轧机轴承
轧机轴承的使用方法(三篇)

轧机轴承的使用方法轧机轴承的使用寿命,不仅与轴承的质量有关,还与其安装使用的情况有密切关系。
为此应重视轴承安装的技术要求,遵守有关的操作规程。
1、安装前的准备(1)安装之前应对各配合作,包括辊颈、轴承箱、轴承套圈和轴承箱盖板等的配合表面进行仔细检查,检查其尺寸、形状位置精度和配合公叉是否符合设计的技术要求。
(2)与轴承相配合的表面,辊颈、轴承箱孔及油孔的棱边和毛刺都必须清除掉,并清洗干净涂上润滑油。
2、四列圆柱滚子轴承的安装(1)安装迷宫环(防水套)迷宫环与辊颈的配合一般为较紧的动配合,安装时需用铜棒轻轻敲进。
迷宫环的两瑞面必须平行并与轴身台肩和轴承内圈紧密贴合。
(2)安装内圈四列圆柱滋子轴承的内圈与辊颈的配合为过盈配合,安装时应先将内圈加热到90-100℃。
切勿超过120℃,以防止内圈冷却后回缩不彻底。
加热方法可用油槽加热也可用感应加热,绝对禁止用明火加热。
用油槽加热时内径的增大量按下列公式计算:△d=12.5×10-6△t.d式中:△d--内圈内径加热后的增大量(mm)△t--油温与室温之差(℃),室温标准为20℃。
d--内圈内径(mm)在安装FCD型等双内圈时,在内圈冷却的过程中必须沿轴向使内圈与内圈,内圈与迷宫环的端面靠贴,并用塞尺进行检验。
(3)安装外圈四列圆柱滚子轴承的外圈与轴承座内孔一般为过渡配合,对于较小型的轴承,可将外圈及滚子与保持架所组成的整体用铜棒轻轻敲入轴承座内。
对于较大型的轴承,可利用外圈或保持架上备有的吊装孔,将外圈与外圈组件吊起,垂直向下装入轴承箱。
对于带活挡边的FCDP型四列圆柱滚子轴承,其边挡圈、外圈组件、中挡圈,同一型号的轴承不宜互换。
外圈端面上打有Ⅰ、Ⅱ、Ⅲ、Ⅳ标记是负荷区的记号(见图1)。
当首次安装使用时,要让轧制负荷方向对准第Ⅰ标记记号,以后清洗再装时可让轧制负荷依次对准其余的标记记号,以延长轴承使用寿命。
3、止推(定位)轴承的安装图1外圈负荷分区标记图止推轴承有四点接角球轴承、双列(单列)角接角球轴承,双向推力圆锥和圆柱滚子轴承四点接角球轴承、双(单)列角接触球轴承用作止推轴承时,不准在径向承受负荷,故轴承座内孔相对应于装配这些轴承的部位,其直径必须比轴承外径大0.5毫米左右。
轧机四列轴承结构优化提升轧机使用寿命

轧机四列轴承结构优化提升轧机使用寿命立题背景一线悬臂式轧机是由美国布兹泼罗公司设计,由新日本工机制作的二十世纪八十年代高速线材生产线中轧机、预精轧机组。
自1989年投产以来,已使用20多年。
经过1999年改造,坯料由135*135方坯改为150*150方坯,目前生产能力已有原来的年产35万吨提高到了55万吨。
中轧机、预精轧机区域每月事故时间占总事故时间的50%左右,成本消耗占用总成本的40%左右。
在生产实践中高线技术人员和设备维护人员为降低φ300、φ400事故率从轧机结构改进、密封形式改进、装配过程优化、润滑油品清洁度指标提升,含水量等级提升等方面做了大量工作,取得了一定效果。
但以上措施都没有从根本上解决轧机轴承使用寿命短这一核心问题。
悬臂式轧机有着无扭转轧制、调整精度高、换辊速度快、设备结构简单、布置紧凑、检修维护方便、轧制品种丰富等优点,更能适应变幻莫测,竞争激烈的钢材市场。
因此保持一高线的生产稳定对唐钢第二钢轧厂的发展显得尤为重要。
针对四列轴承每一列滚动体承载不一样,磨损不均匀这一状况,结合现场实际情况,课题组拟定从两方面对四列圆柱滚子轴承进行改进创新。
第一把轴承内圈外表面加工一定的锥度补偿轴的微小弯曲变形,滚动体、外圈尺寸不变,使改进后的四列滚子轴承在轧辊轴轻微弯曲时每列滚动体受力均匀;第二将梳型铜合金保持架改为窗式冲压钢保持架。
改进后的轴承在故障率高,滚动体受力不均匀状况比较明显的15#轧机试用。
在保证轧机的润滑、装配要求、轧机负荷等环境条件不变的情况下检测轴承使用状况,及时总结并调整改进。
使用成功后逐渐推广到其他架次轧机。
技术方案与创新性成果(一)技术方案1、高线悬臂式轧机的结构高线悬臂式轧机结构见图一其传动方式是电机发出的动力经过齿形联轴器传给齿轮箱,经过变速后,带动安装于辊箱摇臂上的轧辊轴,通过安装在轧辊轴上的轧辊实现线材的轧制。
2、轧辊轴受力分析在轧钢过程中轧辊受到齿轮的传动力矩、轧制力和轧制力矩共同作用。
轧机轴承的使用寿命

轧机轴承的使用寿命轧机轴承的使用寿命目录一、影响轧机轴承使用寿命的因素(一)、基本额定寿命(二)、径向基本额定动负荷(三)、修正额定寿命(四)、油膜润滑参数(五)、密合度(待整理)(六)、影响轧机轴承使用寿命的因素二、轧机轴承的失效分析(一)、轧机轴承失效统计(二)、轧机轴承的主要失效形式和原因三、降低轧机轴承消耗的途径(一)、做好轧机轴承使数据统计(二)、轴承各零件强度要相匹配(三)、采用高质量轴承材料(四)、轧机轴承精度、游隙及配合(五)、改进热处理工艺(六)、在轧机轴承制造过程还应该从以下几方面注意改进。
(七)、轧机轴承的润滑与密封(八)、轧钢机设计与安装(九)、轴承装配(十)、轧制过程中摘要:通过介绍轧机轴承的寿命计算和轧机轴承使用寿命的影响因素,以及轧机轴承失效分析的多年实践经验,进而提出了降低轧机轴承消耗的途径。
关健词:轧机轴承、负荷、使用寿命、工作表面、轴承失效、油膜、润滑、密封、过载、偏载、窜辊、装配、精度、密合度、失效分析。
为了增强轧钢产品的市场竞争力,轧钢厂对轧机轴承的消耗成本及轧钢机作业率都提出了更高的要求;为什么轧制同样的产品,而不同的轧机不同的轴承或同样的轧机同样的轴承或不同的现场使用条件,轧机轴承的使用寿命差距很大,各单位的吨钢轧机轴承消耗及因轴承问题影响的轧钢机作业率有很大的不同。
下面就如何降低轧机轴承消耗,从轧机轴承本身及应用等多方面给予分析提示。
一、影响轧机轴承使用寿命的因素从下面的几个基本概念及计算公式中,可以看出影响轧机轴承寿命的因素及变量关系。
(一)、基本额定寿命基本额定寿命:是指单个轴承或一组在相同条件下运转的近于相同的轴承,其可靠性为90%时的寿命。
L10 =(C/P)ε式中:L10——基本额定寿命百万转C——基本额定动负荷牛顿NP——当量负荷牛顿Nε——寿命指数(球轴承ε=3,滚子轴承ε=10/3)对于转速恒定的轴承寿命用工作时数表示为:L10h=(C/P)ε×106/60n式中:L10h——基本额定寿命小时hn——轴承工作转速转/分钟 r/min 由式中可以看出,轴承基本额定负荷越大及轴承转速越低,轴承基本额定寿命就越长。
轧机轴承图例

轧机轴承图例
四辊热带轧机支承辊轴承装置(四列圆锥滚子轴承+四列圆锥滚子轴承)
高速四辊轧机工作辊轴承装置(四列圆锥滚子轴承+四列圆锥滚子轴承)
高速四辊冷带轧机支承辊轴承装置(双列圆锥滚子轴承+四列圆柱滚子轴承+四列圆柱滚子轴承)
高速四辊轧机工作辊轴承装置(工作端:配对角接触球轴承+四列圆柱滚子轴承;驱动端:四列圆柱滚子轴承+深沟球轴承)
工作辊工作端轴承装置(配对角接触球轴承+四列圆柱滚子轴承)
工作辊驱动端轴承装置(深沟球轴承+四列圆柱滚子轴承)
双棍厚板轧机或开坯轧机轧辊轴承装置(工作端:双向推力圆锥滚子轴承+四列圆柱滚子轴承;
驱动端:四列圆柱滚子轴承+深沟球轴承)
20辊冷轧机支承辊轴承装置(背衬轴承)
轧机压下机构轴承装置
平整机座双辊轧机轧辊轴承配置(驱动端:双列调心滚子轴承+深沟球轴承+四列圆柱滚子轴承;。
国产轴承之轧机油膜轴承技术
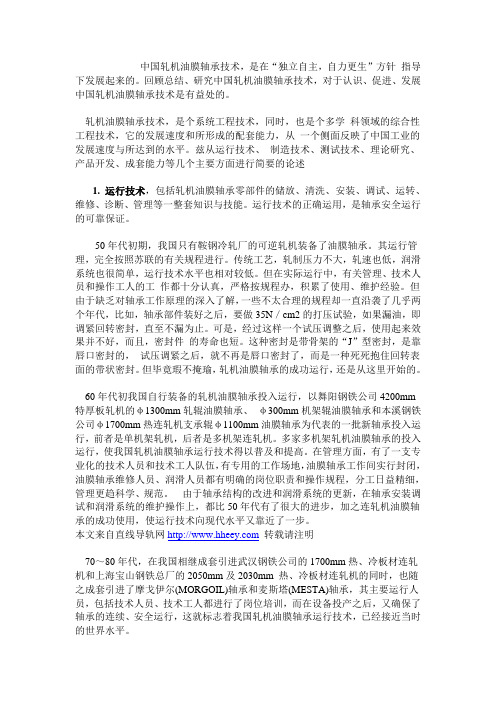
中国轧机油膜轴承技术,是在“独立自主,自力更生”方针指导下发展起来的。
回顾总结、研究中国轧机油膜轴承技术,对于认识、促进、发展中国轧机油膜轴承技术是有益处的。
轧机油膜轴承技术,是个系统工程技术,同时,也是个多学科领域的综合性工程技术,它的发展速度和所形成的配套能力,从一个侧面反映了中国工业的发展速度与所达到的水平。
兹从运行技术、制造技术、测试技术、理论研究、产品开发、成套能力等几个主要方面进行简要的论述1. 运行技术,包括轧机油膜轴承零部件的储放、清洗、安装、调试、运转、维修、诊断、管理等一整套知识与技能。
运行技术的正确运用,是轴承安全运行的可靠保证。
50年代初期,我国只有鞍钢冷轧厂的可逆轧机装备了油膜轴承。
其运行管理,完全按照苏联的有关规程进行。
传统工艺,轧制压力不大,轧速也低,润滑系统也很简单,运行技术水平也相对较低。
但在实际运行中,有关管理、技术人员和操作工人的工作都十分认真,严格按规程办,积累了使用、维护经验。
但由于缺乏对轴承工作原理的深入了解,一些不太合理的规程却一直沿袭了几乎两个年代,比如,轴承部件装好之后,要做35N/cm2的打压试验,如果漏油,即调紧回转密封,直至不漏为止。
可是,经过这样一个试压调整之后,使用起来效果并不好,而且,密封件的寿命也短。
这种密封是带骨架的“J”型密封,是靠唇口密封的,试压调紧之后,就不再是唇口密封了,而是一种死死抱住回转表面的带状密封。
但毕竟瑕不掩瑜,轧机油膜轴承的成功运行,还是从这里开始的。
60年代初我国自行装备的轧机油膜轴承投入运行,以舞阳钢铁公司4200mm 特厚板轧机的φ1300mm轧辊油膜轴承、φ300mm机架辊油膜轴承和本溪钢铁公司φ1700mm热连轧机支承辊φ1100mm油膜轴承为代表的一批新轴承投入运行,前者是单机架轧机,后者是多机架连轧机。
多家多机架轧机油膜轴承的投入运行,使我国轧机油膜轴承运行技术得以普及和提高。
在管理方面,有了一支专业化的技术人员和技术工人队伍,有专用的工作场地,油膜轴承工作间实行封闭,油膜轴承维修人员、润滑人员都有明确的岗位职责和操作规程,分工日益精细,管理更趋科学、规范。
轧机轴承结构类型

轧机轴承结构类型
轧机轴承结构类型大致可分为三大类:滚珠轴承、滑动轴承和副
轴承。
1. 滚珠轴承:由圆柱形滚子和外圆环、内圆环、保持架等来组成,有固定式、内移式和内外移式三种,是轴承结构类型中使用最广泛的。
2. 滑动轴承:由滑轮、附属件等组成,采用流体来构成滑动叠轴
承结构,可以将轴承承载负荷小大化,变化多样,适用于范围广泛。
3. 副轴承:其结构简单,由动尺、副齿轮、轴主设备等构成,几
乎没有滚动摩擦,承载能力较大,但使用寿命较短,适合于大扭矩大
传动动力应用。
轧机油膜轴承失效原因剖析及对策
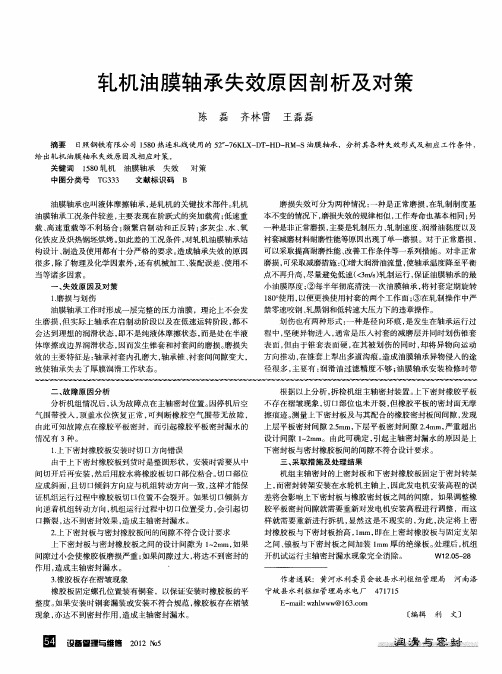
下密封板与密封橡胶板间的间隙不符合设计要求 。
三 、 取 措 施 及处 理 结 果 采
机组主轴密封 的上密封板 和下密封橡胶板 固定于密封转架 上, 而密封转架安装在水轮机主轴上 , 因此发 电机安装高程的误
差将会影响上下密封板与橡胶密封板之间的间隙 ,如果调整 橡
胶平板密封间隙就需要重新对发 电机安装高程进行调整 ,而这 样就需要重新进行拆机 , 显然这是不现实 的, 为此 , 决定将上密 封橡胶板与下密封板抬高 ,m 即在上 密封橡胶板与 固定支架 l m, 之 间、 锒板与下密封板之间加装 1 m厚 的绝缘板 。 m 处理后 , 机组 开机试运行主轴密封漏水现象完全 消除 。 Wl.5 2 0 — 8 2
I 设 管 与 修 22 5 蟊 备理维 0№ 1
— 翊
劐 一
人; 支承辊组装试 压过程 中带人 ; 供油管路 中的铁锈 ; 过滤 器失 效及更换支承辊装拆管接头时带人 。 中, 其 过滤精度不够是造成
2上下密封板 与密封橡胶板问的间隙不符合设计要 求 .
上下 密封板 与密封橡胶板之 问的设计 间隙为 1 2 m, — r 如果 a 间隙过小会使橡胶板磨损严重 ; 如果 间隙过大 , 将达不到密封的
作 用 , 成 主轴 密 封 漏 水 。 造 ’
3橡胶板存 在褶皱现象 .
作者通联:黄河水利委员会故县水利枢纽管理局 河南洛
当等诸多因素。
一
、
失效 原 因及 对 策
1 . 与划伤 磨损 油膜轴承工作 时形成一层完整的压力油膜 ,理论 上不会发 生磨损 , 但实际上轴承在启制动 阶段 以及在低速运转 阶段 , 都不 会达到理想的润滑状态 , 即不是纯液体摩擦状态 , 而是处在半液
轧机烧轴承原因

轧机烧轴承原因轧机烧轴承是指轧机工作过程中轴承发生异常磨损、发热、焦化等现象。
轴承作为支撑轴心和传递力量的重要组成部分,对于轧机的正常运行至关重要。
如果轴承出现问题,将会对轧机的工作效率和质量产生不利影响。
本文将从多个方面深入探讨轧机烧轴承的原因,并分享我的观点和理解。
1. 负载过重:负载过重是导致轧机烧轴承的常见原因之一。
在轧机工作时,轧制压力对轴承承载产生较大影响。
如果轧机工作负载过大,超过了轴承设计的承载能力,会导致轴承过度磨损,进而引发烧轴承的问题。
2. 润滑不良:良好的润滑是轴承正常工作的重要保障。
轴承在高速旋转和高温环境下,需要足够的润滑来减少磨损和摩擦。
如果润滑不良或使用了不合适的润滑剂,会导致轧机工作时轴承摩擦增大,摩擦热量过高,从而引起轴承烧损。
3. 轴承安装不当:轴承安装不当也是轧机烧轴承的一个常见原因。
如果轴承安装不紧密或不平衡,会导致轴承在轧机工作过程中产生振动,进而引发轴承受力不均匀,导致轴承过热。
4. 轴承材料质量问题:轴承材料质量对轧机烧轴承也有一定的影响。
如果轴承材料质量不达标,硬度不符合要求,将会影响其使用寿命和耐高温性能,容易导致轴承在高负载和高温环境下发生异常,从而引发烧轴承问题。
我的观点和理解是,轧机烧轴承是由多个因素共同作用而引起的结果。
除了上述提到的原因之外,还可能存在其他未能详细探讨的因素,如轧机设计缺陷、轧机维护不到位等。
在解决轧机烧轴承问题时,我们应该综合考虑多方面因素,从源头上解决问题,以确保轧机的正常运行和生产效率。
总结回顾一下,轧机烧轴承的原因包括负载过重、润滑不良、轴承安装不当和轴承材料质量问题。
以上是我对这个问题的深入探讨,并分享了我的观点和理解。
希望这篇文章对您的理解起到了一定的帮助和启发。
(字数:492)轧机烧轴承的原因远不止于负载过重、润滑不良、轴承安装不当和轴承材料质量问题。
实际上,轧机烧轴承的原因非常复杂,下面我将继续探讨其中几个可能的原因。
轧机轴承的知识

轧机轴承的知识MSN: shanglin-ly@1。
关于轧机2。
轧辊,轴承箱,轧机轴承3。
轧机轴承的材料4。
轧机轴承的使用寿命和轧制力 5。
轧机轴承的安装6。
轧机轴承的维护与监测7。
轧机轴承的润滑8。
轧机轴承的存放和保管9。
轧机轴承的检测项目和检测标准 10。
常用到的一些词汇关于轧机轧机是直接轧延金属的主机,它利用旋转的轧辊辗压坯料,使金属按规定的要求产生塑性变形。
是生产率最高、成本最低的金属成形方法。
轧延主要有热轧和冷轧两种方式。
热轧是在轧件加热的条件下进行轧延,以降低轧延压力。
冷轧是在室温下进行,可使轧件得到很高的形状尺寸精度和表面光洁度,并可改善轧件的机械性能。
钢厂工艺流程图热轧车间三米四辊中板轧机生产场景轧机的组成五连轧机组装配过程中的立辊轧机轧辊轧机轴承安装在轧辊(工作辊、支撑辊)的辊颈上,还有其他辅助设备上,如压下机构,传动机构等轴承箱轴承就装在轴承箱里轴承座图片轧机轴承轧机轴承轧机轴承的材料一般轧钢机轴承材料常选用渗碳钢或轴承钢。
渗碳钢有:20Cr2Ni4A,20Cr2Mn2MoA,12CrNi3MoA,12Cr2Ni4A等。
渗碳钢表面渗碳后,具有抗疲劳的硬表面层和抗断裂的坚韧心部。
具有较高的抗冲击性能。
轴承钢有GCr15、GCr15SiMn等。
轧钢机轴承材料也可选用GCr18Mo材料,采用下贝氏体淬火工艺,因下贝氏体具有较高韧性,也具有较高的抗冲击性能。
轧机轴承的使用寿命和轧制力对于轧机轴承的寿命,一般不规定使用寿命,因为与各种外部因素有关。
一般要和用户签定协议,规定轧制多少吨钢材(即过钢量),作为轴承使用寿命。
轧制力就是轧辊的压下力。
一般按最大的力计算。
轧制力和轧制的钢材厚度有关,一次轧多少毫米,力量是不一样的,这个和轧机种类有关,不同的轧机,轧制力不一样。
轧机轴承的安装1。
安装前的准备2。
四列圆柱滚子轴承的安装3。
四列圆锥滚子轴承的安装1、安装前的准备(1)安装之前应对各配合作,包括辊颈、轴承箱、轴承套圈和轴承箱盖板等的配合表面进行仔细检查,检查其尺寸、形状位置精度和配合公盖是否符合设计的技术要求,主要包括:轴承箱尺寸、椭圆度,轧辊辊径尺寸、椭圆度。
中厚板轧机滚动轴承失效分析与预防方法

— —
麴 盔 夔型L一
i m  ̄ M 22 l 囡 Q N 0 № B 1
V C 20 T 一 0 B加工 中心主轴故 障排 除
别 自政
摘要
张家 良 谭义军
介绍 3例 V C 2 0 T 一 0 B加 工 中心主 轴故障现 象及 排除过程 。
锥滚 子轴 承。
可 以采用提高润滑油 膜的厚度 ( 如提高润滑油 的黏度 )减低 轴 ,
承的负载等方法 。 2 . 沟道在 圆周方 向呈对称位置剥 落失效及对策
对称位置剥 落表 现在 内圈为周 围环带剥落 ,而外圈呈周 向 对称位置剥落 ( 即椭 圆的短轴 方向 )其产生原 因主要是 因为轴 , 承箱孔椭圆过大。 当轴承压入椭圆偏大 的轴承箱孔中时 , 使轴承 外圈产生椭圆 , 在短轴方 向的游隙明显减少甚至负游隙。 轴承在 载荷的作用 下 , 内圈旋转产生周向剥落痕迹 , 圈滚子只在短轴 外 方 向的对称位置产生剥落痕迹 。 决此 问题 , 解 需要提高轴承箱孔
四列 圆柱滚子轴承 的径 向承载能力要 比相 同尺寸 的四列 圆锥滚 子轴承大 。 四列圆柱滚子轴承不能承受轴向载荷 , 必须要在轧辊 上安装承受轴 向载荷 的轴承 ,才能发挥 四列 圆柱滚子轴承承受
应确保轴承安装到位或将 自由侧轴承外 圈配合改为间隙配
合, 以期轴承过载时使轴承得 到补偿 。如果无法确保安装到位 ,
二、 轧机滚动轴承失效模式及对策
1 . 沟道单侧极 限位置剥落失效及对策 沟道单侧极 限位置剥落主要表现在沟道与挡边交界处有严 重的剥 落环带 。产生原 因是轴承安装不到位或运转过程 中突发
轴 向过载。
的径 向尺寸受到 限制时 , 可依 据轧辊的辊径选择轴承外径 , 都 以 适合保持轧辊辊体最大修磨量 的要求 。 就轴 承的承载力来讲 , 但
国内轧机轴承生产企业名录
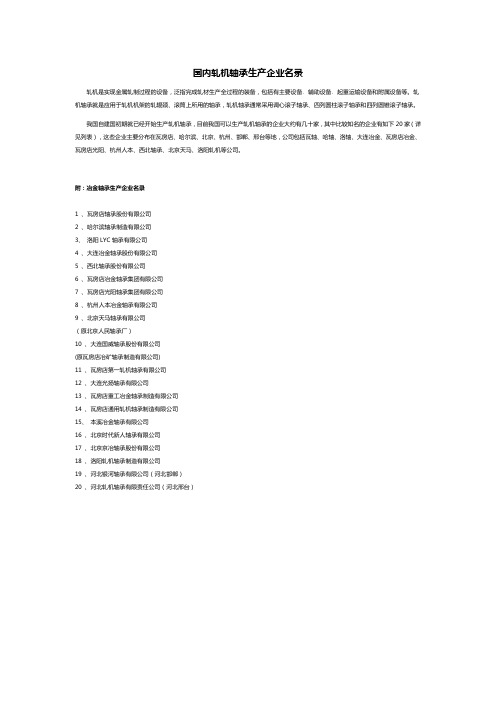
国内轧机轴承生产企业名录
轧机是实现金属轧制过程的设备,泛指完成轧材生产全过程的装备,包括有主要设备﹑辅助设备﹑起重运输设备和附属设备等。
轧机轴承就是应用于轧机机架的轧辊颈、滚筒上所用的轴承,轧机轴承通常采用调心滚子轴承、四列圆柱滚子轴承和四列圆锥滚子轴承。
我国自建国初期就已经开始生产轧机轴承,目前我国可以生产轧机轴承的企业大约有几十家,其中比较知名的企业有如下20家(详见列表),这些企业主要分布在瓦房店、哈尔滨、北京、杭州、邯郸、邢台等地,公司包括瓦轴、哈轴、洛轴、大连冶金、瓦房店冶金、瓦房店光阳、杭州人本、西北轴承、北京天马、洛阳轧机等公司。
附:冶金轴承生产企业名录
1 、瓦房店轴承股份有限公司
2 、哈尔滨轴承制造有限公司
3、洛阳LYC轴承有限公司
4 、大连冶金轴承股份有限公司
5 、西北轴承股份有限公司
6 、瓦房店冶金轴承集团有限公司
7 、瓦房店光阳轴承集团有限公司
8 、杭州人本冶金轴承有限公司
9 、北京天马轴承有限公司
(原北京人民轴承厂)
10 、大连国威轴承股份有限公司
(原瓦房店冶矿轴承制造有限公司)
11 、瓦房店第一轧机轴承有限公司
12 、大连光扬轴承有限公司
13 、瓦房店重工冶金轴承制造有限公司
14 、瓦房店通用轧机轴承制造有限公司
15、本溪冶金轴承有限公司
16 、北京时代新人轴承有限公司
17 、北京京冶轴承股份有限公司
18 、洛阳轧机轴承制造有限公司
19 、河北银河轴承有限公司(河北邯郸)
20 、河北轧机轴承有限责任公司(河北邢台)。
轧机轴承型号大全

轧机轴承型号
内容来源网络,由“深圳机械展(11万㎡,1100多家展商,超10万观众)”收集整理!更多cnc加工中心、车铣磨钻床、线切割、数控刀具工具、工业机器人、非标自动化、数字化无人工厂、精密测量、3D打印、激光切割、钣金冲压折弯、精密零件加工等展示,就在深圳机械展.
随着轧机装机水平的不断提高,带动了轧机油膜轴承的理论研究工作,真正自主开展理论研究工作,始于1974年。
当时的主要工作是探讨工作机理,从经典润滑理论建立数学模型,数值计算方法,准解析方法等,把理论研究又引深一步。
鉴于经典理论的油膜峰值压力达100MPa以上,继而进行了弹流理论的应用研究工作,当时,研究弹流的一些学者,只注重了反形接触的高副弹流的研究,而对滑动轴承,认为是非典型弹流问题,甚至有人认为重载油膜轴承不属于弹流范畴。
那么大家在轧机轴承型号的选择上是否还存在困惑,以下给大家总结的轧机轴承常用的一些型号,希望对大家不管是在理论研究上还是轴承选择上都能有所帮助!
轧机轴承常用型号
内容来源网络,由“深圳机械展(11万㎡,1100多家展商,超10万观众)”收集整理!更多cnc加工中心、车铣磨钻床、线切割、数控刀具工具、工业机器人、非标自动化、数字化无人工厂、精密测量、3D打印、激光切割、钣金冲压折弯、精密零件加工等展示,就在深圳机械展.。
优化冷轧机轴承装配结构形式及维护方案

优化冷轧机轴承装配结构形式及维护方案摘要:本文主要介绍冷轧机轴承座结构形式优化,以及维护方案改进,减少备件辅料消耗,减少事故发生,提高作业率。
关键字:轧机轴承座、轧机轴承、漏油一.前言冷轧机轴承普遍现存在以下几方面问题:(1)轧机工作辊和中间辊轴承到维护周期,油脂被冲刷干净,严重影响轴承使用寿命;(2)轧机支撑辊进水和漏油情况还是比较严重;(3)轴承座卡环脱落事故经常发生,造成轧机断带事故;(4)轴承座铜滑板松动情况普遍,造成铜滑板脱落事故。
这些都严重影响备件和油品辅料费用的消耗。
该篇采取优化轧机轴承座结构和维护方式来解决这些难题,减少备件成本,降低轧线事故。
二、优化冷轧机轴承装配结构形式及维护方案1、轧机工作辊和中间辊轴承座防进水攻关。
对下机后的轴承密封进行检查,发现密封无变形和损坏,后检查发现轴承座密封与轧辊接触存部位,磨损严重,测量磨损沟槽厚度约0.2mm,如图1所示,通过减少密封径向尺寸,增加过盈配合,有效解决轴承座进水问题。
图1密封与轧辊接触存部位检测2、轧机支撑辊进水和漏油技术攻关对支撑辊轴承座通气孔改进,加大了通气孔尺寸,避免堵塞,增加倒U形结构和防护罩,有效减少漏油和进水。
整体结构采用不锈钢材质,主要目的防锈和增加使用寿命,结构示意图如图2所示,安装使用如图3所示。
其工作原理:当轴承座内空气压力小于外界压力时,空气通过由下防贱板和上防贱板的空隙进入,到空心弯管内的通气孔与轴承座内腔,使轴承座内气压与外界相同,保证润滑油重力回油的顺利进行,当乳化液从轴承座上流下时,乳化液喷溅的下防贱板、上防贱板和防护罩上,乳化液被阻止进入通气孔中;当回油管出现部分堵塞造成液位上升,或其它原因造成轴承座内腔气压高于外界气压,轴承旋转过程中造成润滑油流入通气孔时,通气孔和空心弯管的倒U形结构,使得润滑油流到空心弯管一定高度,不再向往外流,有效阻止润滑油从通气孔泄漏的情况。
图2改造通气孔结构示意图图中标记为:通气孔1、空心弯管2、防护罩3、上防贱板4、下防贱板5图3现场安装使用图对支撑辊轴承座通气孔改进后进行跟踪,未发现通气孔漏油的情况,通过二、三和四季度进水和漏油情况,改进后有效减少漏油和进水。
轧机油膜轴承应用探讨

轧机油膜轴承参数选择和应用探讨摘要:油膜轴承广泛于各种板带轧机上,合理的选型和正确的使用对提高轧机运行的稳定性和轴承寿命十分重要。
本文就油膜轴承的基本参数、精度和润滑等方面的问题进行了讨论。
关键词:油膜轴承;精度;润滑1.前言油膜轴承是一种以润滑油为介质的滑动轴承,作为承载元件,广泛应用于中厚板轧机、热轧机、冷轧机等各种板带轧机上。
由于轴承旋转时只需克服润滑油之间很小的内摩擦,因此摩擦系数很小,只有0.003-0.008。
在合理的结构设计、正常的工作条件、细致的维护保养下,油膜轴承的使用寿命一般可达到10年以上。
轧机油膜轴承,按油膜形成机理分,有纯动压油膜轴承和静-动压油膜轴承两种。
纯动压油膜轴承工作时利用流体动压理论,当固定在轴颈上的锥套以一定速度旋转时,在锥套)和轴承衬套的工作区域形成一个完整的压力油膜,使金属脱离接触,形成纯液体摩擦。
静-动压油膜轴承是在纯动压油膜轴承的基础上配备有静压功能,当轴承转速小于某一临界速度时或外载荷超过动压油膜压力时,向轴承内部通入高压油以维持轴承的正常运转。
由于轧机的结构不同、工作制度不同,对应油膜轴承的参数和结构、使用维护方式也不同。
依据轧机本身的结构特点和工作制度合理设计油膜轴承,并科学的使用维护,才能使油膜轴承的功能得到最大发挥。
2.油膜轴承的基本参数轧机的方案设计完成之后,根据轧机的工作制度、轧辊尺寸、牌坊窗口尺寸、自位装置、轴向固定方式以及其他一些要求,可以初步确定油膜轴承基本参数,包括几何参数、运动参数、物理参数等。
通过对轴承承载能力计算分析,不断地修改、调整各参数,使之在实现具体工况的前提下,达到各参数的最佳匹配。
为保证油膜轴承在工作时能形成润滑油膜,产生液体摩擦,必须满足下列条件:①、须使锥套与衬套表面的润滑油层成楔形,并将润滑油导入油楔的狭窄部分。
②、轴承的转速必须足够高,以保证润滑油层中产生的动压力能平衡外载荷。
③、润滑油的粘度必须恰当。
以合理的间隙、适当的润滑油粘度,来满足轧机的不同转速下的轧制压力。
轧机轴承基本知识介绍
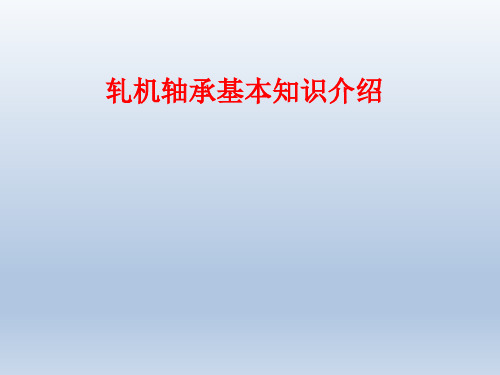
四、轧机轴承的安装
1.内圈加热 (1)加热前内圈表面应清洁。 (2)温度不能超过120℃,有表面发蓝等过烧现象的,内圈报废。 (3)△d=1.25×10-5△t 2.辊颈 (1)表面除锈和杂物。 (2)迷宫装配到位。 (3)内圈端面标记“A”朝向迷宫。 (4)内圈与迷宫之间不得有间隙。
3.端盖与密封 (1)端盖检查,无显著磨损、变形、接触面无凹凸点、毛刺等。 (2)轴承座与端盖接触面清理干净,涂一层薄油脂,加羊毛毡。 (3)密封圈安装到位(密封唇滑动表面必须光滑)。 4.轴承座 (1)加油孔确认,畅通无阻。 (2)内孔表面清除干净,涂一层薄油脂。 (3)检查圆柱度(偏差:0.13mm)。
5.轴承 (1)外圈清理干净。 (2)轴承平放,垂直向下,标记与内圈配合(A-A)。 (3)用铜棒击打外圈端面,不能击打滚动体、保持架。 (4)螺栓不能缺失。 (5)加油。
6.配件 (1)迷宫式压套、挡环。 (2)轴承压套、轴向锁紧螺母。 (3)卡环、外圈螺母、锁紧螺母。 (4)键。 7.检查 (1)轴向间隙。 (2)转动灵活。
3.推力滚子轴承
机架 1#、3# 5#、7# 450短应力 350短应力
型号 350981c 351019c 351019c
4936X3D
三、轧机轴承的特点
1.工作载荷大。 通常轧辊轴承所承受的单位压力比一般用途的轴承高到2-4倍。 2.运转速度差别大。 不同轧机的运转速度差别很大。 3.目录
一、滚动轴承构成 二、滚子轴承 三、轧机轴承的特点 四、轧机轴承的安装
轴承四大件 1.外圈 2.内圈 3.滚动体 4.保持架
一、滚动轴承的构成
1.圆柱滚子轴承 我厂使用机架和型号
二、滚子轴承
机架 1#、3# 5#、7# 9#-12# 350短应力轧机
高速线材轧机轴承表
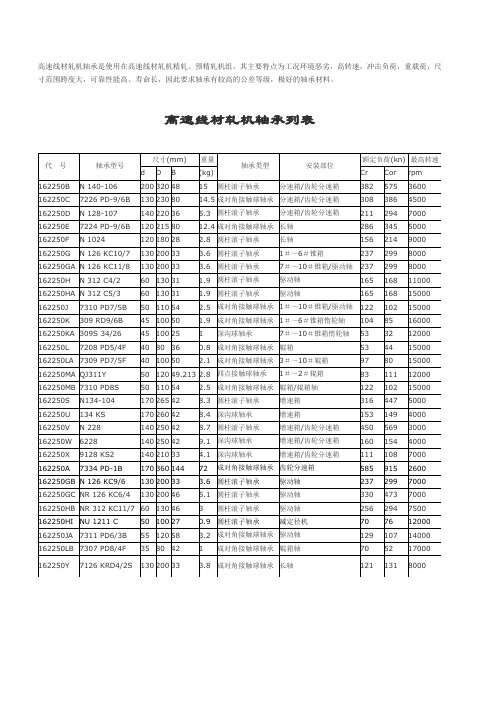
高速线材轧机轴承是使用在高速线材轧机精轧、预精轧机组,其主要特点为工况环境恶劣,高转速,冲击负荷,重载荷,尺寸范围跨度大,可靠性能高、寿命长,因此要求轴承有较高的公差等级,极好的轴承材料。
高速线材轧机轴承列表代号轴承型号尺寸(mm) 重量轴承类型安装部位额定负荷(kn) 最高转速d D B (kg) Cr Cor rpm162250B N 140-106 200 320 48 15 圆柱滚子轴承分速箱/齿轮分速箱382 575 3600 162250C 7226 PD-9/6B 130 230 80 14.5 成对角接触球轴承分速箱/齿轮分速箱308 386 4500 162250D N 128-107 140 220 36 5.3 圆柱滚子轴承分速箱/齿轮分速箱211 294 7000 162250E 7224 PD-9/6B 120 215 80 12.4 成对角接触球轴承长轴286 345 5000 162250F N 1024 120 180 28 2.8 圆柱滚子轴承长轴156 214 9000 162250G N 126 KC10/7 130 200 33 3.6 圆柱滚子轴承1#~6#锥箱237 299 8000 162250GA N 126 KC11/8 130 200 33 3.6 圆柱滚子轴承7#~10#锥箱/驱动轴237 299 8000 162250H N 312 C4/2 60 130 31 1.9 圆柱滚子轴承驱动轴165 168 11000 162250HA N 312 C5/3 60 130 31 1.9 圆柱滚子轴承驱动轴165 168 15000 162250J 7310 PD7/5B 50 110 54 2.5 成对角接触球轴承1#~10#锥箱/驱动轴122 102 15000 162250K 309 RD9/6B 45 100 50 1.9 成对角接触球轴承1#~6#锥箱惰轮轴104 85 16000 162250KA 309S 34/26 45 100 25 1 深沟球轴承7#~10#锥箱惰轮轴53 32 12000 162250L 7208 PD5/4F 40 80 36 0.8 成对角接触球轴承辊箱53 44 15000 162250LA 7309 PD7/5F 40 100 50 2.1 成对角接触球轴承3#~10#辊箱97 80 15000 162250MA QJ311Y 50 120 49.213 2.8 四点接触球轴承1#~2#辊箱83 111 12000 162250MB 7310 PD8S 50 110 54 2.5 成对角接触球轴承辊箱/辊箱轴122 102 15000 162250S N134-104 170 265 42 8.3 圆柱滚子轴承增速箱316 447 5000 162250U 134 KS 170 260 42 8.4 深沟球轴承增速箱153 149 4000 162250V N 228 140 250 42 8.7 圆柱滚子轴承增速箱/齿轮分速箱450 569 3000 162250W 6228 140 250 42 9.1 深沟球轴承增速箱/齿轮分速箱160 154 4000 162250X 9128 KS2 140 210 33 4.1 深沟球轴承增速箱/齿轮分速箱111 108 7000 162250A 7334 PD-1B 170 360 144 72 成对角接触球轴承齿轮分速箱585 915 2600 162250GB N 126 KC9/6 130 200 33 3.6 圆柱滚子轴承驱动轴237 299 7000 162250GC NR 126 KC6/4 130 200 46 5.1 圆柱滚子轴承驱动轴330 473 7000 162250HB NR 312 KC11/7 60 130 46 3 圆柱滚子轴承驱动轴256 294 7500 162250HI NU 1211 C 50 100 27 0.9 圆柱滚子轴承减定径机70 76 12000 162250JA 7311 PD6/3B 55 120 58 3.2 成对角接触球轴承驱动轴129 107 14000 162250LB 7307 PD8/4F 35 80 42 1 成对角接触球轴承辊箱轴70 52 17000 162250Y 7126 KRD4/2S 130 200 33 3.8 成对角接触球轴承长轴121 131 8000。
轧机铸钢轴承座 热处理 调质

轧机铸钢轴承座热处理调质
轧机铸钢轴承座热处理调质是指对轴承座进行热处理工艺,以
提高其硬度、强度和耐磨性的过程。
热处理调质是通过控制材料的
加热和冷却过程,使其获得所需的组织和性能。
在进行热处理调质时,需要考虑以下几个方面:
1. 加热工艺,通常采用加热至一定温度并保温一段时间,以使
材料达到均匀的温度分布。
这有助于减少内部应力和改善组织结构。
2. 冷却工艺,在加热后,需要对轴承座进行控制冷却。
冷却速
度的选择对最终的组织和性能具有重要影响。
通常采用油冷或水冷
的方式进行快速冷却,以获得所需的硬度和强度。
3. 调质工艺,在冷却后,通常需要对材料进行回火处理,以降
低脆性并提高韧性。
回火温度和时间的选择将影响最终的硬度和强度。
4. 控制参数,在整个热处理调质过程中,需要严格控制加热温度、保温时间、冷却速度和回火工艺参数,以确保最终产品达到设
计要求的性能指标。
总的来说,轧机铸钢轴承座热处理调质是一个复杂的工艺过程,需要综合考虑材料的成分、结构和所需的性能指标,通过科学合理
的工艺参数控制,使轴承座获得理想的硬度、强度和耐磨性。
- 1、下载文档前请自行甄别文档内容的完整性,平台不提供额外的编辑、内容补充、找答案等附加服务。
- 2、"仅部分预览"的文档,不可在线预览部分如存在完整性等问题,可反馈申请退款(可完整预览的文档不适用该条件!)。
- 3、如文档侵犯您的权益,请联系客服反馈,我们会尽快为您处理(人工客服工作时间:9:00-18:30)。
轧机工作辊烧轴承的原因分析
某厂生产工艺设备为φ650mm×1/φ500mm×1/11架连轧机组,其中四辊轧机6架,设计能力30万t/a,达产后,平均每天烧工作辊轴承9套,平均每天因轧辊烧轴承换辊所需时间约170min,导致吨钢轴承费用居高不下,有效作业率低,严重制约了钢带的正常生产。
原因分析
JP1~JP6四辊轧机下支承辊轴承座及工作辊承座与轧机牌坊窗口侧间隙的技术要求为0.45~0.90mm,经测量,其数据见表
车移动,工作辊轴承座下沉,产生巨大轴向力,导致工作辊2097938轴承轴向力过载,最终包死。
支承辊FC6890250轴承技术规范硬度为HRC58~61,对仓库现有FC6890250轴承硬度进行抽查,硬度最高为HRC58,最低为HRC54.5,大部分为HRC55,轴承硬度偏低。
从轴承损坏情况分析,锥形套在支承辊运转过程中与支承辊之间产生相对转动,与FC6890250轴承内圈产生磨擦发热,造成轴承内圈退火,硬度降低,使用寿命缩短。
工作辊与支承辊装配过程中存在如下问题:
(1)工作辊每个轴承座中都装有两组两列2097938轴承,两组轴承之间有两个轴承隔圈,用于调整轴承游隙,使每组轴承受力均匀,但是,装配过程中,轴承内圈之间隔圈之间隔圈难以和内圈同心,影响装配速度,装配工将此隔圈省去(约有70),这样就破坏了轴承的承载均匀性,轧制过程中产生的轴向力仅由一只轴承承受,造成过载,最终烧轴承。
(2)支承辊锥形套表面粗糙,运转过程中,破坏了V形密封圈,使其推动密封作用,造成冷却水和氧化铁皮进入轴承,使润滑脂乳化,降低轴承使用寿命。
(3)支承辊轴承座内有一套四点接触式定位球轴承:176160,其内圈由两只圆环组成,要求成对加工、成对组装用,没有互换性,否则,达不到装配精度,造成四列圆柱轴承FC6890250轴向定位不牢,产生轴向窜动,影响轴承使用寿命。
操作过程中存在问题如下:
(1)工作辊万向接轴托手在工作状态下,托不到位,运转过程中万向接轴抖动较大,造成工作辊与支承辊之间接触面不稳定,咬钢瞬间工作辊受力不均,产生巨大的轴向力,造成工作辊轴承过载、包死。
(2)工作辊平衡缸内泄压力不稳,轧辊运转过程中两边辊缝变化,钢咬入瞬间产生轴向力,破坏轧辊轴承。
(3)下支承辊轴承座下调整垫板厚度不等,轧制过程中产生轴向力,导致轧辊轴承过载、包死。
(4)工作辊万向接轴长期使用后,头部轴承间隙大造成动平衡不符合技术要求,导致抖动,啬了工作辊轴承的动载荷,轴承使用寿命下降。
整改措施
结合设备本身情况制定出一套切实可行方案和整改措施,主要内容为:
(1)对每台轧机轧辊轴承座与牌坊窗口内侧间隙定期检测,并建立档案,实行定期更
换衬板,保证侧间隙为0.45~0.90mm。
(2)提高轴承硬度为HRC58~60。
(3)将支承辊轴承座内的锥形套与轧辊之间的配合由间隙配合改为过盈配合,消除相对转动,避免磨擦。
(4)将2097938轴承内隔与轴承内圈合为一体,游隙由外隔圈调整,保证轴承承载均匀。
(5)将支承辊锥形套表面粗糙度由5~10μm改为1.25~2.5μm,延长V形密封圈使用寿命,确保轴承封,并给予轴承定期清洗,定期更换。
(6)在同一个四点接触式轴承座建立相对应的档案,保证定位准确。
(7)改进平衡缸密封结构,采用进口密封件,并定期更换,减少平衡缸内泄。
(8)下支承辊垫板,定人管理,分类堆放,成对更换,保证下支承辊水平度。
(9)工作辊成向接轴规定使用周期,定期更换。