谈薄壁零件数控车工加工工艺.docx
薄壁零件的数控车削加工探讨
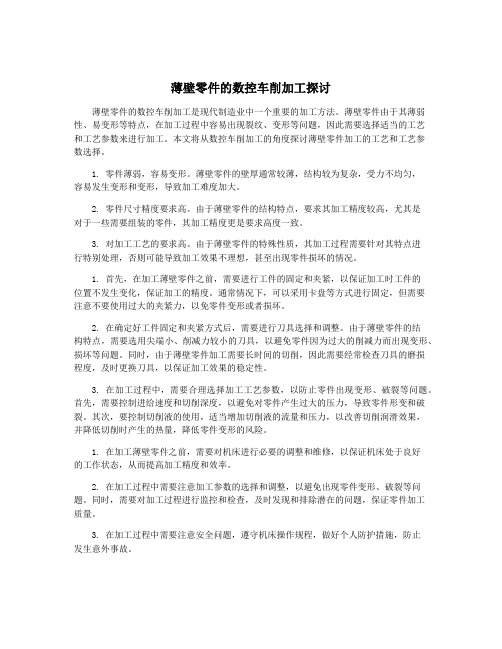
薄壁零件的数控车削加工探讨薄壁零件的数控车削加工是现代制造业中一个重要的加工方法。
薄壁零件由于其薄弱性、易变形等特点,在加工过程中容易出现裂纹、变形等问题,因此需要选择适当的工艺和工艺参数来进行加工。
本文将从数控车削加工的角度探讨薄壁零件加工的工艺和工艺参数选择。
1. 零件薄弱,容易变形。
薄壁零件的壁厚通常较薄,结构较为复杂,受力不均匀,容易发生变形和变形,导致加工难度加大。
2. 零件尺寸精度要求高。
由于薄壁零件的结构特点,要求其加工精度较高,尤其是对于一些需要组装的零件,其加工精度更是要求高度一致。
3. 对加工工艺的要求高。
由于薄壁零件的特殊性质,其加工过程需要针对其特点进行特别处理,否则可能导致加工效果不理想,甚至出现零件损坏的情况。
1. 首先,在加工薄壁零件之前,需要进行工件的固定和夹紧,以保证加工时工件的位置不发生变化,保证加工的精度。
通常情况下,可以采用卡盘等方式进行固定,但需要注意不要使用过大的夹紧力,以免零件变形或者损坏。
2. 在确定好工件固定和夹紧方式后,需要进行刀具选择和调整。
由于薄壁零件的结构特点,需要选用尖端小、削减力较小的刀具,以避免零件因为过大的削减力而出现变形、损坏等问题。
同时,由于薄壁零件加工需要长时间的切削,因此需要经常检查刀具的磨损程度,及时更换刀具,以保证加工效果的稳定性。
3. 在加工过程中,需要合理选择加工工艺参数,以防止零件出现变形、破裂等问题。
首先,需要控制进给速度和切削深度,以避免对零件产生过大的压力,导致零件形变和破裂。
其次,要控制切削液的使用,适当增加切削液的流量和压力,以改善切削润滑效果,并降低切削时产生的热量,降低零件变形的风险。
1. 在加工薄壁零件之前,需要对机床进行必要的调整和维修,以保证机床处于良好的工作状态,从而提高加工精度和效率。
2. 在加工过程中需要注意加工参数的选择和调整,以避免出现零件变形、破裂等问题。
同时,需要对加工过程进行监控和检查,及时发现和排除潜在的问题,保证零件加工质量。
浅谈薄壁零件数控车工加工工艺
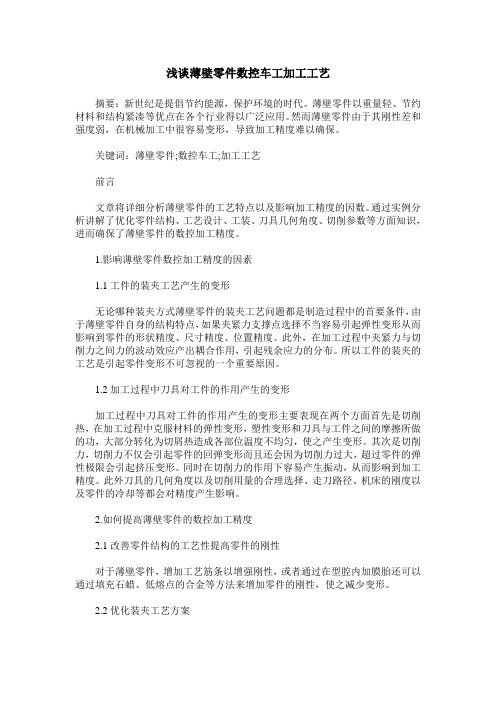
浅谈薄壁零件数控车工加工工艺摘要:新世纪是提倡节约能源,保护环境的时代。
薄壁零件以重量轻、节约材料和结构紧凑等优点在各个行业得以广泛应用。
然而薄壁零件由于其刚性差和强度弱,在机械加工中很容易变形,导致加工精度难以确保。
关键词:薄壁零件;数控车工;加工工艺前言文章将详细分析薄壁零件的工艺特点以及影响加工精度的因数。
通过实例分析讲解了优化零件结构、工艺设计、工装、刀具几何角度、切削参数等方面知识,进而确保了薄壁零件的数控加工精度。
1.影响薄壁零件数控加工精度的因素1.1工件的装夹工艺产生的变形无论哪种装夹方式薄壁零件的装夹工艺问题都是制造过程中的首要条件,由于薄壁零件自身的结构特点,如果夹紧力支撑点选择不当容易引起弹性变形从而影响到零件的形状精度、尺寸精度、位置精度。
此外,在加工过程中夹紧力与切削力之间力的波动效应产出耦合作用,引起残余应力的分布。
所以工件的装夹的工艺是引起零件变形不可忽视的一个重要原因。
1.2加工过程中刀具对工件的作用产生的变形加工过程中刀具对工件的作用产生的变形主要表现在两个方面首先是切削热,在加工过程中克服材料的弹性变形,塑性变形和刀具与工件之间的摩擦所做的功,大部分转化为切屑热造成各部位温度不均匀,使之产生变形。
其次是切削力,切削力不仅会引起零件的回弹变形而且还会因为切削力过大,超过零件的弹性极限会引起挤压变形。
同时在切削力的作用下容易产生振动,从而影响到加工精度。
此外刀具的几何角度以及切削用量的合理选择、走刀路径、机床的刚度以及零件的冷却等都会对精度产生影响。
2.如何提高薄壁零件的数控加工精度2.1改善零件结构的工艺性提高零件的刚性对于薄壁零件,增加工艺筋条以增强刚性,或者通过在型腔内加膜胎还可以通过填充石蜡、低熔点的合金等方法来增加零件的刚性,使之减少变形。
2.2优化装夹工艺方案不同的零件结构和加工方法对应不同的装夹工艺。
在已有的装夹工艺的基础上对其进行改进,优化设计是装夹工艺优化的基本方法。
论述薄壁零件的数控车削加工工艺
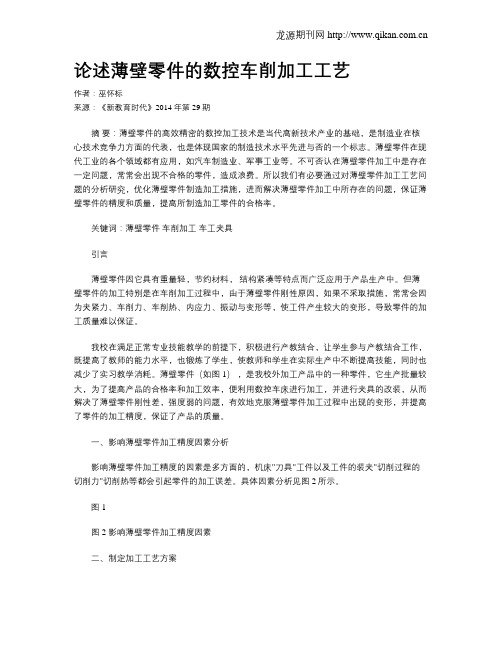
论述薄壁零件的数控车削加工工艺作者:巫怀标来源:《新教育时代》2014年第29期摘要:薄壁零件的高效精密的数控加工技术是当代高新技术产业的基础,是制造业在核心技术竞争力方面的代表,也是体现国家的制造技术水平先进与否的一个标志。
薄壁零件在现代工业的各个领域都有应用,如汽车制造业、军事工业等。
不可否认在薄壁零件加工中是存在一定问题,常常会出现不合格的零件,造成浪费。
所以我们有必要通过对薄壁零件加工工艺问题的分析研究,优化薄壁零件制造加工措施,进而解决薄壁零件加工中所存在的问题,保证薄壁零件的精度和质量,提高所制造加工零件的合格率。
关键词:薄壁零件车削加工车工夹具引言薄壁零件因它具有重量轻,节约材料,结构紧凑等特点而广泛应用于产品生产中。
但薄壁零件的加工特别是在车削加工过程中,由于薄壁零件刚性原因,如果不采取措施,常常会因为夹紧力、车削力、车削热、内应力、振动与变形等,使工件产生较大的变形,导致零件的加工质量难以保证。
我校在满足正常专业技能教学的前提下,积极进行产教结合,让学生参与产教结合工作,既提高了教师的能力水平,也锻炼了学生,使教师和学生在实际生产中不断提高技能,同时也减少了实习教学消耗。
薄壁零件(如图1),是我校外加工产品中的一种零件,它生产批量较大,为了提高产品的合格率和加工效率,便利用数控车床进行加工,并进行夹具的改装,从而解决了薄壁零件刚性差,强度弱的问题,有效地克服薄壁零件加工过程中出现的变形,并提高了零件的加工精度,保证了产品的质量。
一、影响薄壁零件加工精度因素分析影响薄壁零件加工精度的因素是多方面的,机床"刀具"工件以及工件的装夹"切削过程的切削力"切削热等都会引起零件的加工误差。
具体因素分析见图2所示。
图1图 2 影响薄壁零件加工精度因素二、制定加工工艺方案1.机床的选择。
根据零件的材料及零件的形状和精度要求,选用CAK6150Di FANUC Oi mate TC的数控车床。
数控车薄壁零件加工.doc

渤海船舶职业技术学院毕业设计渤海船舶职业技术学院毕业设计前言本课题是以薄壁零件“YX—168”为研究对象, 研究薄壁零件产品的加工工艺及工装设计。
“YX—168”是要加工生产的薄壁零件的名称。
薄壁零件具有体积小、重量轻、结构紧凑的特点,在许多产品中得到应用。
随着一些产品体积小型化,精密化,薄型零件的应用也越来越广泛,已经成为许多产品的关键性零件。
但是,由于薄壁零件壁薄,刚性差,加工时容易变形,不易保证加工质量,给该零件的机械加工造成困难,因而阻碍了产品设计和发展。
因此,薄壁零件的加工工艺已成为机械加工过程中必须解决的工艺问题。
采用什么样的加工工艺,才能保证薄壁零件的精度呢?“YX—168”薄壁零件的生产批量大,而且零件壁厚仅0.75mm,加工精度要求也比较高,以往在普通车床上加工就很难达到零件的技术要求,而且生产效率低,不能适应大批量加工的要求。
因此,研究薄壁零件的加工工艺,对于保证产品质量具有重要意义。
根据“YX—168”薄壁零件的工艺特征,通过理论分析和试验确定一种利用数控车床加工该零件的合理的工艺方法,并设计其专用工装夹具。
经过多次试验,我们采用的这种在数控机床上加工的工艺方法和设计的专用工装夹具,较好地解决薄壁零件的加工问题,。
由于数控车床按照预定的加工程序自动加工,加工过程中避免了由于操作人员造成的人为误差,提高了零件加工精度的一致性,对于保证产品质量的稳定起到重要作用。
而数控车削技术的应用,极大的提高了生产效率。
同时,由于设计和采用了专用的夹具,解决了零件薄壁易变形,加工性能差的难题。
本设计的意义在于,通过对“YX—168”薄壁零件加工工艺以及工装夹具的设计,总结利用数控技术和专用夹具加工薄壁零件的经验,并从理论上加以分析和提高,给制造薄壁零件加工工艺提供依据。
- II -渤海船舶职业技术学院毕业设计薄壁零件的加工问题,一直是较难解决的。
薄壁件目前一般采用数控车削的方式进行加工,为此要对工件的装夹、刀具几何参数、程序的编制等方面进行试验,从而有效地克服了薄壁零件加工过程中出现的变形,保证加工精度。
试论薄壁零件数控车工的加工工艺

试论薄壁零件数控车工的加工工艺数控加工技术是当代高新技术产业,薄壁零件则是该技术的基础。
其本身就具有的重量轻,结构密,材料省等优点,但随着科技的发展,人们对数控加工和薄壁零件都有了更高的精度要求,再加上薄壁零件在加工生产中常出现切削振动,变形等质量问题还尚未得到很好的解决,于是我们不得不思考如何去改进提高薄壁零件数控车工的加工工艺。
文章的立足点就在于此,对其展开进行论述。
标签:薄壁零件;数控车工;加工工艺薄壁零件的精度和质量在数控加工工艺中的重要性可想而知,不仅是产品核心竞争力的代表,更是决定了能否体现国家的加工水平先进与否的重要因素。
而在加工薄壁零件时常会因为不合格造成浪费,再加上薄壁零件的需求量大,自动化批量生产时所产生的错误都会导致产品的不合格,因此改进对薄壁零件的加工工艺刻不容缓。
1 影响薄壁零件数控车工加工的因素薄壁零件,就是壁厚在1mm以下的金属材料的零件。
因为其刚性差,强度弱的特点在生产加工时容易变形这对于质量要求是致命的,这一直是薄壁零件在数控车工加工工艺的一个瓶颈。
下面我们详细分析下都有哪些具体因素。
1.1 受热变形在高负荷的工作强度下数控车常年受热,薄壁零件在切削时或多或少会因此而变形,导致零件加工精度下降质量不合格。
换一种方式说,这种类型的误差是不可避免的,因为在数控车运行精车、半精车或粗工加工程序时必然会产生切削热,而零件特别是薄壁零件必然会因受热发生变形。
而冷却性好的切削润滑液暂时能轻微减小此类影响。
1.2 受力变形由于薄壁零件要达到重量轻的特点,它的加工材料得比较轻薄,这就使这类材料受到某些外力作用时会出现一定程度的变形,导致质量不过关。
同样这样的因素是无法避免,零件在数控车的夹紧力和切削力的作用下,这两者之间相互作用产生波动效应。
1.3 振动变形通常,受力都会引起振动。
零件加工也一样,因受到切削力的作用而产生的振动对零件的外形、精度、表面粗糙度都有一定的影响,其中径向切削力的影响尤其大。
数控车床薄壁零件的加工-精品文档资料
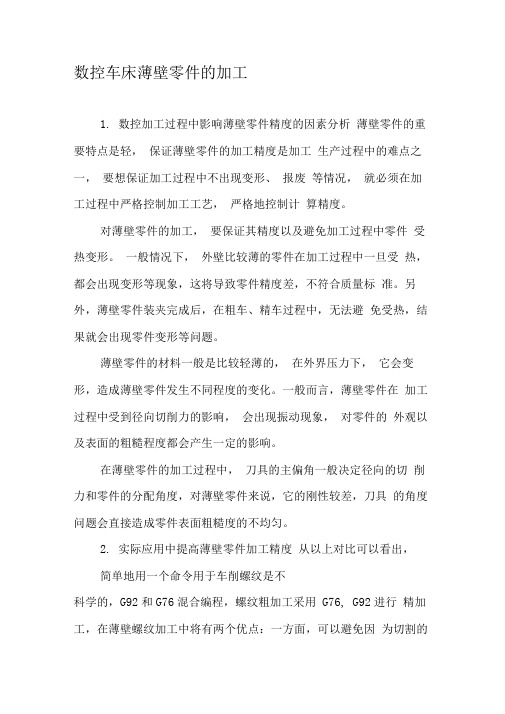
数控车床薄壁零件的加工1. 数控加工过程中影响薄壁零件精度的因素分析薄壁零件的重要特点是轻,保证薄壁零件的加工精度是加工生产过程中的难点之一,要想保证加工过程中不出现变形、报废等情况,就必须在加工过程中严格控制加工工艺,严格地控制计算精度。
对薄壁零件的加工,要保证其精度以及避免加工过程中零件受热变形。
一般情况下,外壁比较薄的零件在加工过程中一旦受热,都会出现变形等现象,这将导致零件精度差,不符合质量标准。
另外,薄壁零件装夹完成后,在粗车、精车过程中,无法避免受热,结果就会出现零件变形等问题。
薄壁零件的材料一般是比较轻薄的,在外界压力下,它会变形,造成薄壁零件发生不同程度的变化。
一般而言,薄壁零件在加工过程中受到径向切削力的影响,会出现振动现象,对零件的外观以及表面的粗糙程度都会产生一定的影响。
在薄壁零件的加工过程中,刀具的主偏角一般决定径向的切削力和零件的分配角度,对薄壁零件来说,它的刚性较差,刀具的角度问题会直接造成零件表面粗糙度的不均匀。
2. 实际应用中提高薄壁零件加工精度从以上对比可以看出,简单地用一个命令用于车削螺纹是不科学的,G92和G76混合编程,螺纹粗加工采用G76, G92进行精加工,在薄壁螺纹加工中将有两个优点:一方面,可以避免因为切割的薄壁零件的变形量;另一方面,可以保证螺纹加工精度。
(2)优化夹具设计。
由于工件薄、刚性差,如果采用常规的方法对工件进行装夹和切削加工,将受到轴向切削力和热变形的影响,工件变形,则很难满足技术要求。
因此,有必要设计一套适合上述零件的专用夹具。
(3)合理选择刀具。
①内镗孔刀采用机夹刀,刀具更换时间缩短,不用刃磨工具,具有良好的刚度,可减少振动变形,防止产生振动痕。
②外圆粗、精车均选用硬质合金90°车刀。
③螺纹刀选用机夹刀,尖端角度标准,耐磨,易更换。
(4)切削用量。
①内孔粗车时,主轴转速每分钟500〜600 转,进给速度F0.2〜F0.25,留精车余量0.2〜0.3mm②内孔精车时,主轴转速每分钟1100〜1200转,为了获得更好的表面粗糙度,进给速度F0.1〜F0.15,采用一次走刀加工完成。
薄壁零件的数控车削加工探讨

薄壁零件的数控车削加工探讨随着工业的不断发展,薄壁零件在机械制造领域中的应用越来越广泛。
薄壁零件因其结构轻巧、重量小、强度高等特点,被广泛应用于汽车、航空航天、电子等领域。
薄壁零件的加工却是一项技术难题,尤其是数控车削加工对薄壁零件的加工要求更加严格。
本文将探讨薄壁零件的数控车削加工技术,并就其加工过程中的难点和解决方法进行深入探讨。
一、薄壁零件的特点薄壁零件在机械制造中具有独特的优势,主要表现在以下几个方面:1. 结构轻巧:薄壁零件由于壁厚较薄,因此重量相对较轻,适合在一些对重量要求较高的场合使用,比如汽车、航空航天等领域。
2. 外形复杂:薄壁零件的结构通常比较复杂,需要经过多道工序的加工才能完成,对加工工艺要求较高。
3. 强度高:尽管薄壁零件壁厚较薄,但是由于采用了特殊的材料和工艺,使得薄壁零件具有比较高的强度,能够满足工程应用的需要。
由于薄壁零件的特点,使得其在加工过程中存在一定的难度和挑战,尤其是在数控车削加工过程中更加明显。
二、数控车削加工对薄壁零件的要求数控车床是一种通过计算机程序控制刀具在数控车床上进行切削加工的设备,其具有高速度、高精度、高效率的特点,因此被广泛应用于薄壁零件的加工中。
由于薄壁零件的特殊性,数控车削加工对薄壁零件有着更高的要求。
1. 加工精度要求高:薄壁零件通常具有复杂的结构和精密的尺寸要求,因此数控车削加工需要保证加工精度,避免零件出现尺寸偏差和表面粗糙度。
2. 避免变形和残余应力:薄壁零件在加工过程中容易发生热变形和残余应力,因此在数控车削加工过程中需要采取有效的措施,避免零件变形和应力积累。
3. 提高加工效率:薄壁零件的加工通常需要多道工序,加工过程中需要保证高效率,提高生产效率。
在薄壁零件的数控车削加工过程中,存在一些难点需要克服:1. 大刚度:由于薄壁零件的壁厚较薄,零件的刚度相对较小,容易导致变形和振动,影响加工精度和表面质量。
2. 刀具选择:薄壁零件具有一定的脆性,因此刀具的选择对加工质量有着重要影响,需要选择合适的刀具以提高加工质量。
薄壁零件的数控车削加工探讨
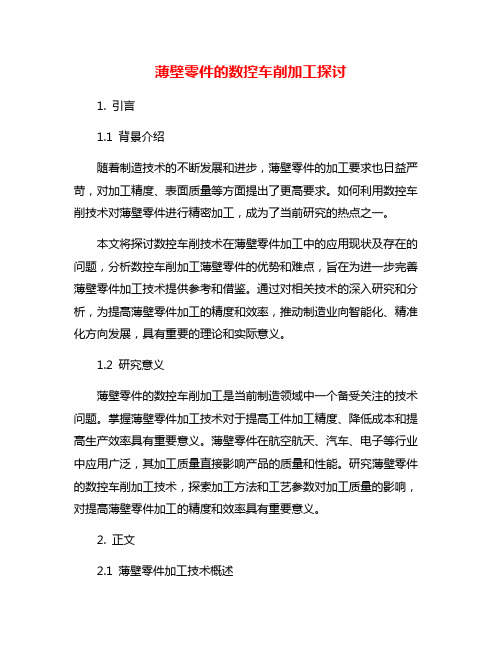
薄壁零件的数控车削加工探讨1. 引言1.1 背景介绍随着制造技术的不断发展和进步,薄壁零件的加工要求也日益严苛,对加工精度、表面质量等方面提出了更高要求。
如何利用数控车削技术对薄壁零件进行精密加工,成为了当前研究的热点之一。
本文将探讨数控车削技术在薄壁零件加工中的应用现状及存在的问题,分析数控车削加工薄壁零件的优势和难点,旨在为进一步完善薄壁零件加工技术提供参考和借鉴。
通过对相关技术的深入研究和分析,为提高薄壁零件加工的精度和效率,推动制造业向智能化、精准化方向发展,具有重要的理论和实际意义。
1.2 研究意义薄壁零件的数控车削加工是当前制造领域中一个备受关注的技术问题。
掌握薄壁零件加工技术对于提高工件加工精度、降低成本和提高生产效率具有重要意义。
薄壁零件在航空航天、汽车、电子等行业中应用广泛,其加工质量直接影响产品的质量和性能。
研究薄壁零件的数控车削加工技术,探索加工方法和工艺参数对加工质量的影响,对提高薄壁零件加工的精度和效率具有重要意义。
2. 正文2.1 薄壁零件加工技术概述薄壁零件是指壁厚较薄的零件,通常在汽车、航空航天等领域中广泛应用。
薄壁零件的加工技术在制造业中起着至关重要的作用。
在薄壁零件的加工中,最主要的挑战之一是加工过程中如何保持零件的形状和尺寸精度。
因为薄壁零件的壁厚较薄,加工过程中很容易产生变形,从而影响零件的质量和使用效果。
为了解决这一问题,可以通过调整加工参数、优化刀具选择和加工路径等方式来降低零件变形的可能性。
薄壁零件的加工还需要考虑到表面质量和加工效率的问题。
薄壁零件通常具有较高的表面要求,因此在加工过程中需要采用合适的刀具和加工策略来保证零件表面的光洁度和精度。
为了提高加工效率,可以通过提高切削速度、加工进给速度等方式来缩短加工周期。
薄壁零件的加工技术在现代制造业中具有重要意义,通过不断优化加工工艺和加工方法,可以更好地满足市场需求,提高产品质量和效率。
2.2 薄壁零件加工存在的问题1. 刀具选择困难:薄壁零件通常由软性材料制成,而软性材料容易产生振动和变形,因此在选择合适的刀具时需要考虑刀具的刚度和稳定性,以避免对薄壁零件造成损伤。
薄壁零件数控车工加工工艺

薄壁零件数控车工加工工艺随着科学技术的进步,经济的飞速发展,在工业生产中薄壁零件的应用范围正在不断的扩大,薄壁零件具有轻重量、密结构、节约材料等优点,但也不可忽略薄壁零件刚性不够、强度比较弱的特点,使它在加工生产中容易出现切削振动、加工变形等问题,使其加工质量难以保证。
本文将对影响薄壁零件精度因素进行分析,对薄壁零件的加工工艺进行简要的探讨,旨在提高薄壁零件的加工技术,进而提高生产效率。
标签:薄壁零件;数控;加工工艺薄壁零件的高效精密的数控加工技术是当代高新技术产业的基础,是制造业在核心技术竞争力方面的代表,也是体现国家的制造技术水平先进与否的一个标志。
薄壁零件在现代工业的各个领域都有应用,如汽车制造业、军事工业等。
不可否认在薄壁零件加工中是存在一定问题,常常会出现不合格的零件,造成浪费。
所以我们有必要通过对薄壁零件加工工艺问题的分析研究,优化薄壁零件制造加工措施,进而解决薄壁零件加工中所存在的问题,保证薄壁零件的精度和质量,提高所制造加工零件的合格率。
1 薄壁零件概述薄壁零件顾名思义,其显著特点就是壁薄,同时它还存在着强度差与抗变形能力低的特点。
加工过程中的表面硬化、颤振、热力、切削等因素都关系到薄壁零件的变形与否。
数控加工的过程可分为三部分,即设计与编程、加工与监控和成品检验三阶段。
对薄壁零件加工来说,突出问题就是零件变形不易控制。
这也说明薄壁零件的加工对加工技术、装夹方式、切割刀具及切割工艺都有着极高的要求。
2 影响薄壁零件数控加工精度的因素分析薄壁零件具有轻量化的动态性能,不过保障薄壁零件的加工精度却是工业生产的一个瓶颈,薄壁零件在数控加工过程中容易变形、损坏。
想要提高薄壁零件加工的精度就需要对影响其精度的因素进行研究。
对薄壁零件数控加工过程中易出现变形,影响零件精度的因素进行分析后,得出存在以下几种主要影响因素。
2.1 热因素导致薄壁零件变形。
通常情况下,比较薄的零件加工过程中受到切削热的作用时,都会不同程度产生热变形现象,导致零件的加工精度下降以及质量不合格等。
浅谈薄壁零件数控车加工工艺分析

浅谈薄壁零件数控车加工工艺分析摘要:伴随着我国科技技术与经济水平的飞速发展,很多行业也都在此背景下发展起来。
在零件质量和加工工艺方面,社会对其有了更高的要求。
在计算机技术的不断革新下,数控技术得到了飞速的发展。
基于这一点,薄壁零件的生产与应用得到了很大的发展。
但是,目前国内外对其加工工艺的研究还不够深入,加工质量很难保证。
在此基础上,文章重点对薄壁零件数控车工加工工艺进行了研究。
关键词:薄壁零件;数控车加工;加工工艺;改进措施1.薄壁零件的概念薄壁零件主要是通过现代数控车床工艺,使零件的内壁和外壁变薄,以达到节省材料的目的。
薄壁零件由于具有良好的机械性能而被广泛应用于航空航天、军事和机械等诸多领域。
在加工薄壁零件时,对加工精度的要求越来越高,而加工时产生的变形会严重地影响产品的质量与生产效率。
所以,对于薄壁零件,必须采用比较严格的工艺,才能确保其质量及合格率。
2.薄壁零件数控车加工工艺质量的影响因素2.1刀具角度对切削量的影响实验结果表明,当机床机构及刀具几何参数一定时,切削力的大小受到切削速度、进给速度和反向进给等因素的影响。
刀具角度是影响加工质量的重要因素。
在切削时,适当增大刀具前角和后角,可有效减小切削变形、降低摩擦、弱化切削作用力,使切削变形达到最大程度。
此外,主偏角和副偏角对切削精度的影响也很大。
在切削时,副偏角对刀具轴向和径向力均有影响。
对于刚性较差的零件,主偏角应尽量接近90度,这样才能提高零件的数控加工强度和加工精度。
2.2走刀方式与路径的影响刀具的走刀方式与路径对零件的数控车加工也有很大的影响,改进刀具的走刀方式与路径,可以有效地提高零件的数控车加工精度。
通过对走刀轨迹及走刀方式的优化,可使工件质量得到明显提高。
其中,一次粗加工法和阶梯粗加工法是一种新的、高效的零件粗加工工艺。
两种方法均沿高线轨迹,并以等量的切削量为切入点。
它克服了常规刀具路径在斜向上加工时存在的缺陷。
此时,刀具沿高线X和 Z两条高线水平运动,将多余的刀具去除,保证了刀具切削过程中均匀地切削多余的金属、延长了刀具的使用寿命,提高了加工质量。
薄壁零件数控车工加工工艺的探讨
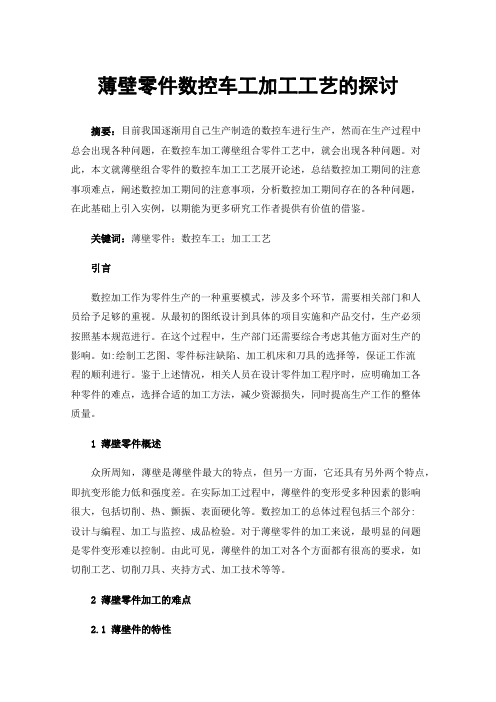
薄壁零件数控车工加工工艺的探讨摘要:目前我国逐渐用自己生产制造的数控车进行生产,然而在生产过程中总会出现各种问题,在数控车加工薄壁组合零件工艺中,就会出现各种问题。
对此,本文就薄壁组合零件的数控车加工工艺展开论述,总结数控加工期间的注意事项难点,阐述数控加工期间的注意事项,分析数控加工期间存在的各种问题,在此基础上引入实例,以期能为更多研究工作者提供有价值的借鉴。
关键词:薄壁零件;数控车工;加工工艺引言数控加工作为零件生产的一种重要模式,涉及多个环节,需要相关部门和人员给予足够的重视。
从最初的图纸设计到具体的项目实施和产品交付,生产必须按照基本规范进行。
在这个过程中,生产部门还需要综合考虑其他方面对生产的影响。
如:绘制工艺图、零件标注缺陷、加工机床和刀具的选择等,保证工作流程的顺利进行。
鉴于上述情况,相关人员在设计零件加工程序时,应明确加工各种零件的难点,选择合适的加工方法,减少资源损失,同时提高生产工作的整体质量。
1薄壁零件概述众所周知,薄壁是薄壁件最大的特点,但另一方面,它还具有另外两个特点,即抗变形能力低和强度差。
在实际加工过程中,薄壁件的变形受多种因素的影响很大,包括切削、热、颤振、表面硬化等。
数控加工的总体过程包括三个部分:设计与编程、加工与监控、成品检验。
对于薄壁零件的加工来说,最明显的问题是零件变形难以控制。
由此可见,薄壁件的加工对各个方面都有很高的要求,如切削工艺、切削刀具、夹持方式、加工技术等等。
2薄壁零件加工的难点2.1薄壁件的特性与一般零件相比,薄壁组合零件具有零件轻、省资源等特点,在各个领域均有体现。
但在实际加工时,薄壁组合零件具有不稳定、易变性等特性,而这也是加工过程应注重的问题。
从其结构来看,薄壁组合零件硬度低,易受压力、温度等因素影响而产生形变,既会影响零件整体尺寸,也会降低其在机械设备中的具体运行情况,进而造成不必要的损失。
2.2刀具的选择薄壁组合零件加工的另一个难点在于刀具的选择。
薄壁套类零件数控车削加工工艺分析

薄壁套类零件数控车削加工工艺分析1.北方工具有限公司劳服牡丹江市链条厂,黑龙江牡丹江,1570002.2.黑龙江北方工具有限公司,黑龙江牡丹江,1570003.3.黑龙江北方工具有限公司,黑龙江牡丹江,157000摘要:随着加工制造业的发展,薄壁类零件的应用范围越来越广泛,技术要求越来越高。
但是在薄壁套类零件的数控车削加工中还存在很多问题,影响到了加工的效率以及零件的质量,因此需要不断改进数控车削加工工艺,提高加工质量,本文将对薄壁套类零件数控车削加工工艺进行简要分析。
关键词:薄壁套类零件;数控车削加工;工艺分析一、薄壁套类零件概述薄壁套类零件有着径向刚度差、外圆及内孔有着不规则变形导致壁厚不均匀、圆度不易控制等特点。
套类零件在机械结构中主要起支撑和导向作用,为此零件需具有较高的同轴度,端面与孔轴线或与外圆有较高的垂直度要求,除了尺寸的精度要求外还对零件的几何形状精度、表面粗糙度也要求较高。
在数控车削加工中急需解决的问题是控制零件装夹变形以及车削变形。
二、薄壁套类零件加工质量的影响因素1.夹紧力对加工质量的影响:零件加工对装夹刚度有较高的要求,如果零件装夹的力度过小不仅会造成脱夹导致零件的报废,甚至会引发安全事故。
2.工件材料的状态对切削力的影响:材料的状态会直接影响到切削力大小,随着材料硬度、强度增高切削力增大[1],同时还会涉及到加工硬化等问题,加工硬化不仅会使材料产生变形还会给材料的进一步加工带来困难。
3.刀具角度对工件的影响:前角大时,切削变形量和摩擦力减小,切削力减小,表面粗糙度好;前角过大,刀具楔角减小,刀具强度降低,散热能力差,磨损速度快,刀具使用寿命降低;后角大,与工件切削表面间隙大,摩擦力小,切削力也相应的减小;后角过大,会形成刀具刃部变薄,强度不足,磨损速度快,刀具使用寿命降低[2]。
4.吃刀量与进给速度对切削力的影响:背吃刀量与切削速度对切削力的交互影响当背吃刀量为常数时,切削速度增大时,切削力变化的幅度不是很大;而当切削速度为常数时,背吃刀量增大,切削力增大较明显[3]。
薄壁零件数控车工加工工艺研究
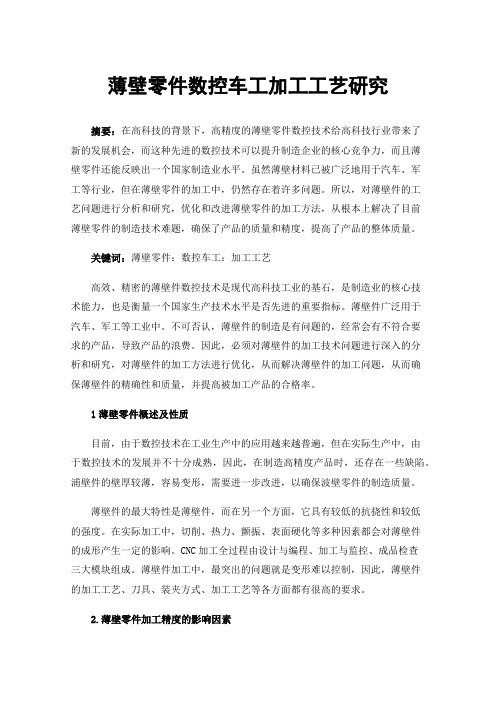
薄壁零件数控车工加工工艺研究摘要:在高科技的背景下,高精度的薄壁零件数控技术给高科技行业带来了新的发展机会,而这种先进的数控技术可以提升制造企业的核心竞争力,而且薄壁零件还能反映出一个国家制造业水平。
虽然薄壁材料已被广泛地用于汽车、军工等行业,但在薄壁零件的加工中,仍然存在着许多问题。
所以,对薄壁件的工艺问题进行分析和研究,优化和改进薄壁零件的加工方法,从根本上解决了目前薄壁零件的制造技术难题,确保了产品的质量和精度,提高了产品的整体质量。
关键词:薄壁零件:数控车工:加工工艺高效、精密的薄壁件数控技术是现代高科技工业的基石,是制造业的核心技术能力,也是衡量一个国家生产技术水平是否先进的重要指标。
薄壁件广泛用于汽车、军工等工业中。
不可否认,薄壁件的制造是有问题的,经常会有不符合要求的产品,导致产品的浪费。
因此,必须对薄壁件的加工技术问题进行深入的分析和研究,对薄壁件的加工方法进行优化,从而解决薄壁件的加工问题,从而确保薄壁件的精确性和质量,并提高被加工产品的合格率。
1薄壁零件概述及性质目前,由于数控技术在工业生产中的应用越来越普遍,但在实际生产中,由于数控技术的发展并不十分成熟,因此,在制造高精度产品时,还存在一些缺陷。
浦壁件的壁厚较薄,容易变形,需要进一步改进,以确保波壁零件的制造质量。
薄壁件的最大特性是薄壁件,而在另一个方面,它具有较低的抗挠性和较低的强度。
在实际加工中,切削、热力、颤振、表面硬化等多种因素都会对薄壁件的成形产生一定的影响。
CNC加工全过程由设计与编程、加工与监控、成品检查三大模块组成。
薄壁件加工中,最突出的问题就是变形难以控制,因此,薄壁件的加工工艺、刀具、装夹方式、加工工艺等各方面都有很高的要求。
2.薄壁零件加工精度的影响因素2.1薄壁零件本身的因素通过分析发现,由于材料和结构的原因,薄壁件的材料和结构会影响到产品的性能,而材料和结构的性能不好,则会对产品的性能造成不利的影响。
简述薄壁类零件数控加工工艺改进

0引言薄壁类零件具有重量轻等多种优势,应用范围十分广泛,但是薄壁类零件的刚性以及强度都比较差,在加工过程中容易出现变形等情况,因此应该优化薄壁类零件数控加工工艺,提高零件的质量。
1薄壁类零件概述薄壁类零件指的是壁厚小于1mm的金属零件,在工业生产中发挥着重要作用。
薄壁类零件具有重量轻、节约材料等特点,而且整体结构较为紧凑,所以薄壁类零件的用途比较多。
但是,薄壁类零件也具有一定的缺陷,比如说刚性比较差,强度比较弱,在加工时很容易出现变形等情况,对零件加工质量造成了严重影响,因此只有不断改进薄壁类零件数控加工工艺才能够提高零件的质量[1]。
2薄壁类零件的数控加工阶段薄壁类零件的数控加工可分为三个阶段,主要包括粗加工阶段、半精加工阶段以及精加工阶段。
①粗加工阶段:主要是对薄壁类零件进行简易加工,需要根据零件的具体类型以及特点选择合适的加工工艺,比如说可以利用粗车外圆等工艺进行薄壁套的加工[2]。
②半精加工阶段:半精加工阶段主要是对薄壁零件的次要表面进行处理,从而保障薄壁零件次要表面的精度能够达到要求。
在加工完次要表面之后需要将薄壁零件的多余部分清除掉,以提高薄壁零件的质量和精度。
③精加工阶段:精加工主要是利用精车零件外圆这种方式对薄壁零件进行细加工,使薄壁零件的精度能够完全符合要求。
3薄壁类零件数控加工工艺的影响因素3.1零件装夹零件装夹在薄壁类零件中发挥着重要作用,如果零件———————————————————————作者简介:汪丽娟(1980-),女,河北唐山人,本科,石家庄盛华企业集团,助理工程师,研究方向为高端精密铸造加工工艺;魏领波(1982-),男,河北石家庄人,本科,河北太行机械工业有限公司,高级工程师,研究方向为数控加工工艺。
气保护焊接技术从电弧中获得热源,最为明显的特点则是使用气体对焊接物进行保护,利用焊接工艺在实际焊接中,电弧周边会产生一层气体保护层,将电弧、空气及熔池进行全面分割,避免气体对焊接质量产生影响。
薄壁零件运用数控技术的加工
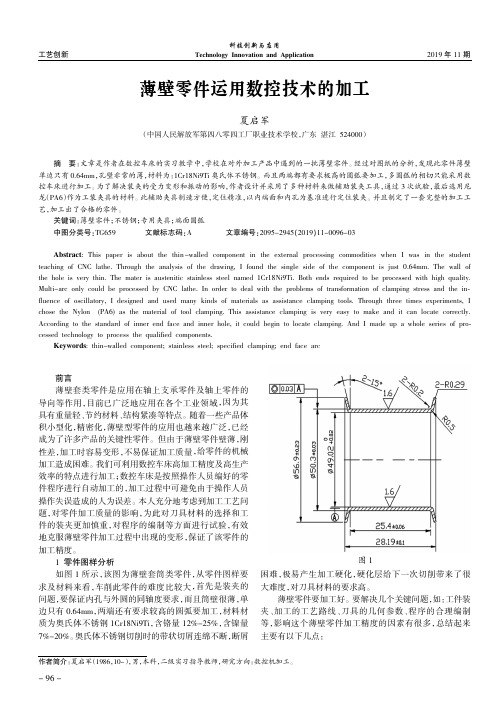
2019年11期工艺创新科技创新与应用Technology Innovation and Application薄壁零件运用数控技术的加工夏启军(中国人民解放军第四八零四工厂职业技术学校,广东湛江524000)前言薄壁套类零件是应用在轴上支承零件及轴上零件的导向等作用,目前已广泛地应用在各个工业领域,因为其具有重量轻、节约材料、结构紧凑等特点。
随着一些产品体积小型化,精密化,薄壁型零件的应用也越来越广泛,已经成为了许多产品的关键性零件。
但由于薄壁零件壁薄,刚性差,加工时容易变形,不易保证加工质量,给零件的机械加工造成困难。
我们可利用数控车床高加工精度及高生产效率的特点进行加工;数控车床是按照操作人员编好的零件程序进行自动加工的,加工过程中可避免由于操作人员操作失误造成的人为误差。
本人充分地考虑到加工工艺问题,对零件加工质量的影响,为此对刀具材料的选择和工件的装夹更加慎重,对程序的编制等方面进行试验,有效地克服薄壁零件加工过程中出现的变形,保证了该零件的加工精度。
1零件图样分析如图1所示,该图为薄壁套筒类零件,从零件图样要求及材料来看,车削此零件的难度比较大,首先是装夹的问题,要保证内孔与外圆的同轴度要求,而且筒壁很薄,单边只有0.64mm ,两端还有要求较高的圆弧要加工,材料材质为奥氏体不锈钢1Cr18Ni9Ti ,含铬量12%-25%,含镍量7%-20%。
奥氏体不锈钢切削时的带状切屑连绵不断,断屑困难,极易产生加工硬化,硬化层给下一次切削带来了很大难度,对刀具材料的要求高。
薄壁零件要加工好。
要解决几个关键问题,如:工件装夹、加工的工艺路线、刀具的几何参数、程序的合理编制等,影响这个薄壁零件加工精度的因素有很多,总结起来主要有以下几点:摘要:文章是作者在数控车床的实习教学中,学校在对外加工产品中遇到的一批薄壁零件。
经过对图纸的分析,发现此零件薄壁单边只有0.64mm ,孔壁非常的薄,材料为:1Cr18Ni9Ti 奥氏体不锈钢。
薄壁零件的数控车削加工探讨

薄壁零件的数控车削加工探讨一、薄壁零件在数控车削加工中的问题1. 变形问题:薄壁零件在数控车削加工中容易受到刀具切削力的影响,从而产生变形。
尤其是在加工过程中,由于热变形效应的存在,薄壁零件更容易出现变形现象。
变形不仅会影响零件的尺寸精度和几何形状,还会降低零件的使用寿命和性能。
2. 振动问题:由于薄壁零件的结构特点,容易受到切削力的作用而产生振动现象。
振动不仅会影响加工质量,还会加剧刀具磨损、降低加工精度、影响加工表面质量等问题。
3. 切屑问题:薄壁零件在数控车削加工中,由于切削力的作用,容易产生大量的切屑,而这些切屑往往会对加工表面造成损坏,同时也会对工件和刀具造成损伤。
以上问题对薄壁零件的加工质量和加工效率都会产生较大的影响。
如何解决这些问题,提高薄壁零件的加工质量和效率,是当前数控车削加工中的一个重要课题。
二、解决问题的方法和技术1. 刀具选择和切削参数的优化:在数控车削加工中,合理选择刀具和优化切削参数对薄壁零件的加工具有重要意义。
选择合适的刀具材料和刀具几何形状对降低切削力、延长刀具使用寿命非常重要。
通过优化切削速度、进给量、切削深度等切削参数,可以有效地减少切削力、降低振动,从而保证薄壁零件的加工质量。
2. 支撑技术:薄壁零件在数控车削加工中,可以采用支撑技术来减少变形和振动。
支撑技术可以通过在零件上设置支撑点、改变切削路线等方式,有效地提高零件的刚度和稳定性,减少变形和振动。
可以在薄壁零件的内部设置支撑件,以增加结构的刚性,减少振动和变形。
3. 刀轴倾角补偿技术:在数控车削加工中,刀轴倾角对薄壁零件的加工具有重要影响。
合理地设置刀轴倾角可以有效地减少切削力和振动,避免因为切削力对零件产生的变形。
通过刀轴倾角补偿技术,可以实现对零件的精密加工,提高加工质量。
4. 加工路径优化技术:在数控车削加工中,通过优化加工路径,可以减少切屑对加工表面的损害,同时也可以减少切削力和振动。
在薄壁零件的加工中,通过合理设置加工路径和切削方向,可以减少切屑的产生,提高加工表面的光洁度和平整度。
薄壁零件的数控车削加工探讨
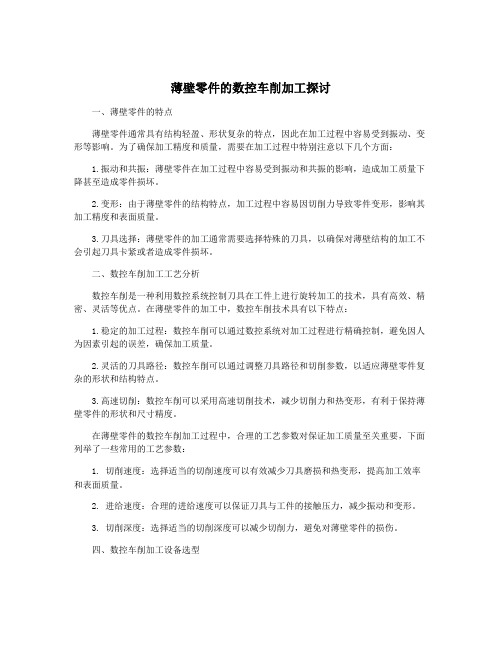
薄壁零件的数控车削加工探讨一、薄壁零件的特点薄壁零件通常具有结构轻盈、形状复杂的特点,因此在加工过程中容易受到振动、变形等影响。
为了确保加工精度和质量,需要在加工过程中特别注意以下几个方面:1.振动和共振:薄壁零件在加工过程中容易受到振动和共振的影响,造成加工质量下降甚至造成零件损坏。
2.变形:由于薄壁零件的结构特点,加工过程中容易因切削力导致零件变形,影响其加工精度和表面质量。
3.刀具选择:薄壁零件的加工通常需要选择特殊的刀具,以确保对薄壁结构的加工不会引起刀具卡紧或者造成零件损坏。
二、数控车削加工工艺分析数控车削是一种利用数控系统控制刀具在工件上进行旋转加工的技术,具有高效、精密、灵活等优点。
在薄壁零件的加工中,数控车削技术具有以下特点:1.稳定的加工过程:数控车削可以通过数控系统对加工过程进行精确控制,避免因人为因素引起的误差,确保加工质量。
2.灵活的刀具路径:数控车削可以通过调整刀具路径和切削参数,以适应薄壁零件复杂的形状和结构特点。
3.高速切削:数控车削可以采用高速切削技术,减少切削力和热变形,有利于保持薄壁零件的形状和尺寸精度。
在薄壁零件的数控车削加工过程中,合理的工艺参数对保证加工质量至关重要,下面列举了一些常用的工艺参数:1. 切削速度:选择适当的切削速度可以有效减少刀具磨损和热变形,提高加工效率和表面质量。
2. 进给速度:合理的进给速度可以保证刀具与工件的接触压力,减少振动和变形。
3. 切削深度:选择适当的切削深度可以减少切削力,避免对薄壁零件的损伤。
四、数控车削加工设备选型1. 设备精度:选择精度高、稳定性好的数控车床,以确保对薄壁零件的加工能够满足工程要求。
2. 加工范围:选择加工范围适中的数控车床,以适应不同尺寸和形状的薄壁零件加工需求。
3. 加工性能:选择具有高速切削、高刚性和稳定性的数控车床,有利于提高加工效率和加工质量。
薄壁零件的数控车削加工是一个复杂而又重要的加工过程。
- 1、下载文档前请自行甄别文档内容的完整性,平台不提供额外的编辑、内容补充、找答案等附加服务。
- 2、"仅部分预览"的文档,不可在线预览部分如存在完整性等问题,可反馈申请退款(可完整预览的文档不适用该条件!)。
- 3、如文档侵犯您的权益,请联系客服反馈,我们会尽快为您处理(人工客服工作时间:9:00-18:30)。
谈薄壁零件数控车工加工工艺
1薄壁零件的性质
薄壁零件在生产过程中对生产工艺的精度有着极其高的要求,当下数控技术在工业生产过程中已经得到了广泛应用,数控技术的应用还不够成熟,在制作工艺精度要求较高的零件过程中,数控加工工艺仍然不够完善。
薄壁零件壁厚较薄、容易变形,为了更好地保证薄壁零件的生产质量,要进一步完善数控加工技术。
2薄壁零件加工工艺的影响因素
2.1热因素
由于薄壁零件质量轻,因此薄壁零件在制作过程中很容易变形。
相对于传统的零件,薄壁零件在制造过程中要尤其重视对热量的控制,薄壁零件在切割和打磨过程中需要进行加热。
这就要求把握好加热的精确度,这样才能确保薄壁零件不会变形。
就我国目前数控车工加工的技术,薄壁零件在生产过程中,很难避免接触到过多的热量而出现变形,这也影响了薄壁零件的生产质量。
2.2力因素
由于薄壁零件壁厚较薄,薄壁零件在生产过程中所用的材料也比较轻薄,因此薄壁零件的原材料很容易受到外力的影响。
在薄壁零件的加工过程中,一旦受到外力的影响,就会出现变形,使得薄壁零件
出现小的瑕疵,严重者将直接导致薄壁零件无法使用。
在薄壁零件制作过程中,零件装夹也会对薄壁零件产生一定的影响。
倘若零件装夹对薄壁零件的作用力过大,超过薄壁零件承受范围,也会导致薄壁零件出现变形。
2.3振动因素
薄壁零件在数控加工过程中,需要进行切削加工,在薄壁零件的切削过程中,会出现震动。
薄壁零件对数控车工的加工精确度要求较高,若零件出现微弱的差距,将造成极大的损失。
在切削薄壁零件过程中,倘若加工工艺不精确,会导致零件被切偏。
这样一来,不仅会导致原材料的浪费,也大大降低了薄壁零件的生产效率。
2.4其他因素
薄壁零件在生产加工过程中,加工技术较为严格,倘若工作人员在薄壁零件的生产过程中没有遵循正确的制作流程,会导致薄壁零件出现瑕疵。
工作人员在薄壁零件加工过程中,很容易忽视对切割材料碎屑的清理。
3薄壁零件的数控加工工艺的完善策略
3.1提高薄壁零件的加工精度
薄壁零件在加工过程中对精确度要求较高,这要求充分保证薄壁零件在制作过程中的精确度。
在进行薄壁零件的打磨和切割时,控制
好打磨和切割的热量[1]。
在薄壁零件的切割之前,要选用高速钢刀,选用润滑性能好的极压切削油,来提高薄壁零件的切高精确度。
在零件的切割过程中,要选择震动最小、切割误差最小的机器进行加工,避免过度振动影响薄壁零件的精确度[2]。
为了避免零件装夹对薄壁零件造成破坏,要计算零件装夹对薄壁零件的作用力,来选择适宜的零件装夹。
在薄壁零件进行装夹时,可以在薄壁零件的闭环处增设一个开口的过渡环,这样一来,可以有效减少中装夹对薄壁零件的压力,能提高薄壁零件的加工精确度。
此外,还可以选择在薄壁零件上制作出加强刚性的辅助凸台,这样才能减小零件装夹对薄壁零件的影响。
3.2完善薄壁零件的加工管理制度
在薄壁零件加工过程中制定严格的生产管理制度,这样才能有效避免人为因素影响薄壁零件的加工进程。
在薄壁零件制造过程中,工作人员的不规范操作是导致薄壁零件加工失败的主要原因。
要完善薄壁零件加工管理制度,要对工作人员进行严格的监督和管理,在加工过程中要明确工作人员的生产责任意识,从而有效减少人为因素对薄壁零件生产的影响。
3.3创新薄壁零件的加工工艺
培养研发人员的创新意识,让研发人员对薄壁零件加工工艺进行不断的完善。
在薄壁零件的生产加工过程中,生产企业要提高薄壁零。