铁矿选矿工艺
铁矿选矿厂工艺流程
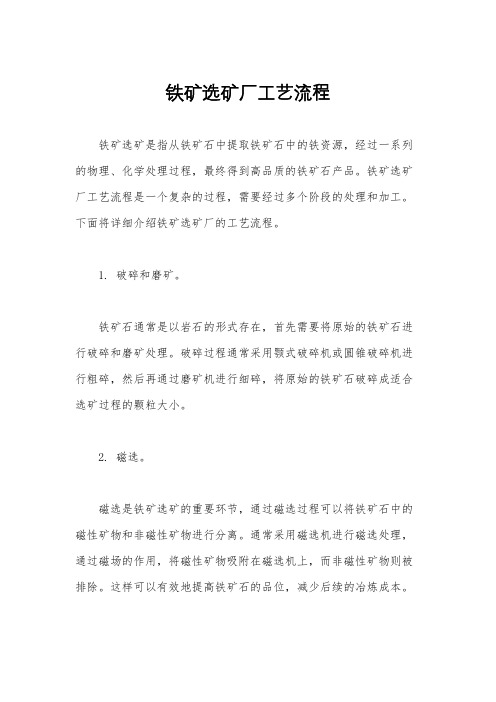
铁矿选矿厂工艺流程铁矿选矿是指从铁矿石中提取铁矿石中的铁资源,经过一系列的物理、化学处理过程,最终得到高品质的铁矿石产品。
铁矿选矿厂工艺流程是一个复杂的过程,需要经过多个阶段的处理和加工。
下面将详细介绍铁矿选矿厂的工艺流程。
1. 破碎和磨矿。
铁矿石通常是以岩石的形式存在,首先需要将原始的铁矿石进行破碎和磨矿处理。
破碎过程通常采用颚式破碎机或圆锥破碎机进行粗碎,然后再通过磨矿机进行细碎,将原始的铁矿石破碎成适合选矿过程的颗粒大小。
2. 磁选。
磁选是铁矿选矿的重要环节,通过磁选过程可以将铁矿石中的磁性矿物和非磁性矿物进行分离。
通常采用磁选机进行磁选处理,通过磁场的作用,将磁性矿物吸附在磁选机上,而非磁性矿物则被排除。
这样可以有效地提高铁矿石的品位,减少后续的冶炼成本。
3. 浮选。
在磁选之后,还需要进行浮选处理,将铁矿石中的硫化物进行分离。
通常采用浮选机进行浮选处理,通过向矿浆中加入药剂,使硫化物和其他矿物发生吸附作用,然后通过气泡的作用将其分离。
这样可以有效地提高铁矿石的品位,减少后续的冶炼成本。
4. 脱水。
经过磁选和浮选处理后,得到的铁矿石浆需要进行脱水处理,将其中的水分进行脱除。
通常采用压滤机或离心机进行脱水处理,将铁矿石浆中的水分进行脱除,得到干燥的铁矿石精矿。
5. 精矿处理。
经过脱水处理后,得到的铁矿石精矿还需要进行进一步的处理,通常包括磨矿、磁选和浮选等环节,以进一步提高铁矿石的品位和品质。
6. 成品铁矿石。
经过以上的一系列处理过程,最终可以得到高品质的成品铁矿石,可以直接用于冶炼生产高品质的铁制品。
以上就是铁矿选矿厂的工艺流程,通过破碎和磨矿、磁选、浮选、脱水和精矿处理等环节,可以将原始的铁矿石进行高效、高品质的提取和加工,为后续的冶炼生产提供优质的原料。
铁矿的选矿工艺(一)

铁矿的选矿工艺(一)铁矿的选矿工艺什么是铁矿选矿工艺?•铁矿选矿工艺是指通过一系列物理和化学方法,将原始铁矿石中的有用矿物与无用矿物分离出来,以提高铁矿石中铁资源的利用率。
铁矿选矿的重要性•铁矿选矿工艺是冶金工业中的关键环节,直接关系到铁矿石的加工质量和资源利用率,对于保障钢铁工业的健康发展具有重要意义。
铁矿选矿方法的分类1.物理选矿•磁选法:利用铁矿石的磁性差异,通过磁力将磁性矿物与非磁性矿物分离。
•重选法:利用铁矿石中矿物的比重差异,通过以水为媒介的重力分选将矿石分离。
•浮选法:利用矿物与水之间的浸润性差异,通过气泡将矿物与尾矿分离。
2.化学选矿•磷酸盐浸提法:利用磷酸盐与矿物的特殊反应性,在适当条件下将磷酸盐矿物与铁矿石分离。
•氰化法:利用氰化物与矿物的特殊反应性,在适当条件下将含金矿石与铁矿石分离。
铁矿选矿工艺的发展趋势1.高效节能•采用先进的设备和工艺,提高选矿效率,减少能耗。
2.环保可持续•选矿过程中减少对环境的污染,提高资源的可持续利用率。
3.自动化与智能化•引入自动化设备和智能控制系统,提高生产效率和质量,降低人工操作对工艺的影响。
结论•铁矿选矿工艺在钢铁工业中具有重要地位和作用,随着科技的进步和工艺的不断发展,铁矿选矿工艺将变得更加高效、环保和智能化,为钢铁工业的可持续发展做出更大的贡献。
铁矿的选矿工艺什么是铁矿选矿工艺?•铁矿选矿工艺是指通过一系列物理和化学方法,将原始铁矿石中的有用矿物与无用矿物分离出来,以提高铁矿石中铁资源的利用率。
铁矿选矿的重要性•铁矿选矿工艺是冶金工业中的关键环节,直接关系到铁矿石的加工质量和资源利用率,对于保障钢铁工业的健康发展具有重要意义。
铁矿选矿方法的分类1.物理选矿–磁选法•利用铁矿石的磁性差异,通过磁力将磁性矿物与非磁性矿物分离。
–重选法•利用铁矿石中矿物的比重差异,通过以水为媒介的重力分选将矿石分离。
–浮选法•利用矿物与水之间的浸润性差异,通过气泡将矿物与尾矿分离。
铁矿工艺流程

铁矿工艺流程铁矿是一种重要的矿石资源,经过一系列的工艺流程可以得到铁制品。
铁矿工艺流程是一个复杂的过程,涉及到矿石的选矿、炼铁、冶炼等环节。
下面将详细介绍铁矿的工艺流程。
1. 铁矿的选矿。
铁矿的选矿是铁矿工艺流程的第一步,其目的是从原矿中提取出含铁的矿石。
常见的铁矿石有赤铁矿、磁铁矿、褐铁矿等。
选矿的方法主要有物理选矿和化学选矿两种。
物理选矿是利用矿石的物理性质进行分选,如密度、磁性等;化学选矿则是利用矿石的化学性质进行分选,如浮选、重选等。
通过选矿,可以得到含铁量较高的矿石,为后续的炼铁过程提供原料。
2. 炼铁。
炼铁是将含铁的矿石还原成金属铁的过程。
炼铁的主要方法有高炉法和直接还原法两种。
高炉法是将矿石、焦炭和石灰石等原料放入高炉中,经过高温煅烧,使铁矿石中的氧化铁还原成金属铁;直接还原法则是利用天然气或其他还原剂直接将铁矿石还原成金属铁。
在炼铁过程中,还会产生大量的炉渣,需要通过冶炼等方法进行处理。
3. 冶炼。
冶炼是将金属铁进行精炼和合金化的过程。
在冶炼过程中,金属铁会经过熔炼、精炼、合金化等环节,得到符合要求的铁制品。
熔炼是将金属铁加热至熔点,使其变成液态;精炼则是通过加入一定的合金元素,调整金属铁的成分和性能;合金化则是将金属铁与其他金属进行合金化,得到具有特定性能的合金铁。
4. 成品加工。
经过上述的工艺流程,铁矿最终可以得到成品铁制品。
这些铁制品还需要进行加工,如锻造、铸造、热处理等,得到最终的产品。
锻造是将金属铁加热至一定温度,通过锻打等方式进行成型;铸造则是将液态金属铁倒入模具中进行成型;热处理则是通过加热和冷却等方式改善铁制品的组织和性能。
总结。
铁矿工艺流程是一个复杂的过程,涉及到选矿、炼铁、冶炼和成品加工等多个环节。
通过这些工艺流程,铁矿最终可以得到各种铁制品,如铁块、铁棒、铁板等,为工业生产和人们的生活提供了重要的材料基础。
同时,铁矿工艺流程也需要注意环保和资源节约,采用清洁生产技术,减少环境污染,实现可持续发展。
铁矿选矿厂工艺流程

铁矿选矿厂工艺流程
铁矿是一种重要的矿石资源,铁矿选矿厂主要通过工艺流程将铁矿石分离出铁和杂质,以得到高纯度的铁矿产品。
下面将介绍一种常见的铁矿选矿厂工艺流程。
首先,铁矿石进入选矿厂后,经过初级破碎和细碎工序。
初级破碎设备将铁矿石压碎成较小的颗粒,然后细碎设备将颗粒更加细化,以便后续的分选工序。
接下来,经过物理分选工序对破碎后的铁矿石进行分选。
物理分选工序主要包括重介质选矿、磁选和重力选矿。
在重介质选矿中,通过将破碎后的铁矿石和重介质悬浮液混合,根据密度的差异使铁矿与杂质分离。
磁选则是利用铁矿石具有一定的磁性,通过磁性分离器将含铁矿物和非磁性杂质分离。
重力选矿是利用铁矿石和杂质的密度差异,通过重力分离设备将铁矿石和杂质分离。
在物理分选之后,还需进行化学分选以进一步提高铁矿的纯度。
化学分选主要是通过浸泡和浸泡浮选过程。
在浸泡过程中,将铁矿浸泡在一种化学药剂中,使得铁矿与某些杂质发生化学反应以分离开来。
而在浮选过程中,铁矿石与液体起泡剂反应,使得铁矿浮到液面上,然后被收集起来。
最后,对铁矿进行干燥和烧结处理。
干燥工序是将湿状的铁矿经过热处理,使其成为干燥的颗粒。
而烧结工序则是通过高温加热使铁矿颗粒间产生结合,形成固体块状。
这样的处理方式不仅可以提高铁矿的密度和强度,还方便后续的运输和储存。
总结起来,铁矿选矿厂的工艺流程包括初级破碎、物理分选、化学分选、干燥和烧结等几个主要工序。
通过这些工艺的组合,可以将铁矿石中的铁和杂质分离出来,得到高纯度的铁矿产品,为后续的钢铁生产提供了重要的原材料。
铁矿石选矿工艺流程
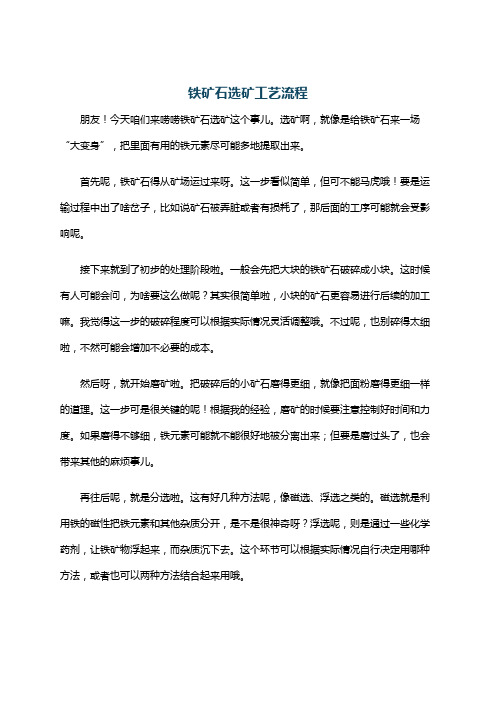
铁矿石选矿工艺流程
朋友!今天咱们来唠唠铁矿石选矿这个事儿。
选矿啊,就像是给铁矿石来一场“大变身”,把里面有用的铁元素尽可能多地提取出来。
首先呢,铁矿石得从矿场运过来呀。
这一步看似简单,但可不能马虎哦!要是运输过程中出了啥岔子,比如说矿石被弄脏或者有损耗了,那后面的工序可能就会受影响呢。
接下来就到了初步的处理阶段啦。
一般会先把大块的铁矿石破碎成小块。
这时候有人可能会问,为啥要这么做呢?其实很简单啦,小块的矿石更容易进行后续的加工嘛。
我觉得这一步的破碎程度可以根据实际情况灵活调整哦。
不过呢,也别碎得太细啦,不然可能会增加不必要的成本。
然后呀,就开始磨矿啦。
把破碎后的小矿石磨得更细,就像把面粉磨得更细一样的道理。
这一步可是很关键的呢!根据我的经验,磨矿的时候要注意控制好时间和力度。
如果磨得不够细,铁元素可能就不能很好地被分离出来;但要是磨过头了,也会带来其他的麻烦事儿。
再往后呢,就是分选啦。
这有好几种方法呢,像磁选、浮选之类的。
磁选就是利用铁的磁性把铁元素和其他杂质分开,是不是很神奇呀?浮选呢,则是通过一些化学药剂,让铁矿物浮起来,而杂质沉下去。
这个环节可以根据实际情况自行决定用哪种方法,或者也可以两种方法结合起来用哦。
小提示:别忘了最后一步哦!经过前面的步骤,得到的铁精矿还得进行脱水处理呢。
这一步要是没做好,铁精矿的含水量过高的话,会影响它的质量和后续的使用哦。
刚开始可能会觉得这个选矿流程有点复杂,但习惯了就好了呀!。
铁矿选矿工艺流程

铁矿选矿工艺流程铁矿选矿工艺流程是指通过一系列的物理和化学方法将铁矿从矿石中分离出来的过程。
下面是一个简化的铁矿选矿工艺流程的描述。
首先,原料的准备。
铁矿选矿的原料主要是含有铁矿石的岩石,其中主要的铁矿石有赤铁矿、磁铁矿和褐铁矿。
岩石通常需要经过破碎和磨矿的处理,将其粉碎为合适的粒度。
其次,矿石的重力分离。
矿石中的铁矿石通常比其它岩石更重,因此可以利用重力分离的原理将铁矿石从矿石中分离出来。
常用的重力分离设备有浮选机和螺旋选矿机等。
这些设备通过调整浮选药剂的配比和旋转速度来实现矿石的分离。
接着,矿石的磁性分离。
对于含有磁性铁矿石的矿石,可以利用磁性分离的原理将铁矿石从矿石中分离出来。
常用的磁性分离设备有湿式磁选机和干式磁选机等。
这些设备通过调整磁场强度和分离速度来实现矿石的分离。
然后,矿石的浮选分离。
铁矿石通常含有硅酸盐和硅酸钙等杂质,通过浮选可以减少这些杂质对铁矿石的影响。
浮选是利用物理和化学性质的差异将矿石中的有用矿物与杂质分离开来。
常用的浮选设备有浮选机和浮选槽等。
浮选药剂的选择和配比对浮选效果有重要影响。
最后,矿石的干燥和精选。
将分离出来的铁矿石进行干燥,除去其表面的水分。
然后对铁矿石进行精选,选取出粒度适中、质量合格的铁矿石。
常用的精选设备有振动筛和鳞状挡板等。
整个铁矿选矿工艺流程需要精细控制各个环节的参数,以达到最佳的分离效果。
此外,还需要进行废水处理和废弃物处理,以保护环境。
铁矿选矿工艺的优化可提高矿石的回收率和品位,降低生产成本,提高生产效益。
总结起来,铁矿选矿工艺流程是一个复杂的过程,需要通过一系列的物理和化学方法将铁矿石从矿石中分离出来。
每个环节都需要合理设计和精细控制,以达到最佳的分离效果。
这是一个既重要又具有挑战性的工艺过程,对于铁矿石行业的发展具有重要意义。
大冶铁矿选矿工艺流程

大冶铁矿选矿工艺流程大冶铁矿是中国重要的铁矿石资源之一,其选矿工艺流程对于提高矿石的品位和回收率至关重要。
本文将介绍大冶铁矿的选矿工艺流程,包括矿石的破碎、磨矿、磁选和浮选等环节。
一、矿石的破碎和磨矿大冶铁矿的矿石首先经过破碎环节,将其破碎成适当的粒度。
破碎后的矿石经过进一步的磨矿处理,以提高磨矿细度,为后续的磁选和浮选过程做好准备。
二、磁选磁选是大冶铁矿选矿的关键环节之一。
磁选主要通过磁性物质对矿石中的铁矿石进行分离,常用的磁选设备有湿式磁选机和干式磁选机。
矿石经过磁选后,磁性较强的铁矿石会被磁选机吸附,而非磁性的杂质则会被排除。
三、浮选浮选是将矿石中的有用矿物通过气泡的作用使其浮起,从而实现矿石的分离。
在大冶铁矿选矿中,浮选主要用于分离矿石中的硅酸盐矿物,如石英等。
浮选过程中,矿石首先经过粗浮选,将较粗的矿物浮起,然后通过细浮选进一步分离细粒度的矿物。
四、脱硫大冶铁矿中的矿石中常含有一定量的硫化物矿物,如黄铁矿等。
脱除硫化物矿物的目的是减少矿石中的硫含量,提高矿石的品位。
常用的脱硫方法有浮选法、氧化法和焙烧法等。
五、脱磷大冶铁矿中的矿石中也常含有一定量的磷酸盐矿物,如磷灰石等。
脱除磷酸盐矿物的目的是降低矿石中的磷含量,以满足冶炼的要求。
常用的脱磷方法有磷酸浸出法、化学浸出法和浮选法等。
六、尾矿处理选矿过程中产生的尾矿需要进行处理。
尾矿中常含有一定量的有价值的矿物,如铁矿石和硅酸盐矿物等。
通过合适的方法对尾矿进行处理,可以实现对有价值矿物的回收,提高资源利用率。
大冶铁矿的选矿工艺流程包括矿石的破碎、磨矿、磁选、浮选、脱硫、脱磷和尾矿处理等环节。
通过这些工艺,可以实现对矿石中的有用矿物的有效分离和回收,提高矿石的品位和回收率,最终为冶炼和利用提供高品质的铁矿石原料。
大冶铁矿选矿工艺的不断改进和优化,将进一步提高选矿效果,推动矿石资源的可持续利用。
铁矿选矿工艺流程

铁矿选矿工艺流程
铁矿选矿工艺流程是指对铁矿石进行选矿处理,从中提取出铁
矿石中的有用矿物,达到冶炼铁的目的。
铁矿选矿工艺流程主要包
括破碎、磨矿、磨选、磁选、重选等环节。
下面将详细介绍铁矿选
矿工艺流程的各个环节及其作用。
首先是破碎环节,破碎是将原始的铁矿石经过机械设备进行破碎,使其达到一定的颗粒度,方便后续的处理。
破碎的目的是将原
始的大块矿石破碎成较小的颗粒,以便后续的磨矿操作。
接下来是磨矿环节,磨矿是指将破碎后的铁矿石进行进一步的
细化处理,通过磨矿设备将其磨成更细的颗粒。
磨矿的目的是增加
矿石的表面积,提高矿石的暴露度,为后续的磨选操作提供条件。
然后是磨选环节,磨选是指利用磨矿后的铁矿石进行选矿处理,通过物理方法将矿石中的有用矿物和非有用矿物进行分离。
磨选的
主要作用是提高矿石的品位,减少有用矿石的损失。
接着是磁选环节,磁选是指利用磁性矿石和非磁性矿石在磁场
中的不同反应,通过磁选设备将磁性矿石和非磁性矿石进行分离。
磁选的作用是提高矿石的品位,减少对环境的污染。
最后是重选环节,重选是指利用矿石在流体中的不同沉降速度,通过重选设备将矿石中的有用矿物和非有用矿物进行分离。
重选的
作用是进一步提高矿石的品位,减少对环境的影响。
总的来说,铁矿选矿工艺流程是一个复杂的过程,需要经过多
个环节的处理,才能最终得到高品位的铁矿石。
各个环节之间相互
配合,共同完成对铁矿石的加工处理,确保最终产品的质量。
希望
本文介绍的铁矿选矿工艺流程能够对相关领域的工作者有所帮助,
谢谢阅读!。
- 1、下载文档前请自行甄别文档内容的完整性,平台不提供额外的编辑、内容补充、找答案等附加服务。
- 2、"仅部分预览"的文档,不可在线预览部分如存在完整性等问题,可反馈申请退款(可完整预览的文档不适用该条件!)。
- 3、如文档侵犯您的权益,请联系客服反馈,我们会尽快为您处理(人工客服工作时间:9:00-18:30)。
我国铁矿石资源供给形势随着我国经济持续高速的发展,钢铁工业迅速发展。
国内各钢铁企业对矿石的需求量增长迅猛,国内的矿山生产已远远满足不了需求,不得不依靠国外的优质铁矿石资源。
据统计,1985年我国进口铁矿石突破1000万t,2002年突破1亿t,2004年突破2亿t,2005年1~7月份累计进口铁矿石已达2亿t。
国内的铁矿石资源中易选的磁铁矿资源日益减少,充分利用国内的资源,提高钢铁企业矿石的自给率,缓解进口铁矿石的压力,维持优质的铁矿原料供给,必须以科技的进步来推动贫铁矿资源的高效开发与利用。
我国铁矿矿床类型多,贮存条件复杂,矿石类型多,硫、磷、二氧化硅等有害组分含量高,多组分共生铁矿石占了很大比重,而且有用组分嵌布粒度细,因此采选难度大、效率低、产品质量差。
几十年来,广大选矿工作者针对我国铁矿资源“贫、细、杂”的特点开展了大量的研究工作,解决了诸多技术难题,使我国铁矿选矿技术得到长足进步和发展,总体水平有很大提高。
尤其是近年来,研制并成功应用了新的高效分选设备、新的高效浮选药剂以及新的分选工艺。
从而使选矿工艺指标取得了突破性进展。
铁矿选矿技术及选矿设备简介(一)矿石破碎我国选矿厂一般采用粗破、中破和细破三段破碎流程破碎铁矿石。
粗破多用1.2m或1.5m旋回式破碎机,中破使用2.1m或2.2m标准型圆锥式破碎机,细破采用2.1m或2.2m 短头型圆锥式破碎机。
通过粗破的矿石,其块度不大于1m,然后经过中、细破碎,筛分成矿石粒度小于12mm的最终产品送磨矿槽。
(二)磨矿工艺我国铁矿磨矿工艺,大多数采用两段磨矿流程,中小型选矿厂多采用一段磨矿流程。
由于采用细筛再磨新工艺,近年来一些选矿厂已由两段磨矿改为三段磨矿。
采用的磨矿设备一般比较小,最大球磨机3.6m×6m,最大棒磨机3.2m×4.5m,最大自磨机5.5m×1.8m,砾磨机2.7m×3.6m。
磨矿后的分级基本上使用的是螺旋分级机。
为了提高效率,部分选矿厂用水力旋流器取代二次螺旋分级机。
(三)选别技术1.磁铁矿选矿主要用来选别低品位的“鞍山式”磁铁矿。
由于矿石磁性强、好磨好选,国内磁选厂均采用阶段磨矿和多阶段磨矿流程,对于粗粒嵌布的磁铁矿采用前者(一段磨矿),细粒、微细粒嵌布的磁铁矿采用后者(二段或三段磨矿)(图3.2.23)。
我国自己研制的系列化的永磁化,使磁选机实现了永磁化。
70年代以后,由于在全国磁铁矿选矿厂推广了细筛再磨新技术,使精矿品位由62%提高到了66%左右,实现了冶金工业部提出精矿品位达到65%的要求。
2.弱磁性铁矿选矿主要用来选别赤铁矿、褐铁矿、镜铁矿、菱铁矿、假象赤铁矿或混合矿,也就是所谓的“红矿”。
这类矿石品位低、嵌布粒度细、矿物组成复杂,选别困难。
80年代后,选矿技术方面对焙烧磁选、湿式强磁选、弱磁性浮选和重选等工艺流程、装备和新品种药剂的研究不断改进,使精矿品位、金属回收率不断提高。
如鞍钢齐大山选矿厂采用弱磁—强磁—浮选的新工艺流程,获得令人鼓舞的成就。
3.多金属共(伴)生矿选矿这类矿石成分复杂、类型多样,因此采用的方法、设备和流程也各不相同,如白云鄂博铁矿采用反浮选—多梯度磁选、絮凝浮选、弱磁-反浮选-强磁选、弱磁-正浮选、焙烧磁选等不同的工艺流程,以提高铁的回收率,并综合回收稀土氧化物。
攀枝花铁矿通过磁选获得TFe53%左右的钒铁精矿,磁选后的尾矿通过弱磁扫选-强磁选-重选-浮选-干燥电选,获得钛精矿和硫钴精矿,回收钛和钴。
大冶铁矿采用弱磁-强磁和浮选,综合回收铁、铜和钴、硫等元素。
(四)烧结球团技术烧结技术是我国人造富矿的主要手段。
1996年共生产人造富矿16095.6万t,其中重点企业9485.9万t,占58.9%,地方国营企业6133.7万t,占38.1%。
我国在细精矿烧结的技术上已达到相当水平。
鞍钢早在50年代初就在烧结机上成功地把酸性烧结矿制作方法改为碱性烧结矿制作方法,在世界上第一个用消石灰或生石灰作熔剂解决了细精矿烧结问题。
烧结球团的装备水平也有所提高,全国共有烧结机419台,总面积15522m2,其中:1 30m2级以上的烧结机有22台,合计面积4107m2;24~129m2的烧结机197台,合计面积9 387m2;小于24m2的烧结机200台,合计面积2028m2。
1994年2月24日在马鞍山钢铁厂投产的300m2烧结机,是我国除宝钢外自行设计、制造和建设的规模最大的现代化烧结机。
磁选矿技术进展磁铁矿选矿是铁矿石选矿的主体,在国内铁精矿产量中,磁铁矿精矿约占3/4。
多年来磁铁矿选矿技术不断发展和进步,磁铁矿选矿厂生产指标有了较大的改善,精矿品位从60%左右提高到65%~67%。
目前钢铁工业对原料的要求越来越高,围绕“提铁降硅”国内做了大量的研发工作,磁铁矿精矿品位由65%提高到68.5%,Si02由8%~9%降至4%。
新型磁选设备的应用和反浮选工艺的推广是“提铁降硅”的主要方向。
(一)磁选矿石1、单一磁铁矿石,主要是沉积变质型磁铁矿石。
矿石中铁矿物绝大部分是磁铁矿,以细粒嵌布为主;脉石矿物主要是石英或角闪石等硅酸盐矿物。
有的含硅酸铁较多,此类矿石选矿生产历史最长,由于矿石组成简单,常采用弱磁选方法。
对于大中型磁选厂,当磨矿粒度大于0.2毫米时,常采用一段磨矿磁先;小于0.2毫米时,则采用两段磨矿磁选。
若在粗磨能分出合格尾矿时,则采用阶段磨矿磁选。
缺水地区,则采用干式磨矿干式磁选,被贫化了富磁铁矿石或贫磁铁矿石,一般用干式磁选剔除脉石,前者得到块状富矿石;后都经磨矿磁选获得精矿。
为了获得高品位精矿,可将磁铁矿精矿用反浮选或击震细筛等方法处理。
为了提高回收率,可考虑尾矿再选等工艺进一步回收。
目前对硅酸铁尚无合理的利用途径,因此,矿石中的硅酸铁在选矿中不强调回收。
用选矿方法虽可回收硅酸铁,但由于含铁硅酸盐矿物中的铁品位低,将会较大幅度地降低总精矿品位,在经济上就显得不合理。
一般说来炉料中含有一定量硅酸铁时,并不影响大中型高炉况顺行,并且硅酸铁中的铁也不会从炉渣中流失;但在小高炉中,由于硅酸铁在冶炼过程中是吸热反应,且融点低。
因之炉料中若含有一定量的硅酸铁时,则会降低炉温使炉况不顺行,并且跑渣。
2、含多金属磁铁矿石,主要是矽卡岩型含硫化物磁铁矿石和少数岩浆型含磷灰石磁铁矿石,矿石中磁铁呈中粒(2~0.2毫米)到细粒嵌布,脉石有硅酸盐或碳酸盐矿物,常伴生蓼铁曆、钴黄铁矿或黄铜矿以及磷灰石等。
此类矿石也有较多的选矿生产实践,一般采用弱磁选与浮选联合流程,即用弱磁选回收铁,浮选回收硫化物或磷灰石等。
原则流程分为弱磁选-浮选和浮选-弱磁选两种,这两种流程的磁铁矿与硫化物的连生体去向不同,前一流程,连生体主要进入铁精矿中;后一流程,主要进入硫化物精矿中,所以,在同样磨矿粒度下,选浮后磁流程可以得到含硫化物较低的铁精矿和回收率较高的硫化物精矿。
贫化矿石也可先用干式磁选剔除脉石,再细筛选别。
此类矿石常有自熔性的,应该注意保持精矿的自熔性。
还有的含镁较高,镁有的呈类质同像赋存于磁铁矿中,难以用机械选矿方法与铁分离。
(二)弱磁性铁矿石1、单一弱磁性铁矿石,包括沉积变质型、沉积型、热液型和风化型矿床的赤铁矿石、菱铁矿石、褐铁矿石和赤铁(镜铁)-菱铁矿石等。
此类矿石选矿生产实践较少,由于矿物种类多,嵌布粒度范围广,所用的选矿方法也比较多,常用的方法可分两种;(1)磁化焙烧磁选或与重选、浮选、强磁选的并联流程。
焙烧磁选是选别细粒到微粒(<0.02毫米)弱磁性铁矿石的有效方法之一。
当矿石中矿物复杂,用其他方法难以得到良好指标时,应该用磁化焙烧磁选法。
75~20毫米的块矿用竖炉还原焙烧已有长期生产经验;20毫米以下的粉矿的磁化焙烧炉生产实践较少。
目前,粉矿常用强磁选、重选、浮选行方法或联合流程进行选别。
(2)重选、浮选、强磁选或其联合流程。
浮选也是选别细粒到微粒弱磁性铁矿石的常用方法之一。
有正浮选和反浮选两种原则流程。
前者适用于不含易浮脉石的石英质赤铁矿石,后者适用于脉石易浮的矿石,均有生产实践。
重选和强磁选主要用于选别粗粒(20~2毫米)和中粒弱磁性铁矿石,由于这两种方法,近年来在技术上有较大的进展,目前我国已开始用于选别细粒弱磁性铁矿石。
粗粒和极粗粒(>20毫米)矿石的重选常用重介质或跳汰选矿;中到细粒矿石则用螺旋选矿机、摇床、扇形溜槽和离心选矿机等流膜重选方法,粗、中粒矿石的强磁选常用干式感应辊式强磁选机;细粒矿石常用温式感应介质强磁选机。
目前,由于细粒矿石的强磁选精矿品位不高,而重选单位处理能力较低,所以常组成强磁-重选联合流程,用强磁选丢弃大量合格尾矿,然后重选进一步处理强磁精矿,以提高品位。
以上各种方法的应用随矿石种类而不同。
沉积变质型赤铁矿石,铁矿物主要是赤铁矿,脉石主要是石英;镜铁-菱铁矿石,铁矿物主要是镜铁矿的菱铁矿,脉石有石英、碧玉、重晶石和铁白云石等。
这些矿石都是细粒嵌布的,工业上采用磁化焙烧磁选或浮选方法,并正在研究强磁选和重选等方法。
沉积型鲕状赤铁矿石和赤铁-菱铁矿石,铁矿物主要是赤铁矿和菱铁矿,脉石有鲕绿泥石、石英,有的还有方解石等。
铁矿物常为微粒嵌布,与脉石紧密共生呈鲕状结构,不易单体解离。
一般都是地下开采,常被围岩贫化。
这种矿石比较难选,如果是富矿石或自熔性矿石,用重介质、跳汰或干式强磁选等方法剔除脉石,得到块状成品矿石,如果是较富的鲕粒矿石,常用焙烧磁选方法,有时在焙烧磁选前预先除去块状脉石,至于较贫的鲕粒矿石,即使采用焙烧磁选,精矿品位也难达到50%以上,可以考虑剔除围岩后与其他高品位精矿配矿使用或研究直接还原等选冶联合方法。
这种矿石往往含铝较高,应该注意铁精矿的硅铝比;对自熔性或碱性矿石应该注意保持精矿的自熔性。
热液型石英质赤铁矿石和赤铁矿-褐铁矿石,常为不均匀嵌布,多采用重选、强磁选,浮选等方法的联流程。
风化矿床的堆积和坡积褐铁矿石,含泥较多,一般采用重选方法,即洗矿后用跳汰和离心选矿机等选别,也可以采用重选-强磁选流程。
2、含多金属弱磁性铁矿石,主要是热液型和沉积型含磷或硫化硪的赤铁矿石或菱铁矿石。
此类矿石一般用重选、浮选、强磁选或其联合流程回收铁矿物,用浮选回收磷或硫化物。
热液型含磷灰石赤铁矿石和含铜硫菱铁矿石可以用浮选方法。
沉积型含磷鲕状赤铁矿石,磷呈胶磷状态,虽然可以用浮选法与铁分离,但往往难于富集成磷精矿,并且铁回收率降低甚多。
可以考虑剔除大粒度脉石后,冶炼高磷生铁,再回收钢渣磷肥。
风化矿床的铁帽含有有色金属的褐铁矿石,常伴有铜、砷、锡等伴生成分无单独矿物,难以用选矿方法与铁分离,正在研究氯化焙烧等方法处理。
红土型含镍铬钴褐铁矿中石,伴生成分也没有单独矿物,焙烧氨浸和离析磁选等方法正在研究中。