炉内脱硫原理
炉内脱硫工艺

炉内脱硫工艺炉内脱硫工艺是一种用于减少燃煤电厂和工业锅炉排放的二氧化硫(SO2)的技术。
这种工艺通过在燃烧过程中添加脱硫剂,将二氧化硫转化为更易于处理的形式,从而达到减少大气污染的目的。
炉内脱硫工艺的核心是在燃烧过程中添加脱硫剂,常用的脱硫剂有石灰石、石膏等。
这些脱硫剂在高温下与燃烧产生的二氧化硫反应,生成硫酸钙等硫化物。
通过这种反应,二氧化硫得以转化为无害的物质,从而达到脱硫的效果。
炉内脱硫工艺的关键是要确保脱硫剂能够与燃烧中的二氧化硫充分接触。
为了实现这一点,燃煤电厂和工业锅炉通常采用喷射式脱硫装置。
这种装置将脱硫剂喷射到燃烧区域,与燃烧产生的二氧化硫进行反应。
在反应过程中,烟气中的二氧化硫会被脱硫剂吸附,形成硫酸钙等硫化物。
炉内脱硫工艺的优点是工艺简单、投资成本低、操作维护便捷。
相比于烟气脱硫工艺,炉内脱硫工艺不需要额外的设备和设施,只需在燃烧过程中添加脱硫剂即可。
这使得炉内脱硫工艺成为一种经济有效的选择。
此外,炉内脱硫工艺还可以在短时间内达到较高的脱硫效率,对SO2的去除率可以达到90%以上。
然而,炉内脱硫工艺也存在一些不足之处。
首先,炉内脱硫工艺只能对二氧化硫进行处理,对其他污染物如氮氧化物(NOx)无法有效处理。
其次,炉内脱硫工艺需要在燃烧过程中添加脱硫剂,这可能会对燃烧过程产生一定的影响,降低燃烧效率。
此外,在脱硫剂的选择和投加量上也需要一定的技术支持,以确保脱硫效果和经济效益的平衡。
为了提高炉内脱硫工艺的效率,研究人员不断进行技术改进和创新。
他们致力于寻找更高效的脱硫剂和更合理的投加方式,以提高脱硫效果和降低成本。
此外,他们还研究如何将炉内脱硫工艺与其他污染治理技术相结合,实现多污染物的综合治理。
炉内脱硫工艺是一种有效的二氧化硫减排技术。
通过在燃烧过程中添加脱硫剂,可以将二氧化硫转化为无害的硫酸钙等硫化物,达到脱硫的效果。
虽然炉内脱硫工艺存在一些不足之处,但通过技术改进和创新,可以进一步提高其效率和经济性。
炉内喷钙的脱硫原理

炉内喷钙的脱硫原理炉内喷钙是一种常见的炉内脱硫技术,被广泛应用于能源领域,特别是煤炭燃烧过程中的烟气脱硫。
它采用钙基吸收剂将炉内废气中的二氧化硫(SO2)转化为无害的石膏,以达到减少环境污染和保护设备的目的。
喷钙的脱硫原理主要涉及两个关键步骤:吸收和转化。
在炉内,当煤燃烧产生的烟气中含有高浓度的SO2时,喷钙系统通过喷洒钙基吸收剂,如石灰石(CaCO3)或石膏(CaSO4),使其与SO2发生反应。
首先,通过喷洒器将细小的钙基吸收剂颗粒均匀地喷洒到炉内废气中,在喷洒过程中,石灰石或石膏颗粒与烟气中的SO2发生接触与吸收作用。
此时,SO2与钙基吸收剂中的碱土金属阳离子(如钙)反应,生成点状或块状的无害钙基硫酸盐。
接下来,石灰石或石膏中的钙基硫酸盐会与其他废气中的成分反应,形成石膏(CaSO4)。
这是一个重要的步骤,因为石膏是一种无害的化合物,可以进行高效的处理和回收利用,减少对环境的负担。
炉内喷钙技术的优点在于其操作相对简单,可以方便地与燃烧设备集成。
此外,喷钙可以在较低的温度下进行,因此可以减少能源损失。
而且,钙基吸收剂通常易得且经济实惠,可以大规模应用。
然而,炉内喷钙也有一些需要注意的问题。
首先,喷钙过程会产生大量的石膏,需要妥善处理和处置。
其次,在喷钙过程中,需要有精确的控制和监测系统,以确保钙基吸收剂的喷洒量和喷洒效果,从而达到脱硫效果的最佳化。
总的来说,炉内喷钙是一种生动、全面并且具有指导意义的炉内脱硫技术。
通过吸收和转化作用,炉内喷钙系统可以高效地将炉内废气中的SO2转化为无害的石膏,保护环境和设备。
同时,需要注意合理处理产生的石膏和确保喷钙过程的精确控制。
这种技术在能源领域具有重要的应用价值,并可为环保工作做出贡献。
锅炉脱硫脱硝的原理
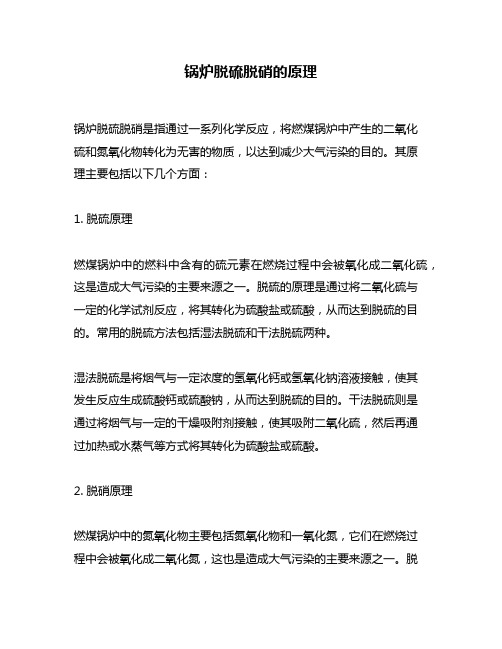
锅炉脱硫脱硝的原理锅炉脱硫脱硝是指通过一系列化学反应,将燃煤锅炉中产生的二氧化硫和氮氧化物转化为无害的物质,以达到减少大气污染的目的。
其原理主要包括以下几个方面:1. 脱硫原理燃煤锅炉中的燃料中含有的硫元素在燃烧过程中会被氧化成二氧化硫,这是造成大气污染的主要来源之一。
脱硫的原理是通过将二氧化硫与一定的化学试剂反应,将其转化为硫酸盐或硫酸,从而达到脱硫的目的。
常用的脱硫方法包括湿法脱硫和干法脱硫两种。
湿法脱硫是将烟气与一定浓度的氢氧化钙或氢氧化钠溶液接触,使其发生反应生成硫酸钙或硫酸钠,从而达到脱硫的目的。
干法脱硫则是通过将烟气与一定的干燥吸附剂接触,使其吸附二氧化硫,然后再通过加热或水蒸气等方式将其转化为硫酸盐或硫酸。
2. 脱硝原理燃煤锅炉中的氮氧化物主要包括氮氧化物和一氧化氮,它们在燃烧过程中会被氧化成二氧化氮,这也是造成大气污染的主要来源之一。
脱硝的原理是通过将二氧化氮与一定的还原剂反应,将其还原成氮气和水,从而达到脱硝的目的。
常用的脱硝方法包括选择性催化还原法和非选择性催化还原法两种。
选择性催化还原法是将烟气与一定浓度的氨水或尿素溶液接触,使其发生反应生成氮气和水,从而达到脱硝的目的。
非选择性催化还原法则是将烟气与一定浓度的碳氢化合物接触,使其发生反应生成氮气和水。
以上就是锅炉脱硫脱硝的主要原理内容。
通过这些化学反应,可以将燃煤锅炉中产生的二氧化硫和氮氧化物转化为无害的物质,从而减少大气污染。
在实际应用中,需要根据锅炉的具体情况选择合适的脱硫脱硝方法,并进行适当的调整和优化,以达到最佳的脱硫脱硝效果。
锅炉脱硫原理

锅炉脱硫原理
锅炉脱硫是指通过一系列的化学与物理反应,将燃煤或燃油锅炉烟气中的二氧化硫(SO2)转化成硫酸盐(SO42-),达到减少大
气污染物的排放的目的。
其主要原理包括湿法脱硫和干法脱硫两种。
湿法脱硫的原理是将含有SO2的烟气通过喷淋装置与喷雾剂
进行接触反应,将SO2气体转化成液体或固体硫酸盐。
喷雾
剂通常是碱性溶液,如石灰浆或氨水溶液。
喷雾与烟气接触时,SO2气体会与喷雾剂中的氢氧化物发生反应生成硫酸盐和水。
干法脱硫主要基于SOR(Sulfation-oxidation-reduction)反应
原理。
该过程通过在烟气中加入硫化剂(如石灰石或活性炭),使烟气中的SO2与硫化剂发生反应,生成硫酸盐或其他易于
分离的化合物。
硫化剂会促使SO2氧化为SO3,然后与硫化
剂表面的水分子反应形成亚硫酸盐,再经由氧化还原反应还原生成硫酸盐。
这种方法适用于高温烟气中SO2的去除。
锅炉脱硫原理的选择取决于燃料的性质、运行条件和减排要求。
无论是湿法脱硫还是干法脱硫,都可以有效地减少锅炉烟气中的SO2排放,从而降低大气污染物的含量。
脱硫技术_干法
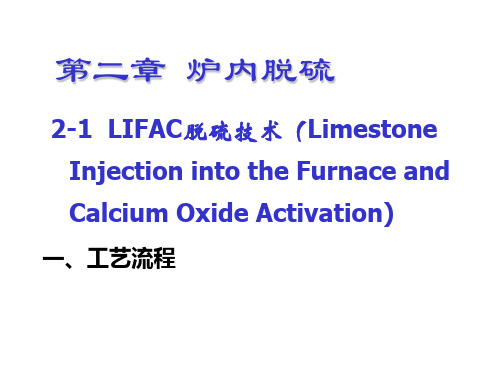
五、喷雾干燥法技术特点
脱硫效率较高,75~85%
投资和运行费用较少、占地较小
反应产物为干的,便于处理 没有废水二次污染
主要应用问题
容器湿壁,管道堵塞
喷雾器的磨损和破裂
烟道和除尘器腐蚀
对除尘器的性能有影响
喷雾干燥塔湿壁情况
喷雾干燥塔湿壁情况
山东黄岛电厂半干法脱硫系统
和SO2作用而脱硫。
CaO H 2O Ca(OH ) 2
Ca(OH ) 2 SO2 H 2O CaSO3 2 H 2O 1 Ca(OH ) 2 SO2 H 2O O2 CaSO4 2 H 2O 2
三、影响参数
1、炉内参数的影响 (1)、温度的影响 最佳的温度为850~1100℃。
H /D 3~5 H / D 0.5 ~ 1
吸收塔下部锥角≤600,塔内烟气停留时间10~12s。 3. 除尘设备 一般采用袋式除尘器和电除尘器。袋式除尘器中的
脱硫效率可达总效率的15~30%,电除尘器中的脱
硫效率可达总效率的10~15%。 4. 运行控制系统 浆液调节系统 联锁保护系统
反应产物以干态脱硫渣形式排出。
喷雾干燥法
烟气循环流化床
NID技术
3-6-1 喷雾干燥法
工艺原理
工艺流程 影响脱硫效率的因素 主要工艺系统
主要特点
应用实例
一、工艺原理
1、化学过程:
生石灰制浆: CaO H 2O Ca(OH ) 2 SO2被液滴吸收:
SO2 H 2O H 2 SO3
* *
H 2 SO4 nH2O* ( H 2 SO4 nH2O)*
影响SO2吸附的因素 废气中含有足够的氧和水蒸气(化学吸附需要) 吸附温度:吸附温度下降,吸附效率增加。 气流速度:气流速度增加,吸附效率下降。 对吸附剂进行处理:利用对SO2氧化起催化作用 的金属盐对活性炭进行处理,以提高活性炭的 吸附能力,如Cu、Fe、Ni、Mn、Cr和Ce等。 吸附剂的种类:各种活性炭由于其制造、原料 的不同,其吸附能力不同。
锅炉脱硫脱硝原理

锅炉脱硫脱硝原理
锅炉脱硫的原理是通过添加脱硫剂吸收烟气中的二氧化硫(SO2),将其转化为硫酸钙(CaSO4)或硫酸钠(Na2SO4)等固体废物,阻止其进入大气中。
常用的脱硫剂有石灰石(CaCO3)、石膏(CaSO4•2H2O)等。
脱硝的原理是通过加入氨水或尿素等还原剂在高温条件下与烟气中的氮氧化物(NOx)发生反应,生成氮气(N2)和水蒸气
(H2O)。
这个过程称为选择性催化还原脱硝。
脱硫和脱硝一般都在锅炉的烟气净化系统中进行。
脱硫装置常用的有湿法烟气脱硫和半干法脱硫。
湿法烟气脱硫主要通过喷淋鼓风或喷淋旋流器,在脱硫剂和烟气中进行充分接触,液相吸收二氧化硫。
而半干法脱硫主要依靠脱硫剂的颗粒直接与烟气反应,生成硫酸钙等固体物质。
脱硝装置主要有选择性催化还原脱硝、非选择性催化还原脱硝和吸收式脱硝等。
选择性催化还原脱硝是最主要的一种方法,其主要依靠金属催化剂(如钒、钛、银等催化剂)在高温下促进氨水与氮氧化物的反应。
非选择性催化还原脱硝则利用金属催化剂催化氨水的氧化分解生成氨气作为还原剂,再与烟气中的氮氧化物反应。
吸收式脱硝则利用吸收剂吸收烟气中的二氧化硫和氮氧化物。
循环流化床锅炉炉内脱硫原理与因素浅析

循 环流 化床 锅炉 运行 实践 表 明 ,随着 炉 内 C a / S 摩 尔 比小 于 2 . 5 范 围 内,脱 硫 效 率 随
1 4— —
流化 床燃 烧直 接脱 硫 是 由于 其燃 烧特 性所 添加 石灰 石量 的增 加 ,脱 硫 效率 逐渐 提高 ,在
C a / S摩 尔 比增 加提高 很快 ,当继续增 加 C a / S 价 格造 成锅 炉 运行 成本 增 加等 。所 以 ,我 们在
含 硫量从低 于 1 % 到高 达 l 0 % 的范 围内变 化 , 我 国大 多数 煤 的含 硫 量 介 于 2 %,这些 燃 料 燃 氧化 硫 的形 式释 放 出来 ,成 为 大 气 中 的 污 染
3 .脱硫影 响因素
影 响脱硫 的因素 包括 床温 ,钙硫 比,床 深
( 1 ) 床 温
( 2 ) 钙硫 比 ( C a / S)
Ca O+S O2 +l / 2 02 =CA S O4
Ca C03 +8 02 : Ca SO3 + C02
Ca CO3 + S O2 +1 / 2 02 = Ca S O4 + C02
( 2 ) 脱 硫特点 确定 的 ,其脱硫 特点如 下 :
摩 尔 比时 ,脱硫 效率 增 加速 度 会 明显 减慢 。而 设 计锅炉 时 ,设置 合理 、经济 的 C a / S 摩 尔 比 且 ,C a / S 摩 尔 比过 高 还会 带 来 一些 副 作 用 ,
为 2~ 2 . 5 。图 3为 C a / S摩 尔 比与脱硫 效率
的关系 。
吸 附剂 的硫酸 盐化 率直 接 与颗 粒单 位表 面 积 有 关 。对 于球 形 颗粒 ,盐 化率 与颗 粒 直径 成 反 比。增大 颗 粒 尺寸 有 可 能起 到 与 减少 C a / S 实际上仍 存在复 杂的 关系 。 4 .结 束语
脱硫的工作原理

脱硫的工作原理
脱硫是指将燃煤和燃油中的硫化物物质去除掉的过程。
脱硫的工作原理主要有以下几种方法:
1. 燃煤脱硫:利用煤中的硫化物(如硫化氢、二氧化硫等)与吸收剂(如氧化钙、氢氧化钠等)进行化学反应,生成不溶于水的硫化物沉淀物或水溶性硫酸盐,从而达到去除硫的目的。
2. 燃油脱硫:燃油中的硫化物主要以硫氧化物的形式存在,可以通过添加一些特定的脱硫剂(如反应性镁、氧化锌等)与其发生反应,使硫氧化物转变为无害的硫酸盐沉淀物,从而使燃油达到脱硫效果。
3. 燃气脱硫:燃气中的硫化氢主要通过催化剂(如铁氧化物、氧化铜等)与硫化氢反应生成硫化铁等物质,从而实现脱硫。
另外一种常用的方法是通过吸收剂(如氧化钙、氨水等)与燃气中的硫化氢发生化学反应,生成无害的硫酸盐或硫化物沉淀物,达到脱硫效果。
4. 生物脱硫:利用一些硫氧化细菌或硫还原细菌来降解燃料中的硫化物。
这些细菌可以利用硫化物作为电子供体或受体,进行代谢过程,将硫化物转变为硫酸盐或硫氧化物,从而实现脱硫。
通过上述不同的脱硫方法,可以有效地减少燃料中的硫含量,降低大气污染物排放,改善环境质量和人体健康。
炉内喷钙脱硫反应方程式
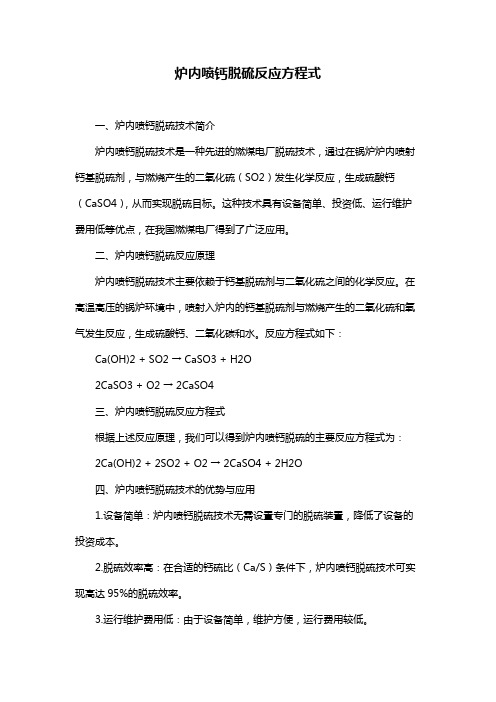
炉内喷钙脱硫反应方程式
一、炉内喷钙脱硫技术简介
炉内喷钙脱硫技术是一种先进的燃煤电厂脱硫技术,通过在锅炉炉内喷射钙基脱硫剂,与燃烧产生的二氧化硫(SO2)发生化学反应,生成硫酸钙(CaSO4),从而实现脱硫目标。
这种技术具有设备简单、投资低、运行维护费用低等优点,在我国燃煤电厂得到了广泛应用。
二、炉内喷钙脱硫反应原理
炉内喷钙脱硫技术主要依赖于钙基脱硫剂与二氧化硫之间的化学反应。
在高温高压的锅炉环境中,喷射入炉内的钙基脱硫剂与燃烧产生的二氧化硫和氧气发生反应,生成硫酸钙、二氧化碳和水。
反应方程式如下:
Ca(OH)2 + SO2 → CaSO3 + H2O
2CaSO3 + O2 → 2CaSO4
三、炉内喷钙脱硫反应方程式
根据上述反应原理,我们可以得到炉内喷钙脱硫的主要反应方程式为:2Ca(OH)2 + 2SO2 + O2 → 2CaSO4 + 2H2O
四、炉内喷钙脱硫技术的优势与应用
1.设备简单:炉内喷钙脱硫技术无需设置专门的脱硫装置,降低了设备的投资成本。
2.脱硫效率高:在合适的钙硫比(Ca/S)条件下,炉内喷钙脱硫技术可实现高达95%的脱硫效率。
3.运行维护费用低:由于设备简单,维护方便,运行费用较低。
4.适用范围广:炉内喷钙脱硫技术适用于各种容量和类型的燃煤锅炉,具有良好的通用性。
五、结论与展望
炉内喷钙脱硫技术作为一种高效、经济的脱硫方法,在我国燃煤电厂取得了显著的环保效益。
随着环保政策的日益严格,炉内喷钙脱硫技术将进一步优化和完善,以满足更加严格的排放标准。
炉内脱硫工艺

炉内脱硫工艺
炉内脱硫工艺是一种常用的污染治理技术,主要用于燃煤、燃油等化石燃料的燃烧过程中产生的二氧化硫进行脱硫。
该技术的原理是在燃烧过程中向炉内加入脱硫剂,使其与二氧化硫发生化学反应,生成不易挥发的硫酸钙等化合物,从而达到减少或消除二氧化硫排放的效果。
炉内脱硫工艺有许多不同的实现方法,其中常见的技术包括湿法脱硫和干法脱硫。
湿法脱硫是通过向燃烧过程中喷洒氢氧化钙等脱硫剂的方式,将硫化氢和氧化钙反应生成硫酸钙,从而实现脱硫。
干法脱硫则是通过向燃烧过程中添加硫化钠等脱硫剂,使其与二氧化硫发生反应生成硫酸钠和硫酸钙等化合物,在烟气中形成微小的颗粒,随着烟气一同排放到大气中。
相比于其他的脱硫技术,炉内脱硫工艺具有操作简便、能耗低、成本较低等优点,因此在实际应用中得到了广泛的应用。
同时,炉内脱硫工艺也存在一些局限性,如脱硫效率较低、脱硫剂对设备的腐蚀性较强等问题,需要在实践中进一步完善和改进。
总之,炉内脱硫工艺是一种实用性强、经济效益好的污染治理技术,对于改善大气环境质量、保护人民健康具有重要意义。
- 1 -。
炉内喷钙的脱硫原理(一)
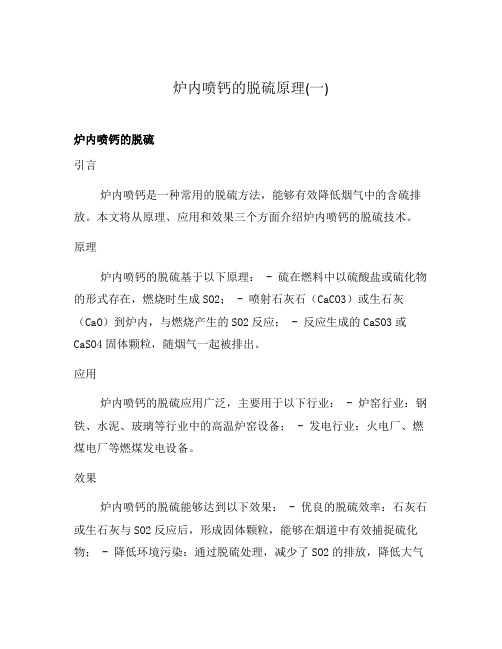
炉内喷钙的脱硫原理(一)炉内喷钙的脱硫引言炉内喷钙是一种常用的脱硫方法,能够有效降低烟气中的含硫排放。
本文将从原理、应用和效果三个方面介绍炉内喷钙的脱硫技术。
原理炉内喷钙的脱硫基于以下原理: - 硫在燃料中以硫酸盐或硫化物的形式存在,燃烧时生成SO2; - 喷射石灰石(CaCO3)或生石灰(CaO)到炉内,与燃烧产生的SO2反应; - 反应生成的CaSO3或CaSO4固体颗粒,随烟气一起被排出。
应用炉内喷钙的脱硫应用广泛,主要用于以下行业: - 炉窑行业:钢铁、水泥、玻璃等行业中的高温炉窑设备; - 发电行业:火电厂、燃煤电厂等燃煤发电设备。
效果炉内喷钙的脱硫能够达到以下效果: - 优良的脱硫效率:石灰石或生石灰与SO2反应后,形成固体颗粒,能够在烟道中有效捕捉硫化物; - 降低环境污染:通过脱硫处理,减少了SO2的排放,降低大气污染; - 提高设备使用寿命:减少了烟气中的硫化物含量,减轻了对设备的腐蚀。
总结炉内喷钙是一项十分有效的烟气脱硫技术,通过在燃烧过程中喷射石灰石或生石灰,能够捕捉和固化硫化物,从而降低烟气中的SO2排放量。
该技术应用广泛,效果显著,对于减少大气污染、保护环境和提高设备使用寿命都具有积极意义。
操作步骤炉内喷钙的脱硫通常需要以下步骤: 1. 准备石灰石或生石灰:选择适用于具体应用场景的石灰石或生石灰,确保其成分纯度和活性适宜。
2. 设计喷钙系统:根据实际情况设计合适的喷钙系统,包括喷钙设备、喷钙位置和喷钙量等。
3. 控制喷钙时机:根据燃烧过程和硫含量,控制喷钙的时机,确保最佳的脱硫效果。
4. 进行喷钙操作:在适当的时机将石灰石或生石灰喷射到炉内,与燃烧产生的SO2进行反应。
5. 监测脱硫效果:通过监测烟气中的SO2排放量和炉内硫含量,评估脱硫效果,并根据需要进行调整。
特点与优势炉内喷钙的脱硫技术具有以下特点和优势: - 执行简单:相对于其他脱硫方法,炉内喷钙操作简单,不需要大规模的设备改造。
炉内喷钙脱硫工艺原理
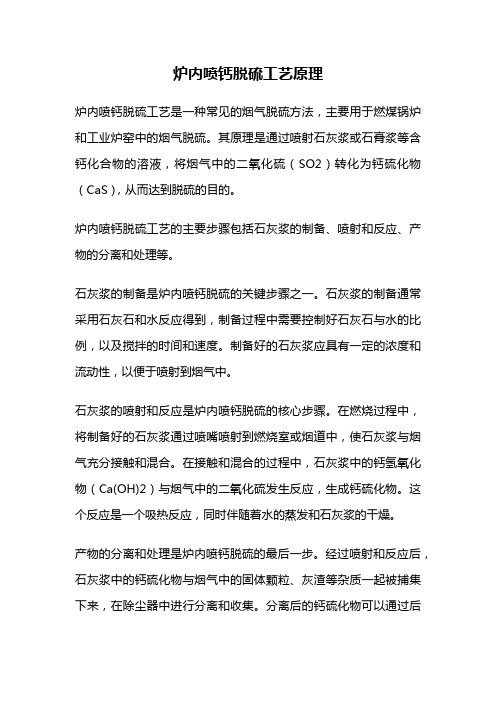
炉内喷钙脱硫工艺原理炉内喷钙脱硫工艺是一种常见的烟气脱硫方法,主要用于燃煤锅炉和工业炉窑中的烟气脱硫。
其原理是通过喷射石灰浆或石膏浆等含钙化合物的溶液,将烟气中的二氧化硫(SO2)转化为钙硫化物(CaS),从而达到脱硫的目的。
炉内喷钙脱硫工艺的主要步骤包括石灰浆的制备、喷射和反应、产物的分离和处理等。
石灰浆的制备是炉内喷钙脱硫的关键步骤之一。
石灰浆的制备通常采用石灰石和水反应得到,制备过程中需要控制好石灰石与水的比例,以及搅拌的时间和速度。
制备好的石灰浆应具有一定的浓度和流动性,以便于喷射到烟气中。
石灰浆的喷射和反应是炉内喷钙脱硫的核心步骤。
在燃烧过程中,将制备好的石灰浆通过喷嘴喷射到燃烧室或烟道中,使石灰浆与烟气充分接触和混合。
在接触和混合的过程中,石灰浆中的钙氢氧化物(Ca(OH)2)与烟气中的二氧化硫发生反应,生成钙硫化物。
这个反应是一个吸热反应,同时伴随着水的蒸发和石灰浆的干燥。
产物的分离和处理是炉内喷钙脱硫的最后一步。
经过喷射和反应后,石灰浆中的钙硫化物与烟气中的固体颗粒、灰渣等杂质一起被捕集下来,在除尘器中进行分离和收集。
分离后的钙硫化物可以通过后续的处理方式得到回收利用或安全处理。
炉内喷钙脱硫工艺的原理是基于钙化合物与二氧化硫的反应。
在喷射和反应过程中,石灰浆中的钙氢氧化物与烟气中的二氧化硫发生反应,生成钙硫化物。
这个反应是一个化学吸收过程,通过将二氧化硫转化为钙硫化物,从而实现烟气中二氧化硫的脱除。
钙硫化物是一种固体物质,能够与其他固体颗粒一起被捕集下来,从而达到脱硫的效果。
炉内喷钙脱硫工艺具有操作简便、投资成本低、脱硫效率高等优点。
然而,也存在着石灰浆制备和喷射、产物的分离和处理等方面的技术难题,需要进一步研究和改进。
此外,炉内喷钙脱硫工艺对燃煤锅炉和工业炉窑的烟气特性有一定的要求,需要根据实际情况进行调整和优化。
炉内喷钙脱硫工艺是一种常见的烟气脱硫方法,通过喷射石灰浆或石膏浆等含钙化合物的溶液,将烟气中的二氧化硫转化为钙硫化物,从而达到脱硫的目的。
炉内脱硫工作原理

炉内脱硫工作原理今天咱来唠唠炉内脱硫这事儿。
你知道吗,这炉内脱硫就像是给炉子里面的那些个有害物质来一场大改造呢。
咱先说说这硫是咋跑到炉子里去的呀。
其实呢,好多燃料里都带着硫这个小“捣蛋鬼”。
像煤炭啊,它本身就含有硫元素。
当这些燃料在炉子里燃烧的时候,硫就跟着一起凑热闹,变成了二氧化硫之类的硫化物。
这些硫化物可不好惹呢,它们要是就这么跑出去了,就会对环境造成好多坏影响,像酸雨啊什么的,那可不得了。
那炉内脱硫就是要把这些硫化物给抓住,不让它们跑出去撒野。
炉内脱硫主要靠的是一些神奇的化学反应。
比如说,往炉子里加入石灰石(CaCO₃),这石灰石就像是一个英勇的小战士。
当炉子里温度升高的时候,石灰石就开始发生反应啦。
它会分解成氧化钙(CaO)和二氧化碳(CO₂),这个过程就像是石灰石变身了一样。
然后呢,这新变出来的氧化钙就开始大展身手喽。
它会和那些硫化物,特别是二氧化硫(SO₂)发生反应。
这个反应就像是一场激烈的战斗,氧化钙会把二氧化硫紧紧抱住,然后生成硫酸钙(CaSO₄)。
你看,原本有害的二氧化硫就被转化成了相对稳定的硫酸钙。
这硫酸钙啊,就可以留在炉子里的灰渣里,不会像二氧化硫那样到处乱跑危害环境啦。
这整个过程就像是一个精心编排的舞台剧。
炉子里的燃料在燃烧,就像是舞台上的灯光和音乐都响起来了。
然后石灰石这个主角登场,先是自己来个华丽变身,再和二氧化硫这个反派进行一场激烈的对决,最后把反派变成了无害的东西。
不过呢,这炉内脱硫也不是那么简单就能完成得特别完美的。
它还受到好多因素的影响呢。
比如说炉子里的温度就很关键。
如果温度不合适,石灰石可能就不能很好地分解,那后面和二氧化硫的反应也就没法好好进行了。
就像一场表演,如果灯光没调好,演员可能就发挥不好一样。
还有啊,石灰石的颗粒大小也很重要。
如果颗粒太大了,它反应起来就会很慢,就像一个大胖子跑步,肯定没有瘦子灵活呀。
而且呢,炉内的气流情况也会影响脱硫的效果。
如果气流太乱了,就像一阵狂风把舞台上的演员都吹得东倒西歪,氧化钙和二氧化硫可能就不能很好地相遇,那反应也就不充分了。
脱硫系统的工作原理
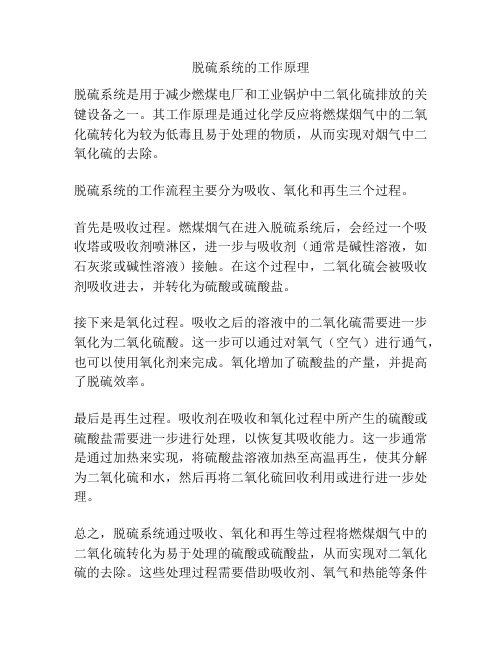
脱硫系统的工作原理
脱硫系统是用于减少燃煤电厂和工业锅炉中二氧化硫排放的关键设备之一。
其工作原理是通过化学反应将燃煤烟气中的二氧化硫转化为较为低毒且易于处理的物质,从而实现对烟气中二氧化硫的去除。
脱硫系统的工作流程主要分为吸收、氧化和再生三个过程。
首先是吸收过程。
燃煤烟气在进入脱硫系统后,会经过一个吸收塔或吸收剂喷淋区,进一步与吸收剂(通常是碱性溶液,如石灰浆或碱性溶液)接触。
在这个过程中,二氧化硫会被吸收剂吸收进去,并转化为硫酸或硫酸盐。
接下来是氧化过程。
吸收之后的溶液中的二氧化硫需要进一步氧化为二氧化硫酸。
这一步可以通过对氧气(空气)进行通气,也可以使用氧化剂来完成。
氧化增加了硫酸盐的产量,并提高了脱硫效率。
最后是再生过程。
吸收剂在吸收和氧化过程中所产生的硫酸或硫酸盐需要进一步进行处理,以恢复其吸收能力。
这一步通常是通过加热来实现,将硫酸盐溶液加热至高温再生,使其分解为二氧化硫和水,然后再将二氧化硫回收利用或进行进一步处理。
总之,脱硫系统通过吸收、氧化和再生等过程将燃煤烟气中的二氧化硫转化为易于处理的硫酸或硫酸盐,从而实现对二氧化硫的去除。
这些处理过程需要借助吸收剂、氧气和热能等条件
来完成。
脱硫系统的设计和运行可以根据具体情况进行调整,以达到高效、低成本、低排放的要求。
炉内脱硫原理
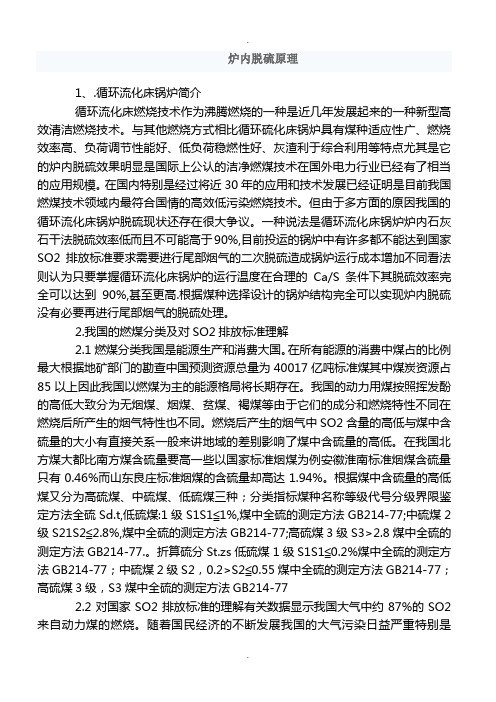
炉内脱硫原理1、.循环流化床锅炉简介循环流化床燃烧技术作为沸腾燃烧的一种是近几年发展起来的一种新型高效清洁燃烧技术。
与其他燃烧方式相比循环硫化床锅炉具有煤种适应性广、燃烧效率高、负荷调节性能好、低负荷稳燃性好、灰渣利于综合利用等特点尤其是它的炉内脱硫效果明显是国际上公认的洁净燃煤技术在国外电力行业已经有了相当的应用规模。
在国内特别是经过将近30年的应用和技术发展已经证明是目前我国燃煤技术领域内最符合国情的高效低污染燃烧技术。
但由于多方面的原因我国的循环流化床锅炉脱硫现状还存在很大争议。
一种说法是循环流化床锅炉炉内石灰石干法脱硫效率低而且不可能高于90%,目前投运的锅炉中有许多都不能达到国家SO2排放标准要求需要进行尾部烟气的二次脱硫造成锅炉运行成本增加不同看法则认为只要掌握循环流化床锅炉的运行温度在合理的Ca/S条件下其脱硫效率完全可以达到90%,甚至更高.根据煤种选择设计的锅炉结构完全可以实现炉内脱硫没有必要再进行尾部烟气的脱硫处理。
2.我国的燃煤分类及对SO2排放标准理解2.1燃煤分类我国是能源生产和消费大国。
在所有能源的消费中煤占的比例最大根据地矿部门的勘查中国预测资源总量为40017亿吨标准煤其中煤炭资源占85以上因此我国以燃煤为主的能源格局将长期存在。
我国的动力用煤按照挥发酚的高低大致分为无烟煤、烟煤、贫煤、褐煤等由于它们的成分和燃烧特性不同在燃烧后所产生的烟气特性也不同。
燃烧后产生的烟气中SO2含量的高低与煤中含硫量的大小有直接关系一般来讲地域的差别影响了煤中含硫量的高低。
在我国北方煤大都比南方煤含硫量要高一些以国家标准烟煤为例安徽淮南标准烟煤含硫量只有0.46%而山东良庄标准烟煤的含硫量却高达1.94%。
根据煤中含硫量的高低煤又分为高硫煤、中硫煤、低硫煤三种;分类指标煤种名称等级代号分级界限鉴定方法全硫Sd.t,低硫煤:1级S1S1≦1%,煤中全硫的测定方法GB214-77;中硫煤2级S21S2≦2.8%,煤中全硫的测定方法GB214-77;高硫煤3级S3>2.8煤中全硫的测定方法GB214-77.。
脱硫的原理及方法
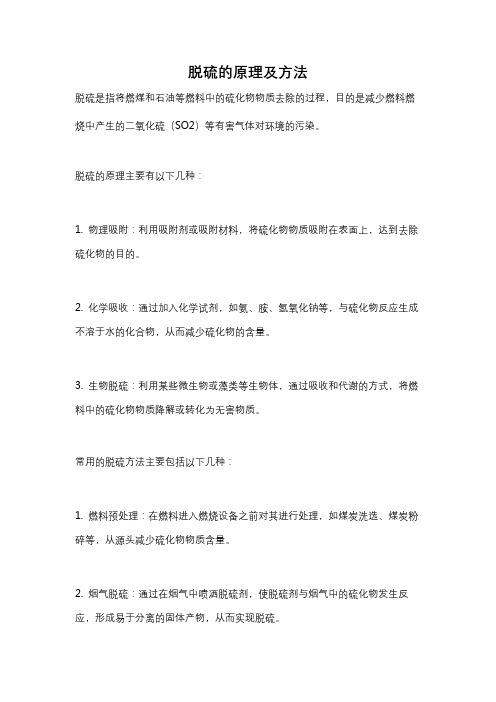
脱硫的原理及方法
脱硫是指将燃煤和石油等燃料中的硫化物物质去除的过程,目的是减少燃料燃烧中产生的二氧化硫(SO2)等有害气体对环境的污染。
脱硫的原理主要有以下几种:
1. 物理吸附:利用吸附剂或吸附材料,将硫化物物质吸附在表面上,达到去除硫化物的目的。
2. 化学吸收:通过加入化学试剂,如氨、胺、氢氧化钠等,与硫化物反应生成不溶于水的化合物,从而减少硫化物的含量。
3. 生物脱硫:利用某些微生物或藻类等生物体,通过吸收和代谢的方式,将燃料中的硫化物物质降解或转化为无害物质。
常用的脱硫方法主要包括以下几种:
1. 燃料预处理:在燃料进入燃烧设备之前对其进行处理,如煤炭洗选、煤炭粉碎等,从源头减少硫化物物质含量。
2. 烟气脱硫:通过在烟气中喷洒脱硫剂,使脱硫剂与烟气中的硫化物发生反应,形成易于分离的固体产物,从而实现脱硫。
3. 生物脱硫:通过利用微生物或藻类等生物体进行脱硫作用,将燃料中的硫化物转化为无害物质。
4. 湿法石膏法:通过喷淋水溶液或石膏浆料于烟气中,使硫化物与水溶液或石膏溶液发生反应,生成易于分离的固体产物。
5. 干法脱硫:通过利用吸附剂吸附烟气中的硫化物,或者通过化学反应将硫化物转化为易于分离的固体产物。
不同的脱硫方法适用于不同的场景和要求,选择合适的脱硫方法需要考虑燃料特性、燃烧设备条件、处理效果和成本等因素。
ito炉脱硫原理及工艺流程

Ito炉脱硫原理及工艺流程
一、脱硫原理
Ito炉脱硫技术主要基于酸碱中和原理,通过在炉内加入适量的脱硫剂,与烟气中的二氧化硫发生反应,生成硫酸盐等物质,从而达到脱硫的目的。
常用的脱硫剂包括石灰石、氧化钙等。
二、工艺流程
Ito炉脱硫工艺流程一般包括以下几个步骤:
1.吸收剂制备:将石灰石或氧化钙磨成粉状,以备后续使用。
2.吸收剂加入:将制备好的吸收剂按照一定的比例加入炉内。
3.烟气引入:将需要处理的烟气引入到炉内,与吸收剂充分接触。
4.反应过程:在炉内的高温环境下,吸收剂与烟气中的二氧化硫发生反应,生成硫酸盐等物质。
5.灰渣排出:反应后的灰渣从炉内排出,进行后续处理。
6.净化后的烟气排放:经过处理的烟气通过烟囱排放到大气中。
三、技术特点
Ito炉脱硫技术具有以下特点:
1.脱硫效率高:采用酸碱中和原理,能够实现高效的脱硫效果。
2.处理能力强:能够处理大量烟气,满足工业生产的需求。
3.操作简便:工艺流程简单,易于操作和维护。
4.投资成本低:设备结构简单,制造成本低。
5.环境友好:处理后的烟气能够达到环保标准,对环境影响较小。
四、应用范围
Ito炉脱硫技术广泛应用于钢铁、电力、化工等领域,主要用于处理工业生产过程中产生的烟气,控制二氧化硫的排放。
五、发展趋势
随着环保要求的不断提高,Ito炉脱硫技术将得到更广泛的应用。
未来,该技术将向高效、低成本、环保等方向发展,以满足市场需求。
同时,随着技术的不断进步,新型的脱硫技术也将不断涌现,为工业生产的可持续发展提供更多选择。
炉内脱硫的基本原理 Word 文档

炉内脱硫的基本原理
循环流化床燃烧(CFBC)技术系指小颗粒的煤与空气在炉膛内处于沸腾状态下,即高速气流与所携带的稠密悬浮煤颗粒充分接触燃烧的技术。
循环流化床锅炉脱硫是一种炉内燃烧脱硫工艺,以石灰石为脱硫吸收剂,燃煤和石灰石自锅炉燃烧室下部送入,一次风从布风板下部送入,二次风从燃烧室中部送入。
石灰石受热分解为氧化钙和二氧化碳。
气流使燃煤、石灰颗粒在燃烧室内强烈扰动形成流化床,燃煤烟气中的SO2与氧化钙接触发生化学反应被脱除。
为了提高吸收剂的利用率,将未反应的氧化钙、脱硫产物及飞灰送回燃烧室参与循环利用。
钙硫比达到2~2.5左右时,脱硫率可达90%以上。
流化床燃烧方式的特点是:1.清洁燃烧,脱硫率可达80%~95%,NOx 排放可减少50%;2.燃料适应性强,特别适合中、低硫煤;3.燃烧效率高,可达95%~99%;4.负荷适应性好。
负荷调节范围30%~100%。
燃料中的S在燃烧过程中产生SO2,与炉内石灰石粉受热分解产生的CaO反应生成CaSO3,CaSO3经氧化生成CaSO4,CaSO4或CaSO3随灰渣排除,从而实现了在燃烧过程中炉内脱硫。
石灰石炉内脱硫热平衡
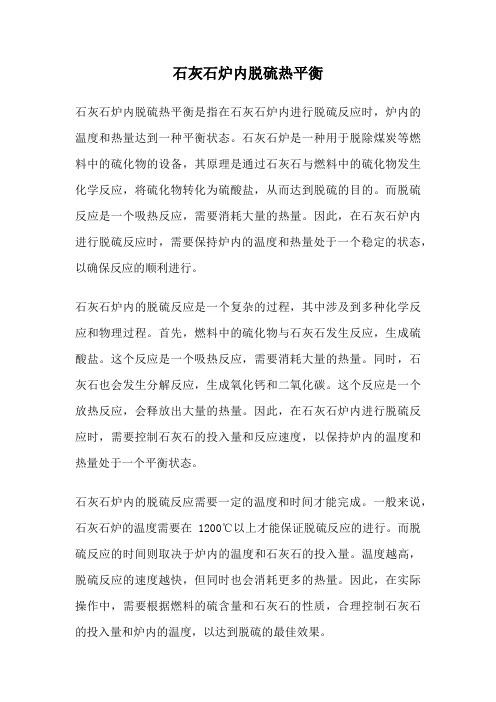
石灰石炉内脱硫热平衡石灰石炉内脱硫热平衡是指在石灰石炉内进行脱硫反应时,炉内的温度和热量达到一种平衡状态。
石灰石炉是一种用于脱除煤炭等燃料中的硫化物的设备,其原理是通过石灰石与燃料中的硫化物发生化学反应,将硫化物转化为硫酸盐,从而达到脱硫的目的。
而脱硫反应是一个吸热反应,需要消耗大量的热量。
因此,在石灰石炉内进行脱硫反应时,需要保持炉内的温度和热量处于一个稳定的状态,以确保反应的顺利进行。
石灰石炉内的脱硫反应是一个复杂的过程,其中涉及到多种化学反应和物理过程。
首先,燃料中的硫化物与石灰石发生反应,生成硫酸盐。
这个反应是一个吸热反应,需要消耗大量的热量。
同时,石灰石也会发生分解反应,生成氧化钙和二氧化碳。
这个反应是一个放热反应,会释放出大量的热量。
因此,在石灰石炉内进行脱硫反应时,需要控制石灰石的投入量和反应速度,以保持炉内的温度和热量处于一个平衡状态。
石灰石炉内的脱硫反应需要一定的温度和时间才能完成。
一般来说,石灰石炉的温度需要在1200℃以上才能保证脱硫反应的进行。
而脱硫反应的时间则取决于炉内的温度和石灰石的投入量。
温度越高,脱硫反应的速度越快,但同时也会消耗更多的热量。
因此,在实际操作中,需要根据燃料的硫含量和石灰石的性质,合理控制石灰石的投入量和炉内的温度,以达到脱硫的最佳效果。
石灰石炉内脱硫热平衡的研究对于提高脱硫效率和降低能耗具有重要意义。
通过合理调控炉内的温度和热量,可以提高脱硫反应的速率,减少反应时间,从而提高脱硫效率。
同时,也可以减少能耗,降低生产成本。
因此,研究石灰石炉内脱硫热平衡是石灰石炉脱硫技术改进的重要方向之一。
石灰石炉内脱硫热平衡的研究可以从多个方面展开。
首先,可以研究石灰石的性质对脱硫反应速率的影响。
不同性质的石灰石具有不同的反应活性,对脱硫效果和反应速率有着直接的影响。
其次,可以研究炉内温度和热量的分布情况,以及对脱硫反应速率的影响。
通过研究炉内温度和热量的分布情况,可以确定最佳的温度控制策略,提高脱硫效率和能耗的控制。
- 1、下载文档前请自行甄别文档内容的完整性,平台不提供额外的编辑、内容补充、找答案等附加服务。
- 2、"仅部分预览"的文档,不可在线预览部分如存在完整性等问题,可反馈申请退款(可完整预览的文档不适用该条件!)。
- 3、如文档侵犯您的权益,请联系客服反馈,我们会尽快为您处理(人工客服工作时间:9:00-18:30)。
炉内脱硫原理
1、.循环流化床锅炉简介
循环流化床燃烧技术作为沸腾燃烧的一种是近几年发展起来的一种新型高效清洁燃烧技术。
与其他燃烧方式相比循环硫化床锅炉具有煤种适应性广、燃烧效率高、负荷调节性能好、低负荷稳燃性好、灰渣利于综合利用等特点尤其是它的炉内脱硫效果明显是国际上公认的洁净燃煤技术在国外电力行业已经有了相当的应用规模。
在国内特别是经过将近30年的应用和技术发展已经证明是目前我国燃煤技术领域内最符合国情的高效低污染燃烧技术。
但由于多方面的原因我国的循环流化床锅炉脱硫现状还存在很大争议。
一种说法是循环流化床锅炉炉内石灰石干法脱硫效率低而且不可能高于90%,目前投运的锅炉中有许多都不能达到国家SO2排放标准要求需要进行尾部烟气的二次脱硫造成锅炉运行成本增加不同看法则认为只要掌握循环流化床锅炉的运行温度在合理的Ca/S条件下其脱硫效率完
全可以达到90%,甚至更高.根据煤种选择设计的锅炉结构完全可以实现炉内脱硫没有必要再进行尾部烟气的脱硫处理。
2•我国的燃煤分类及对SO2排放标准理解
2.1燃煤分类我国是能源生产和消费大国。
在所有能源的消费中煤占的比例最大根据地矿部门的勘查中国预测资源总量为40017亿吨标准煤其中煤炭资源占
85以上因此我国以燃煤为主的能源格局将长期存在。
我国的动力用煤按照挥发酚的高低大致分为无烟煤、烟煤、贫煤、褐煤等由于它们的成分和燃烧特性不同在燃烧后所产生的烟气特性也不同。
燃烧后产生的烟气中SO2含量的高低与煤中含
硫量的大小有直接关系一般来讲地域的差别影响了煤中含硫量的高低。
在我国北方煤大都比南方煤含硫量要高一些以国家标准烟煤为例安徽淮南标准烟煤含硫量只有
0.46%而山东良庄标准烟煤的含硫量却高达 1.94%。
根据煤中含硫量的高低
煤又分为高硫煤、中硫煤、低硫煤三种;分类指标煤种名称等级代号分级界限鉴定方法全硫Sd.t,低硫煤:1级S1S1日%,煤中全硫的测定方法GB214-77;中硫煤2 级
S21S2登.8%,煤中全硫的测定方法GB214-77;高硫煤3级S3>2.8煤中全硫的测定方法GB214-77.。
折算硫分St.zs低硫煤1级S1S1国.2%煤中全硫的测定方法GB214-77 ;中硫煤2级S2, 0.2>S2为.55煤中全硫的测定方法GB214-77 ; 高硫煤3级,S3煤中全硫的测定方法GB214-77
2.2对国家SO2排放标准的理解有关数据显示我国大气中约87%的SO2来自动力煤的燃烧。
随着国民经济的不断发展我国的大气污染日益严重特别是
SO2 排放已经成为造成酸雨的主要原因。
2003 年统计显示我国的酸雨已经覆盖国土面积1/3 左右由于酸雨造成的损失总额已经超过当年国民生产总值的2% ,而且部分地区的酸雨污染呈恶化趋势。
为保持能源、经济和环境之间的协调发展我国政府在2006 年一季度开始控制煤电发展速度后来又提出“节能减排” 的重大战略决策控制SO2 排放势在必行。
在原有的GB13223-1996 标准上重新制定了GB13223 —2003 标准从对电厂SO2 排放标准来分析对污染物都是控制其排放浓度对锅炉的脱硫效率都没有做出相应的规定。
脱硫效率不具有唯一可比性。
因此评判电厂SO2 排放是否达到要求应该看其排放浓度是否达到当地的标准要求。
相对于欧盟、美国等发达国家
GB13223-2003 标准中SO2 排放要求还有一定的差距但是在目前我国国情来看是能够充分满足的。
3. 炉内脱硫原理及影响因素
3.1 炉内脱硫原理循环流化床锅炉炉内脱硫是采用石灰石干法脱硫来实现的即将炉膛内的CaCO 分解煅烧成CaO 与烟气中的SO2 发生反应生成CaSO4 随炉渣排出从而达到脱硫目的石灰石脱硫过程主要分为以下三步:
①石灰石煅烧在常压流化床锅炉中石灰石中的CaCO3 遇热煅烧分解为CaO 煅烧析出CO2 时会生成并扩大CaO 中的孔隙增加其表面积为下步的固硫反应奠定基础。
反应方程CaCO3=CaOCO2
②硫的析出与氧化煤中的硫主要以黄铁矿、有机盐、和硫酸盐三种形式存在有关试验表明煤在加热并燃烧时SO2 的析出呈现明显的阶段性。
黄铁矿燃烧氧化后生成S02。
有机硫在200 C分解并释放出H2S、硫醚、硫醇等这些物质氧化后都生成SO2 。
反应方程S+O2=SO2
③硫的固化反应CaO 与析出的SO2 反应生成硫酸盐。
CaO+SO2+1/2O2=CaSO4
3.2 影响脱硫效率的因素:
①床温对脱硫的影响有关试验表明床温对SO2 的析出影响最大SO2 浓度随着床温的升高而单调增大但是脱硫效率随着床温的升高会迅速下降当床温低于
800 C时脱硫剂孔隙数少孔径小反应速度低而且SO2析出速度慢脱硫效果差当床温高于950 C时CaO内部的孔隙结构会发生部分烧结而减少降低CaO与SO2的反应速度导致脱硫效率降低另外床温过高时已经生成的CaSO4 会重新分解而释放出SO2 图、图 2 分别反映出SO2 浓度和脱硫效率与床温的关系。
②CaS摩尔比对脱硫的影响循环流化床锅炉运行实践表明随着炉内添加石灰石量的增加脱硫效率逐渐提高在Ca/S 摩尔比小于 2.5 范围内脱硫效率随Ca/S 摩尔比
增加提高很快当继续增加Ca/S 摩尔比时脱硫效率增加速度会明显减慢。
而且Ca/S 摩尔比过高还会带来一些副作用比如灰渣热物理损失增大、锅炉热效率下降、NOx排放浓度升高、尾部飞灰量增加、石灰石价格造成锅炉运行成本增加等。
所以我们在设计锅炉时设置合理、经济的Ca/S 摩尔比为25 。
图 3 为Ca/S 摩尔比与脱硫效率的关系。
③石灰石入炉粒度对脱硫效率的影响脱硫剂的粒径分布对脱硫效率也有较大的影响。
理论上讲脱硫剂越小炉内脱硫效果越好因为减少石灰石粒径能增加其表面积从而提高反应面积。
但脱硫剂并非越小越好如果脱硫剂太小就会有很大部分随着烟气逃逸增加尾部烟道的飞灰量从而使除尘器负担加大。
最佳的脱硫剂粒径分布与锅炉设计参数有关一般在0-2mm 属于比较合理的范围平均为100-200um 。
④石灰石品质对脱硫效率的影响石灰石品质对脱硫效率影响十分敏感不同品质的石灰石反应性能差异很大在CaCO3 含量、晶体结构和孔隙特征上也有所不同。
一般应对石灰石做热重分析TGA 测定其反应率指标从而准确推算出Ca/S 摩尔比
⑤煤种特性对脱硫的影响:循环流化炉内脱硫效率的高低直接取决于煤中含硫量的高低。
一般来讲燃煤中含硫量越高脱硫效率就越高但这并不代表SO2 排放浓度低。
在燃用高硫煤时脱硫效率能达到90 甚至更高但S02 排放浓度仍然不能达到国家排放标准的要求。
所以为了降低S02 排放量首先希望选用低硫煤当设计煤中确定后则必须通过提高脱硫效率来降低S02 排放量。
当燃煤中含硫量过高时单靠炉内添加石灰石脱硫已经很难达到S02 国家排放标准要求了这时还要进行尾部烟气的二次脱硫。
⑥石灰石投放方式对脱硫效率的影响传统的石灰石投放方式为与煤混合一起通过给煤口进入到炉膛内这种投放方式虽然方法简单容易操作,但是有很大的弊端煤中含有的外部水分与石灰石接触后使石灰石粉末结块,影响了它在炉内的煅烧效果大大降低了石灰石孔隙面积从而使石灰石的固硫能力受到很大限制。
石灰石投放点也可以设置在二次风口通过特设的风力管道输送系统将石灰石粉末送至二次风支管随二次风一起进入炉膛其优点是投放点分散均匀在炉膛内沸腾扰动强烈,反应速度快程度高从而使脱硫效率提高缺点是系统复杂。
近几年我们经在流化床返料管上设置石灰石投放点并在几个电厂中试验收到了良好的效果需要解决的一个问题就是返料管开孔处的密封。
4. 结论:
循环流化床锅炉炉内脱硫根据煤种的含硫量不同只要能达到S02 国家排放标准要求脱硫效率在70-90% ,都是合理的,在煤种已经定下的前提下通过调节运行床温、合理设置Ca/S 摩尔比、控制石灰石粒度等措施能够有效提高脱硫效率;燃用高
硫煤时若脱硫效率在90 都无法达到S02 国家排放标准时则必须进行尾部烟气脱硫。