橡胶硫化过程的四个阶段
橡胶硫化原理

橡胶硫化原理Company Document number:WTUT-WT88Y-W8BBGB-BWYTT-19998橡胶硫化原理橡胶受热变软,遇冷变硬、发脆,不易成型,容易磨损,易溶于汽油等有机溶剂,分子内具有双键,易起加成反应,容易老化。
为改善橡胶制品的性能,生产上要对生橡胶进行一系列加工过程,在一定条件下,使胶料中的生胶与硫化剂发生化学反应,使其由线型结构的大分子交联成为立体网状结构的大分子,使从而使胶料具备高强度、高弹性、高耐磨、抗腐蚀等等优良性能。
这个过程称为橡胶硫化。
一般将硫化过程分为四个阶段,诱导-预硫-正硫化-过硫。
为实现这一反应,必须外加能量使之达到一定的硫化温度,然后让橡胶保温在该硫化温度范围内完成全部硫化反应。
橡胶硫化的来历硫化是胶料通过生胶分子间交联,形成三维网络结构,制备硫化胶的基本过程。
不同的硫化体系适用于不同的生胶。
以橡胶(生胶)为主体,加以多种辅助材料而成的合成体、(辅助材料有几大体系、填充补强、硫化、防护、增塑、特殊物质加入剂、)而硫化是包覆绝缘层或护套层以后的一种处理方法、其目的就是让辅助体系里的硫化体系发生作用,使橡胶永久交联、增加弹性、减少塑性。
硫化的名词是因最早时间是用硫磺使橡胶交联的故称硫化,沿用至今.橡胶硫化体系不饱和橡胶通常使用如下几类硫化体系:以硫黄,有机二硫化物及多硫化物、噻唑类、二苯胍类,氧化锌及硬脂酸为主的硫化剂。
这是最通用的硫化体系。
但所制得的硫化胶的耐热氧老化性能不高。
烷基酚醛树脂。
多卤化物(如用于聚丁二烯橡胶、丁苯橡胶及丁腈橡胶的六氯乙烷)、六氯-对二甲苯。
双官能试剂[如醌类、二胺类、偶氮及苯基偶氮衍生物(用于丁基橡胶及乙丙橡胶)等]。
双马来酰亚胺,双丙烯酸酯。
两价金属的丙烯酸酯(甲基丙烯酸酯)、预聚醚丙烯酸酯。
用于硫化饱和橡胶的有机过氧化物。
饱和橡胶硫化不同种类的饱和橡胶时,可使用不同的硫化体系。
硫化三元乙丙橡胶时,使用有机过氧化物与不饱和交联试剂,如三烯丙基异氰脲酸酯(硫化剂TAIC)。
硫化工艺课程

硫化工艺课程二.什么是硫化:1.在加热或辐射的条件下,胶料中的生胶与硫化剂发生化学反应,由线型结构的大分子交联成为立体网状结构的大分子,并使胶料的物理机械性能及其它性能随之发生根本的变化,这一过程称为硫化。
2.硫化交联反应是在一定的温度、时间、压力的条件下完成的,这些条件称为硫化条件。
3.橡胶的硫化历程可分四个历程:焦烧阶段、热硫化阶段、平坦硫化阶段、过硫阶段。
3.1.焦烧阶段:是热硫化开始前起延迟作用的时间。
它的时间长短决定与配方、促进剂的影响。
胶料有热积累的特性,所以胶料的实际焦烧时间包括橡胶在混炼、热炼、存放中消耗的焦烧时间+胶料在模具加热中保持流动的时间。
3.2.热硫化阶段:是指在热硫化反应中的交联阶段,逐渐产生网构,使得胶料弹性,拉伸强度急剧上升,热硫化时间的长短决定于胶料配方。
3.3. 平坦硫化阶段:硫化交联反应已经完成。
随后发生交联键重新排列、裂解等反应,因此胶料强度曲线出现了平坦区,它的时间长短决定于胶料配方。
因为这一阶段硫化胶保持最佳阶段,所以作为选定产品的硫化时间的范围。
3.4.过硫阶段:相当于硫化反应中网状结构形成的后期,交联键发生重排,以及交联键和链段热降解的反应。
因此胶料的拉伸性能显著下降。
4.硫化的三要素4.1.温度:温度的作用,开始时,可以软化胶料,促进胶料流动。
提高硫化反应,促进硫化交联,同时对活性剂、促进剂、硫化剂等进行活化。
天然胶最适意的硫化温度是145~155℃。
最好在155℃以下。
丁睛橡胶的最适意的硫化温度是165~170℃。
天然胶硫化温度超出硫化温度范围,有可能发生硫化返原现象,也可能产生热撕裂,影响胶料流动,和粘合性,易出现缺胶,接头不良、尺寸超差、飞边过厚。
硫化温度低,硫化速度慢,生产效率低。
4.2.压力胶料在硫化过程中,由于胶料中含有水分蒸发以及所包含的空气释出,导致产生内压,这种内压使胶料产生气孔,为了防止这种现象产生,硫化时,就必须施加大于胶料可能发生内压的硫化压力。
丁腈橡胶快速硫化体系
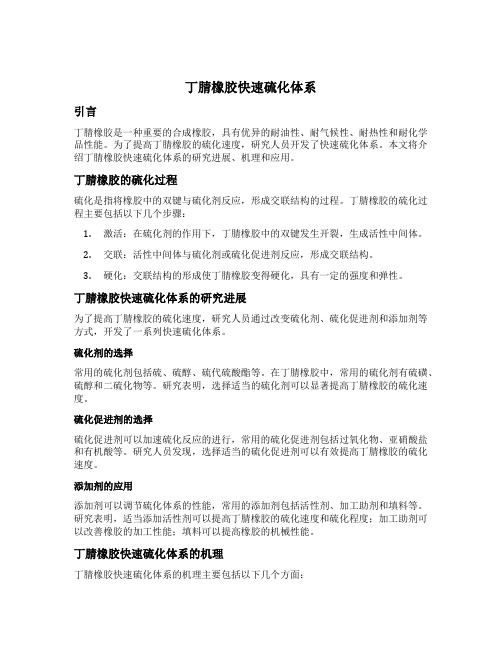
丁腈橡胶快速硫化体系引言丁腈橡胶是一种重要的合成橡胶,具有优异的耐油性、耐气候性、耐热性和耐化学品性能。
为了提高丁腈橡胶的硫化速度,研究人员开发了快速硫化体系。
本文将介绍丁腈橡胶快速硫化体系的研究进展、机理和应用。
丁腈橡胶的硫化过程硫化是指将橡胶中的双键与硫化剂反应,形成交联结构的过程。
丁腈橡胶的硫化过程主要包括以下几个步骤:1.激活:在硫化剂的作用下,丁腈橡胶中的双键发生开裂,生成活性中间体。
2.交联:活性中间体与硫化剂或硫化促进剂反应,形成交联结构。
3.硬化:交联结构的形成使丁腈橡胶变得硬化,具有一定的强度和弹性。
丁腈橡胶快速硫化体系的研究进展为了提高丁腈橡胶的硫化速度,研究人员通过改变硫化剂、硫化促进剂和添加剂等方式,开发了一系列快速硫化体系。
硫化剂的选择常用的硫化剂包括硫、硫醇、硫代硫酸酯等。
在丁腈橡胶中,常用的硫化剂有硫磺、硫醇和二硫化物等。
研究表明,选择适当的硫化剂可以显著提高丁腈橡胶的硫化速度。
硫化促进剂的选择硫化促进剂可以加速硫化反应的进行,常用的硫化促进剂包括过氧化物、亚硝酸盐和有机酸等。
研究人员发现,选择适当的硫化促进剂可以有效提高丁腈橡胶的硫化速度。
添加剂的应用添加剂可以调节硫化体系的性能,常用的添加剂包括活性剂、加工助剂和填料等。
研究表明,适当添加活性剂可以提高丁腈橡胶的硫化速度和硫化程度;加工助剂可以改善橡胶的加工性能;填料可以提高橡胶的机械性能。
丁腈橡胶快速硫化体系的机理丁腈橡胶快速硫化体系的机理主要包括以下几个方面:1.硫化剂与丁腈橡胶中的双键反应生成活性中间体。
2.硫化促进剂加速活性中间体与硫化剂的反应,形成交联结构。
3.添加剂的作用:活性剂促进硫化反应的进行,加工助剂改善橡胶的加工性能,填料提高橡胶的机械性能。
4.硬化过程:交联结构的形成使丁腈橡胶变得硬化,具有一定的强度和弹性。
丁腈橡胶快速硫化体系的应用丁腈橡胶快速硫化体系已广泛应用于橡胶制品的生产中。
丁腈橡胶制品主要包括密封件、管道、胶带、手套等。
【考研化学】第十章 硫化

★混气硫化:在硫化的第一阶段以热空气为介 质.在第二阶段再通入蒸汽作介质。胶鞋硫化 采用该方法。
(3)过热水
优点:既能保持较高的温度,又能赋予较 大的压力,因此常用于高压硫化场合。
缺点:热含量小,导热效率低,且温度不 易掌握均匀。 典型的用途是轮胎硫化时,将过热水充注 于水胎中,以保持内温。
(4)热水
二、欠硫阶段(预硫)
含义:焦烧期以后橡胶开始交联的阶段。 交联程度逐渐增加,橡胶的物理机械性能逐 渐上升。制品轻微欠硫时,强度、弹性、伸长率 未达到预期的水平,但抗撕裂性、耐磨性等却优 于正硫化胶料。
欠料的配方。
三、正硫阶段
含义:橡胶的交联反应达到一定的程度,此 时的各项物理机械性能均达到或接近最佳值,其 综合性能最佳。 正硫化温度
正硫化时间取决于制品性能要求和断面厚薄, 需考虑到“后硫化”。
抗张强度最高值略前的时间
正硫化时间=
强伸积(抗张强度×伸长率) 最高值的时间
四、过硫阶段
含义:正硫化以后继续硫化便进入过硫阶段。 氧化及热断链反应占主导地位,胶料性能下降。 硫化返原;断链多于交联
非返原性:交联继续占优势
过硫阶段胶料的性能变化情况反映了硫化平 坦期的长短。超促进剂,交联键能低,硫化温度 高,则平坦期短。
(1)饱和蒸汽
优点:热含量大、导热效率高、成本低、 压力和温度易调节。 缺点:加热温度要受到压力的牵制;对硫 化容器内壁有较大腐蚀作用。
(2)热空气
优点: 加热温度不受压力影响,比较干燥, 不含水分,产品表面光滑,外观漂亮,而且不 受罐壁腐蚀的影响。 缺点: 含热量低,导热效率很低,硫化时 间长,同时含有大量氧气,在高温高压下易使 制品氧化。
1.中间化合物的生成
促进剂的硫化曲线

促进剂的硫化曲线
硫化曲线指的是在橡胶硫化过程中,不同时间和温度下橡胶中硫化程度的变化曲线。
硫化是橡胶加工工艺中非常重要的步骤,通过硫化可以使橡胶获得优良的弹性、耐热、耐腐蚀等性能。
在硫化曲线中,通常可以分为几个阶段:
1. 延迟期(t0到t1):橡胶在橡胶-硫混合物中,尚未出现硫
化反应,此时橡胶材料保持弹性。
2. 加速期(t1到t2):在此阶段,橡胶中的硫化反应开始加速,硫化速度逐渐增加,橡胶材料的硫化程度也逐渐增加。
橡胶开始变得发硬。
3. 高速期(t2到t3):硫化反应在此阶段达到最高速度,橡
胶材料的硫化程度迅速增加。
此时橡胶开始形成网络结构,整体硬化。
4. 减速期(t3到t4):硫化反应速度开始减慢,硫化程度的
增加趋于平缓。
橡胶变得更加耐磨和耐热。
5. 稳定期(t4到t5):硫化反应基本结束,硫化程度变化很小。
橡胶材料的硫化程度达到最高水平。
不同类型的橡胶和硫化体系会有不同的硫化曲线特征,这取决于使用的促进剂、硫化温度和时间等因素。
硫化曲线的了解有助于合理选择硫化条件,以获得符合要求的橡胶制品。
橡胶的硫化曲线分析

橡胶的硫化反应历程硫化历程是橡胶大分子链发生化学交联反应的过程包括橡胶分子与硫化剂及其他配合剂(主要是活性剂、促进剂)之间发生的一系列化学反应以及在形成网状结构时伴随发生的各种副反应。
硫化仪无转子硫化仪的结构示意图硫化曲线分成四个阶段,即1)焦烧阶段:热硫化开始前的延迟时间2)热硫化阶段:硫化反应的交联阶段,其斜率代表反应速度3)平坦硫化阶段:交联反应基本结束,熟化阶段(短化、重排、裂解),性能最佳4)过硫化阶段:胶料硫化在此阶段,可能出现三种形式1、焦烧期(ab段)焦烧期(诱导期):从胶料放入模具至出现轻微硫化的整个过程所需要的时间叫硫化诱导期,又称为焦烧时间。
焦烧(scorch):加有硫化剂的混炼胶在加工或停放过程中产生的早期硫化现象。
焦烧现象本质是硫化,胶料局部交联。
胶料焦烧后,流动性明显变差,甚至不能流动,后续加工工序无法正常进行。
诱导期反应了胶料的加工安全性。
诱导期短,加工安全性差;诱导期太长,会降低生产效率。
表征参数ts1——焦烧时间(scorchtime),从开始加热起,至胶料的转矩由最低值上升0.1N.m所需要的时间。
tc10——焦烧时间,从开始加热起,至胶料的转矩由最低值上升10个单位所需要的时间。
焦烧时间又分为操作焦烧时间:胶料在加工或停放过程中由于热积累效应所消耗的焦烧时间;剩余焦烧时间:胶料在模具内保持流动的时间。
操作焦烧时间长,剩余焦烧时间就短2、热硫化期(BC段)由焦烧点到工艺正硫化点(C点)所经历的阶段,即硫化反应过程的交联反应期。
曲线快速上升。
热硫化期特性参数:tc90——工艺正硫化时间,从开始加热起,至胶料的转矩由最低值上升90个单位所需要的时间。
斜率k——反映胶料硫化速度快慢,斜率越大,硫化速度越快CRI——加硫指数【CRI=100/(tc90—ts1)】,min-1,反映胶料硫化速度快慢,CRI值大,硫化速度快。
3、平坦硫化期(cd段)曲线保持水平所经历的时间长短,反映胶料在硫化过程中性能稳定性的高低。
硫化曲线t10和t90
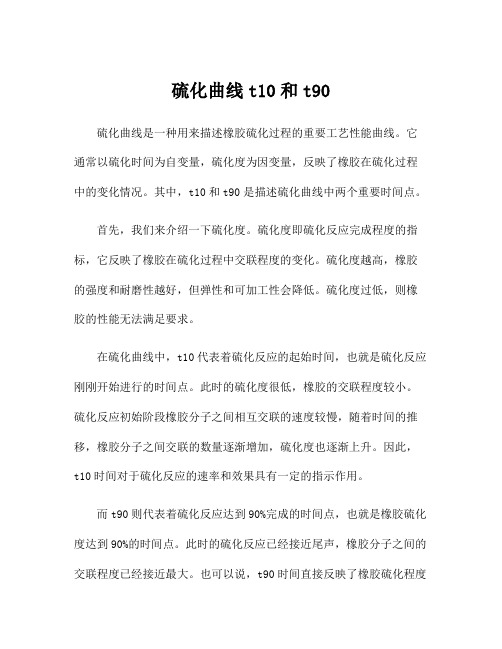
硫化曲线t10和t90硫化曲线是一种用来描述橡胶硫化过程的重要工艺性能曲线。
它通常以硫化时间为自变量,硫化度为因变量,反映了橡胶在硫化过程中的变化情况。
其中,t10和t90是描述硫化曲线中两个重要时间点。
首先,我们来介绍一下硫化度。
硫化度即硫化反应完成程度的指标,它反映了橡胶在硫化过程中交联程度的变化。
硫化度越高,橡胶的强度和耐磨性越好,但弹性和可加工性会降低。
硫化度过低,则橡胶的性能无法满足要求。
在硫化曲线中,t10代表着硫化反应的起始时间,也就是硫化反应刚刚开始进行的时间点。
此时的硫化度很低,橡胶的交联程度较小。
硫化反应初始阶段橡胶分子之间相互交联的速度较慢,随着时间的推移,橡胶分子之间交联的数量逐渐增加,硫化度也逐渐上升。
因此,t10时间对于硫化反应的速率和效果具有一定的指示作用。
而t90则代表着硫化反应达到90%完成的时间点,也就是橡胶硫化度达到90%的时间点。
此时的硫化反应已经接近尾声,橡胶分子之间的交联程度已经接近最大。
也可以说,t90时间直接反映了橡胶硫化程度的快慢与充分性。
通常情况下,t90时间越短,说明橡胶的硫化反应速率快且充分,橡胶材料的性能也会相应提升。
硫化曲线的形状通常可分为四个阶段:橡胶化、股化、稳态硫化和过硫化。
在橡胶化阶段,曲线可以近似看作是一条直线,此时的硫化度较低。
股化阶段是曲线的斜率逐渐减小的阶段,此时的硫化度随时间的增长而逐渐上升。
稳态硫化阶段是指曲线呈现出平缓的状态,此时橡胶的硫化度已经接近最大值。
过硫化阶段是曲线开始出现下降趋势,此时橡胶的硫化度开始下降,原因往往是交联程度过高导致橡胶断裂。
通过观察硫化曲线的t10和t90时间,可以评估硫化反应的速率和完成程度。
通常来说,t10时间越短,说明橡胶的硫化反应速率快;而t90时间越短,说明橡胶的硫化程度充分。
因此,对于某些特定的应用领域,我们可以根据t10和t90时间的要求来优化橡胶材料的硫化工艺。
总结起来,硫化曲线中的t10和t90时间点是描述橡胶硫化过程的重要参数。
o型圈硫化过程

o型圈硫化过程O型圈硫化是一种常见的橡胶制造过程,主要用于制作密封圈等橡胶制品。
在硫化过程中,通过加热和添加硫化剂,将橡胶材料进行交联,从而增加其弹性和耐热性能。
本文将就O型圈硫化过程进行详细介绍。
一、硫化过程的原理橡胶材料在加热的条件下,会发生交联反应,形成网络状的结构。
这一过程主要依赖于硫化剂的作用。
硫化剂能够在高温下与橡胶中的双键发生反应,使其断裂并重新连接,从而形成交联结构。
硫化过程中,还需要添加促进剂和助剂,以提高硫化速度和改善橡胶的硫化性能。
二、硫化过程的步骤1. 橡胶材料的准备:首先需要准备好橡胶原料,包括橡胶胶料、硫化剂、促进剂和助剂等。
其中,硫化剂常用的有硫磺和过氧化物等,促进剂常用的有过硫酸铵和过硫酸钾等,助剂则根据需要选择添加。
2. 混炼:将橡胶材料放入混炼机中进行混炼。
在混炼的过程中,将橡胶胶料与硫化剂、促进剂和助剂等按照一定比例混合,并通过摩擦加热使其混合均匀。
混炼的时间和温度要根据具体材料和硫化剂的要求进行控制,以确保混炼的质量。
3. 成型:将混炼好的橡胶材料放入成型机中进行成型。
O型圈的成型通常采用挤出法或压延法。
在成型的过程中,要控制好温度和压力,确保橡胶材料能够充分填充模具,并保持其形状稳定。
4. 硫化:将成型好的橡胶制品放入硫化炉中进行硫化。
硫化的温度和时间要根据具体材料和硫化剂的要求进行控制。
在硫化的过程中,硫化剂会与橡胶中的双键发生反应,使其交联形成网络结构。
同时,促进剂和助剂的作用也会提高硫化速度和改善硫化效果。
5. 后处理:硫化完成后,需要进行后处理工艺。
主要包括去模、修整和检验等步骤。
去模是将硫化好的橡胶制品从模具中取出,修整是对制品进行切割和修整,以获得需要的尺寸和表面质量。
最后,还需要对制品进行检验,确保其质量符合要求。
三、硫化过程的影响因素1. 温度:硫化温度是影响硫化速度和硫化效果的重要因素。
温度过高会导致橡胶材料老化和烧结,温度过低则会使硫化反应速度变慢。
硫化反应过程

硫化反应过程硫化反应过程是化学反应过程,它包含橡胶分子与硫化剂及其它配合剂之间发生的一系列化学反应以及在形成网状结构时伴随发生各种反应,在这众多的反应中,仍以橡胶分子与硫化剂之间的反应为主,它是生成大分子网状结构的基本反应,对于大多数含有有机促进剂(硫磺)的硫化体系的胶料来说,其硫化反应历程可大致如下:促进剂活性剂↓硫磺(1) 诱导阶段促进剂多硫化合物(T10相同) ↓橡胶含橡胶分子链的硫化合物↓分解自由基(或离子)(2)交联反应阶段↓橡胶交联(3)网构形成阶段交联键重排,裂解,主键改性网构成熟阶段硫化胶↓以上看出硫化反应历程大体分为三个阶段:第一阶段为诱导阶段,在这个阶段中首先是硫磺分子和促进剂体系之间反应生成一种活性更大的中间化合物,然后进一步引发橡胶分子链,形成可交联的自由基(或离子)与橡胶分子链之间产生连锁反应,生成交联链,第三阶段为网构形成阶段,在这一阶段的前期交联反应已趋于完成,产生的交联链发生重排和裂解等反应,在这一阶段的后期交联反应已基本停止,随之而发生的是交联链重排和热裂解等反应,最后得到网构稳定的硫化胶.硫化历程图:在硫化过程中,橡胶的各种性能随着硫化时间而变化,若将橡胶的某一性能变化与时间作曲线图,则可从曲线图中可以表现出整个硫化历程,所以这种曲线图叫做硫化历程图.最常见的硫化历程图如图一所示:图中的曲线,前半部分由门尼焦烧曲线组成,后半部则由扯断强度曲线组成,橡胶的硫化历程可分为四个阶段,即焦烧阶段,热硫化阶段,平坦硫化阶段,过硫化阶段.焦烧阶段---图中的AB段它是指热硫化前延迟作用时间,相当于前述的硫化反应中的诱导期,焦烧时间的长短,是由胶料的配方所决定的, 其中主要受促进剂的影响,而操作过程中的热历史也是一个重要的因素.由于橡胶具有热积累的特性,所以胶料的实际焦烧时间,包括操作焦烧时间A1和剩余焦烧时间A2两部分,操作焦烧时间是指在橡胶加工过程中由于热效应所消耗掉的焦烧时间,它取决于加工程度,(如胶料翻炼次数,热炼程度及压延压出等),剩余焦烧时间是指胶料在模型加热时保持流动性的时间,在操作焦烧时间和剩余焦烧时间之间没有固定的阶限,它随胶料操作和放条件不同而变化,如果一个胶料经历的加工越多,它占去的焦烧时间就越多如图A1’所示,则剩余焦烧时间就越小如图中A2’所示,胶料在模型中流动时间越少,因此一般胶料都应避免经受反复多次的机械作用.热硫化阶段---如图中的BC段这一阶段相当于硫化反应中的交联阶段,在这一阶段中胶料进行着交联反应,逐渐生成网构,于是橡胶的弹性和抗张性能急剧上升,热硫化时间的长短是由交联配方所决定的,它是交联固有的,常作为恒量每种胶料硫化反应进行快慢的标志.平坦硫化阶段---如图中的CD段相当于硫化反应中网构,成熟期的前半期,这时交联反应已趋于完成,反应速度已缓和下来,随之而发生交联键的重排,热裂解等反应,因此胶料的抗张性能曲线出现平坦区,平坦硫化时间的长短也决定于配方,(主要是促进剂及防老剂),由于在这一阶段中硫化保持有最佳性能,所以常作为取得产品质量的硫化阶段,为通常选取正硫化时间的范围.过硫化阶段----D后面部分这一段相当于硫化反应中的网构成熟期的后半期,在这一阶段中主要是交联键重排作用,以及交联键和键段热裂解的反应,因此胶料的抗张性能显著下降.在硫化历程图中,从胶料开始加热时算起至出现平坦期为止所经过的时间称为产品硫化时间,也就是通常所说的”正硫化时间”,它等于焦烧时间与热硫化时间之和,但是由于焦烧时间有一部分为操作过程所消耗,所以实际上胶料在模型内加热硫化只有图上B1的时间,所以我们做的每批胶料的剩余焦烧时间是会有波动的,因此每批胶料的热硫化时间也会有所波动,其波动范围在B1和B2之间.二.硫化的定义线性的高分子在物理或化学作用下,形成三维网状体型结构的过程。
影响橡胶性能的主要因素(橡胶基础知识三)
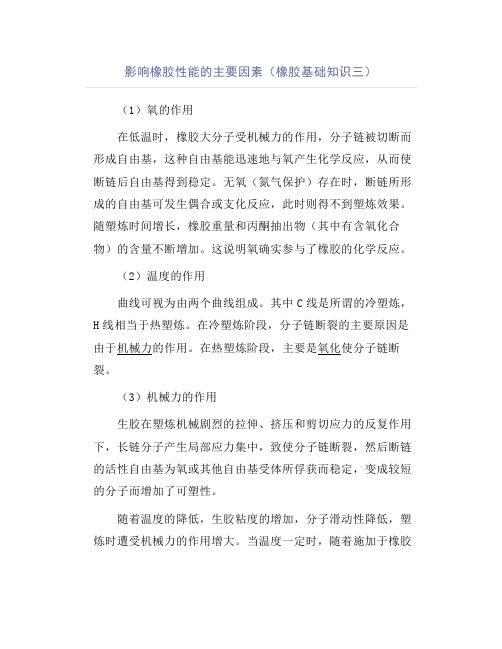
影响橡胶性能的主要因素(橡胶基础知识三)(1)氧的作用在低温时,橡胶大分子受机械力的作用,分子链被切断而形成自由基,这种自由基能迅速地与氧产生化学反应,从而使断链后自由基得到稳定。
无氧(氮气保护)存在时,断链所形成的自由基可发生偶合或支化反应,此时则得不到塑炼效果。
随塑炼时间增长,橡胶重量和丙酮抽出物(其中有含氧化合物)的含量不断增加。
这说明氧确实参与了橡胶的化学反应。
(2)温度的作用曲线可视为由两个曲线组成。
其中C线是所谓的冷塑炼,H线相当于热塑炼。
在冷塑炼阶段,分子链断裂的主要原因是由于机械力的作用。
在热塑炼阶段,主要是氧化使分子链断裂。
(3)机械力的作用生胶在塑炼机械剧烈的拉伸、挤压和剪切应力的反复作用下,长链分子产生局部应力集中,致使分子链断裂,然后断链的活性自由基为氧或其他自由基受体所俘获而稳定,变成较短的分子而增加了可塑性。
随着温度的降低,生胶粘度的增加,分子滑动性降低,塑炼时遭受机械力的作用增大。
当温度一定时,随着施加于橡胶上的总机械功的增大(如增加塑炼机械的转速),分子链降解程度就愈大。
(4)化学增塑剂的作用使用化学塑解剂能提高塑炼效果。
它在塑炼中的作用与氧相似。
不同塑解剂的作用机理也各不相同。
根据他们的使用温度,可分为低温塑解剂:苯醌和偶氮苯,起自由基受体的作用,使断链的橡胶自由基稳定,从而生成较短的分子。
高温塑解剂:过氧化苯甲酰、偶氮二异丁腈,高温时分解成极不稳定的自由基,促使橡胶分子生产自由基,进而氧化断链,起引发剂的作用。
高低温通用型塑解剂:硫醇及其二硫化物类、二邻苯甲酰胺二苯基二硫化物,低温通用型的塑解剂兼有上述两项功能。
(5)静电作用塑炼时,生胶受到炼胶机械的剧烈摩擦作用而产生静电。
辊筒(或转子)的金属表面与橡胶接触处所产生的平均电位差在2000-6000伏特之间,甚至可达15000伏特。
使辊筒与生胶间经常有电火花出现,这种放电作用使生胶表面周围的空气中的氧活化,生成原子态氧和臭氧,从而促进对橡胶分子的断链作用。
橡胶过氧化物硫化体系

橡胶过氧化物硫化体系
橡胶过氧化物硫化体系是一种橡胶硫化体系,其中过氧化物是起硫化剂作用的物质。
橡胶过氧化物硫化体系主要由以下成分组成:
1. 橡胶:最常用的橡胶是天然橡胶和合成橡胶,如丁苯橡胶、丁腈橡胶、氯丁橡胶等。
2. 过氧化物:过氧化物是一种含有氧气和氧键的物质,能够释放活性氧,并促进橡胶的硫化反应。
常用的过氧化物有过氧化苯钠、过氧化二异丙苯。
3. 其他添加剂:除了橡胶和过氧化物外,还可以添加一些辅助剂和助剂,如硫化促进剂、抗氧剂、塑化剂等,以调节橡胶硫化的速度和性能。
橡胶过氧化物硫化体系的硫化过程大致分为两步:首先,过氧化物释放活性氧,在橡胶分子链上引发自由基反应;然后,自由基与硫化活性物质或橡胶分子链发生反应,形成硫化键,使橡胶分子链交联成网状结构,增强其力学性能和耐热性能。
橡胶过氧化物硫化体系具有硫化速度快、硫化温度低、硫化产物无臭味等优点,但也存在一些问题,如储藏稳定性差、硫化剂残留、助剂活性降低等。
因此,在实际应用中需要选择合适的过氧化物和添加剂,以优化橡胶硫化的性能和稳定性。
橡胶硫化鞋工艺流程

橡胶硫化鞋工艺流程下载温馨提示:该文档是我店铺精心编制而成,希望大家下载以后,能够帮助大家解决实际的问题。
文档下载后可定制随意修改,请根据实际需要进行相应的调整和使用,谢谢!并且,本店铺为大家提供各种各样类型的实用资料,如教育随笔、日记赏析、句子摘抄、古诗大全、经典美文、话题作文、工作总结、词语解析、文案摘录、其他资料等等,如想了解不同资料格式和写法,敬请关注!Download tips: This document is carefully compiled by theeditor. I hope that after you download them,they can help yousolve practical problems. The document can be customized andmodified after downloading,please adjust and use it according toactual needs, thank you!In addition, our shop provides you with various types ofpractical materials,such as educational essays, diaryappreciation,sentence excerpts,ancient poems,classic articles,topic composition,work summary,word parsing,copy excerpts,other materials and so on,want to know different data formats andwriting methods,please pay attention!橡胶硫化鞋工艺流程橡胶硫化鞋是一种具有防滑、防水、耐磨等特性的鞋子,制作的工艺流程如下:一、准备工作阶段。
橡胶硫化工艺(1)

促进剂
活化剂
硫磺
促进剂多硫化合物 橡胶
橡胶分子链的多硫化合物
分解 自由基(或离子)
橡胶
交联反应
网络 形成 阶段
交联重排、裂解、主链改性 硫化胶
第一阶段:诱导阶段
先是硫磺、活化剂、促进 剂相互作用,使活化剂在 胶料中溶解度增加,活化 促进剂,使促进剂与硫磺 之间反应生成一种活性更 大的中间产物;然后进一 步引发橡胶分子链产生可 交联的橡胶大分子自由基。
Ø 工艺正硫化时间:指硫化曲线上M90 所对应的硫化时间,即T90;
Ø 二者都是有硫化曲线得到的。
橡胶硫化工艺(1)
Ø 胶料各项性能在某一时间不可能都处于最佳
值,必须综合考虑,生产上根据某些主要指
标来选择正硫化时间,具有工程实际意义,
称为工程正硫化时间。
Ø 当制品厚度小于6mm时,采用T90作为工程正 硫化时间;而大于6mm时,脱模后仍能产生
促进剂
活化剂
硫磺 第三阶段:网络形成阶段
期 阶
促进剂多硫化合物 橡胶
此阶段的前期交联反应
段 橡胶分子链的多硫化合物 已趋完成,初始形成的
交联 反应
分解
自由基(或离子) 交联键发生网络
网络 交联重排、裂解、主链改性 趋于稳定,获得性能稳
形成 阶段
硫化胶
定的硫化胶。
橡胶硫化工艺(1)
(三)硫化曲线及其参数
ML-最小转矩 ; MH-最大转矩; ΔM-最大与最小转矩差; M10= ML +10% ΔM M 90= ML +90% ΔM ;
TH-理论正硫化时间; T10-焦烧时间,M10对应的时间; T90- 工艺正硫化时间,M90对应的时间
橡胶硫化工艺(1)
橡胶硫化

橡胶硫化原理•橡胶受热变软,遇冷变硬、发脆,不易成型,容易磨损,易溶于汽油等有机溶剂,分子内具有双键,易起加成反应,容易老化。
•为改善橡胶制品的性能,生产上要对生橡胶进行一系列加工过程,在一定条件下,使胶料中的生胶与硫化剂发生化学反应,使其由线型结构的大分子交联成为立体网状结构的大分子,使从而使胶料具备高强度、高弹性、高耐磨、抗腐蚀等等优良性能。
这个过程称为橡胶硫化。
•一般将硫化过程分为四个阶段,诱导-预硫-正硫化-过硫。
为实现这一反应,必须外加能量使之达到一定的硫化温度,然后让橡胶保温在该硫化温度范围内完成全部硫化反应。
橡胶硫化的来历硫化是胶料通过生胶分子间交联,形成三维网络结构,制备硫化胶的基本过程。
不同的硫化体系适用于不同的生胶。
以橡胶(生胶)为主体,加以多种辅助材料而成的合成体、(辅助材料有几大体系、填充补强、硫化、防护、增塑、特殊物质加入剂、)而硫化是包覆绝缘层或护套层以后的一种处理方法、其目的就是让辅助体系里的硫化体系发生作用,使橡胶永久交联、增加弹性、减少塑性。
硫化的名词是因最早时间是用硫磺使橡胶交联的故称硫化,沿用至今.橡胶硫化体系不饱和橡胶通常使用如下几类硫化体系。
•以硫黄,有机二硫化物及多硫化物、噻唑类、二苯胍类,氧化锌及硬脂酸为主的硫化剂。
这是最通用的硫化体系。
但所制得的硫化胶的耐热氧老化性能不高。
•烷基酚醛树脂。
•多卤化物(如用于聚丁二烯橡胶、丁苯橡胶及丁腈橡胶的六氯乙烷)、六氯-对二甲苯。
•双官能试剂[如醌类、二胺类、偶氮及苯基偶氮衍生物(用于丁基橡胶及乙丙橡胶)等]。
•双马来酰亚胺,双丙烯酸酯。
两价金属的丙烯酸酯(甲基丙烯酸酯)、预聚醚丙烯酸酯。
•用于硫化饱和橡胶的有机过氧化物。
饱和橡胶硫化不同种类的饱和橡胶时,可使用不同的硫化体系。
•硫化三元乙丙橡胶时,使用有机过氧化物与不饱和交联试剂,如三烯丙基异氰脲酸酯(硫化剂TAIC)。
•硫化硅橡胶时也可使用有机过氧化物。
乙烯基硅橡胶硫化时可在催化剂(Pt)参与条件下进行。
橡胶硫化工艺三要素如何确定(全收藏版)

橡胶硫化工艺三要素如何确定(全收藏版)一、硫化基本概念和工艺要素硫化是橡胶制品生产的最后一个工艺过程。
在这个过程中,胶料中的生胶与硫化剂发生化学发应,由线型结构的大分子交联成为立体的网状结构的大分子,使塑性状态的橡胶转变为弹性状态的橡胶制品,从而获得完善的物理性能和机械性能和化学性能,成为有使用价值的高分子材料。
在工业生产中,这种交联反应是在一定温度,时间和压力条件下完成的,这些条件称为硫化条件。
1、橡胶的硫化反应过程诱导阶段,交联反应阶段,网状形成阶段。
2、硫化历程图烧焦阶段,热硫化阶段,平坦硫化阶段,过硫化阶段3、硫化压力一般橡胶制品在硫化时要施以压力,目的在于:1)防止制品在硫化过程产生气泡,提高胶料的致密性。
2)使胶料易于流动和充满模槽3)提高胶料与胶料的密着力4)有助于提高硫化的物理机械性能硫化加压的方式通常有下列几种:一是用液压泵通过平板硫化机把压力传递给模型,再由模型传递给胶料;二是硫化介质直接加压(如蒸汽加压);三是以压缩空气加压;四是由注压机注压等。
4、硫化温度和硫化时间硫化温度是橡胶发生硫化反应的基本条件,它直接影响硫化速度和产品质量。
硫化温度高,硫化速度快,生产效率高。
反之,硫化速度慢,生产效率低。
硫化温度高低应取决于胶料配方,其中最重要的是取决于橡胶种类和硫化体系。
但应注意的是,高温橡胶分子链裂解,至发生硫化返原现象,结果导致强伸性能下降,困此硫化温度不宜太高。
温度是硫化三大要素之一,与所有化学反应一样,硫化反应随温度升高而加快,并且大体适用范特霍夫定律,即温度每上升8~10。
C(约相当于一个表压的蒸汽压力),其反应速度约增加一倍;或者说,反应时间约减少一半。
随着室温硫化胶料的增加和高温硫化出现,硫化温度趋向两个极端。
从提高硫化效率来说,应当认为硫化温度越高越好,但实际上不能无限提高硫化温度。
首先受到橡胶导热性极小阻碍,对于厚制品来说,采用高温硫化很难使内外层胶料同时达到平坦范围;其次,各种橡胶的耐高温性能不一,有的橡胶经受不了高温的作用,如高温硫化天然橡胶时,溶于橡胶中的氧随温度提高而活性加大,引起强烈的氧化作用,破坏了橡胶的组织,降低了硫化胶的物理机械性能,第三,高温对橡胶制品中的纺织物有害为棉纤维布料超过期作废140℃时,强力下降,在240℃下加热四小时则完全破坏。
橡胶的硫化及成型加工简介

橡胶的硫化及成型加工工艺【摘要】随着我国经济的高速发展,我国橡胶工业的技术水平和生产工艺得到很大程度上的提高。
硫化是橡胶加工的主要工艺之一,在这道工艺中,橡胶经过一系列复杂的化学反应及成型加工,失去了混炼胶的可塑性具有了交联橡胶的高弹性,仅为获得优良的物理机械性能、耐热性、耐溶剂性、及耐腐蚀性能,提高橡胶制品的使用价值和应用范围。
本文以氯丁橡胶为例,介绍橡胶的硫化及成型加工工艺。
【关键字】橡胶硫化行为成型加工工艺氯丁橡胶硫化是橡胶加工最后也是最重要的一个工艺过程。
在硫化过程中,由于橡胶的化学结构发生变化,导致其物理机械性能和化学性能得到显著改进,从而成为有价值的宝贵材料。
1 硫化对结构与性能的影响未硫化时,橡胶分子是呈卷曲状的线形结构,其分子链具有运动的独立性,大分子之间是以范德华力相互作用的。
当受外力作用时,大分子链段易发生位移,在性能上表现出较大的变形,可塑性大,强度不大,具有可溶性。
硫化后,橡胶大分子被交联成网状结构,大分子链之间有主价键力的作用,使大分子链的相对运动受到一定的限制。
在外力作用下,不易发生较大的位移,变形减小,强度增大,失去可溶性。
橡胶在硫化过程中,其分子结构是连续变化的,如交联密度在一定的硫化时间内是逐渐增加的。
硫化时所发生的化学反应是比较复杂的,交联反应和降解反应都在发生,交联反应使橡胶分子成为网状结构,降解反应使橡胶分子断键。
在硫化初期以交联为主,交联密度增加,到一定程度降解反应增加,交联密度又会下降。
硫化过程的橡胶分子结构的变化显著地影响着橡胶各种性能。
橡胶的各种性能随硫化时间的增加而有一定规律的变化。
上图说明在一定硫化时间内,永久变形随硫化时间的增加而逐渐下降;硬度随硫化时间的增加而逐渐增高;拉伸强度、定伸应力、弹性当增高到一定值后边便开始下降。
这些规律都是由于在硫化过程中橡胶分子链产生交联度不同所致。
以氯丁橡胶(CR)为例,随硫化程度的提高:1)力学性能:弹性、定伸强度、撕裂强度、硬度提高。
橡胶硫化六大体系简介

橡胶硫化六大体系简介一、硫磺硫化体系(1)常规硫化体系:由硫磺和少量促进剂等配合剂组成,以多硫键交联为主。
耐高温性能较差,压缩永久变形大,过硫后易出现返原现象,但耐屈挠疲劳行较好、机械强度较高,胶料及制品不易喷霜。
(2)有效、半有效硫化体系:硫磺用量一般在0.5份以下,常用量为0.35份,配合较大量的促进剂,需要较长的焦烧时间(超速促进剂与后效性并用),活性剂应使用足量的硬脂酸(1-8份)。
几乎没有硫化返原现象,,硫化均匀性好,耐热性好,压缩变形低,生热小。
缺点为抗屈挠疲劳性差,易发生喷霜现象。
采用高tmtd 的有效硫化体系配方虽然使用广泛,但加工稳定性差,切喷霜严重。
二、金属氧化物硫化体系优点就是硫化胶硬度和弯曲强度较低,用环氧树脂后,可以提升硫化胶的耐热性和动态性能常用的有氧化锌、氧化镁、氧化钙、氢氧化钙等。
氧化锌容易焦烧,加sa后可稍缓和焦烧倾向。
氧化镁和氧化钙焦烧倾向较小,并以氢氧化钙最好。
氧化镁用量以稍多为宜,增加用量可提高胶料硫化速度,并提高硫化胶强度和硬度。
缺点是生热大,耐屈挠性能差。
三、过氧化物类硫化体系优点就是放大永久变形高,耐磨耐寒性较好,胶料硫化时间长,不污染金属,易于制取透明化橡胶。
缺点就是通常无法用作热空气硫化,刺穿性能极差。
(1)简单型:之改硫化体系只有有机过氧化物,或包括防焦剂。
该体系优点为硫化胶的压缩变形小,缺点是硫化过程中焦烧可控程度低,几乎不存在硫化诱导期。
(2)后效性:该体系硫化组分由过氧化物、活性剂和防焦剂共同组成。
特点就是为可以掌控焦烧时间,又不影响硫化效率。
硫化特性与后效性硫磺硫化体系相近。
过氧化物硫化体系温度系数比硫磺硫化体系高。
温度每提高10度,硫化速度约提高两倍。
(硫磺硫化体系提高一倍)焦烧性能亦是如此。
四、树脂类硫化体系特点就是构成热平衡较低的c-c键和醚键交联。
能够提升硫化胶的耐磨、耐屈挠性能,硫化时几乎没硫化抵原现象。
硫磺、促d、dm、tmtd、cz及胺类防老剂都会降低其硫化效率。
橡胶硫化过程的四个阶段(Four...

橡胶硫化过程的四个阶段(Four stages of vulcanization processof rubber)When the gum is vulcanized, its properties change with the change of vulcanization time, which is called vulcanization curve. From the process of curing time affect the glue material tensile strength of the curing time can be divided into four stages: initial stage, less sulfur curing stage, sulfur and sulfur are stage stage1) vulcanization starting stage (also known as scorch or vulcanization induction period) curing start means that the curing time, rubber began to harden, and then can not conduct thermoplastic flow that point of time. The sulfur start stage, i.e., the previous vulcanization time. In this stage, the crosslinking has not yet started and the adhesive has good fluidity in the model. The starting speed of the vulcanization of the rubber compound directly affects the scorch and operation safety of the rubber compound. The length of this phase depends on the type of complexing agent used, especially the promoter. With a speeding accelerator of the rubber material, its Scorch is relatively short, at this time the rubber material more prone to scorch, poor operation safety. In the use of delayed action accelerator (such as sulphenamide) or with little thiuram accelerator, can obtain longer scorch time and good operation safety. However, different curing methods and products have different requirements for focusing time. In the curing of molded products, always hope to have a longer scorch period, so that the glue has sufficient time to flow in the model, without causing products to appear unclear or lack of glue, until the defects. In the non model curing,the vulcanization should be started as early as possible, because the material starts quickly and hardens rapidly, and it is helpful to prevent the products from being deformed due to the softening of the heating. In most cases, however, a longer scorch time is desired to ensure operation2) the stage of sulfide starting stage (also called pre sulfur stage), the stage of sulfide starting and positive vulcanization, is called the stage of less sulfur. At this stage, because of low degree of crosslinking, most of the properties of rubber products are not obvious. Especially in the early stage, the crosslinking degree of rubber material is very low, and its properties change little. The products have no practical significance. But in the late stage of the product, slightly less sulfur, although the product's tensile strength, elasticity and elongation have not yet reached the desired level, but its tear resistance wear resistance and anti crack of dynamic vulcanization is better. Therefore, if the latter performance is emphasized, the product can be slightly less sulfur.3) the positive sulfur stage, in most cases, the product must be cured in the proper degree of cross-linking, to reach the appropriate stage I called the positive vulcanizing stage, that is, the positive sulfur stage. At this stage, the physical and mechanical properties of vulcanizate are not the highest at the same time, but they reach or close to the optimum value, and their comprehensive performance is the best. The temperature and time taken at this stage are called positive and negative curing times.Proper curing time shall depend on the properties required by the product and the thickness of the product cross section. For example, paper products require good tear resistance, tear resistance should be considered in the curing time at or close to the maximum value of the strength for the curing time; products require high wear resistance, can consider the curing time wear small as the curing time is. For heavy products, the "post cure" should be taken into account when selecting the proper sulfur time. The so-called "post curing", that is when the products of sulfur removal, due to poor thermal conductivity of rubber, heat and long time, due to heat and cool products is slow, so it can continue to be vulcanized, especially it is called "after curing". "Post vulcanization" results in a further increase in tensile strength and hardness, a decrease in elasticity and other mechanical properties, and a damage to the service life of the product. Therefore, the thicker the product, the more should be "after vulcanization" into account. Under normal circumstances, the maximum value of tensile strength may be based on the time before the maximum tensile strength or the product of the tensile strength (elongation of the tensile strength and the elongation).4) after the sulfur stage, the positive sulfur stage, continue to sulfide, entered the sulfur stage. The prophase of this stage belongs to a part of the vulcanization flat period. During the flat period, the physical and mechanical properties of vulcanizate remained basically stable. After the flat period,Natural rubber and butyl rubber as chain breaking than crosslinking appears reversion and soft; synthetic rubber due to crosslinking continue to account for increasing strengthsand cyclization structure and harden, and the elongation decreases, rubber property damage. The length of vulcanization flat stage not only indicates the thermal stability of rubber compound, but also has a direct influence on the safety operation of vulcanizing process and the quality of vulcanized products. For curing, curing the flat period, largely depends on the type and amount of accelerator. With a speeding accelerator (such as TMTD), after the initiation of vulcanization, because of its rapid loss of activity, the cleavage of the cross bond is not supplemented, resulting in shortening of the vulcanization flat period. If the thermal stability of the cross link bond is poor, the reversion phenomenon is easy to occur. When the bond energy of the cross link is higher, even longer period of vulcanization can be obtained even if the accelerator is used, and the system can be achieved by using the low sulfur high promoter system. The higher the sulfidation temperature, the faster the cracking rate and the cross linking rate, the stronger the reversion tendency and the shorter sulfidation period. Therefore, when using high temperature vulcanization, it is necessary to select the accelerant that can prolong the vulcanizing period. When using the overspeed accelerator, the curing temperature is low, otherwise the vulcanizing flat period will be shortened to even prevent the possible excessive sulfur。
橡胶硫化过程的四阶段:起硫、欠硫、正硫和过硫
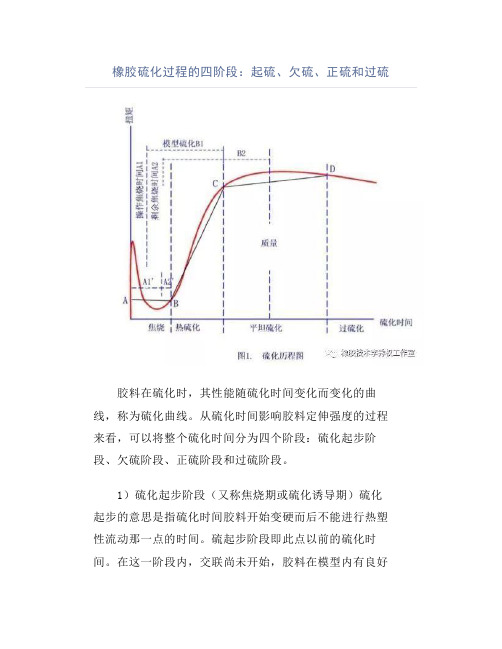
橡胶硫化过程的四阶段:起硫、欠硫、正硫和过硫胶料在硫化时,其性能随硫化时间变化而变化的曲线,称为硫化曲线。
从硫化时间影响胶料定伸强度的过程来看,可以将整个硫化时间分为四个阶段:硫化起步阶段、欠硫阶段、正硫阶段和过硫阶段。
1)硫化起步阶段(又称焦烧期或硫化诱导期)硫化起步的意思是指硫化时间胶料开始变硬而后不能进行热塑性流动那一点的时间。
硫起步阶段即此点以前的硫化时间。
在这一阶段内,交联尚未开始,胶料在模型内有良好的流动性。
胶料硫化起步的快慢,直接影响胶料的焦烧和操作安全性。
这一阶段的长短取决于所用配合剂,特别是促进剂的种类。
用有超速促进剂的胶料,其焦烧比较短,此时胶料较易发生焦烧,操作安全性差。
在使用迟效性促进剂(如亚磺酰胺)或与少许秋兰姆促进剂并用时,均可取得较长的焦烧期和良好的操作安全性。
但是,不同的硫化方法和制品,对焦烧时间的长短亦有不同要求。
在硫化模压制品时,总是希望有较长的焦烧期,使胶料有充分时间在模型内进行流动,而不致使制品出现花纹不清晰或缺胶等到缺陷。
在非模型硫化中,则应要求硫化起步应尽可能早一些,因为胶料起步快而迅速变硬,有利于防止制品因受热变软而发生变形。
不过在大多数情况下仍希望有较长的焦烧时间以保证操作的。
2)欠硫阶段(又称预硫阶段)硫化起步与正硫化之间的阶段称为欠硫阶段。
在此阶段,由于交联度低,橡胶制品应具备的性能大多还不明显。
尤其是此阶段初期,胶料的交联度很低,其性能变化甚微,制品没有实用意义。
但是到了此阶段的后期,制品轻微欠硫时,尽管制品的抗张强度、弹性、伸长率等尚未达到预想的水平,但其抗撕裂性耐磨性和抗动态裂口性等则优于正硫化胶料。
因此,如果着重要求后几种性能时,制品可以轻微欠硫。
3)正硫阶段大多数情况下,制品在硫化时都必须使之达到适当的交联度,达到适当的我联度的阶段叫做正硫化阶段,即正硫阶段。
在此阶段,硫化胶的各项物理机械性能并非在同一时都达到最高值,而是分别达到或接近最佳值,其综合性能最好。
- 1、下载文档前请自行甄别文档内容的完整性,平台不提供额外的编辑、内容补充、找答案等附加服务。
- 2、"仅部分预览"的文档,不可在线预览部分如存在完整性等问题,可反馈申请退款(可完整预览的文档不适用该条件!)。
- 3、如文档侵犯您的权益,请联系客服反馈,我们会尽快为您处理(人工客服工作时间:9:00-18:30)。
4)过硫阶段 正硫阶段之后,继续硫化便进入过硫阶段。这一阶段的前期属于硫化平坦期的一部分。在平坦期中,硫化胶的各项物理机械性能基本上保持稳定。当过平坦期之后,天然橡胶和丁基橡胶由于断链多于交联出现硫化返原现象而变软;合成橡胶则因交联继续占优势和环化结构的增多而变硬,且伸长率也随之降低,橡胶性能受到损害。硫化平坦期的长短,不仅表明胶料热稳定性的高低,而且对硫化工艺的安全操作以及厚制品的硫化质量的好坏均有直接影响。 对于硫黄硫化而言,硫化平坦期的长短,在很大程度上取决于所用促进剂的种类和用量。用有超速促进剂(如TMTD)的胶料,在硫化开始以后,由于它迅速失去活性,交联键的断裂得不到补充,引起硫化平坦期缩短。如果交联键的热稳定性差,则易产生硫化返原现象。当交联键的键能较高时,即使使用超速促进剂也能获得较长的硫化平坦期,使用低硫高促体系,便能达到这一目的。增高硫化温度,裂解比交联的速度增加得更快,硫化返原倾向越强,硫化平坦期也越短。所以采用高温硫化时,必须选取能使硫化平坦期较长的促进剂。使用超速促进剂时,要求硫化温度低,否则硫化平坦期将缩短到甚至(又称预硫阶段) 硫化起步与正硫化之间的阶段称为欠硫阶段。在此阶段,由于交联度低,橡胶制品应具备的性能大多还不明显。尤其是此阶段初期,胶料的交联度很低,其性能变化甚微,制品没有实用意义。但是到了此阶段的后期,制品轻微欠硫时,尽管制品的抗张强度、弹性、伸长率等尚未达到预想的水平,但其抗撕裂性耐磨性和抗动态裂口性等则优于正硫化胶料。因此,如果着重要求后几种性能时,制品可以轻微欠硫。
胶料在硫化时,其性能随硫化时间变化而变化的曲线,称为硫化曲线。从硫化时间影响胶料定伸强度的过程来看,可以将整个硫化时间分为四个阶段:硫化起步阶段、欠硫阶段、正硫阶段和过硫阶段
1)硫化起步阶段(又称焦烧期或硫化诱导期) 硫化起步的意思是指硫化时间胶料开始变硬而后不能进行热塑性流动那一点的时间。硫起步阶段即此点以前的硫化时间。在这一阶段内,交联尚未开始,胶料在模型内有良好的流动性。胶料硫化起步的快慢,直接影响胶料的焦烧和操作安全性。这一阶段的长短取决于所用配合剂,特别是促进剂的种类。用有超速促进剂的胶料,其焦烧比较短,此时胶料较易发生焦烧,操作安全性差。在使用迟效性促进剂(如亚磺酰胺)或与少许秋兰姆促进剂并用时,均可取得较长的焦烧期和良好的操作安全性。但是,不同的硫化方法和制品,对焦烧时间的长短亦有不同要求。在硫化模压制品时,总是希望有较长的焦烧期,使胶料有充分时间在模型内进行流动,而不致使制品出现花纹不清晰或缺胶等到缺陷。在非模型硫化中,则应要求硫化起步应尽可能早一些,因为胶料起步快而迅速变硬,有利于防止制品因受热变软而发生变形。不过在大多数情况下仍希望有较长的焦烧时间以保证操作的
3)正硫阶段 大多数情况下,制品在硫化时都必须使之达到适当的交联度,达到适当的我联度的阶段叫做正硫化阶段,即正硫阶段。在此阶段,硫化胶的各项物理机械性能并非在同一时都达到最高值,而是分别达到或接近最佳值,其综合性能最好。此阶段所取的温度和时间称为正硫化温度和正硫化时间。
正硫化时间须视制品所要求的性能和制品断面的厚薄而定。例如,着重要求抗撕裂性好的制品,应考虑抗撕强度最高或接近最高值的硫化时间定为正硫化时间;要求耐磨性高的制品,则可考虑磨耗量小的硫化时间定为正硫化时间。对于厚制品,在选择正硫时间时,尚需将“后硫化”考虑进去。所谓“后硫化”,即是当制品硫取出以后,由于橡胶导热性差,传热时间长,制品因散热而降温也就较慢,所以它还可以继续进行硫化,特将它称为“后硫化”。“后硫化”导致的抗张强度和硬度进一步增加,弹性和其它机械性能降低,制品的使用寿命因之受到损害。所以,制品越厚就越应将“后硫化”考虑进去。在一般情况下,可以根据抗张强度最高值略前的时间或以强伸积(抗张强度与伸长率的乘积)最高值的硫化时间定为正硫化时间。