氮化硅刻蚀机培训教程
刻蚀培训计划

刻蚀培训计划一、培训概述刻蚀技术是一种在材料表面制造微细结构的加工技术,广泛应用于半导体制造、光电子器件制造、微纳米加工等领域。
随着科技的不断发展,刻蚀技术在相关行业中的需求日益增加。
为了培养专业的刻蚀技术人才,满足行业需求,本次培训计划就专门针对刻蚀技术进行培训,内容包括刻蚀工艺原理、设备操作、安全技术等方面。
二、培训目标1.了解刻蚀技术的基本原理和应用范围。
2.熟练掌握刻蚀工艺过程和设备操作方法。
3.掌握刻蚀技术相关的安全知识和常用故障排除方法。
4.具备一定的刻蚀工程实践能力,能够独立进行一定程度的刻蚀加工。
5.了解国内外刻蚀技术的发展趋势和最新应用领域。
三、培训内容1. 刻蚀技术概述- 刻蚀技术的定义和历史发展- 刻蚀技术的应用范围和发展前景2. 刻蚀工艺原理- 刻蚀过程的基本原理- 刻蚀材料和刻蚀介质的选择- 刻蚀参数对加工效果的影响3. 刻蚀设备操作- 常见刻蚀设备的结构和原理- 刻蚀设备的使用方法和注意事项- 刻蚀设备的日常维护和保养4. 刻蚀工艺实践- 刻蚀样品的准备和加工- 刻蚀工艺中常见问题的解决方法- 刻蚀实验数据的处理和分析5. 刻蚀安全技术- 刻蚀工艺中的安全隐患和预防措施- 突发事件的应急处理和救援措施- 刻蚀设备和材料的安全操作规范6. 刻蚀技术的发展趋势- 国内外刻蚀技术的最新进展- 刻蚀技术在相关领域中的应用案例- 刻蚀技术未来的发展方向和挑战四、培训方法1. 理论讲解:由资深专家讲解刻蚀技术的基本原理和应用知识。
2. 案例分析:通过实际案例分析,让学员了解刻蚀技术在实际应用中的重要性和难点。
3. 实践操作:提供实际的刻蚀设备和材料,让学员亲自操作,掌握刻蚀工艺和设备的操作方法。
4. 网络学习:提供在线学习平台,定期组织学员进行网络学习和交流,分享学习心得和技术经验。
五、培训流程1. 第一阶段:刻蚀技术基础知识培训- 刻蚀技术的基本概念和原理- 刻蚀工艺参数的选择和优化- 刻蚀设备的使用和维护2. 第二阶段:刻蚀工艺实践操作- 刻蚀样品的准备和操作- 常见问题的解决方法和设备操作技巧- 刻蚀实验数据的处理和分析3. 第三阶段:刻蚀安全技术和应急处理- 刻蚀工艺中的安全隐患和预防措施- 突发事件的应急处理和救援措施- 刻蚀设备和材料的安全操作规范4. 第四阶段:刻蚀技术的发展趋势和应用案例- 国内外刻蚀技术的最新进展- 刻蚀技术在相关领域中的应用案例- 刻蚀技术未来的发展方向和挑战六、培训考核1. 理论考核:结合培训内容,进行书面考核,测试学员对刻蚀技术基础知识的掌握程度。
氮化硅刻蚀机培训教程

氮化硅刻蚀机培训教程本页仅作为文档封面,使用时可以删除This document is for reference only-rar21year.MarchTel/lam 氮化硅刻蚀机培训教案一简介:Tel/lam 氮化硅刻蚀机是一种平板式的干法刻蚀设备,用于氮化硅的干法刻蚀,其工作原理为特种气体SF6,CHF3在RF下电离并与氮化硅发生反应。
二结构组成它由以下几部分组成:主机部分、电源部分、泵组部分、射频部分和气体供给部分部分。
1主机部分:它是氮化硅刻蚀机的主体部分,包括显示器、传递腔、反应腔、传动系统及设备的主要控制系统。
2电源部分:系统供电208V进入,经变压器,继电器等变为所需的电压输出。
该设备泵组电源由电源柜控制。
3射频部分:在气体反应时提供的高频电源,以便气体在高真空环境下电离,产生等离子体。
射频匹配系统位于主机上部,用于对射频源所提供的高频通过可变的电感电容进行匹配,以便提供给设备稳定高效的射频。
射频电源为208VAC供电,外接冷却水为本体发热元件降温。
4泵组部分:由机械泵、增压泵和真空管线构成抽反应腔的真空系统,以达到工艺反应时所需的真空度要求。
由18泵及配套的真空管线用于抽传递腔的真空。
现在我们使用的泵组位于一楼回风区内。
5 气体供给部分:由特气柜、特气瓶和特气管线构成。
用于提供反应所需的特种气体,其中用于提供特气的特气瓶至于一楼回风区内,特气经二次减压提供给设备,并由质量流量计进行控制。
三T el/lam 氮化硅刻蚀机的基本操作1 当操作本台设备时,应首先检查该设备的动力条件,具体条件如下:压缩空气:±氮气: ±用于射频冷却的冷却水是否有,反应所用的特气是否有,设备面板的电极温度是否和设定的温度相符,排风是否正常。
2操作:按照设备操作流程进行操作3面板按键:LOAD 用于下载初始化程序 SAVE保存程序 RECIPE用于编辑反应的程序 STATUS 用于观察设备所处的状态 PARAMETERS用于设置设备参数 OPTIONS用于设备的手动操作及观察设备运行时的参数变化 START 开始设备开始运行 STOP终止下一片硅片从传片筐传出 FIELD SELECT 用于切换设定状态设备面板另有四个用于光标移动的按健及一个数字键盘四 Tel/lam 氮化硅刻蚀机的常见故障及应急故障处理1真空故障:主要显示为反应腔或者传递腔真空达不到,真空漏率较大。
刻蚀工序培训讲解

后清洗到PECVD的产品时间最长不能超过4小时,时间过长硅片会污染 氧化,从 而影响产品的电性能及效率.
刻蚀槽液面的注意事项: 正常情况下液面均处于绿色,如果一旦在流片过程中颜色改变,立 即通知工艺人员。
二、刻蚀工序质量培训
刻蚀工序质量控制点
刻蚀工序的质量控制主要分为来料质量控制和刻蚀后的质量 控制。
每批片子的腐蚀重量和绝缘电阻都要检测。 1.要求每批测量4片。 2.每次放测量片时,把握均衡原则。如第一批把测试片放1.3.5.7道, 下一批则放2.4.6.8道,便于监控设备稳定性和溶液的均匀性。
生产没有充足的片子时,工艺要求: 1.如果有1小时以上的停机,要将刻蚀槽的药液排到tank,减少药液的 挥发。 2.停机后15分钟用水枪冲洗碱槽喷淋及风刀,防止酸碱形成的结晶盐 堵塞喷淋口及风刀。 3.停机1小时以上,要在开启机器生产前半小时用水枪冲洗风刀处的滚 轮,杜绝做出来的片子有滚轮印!
冷热探针法的检测原理 探针和N型半导体接触时,传导电流将流向温度较低的区域,使得热探
针处的电子缺少,因而其电势相对于同一材料上的室温触点而言是正的。同 样原理,P型半导体热探针触电相对于室温触点而言是负的。
万用表操作及判断
•1)确认万用表工作正常,量程置于200mv。
•2 )冷探针连接电压表的正电极,热探针与电压表的负极相连。
上片 清洗1 清洗2 清洗3 下片
碱洗 吹干2
刻蚀槽:用于边缘刻蚀,去除背面及边缘的PN结。 所用溶液为
HF+HNO3+H2SO4,主要工艺参数:
Firstfill volume:270.0L;
Firstfill volume H2SO4 :80.0L;
concentrations of chemical:HF(35g/L)&HNO3 (350g/L);
蚀刻培训讲义
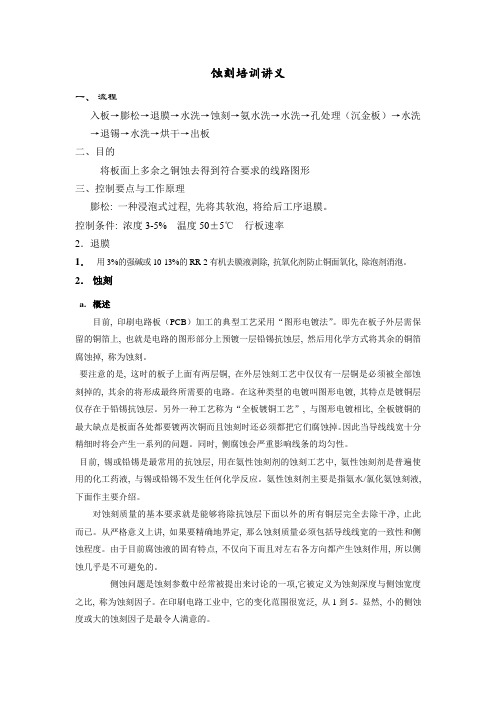
蚀刻培训讲义一、流程入板→膨松→退膜→水洗→蚀刻→氨水洗→水洗→孔处理(沉金板)→水洗→退锡→水洗→烘干→出板二、目的将板面上多余之铜蚀去得到符合要求的线路图形三、控制要点与工作原理膨松: 一种浸泡式过程, 先将其软泡, 将给后工序退膜。
控制条件: 浓度3-5% 温度50±5℃行板速率2.退膜1.用3%的强碱或10-13%的RR-2有机去膜液剥除, 抗氧化剂防止铜面氧化, 除泡剂消泡。
2.蚀刻a.概述目前, 印刷电路板(PCB)加工的典型工艺采用“图形电镀法”。
即先在板子外层需保留的铜箔上, 也就是电路的图形部分上预镀一层铅锡抗蚀层, 然后用化学方式将其余的铜箔腐蚀掉, 称为蚀刻。
要注意的是, 这时的板子上面有两层铜, 在外层蚀刻工艺中仅仅有一层铜是必须被全部蚀刻掉的, 其余的将形成最终所需要的电路。
在这种类型的电镀叫图形电镀, 其特点是镀铜层仅存在于铅锡抗蚀层。
另外一种工艺称为“全板镀铜工艺”, 与图形电镀相比, 全板镀铜的最大缺点是板面各处都要镀两次铜而且蚀刻时还必须都把它们腐蚀掉。
因此当导线线宽十分精细时将会产生一系列的问题。
同时, 侧腐蚀会严重影响线条的均匀性。
目前, 锡或铅锡是最常用的抗蚀层, 用在氨性蚀刻剂的蚀刻工艺中, 氨性蚀刻剂是普遍使用的化工药液, 与锡或铅锡不发生任何化学反应。
氨性蚀刻剂主要是指氨水/氯化氨蚀刻液, 下面作主要介绍。
对蚀刻质量的基本要求就是能够将除抗蚀层下面以外的所有铜层完全去除干净, 止此而已。
从严格意义上讲, 如果要精确地界定, 那么蚀刻质量必须包括导线线宽的一致性和侧蚀程度。
由于目前腐蚀液的固有特点, 不仅向下而且对左右各方向都产生蚀刻作用, 所以侧蚀几乎是不可避免的。
侧蚀问题是蚀刻参数中经常被提出来讨论的一项,它被定义为蚀刻深度与侧蚀宽度之比, 称为蚀刻因子。
在印刷电路工业中, 它的变化范围很宽泛, 从1到5。
显然, 小的侧蚀度或大的蚀刻因子是最令人满意的。
刻蚀机作业指导

刻蚀机作业指导一、概述刻蚀机是一种用于制作微细器件的设备,通过将光刻胶涂覆在基板上,然后使用刻蚀机将光刻胶上的图案转移到基板上。
本文将详细介绍刻蚀机的操作步骤、注意事项和常见问题解决方法。
二、操作步骤1. 准备工作a. 确保刻蚀机的电源温和源已连接并正常工作。
b. 检查刻蚀机内部是否有残留的光刻胶,如有需要进行清理。
c. 将待刻蚀的基板放置在刻蚀机的夹具上,并确保夹具稳固。
2. 设定刻蚀参数a. 打开刻蚀机的控制面板,进入参数设置界面。
b. 根据所需的刻蚀深度和图案要求,设定刻蚀时间、功率温和体流量等参数。
c. 确认参数设置无误后,保存并退出参数设置界面。
3. 开始刻蚀a. 关闭刻蚀机的安全门,并确保周围环境无尘。
b. 打开刻蚀机的真空泵,并等待真空度稳定。
c. 按下启动按钮,刻蚀机开始工作。
d. 在刻蚀过程中,观察刻蚀情况,确保刻蚀深度和图案质量符合要求。
4. 刻蚀完成a. 刻蚀时间到达设定值后,刻蚀机会自动住手工作。
b. 打开刻蚀机的安全门,取出刻蚀完成的基板。
c. 检查刻蚀结果,如有问题需要重新进行刻蚀。
三、注意事项1. 安全操作a. 在操作刻蚀机之前,必须戴好防护眼镜和手套,确保自身安全。
b. 刻蚀机操作过程中,严禁将手指或者其他物品伸入刻蚀区域,以免发生意外。
2. 参数设定a. 在设定刻蚀参数时,应根据实际需要进行调整,避免刻蚀过深或者过浅。
b. 不同材料的刻蚀参数可能不同,需要根据实际情况进行调整。
3. 刻蚀质量控制a. 在刻蚀过程中,应随时观察刻蚀情况,确保刻蚀深度和图案质量符合要求。
b. 如发现刻蚀不均匀或者刻蚀深度不符合要求,应及时调整参数或者重新进行刻蚀。
四、常见问题解决方法1. 刻蚀不均匀a. 检查刻蚀机内部是否有残留的光刻胶,如有需要进行清理。
b. 检查刻蚀参数是否合适,如需调整参数。
c. 检查刻蚀机的真空泵是否正常工作,如需更换或者维修。
2. 刻蚀深度不符合要求a. 检查刻蚀参数是否合适,如需调整参数。
蚀刻机操作方法与技术

蚀刻机操作方法与技术
蚀刻机是一种用来制作微细结构的设备,它可以通过化学或物理方法从材料表面去除部分材料来创建所需的结构。
以下是蚀刻机的基本操作方法和技术:
1. 材料准备:将要刻蚀的材料加工成所需尺寸和形状,并清洁表面以去除杂质和污垢。
2. 遮罩制备:根据所需的结构设计制作遮罩。
遮罩是一种覆盖在材料表面的薄膜,通过它来控制蚀刻液接触材料的位置和方式。
3. 蚀刻液准备:根据材料的性质和所需的蚀刻速率选择适当的蚀刻液。
一般来说,蚀刻液是一种酸性或碱性溶液,可以与材料发生化学反应。
4. 蚀刻机设置:根据材料类型和蚀刻要求,调整蚀刻机的参数,如温度、浸泡时间、液体浓度等。
5. 蚀刻操作:将材料放置在蚀刻槽中,使其与蚀刻液接触。
使用机械手或自动化系统控制材料在蚀刻液中的位置和运动。
6. 监测和控制:通过实时监测蚀刻过程中材料的蚀刻速率和表面质量,及时调整蚀刻参数,确保蚀刻过程的准确性和稳定性。
7. 清洗和处理:蚀刻完成后,将材料从蚀刻槽中取出,并用水或其他溶液洗净蚀刻液残留。
接下来,可能需要进行后续的处理步骤,如去除遮罩,清洗再生,以及其他化学或物理处理。
需要注意的是,蚀刻机的操作要求技术和经验,操作者必须严格遵守操作规程和安全操作规定,以确保人身安全和设备正常运行。
在蚀刻过程中应及时了解蚀刻机的性能和限制,避免蚀刻不均匀、蚀刻深度超出设计要求、蚀刻产生的副产品等问题的发生。
刻蚀机操作培训之一硬件介绍

>90%
MTBF
>250h
MTTR
<4h
MTBC
>200 RFH
MTTC
<6h
设备规格
1. 概述
第2页/共44页
气路系统
Cl2
200sccm
BCl3
300sccm
SF6
300sccm
Ar
200sccm
N2
200sccm
O2
300sccm
真空系统
压力控制范围
0~100mTorr
工艺腔室本底真空
传输工作原理机械手从装载腔取出未刻蚀的托盘,然后旋转180度送入反应腔;或从反应腔取出刻蚀后的托盘,然后旋转180度送回装载腔。
4. 传输模块
第41页/共44页
传输模块的组成及功能
1.机械手本体2.控制柜3.示教盒
技术指标结构形式:柱坐标SCARA式手臂驱动方式:伺服电机重复定位精度:±0.05mm/±0.003°
3. 工艺模块
第23页/共44页
托盘设计
2” PSS 22片
4” PSS 7片
更换托盘即可实现2英寸向4英寸的升级
3. 工艺模块
2” GaN 27片
4” GaN 7片
第24页/共44页
基片控温
高性能,宽温度范围Chiller( -20℃~+40℃ )高压力稳定性,低漏率的氦气控制(649规)
3. 工艺模块
第18页/共44页
特性和优点石英喷嘴抗等离子体耐腐蚀内壁粗糙度控制稳定气流减少颗粒污染喷嘴出口均匀气体分布稳定的气流
均匀气体分布
稳定的气流
3. 工艺模块
进气喷嘴
刻蚀工艺与设备培训

22
4
ICP刻蚀原理及设备
RIE与ICP比较
RIE
离子密度低( ~109 ~1010/cm3) 离子密度与离子能量不能分别控制( 离子密度大,离子能量也大) 离子能量低,刻蚀速率低 低压下刻蚀速率低 DC Bias高损伤大
ICP
离子密度高 (>1011/cm3)(刻蚀速率 高) 离子密度由ICP功率控制,离子能 量由RF功率控制 在低离子能量下可控离子流量达到 高刻蚀速率(形貌控制) 低压下由于高离子流量从而维持高 刻蚀速率 低DC bias损伤小
Si3N4刻蚀 光刻胶掩膜 Profile 85-90° 刻蚀均匀性 <+/-5% 典型刻蚀速率: Si3N4 4000 Å/min PSG 6000 Å/min 选择比: Si3N4: PR >3:1 Si3N4: aluminum >100:1
20
3
RIE刻蚀原理及设备
RIE 操作注意事项
• 初始设置为6寸片刻蚀,必须放在两侧片架里,左侧进 片,右侧出片 • 每次程序运行前要将两边片架重新手动定位 • 射频源功率不宜设置过高,小于500W
2
IBE刻蚀原理及设备
IBE-A150设备
离子源 电控柜
真空室
分子泵
冷却水
12
2
IBE刻蚀原理及设备
IBE相关刻蚀数据
离子能量:350eV 材料 Ni SiO2 Ge Si 刻蚀速率 nm/min 17-18 17-18 33-34 17-18 材料 Ti Al TiN GaAs 刻蚀速率 nm/min 7-8 15-16 5-6 35-40 材料 GaN Au ITO AZ胶 刻蚀速率 nm/min 34-36 55 32-34 18
刻蚀间工艺培训2培训资料共27页文档

谢谢
11、越是没有本领的就越加自命不凡。——邓拓 12、越是无能的人,越喜欢挑剔别人的错儿。——爱尔兰 13、知人者智,自知者明。胜人者有力,自胜者强。——老子 14、意志坚强的人能把世界放在手中像泥块一样任意揉捏。——歌德 15、最具挑战性的挑战莫过于提升自我。——迈克尔·F·斯特利
刻蚀间工艺培训2培训资料
16、自己选择的路、跪着也要把它走 完。 17、一般情况下)不想三年以后的事, 只想现 在的事 。现在 有成就 ,以后 才能更 辉煌。
18、敢于向黑暗宣战的人,心里必须 充满光 明。 19、学习的关键--重复。
20、能 所向披 靡。
激光刻蚀操作规程培训

激光刻蚀操作规程培训激光刻蚀操作规程培训一、操作概述激光刻蚀是一种常见的微细加工技术,通过高能激光束的蚀刻作用,将材料表面或内部部分物质蒸发或烧蚀,实现对材料进行精细加工的过程。
本次培训旨在向操作人员介绍激光刻蚀的操作规程以及相关注意事项,以确保操作安全和加工效率。
二、操作规程1. 操作前准备- 检查激光刻蚀设备的运行状态,确保各部件正常工作。
- 检查激光刻蚀工作台的环境清洁度,清除杂物和灰尘。
- 穿戴个人防护装备,包括防护眼镜、防护手套等。
2. 材料准备- 准备待加工材料,包括样品或工件。
- 对于需要固定的材料,采用夹具或者其他固定装置进行固定。
3. 参数设置- 根据材料的特性和加工要求,设置合适的激光功率、扫描速度、脉冲频率等参数。
- 注意选择合适的激光工作模式,包括连续激光和脉冲激光。
4. 操作步骤- 打开激光刻蚀设备的电源,启动设备,并进行预热。
- 确认激光刻蚀头的位置和对准,确保激光能够准确照射到待加工材料上。
- 进行试刻,通过调整参数,确定合适的刻蚀效果。
- 进行正式的刻蚀操作,根据需求进行刻蚀加工。
5. 操作注意事项- 操作人员应保持警觉,切勿将手部或其他物体靠近激光束。
- 激光刻蚀过程中,切勿随意更改参数,以免影响刻蚀效果。
- 操作人员应保持通畅的听力和健康状态,避免因激光噪音或辐射引起不适。
6. 刻蚀后处理- 刻蚀完成后,关闭激光刻蚀设备,断开电源。
- 对加工后的材料进行检查,确保刻蚀效果符合要求。
- 清理工作台和设备,保持整洁。
三、操作安全1. 避免直接观察激光刻蚀过程,以免损伤视力。
2. 避免长时间暴露在激光束下,以免皮肤灼伤。
3. 坚守激光刻蚀设备的安全操作规程,严禁随意修改设备结构或参数。
4. 若发生设备故障或异常情况,立即停止操作并向维护人员报告。
四、事故处理1. 如果出现事故,如激光束误伤或设备故障,操作人员应立即停止操作并采取紧急措施。
2. 汇报事故情况,并及时向相关责任人说明情况。
刻蚀工艺培训

液,去除硅片表面的磷硅玻璃,主要发生下列化学反应:
HF+SiO2→ H2SiF6 + H2O
四、工艺常见问题以及解决方法
4.1、腐蚀深度:工艺控制在1.2±0.2μm
检测仪器:电子称
腐蚀深度是表征片子刻通与否的一个重要参数,通过
测量刻蚀前后片子减薄量,可以计算出腐蚀深度,根据具
体测量情况可以改变工艺参数:
3.2 碱洗槽
KOH喷淋中和前道刻蚀后残留在硅片表面的酸液,去 除硅片表面的多孔硅及其杂质,去除扩散形成的染色, KOH溶液依靠冷却水降温保持在20℃左右,主要发生下列 化学反应:
Si+2KOH+H2O = K2SiO3+2H2↑
3.3 酸洗槽
HF循环冲刷喷淋中和前道碱洗后残留在硅片表面的碱
负责刻蚀工序点检表格(各台设备的运行情况与关键参数点检表)的编写。
协助工程师,安排刻蚀段的排查或改进实验,如有需要,与其他工序或是其他 职能部门进行沟通,实验结束后,及时给出实验报告。
完成安排的其他工作
工程师: 关注当天的效率、碎片率、良品率等参数、化学品用量,对于出现的外观不良、漏电或是效
Rinse2
HF bath
Rinse3
Dryer2
3.1 刻蚀槽
所用溶液为HF+HNO3+H2SO4,边缘刻蚀,除去边缘PN结,使电流朝同一方
向流动,发生下列化学反应:
3Si + 18HF + 4HNO3 → 3H2SiF6 + 8H2O + 4NO↑
注意:扩散面须向上放置, H2SO4硫酸不参与反应,仅仅是增加氢离子浓度 ,加快反应,增加溶液黏度(增大溶液与PSG薄层间的界面张力)和溶液密度 ,使硅片很好的浮于反应液上(仅上边缘2mm左右和下表面与液体接触)。
刻蚀原理及工艺培训

维护保养
辉光前必须按下橙色按钮对电子管预热10—15min。 。 辉光前必须按下橙色按钮对电子管预热 辉光结束后须冷却15min后,才可关闭电源。 高频电源实际使用功率不能超过800W。 高频电源地线必须独立接地,不允许与其它设备共用地。 反应管需定期旋转,以便延长其使用寿命。 长期停机时反应室应抽为真空状态,以免被污染。 做完一个循环后,若不立即做下一个循环,应盖上盖子。 每天要清洁反应室,特别是密封部位,否则真空漏气。 非设备人员请勿调节高频部分,有问题通知设备人员。
冷热探针测试注意
确认万用表工作正常,量程置于200mV。 冷探针连接电压表的正电极,热探针与电压表的负极相连。
等离子体刻蚀工艺原理
等离子体刻蚀机是基于真空中的高频激励而产生的辉光 等离子体刻蚀机是基于真空中的高频激励而产生的辉光 真空中的高频激励而产生的 放电将四氟化碳中的氟离子电离出来从而获得化学活性 放电将四氟化碳中的氟离子电离出来从而获得化学活性 微粒与被刻蚀材料起化学反应产生辉发性物质进行刻蚀 的。同时为了保证氟离子的浓度和刻蚀速度必须加入一 氧气生成二氧化碳 定比例的氧气生成二氧化碳。 定比例的氧气生成二氧化碳。 这种腐蚀方法也叫做干蚀法 干蚀法。 这种腐蚀方法也叫做干蚀法。 生产过程中, 中掺入O2,这样有利于提高Si和 生产过程中,在CF4中掺入 ,这样有利于提高 和 中掺入 SiO2的刻蚀速率。 的刻蚀速率。 的刻蚀速率
压力控制系统
压力控制仪 电容式薄膜压力 变送器 电子执行器 蝶阀
高频电源和匹配器技术性能
最大输出功率10~1000W 板极电压200~2700V 板极电流0~500mA 转换效率大于80% 振荡频率13.56MHz 反射功率调配小于5% 连续工作时间小于4h
刻蚀机作业指导

刻蚀机作业指导引言概述:刻蚀机是一种常用的半导体制造设备,用于在硅片表面进行微细加工。
正确的刻蚀机操作是确保制造过程高质量和高效率的关键。
本文将为您提供一份刻蚀机作业指导,以帮助您正确使用刻蚀机。
一、刻蚀机的基本原理与操作1.1 刻蚀机的基本原理刻蚀机利用化学反应或物理过程,将特定材料从硅片表面去除。
常用的刻蚀方法包括湿法刻蚀和干法刻蚀。
湿法刻蚀是利用化学溶液溶解材料,而干法刻蚀则是利用气体或等离子体去除材料。
1.2 刻蚀机的操作步骤(1)准备工作:首先检查刻蚀机的各项设备是否正常运行,确保刻蚀室干净无尘。
然后将硅片放置在刻蚀机的夹持装置中,并确保夹持装置牢固。
(2)设定刻蚀参数:根据所需刻蚀的材料和深度,设定刻蚀机的相关参数,如刻蚀时间、功率等。
这些参数的设定需要根据实际情况和经验进行调整。
(3)开始刻蚀:关闭刻蚀室的门,启动刻蚀机,并根据设定的参数开始刻蚀。
在刻蚀过程中,要注意观察刻蚀情况,以确保刻蚀效果符合要求。
二、刻蚀机的操作注意事项2.1 安全操作在进行刻蚀机操作时,要注意安全。
首先,佩戴适当的个人防护装备,如手套、防护眼镜等。
其次,要确保刻蚀机的电源接地良好,以防止静电引起的危险。
此外,刻蚀室内的化学品要妥善存放,避免泄漏和误操作。
2.2 确保刻蚀质量刻蚀质量是刻蚀机操作的核心目标。
在刻蚀过程中,要确保刻蚀室的温度和湿度适宜,以保证刻蚀效果。
同时,要定期检查刻蚀机的设备和刻蚀液的质量,及时更换和维护,以确保刻蚀质量的稳定和一致性。
2.3 确保设备维护刻蚀机是一种复杂的设备,需要定期进行维护和保养。
维护工作包括清洁刻蚀室、更换刻蚀液、检查和更换刻蚀机的零部件等。
定期维护可以延长刻蚀机的使用寿命,提高设备的稳定性和可靠性。
三、常见刻蚀机故障及处理方法3.1 刻蚀液泄漏刻蚀液泄漏是刻蚀机常见的故障之一。
处理方法包括立即停止刻蚀并关闭刻蚀室的门,清理刻蚀液,并检查刻蚀机的密封性。
3.2 刻蚀不均匀刻蚀不均匀是刻蚀机操作中常见的问题。
- 1、下载文档前请自行甄别文档内容的完整性,平台不提供额外的编辑、内容补充、找答案等附加服务。
- 2、"仅部分预览"的文档,不可在线预览部分如存在完整性等问题,可反馈申请退款(可完整预览的文档不适用该条件!)。
- 3、如文档侵犯您的权益,请联系客服反馈,我们会尽快为您处理(人工客服工作时间:9:00-18:30)。
Tel/lam 氮化硅刻蚀机培训教案
一简介:
Tel/lam 氮化硅刻蚀机是一种平板式的干法刻蚀设备,用于氮化硅的干法刻蚀,其工作原理为特种气体SF6,CHF3在RF下电离并与氮化硅发生反应。
二结构组成
它由以下几部分组成:主机部分、电源部分、泵组部分、射频部分和气体供给部分部分。
1主机部分:它是氮化硅刻蚀机的主体部分,包括显示器、传递腔、反应腔、传动系统及设备的主要控制系统。
2电源部分:系统供电208V进入,经变压器,继电器等变为所需的电压输出。
该设备泵组电源由电源柜控制。
3射频部分:在气体反应时提供的高频电源,以便气体在高真空环境下电离,产生等离子体。
射频匹配系统位于主机上部,用于对射频源所提供的高频通过可变的电感电容进行匹配,以便提供给设备稳定高效的射频。
射频电源为208VAC供电,外接冷却水为本体发热元件降温。
4泵组部分:由机械泵、增压泵和真空管线构成抽反应腔的真空系统,以达到工艺反应时所需的真空度要求。
由18泵及配套的真空管线用于抽传递腔的真空。
现在我们使用的泵组位于一楼回风区内。
5 气体供给部分:由特气柜、特气瓶和特气管线构成。
用于提供反
应所需的特种气体,其中用于提供特气的特气瓶至于一楼回风区内,特气经二次减压提供给设备,并由质量流量计进行控制。
三T el/lam 氮化硅刻蚀机的基本操作
1 当操作本台设备时,应首先检查该设备的动力条件,具体条件如下:
压缩空气:±氮气: ±用于射频冷却的冷却水是否有,反应所用的特气是否有,设备面板的电极温度是否和设定的温度相符,排风是否正常。
2操作:按照设备操作流程进行操作
3面板按键:LOAD 用于下载初始化程序 SAVE保存程序 RECIPE 用于编辑反应的程序STATUS 用于观察设备所处的状态PARAMETERS用于设置设备参数 OPTIONS用于设备的手动操作及观察设备运行时的参数变化 START 开始设备开始运行 STOP终止下一片硅片从传片筐传出 FIELD SELECT 用于切换设定状态
设备面板另有四个用于光标移动的按健及一个数字键盘
四 Tel/lam 氮化硅刻蚀机的常见故障及应急故障处理
1真空故障:主要显示为反应腔或者传递腔真空达不到,真空漏率较大。
可能引起该故障的主要原因为:真空泵能力下降,真空管线连接不好,设备内部密封件老化,真空监测系统不准确。
传递腔不能达到大气压.其故障原因为用于检测其是否达到大气
压的压力开关松动或损坏、充气的阀门没有打开或者是系统氮气没有供给
2 射频故障:主要为射频信号加不上,反射功率大,射频源温度过高报警。
可能引起该故障的主要原因为:射频电缆连接处接触不好,匹配单元连接不好,射频源控制板故障,温度高(OVER HEAT)是因为冷却水管线堵塞造成。
4传递系统故障:主要表现为硅片在传递皮带上不动作;装载片筐的升降台不动作;机械手传接片子位置不正,其直接的影响会使硅片碎裂,严重时会导致主反应腔内的针(用于托片子)弯曲。
可能引起故障的原因为:传递皮带断裂及带动皮带的电机出现故障;升降台的保险断开,控制系统有故障此时系统复位即可,机械手的限位不正确或气缸(电机)有故障。
5控制系统故障:常见为屏幕出现乱码。
产生此故障的原因通常为存储块接触不良或是电源不稳定。
6电极冷却部分故障:主要表现为电极温度升高.其产生的原因为用于冷却的系统无氟利昂,热交换器水箱温度设置过低导致水冷凝,传递水的管线堵塞,用于转换水路的电磁阀不能正常动作。