铝合金压铸技术培训教材
压铸安全知识培训教材ppt课件
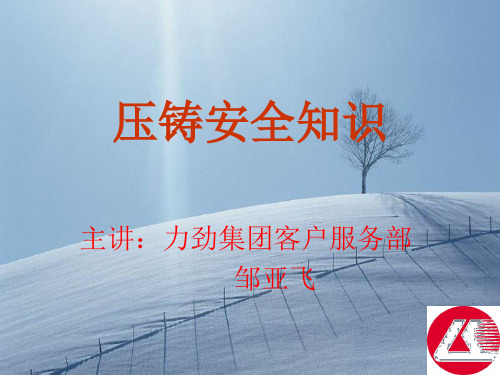
1.3工具定位
建议设置专用的工具架,物料 堆放应设立专门区域。
1.4地面保持清洁
尤其不能有润滑油液压油,防 止滑倒。添加润滑油液压油后 , 应将漏出的油用碎布或锯木屑 清理干净。
1.5劳保 操作者应着耐热手套,面罩,
防护眼镜,防护鞋等劳保用品。
1.6操作区 无关人员不能进入操作区。
1.7安全通道 务必保持畅通。
9、确定安全管理责任人,定期检查, 消除隐患。
第二节 压铸生产的安全隐患
1、锁模速度快 压铸机机械动作速度快,尤其是小吨位热
室压铸机锁模速度可达到数米/秒,操作或 保养不当可导致设备及人身安全事故。 2、环境
压铸生产环境管理不当,例如地面液压 油多可能造成滑倒跌伤。
3、飞料
压铸机射料压力大,速度快, 调整不当或模具未锁紧可能飞 料造成烫伤。
2.10锁模吉制 检查锁模到位及锁模确认吉制。
2.11模具区 开机时严禁进入或将手伸入模具区。取产 品使用专用夹钳。
2.12调整参数
由专人调整参数,机器正在自动 运行时严禁调整参数。
2.13模具
对未使用过的模具要仔细检查, 初次压铸时必须降低射料压力及速 度。
2.14 紧急处理
当机器发生紧急故障(如超压、管 路破裂,漏油及其他可能造成严重人 身、设备等事故的),必须立即停机, 关掉电源,并紧急处理和维修。有火 灾险情时,应放掉蓄能器中氮气。
2.8.10电源装置的外罩处于正确位置 时,才能操作电路开关。
2.9防范火灾
2.9.1在合适位置处应存放灭火器。 2.9.2易燃品至少应与可能产生火源处相
距10米。 2.9.3必须对合金溶液和炉渣冷处理。 2.9.4保持可能产生易燃气体的地方有良
压铸工艺设计培训教材

12.08.2021
3
当以低的充填速度及( A 内/A )>1/3时,除液体金属聚集区的 前沿部分稍有扰动外,其余部分则相当稳定,而且随着聚集区 增长,充填过程越来越平稳。反之,当( A 内/A )<1/3时,在 高的充填速度下,整个充填过程中,聚隼区发生激烈扰动。在
聚集区追上“前流”以前,型腔被液体金属填充部分的长度与
小。如果把流动过程看成在一封闭的管道中进行,根据等流量连续方程则有以下关系:
12.08.2021
由上式可知金属液的充填速 度与压射速度、压室(压射 冲头)直径的平方成正比, 而与内浇口的截面积成反比。 因此调整冲头速度、更换压 室直径、改变内浇口截面积 均能调整充填速度。
19
2.充填速度的选择 过高的充填速度将产生如下不利的影响:
( 2)对填充条件的影响 金属液在高的压射比压作用下填充 型腔动能加大,流动性改善,有利于克服浇注系统和充填簿壁压 铸件型腔的阻力,提高簿壁压铸件质量。
是否压射比压越高越好?
12.08.2021
13
压射比压的选择
当压铸机上的压射系统没有增压机构时,Ill、IV两个阶段的压射 比压是相同的。当压铸机上的压射系统设有增压机构时,这两个 阶段的比压不同。这时,填充比压用来克服浇注系统和型腔中金 属液的流动阻力(特别是内浇口处的阻力),使金属液流保证达 到所需要的内浇口速度;而增压比压则决定了正在凝固的金属液 受到的压力及这时所形成的胀型力的大小。
12.08.2021
11
3.2.2 压射比压
压射比压P比可由压射力或工作压力P压和驱动(压射)缸及压射冲头直径求得,即
12.08.2021
12
压射比压的作用和影响
(1)对压铸件力学性能的影响 压射比压大合金结晶细,细 晶层增厚。由于填充特性改善,压射比压大,压铸件表面质量提 高,气孔缺陷减轻,从而抗拉强度提高,但伸长率有所降低。
压铸培训教材

压铸培训教材压铸是一种加工工艺,与砂型铸造和蜡模铸造不同,具有大批量生产、尺寸精密、外表漂亮的特点。
压铸可分为热室压铸和冷室压铸。
压铸的过程包括低速阶段、高速阶段和增压阶段,目的是为了排出空气、获得漂亮的压铸外观、卷入空气的细微化、补充因冷却收缩导致的缩孔和使铸件获得致密的组织。
新的压铸工艺包括真空压铸、ACURAD压铸、局部加压法和半凝固压铸。
在压铸过程中,需要注意安全事项,例如模具分型面处不得站立,炉子里不能有水分进入,操作时必须切断电源开关等。
应急措施包括铝液爆炸时躲避并高声通知,发现火情或异常动作时立即关闭电源并用灭火器或砂子扑灭,如有人员受伤,必须送医院抢救。
安全的三原则是整理、整顿、清洁、清扫,点检、保养和作业标准化。
铝合金压铸件的不良分析及对策包括尺寸不良、外观不良、内部不良、材质不良和其他不良。
压铸件是铝液高速、高压浇入精密的模具中,不良原因及对策相对明确易掌握。
压铸是一种大批量生产的方法,但是不良发生具有连续性,可能在较短的时间内造成大量废品。
此外,压铸件的尺寸精度很高,稍微的变形都可能导致组装和加工不良,意外的尺寸问题也经常会发生。
压铸模具的冷却速度很快,这可能会导致大型铸件和薄形产品出现花斑等不良现象。
由于高速高压,压铸可能导致气体收缩留在铸件中,因此气孔的彻底消除很困难,电焊补孔也可能导致压铸气孔膨胀,而T6热处理也不现实。
此外,压铸还可能产生硬质点等不良。
压铸不良的直接原因包括产品形状设计不合理、压铸机及充填条件的不合理、模具及浇口系统的不合理、压铸作业的不适当、原材料及溶解技术的不适当以及作业者的失误。
而压铸不良的间接原因则包括工艺的不合理、品质管理(操作、作业标准、检查标准等)的未落实、操作者和管理者不重视等。
尺寸不良包括尺寸不良、错位、型芯让模、滑块让模、变形、多肉、缺肉、浇口、渣包缺肉等。
其中,尺寸不良的原因可能是图面尺寸误记、检查失误、修模遗漏等。
为了解决这些问题,可以加强图纸管理、定期更换型芯、改变浇口方向、改变产品形状、修正模具磨损等。
压铸工艺培训资料
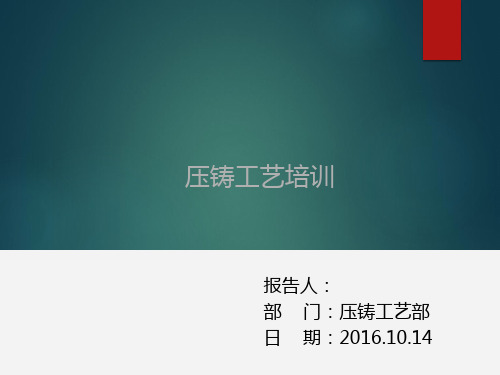
≤0.25
≥240M Pa
≥130M Pa
≥2%
≥60H B
≤0.05
≤0.15
≤0.15
≥240M Pa
≥140M Pa
≥1%
≥70H B
6
AlSi9Cu 3(Fe)
DIN 1706-2010 (DIN 1725-
0.60.8
1983)
3.23.7
8.0- 0.310.0 0.5
0.10.3
不去除材料 表示指定表面是用不去除材料方法获得,此图形符号也可用于表示保持上道工序形成的表面,不管 表面粗糙度 这种状况是通过去除或不去除材料形成的
DIN/JIS /ASTM
德国/日本/ 美国标准
DIN表示德国标准化主管机关Deutsches Institut für Normung,JIS表示日本工业标准: Japanese Industrial Standards,ASTM表示美国材料与实验协会:American Society for Testing and Materials
≤1.2
≤0.3 ≤0.15 ≤0.15 ≤0.1
≤0.2
≤0.15
≥240M Pa
≥140M Pa
≥1%
≥90H 屈强强度 B ≥140Mpa
7
AlSi12C u1(Fe)
DIN 1706
0.7--1.3
0.71.2
10.513.5
≤0.55 ≤0.35 ≤0.55
≤0.3
≤0.2
≤0.1
≤0.1
➢假如产品表面要抛光电镀,外观要求高,那就不得不用锌合金的。铝合金材质是很 难达到很高的表面质量要求的,因为铝合金压铸成型性能较差,在制品表面易产品很 多的气孔,电镀出来后表面质量很差
压铸安全培训教材
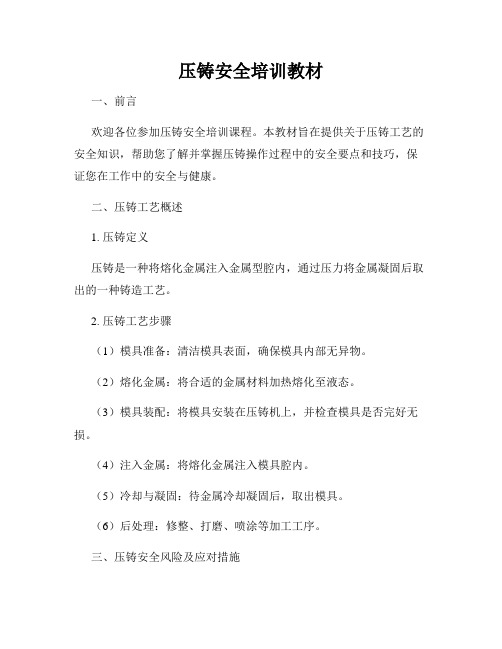
压铸安全培训教材一、前言欢迎各位参加压铸安全培训课程。
本教材旨在提供关于压铸工艺的安全知识,帮助您了解并掌握压铸操作过程中的安全要点和技巧,保证您在工作中的安全与健康。
二、压铸工艺概述1. 压铸定义压铸是一种将熔化金属注入金属型腔内,通过压力将金属凝固后取出的一种铸造工艺。
2. 压铸工艺步骤(1)模具准备:清洁模具表面,确保模具内部无异物。
(2)熔化金属:将合适的金属材料加热熔化至液态。
(3)模具装配:将模具安装在压铸机上,并检查模具是否完好无损。
(4)注入金属:将熔化金属注入模具腔内。
(5)冷却与凝固:待金属冷却凝固后,取出模具。
(6)后处理:修整、打磨、喷涂等加工工序。
三、压铸安全风险及应对措施1. 烫伤风险(1)风险描述:熔化金属温度高,操作不当可能导致烫伤。
(2)应对措施:佩戴隔热手套、护目镜等个人防护装备,确保安全操作。
2. 压力伤害风险(1)风险描述:压铸机在工作过程中产生高压,操作不当可能导致压力伤害。
(2)应对措施:严格按照操作规程操作,确保安全距离,避免身体接近压铸机。
3. 金属飞溅风险(1)风险描述:熔化金属注入模具时,发生喷溅,可能导致人身伤害。
(2)应对措施:佩戴热防护服、面罩等防护装备,保护头部和身体。
4. 模具损坏风险(1)风险描述:操作不当,可能导致模具损坏。
(2)应对措施:正确安装模具,操作时避免撞击、碰撞等危险行为。
5. 职业病风险(1)风险描述:长期接触金属粉尘和有害物质可能导致职业病。
(2)应对措施:佩戴呼吸防护装备,做好通风换气,定期体检。
四、紧急情况处理1. 烧伤处理(1)应立即用清水冲洗烧伤部位,至少持续20分钟。
(2)及时送医院就医,接受专业医生治疗。
2. 失火处理(1)迅速切断电源和燃气供应,确保消防安全。
(2)使用灭火器或呼叫专业消防队伍进行灭火。
五、安全操作指南1. 熟悉压铸机的操作规程和紧急停机按钮位置。
2. 不用手触摸正在运作的压铸机。
3. 遵守防护装备佩戴规定,包括护目镜、防护手套、安全鞋等。
压铸操作工艺培训讲义(连载四)

压铸操作工艺培训讲义(连载四)五、国内外压铸铝合金1、国标牌号标注方法在国标中压铸铝合金的代号是用字母“YL”和其后的数字表示,“Y”及“L”分别为“压”、“铝”两字汉语拼音的第一个字母。
2、国内外主要压铸铝合金化学成分和力学性能如下表:压铸铝合金国家标准:压铸铝合金日本标准:压铸铝合金欧盟标准:压铸铝合金美国标准:3、合金中各元素的主要作用4、各元素对合金的影响①铝合金中硅的作用有两点,第一是增加流动性,但这点主要是对重力铸造等很低压强下的充填而言。
检测与实践都表明,不加硅的铝合金和加了硅的合金在超过1MPa的充型压强下,充型性能差异不大,而现在压铸生产中压射充型压强均达到30MPa以上,即使流动性最差的合金、如变形铝合金及变形镁合金,都不存在充型不足的困难。
第二点,也是铝合金中硅作用的最重要的一点,也是大家最容易忽略的一点。
硅的作用是减少“液-固”相的相变体积收缩率。
特别是高硅铝合金,当硅含量达到20%左右时如B390,ADC14铝合金,相变体积可以保持不变。
由于铝合金压铸属于单方向的高压强充型铸造,不具备有反向补缩作用。
正是这个原因压铸行业才特意配制相变收缩率比较低,含硅量高的铝合金牌号。
②硅含量的降低,压铸件毛坯在同样的压铸条件下,缩孔、疏松现象严重,合格率明显降低。
主要原因是硅含量的降低导致铝合金体积收缩率较大。
③硅及铜含量的降低,产品的机械强度降低,热裂倾向增加。
合金的延伸率增强,变得更软。
顶出时易变形甚至开裂。
一方面通过Mg和Mn 含量的配比提高机械强度,并在压铸工艺参数设定时,调整冷却时间、顶出速度及顶出力及脱模剂的喷涂,解决产品顶出时的变形及开裂的缺陷。
④元素Mn的作用,锰能阻止铝合金的再结晶过程,提高再结晶温度并能显著细化结晶晶粒。
再结晶的细化,主要是通过MnAl6化合物弥散质点对再结晶粒长大起阻碍作用。
过多的MnAl6能溶解杂质铁形成(Fe,Mn)Al6减少铁的有害影响。
故锰的含量也不能太高,控制在0.30-0.40%范围内。
铝合金压铸技术培训教材

压铸零件缺陷
二、压铸件缺陷产生原因及解决方法:
缺陷名称 特征 产生原因 1、模具的顶杆设计布置不平衡及数量不 够; 2、开模时间过早,铸件未能定型引起刚 性不够; 3、或模具抛光不够,引起阻力增大顶出 变形。 首先进入模腔内的金属液形成极薄而又 不完全的金属层后被后来的金属液弥补 而留下的痕迹。 模具的排气不良,内浇口开设不良;金 属液凝固时间不够,过早顶出,受压气 体膨胀。 模腔内两股金属液相互不能融合为一 体,此外由于困气,在型腔最后充填部 位也会产生这种缺陷。 防止方法
2、具有较好的导热性和抗热疲劳性;
3、高温下不易氧化,能抵抗液态金属的粘附和腐蚀; 4、材料热膨胀系数小,热处理变形小,淬透性良好。
二、常用压铸模钢材 国内:4Cr5M0SiV1 美国:H13 瑞典:8418 日本:SKD61
压铸零件缺陷
一、压铸件缺陷分析: 1、 缺陷分类: A、几何缺陷---压铸件形状,尺寸与技术要求偏离,尺寸偏差 变形等。 B、表面缺陷---压铸件外观不良,出现花纹、气泡、冷隔、毛 刺、拉伤、烧伤(冲蚀) C、内部缺陷---加工后出现气孔、缩孔。
2)内浇口厚度尺寸要根据铸件的形状复杂式简单壁厚来选取; 3)塔放合路器的内浇口应设计在底部,目的是使金属液减短路径,减少压射 过程的卷气产生气孔。
压铸模具设计
冷却系统
由于金属液是高速、高温状态下进入模具型腔内,必然会对模具产生激烈的冲 击和冲刷,产生机械的力和热应力,在每一个压铸件的生产过程中,由于模具与金 属液之间的热交换使模具表面产生周期性温度变化,引起周期性的热膨胀和收缩, 产生周期性热应力,模温过高,易产生粘模,使用冷却温控系统,保证模具的工作 温度。 1)如机箱模具,双工器模具的内浇口处,由于金属液首先进入,如不设备冷却水道, 则由高温引起内浇口处粘模,甚至拉裂压铸件。 2)如果模具冷却不充分,会使压铸顶出过程产生凹痕。
压铸培训教程.pptx

r最大= h
R=r+h
压
铸
當h1=h時﹕
模
r≧ h+h1
设
3
计
R=r+ h+h1
2
2020/8/16
K值
鋅﹕1/4 鋁﹕1/2
Macherchen
10
四.成型工艺
(五)孔
鋅:0.8~1.5(最小直径)
鋁:2.0~2.5(最小直径)
(六)文字:凸凹纹﹐直纹
压
铸 例:平行纹(直纹)高0.7MM﹐间距1MM﹐角度60.5。
压 铸 模 设 计
2020/8/16
由喷射﹑喷射流转变为压力流
Macherchen
5
三.压铸制程溶汤的流动方式
(二)压力流
因冲撞,磨擦和气体阻力等(抽象),运动能量耗尽(常发生在加强筋,
凸台,远离浇口之部位),具有接受后继金属液中供给的压力能,从而使金
属液沿着型腔内壁前进的特性.利用这特性,可便以型腔排气.在压力流充
13
五.压铸合金及其性能
压 铸 模 设 计
2020/8/16
鋅合金種類
合 商業習用編號
No.3
金
ASTM
AG40A
代
UNS
Z33251
號
SAE
903
Die Cast Aged
抗拉強度(Kg/mm2) 28.8 24.6
機 降伏強度(Kg/mm2) --
--
伸長率(%)
10
16
械 剪切強率(Kg/mm2) 21.8
铸
模 均匀﹐保证足够强度与刚度的前提)
设
计
2020/8/16
Macherchen
压铸培训教材
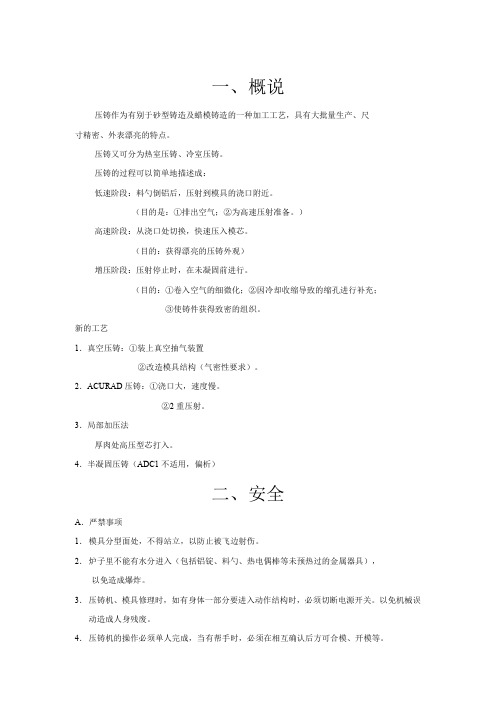
一、概说压铸作为有别于砂型铸造及蜡模铸造的一种加工工艺,具有大批量生产、尺寸精密、外表漂亮的特点。
压铸又可分为热室压铸、冷室压铸。
压铸的过程可以简单地描述成:低速阶段:料勺倒铝后,压射到模具的浇口附近。
(目的是:①排出空气;②为高速压射准备。
)高速阶段:从浇口处切换,快速压入模芯。
(目的:获得漂亮的压铸外观)增压阶段:压射停止时,在未凝固前进行。
(目的:①卷入空气的细微化;②因冷却收缩导致的缩孔进行补充;③使铸件获得致密的组织。
新的工艺1.真空压铸:①装上真空抽气装置②改造模具结构(气密性要求)。
2.ACURAD压铸:①浇口大,速度慢。
②2重压射。
3.局部加压法厚肉处高压型芯打入。
4.半凝固压铸(ADC1不适用,偏析)二、安全A.严禁事项1.模具分型面处,不得站立,以防止被飞边射伤。
2.炉子里不能有水分进入(包括铝锭、料勺、热电偶棒等未预热过的金属器具),以免造成爆炸。
3.压铸机、模具修理时,如有身体一部分要进入动作结构时,必须切断电源开关。
以免机械误动造成人身残废。
4.压铸机的操作必须单人完成,当有帮手时,必须在相互确认后方可合模、开模等。
5.行车吊装模具及坩锅时,在其下方不得有人或压机,不准快速晃动。
B.应急措施1.铝液爆炸时,操作工应尽快躲避,并高声通知。
2.发现火情或异常动作时,应立即关闭电源,随后用灭火器或砂子扑灭。
3.如有人员受伤,必须以最快速度送医院抢救。
C.安全的三原则1.4S—整理、整顿、清洁、清扫a.清洁的场地容易发现漏油、漏水之处,以便及时修理。
b.整齐、整洁的场所在发生意外时便于及时躲避。
c.防止滑倒、绊倒等的发生。
2.点检、保养可以提前发现设备、装置的隐患,尽快解决。
3.作业标准化作业标准含有安全效率、质量考虑,而且也是历次血的教训提炼而成的。
操作者必须无条件执行(不管理解与否),生产主管应进行监督、指导,以利操作者理解、执行。
三、不良分析及对策(铝合金)(一)分类1.尺寸不良2.外观不良3.内部不良4.材质不良5.其他不良(二)特点1.压铸件是铝液高速、高压浇入精密的模具中,发生的不良原因及对策,与其他铸造方法比较相对明确易掌握。
压铸学习培训教材
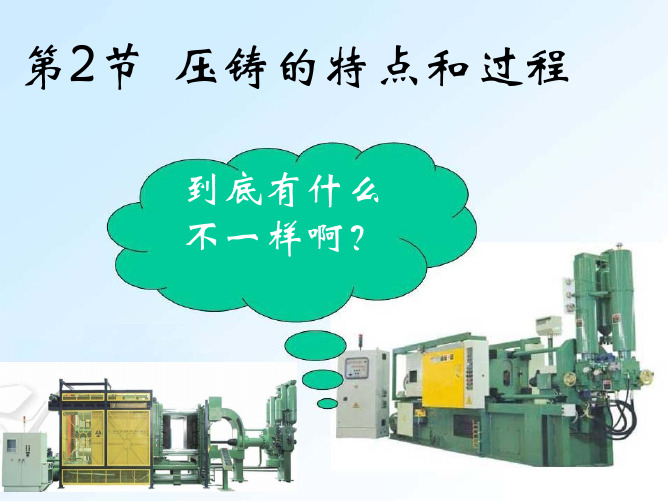
压铸工艺的优势
2.2 压铸的过程
2.2.1 压铸工艺的过程
配置涂料
润滑冲头 喷涂料
让我们作循环
合模
集中熔化
清理模具
给汤
机边保温
取件 顶出
压射 持压冷却
详细介绍压 射的步骤。
开模
以力劲压铸机为例
2.2 压铸的过程
2.2.2 压铸工艺--压射过程
为什么需要 增压?
高了金属利用率,减少了大量的加工设备和工时;
压铸工艺的缺点
1:易产生气孔,一般不能进行热处理; 2:对内凹复杂的铸件,压铸较为困难; 3:高熔点合金(如铜,黑色金属),压铸型寿命较低; 4:不宜小批量生产,其主要原因是压铸模制造成本高。
压铸零件有什 么特色?
2.1 压铸的特点
2.1.3 压铸工艺的特点
耐蚀性优良 力学性能好 加工性较好 加工表面光亮 重量轻 铸造工艺复杂
铝锌合金 铝镁合金
压铸 铝合金
铝硅合金 铝铜合金
流动性好 收缩小 热裂倾向小 气密性较好 力学性能较好 延伸率较低
力学性能很好 加工性好 焊接性好 铸造性能不好 耐蚀性不好 收缩率大
3.1 压铸的三要素—原材料
3.1.5 常用铝合金化学成分和机械性能
压铸工艺特点决定的:排气、补缩、压扁气孔---必须面对的课题
低速
高速
增压
气泡
低速
将注入压室内的合金液运送至浇口。 这时,合金液表面不会产生波纹, 且可从排气口排放压室内的空气, 以防止空气进入合金液内。 但是,如果速度太慢,就会发生凝固;
速度太快,就会卷入空气。
高速
产品的成形。 从合金液满到压室浇道的位置开始高速启动。 压室、浇道內的空气排空。 浇口一般较窄,形成喷雾状,進入产品细小部份 ,完成品质较好的铸件。 产品內的空气不抽空会残留在产品的內部。
压铸技术培训课件
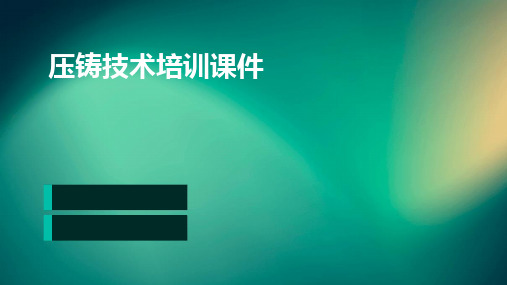
压铸前准备
包括选择合适的压铸合金、预 热模具、准备压铸机等步骤。
压射成型
在压射冲头的作用下,将熔融 金属高速压入模具型腔,并在 压力下冷却凝固。
清理与后处理
对压铸件进行清理、去毛刺、 热处理等后处理工序。
压铸机类型及结构
热室压铸机
压室浸在保温熔炉内,压射冲头直接作用于熔融金属,适用于锌、镁等低熔点合金的压铸。
现阶段
近年来,随着新材料、新工艺和新技术的不断涌现,压铸 技术正朝着高精度、高效率、高自动化方向发展。同时, 环保和节能成为压铸技术发展的重要趋势。
压铸技术应用领域
汽车工业
航空航天工业
汽车是压铸件最大的应用领域之一,包括发 动机缸体、缸盖、曲轴箱、刹车系统零部件 等。
航空航天领域对金属件的性能和质量要求极 高,压铸技术可用于制造飞机发动机零部件、 航空座椅零部件等。
03 压铸材料选择与处理
常用压铸合金材料
铝合金
具有良好的流动性、耐磨性和耐 腐蚀性,适用于制造复杂、薄壁、
耐压铸件。
锌合金
具有优良的铸造性能、机械性能 和耐腐蚀性,适用于制造汽车、 电器等压铸件。
铜合金
具有高强度、高硬度、耐磨性和 耐腐蚀性,适用于制造承受重载、 高温和腐蚀环境的压铸件。
镁合金
具有密度小、比强度高、减震性 好等特点,适用于制造轻量化和
压铸技术培训课件
contents
目录
• 压铸技术概述 • 压铸工艺及设备 • 压铸材料选择与处理 • 压铸过程控制与质量保障 • 缺陷分析与优化措施 • 安全生产与环保要求
01 压铸技术概述
压铸定义与分类
压铸定义
压铸是一种金属成型工艺,通过高压将熔融件。
压铸部培训教材
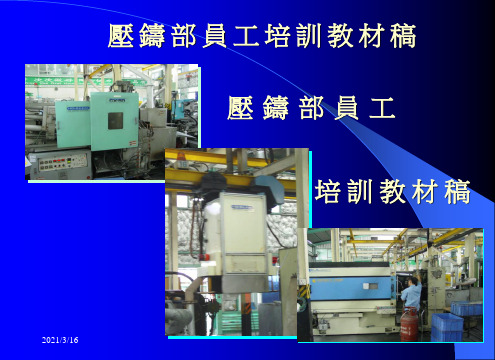
c. 電鍍廢料如混在合金料中﹐ 會帶來后工序加工困難﹐ 因為電鍍廢料中含有鎳﹑鉻﹐會造成鑄件后工序拋光機加工 困難。
2021/3/16
15
壓鑄部員工培訓教材稿
一﹑成型鑄件生產
1. 5. 機台面板控制
1.5.1. 壓鑄部現有機型有五種﹕
所有員工首先必須熟悉每種機器控制面板﹐控制面板有手
動﹐半自動﹐全自動﹐手動鎖模﹐開模﹐調模﹐離合咀﹐頂針﹑
馬達急停制等功能。
2021/3/16
18
壓鑄部員工培訓教材稿
一﹑成型鑄件生產
1. 5. 機台面板控制
1.5.2. 操作控制面板存在的問題: 如不熟悉面板控制鍵之功能而誤操作﹐可能導致工傷
事故或品質事故。 1. 5. 3 . 解決方法﹕
2021/3/16
3
壓鑄部員工培訓教材稿
2. 2 各工位操作技能培訓
2.2.1. 啤工 2.2.2. 由拉長﹑組長或技朮員現場對員工對各型機種面板作講 解并實地操作傳授﹐了解各開關性能及作用。 2.2.3. 工模安裝 2.2.4. 工模預熱 2.2.5. 噴涂技巧 2.2.6. 去水口方法
2021/3/16
a. 如不能清楚了解以上三種模具很容易導 致撞模情況發生
b. 安裝模具時間耗時過長影響效率達成 1. 3. 解決方法﹕
培訓員工各種具按如下上模 流程進行
2021/3/16
8
壓鑄部員工培訓教材稿
一﹑成型鑄件生產
A . 抽心模﹕
取模(用吊機將工模吊起) 裝好前咀運水及勾針運水 用鋼尺量好模具尺寸后 手動鎖模具前后機板尺寸是否與 工模尺寸吻合 (如尺寸達到)手動調模至工模尺寸 開 模 將工模放至機板中心位置 擺入前模對前機板 慢速 鎖模 檢查鎖模壓力是否達到700~~950bar范圍 開模 裝 前模絲杆 對上前機板絲吼推進定位 手動鎖模 開模距 離15mm 左右 手動合咀 射咀對正模具咀 慢度鎖模 對 至射咀吻合后高速鎖模 離咀 用紙放在模咀再合咀
压铸培训教材 ppt课件

PPT课件
19
注意(一):喷涂均匀,水分吹净,当有 水分时,铸出的转子端环、导条会产生缩 松。
注意(二):脱模剂必须规定勾兑(脱模 剂:水=1:80-120),否则容易造成端环疏 松,产生废品。
PPT课件
20
压铸浇口的选择
1)压铸浇口太短,容易造成铸件打不全,导 条缩松; 2)压铸浇口太长,容易顶不出浇口,损坏模 具;
PPT课件
27
压铸机应具有的操作程序
1.合模-(浇料)-压射-开模-顶出(复位) -(取件、清模、喷涂)-【适用于无抽芯器压铸
模】
2.动模抽芯器插芯-合模-(浇料)-压射-开 模-动模抽芯器抽芯-顶出(复位)-(取件、清
模、喷涂)-【适用于有动模抽芯器压铸模】
3.合模-动模抽芯器插芯-(浇料)-压射-开 模-动模抽芯器抽芯—顶出(复位)-(取件、清 模、喷涂)【适用于有动模抽芯器压铸模】
PPT课件
7
压铸过程 起始阶段:金属液开始浇入压室,准备压射。 第Ⅰ阶段:压射冲头慢速移动越过浇料口,金属液 受到冲头的推动 ,这种状况也是在起始压射阶段所 要求的。 第Ⅱ阶段:压射冲头以高于第Ⅰ阶段的速度向前运 动,此时金属液充满整个压室前端,聚集到内浇口 前沿之处,与这一阶段速度响应的压力上升(又称 为金属液堆积阶段)。 第Ⅲ阶段:从这一阶段开始,其压射压力由于受到 内浇口处阻力的影响升高,而此时的冲头速度将要 求达到调定的运动速度,以高速推动金属液通过内 浇口进入型腔,这种冲头速度通称为压射速度,而 这一阶段又称为填充阶段
压铸培训
工艺处
PPT课件
1
钱---------喜欢吗?
怎样赚钱? 怎样学会赚钱? 怎样学会赚更多的钱?
- 1、下载文档前请自行甄别文档内容的完整性,平台不提供额外的编辑、内容补充、找答案等附加服务。
- 2、"仅部分预览"的文档,不可在线预览部分如存在完整性等问题,可反馈申请退款(可完整预览的文档不适用该条件!)。
- 3、如文档侵犯您的权益,请联系客服反馈,我们会尽快为您处理(人工客服工作时间:9:00-18:30)。
压铸模具设计
浇注系统
金属液体在压铸过程中的充型状态是有压力速度、时间、温度、排气等因素综 合作用形成。因而浇注系统与压力传递,合金流速,填充时稳固时间,模具温度, 排气各条件有密切联系。一副有浇注系统良好的合金压铸模具会压铸出好的压铸毛 坯件,反之会产生缺陷。 根据有关资料介绍,压力和流量损失可以用阻力系数Cd来表示: a)无流动损失 Gd=1;
2、具有较好的导热性和抗热疲劳性;
3、高温下不易氧化,能抵抗液态金属的粘附和腐蚀; 4、材料热膨胀系数小,热处理变形小,淬透性良好。
二、常用压铸模钢材 国内:4Cr5M0SiV1 美国:H13 瑞典:8418 日本:SKD61
压铸零件缺陷
一、压铸件缺陷分析: 1、 缺陷分类: A、几何缺陷---压铸件形状,尺寸与技术要求偏离,尺寸偏差 变形等。 B、表面缺陷---压铸件外观不良,出现花纹、气泡、冷隔、毛 刺、拉伤、烧伤(冲蚀) C、内部缺陷---加工后出现气孔、缩孔。
3、GRRU大功率机箱示例说明: 塔放顶杆布置图
顶杆
模具材料
压铸模具的材料要求
一、在压铸循环中,由于高压金属液的强烈冲击与冲蚀作用,成型零件 (模腔、模芯、滑块等)容易损坏,损坏形式多为腐蚀,磨损,龟裂甚至开 裂,因此对成型零件的材料要求如下:
1、在高温下,具有较高的强度,硬度,抗回头的稳定性和热冲击韧度;
YL102、ADC12的化学成分(%)
Si硅
YL102 10.0~13.0
Cu铜
≤0.6
Mn锰
≤0.6
Mg镁
≤0.06
Fe铁
≤1.2
Ni镍
Zn锌
≤0.3
Sn锡
Pb铅
Al铝
其余
ADC12
9.6~12.0 1.5~3.3
0.5
0.3
1.3
0.5
1.0
0.2
其余
YL104
80.~10.5
≤0.3
0.2~0.5 0.17~0.30
变形
压铸件的几何形状与图纸不 符或局部变形
1、合理设备顶杆位置和数量; 2、适当调整开模时间; 3、检查局部位置,重新抛光。
花纹
铸件表面上有与金属液流动 方向一致的条纹 铸件表面上有米粒大小的凸 点,表皮下形成的空洞 压铸件表面有明显的不规则 下陷,呈线形纹路,形状细 小狭长。
提高金属液的温度,模具温度调整内 浇口截面积 调整模具的浇口,排气,溢流槽需增 强 提高浇注温度,模具温度,提高压射 力,压射速度,改进浇注系统,改善 排气。
铝合金压铸技术
讲师:钟谷成
2009年5月
铝合金压铸技术
目录
1
铝合金压铸材料介绍 压铸模具设计 模具材料 压铸零件缺陷
2
3 4
铝合金压铸材料介绍
铝合金压铸材料的应用(主要合金元素:铜、硅、镁、锌、锰)
目前,根据我们所认识在压铸行业中生产通讯行业里面的设备零件一般以铝 硅系合金、铝硅铜合金为主。 1、Al-Si系合金如YL102、YL103特点:流动性好,具有良好的铸造性能,适合于 压铸大型而复杂形状铸件,抗裂性、致密性、耐磨性、导热性好,热膨胀小。
谢 谢 !
气泡
冷隔
压铸零件缺陷
二、压铸件缺陷产生原因及解决方法:
缺陷名称 特征 产生原因 防止方法 模具出模斜度偏小,模具光洁度不够, 适当加大拔模斜度,模具重新抛光, 沿开模方向表面呈现出条状 拉伤 浇注温度,模温过高所致,残留的金属 调整浇注温度和模具温度,在下一个 的拉伤痕迹 液粘附 压铸前模腔要清理干净 适当降低压射速度,浇注温度加强冷 压铸件局部位置,特别是浇 烧伤(冲蚀) 由于内浇口处温度过高引起 却,改变浇注系统的方向,通过后加 口附近有麻点及花纹 工的打磨,喷砂处理 机加工后,铸件内部出现的 1、金属液在高速的充填过程卷入的气体 改进浇注系统,降低压射速度,减少 气孔 气孔,特征是光滑表面,圈 或模具的排气不善; 喷溅改善排气。 形成椭圆形 2、浇注系统设计不良 压铸件内部因收缩形成的孔 提高增压压力,改善浇注系统,防止 缩孔 凝固过程得不到金属液补偿 洞,形状不规则,不光滑 内浇口过早凝固,改善产品的结构。 注:合金浇注630℃-670℃温度,模具温度为浇注温度的1/3左右。
铝合金压铸材料介绍
合金元素的影响
硅(Si):提高流动性、补缩性、抗裂性能,但是随着含硅量增加,强度、硬 度增加,伸长率下降; 铜(Cu): 可提高机械性能,即切削性、研磨性,但是铜含量增加,热裂倾向增大; 镁(Mg): 1)当铝硅铜系合金含镁时,会降低伸长率,冲击值对镁含量严格控制; 2)提高耐蚀性,电镀; 铁(Fe): 铁能减少粘模倾向,易于压铸,铁含量在1.0 - 1.5%之间是有益的,低于0.7% 则铝合金液与模具易粘模,铁含量铁含量太多时,则会降低力学性能,切削性 能,耐蚀性能; 锰(Mn): 能提高耐蚀性和强度,过量也会硬化和脆性; 锌(Zn): 可提高流动性,改善力学性能; 注:近伸率:材料拉伸时,试样拉伸后,其标距部份所增加的长度与原标距长 度的百分比。
2)内浇口厚度尺寸要根据铸件的形状复杂式简单壁厚来选取; 3)塔放合路器的内浇口应设计在底部,目的是使金属液减短路径,减少压射 过程的卷气产生气孔。
压铸模具设计
冷却系统
由于金属液是高速、高温状态下进入模具型腔内,必然会对模具产生激烈的冲 击和冲刷,产生机械的力和热应力,在每一个压铸件的生产过程中,由于模具与金 属液之间的热交换使模具表面产生周期性温度变化,引起周期性的热膨胀和收缩, 产生周期性热应力,模温过高,易产生粘模,使用冷却温控系统,保证模具的工作 温度。 1)如机箱模具,双工器模具的内浇口处,由于金属液首先进入,如不设备冷却水道, 则由高温引起内浇口处粘模,甚至拉裂压铸件。 2)如果模具冷却不充分,会使压铸顶出过程产生凹痕。
2、 Al-Si-Cu系如YL112、YL113(日本牌号ADC12,美国牌号380)特点:此类 压铸铝合金使用最广泛,具有良好的综合性能(铸造性能、机械性能)。应用于 压铸汽车零件,如汽缸盖、泵、阀类;电子通讯设备零件(机箱、塔放、合路器 类);机械及电动工具类零件,尤其多用ADC12。
铝合金压铸材料介绍
压铸模具设计
辅助浇口
浇注系统
三款机箱及塔放浇口比较(扇形流道) 单浇口 40LGRRU机箱 双浇口
浇口
13L机箱
P165机箱 塔放
压铸模具设计
浇注系统
机箱小面板及反射腔 (锥形流道)
浇口
反射腔
浇口
机箱小面板
压铸模具设计
浇注系统
1)内浇口的设计对于机箱要设计在密封槽下3-4mm处,目的是避免高速温度高的铝 合金液冲击模具的凸台以至烧损坏; 铝液进口
油路冷却
油路冷却
压铸模具设计
顶出系统
目的是使顶杆布置平衡,使铸件顶出时受力均匀,变形程度减少。 1)对于塔放、合路器模具顶针的布置不能随意,因为会影响其信号。 2)对于机箱模具则要考虑顶针的数量,布局平衡,使压铸件出模顺畅,不致产生较 大的变形。(机箱要求的平面度0.2mm)
压铸模具设计
顶出系统
≤1.0
≤0.3
≤0.01
≤0.05
其余
铝合金压铸材料介绍
压铸性能及力学性能
铝合金力学性能
抗拉强度σ b/MPa YL102 ADC12 YL104 220 228 220
布氏硬度(HB) 60 74 70
注:①1MPa=0.1kgf/mm2 (千克/毫米2) ②抗拉强度:在单向拉伸载荷作用下,断裂时材料的最大负荷除以原始横 截面面积所得的应力。 ③用一定直径的淬硬钢球压入试样表面,并在规定载荷下保持一定时间以 其载荷除压痕面积的商表面材料的布氏硬度。
b)设计非常好的流道系统 Gd=0.8;
c)一般设计的流动系统 Gd=0.6; d)劣质差的流动系统 Gd=0.4-0.5;
可见,对于一般的流道系统,意味有40%能量损失在流道系统,具有60%的能量 是真正用来将金属液射入模腔内。
注:压射过程 第一阶段:低速射出0.2~0.5m/s,第二阶段:高速压射0.2~4.5m/s, 第三阶段:增压阶段
压铸零件缺陷
二、压铸件缺陷产生原因及解决方法:
缺陷名称 特征 产生原因 1、模具的顶杆设计布置不平衡及数量不 够; 2、开模时间过早,铸件未能定型引起刚 性不够; 3、或模具抛光不够,引起阻力增大顶出 变形。 首先进入模腔内的金属液形成极薄而又 不完全的金属层后被后来的金属液弥补 而留下的痕迹。 模具的排气不良,内浇口开设不良;金 属液凝固时间不够,过早顶出,受压气 体膨胀。 模腔内两股金属液相互不能融合为一 体,此外由于困气,在型腔最后充填部 位也会产生这种缺陷。 防止方法
压射比压:35~70Mpa
压铸模具设计时 , 有效面 积大。 2)设计简单,易于加工。 缺点: 1)当流动角度>90°时,流动 不稳定,易卷气。 2)流道体积大,耗金属量大。 锥形浇道: 优点: 1)流动稳定。 2)金属液的流动加快,有利于充填。 3)流道体积小,节省金属量。 4)适合长浇口,有利于薄壁件充填。