粘土湿型砂特点与缺陷分析与控制
粘土湿型砂及其控制要点(内容清晰)
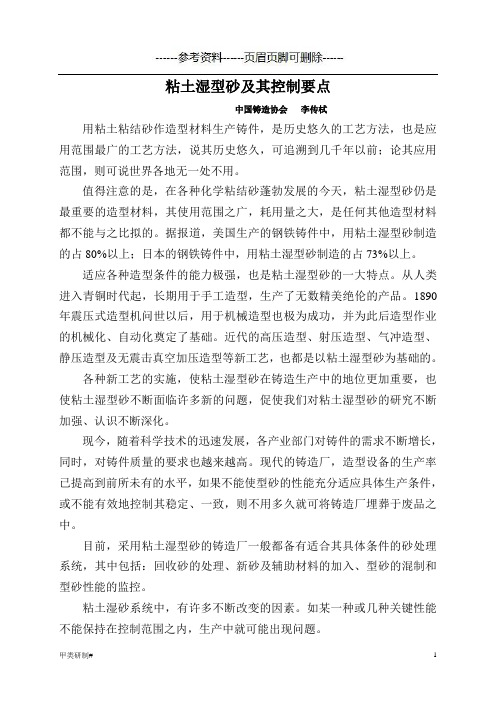
粘土湿型砂及其控制要点中国铸造协会李传栻用粘土粘结砂作造型材料生产铸件,是历史悠久的工艺方法,也是应用范围最广的工艺方法,说其历史悠久,可追溯到几千年以前;论其应用范围,则可说世界各地无一处不用。
值得注意的是,在各种化学粘结砂蓬勃发展的今天,粘土湿型砂仍是最重要的造型材料,其使用范围之广,耗用量之大,是任何其他造型材料都不能与之比拟的。
据报道,美国生产的钢铁铸件中,用粘土湿型砂制造的占80%以上;日本的钢铁铸件中,用粘土湿型砂制造的占73%以上。
适应各种造型条件的能力极强,也是粘土湿型砂的一大特点。
从人类进入青铜时代起,长期用于手工造型,生产了无数精美绝伦的产品。
1890年震压式造型机问世以后,用于机械造型也极为成功,并为此后造型作业的机械化、自动化奠定了基础。
近代的高压造型、射压造型、气冲造型、静压造型及无震击真空加压造型等新工艺,也都是以粘土湿型砂为基础的。
各种新工艺的实施,使粘土湿型砂在铸造生产中的地位更加重要,也使粘土湿型砂不断面临许多新的问题,促使我们对粘土湿型砂的研究不断加强、认识不断深化。
现今,随着科学技术的迅速发展,各产业部门对铸件的需求不断增长,同时,对铸件质量的要求也越来越高。
现代的铸造厂,造型设备的生产率已提高到前所未有的水平,如果不能使型砂的性能充分适应具体生产条件,或不能有效地控制其稳定、一致,则不用多久就可将铸造厂埋葬于废品之中。
目前,采用粘土湿型砂的铸造厂一般都备有适合其具体条件的砂处理系统,其中包括:回收砂的处理、新砂及辅助材料的加入、型砂的混制和型砂性能的监控。
粘土湿砂系统中,有许多不断改变的因素。
如某一种或几种关键性能不能保持在控制范围之内,生产中就可能出现问题。
由于各铸造厂砂处理系统的安排不同,选用的设备也不一样,要想拟定一套通用的控制办法是做不到的。
这里,将扼要谈到粘土湿型砂的特性及一些目前已被广泛认同的控制要点。
在理解这些要点基础上,可根据企业自己的具体条件确定可行的控制办法。
湿型砂的检测要求与质量控制
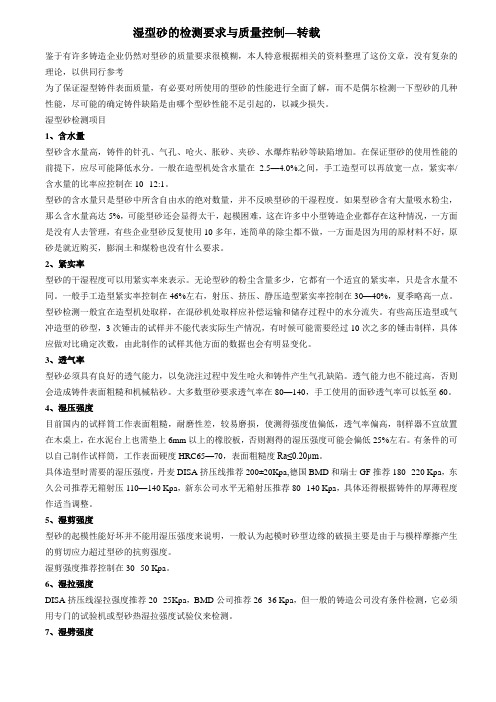
湿型砂的检测要求与质量控制—转载鉴于有许多铸造企业仍然对型砂的质量要求很模糊,本人特意根据相关的资料整理了这份文章,没有复杂的理论,以供同行参考为了保证湿型铸件表面质量,有必要对所使用的型砂的性能进行全面了解,而不是偶尔检测一下型砂的几种性能,尽可能的确定铸件缺陷是由哪个型砂性能不足引起的,以减少损失。
湿型砂检测项目1、含水量型砂含水量高,铸件的针孔、气孔、呛火、胀砂、夹砂、水爆炸粘砂等缺陷增加。
在保证型砂的使用性能的前提下,应尽可能降低水分。
一般在造型机处含水量在 2.5—4.0%之间,手工造型可以再放宽一点,紧实率/含水量的比率应控制在10--12:1。
型砂的含水量只是型砂中所含自由水的绝对数量,并不反映型砂的干湿程度。
如果型砂含有大量吸水粉尘,那么含水量高达5%,可能型砂还会显得太干,起模困难,这在许多中小型铸造企业都存在这种情况,一方面是没有人去管理,有些企业型砂反复使用10多年,连简单的除尘都不做,一方面是因为用的原材料不好,原砂是就近购买,膨润土和煤粉也没有什么要求。
2、紧实率型砂的干湿程度可以用紧实率来表示。
无论型砂的粉尘含量多少,它都有一个适宜的紧实率,只是含水量不同。
一般手工造型紧实率控制在46%左右,射压、挤压、静压造型紧实率控制在30—40%,夏季略高一点。
型砂检测一般宜在造型机处取样,在混砂机处取样应补偿运输和储存过程中的水分流失。
有些高压造型或气冲造型的砂型,3次锤击的试样并不能代表实际生产情况,有时候可能需要经过10次之多的锤击制样,具体应做对比确定次数,由此制作的试样其他方面的数据也会有明显变化。
3、透气率型砂必须具有良好的透气能力,以免浇注过程中发生呛火和铸件产生气孔缺陷。
透气能力也不能过高,否则会造成铸件表面粗糙和机械粘砂。
大多数型砂要求透气率在80—140,手工使用的面砂透气率可以低至60。
4、湿压强度目前国内的试样筒工作表面粗糙,耐磨性差,较易磨损,使测得强度值偏低,透气率偏高,制样器不宜放置在木桌上,在水泥台上也需垫上6mm以上的橡胶板,否则测得的湿压强度可能会偏低25%左右。
铸造粘土湿型砂的特性及其控制要点

铸造粘土湿型砂的特性及其控制要点发表时间:2018-12-25T11:33:27.080Z 来源:《基层建设》2018年第33期作者:赵艳锋1 李晶1 张小荣2 [导读] 摘要:针对铸造湿型砂的特性,组成,回收混配,覆膜砂对型砂的性能影响等方面控制,从而提高铸件的质量。
1.河南省西峡汽车水泵股份有限公司河南西峡 4745002.河南省西峡县天马有限责任公司河南西峡 474500摘要:针对铸造湿型砂的特性,组成,回收混配,覆膜砂对型砂的性能影响等方面控制,从而提高铸件的质量。
关键词:型砂;粘土;覆膜砂前言:铸造技术历史悠久,从人类进入青铜时代起,就用手工铸造生产了精美绝伦的产品。
铸造的三大基础是:炉子、模子、型砂。
型砂的主要原料是:原纱(烘干砂),粘土,旧砂,芯砂;型砂对铸件的质量起着决定性的影响。
1 粘土混型砂的特性通常都说粘土是湿型砂的粘结剂,实际上这种说法是不贴切的,粘土湿型砂中的粘结剂是粘土和水按一定比例混配组成的,水是粘结剂中的重要组成部分,但是水必须是自来水或蒸馏水,否则会影响型砂的湿压强度。
1.1 土水比采用高压造型工艺时,大部分土水比都在3: 1左右。
在这种条件下,型砂的可紧实性也最适合高压造型的要求(约在35~ 45之间)。
水与粘土混合后产生粘土膏,但水分再增多,其粘度随之降低,强度也相应下降。
采用震压式造型机造型时,型砂的强度就应该低一些。
因为型砂的强度越高,其抵抗变形的能力越强, 韧性就差,为适合这种工艺要求,型砂中的土-水比例就应该适当高一些,一般以控制在3: 2左右。
1.2 粘土混型砂的砂粒结构砂粒之间的粘结,是靠粘土来实现的。
理想的情况是:水和粘土混合充分,成为均匀的粘土膏,粘土膏又均匀地分布在每一砂粒的表面,砂粒之间由其表面的粘土膏彼此相连而形成的粘结桥粘结起来,其间的空隙可使型砂具有必要的透气性。
1.3 粘土湿型砂的混砂效率粘土湿型砂的混砂效率是指:型砂中实际上起粘结作用的膨润土量与其中的活性膨润土含量之比就是混砂效率,混砂效率= 有效膨润土量/活性澎润土含量 X 100 %,由于粘土膏属于半固态性质,粘度很高,难以混配均匀,用于混制粘土湿型砂的混砂机,所需的功率比供砂能力相同的树脂砂混砂机大得多,混砂所需要的时间也更长。
粘土湿型砂应用实例分析及对策
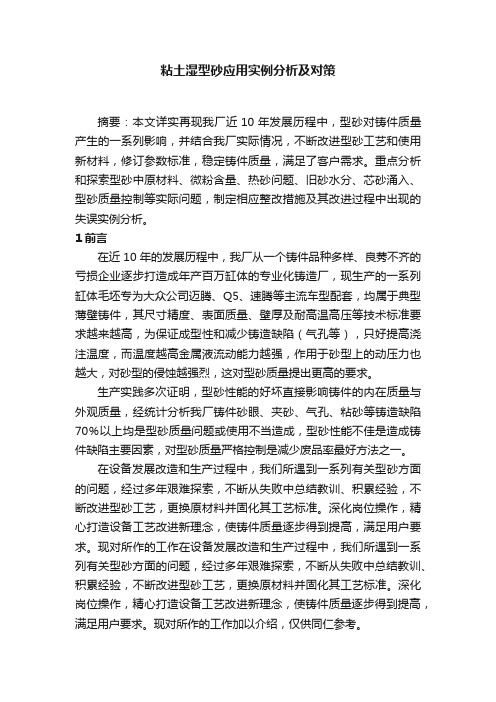
粘土湿型砂应用实例分析及对策摘要:本文详实再现我厂近 10 年发展历程中,型砂对铸件质量产生的一系列影响,并结合我厂实际情况,不断改进型砂工艺和使用新材料,修订参数标准,稳定铸件质量,满足了客户需求。
重点分析和探索型砂中原材料、微粉含量、热砂问题、旧砂水分、芯砂涌入、型砂质量控制等实际问题,制定相应整改措施及其改进过程中出现的失误实例分析。
1前言在近 10年的发展历程中,我厂从一个铸件品种多样、良莠不齐的亏损企业逐步打造成年产百万缸体的专业化铸造厂,现生产的一系列缸体毛坯专为大众公司迈腾、Q5、速腾等主流车型配套,均属于典型薄壁铸件,其尺寸精度、表面质量、壁厚及耐高温高压等技术标准要求越来越高,为保证成型性和减少铸造缺陷(气孔等),只好提高浇注温度,而温度越高金属液流动能力越强,作用于砂型上的动压力也越大,对砂型的侵蚀越强烈,这对型砂质量提出更高的要求。
生产实践多次证明,型砂性能的好坏直接影响铸件的内在质量与外观质量,经统计分析我厂铸件砂眼、夹砂、气孔、粘砂等铸造缺陷70%以上均是型砂质量问题或使用不当造成,型砂性能不佳是造成铸件缺陷主要因素,对型砂质量严格控制是减少废品率最好方法之一。
在设备发展改造和生产过程中,我们所遇到一系列有关型砂方面的问题,经过多年艰难探索,不断从失败中总结教训、积累经验,不断改进型砂工艺,更换原材料并固化其工艺标准。
深化岗位操作,精心打造设备工艺改进新理念,使铸件质量逐步得到提高,满足用户要求。
现对所作的工作在设备发展改造和生产过程中,我们所遇到一系列有关型砂方面的问题,经过多年艰难探索,不断从失败中总结教训、积累经验,不断改进型砂工艺,更换原材料并固化其工艺标准。
深化岗位操作,精心打造设备工艺改进新理念,使铸件质量逐步得到提高,满足用户要求。
现对所作的工作加以介绍,仅供同仁参考。
2型砂材料对铸件质量的影响及其控制标准2.1 选用内蒙优质原砂满足铸件基本质量要求原砂是型砂中主要材料,其性能与参数的变化对铸件质量及生产有直接影响,我们对 SiO2含量、粒度、含泥量、角型系数等参数均有严格要求。
如何控制黏土湿型砂旧砂性能
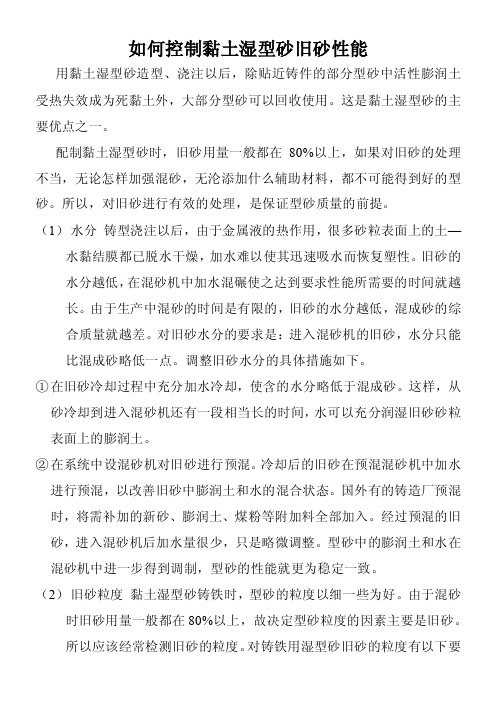
如何控制黏土湿型砂旧砂性能用黏土湿型砂造型、浇注以后,除贴近铸件的部分型砂中活性膨润土受热失效成为死黏土外,大部分型砂可以回收使用。
这是黏土湿型砂的主要优点之一。
配制黏土湿型砂时,旧砂用量一般都在80%以上,如果对旧砂的处理不当,无论怎样加强混砂,无沦添加什么辅助材料,都不可能得到好的型砂。
所以,对旧砂进行有效的处理,是保证型砂质量的前提。
(1)水分铸型浇注以后,由于金属液的热作用,很多砂粒表面上的土—水黏结膜都已脱水干燥,加水难以使其迅速吸水而恢复塑性。
旧砂的水分越低,在混砂机中加水混碾使之达到要求性能所需要的时间就越长。
由于生产中混砂的时间是有限的,旧砂的水分越低,混成砂的综合质量就越差。
对旧砂水分的要求是:进入混砂机的旧砂,水分只能比混成砂略低一点。
调整旧砂水分的具体措施如下。
①在旧砂冷却过程中充分加水冷却,使含的水分略低于混成砂。
这样,从砂冷却到进入混砂机还有一段相当长的时间,水可以充分润湿旧砂砂粒表面上的膨润土。
②在系统中设混砂机对旧砂进行预混。
冷却后的旧砂在预混混砂机中加水进行预混,以改善旧砂中膨润土和水的混合状态。
国外有的铸造厂预混时,将需补加的新砂、膨润土、煤粉等附加料全部加入。
经过预混的旧砂,进入混砂机后加水量很少,只是略微调整。
型砂中的膨润土和水在混砂机中进一步得到调制,型砂的性能就更为稳定一致。
(2)旧砂粒度黏土湿型砂铸铁时,型砂的粒度以细一些为好。
由于混砂时旧砂用量一般都在80%以上,故决定型砂粒度的因素主要是旧砂。
所以应该经常检测旧砂的粒度。
对铸铁用湿型砂旧砂的粒度有以下要求。
①140目筛上的砂粒应在10%~15%之间。
保持较多的细砂,可以减轻铸件表面粘砂,而且会增加砂粒之间黏结桥的数量,从而降低型砂的脆性,避免冲砂缺陷。
此外,这对提高型砂的高温强度和水分凝聚区强度都有好处。
②200目筛、270目筛和底盘上细砂的总和应量少。
这类细砂对改善铸件表面质量的作用不大,却会使混成砂的水分较高,而且会使型砂的透气性降低。
粘土型(芯)砂
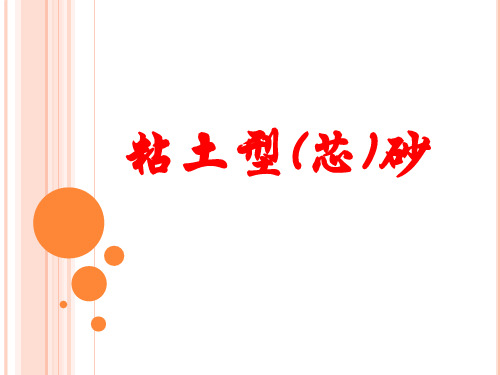
对湿型砂而言,混砂时严格控制加水量是 必要的。工厂中常用的加水量控制办法有 以下几种: ①人工加水。 ②定量水箱、定量水表、时间继电器控制 电磁水阀。边测量、边控制。
28
三、型砂的质量检验和控制
通过型砂的质量检验和宏观控制,不但可了解型砂 是否达到要求的性能,而且还可掌握型砂在使用中 的变化,这样就能及早采取措施,保证型砂符合要 求和保持稳定,保证铸件质量,预防缺陷产生。 试验结果的综合分析 每次取样测出的型砂性能,常在一定范围内波动, 故一次试验结果还不能说明问题,应取每天试验结果 的平均值,才能较好地代表整个型砂系统的状况。
20
铸钢型砂的特点:
为了防止铸件增碳,型砂中不含煤粉和煤粉烧损的残 留物,因而铸钢型砂的含泥量较铸铁型砂低,需水量少 。在同样紧实率下.铸钢型砂的水分低,有利于防止产 生针孔或皮下气孔。水分最好控制在4%-5%(质量分数) 或更低些。 由于型砂中不含煤粉和含泥量低,单一砂和面砂的透 气性容易偏高。单一砂的透气性最好不超过120,面砂 的透气性还应更低才能生产出表面光洁无机械粘砂的铸 件。为此,可选用粒度15Q(或2lQ)的硅砂,不宜使用粒 度为30Q的粗硅砂。
4.高密度造型型砂
(1)高密度造型特点 高密度造型是指提高造型紧实力制得较高紧实程度或较高 密度砂型的造型方法而言。过去高密度造型只指各种高压造 型。近十多年来,高速的冲击造型包括动力(机械)冲击和气 流冲击造型得到了越来越广泛的开发相应用,也属高密度造 型。 一般认为,压实比压高到0.7MPa以上称为高压造型,用 此法生产出来的铸件不仅尺寸精度高,表面粗糙度大大改善 ,而且能使铸件更加致密,力学性能更高,加工余量减少, 铸件质量减轻,劳动条件改善,生产率大大提高等。 高压造型中,由于其不良的砂型强度分布;另外,随着压 实比压的提高,还可能引起“水爆炸”,从而会出现型壁移 动,并使铸件产生气孔、局部表面粗糙和机械粘砂、甚至整 24 个铸件表面粘砂等缺陷 。
膨润土在粘土湿型砂中应用的几个应注意的控制要点

膨润土在粘土湿型砂中应用的几个应注意的控制要点膨润土在铸造中主要用于粘土粘结砂中,因为膨润土具有粘结力强、可塑性高、脱膜好、透气性优、高温湿态条件下物理化学性能稳定等特点。
粘土粘结砂作造型材料生产铸件,本是历史悠久的工艺方法,在各种化学粘结砂蓬勃发展的今天,粘土湿型砂仍是最重要的造型材料,其适用范围之广,耗用量之大,是任何其他造型材料都不能与之比拟的。
近代的高压造型、射压造型、气冲造型、静压造型及无震击真空加压造型等新工艺,也都是以使用粘土湿型砂为前提的,粘土湿型砂适应造型条件的能力极强。
现今,随着科学技术快速发展,各产业部门对铸件的需求不断增长,同时,对铸件品质的要求也越来越高。
也使粘土湿型砂面临许多新的问题,促使我们对粘土湿型砂的研究不断加强、认识不断深化。
前不久,笔者走访了国内一些铸造单位,发现铸件的废品较多,特别是一些小规模铸造单位,问题主要是有气孔等缺陷。
产生问题主要在生产新铸件、换其他厂家膨润土和长期使用旧砂期间。
有必要对膨润土和旧砂的控制要点进行一下强调。
1.膨润土和膨润土粘土粘结砂中的,作用及变化,铸造用膨润土主要有钠基膨润土和钙钠膨润土两类,钠基膨润土是由天然钠基膨润土或人工钠化膨润土加工而成,以其复用性好和湿压强度高而受铸造行业欢迎。
因具有良好的可塑性,可遏止铸件夹砂、结疤、掉块、砂型塌方等现象,加之成型性强、型腔强度高,便于金属行业浇铸湿态或干态型模,是精密铸件首选的型砂粘结剂。
钙钠膨润土由天然基钙钠膨润土加工它以实用和铸件清砂便捷是轻型铸件普遍采用的型砂粘结剂。
而成,而受用户欢迎。
和其他黏结剂相比,膨润土有一个重要的特点,就是它具有一定的耐热能力。
只要加热温度不太高,脱除了自由水的膨润土只要加水,仍能恢复粘能力。
膨润土的粘结能力只有在加水以后才能表现出来。
膨润土失去粘结能力,也与它的脱水有关。
到目前为止,认为膨润土中的水分有3种形态:一种水是自由水,即膨润土颗粒吸附的水,加热到100℃以上,就可脱除自由水,脱除了自由水的膨润土,粘结能力不受影响;二种水是牢固结合水,110℃下长时间加热,膨润土可完全脱除自由水,但不会脱除牢固结合水。
5. 第1章 湿型砂解析
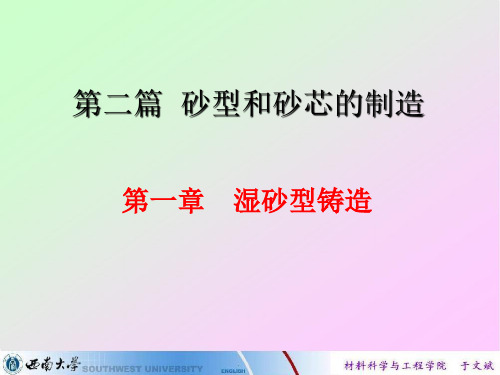
• (3)其它方法 • 激热性能试验法: • 圆饼形型砂试样,开V 形槽,在13000C,的 高温下烘烤。观测型 砂表面开始脱落的时 间,当时间脱落或者 开裂下垂1mm的时间越 长,说明抗夹砂结疤 能力越好。
• 2.7 发气量和有效煤粉含量(铸铁用湿型砂) • (1)目的:防止机械粘砂 • (2)煤粉及附加物可防止机械粘砂的机理: • 浇注烘烤→大量挥发分→分解反应→砂粒表面沉积形成光 泽碳→防止机械粘砂,提高表面光洁度。
(3)测量 方法一:采用测定型砂发气性的办法,将定量待测样 品在密闭系统中加热,测定气体的容积或压力,或称 量残留物的质量,判断发气量大小。 方法二:称取经过干燥的型砂,盛入小舟→推入 850℃管式加热炉加热→产生的气体经冷凝进入带刻 度的玻璃管中→测量大气压力下型砂的发气体积。
小 结
• • • • 1 2 3 4 了解湿型铸造的特点; 掌握型砂的七个方面的性能; 熟悉型砂性能对铸造质量的影响; 了解型砂性能的测试方法。
主要缺点:需烘干设备,燃料,吊车周期,砂箱寿命, 成本增加,生产率降低,落砂比较困难,灰尘。 应用范围:表面质量要求高,或结构特别复杂的单件
或小批生产及大型、重型铸件。
第二节 湿型砂性能、检测及方法
一、型(芯)砂应具备的性能
(1)造型、制芯和合型阶段对型砂性能的要求。
1.湿度:湿态强度和韧性,粘土砂须含适量水分。 2.流动性:型(芯)砂沿模样(或芯盒表面)和砂粒 间相对移动的能力。 3.强度:型砂、芯砂抵抗外力破坏的能力。 4.可塑性:型(芯)砂在外力作用下变形并保持形状 的能力。
• 韧性的测定 • 落球法:标准抗压试样、 φ50mm,510克钢球,12.7mm 的筛。 • 破碎指数:留在筛网上的型 砂质量占试样质量的比值。 • 表示在冲击条件下的韧性 • 高,表示型砂的起模性好, 过高,流动性差,不够致密。
湿型粘土砂应用实例分析及对策(1)

时再进行随流孕育。
X)Y钱立,王峰+灰铸铁、球墨铸铁中的微量杂质元素XZY+现代铸铁,
(5)采用合理的铸造工艺和浇注温度。 (')要加强各生产环节的管理,严格执行工 艺规程。
$%!5,(%$):/"(//+ X5Y程凤军,高顺,莫俊超,等+球墨铸铁中碎块状石墨的形成原因
在近 !% 年的发展中,笔者公司从一个铸件
收稿日期:$%#"("!($'
修定日期:$%!"(%)(!%
作者简介:王艳辉(!*"*+%*(),男,汉族,吉林长春人,毕业于吉林
工学院机电专业,铸造工程师,主要从事铸造材料应用及铸件质
量打造成年产 百万件缸体的专业化铸造厂,现生产的一系列缸 体铸件专为大众公司迈腾、&'、速腾等主流车型 配套,均属于典型薄壁铸件,其尺寸精度、表面质 量、壁厚及耐高温高压等技术标准要求越来越
及防止措施XZY+现代铸铁,$%!',(%)):$*()5+ X'Y巩济民+欧洲不同时期铸铁熔炼车间布置给我们的启示XZY+现
代铸铁,$%!",(%!):!*($"+
参考文献
X"Y万晓民,齐浩,苏培强,等+制动卡钳铸件皮下气孔缺陷的防止
X!Y万仁芳+浅谈近年来铸铁件的发展XZY+现代铸铁,$%!5,(%)):
XZY+现代铸铁,$%!",(%!):"*(0)+
!'($5+
X$Y巩济民,万仁芳,于永来+从 $%!5 年北京展会看我国铸造企业 的发展XZY+现代铸铁,$%!',(%!):!*($$+
影响黏土湿型砂湿压强度的因素和控制

影响黏土湿型砂湿压强度的因素有哪些?应如何控制?
影响黏土湿型砂湿压强度的因素主要有:
①原砂。
在黏土含量一定的情况下,原砂越细,越不均匀,则湿压
强度越高。
②黏土。
水分适当时,黏土量增加,则湿压强度提高;但膨润土增
加到一定程度后容易形成团块,强度不再增高。
膨润土的湿压强度比普通黏土高,钙膨润土比钠膨润土湿压强度高。
③水分。
黏土一定时,随着水分的增加,湿压强度先是增加,达到
最高值后,逐渐下降。
为获得湿压强度的最高值,水对黏土的比值(简称水土比),固定不变,但水土比的具体数值随黏土的品种而异。
对大多数黏土而言:水/(水+黏土)=20%。
④混砂工艺。
混砂时间必须充分,才可获得较高湿强度。
⑤紧实度。
紧实度提高,型砂的湿强度也随之提高,但有一定限度。
一般生产中湿压强度应控制在:手工造型80~150kPa,普通机器造型(压实震击)60~150kPa,高密度造型(高压、气冲、射压、静压)120~180kPa。
粘土砂铸造缺点分析

一.概述粘土砂是以粘土(陶土)作粘结剂的型(芯)砂。
粘土砂造型由于其成本低廉,适合于批量大规模生产,所以目前仍然作为铸件生产的最主要方式。
粘土砂旧沙由于在循环使用过程中各组份的热分解,发生物理性能的变化,如未经再生就加以使用,将使型砂质量不稳定。
据统计铸件废品率中30~40%为型砂质量引起,因此型砂质量的控制在粘土砂造型中起十分重要的作用。
随着目前对铸件要求的提高,对型砂质量的要求也越来越高。
二.粘土砂造型中几种与型砂质量有关的常见缺陷。
1.气孔、浇不到、冷隔粘土砂型砂的组成绝大部分为旧砂(85~95%),由于旧砂循环使用过程中经过反复热冲击,一些组分会出现热分解,发生物理性能的变化:a.粘土在砂型温度高于500度的区域,膨润土晶体结构受到完全破坏,就变成没有湿态粘结力的无效粘土以粉尘状态存在与旧砂中,成为旧砂泥份中的一种;b.煤粉炭化成为枯化物;c.不稳定的砂粒(包含杂质)会粉化。
这些衍生物共同成为旧砂的微粉。
微粉含量超过一定的限度,微粉堵塞砂砾空隙就会造成型砂透气性差。
而且无效粘土吸水能力比有效粘土强,从有效粘土中夺取有效水分,因此当无效粘土含量较多时,达到调匀所需的加水量就得增加。
加大了型砂加水量,在某种程度上也就加大了型砂的发气量。
由于发气量增加而透气性减少,浇铸时液体所收的阻力增大,必然导致侵入性气孔、浇不到、冷隔等缺陷的形成。
2.表面光洁度差(包括砂眼、毛刺、夹砂结疤等)大量的无效粘土造成型砂的抗拉强度差、韧性低、透气性差。
增大型砂的脆性,使型砂易塌箱、掉砂,在浇铸时砂粒容易掉落形成砂眼、毛刺、夹渣结疤等缺陷,进而影响铸件质量。
3.粘砂无效粘土(死黏土)部分约占整个砂型重的2~5%,无效粘土的一部分在高温作用下包裹在砂粒表面上,烧结形成一层牢固的膜,不能用水洗掉,成为砂粒的一部分,这层膜又称为惰性膜。
型砂经过无数次循环混制和浇铸受热,惰性膜将多层重叠包裹,这个过程又叫鱼卵石化现象。
适当的鱼卵石化降低了石英含量,减轻型砂的热膨胀性,减少膨胀类缺陷。
粘土湿型砂所有优缺点及几种常用的附加材料

粘土湿型砂所有优缺点及几种常用的附加材料黏土湿型砂是铸造行业中人人都很熟悉的事物,正是因为我们对它太“熟悉”了,铸造行业不少同仁反而是‘与之久处而不知其香’,对它的一些特性只知其梗概,而未深究其精微,因而,虽然天天离不了它,却不能运用自如,充分发挥它的作用。
一、黏土湿型砂优点1、使用历史最悠久的造型材料从开创人类文明的‘青铜时代’起,我们就离不了黏土湿型砂,由于没有记载可考,不能确切地说出其应用的最早年代,认为其有5000年左右的历史,可能不会是夸大其词。
当然,早期的黏土湿型砂与目前所用的差别很大,而且所用主要是天然的黏土黏结砂,采掘以后,加水混拌后就可以使用。
这种黏土砂中的黏土主要是高岭土质的耐火黏土,一个典型的例子就是我国南京附近出产的六合红砂,以前一度真可谓是闻名遐迩,直到20世纪50年代初期,我国第一个五年计划期间,不少手工作业的铸造厂仍然使用。
18世纪后期,简单的造型机问世以后,逐渐强化了对型砂性能的要求。
随着造型机不断地改进、优化,19世纪初期又催生了混砂机,加速了由天然黏土黏结砂到用混砂机配制的合成砂的转变。
用混砂机配制的合成砂推广应用以后,为了适应不断提高造型机的生产效率、提高铸件质量的要求,莫来石质膨润土的应用,在改善黏土湿型砂的质量方面的作用,应该说是至关重要的、具有划时代的意义。
目前,世界各国所用的黏土湿型砂全都都是加膨润土配制的膨润土的应用至少有一百多年了,但是,我们对膨润土的认知还很不够,今后必须不断深化对它的了解。
2、黏土湿型砂性能控制的空间宽阔,对各种造型方式的适应性很好粘土湿型砂,有较高的湿强度,在舂实过程中,其流动性较差,使砂型紧实所需的能量较多,但是,其适应各种造型方式的能力很好。
从最原始的手工造型,到各种现代化的自动造型生产线,用黏土湿型砂作为造型材料,都有令人满意的效果。
黏土湿型砂对各种舂实方式,如手工紧实、舂实、震实、压实、抛砂、射砂、气冲、静压、等造型工艺,都能适应。
1.2 湿砂型
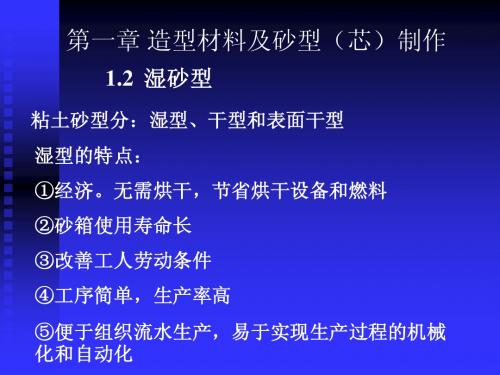
图1.10热湿拉 强度的测定 方法示意图
1.2.2 湿型砂性能要求及检测原理 5. 起模性、韧性和破碎指数 6. 抗夹砂结疤类缺陷的能力
图1.11 热压应力测定示意图 1-固定托架; 2-可动托架; 3-压杆; 4-水浴; 5-测量箱; 6-氧-乙炔烧嘴
1.2.2 湿型砂性能要求及检测原理 5. 起模性、韧性和破碎指数 6. 抗夹砂结疤类缺陷的能力 7. 发气量和有效煤粉含量 造型材料的发气性对气体缺陷的产生有重要影 响。发气性是用试料在高温下产生气体的 量、发气速度和发气时间来表示的。 如用秒表计时,间隔一定时间读一次发气量值, 直至发气量不再增加,即可得知试料的发 气速度和析出气体的时间。
1.2.3 湿型砂制备及质量控制 1.湿型砂性能和配方特点 2.旧砂特性及其处理
经济,环境污染,自然资源 旧砂的变化: ①部分粘土成为死粘土 ②砂粒变粗-一部分死土在高温作用下包在砂粒表面,烧结一 层牢固的膜,即惰性膜,且多层包裹。 ③煤粉等附加物燃烧挥发,成为失效煤粉,并使泥分增加。 ④混入芯砂、铁豆等夹杂物。
1.2.2 湿型砂性能要求及检测原理 5. 起模性、韧性和破碎指数 6. 抗夹砂结疤类缺陷的能力 7. 发气量和有效煤粉含量 有效煤粉含量用于表征铸铁件用湿型砂的抗机械 粘砂能力。
图1.12 发气量测定原理示意图 1-瓷舟; 2-石英管; 3-管式加热炉;4-冷凝管; 5-量管; 6-平衡瓶
1.2.2 湿型砂性能要求及检测原理 1. 水分、最适宜干湿程度(适宜湿度)和紧实率 2. 透气性 :型砂能让气体透过而逸出的能力 3. 湿态强度 4. 流动性 5. 起模性、韧性和破碎指数 6. 抗夹砂结疤类缺陷的能力 7. 发气量和有效煤粉含量
1.2 湿砂型
1.2.1 湿型砂用原材料及质量要求 1. 原砂 2. 粘土 ①分类 ②粘土的表面电荷和交换性阳离子 ③粘土的吸附水分及湿态粘结机理 ④粘土对型砂性能的影响
浅谈粘土湿型砂性能指标及科学管理
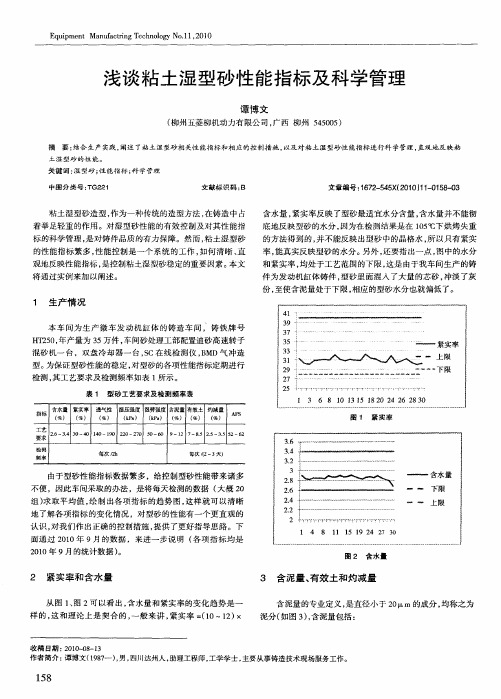
土 湿 型砂 的性 能 。
关键 词 : 型砂 ; 能 指 标 ; 学 管 理 湿 性 科 中 国分 类 号 :G2 1 T 2 文 献标 识 码 : B
交 童 编 号 :6 2 5 5 ( 0 0J1 O 5 — 3 17— 4 X 2 1 一 18 0 1
粘土湿型砂造 型 , 作为一种传 统的造型方法 , 在铸造 中 占 着举足轻重 的作用 。对湿 型砂性能的有效控制及对其性能指 标的科学 管理 , 是对 铸件品质 的有力保障。然而 , 粘土湿型砂
对 型砂 性 能 和 铸 件 品 质 将 起 到 很好 的 帮 助 ,所 以选 用 优 质 的
灼 减 量 来 测 量 有 效 煤 粉 含 量 的 ,也 有 厂 家 通 过 测 定 发 气 量 来 反映 ) ; ( ) 效 组 分— — 经 浇 注 烧 损 的死 膨 润 土 和 死 煤 粉 , 润 2 无 膨 土 、 粉 、 砂 里 的灰 分 , 及 细 小 的 砂粒 。 煤 新 以
面通 过 2 1 0 0年 9 的 数 据 ,来 进 一 步 说 明 ( 项 指 标 均 是 月 各
21 00年 9月的统计数据 ) 。
图 2 含 水 量
2 紧实 率和含水 量
从 图 1图 2可 以看 出 , 、 含水量和紧实率的变化趋势是 一 样的 , 这和理论 上是契合 的 , 一般来讲 , 紧实率 = 1 ( 0~1 ) 2X
18 5
《 装备制造技术) 00 ) 1 年第 1 期 2 1
( ) 效 组 分— — 有 效 膨 润 土 、 效 煤 粉 ( 车 问 是 通 过 1有 有 本
为 微 车 发 动 机 铸 件 , 质 量 相 对 较 小 , 且 砂 箱 较 大 , 铁 比 净 并 砂 为 7 1 经 测 量 , 润土 烧 损 为 05 煤 粉 烧损 为 01 % , 加 :, 膨 .%, . 3 补 量 相 当之 少 , 与我 们 的 砂 铁 比大 、 用 优 质 的膨 润 土 和 煤 粉 这 选 有 很 大 的关 系 。 烧 损 少 , 意 味 着 型 砂 里 面 的无 效 灰 分 少 , 就 这
黏土湿型砂的性能要求

黏土湿型砂的性能要求为了制造出合格的砂型和砂芯,黏土湿型砂应具有良好的常温工艺性能,如湿度、流动性、强度、可塑性与韧性、不粘模性等。
液态合金浇入铸型后,与型腔表面砂层之间发生着机械作用、热作用和化学作用。
机械作用是指液态合金充填过程中对腔壁的动压力和静压力,合金液凝固收缩时对铸型产生的压应力。
热作用是由于合金液与铸型腔存在着很大的温差,型腔壁被强烈加热,靠近合金液的型腔表面加热特别严重,局部甚至开裂或烧结。
化学作用是液态合金及其氧化物与型腔表面的砂层发生化学反应。
因此黏土湿型砂应具有良好的高温性能,如耐火度、发气性、热膨率、溃散性、退让性等。
下面分别简述这些主要性能。
1)湿度(水分)为了得到所需的可塑性、韧性和湿态强度,黏土湿型砂必须含有适量水分。
生产现场判断型砂湿度有以下几种方法:有丰富经验的混砂和造型工人常根据手捏型砂是否容易捏成闭和是否粘手来判断型砂的干湿程度;还可根据捏紧的动作中型砂是否柔软和变形情况来判断型砂的可塑性;根据手指掐碎砂团时用力大小判断型砂的湿强度是否合适。
如果用手捏砂时,只有潮的感觉,不觉得沾手,且柔和,印在砂团上手指痕迹清晰,那这样的型砂干湿度就比较合适。
2)流动性型(芯)砂在外力或自重作用下,沿模样(或芯盒表面)和砂粒间相对移动的能力称为流动性。
流动性好的型砂可形成紧实度均匀、无局部疏松、轮廓清晰、表面光洁的型腔,这有助于防止机械粘砂,获得光洁铸件。
此外,还能减轻型砂紧实时的劳动强度,提高生产率和便于实现造型、制芯过程的机械化。
3)强度型砂必须具备一定的强度以承受各种外力的作用,如果强度不足,在起模、搬运砂型、下芯、合型等过程中,铸型有可能破损塌落;浇注时可能承受不住金属液的冲刷和冲击,冲坏砂型而造成砂眼缺陷,或者造成胀砂(铸件肿胀)或跑火(漏铁液)等现象。
但是强度也不宜过高,因为高强度的型砂需要加入更多的黏土,不但增加了水分需求量,降低了砂型透气性,还会使铸件的生产成本增加,而且给混砂、紧实砂型和落砂等工序带来困难。
粘土湿型砂特点及缺陷分析与控制
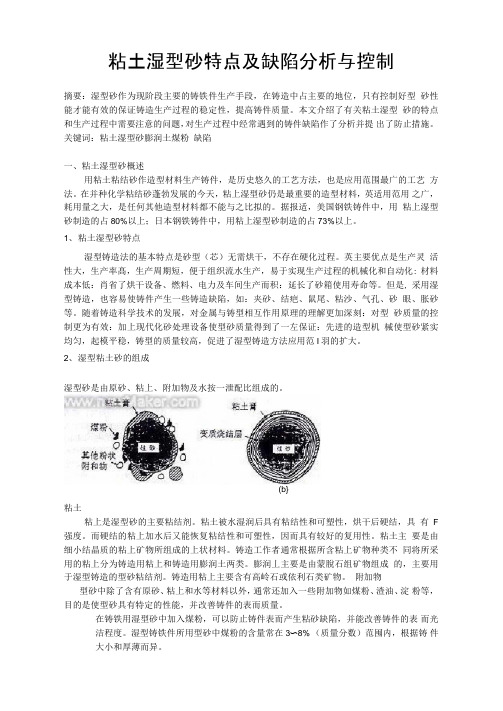
粘土湿型砂特点及缺陷分析与控制摘要:湿型砂作为现阶段主要的铸铁件生产手段,在铸造中占主要的地位,只有控制好型砂性能才能有效的保证铸造生产过程的稳定性,提高铸件质量。
本文介绍了有关粘土湿型砂的特点和生产过程中需要注意的问题,对生产过程中经常遇到的铸件缺陷作了分析并提出了防止措施。
关键词:粘土湿型砂膨润土煤粉缺陷一、粘土湿型砂概述用粘土粘结砂作造型材料生产铸件,是历史悠久的工艺方法,也是应用范围最广的工艺方法。
在并种化学粘结砂蓬勃发展的今天,粘上湿型砂仍是最重要的造型材料,英适用范用之广,耗用量之大,是任何其他造型材料都不能与之比拟的。
据报适,美国钢铁铸件中,用粘上湿型砂制造的占80%以上;日本钢铁铸件中,用粘上湿型砂制造的占73%以上。
1、粘土湿型砂特点湿型铸造法的基本特点是砂型(芯)无需烘干,不存在硬化过程。
英主要优点是生产灵活性大,生产率髙,生产周期短,便于组织流水生产,易于实现生产过程的机械化和自动化: 材料成本低:肖省了烘干设备、燃料、电力及车间生产而积:延长了砂箱使用寿命等。
但是, 采用湿型铸造,也容易使铸件产生一些铸造缺陷,如:夹砂、结疤、鼠尾、粘沙、气孔、砂眼、胀砂等。
随着铸造科学技术的发展,对金属与铸型相互作用原理的理解更加深刻:对型砂质量的控制更为有效:加上现代化砂处理设备使型砂质量得到了一左保证:先进的造型机械使型砂紧实均匀,起模平稳,铸型的质量较高,促进了湿型铸造方法应用范I羽的扩大。
2、湿型粘土砂的组成湿型砂是由原砂、粘上、附加物及水按一泄配比组成的。
(b}粘土粘上是湿型砂的主要粘结剂。
粘土被水湿润后具有粘结性和可塑性,烘干后硬结,具有F 强度。
而硬结的粘上加水后又能恢复粘结性和可塑性,因而具有较好的复用性。
粘土主要是由细小结晶质的粘上矿物所组成的上状材料。
铸造工作者通常根据所含粘上矿物种类不同将所采用的粘上分为铸造用粘上和铸造用膨润土两类。
膨润丄主要是由蒙脫石组矿物组成的,主要用于湿型铸造的型砂粘结剂。
粘土湿型砂

粘土湿型砂及其质量控制一粘土湿型砂的特点湿型砂主要由原砂、膨润土、附加物(煤粉、淀粉等)和水组成。
造型过程中,型砂捣实并达到一定紧实度后,形成砂型。
粘土湿型砂的结构示意图通常使用的硅砂,来源广,便宜,耐火度高。
另一方面,原砂砂粒能为砂型(芯)提供众多孔隙,保证型、芯具有一定的透气性,在浇注时,使型内产生的大量气体顺利逸出。
湿型砂按在造型时的情况,可分为面砂、背砂和单一砂。
二粘土湿型砂用的原材料1 硅砂1)硅砂种类及其SiO2含量天然硅砂河砂、湖砂、、海砂(牟平)、风积砂(大林、围场)。
人工硅砂由硅石岩、硅砂岩采矿、清洗、破碎、筛选加工而成。
硅砂的SiO2含量及不同用途铸铁用砂SiO2≥85%;铸钢用砂SiO2≥95%。
2)石英的结构转变特性石英为硅氧四面体,相变温度:573℃时产生体积膨胀,易夹砂。
870℃时也产生相变,故烧过此温度后,用于复膜砂。
3)硅砂的杂质长石、云母、氧化铁、碳酸盐及粘土,均降低(1)耐火度。
4)硅砂的含泥量原砂含有的直径小于0.02mm的颗粒,其质量分数称为原砂的含泥量。
5)硅砂的粒度和表示方法例如:三筛>75%,40/70;四筛>85%,50/1406)硅砂的颗粒形状和角形因数颗粒较圆(角形因数小)的砂粒,型砂的流动性好,紧实密度较高,透气性好。
2膨润土粘土的主要成分是水化硅酸铝(mAl2O3.SiO2.xH2O)。
晶体结构有两层型(高岭土,即普通粘土),三层型(蒙脱石,即膨润土)。
和普通粘土相比,膨润土有较大的吸水膨胀性、胶体分散性、、吸附性、离子交换性和湿态粘结性能。
故多用于湿型砂。
膨润土在500-700℃时失去结构水,加热到800℃以上时,晶格破坏,失去粘结作用。
膨润土分钙基膨润土和钠基膨润土,钠基膨润土在水分较高时仍有较好的强度,即具有较高的热湿拉强度和抗夹砂能力。
铸造用膨润土按工艺试样湿压强度值分为4级,,热湿拉强度值也分为4级。
(2)各种牌号的铸造用膨润土,其吸附亚甲基蓝量每100克至少应在20克以上;水分不大于12%,膨润土的95%应通过200号铸造用试验筛。
- 1、下载文档前请自行甄别文档内容的完整性,平台不提供额外的编辑、内容补充、找答案等附加服务。
- 2、"仅部分预览"的文档,不可在线预览部分如存在完整性等问题,可反馈申请退款(可完整预览的文档不适用该条件!)。
- 3、如文档侵犯您的权益,请联系客服反馈,我们会尽快为您处理(人工客服工作时间:9:00-18:30)。
粘土湿型砂特点及缺陷分析与控制摘要:湿型砂作为现阶段主要的铸铁件生产手段,在铸造中占主要的地位,只有控制好型砂性能才能有效的保证铸造生产过程的稳定性,提高铸件质量。
本文介绍了有关粘土湿型砂的特点和生产过程中需要注意的问题,对生产过程中经常遇到的铸件缺陷作了分析并提出了防止措施。
关键词:粘土湿型砂膨润土煤粉缺陷一、粘土湿型砂概述用粘土粘结砂作造型材料生产铸件,是历史悠久的工艺方法,也是应用围最广的工艺方法。
在各种化学粘结砂蓬勃发展的今天,粘土湿型砂仍是最重要的造型材料,其适用围之广,耗用量之大,是任何其他造型材料都不能与之比拟的。
据报道,美国钢铁铸件中,用粘土湿型砂制造的占80%以上;日本钢铁铸件中,用粘土湿型砂制造的占73%以上。
1、粘土湿型砂特点湿型铸造法的基本特点是砂型(芯)无需烘干,不存在硬化过程。
其主要优点是生产灵活性大,生产率高,生产周期短,便于组织流水生产,易于实现生产过程的机械化和自动化;材料成本低;节省了烘干设备、燃料、电力及车间生产面积;延长了砂箱使用寿命等。
但是,采用湿型铸造,也容易使铸件产生一些铸造缺陷,如:夹砂、结疤、鼠尾、粘沙、气孔、砂眼、胀砂等。
随着铸造科学技术的发展,对金属与铸型相互作用原理的理解更加深刻;对型砂质量的控制更为有效;加上现代化砂处理设备使型砂质量得到了一定保证;先进的造型机械使型砂紧实均匀,起模平稳,铸型的质量较高,促进了湿型铸造方法应用围的扩大。
2、湿型粘土砂的组成湿型砂是由原砂、粘土、附加物及水按一定配比组成的。
2.1粘土粘土是湿型砂的主要粘结剂。
粘土被水湿润后具有粘结性和可塑性,烘干后硬结,具有干强度。
而硬结的粘土加水后又能恢复粘结性和可塑性,因而具有较好的复用性。
粘土主要是由细小结晶质的粘土矿物所组成的土状材料。
铸造工作者通常根据所含粘土矿物种类不同将所采用的粘土分为铸造用粘土和铸造用膨润土两类。
膨润土主要是由蒙脱石组矿物组成的,主要用于湿型铸造的型砂粘结剂。
铸造用粘土主要含有高岭石或依利石类矿物。
2.2附加物型砂中除了含有原砂、粘土和水等材料以外,通常还加入一些附加物如煤粉、渣油、淀粉等,目的是使型砂具有特定的性能,并改善铸件的表面质量。
在铸铁用湿型砂中加入煤粉,可以防止铸件表面产生粘砂缺陷,并能改善铸件的表面光洁程度。
湿型铸铁件所用型砂中煤粉的含量常在3~8%(质量分数)围,根据铸件大小和厚薄而异。
煤粉的代用材料,包括固体沥青或其乳化液,渣油或煤焦油或其乳合液,膨润土与沥青或其他石油衍生物的混合粉末或浆液,固态或水中分散的合成聚合物和淀粉等。
铸铁面砂中淀粉含量(按质量分数计)一般为0.5%左右。
2.3原砂铸造生产中使用量最大的原砂是以石英为主要矿物成分的天然硅砂。
天然硅砂资源丰富,分布极广,易于开采,价格低廉,能满足铸造上多数情况的要求。
一方面,原砂为砂型(芯)提供了必要的耐高温金属液顺利冲型、在铸型中冷却、凝固并得到所要求形状和性能的铸件。
另一方面,原砂粒度为型砂提供众多空隙,保证砂型具有一定透气性,在浇注过程中,使型腔受热极剧膨胀的气体和铸型本身产生的大量气体能顺利逸出二、旧砂的处理1、旧砂概述用粘土湿型砂造型,浇注以后,除贴近铸件的部分型砂中活性膨润土受热失效成为死粘土外,大部分型砂可以回收使用。
这是粘土湿型砂的主要优点之一。
配制粘土湿型砂时,旧砂用量一般都在90%以上,如果对旧砂的处理不当,无论怎样加强混砂,无论添加什麽辅助材料,都不可得到好的型砂。
所以,对旧砂进行有效的处理,是保证型砂质量的前提。
2、旧砂温度的控制热砂问题,已被公认为粘土湿型砂铸造必须面对的最大问题。
型砂温度太高,铸件容易产生夹砂、表面粗糙、冲砂、气孔等缺陷。
热砂对铸件质量的负面影响,主要由于以下几个方面:1)由于热砂使水分蒸发,混砂时无论怎样注意,也难以控制型砂的性能;2)将热型砂送往造型机的过程中,由于水份损失,型砂性能改变,造型时实际上用的型砂,其性能与混砂时控制的性能差别很大;3)造型时,热型砂的水分容易在模样表面上凝结,型砂粘模;4)合型后,热砂的水分蒸发,凝结在冷的芯子上,会使芯子的强度降低,铸件也易于产生气孔;5)如果旧砂要贮存在砂斗中备用,则热砂容易粘附在砂斗壁上。
严重时,砂斗四周堵满了型砂,只剩中间一个孔洞,使系统中的型砂只有一部分周期使用,这部分型砂周转快、温度又会进一步提高,使热砂问题更加严重。
多高温度的砂算是热砂?判断热砂的温度界限,是看其是否使混砂、造型及铸件质量方面出现问题。
对此,许多研究者从各个方面进行了研究,普遍认为:要保证型砂的性能稳定,温度必须保持在50℃以下。
使型砂冷却,最有效的办法是加水,但是,简单的加水,效果是很差的。
一定要吹入大量空气使水分蒸发,才能有效地冷却。
以下,给出一个简略的计算比较:型砂的比热大致是:9.22×102J/kg·℃,水的比热是:4.19×103J/kg·℃,水的蒸发热是:2.26×106J/kg,1吨砂中加20℃的水10kg(加水1%),使其温度升到50℃,所能带走的热量为4.19×103 ×10×30,即12.57×105J。
1吨砂温度降低1℃,需散热9.22×102×1000 J,即9.22×105 J。
所以,在旧砂中加水1%,只能使温度降低24.5℃。
使1吨砂中的水分蒸发1%(10kg),能带走的热量为2.26×107J,却可使砂温降低24.5℃。
以上的分析表明:简单地向皮带机上加水或向砂堆洒水,冷却效果是很差的。
即使加水后向砂表面吹风,也不能有多大的改善。
加水后,要使水在型砂中分散均匀,然后向松散的砂吹风,使水分迅速蒸发,同时将蒸汽排除。
目前,型砂冷却装置的品种、规格很多,主要有冷却滚筒、双盘冷却器和冷却沸腾床等,都是利用水分蒸发冷却型沙。
其中,冷却沸腾床效果较好。
3、旧砂水分的控制几乎所有的铸造厂都检查和控制混成砂的水分,但是,对于严格控制旧砂水分的重要性,很多铸造厂的领导和技术人员还缺乏足够的认识。
进入混砂的旧砂水分太低,对混砂质量的影响可能并不亚于砂温过高。
试验研究和经验都已证明,加水润湿干膨润土比润滑湿膨润土难得多。
型砂中的膨润土和水,并非简单的混在一起就行,要对其加搓揉,使之成为可塑状态。
这就像用土和水制器一样,将水和土和一和,是松散的,没有粘接能力;经过搓揉和摔打,使每粒土都充分吸收了水分,就成为塑性状态,才可以成形,制成器毛坯。
铸型浇注以后,由于热金属的影响,很多砂粒表面上的土-水粘结膜都脱水干燥了,加水使其吸水恢复塑性是很不容易的。
旧砂的水分较低,在混砂机中加水混碾使之达到要求性能所需要的时间就越长。
由于生产中混砂的时间是有限的,旧砂的水分越低,混成砂的综合质量就越差。
目前,各国铸造工作者已有了这样一种共识:进入混砂机的旧砂,水分只能比混成砂略低一点。
较好的做法是:在旧砂冷却过程中充分加水冷却后所含的水分略低于混成砂。
这样,从砂冷却到进入混砂机还有一段相当长的时间,水可以充分润湿旧砂砂粒表面上的膨润土。
更好的做法是:在系统中设混砂机对旧砂进行预混,冷却后的旧砂在预混混砂机中加水进行预混,以改善旧砂中膨润土和水的混合状态。
国外,有的铸造厂预混时,将需补加的新砂、膨润土、煤粉等附加料全部加入。
的新伟祥铸造公司,用德国制造的EiRich混砂机预混。
经过预混的旧砂,进入混砂机后加水量很少,只是略微调整。
型砂中的膨润土和水在混砂机进一步得到调制,型砂的性能就更为稳定一致。
4、旧砂的粒度对于用粘土湿型砂制造的铸铁件,型砂的粒度以细一些为好。
由于混砂时旧砂用量一般都在90%以上,决定型砂粒度的因素主要是旧砂。
新砂加入量很少,不可能靠加入新砂来改变型砂的粒度。
所以,应该经常检测旧砂的粒度。
检测粒度时,取样后先清洗除去泥分(可用测定含泥量时剩下的砂样),烘干后筛分。
对粒度有以下两点要求:1)140目筛上的砂粒应在10-15%之间。
保持较多的细砂,可以减轻铸件表面粘砂。
而且,会增加砂粒之间粘结桥的数量,从而降低型砂的脆性,避免冲砂缺陷。
此外,这对提高型砂的温强度、干强度和水分迁移后增湿层强度都有好处。
2)200目筛、270目筛和底盘上细砂的总和应尽量地少。
这样的细砂对改善铸件表面质量的作用不大,却会使混成砂的水分较高,而且会使型砂的透气性降低。
细砂的总和一般应少于4%。
5、吸水细粉的含量吸水细粉中主要是死粘土,还包括焦化了的煤粉细粒和其他细粉。
吸水细粉的含量并非越低越好,最好将其控制在2-5%之间。
吸水细粉,混砂时会和膨润土争夺水分,使混成砂达到可紧实性目标值所需的水分增高。
但是,据目前大家的认识,吸水细粉的吸水能力比膨润土强,而保持水分的能力却低于膨润土。
因此,在型砂中加水量略有不当时,吸水细粉对型砂性能有一定的“微调和稳定”作用。
水分高时,细粉首先吸水,膨润土所吸收水可较稳定一致;混成砂在输送过程中水分蒸发时,吸水细粉所吸的水先蒸发,粘结砂粒的粘土膏中的水分较为稳定,型砂的性能也就较小波动。
吸水细粉含量太高也不好,会使型砂的水分较高,易于导致铸件上产生针孔、表面粗糙和砂孔的缺陷。
吸水细粉含量太低,则型砂的性能(尤其是可紧实性)不易稳定。
6、混砂加料顺序混砂时的加料顺序:为了减少混砂所需的能量,采用合理的加料顺序是很重要的。
很多工厂,混砂时习惯于先加干料(砂和粘土),干混一段时间,然后加水混匀。
这种操作方法有三个缺点:1)混干料时粉尘飞扬,污染环境且有害于工人的健康;2)混砂机抽尘会损失大量有效粉料;3)需要较长的混砂时间。
在混匀了的干料中加水,即使水加得很分散,也是一滴一滴地落在干料中。
因为粘土是亲水的,加上水滴表面力的作用,水滴附近的粘土很快就聚集到水滴上,形成较大的粘土球。
将这些粘土球压碎并使它涂布在砂粒表面上是比较困难的,需要的能量也比较大。
如果先加砂和水混匀,后加粉状粘土,因为水已分散,没有较大的水滴,加入粘土后只能形成大量较小的粘土球。
压开这些小粘土球是比较容易的,需要的能量也较小。
也就是说,用同样的混砂设备,得到品质相同的型砂,所需的混碾时间较短。
水3%。
混砂设备是实验室用混砂机。
7、型砂中有效膨润土量和混砂效率粘土湿型砂混砂时,必须加入一定量的膨润土,使型砂中保有必要的膨润土量。
膨润土含量通常用亚甲基蓝法予以测定。
用亚甲基蓝法测得的膨润土量,以前统称之为有效膨润,现在看来,称之为活性膨润土更为适当。
活性膨润土是能与水结合而起作用的,但是,在实际应用的型砂中,并非所有的活性膨润土都起作用,也就是说,并非都是有效的。
有效膨润土是型砂中实际起作用的膨润土,只是活性膨润土的一部分。
C.E.Wenniger提出,用混砂效率来衡量粘土湿砂的调制程度。