碳纤维复合材料在轻量化的应用和前景
碳纤维复合材料在汽车上的应用

碳纤维复合材料在汽车上的应用随着汽车工业的不断发展和技术的不断进步,碳纤维复合材料在汽车制造领域中的应用越来越广泛。
碳纤维复合材料以其优异的强度、轻量化特性和耐腐蚀性能,成为了汽车制造中的重要材料之一。
碳纤维复合材料在汽车上的应用可以实现汽车的轻量化。
传统的金属材料相比,碳纤维复合材料具有更高的比强度和比刚度,可以在减少重量的同时保持车辆的结构强度,提高汽车的燃油效率。
轻量化设计不仅可以减少燃油消耗,还可以减少排放,降低对环境的影响。
碳纤维复合材料具有优异的抗腐蚀性能,可以延长汽车的使用寿命。
在恶劣的环境条件下,传统金属材料容易受到腐蚀的影响,导致汽车零部件的损坏。
而碳纤维复合材料具有良好的耐腐蚀性能,可以有效地抵抗酸碱腐蚀,延长汽车零部件的使用寿命。
碳纤维复合材料还可以提高汽车的安全性能。
碳纤维复合材料具有良好的吸能性能,可以在碰撞事故中有效地吸收冲击能量,保护车辆内部乘客的安全。
与传统金属材料相比,碳纤维复合材料具有更好的吸能性能,可以减少碰撞事故对车辆和乘客造成的损害。
除此之外,碳纤维复合材料还可以提高汽车的外观设计和性能表现。
碳纤维复合材料具有高强度、高刚度和优异的外观质感,可以为汽车提供更加时尚、动感的外观设计。
同时,碳纤维复合材料的优异性能也可以提升汽车的加速性能、操控性能和稳定性能,提升驾驶体验。
碳纤维复合材料在汽车上的应用具有广阔的发展前景和重要意义。
通过在汽车制造中广泛应用碳纤维复合材料,可以实现汽车的轻量化、节能减排,提高汽车的安全性能和外观设计,为汽车工业的可持续发展做出贡献。
相信随着技术的不断进步和应用的不断扩大,碳纤维复合材料在汽车制造领域中的地位将会日益重要,为汽车行业带来更多的创新和发展机遇。
cfrp成型技术在汽车轻量化中的应用-概述说明以及解释
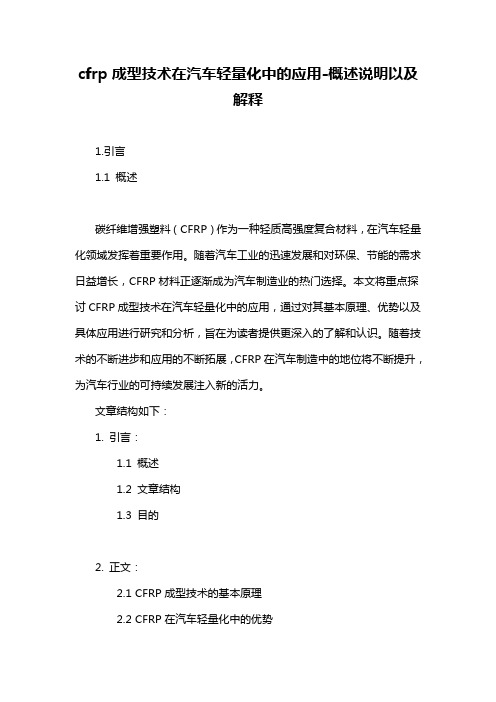
cfrp成型技术在汽车轻量化中的应用-概述说明以及解释1.引言1.1 概述碳纤维增强塑料(CFRP)作为一种轻质高强度复合材料,在汽车轻量化领域发挥着重要作用。
随着汽车工业的迅速发展和对环保、节能的需求日益增长,CFRP材料正逐渐成为汽车制造业的热门选择。
本文将重点探讨CFRP成型技术在汽车轻量化中的应用,通过对其基本原理、优势以及具体应用进行研究和分析,旨在为读者提供更深入的了解和认识。
随着技术的不断进步和应用的不断拓展,CFRP在汽车制造中的地位将不断提升,为汽车行业的可持续发展注入新的活力。
文章结构如下:1. 引言:1.1 概述1.2 文章结构1.3 目的2. 正文:2.1 CFRP成型技术的基本原理2.2 CFRP在汽车轻量化中的优势2.3 CFRP成型技术在汽车制造中的具体应用3. 结论:3.1 总结3.2 展望3.3 结论每个部分将详细探讨CFRP成型技术在汽车轻量化中的应用,并对其基本原理、优势以及具体应用进行深入分析和讨论。
最后总结文章内容,并展望CFRP成型技术在未来的发展趋势和应用前景。
1.3 目的本文旨在探讨CFRP成型技术在汽车轻量化领域的应用,分析其基本原理、优势以及具体应用情况。
通过对CFRP在汽车制造中的应用进行深入研究,旨在为汽车制造企业提供更多关于轻量化技术的参考,促进汽车制造业的发展和创新。
同时,通过本文的撰写,也旨在普及和推广CFRP 成型技术在汽车行业的应用,引领汽车制造业向更加节能环保和高效的方向发展。
2.正文2.1 CFRP成型技术的基本原理碳纤维增强复合材料(CFRP)是一种由碳纤维和树脂共同构成的高强度、轻质材料。
CFRP成型技术是指将碳纤维和树脂进行特定的配置和加工,以制造出具有特定形状和性能的零部件和构件。
其基本原理包括以下几个关键步骤:1. 碳纤维预处理:首先对碳纤维进行表面处理,以增强其与树脂的粘接性和机械性能。
通常采用的预处理方法包括表面氧化、涂覆树脂等。
碳纤维复合材料的研究及其应用前景
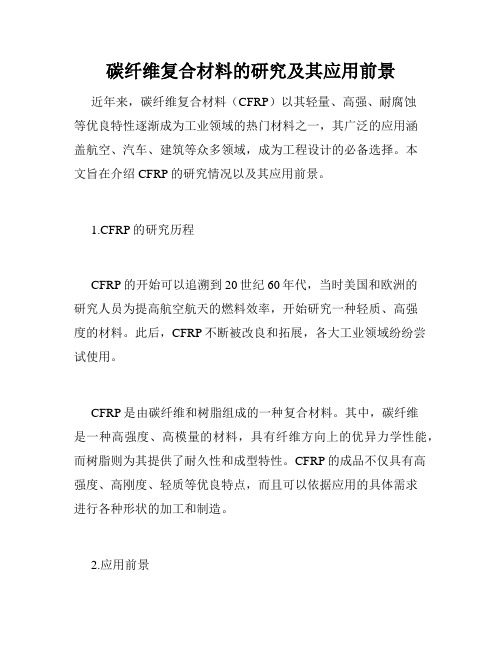
碳纤维复合材料的研究及其应用前景近年来,碳纤维复合材料(CFRP)以其轻量、高强、耐腐蚀等优良特性逐渐成为工业领域的热门材料之一,其广泛的应用涵盖航空、汽车、建筑等众多领域,成为工程设计的必备选择。
本文旨在介绍CFRP的研究情况以及其应用前景。
1.CFRP的研究历程CFRP的开始可以追溯到20世纪60年代,当时美国和欧洲的研究人员为提高航空航天的燃料效率,开始研究一种轻质、高强度的材料。
此后,CFRP不断被改良和拓展,各大工业领域纷纷尝试使用。
CFRP是由碳纤维和树脂组成的一种复合材料。
其中,碳纤维是一种高强度、高模量的材料,具有纤维方向上的优异力学性能,而树脂则为其提供了耐久性和成型特性。
CFRP的成品不仅具有高强度、高刚度、轻质等优良特点,而且可以依据应用的具体需求进行各种形状的加工和制造。
2.应用前景(1)航空航天领域在航空领域,CFRP被广泛应用于飞机、导弹和卫星等组件的制造。
相比传统金属材料,CFRP能够降低构件的重量和阻力,提高飞行性能,达到环保和节能的效果。
其中,波音787客机就采用了50%的CFRP材料,使得飞机的油耗显著降低,从而带来了较大的经济效益。
(2)汽车制造在汽车领域,CFRP被广泛用于轻量化设计,即通过将材料本身的重量减轻来提高汽车的油耗和性能。
例如,宝马公司推出了i3和i8两款车型,其中大量采用了CFRP材料,其车身重量仅有传统汽车的1/3,从而提高了燃料利用率、动力性能和行驶舒适度。
(3)建筑领域在建筑领域,CFRP广泛应用于桥梁和构造物的加固和修复。
由于CFRP具有超强的耐久性和防腐蚀性能,使其可以延长桥梁的使用寿命,降低维修费用。
此外,CFRP还可以实现建筑构造的轻质化设计,增强抗震能力。
(4)其他领域除了上述领域,CFRP还被应用于船舶制造、体育器材、医疗设备等领域,拓展了其应用范围和市场规模。
3.总结综上所述,CFRP作为一种具有广泛应用前景的高科技材料,能够在航空航天、汽车、建筑等领域带来显著的改善。
碳纤维轻量化

碳纤维轻量化碳纤维轻量化是近年来工业界和科技界研究的热点之一。
碳纤维是一种高强度、高模量、低密度的材料,具有优异的力学性能和化学稳定性,被广泛应用于航空、航天、汽车、体育器材等领域。
碳纤维轻量化的研究旨在通过减少材料的重量,提高产品的性能和效率,降低能源消耗和环境污染。
碳纤维轻量化的优势主要体现在以下几个方面:1. 提高产品性能和效率:碳纤维具有高强度、高模量、低密度等优异的力学性能,可以提高产品的强度、刚度和耐久性,同时减少产品的重量,提高产品的效率和性能。
2. 降低能源消耗和环境污染:碳纤维轻量化可以减少产品的重量,降低能源消耗和排放,同时减少废弃物的产生,降低环境污染。
3. 提高产品的设计自由度:碳纤维可以制成各种形状和尺寸的复合材料,可以满足不同产品的设计要求,提高产品的设计自由度和灵活性。
碳纤维轻量化的应用碳纤维轻量化已经广泛应用于航空、航天、汽车、体育器材等领域。
以下是一些典型的应用案例:1. 航空航天领域:碳纤维轻量化在航空航天领域的应用非常广泛,如飞机机身、机翼、尾翼、发动机罩等部件都可以采用碳纤维复合材料制造,可以减轻飞机的重量,提高飞机的性能和效率。
2. 汽车领域:碳纤维轻量化在汽车领域的应用也越来越广泛,如车身、底盘、发动机罩、轮毂等部件都可以采用碳纤维复合材料制造,可以减轻汽车的重量,提高汽车的燃油经济性和性能。
3. 体育器材领域:碳纤维轻量化在体育器材领域的应用也非常广泛,如高尔夫球杆、网球拍、自行车车架、滑雪板等器材都可以采用碳纤维复合材料制造,可以提高器材的强度、刚度和耐久性,同时减轻器材的重量,提高运动员的表现和效率。
碳纤维轻量化的挑战碳纤维轻量化虽然具有很多优势,但也面临着一些挑战,主要包括以下几个方面:1. 成本问题:碳纤维的制造成本较高,目前仍然是一种高端材料,限制了其在大规模应用中的推广和应用。
2. 生产工艺问题:碳纤维的生产工艺比较复杂,需要高温高压等特殊条件,生产周期较长,限制了其产量和应用范围。
碳纤维复合材料在新能源汽车中的应用研究
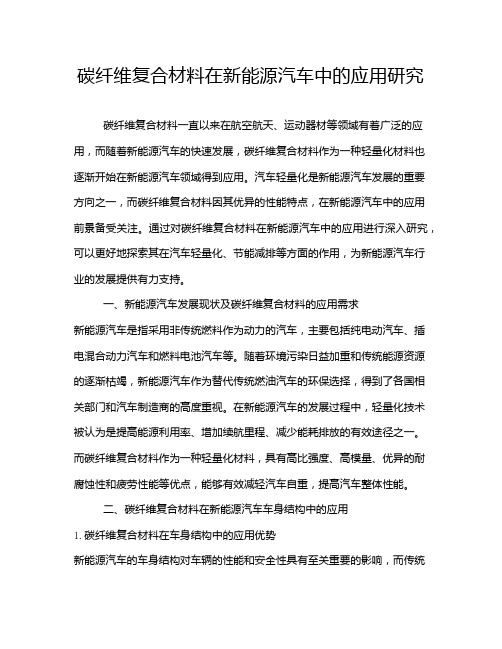
碳纤维复合材料在新能源汽车中的应用研究碳纤维复合材料一直以来在航空航天、运动器材等领域有着广泛的应用,而随着新能源汽车的快速发展,碳纤维复合材料作为一种轻量化材料也逐渐开始在新能源汽车领域得到应用。
汽车轻量化是新能源汽车发展的重要方向之一,而碳纤维复合材料因其优异的性能特点,在新能源汽车中的应用前景备受关注。
通过对碳纤维复合材料在新能源汽车中的应用进行深入研究,可以更好地探索其在汽车轻量化、节能减排等方面的作用,为新能源汽车行业的发展提供有力支持。
一、新能源汽车发展现状及碳纤维复合材料的应用需求新能源汽车是指采用非传统燃料作为动力的汽车,主要包括纯电动汽车、插电混合动力汽车和燃料电池汽车等。
随着环境污染日益加重和传统能源资源的逐渐枯竭,新能源汽车作为替代传统燃油汽车的环保选择,得到了各国相关部门和汽车制造商的高度重视。
在新能源汽车的发展过程中,轻量化技术被认为是提高能源利用率、增加续航里程、减少能耗排放的有效途径之一。
而碳纤维复合材料作为一种轻量化材料,具有高比强度、高模量、优异的耐腐蚀性和疲劳性能等优点,能够有效减轻汽车自重,提高汽车整体性能。
二、碳纤维复合材料在新能源汽车车身结构中的应用1.碳纤维复合材料在车身结构中的应用优势新能源汽车的车身结构对车辆的性能和安全性具有至关重要的影响,而传统的金属车身结构存在着重量较重、成本较高、制造复杂等问题。
碳纤维复合材料由碳纤维和树脂基体组成,具有轻质高强的特点,可以替代部分传统金属材料,有效降低车身自重,提高车辆整体性能。
此外,碳纤维复合材料还具有优异的抗腐蚀性和疲劳性能,延长了车身使用寿命,降低了维护成本。
2.碳纤维复合材料在车身结构中的具体应用在新能源汽车车身结构中,碳纤维复合材料通常应用于车身前部的防撞梁、车顶、车门、车盖等部位。
通过在这些部位使用碳纤维复合材料,可以有效减轻车身自重,提高车辆的燃油经济性和续航里程,同时还能提高车身的抗撞击性能和安全性。
2023年碳纤维复合材料行业市场环境分析

2023年碳纤维复合材料行业市场环境分析随着全球经济的发展,在许多行业中,碳纤维复合材料(CFRP)已成为非常重要的材料。
CFRP由碳纤维和树脂基材料组合而成,具有轻量化、高强度、高耐腐蚀性、良好的疲劳性能和优异的刚度。
因此,它被广泛应用于航空、航天、汽车、建筑等领域。
市场环境分析:1. 消费者需求不断增长随着可持续发展的趋势,消费者对环保、节能、高品质的需求越来越高,这为CFRP 的广泛应用提供了机会。
例如,在汽车和航空领域,为了降低能耗、减少排放、提高性能,CFRP已经成为制造轻量化的重要解决方案。
2. 政策支持提高市场规模许多国家已经制定了政策鼓励以及对CFRP的发展进行了资金支持。
例如,美国能源部正在为汽车领域CFRP的研发提供3亿美元的资金支持,鼓励其广泛应用于汽车制造中。
这些政策和资金支持将进一步提高CFRP的市场规模。
3. 制造技术的发展加速了市场进程CFRP的制造技术越来越成熟,越来越多的公司在投入研发方面进行了重大投资。
例如,BMW、奥迪等汽车厂商已经投入数亿美元用于CFRP的生产,而NASA和空客等航天和航空公司也在持续大规模投入CFRP的研发和制造。
4. 市场竞争日趋激烈在CFRP的应用领域,竞争对手越来越多,市场竞争日趋激烈。
因此,企业必须通过提供高品质、低成本的产品来占领市场份额。
随着制造技术的不断进步,越来越多的企业将进入CFRP制造行业,从而进一步加剧市场竞争。
总之,CFRP在未来的市场环境中将继续保持强劲的增长态势,随着技术的不断进步和政策支持的增加,CFRP的应用领域将越来越广泛,并促进市场规模的持续扩大。
然而,企业必须不断提高产品品质、降低生产成本、强化市场竞争能力才能在市场中获得成功。
碳纤维复合材料的介绍

碳纤维复合材料的介绍碳纤维复合材料是一种由碳纤维和基体树脂组成的复合材料。
碳纤维是一种高强度、高模量的纤维材料,具有轻质、耐热、耐腐蚀等优点,广泛应用于航空航天、汽车、体育器材等领域。
碳纤维复合材料的制备过程主要包括纤维预处理、树脂浸渍、层压成型等步骤。
首先,碳纤维要经过预处理,包括去除杂质、改善表面粗糙度等工艺,以提高纤维与树脂的粘结力。
然后,将预处理后的碳纤维放置在树脂浸渍装置中,通过真空或压力使树脂浸润纤维,形成树脂基体。
最后,将浸润树脂的碳纤维层叠在一起,并经过热压或压力固化,形成最终的碳纤维复合材料。
碳纤维复合材料具有许多优点。
首先,它具有高强度和高模量的特性,比重量相同的金属材料强度更高。
其次,碳纤维具有良好的耐腐蚀性能,不易受化学物质侵蚀。
此外,碳纤维还具有优异的热稳定性和耐高温性能,可以在高温环境下保持其强度和刚度。
此外,碳纤维复合材料还具有良好的电磁屏蔽性能和低热膨胀系数,适用于一些特殊领域的应用。
碳纤维复合材料广泛应用于航空航天领域。
由于其轻质高强的特性,能够减轻飞机的重量,提高燃油效率,降低碳排放。
同时,碳纤维复合材料还具有良好的抗疲劳性能和耐腐蚀性能,能够提高飞机的使用寿命。
因此,在飞机结构中应用碳纤维复合材料可以提高飞机的性能和安全性。
在汽车领域,碳纤维复合材料也得到了广泛应用。
与传统的金属材料相比,碳纤维复合材料具有更低的密度和更高的强度,可以实现汽车的轻量化设计。
轻量化不仅可以提高汽车的燃油效率,减少尾气排放,还可以提高汽车的操控性能和舒适性。
此外,碳纤维复合材料还具有良好的吸能性能,能够提高汽车的碰撞安全性。
碳纤维复合材料还广泛应用于体育器材制造。
例如,高尔夫球杆、网球拍等体育器材常使用碳纤维复合材料制造。
由于碳纤维具有轻质高强的特性,可以使器材更轻便、更易于操作,提高运动员的竞技水平。
此外,碳纤维复合材料还具有良好的振动吸收性能,可以减少运动时的手部震动,减少运动损伤。
碳纤维材料的研究进展与应用前景
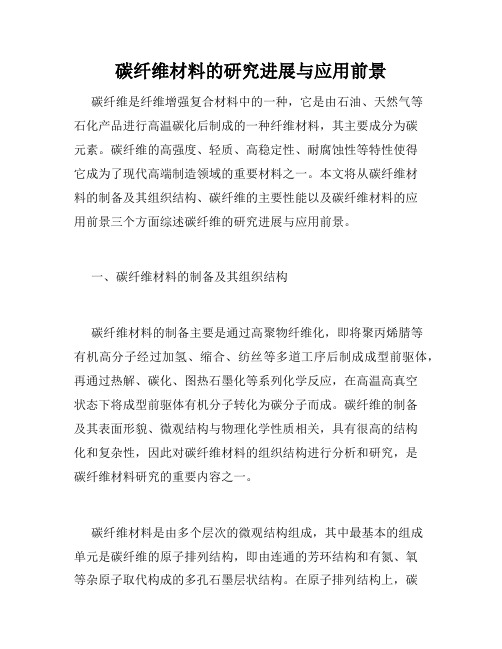
碳纤维材料的研究进展与应用前景碳纤维是纤维增强复合材料中的一种,它是由石油、天然气等石化产品进行高温碳化后制成的一种纤维材料,其主要成分为碳元素。
碳纤维的高强度、轻质、高稳定性、耐腐蚀性等特性使得它成为了现代高端制造领域的重要材料之一。
本文将从碳纤维材料的制备及其组织结构、碳纤维的主要性能以及碳纤维材料的应用前景三个方面综述碳纤维的研究进展与应用前景。
一、碳纤维材料的制备及其组织结构碳纤维材料的制备主要是通过高聚物纤维化,即将聚丙烯腈等有机高分子经过加氢、缩合、纺丝等多道工序后制成成型前驱体,再通过热解、碳化、图热石墨化等系列化学反应,在高温高真空状态下将成型前驱体有机分子转化为碳分子而成。
碳纤维的制备及其表面形貌、微观结构与物理化学性质相关,具有很高的结构化和复杂性,因此对碳纤维材料的组织结构进行分析和研究,是碳纤维材料研究的重要内容之一。
碳纤维材料是由多个层次的微观结构组成,其中最基本的组成单元是碳纤维的原子排列结构,即由连通的芳环结构和有氮、氧等杂原子取代构成的多孔石墨层状结构。
在原子排列结构上,碳纤维材料由平行排列的基础单元堆积而成,具有方向性,呈现出丝状或丝带状等形态。
在材料的宏观结构中,碳纤维材料通常具有纤维状或薄片状形态等。
而碳纤维材料的微观结构是决定性因素,其成长行为和杂原子的存在对碳纤维的性能起到了显著影响。
二、碳纤维的主要性能碳纤维的主要特点是高强度、高模量和高韧性。
碳纤维的强度与其成型前驱体的纤维化程度、加工工艺、化学反应以及表面形貌、微观结构的稳定性等相关。
碳纤维的高强度主要来自于其成型前驱体的内部结构,在碳化过程中生成的“石墨化”的结构与碳分子的排列等也决定了其宏观强度,同时碳纤维的强度与杂原子的存在、石墨晶体的孔隙率、石墨结晶组织的大小以及结晶方向的一致性等也有关系。
碳纤维的高模量来自于其硬质碳化结构,碳纤维的碳化程度越高,其模量也越大。
此外,碳纤维的弹性模量与其成型前驱体的聚合度、纤维结构和方向等因素也有很大的关系。
碳纤维复合材料应用

碳纤维复合材料应用碳纤维复合材料是一种由碳纤维和树脂等材料组合而成的高强度、轻质材料,具有优异的机械性能和耐腐蚀性能。
由于其独特的性能,碳纤维复合材料在航空航天、汽车制造、体育器材、建筑工程等领域得到了广泛的应用。
首先,碳纤维复合材料在航空航天领域的应用十分广泛。
由于碳纤维复合材料具有优异的强度和刚度,同时又非常轻,因此被广泛应用于航空航天领域的飞机结构件制造中。
例如,飞机的机身、机翼和尾翼等部件都可以采用碳纤维复合材料制造,以减轻飞机自重,提高飞行性能和燃油效率。
此外,碳纤维复合材料还可以用于制造航天器的热保护罩和结构件,以应对极端的高温和高速环境。
其次,汽车制造领域也是碳纤维复合材料的重要应用领域。
随着汽车工业的发展,轻量化技术成为了汽车制造的重要方向。
碳纤维复合材料因其轻质高强的特性,被广泛应用于汽车的车身和底盘等部件制造中。
采用碳纤维复合材料可以显著降低汽车的整车重量,提高汽车的燃油经济性和性能表现。
此外,碳纤维复合材料还可以用于制造汽车的内饰件和悬挂系统等部件,提高汽车的舒适性和安全性。
除此之外,碳纤维复合材料在体育器材领域也有着重要的应用。
例如,高尔夫球杆、网球拍、自行车和滑雪板等运动器材都可以采用碳纤维复合材料制造,以提高器材的强度和性能。
碳纤维复合材料制造的运动器材具有较低的重量和较高的强度,能够提高运动员的竞技水平,受到了运动爱好者的青睐。
此外,碳纤维复合材料还在建筑工程领域得到了广泛的应用。
由于其优异的耐腐蚀性能和高强度特性,碳纤维复合材料被用于加固和修复建筑结构。
例如,碳纤维复合材料可以用于加固桥梁、楼房和管道等结构,提高其承载能力和抗震能力。
此外,碳纤维复合材料还可以用于制造建筑外墙板和屋顶材料,提高建筑的耐久性和美观性。
综上所述,碳纤维复合材料具有广泛的应用前景,在航空航天、汽车制造、体育器材和建筑工程等领域都有着重要的应用价值。
随着科技的不断发展和碳纤维复合材料制造工艺的进步,相信碳纤维复合材料将会在更多领域展现其优异的性能和潜力。
碳纤维复合材料发展方向及前景综述

在当今世界,碳纤维复合材料作为一种轻量化、高强度的新型材料,已经在诸多领域展现出了巨大的发展潜力。
从航空航天到汽车制造,从体育器材到建筑材料,碳纤维复合材料都展现出了其独特的优势和潜力。
本文将对碳纤维复合材料的发展方向及前景进行综述,旨在帮助读者更全面、深刻地了解这一重要材料的未来走向。
1. 碳纤维复合材料的基本概念碳纤维复合材料是由碳纤维和树脂基体组成的复合材料。
碳纤维具有轻质、高强度、高模量、耐高温和耐腐蚀等优点。
而树脂基体则起着粘结和保护作用。
碳纤维复合材料的制备工艺主要包括预浸法、纺丝法和层压法等。
2. 碳纤维复合材料在航空航天领域的应用碳纤维复合材料在航空航天领域具有重要意义。
它们可以减轻飞机和航天器的重量,提高飞行性能,延长使用寿命,并且有利于节能减排。
未来的发展方向包括更高强度、更低密度的碳纤维复合材料的研发,以及更加智能化的制造工艺和设计方法。
3. 碳纤维复合材料在汽车制造领域的应用碳纤维复合材料在汽车制造领域也有着广阔的应用前景。
它们可以降低汽车的整体重量,提高燃油效率,增加汽车的安全性和舒适性。
未来汽车领域的发展方向包括降低碳纤维复合材料的成本,加快大规模生产工艺的研发,以及更加环保和可持续的材料回收利用方案。
4. 碳纤维复合材料在体育器材领域的应用在体育器材领域,碳纤维复合材料已经成为了许多高端器材的首选材料。
它们轻盈、坚固、具有良好的弹性和吸震性能,可以有效提高运动员的表现。
未来,随着运动科技的不断发展,碳纤维复合材料在体育器材领域的应用前景将会更加广阔。
5. 碳纤维复合材料在建筑材料领域的应用在建筑领域,碳纤维复合材料在结构加固、新型材料研发等方面具有广泛的应用前景。
它们具有较高的抗拉强度、抗压强度和耐久性能,可以提高建筑结构的安全性和耐久性,同时减轻结构自重,有利于节能减排。
总结回顾通过本文的综合介绍,我们可以看到碳纤维复合材料作为一种新型材料,具有广阔的应用前景和发展空间。
2023年碳纤维行业市场前景分析

2023年碳纤维行业市场前景分析
近年来,碳纤维作为一种新型复合材料,因其高强度、高模量、轻量化等优秀特性,得到了广泛的应用和关注,被誉为21世纪的“黑金属”,被广泛应用于航空航天、
高速铁路、汽车、船舶、建筑等行业领域。
在未来市场前景方面,碳纤维行业的发展将会出现如下几点趋势:
一、产业规模将持续扩大
随着碳纤维技术的不断进步和应用领域的不断扩展,碳纤维产业规模将持续扩大。
据预测,到2020年,全球碳纤维市场规模将超过40亿美元,年复合增长率将达到15%以上。
中国作为世界最大的制造业大国,碳纤维产业也将获得快速发展,加速向高品质、高附加值的产业方向转型升级。
二、应用领域将不断扩展
碳纤维目前的主要应用领域是航空航天、汽车、建筑等领域,而随着新兴产业的不断涌现,未来应用领域也将不断扩展。
例如,碳纤维船舶、碳纤维新能源领域的应用将逐渐得到推广和开发。
据估计,未来中国碳纤维市场最大的应用领域将是汽车、新能源、建筑、航空航天和体育器材等。
三、技术水平将不断提高
随着碳纤维应用领域的不断拓展,对碳纤维的性能和质量等方面提出了更高的要求,碳纤维技术水平也将不断提高。
目前,国内的碳纤维技术和质量水平已经取得了很大进步,但与国外先进水平相比还有差距。
未来碳纤维产业将会继续加强技术储备、提高自主创新能力,推动行业技术水平不断提高。
总之,碳纤维是一个发展前景广阔的新兴产业,在新材料、新能源、环保等方面都具有很大的应用前景。
随着技术的不断提高和应用范围的不断扩展,碳纤维产业将会迎来更加美好的发展前景。
浅析碳纤维复合材料的应用现状与发展趋势
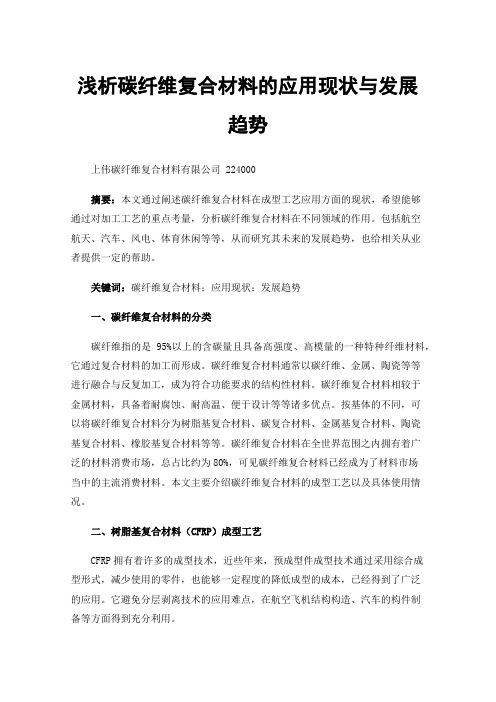
浅析碳纤维复合材料的应用现状与发展趋势上伟碳纤维复合材料有限公司 224000摘要:本文通过阐述碳纤维复合材料在成型工艺应用方面的现状,希望能够通过对加工工艺的重点考量,分析碳纤维复合材料在不同领域的作用。
包括航空航天、汽车、风电、体育休闲等等,从而研究其未来的发展趋势,也给相关从业者提供一定的帮助。
关键词:碳纤维复合材料;应用现状;发展趋势一、碳纤维复合材料的分类碳纤维指的是95%以上的含碳量且具备高强度、高模量的一种特种纤维材料,它通过复合材料的加工而形成。
碳纤维复合材料通常以碳纤维、金属、陶瓷等等进行融合与反复加工,成为符合功能要求的结构性材料。
碳纤维复合材料相较于金属材料,具备着耐腐蚀、耐高温、便于设计等等诸多优点。
按基体的不同,可以将碳纤维复合材料分为树脂基复合材料、碳复合材料、金属基复合材料、陶瓷基复合材料、橡胶基复合材料等等。
碳纤维复合材料在全世界范围之内拥有着广泛的材料消费市场,总占比约为80%,可见碳纤维复合材料已经成为了材料市场当中的主流消费材料。
本文主要介绍碳纤维复合材料的成型工艺以及具体使用情况。
二、树脂基复合材料(CFRP)成型工艺CFRP拥有着许多的成型技术,近些年来,预成型件成型技术通过采用综合成型形式,减少使用的零件,也能够一定程度的降低成型的成本,已经得到了广泛的应用。
它避免分层剥离技术的应用难点,在航空飞机结构构造、汽车的构件制备等方面得到充分利用。
2.1模压成型工艺模压成型是一种非常传统的工艺形式,它是由普通的塑料制品模压成型逐渐转化而来。
在加工的过程当中,通过将碳纤维预浸料置于上下模之间,从而利用专业的设备进行加工过程。
将模具放置在液压成型台上,在高温高压的作用之下,让树脂材料产生固化反应,得到最终的制品。
这种工艺加工形式具备着制件质量优、技术处理高效的优势,而且它能够在尺寸精度方面得到较高控制,且加工形式不易受周围环境的影响。
但是其总体的投入成本较高,也容易受到机械设备的限制,拥有着前期模具制造复杂的缺点[1]。
碳纤维性能优缺点及应用前景
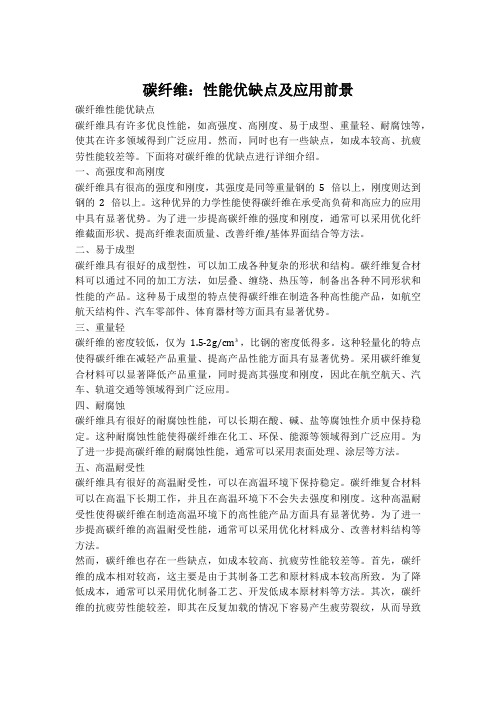
碳纤维:性能优缺点及应用前景碳纤维性能优缺点碳纤维具有许多优良性能,如高强度、高刚度、易于成型、重量轻、耐腐蚀等,使其在许多领域得到广泛应用。
然而,同时也有一些缺点,如成本较高、抗疲劳性能较差等。
下面将对碳纤维的优缺点进行详细介绍。
一、高强度和高刚度碳纤维具有很高的强度和刚度,其强度是同等重量钢的5倍以上,刚度则达到钢的2倍以上。
这种优异的力学性能使得碳纤维在承受高负荷和高应力的应用中具有显著优势。
为了进一步提高碳纤维的强度和刚度,通常可以采用优化纤维截面形状、提高纤维表面质量、改善纤维/基体界面结合等方法。
二、易于成型碳纤维具有很好的成型性,可以加工成各种复杂的形状和结构。
碳纤维复合材料可以通过不同的加工方法,如层叠、缠绕、热压等,制备出各种不同形状和性能的产品。
这种易于成型的特点使得碳纤维在制造各种高性能产品,如航空航天结构件、汽车零部件、体育器材等方面具有显著优势。
三、重量轻碳纤维的密度较低,仅为 1.5-2g/cm³,比钢的密度低得多。
这种轻量化的特点使得碳纤维在减轻产品重量、提高产品性能方面具有显著优势。
采用碳纤维复合材料可以显著降低产品重量,同时提高其强度和刚度,因此在航空航天、汽车、轨道交通等领域得到广泛应用。
四、耐腐蚀碳纤维具有很好的耐腐蚀性能,可以长期在酸、碱、盐等腐蚀性介质中保持稳定。
这种耐腐蚀性能使得碳纤维在化工、环保、能源等领域得到广泛应用。
为了进一步提高碳纤维的耐腐蚀性能,通常可以采用表面处理、涂层等方法。
五、高温耐受性碳纤维具有很好的高温耐受性,可以在高温环境下保持稳定。
碳纤维复合材料可以在高温下长期工作,并且在高温环境下不会失去强度和刚度。
这种高温耐受性使得碳纤维在制造高温环境下的高性能产品方面具有显著优势。
为了进一步提高碳纤维的高温耐受性能,通常可以采用优化材料成分、改善材料结构等方法。
然而,碳纤维也存在一些缺点,如成本较高、抗疲劳性能较差等。
首先,碳纤维的成本相对较高,这主要是由于其制备工艺和原材料成本较高所致。
2024年碳基复合材料市场前景分析

碳基复合材料市场前景分析引言碳基复合材料是一种具有轻质高强度、高温抗性和优异导热性能的先进材料。
随着全球经济的快速发展和科技进步,碳基复合材料市场正迅速扩大。
本文将对碳基复合材料市场的前景进行分析,并探讨其未来的潜力。
碳基复合材料市场的现状目前,碳基复合材料在航空航天、汽车、能源和电子等领域得到广泛应用。
碳纤维复合材料以其轻量化、高强度和优异阻燃性能,在航空航天领域具有巨大潜力。
汽车制造商也开始采用碳基复合材料来减轻汽车重量,提高燃油效率。
此外,碳基复合材料的热导性能使其成为高效散热的材料选择,因此在电子设备中的应用前景广阔。
碳基复合材料市场的驱动因素1.轻量化需求:随着全球经济的快速发展,对节能减排的需求日益增加。
碳基复合材料由于其轻质高强度的特性,被广泛应用于汽车、航空航天和能源等领域,以减轻重量,提高能源利用效率。
2.技术进步:碳纤维复合材料的生产技术和工艺不断改进,使其成本降低,生产效率提高,从而推动了碳基复合材料市场的发展。
3.可再生能源发展:碳基复合材料在风力和太阳能等可再生能源领域具有广泛的应用前景。
随着可再生能源的推广和发展,碳基复合材料市场将受益并持续增长。
碳基复合材料市场的挑战1.高成本:目前,碳基复合材料的制造成本较高,限制了其在一些领域的广泛应用。
2.市场竞争:碳纤维复合材料市场存在着激烈的竞争,来自于其他材料如铝、钢、塑料等,这些材料也在不断发展和改进,给碳基复合材料市场带来一定的压力。
碳基复合材料市场的未来发展尽管碳基复合材料市场面临一些挑战,但其仍具有广阔的发展前景。
1. 新兴应用领域:随着先进制造技术和新材料的不断涌现,碳基复合材料将在新兴领域如医疗、体育用品和建筑等领域得到更广泛的应用。
2. 技术创新:随着碳基复合材料生产技术的进一步改进和创新,其成本将进一步降低,推动市场规模的扩大。
3. 可持续发展:碳基复合材料的可持续性特点使其成为未来材料发展的重要方向,与可再生能源和环境保护相结合,将有更大的市场需求和潜力。
2024年碳纤维复合材料市场调查报告
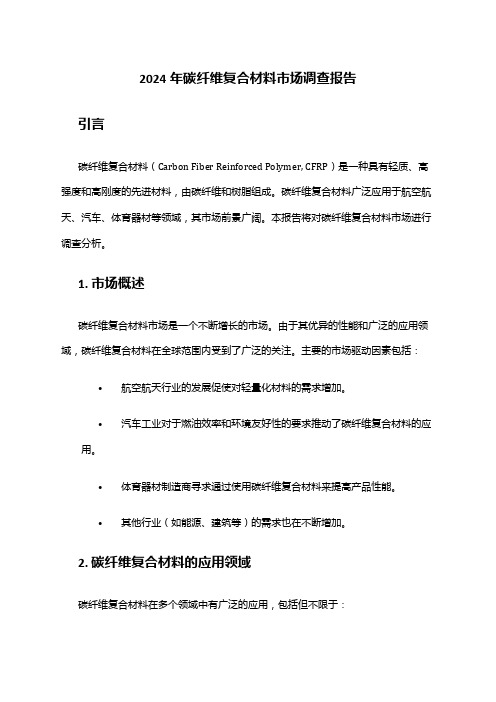
2024年碳纤维复合材料市场调查报告引言碳纤维复合材料(Carbon Fiber Reinforced Polymer, CFRP)是一种具有轻质、高强度和高刚度的先进材料,由碳纤维和树脂组成。
碳纤维复合材料广泛应用于航空航天、汽车、体育器材等领域,其市场前景广阔。
本报告将对碳纤维复合材料市场进行调查分析。
1. 市场概述碳纤维复合材料市场是一个不断增长的市场。
由于其优异的性能和广泛的应用领域,碳纤维复合材料在全球范围内受到了广泛的关注。
主要的市场驱动因素包括:•航空航天行业的发展促使对轻量化材料的需求增加。
•汽车工业对于燃油效率和环境友好性的要求推动了碳纤维复合材料的应用。
•体育器材制造商寻求通过使用碳纤维复合材料来提高产品性能。
•其他行业(如能源、建筑等)的需求也在不断增加。
2. 碳纤维复合材料的应用领域碳纤维复合材料在多个领域中有广泛的应用,包括但不限于:2.1 航空航天碳纤维复合材料在航空航天行业中的应用越来越广泛。
它的轻量化特性和高强度使得飞机更省油、更环保。
碳纤维复合材料被广泛用于飞机机身、翼面、尾翼等部件的制造。
2.2 汽车碳纤维复合材料在汽车制造中的应用也在不断增加。
通过使用碳纤维复合材料,汽车的重量可以减轻,从而提高燃油效率。
碳纤维复合材料被应用于车身、底盘、悬挂系统等部件的制造。
2.3 体育器材碳纤维复合材料在体育器材制造中有着广泛的应用。
使用碳纤维复合材料可以增加器材的强度和刚度,同时减轻重量。
碳纤维复合材料常被用于制造高尔夫球杆、网球拍、自行车车架等。
3. 市场竞争情况碳纤维复合材料市场竞争激烈,存在着多家主要供应商。
其中一些供应商包括:•Toray Industries•Hexcel Corporation•SGL Carbon•Mitsubishi Chemical Holdings Corporation这些供应商在碳纤维复合材料领域拥有雄厚的技术实力和丰富的经验,并且持续进行研发和创新来提高产品性能和降低成本。
碳纤维技术的应用和未来发展趋势
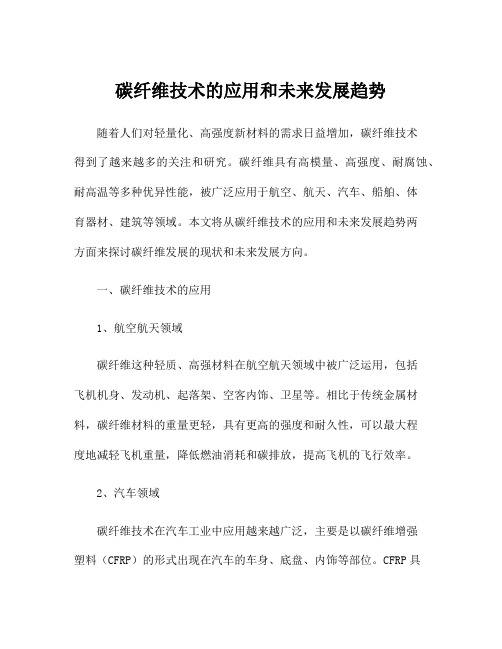
碳纤维技术的应用和未来发展趋势随着人们对轻量化、高强度新材料的需求日益增加,碳纤维技术得到了越来越多的关注和研究。
碳纤维具有高模量、高强度、耐腐蚀、耐高温等多种优异性能,被广泛应用于航空、航天、汽车、船舶、体育器材、建筑等领域。
本文将从碳纤维技术的应用和未来发展趋势两方面来探讨碳纤维发展的现状和未来发展方向。
一、碳纤维技术的应用1、航空航天领域碳纤维这种轻质、高强材料在航空航天领域中被广泛运用,包括飞机机身、发动机、起落架、空客内饰、卫星等。
相比于传统金属材料,碳纤维材料的重量更轻,具有更高的强度和耐久性,可以最大程度地减轻飞机重量,降低燃油消耗和碳排放,提高飞机的飞行效率。
2、汽车领域碳纤维技术在汽车工业中应用越来越广泛,主要是以碳纤维增强塑料(CFRP)的形式出现在汽车的车身、底盘、内饰等部位。
CFRP具有良好的强度、刚度和韧性,可以减轻汽车重量,提高汽车的燃油经济性和性能表现。
3、体育器材碳纤维技术在体育器材领域也得到了广泛应用,如高尔夫球杆、自行车、冰球杆、滑板等。
碳纤维材料的强度和轻量化特性可以使器材更加灵活、强度更高,提高运动员的表现和训练效果。
4、建筑领域碳纤维材料在建筑领域也具有广泛的应用前景,比如作为钢筋的替代品,可以用于建造高楼、桥梁和地下管道等设施,提高建筑结构的强度和稳定性。
二、碳纤维技术的未来发展趋势碳纤维技术目前还存在着一些问题,如生产成本高、生产周期长、可回收性差等。
因此,未来的碳纤维技术需要面对和解决这些问题,以推动碳纤维材料的更广泛应用。
1、生产成本下降高成本一直是制约碳纤维材料应用的一个制约因素。
未来随着生产技术的不断发展和成熟,碳纤维的生产成本将逐渐下降,从而更广泛的应用在各个领域中。
2、生产效率提高目前碳纤维材料的生产过程较为繁琐,需进行多次处理和加工。
未来随着技术的进步和趋势的推进,生产碳纤维材料的效率将得到大幅提高,这将使碳纤维材料的推广更为容易。
3、研究新的材料组合随着对碳纤维性能的深入研究,未来研究工作者将进一步探索碳纤维与其他材料的组合,以更好地发挥碳纤维的优点。
碳纤维复合材料的应用及其发展趋势

碳纤维复合材料的应用及其发展趋势碳纤维复合材料是由碳纤维和树脂基体组成的复合材料。
由于其轻质、高强度、高刚度和耐腐蚀等优点,广泛应用于航空航天、汽车、体育器材和建筑等领域。
在未来,碳纤维复合材料的应用将继续增加,且发展趋势主要包括以下几个方面。
首先,碳纤维复合材料在航空航天领域的应用将进一步扩大。
由于碳纤维复合材料的高强度和轻质特性,可以减少航空器的自重,提高燃油效率。
未来,碳纤维复合材料将在飞机机身、翼面和发动机部件等方面得到更广泛的应用,从而实现飞机的结构轻量化。
其次,碳纤维复合材料在汽车领域的应用将逐渐增加。
随着汽车工业的不断发展,对车辆轻量化的需求日益增加。
由于碳纤维复合材料具有较高的强度和刚度,并且重量轻,可以减少汽车的燃油消耗和排放量。
未来,碳纤维复合材料将在汽车车身、底盘和内饰等方面得到广泛应用,从而实现汽车整体的轻量化和节能减排。
此外,碳纤维复合材料在体育器材领域的应用也将持续增加。
碳纤维复合材料具有优异的强度和刚度,可以提高体育器材的性能,如高尔夫球杆、网球拍和自行车等。
未来,碳纤维复合材料将在体育器材制造中得到更广泛的应用,从而提高运动员的竞技水平和运动性能。
最后,碳纤维复合材料在建筑领域的应用也将逐渐增多。
由于碳纤维复合材料具有良好的抗拉性能和耐腐蚀性能,可以用于加固混凝土结构和制造轻型建筑材料。
在未来,碳纤维复合材料将在建筑工程领域得到更广泛的应用,从而提高建筑结构的安全性和耐久性。
总之,碳纤维复合材料的应用将在航空航天、汽车、体育器材和建筑等领域继续拓展。
随着科学技术的不断进步和人们对环境保护和能源节约的要求日益增加,碳纤维复合材料的发展趋势将更加明显。
未来,碳纤维复合材料将在材料科学领域起着至关重要的作用。
碳纤维与碳纤维复合材料

碳纤维与碳纤维复合材料碳纤维是一种由轻质高强度的碳元素组成的纳米级纤维。
由于其独特的物理和化学性质,碳纤维在各种领域得到了广泛的应用,特别是在航空航天、汽车、体育器材和建筑等领域。
同时,碳纤维也可以与其他材料进行复合,形成碳纤维复合材料,以进一步提高其性能和应用范围。
首先,碳纤维具有极高的强度和刚度。
与传统的金属材料相比,碳纤维的强度可以达到其重量的数倍。
这使得碳纤维成为制造轻量化产品的理想材料,尤其是在航空航天和汽车工业中。
通过使用碳纤维,可以减轻飞机和汽车的重量,提高燃油效率,并降低碳排放。
此外,碳纤维的高刚度也可以提供更好的结构稳定性和抗挠度,使得制造出的产品更加坚固和耐用。
其次,碳纤维具有良好的耐腐蚀性能。
与金属材料相比,碳纤维对酸、碱、盐等化学物质的抵抗能力更强。
这使得碳纤维复合材料成为一种理想的选择,以应对恶劣的环境条件和长期暴露下的腐蚀问题。
碳纤维复合材料可以在海水中长期使用而不会受到腐蚀,这使其在海洋工程、船舶和海上风电等领域中得到广泛应用。
此外,碳纤维还具有优异的导热性能和导电性能。
碳纤维可以作为导电线材和热导材料,广泛应用于电子和电气领域。
例如,碳纤维可以用于制造电池极板、传输导线和散热材料,以提高电子设备的性能和稳定性。
同时,由于碳纤维的导电性能,它还可以用于制造抗静电材料和地面静电材料,以保护电子设备和敏感元器件。
在碳纤维复合材料中,碳纤维通常与树脂等绑定材料结合使用。
树脂可以提供碳纤维所缺乏的韧性和防护能力,从而增强复合材料的整体性能。
其中,最常用的树脂是环氧树脂。
环氧树脂具有良好的粘接性能和耐久性,可以与碳纤维形成牢固的结合。
通过调整树脂的成分和结构,可以进一步改变碳纤维复合材料的性能,以满足特定的应用需求。
总的来说,碳纤维及碳纤维复合材料具有一系列独特的性能和特点,使其成为许多领域的理想材料选择。
随着技术的不断进步,碳纤维及其复合材料的应用前景也将更加广阔。
2023年碳纤维复合材料轮毂行业市场前景分析

2023年碳纤维复合材料轮毂行业市场前景分析随着汽车工业的发展,市场对于轻量化、高强度的需求也越来越大。
而碳纤维复合材料轮毂作为一种轻质、高强度材料,正逐渐受到汽车厂商以及车主的青睐。
本文将从行业现状、发展趋势及市场前景三个方面进行分析。
一、行业现状国内碳纤维复合材料轮毂制造商数量较少,主要有极地轮毂、三友轮毂、尚轮汽车等。
虽然国内碳纤维复合材料轮毂市场的规模较小,但随着汽车厂商对轻量化的需求增加,轮毂行业将迎来快速发展的机遇。
二、发展趋势1. 轻量化是未来发展趋势近年来,汽车行业对于轻量化的需求越来越高,而碳纤维复合材料轮毂就是一种轻量化的好选择。
碳纤维复合材料轮毂相比普通的金属轮毂,重量降低了30%以上,可以有效提高汽车的燃油效率、减少排放等。
2. 新材料技术的应用随着技术的进步,碳纤维复合材料轮毂的性能也得到了不断提升。
新材料技术的应用,将有助于碳纤维复合材料轮毂在强度、耐磨性等方面实现更大的突破,提高产品的竞争力。
3. 高端定制市场的需求增加随着汽车市场的日益成熟,消费者对个性化、定制化的需求也越来越高。
碳纤维复合材料轮毂作为高端轮毂,将会受到一些高端消费者的追捧,这也将成为市场的一个重要趋势。
三、市场前景碳纤维复合材料轮毂作为一种轻量化、高强度材料,将有望在未来的市场中发挥重要作用。
国内市场虽然规模有限,但在未来几年将会有大幅增长的趋势。
根据相关机构预测,到2025年,全球碳纤维轮毂的市场规模有望达到100亿美元以上。
目前,国际上碳纤维复合材料轮毂市场主要由欧美厂商垄断,国内企业还有较大的发展空间。
总之,碳纤维复合材料轮毂市场前景广阔。
随着汽车工业的不断发展和技术的提升,碳纤维复合材料轮毂将保持持续的增长态势,并成为汽车行业的一个重要发展方向。
- 1、下载文档前请自行甄别文档内容的完整性,平台不提供额外的编辑、内容补充、找答案等附加服务。
- 2、"仅部分预览"的文档,不可在线预览部分如存在完整性等问题,可反馈申请退款(可完整预览的文档不适用该条件!)。
- 3、如文档侵犯您的权益,请联系客服反馈,我们会尽快为您处理(人工客服工作时间:9:00-18:30)。
碳纤维复合材料在轻量化的应用和前景摘要:碳纤维是一种含碳量在95%以上的高强度、高模量特种纤维,但几乎所有的碳纤维都将进一步加工成复合材料以供终端使用。
碳纤维复合材料是以碳纤维为增强材料,以树脂、金属、陶瓷等作为基体材料,经过复合成型制成的结构材料,与传统的金属材料相比,其具有密度小、比强度/比刚度高、耐腐蚀、抗疲劳、耐高温、便于设计、易于大面积整体成型加工等优点。
目前,碳纤维复合材料在我国的各个领域得到了广泛应用,基于此,文章对碳纤维复合材料在轻量化的应用于发展前景进行了研究,以供参考。
关键词:碳纤维复合材料;轻量化;应用研究1不同型号碳纤维对比碳纤维作为具有优越性质的复合材料之一,其具备高强度、高模量、耐腐蚀等性能,在军用及民用等方面均具有广阔的发展前景。
但由于国外碳纤维的研究起步较早,同时又受到来自美国、日本等国家的技术垄断,导致我国的碳纤维生产技术相对落后。
近年来,我国在碳纤维生产方面投入了大量资金,生产技术与研发等方面已取得阶段性成果。
本文分别选取了T700级碳纤维、T800级碳纤维和东丽T700级碳纤维对其性能进行对比研究。
1.1.T700级碳纤维国产T700级碳纤维表面相对粗糙,有颗粒依附,沟槽结构多,粗糙度较高,虽然有利于树脂基体之间浸润性的提高,但可能会降低产品性能的稳定性;表面氧碳含量较高有利于与树脂基体的结合;界面剪切强度与层间剪切强度相对较高,与进口碳纤维的力学特性不相上下;产品价格低于进口碳纤维,较高的性价比有利于提升其在碳纤维市场的竞争力。
1.1.T800级碳纤维国产T800级碳纤维表面较为光滑,沟槽结构浅而细,凸起结构较少,产品性能较稳定;表面含氧量较高,能够有效提高表面的化学活性;可以表明:国产T800级碳纤维界面剪切强度、拉伸强度相对较高,其具有良好的力学性能。
另一方面国产T800级碳纤维质量控制较稳定,与环氧树脂融合性较好。
1.3东丽T700级碳纤维东丽T700碳纤维分为T700S和T700G两种型号。
T700S型号表面光滑,无明显沟槽结构,凸起结构少,拉伸模量高;表面石墨化程度高,碳纤维排布有序度高,提高了碳纤维的拉伸模量;碳纤维界面剪切强度高,力学性能优越。
而T700G 在T700S的基础上提升了碳纤维的模量和性能,应用更加广泛,市场竞争的优势会更大。
2碳纤维复合材料成型工艺2.1模压成型工艺模压成型是复合材料生产中一种传统常用的成型方法,由普通的塑料制品模压成型演变而来。
工艺流程为:将碳纤维预浸料置于上下模之间,合模将模具置于液压成型台上,经过一定时间的高温高压使树脂固化后,取下CFRP制品。
这种成型技术具有高效、制件质量好、尺寸精度高、受环境影响小等优点,适用于批量化、强度高的复合材料制件的成型,其缺点是前期模具制造复杂,投入高,且制件大小受压机尺寸的限制。
2.2热压罐成型工艺热压罐成型是最早开发用于航空结构复合材料制造并仍普遍使用的一种技术,特别是针对于一些大尺寸、形状复杂的制件。
热压罐成型工艺流程为:将单层预浸料按预定方向铺叠成的复合材料坯料放在热压罐内,在一定温度和压力下完成固化过程。
这种成型工艺采用的原料也是碳纤维预浸料中间体,其具有可固化不同厚度的层合板、可制造复杂曲面零件、使用范围广泛、工艺稳定可靠等优点,但也存在设备投资成本高、工艺生产成本高、制品大小受热压罐尺寸限制等缺点,适用于制造飞机舱门、整流罩、机载雷达罩,支架、机翼、尾翼等产品。
2.3树脂转移模塑成型工艺树脂转移模塑成型(RTM)技术是一种低成本复合材料的制造方法,最初主要用于飞机次承力结构件,如舱门和检查口盖,现已经成为近几年航空航天材料加工、汽车组件装配领域研究最为活跃的方向之一。
RTM技术具有高效、低成本、制件质量好、尺寸精度高等优点,可应用于体积大、结构复杂、强度高的复合材料制件的成型。
RTM工艺的主要原理是在模腔(模腔需要预先制作成特定尺寸)中铺放按性能和结构要求设计的增强材料预成形体,在一定压力范围内,采用注射设备将专用树脂体系注入闭合模腔,通过树脂与增强体的浸润固化成型。
它是一种不采用预浸料,也不采用热压罐的成形方法。
RTM主要的派生技术有真空导入模塑工艺、柔性辅助RTM、共注射RTM及高压RTM(HP—RTM)等。
其中,HP—RTM 采用预成型件、钢模、真空辅助排气,高压注射和高压下完成高性能热固性复合材料的浸渍和固化工艺,实现低成本、短周期(大批量)、高质量生产,宝马在德国兰茨胡特工厂的碳纤维车身生产便是采用该工艺,康得复材年产150万件碳纤维复合材料部件项目也将采用该工艺。
HP—RTM可以生产高质量、高精度、低孔隙率、高纤维含量的复杂复合材料构件,具有生产效率高、数分钟内即可固化、模具产品采用CAD设计、制造容易并可多次使用等优点。
3碳纤维复合材料在轻量化的应用轻量化研究是现代材料设计制造的一大主流,随着节能减排要求的提高,轻量化材料在各领域的应用将会更为广泛。
轻量化材料是未来的重要发展趋势,这正是这个领域目前所面临的巨大变化的一个重要方面。
因为随着化石燃料储量不断减少,传统的机动化及金属材料使用即将达到极限。
日益增加的二氧化碳排放对气候和环境造成了威胁,那么轻量化的需求将会越来越大,碳纤维复合材料面对全世界不断增长的轻量化市场将会是全新的一次挑战。
另一方面碳纤维具有优异的力学性能、环境稳定性和轻质性,是材料领域的轻质、高强高模的典型代表。
就材料性能而言,碳纤维复合材料是目前最理想的、可应用最广泛的轻量化材料。
3.1在航空航天领域中的应用碳纤维复合材料已成为21世纪不可缺少的新型制造材料,高性能碳纤维复合材料以轻质、高强等特性能够满足高性能航空、航天飞行器的使用要求,在航空航天领域广泛应用,且目前仍然是其研发应用的重点。
近年来,在航空航天等领域受到越来越多的关注。
由于碳纤维复合材料有着很好的耐烧蚀,耐高温等优越性能,能有效地解决飞行器因启动加热带来的高温冲刷,在飞行器的热防护方面有着其他材料不可比拟的作用。
碳纤维复合材料制成的火箭可以将噪声降低到最低水平。
与相同体积的复合材料相比,可以减少大量的动能损失。
据报道航天飞行器质量每减轻1kg,可减少运载火箭质量500kg,其能耗也将会降到最低水平。
将碳纤维应用于火箭发动机喷管可以减轻20%~30%的质量,能够有效提高复合材料的应用效率。
在航空领域,我国碳纤维复合材料的生产和应用主要是歼击机的机身、机翼等部件。
由于碳纤维复合材料密度小,大大减轻了战斗机的质量,减少了能耗,使战斗机的作战时间得到了有效延长。
采用碳纤维复合材料将大大减轻战机质量,实现轻量化,增加飞行时间。
这在大型飞机上更为明显。
在大型飞机的研制过程中,克服重力是最重要的因素。
3.2在汽车领域中的应用汽车轻量化技术主要包括轻量化材料应用、结构优化设计和改进制造工艺三方面。
轻量化材料应用是汽车轻量化最直接有效的方法。
常见的轻量化材料包括高强钢、铝镁合金等金属材料,以及工程塑料和复合材料为代表的非金属材料。
在具体车型的工程开发过程中,可根据车型定位、成本目标、开发周期、生产效率等要求,选择合适的材料,应用于合适的部件。
碳纤维增强复合材料的密度远低于钢、铝等车身常用金属材料,比强度和比刚度远高于铝镁合金和高强钢,可以广泛应用于车身覆盖件、内饰件、动力系统、底盘系统、车身结构件等部件,替代传统金属材料,达到轻量化的目的。
此外,碳纤维复合材料还具有耐腐蚀、吸音、降噪、隔热、可导电等特性,在汽车工业中具有广泛的潜在应用价值。
如使用缠绕工艺可生产碳纤维复合材料传动轴,在轻量化同时,还具有抗阻尼性好、临界转速提高、不锈蚀等优点。
利用碳纤维可导电特性,有厂家已研发出可以储存电能的碳纤维复合材料,用储电材料替代电动汽车的金属车门、顶盖、发动机盖等部件,可以减轻蓄电池和车身重量,达到轻量化和储能节能的双重目的。
随着世界经济的发展,能源危机不断加重,碳排放造成的环境压力日益凸显,汽车工业面临的节能减排政策法规日趋严格,碳纤维复合材料以其轻质、高性能的优势越来越受到汽车工业的重视,在汽车部件中的应用也越来越广泛。
国外在碳纤维复合材料研究使用方面起步较早。
早在1979年,福特汽车公司就试制了碳纤维复合材料车身,整车减重33%。
日本、美国等碳纤维技术领先的国家,均将碳纤维复合材料应用于汽车制造装配纳入近期的战略目标,制定了汽车产业的发展计划。
碳纤维复合材料传动轴、尾翼、引擎盖等部件都已在日本和欧美品牌汽车上应用。
在不降低安全性的前提下获得了极高的轻量化效果。
3.3在体育用品中的应用随着健康生活方式的普及和人们对通过健身运动保持健康体魄的需求的显著上升,以及专项竞技体育向更强、更高、更快方向的迅速发展,从而促进了体育用品产业的发展。
运动器材的好坏影响着运动效果,随着时代的进步和科技的发展,体育设施和运动器材也在不断地更新换代,要想制造出性能更优越的运动器材,就要选择更优越的制作材料。
在体育器材领域,其质量的选择是由使用需求决定的,并不是越轻越好。
例如,举重和铅球等运动项目对质量有着严格的要求。
但是像羽毛球拍和网球拍就需要质量轻巧,碳纤维复合材料在这类轻质器材制造中有着举足轻重的作用。
另外在射箭项目中也有碳纤维的身影,提高弓箭的稳定性和准确性最简单有效的方法就是通过提高弓和箭的比弹性来提高弓箭本身的性能。
碳纤维的抗疲劳程度高且质量较轻,能承受更高的弯曲应力,这样就赋予了弓箭更高的初速度和稳定性。
正因为碳纤维的这些特性,使其在体育用品领域越来越受青睐。
上述碳纤维材料在体育器材中的应用优势表明碳纤维材料是节能的新型环保材料,具有优良的安全性和卫生性,可大大节约体育器材的生产成本。
这些优异的性能成为碳纤维材料在运动器材领域的优势。
5发展趋势及建议随着我国航空航天、国防军工等战略新兴产业的发展,以及汽车及轨道交通轻量化的不断推进,碳纤维复合材料仍将是我国需要迫切发展的关键战略材料。
如何通过高端应用来引领碳纤维复合材料行业的创新,发展高效低成本工艺技术,快速提升行业竞争力,是未来行业发展需要重点考虑的问题。
未来,碳纤维复合材料的发展将呈现以下几大发展趋势:(1)成型技术及设备的国产化。
国内企业开始注重新技术的研究,如3D打印碳纤维复合材片料成型技术,并致力于成型工艺设备的国产化。
(2)树脂基体技术的发展。
碳纤维或复材生产企业与树脂企业加快开发适合高端碳纤维复合材料的改性树脂基体,如用于国产大飞机的改性增韧耐湿热环氧树脂。
(3)调整产业需求结构,向高端化发展。
随着我国航空航天的产业化发展及汽车轻量化的快速推进,航空航天、汽车、轨道交通将是未来碳纤维复合材料需求的主要拉动力。
根据国内外碳纤维复合材料市场的发展趋势及国内市场现状,提出如下几点建议:(1)发展低成本碳纤维,降低碳纤维复合材料成本,增强国产碳纤维复合材料竞争力;(2)实现碳纤维及其复材主要设备的国产化;(3)加强企业间的垂直合作,通过产、学、研、用有机结合,提高碳纤维生产企业提供一整套解决方案的能力,即产品研发一复材配比一模具设计一终端应用。