质量保证体系(英文材料)
质量保证计划QAP中英文版
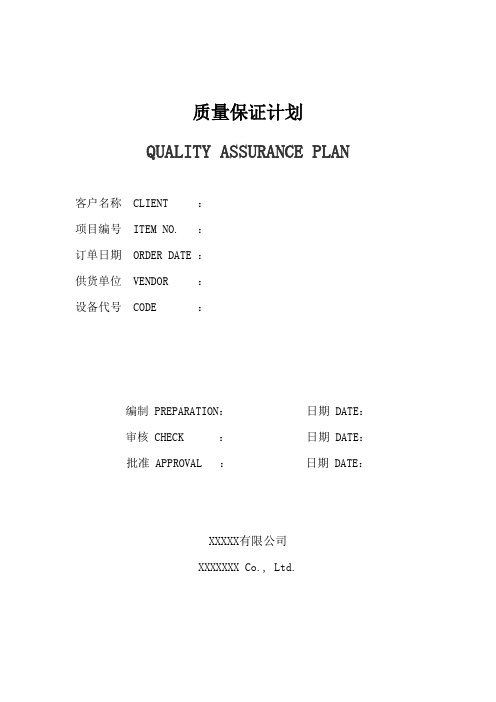
质量保证计划QUALITY ASSURANCE PLAN客户名称 CLIENT :项目编号 ITEM NO. :订单日期 ORDER DATE :供货单位 VENDOR :设备代号 CODE :编制 PREPARATION:日期 DATE:审核 CHECK :日期 DATE:批准 APPROVAL :日期 DATE:XXXXX有限公司XXXXXXX Co., Ltd.1、适用范围和目的 Scope and purpose本质量保证计划适用于UPL项目产品的制造、检验和验收。
确保该产品的制造、检验和验收符合图样、规范、标准的要求。
This quality assurance plan is applicable to the manufacture, inspection and acceptance of UPL project products.To ensure that the manufacture, inspection and acceptance of the products meet the requirements of drawings, specifications and standards2、编制依据 Compilation basisTSG R0004-2009《固定式压力容器安全技术监察规程》TSG R0004-2009《Supervision Regulations on Safety Technology for Stationary Pressure Vessels》GB150.1~150.4-2011《压力容器》GB150.1~150.4-2011 《The Pressure Vessel》GB/T18442.1~5-2011《固定式真空绝热深冷压力容器》GB/T18442.1~5-2011《Fixed Vacuum Insulated Cryogenic Pressure Vessel》MAX/SC-2011《压力容器制造质量保证手册》MAX/SC-2011《Pressure Vessel Manufacturing Quality Assurance Manual》3、制造、检验依据的标准、规范或技术条件 Standards, specifications or technical conditions on which manufacturing or inspection is based 设计图样和工艺文件 Design drawings and process documentsTSG R0004-2009《固定式压力容器安全技术监察规程》TSG R0004-2009《Supervision Regulations on Safety Technology for Stationary Pressure Vessels》GB150.1~150.4-2011 《压力容器》GB150.1~150.4-2011 《The Pressure Vessel》GB/T18442.1~5-2011《固定式真空绝热深冷压力容器》GB/T18442.1~5-2011《Fixed Vacuum Insulated Cryogenic Pressure Vessel》JB/T4711-2003《压力容器涂敷与运输包装》JB/T4711-2003《Pressure Vessel Coating and Transportation Packaging》GB713-2008《锅炉和压力容器用钢板》GB713-2008《Steel plates for boilers and pressure vessels》GB9948-2006《石油裂化用无缝钢管》GB9948-2006《Seamless Steel Pipe for Petroleum Cracking》GB/T14976-2012《流体输送用不锈钢无缝钢管》GB/T14976-2012《Stainless steel seamless steel pipe for fluid conveying》NB/T47008-2010《承压设备用碳素钢和合金钢锻件》NB/T47008-2010《Carbon steel and alloy steel forgings for pressure equipment》NB/T47014-2011《Welding Process Assessment of Pressure Equipment》NB/T47015-2011《压力容器焊接规程》JB/T4730-2005《承压设备无损检测》JB/T4730-2005《Nondestructive testing of pressure equipments》GB/T25198-2010《压力容器封头》GB/T25198-2010《Pressure Vessel Head》HG/T20592~20635-2009《钢制管法兰、垫片、紧固件》HG/T20592~20635-2009《Steel pipe flanges, gaskets, fasteners》HG/T21514~21535-2005《钢制人孔和手孔》HG/T21514~21535-2005《Steel manholes and hand holes》5.1、低温液体储罐设备的检验和试验应符合设计图样、工艺文件及相关标准规范的要求。
杜邦质量保证书(英文版)

Feb.-18-2003DUPONT PAINT WARRANTY TOVANTAGE’s “Project Name”I. Warranty. The DuPont paint warranty covers the areas of PVC profile finished with the PVC painting process (page 3) recommended by DuPont, according to the process recommended by DuPont and exclusively with DuPont MULTIMIX paint materials (hereinafter “Multimix System”) for a period of 5 years of color change and gloss loss and 15 years of adhesion from the date the profile is finished. DuPont warrants that the areas finished with the “Multimix System", will be free throughout the warranty period from defects causing paint failures resulting in cracking, checking, detachment, or unreasonable loss of gloss throughout the entire area finished. Conditions that include failure include: a. Detachment of the paint film as measured by DIN EN ISO 2409. b. Loss of gloss in excess of 30% of the original gloss (at least 60 units) as measured by DIN 67537 60 degree gloss meter. c. Color change according Qualicoat Norm (see enclosure) measured by ISO 7724-3 Photometric Instrument Comparison with control sample. *This may be adjusted by a written agreement between Vantage and DuPont to account for the pigments high ultraviolet light exposure. The conditions are related to the tested PVC-Profiles. II. Excluded from coverage under this warranty are the following: paint failures resulting from improper substrate preparation or treatment; paint failures resulting from failure to use the “Multimix System”; paint failures resulting from the use of paint materials not manufactured or sold by DuPont; paint failures resulting from work performed by non-DuPont certified painters;paint failures caused by improper care, abrasive polishes, cleaning agents, heavy duty pressure washing, or aggressive mechanical wash systems; paint failures caused by abuse, accidents, acid rain, chemical fallout or acts of nature; paint failures resulting from product misuse or abuse; any paint failure that Vantage fails to inspect with an authorized DuPont representative as set forth in the Claims Procedure section.This letter sets forth the entire warranty made by DuPont. THERE ARE NO OTHER WARRANTIES, EXPRESSED OR IMPLIED, INCLUDING WITHOUT LIMITATION, ANY WARRANTY OF MERCHANTABILITY OR FITNESS FOR A PARTICULAR PURPOSE AND ANY SUCH WARRANTIES ARE DISCLAIMED. The remedy set forth herein shall be the sole and exclusive remedy for any breach of warranty. This warranty runs only to Vantage and is not transferable. III. Claims Procedure. In the event a piece of PVC profile covered by the DuPont warranty demonstrates evidence of a paint failure resulting from a paint defect set forth above, the PVC profile must be inspected by an authorized representative of Vantage and DuPont for a determination of whether a paint failure covered by the DuPont warranty exists. Any paint failure determined to result from a paint defect subject to the warranty must be approved and authorized in advance of the work by a DuPont representative and the work must be performed in the described DuPont painting PVC painting process (page 3). In the event work is covered by this warranty, DuPont will replace the product and, where necessary to effect a repair, provide a reasonable allowance for direct labor costs, which costs shall not include overhead or profit. The actual labor allowance will be determined by DuPont in its sole discretion. Any paint failure determined to result from any paint defect not covered by the warranty will be the sole responsibility of the Vantage.DateAccount Manager: _______________________________Business Manager China & Hong Kong________________________________________Process Guide for PVC Painting of Vantage's “Project Name”1. Clean PVC with suitable cleaning agent in order to remove dust, glue residue and other contaminants. 2. Wipe surface to be coated using lint-free cloth soaked with Multimix etching promoter. 3. Allow etching promoter to react with PVC substrate for a minimum of 5 minutes prior to topcoat application 4. Pretreatment inspection, surface to be coated requires full coverage of etching promoter. 5. Prepare Multimix 2K Acryl 100 Topcoat for application, follow all label and Technical Data Sheet instructions. Mix ratio is 5 parts Multimix 2K Acryl 100 Topcoat to 1 part Multimix 2K LR Hardener Fast 6. Set fluid delivery and automizing air pressure in accordance with Technical Data Sheet instructions. 7. Apply 1st pass of paint materials between 5 minutes and 1.5 hours after etching promoter wiping. 8. Apply 2nd pass after 10 minutes flash. 9. Allow the finish to flash for 10 minutes, then force dry for 2 hours at 40 degree centigrade. 10. Inspect for defects and correct as necessary. 11. The final paint properties reached after complete through drying., The information contained here represents the current state of our knowledge and is intended as a guide to our products and their uses.。
质量保证体系(英文材料)

Quality AssuranceQuality has become one of the most important consumer decision factors in the selecting among competing products and services. This is true not only for individual consumers but also for large corporations, government organizations and the taxpaying public as a group. In its broadest sense, quality is a degree of excellence: the extent to which something is fit for its purpose. In the narrow sense, product or service quality is defined as conformance with requirement, freedom from defects or contamination, or simply a degree of customer satisfaction.Figure 1: Taking aPavement Core for DensityQuality ControlFigure 2: Taking a PavementCore for Density Quality ControlFigure 3: Using the NCATOven to Determine AsphaltContentAASHTO and the FHWA subscribe to definitions that designate “quality assurance” as anall-encompassing term, to include “quality control”, “independent assurance” and “acceptance” as its three key components (TRB, 1999[1]):Quality assurance. All those planned and systematic actions necessary to provideconfidence that a product or facility will perform satisfactorily in service. Qualityassurance addresses the overall problem of obtaining the quality of a service, product,or facility in the most efficient, economical, and satisfactory manner possible. Withinthis broad context, quality assurance involves continued evaluation of the activities ofplanning, design, development of plans and specifications, advertising and awarding ofcontracts, construction, and maintenance, and the interactions of these activities.Quality control. Those quality assurance actions and considerations necessary to assessproduction and construction processes so as to control the level of quality beingproduced in the end product. This concept of quality control typically includes samplingand testing by the contractor to monitor the process but usually does not includeacceptance sampling and testing by the agency/owner. Also called process control.Acceptance. Sampling, testing, and the assessment of test results to determine whether or not the quality of produced material or construction is acceptable in terms of thespecifications.Independent assurance. A management tool that requires a third party, not directlyresponsible for process control or acceptance, to provide an independent assessment of the product and/or the reliability of test results obtained from process control andacceptance testing. The results of independent assurance tests should not be used as abasis of product acceptance.Figure 4: Quality Assurance Diagram.Quality control, acceptance and independent assurance are wholly separate components of quality assurance. It is difficult, if not impossible, to influence one component, solely through actions within another component. For instance, acceptance procedures are essentially monitoring methods used to determine whether or not a particular process is meeting quality standards. As such, they can be used to accept or reject material based on its quality but they should never be used as a method to control or improve quality; quality will not necessarily improve based on increased or stricter monitoring alone. In short, no amount of inspection changes the quality of a product or service (IQA, 2001). Quality control (process control) is used to control and systematically improve quality. Furthermore, independent assurance test results should not be used for acceptance or quality control. If they are, the tests are no longer independent and should not be used as if they were.Footnotes (↵ returns to text)1.TRB. (1999). Glossary of Highway Quality Assurance Terms. Transportation Research Circular, No.E-C010. Transportation Research Board, National Research Council. Washington, D.C.↵•。
质量保证书英语
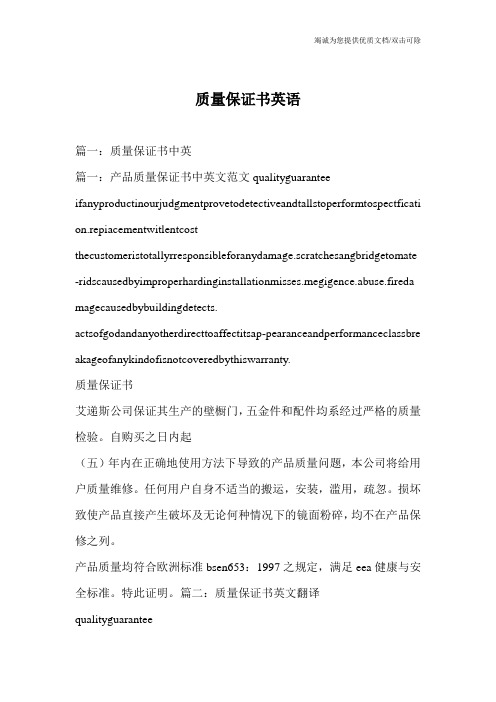
质量保证书英语篇一:质量保证书中英篇一:产品质量保证书中英文范文qualityguarantee ifanyproductinourjudgmentprovetodetectiveandtallstoperformtospectficati on.repiacementwitlentcost thecustomeristotallyrresponsibleforanydamage.scratchesangbridgetomate -ridscausedbyimproperhardinginstallationmisses.megigence.abuse.fireda magecausedbybuildingdetects. actsofgodandanyotherdirecttoaffectitsap-pearanceandperformanceclassbre akageofanykindofisnotcoveredbythiswarranty.质量保证书艾递斯公司保证其生产的壁橱门,五金件和配件均系经过严格的质量检验。
自购买之日内起(五)年内在正确地使用方法下导致的产品质量问题,本公司将给用户质量维修。
任何用户自身不适当的搬运,安装,滥用,疏忽。
损坏致使产品直接产生破坏及无论何种情况下的镜面粉碎,均不在产品保修之列。
产品质量均符合欧洲标准bsen653:1997之规定,满足eea健康与安全标准。
特此证明。
篇二:质量保证书英文翻译qualityguaranteethankyouforchoosingtobuyourproducts! toensureproductsquality,theclearresponsibilityofbuyerandseller,andthepro ducts(:质量保证书英语)afety,wemakethefollowingpromise:second,thesupplierprovidesthecopyofbusinesslicensewithofficialsealstam pedtothebuyer.third,thesupplierprovidesthecopyofthetechnicalspecoftheproductswithoffi cialsealstampedtothebuyer.fifth,thesupplierensuresthatthepackagingandregisteredtrademarkoftheprod uctsmatchtherelevantstateregulation.eighth,thetreatmentofthequalitydispute: thebuyershouldstrictlyobservethetechnicalstandardsshippedwiththesupplie rproductsforinspection,ensurefairandsciencetesting.theremainingsamplesf ailtopasstheexaminationshouldbekeptforoneweek. incaseoftheindeedqualityproblemofthesupplierproducts,thebuyerandseller negotiatetodealwiththeunusedproducts.ninth,theproductguaranteesincebothsidessignasupplycontractanddeliveryo ccurs,terminatesatthesametimeasthebusinessends.篇三:质量保证书-英文certificateofquality,health,purityandanalysissanitaryandveterinarycertifica tetowhomitmayconcernhumanconsumption.theproductsareproducedinvaloediblefatsandingredient s,productsispermittedanywhereinfinland.theproductisfreefromb.s.e.eu-reg istrationnumber:60220exporter:destination:specificationproductsdemineralizedwheypowderaspercontractno.ch/99/66.809and4760bagsprotein(nx6.38)moistureash(550c)ph(10%sol.20c)scorchedparticles(admi) nitrate standardplatecountenterobacteriaceaeyeastsmounds sulphitereducingclostridiaspecificationmin.max.max.6.2discamax.max.max.max.max.max.g5,000/g10/g50/g50/g10/g12.0%4.0%1.0%--6.930mg/kanalysis13.5%2.1%0.5%6.4discapassestest3,000/g121,380.00kgsgross11 9,000.00kgsnetvaloediblefatsandingredients,helsinki,finlandshenzhen,chinaweight(kg)dateofexport:apr.20,20XXstaphylococcusaureussalmonella shippingmarks:neg.inneg.inch99/66.8091g50gneg.in1gneg.in50g------------------shenzhenchina篇二:产品质量保证书中英文范文QualityGuarantee。
质量保证书英文
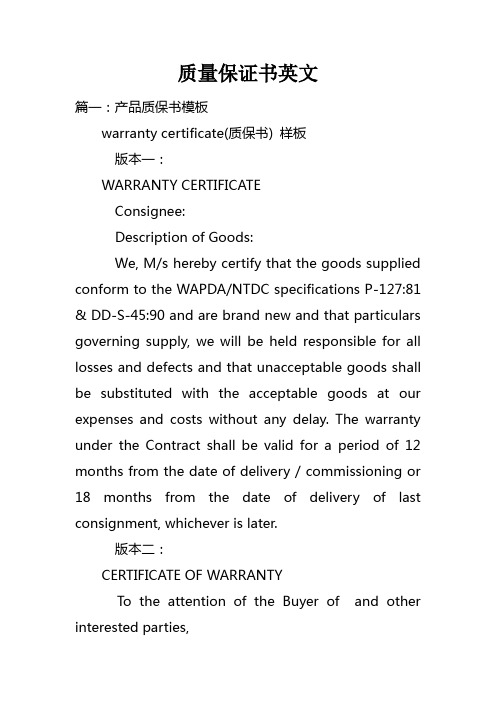
质量保证书英文篇一:产品质保书模板warranty certificate(质保书) 样板版本一:WARRANTY CERTIFICATEConsignee:Description of Goods:We, M/s hereby certify that the goods supplied conform to the WAPDA/NTDC specifications P-127:81 & DD-S-45:90 and are brand new and that particulars governing supply, we will be held responsible for all losses and defects and that unacceptable goods shall be substituted with the acceptable goods at our expenses and costs without any delay. The warranty under the Contract shall be valid for a period of 12 months from the date of delivery / commissioning or 18 months from the date of delivery of last consignment, whichever is later.版本二:CERTIFICATE OF WARRANTYTo the attention of the Buyer of and other interested parties,Vendor Name: Vendor's Address:Vendor's Commercial Invoice Number: Bill of Lading Number: Vendor's Proforma Invoice Number: Bill of Lading Date: Descriptions of GoodsConsignee Name: Consignee's Address:Purchase Order Number:Dear Madam / Sir,We, (here known as the above mentioned Vendor), hereby warrant that the above mentioned Goods; which is listed in the above mentioned Commercial Invoice and Bill of Lading, and consigned to the above mentioned Consignee, are in accordance to the samples approved by the Consignee, and complies with the terms and condition stipulated in the above mentioned Purchase Order Number. Should the Goods were to be deemed as defective and rejected by the Quality Control Department of the Consignee at the final goods reception site of the Consignee, in addition to the handling chargesincurred for the rejected goods; the Consignee is entitle to a compensation at a rate of 1-to-1 for all the rejected good involved; at the same equal amount ofquantity and value of Goods deemed defective.This Warranty shall expire after the 90th day from the above mentioned Bill of Lading Date.济钢产品质保书实现信息化管理日前,随着中厚板、热连轧和冷轧三条生产线MES信息化系统的上线运行,济钢集团产品质量保证书同步实现了信息化管理。
HACCP体系及GMP体系基本介绍

HACCP体系认证及GMP认证基本状况简介HACCP是"Hazard Analysis Critical Control Point"英文缩写, 即危害分析和关键控制点。
HACCP体系被认为是控制食品安全最佳最有效旳管理体系。
什么是HACCP体系?国标GB/T 15091-1994《食品工业基本术语》对HACCP旳定义为:生产(加工)安全食品旳一种控制手段;对原料、关键生产工序及影响产品安全旳人为原因进行分析, 确定加工过程中旳关键环节, 建立、完善监控程序和监控原则, 采用规范旳纠正措施。
国际原则CAC/RCP-1《食品卫生通则1997修订3版》对HACCP旳定义为:鉴别、评价和控制对食品安全至关重要旳危害旳一种体系。
一、HACCP旳产生与国外发展概况近40年来, HACCP已经成为国际上共同承认和接受旳食品安全保证体系, 重要是对食品中微生物、化学和物理危害旳安全进行控制。
近年来政府及消费者对食品安全性旳普遍关注和食品传染病旳持续发生是HACCP体系得到广泛应用动力。
HACCP发展大体分为两个阶段。
1.创立阶段●HACCP系统是20世纪60年代由美国Pillsbury企业与宇航局和美国陆军Natick研究所共同开发旳, 重要用于航天食品中。
●1971年在美国第一次国家食品保护会议上提出了HACCP原理, 立即被食品药物管理局(FDA)接受, 并决定在低酸罐头食品旳GMP中采用。
●FDA于1974年公布了将HCCP原理引入低酸罐头食品旳GMP。
●1985年美国科学院(NAS)就食品法规中HACCP有效性刊登了评价成果。
随即由美国农业部食品安全检查署(FSIS)、美国陆军Natick研究所、食品药物管理局(FDA)、美国海洋渔业局(NMFS)四家政府机关及大学和民间机构旳专家构成旳美国食品微生物学基准征询委员会(NACMCF)于1992年采纳了食品生产旳HACCP七原则。
1993年FAO/WHO食品法典委员会同意了《HACCP体系应用准则》, 1997年颁发了新版法典指南《HACCP体系及其应用准则》, 该指南已被广泛地接受并得到了国际上普遍旳采纳, HACCP概念已被承认为世界范围内生产安全食品准则。
质量管理常用英文单词

QM-—quality management--质量管理qualitymanager 质量经理QE-—quality engineer—-质量工程师QA—-quality assurance-—质量保证QC-—quality control——质量控制IQC—-incoming quality control-—进料检验PQC--process quality control ——制程检验FQC—-finished quality control —-成品检验OQC--outgoing q uality control--出货检验SQE—-supplier quality en g SPC,six g i m a n TS16949,e MSA,FMEA e r--供应商质量工程师QSE——quality system engineer-—质量体系工程师六A西格玛品质论Q坛QD9b-E--assistant quality engineer--质量助理工程师PQE--process quality engineer ——过程质量工程师CS--client server ——客户服务PQC-—pro c{#`8C3e ss quality control-—制程检验,,,,,,,,,improcessFQC——finished quality control ——成品检验,,,,,,,,,final加之VQA--Vendorquality assurance--供应商质量保证parts pe bbs.6sq n r et'n#m i l i o n,简称PPM}就是每百万坏品率少于3 。
全面质量管理(TQM)质量一致性检验inspecton of quality conformity 仲裁性质质量监督quality supervision for arbitration产品保护product protection 产品定型product approval产品分等product classificatin 产品规范product specification产品设计product design 产品质量product quality 产品合格率product percent of pass产品系列化product seriation 产品管理标准product management standard产品计量单位unit of measurement of product 产品售后服务after service产品质量标志product quality mark 产品质量标准product quality standard产品质量管理product quality management 产品质量检验product quality inspection产品质量监督检验product quality supervision and inspection产品质量认证标志certification marking of product quality产品质量认证程序certification procedure of product quality产品质量认证制度certification system of product quality认证certification 立法legislation 自行认证self-certification 认可accreditation 安全认证safety certification安全认证标志mark of safety certification 强制性认证compulsory certificate实验室鉴定laboratory qualification 实验室认证laboratory certification自愿认证制voluntary system of certification 法规机构regulatory authorities认证活动certification activity 认证体系certification system认证计划certification scheme 认证机构certification body检验机构inspecton body许可证licence 申请人applicant 许可证持有者licensee 合格证书certificate of conformity合格标记mark of conformity 认证体系的利用access to certification system认证体系的参预者participant in certification system 认证体系的成员member of certification system批准approval 型式批准type approval测试实验室的认可accreditation of testing laboratory认可accreditation 认可体系accreditation system认可机构accreditation body认可的实验室accredited laboratory认可准则acreditatin criteria 实验室评定laboratory assessment实验室评定者laboratory assessor 认可的实验室的试验报告accredited laboratory test report批准签署人approved signatory 承认和批准协议recognition and approval arrangement承认协议recognition arrangement 单边协议unilateral arrangement双边协议bilateral arrangement 多边协议multilateral arrangemetn互利reciprocity 平等待遇equal treatmetn 国家待遇national treatment国家和平等待遇national and equal treatment 合格及有关的通用概念conformity and related general concept合格conformity 合格测试conformity testing合格acceptable 合格品acceptable part 合格标志mark of conformity合格认证conformity certification 合格认证标志mark of conformity certification合格品标志mark of acceptable product 合格证书certificate of conformity合格证检查inspection by certificate 合格质量检查acceptable quality level评定合格assessment of conformity 合格评定conformity assessment型式评价type evaluation 合格监督conformity surveillance合格证明verification of conformity 合格保证assurance of conformity供货商声明supplier’s declaration 生产许可证production licence一致consensus 检验inspection 不定期检验nonperiodic inspection抽样检验sampling inspection 出厂检验exfactory inspection第一方检验first party inspection 第二方检验second party inspection第三方检验third party inspection 第三方认证制度third pary certification定期检验periodic inspection 交收检验acceptance inspeciton例行检验routine inspeciton 生产检验produciton inspeciton生产定型检验production approval inspeciton 验收检验acceptance inspeciton验证检验compliance test 仲裁检验arbitration inspection创造商担保guarantee by manufacturer 百分比抽样检查percent sampling inspection不合格判定数rejection number 不合格质量水平rejecton quality level抽查型质量监督sampling quality supervision 环境监测environmental monitoring抽样sampling 多次抽样multiple sampling 分层抽样stratified sampling分层随机抽样stratified random smapling 多级抽样multistage sampling二次抽样double sampling 试件test piece 试验报告test report试样test sample 测试设备testing equipment 测试试验室testing laboratority商标trademark 商品名称trade-name 测试testing 试验test 实验室间的试验比较interlaboratorytest comparisons熟练水平试验proficiency testing 次品defective product代用产品substitute product 定量试验quantitative test 出口管理export control出口许可证制度export control 进口许可证制度import licence system定额管理quota management 非关税壁垒non-tarrif barrier 关税壁垒tariff barrier关税普遍优惠制general preferential dutiesCore value (核心价值) Love 愛心Confidence 信心Decision 決心Corporate culture (公司文化)Integration 融合Responsibility 責任Progress 進步3T STRATEGYTime to market 及時切入生產Time to volume 及時大量生產Time to money 及時大量交貨FOUR CONTROL SYSTEM 四大管制系統Engineering control system 工程管制系統Quality control system 品質管制系統Manufacturing control system 生產管制系統Management control system 經營管制系統7SClassification 整理(sorting, organization) -seiriRegulation 整頓(arrangement, tidiness)-seitonCleanliness 清掃(sweeping, purity)—seisoConservation 清洁(cleaning, cleanliness)—seiktsuCulture 教養(discipline)-shitsukeSave 節約Safety 安全二:英文縮寫品質人員名稱類QC quality control 品質管理人員FQC final quality control 終點品質管制人員IPQC in process quality control 制程中的品質管制人員OQC output quality control 最終出貨品質管制人員IQC incoming quality control 進料品質管制人員TQC total quality control 全面質量管理POC passage quality control 段檢人員QA quality assurance 質量保證人員OQA output quality assurance 出貨質量保證人員QE quality engineering 品質工程人員品質保證類FAI first article inspection 新品首件檢查FAA first article assurance 首件確認CP capability index 能力指數CPK capability process index 模具製程能力參數SSQA standardized supplier quality audit 合格供應商品質評估FMEA failure model effectiveness analysis 失效模式分析FQC 運作類AQL Acceptable Quality Level 運作類允收品質水準S/S Sample size 抽樣檢驗樣本大小ACC Accept 允收REE Reject 拒收CR Critical 極嚴重的MAJ Major 主要的MIN Minor 輕微的Q/R/S Quality/Reliability/Service 品質/可靠度/服務P/N Part Number 料號L/N Lot Number 批號AOD Accept On Deviation 特采UAI Use As It 特采FPIR First Piece Inspection Report 首件檢查報告PPM Percent Per Million 百萬分之一制程統計品管專類SPC Statistical Process Control 統計製程管制SQC Statistical Quality Control 統計品質管制GRR Gauge Reproductiveness &Repeatability 量具之再制性及重測性判斷量可靠與否DIM Dimension 尺寸DIA Diameter 直徑N Number 樣品數其它品質術語類QIT Quality Improvement Team 品質改善小組ZD Zero Defect 零缺點QI Quality Improvement 品質改善QP Quality Policy 目標方針TQM Total Quality Management 全面品質管理RMA Return Material Audit 退料認可7QCTools 7 Quality Control Tools ECN Engineering Change Notice ECO Engineering Change Order 序改動通知PMP Product Management Plan品管七大手法通用之件類工程變更通知(供應商)工程改動要求(客戶) PCN生產管制計劃Process Change Notice 工SIP SOP 驗規範BOM SPEC Standard Inspection ProcedureStandard Operation ProcedureBill Of Material 物料清單PS Package Specification 包裝規範Specification 規格DWG Drawing 圖面系統文件類製程檢驗標準程序製造作業規範IS Inspection Specification 成品檢ES Engineering Standard 工程標準CGOO China General PCE 龍華廠文件IWS International Workman Standard 工藝標準ISO International Standard Organization 國際標準化組織GS General Specification 普通規格部類PMC Production & Material Control 生產和物料控制PCC Product control center 生產管制中心PPC Production Plan Control 生產計劃控制MC Material Control 物料控制DC Document Center 資料中心QE Quality Engineering 品質工程(部)QA Quality Assurance 品質保證(處)QC Quality Control 品質管制(課)PD Product Department 生產部LAB Laboratory 實驗室IE Industrial Engineering 工業工程R&D Research &Design 設計開發部生產類PCs Pieces 個(根,塊等)PRS Pairs 雙(對等)CTN Carton 卡通箱PAL Pallet/skid 棧板PO Purchasing Order 采購訂單MO Manufacture Order 生產單D/C Date Code 生產日期碼ID/C Identification Code (供應商)識別碼SWR Special Work Request 特殊工作需求L/N Lot Number 批號P/N Part Number 料號OEM Original Equipment Manufacture 原設備製造PC Personal Computer 個人電腦CPU Central Processing Unit 中央處理器A 。
质量保证承诺(中英文)
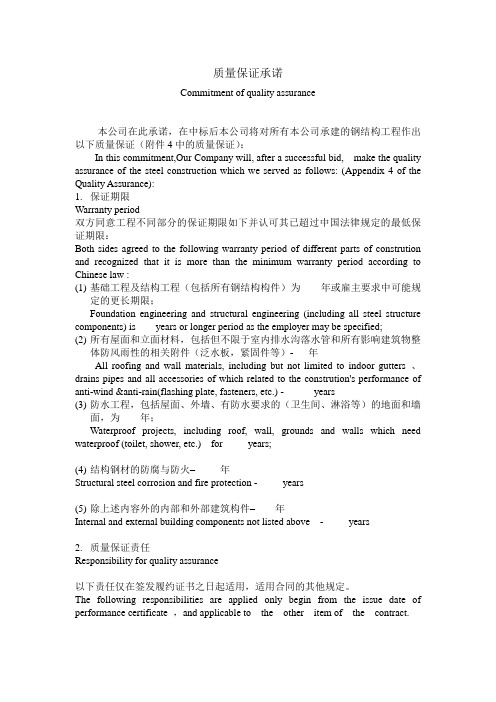
质量保证承诺Commitment of quality assurance本公司在此承诺,在中标后本公司将对所有本公司承建的钢结构工程作出以下质量保证(附件4中的质量保证):In this commitment,Our Company will, after a successful bid, make the quality assurance of the steel construction which we served as follows: (Appendix 4 of the Quality Assurance):1.保证期限Warranty period双方同意工程不同部分的保证期限如下并认可其已超过中国法律规定的最低保证期限:Both sides agreed to the following warranty period of different parts of constrution and recognized that it is more than the minimum warranty period according to Chinese law :(1)基础工程及结构工程(包括所有钢结构构件)为年或雇主要求中可能规定的更长期限;Foundation engineering and structural engineering (including all steel structure components) is years or longer period as the employer may be specified;(2)所有屋面和立面材料,包括但不限于室内排水沟落水管和所有影响建筑物整体防风雨性的相关附件(泛水板,紧固件等)- 年All roofing and wall materials, including but not limited to indoor gutters 、drains pipes and all accessories of which related to the constrution's performance of anti-wind &anti-rain(flashing plate, fasteners, etc.) - years(3)防水工程,包括屋面、外墙、有防水要求的(卫生间、淋浴等)的地面和墙面,为年;Waterproof projects, including roof, wall, grounds and walls which need waterproof (toilet, shower, etc.) for years;(4)结构钢材的防腐与防火–年Structural steel corrosion and fire protection - years(5)除上述内容外的内部和外部建筑构件–年Internal and external building components not listed above - years2.质量保证责任Responsibility for quality assurance以下责任仅在签发履约证书之日起适用,适用合同的其他规定。
质量专有中英文对照名词

部门名称的专有名词QS---Quality system品质系统CS---Coutomer Sevice 客户服务QC---Quality control品质管理IQC---Incoming quality control 进料检验LQC---Line Quality Control 生产线品质控制IPQC---In process quality control 制程检验FQC---Final quality control 最终检验OQC---Outgoing quality control 出货检验QA---Quality assurance 品质保证SQA---Source(supplier) Quality Assurance 供应商品质保证(VQA) CQA---Customer Quality Assurance客户质量保证PQA rocess Quality Assurance 制程品质保证QE---Quality engineer 品质工程CE---component engineering零件工程EE---equipment engineering设备工程ME---manufacturing engineering制造工程TE---testing engineering测试工程PPE roduct Engineer 产品工程IE---Industrial engineer 工业工程ADM--- Administration Department行政部RMA---客户退回维修CSDI---检修PC---producing control生管MC---mater control物管GAD--- General Affairs Dept总务部A/D--- Accountant /Finance Dept会计LAB--- Laboratory实验室DOE---实验设计HR---人资PMC---企划RD---研发W/H---仓库SI---客验PD--- Product Department生产部PA---采购(PUR--- Purchaing Dept)SMT---Surface mount technology 表面粘着技术MFG---Manufacturing 制造MIS---Management information system 资迅管理系统DCC---document control center 文件管制中心厂内作业中的专有名词QT---Quality target品质目标QP---Quality policy目标方针QI---Quality improvement品质改善CRITICAL DEFECT---严重缺点(CR)MAJOR DEFECT---主要缺点(MA)MINOR DEFECT---次要缺点(MI)MAX---Maximum最大值MIN---Minimum最小值DIA iameter直径DIM imension尺寸LCL---Lower control limit管制下限UCL---Upper control limit管制上限EMI---电磁干扰ESD---静电防护EPA---静电保护区域ECN---工程变更ECO---Engineering change order工程改动要求(客户)ECR---工程变更需求单CPI---Continuous Process Improvement 连续工序改善Compatibility---兼容性Marking---标记DWG rawing图面Standardization---标准化Consensus---一致Code---代码ZD---Zero defect零缺点Tolerance---公差Subject matter---主要事项Auditor---审核员BOM---Bill of material物料清单Rework---重工ID---identification识别,鉴别,证明PILOT RUN--- (试投产)FAI---首件检查FPIR---First Piece Inspection Report首件检查报告FAA---首件确认SPC---统计制程管制CP--- capability index(准确度)CPK--- capability index of process(制程能力)PMP---制程管理计划(生产管制计划)MPI---制程分析DAS efects Analysis System 缺陷分析系统PPB---十亿分之一Flux---助焊剂P/N---料号L/N---Lot Number批号Version---版本Quantity---数量Valid date---有效日期MIL-STD---Military-Standard军用标准ICT--- In Circuit Test (线路测试)ATE---Automatic Test Equipment自动测试设备MO--- Manafacture Order生产单T/U--- Touch Up (锡面修补)I/N---手插件P/T---初测F/T--- Function Test (功能测试-终测)AS 组立P/K---包装TQM---Total quality control全面品质管理MDA---manufacturing defect analysis制程不良分析(ICT) RUN-IN---老化实验HI-pot---高压测试FMI---Frequency Modulation Inspect高频测试DPPM--- Defect Part Per Million(不良率的一种表达方式---百万分之一) 1000PPM即为0.1% Corrective Action--- (CAR改善对策)ACC---允收REJ---拒收S/S---Sample size抽样检验样本大小SI-SIV---Special I-Special IV特殊抽样水平等级CON---Concession / Waive特采ISO---国际标准化组织ISA---Industry Standard Architecture工业标准体制结构OBA---开箱稽核FIFO---先进先出PDCA---管理循环Plan do check action计划,执行,检查,总结WIP---在制品(半成品)S/O--- Sales Order (业务订单)P/O--- Purchase Order (采购订单)P/R--- Purchase Request (请购单)AQL---acceptable quality level允收品质水准LQL;Limiting quality level最低品质水准QVL---qualified vendor list合格供应商名册AVL---认可的供货商清单(Approved Vendor List)QCD--- Quality cost delivery(品质,交期,成本)MPM---Manufacturing project management制造专案管理KPI---Key performance indicate重要绩效指标MVT---Manufacturing Verification Test制造验证试产Q/R/S---Quality/Reliability/Service质量/可靠度/服务STL---ship to line(料到上线)NTF---No trouble found误判CIP---capacity improvement plan(产能改善计划)MRB---material review board(物料审核小组)MRB---Material reject bill退货单JIT---just in time(即时管理)5S---seiri seiton seiso seiketsu shitsuke(整理,整顿,清扫,清洁,修养)SOP---standard operation process(标准作业程序)SIP---Specification inspection process制程检验规格TOP--- Test Operation Process (测试作业流程)WI--- working instruction(作业指导书)SMD---surface mounting device(表面粘着原件)FAR---failure aualysis report故障分析报告CAR---Corrective action report改善报告BPR--- 企业流程再造 (Business Process Reengineering)ISAR---首批样品认可(Initial Sample Approval Request)-JIT---实时管理 (Just In Time)QCC---品管圈 (Quality Control Circle)Engineering Department (工程部)TQEM--- Total Quality Environment Management(全面品质环境管理)PD--- Production Department (制造)LOG--- Logistics (后勤支持)Shipping--- (进出口)AOQ---Average Output Quality平均出货质量AOQL---Average Output Quality Level平均出货质量水平FMEA---failure model effectiveness analysis失效模式分析CRB--- Change Review Board (工程变更会议)CSA---Customer Simulate Analysis客户模拟分析SQMS---Supplier Quality Management System供应商品质管理系统QIT--- Quality Improvement Team 品质改善小组QIP---Quality Improvement Plan品质改善计划CIP---Continual Improvement Plan持续改善计划M.Q.F.S--- Material Quality Feedback Sheet (来料品质回馈单) SCAR--- Supplier Corrective Action Report (供货商改善对策报告) 8D Sheet--- 8 Disciplines sheet ( 8D单)PDCA---PDCA (Plan-Do-Check-Action) (管理循环)MPQ--- Material Packing Quantity (物料最小包装量)DSCN--- Delivery Schedule Change Notice (交期变更通知)QAPS--- Quality Assurance Process Sheet (品质工程表)DRP---运销资源计划 (Distribution Resource Planning)DSS---决策支持系统 (Decision Support System)EC---电子商务 (Electronic Commerce)EDI---电子资料交换 (Electronic Data Interchange)EIS---主管决策系统 (Excutive Information System)ERP---企业资源规划 (Enterprise Resource Planning) FMS---弹性制造系统 (Flexible Manufacture System)KM---知识管理 (Knowledge Management)4L---逐批订购法 (Lot-for-Lot)LTC---最小总成本法 (Least Total Cost)LUC---最小单位成本 (Least Unit Cost)MES---制造执行系统 (Manufacturing Execution System) MPS---主生产排程 (Master Production Schedule)MRP---物料需求规划 (Material Requirement Planning) MRPⅡ---制造资源计划 (Manufacturing Resource Planning) OEM---委托代工 (Original Equipment Manufacture)ODM---委托设计与制造 (Original Design & Manufacture) OLAP---线上分析处理 (On-Line Analytical Processing) OLTP---线上交易处理 (On-Line Transaction Processing) OPT---最佳生产技术 (Optimized Production Technology) PDCA---PDCA管理循环 (Plan-Do-Check-Action)PDM---产品数据管理系统 (Product Data Management)) RCCP---粗略产能规划 (Rough Cut Capacity Planning) SCM---供应链管理 (Supply Chain Management)SFC---现场控制 (Shop Floor Control)TOC---限制理论 (Theory of Constraints)TQC---全面品质管制 (Total Quality Control)FYI/R---for your information/reference仅供参考ASAP---尽快S/T---Standard time标准时间TPM---total production maintenance---全面生产保养ESD Wrist strap---静电环IT---information technology信息技术,资讯科学CEO---Chief Executive Officer执行总裁COO---Chief Operaring Officer首席业务总裁SWOT---Strength,Weakness,Opportunity,Threat优势﹐弱点﹐机会﹐威胁Competence---专业能力Communication---有效沟通Cooperation---统御融合Vibration Testing---振动测试IDP---Individual Development Plan个人发展计划MRP---Material Requirement Planning物料需求计划MAT'S---Material材料LRR---Lot Rejeet Rate批退率ATIN---Attention知会3C---Computer ,Communication , Consumer electronic消费性电子5W1H---When , Where , Who , What , Why , Ho5M--- Man , Machine , Material , Method , Measurement人,机器,材料,方法,测量4MIE--- Man,Material,Machine,Method,Environment人力,物力,财务,技术,时间(资源)7M1I--- Manpower , Machine , Material , Method, Market , Management , Money , Information人力,机器,材料,方法, 市场,管理,资金,资讯1 Accuracy 准确度2 Action 行动3 Activity 活动4 Analysis Covariance 协方差分析5 Analysis of Variance 方差分析6 Approved 承认7 Attribute 计数值8 Average 平均数9 Balance sheet 资产负债对照表10 Binomial 二项分配11 Brainstorming Techniques 脑力风暴法12 Cause and Effect Matrix 因果图(鱼骨图)13 CL---Center Line 中心线14 Check Sheets 检查表15 Complaint 投诉16 Conformity 合格(符合)17 Control 控制18 Control chart 控制(管制)图19 Correction 纠正20 Correlation Methods 相关分析法21 CPI--- continuouse Process Improvement 连续工序改善22 Cross Tabulation Tables 交叉表23 CS--- Customer Sevice 客(户)服(务)中心24 DSA--- Defects Analysis System 缺陷分析系统25 Data 数据 Description---品名26 DCC--- Document Control Center 文控中心27 Decision 决策、判定28 Defects per unit 单位缺点数29 Description 描述30 Device 装置31 Do 执行32 DOE--- Design of Experiments 实验设计33 Element 元素34 Engineering recbnology 工程技35 Environmental 环境36 Equipment 设备37 Estimated accumulative frequency 计算估计累计数38 E Equipment Variation 设备变异39 External Failure 外部失效,外部缺陷40 FA--- Failure Analysis 失效分析41 Fact control 事实管理42 Fatigue 疲劳43 FMEA--- Failure Mode and Effect Analysis失效模式与效果分析44 FP First-Pass Yield (第一次通过)合格率45 FQA--- Final Quality Assurance 最终品质保证46 FQC--- Final Quality control 最终品质控制47 Gauge system 测量系统48 Grade 等级49 Histogram 直方图50 Improvement 改善51 Initial review 先期审查52 Inspection 检验53 Internal Failure 内部失效、内部缺陷54 IPQC--- In Process Quality Control 制程品质控制55 IQC--- Incomming Quality Control 来料品质控制56 IS International Organization for Standardization 国际标准化组织57 LCL--- Lower Control limit 管制下限58 LQC--- Line Quality Control 生产线品质控制59 LSL--- Lower Size Limit 规格下限60 Machine 机械61 Manage 管理62 Materials 物料63 Measurement 测量64 Median 中位数65 MSA--- Measurement System Analysis 测量系统分析66 Occurrence 发生率67 Operation Instruction 作业指导书68 Organization 组织69 Parto 柏拉图70 PPM arts per Million (百万分之)不良率71 Plan 计划72 Policy 方针73 Population 群体74 PQA--- Process Quality Assurance 制程品质保证75 Practice 实务(践)76 Prevention 预防77 Probability 机率78 Probability density function 机率密度函数79 Procedure 流程80 Process 过程81 Process capability analysis 制程能力分析(图)82 Process control and Process capability制程管制与制程能力83 Product 产品84 Production 生产85 Projects 项目86 QA--- Quality Assurance 品质保证87 QC--- Quality Control 品质控制88 QE--- Quality Engineering 品质工程89 QFD--- Quality Function Desgin 品质机能展开(法)90 Quality 质量91 Quality manual 品质手册92 Quality policy 品质政策(质量方针)93 Random experiment 随机试验94 Random numbers 随机数95 R---Range 全距(极差)96 Reject 拒收97 Repair 返修98 Repeatusility 再现性99 Reproducibility 再生性100 Requirement 要求101 Responsibilities 职责102 Review 评审103 Reword 返工104 Rolled yield 直通率105 RPN--- Risk Priority Number 风险系数106 Sample 抽样,样本107 Sample space 样本空间108 Sampling with replacement 放回抽样109 Sampling without replacement 不放回抽样110 Scatter diagram 散布图分析111 Scrap 报废112 Simple random sampling 简单随机取样113 Size 规格114 SL--- Size Line 规格中心线115 Stratified random sampling 分层随机抽样116 SOP--- Standard Operation Procedure 标准作业书117 SPC--- Statistical Process Control 统计制程管制118 Specification 规范119 SQA--- Source(Supplier) Quality Assurance 供货商品质保证120 Stage sampling 分段随机抽样121 Standard Deviation 标准差122 Sum of squares 平方和123 Taguchi-method 田口(试验)方法124 Theory 原理125 TQC--- Total Quality Control 全面品质控制126 TQM--- Total Quality Management 全面品质管理127 Traceablity 追溯128 Training 培训129 UCL--- Upper Control Limit 管制(控制)上限130 USL--- Upper Size Limit 规格上限131 Validation 确认132 Variable 计量值133 Verification 验证134 Version 版本135 VOC--- Voice of Customer 客户需求136 VOE--- Voice of Engineer 工程需求137 Inventory stock report---庫存清单报告138 Sales order report---出货报告质量人员名称类QC quality control 品质管理人员FQC final quality control 终点质量管理人员IPQC in process quality control 制程中的质量管理人员OQC output quality control 最终出货质量管理人员IQC incoming quality control 进料质量管理人员TQC total quality control 全面质量管理POC passage quality control 段检人员QA quality assurance 质量保证人员OQA output quality assurance 出货质量保证人员QE quality engineering 质量工程人员质量保证类FAI first article inspection 新品首件检查FAA first article assurance 首件确认CP capability index 能力指数CPK capability process index 模具制程能力参数SSQA standardized supplier quality audit 合格供货商质量评估FMEA failure model effectiveness analysis 失效模式分析FQC运作类AQL Acceptable Quality Level 运作类允收质量水平S/S Sample size 抽样检验样本大小ACC Accept 允收REE Reject 拒收CR Critical 极严重的MAJ Major 主要的MIN Minor 轻微的Q/R/S Quality/Reliability/Service 质量/可靠度/服务P/N Part Number 料号L/N Lot Number 批号AOD Accept On Deviation 特采UAI Use As It 特采FPIR First Piece Inspection Report 首件检查报告PPM Percent Per Million 百万分之一制程统计品管专类SPC Statistical Process Control 统计制程管制SQC Statistical Quality Control 统计质量管理GRR Gauge Reproductiveness & Repeatability 量具之再制性及重测性判断量可靠与否DIM Dimension 尺寸DIA Diameter 直径N Number 样品数其它质量术语类QIT Quality Improvement Team 质量改善小组ZD Zero Defect 零缺点QI Quality Improvement 质量改善QP Quality Policy 目标方针TQM Total Quality Management 全面质量管理RMA Return Material Audit 退料认可7QCTools 7 Quality Control Tools 品管七大手法通用之件类ECN Engineering Change Notice 工程变更通知(供货商)ECO Engineering Change Order 工程改动要求(客户)PCN Process Change Notice 工序改动通知PMP Product Management Plan 生产管制计划SIP Standard Inspection Procedure 制程检验标准程序SOP Standard Operation Procedure 制造作业规范IS Inspection Specification 成品检验规范BOM Bill Of Material 物料清单PS Package Specification 包装规范SPEC Specification 规格DWG Drawing 图面系统文件类ES Engineering Standard 工程标准CGOO China General PCE龙华厂文件IWS International Workman Standard 工艺标准ISO International Standard Organization 国际标准化组织GS General Specification 一般规格部类PMC Production & Material Control 生产和物料控制PCC Product control center 生产管制中心PPC Production Plan Control 生产计划控制MC Material Control 物料控制DC Document Center 资料中心QE Quality Engineering 质量工程(部)QA Quality Assurance 质量保证(处)QC Quality Control 质量管理(课)PD Product Department 生产部LAB Laboratory 实验室IE Industrial Engineering 工业工程R&D Research & Design 设计开发部生产类PCs Pieces 个(根,块等)PRS Pairs 双(对等)CTN Carton 卡通箱PAL Pallet/skid 栈板PO Purchasing Order 采购订单MO Manufacture Order 生产单D/C Date Code 生产日期码ID/C Identification Code (供货商)识别码SWR Special Work Request 特殊工作需求L/N Lot Number 批号P/N Part Number 料号OEM Original Equipment Manufacture 原设备制造PC Personal Computer 个人计算机CPU Central Processing Unit 中央处理器A.S.A.P As Soon As Possible 尽可能快的E-MAIL Electrical-Mail 电子邮件N/A Not Applicable 不适用QTY Quantity 数量I/O input/output 输入/输出NG Not Good 不行,不合格C=0 Critical=0 极严重不允许APP Approve 核准,认可,承认CHK Check 确认ASS'Y Assembly 装配,组装T/P True Position 真位度5WIH When, Where, Who, What, Why, How to6M Man, Machine, Material, Method, Measurement, Message4MTH Man, Material, Money, Method, Time, How 人力,物力,财务,技术,时间(资源) SQA Strategy Quality Assurance 策略质量保证DQA Design Quality Assurance 设计质量保证MQA Manufacture Quality Assurance 制造质量保证SSQA Sales and service Quality Assurance 销售及服务质量保证LRR Lot Reject Rate 批退率SPS Switching power supply 电源箱DT Desk Top 卧式(机箱)MT Mini-Tower 立式(机箱)DVD Digital Video DiskVCD Video Compact DiskLCD Liquid Crystal DisplayCAD Computer Aided DesignCAM Computer Aided ManufacturingCAE Computer Aided EngineeringPCB Printed Circuit Board 印刷电路板CAR Correction Action Report 改善报告NG Not Good 不良WDR Weekly Delivery Requirement 周出货要求PPM Percent Per Million 百万分之一TPM Total Production Maintenance 全面生产保养MRP Material Requirement Planning 物料需计划OS Operation System 操作系统TBA To Be Assured 待定,定缺D/C Drawing ChangeP/P Plans & ProcedureEMI Electrical-Music Industry 电子音乐工业Electrical Magnetic Interference 电子干扰RFI Read Frequency Input 读频输入MMC Maximum Material ConditionMMS Maximum Material SizeLMC Least Material ConditionLMS Least Material SizeLED lighting-emitting diode 发光二极管。
质量手册翻译中英文术语表
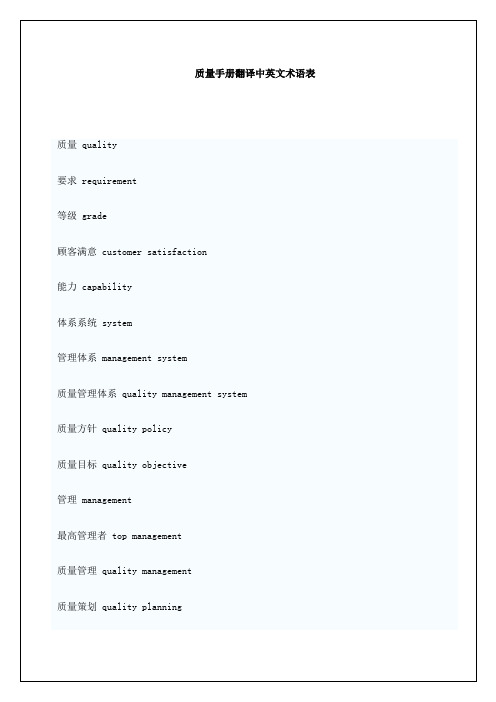
质量体系审核指南 质量体系审核员的评定准则 Guidelines for auditing quality systems--Part 2: Qualification criteria for quality systems auditors
P
preventive action
procedure
process
product
project
Q
qualification process
quality
quality assurance
quality characteristic
quality control
quality improvement
质量管理体系 业绩改进指南 Quality management systems--Guidelines for performance improvements
质量管理和质量体系要素 第2部分: 服务指南 Quality management and quality system elements--Part 2: Guidelines for services
测量设备的质量保证 第2部分: 测量过程控制指南 Quality assurance for measuring equipment--Part 2: Guidelines for control of measurement processes
质量手册编制指南 Guidelines for developing quality manuals
质量管理和质量保证标准 第2部分: GB/T 19001、GB/T 19002和GB/T 19003实施通用指南 Quality management and quality assurance standards--Part 2: Generic guidelines for the application of GB/T 19001、GB/T 19002 and GB/T 19003
质量体系缩写中英文对照
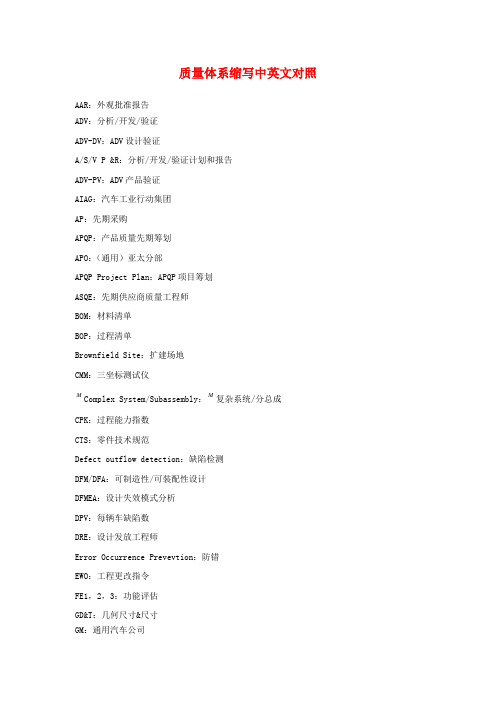
质量体系缩写中英文对照AAR:外观批准报告ADV:分析/开发/验证ADV-DV:ADV设计验证A/S/V P &R:分析/开发/验证计划和报告ADV-PV:ADV产品验证AIAG:汽车工业行动集团AP:先期采购APQP:产品质量先期筹划APO:(通用)亚太分部APQP Project Plan:APQP项目筹划ASQE:先期供应商质量工程师BOM:材料清单BOP:过程清单Brownfield Site:扩建场地CMM:三坐标测试仪M Complex System/Subassembly:M复杂系统/分总成CPK:过程能力指数CTS:零件技术规范Defect outflow detection:缺陷检测DFM/DFA:可制造性/可装配性设计DFMEA:设计失效模式分析DPV:每辆车缺陷数DRE:设计发放工程师Error Occurrence Prevevtion:防错EWO:工程更改指令FE1,2,3:功能评估GD&T:几何尺寸&尺寸GM:通用汽车公司GME:通用汽车欧洲分部GM9000:指QS9000GP:总体环节GPDS:全球产品描述系统GPS:全球采购系统GQTS:全球质量跟踪系统GR&R:量具旳反复性与再现性Greenfield Site:新建工厂GVDP:全球车辆开发工程IPTV:每千辆车缺陷数KCC:核心控制特性KCDS:核心特性批示系统Kiek-Off Meeting:启动会议KPC:核心产品特性LAO:(通用)拉丁美洲分部LCR:最低生产能力MCR:最大生产能力MOP:制造/采购MPC:物料生产控制MPCE:欧洲物料生产控制MRD:物料需求日期MSA:测量系统分析MVBns:非销售车制造验证MVBs:销售车制造验证NAO:(通用)北美分部NBH:停止新业务N.O.D:决策告知OEM:主机客户PAD:生产装配文献PC&L:生产控制&物流PDT:产品开发小组PFMEA:潜在失效模式分析PPAP:生产件批准程序PPM:1)项目采购经理2)每百万件旳产品缺陷数PPK:过程能力指数PQC:产品质量特性PR/R:问题报告及解决PSA:潜在供应商评审QSA:质量系统评审QTC:工装报价能力RASIC:负责、批准、支持、告知、讨论RFQ:报价规定RPN:风险顺序数RPN Reduction Plan:减少RPN值计划SDE:供应商开发工程师SFMEA:系统失效模式失效SMT:系统管理小组SOA:加速开始SOP:正式生产SOR:规定声明:SPC:记录过程控制SPO:(通用汽车)零件与服务分部SQ:供应商质量SQE:供应商质量工程师SQIP:供应商质量改善过程SSF:系统填充开始SSTS:分系统技术规范S.T.E.P:采购定点小组评估过程M Subcontractor:M分供方Team Feasibility Commitment:小组可行性承诺UG:UG工程绘图造型系统VDP:车辆开发过程VLE:车辆平台负责人WWP:全球采购序号缩写英文原文解释1 OTS overall tooling sample用批量生产旳工模器具制造出旳样件2 PVS Produktions – Versuchs - Serie 批量试生产3 TMA Trial Manufacturing Agreement 试制合同4 QSV Qualitaes-Sicherungs-Vereinbarung 质量保证合同5 BMG Bau-Muster-Genehmigung产品工程样件性能检查承认6 B- Freigabe 采购承认7 D- Freigabe 试制/0批量旳承认8 P- Freigabe 计划承认9 TL 技术资料汇编10 LH LastenHeft 规定汇总书11 Pflichtenheft 责任汇总书12 ME Markt-Einfuehrung 市场导入13 MIS Management Informations-System 管理信息系统14 Nullserie 零批量15 QPN Qualifizierungs-Programm Neuteile 新零件质量提高计划16 SOP Start-Of-Production 批量生产启动Standard Operating Procedure 原则操作程序17 QSR 质量体系规定18 APQP Adavanced part quality plan 高级产品质量计划19 PPAP product part approval procedure 生产件批准程序20 QSA 质量体系评审21 MSA measurement system analysis 测量系统分析22 FMEA 失效模式及成果分析23 SPC 记录过程控制QC(Quality Control)质量控制,就是质检,通俗说就是检查QA(Quality Assurance)QA中文全称:质量保证IPQC(In-Process Quality Control)品质管理项目制程检查IQC来料检查,就是原材料检查QC旳层次要比QA低,通俗来说就是检查员QA人员旳重要任务就是监督药物从原料进厂到成品出厂旳全过程旳质量;QC 就是对药物原料和成品旳所含重要成分进行检测,重要是给出原料和成品旳检测数据.在药厂QC比QA轻松一点,但QA不需要懂得仪器旳操作,只要懂得成品和原料旳指标,并用QC提供旳数据来判断原料和成品与否合格批准进厂或出厂.在液相中设立这个重要是为制药厂考虑旳,能减少诸多不必要旳反复工作.IQC 是来料控制,也就是进货检查OQC 是出货检查也就是出厂检查QC 是质量检查QA 指质量测试IPQC 制程控制PE 指制程工程师IE 指文献工程师-----------------------------------------------QC中文全称: 即英文QUALITY CONTROL旳简称,中文意义是品质控制,质量检查。
英文质量承诺书
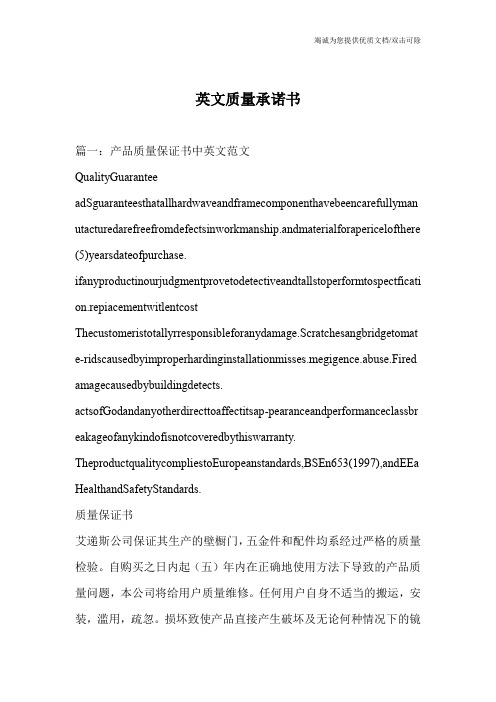
英文质量承诺书篇一:产品质量保证书中英文范文QualityGuarantee adSguaranteesthatallhardwaveandframecomponenthavebeencarefullyman utacturedarefreefromdefectsinworkmanship.andmaterialforapericelofthere (5)yearsdateofpurchase. ifanyproductinourjudgmentprovetodetectiveandtallstoperformtospectficati on.repiacementwitlentcost Thecustomeristotallyrresponsibleforanydamage.Scratchesangbridgetomat e-ridscausedbyimproperhardinginstallationmisses.megigence.abuse.Fired amagecausedbybuildingdetects. actsofGodandanyotherdirecttoaffectitsap-pearanceandperformanceclassbr eakageofanykindofisnotcoveredbythiswarranty. TheproductqualitycompliestoEuropeanstandards,BSEn653(1997),andEEa HealthandSafetyStandards.质量保证书艾递斯公司保证其生产的壁橱门,五金件和配件均系经过严格的质量检验。
自购买之日内起(五)年内在正确地使用方法下导致的产品质量问题,本公司将给用户质量维修。
任何用户自身不适当的搬运,安装,滥用,疏忽。
损坏致使产品直接产生破坏及无论何种情况下的镜面粉碎,均不在产品保修之列。
质量体系英文缩写
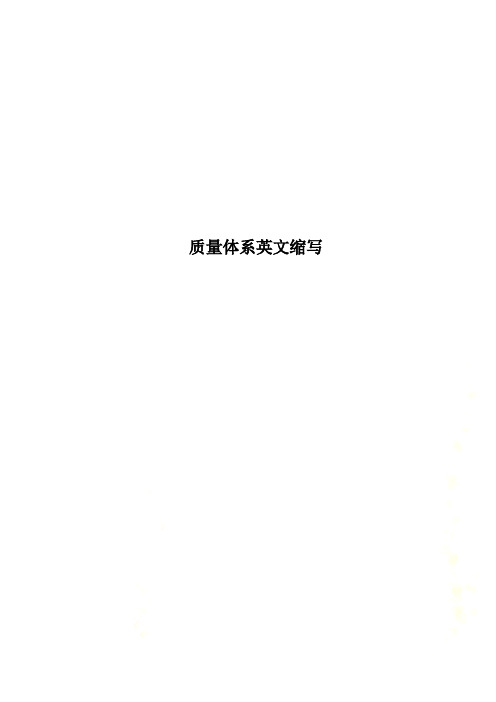
质量体系英文缩写1.PDCA:Plan、Do、Check、Action 策划、实施、检查、处置2.PPAP:Production PartApproval Process生产件批准程序3.APQP:Advanced ProductQuality Planning 产品质量先期策划4.FMEA:Potential FailureMode and Effects Analysis 潜在失效模式及后果分析5.SPC:Statistical ProcessControl统计过程控制6.MSA:Measurement SystemAnalysis 测量系统控制7.CP:Control Plan 控制计划8.QSA:Quality SystemAssessment 质量体系评定9.PPM:Parts Per Million 每百万零件不合格数10.QM:Quality Manua质量手册11.QP:Quality Procedure质量程序文件/Quality Planning质量策划/Quality Plan 质量计划12.CMK:机器能力指数13.CPK:过程能力指数14.CAD:Computer-AidedDesign 计算机辅助能力设计15.OEE:Overall Equipment Effectiveness 设备总效率16.QFD:Quality FunctionDeployment质量功能展开17.FIFO:First in, First out先进先出18.COPS:Customer OrientedProcesses顾客导向过程19.TCQ:Time、Cost、Quality时间、成本、质量20.MPS:Management Processes管理性过程21.SPS:Support Processes支持性过程22.TQM:Total QualityManagement全面质量管理23.PQA:Product QualityAssurance产品质量保证(免检)24.QP-QC-QI:质量三步曲,质量计划-质量控制-质量改进25.QAF:Quality AssuranceFile质量保证文件26.QAP:Quality AssurancePlan质量保证计划27.PFC:Process Flow Chart过程流程图28.QMS:Quality ManagementSystems质量管理体系29.JIT:Just In Time准时(交货)30.ERP:EnterpriseRequirement Planning企业需求计划31.QC:Quality Control 质量控制32.QA:Quality Audit 质量审核/QalityAssurance 质量保证33.IQC:In Come QualityControl 进货质量控制34.IPQC:In Process QualityControl 过程质量控制35.FQC:Final QualityControl 成品质量控制36.OQC:Out Quality Control 出货质量控制37.4M1E:Man、Machine、Material、Method、Environment人、机、料、法、环38.5W1H:Why、What、Who、When、Where、How 为何/做什么/谁做/时间/地点/如何做39.6S:Seiri、Seiton、Seiso、Seiketsu、Shitsuke、Safety 整理、整顿、清扫、清洁、素养、安全40.TRI值:Total Record Injury(三种)可记录工伤值41.SMART:精明原则,SpecificMeasurable Achievable Result Oriented Timed(具体的描述、可以测量的、可以通过努力实现的、有结果导向性的、有时间性的)——————企业常用英文缩写——————1.5S:5S管理2.ABC:作业制成本制度(Activity-BasedCosting)3.ABB:实施作业制预算制度(Activity-BasedBudgeting)4.ABM:作业制成本管理(Activity-BaseManagement)5.APS:先进规画与排程系统(AdvancedPlanning and Scheduling)6.ASP:应用程序服务供货商(ApplicationService Provider)7.ATP:可承诺量(Available ToPromise)8.AVL:认可的供货商清单(ApprovedVendor List)9.BOM:物料清单(Bill OfMaterial)10.BPR:企业流程再造(BusinessProcess Reengineering)11.BSC:平衡记分卡(BalancedScoreCard)12.BTF:计划生产(Build ToForecast)13.BTO:订单生产(Build To Order)14.CPM:要径法(Critical PathMethod)15.CPM:每一百万个使用者会有几次抱怨(Complaintper Million)16.CRM:客户关系管理(CustomerRelationship Management)17.CRP:产能需求规划(CapacityRequirements Planning)18.CTO:客制化生产(ConfigurationTo Order)19.DBR:限制驱导式排程法(Drum-Buffer-Rope)20.DMT:成熟度验证(DesignMaturing Testing)21.DVT:设计验证(DesignVerification Testing)22.DRP:运销资源计划(DistributionResource Planning)23.DSS:决策支持系统(DecisionSupport System)24.EC:设计变更/工程变更(EngineerChange)25.EC:电子商务(ElectronicCommerce)26.ECRN:原件规格更改通知(EngineerChange Request Notice)27.EDI:电子数据交换(ElectronicData Interchange)28.EIS:主管决策系统(ExecutiveInformationSystem)29.EMC:电磁相容(ElectricMagnetic Capability)30.EOQ:基本经济订购量(EconomicOrder Quantity)31.ERP:企业资源规划(EnterpriseResource Planning)32.FAE:应用工程师(FieldApplication Engineer)33.FCST:预估(Forecast)34.FMS:弹性制造系统(FlexibleManufacture System)35.FQC:成品质量管理(Finish orFinal Quality Control)36.IPQC: 制程质量管理(In-ProcessQuality Control)37.IQC:进料质量管理(IncomingQuality Control)38.ISO:国际标准组织(InternationalOrganization forStandardization)39.ISAR:首批样品认可(InitialSample Approval Request)40.JIT:实时管理(Just In Time)41.KM:知识管理(KnowledgeManagement)42.L4L:逐批订购法(Lot-for-Lot)43.LTC:最小总成本法(Least TotalCost)44.LUC:最小单位成本(Least UnitCost)45.MES:制造执行系统(ManufacturingExecution System)46.MO:制令(Manufacture Order)47.MPS:主生产排程(MasterProduction Schedule)48.MRO:请修(购)单(MaintenanceRepair Operation)49.MRP:物料需求规划(MaterialRequirement Planning)50.MRPII:制造资源计划(ManufacturingResource Planning)51.NFCF:更改预估量的通知Notice forChanging Forecast52.OEM:委托代工(OriginalEquipment Manufacture)53.ODM:委托设计与制造(OriginalDesign & Manufacture)54.OLAP:在线分析处理(On-LineAnalytical Processing)55.OLTP:在线交易处理(On-LineTransaction Processing)56.OPT:最佳生产技术(OptimizedProduction Technology)57.OQC:出货质量管理(Out-goingQuality Control)58.PDCA:PDCA管理循环(Plan-Do-Check-Action)59.PDM:产品数据管理系统(ProductData Management)60.PERT:计划评核术(ProgramEvaluation and Review Technique)61.PO:订单(Purchase Order)62.POH:预估在手量(Product onHand)63.PR:采购申请(PurchaseRequest)64.QA:品质保证(QualityAssurance)65.QC:质量管理(Quality Control)66.QCC:品管圈(Quality ControlCircle)67.QE:品质工程(QualityEngineering)68.RCCP:粗略产能规划(Rough CutCapacity Planning)69.RMA:退货验收(ReturnedMaterial Approval)70.ROP:再订购点(Re-Order Point)71.SCM:供应链管理(Supply ChainManagement)72.SFC:现场控制(Shop FloorControl)73.SIS:策略信息系统(StrategicInformation System)74.SO:订单(Sales Order)75.SOR:特殊订单需求(Special OrderRequest)76.SPC:统计制程管制(StatisticProcessControl)77.TOC:限制理论(Theory ofConstraints)78.TPM:全面生产管理(TotalProduction Management)79.TQC:全面质量管理(Total QualityControl)80.TQM:全面品质管理(Total QualityManagement)81.WIP:在制品(Work In Process)——————部门名称的专有名词——————QS:Quality system品质系统CS:Coutomer Sevice 客户服务QC:Quality control品质管理IQC:Incoming quality control 进料检验LQC:Line Quality Control 生产线品质控制IPQC:In process quality control 制程检验FQC:Final quality control 最终检验OQC:Outgoing quality control 出货检验QA:Quality assurance 品质保证SQA:Source(supplier) Quality Assurance 供应商品质保证(VQA)CQA:Customer Quality Assurance客户质量保证PQA rocess Quality Assurance 制程品质保证QE:Quality engineer 品质工程CE:component engineering零件工程EE:equipment engineering设备工程ME:manufacturing engineering制造工程TE:testing engineering测试工程PPE roduct Engineer 产品工程IE:Industrial engineer 工业工程ADM: Administration Department行政部RMA:客户退回维修CSDI:检修PC:producing control生管MC:mater control物管GAD: General Affairs Dept总务部A/D: Accountant /Finance Dept会计LAB: Laboratory实验室DOE:实验设计HR:人资PMC:企划RD:研发W/H:仓库SI:客验PD: Product Department生产部PA:采购(PUR: Purchaing Dept)SMT:Surface mount technology 表面粘着技术MFG:Manufacturing 制造MIS:Management information system 资迅管理系统DCC:document control center 文件管制中心——————场内作业中的专有名词——————QT:Quality target品质目标QP:Quality policy目标方针QI:Quality improvement品质改善CRITICAL DEFECT:严重缺点(CR)MAJOR DEFECT:主要缺点(MA)MINOR DEFECT:次要缺点(MI)MAX:Maximum最大值MIN:Minimum最小值DIA iameter直径DIM imension尺寸LCL:Lower control limit管制下限UCL:Upper control limit管制上限EMI:电磁干扰ESD:静电防护EPA:静电保护区域ECN:工程变更ECO:Engineering change order工程改动要求(客户)ECR:工程变更需求单CPI:Continuous Process Improvement 连续工序改善Compatibility:兼容性Marking:标记DWG rawing图面Standardization:标准化Consensus:一致Code:代码ZD:Zero defect零缺点Tolerance:公差Subject matter:主要事项Auditor:审核员BOM:Bill of material物料清单Rework:重工ID:identification识别,鉴别,证明PILOT RUN: (试投产)FAI:首件检查FPIR:First Piece Inspection Report首件检查报告FAA:首件确认SPC:统计制程管制CP: capability index(准确度)CPK: capability index of process(制程能力) PMP:制程管理计划(生产管制计划)MPI:制程分析DAS efects Analysis System 缺陷分析系统PPB:十亿分之一Flux:助焊剂P/N:料号L/N:Lot Number批号Version:版本Quantity:数量Valid date:有效日期MIL-STD:Military-Standard军用标准ICT: In Circuit Test (线路测试)ATE:Automatic Test Equipment自动测试设备MO: Manafacture Order生产单T/U: Touch Up (锡面修补)I/N:手插件P/T:初测F/T: Function Test (功能测试-终测)AS 组立P/K:包装TQM:Total quality control全面品质管理MDA:manufacturing defect analysis制程不良分析(ICT)RUN-IN:老化实验HI-pot:高压测试FMI:Frequency Modulation Inspect高频测试DPPM: Defect Part Per Million(不良率的一种表达方式:百万分之一) 1000PPM 即为0.1%Corrective Action: (CAR改善对策)ACC:允收REJ:拒收S/S:Sample size抽样检验样本大小SI-SIV:Special I-Special IV特殊抽样水平等级CON:Concession / Waive特采ISO:国际标准化组织ISA:Industry Standard Architecture工业标准体制结构OBA:开箱稽核FIFO:先进先出PDCA:管理循环Plan do check action计划,执行,检查,总结WIP:在制品(半成品)S/O: Sales Order (业务订单)P/O: Purchase Order (采购订单)P/R: Purchase Request (请购单)AQL:acceptable quality level允收品质水准LQL;Limiting quality level最低品质水准QVL:qualified vendor list合格供应商名册AVL :认可的供货商清单(Approved Vendor List)QCD: Quality cost delivery(品质,交期,成本)MPM:Manufacturing project management制造专案管理KPI:Key performance indicate重要绩效指标MVT:Manufacturing Verification Test制造验证试产Q/R/S:Quality/Reliability/Service质量/可靠度/服务STL:ship to line(料到上线)NTF:No trouble found误判CIP:capacity improvement plan(产能改善计划)MRB:material review board(物料审核小组)MRB:Material reject bill退货单JIT:just in time(即时管理)5S:seiri seiton seiso seiketsu shitsuke (整理,整顿,清扫,清洁,修养)SOP:standard operation process(标准作业程序)SIP:Specification inspection process制程检验规格TOP: Test Operation Process (测试作业流程) WI: working instruction(作业指导书)SMD:surface mounting device(表面粘着原件)FAR:failure aualysis report故障分析报告CAR:Corrective action report改善报告BPR:企业流程再造(Business Process Reengineering)ISAR :首批样品认可(Initial Sample Approval Request)-JIT:实时管理 (Just In Time)QCC :品管圈 (Quality Control Circle) Engineering Department (工程部)TQEM: Total Quality Environment Management (全面品质环境管理)PD: Production Department (制造)LOG: Logistics (后勤支持)Shipping: (进出口)AOQ:Average Output Quality平均出货质量AOQL:Average Output Quality Level平均出货质量水平FMEA:failure model effectiveness analysis 失效模式分析CRB: Change Review Board (工程变更会议) CSA:Customer Simulate Analysis客户模拟分析SQMS:Supplier Quality Management System 供应商品质管理系统QIT: Quality Improvement Team 品质改善小组QIP:Quality Improvement Plan品质改善计划CIP:Continual Improvement Plan持续改善计划M.Q.F.S: Material Quality Feedback Sheet (来料品质回馈单)SCAR: Supplier Corrective Action Report (供货商改善对策报告)8D Sheet: 8 Disciplines sheet ( 8D单) PDCA:PDCA (Plan-Do-Check-Action) (管理循环)MPQ: Material Packing Quantity (物料最小包装量)DSCN: Delivery Schedule Change Notice (交期变更通知)QAPS: Quality Assurance Process Sheet (品质工程表)DRP :运销资源计划 (Distribution Resource Planning)DSS:决策支持系统 (Decision Support System) EC :电子商务 (Electronic Commerce)EDI :电子资料交换(Electronic Data Interchange)EIS :主管决策系统 (Excutive Information System)ERP:企业资源规划 (Enterprise Resource Planning)FMS :弹性制造系统 (Flexible Manufacture System)KM :知识管理 (Knowledge Management)4L :逐批订购法 (Lot-for-Lot)LTC :最小总成本法 (Least Total Cost) LUC :最小单位成本 (Least Unit Cost)MES :制造执行系统(Manufacturing Execution System)MPS :主生产排程(Master Production Schedule)MRP :物料需求规划 (Material Requirement Planning)MRPⅡ:制造资源计划(Manufacturing Resource Planning)OEM :委托代工(Original Equipment Manufacture)ODM :委托设计与制造 (Original Design & Manufacture)OLAP:线上分析处理(On-Line Analytical Processing)OLTP:线上交易处理 (On-Line Transaction Processing)OPT :最佳生产技术 (Optimized Production Technology)PDCA:PDCA管理循环 (Plan-Do-Check-Action) PDM:产品数据管理系统(Product Data Management))RCCP:粗略产能规划(Rough Cut Capacity Planning)SCM :供应链管理 (Supply Chain Management) SFC :现场控制 (Shop Floor Control) TOC:限制理论 (Theory of Constraints) TQC :全面品质管制 (Total Quality Control) FYI/R:for your information/reference仅供参考ASAP:尽快S/T:Standard time标准时间TPM:total production maintenance:全面生产保养ESD Wrist strap:静电环IT:information technology信息技术,资讯科学CEO:Chief Executive Officer执行总裁COO:Chief Operaring Officer首席业务总裁SWOT:Strength,Weakness,Opportunity,Threat 优势﹐弱点﹐机会﹐威胁Competence:专业能力Communication:有效沟通Cooperation:统御融合Vibration Testing:振动测试IDP:Individual Development Plan个人发展计划MRP:Material Requirement Planning物料需求计划MAT'S:Material材料LRR:Lot Rejeet Rate批退率ATIN:Attention知会3C:Computer ,Communication , Consumer electronic消费性电子5W1H:When , Where , Who , What , Why , Ho 5M: Man , Machine , Material , Method , Measurement人,机器,材料,方法,测量4MIE:Man,Material,Machine,Method,Environment人力,物力,财务,技术,时间(资源)7M1I: Manpower , Machine , Material , Method, Market , Management , Money , Information 人力,机器,材料,方法, 市场,管理,资金,资讯Accuracy 准确度Action 行动Activity 活动Analysis Covariance 协方差分析Analysis of Variance 方差分析Approved 承认Attribute 计数值Average 平均数Balance sheet 资产负债对照表Binomial 二项分配Brainstorming Techniques 脑力风暴法Cause and Effect Matrix 因果图(鱼骨图) CL:Center Line 中心线Check Sheets 检查表Complaint 投诉Conformity 合格(符合)Control 控制Control chart 控制(管制)图Correction 纠正Correlation Methods 相关分析法CPI: continuouse Process Improvement 连续工序改善Cross Tabulation Tables 交叉表CS: Customer Sevice 客(户)服(务)中心 DSA: Defects Analysis System 缺陷分析系统 Data 数据 Description:品名DCC: Document Control Center 文控中心Decision 决策、判定Defects per unit 单位缺点数Description 描述Device 装置Do 执行DOE: Design of Experiments 实验设计Element 元素Engineering recbnology 工程技Environmental 环境Equipment 设备Estimated accumulative frequency 计算估计累计数E Equipment Variation 设备变异External Failure 外部失效,外部缺陷FA: Failure Analysis 失效分析Fact control 事实管理Fatigue 疲劳FMEA: Failure Mode and Effect Analysis失效模式与效果分析FP First-Pass Yield (第一次通过)合格率 FQA: Final Quality Assurance 最终品质保证 FQC: Final Quality control 最终品质控制 Gauge system 测量系统Grade 等级Histogram 直方图Improvement 改善Initial review 先期审查Inspection 检验Internal Failure 内部失效、内部缺陷IPQC: In Process Quality Control 制程品质控制IQC: Incomming Quality Control 来料品质控制IS International Organization for Standardization 国际标准化组织LCL: Lower Control limit 管制下限LQC: Line Quality Control 生产线品质控制 LSL: Lower Size Limit 规格下限Machine 机械Manage 管理Materials 物料Measurement 测量Median 中位数MSA: Measurement System Analysis 测量系统分析Occurrence 发生率Operation Instruction 作业指导书Organization 组织Parto 柏拉图PPM arts per Million (百万分之)不良率 Plan 计划Policy 方针Population 群体PQA: Process Quality Assurance 制程品质保证Practice 实务(践)Prevention 预防Probability 机率Probability density function 机率密度函数 Procedure 流程Process 过程Process capability analysis 制程能力分析(图)Process control and Process capability制程管制与制程能力Product 产品Production 生产Projects 项目QA: Quality Assurance 品质保证QC: Quality Control 品质控制QE: Quality Engineering 品质工程QFD: Quality Function Desgin 品质机能展开(法)Quality 质量Quality manual 品质手册Quality policy 品质政策(质量方针)Random experiment 随机试验Random numbers 随机数R:Range 全距(极差)Reject 拒收Repair 返修Repeatusility 再现性Reproducibility 再生性Requirement 要求Responsibilities 职责Review 评审Reword 返工Rolled yield 直通率RPN: Risk Priority Number 风险系数Sample 抽样,样本Sample space 样本空间Sampling with replacement 放回抽样Sampling without replacement 不放回抽样Scatter diagram 散布图分析Scrap 报废Simple random sampling 简单随机取样Size 规格SL: Size Line 规格中心线Stratified random sampling 分层随机抽样SOP: Standard Operation Procedure 标准作业书SPC: Statistical Process Control 统计制程管制Specification 规范SQA: Source(Supplier) Quality Assurance 供货商品质保证Stage sampling 分段随机抽样Standard Deviation 标准差Sum of squares 平方和Taguchi-method 田口(试验)方法Theory 原理TQC: Total Quality Control 全面品质控制TQM: Total Quality Management 全面品质管理Traceablity 追溯Training 培训UCL: Upper Control Limit 管制(控制)上限USL: Upper Size Limit 规格上限Validation 确认Variable 计量值Verification 验证Version 版本VOC: Voice of Customer 客户需求VOE: Voice of Engineer 工程需求Inventory stock report:庫存清单报告Sales order report:出货报告。
质量保证协议-英文版
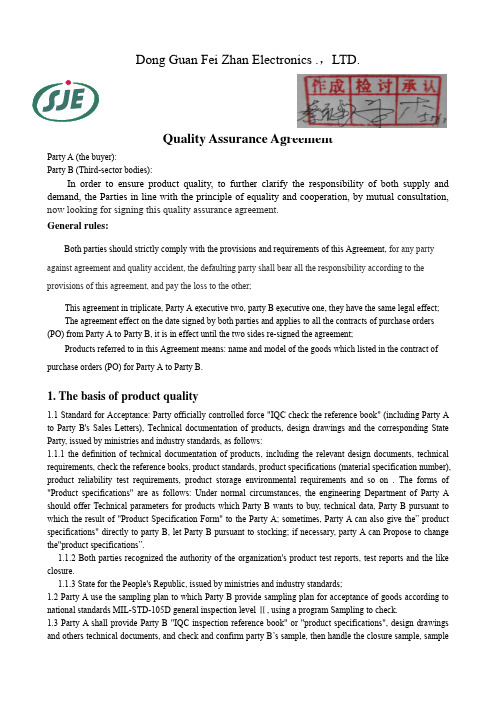
Quality Assurance AgreementParty A (the buyer):Party B (Third-sector bodies):In order to ensure product quality, to further clarify the responsibility of both supply and demand, the Parties in line with the principle of equality and cooperation, by mutual consultation, now looking for signing this quality assurance agreement.General rules:Both parties should strictly comply with the provisions and requirements of this Agreement, for any party against agreement and quality accident, the defaulting party shall bear all the responsibility according to the provisions of this agreement, and pay the loss to the other;This agreement in triplicate, Party A executive two, party B executive one, they have the same legal effect;The agreement effect on the date signed by both parties and applies to all the contracts of purchase orders (PO) from Party A to Party B,it is in effect until the two sides re-signed the agreement;Products referred to in this Agreement means: name and model of the goods which listed in the contract of purchase orders (PO) for Party A to Party B.1. The basis of product quality1.1 Standard for Acceptance: Party officially controlled force "IQC check the reference book" (including Party A to Party B's Sales Letters), Technical documentation of products, design drawings and the corresponding State Party, issued by ministries and industry standards, as follows:1.1.1 the definition of technical documentation of products, including the relevant design documents, technical requirements, check the reference books, product standards, product specifications (material specification number), product reliability test requirements, product storage environmental requirements and so on . The forms of "Product specifications" are as follows: Under normal circumstances, the engineering Department of Party A should offer Technical parameters for products which Party B wants to buy, technical data, Party B pursuant to which the result of "Product Specification Form" to the Party A; sometimes, Party A can also give the” product specifications" directly to party B, let Party B pursuant to stocking; if necessary, party A can Propose to change the"product specifications”.1.1.2 Both parties recognized the authority of the organization's product test reports, test reports and the like closure.1.1.3 State for the People's Republic, issued by ministries and industry standards;1.2 Party A use the sampling plan to which Party B provide sampling plan for acceptance of goods according to national standards MIL-STD-105D general inspection level , usingⅡ a program Sampling to check.1.3 Party A shall provide Party B "IQC inspection reference book" or "product specifications", design drawings and others technical documents, and check and confirm party B’s sample, then handle the closure sample, sampleletters is one of the criteria for dealing with product quality .1.4 Party A under this Agreement Article 1.1 and Article 1.2 of the product acceptance criteria for incoming inspection, if testing is uunqualified,IQC issued a "quality of measures to form an exception", according to paragraph 9.3.1 of the protocol processing.1.5 When Party A Continuously Check three batches of failed inspection, Party A issued a notice to suspend delivery to Party B, Party A under the circumstances, decide whether to stop supply, deal with according to Section 8.4 of this Agreement.1.6 In order to ensure the management of products of Party A, Party A request Party B to provide the product packaging should meet the following requirements:Inner Packing: There are products inspection reports, indicating the product type, party materials, number, date of production.Outer Packing: carton identification must contain the following content ----- product name, type, quantity, date, material manufacturers and party number. The security for critical parts or pieces of material to be identified by Party A. Party B should designate the outer side packing of specified safety components or key pieces of signs. For example: Environmental RoHS marking, anti-static ESD marking and so on.1.7 The contract for Party B for the product, if the party A find that in the discovery and specification does not match the content specified in the right to refuse to receive, and withdraw all or part of the relevant order. In this case, Party A can look as there is no delivery of goods from party B.1.8 The products should be examined after Party B delivered to Party A. Party A have Objection to the product shall be received within 15 working days after the received the brand , this objection is not affected by the end of testing, which does not affect the effectiveness of the quality of opposition that Party A use in the production of products made from party B and the effectiveness of the quality of opposition after repairing returned to the factory that from Party B’s products when using the products in the market, Party B is obligated to challenge the part of the Party A to be replaced, repairs, returns, such as the product of the existence of defects in all or part of the subject can not properly use , Return to the B Party A has the right to request compensation for the corresponding from party B.2. The product testing requirements and spare parts2.1 Party A tests the products from party B under the acceptance criteria, and product technical documentation (1.1 and 1.2 requirements).3. The products quality control of raw materials3.1 If Party B is as contracts for the supply of product manufacturers for party B, then:3.1.1 Party B shall be determined to establish the system of raw materials, auxiliary products for the Party A of raw materials to be used in the implementation of identified and fixed supply, both sides should confirm the production of qualified materials for the manufacturers of the existing situation, and establish the vendor files.3.1.2 Party B need to change the supply of raw materials manufacturers for some reason, shall notify Party A and provide the appropriate factory or neutral bodies such as inspection reports and sample data to Party A, recognized as qualified by the party A before we can carry out the changes. Unauthorized changes without Party A approval of raw materials, all the consequences caused by this and Party B shall be borne entirely.3.1.3 Party B shall strictly inspect incoming of raw materials, inspect to establish and preserve the original records, the quality of the material suppliers to track assessment, and establish the quality of the file.3.1.4 Party B shall implement raw materials using "FIFO" batch management system, extended the material is strictly prohibited.3.1.5 For the above, the Party A have rights to inspect the implementation of the Party B, and to conformity assessment, if not comply, Party A shall have the right to Punish party B, such as punitive measures.3.2 Party B is the middlemen for supply the products according to the contract, Party B shall supervise and ensurethat manufacturers fulfill the above requirements on quality control of raw materials; otherwise, Party A shall be entitled to section 3.1.5 of this Agreement to exercise for the provisions of party B’s power.3.3 Party B provide products according to the contact that the samples of raw materials must comply with the Party A or the Party A designate the major raw material suppliers and brands, specific requirements are as follows:4. The production process quality control4.1 If Party B is the supply of product manufacturers as contracts, then:4.1.1 Party B shall perfect the production process control and management, need to develop the production process control documentation and work instructions, etc., establish the necessary quality control points in the final affect product quality critical manufacturing processes, all quality control points party B shall set the person responsible for the original records and statistics do strictly monitor the process quality and product quality, timely detection and correction of irregularities of the production process to ensure consistency of product quality and stability.4.1.2 Party B shall be completely controlled the production, if out of control, it is timely to take corrective measures to identify the cause and take the initiative to notify Party A to take the appropriate measures, otherwise all the consequences borne entirely by the party B.4.1.3 Party A has the right to supervise the investigation, and the conformity assessment, on the effectiveness of the implementation does not meet party A, Party A pointed out that, Party B shall timely and effective rectification, correction or rectification of the situation is not without meet the requirements of Party A, Party A may terminate the supply relationship.4.2 Party B is the middlemen as the contact, Party B shall supervise and ensure that manufacturers fulfill the above provisions of the production process quality control, otherwise the buyer has right to terminate the supplier relationship.5. The level of quality control of product qualification5.1 The employee shall submit a monthly settlement batch of products pass rate ≥98%, for three consecutive times (including three) or more less than the required level of qualified and with no effective corrective measures, Party A has right to suspend Party B’s goods or impose financial penalties accordingly to party B.5.2 Party B or part B ensure that manufacturers in the key process in the product should be set up the personnel or automated equipment for the effective testing (full inspection or sampling) station.5.3 the quality inspection departments for party B in the acceptance of its products, the level of acceptable quality should be higher than the level of party A acceptance of a level of quality products ,for Party A under this Agreement when the requirements of Article 1.7, Party B shall truthfully provide product inspection reports .5.4 Party B shall stock products in more than three months in the normal procedures to re-test. When the product has overdue three months that party A can not be recognized, Party A shall be deemed to fail treatment.5.5 Party B for the production in the process of using, when the Party B for the product defect rate exceeds the quality level of qualified agreement, Party A shall promptly report to the quality information feedback, while providing the defective for party B analysis, party B after receiving the feedback information must respond in 4 hours, within 3 working days to submit an analytical report to the Party A, if necessary, both parties can identify effective measures to correct the common party.5.6 Party B shall ensure that no accidents about mixing and less material occur, the mixing accident will be disqualified, and thus causing loss to the Party A will deal with Article 9 of this Agreement. Settlement examination of less material issues, the Party A will charge as small amount of cross-delivery processing. The process of using less material problems, the Party A will deal with as less the actual proportion of the claim or the actual number of claims expected manner.6. The product cycle test and reliability test6.1 Party B or Party B through manufacturers must strictly follow the standards of this Section 1.1, periodic testsand reliability tests. Party B shall provide at least quarterly to more than one relevant test reports. Party A has requested, the test should be carried on neutral country or the laboratory of authority.6.2 As soon as Party B find the products have effect on the reliability of any hidden dangers exist, it shall promptly notify to Party A and with Party A promptly working out remedial measures.6.3 If Party A found hidden failure in the course of early failure or mid-term, the party A shall timely information back to Party B, Party B analysis immediately after receiving the information, identify the reasons for developing remedial measures to shall submit a written report to party A.6.4 products offered by party B under the relevant testing facilities, due to quality problems caused by Party B for all losses borne entirely by the party B.6.5 For party B’s Reliability caused to Party A’s loss, Party B shall bear all.7. design, technology, technical performance change control7.1 identified bulk supply of products for Party B from Party A, can not own or through the manufacturer free to change the design, engineering, and installation of the main technical parameters Dimensions and so on. If you do need to change, must notify the Party A, and to test and submit test reports and samples after the change, give "product specifications" to the owner recognized as qualified by the party only after the delivery, or Party B shall bear all the losses all.7.2 after the program changed; both sides should be incorporated into the document management.8. The quality of feedback8.1 Party A to Party B's delivery of incoming inspection, if meet the failure batch, party A should carry out, "quality Exception Notice" concurrent "return list" with substandard goods to party B, for party B to sign.8.2 Party B received the feedback in 4 hours should respond and complete the analysis, processing and quality to the Party to provide a written report of analysis and rectification within 3 working days, before the quality issue is not properly handled, Party A may suspend depending on the circumstances require Party B to supply.8.3 Party B failed to after improve the products for three batches, Party A has right to cancel the supply status for party B, and Party B shall bear the result of all the losses related to delivery.8.4 Party A should make a comprehensive evaluation of the quality of information and feedback about the quality of party B each year.8.5 Both sides should have someone responsible for the quality of feedback processing.9. Quality assurance and liability arising9.1 General requirements of quality assurance9.1.1 Party B shall ensure strict accordance with the ISO9000/14001 quality and environmental management system similar to the agreement, both sides recognized standards for production and management.9.1.2 Party B shall ensure that the quality of products and accessories for compliance with national standards, industry standards or industry practice and in accordance with the agreement of the contract, the product is new and never used (due to owner required or used to test the product the exception). In addition, party B’s basic shipment inspection, shipment inspection items and methods in accordance with the Party's "IQC inspection reference book" or a specification implementation.9.1.3 Product performance, specifications, quality requirements should be consistent with the use of party A request.9.1.4 The technical performance and product specifications described in detail in the manual. If Party B and PartyA have not reached relevant agreement, the product specification will use the product specifications of Party A.9.1.5 Party B as the product manufacturer according the contract for the supply, party A has right to prior notice to Party B, to test party B in the statutory working on their production processes, quality management system, the production quality on-site inspections can also be used on the B sample and other methods of quality and delivery of products to investigate the situation. During the inspections, if Party B did not meet in some companies thequality requirements of Party A, Party B shall immediately and unconditionally take appropriate remedial and improvement measures; eventually reach the required quality standards of Party A.9.1.6 Party B must commit to their product specifications for the product and the content described in the agreement, and its products have no flawless in design, materials, and workmanship.9.2 free of charge to ensure that the responsibility (product quality assurance period)9.2.1 When party B line of products, reference check, and to the Party identified the following products in the Party within 18 months after shipment or Party B's product manufactured using the products submitted to the hands of customers after within the 12 months between the two earlier period, when the product was sentenced tomorrow for the Party B does not meet specifications, defective party B should be fully compensated and the resulting loss.9.2.2 Party B shall ensure that immediately after receiving the return to take remedial measures, such as: repair, replace, redo, return and other measures.9.3 Treatment of non-conforming product9.3.1 Failed to pass incoming inspection Ordnance Disposal:A) Party A to Party B provide the product acceptance, if unqualified, Party A shall maintain physical and inform Party B, Party B should verify or put forward opinions immediately after receiving the notice and to identify the reasons and take corresponding measures. Party B shall reply relevant observations within 4 hours, not respondents Party B shall unconditionally accept the return processing,B) Inspection of incoming batches of substandard goods, in principle, the whole batch back to Party B, Party A must use the urgent need for the special mining deal, agreed by Party A, Party B may allow the location of Party A special mining deal processing, and then a second inspection to Party A (Heavy batch B boxes and packing must be clearly marked on the delivery note), in particular on the principles adopted by the Party to complete, entrust Party B to handle Party A's working hours according to the actual cost of processing fee (according to 42 Yuan RMB / person * hours to calculate.)C) "party a" for "party b" special mining the quality problem of the use of part and in the same state repeatedly supply, "party a" shall have the right to according to a certain ratio reduced the price of product, the "party b" not to raise an objection, reduced ratio according to the purchase of 5-20% for degradation process.9.3.2 deal with the process failed.The failure occurred under normal use; Party B shall be responsible for analysis and returned.9.4 nonconforming approach9.4.1 Party A in the incoming inspection, if a shipment tests failure, Party A shall notify Party B, Party B shall give reply within 4 hours. In the case, Party A can select one from the following treatment:A) Return;B) To the Party A by the Party B to conduct the inspection;C) Qualified by the Party A to receive, return defective productsD) by mutual agreement, Party A Party B commissioned special mining all seized materials, the party pays full inspection labor costs and related costs (including staff salaries by 42 Yuan RMB / person * hour basis), costs from Party B deducted from the purchase price, all seized by the Party A after receiving qualified product.9.5 Punishment and Improvement9.5.1 Party B has been determined to take responsibility and a related cost, Party A has right to choose one of the following methods:A) Replacement of defective products, B) repair of defective products, C) the purchase price to return defective products, D) penaltiesA) Replacement of defective productsParty B shall receive written notice within 1 business day replacement of defective products, and transported tothe party designated place of delivery. The time spent for the delivery by, the Party B shall bear all costs.B) Repair of defective productsParty B shall receive written notice within one working day repair defective products.C) The purchase price to return defective productswhen party A required returning defective product payment, Party B shall purchase the amount of defective items until the occurrence of place of delivery until pay the full cost method specified by Party A.D) penaltiesD-1) Party B constitutes a major quality accidents to Party A’s Company (including the Party A customer claims and punishment), liability related to the actual Party B In addition to compensation for all losses (including direct economic losses and indirect economic losses) outside, in addition to a 1000 - 10,000 Yuan RMB penalty.D-2) such as online quality issues due to party B three times with same quality and no follow-up to Party A grant to improve the effect of withdrawal, or within the specified time is not in time, seriously affecting the delivery for party A and impose a per B 1000-5000 RMB punishment to party B.D-3) Party B for Heavy Goods Party submission was approved back three times, seriously affecting the delivery for party A and impose a penalty party B RMB 1000-5000 Yuan.D-4) Party B consecutive three month of serious complaints of quality problems, improve the effect is not obvious or does not improve, to cancel its supplier qualification.D-5) party B unauthorized changes to key materials and technology parameters and the sample does not match the Party acknowledged, without prior written notice to Party A, seriously affecting the quality of party products, and impose penalties for party B 2000-10000 Yuan RMB.D-6) productions by Party A urgently needed materials for the failure of tolerance need to use special mining, processing according to9.4.19.5.4 To prevent the recurrence of defective productsAccording to test results of Party A of the purchase in the product warranty period the product is found to have any adverse, and it is necessary to determine and notify Party B, Party B or Party B by manufacturers to be on the manufacture of products or manufacturing processes, not the goods, products should be examined to ensure that the goods delivered to the Party will not happen again similar to the poor. Party B or party B by the same time manufacturers analyzes the reasons for its poor, research, and to take to prevent a recurrence of temporary and long-term measures, and report to party A.9.5.5 Quality of diagnosisA) Party A needed, on the Party B's quality control system, control procedures and products together with the B-site inspection, and based on the results of the necessary guidance and suggestions for improvement.B) Party B for the above recommendations for improvement must quickly work out improvement measures and report to Party A after the implementation and results.9.6 manufacturing, materials and design changes9.6.1 Party B or Party B by manufacturer specifications for the main material change to make changes to the materials, or other design changes must be approved in writing by Party A in accordance with the method indicated by the Party A.9.6.2 Party B or Party B changes by manufacturers in the production of material must be presented prior written notice to Party A, in obtaining recognition from Party A, then changes.9.6.3 Without the written consent of Party A, Party B or Party B by unilateral manufacturers manufacturing, material specifications, materials, materials and design changes to address this for all damage caused to the party liable. And party A has right to reject the goods, until the abolition of subsequent orders.9.6.4 Party A shall have the right to Party B based on the actual situation on the product specifications for the proposed change or amendment to a reasonable request, to the material change notice issued by Party B, Party Bshall, after receipt of the notice reply within 1 working day or propose amendments to the program, and excessive use of material handling consultation program. If Party B refuses to reply or refuse to propose amendments to the program and cause the loss of Party, then Party B shall bear all the losses.10. Other10.1 Both sides should strictly abide by the provisions of this Agreement, the terms and requirements of thedefaulting party should bear its full responsibility for causing the accident, and in accordance with the Society's request for damages.10.2 Both sides for business generated delivery notes, correspondence and other documents relating toproduct quality issues in the formulation as inconsistent with this Agreement, this Agreement shall prevail.10.3 The Agreement interpretation belongs to the party B’S Quality Department.10.4 The Agreement and the "procurement contract" have the same legal effect.Party A: Dong Guan Fei Zhan Electronics .,LTD.Legal representative (or authorized representative):Date:Party B:Legal representative (or authorized representative):Date:。
质量保证书英文范本
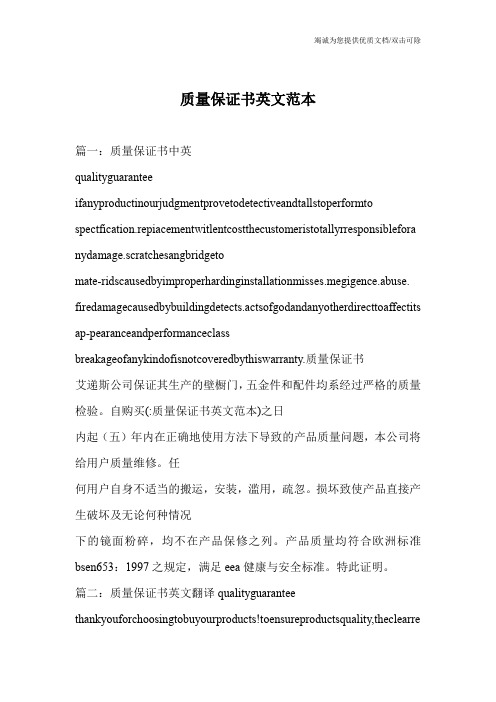
质量保证书英文范本篇一:质量保证书中英qualityguarantee ifanyproductinourjudgmentprovetodetectiveandtallstoperformto spectfication.repiacementwitlentcostthecustomeristotallyrresponsiblefora nydamage.scratchesangbridgetomate-ridscausedbyimproperhardinginstallationmisses.megigence.abuse. firedamagecausedbybuildingdetects.actsofgodandanyotherdirecttoaffectits ap-pearanceandperformanceclass breakageofanykindofisnotcoveredbythiswarranty.质量保证书艾递斯公司保证其生产的壁橱门,五金件和配件均系经过严格的质量检验。
自购买(:质量保证书英文范本)之日内起(五)年内在正确地使用方法下导致的产品质量问题,本公司将给用户质量维修。
任何用户自身不适当的搬运,安装,滥用,疏忽。
损坏致使产品直接产生破坏及无论何种情况下的镜面粉碎,均不在产品保修之列。
产品质量均符合欧洲标准bsen653:1997之规定,满足eea健康与安全标准。
特此证明。
篇二:质量保证书英文翻译qualityguarantee thankyouforchoosingtobuyourproducts!toensureproductsquality,theclearresponsibilityofbuyerandseller,andtheproductsafety,wemakethefollowingpromise:second,thesupplierprovide sthecopyofbusinesslicensewithofficialsealstampedtothebuyer.third,thesupplierprovidesthecopyofthetechnicalspecoftheproductswith officialsealstampedtothebuyer.fifth,thesupplierensuresthatthepackagingan dregisteredtrademarkofthe productsmatchtherelevantstateregulation.sixth,thestorageandsafekeepingc onditionisindicatedontheproductpackage, toensuretheproductqualitythebuyerhastostrictlyfollowit,orisresponsible forthecausedqualityproblem.eighth,thetreatmentofthequalitydispute:thebu yershouldstrictlyobservethetechnicalstandardsshippedwiththe supplierproductsforinspection,ensurefairandsciencetesting.theremaining samplesfailtopasstheexaminationshouldbekeptforoneweek.incaseoftheind eedqualityproblemofthesupplierproducts,thebuyerand sellernegotiatetodealwiththeunusedproducts.ninth,theproductguaranteesin cebothsidessignasupplycontractanddeliveryoccurs,terminatesatthesametimeasthebusinessends.篇三:住宅质量保证书中英文版(中英文已改)太原星河湾(二号园)住宅质量保证书星河湾住宅质量保证书02/03敬告用户:1、保修期从房屋交付使用日起计。
- 1、下载文档前请自行甄别文档内容的完整性,平台不提供额外的编辑、内容补充、找答案等附加服务。
- 2、"仅部分预览"的文档,不可在线预览部分如存在完整性等问题,可反馈申请退款(可完整预览的文档不适用该条件!)。
- 3、如文档侵犯您的权益,请联系客服反馈,我们会尽快为您处理(人工客服工作时间:9:00-18:30)。
Quality Assurance
Quality has become one of the most important consumer decision factors in the selecting
among competing products and services. This is true not only for individual consumers but also for large corporations, government organizations and the taxpaying public as a group. In its broadest sense, quality is a degree of excellence: the extent to which something is fit for its purpose. In the narrow sense, product or service quality is defined as conformance with requirement, freedom from defects or contamination, or simply a degree of customer
satisfaction.
Figure 1: Taking a
Pavement Core for Density Quality Control
Figure 2: Taking a Pavement
Core for Density Quality Control Figure 3: Using the NCAT Oven to Determine Asphalt
Content Quality assurance. All those planned and systematic actions necessary to provide
confidence that a product or facility will perform satisfactorily in service. Quality
assurance addresses the overall problem of obtaining the quality of a service,
product, or facility in the most efficient, economical, and satisfactory manner
possible. Within this broad context, quality assurance involves continued
evaluation of the activities of planning, design, development of plans and
specifications, advertising and awarding of contracts, construction, and
maintenance, and the interactions of these activities.
∙Quality control. Those quality assurance actions and considerations necessary to assess production and construction processes so as to control the level of quality being produced in the end product. This concept of quality control typically
includes sampling and testing by the contractor to monitor the process but usually does not include acceptance sampling and testing by the agency/owner. Also
called process control.
∙Acceptance. Sampling, testing, and the assessment of test results to determine whether or not the quality of produced material or construction is acceptable in
terms of the specifications.
∙Independent assurance. A management tool that requires a third party, not directly responsible for process control or acceptance, to provide an independent assessment of the product and/or the reliability of test results obtained from
process control and acceptance testing. The results of independent assurance
tests should not be used as a basis of product acceptance.
Figure 4: Quality Assurance Diagram.
Quality control, acceptance and independent assurance are wholly separate components of quality assurance. It is difficult, if not impossible, to influence one component, solely through actions within another component. For instance, acceptance procedures are essentially monitoring methods used to determine whether or not a particular process is meeting quality standards. As such, they can be used to accept or reject material based on its quality but they should never be used as a method to control or improve quality; quality will not necessarily improve based on increased or stricter monitoring alone. In short, no amount of inspection changes the quality of a product or service (IQA, 2001). Quality control (process control) is used to control and systematically improve quality. Furthermore, independent assurance test results should not be used for acceptance or quality control. If they are, the tests are no longer independent and should not be used as if they were.
Footnotes (↵ returns to text)
1. TRB. (1999). Glossary of Highway Quality Assurance Terms. Transportation Research Circular,
No. E-C010. Transportation Research Board, National Research Council. Washington, D.C.↵∙。