特钢连铸技术和生产的现状及发展
连铸技术的发展状况及高效连铸

机作业率大大提高(≥80%)。
1.2高效连铸的主要作用
1.2.1
连铸坯产量大幅度提高
004
从1989年到2001年我国连铸坯产量由1
投资3~4亿元。
万t增加到12 000万t以上,连铸比由16.3%提高 到87.5%。如果只靠投资新建铸机,而没有连铸机 的高效化,新建和原有铸机都是那样的低生产率,要 想达到这样的总产量是不可想象的,无论资金投入、 场地占用等许多方面都是难以承受的。高教连铸技 术为钢铁行业的调整结构降低成本作出了贡献。 1.2.2 实现炼钢车间的炉机匹配 我国的转炉车间炉容从几吨到200 t都有小方坯 生产。由于小方坯铸机生产能力低,3台转炉配4、5 台甚至6台连铸机,匹配关系复杂混乱,工艺制度不 能保证。这反过来又影响了铸机生产和铸坯质量。 经过连铸机的高效化改造,设备可靠性增加,浇 铸速度提高,连铸机的台时产量大幅提高。实现了各 种模式的炉机匹配生产。如原3炉4、5机全连铸炼 钢车间只需要3台铸机.1炉对1机生产。原来炉容 较小的3炉2机加模铸的车间可实现3炉对2机的 全连铸生产。 炉机匹配后的最大好处全车间生产顺行,工艺制 度得以执行。钢水的温度、氧化性、到位时间都可保 证。这又促进了铸机生产的稳定、高速、优质。 1.2.3经济效益 实现高教连铸使各项技术指标提高,消耗下降, 铸坯质量改善,可使企业降低成本节省投资,获得很 大的经济效益。 连铸直接效盎首钢三炼钢厂统计,由于提高合 格坯收得率、节省备件费用、减少耐材消耗等可降低 连铸坯成本约7元/t。广钢转炉厂节省中间包材料 及提高铸坯收得率可降低连铸坯成本10元/t。 综合经济效益包括降低冶炼消耗、降低连铸成 本、提高综合成材率等,见表4。
450
mm,带厚度2.3~3.2
mm,拉速达35~70 m/rain,该生产线计划于2001年
连铸技术国内外现状及发展趋势

连铸技术国内外现状及发展趋势
连铸技术是钢铁工业中的重要技术之一,它可以实现高效连续生产,提高生产效率,降低成本。
目前,国内外的连铸技术都在不断发展和完善中。
在国内,连铸技术已经实现了从单流到双流、三流、四流等多流程的升级。
同时,还出现了带分段式结晶器、上下扫描式结晶器等新型结晶器,提高了连铸成材率和质量。
此外,国内的连铸技术还在不断推广智能化生产、绿色环保等方面的应用。
在国外,美国、日本等发达国家在连铸技术方面也有很多创新。
例如,美国的Hazelett连铸技术可以实现高品质的铝合金连铸,日本的CCS连铸技术则可以实现高浓度的钢水连铸。
此外,欧洲的一些连铸厂还在探索使用第三方能源进行加热,以实现更高的能源利用效率。
未来,随着新材料、新工艺、新技术的不断涌现,连铸技术将继续发展和创新。
同时,环保、智能化、自动化等方面也将成为连铸技术发展的重要方向。
- 1 -。
连铸工作中的问题与总结
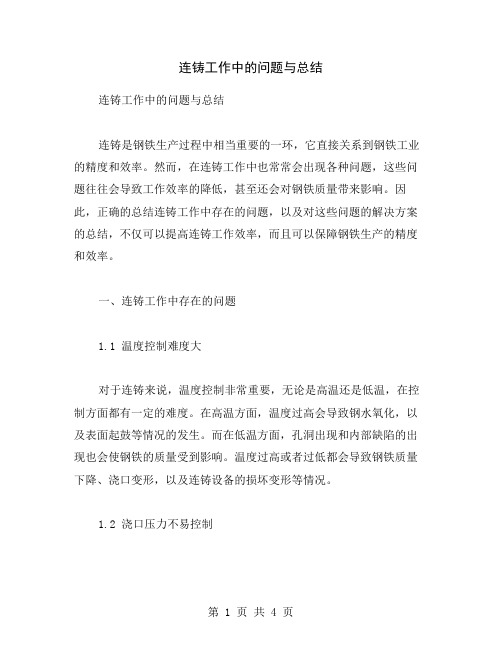
连铸工作中的问题与总结连铸工作中的问题与总结连铸是钢铁生产过程中相当重要的一环,它直接关系到钢铁工业的精度和效率。
然而,在连铸工作中也常常会出现各种问题,这些问题往往会导致工作效率的降低,甚至还会对钢铁质量带来影响。
因此,正确的总结连铸工作中存在的问题,以及对这些问题的解决方案的总结,不仅可以提高连铸工作效率,而且可以保障钢铁生产的精度和效率。
一、连铸工作中存在的问题1.1 温度控制难度大对于连铸来说,温度控制非常重要,无论是高温还是低温,在控制方面都有一定的难度。
在高温方面,温度过高会导致钢水氧化,以及表面起鼓等情况的发生。
而在低温方面,孔洞出现和内部缺陷的出现也会使钢铁的质量受到影响。
温度过高或者过低都会导致钢铁质量下降、浇口变形,以及连铸设备的损坏变形等情况。
1.2 浇口压力不易控制在连铸过程中,浇口的压力也是一个很重要的因素。
因为,当浇口的压力不稳定的时候,就会导致钢水流速的不稳定,出现一些问题,如不稳定的流速就会导致钢铁坯面整平不良、表面有凸起等问题;如果压力太大,就会导致过削钢铁表面,影响钢铁的外观质量。
1.3 浇注速度控制困难在连铸中,加工铸坯的速度对钢水流体的控制也会有影响。
高速浇注增加了钢水氧化和钢水粘滞度的风险,同时也并不利于钢水的混匀,会对钢铁产品的质量产生负面影响。
低速浇注的阻力较大,只能增加钢水流体的切应力,不能达到良好的混合效果。
因此,快并不一定好,慢也不一定准确,调节浇注速度是一项十分困难的任务。
1.4 非均匀铸坯厚度虽然连铸设备可以控制铸坯的厚度,但越往两端,铸坯的厚度也越难控制。
对于非均匀厚度的铸件,在铸造过程中,可能会出现鱼鳞状的铸态,严重影响铸件表面质量。
同时,厚度的不均匀也会导致温度不均匀,进一步影响铸坯质量。
二、针对问题的解决方案2.1 温度控制温度控制是一项非常重要的工作,如果能保持均衡的温度,并且能够避免过高或者过低的温度,就可以使得铸坯的质量得到保证。
连铸工作中的改进方案和总结
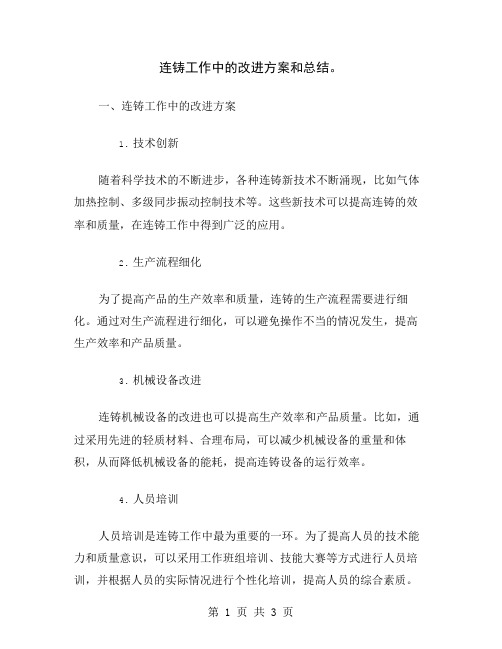
连铸工作中的改进方案和总结。
一、连铸工作中的改进方案1.技术创新随着科学技术的不断进步,各种连铸新技术不断涌现,比如气体加热控制、多级同步振动控制技术等。
这些新技术可以提高连铸的效率和质量,在连铸工作中得到广泛的应用。
2.生产流程细化为了提高产品的生产效率和质量,连铸的生产流程需要进行细化。
通过对生产流程进行细化,可以避免操作不当的情况发生,提高生产效率和产品质量。
3.机械设备改进连铸机械设备的改进也可以提高生产效率和产品质量。
比如,通过采用先进的轻质材料、合理布局,可以减少机械设备的重量和体积,从而降低机械设备的能耗,提高连铸设备的运行效率。
4.人员培训人员培训是连铸工作中最为重要的一环。
为了提高人员的技术能力和质量意识,可以采用工作班组培训、技能大赛等方式进行人员培训,并根据人员的实际情况进行个性化培训,提高人员的综合素质。
二、连铸工作中的总结1.高品质的原材料在连铸工作中,高品质的原材料是保证产品质量的基础。
因此,在原材料采购时,一定要选择质量好、纯度高的原材料。
2.加强管理和监控为了确保连铸工作的正常进行,必须要加强对生产过程的管理和监控。
通过实时监测,可以及时发现和解决生产过程中的问题,避免问题扩大并影响生产效率和产品质量。
3.用先进技术提升质量为了确保连铸生产的高效率和高质量,必须使用先进技术。
只有掌握了先进技术,才能不断提升连铸生产的效率和质量。
4.确保生产安全安全是连铸工作中最为重要的一环。
为了确保生产过程的安全,必须严格遵守生产规程,在工作过程中注意安全,提高员工的安全意识,加强设备的安全保障。
连铸工作中的改进方案和总结可以提高生产效率和产品质量,以适应市场需求的不断增长。
通过不断探索和发展,连铸技术和生产工艺将会得到更加广泛的应用,为实现精准制造和高质量发展做出贡献。
连铸技术国内外现状及发展趋势

连铸技术国内外现状及发展趋势
随着钢铁工业的不断发展,连铸技术作为钢铁生产中的重要工艺技术,也在不断发展和改进。
本文旨在探讨连铸技术的国内外现状和发展趋势。
一、连铸技术国内外现状
1. 国内现状
目前我国连铸技术已经成为钢铁生产中的主要工艺技术之一,国内的连铸设备和技术水平也不断提高。
目前,我国铸造模具、连铸机、冷却系统等连铸设备已经实现国产化,并且在连铸技术的研究和应用方面也取得了不少成果。
然而,与国外相比,我国的连铸技术仍然存在一定的差距。
2. 国外现状
国外的连铸技术相对较为成熟,特别是在技术水平和设备精度方面已经达到了相当高的水平。
目前,欧美等发达国家的连铸技术已经开始向高端化、多功能化方向发展,能够适应更加复杂的钢铁材料生产需求。
二、连铸技术的发展趋势
1. 高端化
随着我国钢铁产业的不断发展,钢铁材料的品质和精度要求也越来越高。
因此,连铸技术也需要不断提升,向高端化方向发展。
2. 多功能化
在连铸技术的应用过程中,还需要考虑人工智能、大数据、机器
视觉等技术的应用。
未来,连铸技术将朝着多功能化的方向发展。
3. 绿色化
连铸技术的发展也需要考虑环保和资源节约。
因此,在设备制造和生产过程中,需要更多地考虑环保和资源节约问题,实现连铸技术的绿色化。
综上所述,连铸技术作为钢铁生产中的重要工艺技术,其国内外现状和发展趋势也在不断变化。
随着技术的不断提升和应用范围的扩大,连铸技术有望在未来实现更加高端化、多功能化和绿色化的发展。
特钢行业发展现状

特钢行业发展现状1. 概述特钢行业是指生产高品质合金钢、无缝钢管和特殊钢材的行业,它在现代工业中发挥着重要作用。
特钢具有优异的力学性能、耐磨性、耐腐蚀性等特点,广泛应用于冶金、机械制造、汽车制造、航空航天等领域。
本文将对特钢行业的发展现状进行全面、详细地探讨。
2. 特钢行业的背景特钢行业起源于上世纪60年代,当时中国经济实力较弱,对高品质特钢的需求主要依赖进口。
随着中国工业化进程的加快,特钢行业逐渐兴起。
特钢企业通过引进先进技术,提高研发能力和生产技术水平,逐渐摆脱了对进口特钢的依赖。
特钢行业开始逐步发展壮大,成为中国制造业的重要支撑。
3. 特钢行业的现状特钢行业在近年来取得了长足发展,以下是其现状的一些要点:3.1 产量持续增长特钢行业的产量不断增长,表明其发展势头良好。
特钢行业的产量在最近五年内呈现稳定增长的趋势,特别是在加快工业化进程和推动国内制造业升级的背景下,特钢行业的产量增速更加明显。
3.2 技术水平提高特钢行业的技术水平不断提高,通过引进国外先进技术和自主研发,特钢企业在生产工艺、材料配比、产品质量等方面取得了可喜的进展。
特钢产品的质量和性能得到了极大的提升,能够满足国内外高端市场的需求。
3.3 产品结构优化特钢行业的产品结构越来越趋向多元化和高附加值。
除了生产传统的合金钢、无缝钢管等产品外,特钢企业还逐渐拓展至特殊钢材领域,如高速钢、模具钢、不锈钢等。
这些高附加值产品不仅在国内市场有很大需求,还出口到世界各地。
3.4 环保意识增强特钢行业正积极响应国家的环保政策,加大绿色生产和节能减排的力度。
特钢企业通过技术改造和设备升级,减少了产生大气污染和固体废弃物的排放。
同时,特钢企业还加强了资源循环利用,提高了能源利用效率。
4. 特钢行业面临的挑战与机遇虽然特钢行业取得了显著的发展成果,但仍面临许多挑战和机遇。
4.1 挑战•市场竞争激烈:特钢行业竞争激烈,国内外企业纷纷进入市场,企业之间的竞争压力加大。
特钢行业发展现状

特钢行业发展现状特钢行业是钢铁行业的一部分,主要生产高品质、高强度、高精度的钢材产品。
近年来,随着社会经济的发展和科技进步的加速,特钢行业也得到了快速的发展。
一、行业现状国内特钢行业已经形成了一定规模的生产体系,主要集中在东北、华北、华东、华中、西南和华南等地区。
根据行业统计数据,2019年我国特钢总产量达到1.12亿吨,同比增长2.3%。
其中高速线材产量达到1.7亿吨,同比增长9.2%。
钢板、钢管、合金钢和工具钢等产品也均有较大幅度的增长。
二、技术创新技术创新是特钢行业发展的重要推动力。
目前,特钢行业主要采用先进的生产工艺和技术,如连铸、轧制、热处理、表面处理等,不断提升产品的质量和性能。
此外,特钢行业还注重新材料的研发和应用,如高强度钢、高温合金、耐磨材料等。
三、市场需求特钢行业的发展离不开市场需求的支撑。
近年来,随着国家经济的持续发展和产业结构的调整,特钢行业市场需求也发生了一定的变化。
目前,建筑业、汽车制造业、机械制造业、能源建设和航空航天等领域对特钢产品的需求不断增加。
此外,特钢产品的出口也占据了一定的市场份额。
四、面临的挑战特钢行业发展也面临着一些挑战。
首先是原材料价格的波动。
特钢生产需要大量的原材料,如铁矿石、焦炭、铬铁等,价格波动会直接影响到特钢产品的成本和利润。
其次是环保压力。
特钢生产过程中会产生大量废气、废水和废渣等污染物,如何处理这些污染物成为了特钢企业必须面对的难题。
此外,国内特钢行业还存在一些技术瓶颈和人才短缺等问题。
五、未来发展趋势未来,特钢行业仍将面临着机遇与挑战。
随着国家对环保和能源的重视程度不断加强,特钢行业也将朝着绿色、低碳、高效的方向发展。
此外,随着国家制造业的转型升级,市场对于高品质、高性能特钢产品的需求将不断增加。
未来,特钢行业也将加强技术创新和科学研究,提升产品的质量和性能,不断满足市场需求。
特钢行业是我国钢铁行业中重要的组成部分,也是国家制造业的重要支撑。
特钢行业发展现状

特钢行业是指用于制造工程机械、汽车、航空器、船舶等高端装备的特种钢材产业。
目前,全球特钢行业发展呈现以下几个特点:
1. 产能增长有所放缓:随着全球经济增长的乏力,以及环保和过剩产能治理政策的推进,部分国家和地区的特钢行业产能增长有所放缓。
2. 全球市场竞争加剧:随着国际贸易保护主义抬头,全球特钢生产商之间的竞争愈加激烈,价格和利润空间持续下滑。
3. 产品结构不断优化:特钢行业的发展也面临来自新材料、新工艺和新技术的挑战。
德国、日本等发达国家正加快向高强度、高刚性、高耐腐蚀特种钢材的转型,而中国等发展中国家则积极研发含高硼、高锰等特种钢材。
4. 技术水平提高:全球特钢制造技术在提高质量和精度方面取得了巨大进展,也让特钢产品不断向高端、高品质方向发展。
在中国,特钢行业也面临着前所未有的挑战和机遇。
一方面,随着环保和产能过剩治理政策的推进,中国特钢行业整体表现出产能过剩和盈利能力下降的态势;另一方面,在国内经济转型升级和“一带一路”建设的背景下,一些细分市场逐渐呈现出需求增
长和结构优化的趋势,如高速铁路、航空航天、新能源汽车等领域。
因此,特钢企业需要不断提高技术含量,加强产品创新,积极拓展海外市场,才能在未来的竞争中取得更大的优势。
特殊钢连铸技术的发展及关键技术研究

结晶器液面自动控制 结晶器自动加渣 结晶器漏钢预报 结晶器振动在线检测
3、特殊钢连铸关键技术
3.1 全程保护浇注
全程保护浇注:连铸过程中 为避免钢水二次氧化而采取的 保护措施。钢水运行轨迹为:
钢包-中间包-结晶器 具体环节包括:
——大包液面的保护 —— 大包至中包间注流的保护: —— 中包液面的保护 —— 中包至结晶器间注流的保护 —— 结晶器液面的保护 全程保护浇注示意图
连铸技术优化发展阶段(1980~至今)
主要技术包括: 间包冶金技术 结晶器冶金技术(流动控制、空心保护渣) 结晶器热流成像及漏钢预报 非正弦振动技术 连铸机辊列设计技术(液芯压下、末端压下) 现代电磁技术应用(电磁制动、电磁搅拌) 无缺陷铸坯生产技术等。
1.2 特殊钢模铸与连铸生产流程的比较
—— 能源消耗解析
省去了脱模、整模、钢锭均热、初轧开坯等 工序。由此可节省基建投资费用约40%,减少占地 面积约30%,劳动力节省约70%。
提高了金属收得率 采用模铸工艺,从钢水到钢坯,金属收得率 为84-88%,而连铸工艺则为95-96%,金属收得率 提高10-14%。
—— 连续铸钢的优越性
降低了能源消耗
采用连铸工艺比传统工艺可节能1/4-1/2。
装备; 科技前沿:航空航天、核能、海洋开发。
国内现状及存在的问题
发展现状:生产装备进步,产能大国,总体技术水平相对落后。 主要问题:
—— —— —— —— ——
产品结构不合理,高端品种不足; 工艺技术差距明显,产品质量欠稳定; 资源和能源消耗高,制约可持续发展; 产业集中度与专业化程度低,缺少规模经济效益 基础研究薄弱,共性关键技术自主研发能力不足
2024年连铸坯市场分析现状

2024年连铸坯市场分析现状1. 引言连铸坯是指通过连铸工艺从铁水中直接浇铸而成的钢坯,它具有高品质、高效率等优势,在钢铁行业中得到了广泛应用。
本文将对当前连铸坯市场进行分析,探讨其现状。
2. 连铸坯市场概况近年来,全球钢铁行业发展迅猛,推动了连铸坯市场的增长。
据统计数据显示,全球连铸坯产量逐年增加,市场规模不断扩大。
中国作为世界上最大的钢铁生产国,其连铸坯产量在全球市场占据较大份额。
3. 连铸坯市场竞争态势目前,全球连铸坯市场竞争激烈,主要集中在少数大型钢铁企业之间。
这些企业拥有先进的连铸设备和技术,可以实现高效、高质量的生产。
随着市场竞争的加剧,企业之间不仅在价格上竞争,还在产品质量、交货时间等方面展开竞争,以提升市场份额。
4. 连铸坯市场的发展趋势未来连铸坯市场存在一些发展趋势:4.1 技术进步与创新随着科技的发展,连铸技术不断创新和进步,不仅提高了生产效率,还提升了产品质量。
例如,电磁搅拌技术的应用,在连铸过程中可以有效消除浮渣,提高坯料质量。
4.2 环保要求的提高全球对环境问题的关注度不断提高,连铸坯市场也不例外。
未来,环保要求将成为连铸坯市场发展的重要动力。
企业需要加强环保意识,改进生产工艺,减少污染排放,提升可持续发展能力。
4.3 市场结构调整连铸坯市场结构将进一步调整。
随着市场竞争的加剧,一些低效益的小型铸造企业可能面临淘汰。
同时,一些中型和大型企业将通过并购、兼并等方式扩大规模,提高市场集中度。
5. 连铸坯市场的挑战连铸坯市场面临一些挑战:5.1 市场需求波动全球经济形势的不稳定性,可能导致连铸坯市场需求波动。
市场需求的不确定性将对企业的生产计划和投资决策产生一定影响。
5.2 原材料价格波动连铸坯的主要原材料是铁矿石和煤炭,而这两种原材料价格波动较大。
原材料价格的不确定性使得企业难以进行准确的成本控制,增加了市场不确定性。
6. 总结连铸坯市场作为钢铁行业的关键环节之一,其发展形势和市场竞争态势对于行业发展至关重要。
炼钢连铸年度总结(3篇)

第1篇一、前言随着我国经济的快速发展,钢铁行业作为国民经济的重要支柱产业,其地位和作用日益凸显。
炼钢连铸作为钢铁生产的关键环节,其技术水平的高低直接影响着钢铁企业的生产效率和产品质量。
本年度,我单位在炼钢连铸领域取得了显著成绩,现将年度总结如下:二、工作回顾1. 技术创新与改进(1)设备升级:本年度,我单位对炼钢连铸设备进行了全面升级,引进了国际先进的炼钢连铸生产线,提高了生产效率和产品质量。
(2)工艺优化:针对生产过程中存在的问题,我们不断优化炼钢连铸工艺,降低能耗,提高金属收得率,确保产品质量稳定。
(3)技术创新:我单位积极开展技术创新,成功研发了多项新技术、新工艺,为炼钢连铸生产提供了有力保障。
2. 安全生产(1)加强安全管理:我们始终把安全生产放在首位,严格执行安全生产责任制,确保生产过程安全稳定。
(2)隐患排查治理:定期开展安全隐患排查,及时发现并消除安全隐患,降低事故发生率。
(3)员工安全培训:加强员工安全教育培训,提高员工安全意识和操作技能。
3. 降本增效(1)优化生产流程:通过优化生产流程,提高生产效率,降低生产成本。
(2)节能降耗:加大节能降耗工作力度,降低能源消耗,提高资源利用率。
(3)技术创新:通过技术创新,降低原材料消耗,提高产品附加值。
4. 市场拓展(1)开拓新市场:积极拓展国内外市场,提高产品市场占有率。
(2)加强客户关系维护:与客户保持良好沟通,提高客户满意度。
(3)提升品牌形象:通过优质的产品和服务,提升企业品牌形象。
三、工作亮点1. 生产指标完成情况(1)产量:本年度,炼钢连铸产量同比增长10%,超额完成年度生产任务。
(2)质量:产品质量稳定,合格率高达99.8%,顾客满意度不断提高。
(3)能耗:通过节能降耗措施,能耗同比下降5%,为企业节约了大量成本。
2. 技术创新成果(1)成功研发了新型炼钢连铸工艺,提高了生产效率和产品质量。
(2)引进了国际先进的炼钢连铸生产线,提升了企业核心竞争力。
最新兴澄特殊钢连铸技术概述
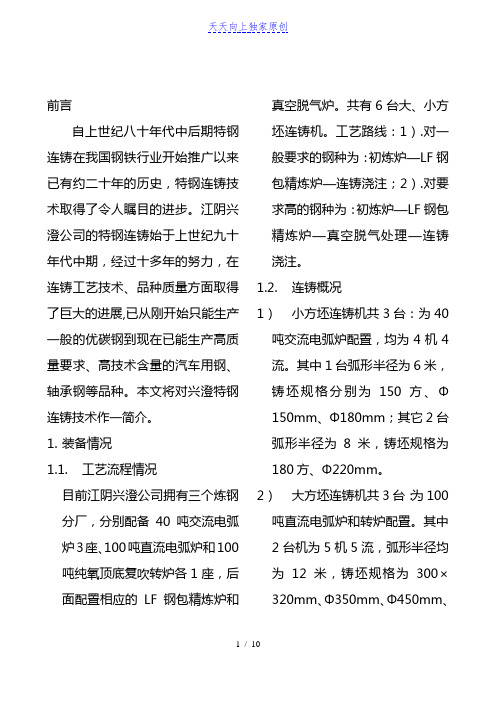
天天向上独家原创前言自上世纪八十年代中后期特钢连铸在我国钢铁行业开始推广以来已有约二十年的历史,特钢连铸技术取得了令人瞩目的进步。
江阴兴澄公司的特钢连铸始于上世纪九十年代中期,经过十多年的努力,在连铸工艺技术、品种质量方面取得了巨大的进展,已从刚开始只能生产一般的优碳钢到现在已能生产高质量要求、高技术含量的汽车用钢、轴承钢等品种。
本文将对兴澄特钢连铸技术作一简介。
1.装备情况1.1.工艺流程情况目前江阴兴澄公司拥有三个炼钢分厂,分别配备40吨交流电弧炉3座、100吨直流电弧炉和100吨纯氧顶底复吹转炉各1座,后面配置相应的LF钢包精炼炉和真空脱气炉。
共有6台大、小方坯连铸机。
工艺路线:1).对一般要求的钢种为:初炼炉—LF钢包精炼炉—连铸浇注;2).对要求高的钢种为:初炼炉—LF钢包精炼炉—真空脱气处理—连铸浇注。
1.2.连铸概况1)小方坯连铸机共3台:为40吨交流电弧炉配置,均为4机4流。
其中1台弧形半径为6米,铸坯规格分别为150方、Φ150mm、Φ180mm;其它2台弧形半径为8米,铸坯规格为180方、Φ220mm。
2)大方坯连铸机共3台:为100吨直流电弧炉和转炉配置。
其中2台机为5机5流,弧形半径均为12米,铸坯规格为300×320mm、Φ350mm、Φ450mm、Φ500mm、Φ600mm。
另1台为3机3流,弧形半径为16.5米,铸坯规格为370×490mm。
2.特殊钢连铸面临的技术课题[1]兴澄公司主要生产轴承钢、弹簧钢、齿轮钢、易切削非调钢、高压管坯钢、油田用钢、系泊链钢、硬线钢等特殊钢。
这些钢种比普通碳素钢对钢质有更高要求。
⑴由于特殊钢中的合金元素较多,含量较高,碳含量控制范围大(0.02%~1.1% C),因此其凝固特性与普通碳素钢有所不同。
⑵特殊钢的纯净度(气体含量、夹杂物数量及形态)、均匀性(低倍组织、微观组织)等要求比普通碳素钢高。
⑶特殊钢中常含有V、Ti、Nb、Al 等活泼元素,极易与氧、氮反应生成高熔点化合物;某些特殊钢中含有S、Al、N元素在浇注、凝固过程中极易形成脆性区或者坚硬质点,这给铸坯质量尤其是表面及内在质量带来一定危害。
我国连铸技术的发展

可节 省 4 %, 0 占地 面 积 可 减 少 3% , 作 费 用 可 节 0 操 省 4%, 火材料 的消耗可 减少 l%。 0 耐 5 ( 提 高 了金 属 收 得率 , 方面 大 幅 度减 少 了 2) 一
钢坯的切头切尾损失 ;另一方面生产 出的铸坯更接 近最终产品形状 , 省去了模铸工艺的加热开坯工序 ,
差, 事故相对较多 , 作业率还偏低 , 铸坯质量还有一
定 的差 距 。
() 2 近终形连铸连轧技术在国外 已实现2 0 年第 2期 07
张成元 , : 等 我国连铸技术的发展
或正加快实现产业化步伐 。 前 , 目 国外 已投产和在建 中的薄板坯连铸连轧生产线约有 5 多套 , 0 薄带连铸 已建多台工业试验机组 , 预计不久将实现产业化。 而 我国已建和在建的 l 流生产线均 由国外引进 , 3 自主 研发 总体 上还 处 于实验 室阶段 [ 。 6 ] () 3 国外高效连铸技术发展很快 , 低碳板坯拉 速普遍大于 2 nmn最高可达 3 mmn 10 m× .  ̄ i, 0 . / i;3 m 0 10m 3 m和 10I 5 l T m×10 m低碳方坯最大拉速分 5 m 别超过 4 / i 3 /i,连铸机生产效率大 . mmn和 .mrn 0 5 a 大提高 , 而我 国还存在较大差距。 () 4 国外的连铸生产 自动控制水平提高迅速 , 已 普遍采用结晶器液面检测与控制技术、 计算机铸坯质 量跟踪和判定技术 、 漏钢预报警与控制技术 , 此外 , 智 能化技术也有了很大发展 ( 如智能化二冷段 )而我 ,
连铸工艺技术
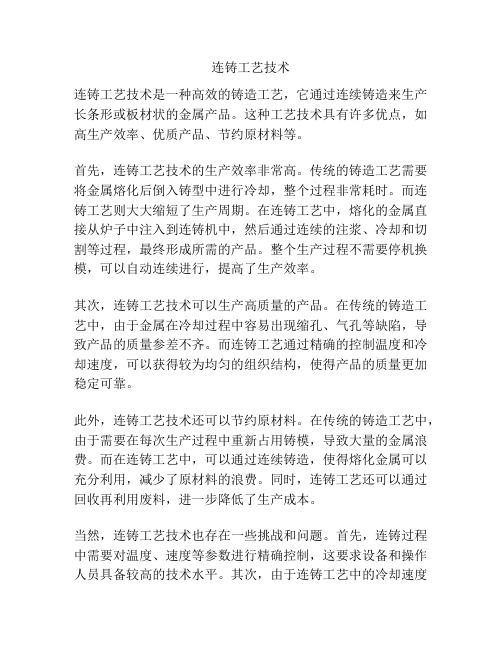
连铸工艺技术连铸工艺技术是一种高效的铸造工艺,它通过连续铸造来生产长条形或板材状的金属产品。
这种工艺技术具有许多优点,如高生产效率、优质产品、节约原材料等。
首先,连铸工艺技术的生产效率非常高。
传统的铸造工艺需要将金属熔化后倒入铸型中进行冷却,整个过程非常耗时。
而连铸工艺则大大缩短了生产周期。
在连铸工艺中,熔化的金属直接从炉子中注入到连铸机中,然后通过连续的注浆、冷却和切割等过程,最终形成所需的产品。
整个生产过程不需要停机换模,可以自动连续进行,提高了生产效率。
其次,连铸工艺技术可以生产高质量的产品。
在传统的铸造工艺中,由于金属在冷却过程中容易出现缩孔、气孔等缺陷,导致产品的质量参差不齐。
而连铸工艺通过精确的控制温度和冷却速度,可以获得较为均匀的组织结构,使得产品的质量更加稳定可靠。
此外,连铸工艺技术还可以节约原材料。
在传统的铸造工艺中,由于需要在每次生产过程中重新占用铸模,导致大量的金属浪费。
而在连铸工艺中,可以通过连续铸造,使得熔化金属可以充分利用,减少了原材料的浪费。
同时,连铸工艺还可以通过回收再利用废料,进一步降低了生产成本。
当然,连铸工艺技术也存在一些挑战和问题。
首先,连铸过程中需要对温度、速度等参数进行精确控制,这要求设备和操作人员具备较高的技术水平。
其次,由于连铸工艺中的冷却速度较快,可能导致金属材料的内应力过大,从而影响产品的机械性能。
因此,在连铸工艺中需要采取相应的措施来改善产品的内应力。
综上所述,连铸工艺技术是一种高效、高质量的铸造工艺,它通过连续铸造来生产金属产品。
连铸工艺具有高生产效率、优质产品、节约原材料等优点,但也存在一些挑战和问题。
随着科技的不断进步和工艺的不断改进,连铸工艺技术有望在金属制造领域中得到更广泛的应用。
国内外现代连铸技术的应用现状与发展前景
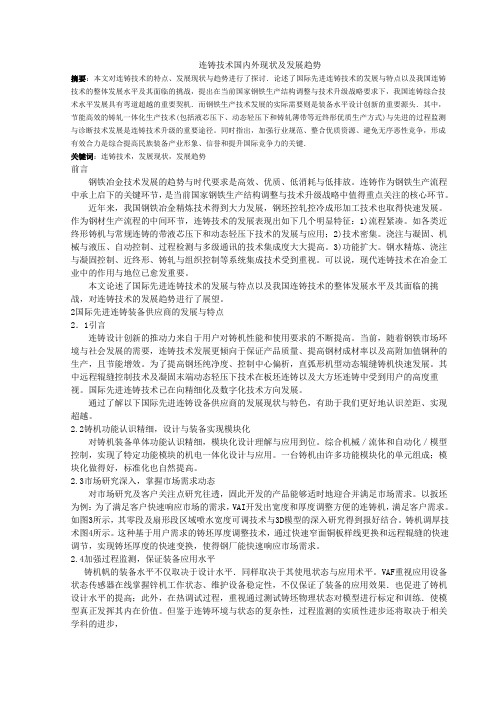
连铸技术国内外现状及发展趋势摘要:本文对连铸技术的特点、发展现状与趋势进行了探讨.论述了国际先进连铸技术的发展与特点以及我国连铸技术的整体发展水平及其面临的挑战,提出在当前国家钢铁生产结构调整与技术升级战略要求下,我国连铸综合技术水平发展具有弯道超越的重要契机.而钢铁生产技术发展的实际需要则是装备水平设计创新的重要源头.其中,节能高效的铸轧一体化生产技术(包括液芯压下、动态轻压下和铸轧薄带等近终彤优质生产方式)与先进的过程监测与诊断技术发展是连铸技术升级的重要途径。
同时指出,加强行业规范、整合优质资源、避免无序恶性竞争,形成有效合力是综合提高民族装备产业形象、信誉和提升国际竞争力的关键.关键词:连铸技术,发展现状,发展趋势前言钢铁冶金技术发展的趋势与时代要求是高效、优质、低消耗与低排放。
连铸作为钢铁生产流程中承上启下的关键环节,是当前国家钢铁生产结构调整与技术升级战略中值得重点关注的核心环节。
近年来,我国钢铁冶金精炼技术得到大力发展,钢坯控轧控冷成形加工技术也取得快速发展。
作为钢材生产流程的中间环节,连铸技术的发展表现出如下几个明显特征:1)流程紧凑。
如各类近终形铸机与常规连铸的带液芯压下和动态轻压下技术的发展与应用;2)技术密集。
浇注与凝固、机械与液压、自动控制、过程检测与多级通讯的技术集成度大大提高。
3)功能扩大。
钢水精炼、浇注与凝固控制、近终形、铸轧与组织控制等系统集成技术受到重视。
可以说,现代连铸技术在冶金工业中的作用与地位已愈发重要。
本文论述了国际先进连铸技术的发展与特点以及我国连铸技术的整体发展水平及其面临的挑战,对连铸技术的发展趋势进行了展望。
2国际先进连铸装备供应商的发展与特点2.1引言连铸设计创新的推动力来自于用户对铸机性能和使用要求的不断提高。
当前,随着钢铁市场环境与社会发展的需要,连铸技术发展更倾向于保证产品质量、提高钢材成材率以及高附加值钢种的生产,且节能增效。
为了提高钢坯纯净度、控制中心偏析,直弧形机型动态辊缝铸机快速发展。
连铸技术国内外现状及发展趋势

连铸技术国内外现状及发展趋势
连铸技术是一种现代化的钢铁生产工艺,旨在提高钢铁生产效率与质量。
自上世纪80年代起,连铸技术在全球范围内得到广泛应用,并不断发展。
当前,连铸技术已成为钢铁工业中的主流生产工艺之一。
国内,随着钢铁行业的不断发展,连铸技术也发展壮大。
目前,国内的连铸机数量和产量均居世界前列。
同时,国内企业也在不断引进新的技术和设备,以提高生产效率和质量。
此外,国内的连铸技术也在不断创新,如微量元素控制技术、智能化控制技术等,为生产提供更多的选择。
国外,欧美、日本等工业发达国家一直处于连铸技术的领先地位。
他们在研究和应用连铸技术方面投入巨大,不断创新。
如今,一些新的连铸技术已经应用于生产中,比如脱氧合金化技术、超细化技术等。
同时,在连铸技术的数字化、智能化方面,国外也取得了一定的进展和成果。
这些技术的应用,使得钢铁生产效率和质量得到了进一步提高。
总的来说,连铸技术已经成为了钢铁生产的主流工艺之一,国内外的企业都在不断发展和创新。
未来,随着科技的不断进步和工业的不断发展,连铸技术将会更加完善和智能化,为钢铁生产带来更多的发展机遇。
- 1 -。
连铸技术的现状及发展趋势

连铸技术的现状及发展趋势摘要:随着科学技术的发展,连铸技术的发展也越来越趋向于成熟。
本文主要介绍了连铸技术在国内外的发展现状和趋势,用到电磁冶金、终形连铸、中间包的加热、结晶器液压振动、在线调宽、摩擦力监控和中间包连续测温等技术,在介绍技术的同时,又联系现实的生产状况,分析了它的发展状况。
关键词:连铸技术;现状;发展;趋势一、近终形连铸技术的介绍近终形连铸技术就是一种集连铸、轧制和热处理为一体的可以生产特殊新材料的一种技术,它最大的特点就是快速凝固,这样可以生产出传统轧制工艺无法生产的材料。
连铸技术分为多种,下面介绍薄板坯连铸和薄带连铸技术。
对于薄板坯连铸技术,薄板坯连铸技术早在1989年就开始投产,在美国最先兴起,结合了德国当时最先进的生产技术。
随着时代的发展,薄板坯连铸技术也日渐成熟,早先只有国外公司拥有这种生产技术,现在,中国已经成为薄板坯连铸产能最大、生产线最多的国家。
对于薄带连铸技术,它相对于其它连铸技术更为先进,它属于冶金领域中一项前沿技术。
它又分为前期传统的技术和现代薄带连铸技术,区别于以前它最大的特点就是薄带连铸技术更加综合,它集连铸、轧制和热处理技术为一体,生产的薄带坯更加精细,并且可以一次成型。
现在的连铸技术中最受关注还有就是双辊薄带连铸技术,它广受关注的原因就是此种高效的生产工艺可以提高生产效率,增加高额的经济效益[1]。
双辊薄带连铸这种工艺非常复杂,所以至今没有完全掌握,虽然近些年有些突破性进展,但是,想要达到商业化量产阶段是不可能的,还是需要大量的研究和探索工作。
其中有几大问题,第一就是生产中的裂纹,这是制约此项技术发展的重大原因之一。
第二就是厚度不均匀的问题,现在能实现的厚度就是在小范围内波动,但还是不利于冷轧过程的进行。
第三就是连铸的速度,上面也提到,现在的技术不足,生产成品的速率低下,不能满足商业化需求。
第四就是薄带的宽度小,并且侧封还不理想。
剩下的还有铸辊的材质问题、钢液的氧化问题、二次冷却问题等等。
- 1、下载文档前请自行甄别文档内容的完整性,平台不提供额外的编辑、内容补充、找答案等附加服务。
- 2、"仅部分预览"的文档,不可在线预览部分如存在完整性等问题,可反馈申请退款(可完整预览的文档不适用该条件!)。
- 3、如文档侵犯您的权益,请联系客服反馈,我们会尽快为您处理(人工客服工作时间:9:00-18:30)。
特钢连铸技术和生产的现状及发展干勇王忠英(钢铁研究总院)f连铸技术国家工程研究中心)摘要:本文通过对国外特钢连铸技术和国内特钢连铸生产及主要产品质量的分析对我国特钢连铸技术的发展进行了探讨。
关键词:特殊钢。
连铸现式发展x随着现代工业的发展,对钢铁材料的质量提出了更高的要求。
高质量钢的主要特点是表现在,i个方面:(1)高洁净度,根据钢种的不『司,通过对原材料的控制、冶炼工艺的优化和保护浇铸措施的实施,使钢中残余元素、气体含量及夹杂物组成及分布符合特定的要求;(2)均匀的化学成分及组织,通过连铸工艺和加工热处理工艺的优化减轻由于凝固造成的宏观成分偏析和微观组织偏析;(3)细小的晶粒度,通过全流程的控制保证形成细小均匀的晶粒度。
由于连铸技术具有显著提高生产效率、成材率及产品质量等特点,自50年代开始钢的连铸工业化以来,得到迅速的发展,目前世界大多数国家的连铸比达到或超过90%。
我国自1996年钢产量超过日本,成为世界第一产钢大国以来,连铸比连年增加,到2001年的连铸比达到89.4%.丰目比与普钢连铸,我国特钢的连铸技术明显处于落后状态,2001年特钢连铸比43.5%。
下面通过对国内外特钢连铸技术的分析,对我国特钢连铸技术的发展进行探讨。
1国外特钢生产技术现状及进展表1是国外几家典型特钢企业的工艺流程及主要产品,从表1可见,除一些特殊用途的高合金钢、轴承钢和工模具钢等仍采用模铸工艺生产外,几乎所有大量生产的商用特殊钢都可以用连铸工艺来生产。
表1国外特殊钢生产典型工艺流程及主要品种120tEAFCC(280mm375ram“可一LF.×)砰惜军聃q“崭70tEAFVDCCI55ramI55mm毫≤氐一LF-一(o)qa聃一珥峙¥器80tEAF85tAODCC150mm800ram2801600ram200mm始丑鞯《一一(o~×oq=珊幂世1“E制一Krefeld一竺竺::竺竺!坚二苎——甭疆■一一100tEAF.120tAOD.CC(斟蜒轻蜊)K举器沣:EBT:偏心底允渣…制.VSC:真卒除渣,TBM:铁水颓处』甲,SKF.MR:SKF的烈壳熔炼炉.FW:喂介fnF特殊钢对钢材洁净度、成分和组织的均匀性和钢材的致密性都有严格的要求,而且由』.【幺类钢合金元素高,易偏析元素多,在连铸时易产生一h心偏析、裂纹和缩孔等缺陷,因此为保汪最终成品的质量,一般都配有以下技术。
(1)保护浇注为保证铡水二次精炼的效果.钢包一中间包一结晶器的全程保护浇注模式已在仝世界各铡J_r泛应用。
其具体措施一般为钢包一中间包采用长水口浇注,中包加覆盖剂;q,问包一结晶器采用浸入式长水口,并在滑动水口与浸入式水【J的接缝处吹氩或吹氮气保护,防止宅气进入;为降低中包内的氧浓度,在开浇前对中包充惰性气体排除窄气,并在中间包上端及包盖周围采川水冷结构,防jj:使用过程中由T热应力引起的变形,使空气进入中包,保证整个浇铸过程中,},包内的气氛鞔浓度小于0.1%;为防止钢包渣进入中包,采用电磁检测设备进行钢包留治操作:采用夫容量中包和优化q,包内结构,延长钢液在q,包内的停留时间,促使犬颗粒夹杂的上浮和排f}{:采jH液血自动控制装置,稳定浇铸速度,防止浇铸过程卷渣或拉漏事故的发生:针对不川钢种,采用相应的结晶器保护渣,以吸附钢中央杂物和起到良好的润滑和均匀导热作用。
通过这些措施的采用,可避免钢液的-次氧化.有效地减少连铸坯中的夹杂物。
f2)增大连铸坯断面巾}』铸坯的部分低倍缺陷可以通过一定的{Ii缩比得以减轻或消除,而且一定的匿缩比也是稳定最终钢材性能的必要措施,如为保证气孔焊合一股要求压缩比为4以上,为得到稳定的机械性能,要求压缩比为7~12,因此,特钢连铸的发展方向是根据所产钢材种类和规格的不同,采用人弧形半径的大断面铸机,其原吲一是继续发挥原有秒J轧机的作用,二是通过大压缩比改薄轧材的组织。
表2是日本大间知多厂对不同钢材的J&缩比要求。
表2日本大同知多厂对不同钢材的压缩比要求钢种压缩比优质碳素结构钳f低、中碳制)≥10台金结构钢f禽凶轮钢)≥12碳索和合金r具N(O8%)≥151F滚动体Ⅲ轴康锊J≥15滚动体用轴承钢≥50但随着高洁净钢生产技术的发展和连铸技术的改进,使钢【}】有害杂质和夹杂物总量显著降低,电磁搅拌和液相穴压F技术的采用有效地减轻了中心偏析.这些都为减小铸坯断面、采用火成材创造了条件。
f31低过热度浇铸及配套技术由于高碳钢在凝固时体积收缩较大,如果钢水过热度太高,则铸坯内柱状晶发达,在热应力综合作用下,易产生中心蔬松、缩孔和内裂,而采用较低豹过热度浇铸钢液除使铸坯中心消除过热后完全凝固,缩短柱状晶区长度、发展等轴晶区,使坯芯成分均匀,避免中心偏析、疏松和裂纹等低倍缺陷的发展外,还具有提高生产率和钢水收得率的作用,凶此低过热度浇铸已越柬越引起人们的关注。
低过热度浇铸技术开发的首要关键是准确控制连铸过程中包钢水温度稳定,在此基础上再考虑降低过热度的措施。
如日本大『岍J知多厂为保证其中包钢水温度稳定,在其新建连铸机上增设中包感应加热装置,其新旧铸机情况见表3所示。
表3大同特钢知多厂连铸机参数目前通过炉外精炼可将钢液温度控制在很窄的范围内,再加上中包保温技术的采用和钢中央杂物控制技术的采用,为低温低速浇铸创造了条件。
研究表明,控制中包钢液温度稳定最有效的手段是采用等离子加热装置向中包补充稳定、可靠的中性热能。
此外,降低钢液过热度还町考虑采用水冷水口或在钢液弯月面用圆锥形无耗冷凝器进行辅助冷却。
尽管低温低速浇铸可在一定程度上改善铸坯的偏析.但此工艺在大生产操作中很难控制,考虑到上述主要低倍缺陷f疏松、偏析)都是在铸坯的液相穴的糊状区形成,因此采用低温浇铸与电磁搅拌相结合的办法,通过控制液芯金属的流动,扩大等轴晶区来减轻偏析。
f4)电磁搅拌技术近年来,为改善连铸坯质量,电磁搅拌技术(EMS)已被广泛应用.其工艺已由单~式的搅拌J‘艺发展成组合式搅拌工艺,其作用已由减轻中碳钢和高碳钢方坯的中心偏析,发展为进一步诱发等轴晶。
对轴承钢而言,为获得良好的表面、皮F、凝固结构、中心疏松和中心偏析质量,须采用组合式i段电磁搅拌工艺,安装在结晶器的搅拌器(M.EMS)用于消除过热,促进等轴晶凝固;安装在二冷区的搅拌器(s.EMs)用于改善晶粒尺寸:安装在凝固末端的搅拌器(F·EMS)可减轻偏析的最终等级,特别是采用凝固末段的电磁搅拌可以阻止粘稠钢液在等轴晶区域内移动,使铸坯的中心偏析得以分散.中心疏松得以改善,现在山阳、神户、大同等公司都采用多级电磁搅拌。
(5)合理的冷却制度二冷配水制度对铸坯表面和内在质量均有很大的影响,合适的配水量可抑制铸坯内部柱状晶迅速生长,避免产生严重的中心疏松。
同时由于钢液在其液相线以下,有一个塑性骤减区,对于高碳钢,此区域在700.900。
C之间,在此温度范围内,即使铸坯受到很小应力也会导致裂纹的产生,并沿晶界(柱状晶)扩展,因此,正确控制二冷段的冷却强度和喷淋水的均匀性,保护铸坯出二冷室到拉矫机前的表面温度在900。
C以上,可以有效防止铸坯内部裂纹的产生。
在其它条件(如过热度、拉速)一定的情况下,对高碳钢连铸二次配水有两种观点:一种是采用弱冷却抑制柱状晶生长,比水量0.3.0.7L/kg,对铸坯形成的中心疏松、偏析采用EMS或轻压下来解决:二是采用高压水冷却(比水量可达2-3L/kg)促进柱状晶生长以减轻铸坯中心缺陷。
对高碳钢(c=o.8%)采用强冷后轧制的中1Imm线材上,由渗碳体所表示的碳偏析几乎消除。
目前广泛采用的二冷还是以弱冷为主,对于小方坯连铸高碳钢,通过采用比水量为0.4-0.5L/kg+F-EMS,同样可获得内部组织致密,中心疏松、偏析小铸坯的铸坯,其关键在于二冷水的合理分配。
(6)液相穴压下技术为解决高碳钢连铸坯凝固过程中,由于导辊之间铸坯产生鼓肚引起的坯壳内容积变化和补偿凝固收缩,导致因残留钢液的宏观流动引起的中心偏析,对液相穴附近进行压下处理,具体方法一般有以下四种:①轻压下近几年,为解决轴承钢连铸坯中心偏析等问题,日本、意大利和韩国等的有关厂家采用“轻压下”技术,用于补偿铸坯最后凝固时的收缩,防止浓化钢液的流动,避免中心偏析和中心疏松的发生。
最合适的压下量是液相穴内残留钢液处于被挤出而又没被挤出的』艋界状态。
严格地说,针对不同的钢种和浇铸条件控制最佳压下量是很困难的,必须通过大量的试验来确定。
采用分段小直径辊在扇形段对铸坯进行轻压下还比较容易控制合适的压下量。
法国Sollac公司大方坯连铸拉速为0.70.1.10m/min时,在4m长区域内压下量在O-12ram之间调节,铸坯中心碳偏析指数南1.15.1.30降到1.1.1.2。
②大直径辊强压下与普通轻压下相比,大直径辊强压下可充分保证铸坯内部变形量,而且凝固界面的畸变也较小。
当采用大直径辊压下时,以较小的压下量就能改善中心偏析,另外,由于在等轴晶区内压下,有助于减轻铸坯内裂纹。
③连续锻压连续锻压法是利用装有异形锻头的锻压装置对液相穴端进行连续锻压,使凝固末端的固液共存层压台在一起,可有效地使浓缩的钢水和破碎的晶粒向上游方向移动,同时大压下变形还可以防止铸坯内裂。
日本川崎在凝固末段对铸坯进行大压下量锻造,即靠往复式锥形铁砧,逆4浇铸方向排出钢液中心的浓缩钢液。
应用连锻工艺,不仅能完全消除中心偏析,而且能根据质量要求选择在产品中心部位元素的最佳浓度及降低中心部位的P、S浓度,所得到SUJ2材的滚动接触疲劳寿命是常规锻造棒材的2倍。
④热应力压下所谓的热应力压下技术也被称之为二冷强冷技术,其基本原理是是在接近凝固末段的位置,对铸坯表面进行高强度冷却,致使凝固坯壳向内收缩,产生与机械应力压力相同的效果。
但该技术主要适用于小方坯连铸。
2国内特钢连铸技术现状我国特殊钢连铸的起步是从上世纪八十年代,太钢引进不锈钢板坯及陕钢、大冶和长城引进合金小方坯连铸机开始的,但当时由于电炉容量小、精炼设备差、钢水洁净度低、铸坯断面小等原凶,并未取得迅速发展,到了九十年末,各主要特钢厂先后自建或从国外引进大电炉和合金连铸机,推动了特钢连铸的技术的发展。
2.1国内特钢企业工艺流程及连铸装备目前,国内主要特钢厂除本特、大连、首特外,其它各厂均已建或正在建合金钢连铸设备,具体情况如表4所示。
其中兴澄、抚顺、上五、西宁、贵阳等都是从国外引进的合金钢连铸机,这些连铸机均配有钢包和中包称重系统,保护浇铸、液面自动控制、结晶器电磁搅拌和二冷自动配水等装置和系统,个别铸机还装有末段电磁搅拌。
从国内外主要特钢厂工艺流程和连铸装备比较可知,国内主要特钢厂的连铸设备已基本具备合金钢连铸的条件,为我国全面开展特殊钢连铸工作提供了坚实的设备保障,但与国外特钢流程相比,还有一些不足,具体如下:f1)国外特钢厂粗钢供应均采用大电炉或高炉一转炉流程,而国内特钢厂经过改造后均采用大电炉提供粗钢,与转炉粗钢相比,钢中残余元素高、成本竞争优势弱。