差
最小模厚
整机螺丝有无松动
移模行程
硬管走向是否平直/合理
顶出行程各报警动作是否灵敏注来自行程各电器动作是否灵敏
拉杆直径
各电器是否按要求装配
负载平行度
有无接地标志
空载平行度料筒中心平行度
电脑型号有无装错
料筒直径
油泵型号和单位是否正确
料筒止逆直径
电机伺服电机功率/单位
冷却效果
电热功率单位
整机噪音
接触器生产单位
预塑背压可调
比例阀型号/单位
负载运行
电磁阀型号/单位
射移动作
变频器型号/单位
调模动作
冷却器面积
润滑检漏
标牌平直度
液压部件检漏
钣金装配平直度
温度偏差
3/附件
4/包装
随机配件和说明书是否齐全
包装是否符合要求
检验结论:
调试员:年月日检验员:年月日
注塑机产品质检工作总结
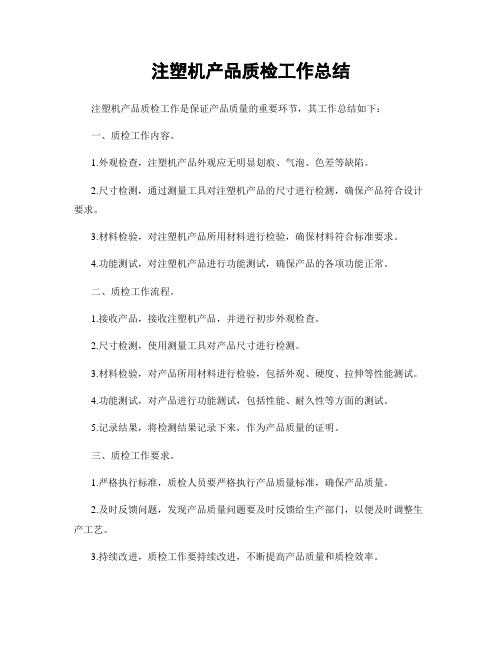
注塑机产品质检工作总结注塑机产品质检工作是保证产品质量的重要环节,其工作总结如下:一、质检工作内容。
1.外观检查,注塑机产品外观应无明显划痕、气泡、色差等缺陷。
2.尺寸检测,通过测量工具对注塑机产品的尺寸进行检测,确保产品符合设计要求。
3.材料检验,对注塑机产品所用材料进行检验,确保材料符合标准要求。
4.功能测试,对注塑机产品进行功能测试,确保产品的各项功能正常。
二、质检工作流程。
1.接收产品,接收注塑机产品,并进行初步外观检查。
2.尺寸检测,使用测量工具对产品尺寸进行检测。
3.材料检验,对产品所用材料进行检验,包括外观、硬度、拉伸等性能测试。
4.功能测试,对产品进行功能测试,包括性能、耐久性等方面的测试。
5.记录结果,将检测结果记录下来,作为产品质量的证明。
三、质检工作要求。
1.严格执行标准,质检人员要严格执行产品质量标准,确保产品质量。
2.及时反馈问题,发现产品质量问题要及时反馈给生产部门,以便及时调整生产工艺。
3.持续改进,质检工作要持续改进,不断提高产品质量和质检效率。
四、质检工作意义。
1.保证产品质量,质检工作能够保证注塑机产品的质量,提高产品的可靠性和稳定性。
2.降低成本,质检工作能够及时发现产品质量问题,避免不合格产品流入市场,降低后续成本。
3.提升企业形象,通过严格的质检工作,能够提升企业产品的品质形象,增强市场竞争力。
总之,注塑机产品质检工作是非常重要的,需要质检人员严格执行标准,及时反馈问题,持续改进工作,以保证产品质量,降低成本,提升企业形象。
希望各企业能够重视质检工作,确保产品质量和用户满意度。
注塑机拉力测试标准

注塑机拉力测试标准
本标准规定了注塑机拉力测试的设备、试样准备、测试环境、测试方法和结果分析。
本标准适用于注塑机生产的塑料制品的拉力测试。
1. 测试设备
1.1. 测试设备应包括一台精密的拉力试验机,其精度应不低于1%。
1.2. 测试设备应配备合适的夹具,以便于固定试样和防止试样在测试过程中滑动。
1.3. 测试设备应具有一个适当的传感器,能够测量并记录试样的拉力值。
2. 试样准备
2.1. 试样应为注塑机生产的塑料制品,且应具有相同的形状、尺寸和材料。
2.2. 每个试样应标记好其尺寸和编号,以便于后续测试和分析。
2.3. 试样应在使用前进行干燥处理,以消除湿度对测试结果的影响。
3. 测试环境
3.1. 测试应在恒温、恒湿的环境中进行,以保持测试结果的稳定性。
3.2. 测试环境的温度应保持在23℃±2℃,湿度应保持在50%±5%。
4. 测试方法
4.1. 将试样固定在夹具上,确保试样不会在测试过程中滑动。
4.2. 设置拉力试验机的传感器,使其能够测量并记录试样的拉力值。
4.3. 以恒定的速度逐渐增加拉力,直到试样断裂或达到规定的拉力
值。
4.4. 记录试样的最大拉力值和断裂时的拉力值。
5. 结果分析
5.1. 对每个试样的最大拉力值和断裂时的拉力值进行分析,以确定其平均值和标准差。
5.2. 将结果与注塑机的生产标准进行比较,以评估其性能是否满足要求。
注塑检验成绩报告
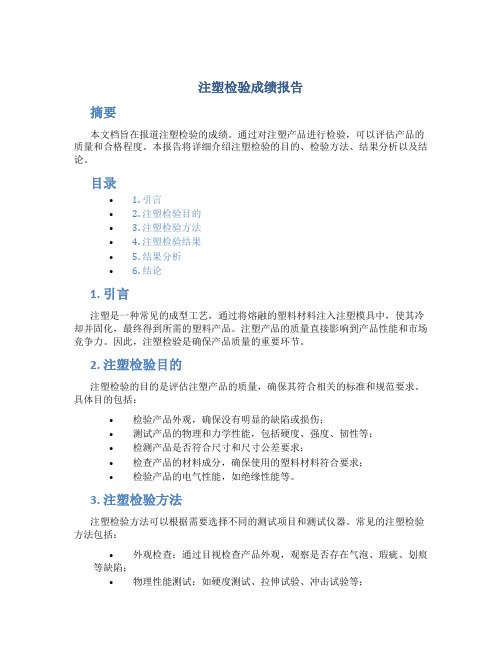
注塑检验成绩报告摘要本文档旨在报道注塑检验的成绩。
通过对注塑产品进行检验,可以评估产品的质量和合格程度。
本报告将详细介绍注塑检验的目的、检验方法、结果分析以及结论。
目录• 1. 引言• 2. 注塑检验目的• 3. 注塑检验方法• 4. 注塑检验结果• 5. 结果分析• 6. 结论1. 引言注塑是一种常见的成型工艺,通过将熔融的塑料材料注入注塑模具中,使其冷却并固化,最终得到所需的塑料产品。
注塑产品的质量直接影响到产品性能和市场竞争力。
因此,注塑检验是确保产品质量的重要环节。
2. 注塑检验目的注塑检验的目的是评估注塑产品的质量,确保其符合相关的标准和规范要求。
具体目的包括:•检验产品外观,确保没有明显的缺陷或损伤;•测试产品的物理和力学性能,包括硬度、强度、韧性等;•检测产品是否符合尺寸和尺寸公差要求;•检查产品的材料成分,确保使用的塑料材料符合要求;•检验产品的电气性能,如绝缘性能等。
3. 注塑检验方法注塑检验方法可以根据需要选择不同的测试项目和测试仪器。
常见的注塑检验方法包括:•外观检查:通过目视检查产品外观,观察是否存在气泡、瑕疵、划痕等缺陷;•物理性能测试:如硬度测试、拉伸试验、冲击试验等;•尺寸测量:使用尺寸测量工具,如卡尺、游标卡尺等,测量产品的尺寸和公差;•成分分析:使用化学分析仪器,如红外光谱仪、质谱仪等,测试产品的材料成分;•电气性能测试:使用绝缘测试仪、耐电压测试仪等,检验产品的电气性能。
4. 注塑检验结果经过注塑检验后,获得了以下结果:•外观检查:产品表面光滑,没有明显的气泡、凹陷和划痕;•硬度测试:产品硬度符合要求,满足产品设计的强度要求;•拉伸试验:产品的拉伸强度和伸长率均符合标准要求;•尺寸测量:产品的尺寸和公差在允许误差范围内;•成分分析:产品使用的塑料材料成分符合要求;•电气性能测试:产品的绝缘性能和耐电压性能均达标。
5. 结果分析根据注塑检验结果的分析,可以得出以下结论:•本次注塑产品的质量良好,外观无明显缺陷;•物理性能符合要求,产品具有足够的强度和韧性;•尺寸精度良好,满足设计要求;•材料成分符合要求,使用的塑料材料没有问题;•电气性能良好,产品绝缘性能和耐电压能力达标。
注塑机检验报告

注塑机检验报告1. 检验目的本文档旨在对注塑机进行全面的检验,并报告其性能和质量状况。
通过本次检验,我们将评估注塑机的工作效率、生产能力以及安全性能,以确保其能够符合生产需求并保证员工的安全。
2. 检验范围本次检验的范围涵盖注塑机的以下方面:•注塑机外观检查•控制系统功能检验•成型参数验证•安全装置检查•液压系统和气动系统检验3. 检验过程3.1 注塑机外观检查检验人员对注塑机的外观进行了仔细的检查,包括机身、控制面板、油泵等部件的正常工作状态和整体卫生状况。
未发现任何异常情况。
3.2 控制系统功能检验通过对注塑机的控制系统进行测试,验证其各个功能模块是否正常工作。
测试结果显示,注塑机的控制系统功能良好,能够准确地控制注射速度、注射压力和模具开合等参数。
3.3 成型参数验证考察了注塑机的成型参数是否满足生产要求。
进行了多组试验,根据产品要求调整注射速度、注射压力、射胶量等参数,并对成型品进行了质量检查。
结果显示,注塑机的成型参数稳定,产品质量符合要求。
3.4 安全装置检查对注塑机的安全装置进行了细致的检查,包括保护罩、急停按钮、安全门等。
检查结果显示,注塑机的安全装置完好有效,能够确保操作人员的安全。
3.5 液压系统和气动系统检验对注塑机的液压系统和气动系统进行了测试,验证其是否正常工作。
测试结果表明,注塑机的液压系统和气动系统正常运行,能够提供稳定的动力和压力。
4. 检验结果通过本次检验,我们得出以下结论:•注塑机外观正常,无明显损伤或故障。
•控制系统功能良好,能够准确控制生产过程。
•成型参数稳定,产品质量符合要求。
•安全装置完好有效,能够确保操作人员的安全。
•液压系统和气动系统正常运行,提供稳定的动力和压力。
5. 检验结论根据本次检验结果,我们认为此注塑机在功能、性能和安全性方面均符合要求,能够满足生产需要。
建议在日常生产中继续对注塑机进行定期检查和维护,以确保其稳定的运行和使用寿命。
以上为注塑机检验报告,如有任何问题,请随时与我们联系。
注塑品质检验流程
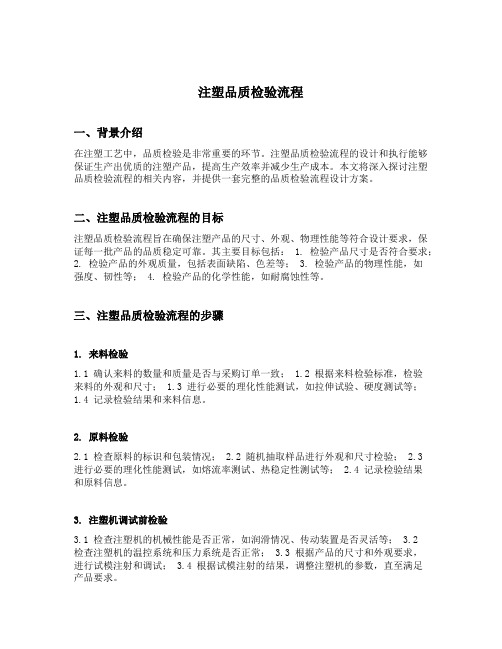
注塑品质检验流程一、背景介绍在注塑工艺中,品质检验是非常重要的环节。
注塑品质检验流程的设计和执行能够保证生产出优质的注塑产品,提高生产效率并减少生产成本。
本文将深入探讨注塑品质检验流程的相关内容,并提供一套完整的品质检验流程设计方案。
二、注塑品质检验流程的目标注塑品质检验流程旨在确保注塑产品的尺寸、外观、物理性能等符合设计要求,保证每一批产品的品质稳定可靠。
其主要目标包括: 1. 检验产品尺寸是否符合要求;2. 检验产品的外观质量,包括表面缺陷、色差等;3. 检验产品的物理性能,如强度、韧性等; 4. 检验产品的化学性能,如耐腐蚀性等。
三、注塑品质检验流程的步骤1. 来料检验1.1 确认来料的数量和质量是否与采购订单一致; 1.2 根据来料检验标准,检验来料的外观和尺寸; 1.3 进行必要的理化性能测试,如拉伸试验、硬度测试等;1.4 记录检验结果和来料信息。
2. 原料检验2.1 检查原料的标识和包装情况; 2.2 随机抽取样品进行外观和尺寸检验; 2.3 进行必要的理化性能测试,如熔流率测试、热稳定性测试等; 2.4 记录检验结果和原料信息。
3. 注塑机调试前检验3.1 检查注塑机的机械性能是否正常,如润滑情况、传动装置是否灵活等; 3.2检查注塑机的温控系统和压力系统是否正常; 3.3 根据产品的尺寸和外观要求,进行试模注射和调试; 3.4 根据试模注射的结果,调整注塑机的参数,直至满足产品要求。
4. 注塑生产过程中的检验4.1 定期抽取注塑过程中的产品样品进行尺寸和外观质量检验; 4.2 根据产品的特性和要求,进行必要的物理性能测试,如弯曲试验、耐磨试验等; 4.3 定期测试注塑机的温控系统和压力系统,确保其运行正常; 4.4 记录检验结果和生产过程数据,分析生产过程的稳定性和品质可控性。
5. 成品检验5.1 根据产品的要求,选取典型样品进行尺寸和外观质量检验; 5.2 进行产品的物理和化学性能测试,确保其符合设计要求; 5.3 进行必要的耐用性测试,如抗老化试验等; 5.4 根据检验结果判定产品的合格与否。
注塑件的检验流程
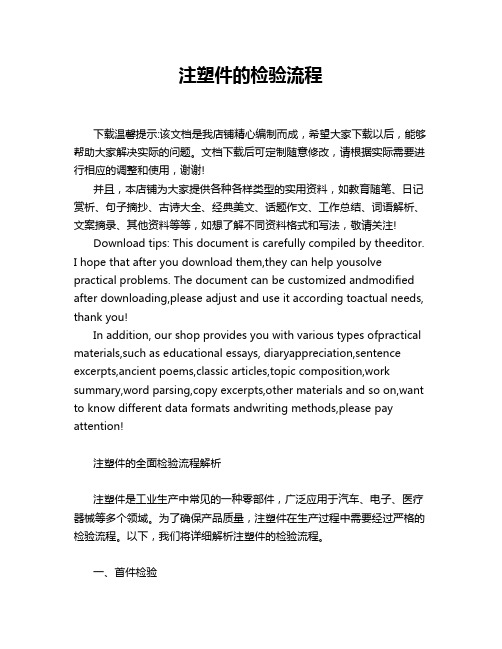
注塑件的检验流程下载温馨提示:该文档是我店铺精心编制而成,希望大家下载以后,能够帮助大家解决实际的问题。
文档下载后可定制随意修改,请根据实际需要进行相应的调整和使用,谢谢!并且,本店铺为大家提供各种各样类型的实用资料,如教育随笔、日记赏析、句子摘抄、古诗大全、经典美文、话题作文、工作总结、词语解析、文案摘录、其他资料等等,如想了解不同资料格式和写法,敬请关注!Download tips: This document is carefully compiled by theeditor.I hope that after you download them,they can help yousolve practical problems. The document can be customized andmodified after downloading,please adjust and use it according toactual needs, thank you!In addition, our shop provides you with various types ofpractical materials,such as educational essays, diaryappreciation,sentence excerpts,ancient poems,classic articles,topic composition,work summary,word parsing,copy excerpts,other materials and so on,want to know different data formats andwriting methods,please pay attention!注塑件的全面检验流程解析注塑件是工业生产中常见的一种零部件,广泛应用于汽车、电子、医疗器械等多个领域。
- 1、下载文档前请自行甄别文档内容的完整性,平台不提供额外的编辑、内容补充、找答案等附加服务。
- 2、"仅部分预览"的文档,不可在线预览部分如存在完整性等问题,可反馈申请退款(可完整预览的文档不适用该条件!)。
- 3、如文档侵犯您的权益,请联系客服反馈,我们会尽快为您处理(人工客服工作时间:9:00-18:30)。
Closed Loop injection Machine Commissioning & TestingIntroductionThis document provides guidance for the commissioning and testing closed loop injection moulding hardware, injection system & control softwareCaution: Please ensure all instructions and guidelines regarding safety and normal operation of the machine referred to in the installation and normal operation provided by the manufacturer of the machine.Caution: It is the responsibility of the commissioning / testing technical team to ensure safe installation and initial operation of all systems of the injection moulding machine. Any person operating this equipment must be fully qualified and undergone comprehensive training. All documentation regarding the machines safe installation and operation provided by the machine manufacturer must be read and understood before the machine installation / operation of the machine.Caution: in order to prevent injuries from the machine and damage to the machine ensure enough caution and professional understanding is applied towards the setup of the machine.Additional Information:For further information, parts, service, or latest information related to the full installation and operating of this equipment etc, contact the Equipment Manufacturer.1.Pre-Commission / Testing Checks1.1.M achine1.1.1.C heck that the machine is installed per the manufacturers instructions and that properguarding and safety precautions have been observed.1.2.F acilities & Ancillary Equipment1.2.1.A ll facilities and equipment required to conduct moulding / machines trials should be availablee.g. Appropriate Power Supply, Compressed Air Supply, Mould Temperature Control; HotWater, Chilled Water, Normal Water with appropriate connections. Closed loop MaterialDryers & Dehumidifiers.1.2.2.A n appropriate mould should be selected, installed in the machine and allowed reach specifiedtemperature.1.2.3.R esin should be allowed sufficient time in the hopper / dryer to reach specified moisture levelsprior to beginning the machine set up and initial checks.1.2.4.O perators should be provided by all necessary equipment, safety and otherwise to safelyoperate the equipment.2.Machine Set-up & Testing2.1.Calibrate screw bottom reads zeroCheck that the screw bottom or zero point, switch the cycle to manual with low pressure and bring the screw full forward. Check the screw position reading: It should be zero. If not, recalibrate the position sensor.2.2.Check: Screw Drift, Shot-Size & Position Cut Off consistencyWith the machine cycling, check that the screw is not moving as the mould is opens, ejection / re-loading and then closing the screw should not move. Note the position of the screw at the end of screwrecovery, this should be identical on every shot. Check that the machine is switching from first to second stage as the screw hits the set cut off position (assuming cut off is via stroke position). Variation should be less than 0.05 mm. If the machine fails any of these tests, the shot size is fluctuating beyondacceptable levels.2.3.Load Compensation ChecksC hecks the machine’s ability to keep fill time constant by adapting to viscosity changes, such astemperature cycles, resin lot changes, colour changes, and other normal process variations.Start up the machine following your normal procedures, making sure you are operating with anappropriate Delta P and switching from first stage to second stage via stroke position. Make short shots by reducing Second-Stage Pressure as low as possible while leaving some time on the hold timer.Select three injection velocities, low, med and high. At each in turn, note the fill time and pressure at transfer to make this 90-99% full shot. The fill time is FT1 and the pressure at transfer is PK1. Now, either manually or in automatic cycle using screw decompression before screw rotation, pull the screw back (without screw rotation) to the exact same position used to make your 90-99% full part. That is, you have a shot of air, no plastic in front of the screw. Before you make this air shot, make sure you can easily dig out a very short shot. Now, on semi- or fully automatic cycle, shoot air into the mould and note the fill time and pressure at transfer. This is FT2 and PK2. The fill time should be the same, with asignificantly reduced pressure at transfer. The following equation calculates the machine’s loadsensitivity:(FT1 – FT2) ÷ FT1) ÷ (PK1 – PK2) ÷ 1000) × 100 = % error/1000 psi.The percent error should be near zero; slightly negative is ideal. If the error is greater than +5% error are not properly load compensated. Test at three different injection velocities—slow, medium, and fast. If your machine passes this severe load-variation test, it will keep fill time constant during production.2.4.Velocity LinearityCaution: Before beginning this test, make sure short shots can be ejected easily. If shorts cannot be easily ejected you will have to use second-stage pressure to finish filling the part.The purpose of this test is to compare a machine’s set velocity with what is actually achieved. To get good data, it’s recommended that the shot should be at least 60% of the barrel capacity. If you are using less than 40% of barrel capacity, do not use that mould for this velocity linearity test, as theresults may be useless.In normal production mode using normal procedures to begin production making full parts. Lower the second-stage, or pack and hold, pressure as far as the machine will allow. At whatever velocity is currently set on the machine’s controller, this should make a short shot. If not, adjust the position transfer to make a part that is short but at least 80% full.Make sure the machine is running under velocity control and you have an appropriate Delta P. Now increase the set injection velocity in reasonable (safe) increments until the machine is set to thefastest injection velocity allowable. As you increase the velocity, you may have to adjust the position transfer to ensure you are making short shots, and double check that you are still under velocitycontrol with an appropriate Delta P. Once at the fastest allowable velocity, adjust the positiontransfer to make a 99% full part.Once you are making 99% full parts under velocity control, you can start taking data. Note the actual “screw start position”—don’t go by the set shot size and decompression or suck back, if any. Then note the cut off or stroke transfer position and the fill time (to within 0.01 sec). Without changinganything but injection velocity, reduce the set velocity from as fast as the machine can go to nearly as slow as the machine can go. Make sure you are transferring on position and not time; that is,make sure the overall injection timer has enough time on it to allow you to reach the transferposition. The parts may change in size but do not readjust shot size or position transfer during the test.Set up the data table to look like Table 1 and if you want, graph the data as shown in Fig. 1. Tocalculate the actual velocity, subtract the cut off or transfer position from the actual screw startposition and divide by the fill time. Because this method includes the initial inertia to get the screw up to speed, expect the fastest actual velocities to be only 85% to 95% of the set velocities.Shot Set Velocitymm/sec.Fill Time sec.Actual Velocitymm/sec.% of Set Velocity1 2 3 4 5 6 7 8 9101112Note: At high velocities actual being a bit slower then set is to be expected because of inertia. If the data shows actual velocities hitting a maximum and levelling out this test has failed.2.5.Switchover Response from First to Second StageSwitchover response is the phase of the cycle is the critical stage where the first stage of filling the part to 90+% full ends and the second stage (pack and hold) begins.Try, check two methods, 100 parts each method:5.1.1. Rapid TransferRapid transfer from first to second stage, very little plastic has to be delivered to the cavity, the rapid drop of plastic pressure in the nozzle does not over pack or accentuate the rapid development of cavity pressure. If this method does produce consistent parts the performance of the screw’s check ring is suspect.5.1.2.Slow, Velocity Controlled PackRequires a three-stage moulding process, the filling or first stage gets the part 90+% full. Second Stage, packing is velocity controlled to slow the cavity-pressure development and ends when the cavity pressure reaches a level previously found to produce an acceptable part. Once this cavity pressure is achieved, the machine transfers to holding (third stage) to keep all the plastic in the cavity and hold the part to specified dimensions. This method will compensate for viscosityvariations and any leakage of the check ring.Data Recording:。