影响镀层厚度因素
镀层不够解决方案

镀层不够解决方案
《镀层不够解决方案》
镀层是一种常用的表面处理技术,它可以给材料表面增加一层防腐蚀、耐磨、抗氧化等性能。
然而,在实际应用中,有时候会出现镀层不够厚的情况,这就需要寻找解决方案。
首先,对于镀层不够厚的问题,可以通过增加镀层的时间和温度来解决。
镀层的厚度与镀液的成分、浓度、温度、电流密度等因素有关,因此可以通过调整这些参数来增加镀层的厚度。
例如,可以增加镀液的浓度,增加镀液的温度,提高电流密度等方式来提高镀层的厚度。
其次,可以考虑改变镀层的材料。
有时候,使用不同的镀层材料会影响镀层的厚度。
因此,可以尝试使用不同的材料来进行镀层,以寻找更适合的材料来增加镀层的厚度。
此外,还可以考虑使用其他的表面处理技术来替代镀层。
例如,可以使用喷涂、涂层等技术来增加材料表面的性能,以弥补镀层不够厚的问题。
总之,镀层不够厚的问题可以通过调整镀层的时间和温度,改变镀层材料,或者使用其他的表面处理技术来解决。
只要找到合适的方法,就可以解决镀层不够厚的问题。
镀银工艺技术要求

镀银工艺技术要求镀银工艺技术是将银镀层均匀地镀在物体表面上的一种工艺,常用于金属制品的表面装饰和保护。
以下是镀银工艺技术的一些要求:1.物体表面清洁。
在镀银之前,必须对物体表面进行彻底的清洁,以确保镀银层能够牢固附着在物体表面上。
常用的清洁方法包括机械清洁、化学清洗和电解清洗等。
机械清洁可采用打磨、抛光等方法,化学清洗可用碱性、酸性或有机溶剂,电解清洗可通过电解池中的电解液清洗。
2.有良好的导电性。
银是良好的导电材料,因此镀银层必须具有良好的导电性能。
为了提高导电性,可在镀银层前进行一层导电层的镀覆(如镀铜),导电层能够增加银镀层与物体之间的接触面积,提高导电性能。
3.镀液的配制。
镀液是实现镀银的重要元素,必须严格按照要求进行配制。
镀液中主要包含硝酸银、氧化剂、络合剂等成分。
硝酸银提供银离子,氧化剂用于氧化还原反应,络合剂可与镀液中的杂质离子形成络合物,防止杂质对镀银层的影响。
4.适当的电压和电流密度。
电压和电流密度是控制镀银过程中的重要参数。
在选择电压时,应根据物体的材质和形状,以及所需镀银层的厚度等情况进行调整。
电流密度指单位面积上通过的电流量,过高的电流密度可能导致镀银层不均匀、起皱、放电等问题,因此在实际操作中应选择适当的电流密度。
5.合理的镀银时间。
镀银时间是影响镀银层厚度的重要因素。
在实际操作中,应根据镀银层的要求和物体的大小、形状等因素来确定合适的镀银时间。
镀银时间过长可能导致镀层厚度过厚,而过短可能导致镀层太薄。
6.注意镀银层的附着力。
良好的镀银层应能够牢固地附着在物体表面上,不易剥落。
为了增加镀银层的附着力,可以在镀银之前进行一些前处理,如机械粗糙化、化学活化处理等。
此外,镀银层的厚度也会影响附着力,一般镀银层的厚度应在5-10微米之间。
综上所述,镀银工艺技术要求物体表面清洁、镀液配制合理、良好的导电性能、适当的电压和电流密度、合理的镀银时间以及良好的附着力等。
这些要求的达成将有助于获得高质量的镀银层,提高物体的表面装饰性和保护性能。
影响电镀层质量的因素及生产中注意事项

影响电镀层质量的因素及生产中注意事项摘要:介绍了影响电镀层质量的物理、化学及人为三大影响因素,物理因素主要为镀件材料、形状及表面状态等;化学因素主要为化工材料及配液用水等。
论述了电镀工艺中挂具、阳极、设备及包装对镀房质量的影响,并针对这些质量影响因素在生产过程中应注意的事项进行了详细阐述。
关键词:镀层质量;影响因素;注意事项引言电镀过程中影响电镀层质量的因素较多且复杂,但总的可以归结为物理的、化学的和人为的三种影响因素,在生产过程中,对这三种影响因素加以控制和注意,就会获得满意的、稳定的镀层质量。
一、物理因素影响电镀层质量的物理因素主要有受镀零件、挂具、装挂方式、阳极、设备、包装及贮存环境等。
1受镀零件受镀零件基体材料、形状大小、表面质量对电镀层的影响非常大,这是不容忽视的。
1.1基体材料在设计产品零件时,如该零件需要镀覆,设计者应充分考虑零件材料的镀覆性,当合金中非主成分的铜、铝及镁等金属总含量超过指标时,其表面就很难获得合格的镀覆层;另外,有些采用不符合标准或劣质原材料加工零部件,当加工零部件材料中的铅、锡或镉等金属杂质含量超过一定量时,也难以在零部件表面获得优质的镀覆层。
针对基体材料影响因素应注意以下几点:1〉设计者在选择零部件材料时,除考虑材料在产品中的性能外,还应考虑表面处理对材料的选择性。
2〉应选择符合标准要求的材料加工零部件。
1.2形状对于电镀来说,产品零件的几何形状是不确定的,是变动量最大的物理因素,也是决定电镀加工难易程度的重要因素。
零件形状越复杂,电镀难度系数就越大,对于外形复杂的零件,在进行电镀加工时,突起的部位会因电流过大而烧焦,而低凹部位又因电流过小而镀层很薄或根本镀不上镀层,即便是简单的平板零件,如不采取保护措施,也会使平板四周镀层较厚,而中心部位镀层厚度较薄。
针对形状大小影响因素应注意以下几点:1〉镀覆形状复杂的零件时,应尽可能选取分散能力好的镀液。
2〉根据零件形状选择合适的挂具及装挂方式,避免窝气、尖端放电或深孔无镀层等疵病的产生。
镀锌对工件表面粗糙度的要求

镀锌对工件表面粗糙度的要求
【原创实用版】
目录
1.镀锌对工件表面粗糙度的要求概述
2.影响镀锌表面粗糙度的因素
3.镀锌前对工件表面粗糙度的处理方法
4.镀锌后对工件表面粗糙度的检测与评估
5.结论
正文
一、镀锌对工件表面粗糙度的要求概述
镀锌是一种常见的金属表面处理方法,可以提高工件的耐腐蚀性和使用寿命。
在镀锌过程中,工件表面的粗糙度对镀层的质量、附着力和使用寿命有着重要的影响。
因此,对工件表面粗糙度的要求十分重要。
二、影响镀锌表面粗糙度的因素
影响镀锌表面粗糙度的因素主要有以下几个方面:
1.镀前处理:工件在镀锌前需要进行喷砂、抛光等处理,以去除表面氧化物、油污等,提高镀层的附着力。
2.镀液温度:镀液温度对镀锌层的厚度和粗糙度有直接影响。
温度过高或过低都会导致镀层粗糙度增大。
3.电流密度:电流密度是影响镀锌层厚度的重要因素,电流密度过大或过小都会导致镀层粗糙度增大。
4.镀锌时间:镀锌时间过长或过短都会影响镀层的厚度和粗糙度。
三、镀锌前对工件表面粗糙度的处理方法
为了保证镀锌质量,工件在镀锌前需要进行表面处理,以去除表面氧化物、油污等,提高镀层的附着力。
常见的处理方法有喷砂、抛光等。
四、镀锌后对工件表面粗糙度的检测与评估
镀锌后,需要对工件表面粗糙度进行检测和评估。
常见的检测方法有比较法、光切法、干涉法等。
根据检测结果,可以对镀锌质量进行评估,并采取相应措施进行改进。
五、结论
镀锌对工件表面粗糙度的要求十分重要,影响镀层的质量、附着力和使用寿命。
电镀镀层厚度标准
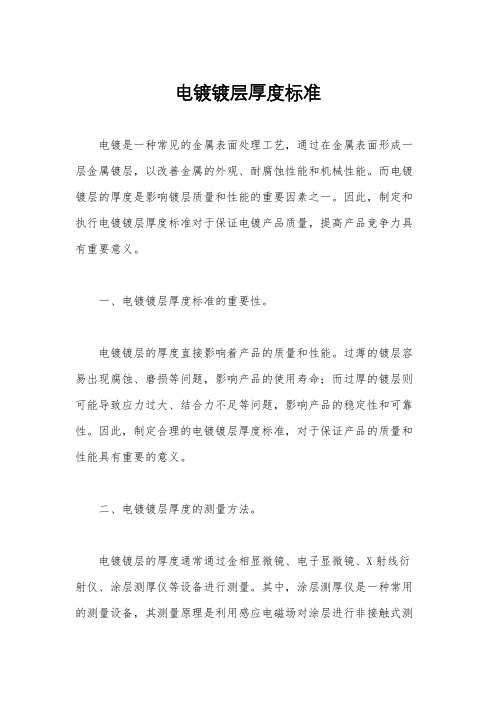
电镀镀层厚度标准电镀是一种常见的金属表面处理工艺,通过在金属表面形成一层金属镀层,以改善金属的外观、耐腐蚀性能和机械性能。
而电镀镀层的厚度是影响镀层质量和性能的重要因素之一。
因此,制定和执行电镀镀层厚度标准对于保证电镀产品质量,提高产品竞争力具有重要意义。
一、电镀镀层厚度标准的重要性。
电镀镀层的厚度直接影响着产品的质量和性能。
过薄的镀层容易出现腐蚀、磨损等问题,影响产品的使用寿命;而过厚的镀层则可能导致应力过大、结合力不足等问题,影响产品的稳定性和可靠性。
因此,制定合理的电镀镀层厚度标准,对于保证产品的质量和性能具有重要的意义。
二、电镀镀层厚度的测量方法。
电镀镀层的厚度通常通过金相显微镜、电子显微镜、X射线衍射仪、涂层测厚仪等设备进行测量。
其中,涂层测厚仪是一种常用的测量设备,其测量原理是利用感应电磁场对涂层进行非接触式测量,具有快速、准确、非破坏性等特点。
三、电镀镀层厚度标准的制定。
制定电镀镀层厚度标准需要考虑产品的具体用途、材料的特性、工艺条件等因素。
一般来说,标准应包括镀层的最小厚度、最大厚度、均匀性要求、测量方法、检验规程等内容。
同时,针对不同的产品和行业,可以制定相应的专用标准,以满足不同领域的需求。
四、电镀镀层厚度标准的执行。
制定标准只是第一步,执行标准同样重要。
企业应建立健全的质量管理体系,加强对电镀生产过程的监控和管理,确保电镀镀层厚度符合标准要求。
同时,加强对原材料、设备、工艺的管理,提高产品的稳定性和可靠性。
五、电镀镀层厚度标准的意义。
制定和执行电镀镀层厚度标准,对于提高产品的质量和性能,增强产品的市场竞争力具有重要意义。
同时,标准的制定还可以促进电镀行业的健康发展,提高整个行业的技术水平和产品质量。
六、结语。
电镀镀层厚度标准的制定和执行,对于提高产品质量、保障产品安全、促进行业发展具有重要意义。
各企业应加强标准化意识,推动标准的制定和执行,共同推动电镀行业向着更加规范化、高质量的方向发展。
镀层厚度计算 (2)
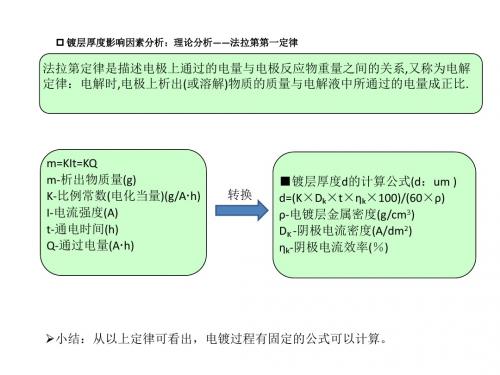
If Dk = 8A /dm2 =0.08 A/cm² If Dk = 9A /dm2 =0.09A/cm²
,δ= 0.000856cm =8.56μm ,δ= 0.000963cm =9.63μm
要求镀层厚度值为9μm,所以DK选取8~9A/dm²。
Package QFN
Lead frame area Steel belt area (cm2) (cm2) 3550 640
Note: δ= Plating thickness,(Unit:cm)。P ( Metal proportion of plating layer)=7.3,(Unit:g / cm3). t = Plating Time,(Unit:hour) Dk = Cathode current density,(Unit:A / dm2,convert to A / cm2)。K = electrochemistry of metal,(Unit:g / AH) η= Cathode current efficiency,assume 80 % in acidic Sn; P(Sn)= 7.3 g / cm 3,K(Sn)= 2.2146 g / AH
转换
■镀层厚度d的计算公式(d:um ) d=(K×Dk×t×ηk×100)/(60×ρ) ρ-电镀层金属密度(g/cm3) DK -阴极电流密度(A/dm2) ηk-阴极电流效率(%)
小结:从以上定律可看出,电镀过程有固定的公式可以计算。
镀层厚度影响因素分析:具体计算推导 The length of 14# plating cell is 2mX4=8m,Belt speed 3.0m/ min, plating time : t = 2.67min = 0.044H δ= t· Dk· K· η / P = 0.044· Dk· 2.2146· 0.80/ 7.3 = 0.0107· Dk
影响镀层厚度和质量的主要因素
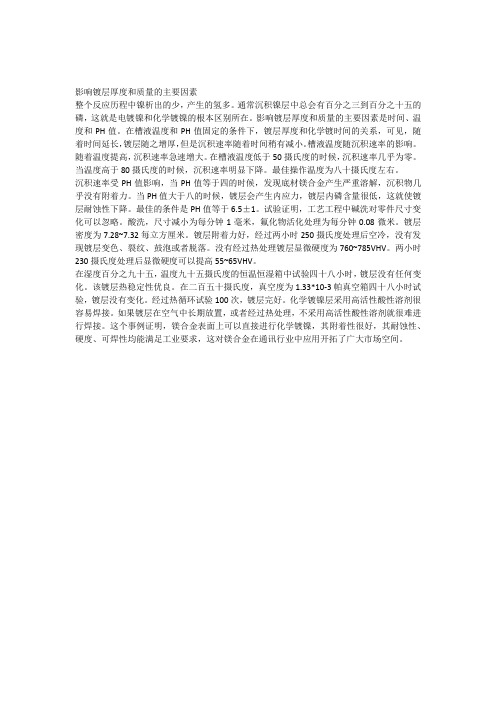
影响镀层厚度和质量的主要因素整个反应历程中镍析出的少,产生的氢多。
通常沉积镍层中总会有百分之三到百分之十五的磷,这就是电镀镍和化学镀镍的根本区别所在。
影响镀层厚度和质量的主要因素是时间、温度和PH值。
在槽液温度和PH值固定的条件下,镀层厚度和化学镀时间的关系,可见,随着时间延长,镀层随之增厚,但是沉积速率随着时间稍有减小。
槽液温度随沉积速率的影响。
随着温度提高,沉积速率急速增大。
在槽液温度低于50摄氏度的时候,沉积速率几乎为零。
当温度高于80摄氏度的时候,沉积速率明显下降。
最佳操作温度为八十摄氏度左右。
沉积速率受PH值影响,当PH值等于四的时候,发现底材镁合金产生严重溶解,沉积物几乎没有附着力。
当PH值大于八的时候,镀层会产生内应力,镀层内磷含量很低,这就使镀层耐蚀性下降。
最佳的条件是PH值等于6.5±1。
试验证明,工艺工程中碱洗对零件尺寸变化可以忽略。
酸洗,尺寸减小为每分钟1毫米,氟化物活化处理为每分钟0.08微米。
镀层密度为7.28~7.32每立方厘米。
镀层附着力好,经过两小时250摄氏度处理后空冷,没有发现镀层变色、裂纹、鼓泡或者脱落。
没有经过热处理镀层显微硬度为760~785VHV。
两小时230摄氏度处理后显微硬度可以提高55~65VHV。
在湿度百分之九十五,温度九十五摄氏度的恒温恒湿箱中试验四十八小时,镀层没有任何变化。
该镀层热稳定性优良。
在二百五十摄氏度,真空度为1.33*10-3帕真空箱四十八小时试验,镀层没有变化。
经过热循环试验100次,镀层完好。
化学镀镍层采用高活性酸性溶剂很容易焊接。
如果镀层在空气中长期放置,或者经过热处理,不采用高活性酸性溶剂就很难进行焊接。
这个事例证明,镁合金表面上可以直接进行化学镀镍,其附着性很好,其耐蚀性、硬度、可焊性均能满足工业要求,这对镁合金在通讯行业中应用开拓了广大市场空间。
紧固件表面镀层标准
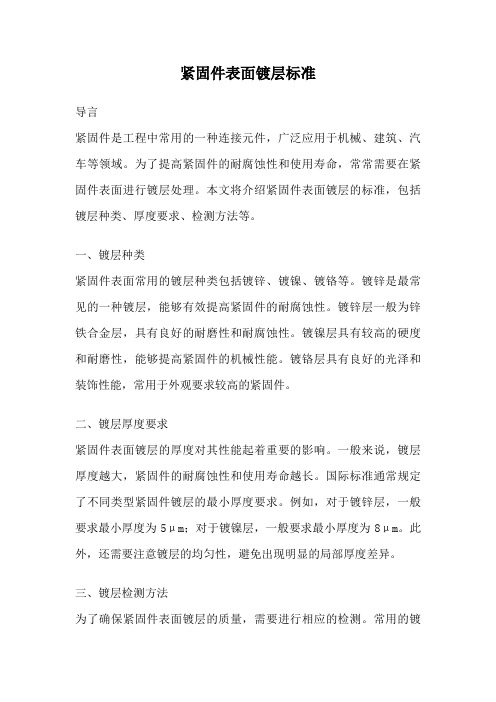
紧固件表面镀层标准导言紧固件是工程中常用的一种连接元件,广泛应用于机械、建筑、汽车等领域。
为了提高紧固件的耐腐蚀性和使用寿命,常常需要在紧固件表面进行镀层处理。
本文将介绍紧固件表面镀层的标准,包括镀层种类、厚度要求、检测方法等。
一、镀层种类紧固件表面常用的镀层种类包括镀锌、镀镍、镀铬等。
镀锌是最常见的一种镀层,能够有效提高紧固件的耐腐蚀性。
镀锌层一般为锌铁合金层,具有良好的耐磨性和耐腐蚀性。
镀镍层具有较高的硬度和耐磨性,能够提高紧固件的机械性能。
镀铬层具有良好的光泽和装饰性能,常用于外观要求较高的紧固件。
二、镀层厚度要求紧固件表面镀层的厚度对其性能起着重要的影响。
一般来说,镀层厚度越大,紧固件的耐腐蚀性和使用寿命越长。
国际标准通常规定了不同类型紧固件镀层的最小厚度要求。
例如,对于镀锌层,一般要求最小厚度为5μm;对于镀镍层,一般要求最小厚度为8μm。
此外,还需要注意镀层的均匀性,避免出现明显的局部厚度差异。
三、镀层检测方法为了确保紧固件表面镀层的质量,需要进行相应的检测。
常用的镀层检测方法包括厚度测量、附着力测试和耐腐蚀性测试等。
常见的厚度测量方法有磁性法、涂层测厚仪等。
附着力测试是用来评估镀层与基材之间的结合力,常用的测试方法包括划格法、剥离法等。
耐腐蚀性测试是评估镀层在不同腐蚀介质中的性能,常用的测试方法有盐雾试验、湿热试验等。
四、国际标准紧固件表面镀层的标准是根据国际标准组织制定的。
ISO 4042是紧固件表面镀层的通用规范,其中包括了镀层种类、厚度要求、检测方法等内容。
ISO 10684是针对紧固件镀锌层的特殊规范,详细规定了镀锌层的厚度要求、试验方法等。
此外,不同行业和国家也有各自的标准和规范,如ASTM、DIN等。
五、镀层的影响因素紧固件表面镀层的质量受到多种因素的影响。
首先是基材的选择,不同材料的紧固件对镀层的要求不同。
其次是镀液的配方和处理工艺,不同的镀液组成和工艺参数会影响镀层的均匀性和质量。
影响镀层厚度分布均匀性的因素

一、影响镀层厚度分布均匀性的因素:使镀层厚度分布均匀的重要性电沉积时总希望镀层厚度在工件上的分布越均匀越好。
当工件上沉积的总金属量相同时,若厚度分布不均匀,则会带来很多坏处:(1)对于阳极性镀层,镀层薄处经不起牺牲腐蚀会先使基体产生锈蚀。
而一个制件部分锈蚀后则已不合格,造成了镀层过厚处金属的浪费。
若为保证最薄处不生锈,只能加大平均厚度,导致电镀成本增大。
(2)对于阴极性镀层,薄处镀层孔隙率高,很易产生点状锈蚀,继而锈点加大,形成连片锈蚀。
与阳极性镀层相比,阴极性镀层薄处锈蚀更快。
对于局部防渗氮、渗碳镀层,薄处易形成孔眼,失去保护作用。
若厚度均匀则各部分孔隙率差别不大,总体防蚀性提高。
例如,对电池钢壳滚镀亮镍,壳内(特别是靠底部的地方)镀层很薄,甚至在清洗烘干时即已起小锈点、泛黄,为此要“出白”处理,迅速用水溶性封闭剂封闭后干燥。
(3)对于光亮性电镀,镀层薄处因阴极电流密度小,故光亮整平性差,影响整体外观。
(4)合金电沉积时,不同厚度处的合金组分不相同,或外观不均(如仿金镀),又或抗蚀性不一致(如锌镍合金)。
(5)不同厚度处镀层的物理、机械性能(如脆性、内应力等)不一样。
若镀后还要作冲压成型等机加工处理,镀层过厚处往往机加工性能不良(起皮、开裂、粉状脱落等)。
无论从防蚀性,还是外观、机加工性能等方面讲,都希望提高镀层厚度的均匀性。
对于尺寸镀硬铬,若用户要求镀后不作磨削处理,则很难办到;有时为了保证最薄处达到最终尺寸要求,厚度均匀性差时,不得不大大加大平均厚度,这在生产中并不少见。
为使制件上镀层各部分厚度尽量接近,必须了解影响厚度分布均匀性的因素。
二、影响镀层厚度分布均匀性的因素:镀液性能因素-镀液的分散能力与深镀能力这是镀液的两项重要技术指标,一般为新工艺研究的必测指标。
镀液的分散能力是指镀液使镀层厚度分布均匀的能力,又称均镀能力,通常用T·P表示。
在其他条件相同时,分散能力越好,则镀层厚度分布越均匀。
电镀挂镀镀层不均匀的原因

电镀挂镀镀层不均匀的原因主要包括以下几个方面:
1. 电流密度分布不均:电流密度是电化学反应过程中反应速率的一个重要因素。
若电流密度分布不均,就会导致电化学反应在不同区域中发生的速率不同,进而造成镀层不均匀。
此时,需要通过调整阳极和阴极之间的距离、调整电极形状、改变电极的倾斜角度等方法,使电流在阳极和阴极表面分布均匀。
2. 磁场分布不均匀或电极放置不当:会影响电极上的电流密度分布,导致电镀厚度不均匀。
此时可加入电解液搅拌,调整电极布局或更换设备来解决问题。
3. 基材表面不干净或有油污、氧化皮等物质:会影响电镀液与基材的接触,导致电流只流过一部分区域,造成电镀厚度不均匀。
此时可加强前处理工序、增加电镀锌层厚度或更换质量更好的基材来解决问题。
4. 电镀车间温度、湿度、灰尘、气流等因素的影响:温度过高或过低会影响电镀液的活性,湿度太高会使电镀液中的水分增加,造成气泡等问题;空气中的灰尘会与电镀液中的金属离子结合,影响电极表面,导致电镀厚度不均匀。
此时可加强环境管理,保持车间温湿度适宜,减少灰尘等污染物的产生。
此外,材料选择不合适、操作时未严格按工艺要求进行
等也是导致电镀挂镀镀层不均匀的原因。
为解决电镀挂镀镀层不均匀的问题,需综合考虑多方面因素,从多个环节进行优化和控制。
电镀镀层厚度标准
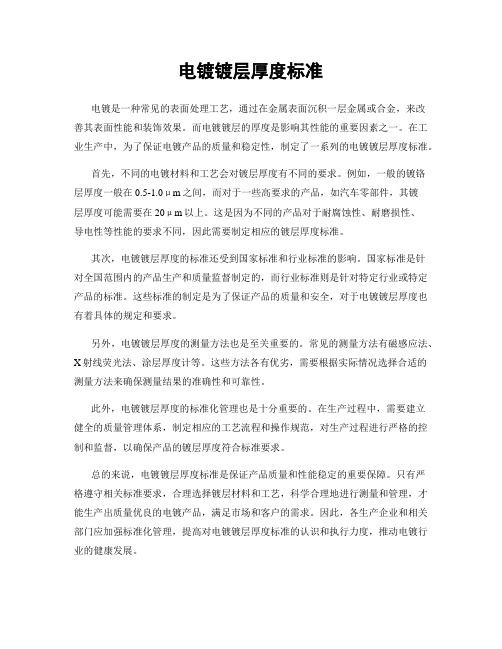
电镀镀层厚度标准电镀是一种常见的表面处理工艺,通过在金属表面沉积一层金属或合金,来改善其表面性能和装饰效果。
而电镀镀层的厚度是影响其性能的重要因素之一。
在工业生产中,为了保证电镀产品的质量和稳定性,制定了一系列的电镀镀层厚度标准。
首先,不同的电镀材料和工艺会对镀层厚度有不同的要求。
例如,一般的镀铬层厚度一般在0.5-1.0μm之间,而对于一些高要求的产品,如汽车零部件,其镀层厚度可能需要在20μm以上。
这是因为不同的产品对于耐腐蚀性、耐磨损性、导电性等性能的要求不同,因此需要制定相应的镀层厚度标准。
其次,电镀镀层厚度的标准还受到国家标准和行业标准的影响。
国家标准是针对全国范围内的产品生产和质量监督制定的,而行业标准则是针对特定行业或特定产品的标准。
这些标准的制定是为了保证产品的质量和安全,对于电镀镀层厚度也有着具体的规定和要求。
另外,电镀镀层厚度的测量方法也是至关重要的。
常见的测量方法有磁感应法、X射线荧光法、涂层厚度计等。
这些方法各有优劣,需要根据实际情况选择合适的测量方法来确保测量结果的准确性和可靠性。
此外,电镀镀层厚度的标准化管理也是十分重要的。
在生产过程中,需要建立健全的质量管理体系,制定相应的工艺流程和操作规范,对生产过程进行严格的控制和监督,以确保产品的镀层厚度符合标准要求。
总的来说,电镀镀层厚度标准是保证产品质量和性能稳定的重要保障。
只有严格遵守相关标准要求,合理选择镀层材料和工艺,科学合理地进行测量和管理,才能生产出质量优良的电镀产品,满足市场和客户的需求。
因此,各生产企业和相关部门应加强标准化管理,提高对电镀镀层厚度标准的认识和执行力度,推动电镀行业的健康发展。
电镀的主要工艺参数

电镀的主要工艺参数电镀是一种常见的表面处理工艺,通过在物体表面上镀上一层金属薄膜,以改善物体的外观、耐腐蚀性和导电性能。
在进行电镀过程中,有许多关键的工艺参数需要控制和调整,以确保镀层的质量和性能达到要求。
电镀液的成分是决定电镀效果的关键因素之一。
电镀液主要包括金属盐、添加剂和溶剂等组分。
金属盐通常是金属阳离子的盐酸或硫酸盐,而添加剂则包括控制镀层均匀性、增加附着力和改善电镀速度的化学物质。
溶剂的选择要考虑到溶解性、挥发性和安全性等因素。
电镀液的温度是影响电镀过程的重要参数。
一般来说,液体温度越高,电镀速度越快,但过高的温度可能导致电镀液的挥发和分解,影响镀层的质量。
因此,需要根据金属的性质和电镀液的成分来确定合适的温度范围。
电镀液的酸碱度(pH值)也是一个关键的工艺参数。
不同金属的电镀液对pH值的要求不同,一般建议在合适的酸碱度范围内进行电镀。
酸碱度的调整可以通过添加酸或碱来实现,但要注意避免过高或过低的pH值对电镀液和镀层的影响。
电流密度是控制电镀速度和镀层均匀性的重要参数。
电流密度过高会导致局部电流过大,造成镀层厚度不均匀或甚至出现气孔和裂纹等缺陷。
而电流密度过低则会导致镀层速度过慢,影响生产效率。
因此,需要根据工件的形状、大小和电镀液的性质来选择合适的电流密度。
电镀时间是影响镀层厚度和质量的关键因素。
电镀时间过长可能导致镀层厚度过厚或出现过量金属沉积,而电镀时间过短则可能导致镀层厚度不足。
因此,需要根据要求的镀层厚度和电镀液的特性来确定适当的电镀时间。
还需要注意电极的选择和放置位置。
电极应与工件接触良好,以确保电流的传导和镀层的均匀性。
放置位置的选择要考虑到工件的形状和尺寸,以避免电流过于集中或过于分散。
电镀的主要工艺参数包括电镀液的成分、温度、酸碱度,以及电流密度、电镀时间和电极的选择和放置位置等。
合理控制和调整这些参数,可以获得满足要求的电镀镀层,提高产品的质量和性能。
金属镀覆层与化学镀覆层选择原则与厚度
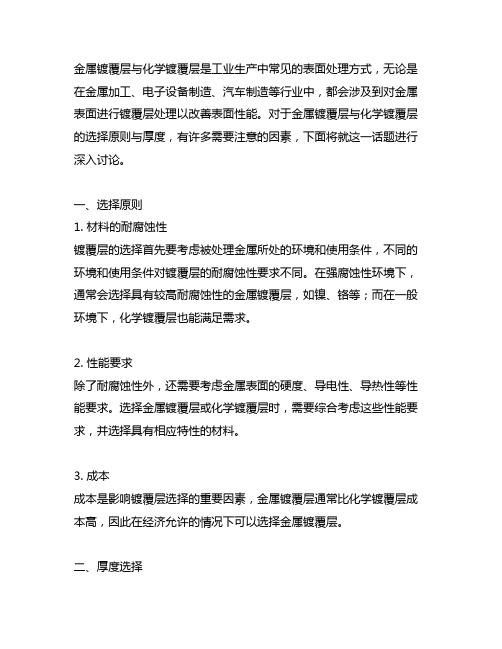
金属镀覆层与化学镀覆层是工业生产中常见的表面处理方式,无论是在金属加工、电子设备制造、汽车制造等行业中,都会涉及到对金属表面进行镀覆层处理以改善表面性能。
对于金属镀覆层与化学镀覆层的选择原则与厚度,有许多需要注意的因素,下面将就这一话题进行深入讨论。
一、选择原则1. 材料的耐腐蚀性镀覆层的选择首先要考虑被处理金属所处的环境和使用条件,不同的环境和使用条件对镀覆层的耐腐蚀性要求不同。
在强腐蚀性环境下,通常会选择具有较高耐腐蚀性的金属镀覆层,如镍、铬等;而在一般环境下,化学镀覆层也能满足需求。
2. 性能要求除了耐腐蚀性外,还需要考虑金属表面的硬度、导电性、导热性等性能要求。
选择金属镀覆层或化学镀覆层时,需要综合考虑这些性能要求,并选择具有相应特性的材料。
3. 成本成本是影响镀覆层选择的重要因素,金属镀覆层通常比化学镀覆层成本高,因此在经济允许的情况下可以选择金属镀覆层。
二、厚度选择1. 保护性要求镀覆层的厚度与其保护性能密切相关,通常来说,厚度越大,保护性能越好。
在实际选择中,需要根据被处理金属的使用环境和需求确定合适的镀层厚度。
2. 应力控制厚度过大的金属镀覆层容易产生内应力,导致镀层脱落、开裂等问题,因此需要考虑镀层的内应力,并控制合适的厚度。
3. 工艺限制金属镀覆层与化学镀覆层的工艺限制也是厚度选择的重要考虑因素。
不同的镀层工艺对厚度有一定的要求,需要根据实际工艺条件确定合适的厚度。
4. 成本考虑镀覆层的厚度与成本也有一定的关系,过大的厚度会增加成本,因此需要综合考虑保护性和成本,选择合适的厚度。
金属镀覆层与化学镀覆层的选择原则与厚度选择需要综合考虑材料的耐腐蚀性、性能要求、成本等因素,并在保护性要求、应力控制、工艺限制和成本考虑等方面进行合理选择。
随着工艺技术的不断发展,对镀覆层的要求也在不断提高,因此金属镀覆层与化学镀覆层的选择需结合实际情况进行科学的分析与评估,以确保被处理金属的表面质量和性能达到预期要求。
铜排镀锡厚度标准
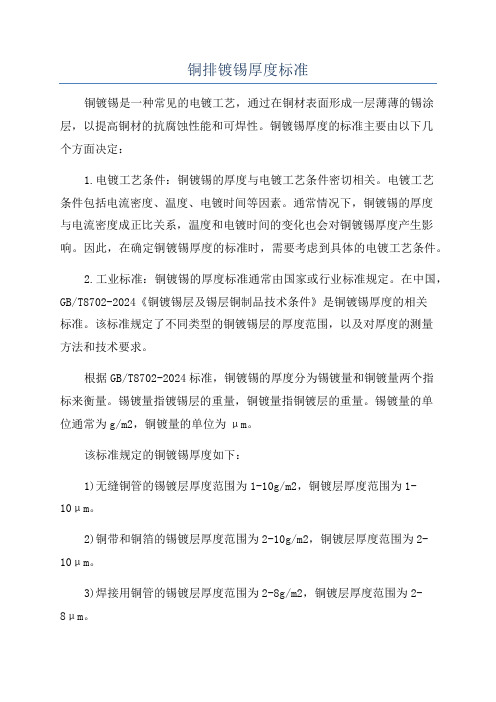
铜排镀锡厚度标准铜镀锡是一种常见的电镀工艺,通过在铜材表面形成一层薄薄的锡涂层,以提高铜材的抗腐蚀性能和可焊性。
铜镀锡厚度的标准主要由以下几个方面决定:1.电镀工艺条件:铜镀锡的厚度与电镀工艺条件密切相关。
电镀工艺条件包括电流密度、温度、电镀时间等因素。
通常情况下,铜镀锡的厚度与电流密度成正比关系,温度和电镀时间的变化也会对铜镀锡厚度产生影响。
因此,在确定铜镀锡厚度的标准时,需要考虑到具体的电镀工艺条件。
2.工业标准:铜镀锡的厚度标准通常由国家或行业标准规定。
在中国,GB/T8702-2024《铜镀锡层及锡层铜制品技术条件》是铜镀锡厚度的相关标准。
该标准规定了不同类型的铜镀锡层的厚度范围,以及对厚度的测量方法和技术要求。
根据GB/T8702-2024标准,铜镀锡的厚度分为锡镀量和铜镀量两个指标来衡量。
锡镀量指镀锡层的重量,铜镀量指铜镀层的重量。
锡镀量的单位通常为g/m2,铜镀量的单位为μm。
该标准规定的铜镀锡厚度如下:1)无缝铜管的锡镀层厚度范围为1-10g/m2,铜镀层厚度范围为1-10μm。
2)铜带和铜箔的锡镀层厚度范围为2-10g/m2,铜镀层厚度范围为2-10μm。
3)焊接用铜管的锡镀层厚度范围为2-8g/m2,铜镀层厚度范围为2-8μm。
需要注意的是,这只是一个参考值,具体的铜镀锡厚度要根据具体产品的要求来确定。
对于一些特殊用途的产品,如电子元件等,可能需要更精确的铜镀锡厚度。
同时,铜镀锡的厚度还与产品的具体应用有关。
不同的产品对铜镀锡的要求有所差异。
比如,对于需要进行大量的焊接的电路板,铜镀锡的厚度一般要求较厚,以提高可焊性;而对于需要高度精密的电子元件,铜镀锡的厚度一般要求较薄,以保证产品的净重量和尺寸精度。
在实际应用中,对于通常的铜镀锡需求,可以按照GB/T8702-2024标准制定的范围来选择。
对于一些特殊要求的产品,则需要根据实际情况进行调整。
总的来说,铜镀锡厚度的标准由电镀工艺条件、工业标准和具体产品要求共同决定。
磁铁镀层镍铜镍厚度

磁铁镀层镍铜镍厚度全文共四篇示例,供读者参考第一篇示例:磁铁是一种具有磁性的物质,它能够吸引铁、镍、钴等金属。
在现代工业生产中,磁铁被广泛应用于各种领域,如电子、通信、汽车、医疗等。
为了提高磁铁的性能和防止氧化,往往会进行镀层处理。
镍铜镍镀层是一种常见的处理方法。
镍铜镍镀层是指在磁铁表面先镀一层镍,然后再镀一层铜,最后再镀一层镍。
这种处理方法可以有效提高磁铁的耐腐蚀性能和机械性能,延长使用寿命。
镀层还可以改善磁铁的外观,更加美观。
在进行镍铜镍镀层处理时,镍的厚度是一个非常关键的参数。
镀镍的厚度会直接影响磁铁的性能和成本。
一般来说,镍的厚度越大,磁铁的耐腐蚀性能越好,但也会增加成本。
在实际应用中,需要根据具体的需求来确定镍的厚度。
镀层厚度的测量是非常重要的,它可以确保镀层的质量和稳定性。
常见的测量方法包括X射线衍射法、电子探针法、微硬度计测量等。
这些方法可以准确地测量镍铜镍镀层的厚度,帮助控制生产过程,提高产品质量。
除了镍的厚度外,铜的厚度和镍之间的结合层也是需要关注的。
铜的厚度对磁铁的电导率和导磁率有影响,而结合层的质量会影响铜和镍层的结合力和稳定性。
在进行镀层处理时,需要保证铜和镍的厚度以及结合层的质量均符合技术要求。
磁铁镀层镍铜镍的厚度是影响磁铁性能和质量的重要因素。
在实际生产中,需要根据具体的需求和技术要求来确定合适的镍厚度,并通过合适的测量方法来确保镀层质量。
只有这样,才能生产出高质量的磁铁产品,满足不同领域的需求。
第二篇示例:磁铁镀层镍铜镍是一种常见的表面处理工艺,通常用于改善磁铁的表面性能和延长其使用寿命。
镀层的厚度直接影响着其耐腐蚀性、外观和磁性能。
本文将对磁铁镀层镍铜镍的厚度进行详细探讨。
一、磁铁镀层的作用1. 保护磁铁表面:磁铁本身易受氧化、腐蚀等影响,镀层可以有效保护磁铁表面,延长其使用寿命。
2. 改善磁铁的外观:镀层可以使磁铁表面光滑、均匀,提高其外观质量。
3. 提高磁铁的性能:适当的镀层可以改善磁铁的磁性能,增加其磁导率和磁化强度。
怎么控制镀锌层的厚度

调整锌液合金比例;温度,及浸锌时间.如果钢材的硅含量较高,可加入锌镍合金降低上锌量。
也可加入助镀剂添加剂来改变助镀剂的性质,使镀层变得漂亮。
在热镀锌过程中,如果要使镀件表面光亮、镀层博,这跟各道工序都有很大关系,酸洗不到位,助镀液配方不对,锌温高低,人工操作,行车的起吊速度,这都是有很大关系的,这个问题你最好买一本热镀锌的工艺相关的书籍好好看下。
太多学问在里面了。
热镀锌层形成过程是铁基体与最外面的纯锌层之间形成铁-锌合金的过程,工件表面在热浸镀时形成铁-锌合金层,才使得铁与纯锌层之间很好结合,其过程可简单地叙述为:当铁工件浸入熔融的锌液时,首先在界面上形成锌与α铁(体心)固熔体。
这是基体金属铁在固体状态下溶有锌原子所形成一种晶体,两种金属原子之间是融合,原子之间引力比较小。
因此,当锌在固熔体中达到饱和后,锌铁两种元素原子相互扩散,扩散到(或叫渗入)铁基体中的锌原子在基体晶格中迁移,逐渐与铁形成合金,而扩散到熔融的锌液中的铁就与锌形成金属间化合物FeZn13,沉入热镀锌锅底,即为锌渣。
当工件从浸锌液中移出时表面形成纯锌层,为六方晶体。
其含铁量不大于%。
减小厚度提高热镀锌锌温,但要考虑锌锅情况,铁锅不宜超过480度,陶瓷锅可以到530度减少浸锌时间取出时速度要缓慢添加锌铝合金可以减少镀层厚度1.放慢工件提升速度。
2.尽量控制镀锌时间。
3.适量添加减薄合金。
关于热镀锌层厚度的说明关于热镀锌层厚度的说明热镀锌镀层的形成机理热浸镀锌是一个冶金反应过程.从微观角度看,热浸镀锌过程是两个动态平衡:热平衡和锌铁交换平衡.当把钢铁工件浸入450℃左右的熔融锌液时,常温下的工件吸收锌液热量,达到200℃以上时,锌和铁的相互作用逐渐明显,锌渗入铁工件表面.随着工件温度逐渐接近锌液温度,工件表面形成含有不同锌铁比例的合金层,构成锌镀层的分层结构,随着时间延长,镀层中不同的合金层呈现不同的成长速率.从宏观角度看,上述过程表现为工件浸入锌液,锌液面出现沸腾,当锌铁反应逐渐平衡,锌液面逐渐平静.工件被提出锌液面,工件温度逐渐降低至200℃以下时,锌铁反应停止,热镀锌镀层形成,厚度确定.热镀锌镀层厚度要求影响锌镀层厚度的因素主要有:基体金属成分,钢材的表面粗糙度,钢材中的活性元素硅和磷含量及分布状态,钢材的内应力,工件几何尺寸,热浸镀锌工艺.现行的国际和中国热镀锌标准都根据钢材厚度划分区段,锌镀层平局厚度以及局部厚度应达到相应厚度,以确定锌镀层的防腐蚀性能.钢材厚度不同的工件,达成热平衡和锌铁交换平衡所需的时间不同,形成的镀层厚度也不同.标准中的镀层平均厚度是基于上述镀锌机理的工业生产经验值,局部厚度是考虑到锌镀层厚度分布的不均匀性以及对镀层防腐蚀性要求所需要的经验值.因此,ISO标准,美国ASTM标准,日本JIS标准和中国标准在锌镀层厚度要求上略有不同,大同小异.热镀锌镀层厚度的作用和影响热镀锌镀层的厚度决定了镀件的防腐蚀性能.详细讨论请参见附件中由美国热镀锌协会提供的相关数据.用户可以选择高于或低于标准的锌镀层厚度.对于表面光滑的3mm以下薄钢板,工业生产中得到较厚的镀层是困难的,另外,与钢材厚度不相称的锌镀层厚度会影响镀层与基材的结合力以及镀层外观质量.过厚的镀层会造成镀层外观粗糙,易剥落,镀件经不起搬运和安装过程中的碰撞.钢材中如果存在较多的活性元素硅和磷,工业生产中得到较薄的镀层也十分困难,这是由于钢中的硅含量影响锌铁间的合金层生长方式,会使ζ相锌铁合金层迅速生长并将ζ相推向镀层表面,致使镀层表面粗糙无光,形成附着力差的灰暗镀层.因此,如上述讨论结果,镀锌层的生长存在不确定性,实际生产中要取得某一范围的镀层厚度常常是困难的,热镀锌标准中规定的厚度是大量实验后产生的经验值,照顾到了各种因素和要求,较为合理.上海永丰热镀锌有限公司2007年8月热镀锌原理及工艺说明1 引言热镀锌也称热浸镀锌,是钢铁构件浸入熔融的锌液中获得金属覆盖层的一种方法。
镀锌板镀层厚度标准

镀锌板镀层厚度标准镀锌板是一种常见的金属制品,具有耐腐蚀、耐磨损等优良性能,广泛应用于建筑、汽车、家电等行业。
而镀锌板的质量与其镀层厚度密切相关。
本文将探讨镀锌板镀层厚度的标准,以帮助读者更好地了解和选购镀锌板产品。
一、镀锌板镀层厚度标准的背景和意义在制造镀锌板时,通过将钢材浸泡在熔融的锌液中,形成一层锌的覆盖层,起到保护基材、延长使用寿命的作用。
因此,镀锌板镀层厚度的标准制定具有重要意义。
合理的镀层厚度能够有效提高镀锌板的防腐性能,阻止氧气和水分接触到钢材表面,减少钢材的腐蚀速度。
同时,良好的镀层厚度还能保护钢材不受机械磨损,提高产品的使用寿命。
二、国际标准:ASTM A123和EN ISO 1461国际上对于镀锌板镀层厚度的标准主要有美国材料和试验协会(ASTM)的A123标准和欧洲标准化组织(ISO)的EN ISO 1461标准。
根据ASTM A123标准,热浸镀锌钢制品的厚度应为145μm(4.5mil)以上。
该标准对不同类型的钢材,如薄板、厚板和管材等,均有详细的镀层厚度要求。
而EN ISO 1461标准则规定了镀锌层的最小厚度。
根据不同的基材类型,其要求的最小镀层厚度范围为35μm至85μm。
这个标准同样也覆盖了各类镀锌板制品。
三、国内标准:GB/T 11533-2011在国内,国家标准《钢铁产品热浸镀锌层技术条件与试验方法》(GB/T 11533-2011)对于镀锌板镀层厚度也有明确规定。
根据该标准的要求,镀锌板的镀层厚度应符合以下规定:1.薄镀层:镀层厚度为5μm至15μm,适用于一般室内、干燥环境下的使用。
2.普通镀层:镀层厚度为20μm至25μm,适用于一般室外、不暴露在雨水等恶劣环境下的使用。
3.增强镀层:镀层厚度为55μm至70μm,适用于室外、暴露在雨水等恶劣环境下的使用。
国内标准GB/T 11533-2011的制定,旨在保证国内生产的镀锌板在质量上达到国际先进水平,并为消费者提供明确的产品选择参考。
电镀镍厚度

电镀镍厚度1. 介绍电镀镍厚度是指在电镀过程中,通过控制电镀时间和电流密度,使镍层在被电解液中沉积的厚度。
电镀镍常用于提高金属表面的耐腐蚀性能、增加材料的硬度和改善外观。
2. 电镀镍的原理电镀镍的原理是利用电解液中的金属离子在电极上还原成金属沉积,从而形成金属镀层。
一般来说,电镀液中的金属离子来源于溶解的金属盐。
在电镀镍过程中,需要准备一个阳极和一个阴极。
阳极通常是镍板,而阴极则是待镀物。
当施加电流时,金属离子从电解液中被还原到阴极上,形成金属镀层。
通过控制电流密度和电镀时间,可以控制镀层的厚度。
3. 影响电镀镍厚度的因素3.1 电流密度电流密度是指单位面积上的电流值。
电流密度越大,单位时间内金属离子被还原的数量就越多,形成的镀层厚度也就越大。
因此,调整电流密度可以控制镀层的厚度。
3.2 电镀时间电镀时间是指将待镀物放入电镀槽中的时间。
电镀时间越长,金属离子被还原的数量就越多,形成的镀层厚度也就越大。
因此,延长电镀时间可以增加镀层厚度。
3.3 温度温度对电镀过程有一定影响。
一般来说,提高温度可以加快电镀速度,使镀层更加均匀。
但是,过高的温度可能导致电解液的挥发和气泡的产生,影响电镀质量。
3.4 电解液成分电解液的成分也会影响电镀镍的厚度。
不同的电解液中含有不同的金属离子,因此选择合适的电解液对于控制镀层厚度非常重要。
3.5 待镀物表面处理待镀物的表面处理也会影响电镀镍的厚度。
如果待镀物表面有氧化物或油污等杂质,会影响电流的传导和金属离子的沉积,从而影响镀层的厚度。
4. 电镀镍厚度的测量方法4.1 金相显微镜法金相显微镜法是一种常用的测量电镀镍厚度的方法。
通过在待测样品上切割一条横截面,然后使用金相显微镜观察镀层的厚度。
这种方法可以提供较高的分辨率和精确度。
4.2 X射线荧光光谱法X射线荧光光谱法是一种非破坏性的测量方法。
通过使用X射线照射待测样品,然后测量被激发的荧光光谱,从而获得镀层的厚度信息。
- 1、下载文档前请自行甄别文档内容的完整性,平台不提供额外的编辑、内容补充、找答案等附加服务。
- 2、"仅部分预览"的文档,不可在线预览部分如存在完整性等问题,可反馈申请退款(可完整预览的文档不适用该条件!)。
- 3、如文档侵犯您的权益,请联系客服反馈,我们会尽快为您处理(人工客服工作时间:9:00-18:30)。
影响电镀层厚度的因素
电镀过程的实质是金属离子还原为金属晶体而组成镀层的过程,因此,影响镀层厚度的因素也就是影响电结晶过程的因素。
从电化学的角度,法拉第定律和电极电位方程都可以作为分析影响镀层厚度因素的依据。
首先,根据法拉第定律,金属离子在电极还原为金属的多少与通电量成正比,因此,电流是影响镀层厚度的重要因素,具体到电镀工艺中,就是电流密度的影响,电流密度高,镀层沉积的速度也高。
当然电镀时间也是决定镀层厚度的重要因素,显然,一般情况下,时间和电流密度都是与镀层厚度成正比关系的。
除了电流密度和时间,温度、主盐浓度、阳极面积、镀液搅拌等,都会对镀层的厚度产生影响,但是分析起来,温度、主盐浓度、阳极面积、镀液搅拌都是通过影响电流密度的方式来影响镀层厚度的。
温度高,电流密度就可以提高,同样搅拌镀液也可以提高电流密度而有利于增加镀层厚。
保持阳极面积对保持正常的电流分布和阳极的正常溶解很重要,从而对镀层厚度有直接影响。
而主盐浓度只有在正常范围,才能允许电镀在正常的电流密度范围内工作。