数控磨削加工工艺
数控车削加工工艺
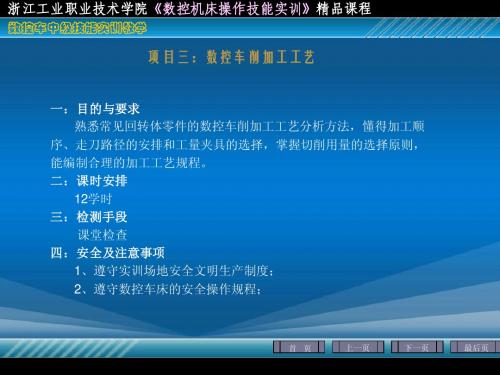
首 页
上一页
下一页
ห้องสมุดไป่ตู้最后页
浙江工业职业技术学院《数控机床操作技能实训》精品课程
数控车中级技能实训教学
一、数控车床加工工艺分析的主要内容 工艺分析是数控车削加工的前期准备工作。工艺制定的合理与否,对程序 编制、加工效率、加工精度等都有重要影响。因此,应遵循一般的工艺原则并 结合数控车床的特点,认真而详细的制定好零件的数控车削加工工艺。 数控车削加工工艺包括以下主要内容: 1、分析被加工零件的工艺性; 2、拟定加工工艺路线,包括划分工序、选择定位基准、安排加工顺序和组 合工序等; 3、设计加工工序,包括选择工装夹具与刀具、确定走刀路径、确定切削用 量等; 4、编制工艺文件。 二、数控车床加工零件的工艺性分析 适合数控车床加工的零件或工序内容选定后,首要工作是分析零件结构工 艺性、轮廓几何要素和技术要求。
首 页
上一页
下一页
最后页
浙江工业职业技术学院《数控机床操作技能实训》精品课程
数控车中级技能实训教学
1、循环切除余量 数控车削加工过程一般要经过循环切除余量、粗加工和精加工三道工序。应根 据毛坯类型和工件形状确定循环切除余量的方式,以达到减少循环走刀次数、 提高加工效率的目的。 (1)轴套类零件 轴套类零件安排走刀路线的原则是轴向走刀、径向进刀,循环切除余量的循环 终点在粗加工起点附近。这样可以减少走刀次数,避免不必要的空走刀,节省 加工时间。 (2)轮盘类零件 轮盘类零件安排走到路线的原则是径向走刀、轴向进刀,循环切除余量的循环 终点在粗加工起点附近。编制轮盘类零件的加工程序时,与轴套类零件相反, 是从大直径端开始顺序向前。 (3)铸锻件 铸锻件毛坯形状与加工后零件形状相似,为加工留有一定的余量。循环去除余 量的方式是刀具轨迹按工件轮廓线运动,逐渐逼近图纸尺寸。 2、确定退刀路线 数控机床加工过程中,为了提高加工效率,刀具从起始点或换刀点运动到接近 工件部位及加工后退回起始点或换刀点是以G00(快速点定位)方式运动的。 考虑退刀路线的原则是:第一、确保安全性,即在退刀过程中不与工件发生碰
磨工培训计划及大纲

磨工培训计划及大纲一、培训目的磨工是机械加工中非常重要的一个环节,他们负责对工件进行精密磨削,提高工件的精度和表面质量。
为了培养高素质的磨工,提高企业的生产效率和产品质量,制定了此培训计划及大纲。
二、培训对象本培训计划及大纲主要面向磨工初级和中级人员。
三、培训内容1.磨削工艺基础知识(1)磨削工艺的基本原理(2)磨削工艺的分类及特点(3)磨削机床的构造与工作原理(4)磨削刀具的选择与使用2.磨削工艺技术(1)外圆磨削技术(2)内圆磨削技术(3)平面磨削技术(4)磨削工艺的质量控制3.磨削加工工艺(1)数控磨削加工工艺(2)普通磨削加工工艺(3)特种磨削加工工艺4.磨削刀具的应用与保养(1)各类磨削刀具的使用方法(2)磨削刀具的保养和维护(3)磨削刀具的寿命管理5.安全生产与环保知识(1)磨削工艺中的安全操作规程(2)磨削工艺中的环境保护知识(3)磨削工艺中的事故预防与处理四、培训方式本培训采取理论与实践相结合的方式进行。
培训内容主要通过教学讲解、案例分析、现场实习等方式进行。
五、培训时间为期2个月,每周5天,每天8小时,根据实际情况可适当调整培训时间。
六、培训具体安排第一阶段时间:第1周-第2周内容:磨削工艺基础知识的讲解,学员应通过听课、讨论等方式深入理解。
学习目标:掌握基本的磨削工艺知识,了解不同磨削工艺的特点、应用范围及工艺要点。
第二阶段时间:第3周-第4周内容:磨削工艺技术的讲解,学员应通过书面资料、图解等方式深入理解。
学习目标:熟练掌握磨削工艺的操作技术,了解磨削加工的各项参数及其调整方法。
第三阶段时间:第5周-第6周内容:磨削加工工艺的讲解,引导学员进行实地操作。
学习目标:培养学员实际操作的能力,熟练掌握各种磨削加工工艺及其应用范围。
第四阶段时间:第7周-第8周内容:磨削刀具的应用与保养的讲解,引导学员进行实地操作和维护。
学习目标:了解各类磨削刀具的使用方法,掌握磨削刀具的保养和维护技术。
磨削生产工艺流程
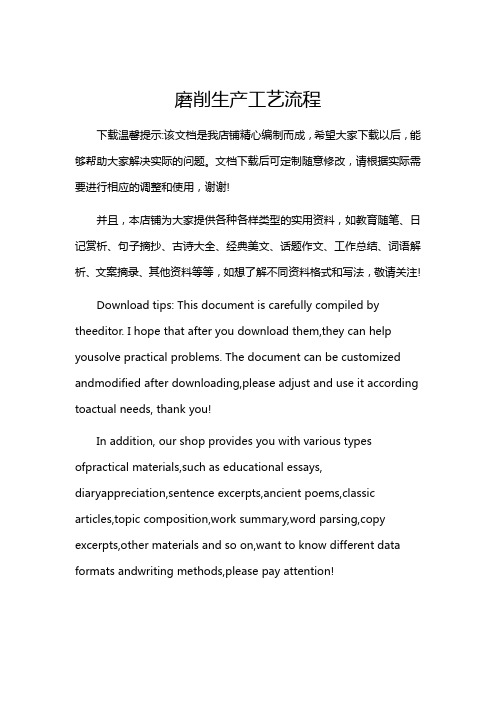
磨削生产工艺流程下载温馨提示:该文档是我店铺精心编制而成,希望大家下载以后,能够帮助大家解决实际的问题。
文档下载后可定制随意修改,请根据实际需要进行相应的调整和使用,谢谢!并且,本店铺为大家提供各种各样类型的实用资料,如教育随笔、日记赏析、句子摘抄、古诗大全、经典美文、话题作文、工作总结、词语解析、文案摘录、其他资料等等,如想了解不同资料格式和写法,敬请关注!Download tips: This document is carefully compiled by theeditor. I hope that after you download them,they can help yousolve practical problems. The document can be customized andmodified after downloading,please adjust and use it according toactual needs, thank you!In addition, our shop provides you with various types ofpractical materials,such as educational essays, diaryappreciation,sentence excerpts,ancient poems,classic articles,topic composition,work summary,word parsing,copy excerpts,other materials and so on,want to know different data formats andwriting methods,please pay attention!磨削生产工艺流程磨削生产工艺流程磨削生产工艺流程包括磨削准备、磨削加工、磨削后处理等步骤。
数控车削加工工艺
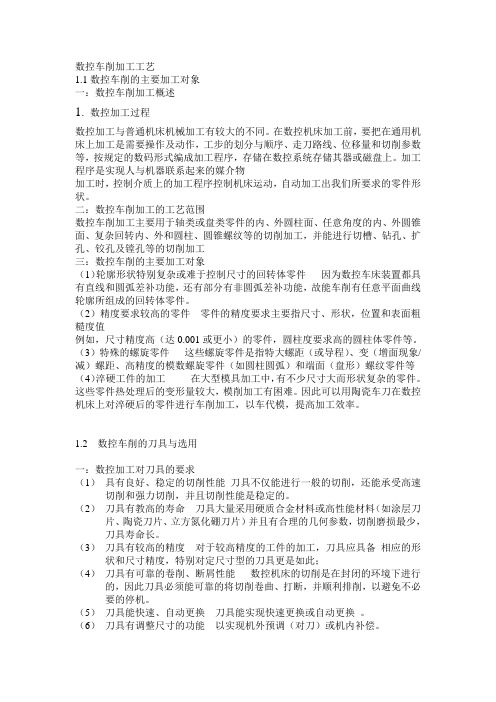
数控车削加工工艺1.1数控车削的主要加工对象一:数控车削加工概述1.数控加工过程数控加工与普通机床机械加工有较大的不同。
在数控机床加工前,要把在通用机床上加工是需要操作及动作,工步的划分与顺序、走刀路线、位移量和切削参数等,按规定的数码形式编成加工程序,存储在数控系统存储其器或磁盘上。
加工程序是实现人与机器联系起来的媒介物加工时,控制介质上的加工程序控制机床运动,自动加工出我们所要求的零件形状。
二:数控车削加工的工艺范围数控车削加工主要用于轴类或盘类零件的内、外圆柱面、任意角度的内、外圆锥面、复杂回转内、外和圆柱、圆锥螺纹等的切削加工,并能进行切槽、钻孔、扩孔、铰孔及镗孔等的切削加工三:数控车削的主要加工对象(1)轮廓形状特别复杂或难于控制尺寸的回转体零件因为数控车床装置都具有直线和圆弧差补功能,还有部分有非圆弧差补功能,故能车削有任意平面曲线轮廓所组成的回转体零件。
(2)精度要求较高的零件零件的精度要求主要指尺寸、形状,位置和表面粗糙度值例如,尺寸精度高(达0.001或更小)的零件,圆柱度要求高的圆柱体零件等。
(3)特殊的螺旋零件这些螺旋零件是指特大螺距(或导程)、变(增面现象/减)螺距、高精度的模数螺旋零件(如圆柱圆弧)和端面(盘形)螺纹零件等(4)淬硬工件的加工在大型模具加工中,有不少尺寸大而形状复杂的零件。
这些零件热处理后的变形量较大,模削加工有困难。
因此可以用陶瓷车刀在数控机床上对淬硬后的零件进行车削加工,以车代模,提高加工效率。
1.2 数控车削的刀具与选用一:数控加工对刀具的要求(1)具有良好、稳定的切削性能刀具不仅能进行一般的切削,还能承受高速切削和强力切削,并且切削性能是稳定的。
(2)刀具有教高的寿命刀具大量采用硬质合金材料或高性能材料(如涂层刀片、陶瓷刀片、立方氮化硼刀片)并且有合理的几何参数,切削磨损最少,刀具寿命长。
(3)刀具有较高的精度对于较高精度的工件的加工,刀具应具备相应的形状和尺寸精度,特别对定尺寸型的刀具更是如此;(4)刀具有可靠的卷削、断屑性能数控机床的切削是在封闭的环境下进行的,因此刀具必须能可靠的将切削卷曲、打断,并顺利排削,以避免不必要的停机。
4磨削
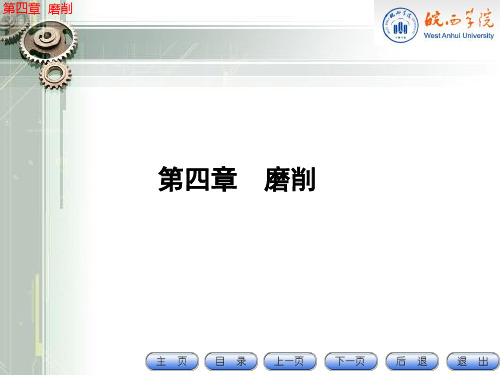
第四章 磨削
二、磨削温度
磨粒磨削点温度θdot 磨粒切削刃与切屑接触部分的温度,是磨削中温度 最高的部位,也是磨削热的热源。它不但影响工件 表面质量,且与磨粒的磨损以及切屑的熔着现象有 密切关系。
f v v
0 . 240 . 26 0 . 13 dot w r
v、vw——分别为砂轮及工件的线速度(m/s); fr——径向进给量(mm)。
工件干磨时常发生这种情况 。
第四章 磨削
二、磨削温度
(2)淬火烧伤 磨削时,工件表面层温度超过相变温度 Ac3 ,如果此时冷 却充分,则表层将急冷形成二次淬火马氏体组织。工件 表层硬度较原来的回火马氏体高,但很薄,其下层因冷 却速度慢仍为硬度较低的回火索氏体和屈氏体。这种情 况称为淬火烧伤。
⑷砂轮的磨损会使磨削力增大。
第四章 磨削
一、磨削力和磨削功率
主运动所消耗的功率定义为磨削功率。
磨削功率:
Pm Fz 1000
第四章 磨削
二、磨削温度
(一)磨削温度的概念 磨削时由于速度很高,且单位切削功率也大(约为车 削的10~20倍)。因此磨削温度很高。 磨削温度 :砂轮与工件接触面的平均温度 磨削温度区分为: 砂轮磨削区温度θA和磨粒磨削点温度θdot。
第四章 磨削
二、磨削温度
烧伤表面的硬度变化
第四章 磨削
二、磨削温度
磨削烧伤的表现形式
磨削烧伤会破坏工件表面层组织,严重的会出现裂纹, 从而影响工件的耐磨性和使用寿命。
(1)退火烧伤
(2)淬火烧伤 (3)回火烧伤
第四章 磨削
二、磨削温度
(1)退火烧伤 在磨削时,如工件表面层温度超过相变温度Ac3,则马 氏体转变为奥氏体,如果此时无冷却液,则表面层硬度 急剧下降,工件表面层被退火,故这种烧伤称退火烧伤。
数控铣削加工工艺与编程
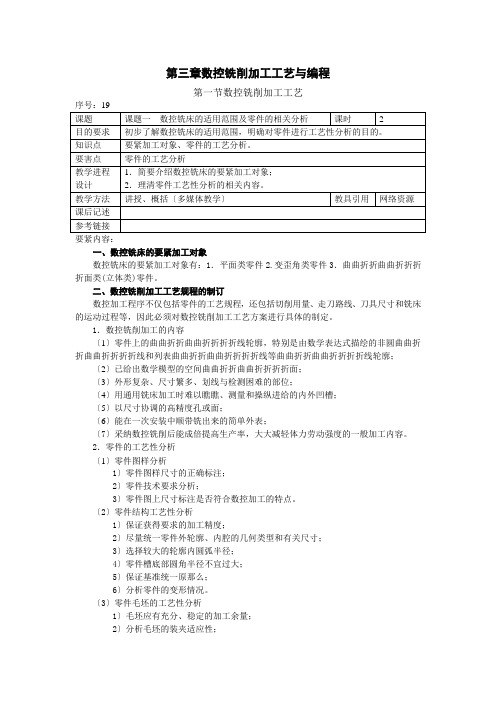
第三章数控铣削加工工艺与编程第一节数控铣削加工工艺序号:19要紧内容:一、数控铣床的要紧加工对象数控铣床的要紧加工对象有:1.平面类零件2.变歪角类零件3.曲曲折折曲曲折折折折面类(立体类)零件。
二、数控铣削加工工艺规程的制订数控加工程序不仅包括零件的工艺规程,还包括切削用量、走刀路线、刀具尺寸和铣床的运动过程等,因此必须对数控铣削加工工艺方案进行具体的制定。
1.数控铣削加工的内容〔1〕零件上的曲曲折折曲曲折折折折线轮廓,特别是由数学表达式描绘的非圆曲曲折折曲曲折折折折线和列表曲曲折折曲曲折折折折线等曲曲折折曲曲折折折折线轮廓;〔2〕已给出数学模型的空间曲曲折折曲曲折折折折面;〔3〕外形复杂、尺寸繁多、划线与检测困难的部位;〔4〕用通用铣床加工时难以瞧瞧、测量和操纵进给的内外凹槽;〔5〕以尺寸协调的高精度孔或面;〔6〕能在一次安装中顺带铣出来的简单外表;〔7〕采纳数控铣削后能成倍提高生产率,大大减轻体力劳动强度的一般加工内容。
2.零件的工艺性分析〔1〕零件图样分析1〕零件图样尺寸的正确标注;2〕零件技术要求分析;3〕零件图上尺寸标注是否符合数控加工的特点。
〔2〕零件结构工艺性分析1〕保证获得要求的加工精度;2〕尽量统一零件外轮廓、内腔的几何类型和有关尺寸;3〕选择较大的轮廓内圆弧半径;4〕零件槽底部圆角半径不宜过大;5〕保证基准统一原那么;6〕分析零件的变形情况。
〔3〕零件毛坯的工艺性分析1〕毛坯应有充分、稳定的加工余量;2〕分析毛坯的装夹适应性;3〕分析毛坯的余量大小及均匀性。
小结:数控铣床要紧加工对象的特点、零件的工艺性分析。
序号:20课题课题二数控铣削工艺路线课时 2目的要求具体了解制定数控铣削工艺路线的各个环节,明确各项细那么,掌握“合理〞度。
知识点加工方法、工序、加工顺序、装夹方案、进给路线、切进、切出、行切、环切。
要害点加工方法、加工顺序、进给路线、切进、切出教学进程设计1.具体介绍数控铣削工艺路线的各个环节;2.强调合理性;3.举例引证。
数控磨床综合--技巧,难题,解决方案
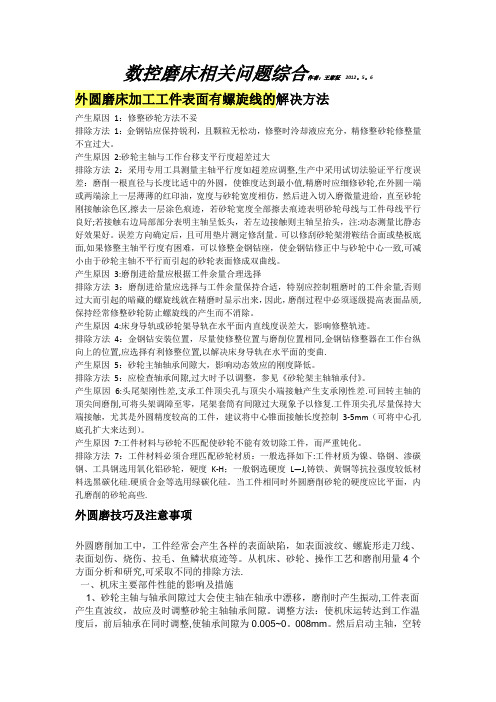
数控磨床相关问题综合作者:王家征2012。
5。
6外圆磨床加工工件表面有螺旋线的解决方法产生原因1:修整砂轮方法不妥排除方法1:金钢钻应保持锐利,且颗粒无松动,修整时泠却液应充分,精修整砂轮修整量不宜过大。
产生原因2:砂轮主轴与工作台移支平行度超差过大排除方法2:采用专用工具测量主轴平行度如超差应调整,生产中采用试切法验证平行度误差:磨削一根直径与长度比适中的外圆,使锥度达到最小值,精磨时应细修砂轮,在外圆一端或两端涂上一层薄薄的红印油,宽度与砂轮宽度相仿,然后进入切入磨微量进给,直至砂轮刚接触涂色区,擦去一层涂色痕迹,若砂轮宽度全部擦去痕迹表明砂轮母线与工件母线平行良好;若接触右边局部部分表明主轴呈低头,若左边接触则主轴呈抬头,注:动态测量比静态好效果好。
误差方向确定后,且可用垫片测定修刮量。
可以修刮砂轮架滑鞍结合面或垫板底面,如果修整主轴平行度有困难,可以修整金钢钻座,使金钢钻修正中与砂轮中心一致,可减小由于砂轮主轴不平行而引起的砂轮表面修成双曲线。
产生原因3:磨削进给量应根据工件余量合理选择排除方法3:磨削进给量应选择与工件余量保持合适,特别应控制粗磨时的工件余量,否则过大而引起的暗藏的螺旋线就在精磨时显示出来,因此,磨削过程中必须逐级提高表面品质,保持经常修整砂轮防止螺旋线的产生而不消除。
产生原因4:床身导轨或砂轮架导轨在水平面内直线度误差大,影响修整轨迹。
排除方法4:金钢钻安装位置,尽量使修整位置与磨削位置相同,金钢钻修整器在工作台纵向上的位置,应选择有利修整位置,以解决床身导轨在水平面的变曲.产生原因5:砂轮主轴轴承间隙大,影响动态效应的刚度降低。
排除方法5:应检查轴承间隙,过大时予以调整,参见《砂轮架主轴轴承付》。
产生原因6:头尾架刚性差,支承工件顶尖孔与顶尖小端接触产生支承刚性差.可回转主轴的顶尖间磨削,可将头架调障至零,尾架套筒有间隙过大现象予以修复.工件顶尖孔尽量保持大端接触,尤其是外圆精度较高的工件,建议将中心锥面接触长度控制3-5mm(可将中心孔底孔扩大来达到)。
数控磨床的结构与工作原理

数控磨床的结构与工作原理数控磨床是一种高效的精密加工设备,主要利用高速旋转的砂轮对工件进行切削加工。
它的结构和工作原理都非常复杂,下面我们来逐一探讨。
一、数控磨床的结构数控磨床主要由以下部分组成:1.机床基础部分机床基础是整个磨床的支撑结构,它的主要作用是在加工过程中稳定机床的位置、振动等。
常见的机床基础材料有铸铁、钢、混凝土等,其中钢材的强度最高。
2.工作台部分工作台是加工工件的载体,它有两种类型:圆形工作台和方形工作台。
圆形工作台适用于圆锥面、球面等曲线面的加工;方形工作台适用于平面、倾斜面等直线面的加工。
通常工作台可以在X、Y、Z三个方向上进行移动和旋转,以满足加工质量的要求。
3.主轴部分主轴是数控磨床的重要组成部分,它负责带动砂轮旋转。
主轴的旋转速度通常在1000~10000转/分之间,高速实现了磨削加工。
4.砂轮部分砂轮是精密加工的重要工具,它由磨粒、结合剂和孔道构成。
砂轮磨粒的形状和大小不同,可以满足不同的加工需要。
结合剂可以提高磨轮的强度和磨削性能。
孔道则负责冷却和润滑砂轮。
5.数控系统数控系统是数控磨床的核心部分,它由磨削程序、控制系统和伺服系统组成。
磨削程序是指磨削加工的具体步骤和操作方法。
控制系统则负责控制机床的移动和旋转,保证工件的精度和加工质量。
伺服系统则监督加工过程中的各种参数变化,及时调整机床位置和速度,确保加工过程顺利进行。
二、数控磨床的工作原理数控磨床的工作原理可以分为以下几个步骤:1.刀具的装夹在加工之前,需要将砂轮装载到主轴上,然后装夹工件。
然后将刀具固定在刀头上,使其能够接触到工件并对其进行加工。
2.磨削加工在数控磨床的加工过程中,主轴高速旋转,带动砂轮进行磨削。
砂轮在加工过程中通过加工液润滑,确保工件表面的光洁度。
同时数控系统监测加工过程中的各种参数变化,对加工过程进行及时调整。
3.工件的移动和旋转在加工过程中,工件通常会在X、Y、Z三个方向上进行移动和旋转,以实现圆锥面、圆球面等曲线面的加工。
磨削加工技术
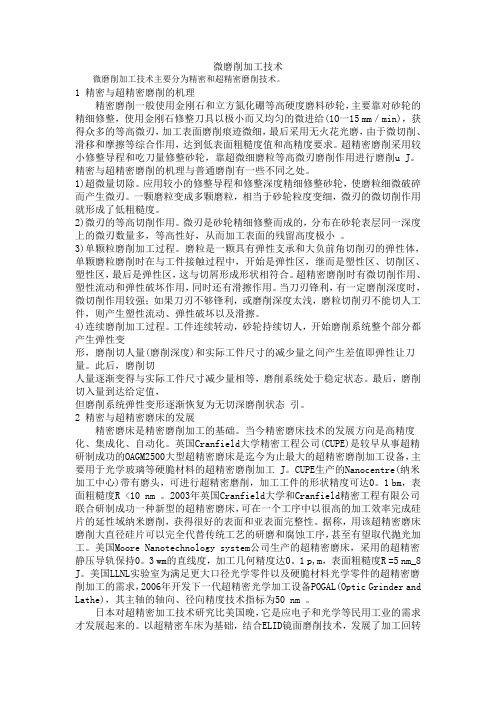
微磨削加工技术微磨削加工技术主要分为精密和超精密磨削技术。
1 精密与超精密磨削的机理精密磨削一般使用金刚石和立方氮化硼等高硬度磨料砂轮,主要靠对砂轮的精细修整,使用金刚石修整刀具以极小而又均匀的微进给(1O一15 mm/min),获得众多的等高微刃,加工表面磨削痕迹微细,最后采用无火花光磨,由于微切削、滑移和摩擦等综合作用,达到低表面粗糙度值和高精度要求。
超精密磨削采用较小修整导程和吃刀量修整砂轮,靠超微细磨粒等高微刃磨削作用进行磨削u J。
精密与超精密磨削的机理与普通磨削有一些不同之处。
1)超微量切除。
应用较小的修整导程和修整深度精细修整砂轮,使磨粒细微破碎而产生微刃。
一颗磨粒变成多颗磨粒,相当于砂轮粒度变细,微刃的微切削作用就形成了低粗糙度。
2)微刃的等高切削作用。
微刃是砂轮精细修整而成的,分布在砂轮表层同一深度上的微刃数量多,等高性好,从而加工表面的残留高度极小。
3)单颗粒磨削加工过程。
磨粒是一颗具有弹性支承和大负前角切削刃的弹性体,单颗磨粒磨削时在与工件接触过程中,开始是弹性区,继而是塑性区、切削区、塑性区,最后是弹性区,这与切屑形成形状相符合。
超精密磨削时有微切削作用、塑性流动和弹性破坏作用,同时还有滑擦作用。
当刀刃锋利,有一定磨削深度时,微切削作用较强;如果刀刃不够锋利,或磨削深度太浅,磨粒切削刃不能切人工件,则产生塑性流动、弹性破坏以及滑擦。
4)连续磨削加工过程。
工件连续转动,砂轮持续切人,开始磨削系统整个部分都产生弹性变形,磨削切人量(磨削深度)和实际工件尺寸的减少量之间产生差值即弹性让刀量。
此后,磨削切人量逐渐变得与实际工件尺寸减少量相等,磨削系统处于稳定状态。
最后,磨削切入量到达给定值,但磨削系统弹性变形逐渐恢复为无切深磨削状态引。
2 精密与超精密磨床的发展精密磨床是精密磨削加工的基础。
当今精密磨床技术的发展方向是高精度化、集成化、自动化。
英国Cranfield大学精密工程公司(CUPE)是较早从事超精研制成功的OAGM2500大型超精密磨床是迄今为止最大的超精密磨削加工设备,主要用于光学玻璃等硬脆材料的超精密磨削加工 J。
数控加工中的高效刀具磨削与涂层技术应用
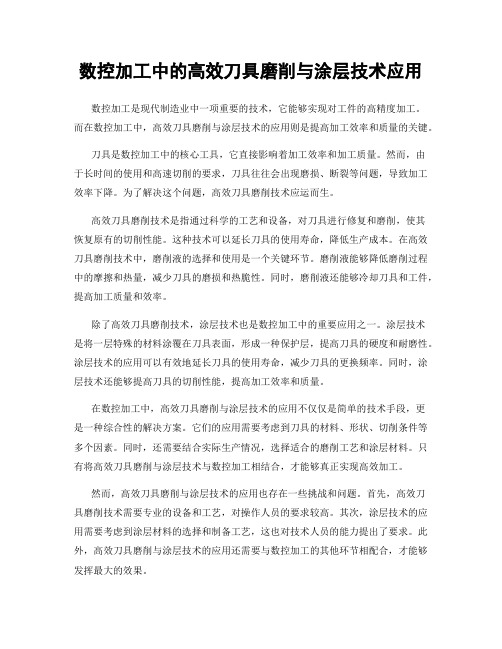
数控加工中的高效刀具磨削与涂层技术应用数控加工是现代制造业中一项重要的技术,它能够实现对工件的高精度加工。
而在数控加工中,高效刀具磨削与涂层技术的应用则是提高加工效率和质量的关键。
刀具是数控加工中的核心工具,它直接影响着加工效率和加工质量。
然而,由于长时间的使用和高速切削的要求,刀具往往会出现磨损、断裂等问题,导致加工效率下降。
为了解决这个问题,高效刀具磨削技术应运而生。
高效刀具磨削技术是指通过科学的工艺和设备,对刀具进行修复和磨削,使其恢复原有的切削性能。
这种技术可以延长刀具的使用寿命,降低生产成本。
在高效刀具磨削技术中,磨削液的选择和使用是一个关键环节。
磨削液能够降低磨削过程中的摩擦和热量,减少刀具的磨损和热脆性。
同时,磨削液还能够冷却刀具和工件,提高加工质量和效率。
除了高效刀具磨削技术,涂层技术也是数控加工中的重要应用之一。
涂层技术是将一层特殊的材料涂覆在刀具表面,形成一种保护层,提高刀具的硬度和耐磨性。
涂层技术的应用可以有效地延长刀具的使用寿命,减少刀具的更换频率。
同时,涂层技术还能够提高刀具的切削性能,提高加工效率和质量。
在数控加工中,高效刀具磨削与涂层技术的应用不仅仅是简单的技术手段,更是一种综合性的解决方案。
它们的应用需要考虑到刀具的材料、形状、切削条件等多个因素。
同时,还需要结合实际生产情况,选择适合的磨削工艺和涂层材料。
只有将高效刀具磨削与涂层技术与数控加工相结合,才能够真正实现高效加工。
然而,高效刀具磨削与涂层技术的应用也存在一些挑战和问题。
首先,高效刀具磨削技术需要专业的设备和工艺,对操作人员的要求较高。
其次,涂层技术的应用需要考虑到涂层材料的选择和制备工艺,这也对技术人员的能力提出了要求。
此外,高效刀具磨削与涂层技术的应用还需要与数控加工的其他环节相配合,才能够发挥最大的效果。
总之,高效刀具磨削与涂层技术在数控加工中的应用具有重要的意义。
它们能够提高加工效率和质量,降低生产成本。
连续磨削加工实验报告
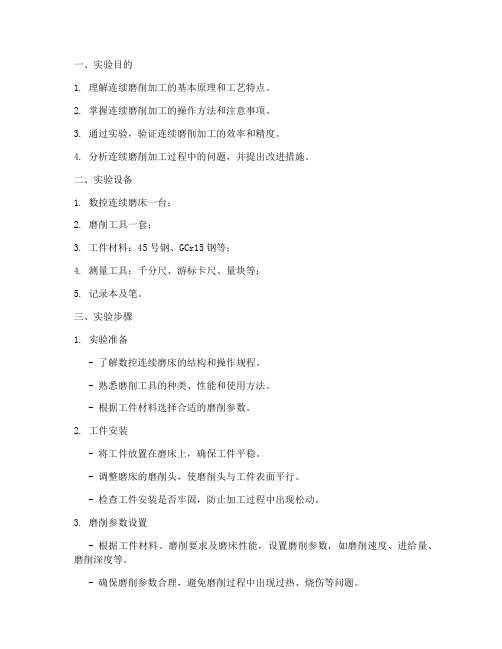
一、实验目的1. 理解连续磨削加工的基本原理和工艺特点。
2. 掌握连续磨削加工的操作方法和注意事项。
3. 通过实验,验证连续磨削加工的效率和精度。
4. 分析连续磨削加工过程中的问题,并提出改进措施。
二、实验设备1. 数控连续磨床一台;2. 磨削工具一套;3. 工件材料:45号钢、GCr15钢等;4. 测量工具:千分尺、游标卡尺、量块等;5. 记录本及笔。
三、实验步骤1. 实验准备- 了解数控连续磨床的结构和操作规程。
- 熟悉磨削工具的种类、性能和使用方法。
- 根据工件材料选择合适的磨削参数。
2. 工件安装- 将工件放置在磨床上,确保工件平稳。
- 调整磨床的磨削头,使磨削头与工件表面平行。
- 检查工件安装是否牢固,防止加工过程中出现松动。
3. 磨削参数设置- 根据工件材料、磨削要求及磨床性能,设置磨削参数,如磨削速度、进给量、磨削深度等。
- 确保磨削参数合理,避免磨削过程中出现过热、烧伤等问题。
4. 磨削加工- 启动磨床,进行连续磨削加工。
- 观察磨削过程中的现象,如磨削噪声、温度等,及时调整磨削参数。
- 控制磨削速度和进给量,确保磨削质量。
5. 磨削后检查- 磨削完成后,检查工件尺寸、形状和表面质量。
- 使用测量工具进行检测,确保工件符合要求。
6. 实验数据记录- 记录磨削参数、磨削时间、磨削效率、磨削质量等数据。
- 分析实验结果,总结经验。
四、实验结果与分析1. 磨削效率- 通过实验,连续磨削加工的效率较高,平均磨削速度达到150m/min。
- 与普通磨削加工相比,连续磨削加工时间缩短了约30%。
2. 磨削质量- 连续磨削加工的工件尺寸精度高,表面质量好。
- 实验结果显示,工件尺寸精度达到IT6级,表面粗糙度达到Ra0.8μm。
3. 问题分析- 在实验过程中,发现部分工件磨削过程中出现烧伤现象。
- 分析原因,可能是磨削参数设置不合理、磨削工具磨损严重等因素。
五、改进措施1. 优化磨削参数,如磨削速度、进给量、磨削深度等,提高磨削效率和质量。
数控机床编程及操作数控车削加工工艺
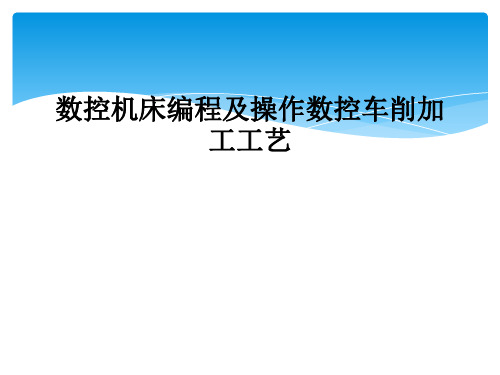
第5讲 数控车削加工工艺
5.1 数控加工工艺概述 5.2 数控加工工艺分析的一般步骤与方法 5.3 数控车削工艺 5.4 数控车削零件工艺分析举例 5.5 数控加工工艺文件
第5讲 数控车削加工工艺
5.1 数控加工工艺概述
1.数控加工工艺的基本特点
在普通机床上加工零件时,是用工艺规程来规定每道加 工工序的操作顺序的,操作者严格按工艺卡规定的操作顺序 进行加工。而在数控机床上加工零件时,要把加工零件的全 部工艺过程、工艺参数等编制成程序,存储在数控系统的存 储器内,来控制机床进行加工。因此,数控机床加工工艺与 普通机床加工工艺原则基本相同,但数控加工的整个过程是 自动进行的,又有其特点:
② 尽量减少装夹次数,尽可能在一次定位装夹后加工出全部 待加工表面。
③ 避免用占机人工调整加工方案,以便充分发挥数控机床的 效能。
第5讲 数控车削加工工艺
(2)选择夹具的基本原则
数控加工的特点对夹具提出了两点要求:一是要保证夹 具的坐标方向与机床的坐标方向相对固定不变;二是要零件 和机床坐标系的尺寸关系。除此之外还应考虑以下几点: ① 当零件加工批量不大时,应尽量采用组合夹具、可调式夹 具或其他通用夹具,以缩短生产准备时间,节省生产费用。
第5讲 数控车削加工工艺
② 不能在一次安装中完成加工的星形零件或部位,采用数 控车削加工,效果不明显。 2.对零件图进行数控加工工艺分析 (1)结构工艺性分析
1)零件结构工艺性 零件结构工艺性是指在满足使用要求的前提下,零件
加工的可行性和经济性,换言之就是设计的零件结构要求 便于加工且成本低、效率高。
(2)零件各加工部位的结构工艺性应符合数控加工的特点
1)零件的内腔和外形最好采用统一的几何类型和尺寸。这 样可以减少使用刀具的规格和加工中换刀的次数,使得 编程方便,生产效益提高。
数控磨床编程及加工工艺控制

数控磨床编程及加工工艺控制数控磨床是一种高精度的加工设备,广泛应用于机械、航空、汽车等领域。
与传统的手工磨削相比,数控磨床通过程序控制磨头的移动,可以实现更加精确的磨削效果。
数控磨床编程及加工工艺控制是数控磨床加工过程中关键的环节,只有编写出符合加工要求的程序,才能保证产品的质量和精度。
一、数控磨床编程数控磨床编程是一项关键的技术,它直接决定了加工成品的质量和效率。
在数控磨床编程过程中,需要完成以下几个步骤:1.准备工作在开始编写程序之前,需要进行准备工作。
首先,需要清洁加工零件和磨头,并安装好磨头,并根据零件的尺寸要求选择合适的磨头,并将其安装到数控磨床上。
其次,需要测量零件的尺寸和形状等参数,以便编写符合零件要求的程序。
2.编写程序编写程序是数控磨床编程的核心工作。
程序的编写需要根据零件的尺寸和形状等参数来确定磨头的移动轨迹和磨削的深度。
编写程序需要使用CAD/CAM软件,使用软件绘制出零件的三维模型,然后将零件模型导入到数控磨床中。
然后根据零件的尺寸和形状编写加工程序,包括切削深度、移动速度等参数。
编写好程序之后,需要进行程序的仿真和检验,确保程序符合加工要求。
3.加工加工是数控磨床编程的最终环节。
在开始加工之前,需要将编写好的程序导入到数控磨床中,并进行加工之前的调试和检查。
开始加工后,需要对加工过程进行监控和控制,确保加工质量和效率。
二、加工工艺控制加工工艺控制是数控磨床加工过程中非常重要的环节,它直接影响到加工质量和效率。
在加工工艺控制过程中,需要注意以下几点:1.刀具选择刀具的选择直接影响到加工效果。
选择合适的刀具可以提高加工质量和效率。
在选择刀具时,需要考虑磨削材料的硬度、形状等因素,同时需要根据加工要求选择合适的切削速度、进给速度等参数。
2.加工参数控制加工参数控制是加工过程中非常重要的环节,它直接影响到加工质量和效率。
在加工过程中,需要采用合适的切削力和切削速度,同时需要控制进给量和加工深度。
数控车削加工工艺与分析
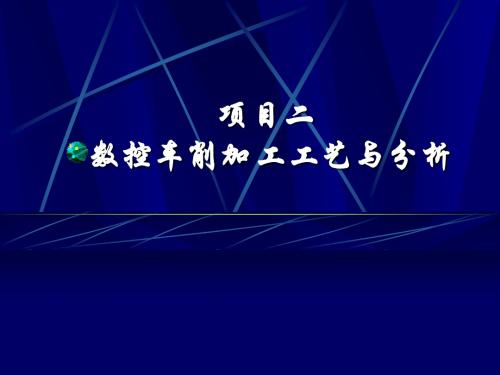
数控加工工艺分析的一般步骤与 方法
10.工艺加工路线的确定
工艺加工路线是指数控加工过程中 刀位点相对于被加工零件的运动轨迹。 编程时,确定工艺加工路线的原则是: (1)保证零件的加工精度和表面粗糙度; (2)方便数值计算,减少编程工作量; (3)缩短加工运行路线,减少空运行行程。
数控车削工艺
1. 选择正确数控车削加工内容
(c)“矩形”进给路
数控加工工艺分析的一般步骤与 方法
5. 零件的安装
1、设计基准、工艺基准和编程计算基准统一。 2、尽量减少装夹次数,尽可能在一次定位装夹 后,加工出全部待加工表面。 3、避免采用占机人工调整加工方案,以便能充 分发挥出数控机床的效能。
数控加工工艺分析的一般步骤与 方法
6. 夹具的选择
3. 加工方法的选择与加工方案的确定 1.加工方法的选择 数控车削内、外回转表面的加工方案的确定,应 注意以下几点。 (1)加工精度为IT8~IT9级、表面粗糙度Ra1.6~3.2 m、 除淬火钢以外的常用金属,可采用普通型数控车床,按粗车、 半精车、精车的方案加工。 (2)加工精度为 IT6~IT7级、表面粗糙度Ra0.2~0.63 m、 除淬火钢以外的常用金属,可采用精密型数控车床,按粗车、 半精车、精车、细车的方案加工。 (3)加工精度为IT5级、表面粗糙度Ra<0.2 m的除淬火 钢以外的常用金属,可采用高档精密型数控车床,按粗车、 半精车、精车、精密车的方案加工。
只需确定每次背吃刀量 也需计算粗车时终刀距S。 ap ,而不需计算终刀距 , 按此种加工路线,刀具切 编程方便。但在每次切 削运动的距离较短,精车 削中背吃刀量 是变化的 , 时背吃刀量相同。 且刀具切削运动的路线 较长。
数控加工工艺分析的一般步骤与 方法
毕业设计数控磨床
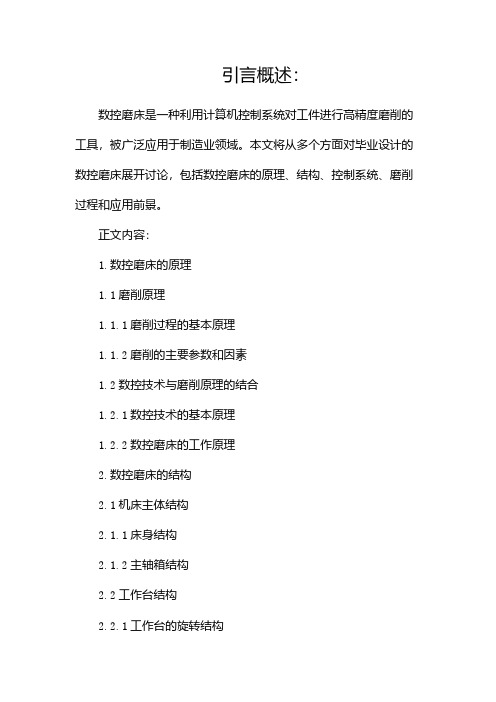
引言概述:数控磨床是一种利用计算机控制系统对工件进行高精度磨削的工具,被广泛应用于制造业领域。
本文将从多个方面对毕业设计的数控磨床展开讨论,包括数控磨床的原理、结构、控制系统、磨削过程和应用前景。
正文内容:1.数控磨床的原理1.1磨削原理1.1.1磨削过程的基本原理1.1.2磨削的主要参数和因素1.2数控技术与磨削原理的结合1.2.1数控技术的基本原理1.2.2数控磨床的工作原理2.数控磨床的结构2.1机床主体结构2.1.1床身结构2.1.2主轴箱结构2.2工作台结构2.2.1工作台的旋转结构2.2.2工作台的移动结构2.3其他重要结构2.3.1冷却系统2.3.2磨削轮装置3.数控磨床的控制系统3.1数控系统的基本组成3.1.1数控主机3.1.2驱动系统3.1.3传感器和探测器3.2数控系统的工作原理3.2.1CNC控制器的功能和作用3.2.2数据输入和处理3.2.3运动控制和插补算法4.数控磨床的磨削过程4.1磨削前的准备工作4.1.1刀具和工件的安装4.1.2磨削参数的选择4.2磨削的基本步骤4.2.1粗磨削4.2.2半精磨削4.2.3精密磨削4.3磨削中的常见问题和解决方法4.3.1磨损和断刀问题4.3.2磨削过程中的加工误差4.4磨削后的处理4.4.1检查和测试4.4.2表面处理和保护5.数控磨床的应用前景5.1数控磨削技术的发展趋势5.2数控磨床在制造业的应用领域5.2.1精密零部件制造5.2.2模具制造5.3数控磨床的市场前景5.3.1国内市场状况和竞争格局5.3.2国际市场发展趋势总结:本文全面介绍了毕业设计的数控磨床,包括其原理、结构、控制系统、磨削过程和应用前景等方面。
数控磨床通过结合数控技术和磨削原理,实现了对工件的高精度磨削。
数控磨床的控制系统是数控磨床实现自动化的关键,而磨削过程中需要进行一系列准备工作和注意问题。
数控磨床在制造业领域有着广泛的应用,特别是在精密零部件制造和模具制造等领域,其市场前景十分广阔。
数控加工工艺
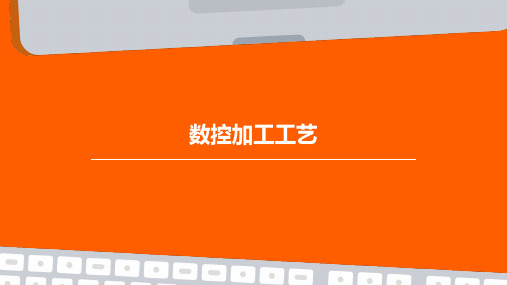
切削用量的优化
01
切削深度与宽度
切削深度与宽度是影响切削用 量的重要因素。在保证加工质 量和刀具寿命的前提下,合理 增大切削深度与宽度可以提高 加工效率。
02
切削路径规划
合理的切削路径规划可以减少 空行程时间和提高材料去除率 ,进而优化切削用量。常用的 切削路径规划方法包括往复式 切削、螺旋式切削等。
03
冷却与润滑
04
切削过程中的冷却与润滑对切削 用量也有影响。合适的冷却润滑 方式可以减小切削力、降低刀具 磨损,并提高加工表面的质量。
工艺系统刚性
工艺系统的刚性对切削用量有较 大影响。在切削过程中,如果工 艺系统刚性不足,可能会导致振 动、过切等问题,影响加工质量 。因此,在选择切削用量时,需 充分考虑工艺系统的刚性。
数控加工的重要性
提高加工精度和效率
促进制造业转型升级
数控加工可以实现高精度和高效率的 加工,提高生产效率和产品质量。
数控加工技术的应用可以推动传统制 造业的转型升级,提高制造业的技术 水平和市场竞争力。
适应个性化生产需求
数控加工可以快速调整工艺参数和加 工过程,适应个性化生产需求,缩短 产品研发周期。
螺纹车削
切槽加工
用于加工各种螺纹,通过调整刀具的角度 和切削参数,实现高质量螺纹车削。
用于在轴类零件上加工各种槽形,通过选 择合适的刀具和切削参数,实现高效切槽 加工。
线切割加工工艺
快走丝线切割
采用快速往复运动的电极丝进行切割,适用于加 工厚度较大的工件。
大锥度线切割
适用于加工大锥度或非圆形工件,能够实现复杂 形状的切割。
质量控制
建立严格的质量控制体系,对加工过 程进行实时监测和记录,确保产品质 量的稳定性和可靠性。
- 1、下载文档前请自行甄别文档内容的完整性,平台不提供额外的编辑、内容补充、找答案等附加服务。
- 2、"仅部分预览"的文档,不可在线预览部分如存在完整性等问题,可反馈申请退款(可完整预览的文档不适用该条件!)。
- 3、如文档侵犯您的权益,请联系客服反馈,我们会尽快为您处理(人工客服工作时间:9:00-18:30)。
工要求,确定加工方案,选择合适的数控磨床,提
出夹具设计任务书,选择砂轮,确定合理的磨削方 式、 磨削用量及冷却方式等。
第五章 数控磨削加工工艺
第一节 第二节 第三节
数控磨削加工概述 数控磨削加工工艺的分析 典型零件的数控磨削工艺分析
第五章 数控磨削加工工艺
第二节 数控磨削加工工艺的分析
一、 磨削步骤的制定
(11) 半精磨各部位, 均留余量0.08~0.10mm。 (12) 选用螺纹磨床磨削M35×1.5—6g的螺纹至尺寸要求。 (13) 精研中心孔, 保证与磨床顶尖接触率大于85%,表面
粗糙度Ra≤0.2μm。
(14) 按普通参数精修砂轮。
第五章 数控磨削加工工艺
3. 零件的精密磨削要点
(1) 在同一台磨床上磨削机床工作顶尖和专用铸铁顶尖。 (2) 利用专用铸铁顶尖配研磨剂精研中心孔,保证与机床工作顶
第五章 数控磨削加工工艺
第一节 第二节 第三节
数控磨削加工概述 数控磨削加工工艺的分析 典型零件的数控磨削工艺分析
第五章 数控磨削加工工艺
第一节 数控磨削加工概述 一、 数控磨削加工的主要对象
1. 重复性投产的零件 2. 要求重点保证加工质量又能高效生产的中、小 批量关键零件 3. 零件的加工批量应大于经济批量 4. 所加工的零件应符合能充分发挥数控磨床多工 序集中加工的工艺特点 5. 加工有生产平衡要求的零件 6. 加工具有特殊型面的零件
第五章 数控磨削加工工艺
4. 注意事项
(1) 精细修整砂轮。 (2) 调整工件,磨削莫氏4号锥面。 (3) 将工件莫氏锥面涂色, 根据颜色的变化参照火花、 声
音认真对刀。
(4) 砂轮采用双程进给方式,从莫氏锥体大端开始向小端方 向纵磨。 (5) 砂轮移至小端时,应将砂轮的超越量控制为(1/ 2~2/ 3)B。 (6) 最终采用无进给“光磨” 1~2个单程将莫氏锥面磨出。
第五章 数控磨削加工工艺
4. 磨床和夹具的选择
(1) 选择磨尺寸的确定
第五章 数控磨削加工工艺
二、 复杂外轮廓的磨削路线
1. 砂轮沿零件表面走出轮廓形状
用砂轮沿零件表面走出轮廓形状
第五章 数控磨削加工工艺
2. 用成形砂轮磨削
用成形砂轮磨削
复合磨削
第五章 数控磨削加工工艺
二、 数控磨削加工工艺的基本特点
1. 磨削效率高
6. 实现机床操纵 加工过程的 自动化
2. 能获得很高的 加工精度很小的 表面粗糙度值
基本特点
3. 切削功率大 消耗能量多
5. 柔性高
4. 加工范围广泛
第五章 数控磨削加工工艺
三、 数控磨削加工工艺的主要内容
数控磨削加工工艺设计的内容一般包括: 根据零件技术要求进行综合工艺分析,明确加
1. 分析零件图 2. 定位基准的选择 3. 磨削工艺的制定
(1) 划分加工阶段的原则 1) 粗磨阶段 2) 半精磨阶段 3) 精磨阶段
第五章 数控磨削加工工艺
(2) 工序的集中和分散原则 1) 工序集中的特点 (3) 磨削顺序的安排 1) 当工件位置精度要求较高时,可采用统一的基准, 通过一次装夹完成工件的全部工步,此时应提高统一 基准面的精度。 2) 当工件由两个相互位置精度要求较高的表面组成时, 应选用其中精度较高的表面定位,由此来磨削另一面。 3) 热处理工序主要用来改善材料的性能和消除内应力, 精密零件在粗磨后、 精磨前一般需进行人工时效, 以 消除粗磨所产生的内应力 2) 工序分散的特点
检测标杆
第五章 数控磨削加工工艺
1. 加工工艺
检测标杆的磨削加工工艺见表5—1。
2. 工艺分析
(1) 磨削ϕ16mm工艺孔 时要求将单边过盈量控 制在0.0025~0.005mm之
间。
工艺堵
第五章 数控磨削加工工艺
(2) 磨削加工时采用工序分开的方法, 分粗磨、 半精磨、 精磨和精密磨, 这样可以合理地分配余量, 保证工件在加
第五章 数控磨削加工工艺
二、 内圆零件的磨削
主轴套筒
第五章 数控磨削加工工艺
1. 工艺分析
(1) 主轴套筒主要尺寸和几何公差要求 (2) 定位基准的选择 (3) 磨削顺序的安排 (4) 夹具的选择
第五章 数控磨削加工工艺
2. 磨削步骤
(1) 粗磨外圆 (2) 半精磨外圆 (3) 粗磨内孔
(4) 精磨外圆
(7) 工件用三爪自定心卡盘夹持左端ϕ24mm外圆。
(8) 研两端中心孔。 (9) 用两顶尖装夹, 粗磨各部位外圆, 均留余量0.2~0.25mm。
第五章 数控磨削加工工艺
(10) 利用三棱硬质合金顶尖研磨经去应力处理后的中 心孔,当氧化层研掉后换机床顶尖研中心孔, 保证接
触率在70%以上,表面粗糙度Ra≤0.8μm。
3. 复合磨削——既有成形磨削又有沿廓形进给磨削
在普通磨床上进行复杂外轮廓的磨削与在数控 磨床上有什么不同?
第五章 数控磨削加工工艺
第一节 第二节 第三节
数控磨削加工概述 数控磨削加工工艺的分析 典型零件的数控磨削工艺分析
第五章 数控磨削加工工艺
第三节 典型零件的数控磨削工艺分析 一、 外圆零件的磨削
(5) 精磨内孔 (6) 精密磨削外圆
第五章 数控磨削加工工艺
三、 薄板平面的磨削
薄板
第五章 数控磨削加工工艺
1. 加工工艺 薄板平面磨削工艺见表5—2。
2. 磨削操作与操作技巧
(1) 粗定位基准的制作 1) 根据零件的变形情况,将凹面用速干胶水层层粘 纸填满后晾干, 放在平板上用大直径砂轮的端面将 多余的纸研平即可。
性工作台的给磁量。 4) 零件翻面,重复上述操作,以较小的磁力精磨表面至尺寸。 5) 精磨时要保证砂轮与零件呈顺磨状态;但无论粗磨还是精 磨都需做无磁状态下的光磨。
2) 在平板上用敲击法检测填充质量。
第五章 数控磨削加工工艺
(2) 粗磨平面
1) 以粘纸的平面为基准,将工件吸在机床磁性工作台上并在
端面设挡块。 2) 选择刚玉砂轮,工作台移动速度为18m/min,垂直进给量 为0.01~0.03mm/min,粗磨上平面。 3) 将磁性工作台退磁,光磨零件至无火花后取下零件。
(4) 工件在进行精磨时,应确保工件各部位外圆的圆度、 圆柱度
及径向圆跳动误差在0.005mm之内,以保证下道工序的加工。 (6) 用两顶尖装夹, 粗磨ϕ30mm右端中心架支撑圆, 磨圆为止, 掉 头磨削ϕ24mm的外圆, 磨圆为止。
(5) 利用三棱硬质合金顶尖粗研右端ϕ16mm的孔口及左端中心孔。
工中的精度。
(3) 研磨中心孔时, 应根据工件不同阶段的加工性质保证 相应的研磨质量。 1) 半精磨前中心孔的研磨应保证与机床工作顶尖的接触 率大于70%,表面粗糙度Ra≤0.8μm。 2) 精磨和精密磨削前中心孔的研磨应保证与机床工作顶 尖的接触率大于85%,表面粗糙度Ra≤0.2μm。
第五章 数控磨削加工工艺
尖接触率大于85%,表面粗糙度Ra≤0.2μm。
(3) 磨削用量。 (4) 用模拟试件调整机床, 精密磨削外圆至尺寸要求。 (5) 将全部余量分3~4次磨去,并进行1~2次无进给“光磨”。 (6) 用模拟试件调整机床,精密磨削莫氏4号锥面至尺寸要求,
保证接触率大于80%,表面粗糙度Ra≤0.1μm。
4) 检测已磨表面的翘曲情况,根据情况在未磨到的部位粘纸
并研平,吸磨另一面, 当平面磨出80%~90%时退磁光磨。 5) 重复上述操作, 以较小的进给量反复磨削两面,控制尺寸。
第五章 数控磨削加工工艺
(3) 精磨操作 1) 精修砂轮。 2) 精磨工作台面(或精磨导磁板台面)。
3) 以零件较平整的表面为基准精磨另一面。 要注意减少磁