莱钢活炉底复吹转炉炉型控制工艺实践
转炉工艺流程

转炉工艺流程转炉工艺流程是一种重要的冶炼方法,主要用于炼钢过程中。
它可以通过高温和氧化剂将生铁中的杂质去除,得到高纯度的钢材。
下面将介绍转炉工艺流程的主要步骤和流程。
首先,将生铁和废钢等原料加入转炉中。
生铁是从高炉中得到的,含有较多的杂质。
废钢则是来自于废弃的钢铁制品,通过再生利用可以减少资源浪费。
接下来,将炉膛中的空气预热并压缩成雾状,形成高压氧枪。
高压氧枪将高速喷射的氧气和炉膛中的原料充分混合,并在高温下进行氧化反应。
这个步骤被称为“吹炼”,它的作用是将生铁中的杂质氧化并去除。
在吹炼过程中,氧化反应会产生大量的热量,使炉温急剧上升。
为了控制温度,需要加入适量的废钢和石灰石等冷却剂。
这些冷却剂可以吸收部分热量,同时还可以用于与杂质反应生成渣。
当炉温升至一定程度后,会进行凿渣操作。
凿渣是将转炉中的渣从炉膛底部排出的过程。
渣中含有大量的杂质,需要及时清理,以保证后续冶炼的顺利进行。
在凿渣之后,转炉中的钢水与冷却剂继续进行反应。
这时的炉温已经下降,反应速率较慢。
冷却剂会吸热,将剩余的热量带走。
同时,继续吹入氧气,使冷却剂氧化并与杂质很好地结合,形成不溶于钢水的浮渣。
这个过程被称为“吹碱”,它能进一步净化钢水,并使其达到所需的成分要求。
最后,将净化后的钢水倾注出炉。
倾钢是将钢水从转炉中倾出的过程。
为了保证钢水的流动性,可以在转炉背部设置倾钢孔,通过倾钢孔将钢水导入倾钢罐中。
倾钢过程需要控制倾出速度和流量,以保证钢水的质量和稳定性。
总结起来,转炉工艺流程包括原料加入、吹炼、凿渣、吹碱和倾钢等主要步骤。
通过这些步骤,可以将生铁中的杂质氧化并去除,从而得到高纯度的钢材。
转炉工艺流程在炼钢过程中起到了重要的作用,提高了钢材的质量和效率。
复吹转炉控制碳氧积的技术实践

銎
流动 , 冲刷供 气 元 件 周 围耐 材 的现 象 。气 流 量越 大, 水锤 现象 引起 的钢 水 冲刷 侵蚀 越严 重 。 凹坑 熔 蚀 : 由于气 体 与钢 水 的冲刷 , 在供 气 元 件周 围形 成 凹坑 。 凹坑越 深 , 流 传热越 差 , 对 加剧
浓度 的增 加 下 降而 上升 , 在 [ = .2 但 C] 0 0 %
~
2 0 % 时 c和. 的积 变化 不大 , .0 厂 接近 于 1 。因
02 % , 于 中磷铁 水 , 了降低转 炉终 点钢 水 的 .1 属 为
而在 实 际生产 中 厂 x o=1 cf 。则式 ( ) 为 : 1变
磷含量 , 必须充分发挥转炉底吹系统的作用 , 而转
炉 底 吹效果 的好 坏是 转炉碳 氧积 的直 接反 映 。过 去梅 钢转炉 的碳 氧积 控制 波动较 大 , 0020~ 在 .0 0040 影 响转 炉 的冶炼 效果 。转 炉 碳 氧积 过 低 .0 , 影 响转炉 炉底 的安 全 和 转 炉 炉况 的稳 定 性 , 底 炉 偏 移 程度 大 ; 氧积 过高底 吹效 果不好 , 水氧 含 碳 钢 量 高 , 金 收 得率 低 , 铁 料 消耗 高 , 炼效 果 下 合 钢 冶 降, 操作 困难 , 同时影 响钢水质 量 。通过 对历史 数 据 的分析 , 为把转 炉终点 碳 氧积控 制在 0 024 认 .0
m p 为 钢 水 的 密 度 , c p m;金 m ;清为 炉 渣 的密 度 , g c 为金属 液表面张力 ,/ r 为气泡半 径 , /m ; N m; c o
0030时 , 方 面都可 以达 到一个 比较 理想 的 .0 各
转炉工艺操作规程
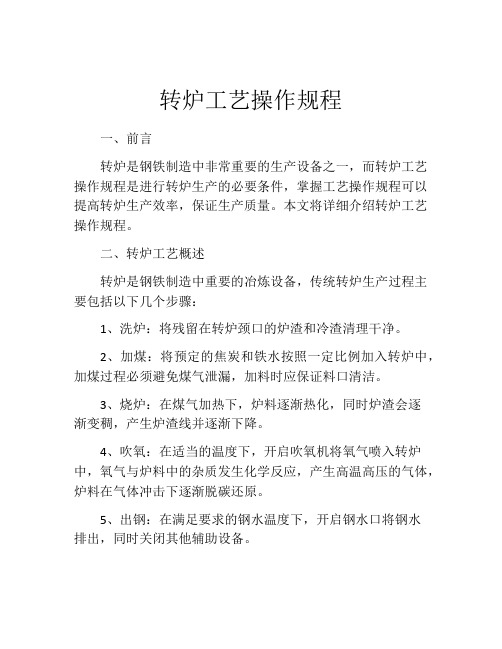
转炉工艺操作规程一、前言转炉是钢铁制造中非常重要的生产设备之一,而转炉工艺操作规程是进行转炉生产的必要条件,掌握工艺操作规程可以提高转炉生产效率,保证生产质量。
本文将详细介绍转炉工艺操作规程。
二、转炉工艺概述转炉是钢铁制造中重要的冶炼设备,传统转炉生产过程主要包括以下几个步骤:1、洗炉:将残留在转炉颈口的炉渣和冷渣清理干净。
2、加煤:将预定的焦炭和铁水按照一定比例加入转炉中,加煤过程必须避免煤气泄漏,加料时应保证料口清洁。
3、烧炉:在煤气加热下,炉料逐渐热化,同时炉渣会逐渐变稠,产生炉渣线并逐渐下降。
4、吹氧:在适当的温度下,开启吹氧机将氧气喷入转炉中,氧气与炉料中的杂质发生化学反应,产生高温高压的气体,炉料在气体冲击下逐渐脱碳还原。
5、出钢:在满足要求的钢水温度下,开启钢水口将钢水排出,同时关闭其他辅助设备。
6、停炉:在出钢完成后,将转炉进行清理,消除隐患,准备下一次生产。
三、转炉工艺操作规程1、洗炉操作人员进入转炉周围进行检查,确认转炉颈口、台阶等部位无异物。
在高温状态下,使用聚乙烯皮扫、黑铁皮扫等清洁品,进行全面的清洗。
清洗完毕后反复检查,确保转炉内外部干净无异物。
2、加煤在加煤过程中,操作人员需要在上料前先确认料口无异物,且料口周围没有明火等安全隐患。
根据生产计划,按照一定的比例开足橱门,平均分配炉料。
在加料过程中,需要注意煤气泄漏,并及时清理料口,保证料口干净,加料完毕后及时关闭料门,防止煤气泄漏。
3、烧炉加煤后,操作人员需要监控转炉内部温度,确认炉体温度达到烧炉条件,才能进行下一步操作,同时应注意炉内温度和氧气流量的平衡,保证热量分布均匀。
在炉渣变稠时,要注意炉门、倾炉口等设备的密封,防止炉渣外溢。
4、吹氧吹氧是冶炼中重要的步骤,操作人员要掌握合理的吹氧时间和氧气流量,以保证化学反应的完全性和热量的平衡性。
在吹氧后,需要确认炉料的C、Si等指标已经达到要求,同时也需要注意控制炉内的压力和氧气流量。
莱钢120t复吹转炉终点脱磷平衡研究
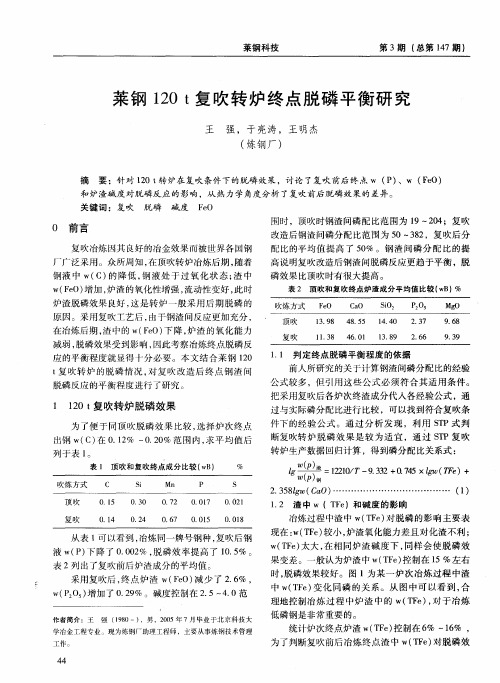
中 w( F ) 化 同磷 的关 系。从 图 中可 以看 到 , Te 变 合 理地控 制冶 炼 过 程 中炉 渣 中 的 W( F ) 对 于冶 炼 Te ,
低 磷钢是 非常 重要 的。 统计 炉次 终点 炉渣 W( F ) 制在 6 ~1 % , Te控 % 6
学 冶金工程专业。现 为炼钢厂助理工程师 ,主要从事炼钢技术管理
…
l — ) ̄ g wk P
一
/一、
【 钢 p)
_
=
120 T一 .3 Q75× 21/ 932+ 4
( F )+ Te
2 3 8 w( a …… ……… …… ……… ……… ( ) . 5 1 C O) g 1 12 渣 中 W (T e . F )和碱 度的影 响
时, 脱磷 效果较 好 。 图 1为某 一 炉 次 冶炼 过程 中渣
采用 复 吹后 , 点炉 渣 w( e 减 少 了 26 , 终 F O) .%
w( 。 增 加了 0 2 % 。碱度 控制在 2 5- . PO ) .9 . 4 0范
作者 简 介 :王 强 (9 0一) 18 ,男 ,2 0 0 5年 7月 毕业 于北 京科 技 大
脱磷 碱度 FO e
和 炉渣碱度 对脱磷 反应 的影 响 ,从 热力 学角度 分析 了复吹前后 脱磷 效果 的差异 。
关键 词 :复吹
0 前 言
复吹冶炼 因其 良好 的冶金效 果而 被世界 各 国钢 厂广 泛采用 。众所 周知 , 在顶 吹转炉 冶炼后期 , 随着 钢液 中 W( 的降 低 , 液处 于 过 氧化 状 态 ; 中 C) 钢 渣 w( e ) 加 , FO 增 炉渣 的氧化性 增强 , 流动性 变好 , 时 此 炉渣脱 磷效果 良好 , 这是 转 炉一 般 采 用后 期 脱 磷 的 原 因。采用 复吹工 艺后 , 由于钢 渣间反 应更加 充分 ,
转炉工艺流程
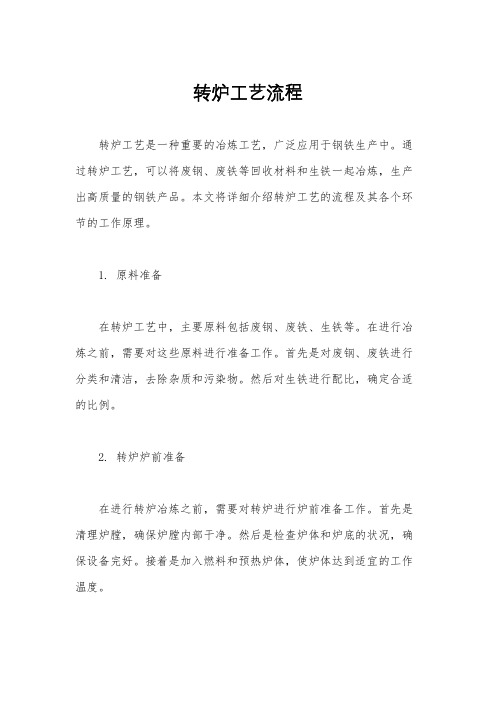
转炉工艺流程转炉工艺是一种重要的冶炼工艺,广泛应用于钢铁生产中。
通过转炉工艺,可以将废钢、废铁等回收材料和生铁一起冶炼,生产出高质量的钢铁产品。
本文将详细介绍转炉工艺的流程及其各个环节的工作原理。
1. 原料准备在转炉工艺中,主要原料包括废钢、废铁、生铁等。
在进行冶炼之前,需要对这些原料进行准备工作。
首先是对废钢、废铁进行分类和清洁,去除杂质和污染物。
然后对生铁进行配比,确定合适的比例。
2. 转炉炉前准备在进行转炉冶炼之前,需要对转炉进行炉前准备工作。
首先是清理炉膛,确保炉膛内部干净。
然后是检查炉体和炉底的状况,确保设备完好。
接着是加入燃料和预热炉体,使炉体达到适宜的工作温度。
3. 转炉冶炼转炉冶炼是整个工艺的核心环节。
在冶炼过程中,首先将原料加入转炉中,然后通过吹氧工艺进行氧化还原反应,使原料中的杂质和有害元素得以去除,同时控制合金元素的含量。
在冶炼过程中,需要控制冶炼温度、氧气流量等参数,确保冶炼过程的稳定性和高效性。
4. 炉渣处理在转炉冶炼过程中,会产生大量炉渣。
炉渣中含有大量的有价金属和合金元素,需要进行有效的处理和回收。
通常采用炉渣精炼工艺,通过冷却、浇铸和破碎等步骤,将炉渣中的有价金属和合金元素分离出来,实现资源的综合利用。
5. 钢水处理在转炉冶炼过程中,产生的钢水需要进行进一步的处理。
主要包括脱氧、脱硫、合金调整等工艺。
通过加入适量的脱氧剂和脱硫剂,可以有效地降低钢水中的氧含量和硫含量,提高钢水的质量。
同时,根据产品要求,可以加入适量的合金元素,调整钢水的成分和性能。
6. 连铸经过上述工艺处理后的钢水,可以进行连铸工艺,将其铸造成板坯、方坯、圆坯等不同形状的铸坯。
连铸工艺是钢铁生产中的关键环节,直接影响产品的成形质量和生产效率。
7. 精炼对连铸坯进行精炼处理,通过真空处理、气体吹扫等工艺,进一步提高钢水的纯净度和均匀度,确保最终产品的质量。
8. 成品质检最后,对精炼后的钢材进行成品质检,包括化学成分分析、力学性能测试、表面质量检测等。
莱钢高铁水比转炉冶炼工艺实践

摘
要: 莱钢在转炉工序采用高铁水 比装入制度 , 由于造渣制度及枪位控制不合理、 炉型控制不 当及铁水流冲击 , 导致喷溅
加剧 , 兑铁 位侵 蚀 。通过优 化造 渣工 艺 、 位控 制及溅 渣护 炉工 艺 , 枪 喷溅渣 量 由 2 . k/降 至 1. k/, 铁料 消耗 由 55 g t 75 g 钢 t 10 9 gt 6 .k / 5 降至 1040k/, 6 . gt耐材消耗由04 g 降至O2 gt氧枪寿命由 20炉提高至 3 5 . k/ 2 t . k/ 0 , 1 2 炉。 关键词 : 转炉 ; 高铁水 比; 喷溅; 枪位
发炉 渣 “ 干 ” 且 持续 时 间较 长 , 返 , 后期 调 整 “ 返干 ”
过度 , 造成金属 喷溅 。 22 枪位控 制不 合理 . 采用恒压 变枪位操作 , 氧压 08MP 。前期枪 位 . a 过 高 ( 0 13 0mm) 渣 中 T e 量 高 (0 , 渣 量 , F含 3 %) 溢 大 , 渣时 间长 达 3m n 溢 i。碳 氧 反应 开始 时 间后 延 , 后 期 枪位 控 制过 低 ( 5 0mT , 剧 “ 干 ” 度 。 1 0 l) 加 1 返 程 整 个 过程 熔池 温 度上 升不 均 衡 , 脱碳 反 应 不均 衡 ,
相应延后 , 等熔池温 度上升 , 头批渣料充分化透后 n, 在开吹 4 . mi加入 二批 渣料 。二 批渣料 的加入 ~45 n
原则 : 勤加 、 少加 。但 石灰要 在 吹炼 9 n 前全 部加 mi
完 ,0 n 1 后仅 留少 量冷却剂调整 渣子用 。 mi
32 优化枪位控 制 , 321 建立枪位控 制标 准化模 式 . .
转炉吹氧自动控制在转炉炼钢中的研究和应用
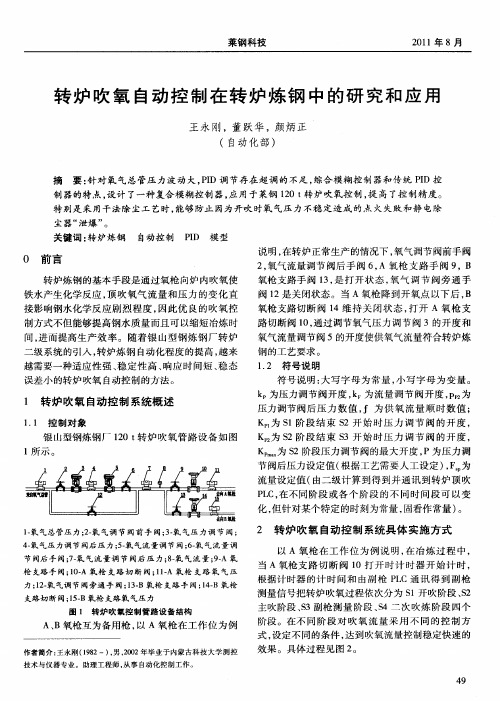
4氧 气 压 力 调 节 阀后 压 力 ;一 气 流 量 调 节 阀 ;一 气 流 量 调 一 5氧 6氧
2 转 炉 吹 氧 自动 控 制 系统 具 体 实 施 方 式
以 A氧 枪 在 工 作 位 为 例 说 明 , 冶 炼 过 程 中 , 在 当 A氧枪支 路 切 断 阀 l 开 时 计 时 器 开 始 计 时 , 0打
2 氧气 流量 调节 阀后 手 阀 6 A氧 枪 支路 手 阀 9, , , B 氧 枪支 路手 阀 1 , 打 开状 态 , 3是 氧气 调 节 阀旁 通 手
阀1 2是关 闭 状态 。 当 A氧枪 降 到开 氧点 以下后 , B
Байду номын сангаас
氧 枪支 路切 断 阀 l 持 关 闭状 态 , 4维 打开 A 氧枪 支 路 切断 阀 1 , 过调节 氧气 压 力 调节 阀 3的开 度 和 0通 氧 气流量 调节 阀 5的开 度使供 氧气 流量 符合转 炉炼
钢 的工 艺要求 。
1 2 符 号说 明 .
制方 式不但 能 够提 高钢水 质量 而且 可 以缩短 冶炼 时 间 , 而提 高生 产 效 率 。 随着 银 山 型钢 炼 钢 厂 转 炉 进
二级 系统 的引 入 , 炉炼 钢 自动化 程度 的提 高 , 来 转 越 越需 要一种 适应 性 强 、 定 性 高 、 应 时 间 短 、 态 稳 响 稳
制 器的特 点 , 计 了一种 复合模 糊控 制 器 , 用 于 莱钢 10 t 炉吹 氧控 制 , 高 了控 制 精度 。 设 应 2 转 提
特 别是 采 用干 法除 尘工 艺时 , 能够 防止 因为 开吹 时氧 气 压 力不 稳 定造 成 的 点 火失 败 和静 电除
炼钢工艺控制点

炼钢主要工艺控制点一、转炉炉后工艺控制点1、脱氧合金化要求:(1)合金加入顺序必须遵循先弱后强的原则。
即硅锰——硅铁——脱氧剂;为了保证合金的有效收得率,在过氧化钢水的处理上可以先加部分硅铁或脱氧剂进行预脱氧,但为了避免钢水翻包,预脱氧剂不能加到包底。
(2)合金加入时间必须遵循在出钢到四分之一开始加入,在钢水出到四分之三时必须加完。
出钢时间必须大于三分钟。
(3)为避免钢水成分不均匀,严禁在出完钢后补加合金。
(4)有条件的钢车可以在加入合金后来回晃动,增加合金的融化速度和均匀性。
(5)合金加入点必须对准钢流加入。
2、出钢挡渣要求:(1)任何钢种必须进行双挡渣操作。
即出钢之前必须检查挡渣塞是否堵好。
(2)出钢到五分之四时必须加入挡渣锥或挡渣球。
(3)出完钢后检查出钢口情况,必须把残渣或堵塞物清理干净,然后堵上挡渣塞。
3、精炼要求:(1)出完钢后必须进行吹氩气(或氮气)操作,有条件的必须在出钢过程中进行。
(2)吹气时间必须大于五分钟,吹气效果以钢水表面微翻波动为准则,为避免钢水二次氧化不允许钢水大翻。
吹气压力0.4-.0.6Mp.(3)吹气前和吹完气后必须进行钢水测温,其温度制度根据不同的钢种和上连铸包次要求执行工艺制度。
(4)同时在吹完气后必须进行取样观察和检验,如果钢水成分和含氧量不合乎要求,必须经行喂丝操作,具体数量根据成分和含氧量而定。
(5)完毕后必须加入钢包覆盖剂,具体数量已覆盖钢包表面为原则。
二、钢包工艺控制点1、必须热包出钢,钢包烘烤温度大于800℃要求。
2、钢包出钢前必须清理干净,不允许有残渣或残钢,特别是水口和透气砖部分。
3、出钢前必须对底吹透气砖进行确认检查是否透气。
4、出钢前必须对引流砂确认检查,要求覆盖碗口且成堆积状。
三、连铸浇注平台工艺控制点1、中间包浇注前工艺检查要求(1)中间包浇注前必须烘烤,烘烤温度必须大于800℃。
(2)中间包浇注前必须检查是否清理干净,特别是水口部位。
50t复吹转炉高炉龄状态下炉型控制
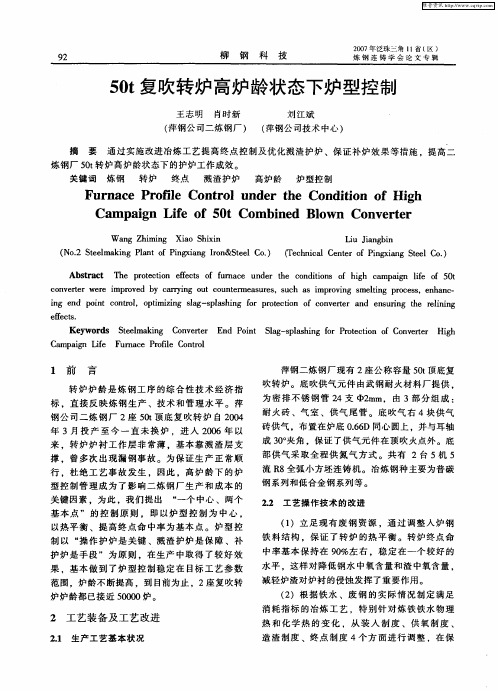
流R 8全 弧小方 坯连 铸机 。冶炼 钢 种主要 为普 碳
钢 系列和低 合金 钢系列 等 。
2 . 工 艺 操 作 技 术 的 改 进 2
关键 因 素 。为此 ,我们 提 出
“ 个 中心 、两 个 一
基 本 点 ” 的 控 制 原 则 ,即 以 炉 型 控 制 为 中 心 ,
以热平 衡 、提 高 终 点 命 中率 为 基 本 点 。 炉 型 控
撑 。曾 多次 出现 漏 钢 事 故 。为 保 证 生 产 正 常 顺 行 。杜绝 工 艺 事 故 发 生 ,因此 ,高 炉 龄 下 的 炉 型 控 制管 理 成 为 了影 响 二炼 钢 厂 生 产 和 成本 的
成 3。 0 夹角 ,保 证 了供气 元 件在 顶 吹火 点外 。底
部 供 气 采取 全 程 供 氮 气 方 式 。 共有 2台 5机 5
维普资讯
9 2
柳
钢
科
技
20 年泛珠三角I省( 07 1 区)
炼 钢 连 铸 学 会 论 文 专 辑
5t 0 复吹转炉 高炉龄状态下炉型控制
王 志 明 肖时新
刘江斌
( 萍钢公 司二炼 钢 厂 ) ( 萍钢 公 司技 术 中心 )
摘 要 通 过实 施改 进冶 炼工 艺 提高 终点 控 制 及优 化溅 渣护 炉 、保 证补 炉效 果 等措 施 ,提高 二
Ca p i n Lie o 0 mb n d Bl wn Co v r e m a g f f 5 t Co ie o n etr
W a g Z i n Xio S ii n hmig a hxn Lu J n bn i i g i a
( o2 Se l a ig Pato igin rn te C . N . t m kn l fPn xa g I &Sel o) e n o
炼钢转炉工艺流程

炼钢转炉工艺流程
《炼钢转炉工艺流程》
炼钢转炉是一种常见的钢铁冶炼设备,采用氧气作为原料,通过不断升温、熔化、脱碳和合金化,将生铁或废钢冶炼成高品质的钢材。
其工艺流程主要包括加料、通氧、出渣、出钢四个主要过程。
首先是加料过程,将生铁、废钢、合金等原料按照一定的配比投入转炉中,并在炉内预热至适宜的温度。
加料过程中需要保证稳定的投料速度和均匀的加热,以确保后续工艺的顺利进行。
接着是通氧过程,氧气通过一定的喷嘴直接通入炉内,与炉料进行充分的混合和燃烧,产生高温的炉内环境。
在此过程中需要控制氧气的进气量和温度,使炉内气氛能够达到最佳的燃烧条件,促进炉料的融化和氧化还原反应的进行。
随后是出渣过程,炉脚下部设置有出渣孔,脱碳反应产生的气体和氧化物等杂质会通过这一孔口不断排出。
出渣的效率和质量直接关系到后续的钢液质量和工艺稳定性。
出渣过程需要通过适当的控制和处理,使得炉内的杂质尽可能排出并避免对钢液产生影响。
最后是出钢过程,当炉内的炉料达到设计要求后,将铁水通过转炉底部的出钢孔排出,经过连铸机进行浇铸成型。
出钢过程需要严格控制排钢速度和温度,以确保钢液的质量和成型的规格。
总的来说,炼钢转炉工艺流程需要进行一系列严格的操作和控制,确保原料得到充分融化和反应,以得到满足生产要求的高品质钢材。
转炉冶炼的工艺流程

转炉冶炼的工艺流程
转炉冶炼的工艺流程如下:
1.准备阶段:主要原料包括铁水、废钢和铁合金。
根据需求,加入不同的造渣材料,如石灰、白云石、铁皮球、矿石和萤石。
2.吹炼阶段:温度逐渐上升,碳含量逐渐下降。
炉口由浓烟滚滚逐渐变得明亮。
在这一阶段,通过控制枪位位置,可以防止喷溅和返干。
3.脱碳阶段:脱碳速度降低,熔池温度上升。
炉口由烟气明亮逐渐变得稀疏透明。
此时,需要确定冶炼终点,即检查碳、硫、磷和温度是否满足要求。
4.出钢阶段:通过经验法,如炉口明亮度、副枪和吹氧累积量来确定何时结束吹氧并提升氧枪。
副枪系统的使用取消了人工取样和测温,这不仅可以节省时间,而且降低了对操作人员的技能要求。
炼钢全流程钢铁料消耗的实践与分析
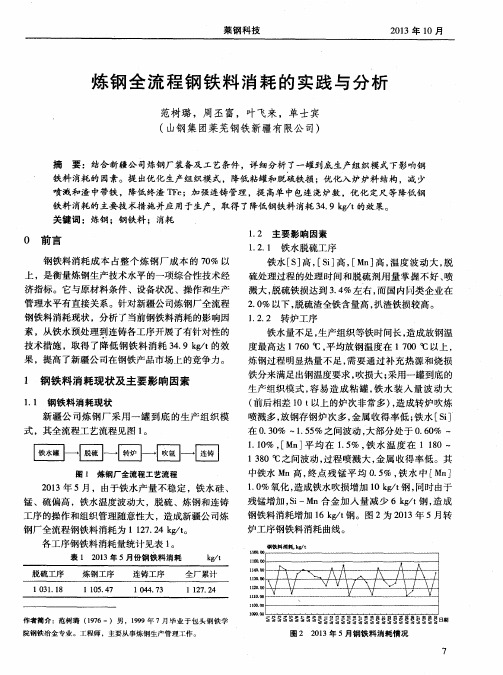
喷溅多 , 放钢存钢炉次多, 金属收得率低 ; 铁水 [ s i ]
在0 . 3 0 % 一1 . 5 5 % 之 间波动 , 大部 分 处 于 0 . 6 0 % ~ 1 . 1 0 %, [ Mn ] 平均 在 1 . 5 %, 铁水 温度 在 1 1 8 0~
1 . 2 . 2 转炉工 序
济指标。它与原材料条件、设备状况 、操作 和生产
管理 水平 有直 接关 系 。针对 新疆 公 司炼钢 厂全 流程
钢铁料消耗现状,分析 了当前钢铁料消耗的影响因 素, 从铁水预处理到连铸各工序开展了有针对性 的 技术措施 ,取得 了降低钢铁料消耗 3 4 . 9 k g / t 的效 果 ,提 高 了新疆 公 司在钢 铁产 品市 场上 的竞 争力 。
钢铁料消耗。 k Wt
i 瑚 . ∞
2 0 1 3年 5月 ,由于铁 水 产 量 不稳 定 ,铁 水 硅 、 锰 、硫偏 高 ,铁水 温度 波 动大 ,脱硫 、炼 钢和 连铸 工序 的操作 和 组织 管理 随意性 大 ,造 成新 疆公 司炼 钢厂 全流 程钢 铁料 消耗 为 1 1 2 7 . 2 4 k g / t 。
1 . 1 钢 铁料 消 耗现状
铁 分来 满足 出钢 温度要 求 , 吹损 大 ; 采 用一 罐到底 的 生 产组 织模 式 , 容易造成粘罐 , 铁 水 装 入 量 波 动 大 ( 前 后相 差 1 0 t 以上 的炉次 非 常 多 ) , 造 成 转 炉 吹炼
新疆公 司炼钢 厂采用一罐到底 的生产组织模
目的。经过对顶底复吹转炉氧枪枪位控制的调查研
究 ,提出 了吹炼过 程 的枪位 控制制 度 ,见 图 4 。
50吨顶底复吹转炉改造及工艺实践
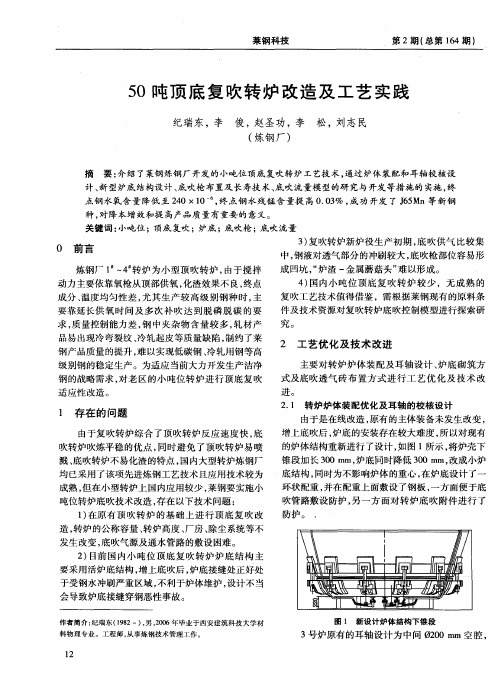
第 2期 ( 总第 1 6 4期 )
5 O吨 顶 底 复 吹 转 炉 改 造 及 工 艺 实 践
纪瑞东 , 李 俊 , 赵 圣功 , 李 松, 刘 志民
( 炼钢厂)
摘
要: 介 绍 了莱钢 炼钢 厂开发 的 小吨位 顶底 复吹转 炉 工艺技 术 , 通 过 炉体装 配和 耳轴校 核设
由于 复 吹转 炉综 合 了顶 吹转 炉 反应 速 度 快 , 底
2 . 1 转 炉炉体 装 配优化及 耳轴 的校 核设 计
由于是在 线改 造 , 原 有 的主体装 备 未发 生改 变 ,
增 上底 吹后 , 炉底 的安装 存在 较大 难度 , 所 以对现 有
吹转炉 吹炼 平稳 的优 点 , 同 时避 免 了顶 吹转 炉 易 喷
计、 新型 炉底 结构设 计 、 底 吹枪 布置及 长寿技 术 、 底吹 流 量模型 的研 究与 开发 等措 施 的 实施 , 终
点钢 水氧 含 量 降低 至 2 4 0×1 0~, 终 点钢 水 残锰 含 量提 高 0 . 0 3 %, 成 功 开发 了 J 6 5 Mn等 新钢 种, 对 降本增 效和提 高产品质 量有 重要 的意 义。
会 导致 炉底 接缝 穿钢 恶性 事故 。
作者简介 : 纪瑞东( 1 9 8 2一) , 男, 2 0 0 6年毕业于西安建筑科技大学材 料物理专业 。工程师 , 从事炼钢技术 管理工作 。
1 2
图1 新 设 计 炉 体 结 构 下 锥 段
3号 炉原有 的耳轴 设 计 为 中 间 0 2 0 0 mm空 腔 ,
3 ) 复 吹转炉新 炉 役 生产 初 期 , 底 吹 供 气 比较 集
中, 钢 液对 透气 部分 的冲刷 较大 , 底 吹枪部 位容 易形 成 凹坑 , “ 炉渣 一金属蘑 菇 头” 难 以形 成 。 4 ) 国 内小 吨 位 顶 底 复 吹转 炉较 少 ,无 成 熟 的 复 吹工艺 技术值 得借 鉴 ,需根 据莱 钢 现有 的原料 条
莱钢120t转炉烟气干法除尘工艺技术

蒸发冷却器还有对烟气进行调节改善的功能, 即在降低气体温度的同时提高其露点, 改变粉尘比 电阻, 有利于在静电除尘器中将粉尘分离出来。除了 废气冷却和调节以外, 占废气中总灰尘含量 40%~ 50%的粗灰也在蒸发冷却器中进行收集。 2.2.2 静电除尘器 静电除尘器放置在炼钢车间的 外部, 其集尘电极通过除尘器的外壳接地, 集尘电极 之间形成通道, 而要净化的炉气流经这些通道。在集 尘电极之间布置高压框架, 框架中装有放电极 ( 阴 极) 并和高压供电系统连接, 由绝缘子支撑。在放电 极的紧邻区域是极高强度的电压, 由于电晕电压排 放的结果, 导致形成带负电荷的气体离子, 在放电电
1200℃进入蒸发冷却 器; 蒸发冷却器内 12 个双介 质 雾 化 冷 却 喷 嘴 , 对 烟 气 进 行 降 温 、调 质 、粗 除 尘 , 烟 气 温 度 降 低 到 150~200℃, 同 时 约 有 40%的 粉 尘在蒸发冷却器的作用下被捕获, 形成的粗颗粒粉 尘通过 链式输送机、双板阀进入 粗灰料 仓 由汽 车 外 运。经冷却、粗除尘和调质后的烟气进入 有 4 个电 场的圆形静电除尘器, 烟气经静电除尘器除尘后含 尘 量 降 至 10mg/m3 以 下 。 静 电 除 尘 器 收 集 的 细 灰 , 经过扇形刮板器、底 部链板输送机和 细灰 输送 装 置 排 到 细 烟 尘 仓 由 汽 车 外 运 至 烧 结 厂 重 复 利 用 。经 过 静电除尘器精除尘的合格烟气经过煤气冷却器降 温 到 70~80℃后 进 入 煤 气 柜 , 不 合 格 烟 气 通 过 火 炬装置放散。整套系统采用自动控制, 与转炉的控 制相联系。
转炉炼钢原理及工艺介绍
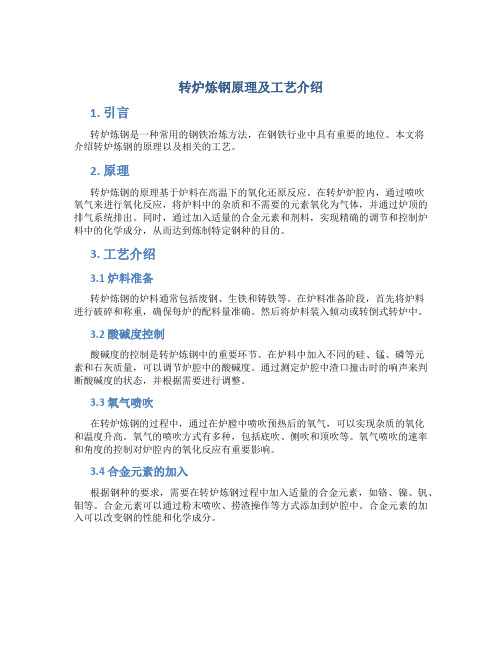
转炉炼钢原理及工艺介绍1. 引言转炉炼钢是一种常用的钢铁冶炼方法,在钢铁行业中具有重要的地位。
本文将介绍转炉炼钢的原理以及相关的工艺。
2. 原理转炉炼钢的原理基于炉料在高温下的氧化还原反应。
在转炉炉腔内,通过喷吹氧气来进行氧化反应,将炉料中的杂质和不需要的元素氧化为气体,并通过炉顶的排气系统排出。
同时,通过加入适量的合金元素和剂料,实现精确的调节和控制炉料中的化学成分,从而达到炼制特定钢种的目的。
3. 工艺介绍3.1 炉料准备转炉炼钢的炉料通常包括废钢、生铁和铸铁等。
在炉料准备阶段,首先将炉料进行破碎和称重,确保每炉的配料量准确。
然后将炉料装入倾动或转倒式转炉中。
3.2 酸碱度控制酸碱度的控制是转炉炼钢中的重要环节。
在炉料中加入不同的硅、锰、磷等元素和石灰质量,可以调节炉腔中的酸碱度。
通过测定炉腔中渣口撞击时的响声来判断酸碱度的状态,并根据需要进行调整。
3.3 氧气喷吹在转炉炼钢的过程中,通过在炉膛中喷吹预热后的氧气,可以实现杂质的氧化和温度升高。
氧气的喷吹方式有多种,包括底吹、侧吹和顶吹等。
氧气喷吹的速率和角度的控制对炉腔内的氧化反应有重要影响。
3.4 合金元素的加入根据钢种的要求,需要在转炉炼钢过程中加入适量的合金元素,如铬、镍、钒、钼等。
合金元素可以通过粉末喷吹、捞渣操作等方式添加到炉腔中。
合金元素的加入可以改变钢的性能和化学成分。
3.5 钢渣处理在转炉炼钢过程中,钢渣是产生的副产物。
钢渣中含有大量的氧化物和杂质,需要进行适当的处理。
一般采用钢渣保温、捞渣、保护渣、中性渣等措施来处理钢渣,以确保钢渣中的氧化元素被充分还原并排出炉外。
3.6 出钢经过一系列的氧化还原反应和调度控制,转炉中的炼钢过程逐渐接近尾声。
当出钢温度达到要求后,打开炉底的出钢口,将液态钢水流入连铸机进行继续加工。
4. 总结转炉炼钢是一种重要的钢铁冶炼方法,其原理是基于氧化和还原反应。
通过适当的酸碱度控制、氧气喷吹和合金元素的加入,可以实现炼制特定钢种的目的。
90吨顶底复吹转炉炉体维护生产实践

【 K e y w o r d s ] B O F f u ma c e ; O p e r a t i o n ; B o t t o m b l o w i n g ; M a i n t e n a n c e
L EB . Th e c o n v e r t e r f u ma c e ma i n t e n a n c e me a s u r e i s e l a b o r a t e d f r o m s me l t i n g o p e r a t i o n s , f e t t l i n g , b o t t o m b l o wi n g e l e me n t s a n d o t h e r a s pe c t s . Th r o u g h
0 前言
复 吹转炉炉体 的维护主要是炉衬和底吹元 件的维 护。 转炉炉龄 的 长 短主要 取决于炉衬寿命和底吹元件 的同步。在转 炉炼 钢生产 中, 提 3 炉体维护措施 高 炉龄对提高生产率 、 提高钢产量 、 提高钢水质量 、 改善转炉炼钢 的品 根据炉衬侵蚀的机理 . 最大限度的降低 或消除危害转炉炉衬的不 种 结构 以及降低 耐火 材料消耗 、增加经 济效益都具有 十分重要的意 利 因素 . 以溅渣护 炉为主要护 炉措施 . 把 握住重点部 位 . 达到均衡 炉 义。 本座 9 O吨复吹转 炉在炉体维护方面总结 出一系列措施 , 取得 良好 衬. 同时合理 的维护底吹元件 效果 。 3 . 1 合理 的溅渣护炉制度 溅渣护炉是炉体维护的最主要和有效的手段 溅渣护炉采用高压 1 影响炉衬 寿命 的因素 氮气 . 将出钢后 留在炉 内的炉渣溅起来 . 涂敷 在炉衬上形成溅渣层 . 对 转 炉在吹炼 过程 中, 炉 内进行着极 其复杂 、 激 烈的物 理化学反应 下一炉形成保 护作用 完成溅渣操作以后倒渣过程中观察到炉膛 内有 和机械运动 , 再加上兑入铁水 、 加入废钢时对炉衬 的冲刷及机械磨损 . 较厚的溅渣层 . 粘稠余 渣能从炉底缓慢 流到炉 口. 有少部 分能倒入渣 转炉炉衬 在使 用中很 容易受到损坏 炉衬 除了正常的冶炼过程中受钢 罐时效果最佳 。 如余渣成块状 。 倒渣 时滚到炉 口 则视为溅渣太干。 如在 水、 炉渣 以及 炉气 的机械 冲刷和化 学侵蚀外 , 影 响其寿命更重要 的环 倒渣过程中能迅速流 到炉 口则视为溅渣太稀 . 以上两种情况都会影响 节在于冶炼操作 和工艺 到溅渣效果 。同时 . 转炉终渣对溅渣 效果也非常重要 . 对于过氧化炉 1 . 1 出钢温度高 次, 在溅渣操作以前 要加入适量 白云石进行调渣 , 从 而保证溅渣效果 。 炉衬在高温热流的作用下 表面会软化熔融 炉衬溅渣层受高温的 3 . 2 合理的冶炼操作 作用更加 明显 .拉碳 温度在 1 6 5 0  ̄ C 以下溅 渣层 保存较好 .完好 率在 1 ) 适量控制炉渣中氧化铁 的含量 炉渣 中氧化铁的含量增加会加 8 0 %左右。如果拉碳温度在 1 6 8 0 %以上溅渣 层大部分被融化掉 。 出钢 速对炉衬 的侵 蚀 在 冶炼操 作中控制合适的氧化铁含量, 能够减少 对 温度 高 的原 因主要有 两方面 : 一是 , 冶炼 过程操作 不 当, 温度控制 过 炉衬 的侵蚀。 高; 二是 , 本座 9 0吨转 炉承担着 冶炼 2 0 C r M n T i H、 G c r 1 5 、 4 2 C r M o A等 2 ) 采 用活性及活性大 的石灰或采 用生 白云 石 、 轻烧 白云石造渣 , 钢种 . 这些钢种对 出钢温度要求高 . 一般控制在 1 6 8 0 %以上 。 可以加速成渣速度, 促进炉前期渣早化, 能够减轻炉渣对炉衬的侵蚀 。 1 - 2 过氧化 3 ) 采用合理枪位控制 . 若前 期枪位低会造成金 属喷溅 为保证快 速 钢水过氧化对炉衬 的侵蚀作用非常大 . 它不仅加剧 了镁碳砖 的脱 成 渣宜采取较高枪位来增加吹炼前期 f F e O ) 含量. 然后根据化 渣情 况 碳速度而且还改变 了炉渣的成分 . 降低 了炉渣的熔点。溅渣层 的熔损 逐 步降低枪位 . 炉渣返干时要适 当提高氧枪枪位提高渣中( F e 0 ) 含量。 率 主要 与溅渣层 中 T F e 有关系 . T F e 越高 . 熔损率就越高。 过 氧化 的炉 吹炼末期 降枪至终点枪位保证压枪 时间 渣 渣中 T F e 含量 高. 大大降低溅渣护炉的效果 4 ) 适 当控制炉渣碱度 转炉的炉渣碱度一般控制在 2 . 8 — 3 . 2 左右, 1 - 3 返 干 使S i 0 2 活度基本稳定. 从 而减少对炉衬 的侵蚀 在 正常冶炼过程 中炉膛 内应充满泡沫炉渣 . 如果炉渣返干炉膛 内 5 ) 在生产 中, 不停 炉的情况下 , 利用测 温枪来测量炉体各 部位表 没有泡沫渣保护 . 则氧气直接传送 到金属不可能完 全被吸收 . 有一部 面的温度情况 . 并做好记 录. 针对温度异常高的部位进行重点观察 , 以 分就会返 回到炉膛 内与炉衬作用 . 侵蚀 炉衬 . 还有一 部分直接传到炉 免出现严重的侵蚀情况 . 如遇到十分严 重的异常的温度升 高 , 应进行 衬使炉衬受到氧气流股 的冲刷 相 应 的 补 炉措 施 1 . 4 重点部位 的侵蚀 3 . 3 底 吹元 件 的维 护 1 ) 炉帽。 炉底上涨会破坏原来 的炉型 . 反应 区上移喷溅率上升、 加 提高底吹供气元件 寿命 ,必须针对底吹供气元件的熔损机理 , 采 剧了对炉帽的侵 蚀 用具体的技术 措施 。通 常所采用的办法如下 : 2 ) 钢面和渣 面。两 个大面 由于其工作性质决定 , 一 直是转 炉的薄 1 ) 生成 “ 蘑 菇头” 保护供气元 件 . 蘑菇 头是 以 M g O为主相 的弥散 弱部位 , 也是转炉重点维 护的部位 。 主要 问题是两大面侵蚀严重 , 存 在 多孔形保护渣层 . 覆 盖在炉底供气砖 的上方 . 能够有效地 防止铁水 、 废 深坑 , 特另 4 是渣面兑铁位 置 , 钢 面出钢 口以下是深坑最严重的地方 。 钢、 炉渣 、 钢水 、 炉气 、 溅渣气体对供气砖的损坏 。蘑菇头形成初期 , 随 3 ) 炉底。炉底高度 主要受 冶炼和溅渣护炉 的影响 , 上涨 和下降过 着底吹气冷却 , 炉 渣迅 速降温 . 黏度 进一步增大 , 上 升气 流贯穿其 中 , 快均对炉体维护产生 不利影 响 慢慢形成弥散多孔的保护层 或蘑菇头 , 可减缓供气砖侵蚀 。蘑 菇头形 成具体方法主要是采 用挂渣 护炉底法 溅渣用终点渣应具有一定粘 度 2 影响底吹元件 寿命 的因素 和碱度 , 保证在 出钢时渣子碱度 2 . 9 ~ 3 . 4 , M g 0含量 9 %~ l 1 %。溅完渣 底吹供气元件的熔 损机理 主要有气泡反击 、 水锤 冲刷 、 凹坑熔蚀 , 后, 将炉子先向后摇动 5 O 。 , 再倒掉炉渣, 使炉渣均匀粘挂在 炉底 上 。 过 此外冶炼过程操作不当仍旧会 缩短 底吹元件
莱钢120t顶底复吹转炉炉体维护技术

谢 建勇等
莱钢 10 顶底复 吹转炉炉体维护技术 2 t
20 年第 6 08 期
( 测零位 除外 ) 。
223 操作护 炉制度 ..
降温 , 黏度进一步增大 , 上升气流贯穿其 中, 慢慢形 成弥散多孔的保护层或蘑菇头, 可减缓供气砖侵蚀。 ④蘑菇头形成后的操作。当蘑菇头形成之后 ,
炉底 同心 圆上均匀 分布 。选用 6 根单 独 的管 路分别 控 制 6 供气 砖 , 能对 每块 砖单 独 调节 又便 于 管 块 既 路、 阀门 的维 护与更 换 , 且 即使其 中的 1 砖 出现 并 块 问题 , 不影 响其他 砖 的供气 效果 。采 用空 气源 的 也 吹堵 空气 系统 , 随 时 向复 吹 系统提供 高压 无油 空 可
重 点 是 防 止炉 底 上涨 造 成 的供 气 砖 堵塞 。溅渣 护
1供 气 钢管 。保 证 每根 钢管 畅通 且不 漏 气 , ) 气 室及 管 路不 漏 气 ; 焊 接 管路 时不 带 人杂 物 , 留 在 并
嘴, 均匀分布 于炉底 同心 圆上 ; 根据 目标碳含量确定合理的供气制度 ; 通过加长透气砖加快 形成金 属蘑菇 头、 针对不 同部位 采 用不 同的底 吹吹堵技 术 以及 复吹转 炉炉体维护 特有 的维护技术要 点 。莱 钢 3 10 t 座 2 顶底 复吹转炉 首个炉役 平均炉 龄 2 0 炉 以上 , 000 最高 2 6 炉 , 6 6 8 且实现 了底吹与炉龄同寿命 。 关键词 : 顶底复吹转炉 ; 维护; 炉体 供气元件 ; 炉龄 中图分类号 :F 2 T 79 文献标识码 : B 文章编号 : 0 — 60 2 0 )6 0 4 — 2 1 4 4 2 (0 8 0 — 0 0 0 0
第3卷 第6 O 期
转炉底吹工艺优化的研究与实践

转炉底吹工艺优化的研究与实践尚 游(山东钢铁股份有限公司莱芜分公司炼钢厂 济南 271104)摘 要:目前,莱钢型钢炼钢厂转炉底吹工艺比较落后,底吹工艺对转炉冶金效果的促进作用不够明显。
为了充分改善底吹工艺、吹炼参数,莱钢型钢炼钢厂根据生产实际情况,调整了底吹枪分布,研究了最佳底吹流量参数,通过稳定炉底,加强对底吹“炉渣-金属蘑菇头”的维护,使转炉碳氧积在炉龄增长的情况下得到良好控制,促进了低成本、高效化冶炼。
关键词:底吹分布;供气强度优化;碳氧积RESEARCH AND PRACTICE ON OPTIMIZATION OF CONVERTER BOTTOM BLOWING PROCESSShang You(The Steelmaking Plant, Laiwu Branch of Shandong Iron and Steel Co., Ltd., Jinan 271104, China)Abstract: At present, the bottom blowing process of the converter in the steel section mill of Lai Steel is relatively backward, and the bottom blowing process has not promoted the metallurgical effect of the converter obviously. In order to fully improve the bottom blowing process and blowing parameters, the section steel mill of Lai Steel adjusted the distribution of bottom blowing gun according to the actual production situation, studied the optimum parameters of the bottom blowing flow, and strengthened the maintenance of the bottom blowing “furnace slag-metal mushroom head” by stabilizing the furnace bottom. The maintenance of the “head” ensures the good control of the carbon and oxygen product of the converter under the condition of growing furnace age, and promotes low-cost and high-efficiency smelting. Key words: bottom blowing distribution; optimization of gas supply intensity; carbon and oxygen product作者:尚游,男,38岁,工程师收稿日期:2020-07-24莱钢银山型钢炼钢厂自2004年7月份开始,逐步投产了4座120 t顶底复吹转炉,通过不断摸索操作工艺,采用更加科学合理的操作技术,复吹技术有了很大的进步,底吹透气砖寿命实现了与转炉炉龄同步,已突破万炉大关。
转炉炼钢工艺简介
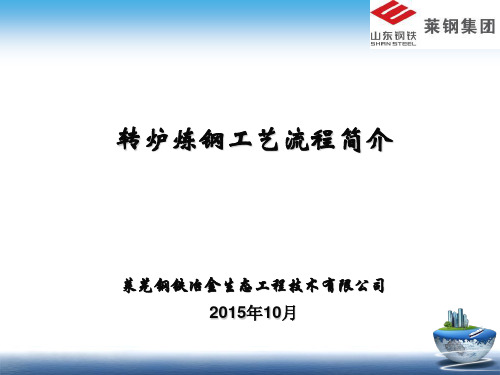
6、连铸
连续铸钢是将高温钢水连 续不断的浇到一个或几个用强 制水冷带有活底的铜模内(结
晶器),钢水在结晶器内凝固
成有一定厚度的坯壳后,连续 不断的从水冷结晶器被拉出,
在二次冷却区继续喷水冷却,
直至完全凝固为止。
2、混铁炉
混铁炉是高炉和转炉之 间的炼钢辅助设备,它主要 用于调节和均衡高炉和转炉 之间铁水供求的设备,保证 不间断地供给转炉需要的铁 水,铁水在混铁炉中储存和 混匀铁水成份及均匀温度, 它对转炉炼钢非常有利。
3、转炉
转炉炼钢是以铁水、 废钢、铁合金为主要原料, 不借助外加能源,靠铁液 本身的物理热和铁液组分 间化学反应产生热量而在 转炉中完成炼钢过程。 氧气顶吹和顶底复吹 转炉由于其生产速度快、 产量大,单炉产量高、成 本低、投资少,为目前使 用最普遍的炼钢设备。
转炉炼钢工艺流程简介
莱芜钢铁冶金生态工程技术有限公司 2015年10月
内容提纲
1 2 3
工艺流程 炼钢厂工艺装备概述 主要装备简介
一、工艺流程
渣 料 铁 合 金 LF 炉
铁 水 包
脱 硫 站
混 铁 炉
铁 水 包
转 炉
钢 包
连 铸
废 钢
吹 氩
二、炼钢厂工艺装备概述
以年产100万吨合格连铸坯炼钢系统为例,主要 产品为螺纹、普碳系列钢种的转炉炼钢厂工艺装备包 括: 由1套双工位的脱硫装置、 1座600吨混铁炉、1
4、钢包吹氩
钢包吹氩搅拌是最基本也是最普通的炉外处理工艺。 钢包吹氩搅拌的作用是: (1)均匀钢水温度。从炼钢炉流到钢包的钢水,在钢包内的温度分布是不均匀 的。钢包吹氩搅拌促使钢包钢水温度均匀,并且能使钢水向包衬的传热进入稳 定态,这样连铸过程钢水温度稳定均匀,有利于提高铸坯内部质量,使结晶器 内坯壳生长均匀,避免开浇水口冻钢断流。 (2)均匀钢水成分。出钢时在钢包内加入大量的铁合金,成分不均匀,吹氩搅 拌可使钢水成分均匀。在吹氩搅拌过程中可根据快速分析提供的钢水成分而进 行成分微调,以使钢的成分控制范围更窄,以确保钢材性能均匀。
转炉炼钢原理及工艺介绍

转炉炼钢原理及工艺介绍引言转炉炼钢是一种常用的钢铁生产工艺,具有高效、灵活、环保等特点。
本文将介绍转炉炼钢的原理及工艺流程。
一、转炉炼钢原理转炉炼钢是通过在高温下将生铁与废钢等原料进行反应,去除杂质,调整合金成分来生产钢铁。
其原理基于以下几个重要的化学反应步骤:1.氧化反应:在高温下,将生铁中的杂质氧化为气体或溶于渣中。
主要的氧化反应有:Fe+C+O2=FeO+CO、Mn+C+O2=MnO+CO等。
2.还原反应:在氧化反应的基础上,通过还原剂(如脱氧剂)来还原产生的氧化物。
主要还原反应有:FeO+CO=Fe+CO2、MnO+CO=Mn+CO2等。
3.合金化反应:在还原反应的基础上,通过加入适量合金元素来调整合金成分。
合金化反应可以通过添加合金块、废钢等方式实现。
通过以上化学反应的组合,转炉炼钢可以控制合金成分、去除杂质、调整温度等,从而得到符合要求的钢铁产品。
二、转炉炼钢工艺介绍转炉炼钢的工艺可以分为以下几个主要步骤:1.预处理:生铁、废钢等原料经过破碎、除尘等处理后,进入转炉炉前料斗。
2.加料:原料从炉前料斗通过螺旋输送机被输送至转炉炉缸中。
3.预热:将炉缸中的原料进行预热,以提高反应效果。
4.吹炼:将炉底引入的高纯氧吹入炉缸中,通过氧化反应和还原反应去除杂质、调整合金成分。
5.加料:在吹炼过程中,适量添加合金块、废钢等调整合金成分。
6.测温:通过测温仪器监测和调节炉内温度。
7.出渣:通过倾炉装置将产生的渣浆从转炉中排出。
8.抽炉:将炉内得到的钢液通过倾炉装置倾出,并进行钢液处理(如脱氧、出气、精炼等)9.浇铸:将经过处理的钢液进行浇铸,得到需要的钢铁产品。
三、转炉炼钢的优势转炉炼钢工艺具有以下几个优势:1.高效:转炉炼钢的操作灵活,能够快速调整合金成分和生产规格,生产效率高。
2.资源利用:转炉炼钢可以利用废钢等再生资源,减少资源浪费。
3.环保:转炉炼钢排放的烟尘、废气等污染物可以通过环保设施进行处理,达到环保要求。
- 1、下载文档前请自行甄别文档内容的完整性,平台不提供额外的编辑、内容补充、找答案等附加服务。
- 2、"仅部分预览"的文档,不可在线预览部分如存在完整性等问题,可反馈申请退款(可完整预览的文档不适用该条件!)。
- 3、如文档侵犯您的权益,请联系客服反馈,我们会尽快为您处理(人工客服工作时间:9:00-18:30)。
PROCESS PRACTICE OF PROFILE CONTROL OF COMBINED BLOWING CONVERTER WITH MOVABLE FURNACE BOTTOM IN LAIWU STEEL
Zheng Jie ( Laiwu Iron and Steel Stock Co. , Ltd) ABSTRACT During the production, the height fluctuations of furnace bottom may arise easily on the combined blowing con-
the depression occurs on both sides of slag in large area, the shape of welding pool turns verter with movable furnace bottom, irregular , the inner diameter with adherent slag of converter mouth gets movable, so Special Steel Works adopts such measures as: dynamic control the height of furnace bottom, proper maintenance of both sides of the slag, quantization control of the inner the height of furnace stays at 6. 60 m ~ 6. 80 m, no pits diameter with adherent slag at converter mouth. In the past two years, are on both sides of slag, no clear grooves on the part of welding pool and slag line, the inner diameter with adherent slag are the converter furnace keeps stable under control,which offers advantages for converter operating. at 1. 90 m ~ 2. 35 m, KEY WORDS converter profile slag splashing basicity
熔池部位的溅渣层会增厚, 炉底会出现上 的钢种, 涨, 反之就会出现炉底下陷的情况。 1. 2 熔池、 渣线部位形状不规则 在炉役生产过程当中, 活炉底复吹转炉由于存
在底吹气易从炉底砌炉砖砖缝中渗出的隐患 , 使炉 壳发红。为了保证炉底的安全, 一般将炉底高度控 制在接缝以上的位置, 这样就造成熔池上移, 熔池上 。 移后恶化了操作条件 吹炼过程中的渣钢界面化学 反应在熔池四周形成一圈凹槽; 在转炉拉碳放钢过 程中受钢水浸泡侵蚀, 熔池钢面和渣面部位易形成 一块大凹坑; 在炉体维护时倒入熔池部位的补炉料 经烧结后, 也会使熔池部位的形状变得不够规则 。 1. 3 炉口粘渣内径偏离正常范围 在一个炉役服役期内, 炉口粘渣内径的波动值
莱钢特钢事业部银山前区 90 t 活炉底复吹转炉 生产钢种较为复杂, 包括轴承、 齿轮、 合结、 螺纹、 普 碳等约四十余个钢种。 每一类钢种对终点渣况, 终 点钢水碳含量﹑出钢温度﹑炉渣氧化性的要求均不 同。如同一座转炉长时间连续生产终点渣较粘, 终 点钢水碳含量较高, 出钢温度较低, 炉渣氧化性较弱
2012 年 第 3 期
河
南
冶
金
· 53·
的连续性。 4. 2 降低了劳动强度 改进前, 频繁进行更换工作泵, 油箱清理、 换油、 补油等工作, 工作量繁重。改进后, 大大缩减了维修 人员的劳动时间和劳动强度。 4. 3 降低了维护成本
油品约消耗 2 桶 / 月, 每年需要更换 换周期为 3 个月, 两次油液并清理油箱。改进后工作泵的更换周期为 2 ~ 3 年, 只要每年更换一次油液并清理油箱即可。 5 参考文献
回摇炉, 在炉衬表面挂上一厚层渣子, 另外在装料之 前将溅渣后的渣子留在炉内, 将炉子摇到合适的角 度停留一段时间, 将粘渣子挂在大面的薄弱位置。 也可采用先加废钢后兑铁水的方式, 避免铁水直接 冲击炉衬。如果有工艺停机、 检修等较长的时间, 可 将补炉料倒在凹陷处, 进行烧结填充。 2. 3 量化掌控炉口粘渣直径 从保证炉口水箱安全、 便于装料和操作的可行
炉渣氧化镁含量 / % 8 ~ 11 溅渣时间 / min 2. 5 ~ 4. 0 溅渣氮气压力 / MPa 0. 95 ~ 1. 05
炉底正常情况下的操作标准
1 ) 动态监测炉底高度。 每个生产班组接班后 采用吹氧管和铝条相结合的方式测量金属液面 , 采 用标尺杆人工测量炉底高度, 及时做好金属液面和 绘制数值走势图。 达到及时准确了 炉底高度记录, 解炉底情况, 并采取相应的控制措施。 2 ) 动态调整炉底高度。在生产过程中, 每班测量 炉底高度和金属液面, 如果该数值低于表 1 的范围,
2012 年 第 3 期
河
南
冶
金
· 29·
加, 最高可达 30 m, 极易造成烟道粘钢渣事故。 在生产过程中出现炉底上涨后, 使得有效容积减 小, 降低了炉容比, 从而增加了转炉发生喷溅的机 [ 2 ] 钢水冲刷炉口内沿粘 率 。喷溅时高温液态炉渣、 使得炉口直径逐步扩大; 反之如果炉底下陷后, 炉 渣, 口直径就会逐步缩小。另外通过生产实践总结发现, 炉帽部位的炉壳钢板外侧如敷设冷却钢管, 通水冷却 , 将会给炉帽提供较好的冷却效果 炉帽有水冷的炉 役, 炉口及炉帽部位极易形成厚粘渣层, 使得炉口直 径缩小, 炉帽部位无水冷的炉役, 炉口直径相对较大。 1. 4 出渣侧和出钢侧大面凹陷 转炉装料过程中的铁水冲刷和重型废钢的冲 击, 使得出渣侧大面受到较大程度的伤害 , 拉碳倒炉 过程高温钢水、 炉渣对出渣侧大面的浸泡和冲刷 , 都 会侵蚀部分渣层; 银山前区转炉生产 50% 的炉次拉 碳时需取块样用光谱仪化验钢水成份, 取样时间的 延长加重了终点钢水和炉渣对出渣侧大面的侵蚀 。
2012 年 6 月 第 20 卷 第 3 期
河 南 冶 金 HENAN METALLURGY
Jun. 2012 Vol. 20 No. 3
莱钢活炉底复吹转炉炉型控制工艺实践
*
郑
杰
( 莱芜钢铁股份有限公司) 摘要 针对活炉底复吹转炉在生产中易出现的炉底高度波动, 钢渣两侧大面凹陷, 熔池部位形状不规则和炉口粘
可达到 ± 400 mm。直径过大时, 炉口水箱得不到渣 子的包裹保护, 在拉碳和放钢倒炉过程中, 容易被钢 水烧漏; 直径过小时, 一方面造成转炉装料困难, 影 响生产节奏, 另一方面当出现喷溅时, 由于炉口缩 小, 从而增加了喷溅渣的压力, 使喷溅渣喷溅高度增
收稿日期: 2012 —2 —3
*
联系人: 郑杰, 工程师,山东. 莱芜( 271105 ) , 莱芜钢铁股份有限公司特钢事业部;
表2
项目 炉底上涨 炉底下陷 炉底高度 范围 / m < 6. 60 > 6. 80 金属液面 范围 / mm < 500 > 800 炉渣 碱度 2. 70 ~ 3. 00 3. 00 ~ 3. 30
“炉底上涨” 可按表 2 当中 的参数来控制, 溅渣过程不 加调渣剂, 溅渣时全程采用低枪位, 溅渣后的残渣状 态以稍稀为准, 残渣直接倒净, 避免挂炉底; 如果数值 “炉底下陷” 可按 的参数来控制, 溅 高于表 1 的范围, 渣时适当加入 50 kg ~ 200 kg 镁块调整炉渣, 溅渣过 “高 - 中 - 高” 程采用 的模式操作枪位高度, 溅渣后的 残渣状态以较干为准, 利用生产间隙残渣挂炉底。
性等方面综合确定炉口粘渣内径范围为 1. 90 m ~ 2. 35 m。制定定期测量炉口内径制度和相应的处理 预案, 使炉口粘渣内径绝大部分时间处于受控范围 内。 “X 架 ” 采用标杆和 等工具每班测量炉口内径, ( 下转第 53 页中) 并填写台账。如检测到炉口
渣面兑铁位无明显凹坑, 渣面和钢面熔池无凹 槽, 与其它部位衔接曲线光滑。 如检查到两侧大面 较深时, 可在适当提高炉渣碱度和氧化镁含量的前 提下, 溅渣完毕在下一炉装料之前钢渣两侧大面来
炉渣氧化镁 含量 / % 6 ~9 9. 5 ~ 13 溅渣时间 / min 2. 0 ~ 3. 5 3. 0 ~ 5. 0 溅渣氮气 压力 / MPa 1. 0 ~ 1. 1 0. 8 ~ 1. 0 溅渣时加料 / kg 不加 50 ~ 200 ( 镁块)
炉底上涨、 下陷情况下的操作标准
2. 2
合理维护两侧大面 建立两侧大面深度定期检查及相应的维护标准,
[ 1] 陈奎生. 液压与气压传动[M] . 武汉: 武汉理工大学出版社, 2001 : 127 - 128. [ 2] 成大先. 机械设计手册[M] . 北京. 化学工业出版社, 2010 : 21 - 671.
除了定期更换过滤器滤芯外, 改进前工作泵的更 ( 上接第 29 页) 内径大于 2. 35 m, 可将炉 通过对影响活炉底复吹转炉炉型控制的因素进 渣碱度、 炉渣氧化镁含量控制在下限, 同时溅渣时将 行系统分析, 对关键指标和数值进行定期监测 , 在实 残渣溅粘, 挂渣时将粘渣挂到炉口或炉帽位置 ; 开通 炉帽冷却水促进炉口、 炉帽部位粘渣。 如检测到炉 口内径小于 1. 90 m, 可将炉渣碱度、 炉渣氧化镁含 , , 量控制在上限 溅渣时将残渣溅干 挂渣时注意避免 将粘渣挂到炉口或炉帽位置; 关闭炉帽冷却水, 减少 炉帽部位粘渣的机率; 另外可采取拉碳提枪时 炉口、 晚关氧 2 s ~ 3 s , 用氧气清理炉口内径粘渣。 3 改进效果
表1
炉底高度范围 / m 6. 60 ~ 6. 80 金属液面范围 / m 500 ~ 800 炉渣碱度 2. 80 ~ 3. 20