粘土型(芯)砂
造型材料

用湿法制取的水玻璃模数M一般小于3。
三、水玻璃模数的调整
在铸造行业习惯用波美度(Be' )表示。20摄氏
度时波美度( B)e与' 密度 的换算关系为:
=
144 .3
144.3—Be '
四、水玻璃模数的调整
水玻璃的模数就是其溶液中SiO2和Na2O的 摩尔比值。
要求降低模数时,向水玻璃中加入NaOH; 要求升高水玻璃模数时加入NH4Cl.
1.水分的在线检测与控制系统
检测方法的原理通常有:
电阻法、电容法、微波法、成型性控制法
(1)电阻法。测试棒作为一极,以混砂机的 底板和侧壁作为另一极,测其电压。当型 砂含水量少时,其电阻大,根据这一原理 测出水分多少。
第三章 水玻璃砂及其他 无机粘结剂砂
第一节 概述
CO2硬化水玻璃砂从发明后就得到快速推广 应用,它使得造型、制芯速度大大提高,其硬 化方式有以下几种:
适用范围:
用于混制各类黏土砂的单一砂和背砂, 及水玻璃砂。
3.转子式混砂机 特点:
利用安装在转子上的叶片的高速旋转时 对逆向流动的砂流施以强烈的冲击力,引 起砂粒间相对运动,破碎粘土团。
混砂质量好,生产效率高。
适用范围:
适于混制各类型砂,是现代高速高型的 首选。
(三)砂处理系统的自动检测与型砂质量控 制。
固化剂:硅酸二钙、硅铁粉、氟硅酸钠,此外还 有近年来开发的有机酯等。
一、水玻璃固化剂——有机酯 硬化机理:
1)有机酯在碱性溶液中发生水解,生产酸和 醇。它决定了型砂的可使用时间长短。
2)有机酯与水玻璃反应析出硅酸溶胶。 优点:
1)型砂流动性好,便于紧实和机械化 2)型砂不粘模,不必涂防粘剂 3)出砂性好 缺点: 价格高 粘结强度的影响因素: 1)水玻璃的模数,在此采用模数较高的 2)酯加入量要在8%-15%之间
第二篇砂型和砂芯制造_湿型

第一章
湿 型
第二篇 砂型和砂芯的制造
1
第二篇 砂型和砂芯的制造
第一章
湿 型
用型砂、芯砂造型、造芯,根据砂型、砂芯本身建 立强度过程中其粘(固)结机理的不同,通常可分三种类 型的方法,即机械黏结造型(芯);化学黏结造型(芯)和 物理固结造型(芯)。
2
第二篇 砂型和砂芯的制造
含水量只能说明型砂中所含自由水的绝对数值,并不 能反映型砂的干湿程度。
10
第二篇 砂型和砂芯的制造第一章ຫໍສະໝຸດ 湿 型(3)紧实率
试验时,使型砂通过3mm的筛网松散的填入直径
50mm、有效高度120mm的试样筒中,将试样筒上端 实践表明:比较干的型砂在未紧实前,颗粒间堆积比较紧密, 用刮板刮平,然后用压头给型砂施以1MPa的压力或 即松态密度高,紧实后,体积减小不多;而比较湿的型砂,未 用锤击式制样机(见下图)锤击3次,试样体积被压 紧实前的松态密度小,紧实后,体积减小大。所以可以根据型 缩的程度作为其紧实率,紧实率可直接从制样机上读 砂在试样筒内紧实前后的体积变化(紧实率)来检查型砂的干 出或用紧实高度与试样筒高度之比来表示。 湿状态。
9
第二篇 砂型和砂芯的制造
第一章
湿 型
一、水分、最适宜湿程度和紧实率
水分不足时,型砂太干时,型砂强度低,韧性和可塑 性差,砂型易破碎,不易起模,铸件易产生冲砂、砂眼 等缺陷。 水分过高时,可塑性和韧性虽好,但湿强度却较低, 砂型易变形,铸件薄处可能浇不足,厚处则表面粗糙, 易产生夹砂缺陷。故控制型砂适宜水分十分重要。 (l)含水量 它是表示型砂中所含水分的质量百分数。
15
第二篇 砂型和砂芯的制造
第一章
湿 型
造型材料及型芯砂工艺(精)
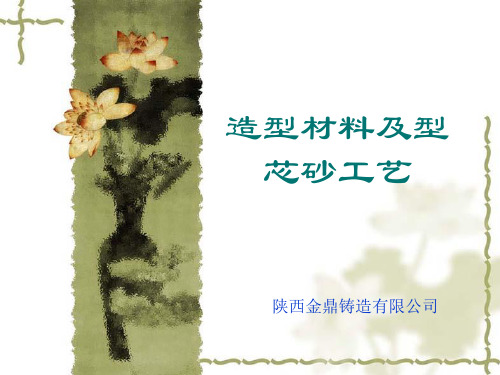
陕西金鼎铸造有限公司
从广义上讲,凡是用来制造铸型(包 括芯子)的材料都属于造型材料。铸造生 产中使用的铸型有砂型、金属型、陶瓷型、 石膏型等等,需要各种各样大量的造型材 料。在以上各种铸型中,最普遍和大量使 用的是砂型。在我国或世界范围内,用砂 型生产的铸件占铸件总生产量的80%以上, 因此,在铸造行业里,一般说到造型材料, 通常指的是砂型铸造用的造型材料,包括 所用的各种原材料、混合料及涂料等。
不同的膨润土,丧失粘结能力的温度不同。 由差热分析实验证明: 天然钠基膨润土的失效温度为638℃,钙基膨 润土为316℃.由此可见,粘土砂中,存在两种 膨润土:一种是有效膨润土,另一种是死粘土。 死粘土越多,粘土粘结性能越差。
1.3煤粉
铸铁用湿型砂中加入煤粉,可以防止铸 件表面粘砂缺陷,改善铸铁件的表面光洁程 度,能减少夹砂缺陷,同时也起到提高型砂溃 散性的作用。对于湿型铸造球墨铸铁件,型 砂中加入煤粉,还能防止产生皮下气孔。
第一章
湿型砂
第一节 湿型用原材料
湿型砂造型使用的原材料通常包括原砂、 膨润土、煤粉及其它一些辅助材料,例如糊精、 淀粉、重油等。
1.1硅砂(原砂) 硅砂的主要化学成分是SiO2。我国铸造生产中 所用硅砂,根据其来源和加工方法不同,可以 分为天然硅砂和人工硅砂两大类。
天然硅砂是由火成岩经过风化或变质作用, 逐渐剥裂、细化,坚硬的石英颗粒与其他矿物 颗粒部分分离,然后再经水流或风力搬运沉积 形成砂矿。这些砂矿按其成矿条件和特点,可 分为河沙、湖砂、海砂、风积砂等几种。海砂 和湖砂又可细分为海(湖)滩砂、沉积砂、堆 积砂等。
方法和AFS平均细度表示法。 硅砂的颗粒形状是根据砂粒的圆整度和表 面棱角磨圆的程度来区分的。我国现行的《铸 造用硅砂》标准采用角形因数值对硅砂的各种 粒型进行大致的定量划分。但是实际应用中大 部分硅砂其颗粒形状都是混合的,天然硅砂的 角形因数都在1.2~1.45之间。颗粒较圆的砂粒, 混合料的流动性和紧实密度较高,砂粒间的接 触点和粘结剂“连接桥”的截面积增大,对提 高混合料的强度有利,砂粒排列约紧密,对提 高混合料的强度越有利,但是砂粒在高温状态 下的线膨胀量及膨胀应力也越大。
粘土砂铸造工艺

粘土砂铸造工艺LG GROUP system office room 【LGA16H-LGYY-LGUA8Q8-LGA162】粘土砂铸造工艺一.概述粘土砂是以粘土(陶土)作粘结剂的型(芯)砂。
粘土砂造型由于其成本低廉,适合于批量大规模生产,所以目前仍然作为铸件生产的最主要方式。
粘土砂旧沙由于在循环使用过程中各组份的热分解,发生物理性能的变化,如未经再生就加以使用,将使型砂质量不稳定。
据统计铸件废品率中30~40%为型砂质量引起,因此型砂质量的控制在粘土砂造型中起十分重要的作用。
随着目前对铸件要求的提高,对型砂质量的要求也越来越高。
二.粘土砂造型中几种与型砂质量有关的常见缺陷。
1.气孔、浇不到、冷隔粘土砂型砂的组成绝大部分为旧砂(85~95%),由于旧砂循环使用过程中经过反复热冲击,一些组分会出现热分解,发生物理性能的变化:a. 粘土在砂型温度高于500度的区域,膨润土晶体结构受到完全破坏,就变成没有湿态粘结力的无效粘土以粉尘状态存在与旧砂中,成为旧砂泥份中的一种;b. 煤粉炭化成为枯化物;c. 不稳定的砂粒(包含杂质)会粉化。
这些衍生物共同成为旧砂的微粉。
微粉含量超过一定的限度,微粉堵塞砂砾空隙就会造成型砂透气性差。
而且无效粘土吸水能力比有效粘土强,从有效粘土中夺取有效水分,因此当无效粘土含量较多时,达到调匀所需的加水量就得增加。
加大了型砂加水量,在某种程度上也就加大了型砂的发气量。
由于发气量增加而透气性减少,浇铸时液体所收的阻力增大,必然导致侵入性气孔、浇不到、冷隔等缺陷的形成。
2.表面光洁度差(包括砂眼、毛刺、夹砂结疤等)大量的无效粘土造成型砂的抗拉强度差、韧性低、透气性差。
增大型砂的脆性,使型砂易塌箱、掉砂,在浇铸时砂粒容易掉落形成砂眼、毛刺、夹渣结疤等缺陷,进而影响铸件质量。
3.粘砂无效粘土(死黏土)部分约占整个砂型重的2~5%,无效粘土的一部分在高温作用下包裹在砂粒表面上,烧结形成一层牢固的膜,不能用水洗掉,成为砂粒的一部分,这层膜又称为惰性膜。
粘土砂铸造工艺流程

粘土砂铸造工艺流程一、模具制造模具是粘土砂铸造的关键部分,它用于形成砂型,保持金属液体在浇注过程中的形状。
模具可以分为两种类型:单件模和多件模。
单件模用于制造形状简单的零件,而多件模则用于制造形状复杂的零件。
模具制造的步骤主要包括模板设计、模板制造、模板组装和模板调整等。
二、砂型制作砂型是粘土砂铸造的重要组成部分,它用于容纳金属液体并形成最终产品的外部形状。
砂型制作的步骤如下:1.振动:首先将砂料加载到模具中,然后用振动设备将其压实和排气,以确保砂型的密实度和平整度。
2.砂芯制作:对于一些需要内部空间的零件,需要制作砂芯。
砂芯可以通过制作模具进行成型,然后放入砂型中。
3.分模:将模具分开,取出零件的上下型。
4.拼装:拼装上下型,然后用销、夹具或模压机将其固定在一起。
5.排气:通过在砂型中钻孔或打孔,以释放零件浇注过程中产生的气体。
三、熔炼及浇铸1.配料:将合适比例的金属材料和熔剂放入熔炉中进行加热熔化,以达到所需的浇注温度。
2.准备浇注:当金属液体达到合适的浇注温度后,将其倒入专用容器中,以备浇注。
3.浇注:将金属液体从容器中倒入砂型中,并通过控制浇注速度和压力,使其填充整个砂型。
四、冷却和清理1.冷却:当金属液体充满整个砂型后,需要等待一定的时间,以便金属液体冷却和凝固。
冷却时间根据铸件的尺寸和形状而定。
2.分离:在金属凝固之后,拆开模具,取出砂型。
3.去除余料:清理过程中,需要去除铸件上的闪光部分,也就是余料。
可以使用切割、剥离、抛光等工艺进行处理。
4.表面处理:根据要求,可以对铸件表面进行进一步的处理,如抛光、喷砂、喷涂等。
总结:粘土砂铸造工艺流程包括模具制造、砂型制作、熔炼及浇铸、冷却和清理等步骤。
这种工艺可以用于制造各种形状和尺寸的金属零件,广泛应用于汽车、机械、航空航天等行业。
在制造过程中,需要注意模具制作、砂型制作和浇铸等环节的精度和质量控制,以确保最终产品的质量和性能。
黏土砂型铸造工艺过程及特点
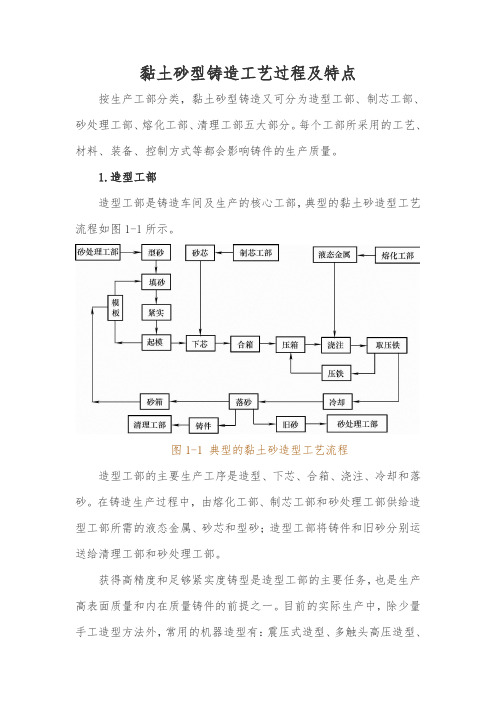
黏土砂型铸造工艺过程及特点按生产工部分类,黏土砂型铸造又可分为造型工部、制芯工部、砂处理工部、熔化工部、清理工部五大部分。
每个工部所采用的工艺、材料、装备、控制方式等都会影响铸件的生产质量。
1.造型工部造型工部是铸造车间及生产的核心工部,典型的黏土砂造型工艺流程如图1-1所示。
图1-1 典型的黏土砂造型工艺流程造型工部的主要生产工序是造型、下芯、合箱、浇注、冷却和落砂。
在铸造生产过程中,由熔化工部、制芯工部和砂处理工部供给造型工部所需的液态金属、砂芯和型砂;造型工部将铸件和旧砂分别运送给清理工部和砂处理工部。
获得高精度和足够紧实度铸型是造型工部的主要任务,也是生产高表面质量和内在质量铸件的前提之一。
目前的实际生产中,除少量手工造型方法外,常用的机器造型有:震压式造型、多触头高压造型、射压造型、静压造型、气冲造型等。
不同的铸件产品、质量要求和生产率,可选择不同的造型方法及装备。
2.制芯工部制芯工部的任务是生产出合格的砂芯。
典型的制芯工部工艺流程如图1-2所示。
图1-2 典型的制芯工部工艺流程由于采用的黏结剂不同,芯砂的性能(流动性、硬化速度、强度、透气性等)都不相同,型芯的制造方法及其所用的设备也不相同。
根据黏结剂的硬化特点,制芯工艺有如下几种:1)型芯在芯盒中成形后,从芯盒中取出,再放进烘炉内烘干。
属于此类制芯工艺的芯砂有黏土砂、油砂、合脂砂等。
2)型芯的成形及加热硬化均在芯盒中完成。
属于这类制芯工艺的有热芯盒及壳芯制芯等。
3)型芯在芯盒里成形并通入气体而硬化。
属于这类制芯工艺的有水玻璃CO2法及气雾冷芯盒法等。
4)在芯盒中成形并在常温下自行硬化到形状稳定。
这类制芯工艺有自硬冷芯盒法、流态自硬砂法等。
在制芯工部中,制芯机是核心设备。
但砂芯的质量除与制芯机装备水平有直接关系外,还与芯砂种类、硬化方式、砂芯的形状结构等有关。
3.砂处理工部砂处理工部的任务是提供造型、制芯工部所需要的合乎一定技术要求的型砂及芯砂。
粘土型砂

常用的内部检验方法有化学成分检验、金相检验、 力学性能检验、耐压试验、超声波探伤等。
我国铸造行业造型材料的现状
义。我国是铸造大国但不是铸造强国。
现有水平与铸造强国要求
目前水平
生产效益 铸件质量 8.4吨/人· 年 4万元/人· 年 废品率10~15% 加工余量20%
强国要求
60~80吨/人· 年 30万元/人· 年 <5% 10%
铸件出口
铸件品种
占总产量10% (技术含量低产品)
铝合金 5% 球铁 14% 合金钢 25%
(1) 手工造型
全部用手工或手动工具完成造型过程的造型方法称 为手工造型。 手工造型方法有以下几种:
①整模造型 ②分模造型 ③挖砂造型 ④假箱造型 ⑤活块造型 ⑥三箱造型 ⑦刮板造型
图7-2所示 图7-3所示 图7-4所示 图7-5所示 图7-6所示 图7-7所示 图7-8所示
(2) 落砂清理
用手工或机械使铸件和铸型、型芯(芯砂)、 砂箱分离的操作过程称为落砂。
清除铸件表面的型砂,内部砂芯,飞边毛刺, 浇、冒口以及修补缺陷一等系列工作,叫铸 件的清理。 人工清理时劳动强度大,卫生条件差,费工、 费时。目前,有很多清理工作已由机械来完 成。
(3) 检验
铸件的质量检验方法分为外部检验和内部检验。
6、合箱浇注、落砂清理和检验
砂型铸造——黏土砂型
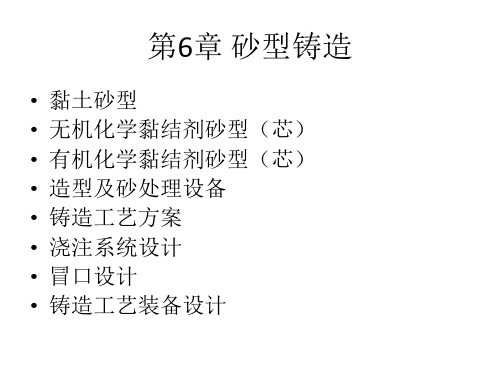
固整体的岩石则称为石英岩。
6.1 黏土砂型
对原砂提出的质量要求:
1)含泥量――含泥量指原砂中直径小于0.02mm(20µm)的细小颗 粒的含量(质量分数),其中既有黏土,也包括极细的砂子和其它 非粘土质点。 原砂含泥量检测方法: 利用不同颗粒尺寸的砂粒在水中下降速度不同,将原砂中颗粒 直径>20µm 与直径<20µm的颗粒分开。检验时,称量烘干的原砂并 置入烧杯中,加入水及分散剂,煮沸及搅拌使其充分分散;然后反 复按规定时间沉淀,虹吸排除浑水和冲入清水。直到水清后,由烘 干的残留砂样质量即可计算出原砂含泥量。
适宜干湿程度的水分一也不同。
6.1 黏土砂型
6.1.2 湿型砂性能要求
1.水分和紧实率
2)紧实率:湿型砂用1 MPa的压力压实或者在锤击式制样机上打击3
次,用试样紧实前后高度变化的百分数来表示。 (1)测定方法的依据:较干的型砂自由流入试样筒中时,砂粒松散 密度较高,在相同的紧实力作用下,型砂体积减小较少。 (2)根据型砂紧实率大小的变化,就可以检查出型砂水分是否合
6.1 黏土砂型
6.1.2 湿型砂性能要求
5.起模性、变形量、韧性和破碎指数
1)型砂的起模性是表示起模时模样或模板与砂型分离时,砂型是
否容易损坏,产生开裂或掉落的性能。
6.1 黏土砂型
6.1.2 湿型砂性能要求
起模性的好坏与型砂的湿态抗压强度是两种不同的特性。
(1)抗压强度不仅反映了型砂的黏结力大小,还反映了砂粒受压
(1)湿型(简称湿型):造好的砂型不经烘干,直接浇人高温金属 液体; (2)干砂型(简称干型):在合箱和浇注前将整个砂型送入窑中烘 干;
(3)表面烘干砂型(简称表干型):在浇注前对型腔表层用适当方
铸造黏土砂.ppt

(3)位置:气孔可分布在铸件的任何位置。可 分为:
内部气孔、皮下气孔、表面气孔。
内部气孔存在于铸件的内部,目视检查无法发 现;
皮下气孔成串横列于铸件表面以下1~3mm,一 般为圆球形、团球形、泪滴形或长针形;
表面气孔存在于铸件毛坯表面,落砂清理后可 以发现,
(4)气孔的种类:
从气孔的形成原因或形成机理来分类,气孔可分为5种 类型:
1.可塑性
可塑性与韧性
1)定义:型砂在外力作用下变形,外力去除 后仍保持所赋予形状的能力。
2)可塑性的获得:粘土被水润湿形成一层薄 膜覆盖在砂粒上,外力作用时砂粒沿薄膜产 生滑移。
3)检测标准:
型砂标准试样破坏前的变形量(cm)
型砂极限应变值: sH 1000
型砂标准试样的湿压强度(104MPa)
钠钙膨润土(PNaCa):任一交换性阳离子 量 均 占 阳 离 子 交 换 容 量 的 50 % 以 下 , 且 钠 的 含量较多;
附加物
附加物的作用是使型砂具有特定的性 能,并改善铸件的表面质量。
1.煤粉 煤粉可以有效防止铸件表面产生粘砂
缺陷,减少夹砂、结疤缺陷,改善型砂的 流动性和柔韧性,改善铸件的表面光洁度。
准漏斗(又称流速计)是用150目金刚砂粉末, 在40秒内流完50克来标定和校准的。美国标 准还规定用孔径1/5英寸的标准漏斗测定流 动性差的粉末。
测量方法-2 采用粉末自然堆积角(又称安息角/休止
角)试验测定流动性。让粉末通过一粗筛网 自然流下并堆积在直径为一英寸的圆板上。 当粉末堆满圆板后,以粉末锥的高度衡量流 动性,粉末锥的底角称为安息角,也可作为 流动性的量度。锥愈高或安息角愈大,则表 示粉末的流动性愈差,反之则流动性愈好。
型砂与芯砂

• 4.水
• 通过水使黏土和原砂混成一体,并具有一定的强 度和透气性。水分过多,易使型砂湿度过大,强 度低,造型时易粘模,使造型操作困难;水分过 少,型砂则干而脆,造型、起模困难。因此,水 分要适当,当黏土和水分的质量比为3∶1时, 强度达最大值。
5.扑料和涂料
• 为防止铸件表面粘砂,并使铸铁件表面光滑,常在铸型型 腔表面覆盖一层耐火材料。
• 型(芯)砂的性能用型砂性能试验仪检测,单件小批量生 产时,可用手捏检验法,如图所示。当型砂湿度适当时可 用手捏成团,手放开后不松散,手上不粘砂,往上一抛就 散开,这时的型砂湿度即可。
【实训操作与思考】
• 在实训老师的指导下,按规定的配比配制黏土砂。 • 型砂中加入锯木屑、煤粉起什么作用? • 型砂反复使用后,为什么性能会降低?再次使用旧砂有什
• 型(芯)砂的混制是在混砂机中进行,目前工厂常用的是 辗轮式混砂机,如图所示。
• 混砂工艺是:
• 按比例将新砂、旧砂、黏土、煤粉等加入混砂机中先干混 2~3min,混拌均匀后再加水、液态黏结剂(水玻璃、 桐油等)湿混10min左右,即可出砂。
• 混制好的型砂应堆放2~4h,使水份分布得更均匀,这 一过程叫调匀。型砂在使用前还需进行松散处理,使砂块 松开,空隙增加。
2.透气性
• 紧实的型(芯)砂允许气体透过的能力称为透气性。 • 透气性不好,易在铸件内部形成气孔等缺陷。 • 型砂的颗粒粗大、均匀,且为圆形,黏土含量少,型(芯)
砂舂得不过紧,均可使透气性提高。 • 含水量过少时,砂粒表面黏土膜不光滑,透气性不高 • 含水量过多,空隙被堵塞,亦使透气性降低。
3.耐火性
• 中小铸铁件芯砂的配比:新砂40%,旧砂 60%;另加黏土5%~7%,纸浆2%~3%, 水分75%~85%
粘土型砂讲座(1)

分别用符号“PNa ”和“PCa”表示。
第一节 粘土砂材料及其质量要求
7、两种粘土的主要共同点:
● 都是亲水的,都具有吸水膨胀增加自身体
积的能力 ● 粘土的最大特性是粘结性和可塑性,这种 特性只有当被水充分湿润后才能表现出出来。 ● 在显微镜下观察,都属于层片状结构
5、粘土的粘结机理: 带负电荷的粘土颗粒将极性水分子吸附 在自己的周围,形成胶团的水化膜,依靠粘 土颗粒间的公共水化膜,通过其中的水化阳 离子起“桥”的作用,使粘土颗粒相互连结
起来。
第一节 粘土砂材料及其质量要求
6、铸造用粘土分类:
铸造用粘土可分为两大类: 膨润土和普通粘土
分别用符号“P”和“N”来表示。
一、石英质原砂 1、原砂的来源: 天然砂: 山砂、海砂、湖砂、河砂、风积砂等。 人造砂:是由石英岩或石英砂岩经人工破碎而得到。 2、原砂的矿物组成: 原砂的主要矿物组成是石英。其次是长石及少量的云 母、铁的氧化物、硫化物和碳酸盐等。
第一节 粘土砂材料及其质量要求
3、原砂的化学成分及物理特性:
原砂的化学成分主要是SiO2。其理化特性为: SiO2的熔点为1713℃,硬度为莫氏7级,密度 为2.65 。 纯洁的石英呈无色透明或半透明状态,有杂质存在时 呈红、黄等其他颜色。石英的最大特点:耐磨、耐 高温。
第一节 粘土砂材料及其质量要求
8、两种粘土的主要异同点:
① 矿物组成不同 ● 普通粘土的主要矿物组成为高岭石,其分子式结构
为Al2O3· 2SiO2· 2H2O ,带有2个层间水
● 膨润土的主要矿物组成为蒙脱石,其分子式结构为
Al2O3· 4SiO2· H2O ·nH2O ,带有N个层间水
第二篇砂型和砂芯_有机化学粘结剂砂芯

砂型和砂芯的制造
第三章
有机化学粘结剂砂芯(型)
§3 —1
第三章 有机化学粘结剂砂芯(型) 概 述
一、砂芯的分级 砂芯主要用来形成铸件的内 腔、孔洞和凹坑等部分,在浇注 时,它的大部分或部分表面被液 态金属包围,受金属液的热作用 和机械作用强烈,排气条件差, 出砂及清理困难,因此对芯砂的 性能要求一般比型砂高。
6
第二篇
砂型和砂芯的制造
第三章
有机化学粘结剂砂芯(型)
§ 3 —2 壳 芯 ( 型) 一、壳芯(型)的制造
用热塑性酚醛树脂加潜伏性固化剂(如乌洛托品)与 润滑剂(如硬脂酸钙)通过一定的覆膜工艺配制成覆膜砂。 覆膜砂用于壳 型(芯)的工艺主 要有两种,用于 制造壳型的翻斗 法和制造壳芯的 吹砂法。
7
还可形成右图所示仲胺链,大 部分氮成为氨排放到大气中。
11
第二篇
砂型和砂芯的制造
第三章
有机化学粘结剂砂芯(型)
(二)原砂 一般选用天然水洗硅砂。只有特殊要求的铸钢件或铸 铁才采用锆砂或铬铁矿砂。对硅砂的一般要求是: ①Si02含量高。铸铁及有色铸造用砂要求SiO2>90%, 对铸钢件SiO2>97%。
15
第二篇
砂型和砂芯的制造第三章有机化学粘结剂砂芯(型)
(二)壳型(芯)表面疏松 壳型(芯)表面局部密实度太低。 产生的主要原因 射芯压力过高或过低,模具排 气不畅;模具由于分盒面间隙大而跑砂,覆膜砂流动性 差或透气性差;原砂太粗;覆膜砂熔点太低。 解决措施 选用合理射砂压力,改善排气系统, 防止憋气,采用变形小的材料作芯盒;选用流动性和透 气性好的覆膜砂 (三)壳型芯在浇注时破裂 浇注时型、芯破裂,造成铁水进入壳芯内,或壳型 跑火而使铸件报废。
黏土湿型砂的性能要求

黏土湿型砂的性能要求为了制造出合格的砂型和砂芯,黏土湿型砂应具有良好的常温工艺性能,如湿度、流动性、强度、可塑性与韧性、不粘模性等。
液态合金浇入铸型后,与型腔表面砂层之间发生着机械作用、热作用和化学作用。
机械作用是指液态合金充填过程中对腔壁的动压力和静压力,合金液凝固收缩时对铸型产生的压应力。
热作用是由于合金液与铸型腔存在着很大的温差,型腔壁被强烈加热,靠近合金液的型腔表面加热特别严重,局部甚至开裂或烧结。
化学作用是液态合金及其氧化物与型腔表面的砂层发生化学反应。
因此黏土湿型砂应具有良好的高温性能,如耐火度、发气性、热膨率、溃散性、退让性等。
下面分别简述这些主要性能。
1)湿度(水分)为了得到所需的可塑性、韧性和湿态强度,黏土湿型砂必须含有适量水分。
生产现场判断型砂湿度有以下几种方法:有丰富经验的混砂和造型工人常根据手捏型砂是否容易捏成闭和是否粘手来判断型砂的干湿程度;还可根据捏紧的动作中型砂是否柔软和变形情况来判断型砂的可塑性;根据手指掐碎砂团时用力大小判断型砂的湿强度是否合适。
如果用手捏砂时,只有潮的感觉,不觉得沾手,且柔和,印在砂团上手指痕迹清晰,那这样的型砂干湿度就比较合适。
2)流动性型(芯)砂在外力或自重作用下,沿模样(或芯盒表面)和砂粒间相对移动的能力称为流动性。
流动性好的型砂可形成紧实度均匀、无局部疏松、轮廓清晰、表面光洁的型腔,这有助于防止机械粘砂,获得光洁铸件。
此外,还能减轻型砂紧实时的劳动强度,提高生产率和便于实现造型、制芯过程的机械化。
3)强度型砂必须具备一定的强度以承受各种外力的作用,如果强度不足,在起模、搬运砂型、下芯、合型等过程中,铸型有可能破损塌落;浇注时可能承受不住金属液的冲刷和冲击,冲坏砂型而造成砂眼缺陷,或者造成胀砂(铸件肿胀)或跑火(漏铁液)等现象。
但是强度也不宜过高,因为高强度的型砂需要加入更多的黏土,不但增加了水分需求量,降低了砂型透气性,还会使铸件的生产成本增加,而且给混砂、紧实砂型和落砂等工序带来困难。
型砂配制及性能检测实验

实验一型砂配制及性能检测材料成形工艺实验名称:型砂配制及性能检测一、分组:每班45min一班:7:30~8:15按学号每五人一组(分六组);二班:8:15~9:00 按学号每五人一组(分六组)二、实验内容1.型砂配制(粘土砂),每三组配砂一碾子(3kg)。
型砂性能检测:每组进行三个试样的测定取平均值(但其中任一试样与平均值相差超出10%时,实验应重新进行)。
2.透气性能测定3.湿压强度测定三、型砂配方干混2~3min 湿混4~6min 原砂(50/100)100%+膨润土5~7% +水4~7% 出砂四、制样按标准操作(现场教师指导)(标准方法,GB268d-81)首先,用SHN型辗轮式混砂机混制型砂,将混制好的试样混合料,在SAC-A型锤击式制样机上冲击三次,制成φ50×50mm圆柱形标准试样,紧实后标准圆柱试样的直径为φ50±0.2毫米,高度为50±1毫米。
标准圆柱形试样的舂制过程如下:(1)称出一定重量的试样(约为160~180g),倒入带底垫的标准圆柱形试样筒中(试样筒内径带锥度的一头应朝上,不能装反);(2)搬动手柄将冲头举起,把底垫和砂样筒放于冲头下,慢慢放下手柄,使冲头进入砂样筒内。
3)转动偏心轮手柄三次,使落锤舂试样三次,此时捡查芯棒的红线位置是否在试样高度的公差线之内,如在公差线之内,试样便制成。
如试样高度超出公差,该试样应作废,在调整试料的重量后,再按上述步骤操作,直到获得合格的试样。
(4)搬动手柄使冲头提起,取出砂样筒。
在砂样筒内的试样,用于测透气性,测完透气性后,用顶棒将砂样顶出后即可用来进行强度试验。
五、透气性测定在STZ-A型透气性测定仪上进行,透气性测定仪的原理图如附图。
试验前应该先检查仪器的准确度:(1)仪器的全部系统不应有漏气现象,用密封样筒做试验时,保持10分钟,钟罩应不下降。
(2)用密封样筒做试验时,水柱的高度应为10厘米,不得低于9.8厘米。
铸造芯砂工艺流程

铸造芯砂工艺流程一、芯砂的选择。
芯砂的种类那可不少呢。
有黏土砂,这就像咱小时候玩泥巴一样,不过是有专业要求的那种。
黏土砂成本低,来源广,用起来比较顺手。
还有树脂砂,这就比较高级啦。
它强度高,造型很方便,能做出各种复杂的形状,就像个百变精灵似的。
水玻璃砂也很有特点,耐火性不错,在一些特定的铸造环境里特别好用。
不同的芯砂适用于不同的铸造产品,就像不同性格的人适合不同的工作一样。
二、芯砂的混制。
混制芯砂可是个有趣的过程。
把各种原料按照一定的比例放在混砂机里。
这就像是做一道特别的菜肴,各种调料得放对量才行。
比如说,要是砂多了,可能做出来的芯子就不够结实;要是黏结剂多了呢,又可能会太黏糊,不好操作。
混砂机就像个大厨师的锅,把这些原料搅拌均匀。
在这个过程中,要注意搅拌的时间和速度。
时间太短,混合不均匀,时间太长呢,可能会破坏原料的一些特性。
速度也得合适,就像人走路一样,太快了容易摔倒,太慢了又到不了目的地。
三、芯砂的制芯。
制芯的方法有好多呢。
有手工制芯,这就很考验工人师傅的手艺啦。
就像捏泥人一样,得有一双巧手。
手工制芯可以做出一些比较精细的芯子,不过效率可能低一点。
还有机器制芯,这就像开了挂一样。
机器制芯速度快,质量也比较稳定。
不管是用哪种方法,都要保证芯子的形状和尺寸准确无误。
要是芯子的形状不对,就像穿错了鞋子,那整个铸造产品可就出问题啦。
四、芯砂芯子的干燥。
芯子做好了还不能直接用,得干燥一下。
干燥就像是给芯子做个SPA。
干燥的方式也有不同的选择。
有的是自然干燥,把芯子放在通风良好的地方,让它慢慢地晾干。
这种方式比较环保,不过时间会长一点。
还有烘干的方式,就像用吹风机吹干头发一样,把芯子放在烘干炉里,用合适的温度烘干。
温度很关键哦,温度低了,干燥不完全,温度高了,可能会把芯子烤坏,那就前功尽弃啦。
五、芯砂芯子的检验。
检验芯子也是很重要的一步。
就像检查一个艺术品有没有瑕疵一样。
要看看芯子的尺寸是不是符合要求,有没有裂缝之类的缺陷。
铸造材料型(芯)砂的种类及应用
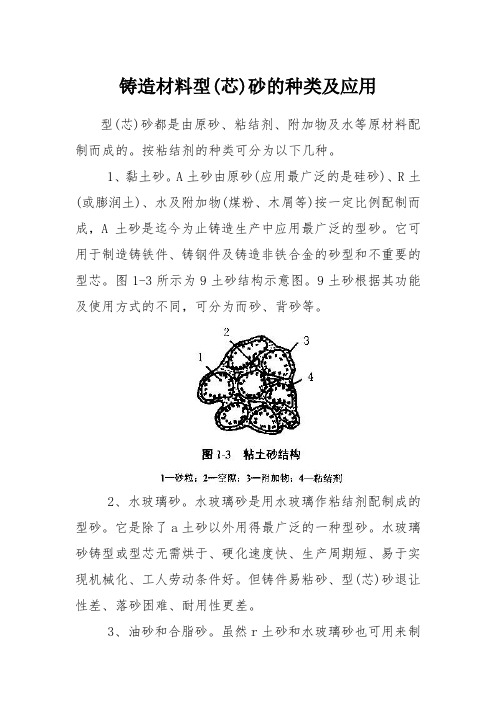
铸造材料型(芯)砂的种类及应用
型(芯)砂都是由原砂、粘结剂、附加物及水等原材料配制而成的。
按粘结剂的种类可分为以下几种。
1、黏土砂。
A土砂由原砂(应用最广泛的是硅砂)、R 土(或膨润土)、水及附加物(煤粉、木屑等)按一定比例配制而成,A土砂是迄今为止铸造生产中应用最广泛的型砂。
它可用于制造铸铁件、铸钢件及铸造非铁合金的砂型和不重要的型芯。
图1-3所示为9土砂结构示意图。
9土砂根据其功能及使用方式的不同,可分为而砂、背砂等。
2、水玻璃砂。
水玻璃砂是用水玻璃作粘结剂配制成的型砂。
它是除了a土砂以外用得最广泛的一种型砂。
水玻璃砂铸型或型芯无需烘于、硬化速度快、生产周期短、易于实现机械化、工人劳动条件好。
但铸件易粘砂、型(芯)砂退让性差、落砂困难、耐用性更差。
3、油砂和合脂砂。
虽然r土砂和水玻璃砂也可用来制造型芯,但对于结构形状复杂、要求高的型芯,则难以满足要求。
因为型芯在浇注后被高温金属液所包围,型芯砂应具有比一般型砂更高的性能要求。
尺寸较小、形状复杂或较重要的型芯,可用油砂或合脂砂制造。
4、树脂砂。
树脂砂是以树脂为粘结剂而配制成的型砂。
用树脂砂造型或造芯,铸件质量好、生产率高、节省能源和工时费用、减少清理上作量、工人劳动强度低、易于实现机械化及自动化、适宜于成批大量生产。
除此以外,还有白硬砂、石灰石砂等。
- 1、下载文档前请自行甄别文档内容的完整性,平台不提供额外的编辑、内容补充、找答案等附加服务。
- 2、"仅部分预览"的文档,不可在线预览部分如存在完整性等问题,可反馈申请退款(可完整预览的文档不适用该条件!)。
- 3、如文档侵犯您的权益,请联系客服反馈,我们会尽快为您处理(人工客服工作时间:9:00-18:30)。
为了防止铸件表面产生化学粘砂,铸钢用原砂的Si02含 量大多在96%(质量分数)以上,厚壁和浇温高的铸件要 求硅砂SiO 2含量更高些。 由于硅砂含Si02高,型砂中又缺少煤粉等缓冲材料, 因此铸钢件产生夹砂结疤类缺陷倾向性更大些。可采用 活化膨润土或天然钠质膨润土来提高型砂的热湿拉强度 和抗夹砂结疤能力。 为了提高型砂的韧性和表面风干强度,防止冲砂和砂 孔,型砂中可加入适量的渣油液和淀粉类材料(例如冻胶 化淀粉、糊精等)。必要时,需在砂型表面喷涂糖浆、纸 浆废液、水玻璃等的稀释水镕液,或酚醛树脂酒精溶液 ,以提高其表面强度。喷涂后应经停放几小时或用喷灯 22 表面喷烧后才能合箱。
14
判断型砂干湿程 度的几种方法: 1、含水量测定 2、手捏感觉 3、紧实率
4、过筛性
15
最适宜的水分范围
一般将使型砂诸性能均能 达到技术条件要求的水分 范围称为最适宜水分范围。
16
17
Ⅱ、湿型砂制备及质量控制
在拟定型砂的配方之前,必须首先根据浇注合金种 类、铸件特征和耍求、造型方法和工艺、清理方法 等因素确定型砂应具有的性能范围。然后再根据各 种造型原材料的品种和规格、砂处理方法和设备性 能、砂铁比和各项材料烧损比例等因素拟定型砂的 配方。
2
一、强
度
3
(一)湿强度
影响因素: (1)粘土及水分
4
(2)原砂颗粒特性
(3)型砂紧实度
(二)干强度
型砂经烘干或硬化后的强度称为干强度。干强度对干型、干 芯和表面干型在搬运、合箱和浇注过程中具有重要意义。 粘土型砂在烘干时,随着温度升高水分不断蒸发,砂粒之间 的距离不断地减少,质点间的附着力不断增大,因而使型砂 的干强度比湿强度大得多。 影响型砂干强度的主要因素:粘土加入量、含水量和烘 5 干规范
11
四、流动性
型砂在外力和本身重力的作用下,颗粒质点互相移动的能 力称为流动性。型砂流动性好易于紧实,铸型尺寸准确,表面 光洁,造型效率高,易于实现造型、制芯机械化。
型砂流动性主要取决于原砂颗粒特性、粘结剂的种 类及加入量、含水量及混砂质量等
五、发气性
型(芯)砂在高温作用下产生气体的能力称为发气性, 一般用发气量来衡量。 发气量 发气速度 12
六、不沾模性
型砂不沾附模样及芯盒表面的性能称为不沾模性。 沾模性强的型砂,造型制芯不方便,生产率低,铸 件表面质量差。一般说来,型砂含水量愈高,型砂 与模样及芯盒的温度差愈大,则沾模就愈严重。
七、其它性能
(1)耐火度
型砂抵抗高温热作用的性能称为耐火度
(2)退让性:型砂在金属凝固、冷却过捏中,能相应
粘土湿型砂的混砂效率
当前高水平的混砂设备,混砂效率也不过是60~70%。
另一方面,从要求型砂适于造型的可紧实性看来,也 不应该让所有的活性粘土都充分吸水并混合均匀。
18
一、湿型砂的性能和配方特点 1.铸铁件湿型砂
手工造型和振压式机器造型用型砂的紧实率大多在50% 左右。由于铸铁型砂中含有煤粉及失效煤粉,单一砂和 面砂中又都有大量旧砂。型砂中泥分含量常达12%-16 %(质量分数),能吸收多量水份。所以,型砂含水量通 常高达4.5%一6%(质量分数)。 一般铸铁件的湿型砂,用发气量测出的有效煤粉含量( 按质量分数计)在5%-8%左右。但对于薄壁小件,型砂 中有效煤粉只需3%-4%即可。煤粉含量是否适当,可 根据铸态铸件表面情况来判断,如果铸件表面有粘砂, 可能是表面透气性过高或有效煤粉不足。如铸件表面光 19 洁且呈蓝色,则表明煤粉可能已过量,应核对型砂的发 气量,并适当减少煤粉加入量。
粘土型(芯)砂
Ⅰ、粘土型(芯)砂的性能及其影响因素
型砂应具备的性能很多,其中直接影响铸件质量的 有:型砂的湿度、强度、透气性、发气性、耐火度、 退让性和导热性等。影响铸件劳动生产率,同时也 影响铸件质量的有:型的流动性、可塑性、吸湿 性、不沾模性、出砂性及复用性等。
湿度(含水量)、湿压强度、透气性、粘土含 量、吸蓝量(有效膨润土含量)
4.高密度造型型砂
(1)高密度造型特点 高密度造型是指提高造型紧实力制得较高紧实程度或较高 密度砂型的造型方法而言。过去高密度造型只指各种高压造 型。近十多年来,高速的冲击造型包括动力(机械)冲击和气 流冲击造型得到了越来越广泛的开发相应用,也属高密度造 型。 一般认为,压实比压高到0.7MPa以上称为高压造型,用 此法生产出来的铸件不仅尺寸精度高,表面粗糙度大大改善 ,而且能使铸件更加致密,力学性能更高,加工余量减少, 铸件质量减轻,劳动条件改善,生产率大大提高等。 高压造型中,由于其不良的砂型强度分布;另外,随着压 实比压的提高,还可能引起“水爆炸”,从而会出现型壁移 动,并使铸件产生气孔、局部表面粗糙和机械粘砂、甚至整 24 个铸件表面粘砂等缺陷 。
9
(二)透气性的测定原理
10
三、可塑性与韧性
可塑性是指型砂在外力作用下变形,外力去除后仍保持 所赋予形状的能力。可塑性好的型砂,造型起模修型方 便,铸件表面质量较高。一般情况下,凡是增加型砂湿 强度的因素,均可使可塑性提高。 韧性是指型砂抵抗外力破坏的性能。它是材料强度 与变形量的总合。韧性差的型砂起模时铸型容易损坏。 增加粘土加入量和相应地增加含水量可明显地提高型砂 的韧性。增加型砂中失效粘土和粉尘的含量,将使型砂 的变形量显著减小,韧性变差,起模困难。
(五)热湿拉强度
型砂试样在高温急速加热时 所形成的水分凝聚区的拉伸 强度称为热湿拉强度。
型砂热湿拉强度是衡量型 砂抗膨胀能力的重要性能 指标。
7
二、透气性
型砂使气体逸出的能力称为透气性。
(一)影响型砂透气性的因素 (1)原砂的颗粒特性
8
(2)水分 (3)粘土 4)附加物、混砂工艺及紧实度
型砂透气性峰值时 的含水量比湿压强 度峰值时的含水量 多。
二、湿型砂的混制工艺
有些工厂常用的加料顺序是先将回用砂和新砂、粘土粉、 煤粉等干料混匀,再加水混合至要求的水分。如果型砂中 含有渣油液,则渣油液应在加水混匀后加入。加渣油液后 的混碾时间不要太长,只要混匀即可。这种先加干料后加 水的顺序会带来一些问题,当回用砂较干时则更是这样。 因为干料很难混匀,在碾盘边缘会遗留一些粉料未被混合。 这些粉料吸水后,在混碾的后期和卸砂时才脱落,使在型 砂中混有一些粘土和煤粉团块。如果先向回用砂中加水, 则水可在砂粒上形成水膜,再加入粘土就能更快地分散在 砂粒上,强度的发展较快。此外,先混干料会使粉尘飞扬, 恶化劳动条件。因此通常认为加料顺序宜先加砂和水,湿 混后再加粘土和煤粉混匀,最后加少量水调整紧实率,可 27 以更快地达到预定的型砂性能,缩短混砂时间。
对湿型砂而言,混砂时严格控制加水量是 必要的。工厂中常用的加水量控制办法有 以下几种: ①人工加水。 ②定量水箱、定量水表、时间继电器控制 电磁水阀。边测量、边控制。
28
三、型砂的质量检验和控制
通过型砂的质量检验和宏观控制,不但可了解型砂 是否达到要求的性能,而且还可掌握型砂在使用中 的变化,这样就能及早采取措施,保证型砂符合要 求和保持稳定,保证铸件质量,预防缺陷产生。 试验结果的综合分析 每次取样测出的型砂性能,常在一定范围内波动, 故一次试验结果还不能说明问题,应取每天试验结果 的平均值,才能较好地代表整个型砂系统的状况。
地变形、退让而不阻碍铸件收缩的性能称为退让性。 退让性主要取决于型砂的高温强度,高温强度愈大退让 为愈差。 13 (3)复用性:型砂复用性又称耐用性。它指型砂经多 次使用仍保持原来性能的能力。
八、水分、最适宜干湿程度和紧实率
水分不足,型砂太干时,型砂强度低,韧性和可 塑性差,砂型易破碎,不易起模,铸件易产生冲砂、 砂眼等缺陷。水分高时,可塑性和韧性虽好,但湿 强度却较低,砂型易变形,铸件薄处可能浇不足, 厚处则表面粗糙,易产生夹砂缺陷。型砂过湿,干 强度和热强度则过大,会使退让性太差,铸件产生 裂纹,也使落砂困难。故控制型砂适宜水分十分重 要。
29
30
粘土湿型砂及其控制要点
砂处理系统 包括: 回收砂的处理、 新砂及辅助材 料的加入、 型砂的混制 型砂性能的监 控。
31
铸铁湿型单一砂循环过程示意图
一、粘土湿型砂的特性
粘土膏属半固态性质,粘度很高,难以混匀
粘土湿型砂理想的砂粒结构
用新砂配制的粘土湿型砂砂粒结构示意图
32
粘土湿型砂的砂粒结构
3.有色合金用湿型砂
生产中应用最多的铸造有色合金是铜合金、铝合金和镁合金。 主要要求型砂能防止金属液渗入铸型和制得的铸件表面光洁 清晰美观。原砂粒度大多较细,为10Q的硅砂或天然粘土砂。 天然粘土砂中加入适量水后具有良好的塑性和一定的湿强度。 铝合金液较轻,使用天然粘土砂时要注意控制含水量,以 免由于型砂透气性低而造成呛火和气孔缺陷。铝合金的浇注 温度低,热容量小,对砂粒和粘结剂的破坏少,型砂可反复 应用。 为了防止燃烧,型砂中含水量应尽可能低。过去在型砂中 还要加入硼酸、硫磺和氮化物作保护剂,以形成保护性气体 和保护膜防止镁被氧化和燃烧,但在浇注后产生大量有毒气 体。现在国内工厂已改用含有硼酸、菱镁矿和烷基磺酸钠等 23 附加物的“无毒型砂”,其毒性小,烟气少,对镁合金有良 好的保护效果。
(三)高温强度
型砂高温强度又称热强度, 是指型砂在高温作用下的强 度
影响粘土型砂高温强度的主要因 素有:粘土的种类及加入量、湿 态含水量、附加物的性质及加入 量等。
6
(四)表面强度
系指铸型或砂芯的表层强度。
提高铸型和砂芯的表面强度的两种方法:一是采用颗 粒分散的原砂、增加粘土加入量、采用膨润土代替普 通粘土等以提高型砂的整体强度;二是在铸型或砂芯 表面喷刷涂料。
3)透气性。高密度造型的砂粒排列比较密实,所以要求透气 性稍微高些。多数集中于100-120。 4)抗夹砂结疤能力。高密度造型的紧实程度高,所以希望 型砂具有较好的抗夹砂结疤能力,工厂根据铸件的特点不 同,对型砂的热湿拉强度有不同的要求。普通铸件用型砂 热湿拉强度一般为1.0-2.0kPa,较敏感铸件用型砂有时要求 >2.5kPa。因此在选用粘土时,可以混合使用钙质和钠质 膨润土,或是全部采用质量优良的钠质膨润土或活化膨润 土。 5)抗机械粘砂能力。由于高密度造型的砂型比较紧实,生 产铸铁件时可以降低型砂中的有效煤粉含量。这对于防止 呛火和火爆炸粘砂也有好处。一些工厂使用的型砂实际煤 粉含量大体在3%-6%(质量分数)范围内,典型的为挥发物 26 约2.o%,灼烧减量约6.o%。