机械优化设计实例
机械优化设计方案三个案例

机械优化设计案例11. 题目对一对单级圆柱齿轮减速器,以体积最小为目标进行优化设计。
2.已知条件已知数输入功p=58kw,输入转速n=1000r/min,齿数比1?]=550Mpa,许用弯用应力[曲应力u=5,齿轮的许H?]=400Mpa。
[ F3.建立优化模型3.1问题分析及设计变量的确定由已知条件得求在满足零件刚度和强度条件下,使减速器体积最小的各项设计参数。
由于齿轮和轴的尺寸(即壳体内的零件)是决定减速器体积的依据,故可按它们的体积之和最小的原则建立目标函数。
单机圆柱齿轮减速器的齿轮和轴的体积可近似的表示为:222222??)?0.25(b?c)(.25Db(d?d?dv?0.25)b(d??d)?02gzz1g122222222????d?)?0.257l(d8?dddc?2112 zzzz022222222??)10m(mzu?d?b.25?[m0zb?d.b?m8zbub0?1112zz12222]3228dd6d)?d?l?05bd.?005 b(mzu?10m?1..2 2zz2zz2z121式中符号意义由结构图给出,其计算公式为d?mz,d?mz2112D?umz?10m12g d?1.6d,d?0.25(umz?10m?1.6d)2z2g210z c?0.2b由上式知,齿数比给定之后,体积取决于b、z、m、l、d 和z11d 六个参数,则设计变量可取为z2TT]ddbzmxxxxx]l?[xx?[23145z61z213.2目标函数为222222f(x)?0.785398(4.75xxx?85xxx?85xx?0.92xx?xx?5231116233112222220.8xxxx?1.6xxx?xx?xx?28x ?32x)?min6646213316545约束条件的建立3.3.zz?17?,得1)为避免发生根切,应有min0??17?xg(x)21b???????maxmin d的最大值为齿宽系数2 )齿宽应满足和,dmaxmin??,,得和最小值,一般取=1.4=0.9maxmin g(x)?0.9?x(xx)?03212g(x)?x(xx)?1.4?031323)动力传递的齿轮模数应大于2mm,得g(x)?2?x?0344)为了限制大齿轮的直径不至过大,小齿轮的直径不能大于d,得max1g(x)?xx?300?0352d?d?d5)齿轮轴直径的范围:得maxzminzz0?100?xxg()?560?x150?g(x)?570?x?g(x)?130680200?x)?x?g(69l按结构关系,应距离满足条件:撑6)轴的支?b?2??0.5d?l=20),得(可取2zminmin g(x)?x?0.5x?x?40?041610)齿轮的接触应力和弯曲应力应不大于许用值,得7.0550?xxx)?1468250g(x)?(1231170980?x)??400g(42??2212)x?0.854?10xxxx(0.169?0.6666?102223170 980g(x??400?)4?22213)x?10?0.?xxx(0.2824?0.17710394x23221??][ 8)齿轮轴的最大挠度,得不大于许用值max440?.003xxx(xx)?0g(x)?117.04 4521443??][ 9)齿轮轴的弯曲应力,得不大于许用值ww6x?102.8512124?5.5?2.4?100g(x)?()?153xxx3526x1085?12.2124?5.5?10?0?g(x)()?6163xxx3624.优化方法的选择由于该问题有6个设计变量,16个约束条件的优化设计问题,采用传统的优化设计方法比较繁琐,比较复杂,所以选用Matlab优化工具箱中的fmincon函数来求解此非线性优化问题,避免了较为繁重的计算过程。
机械优化设计案例

机械优化设计案例:某生产线自动送料机构的改进
在制造领域,生产线上的自动送料机构是确保生产流程顺畅、高效的关键环节。
然而,传统的自动送料机构往往存在效率低下、易损坏、维护成本高等问题。
为了解决这些问题,我们采用了机械优化设计的方法,对某生产线上的自动送料机构进行了改进。
该自动送料机构的主要任务是将原材料从存储区输送到生产线,并确保每次输送的数量准确。
但是,在长时间使用后,传统的送料机构常常出现卡顿、输送不准确等问题。
经过分析,我们发现这些问题主要是由于机构中的某些部件设计不合理,导致机械效率降低。
为了解决这些问题,我们采用了以下优化策略:
结构优化:利用拓扑优化技术,对送料机构的主体结构进行了重新设计,使其在满足强度和刚度的同时,减轻了重量,从而减少了动力消耗。
传动系统优化:采用了新型的齿轮和链条传动系统,减少了传动过程中的摩擦和能量损失,提高了传动效率。
控制系统优化:引入了PLC和传感器技术,实现了对送料过程的精确控制,确保了每次输送的数量准确。
维护性优化:设计了易于拆卸和维护的结构,减少了维护时间和成本。
经过上述优化后,新的自动送料机构的性能得到了显著提升。
与传统的送料机构相比,新的机构在输送速度、准确性、使用寿命和维护成本等方面都有了显著的优势。
经过实际生产验证,新的自动送料机构不仅提高了生产效率,还降低了生产成本,为企业带来了显著的经济效益。
第八章机械优化设计应用实例

最优值 上面的最优解是连续性的,需进一步离散化处理,从略。
1,确定设计变量
铰链四杆机构按主从动连架杆给定的角度对应关系进行 设计时,各杆长度按同一比例缩放并不影响主,从动杆转 角的对应关系。因此可把曲柄长度作为单位长度,即令 L1=1,其余三杆表示为曲柄长度的倍数,用其相对长度l2, L3,l4作为变量。一般考虑,本问题与初始角 , 也有 关系,所以变量本应为l2,l3,l4, 和 五个。但是两 转角变量并不是独立变量,而是杆长的函数。写出如下式
D:
二,选择优化方法及结果分析
该题维数较低,用哪一种优化方法都适宜。这里选用约束 坐标轮换法。
计算时,曾用若干组不同的初始数据进行计算,从中选出 其中三组。见课本表8.1
由其中的计算结果可以看出,第二次计算结果应为最优解。
, 为相对杆长。最后,根据机构的结构设计需要按一定 的比例尺求出机构实际杆长L1,L2,L3,L4。
由余弦定理a图
整理得约束条件 同理由上页b图传动角最小位置写出 整理得约束条件
⑵按曲柄存在条件建立约束条件 写成约束条件有
用全部约束条件画成次下图所示的平面曲线,则可见, g3(x)~g7(x)均是消极约束。而可行域D实际上只是由g1(x) 与g2(x)两个约束条件围成的。综合上述分析,本题的优 化数学模型如下
输 出 角 函 数 图
对于该机构设计问题,可以取机构输出角的平方偏差 最小为原则建立目标函数。为此,将曲柄转角为
的区间分成n等分,从动摇杆输出角也有相对
应的分点。若各分点标号记作i,以各分点输出角的偏差 平方和作为目标函数,则有
式中的有关参数按如下步骤及公式计算 ①曲柄各等分点的转角
②期望输出角 ③实际输出角
机械优化设计范例(共9张PPT)
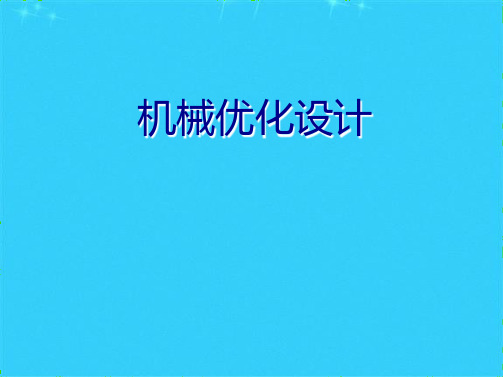
设计变量
现设 甲矿运往东站x万吨
乙矿运往东站y万吨
则甲矿运往西站200-x万吨
乙矿运往西站260-y万吨 令x=x1,y=x2
所以:X43;1.5(200-x1)+0.8x2+1.6(260-x2) =716-0.5x1-0.8x2(万元)
所以:Min f(X)= 716-0.5x1-0.8x2
约束条件
- x1 ≤0 X1-200 ≤0 -x2 ≤0 x2 - 260 ≤ 0
x1+x2-280≤ 0 100-x1-x2≤0
求解结果
x2 280 260
100
Z
(20,260)
x1=20 x2=260
Minf(X)= 498万元
100
200 280
x1
所以: 乙矿运往西站260-y万吨
Mx2in-f(26X0)≤ =0 498万元 则令甲x=矿x1运,y=往x2西站200-x万吨
最少的运费为498万元 x令1x+=xx21-2,y8=0x≤20
己 x1知+x甲2-、28乙0≤两0煤矿每年的产量分别为200万吨和260万吨,需经过东、西两个车站运外地。 M甲i煤nf(矿X运)往=东49站8和万西元车站的运费价格分别为1元/吨和1.5元/吨,乙煤矿运往东车站和西车站的运费价格分别为0.8元/吨和1.6元/吨 所。以:Min f(X)= 716-0. 煤乙矿应 运怎往样东编站制y万调吨运方案才能使总运费最少? 己x1知+x甲2-、28乙0≤两0煤矿每年的产量分别为200万吨和260万吨,需经过东、西两个车站运外地。 xM1i+nfx(2-X2)80=≤ 4098万元 现甲设煤矿甲运矿往运东往站东和站西x万车吨站的运费价格分别为1元/吨和1.5元/吨,乙煤矿运往东车站和西车站的运费价格分别为0.8元/吨和1.6元/吨 所 。以:X = [ x1, x2 ]T
机械优化设计_经典实例
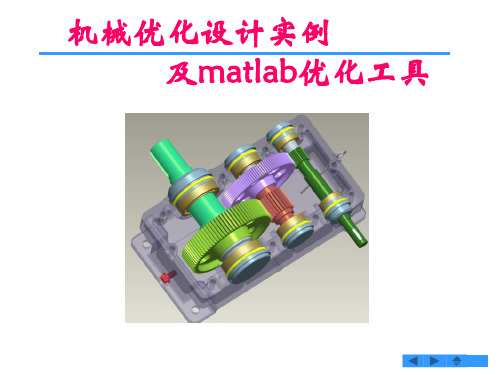
1.5 f max
1
1 321
x1 x22
1
0
g5 (x) x1 0
g6 (x) x2 0
盖板优化实例
f (x) 2 60t 2 0.5h 120 x1 x2
盖板优化实例
g1 ( x)
1
1 4
x2
0
7 g2 (x) 1 45 x1x2 0
目标函数:
f (x) 2 60t 2 0.5h 120 x1 x2
约束:
g1 ( x)
[ ] max
1
1 4
x2
1
0
g2 (x)
[ ] max
1
7 45
x1 x2
1
0
g3 (x)
c max
1
7 45
x13 x2
1
0
g4 (x)
第2部分 优化计算工具
2.1 线性规划优化函数 2.2 无约束非线性优化函数 2.3 约束优化函数
MATLAB解决的线性规划问题的标准形式为:
min cT x s.t. Ax b, x 0
A (aij )mn , x (x1, x2, x3,...xn )T c (c1, c2, )T ,b (b1,b2,...bm )T ,且b 0
a2
1 b2
an
1 bn
(a、b维数必须相同)
1.4 源文件(M-文件)
分为两类: 函数文件和非函数文件 都用扩展名.M
1.4.1 函数文件(相当于子程序)
机械优化设计范例
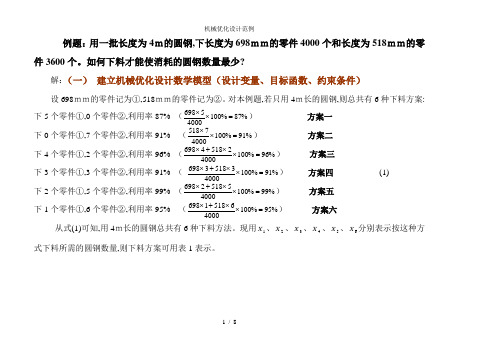
1 / 8例题:用一批长度为4m的圆钢,下长度为698mm的零件4000个和长度为518mm的零件3600个。
如何下料才能使消耗的圆钢数量最少?解:(一) 建立机械优化设计数学模型(设计变量、目标函数、约束条件)设698mm的零件记为①,518mm的零件记为②。
对本例题,若只用4m长的圆钢,则总共有6种下料方案:下5个零件①,0个零件②,利用率87% (%87%10040005698=⨯⨯) 方案一 下0个零件①,7个零件②,利用率91% (%91%10040007518=⨯⨯) 方案二下4个零件①,2个零件②,利用率96% (%96%100400025184698=⨯⨯+⨯) 方案三下3个零件①,3个零件②,利用率91% ( %91%100400035183698=⨯⨯+⨯) 方案四 (1)下2个零件①,5个零件②,利用率99% (%99%100400055182698=⨯⨯+⨯) 方案五下1个零件①,6个零件②,利用率95% (%95%100400065181698=⨯⨯+⨯) 方案六从式(1)可知,用4m长的圆钢总共有6种下料方法。
现用1X 、2X 、3X 、4X 、5X 、6X 分别表示按这种方式下料所需的圆钢数量,则下料方案可用表1表示。
2 / 8表1 下料方案Tab.1 Cutting material plan 原钢种类(m )数量零件① 零件② 方 案 4 1X5 0 方案一 4 2X0 7 方案二 4 3X 4 2 方案三 4 4X 3 3 方案四 4 5X 2 5 方案五 46X16方案六表示为数学模型就是Min 654321654321),,,,,(X X X X X X X X X X X X f +++++= (2)51X +43X +34X +25X +6X ≥4000 (3) 72X +23X +43X +55X +66X ≥3600 (4) X1≥0,X2≥0,X3≥0,X4≥0,X5≥0,X6≥0 (5)3 / 8式(2)称为目标函数,式(3)、式(4)和式(5)都称为约束条件。
机械优化设计经典实例

机械优化设计经典实例机械优化设计是指通过对机械结构和工艺的改进,提高机械产品的性能和技术指标的一种设计方法。
机械优化设计可以在保持原产品功能和形式不变的前提下,提高产品的可靠性、工作效率、耐久性和经济性。
本文将介绍几个经典的机械优化设计实例。
第一个实例是汽车发动机的优化设计。
汽车发动机是汽车的核心部件,其性能的提升对汽车整体性能有着重要影响。
一种常见的汽车发动机优化设计方法是通过提高燃烧效率来提高功率和燃油经济性。
例如,通过优化进气和排气系统设计,改善燃烧室结构,提高燃烧效率和燃油的利用率。
此外,采用新材料和制造工艺,减轻发动机重量,提高动力性能和燃油经济性也是重要的优化方向。
第二个实例是飞机机翼的优化设计。
飞机机翼是飞机气动设计中的关键部件,直接影响飞机的飞行性能、起降性能和燃油经济性。
机翼的优化设计中,常采用的方法是通过减小机翼的阻力和提高升力来提高飞机性能。
例如,优化机翼的气动外形,减小阻力和气动失速的风险;采用新材料和结构设计,降低机翼重量,提高飞机的载重能力和燃油经济性;优化翼尖设计,减小湍流损失,提高升力系数。
第三个实例是电机的优化设计。
电机是广泛应用于各种机械设备和电子产品中的核心动力装置。
电机的性能优化设计可以通过提高效率、减小体积、降低噪音等方面来实现。
例如,采用优化电磁设计和轴承设计,减小电机的损耗和噪音,提高效率;通过采用新材料和工艺,减小电机的尺寸和重量,实现体积紧凑和轻量化设计。
总之,机械优化设计在提高机械产品性能和技术指标方面有着重要应用。
通过针对不同机械产品的特点和需求,优化设计可以提高机械产品的可靠性、工作效率、耐久性和经济性。
这些经典实例为我们提供了有效的设计思路和方法,帮助我们在实际设计中充分发挥机械优化设计的优势和潜力。
第八章机械优化设计实例
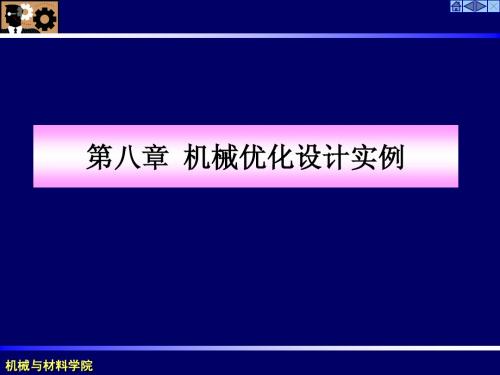
机械与材料学院
×
2、目标函数: 、目标函数:
考虑主轴最轻, 考虑主轴最轻,所以机床主轴优化设计的 目标函数为
材料的密度
机械与材料学院
×
3、约束条件: 、约束条件:
1)刚度约束条件:由于主轴刚度是一个重要 )刚度约束条件: 的性能指标,其外伸端的挠度y不得超过规定值 不得超过规定值y 的性能指标,其外伸端的挠度 不得超过规定值 0 所以可依此建立性能约束: 所以可依此建立性能约束:
例子
机械与材料学院
×
尺度变换前的等值线图
尺度变换后的等值线图
机械与材料学院
×
2、设计变量的尺度变换 、 ——对设计变量进行重新标度,使它们称 对设计变量进行重新标度, 对设计变量进行重新标度 为无量纲和规格化的设计变量。 为无量纲和规格化的设计变量。 方法: 方法:
原 设 计 变 量 新 设 计 变 量
机械与材料学院
×
2、目标函数的确定 、
目标函数——一项设计所追求的指标的数学反映 一项设计所追求的指标的数学反映 目标函数 要求: 要求: 能够用来评价设计的优劣 必须是设计变量的可计算函数
机械与材料学院
×
1)、优化目标的选择: )、优化目标的选择: )、优化目标的选择
应当对所追求的各项指标进行细致分析, 应当对所追求的各项指标进行细致分析,从 中选择最重要、 中选择最重要、最具代表性的指标作为优化 目标
机械与材料学院
×
•在性能约束中,又有复杂和简单之分 在性能约束中, 在性能约束中 约束函数有的很简单,可以表示成显式形式, 约束函数有的很简单,可以表示成显式形式, 即反映设计变量之间明显的函数关系,这类约束叫 即反映设计变量之间明显的函数关系, 显式约束。 做显式约束。例如设计曲柄连杆机构时的曲柄存在 约束条件 有的只能表示成隐式形式,例如复杂结构的性 有的只能表示成隐式形式, 能约束函数(变形、应力、频率等) 能约束函数(变形、应力、频率等),需要通过有 限元或动力学计算求得,机构的运动误差要用数值 限元或动力学计算求得, 积分来计算,这类约束叫做隐式约束 隐式约束。 积分来计算,这类约束叫做隐式约束。
- 1、下载文档前请自行甄别文档内容的完整性,平台不提供额外的编辑、内容补充、找答案等附加服务。
- 2、"仅部分预览"的文档,不可在线预览部分如存在完整性等问题,可反馈申请退款(可完整预览的文档不适用该条件!)。
- 3、如文档侵犯您的权益,请联系客服反馈,我们会尽快为您处理(人工客服工作时间:9:00-18:30)。
机械优化设计实例
压杆的最优化设计
压杆是一根足够细长的直杆,以学号为p值,自定义有设计变量的
尺寸限制值,求在p一定时d1、d2和l分别取何值时管状压杆的体积或重
量最小?(内外直径分别为d1、d2)两端承向轴向压力,并会因轴向压力
达到临界值时而突然弯曲,失去稳定性,所以,设计时,应使压应力不
超过材料的弹性极限,还必须使轴向压力小于压杆的临界载荷。
解:根据欧拉压杆公式,两端铰支的压杆,其临界载荷为:I——材料的惯性矩,EI为抗弯刚度
1、设计变量
现以管状压杆的内径d1、外径d2和长度l作为设计变量
2、目标函数
以其体积或重量作为目标函数
3、约束条件
以压杆不产生屈服和不破坏轴向稳定性,以及尺寸限制为约束条件,在外力为p的情况下建立优化模型:
1)
2)
3)
罚函数:
传递扭矩的等截面轴的优化设计解:1、设计变量:
2、目标函数
以轴的重量最轻作为目标函数:
3、约束条件:
1)要求扭矩应力小于许用扭转应力,即:
式中:——轴所传递的最大扭矩
——抗扭截面系数。
对实心轴
2)要求扭转变形小于许用变形。
即:
扭转角:
式中:G——材料的剪切弹性模数
Jp——极惯性矩,对实心轴:
3)结构尺寸要求的约束条件:
若轴中间还要承受一个集中载荷,则约束条件中要考虑:根据弯矩联合作用得出的强度与扭转约束条件、弯曲刚度的约束条件、对于较重要的和转速较高可能引起疲劳损坏的轴,应采用疲劳强度校核的安全系数法,增加一项疲劳强度不低于许用值的约束条件。
二级齿轮减速器的传动比分配
二级齿轮减速器,总传动比i=4,求在中心距A最小下如何
分配传动比?设齿轮分度圆直径依次为d1、d2、d3、d4。
第一、二
级减速比分别为i1、i2。
假设d1=d3,则:
七辊矫直实验
罚函数法是一种对实际计算和理论研究都非常有价值的优化方法,广泛用来求解约束问题。
其原理是将优化问题中的不等式约束和等式约束加权转换后,和原目标函数结合成新的目标函数,求解该新目标函数的无约束极小值,以期得到原问题的约束最优解。
考虑到本优化程序要处理的是一个兼而有之的问题,故采用混合罚函数法。
一)、优化过程
(1)、设计变量
以试件通过各矫直辊时所受到的弯矩为设计变量:
(2)、目标函数
以矫直机的驱动功率为目标函数
式中:——矫直速度,mm/s
——矫直辊直径,mm
——传动效率
——作用在辊子上的总传动力矩
——轧件弯曲变形所需的转动力矩,N.mm
——克服轧件与辊子间滚动摩擦所需的转动力矩,N.mm
——克服辊子轴承的摩擦及支承辊与工作辊间的滚动摩擦所需力矩,N.mm
上式表明,编制程序时也可以把目标函数简化为求弯矩和的最小值。
简化问题,可以将程序中的目标函数改为
(3)、不等式约束
首先,试件应满足咬入条件,即
式中:——一、二辊之间的相对压下量
——试件与矫直辊之间的滑动摩擦系数
其次,要保证试件每经过一个矫直单元,实现一次反向弯曲,且弯矩值在极限范围内,即
式中:——使试件产生反向弯曲的最小弯矩值,N.mm
为了使试件变形充分、均匀,在经过第一、第二个矫直单元时反弯曲率值与原始曲率值应尽量接近。
也就是说,前几个矫直单元采用大变形矫直方案。
试件从最后一个矫直辊中出来后,要满足质量要求,符合国家有关标准,即有
式中:——有关标准规定的残余曲率值,对于本试件
(4)、等式约束
应满足
式中:、、、——分别为相邻两辊之间的相对压下量
二)、优化数据
以原始曲率半径为2000mm的08F双层焊管为例,得到优化矫直力矩为
优化矫直力为
分别对原始双层曲率半径为1500mm、2500mm和3000mm的断面系数相同的08F双层卷焊管进行矫直力矩优化,得到的优化值与原始曲率半径为2000mm的值相差不大。
5级齿轮传动的传动比分配
在指挥仪及精密仪器中,常用如图所
示的多级减速器。
为了提高运动精度,不仅
要求减重,还要求转动惯量小。
已知总减速比为i,假定各级小齿轮参
数相同,各级减速比分别为,
且有。
下面推导转动惯量和
中心距的表达式。
解: 1.总转动惯量
式中为小齿轮转动惯量,。
若令等于下式右端括号内各项,即
当一定时,对求极小,则必为极小,称传动的转动惯量系数。
2.中心距
式中为小齿轮分度圆直径。
令等于下式右端括号内各项,则一定下,对求极小,必使亦极小,这意味着重量亦小。
称中心距系数,即
本问题要求减速器重量和转动惯量小,这是双目标优化问题,设计变量为,可用线形加权法构造双目标转化为单目标无约束优化问题,即
式中、为权因子,表明设计者对(标志转动惯量)和(标志重量)的重要程度而选定的系数,一般有,例如选,等。
选取不同、求解,可了解它们对传动比分配的影响,从中选设计者认为满意的解。
曲柄摇杆机构运动规律的最优化设计(复合形法)
当曲柄由其初始位置转到时,要求摇杆由其极限角开始按下列规律运动:
并且其传动角(机构的连杆与摇杆之间的夹角)的最大值及最小值应分别不大于、
不小于其许用值,即;。
1.确定设计变量
考虑到机构杆长按比例变化时不会改变其运动规律,因此在计算时常取曲柄为单位长度,即,而其他杆长则按比例取为的倍数;机架长常由结构布置事先给定,分析上图得关系式:
因此,仅,为独立变量,是二维最优化设计问题,
2.建立目标函数
可根据期望与偏差为最小的要求,来建立目标函数:
式中——期望输出角
——实际输出角
由右图求得
摇杆与BD连线夹角
机架与BD连线夹角
BD连线长度
式中(单位长度)、为已定常量。
3.给定约束条件
曲柄与机架处于共线位置时:
及得约束条件:
4.设计变量的可行域
曲柄存在的条件:
得约束条件:
取单位长度即,只有和为起作用约束,它们是两个椭圆方程。
最后的数学模型为
这是一个带有不等式约束具有两个设计变量的小型最优化设计问题,可采用直接法来求解。
曲柄摇杆机构
如图所示,当曲柄AB整周转动时,连杆BC上一点M实现给定轨迹,轨迹坐标方程为
要求确定各构件的长度,使点M的实际轨迹与给定轨迹间的偏差最小。
解:1.确定设计变量:
取各构件的杆长为设计变量,即
2.建立目标函数:
按连杆上点M实际实现的轨迹与要求实现的轨迹的均方偏差最小的原则建立目标函数,其函数形式可表达为,
式中,(s表示将曲柄转角分成s等份);
,为连杆上点M第j个位置所要求实现的坐标值;为点M实际实现的坐标值。
与可按下列公式计算得到:
式中,
其中第三式中的根号前的正负号应参照运动连续性来选取。
3.确定约束条件:
首先要保证曲柄AB能作整周回转。
若结构上要求,则可取下列约束条件(曲柄存在条件):
其次考虑机构具有较好的传力性能,按最小传动角大于写成的约束条件为
综上所述,这一优化设计问题的数学模型可表示为
求设计变量,使
满足于约束条件
4.计算结果:
以为例,计算结果为:
初始步长TT=0.01TT=0.05TT=0.1
0.062830.062150.08434
简化的机床主轴
当跨距l,外伸端a 求轴的内、外径d、D取何值的时候,主轴重量最轻?
解:1、确定设计变量
由于材料一定时,主轴内孔只与机床型号有关,所以设计变量为:
x = [ x 1x2x3]T=[l D a]T
2、目标函数:
考虑主轴最轻,所以
式中:ρ——材料密度
3、约束条件:
由于主轴刚度是一个重要的性能指标,其外伸端的挠度y不得超过规定值y0所以可依此建立性能的约束:
在外力F给定的情况下,挠度,
所以:
由于机床主轴对刚度要求比较高,当满足刚度要求时,强度有富裕,所以这里可以不考虑应力约束条件。
边界的约束条件由具体机床结构与主轴材料而定:
即:也即:
例子:d=30mm,F=15000N,y-5-5,r0设计变量x1 x2x3
初始值480100120
下限值3006090
上限值650140150
解:采用内点惩罚函数法解,代入已知数据后,经过17次迭代,计算收敛,最优解为:x* = [300.036 75.244 90.001]T
f(x*) = 11.37。