风冷散热设计专题
风冷散热原理
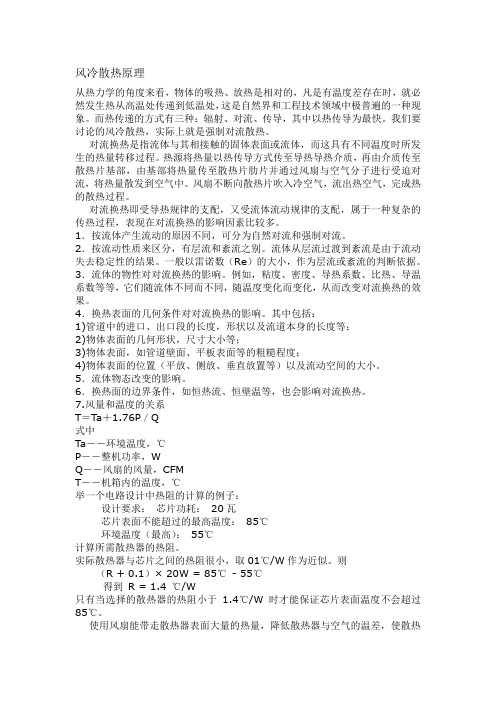
风冷散热原理从热力学的角度来看,物体的吸热、放热是相对的,凡是有温度差存在时,就必然发生热从高温处传递到低温处,这是自然界和工程技术领域中极普遍的一种现象。
而热传递的方式有三种:辐射、对流、传导,其中以热传导为最快。
我们要讨论的风冷散热,实际上就是强制对流散热。
对流换热是指流体与其相接触的固体表面或流体,而这具有不同温度时所发生的热量转移过程。
热源将热量以热传导方式传至导热导热介质,再由介质传至散热片基部,由基部将热量传至散热片肋片并通过风扇与空气分子进行受迫对流,将热量散发到空气中。
风扇不断向散热片吹入冷空气,流出热空气,完成热的散热过程。
对流换热即受导热规律的支配,又受流体流动规律的支配,属于一种复杂的传热过程,表现在对流换热的影响因素比较多。
1.按流体产生流动的原因不同,可分为自然对流和强制对流。
2.按流动性质来区分,有层流和紊流之别。
流体从层流过渡到紊流是由于流动失去稳定性的结果。
一般以雷诺数(Re)的大小,作为层流或紊流的判断依据。
3.流体的物性对对流换热的影响。
例如,粘度、密度、导热系数、比热、导温系数等等,它们随流体不同而不同,随温度变化而变化,从而改变对流换热的效果。
4.换热表面的几何条件对对流换热的影响。
其中包括:1)管道中的进口、出口段的长度,形状以及流道本身的长度等;2)物体表面的几何形状,尺寸大小等;3)物体表面,如管道壁面、平板表面等的粗糙程度;4)物体表面的位置(平放、侧放、垂直放置等)以及流动空间的大小。
5.流体物态改变的影响。
6.换热面的边界条件,如恒热流、恒壁温等,也会影响对流换热。
7.风量和温度的关系T=Ta+1.76P/Q式中Ta--环境温度,℃P--整机功率,WQ--风扇的风量,CFMT--机箱内的温度,℃举一个电路设计中热阻的计算的例子:设计要求:芯片功耗:20瓦芯片表面不能超过的最高温度:85℃环境温度(最高):55℃计算所需散热器的热阻。
实际散热器与芯片之间的热阻很小,取01℃/W作为近似。
风冷散热设计专题

风冷散热设计专题风冷散热原理:散热片的核心是同散热片底座紧密接触的,因此芯片表面发出的热量就会通过热传导传到散热片上,再由风扇转动所造成的气流将热量“吹走”,如此循环,便是处理器散热的简单过程。
散热片材料的比较:现在市面上的散热风扇所使用的散热片材料一般都是铝合金,只有极少数是使用其他材料。
学过物理的人应该都知道铝导热性并不是最好的,从效果来看最好的应该是银,接下来是纯铜,紧接着才会是铝。
但是前两种材料的价格比较贵,如果用来作散热片成本不好控制。
使用铝业也有很多优点,比如重量比较轻,可塑性比较好。
因此兼顾导热性和其他方面使用铝就成为了主要的散热材料。
不过我们使用的散热片没有百分之百纯铝的产品,因为纯铝太过柔软,如果想做成散热片一般都会加入少量的其他金属,成为铝合金(得到更好的硬度)。
风扇:单是有了一个好的散热片,而不加风扇,就算表面积再大,也没有用!因为无法同空气进行完全的流通,散热效果肯定会大打折扣。
从这个来看,风扇的效果有时甚至比散热片还重要。
假如没有好的风扇,则散热片表面积大的特点便无法充分展现出来。
挑选风扇的宗旨就是,风扇吹出来的风越强劲越好。
风扇吹出来的风力越强,空气流动的速度越快,散热效果同样也就越好。
要判断风扇是否够强劲,转速是一个重要的依据。
转速越快,风就越强,简单看功率的大小。
轴承:市面上用的轴承一般有两种,滚珠轴承和含油轴承,滚珠轴承比含油轴承好,声音小、寿命长。
但是滚珠轴承的设计比较难,其中一个工艺是预压,是指将滚珠固定到轴承套中的过程,这要求滚珠与轴承套表面结合紧密,没有间隙,以使钢珠磨损度最小。
通常在国内厂家轴承制造中,预压前上下轴承套是正对的,因为钢珠尺寸与轴承套尺寸肯定会存在一定误差,所以在预压受力后,滚珠同轴承套之间总有5—10微米的间隙,就是这个间隙,使得轴承的老化磨损程度大大增加,使用寿命缩短。
同样过程,在NSK公司的轴承制造中,预压时上下轴承套的会有一个5微米左右的相对距离,这样轴承套在受压后就会紧紧的卡住滚珠,使其间的间隙减小为零,在风扇工作中,滚珠就不会有跳动,从而使磨损降至最小,保证风扇畅通且长久高速运转。
风冷模块设计方案
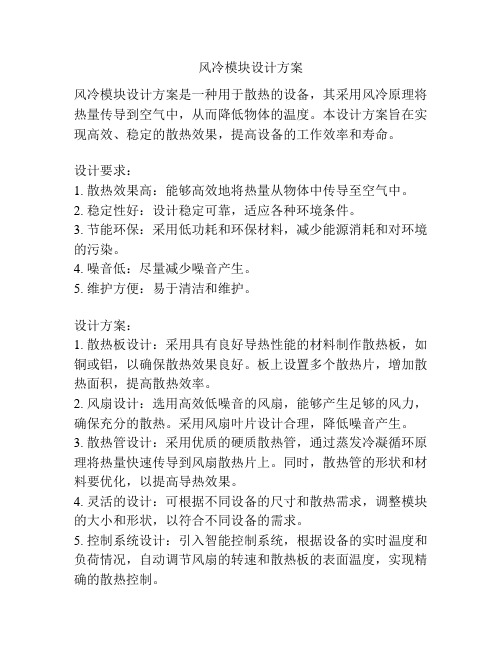
风冷模块设计方案风冷模块设计方案是一种用于散热的设备,其采用风冷原理将热量传导到空气中,从而降低物体的温度。
本设计方案旨在实现高效、稳定的散热效果,提高设备的工作效率和寿命。
设计要求:1. 散热效果高:能够高效地将热量从物体中传导至空气中。
2. 稳定性好:设计稳定可靠,适应各种环境条件。
3. 节能环保:采用低功耗和环保材料,减少能源消耗和对环境的污染。
4. 噪音低:尽量减少噪音产生。
5. 维护方便:易于清洁和维护。
设计方案:1. 散热板设计:采用具有良好导热性能的材料制作散热板,如铜或铝,以确保散热效果良好。
板上设置多个散热片,增加散热面积,提高散热效率。
2. 风扇设计:选用高效低噪音的风扇,能够产生足够的风力,确保充分的散热。
采用风扇叶片设计合理,降低噪音产生。
3. 散热管设计:采用优质的硬质散热管,通过蒸发冷凝循环原理将热量快速传导到风扇散热片上。
同时,散热管的形状和材料要优化,以提高导热效果。
4. 灵活的设计:可根据不同设备的尺寸和散热需求,调整模块的大小和形状,以符合不同设备的需求。
5. 控制系统设计:引入智能控制系统,根据设备的实时温度和负荷情况,自动调节风扇的转速和散热板的表面温度,实现精确的散热控制。
6. 安全性设计:设置过热保护装置,当散热模块超过设定温度时,自动切断电源,避免设备损坏和火灾风险。
实施方案:1. 选择合适的材料和零部件,如铜、铝、风扇、散热片等。
2. 根据设计需求,制作散热板和散热管,确保其形状和尺寸与设备相匹配。
3. 安装风扇和控制系统,调试和测试其散热效果和噪音情况。
4. 进行实际的工作环境测试,验证散热模块的稳定性和效果。
5. 对设计的风冷模块进行改进和优化,以适应不同设备的需求。
此外,还可以在设计中考虑使用新型材料,如石墨烯等,以提高散热效果和节能性能。
通过不断的研究和改进,可以使风冷模块设计更加高效和可靠,为各种设备提供优良的散热解决方案。
翅片式风冷换热器设计

翅片式风冷换热器设计一、设计原理翅片式风冷换热器由翅片管和冷却风机组成。
工作时,热媒流经管道,通过管道壁与外界冷却空气进行热量交换,从而将热量传递给空气。
同时,冷却风机通过流过翅片管的冷却空气,将其吹入翅片间隙,增加换热面积,提高换热效率。
二、换热器设计参数1.翅片管长度和直径翅片管长度和直径的选择应根据换热器的工作条件来确定。
一般来说,较长的翅片管长度可以增加换热面积,提高换热效率,但也会增加阻力和成本。
而较大的翅片管直径可以增加流体的流量和传热量,但同样也会增加阻力和成本。
2.翅片间距和数量翅片间距和数量的选择需要根据换热介质的温度和流速来确定。
较小的翅片间距可以增加换热面积,提高换热效率,但也会增加阻力。
翅片数量应根据实际需求来确定,一般来说,较大的翅片数可以增加换热面积,提高换热效率,但也会增加成本和复杂性。
3.翅片高度和厚度翅片高度和厚度的选择应根据换热介质的温度和流速以及换热需求来确定。
较大的翅片高度和厚度可以增加换热面积,提高换热效率,但也会增加阻力和成本。
三、翅片式风冷换热器的工作原理具体工作流程如下:1.热媒从换热器的进口进入管道,流经管道内部。
2.在管道内部,热媒通过管道壁与外界冷却空气进行热量交换。
热媒的热量传递给冷却空气,使其升温。
3.升温的冷却空气经过冷却风机的吹扫,被吹入翅片间隙。
4.在翅片间隙中,冷却空气与翅片接触,进行热量交换。
冷却空气吸收翅片的热量,并将其带走。
5.冷却的热媒经过管道进一步流动,从换热器的出口排出。
四、翅片式风冷换热器的优缺点1.结构紧凑,占用空间小。
由于翅片式风冷换热器利用翅片增加了换热面积,故相同换热量下其体积相对较小。
2.热量传递效率高。
翅片式风冷换热器具有较大的换热面积,能够实现高效的热量传递。
3.适用范围广。
翅片式风冷换热器适用于多种介质的换热,例如空气、水等。
1.清洗困难。
由于翅片之间的间隙较小,难以将污物清洗干净。
2.阻力较大。
翅片式风冷换热器会增加流体的阻力,降低了流体的流动速度。
一种机载设备的风冷散热优化设计

以自带风机 为散热手段 的典 型机 载设备为研究对
象, 利用理 论计算 与 热 仿 真 分析 相 结 合 对散 热进 行
优 设计 。
2 热 设 计 方 案 1 方 案 概 述
由于该设备外形 尺寸 为 18 m 2 m x 0 m x 6m 1 25m 设备总功耗为 39 9 同时其部分器件 6 m, 0 .5W, 的热耗 比较集中, 单个器件功耗为 16W, 7 器件表面
Vo . 7 N . 14 o 3
Jn20 u.07
工作模式 为 1 1 : 模式 时, 不垫紫铜板, 工作 3 O a r n的情 况下器 件 的温 度如 表 2所 示 。 i
表 2 不 垫 紫铜板 时 的器件 温度
时间( ) s
5 . 13 8 86
器件 1 ℃ ) 器 件 2 ℃) 器件 3 ℃) ( ( (
热 流密度 为 2 c 热设 计环 境技 术条 件 中最 高 8W/m ;
2 1 风机 选型 .
由于本方案选 用设备 自带风机强迫风冷 的形
式 , 机成 为散 热环节 中 的关 键 因素 。 风 风 机初步 选 型通过 经验 公式 进行估 算 :
Q 1.- .1 . 9
pLp凸
Ke r s ar o n lcr n c e u p n ; o v ci n a rc o i g o t z d d sg C D NHT s lt n y wo d : i r e ee t i q ime t c n e t i o l ; p i e e in; F / b o o n mi i ai mu o
( 中国西南 电子技术研究所 , 成都 60 3 ) 106
关于风冷散热器的性能研究
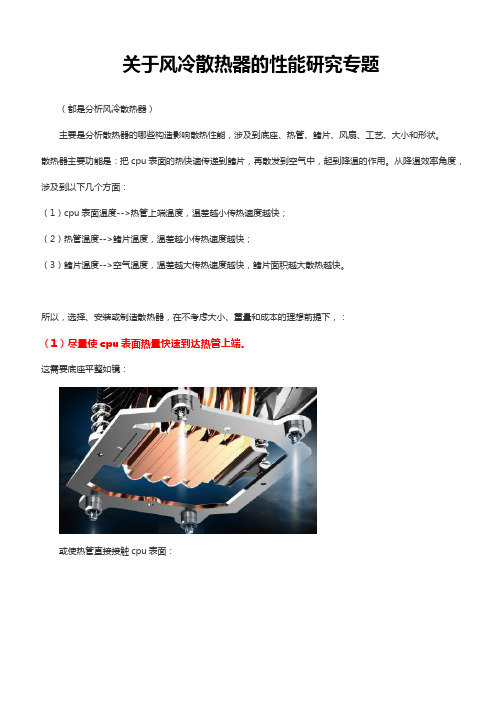
关于风冷散热器的性能研究专题(都是分析风冷散热器)主要是分析散热器的哪些构造影响散热性能,涉及到底座、热管、鳍片、风扇、工艺、大小和形状。
散热器主要功能是:把cpu表面的热快速传递到鳍片,再散发到空气中,起到降温的作用。
从降温效率角度,涉及到以下几个方面:(1)cpu表面温度-->热管上端温度,温差越小传热速度越快;(2)热管温度-->鳍片温度,温差越小传热速度越快;(3)鳍片温度-->空气温度,温差越大传热速度越快,鳍片面积越大散热越快。
所以,选择、安装或制造散热器,在不考虑大小、重量和成本的理想前提下,:(1)尽量使cpu表面热量快速到达热管上端。
这需要底座平整如镜:或使热管直接接触cpu表面:或采用铜底座:安装时不要过分挤压两端,导致底座拱起变形,不能与cpu表面完全吻合;导热硅脂要均匀涂抹。
热管热量要快速到达鳍片:可采用增加热管数目,采用较粗热管等办法。
(2)尽快使热管上的热量到达鳍片,并分布到鳍片的所有表面上。
--好的工艺使鳍片紧扣热管,不留间隙,尽快导出热管上的热量。
--采用导热更好的材料做鳍片,让热量快速分布到整个表面。
目前基本都是铝质鳍片,少量铜质鳍片。
--合理排列热管位置,让导热更有效。
(3)尽快把鳍片上的热量导入空气中。
保持适当风速。
风速太低太高都不行,低了导热不够快,高了...摩擦生热,还有噪音。
尽量增大鳍片面积。
越大越好。
保持机箱风道通畅,使空气保持低温。
利用工艺改变鳍片形状,使空气流动效率更高,如图所示:下面分类详谈。
先谈谈热管,到底几根热管够用?是否越多越粗越好?一般都是6mm粗的热管,粗的有8mm的,如果热管数量多,底座挤满了。
对高发热量(如125W)的cpu来说,1根2根的是少了点,3根可能刚好足够,4根比3根有提高是肯定的,但随着根数的增加,从热管传热角度看,效率提升会越来越少。
所以中低端散热器基本是3根4根。
对5根6根甚至8根热管的散热器来说,增加热管对进一步降低cpu表面与热管上端温差的效果不明显,多热管的作用更多在第二个环节:让热管更快向鳍片传热。
散热结构设计案例

散热结构设计案例一些常见的散热结构设计案例包括:1. 散热片:散热片可以看作是一个传导热量的空间,使得热量可以在其中扩散,从而提高散热效果。
2. 风扇散热:风扇散热是一种通过强制空气流动来加快热量散发的方式。
在设计中,需要考虑风扇的大小、转速、方向和位置等因素来实现最佳的散热效果。
3. 液冷散热:液冷散热使用循环的液体冷却器来将热量从CPU等组件中转移。
这种设计需要考虑循环泵的大小、散热器的大小和形状、管道布局等因素。
4. 热管式散热:热管式散热通过将热能从一个端点传输到另一个端点来实现热量散发。
这种设计需要考虑热管的长度、直径、材质和散热器的大小和形状等因素。
5. 热管翅片散热系统:这种系统结合了热管和翅片两种散热方式。
热管将热量从热源传输到翅片,而翅片则通过扩大散热表面积,提供更大的热散发面来提高散热效果。
6. 相变散热:相变散热利用材料的相变特性,例如从液态到气态的转变,释放大量的潜热来散热。
这种设计适用于高功率密度的设备,例如电子芯片。
7. 热管塔式散热:热管塔式散热是一种使用多个热管和散热鳍片组成的结构。
这种设计有助于提高热传导和散热面积,从而提高散热效果。
8. 微流道散热器:微流道散热器利用微小通道将热量从热源传输到冷却介质中。
这种设计具有高热传导效率和紧凑的结构,适用于小型电子设备和高功率密度场景。
9. 聚合散热:聚合散热是一种通过将多个散热结构组合在一起来提高整体散热效果的设计。
例如,可以将散热片、风扇和热管等结构组合在一起,以增加散热能力。
以上是一些常见的散热结构设计案例,不同的散热结构都有着自己的优缺点和适用场景,选择合适的散热结构需要考虑多方面因素并进行综合分析。
实际设计过程中需要根据具体应用场景和要求来选择最合适的散热结构,并进行合理的优化和调整。
icepak应用分析-强迫风冷散热器

icepak应⽤分析-强迫风冷散热器应⽤icepak分析强迫风冷散热器1 引⾔本⽂所叙述的风冷散热器,总功率为500W,设计进风温度为50℃,要求冷板最⾼点温度≤85℃,由于条件较苛刻,因此对散热器设计提出了较⾼的要求。
我们⾸先⽤⼀般数学计算⽅法(借助计算机)对散热器进⾏计算,得到较佳的散热器参数(散热齿⾼度、厚度、间距)及需要的风量,初选风机;然后⽤专业热分析软件icepak建⽴模型、进⾏仿真分析;最后⽤了散热器优化软件Qfin对散热器进⾏了优化,再根据优化结果,确定散热器参数。
本⽂叙述了对散热器进⾏分析、优化的过程和结果,通过这些软件的综合应⽤、相互映证,可以提⾼计算精度、优化结构参数,使散热器满⾜设计要求,并尽量达到最佳的散热效果,提⾼设备可靠性。
2 组成与结构散热器的组成与结构如图1所⽰。
图1 散热器结构该散热装置主要由以下部分组成:发热器件两个,散热器,风机两个,通风风道。
处于散热器上⾯的为发热器件1,总功率为400W,主要集中在前⾯,即前⾯部分360W,其余部分40W;处于散热器下⾯的为发热器件2,功率100W,均匀分布。
3 确定散热器基本参数根据已知条件、借助经验设定散热器尺⼨参数、风机风量,通过公式对散热器性能进⾏计算,可得到散热器基板平均温度,然后根据计算结果调整尺⼨参数及风量,再计算,通过反复⼏次计算就可以得到⼀组满⾜散热条件、且散热性能较好的散热器参数,并选定风机。
4 icepak计算模型根据散热器结构及初步计算、分析得出的散热器参数,建⽴icepak计算模型如图2所⽰。
openingFan1Fan2图2 icepak计算模型计算模型包括以下部分:a.热源(sources):发热器件1简化成两个热源,⼀个为360W(source 1),尺⼨60mm×120mm,另⼀个为40W(source 2),尺⼨60mm×180mm,此两个热源紧贴在⼀个块(block 1)上,block 1紧贴在散热器的散热齿顶⾯;发热器件2简化成⼀个热源(source 3),功率100W,尺⼨150mm×330mm,紧贴散热器基板上。
风冷原理图
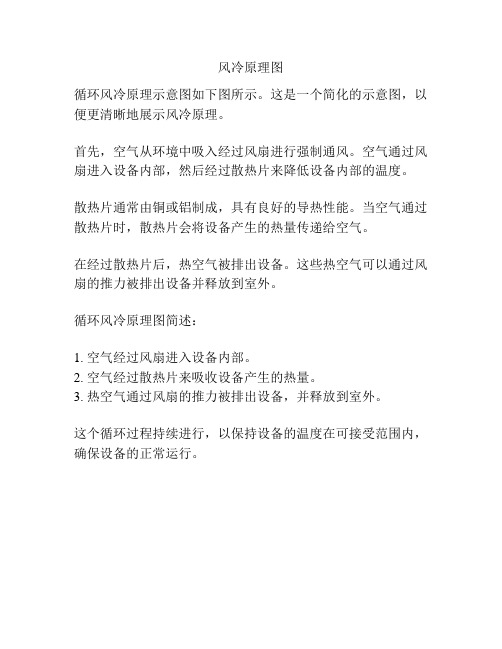
风冷原理图
循环风冷原理示意图如下图所示。
这是一个简化的示意图,以便更清晰地展示风冷原理。
首先,空气从环境中吸入经过风扇进行强制通风。
空气通过风扇进入设备内部,然后经过散热片来降低设备内部的温度。
散热片通常由铜或铝制成,具有良好的导热性能。
当空气通过散热片时,散热片会将设备产生的热量传递给空气。
在经过散热片后,热空气被排出设备。
这些热空气可以通过风扇的推力被排出设备并释放到室外。
循环风冷原理图简述:
1. 空气经过风扇进入设备内部。
2. 空气经过散热片来吸收设备产生的热量。
3. 热空气通过风扇的推力被排出设备,并释放到室外。
这个循环过程持续进行,以保持设备的温度在可接受范围内,确保设备的正常运行。
风冷散热器设计方法

风冷散热器设计方法随着电子设备的不断发展和普及,散热问题成为了一个亟待解决的挑战。
而风冷散热器作为一种常见的散热解决方案,其设计方法显得尤为重要。
本文将介绍一种有效的风冷散热器设计方法,以帮助读者更好地理解和应用。
风冷散热器的设计需要考虑散热效率和噪音控制两个方面。
在散热效率方面,我们可以通过优化散热器的结构和材料来提高其散热性能。
例如,增加散热片的数量和表面积,采用高导热材料,以提高散热效果。
此外,合理设计散热器的通风道路,确保空气能够顺畅地流过散热器,也是提高散热效率的关键。
噪音控制是风冷散热器设计中需要考虑的另一个重要因素。
散热器在工作时会产生一定的噪音,而过高的噪音会对用户的使用体验造成不良影响。
为了降低噪音,我们可以采用一些措施,如增加散热器的散热面积,减小风扇的转速,改善风扇叶片的设计等。
此外,合理布置散热器和其他设备之间的距离,避免共振和震动也是降低噪音的有效手段。
在风冷散热器的设计过程中,我们还需要考虑散热器的尺寸和重量。
尺寸过大会占用过多的空间,而尺寸过小则可能导致散热不足。
因此,我们需要根据实际需求和限制,合理确定散热器的尺寸。
同时,散热器的重量也需要考虑,过重的散热器可能会给设备带来额外的负担,甚至影响设备的正常运行。
除了上述因素,风冷散热器的设计还需要考虑材料的选择和制造工艺。
合适的材料可以提高散热器的散热性能和耐久性。
常见的散热器材料包括铝合金、铜等,它们具有良好的导热性能和机械强度。
而制造工艺的选择则直接影响到散热器的成本和质量。
因此,在设计过程中,我们需要综合考虑材料的性能和制造工艺的可行性,以达到最佳的设计效果。
总结起来,风冷散热器的设计方法需要综合考虑散热效率、噪音控制、尺寸和重量、材料选择和制造工艺等多个因素。
通过合理优化这些因素,我们可以设计出性能优良、稳定可靠的风冷散热器,以满足不同设备的散热需求。
希望本文所介绍的设计方法能够对读者在实际应用中有所帮助,提高散热器的设计水平和效果。
风冷散热的设计及计算
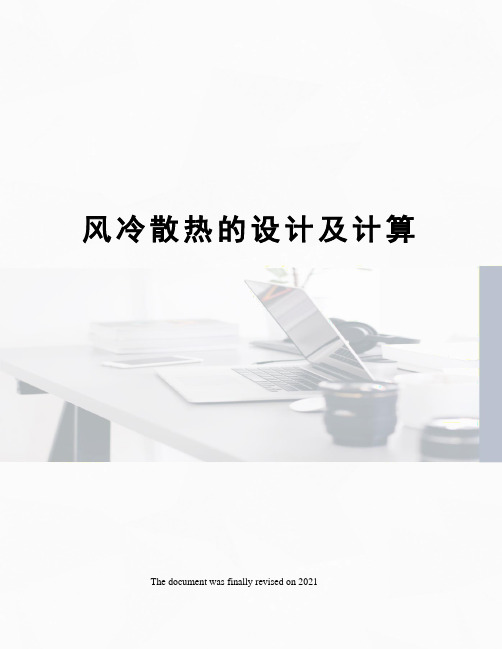
风冷散热的设计及计算 The document was finally revised on 2021风冷散热的设计及计算风冷散热原理:散热片的核心是同散热片底座紧密接触的,因此芯片表面发出的热量就会通过热传导传到散热片上,再由风扇转动所造成的气流将热量“吹走”,如此循环,便是处理器散热的简单过程。
散热片材料的比较:现在市面上的散热风扇所使用的散热片材料一般都是铝合金,只有极少数是使用其他材料。
学过物理的人应该都知道铝导热性并不是最好的,从效果来看最好的应该是银,接下来是纯铜,紧接着才会是铝。
但是前两种材料的价格比较贵,如果用来作散热片成本不好控制。
使用铝业也有很多优点,比如重量比较轻,可塑性比较好。
因此兼顾导热性和其他方面使用铝就成为了主要的散热材料。
不过我们使用的散热片没有百分之百纯铝的产品,因为纯铝太过柔软,如果想做成散热片一般都会加入少量的其他金属,成为铝合金(得到更好的硬度)。
风扇:单是有了一个好的散热片,而不加风扇,就算表面积再大,也没有用!因为无法同空气进行完全的流通,散热效果肯定会大打折扣。
从这个来看,风扇的效果有时甚至比散热片还重要。
假如没有好的风扇,则散热片表面积大的特点便无法充分展现出来。
挑选风扇的宗旨就是,风扇吹出来的风越强劲越好。
风扇吹出来的风力越强,空气流动的速度越快,散热效果同样也就越好。
要判断风扇是否够强劲,转速是一个重要的依据。
转速越快,风就越强,简单看功率的大小。
轴承:市面上用的轴承一般有两种,滚珠轴承和含油轴承,滚珠轴承比含油轴承好,声音小、寿命长。
但是滚珠轴承的设计比较难,其中一个工艺是预压,是指将滚珠固定到轴承套中的过程,这要求滚珠与轴承套表面结合紧密,没有间隙,以使钢珠磨损度最小。
通常在国内厂家轴承制造中,预压前上下轴承套是正对的,因为钢珠尺寸与轴承套尺寸肯定会存在一定误差,所以在预压受力后,滚珠同轴承套之间总有5—10微米的间隙,就是这个间隙,使得轴承的老化磨损程度大大增加,使用寿命缩短。
电动车风冷散热系统解析
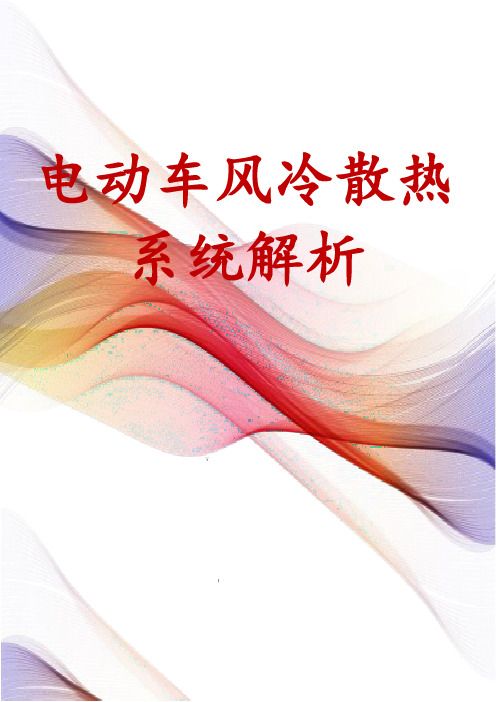
电动车风冷散热系统解析电动车风冷散热系统解析电动车风冷散热系统是为了解决电动车在高负荷运行时产生的热量而设计的。
下面将按步骤解析电动车风冷散热系统的工作原理。
第一步是热量的产生。
当电动车在高速行驶或承载重物时,电动机和电池可能会产生大量热量。
这些热量需要及时散发,否则会对电动车的性能和寿命产生负面影响。
第二步是热量的传导。
电动车的电机和电池通常位于车辆的底部,这意味着它们与周围环境之间的接触面积有限。
因此,必须通过散热系统来提高热量的传导效率。
第三步是热量的传导介质。
散热系统通常使用散热器作为传导介质。
散热器通常由金属制成,具有良好的导热性能。
电动车的散热器通常位于车辆底部或后部,以最大限度地增加与周围环境的接触面积。
第四步是热量的传导路径。
电动车的散热系统通过风扇和进气口与外界空气进行热量交换。
风扇通常位于散热器后面,通过吸入冷空气并将其引导到散热器中,加速热量的传导。
而进气口则用于引导空气流向散热器。
第五步是热量的散发。
一旦冷空气流经散热器,它会吸收热量并变热。
然后,热空气将通过散热器的另一侧排出,以确保热量能够尽快散发到周围环境中。
第六步是热量的循环。
为了进一步提高散热效率,一些电动车散热系统还采用了循环风的设计。
这种设计通过在散热器前方安装风道,将热空气重新引导到散热器前面,从而形成循环流动,提高热量的散发效率。
总的来说,电动车风冷散热系统通过热量产生、传导介质、传导路径、热量散发和循环等步骤,确保电动车在高负荷运行时能够及时有效地散发热量,保证车辆的性能和寿命。
这种设计在提高电动车的可靠性和稳定性方面起到了重要作用。
风冷散热的设计与计算

风冷散热的设计及计算风冷散热原理:散热片的核心是同散热片底座紧密接触的,因此芯片表面发出的热量就会通过热传导传到散热片上,再由风扇转动所造成的气流将热量“吹走”,如此循环,便是处理器散热的简单过程。
散热片材料的比较:现在市面上的散热风扇所使用的散热片材料一般都是铝合金,只有极少数是使用其他材料。
学过物理的人应该都知道铝导热性并不是最好的,从效果来看最好的应该是银,接下来是纯铜,紧接着才会是铝。
但是前两种材料的价格比较贵,如果用来作散热片成本不好控制。
使用铝业也有很多优点,比如重量比较轻,可塑性比较好。
因此兼顾导热性和其他方面使用铝就成为了主要的散热材料。
不过我们使用的散热片没有百分之百纯铝的产品,因为纯铝太过柔软,如果想做成散热片一般都会加入少量的其他金属,成为铝合金(得到更好的硬度)。
风扇:单是有了一个好的散热片,而不加风扇,就算表面积再大,也没有用!因为无法同空气进行完全的流通,散热效果肯定会大打折扣。
从这个来看,风扇的效果有时甚至比散热片还重要。
假如没有好的风扇,则散热片表面积大的特点便无法充分展现出来。
挑选风扇的宗旨就是,风扇吹出来的风越强劲越好。
风扇吹出来的风力越强,空气流动的速度越快,散热效果同样也就越好。
要判断风扇是否够强劲,转速是一个重要的依据。
转速越快,风就越强,简单看功率的大小。
轴承:市面上用的轴承一般有两种,滚珠轴承和含油轴承,滚珠轴承比含油轴承好,声音小、寿命长。
但是滚珠轴承的设计比较难,其中一个工艺是预压,是指将滚珠固定到轴承套中的过程,这要求滚珠与轴承套表面结合紧密,没有间隙,以使钢珠磨损度最小。
通常在国内厂家轴承制造中,预压前上下轴承套是正对的,因为钢珠尺寸与轴承套尺寸肯定会存在一定误差,所以在预压受力后,滚珠同轴承套之间总有5—10微米的间隙,就是这个间隙,使得轴承的老化磨损程度大大增加,使用寿命缩短。
同样过程,在NSK公司的轴承制造中,预压时上下轴承套的会有一个5微米左右的相对距离,这样轴承套在受压后就会紧紧的卡住滚珠,使其间的间隙减小为零,在风扇工作中,滚珠就不会有跳动,从而使磨损降至最小,保证风扇畅通且长久高速运转。
强制风冷的电源设备散热设计
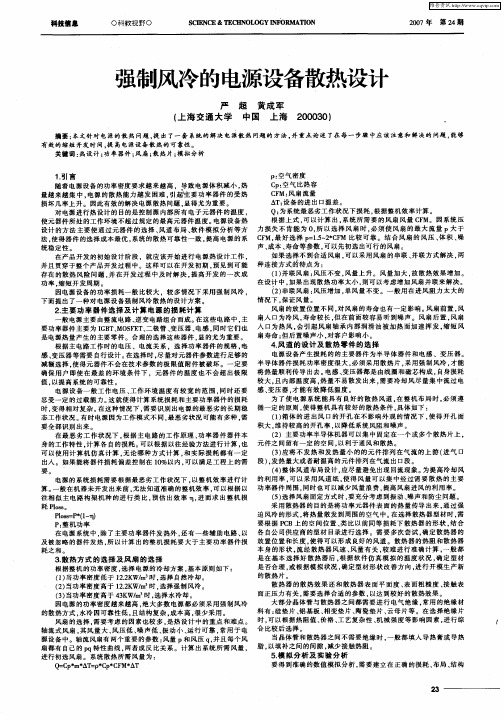
2主 要 功 率 器 件 选 择 及 计 算 电 源 的 损耗 计 算 .
一
4风 道 的 设计 及 散热 零 件 的选 择 . 根 据 主 电 路 工 作 时 的 电 压 、 电 流 关 系 ,选 择 功 率 器 件 的规 格 , 电 电源 设 备 产 生 损 耗 的 的主 要 器 件 为 半 导 体 器 件 和 电 感 、变 压 器 。 感 、 压 器 等 需 要 自行 设 计 。 选 择 时 , 量 对 元 器 件 参 数 进 行 足 够 的 变 在 尽 必 采 才 减 额 选 择 . 得 元 器 件 不 会 在 技 术参 数 的 极 限 值 附 件 被 破 坏 。 一 定 要 半 导 体 器 件 损 耗 功 率 密 度 很 大 , 须 采 用 散 热 片 , 用 强 制 风 冷 , 能 使 电感 、 变压器都是 由线圈和磁芯构成 。 自身损耗 确 保 用 户 即 使 在 最 差 的 环 境 条 件 下 ,元 器 件 的 温 度 也 不 会 超 出极 限 将热量顺利传导 出去 。 较 大 。 内部 温 度 高 。 量 不 易 散 发 出 来 , 要 冷 却 风尽 量 集 中 流 过 电 且 热 需 值。 以提高系统的可靠性。
声、 成本 、 寿命等参数 , 以先初选 出可行 的风扇。 可 统稳定性。 如 果 选 择 不 到 合 适 风 扇 。 以采 用 风 扇 的 串联 、 联方 式 解 决 , 可 并 两 在 产 品 开 发 的 初 始设 计 阶 段 ,就应 该 开 始 进 行 电源 热 设 计 工 作 , 并 且 贯 穿 于 整 个 产 品 开 发 过 程 中 。这 样 可 以在 开 发 初 期 , 见 到 可 能 种 连 接 方 式 的特 点 为 : 预 () 联风扇 : 压不变 , 量上升。风量加大 , 散热效 果增加 。 1并 风 风 故 存 在 的散 热 风 险 问 题 , 在 开 发 过 程 中及 时 解 决 , 高 开 发 的一 次 成 并 提 在 设 计 中 。 果 出现 散 热 功 率 太 小 , 可 以 考 虑 增 加 风 扇 并 联来 解 决 。 如 则 功率 . 短开发周期。 缩 () 2 串联 风 扇 : 压 增 加 , 风 量 不 变 。一 般 用 在 进 风 阻 力 太 大 的 风 单 因 电 源 设 备 的 功 率 损 耗 一般 比 较 大 ,较 多 情 况 下 采 用 强 制 风冷 ,
基于flotherm的风冷机箱散热设计及优化分析

优化,得到冷板翅片参数的最优组合,使热源温度降低了 5 ℃ 。 通过对优化结果数据的分析,
得到以下结论:在结构尺寸允许范围内及考虑了加工难易程度情况下,尽量增加翅片高度对散
热是有益的;冷板翅片厚度与翅片个数对散热效果的影响是相关联的,并不是翅片越多越好,
5 W / cm 2 时多采用风冷的冷却 方 式。 相 比 于 液 冷 冷
备的热设计是十分重要的。 随着微电子工艺技术的不
且不需要冷却液输入输出,电子机箱可以独立工作。
电子设备需要在合适的温度范围内才能正常工
升高 10 ℃ ,其可靠性就会降低 50%” 。 因此,电子设
断进步,功率器件向着轻、薄、短、小型化发展,并且发
热功率也越来越大,导致发热热流密度成倍增加。 器
性能是影响产品可靠性的重要因素。[1]
电子机箱内,冷板上电子元件发热热流密度低于
却,风冷冷却的结构相对简单,安全系数相对较高,并
众所周知,热量是通过热传导、热对流和热辐射 3
种方式传递的。[2] 电子设备的散热设计就是基于这 3
收稿日期:2019⁃08⁃09;修回日期:2019⁃08⁃25
对于常用的 1 ~ 2.5 mm 厚的冷板翅片,其最优的翅片间隙在 4 mm 左右。
关键词:风冷机箱;冷板;散热设计;优化分析
中图分类号:TN957.8 文献标志码:A 文章编号:1009⁃0401(2019)04⁃0036⁃05
Thermal design and optimization analysis of an air⁃cooled
种原理,通过尽量减少热流通路上的热阻来进行的。
在电子设备的热设计中,对于热传导的运用,通常是将
第五讲 机柜风冷设计课件
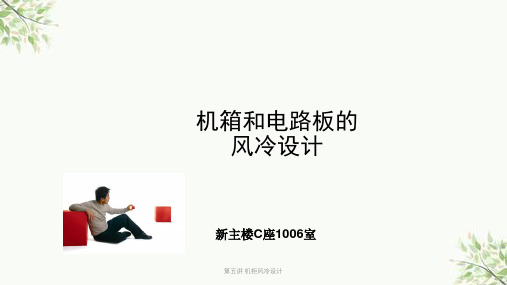
to the blower axis前弯叶片离心风机产生径向气流
• They deliver a low flow rate in a very high pressure environment
• 都随风机体积流量而改变
第五讲 机柜风冷设计
第五讲 机柜风冷设计
第五讲 机柜风冷设计
第五讲 机柜风冷设计
▪ 如果进入风机的没有不稳定气流,那
▪ 最么风大机效可率以点工靠作在近一静个压较的宽最的工大作值范点。
▪ ▪
可功围内能率。具随备气较流高体的积出流口量流的速增加迅速
▪ 由提过载于高情功。况率较曲少线发生平。坦,所以出现过
第五讲 机柜风冷设计
Static Pressure (in of water)
Characteristic Curves
Sample fan and system curves
0.5 0.4 0.3 0.2 0.1
0 0
Fan Curve
Operating Point
System Curve
20
40
第五讲 机柜风冷设计
Fans, Impellers and
Blowers • Fans move air in a direction parallel to the fan axis 风扇使空气 产生平行于轴的气流 • They are designed to produce high flow rate in a low pressure environment它们用在低压环境提高气流流量
机箱和电路板的 风冷设计
风冷散热的设计及计算

风冷散热的设计及计算风冷散热原理:散热片的核心是同散热片底座紧密接触的,因此芯片表面发出的热量就会通过热传导传到散热片上,再由风扇转动所造成的气流将热量“吹走”,如此循环,便是处理器散热的简单过程。
散热片材料的比较:现在市面上的散热风扇所使用的散热片材料一般都是铝合金,只有极少数是使用其他材料。
学过物理的人应该都知道铝导热性并不是最好的,从效果来看最好的应该是银,接下来是纯铜,紧接着才会是铝。
但是前两种材料的价格比较贵,如果用来作散热片成本不好控制。
使用铝业也有很多优点,比如重量比较轻,可塑性比较好。
因此兼顾导热性和其他方面使用铝就成为了主要的散热材料。
不过我们使用的散热片没有百分之百纯铝的产品,因为纯铝太过柔软,如果想做成散热片一般都会加入少量的其他金属,成为铝合金(得到更好的硬度)。
风扇:单是有了一个好的散热片,而不加风扇,就算表面积再大,也没有用!因为无法同空气进行完全的流通,散热效果肯定会大打折扣。
从这个来看,风扇的效果有时甚至比散热片还重要。
假如没有好的风扇,则散热片表面积大的特点便无法充分展现出来。
挑选风扇的宗旨就是,风扇吹出来的风越强劲越好。
风扇吹出来的风力越强,空气流动的速度越快,散热效果同样也就越好。
要判断风扇是否够强劲,转速是一个重要的依据。
转速越快,风就越强,简单看功率的大小。
轴承:市面上用的轴承一般有两种,滚珠轴承和含油轴承,滚珠轴承比含油轴承好,声音小、寿命长。
但是滚珠轴承的设计比较难,其中一个工艺是预压,是指将滚珠固定到轴承套中的过程,这要求滚珠与轴承套表面结合紧密,没有间隙,以使钢珠磨损度最小。
通常在国内厂家轴承制造中,预压前上下轴承套是正对的,因为钢珠尺寸与轴承套尺寸肯定会存在一定误差,所以在预压受力后,滚珠同轴承套之间总有5—10微米的间隙,就是这个间隙,使得轴承的老化磨损程度大大增加,使用寿命缩短。
同样过程,在NSK公司的轴承制造中,预压时上下轴承套的会有一个5微米左右的相对距离,这样轴承套在受压后就会紧紧的卡住滚珠,使其间的间隙减小为零,在风扇工作中,滚珠就不会有跳动,从而使磨损降至最小,保证风扇畅通且长久高速运转。
翅片式风冷换热器设计

翅片式风冷换热器设计一、翅片式风冷换热器的设计原理翅片的设计要求较高,首先是要有足够的散热面积,以增加热量的传导面积。
其次,翅片要有较高的导热性能,以便迅速将热量传导到整个翅片表面。
此外,翅片的间距和形状也对流体流动和传热有着重要的影响。
二、翅片式风冷换热器的结构管道是用于传递热介质的通道,通常是通过焊接或套管连接到翅片上。
管道的材料选用应根据热介质的特性和工作环境来确定。
支撑结构是用于支撑翅片和管道的框架,通常由钢材制成。
其设计通常考虑到整个结构的强度和稳定性。
风扇是通过产生强风使翅片散热的关键组件。
风扇的功率和风速需要根据换热器的散热要求和风道设计来确定。
三、翅片式风冷换热器的性能指标1.散热面积:散热面积是决定换热器换热效果的关键因素,它与翅片的面积有关。
通常情况下,散热面积越大,换热效果越好。
2.热传导系数:热传导系数是指翅片材料导热的性能,高热导率的材料可以提高热量的传导速度和效率。
3.风压损失:风压损失是指在风扇吹风的过程中由于风扇本身的设计或管道布局引起的压力损失。
风压损失越小,换热器的风量越大,换热效果越好。
4.温度差:温度差是指热介质进入和离开换热器之间的温度差。
温度差越大,换热器的效果越好。
四、翅片式风冷换热器的应用1.电子设备散热:翅片式风冷换热器被广泛用于电子设备和计算机中,以帮助散热,防止过热导致设备损坏。
2.汽车冷却系统:翅片式风冷换热器被用于汽车发动机的冷却系统中,以将发动机产生的热量散发。
3.空调系统:翅片式风冷换热器被应用于空调系统中,将室内的热量传递到室外。
4.工业生产过程中的热交换:翅片式风冷换热器被广泛应用于工业生产过程中,如化工、石油和能源行业等,以完成热交换的任务。
综上所述,翅片式风冷换热器作为一种常见的换热设备,在工业领域中有着广泛的应用。
通过合理设计翅片和风扇结构,以及选择合适的材料和管道布局,能够获得较好的换热效果。
因此,在设计翅片式风冷换热器时,需要充分考虑其原理、结构和性能指标,以满足不同领域中的实际应用需求。
风冷散热设计及验算方案
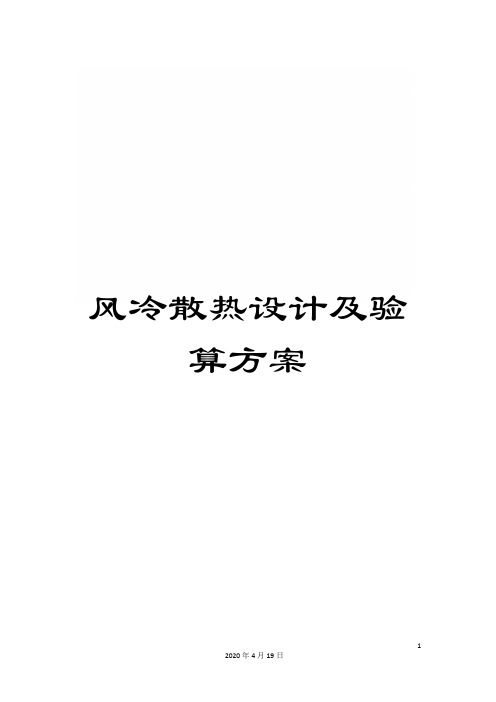
风冷散热设计及验算方案12020年4月19日22020年4月19日风冷散热设计及验算方案一、散热器的选配1、选用散热器的依据电力半导体器件(以下简称器件)的耗散功率、热阻(结壳热阻与接触热阻之和)和冷却介质的入口温度等,是选用散热器的基本依据。
器件被应用在各种各样的工况,在选用散热器时应该正确识别散热器、绝缘件和紧固件的型号和含义,了解不同散热器的散热能力和范围。
一般,一种器件仅从参数看,可能有两、三种散热器都能满足要求,但应结合自己的应用情况,诸如:冷却、安装、通用互换和经济性来综合考虑选取一种最佳的散热器。
2、散热器选用计算方法散热器的配置目的,是必须保证它能将元件的热损耗有效地传导至周围环境,并使其热源即结点的温度不超过j T ,取环境温度a T ,用公式表示为:P Q < ‥…‥…‥…‥…①()/j a Q T T R =-‥…‥…②其中:P ,元件的损耗功率;Q ,耗散功率,散热结构的散热能力;32020年4月19日j T ,元件工作结温,即元件允许的最高工作温度极限,取j T =125°C ;a T ,环境温度,水冷时规定为35°C ,风冷时规定为40°C 。
R ,热阻,热量在媒质之间传递时,单位功耗所产生的温升; jc cs sa R R R R =++‥…‥…③jc R ,结点至管壳的热阻,Rjc 与元件的工艺水平和结构有很大关系由制造商给出,范围一般为 0.8~2.0 K/W ;cs R ,管壳至散热器的热阻,与管壳和散热器之间的填隙,介质接触面的粗糙度平面度以及安装的压力等密切相关,影响接触热阻的因素较多,迄今没有一个普遍适用的经验公式加以归纳,因此工程设计中都是根据实验或参考实测数据来选择接触热阻,表1为某些典型接触面的接触热阻值;sa R ,散热器至空气的热阻,是散热器选择的重要参数,它与材质材料的形状和表面积体积以及空气流速等参量有关。
- 1、下载文档前请自行甄别文档内容的完整性,平台不提供额外的编辑、内容补充、找答案等附加服务。
- 2、"仅部分预览"的文档,不可在线预览部分如存在完整性等问题,可反馈申请退款(可完整预览的文档不适用该条件!)。
- 3、如文档侵犯您的权益,请联系客服反馈,我们会尽快为您处理(人工客服工作时间:9:00-18:30)。
风冷散热设计专题风冷散热原理:散热片的核心是同散热片底座紧密接触的,因此芯片表面发出的热量就会通过热传导传到散热片上,再由风扇转动所造成的气流将热量“吹走”,如此循环,便是处理器散热的简单过程。
散热片材料的比较:现在市面上的散热风扇所使用的散热片材料一般都是铝合金,只有极少数是使用其他材料。
学过物理的人应该都知道铝导热性并不是最好的,从效果来看最好的应该是银,接下来是纯铜,紧接着才会是铝。
但是前两种材料的价格比较贵,如果用来作散热片成本不好控制。
使用铝业也有很多优点,比如重量比较轻,可塑性比较好。
因此兼顾导热性和其他方面使用铝就成为了主要的散热材料。
不过我们使用的散热片没有百分之百纯铝的产品,因为纯铝太过柔软,如果想做成散热片一般都会加入少量的其他金属,成为铝合金(得到更好的硬度)。
风扇:单是有了一个好的散热片,而不加风扇,就算表面积再大,也没有用!因为无法同空气进行完全的流通,散热效果肯定会大打折扣。
从这个来看,风扇的效果有时甚至比散热片还重要。
假如没有好的风扇,则散热片表面积大的特点便无法充分展现出来。
挑选风扇的宗旨就是,风扇吹出来的风越强劲越好。
风扇吹出来的风力越强,空气流动的速度越快,散热效果同样也就越好。
要判断风扇是否够强劲,转速是一个重要的依据。
转速越快,风就越强,简单看功率的大小。
轴承:市面上用的轴承一般有两种,滚珠轴承和含油轴承,滚珠轴承比含油轴承好,声音小、寿命长。
但是滚珠轴承的设计比较难,其中一个工艺是预压,是指将滚珠固定到轴承套中的过程,这要求滚珠与轴承套表面结合紧密,没有间隙,以使钢珠磨损度最小。
通常在国内厂家轴承制造中,预压前上下轴承套是正对的,因为钢珠尺寸与轴承套尺寸肯定会存在一定误差,所以在预压受力后,滚珠同轴承套之间总有5—10微米的间隙,就是这个间隙,使得轴承的老化磨损程度大大增加,使用寿命缩短。
同样过程,在NSK公司的轴承制造中,预压时上下轴承套的会有一个5微米左右的相对距离,这样轴承套在受压后就会紧紧的卡住滚珠,使其间的间隙减小为零,在风扇工作中,滚珠就不会有跳动,从而使磨损降至最小,保证风扇畅通且长久高速运转。
强迫风冷设计当自然风冷不能解决问题时,需要用强迫空气冷却,即强迫风冷。
强迫风冷是利用风机进行鼓风或抽风,提高设备的空气流动速度,达到散热目的。
强迫风冷在中大功率的电子设备中应用广泛,因为它具有比自然风冷多几倍的热转移能力。
与其他形势强迫风冷比较有结构简单,费用低,维护简便等优点。
整机强迫风冷有两种形式:鼓风冷却和抽风冷却。
鼓风冷却特点是风压大,风量集中。
适用于单元内热量分布不均匀,风阻较大而元器件较多的情况。
当单元内风阻较大,需要单独冷却的元件和热敏元件较多,且各单元间热损相差有较大时,建议用凤管冷却,以便控制各单元风量的需要。
当旨在机柜底层具有风阻较大元件,中上层五热敏元件的情况下,建议用无风管形式来降低成本。
抽风冷却特点是风量大,风压小,风量分布比较均匀,在强迫风冷中应用更广泛。
他也可分为有管道和无管道两种情况。
对无管道的机框抽风,整个机框相当于一个大风管,要求机柜四周密封好,侧壁也不应开空,只允许有进出风口,考虑热空气上升,抽风机常装在机框上部或顶部,出风口面对大气,进风口装在机柜底部,这种无管道风冷方式常用于机柜内各元件冷却表面风阻较小的设备。
对于在气流上升部位又热敏元件或不耐热元件则要必须用风管使气流弊开,并沿需要的方向流动,其进风口通常在机框侧面,出风口在机柜顶部。
对某些发热较大的功率管,整流管等器件可以单独风冷或用管道风冷。
由于在强迫风冷时灰尘,油雾,水蒸气和烟等会被气流带进设备而滋生内部污染,以及如何提高制冷效果等,因此,在进行强迫风冷设计时,应遵循以下基本要求;1.强迫空气的流动方向应于自然对流空气的流动方向尽量一致。
2.在气流通道上,应尽量减小阻力,并避免大型元器件阻塞奇六。
要将气流合理分配给给单元和元器件。
使所有元器件,部件都能顺利冷却,并使其谏缘陀诙疃ㄎ露认鹿ぷ鳎衫梅至髌偷髡蛊髦苯恿鞴⑷仍?3.要合理排列元器件,应尽可能把不发热与发热小的和耐热性能低的及热敏的元件排在冷空气的上游(靠近进风口),其余元件尽量按他们的温度高低以递增的顺序排列,对那些发热量大而导热性差的器件必须暴露在冷却空气中,必要时进行单独冷却。
4.在不影响电性能的前提下,将发热量大的元器件集中在一起排列,并与其他元器件热绝缘,这样可以减少风量,风压,而减少风机功率。
5.赠机通风系统的近出风口应尽量远离,要避免气流短路,且入口空气温度与出口温度之差一般不要超过14度。
6.用于冷却电子设备内部元器件的空气,必须经过过滤,要安装防尘口。
7.在湿热环境下,为避免潮湿空气对元器件直接影响,可采用空芯印制板组装结构。
8.为保证通风系统安全可靠工作,必要时要在冷却系统中社控制保护装置。
9.应尽量减少强迫风冷系统的气流噪声和风机的噪声。
10.通风孔应满足电磁兼容性及安全性要求。
11.在一些大型电子设备中为提高电子线路对电磁干扰的屏蔽能力常将多块印制板在一个用金属板构成的密封小盒内,让元件产生的热量通过盒内的对流,传导,和辐射传给盒壁,再有盒壁传给冷却空气把热量散掉。
12.当机柜或机箱内有多块印制板平行排列时,印制板的间距不宜相差太大,否则,气流将直接从间距大的地方流过,而降低对其印制板的冷却效果。
13.再强迫风冷冷却的设计中,正确选择风机很重要。
风机有离心式和轴流式,其中离心式风机特点是风压高,风量集中,风量小;轴流式风机是风压小,风量大。
选择风机时要根据空气流量,风压大小,风道的阻力特性,体积,重量和噪声等等进行综合分析。
有关强迫风冷方面的一些看法:1、风机的先择:选择风机时,应考虑的因素包括:风量,风压,效率,空气流速,系统或风道的阻力特性,应用环境条件,噪声,以及体积,重量等,其中风量和风压是主要参数,要求风量大,风压低的设备,尽量采用軸流式风机,(反之,则选用离心式风机);所选风机的风量或风压不能满足要求时,可以采用串联或并联的方式来满足要求。
2、风机的安装:A, 外壳进风孔(或出风孔)的总面积要不小于风机总的通风面积;B, 风机不论是抽风还是鼓风,安装时都最好不要直接贴装在开孔的钣金上;3、风道的设计:风道要短而直,拐弯要少;在结构尺寸不受影响时,增大风道面积可减小压力损失,同时可降低风机的噪声;当风道进口需要安装防尘时,在防尘的效果和流体阻力之间要权衡;元件应按叉排列方式,这样可以提高气流的紊流程度,增强散热能力。
v 自然冷却的风路设计Ø 设计要点ü 机柜的后门(面板)不须开通风口。
ü 底部或侧面不能漏风。
ü应保证模块后端与机柜后面门之间有足够的空间。
ü机柜上部的监控及配电不能阻塞风道,应保证上下具有大致相等的空间。
ü对散热器采用直齿的结构,模块放在机柜机架上后,应保证散热器垂直放置,即齿槽应垂直于水平面。
对散热器采用斜齿的结构,除每个模块机箱前面板应开通风口外,在机柜的前面板也应开通风口。
风路设计方法v 自然冷却的风路设计Ø 设计案例风路设计方法v 自然冷却的风路设计Ø 典型的自然冷机柜风道结构形式风路设计方法v 强迫冷却的风路设计Ø 设计要点ü 如果发热分布均匀,元器件的间距应均匀,以使风均匀流过每一个发热源.ü 如果发热分布不均匀,在发热量大的区域元器件应稀疏排列,而发热量小的区域元器件布局应稍密些,或加导流条,以使风能有效的流到关键发热器件。
ü 如果风扇同时冷却散热器及模块内部的其它发热器件,应在模块内部采用阻流方法,使大部分的风量流入散热器。
ü进风口的结构设计原则:一方面尽量使其对气流的阻力最小,另一方面要考虑防尘,需综合考虑二者的影响。
ü风道的设计原则风道尽可能短,缩短管道长度可以降低风道阻力;尽可能采用直的锥形风道,直管加工容易,局部阻力小;风道的截面尺寸和出口形状,风道的截面尺寸最好和风扇的出口一致,以避免因变换截面而增加阻力损失,截面形状可为园形,也可以是正方形或长方形;风路设计方法v 强迫冷却的风路设计风路设计方法v 强迫冷却的风路设计Ø 电源系统典型的风道结构-吹风方式风路设计方法热设计的基础理论v 自然对流换热Ø 大空间的自然对流换热Nu=C(Gr.Pr)n.定性温度: tm=(tf+tw)/2定型尺寸按及指数按下表选取散热器的设计方法v 散热器冷却方式的判据Ø 对通风条件较好的场合:散热器表面的热流密度小于0.039W/cm2,可采用自然风冷。
Ø 对通风条件较恶劣的场合:散热器表面的热流密度小于0.024W/cm2,可采用自然风冷。
v 散热器强迫风冷方式的判据Ø 对通风条件较好的场合,散热器表面的热流密度大于0.039W/cm2而小于0.078W/cm2,必须采用强迫风冷。
Ø 对通风条件较恶劣的场合:散热器表面的热流密度大于0.024W/cm2而小于0.078W/cm2,必须采用强迫风冷。
散热器的设计方法v 散热器设计的步骤通常散热器的设计分为三步1:根据相关约束条件设计处轮廓图。
2:根据散热器的相关设计准则对散热器齿厚、齿的形状、齿间距、基板厚度进行优化。
3:进行校核计算。
散热器的设计方法v 自然冷却散热器的设计方法Ø 考虑到自然冷却时温度边界层较厚,如果齿间距太小,两个齿的热边界层易交叉,影响齿表面的对流,所以一般情况下,建议自然冷却的散热器齿间距大于12mm,如果散热器齿高低于10mm,可按齿间距≥1.2倍齿高来确定散热器的齿间距。
Ø 自然冷却散热器表面的换热能力较弱,在散热齿表面增加波纹不会对自然对流效果产生太大的影响,所以建议散热齿表面不加波纹齿。
Ø 自然对流的散热器表面一般采用发黑处理,以增大散热表面的辐射系数,强化辐射换热。
Ø 由于自然对流达到热平衡的时间较长,所以自然对流散热器的基板及齿厚应足够,以抗击瞬时热负荷的冲击,建议大于5mm以上。
散热器的设计方法v 强迫冷却散热器的设计方法Ø 在散热器表面加波纹齿,波纹齿的深度一般应小于0.5mm。
Ø 增加散热器的齿片数。
目前国际上先进的挤压设备及工艺已能够达到23的高宽比,国内目前高宽比最大只能达到8。
对能够提供足够的集中风冷的场合,建议采用低温真空钎焊成型的冷板,其齿间距最小可到2mm。
Ø 采用针状齿的设计方式,增加流体的扰动,提高散热齿间的对流换热系数。
Ø 当风速大于1m/s(200CFM)时,可完全忽略浮升力对表面换热的影响。
散热器的设计方法v 在一定冷却条件下,所需散热器的体积热阻大小的选取方法散热器的设计方法v 在一定的冷却体积及流向长度下,确定散热器齿片最佳间距的大小的方法散热器的设计方法v 不同形状、不同的成型方法的散热器的传热效率比较散热器的设计方法v 散热器的相似准则数及其应用方法v 机箱的热设计计算Ø 密封机箱WT=1.86(Ss+4St/3+2Sb/2)Δt 1.25+4σεTm3ΔTØ 对通风机箱WT=1.86(Ss+4St/3+2Sb/2)Δt 1.25+4σεTm3ΔT+1000uAΔT。