乘用车副车架静刚度分析规范
乘用车副车架计算模态分析边界当量方法研究

乘用车副车架计算模态分析边界当量方法研究乘用车副车架的计算模态分析是一项重要的技术,可以用来评估车身的刚性和强度。
在该领域,边界当量方法是一种常用的近似方法,通过将实际加载替代为等效静态和动态力载荷,以简化计算过程。
本文将介绍乘用车副车架计算模态分析边界当量方法的研究进展,并探讨其优缺点。
边界当量方法的基本原理是将实际载荷替换为等效载荷,使得系统的动态响应与实际载荷下的响应一致。
该方法的优点在于可以简化计算过程,减少计算时间和成本。
此外,边界当量方法可以将动态载荷解决为对应的静态载荷,以简化结构分析。
边界当量方法的缺点在于,其计算结果可能会出现误差,因为实际载荷会随时间变化而产生变化,而静态边界当量方法无法精确模拟这种变化。
边界当量方法可以分为几种类型,包括静态和动态的方法。
静态边界当量方法使用最小和最大值的载荷范围来模拟实际载荷。
动态边界当量方法使用均方根振幅等参数来描述实际载荷的动态性。
此外,还有一些其他边界当量方法,例如基于统计学的方法,可以在不知道实际载荷的情况下对其进行近似估计。
乘用车副车架计算模态分析边界当量方法的研究领域广泛,包括对载荷的测量、建立边界当量模型以及验证模型精度等方面。
最近的研究还关注了不同载荷模拟方法的比较,以及不同设计方案的模态优化。
例如,研究表明使用动态边界当量方法可以获得更准确的结果,而基于统计学的方法可以在无法确定载荷的情况下进行设计。
总之,乘用车副车架计算模态分析边界当量方法是一种广泛应用的技术,其优点在于简化计算过程,在有限时间内获得较精确的结果。
然而,该方法的缺点需要注意,在设计过程中需要慎重考虑误差问题。
研究还需要进一步探讨如何将边界当量方法与优化设计相结合,以提高车身的性能和强度。
近年来,随着汽车市场的快速发展,乘用车副车架的设计已经受到了越来越多的关注。
在副车架的设计中,计算模态分析是一项重要的技术,可以评估车身的刚性和强度。
在计算模态分析中,边界当量方法是一种常用的技术,可以将实际载荷转换为等效载荷,从而简化计算过程。
探讨汽车副车架强度模态分析及结构优化

探讨汽车副车架强度模态分析及结构优化1. 引言1.1 研究背景汽车副车架是汽车重要的结构部件之一,承担着支撑车身、吸收冲击力、传递动力等重要功能。
随着汽车的发展,人们对汽车副车架的要求也越来越高,希望能够在保证结构强度的前提下减轻重量,提高燃油效率和安全性。
现有汽车副车架结构往往存在过多的冗余部分和设计缺陷,导致结构重量过大、强度不足等问题。
对汽车副车架进行强度模态分析和结构优化显得尤为重要。
通过分析副车架在不同工况下的受力特点和振动模态,可以发现潜在的弱点和瓶颈,从而有针对性地进行结构优化,提高其整体性能。
基于以上背景,本文将针对汽车副车架的强度模态分析和结构优化展开研究,旨在为汽车工程领域提供更有效的设计方案和优化策略,促进汽车轻量化、高效化的发展。
1.2 研究意义汽车副车架是汽车重要的结构部件之一,其负责支撑整车重量并承载各种动态载荷。
对汽车副车架进行强度模态分析和结构优化是非常重要的,具有以下几个方面的研究意义:汽车副车架的强度模态分析可以帮助工程师了解其在不同工况下的受力情况,从而预测可能存在的强度问题,为设计提供参考和改进方向。
通过分析副车架的振动模态,可以确定其固有频率和形态,进而评估结构的动力性能和耐久性。
结构优化可以有效地降低副车架的重量,提高结构的刚度和强度,降低振动和噪音,进而改善车辆的行驶性能和安全性。
通过优化设计,可以有效地降低生产成本和能源消耗,提高汽车整体的竞争力。
研究汽车副车架强度模态分析及结构优化还可以推动汽车工程技术的进步和创新,促进汽车制造业的可持续发展。
通过优化设计,可以提高汽车的整体性能和环保性能,满足不断提升的市场需求和法规标准。
对汽车副车架进行强度模态分析和结构优化具有重要的意义和价值。
1.3 研究目的研究目的是为了深入探讨汽车副车架的强度和振动特性,为设计和优化提供理论支持和技术指导。
具体包括以下几个方面的目标:1. 分析副车架的承载能力和抗疲劳性能,找出存在的弱点和瓶颈,为提高车辆整体结构的稳定性和安全性提供依据。
探讨汽车副车架强度模态分析及结构优化
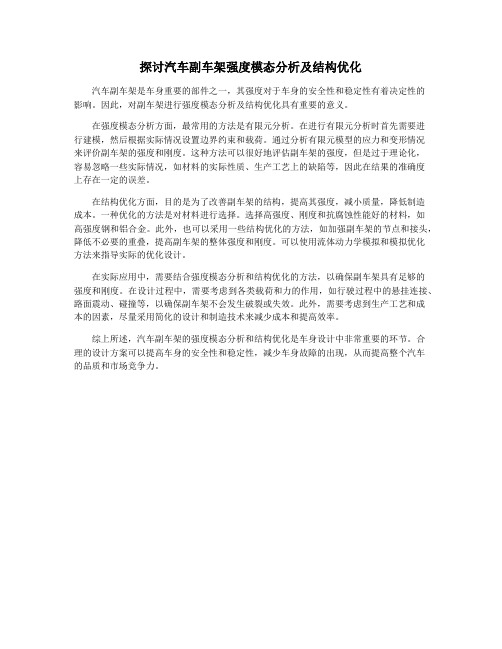
探讨汽车副车架强度模态分析及结构优化汽车副车架是车身重要的部件之一,其强度对于车身的安全性和稳定性有着决定性的影响。
因此,对副车架进行强度模态分析及结构优化具有重要的意义。
在强度模态分析方面,最常用的方法是有限元分析。
在进行有限元分析时首先需要进行建模,然后根据实际情况设置边界约束和载荷。
通过分析有限元模型的应力和变形情况来评价副车架的强度和刚度。
这种方法可以很好地评估副车架的强度,但是过于理论化,容易忽略一些实际情况,如材料的实际性质、生产工艺上的缺陷等,因此在结果的准确度上存在一定的误差。
在结构优化方面,目的是为了改善副车架的结构,提高其强度,减小质量,降低制造成本。
一种优化的方法是对材料进行选择。
选择高强度、刚度和抗腐蚀性能好的材料,如高强度钢和铝合金。
此外,也可以采用一些结构优化的方法,如加强副车架的节点和接头,降低不必要的重叠,提高副车架的整体强度和刚度。
可以使用流体动力学模拟和模拟优化方法来指导实际的优化设计。
在实际应用中,需要结合强度模态分析和结构优化的方法,以确保副车架具有足够的强度和刚度。
在设计过程中,需要考虑到各类载荷和力的作用,如行驶过程中的悬挂连接、路面震动、碰撞等,以确保副车架不会发生破裂或失效。
此外,需要考虑到生产工艺和成本的因素,尽量采用简化的设计和制造技术来减少成本和提高效率。
综上所述,汽车副车架的强度模态分析和结构优化是车身设计中非常重要的环节。
合理的设计方案可以提高车身的安全性和稳定性,减少车身故障的出现,从而提高整个汽车的品质和市场竞争力。
汽车车架刚度评价标准
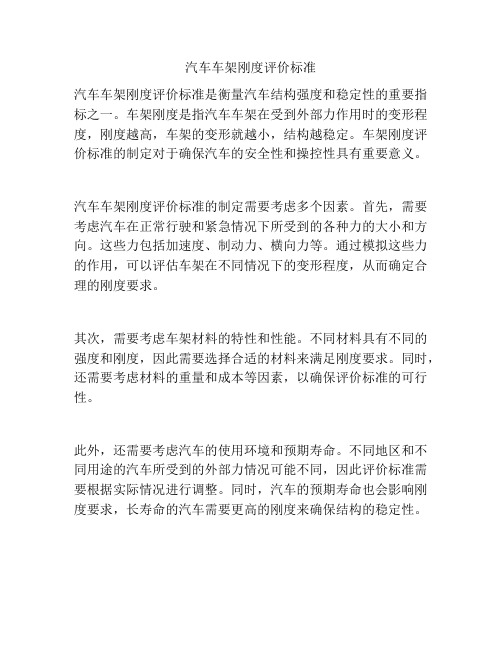
汽车车架刚度评价标准汽车车架刚度评价标准是衡量汽车结构强度和稳定性的重要指标之一。
车架刚度是指汽车车架在受到外部力作用时的变形程度,刚度越高,车架的变形就越小,结构越稳定。
车架刚度评价标准的制定对于确保汽车的安全性和操控性具有重要意义。
汽车车架刚度评价标准的制定需要考虑多个因素。
首先,需要考虑汽车在正常行驶和紧急情况下所受到的各种力的大小和方向。
这些力包括加速度、制动力、横向力等。
通过模拟这些力的作用,可以评估车架在不同情况下的变形程度,从而确定合理的刚度要求。
其次,需要考虑车架材料的特性和性能。
不同材料具有不同的强度和刚度,因此需要选择合适的材料来满足刚度要求。
同时,还需要考虑材料的重量和成本等因素,以确保评价标准的可行性。
此外,还需要考虑汽车的使用环境和预期寿命。
不同地区和不同用途的汽车所受到的外部力情况可能不同,因此评价标准需要根据实际情况进行调整。
同时,汽车的预期寿命也会影响刚度要求,长寿命的汽车需要更高的刚度来确保结构的稳定性。
根据以上因素,汽车车架刚度评价标准可以分为静态刚度和动态刚度两个方面进行评价。
静态刚度是指汽车在静止状态下所受到的外部力作用时的变形程度。
动态刚度是指汽车在运动状态下所受到的外部力作用时的变形程度。
静态刚度评价主要包括静态弯曲刚度、静态扭转刚度等指标,动态刚度评价主要包括动态弯曲刚度、动态扭转刚度等指标。
静态刚度评价可以通过实验和数值模拟两种方法进行。
实验方法可以通过在实际道路上进行测试或者在实验室中进行模拟试验来获取相关数据。
数值模拟方法可以通过计算机软件对车架进行建模,并模拟不同情况下的力作用,从而评估车架的变形程度。
动态刚度评价主要通过道路试验来进行。
在实际道路上进行加速、制动、转弯等操作,通过测量车架的变形程度来评估其动态刚度。
同时,也可以通过计算机仿真来模拟不同情况下的动态刚度。
总之,汽车车架刚度评价标准是确保汽车结构强度和稳定性的重要手段。
通过合理制定评价标准,可以提高汽车的安全性和操控性,并满足不同地区和用途的需求。
副车架设计规范-----------新能源汽车

为便于简化后期焊接工艺,外部安装套管类零部件设计过程中,一定要保证在上下颠倒焊接时可互换通用,一般需注意上下表面公差要求相同、两端倒角相同等,且凸出高度推荐大于6mm,套管与钣金件留有(0-0.5)mm间隙。
图1-15 某车型外部安装套管
4.12副车架平台化设计
副车架设计之初就应考虑需搭载此副车架的所有车型的平台化设计,前副车架主要考虑不同动力总成、两四驱、左右舵等因素影响,如某车型共搭载4款动力总成,在此基础上需同步开发两四驱、左右舵车型,在副车架设计过程中,需考虑满足所有动力总成的最大包络要求、右舵转向器、四驱分动器等零部件的安装要求。
4.3 副车架与车身安装点、定位点设计
副车架与车身安装点一般为4个或者6个,且左右两侧相互对称,,4个安装点设计位置一般位于副车架的4个边角处, 如图1-3、1-4、1-5所示,6个安装点设计方式相对4个安装点方案一般在下摆臂安装点之间采用焊接支架的形式增加2个对称的安装点,如图1、2所示,安装点设计完成后需进行装配可行性、可维修性校核,特别是位于下摆臂之间的副车架安装点,摆臂设计过程中应对其安装点进行避让,且此安装点装配可行性校核时需将下摆臂跳动到下极限状态进行校核,如图1-1所示。
动力学性能分析部
NC阶段
5
前后悬架系统疲劳分析
可靠性工程研究院
NC阶段
6
前后悬架系统焊点及焊缝疲劳分析
可靠性工程研究院
NC阶段
6.2 副车架CAE分析所需输入
1、副车架设计数模及悬架系统数据;
2、各钣金件材质明细清单;
3、悬架系统运动硬点列表;
4、悬架系统所有弹性元件(包括副车架衬套等)刚度曲线;
5、最新副车架数据相对上版数据具体变更点。
乘用车悬架安装点静刚度分析规范
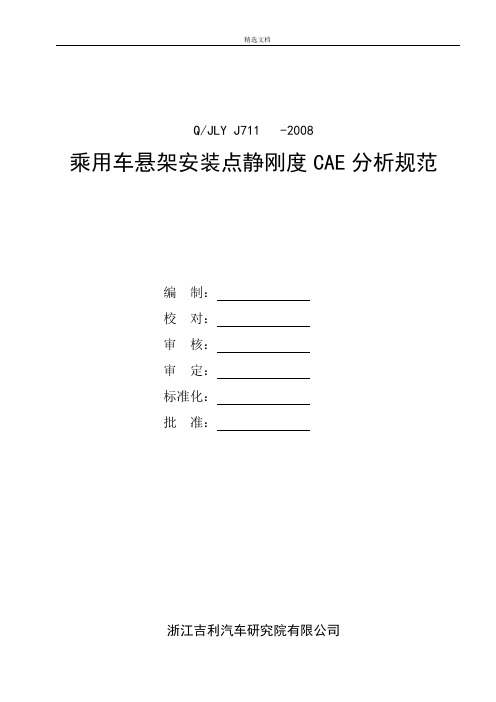
Q/JLY J711 -2008乘用车悬架安装点静刚度CAE分析规范编制:校对:审核:审定:标准化:批准:浙江吉利汽车研究院有限公司二〇〇八年九月前言为了给新车型开发提供设计依据,指导新车设计,评估新车结构性能,结合本企业实际情况,制定本标准。
本规范由浙江吉利汽车研究院有限公司提出。
本规范由浙江吉利汽车研究院有限公司综合技术部负责起草。
本规范主要起草人:汤志鸿。
本规范于2008年9月15日发布并实施。
1 范围本标准规定了乘用车悬架安装点静刚度CAE分析的软硬件设施、输入条件、输出物、分析方法、分析数据处理及分析报告。
本标准适用于乘用车悬架安装点静刚度CAE分析。
2 软硬件设施乘用车悬架安装点静刚度CAE分析,主要包括以下设施:a)软件设施:主要用于求解的软件,采用MSC/NASTRAN;b)硬件设施:高性能计算机。
3 输入条件3.1 白车身3D几何模型乘用车悬架安装点静刚度CAE分析的白车身3D几何模型,数据要求如下:a)白车身各个零件的厚度或厚度线;b)白车身几何焊点数据;c)3D CAD数据中无明显的穿透或干涉;d)白车身各个零件的明细表。
3.2 白车身有限元模型乘用车悬架安装点静刚度分析的输入条件主要指白车身的有限元模型,一个完整的白车身有限元模型中含内容如下:a)白车身各个零件的网格数据;b)白车身焊点数据;c)各个零件的材料数据;d)各个零件的厚度数据。
4 输出物乘用车悬架安装点静刚度分析的输出物为PDF文档格式的分析报告,针对不同的车型统一命名为《车型悬架安装点静刚度分析报告》(“车型”用具体车型代号替代如:车型为GC-1,则分析报告命名为《GC-1悬架安装点静刚度分析报告》),报告内容的按7规定的内容编制。
5 分析方法5.1 分析模型分析模型包括白车身的有限元模型(不含四门两盖和前、后挡风玻璃),钣金件均采用壳单元模拟。
5.2 分析模型建立建立有限元模型,应符合下列要求:a)白车身各个零件的网格质量应符合求解器的要求;b)白车身同一总成的零件,须放在同一个“集合”里;c)白车身各个零件的材料,须与明细表规定的材料相对应;d)白车身各个零件的厚度,须与明细表规定的厚度相对应;e)焊点几何坐标须与3D焊点坐标一致,焊点连接的层数须明确,焊点单元的直径设为6mm;f)白车身有限元模型的质量应该与实车相等。
某纯电动汽车后副车架安装点刚度分析与优化设计
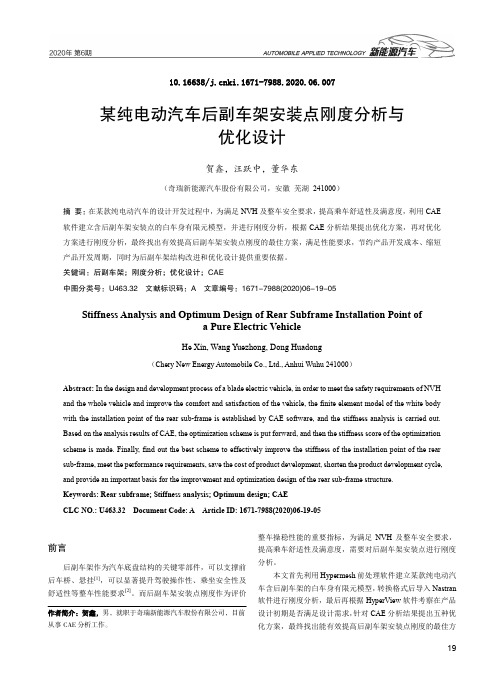
10.16638/ki.1671-7988.2020.06.007某纯电动汽车后副车架安装点刚度分析与优化设计贺鑫,汪跃中,董华东(奇瑞新能源汽车股份有限公司,安徽芜湖241000)摘要:在某款纯电动汽车的设计开发过程中,为满足NVH及整车安全要求,提高乘车舒适性及满意度,利用CAE 软件建立含后副车架安装点的白车身有限元模型,并进行刚度分析,根据CAE分析结果提出优化方案,再对优化方案进行刚度分析,最终找出有效提高后副车架安装点刚度的最佳方案,满足性能要求,节约产品开发成本、缩短产品开发周期,同时为后副车架结构改进和优化设计提供重要依据。
关键词:后副车架;刚度分析;优化设计;CAE中图分类号:U463.32 文献标识码:A 文章编号:1671-7988(2020)06-19-05Stiffness Analysis and Optimum Design of Rear Subframe Installation Point ofa Pure Electric VehicleHe Xin, Wang Yuezhong, Dong Huadong(Chery New Energy Automobile Co., Ltd., Anhui Wuhu 241000)Abstract: In the design and development process of a blade electric vehicle, in order to meet the safety requirements of NVH and the whole vehicle and improve the comfort and satisfaction of the vehicle, the finite element model of the white body with the installation point of the rear sub-frame is established by CAE software, and the stiffness analysis is carried out. Based on the analysis results of CAE, the optimization scheme is put forward, and then the stiffness score of the optimization scheme is made. Finally, find out the best scheme to effectively improve the stiffness of the installation point of the rear sub-frame, meet the performance requirements, save the cost of product development, shorten the product development cycle, and provide an important basis for the improvement and optimization design of the rear sub-frame structure. Keywords: Rear subframe; Stiffness analysis; Optimum design; CAECLC NO.: U463.32 Document Code: A Article ID: 1671-7988(2020)06-19-05前言后副车架作为汽车底盘结构的关键零部件,可以支撑前后车桥、悬挂[1],可以显著提升驾驶操作性、乘坐安全性及舒适性等整车性能要求[2]。
汽车车架的静态强度分析
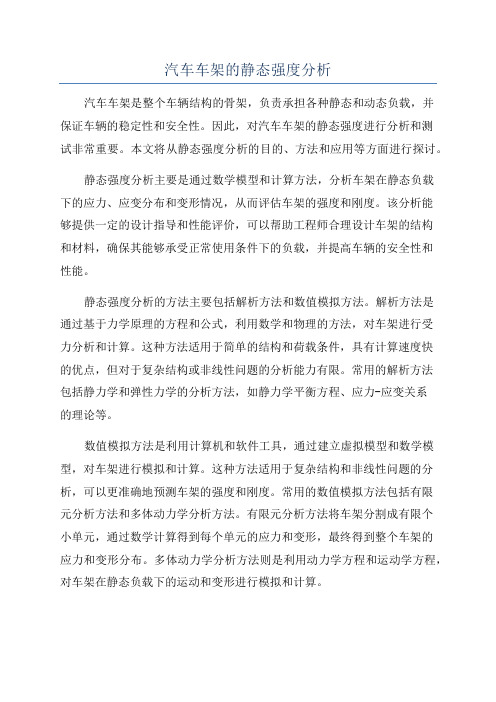
汽车车架的静态强度分析汽车车架是整个车辆结构的骨架,负责承担各种静态和动态负载,并保证车辆的稳定性和安全性。
因此,对汽车车架的静态强度进行分析和测试非常重要。
本文将从静态强度分析的目的、方法和应用等方面进行探讨。
静态强度分析主要是通过数学模型和计算方法,分析车架在静态负载下的应力、应变分布和变形情况,从而评估车架的强度和刚度。
该分析能够提供一定的设计指导和性能评价,可以帮助工程师合理设计车架的结构和材料,确保其能够承受正常使用条件下的负载,并提高车辆的安全性和性能。
静态强度分析的方法主要包括解析方法和数值模拟方法。
解析方法是通过基于力学原理的方程和公式,利用数学和物理的方法,对车架进行受力分析和计算。
这种方法适用于简单的结构和荷载条件,具有计算速度快的优点,但对于复杂结构或非线性问题的分析能力有限。
常用的解析方法包括静力学和弹性力学的分析方法,如静力学平衡方程、应力-应变关系的理论等。
数值模拟方法是利用计算机和软件工具,通过建立虚拟模型和数学模型,对车架进行模拟和计算。
这种方法适用于复杂结构和非线性问题的分析,可以更准确地预测车架的强度和刚度。
常用的数值模拟方法包括有限元分析方法和多体动力学分析方法。
有限元分析方法将车架分割成有限个小单元,通过数学计算得到每个单元的应力和变形,最终得到整个车架的应力和变形分布。
多体动力学分析方法则是利用动力学方程和运动学方程,对车架在静态负载下的运动和变形进行模拟和计算。
静态强度分析在汽车工程中具有广泛的应用。
首先,它可以用于评估车架的设计方案和材料选择。
通过对不同设计方案进行静态强度分析,可以找到最优的设计方案,并选择适当的材料,以提高车架的抗弯、抗压和抗扭强度。
其次,静态强度分析也可以用于验证车架的安全性能。
通过模拟车架在极端负载情况下的应力、应变和变形,可以评估车架的安全性能,并指导相关安全措施的设计。
此外,静态强度分析还可以应用于车架的优化设计和性能改进,以满足不同使用条件和需求。
探讨汽车副车架强度模态分析及结构优化

探讨汽车副车架强度模态分析及结构优化汽车副车架是汽车结构中的重要组成部分,它承担着车辆的重量、扭矩和振动的传递,同时在车辆碰撞时发挥着重要的承载作用。
汽车副车架的强度分析和结构优化对于车辆的安全性和性能至关重要。
本文将就汽车副车架强度模态分析及结构优化进行探讨。
我们来看一下汽车副车架的强度模态分析。
汽车副车架主要受到来自发动机和车辆行驶时的负载作用,因此在强度模态分析中,需要考虑副车架在不同工况下的受力情况。
通过有限元分析等方法,可以对副车架的应力、应变和振动特性进行分析,找出其在不同工况下的受力状态和强度情况。
这对于设计和改进副车架的结构和材料具有很大的指导作用。
结构优化是提高汽车副车架强度的重要手段。
通过结构优化,可以改进副车架的设计方案,使其在不增加重量的情况下提高强度和刚度。
可以采用新的材料和工艺,提高副车架的耐疲劳性和抗冲击能力。
还可以通过减少副车架的零部件数量和连接处,降低副车架的制造成本和装配难度。
这些优化措施将有助于提高汽车副车架的整体性能和使用寿命。
在进行汽车副车架强度模态分析和结构优化时,需要注意以下几点。
需要充分考虑副车架的受力特点和工况,不同的车型和用途对副车架的要求是不同的,因此在分析和优化过程中需要进行针对性的研究。
要充分利用现代化的分析和优化工具,如有限元分析软件、拓扑优化算法等,以更有效地进行副车架强度模态分析和结构优化。
在进行结构优化时,需要综合考虑副车架的强度、刚度、重量和成本等多方面因素,以找出最合适的设计方案。
汽车副车架强度模态分析及结构优化是提高汽车安全性和性能的重要手段。
通过对副车架的受力特点和工况进行分析,可以找出其在实际使用中的弱点和问题,通过结构优化提出改进方案,从而使汽车副车架在保证安全的前提下具有更高的强度和刚度。
希望本文的内容对于相关领域的研究者和从业者有所帮助,促进汽车副车架结构的不断优化和提升。
轿车后副车架多轴疲劳分析
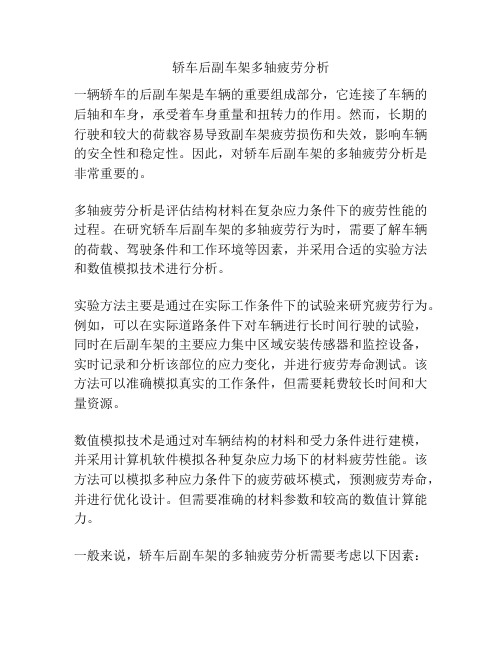
轿车后副车架多轴疲劳分析一辆轿车的后副车架是车辆的重要组成部分,它连接了车辆的后轴和车身,承受着车身重量和扭转力的作用。
然而,长期的行驶和较大的荷载容易导致副车架疲劳损伤和失效,影响车辆的安全性和稳定性。
因此,对轿车后副车架的多轴疲劳分析是非常重要的。
多轴疲劳分析是评估结构材料在复杂应力条件下的疲劳性能的过程。
在研究轿车后副车架的多轴疲劳行为时,需要了解车辆的荷载、驾驶条件和工作环境等因素,并采用合适的实验方法和数值模拟技术进行分析。
实验方法主要是通过在实际工作条件下的试验来研究疲劳行为。
例如,可以在实际道路条件下对车辆进行长时间行驶的试验,同时在后副车架的主要应力集中区域安装传感器和监控设备,实时记录和分析该部位的应力变化,并进行疲劳寿命测试。
该方法可以准确模拟真实的工作条件,但需要耗费较长时间和大量资源。
数值模拟技术是通过对车辆结构的材料和受力条件进行建模,并采用计算机软件模拟各种复杂应力场下的材料疲劳性能。
该方法可以模拟多种应力条件下的疲劳破坏模式,预测疲劳寿命,并进行优化设计。
但需要准确的材料参数和较高的数值计算能力。
一般来说,轿车后副车架的多轴疲劳分析需要考虑以下因素:1.荷载:轿车后副车架承受着车身和后轴的质量和加速、制动等力的作用。
因此,荷载是影响后副车架疲劳寿命的重要因素。
2.材料:后副车架的材料应具有较高的强度、塑性和韧性,以抵抗荷载引起的应力和变形。
同时,也需要考虑材料在不同应力下的疲劳寿命和破坏模式。
3.几何形状:后副车架的形状和尺寸影响了它的刚度和应力分布。
因此,需要进行优化设计,以减少应力集中和疲劳破坏的风险。
4.工作环境:轿车后副车架在不同的工作环境下,如高温、湿度、盐雾等条件下,也会受到不同的腐蚀和疲劳作用,因此需要特别考虑。
总之,轿车后副车架的多轴疲劳分析是保证车辆安全性和性能的重要环节。
通过合理的实验方法和数值模拟技术,可以准确评估后副车架的疲劳寿命和破坏模式,并进行结构优化,提高车辆的安全性和稳定性。
汽车底盘车架设计的静态与动态分析

汽车底盘车架设计的静态与动态分析汽车底盘车架是整车结构的基础,它承受着车辆整体重量及各种力和扭矩。
因此,在汽车底盘车架设计过程中,静态和动态分析是必不可少的步骤。
静态分析是指在车身静止的情况下,对底盘车架进行受力分析。
首先,我们需要确定车辆的载荷条件,包括车身质量、乘客数量、行李负荷等。
然后,根据这些载荷条件和设计要求,计算车架在静态状态下的应力和变形情况。
在进行静态分析时,需要考虑以下几个方面:1. 材料强度和刚度:选择合适的材料,并确定其强度和刚度参数。
常见的材料包括钢材和铝合金等。
根据材料的特性,计算车架在载荷作用下的应力和变形情况。
2. 荷载条件:准确确定车身的质量分布情况,包括车轮的荷载情况、前后配重比例等。
根据这些荷载条件,计算车架在不同载荷情况下的应力。
3. 过程动力学:考虑车辆行驶过程中的加速、制动、转向等动力学载荷,并进行相应的静态分析。
这些载荷往往是不稳定和非均匀的,需要进行合理的荷载分析和参数计算。
动态分析是指在车身运动的情况下,对底盘车架进行受力分析。
与静态分析相比,动态分析更加复杂,需要考虑更多的因素。
在进行动态分析时,需要注意以下几个方面:1. 荷载分析:根据车辆的动力学特性,确定车架在不同行驶条件下的荷载条件。
包括车辆加速、制动、转向、行驶过程中的颠簸等。
确保车架能够承受这些荷载并保持合适的刚度和强度。
2. 振动分析:考虑车辆行驶时的振动情况,采用有限元分析等方法,计算车架在不同频率下的振动响应。
并结合相关标准和限制条件,设计合适的减振措施。
3. 动态稳定性:确保车架在各种行驶条件下保持稳定和可控。
通过优化设计,提高车辆的操控性和安全性。
综上所述,汽车底盘车架设计的静态与动态分析是保证车辆安全性和可靠性的关键步骤。
在设计过程中,需要考虑车辆的载荷条件、材料强度和刚度、动力学特性、振动响应等因素。
通过合理的分析和优化设计,确保底盘车架能够承受各种力和扭矩,保持良好的稳定性和控制性,为驾驶员提供安全、舒适的行驶体验。
轿车车身静态刚度计算及静态竖直弯曲刚度优化分析
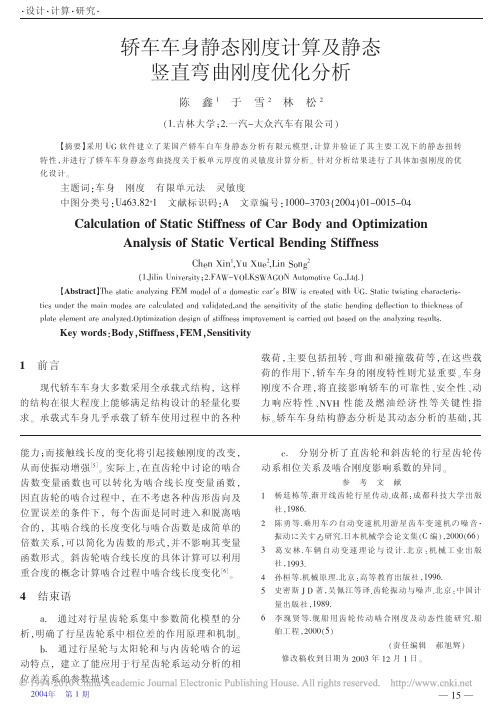
02(, ! $ 弯曲刚度和弯曲最大挠度的计算值与试验
值偏差几乎为零 ! 因此 " 认为模拟计算的模型是准确 的 "可以用于进一步的分析 !
"
结构修改灵敏度分析
在结构优化设计中 " 需要知道结构性能指标对
,(" %$* - +)&<
"$* "+)
现代的设计分析软件引入了灵敏度分析的功能 模块 " 使得灵敏度的计算分析成为方便有效的结构 分析方法 ! #$%&% 的灵敏度分析被安排在优化模块
(
!
轿车车身静态特性的计算及试验
采用 !" 软件建立有限元模型 " 使用 #$%&% 软
件进行模拟计算 ! 主要步骤有 #在三维实体模型的基 础上 " 采用 ’ 结点或 ( 结点空间板壳单元 %)*++,( 进 行有限元网格的划分 " 将车身离散划分为 - ../ 个 结点 "/ 0// 个单元 $ 确定单元的材料特性和常数 $ 给 定边界条件和载荷工况 $计算 $优化分析 ! 计算时采用的边界条件和载荷 工 况 % 图 .& 为 # 计算扭转刚度时 " 参照试验情况 "边界条件是约束后 悬架固定座支撑点的所有自由度 $ 载荷条件是在左 右前轮罩悬架弹簧支座支撑点处施加大小相等 ’ 方 向相反的铅垂力 - ,1- $ " 相当于施加扭矩 , 1-(2( $ 3 ! 计算弯曲刚度时 " 参照试验情况 " 边界条件是 约束前 ’ 后悬架固定座支撑点的所有自由度 $载荷条 件是在座椅固定处左右对称施加向下的力 " 大小总 和为 / 0(02’ $ !
探讨汽车副车架强度模态分析及结构优化
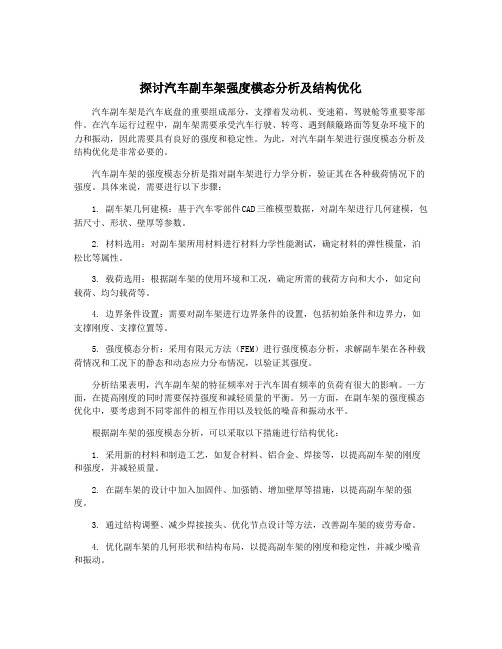
探讨汽车副车架强度模态分析及结构优化汽车副车架是汽车底盘的重要组成部分,支撑着发动机、变速箱、驾驶舱等重要零部件。
在汽车运行过程中,副车架需要承受汽车行驶、转弯、遇到颠簸路面等复杂环境下的力和振动,因此需要具有良好的强度和稳定性。
为此,对汽车副车架进行强度模态分析及结构优化是非常必要的。
汽车副车架的强度模态分析是指对副车架进行力学分析,验证其在各种载荷情况下的强度。
具体来说,需要进行以下步骤:1. 副车架几何建模:基于汽车零部件CAD三维模型数据,对副车架进行几何建模,包括尺寸、形状、壁厚等参数。
2. 材料选用:对副车架所用材料进行材料力学性能测试,确定材料的弹性模量,泊松比等属性。
3. 载荷选用:根据副车架的使用环境和工况,确定所需的载荷方向和大小,如定向载荷、均匀载荷等。
4. 边界条件设置:需要对副车架进行边界条件的设置,包括初始条件和边界力,如支撑刚度、支撑位置等。
5. 强度模态分析:采用有限元方法(FEM)进行强度模态分析,求解副车架在各种载荷情况和工况下的静态和动态应力分布情况,以验证其强度。
分析结果表明,汽车副车架的特征频率对于汽车固有频率的负荷有很大的影响。
一方面,在提高刚度的同时需要保持强度和减轻质量的平衡。
另一方面,在副车架的强度模态优化中,要考虑到不同零部件的相互作用以及较低的噪音和振动水平。
根据副车架的强度模态分析,可以采取以下措施进行结构优化:1. 采用新的材料和制造工艺,如复合材料、铝合金、焊接等,以提高副车架的刚度和强度,并减轻质量。
2. 在副车架的设计中加入加固件、加强销、增加壁厚等措施,以提高副车架的强度。
3. 通过结构调整、减少焊接接头、优化节点设计等方法,改善副车架的疲劳寿命。
4. 优化副车架的几何形状和结构布局,以提高副车架的刚度和稳定性,并减少噪音和振动。
总之,强度模态分析及结构优化对于汽车副车架的设计和制造至关重要,可以提高汽车底盘的强度和稳定性,进而提高汽车的安全性和驾驶舒适性。
探讨汽车副车架强度模态分析及结构优化

探讨汽车副车架强度模态分析及结构优化汽车副车架是汽车结构中的重要部分,它不仅承载着车身和发动机的重量,还需要具有足够的强度和刚度以保证车辆的稳定性和安全性。
在汽车设计中,副车架的强度和刚度是至关重要的,因此进行强度模态分析和结构优化是非常必要的。
我们来谈谈汽车副车架的强度模态分析。
强度模态分析是指通过数学模型和有限元分析方法,对副车架进行受力和振动情况的研究。
通过强度模态分析,可以得到副车架在不同受力情况下的应力分布和变形情况,从而找出存在的弱点和问题,为结构优化提供基础数据。
副车架的强度模态分析主要包括静态受力分析和模态振动分析两个方面。
在静态受力分析中,通过施加不同方向和大小的受力,可以得到副车架在负载情况下的应力分布情况。
而在模态振动分析中,可以得到副车架在外界激励下的振动模态和频率响应情况。
通过这两个方面的分析,可以全面了解副车架的受力和振动特性,找出存在的问题和改进的空间。
接下来,我们来谈谈副车架的结构优化。
在进行强度模态分析后,根据得到的数据和分析结果,可以对副车架的结构进行优化设计。
结构优化的目标是在保证强度和刚度的前提下,降低结构的重量和成本,提高车辆的性能和经济性。
副车架的结构优化主要包括材料选择、结构形式、布局设计和连接方式等方面。
首先是材料选择,通过选用高强度且轻量化的材料,可以在保证强度和刚度的前提下减少结构的重量。
其次是结构形式的优化,可以通过优化结构的形式和布局,使得副车架在受力和振动情况下能够更加均匀和合理地分布应力和变形。
最后是连接方式的优化,通过合理的连接方式和接缝设计,可以提高结构的稳定性和可靠性。
在进行结构优化时,还需要考虑到生产工艺、成本和可靠性等方面的因素。
结构的复杂程度和加工难度,对材料的加工性和成本,以及对车辆的使用寿命和安全性等方面都需要进行全面考虑。
探讨汽车副车架强度模态分析及结构优化
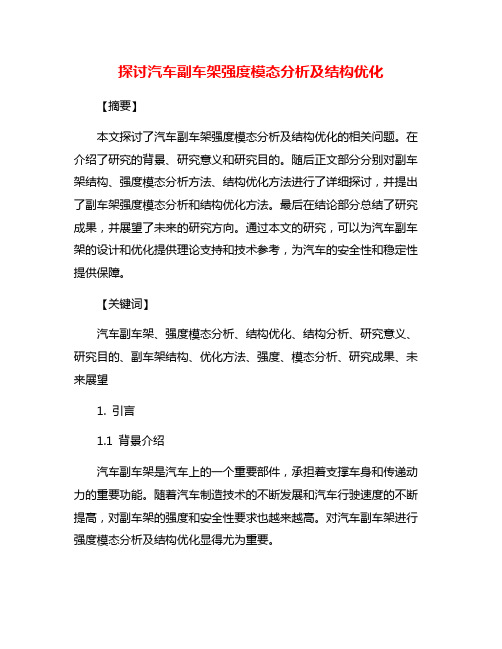
探讨汽车副车架强度模态分析及结构优化【摘要】本文探讨了汽车副车架强度模态分析及结构优化的相关问题。
在介绍了研究的背景、研究意义和研究目的。
随后正文部分分别对副车架结构、强度模态分析方法、结构优化方法进行了详细探讨,并提出了副车架强度模态分析和结构优化方法。
最后在结论部分总结了研究成果,并展望了未来的研究方向。
通过本文的研究,可以为汽车副车架的设计和优化提供理论支持和技术参考,为汽车的安全性和稳定性提供保障。
【关键词】汽车副车架、强度模态分析、结构优化、结构分析、研究意义、研究目的、副车架结构、优化方法、强度、模态分析、研究成果、未来展望1. 引言1.1 背景介绍汽车副车架是汽车上的一个重要部件,承担着支撑车身和传递动力的重要功能。
随着汽车制造技术的不断发展和汽车行驶速度的不断提高,对副车架的强度和安全性要求也越来越高。
对汽车副车架进行强度模态分析及结构优化显得尤为重要。
汽车副车架结构复杂,受到多种力的作用,如静载、动载、撞击载荷等。
传统的计算方法难以满足精确的分析需求,因此需要借助现代计算机辅助工程技术进行分析。
通过强度模态分析方法和结构优化方法,可以对汽车副车架的受力情况进行深入研究,找出其弱点并进行优化改进,提高副车架的整体性能和安全性。
本文旨在通过对汽车副车架强度模态分析及结构优化的研究,为汽车制造行业提供参考和借鉴,提高汽车副车架的设计水平和质量。
也希望通过本文的研究成果,为未来进一步深入探讨汽车结构优化提供基础和方向。
1.2 研究意义汽车副车架是汽车重要的结构组件之一,承担着支撑车身和保护乘客的重要任务。
副车架的强度和稳定性直接影响着汽车的行驶安全和乘坐舒适性。
对汽车副车架的强度模态分析及结构优化具有重要的研究意义。
通过对副车架的结构分析,可以深入了解副车架的构造特点和受力情况,为进一步的强度模态分析和结构优化提供基础。
强度模态分析可以帮助工程师评估副车架在不同工况下的受力情况,确定其承载能力和安全性,为汽车设计提供科学依据。
探讨汽车副车架强度模态分析及结构优化

探讨汽车副车架强度模态分析及结构优化
汽车副车架是承载引擎和变速器等动力传动装置,连接前后悬架系统以及车身其他结构的重要组成部分。
强度模态分析是对副车架进行力学计算和模拟,预测其在各种工况下的受力情况,以及发现和解决可能存在的结构强度问题。
结构优化则是对副车架进行设计和改进,以提高其强度和刚度。
在进行汽车副车架强度模态分析时,首先需要对其进行建模。
一般可以采用有限元方法进行建模和分析。
建模时需考虑副车架的几何形状、材料属性以及连接点等因素。
建模完成后,可以进行强度分析,包括静态强度分析和模态分析。
静态强度分析是对副车架在静载荷作用下的受力情况进行分析。
可以通过施加引擎质量和悬挂装置载荷等,预测副车架在行驶和停车过程中受到的应力和变形情况。
通过分析得到的应力分布和变形情况,可以评估副车架的强度和刚度是否满足设计要求,并在需要时进行结构优化。
模态分析是对副车架在动态工况下的振动特性进行分析。
可以对副车架在行驶过程中的共振频率、振动模态和振动形态等进行预测和分析。
通过模态分析,可以了解副车架的固有频率分布情况,从而避免悬挂系统与副车架的共振,提高行驶平稳性和乘坐舒适性。
针对强度模态分析中可能发现的结构强度问题,可以采取结构优化的方法进行解决。
结构优化可以通过改变副车架的几何形状、增加材料的强度和刚度,或者改变连接方式等来提高其强度和刚度。
结构优化还需要考虑副车架的重量、成本和制造工艺等因素,以实现最佳的设计方案。
- 1、下载文档前请自行甄别文档内容的完整性,平台不提供额外的编辑、内容补充、找答案等附加服务。
- 2、"仅部分预览"的文档,不可在线预览部分如存在完整性等问题,可反馈申请退款(可完整预览的文档不适用该条件!)。
- 3、如文档侵犯您的权益,请联系客服反馈,我们会尽快为您处理(人工客服工作时间:9:00-18:30)。
精选文档
Q/JLY J711 -2009
乘用车副车架静刚度CAE分析规范
编制:
校对:
审核:
审定:
标准化:
批准:
浙江吉利汽车研究院有限公司
二〇〇九年三月
精选文档
前言
为了给新车型开发提供设计依据,指导新车设计,评估新车结构性能,结合本企业实际情况,制定本规范。
本规范是对Q/JLY J711160-2008《乘用车副车架刚度CAE分析规范》的修订。
与Q/JLY J711160-2008相比,主要差异如下:
——对原有章节进行重新编排;
——对分析模型的处理进行重新定义;
——对数据处理进行详细表述;
——对评价标准进行补充;
——对分析报告内容进行修改。
本规范由浙江吉利汽车研究院有限公司提出。
本规范由浙江吉利汽车研究院有限公司工程分析部负责起草。
本规范主要起草人:李慧梅。
本规范于2009年4月15日发布并实施。
标准号为Q/JLY J711160-2008的规范于2008年7月28日第一次发布,本次修订为第一次。
1 范围
本规范规定了乘用车副车架静刚度CAE分析的软硬件设施、输入条件、输出物、分析方法、分析数据处理及分析报告。
本标准适用于乘用车副车架静刚度CAE分析。
2 软硬件设施
a)软件设施:主要用于求解的软件,采用MSC/NASTRAN;
b)硬件设施:高性能计算机。
3 输入条件
乘用车副车架静刚度分析的输入条件主要指副车架有限元模型,一个完整的副车架有限元模型含内容如下:
a)副车架各个零件的网格数据;
b)副车架焊点数据;
c)各个零件的材料数据;
d)各个零件的厚度数据。
4 输出物
乘用车副车架静刚度分析的输出物为PDF文档格式的分析报告,针对不同的车型统一命名为《车型副车架静刚度分析报告》(“车型”代表车型代号,如:车型为GC-1,则分析报告命名为《GC-1副车架静刚度分析报告》)。
5 分析方法
5.1 分析模型
分析模型包括副车架的有限元模型,钣金件均采用壳单元模拟,点焊采用CWELD模拟,线焊采用RBE2或壳单元模拟。
5.2 分析模型的建立
建立有限元模型,应符合下列要求:
a)副车架各个零件的网格质量应符合求解器的要求;
b)副车架各个零件的材料,须与明细表规定的材料相对应;
c)副车架各个零件的厚度,须与明细表规定的厚度相对应;
d)焊点几何坐标须与3D焊点坐标一致,焊点连接的层数须明确,点焊采用CWELD模拟,线焊采用
RBE2或壳单元模拟;
e)副车架有限元模型的质量应该与实车相等。
5.3 刚度分析
a)定义分析类型为静态线性分析;
b)定义输出结果类型包括位移和应力;
c)定义刚度分析求解工况。
5.4 分析工况
5.4.1 约束条件
约束副车架与车身连接处的所有自由度,如图1所示。
5.4.2 载荷条件
在每个关键点X、Y、Z三个方向分别施加1000N的载荷,如图1所示。
图1 乘用车副车架静刚度分析约束及载荷条件
6 分析数据处理
6.1 数据处理
乘用车副车架静刚度分析的数据处理主要是获取各关键点在力的作用方向上的位移(单位为mm),并计算相应的刚度值。
其刚度值计算公式如下:
式中:——刚度值,单位牛顿/毫米(N/mm);
——施加载荷大小,单位牛顿(N);
——载荷方向上的位移,单位毫米(mm)。
6.2 结果输出
乘用车副车架静刚度分析输出结果示例见表1。
表1 乘用车副车架静刚度分析结果(CE-1车型(配置3G10发动机))
7 评价标准
乘用车副车架静刚度CAE分析的评价标准:
a)设计部门提供目标值;
b)参考同类车型目标值;
c)与试验结果进行对比。
8 分析报告
乘用车副车架静刚度CAE分析的分析报告统一为PDF格式的文档,其报告内容如下:
a) 分析结论;
b) 分析概述;
c) 模型概述;
d) 分析工况;
e) 分析结果;
f) 分析文件归档清单。
__________________________。