关于铝合金材料的螺纹加工的毛刺及铝屑的原理及解决方案
铝合金锯片切割有毛刺处理方法

铝合金锯片切割有毛刺解决方法铝合金锯片切割之所以出现毛刺,其实造成这个问题的原因有很多,比如锯片的齿数与切割材料不匹配,精度要求没达标导致锯片平整度不够,切出来噪音大或者有异响,再比如齿磨的角度精度不对,锯齿的同心度不对,向心角不对从而影响光洁度等等,这些原因都有可能都有可能造成铝合金锯片在切割时出现毛刺。
那么如何分析铝合金锯片切割毛刺引起的原因,以及相应的处理方法呢?丰金锐刀具有着17年锯片研发生产经验,服务铝加工各大行业客户达到3000多家,下面为大家总结一下,不同原因引起的铝合金锯片毛刺解决方法。
1、锯片问题引起的毛刺:A、锯片齿数不对:如果是锯片齿数不对造成锯切毛刺,可以根据材料的厚度和要求,让锯片推荐合作的齿数,材料厚的相对齿数稀一些,材料薄的相对齿数密一些。
齿数选择对了,自然铝屑排屑通畅,毛刺问题出现的概率也小了。
B、锯片钝了:意思就是锯片不锋利,需要修磨了。
锯片在使用一段时间之后,会出现毛刺也有可能是锯片钝了,丰金锐刀具建议把锯片发给专业的锯片厂家进行修磨就可以解决这个问题了。
C、锯片质量问题:锯片角度精度,锯齿同心度,向心度等问题造成的锯切毛刺,像这种问题都是专业性比较高的,丰金锐刀具就是使用专用的仪器来给客户进行检测排查,然后再从根本上去帮客户解决这个问题。
所以在选择锯片厂家的时候,要慎重了,尽量选生产规模大一些,行业经验比较丰富的锯片厂家,这样锯片的质量相对会有保障一些。
2、锯切设备问题引起的毛刺:A、设备主轴精度不高:给设备主轴精度进行打表,如果跳动在5个丝以上,说明主轴跳动太大,会引起锯片偏摆,晃动,锯切不稳定,导致锯切毛刺。
这时候就需要更换设备主轴了,主轴的精度最好在1-3丝以内比较好,锯片锯切会相对稳定一些。
这个涉及到设备精度的问题,一般的锯片厂家也很少会帮客户考虑到这个问题,像丰金锐刀具是可以免费提供这方面的技术服务和支持,并且在设备问题造成的锯片毛刺问题方面有着丰富的经验。
发动机缸盖有加工毛刺原因分析及解决
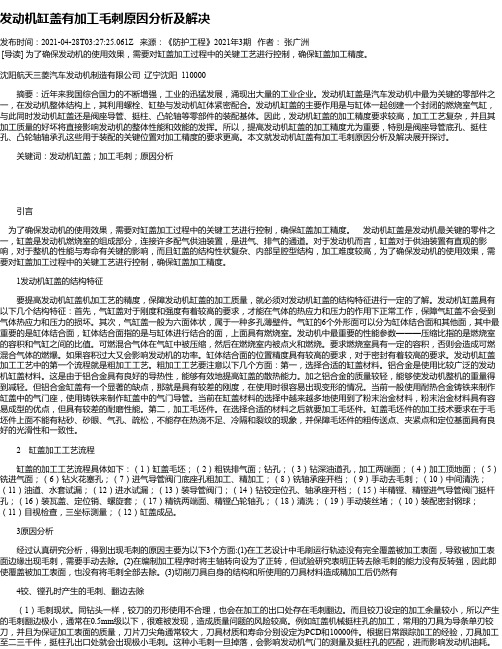
发动机缸盖有加工毛刺原因分析及解决发布时间:2021-04-28T03:27:25.061Z 来源:《防护工程》2021年3期作者:张广洲[导读] 为了确保发动机的使用效果,需要对缸盖加工过程中的关键工艺进行控制,确保缸盖加工精度。
沈阳航天三菱汽车发动机制造有限公司辽宁沈阳 110000摘要:近年来我国综合国力的不断增强,工业的迅猛发展,涌现出大量的工业企业。
发动机缸盖是汽车发动机中最为关键的零部件之一,在发动机整体结构上,其利用螺栓、缸垫与发动机缸体紧密配合。
发动机缸盖的主要作用是与缸体一起创建一个封闭的燃烧室气缸,与此同时发动机缸盖还是阀座导管、挺柱、凸轮轴等零部件的装配基体。
因此,发动机缸盖的加工精度要求较高,加工工艺复杂,并且其加工质量的好坏将直接影响发动机的整体性能和效能的发挥。
所以,提高发动机缸盖的加工精度尤为重要,特别是阀座导管底孔、挺柱孔、凸轮轴轴承孔这些用于装配的关键位置对加工精度的要求更高。
本文就发动机缸盖有加工毛刺原因分析及解决展开探讨。
关键词:发动机缸盖;加工毛刺;原因分析引言为了确保发动机的使用效果,需要对缸盖加工过程中的关键工艺进行控制,确保缸盖加工精度。
发动机缸盖是发动机最关键的零件之一,缸盖是发动机燃烧室的组成部分,连接许多配气供油装置,是进气、排气的通道。
对于发动机而言,缸盖对于供油装置有直观的影响,对于整机的性能与寿命有关键的影响,而且缸盖的结构性状复杂、内部呈腔型结构,加工难度较高,为了确保发动机的使用效果,需要对缸盖加工过程中的关键工艺进行控制,确保缸盖加工精度。
1发动机缸盖的结构特征要提高发动机缸盖机加工艺的精度,保障发动机缸盖的加工质量,就必须对发动机缸盖的结构特征进行一定的了解。
发动机缸盖具有以下几个结构特征:首先,气缸盖对于刚度和强度有着较高的要求,才能在气体的热应力和压力的作用下正常工作,保障气缸盖不会受到气体热应力和压力的损坏。
其次,气缸盖一般为六面体状,属于一种多孔薄壁件。
铝合金带材切边铝屑产生原因
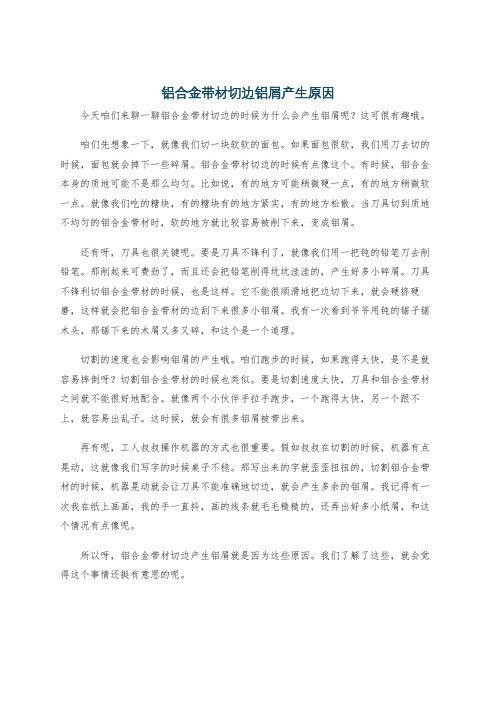
铝合金带材切边铝屑产生原因今天咱们来聊一聊铝合金带材切边的时候为什么会产生铝屑呢?这可很有趣哦。
咱们先想象一下,就像我们切一块软软的面包。
如果面包很软,我们用刀去切的时候,面包就会掉下一些碎屑。
铝合金带材切边的时候有点像这个。
有时候,铝合金本身的质地可能不是那么均匀。
比如说,有的地方可能稍微硬一点,有的地方稍微软一点。
就像我们吃的糖块,有的糖块有的地方紧实,有的地方松散。
当刀具切到质地不均匀的铝合金带材时,软的地方就比较容易被削下来,变成铝屑。
还有呀,刀具也很关键呢。
要是刀具不锋利了,就像我们用一把钝的铅笔刀去削铅笔。
那削起来可费劲了,而且还会把铅笔削得坑坑洼洼的,产生好多小碎屑。
刀具不锋利切铝合金带材的时候,也是这样。
它不能很顺滑地把边切下来,就会硬挤硬磨,这样就会把铝合金带材的边刮下来很多小铝屑。
我有一次看到爷爷用钝的锯子锯木头,那锯下来的木屑又多又碎,和这个是一个道理。
切割的速度也会影响铝屑的产生哦。
咱们跑步的时候,如果跑得太快,是不是就容易摔倒呀?切割铝合金带材的时候也类似。
要是切割速度太快,刀具和铝合金带材之间就不能很好地配合。
就像两个小伙伴手拉手跑步,一个跑得太快,另一个跟不上,就容易出乱子。
这时候,就会有很多铝屑被带出来。
再有呢,工人叔叔操作机器的方式也很重要。
假如叔叔在切割的时候,机器有点晃动,这就像我们写字的时候桌子不稳。
那写出来的字就歪歪扭扭的,切割铝合金带材的时候,机器晃动就会让刀具不能准确地切边,就会产生多余的铝屑。
我记得有一次我在纸上画画,我的手一直抖,画的线条就毛毛糙糙的,还弄出好多小纸屑,和这个情况有点像呢。
所以呀,铝合金带材切边产生铝屑就是因为这些原因。
我们了解了这些,就会觉得这个事情还挺有意思的呢。
铝型材表面颗粒状毛刺的形成原因
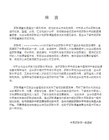
由于高温铸造,铸造速度快,冷却强度大,造成合金中的β相AlFeSi不能及时转变为球状α相AlFeSi,由于β相AlFeSi在合金中呈现针状组织,硬度高、塑性差,抗拉强度很低,在高温挤压时不仅会诱发挤压裂纹,而且会产生颗粒状毛刺,这种毛刺不易清理,手感强烈,颗粒常伴随有蝌蚪状拖尾,在金相显微镜下观察,呈现灰褐色,成分中富含铁元素。
二.模具的影响
在挤压生产中,模具是在高温高压的状态下工作的,受压力和温度的影响,模具产生弹性变形。模具工作带由开始平行于挤压方向,受到压力后,工作带变形成为喇叭状,只有工作带的刃口部分接触型材形成的粘铝,类似于车刀的刀屑瘤。在粘铝的形成过程中,不断有颗粒被型材带出,粘附在型材表面上,造成了"吸附颗粒"。随着粘铝的不断增大,模具产生瞬间回弹,会形成型材的表面粗糙、亮条、型材撕裂、堵模等问题。模具的粘铝现象见图1。我们现在使用的挤压模具基本是平面模,在铸棒不剥皮的情况下,铸棒表面及内在的杂质堆积在模具内金属流动的死区,随着挤压铸棒的推进及挤压根数的增多,死区的杂质也在不断的变化,有一部分被正常流动的金属带出,堆积在工作带变形后的空间内。
有的被型材拉脱,形成了颗粒状毛刺。因此,模具是造成颗粒状毛刺的关键因素。另外工模具表面的粗糙度越高、工作带表面的硬度越低,也是造成粘铝,形成颗粒状毛刺原因之一。
三.挤压工艺的影响
挤压中发现,挤压工艺参数的选择正确与否也是影响颗粒状毛刺的重要因素。经过现场观察,挤压温度、挤压速度过快颗粒毛刺就越多,原因温度高、速度快,型材流动速度增加模具变形的程度增加,金属的流动加快,金属的变形抗力相对减弱,更易形成粘铝现象;对大的挤压系数来说,金属的变形抗力相对增加了,死区相对增大,提高了形成粘铝的条件,形成"吸附颗粒"的概率增加;铸棒加热温度与模具温度之差过大,也易造成颗粒状毛刺问题。
丝锥加工铝合金磨损过快的原因
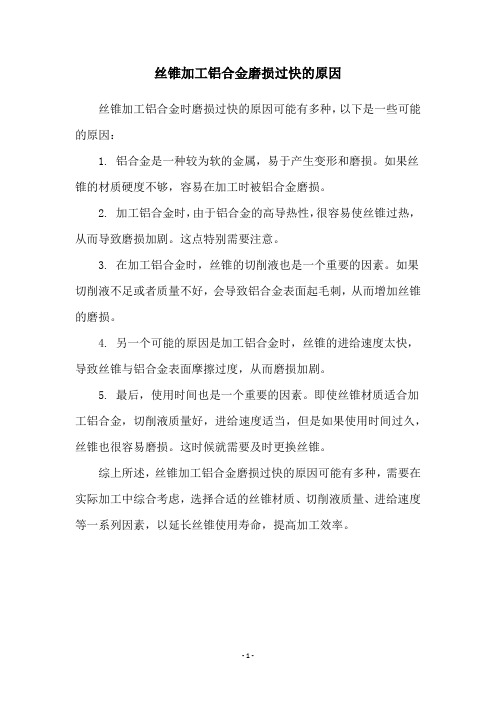
丝锥加工铝合金磨损过快的原因
丝锥加工铝合金时磨损过快的原因可能有多种,以下是一些可能的原因:
1. 铝合金是一种较为软的金属,易于产生变形和磨损。
如果丝锥的材质硬度不够,容易在加工时被铝合金磨损。
2. 加工铝合金时,由于铝合金的高导热性,很容易使丝锥过热,从而导致磨损加剧。
这点特别需要注意。
3. 在加工铝合金时,丝锥的切削液也是一个重要的因素。
如果切削液不足或者质量不好,会导致铝合金表面起毛刺,从而增加丝锥的磨损。
4. 另一个可能的原因是加工铝合金时,丝锥的进给速度太快,导致丝锥与铝合金表面摩擦过度,从而磨损加剧。
5. 最后,使用时间也是一个重要的因素。
即使丝锥材质适合加工铝合金,切削液质量好,进给速度适当,但是如果使用时间过久,丝锥也很容易磨损。
这时候就需要及时更换丝锥。
综上所述,丝锥加工铝合金磨损过快的原因可能有多种,需要在实际加工中综合考虑,选择合适的丝锥材质、切削液质量、进给速度等一系列因素,以延长丝锥使用寿命,提高加工效率。
- 1 -。
铝型材挤压工艺造成毛刺震痕解决方法

毛刺和震痕是在铝型材挤压加工中经常会出现的两种缺陷。
造成毛刺和震痕的原因有很多种,今天,我们就来一起研究挤压工艺对毛刺和震痕产生有什么样的影响,以及怎样解决这个问题。
挤压工艺对产生毛刺和震痕的影响:在挤压铝型材时,粘铝是造成毛刺和震痕的主要原因。
如果金属液流的温度过高、流动的速度过快,就会导致模具变形的程度增加,这样容易形成粘铝现象。
而且,这样还会使铝型材的变形抗力相对增加,从而在模具内腔的金属死区内更容易形成粘铝。
另外,如果铸棒的温度、模具的温度、盛锭筒的温度三者之间相差过大,也容易产生粘铝问题。
在模具投入生产前,一定要使用指定的模垫或专用垫进行保护。
同时还要特别注意,模垫、专用垫和模具之间的配合是否存在间隙,是否有撞击位、裂纹以及由于退火而产生的凹痕等。
如果某一个工件的端面不平,在挤压生产过程中,就会给模具的弹性变形留下空间。
挤压工艺造成毛刺和震痕的解决方法:首先,要想解决问题,就必须及时发现问题。
这就要求在挤压机出口处按装白色灯光,以便“明察秋毫”,及时观察到“毛刺”的产生情况。
然后,就是要根据“毛刺”问题的实时情况,以及根据铝型材的挤压系数、型材断面情况、模具情况、设备情况等,选择最合适的挤压温度、铸棒加热温度、模具温度以及挤压速度,并在生产过程中,不断对这些参数进行调整。
随着一次上机生产棒数量的增加,工作带的温度会上升,这样会导致铝水与工作带的摩擦加剧,使工作带硬度下降,表面变得粗糙,积铝越来越多,从而形成毛刺和震痕。
因此,对一次上机生产的铸棒数量进行限制时非常有必要的。
挤压铝型材的操作人员应在加工开始前,对模垫、专用垫、模具之间是否存在间隙进行检查。
如果存在间隙,可以采取磨平的方法加以解决。
如果磨掉的量过大,模垫和专用垫不能立即投入生产,必须要进行加温后,再重新投入生产。
模具的挤压中心位核挤压杆的位置一定要正。
假如模具中心位不正,棒皮就容易进入模具内;假如挤压杆的位置不正,盛锭筒的筒壁会把本应倒流的杂质送入模具。
干货,螺纹加工常见问题及解决方法,车工必备

扎刀1、主要原因(1)车刀的前角太大,机床X轴丝杆间隙较大;(2)车刀安装得过高或过低;(3)工件装夹不牢;(4)车刀磨损过大;(5)切削用量太大。
2、解决方法(1)减小车刀前角,维修机床调整X 轴的丝杆间隙,利用数控车床的丝杆间隙自动补偿功能补偿机床X 轴丝杆间隙。
(2)车刀安装得过高或过低:过高,则吃刀到一定深度时,车刀的后刀面顶住工件,增大摩擦力,甚至把工件顶弯,造成扎刀现象;过低,则切屑不易排出,车刀径向力的方向是工件中心,加上横进丝杠与螺母间隙过大,致使吃刀深度不断自动趋向加深,从而把工件抬起,出现扎刀。
此时,应及时调整车刀高度,使其刀尖与工件的轴线等高(可利用尾座顶尖对刀)。
在粗车和半精车时,刀尖位置比工件的中心高出1%D左右(D表示被加工工件直径)。
(3)工件装夹不牢:工件本身的刚性不能承受车削时的切削力,因而产生过大的挠度,改变了车刀与工件的中心高度(工件被抬高了),形成切削深度突增,出现扎刀,此时应把工件装夹牢固,可使用尾座顶尖等,以增加工件刚性。
(4)车刀磨损过大:引起切削力增大,顶弯工件,出现扎刀。
此时应对车刀加以修磨。
(5)切削用量(主要是背吃刀量和切削速度)太大:根据工件5 导程大小和工件刚性选择合理的切削用量。
乱扣1、故障现象当丝杠转一转时,工件未转过整数转而造成的。
2、主要原因(1)机床主轴编码器同步传动皮带磨损,检测不到主轴的同步真实转速;(2)编制输入主机的程序不正确;X轴或Y轴丝杆磨损。
3、解决方法(1)主轴编码器同步皮带磨损由于数控车床车削螺纹时,主轴与车刀的运动关系是由机床主机信息处理中心发出的指令来控制的,车削螺纹时,主轴转速恒定不变,X 或Y 轴可以根据工件导程大小和主轴转速来调整移动速度,所以中心必须检测到主轴同步真实转速,以发出正确指令控制X 或Y 轴正确移动。
如果系统检测不到主轴的真实转速,在实际车削时会发出不同的指令给X或Y,那么这时主轴转一转,刀具移动的距离就不是一个导程,第二刀车削时螺纹就会乱扣。
数控外螺纹加工及毛刺去除
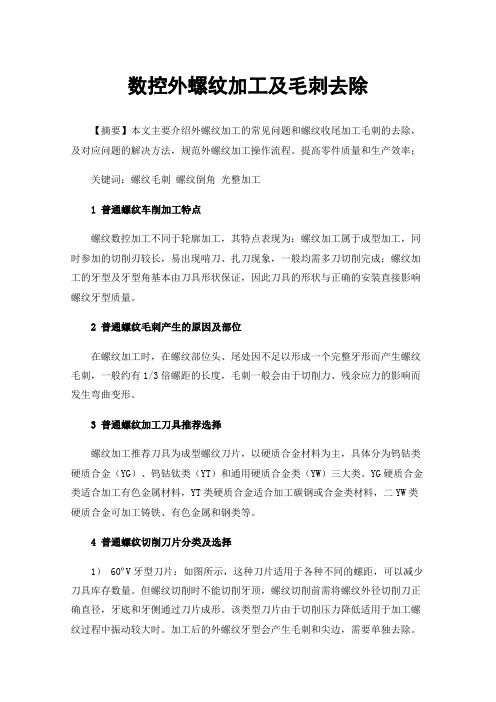
数控外螺纹加工及毛刺去除【摘要】本文主要介绍外螺纹加工的常见问题和螺纹收尾加工毛刺的去除,及对应问题的解决方法,规范外螺纹加工操作流程。
提高零件质量和生产效率;关键词:螺纹毛刺螺纹倒角光整加工1普通螺纹车削加工特点螺纹数控加工不同于轮廓加工,其特点表现为:螺纹加工属于成型加工,同时参加的切削刃较长,易出现啃刀、扎刀现象,一般均需多刀切削完成;螺纹加工的牙型及牙型角基本由刀具形状保证,因此刀具的形状与正确的安装直接影响螺纹牙型质量。
2普通螺纹毛刺产生的原因及部位在螺纹加工时,在螺纹部位头、尾处因不足以形成一个完整牙形而产生螺纹毛刺,一般约有1/3倍螺距的长度,毛刺一般会由于切削力、残余应力的影响而发生弯曲变形。
3普通螺纹加工刀具推荐选择螺纹加工推荐刀具为成型螺纹刀片,以硬质合金材料为主,具体分为钨钴类硬质合金(YG)、钨钴钛类(YT)和通用硬质合金类(YW)三大类。
YG硬质合金类适合加工有色金属材料,YT类硬质合金适合加工碳钢或合金类材料,二YW类硬质合金可加工铸铁、有色金属和钢类等。
4普通螺纹切削刀片分类及选择1)60ºV牙型刀片:如图所示,这种刀片适用于各种不同的螺距,可以减少刀具库存数量。
但螺纹切削时不能切削牙顶,螺纹切削前需将螺纹外径切削刀正确直径,牙底和牙侧通过刀片成形。
该类型刀片由于切削压力降低适用于加工螺纹过程中振动较大时。
加工后的外螺纹牙型会产生毛刺和尖边,需要单独去除。
2)全牙型刀片:螺纹切削时可切削处包括牙顶在内的整个螺纹牙型,现场也称为为带修光刃刀片。
使用这种刀片切制外螺纹时能够很好的控制螺纹的几何特性。
因为牙底与牙顶之间的距离能够很好的控制,随着刀片同时加工出牙底和牙顶,进而可去除螺纹牙形毛刺,但这种刀片只能切削一种螺距且切削压力较大。
全牙型刀片的修光刃作用为去除螺纹尖边形成的毛刺及加工过程中产生的积屑瘤,起到螺纹尖边毛刺的去除作用。
加工时推荐选用标准带有螺纹修光刃刀片。
铝合金型材表面金属豆、毛刺、三角口产生的原因及解决办法
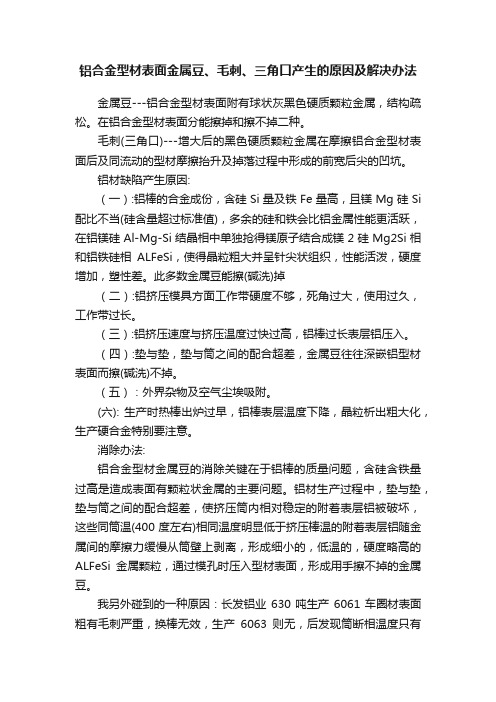
铝合金型材表面金属豆、毛刺、三角口产生的原因及解决办法金属豆---铝合金型材表面附有球状灰黑色硬质颗粒金属,结构疏松。
在铝合金型材表面分能擦掉和擦不掉二种。
毛刺(三角口)---增大后的黑色硬质颗粒金属在摩擦铝合金型材表面后及同流动的型材摩擦抬升及掉落过程中形成的前宽后尖的凹坑。
铝材缺陷产生原因:(一):铝棒的合金成份,含硅Si量及铁Fe量高,且镁Mg硅Si 配比不当(硅含量超过标准值),多余的硅和铁会比铝金属性能更活跃,在铝镁硅Al-Mg-Si结晶相中单独抢得镁原子结合成镁2硅Mg2Si相和铝铁硅相ALFeSi,使得晶粒粗大并呈针尖状组织,性能活泼,硬度增加,塑性差。
此多数金属豆能擦(碱洗)掉(二):铝挤压模具方面工作带硬度不够,死角过大,使用过久,工作带过长。
(三):铝挤压速度与挤压温度过快过高,铝棒过长表层铝压入。
(四):垫与垫,垫与筒之间的配合超差,金属豆往往深嵌铝型材表面而擦(碱洗)不掉。
(五):外界杂物及空气尘埃吸附。
(六): 生产时热棒出炉过早,铝棒表层温度下降,晶粒析出粗大化,生产硬合金特别要注意。
消除办法:铝合金型材金属豆的消除关键在于铝棒的质量问题,含硅含铁量过高是造成表面有颗粒状金属的主要问题。
铝材生产过程中,垫与垫,垫与筒之间的配合超差,使挤压筒内相对稳定的附着表层铝被破坏,这些同筒温(400度左右)相同温度明显低于挤压棒温的附着表层铝随金属间的摩擦力缓慢从筒壁上剥离,形成细小的,低温的,硬度略高的ALFeSi金属颗粒,通过模孔时压入型材表面,形成用手擦不掉的金属豆。
我另外碰到的一种原因:长发铝业630吨生产6061车圈材表面粗有毛刺严重,换棒无效,生产6063则无,后发现筒断相温度只有365度,修好后390度挤压型材毛刺消失。
原因是6061车圈材挤速慢,棒(520度)外层与筒壁传热冷却过程中镁2硅Mg2Si相和铝铁硅相ALFeSi析出集中在铝棒表层,经死区在型材表面反映出来。
金属切削毛刺形成机理及去除方法综述
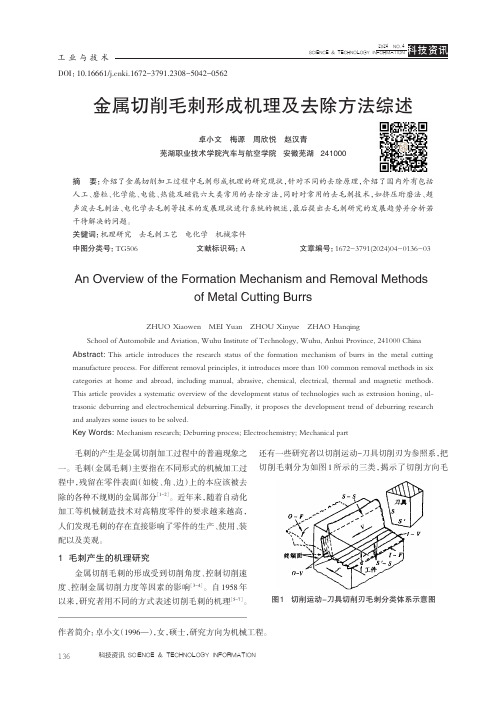
金属切削毛刺形成机理及去除方法综述卓小文 梅源 周欣悦 赵汉青芜湖职业技术学院汽车与航空学院 安徽芜湖 241000摘要:介绍了金属切削加工过程中毛刺形成机理的研究现状,针对不同的去除原理,介绍了国内外有包括人工、磨粒、化学能、电能、热能及磁能六大类常用的去除方法,同时对常用的去毛刺技术,如挤压珩磨法、超声波去毛刺法、电化学去毛刺等技术的发展现状进行系统的概述,最后提出去毛刺研究的发展趋势并分析若干待解决的问题。
关键词:机理研究 去毛刺工艺 电化学 机械零件中图分类号:TG506文献标识码:A 文章编号:1672-3791(2024)04-0136-03An Overview of the Formation Mechanism and Removal Methodsof Metal Cutting BurrsZHUO Xiaowen MEI Yuan ZHOU Xinyue ZHAO Hanqing School of Automobile and Aviation, Wuhu Institute of Technology, Wuhu, Anhui Province, 241000 China Abstract:This article introduces the research status of the formation mechanism of burrs in the metal cutting manufacture process. For different removal principles, it introduces more than 100 common removal methods in six categories at home and abroad, including manual, abrasive, chemical, electrical, thermal and magnetic methods. This article provides a systematic overview of the development status of technologies such as extrusion honing, ul⁃trasonic deburring and electrochemical deburring.Finally, it proposes the development trend of deburring research and analyzes some issues to be solved.Key Words: Mechanism research; Deburring process; Electrochemistry; Mechanical part毛刺的产生是金属切削加工过程中的普遍现象之一。
铝材挤压加工毛刺的产生原因及解决方法
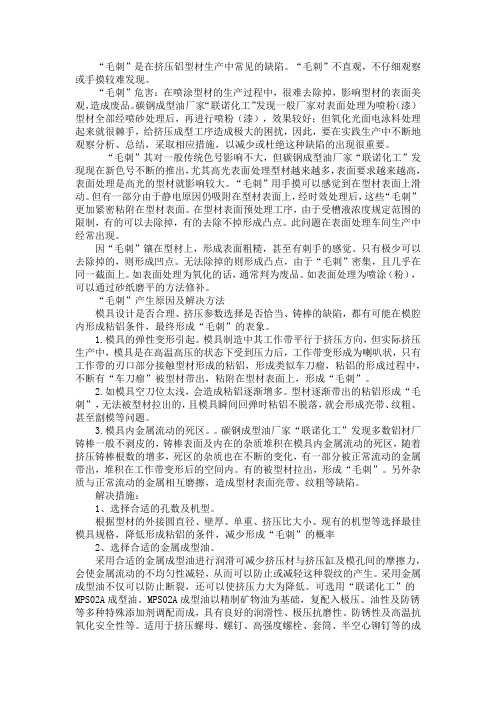
“毛刺”是在挤压铝型材生产中常见的缺陷。
“毛刺”不直观,不仔细观察或手摸较难发现。
“毛刺”危害:在喷涂型材的生产过程中,很难去除掉,影响型材的表面美观,造成废品。
碳钢成型油厂家“联诺化工”发现一般厂家对表面处理为喷粉(漆)型材全部经喷砂处理后,再进行喷粉(漆),效果较好;但氧化光面电泳料处理起来就很棘手,给挤压成型工序造成极大的困扰,因此,要在实践生产中不断地观察分析、总结,采取相应措施,以减少或杜绝这种缺陷的出现很重要。
“毛刺”其对一般传统色号影响不大,但碳钢成型油厂家“联诺化工”发现现在新色号不断的推出,尤其高光表面处理型材越来越多,表面要求越来越高,表面处理是高光的型材就影响较大。
“毛刺”用手摸可以感觉到在型材表面上滑动。
但有一部分由于静电原因仍吸附在型材表面上,经时效处理后,这些“毛刺”更加紧密粘附在型材表面。
在型材表面预处理工序,由于受槽液浓度规定范围的限制,有的可以去除掉,有的去除不掉形成凸点。
此问题在表面处理车间生产中经常出现。
因“毛刺”镶在型材上,形成表面粗糙,甚至有刺手的感觉。
只有极少可以去除掉的,则形成凹点。
无法除掉的则形成凸点,由于“毛刺”密集,且几乎在同一截面上。
如表面处理为氧化的话,通常判为废品。
如表面处理为喷涂(粉),可以通过砂纸磨平的方法修补。
“毛刺”产生原因及解决方法模具设计是否合理、挤压参数选择是否恰当、铸棒的缺陷,都有可能在模腔内形成粘铝条件,最终形成“毛刺”的表象。
1.模具的弹性变形引起。
模具制造中其工作带平行于挤压方向,但实际挤压生产中,模具是在高温高压的状态下受到压力后,工作带变形成为喇叭状,只有工作带的刃口部分接触型材形成的粘铝,形成类似车刀瘤,粘铝的形成过程中,不断有“车刀瘤”被型材带出,粘附在型材表面上,形成“毛刺”。
2.如模具空刀位太浅,会造成粘铝逐渐增多。
型材逐渐带出的粘铝形成“毛刺”,无法被型材拉出的,且模具瞬间回弹时粘铝不脱落,就会形成亮带、纹粗、甚至劏模等问题。
零件毛刺的产生和改善

【干货】零件毛刺的产生和改善01什么是毛刺毛刺的定义是指加工金属或树脂等材料时,产生的突出物,通常在镜像过程中或过程之后产生。
常用毛刺的高度、厚度和长度来表示。
在本文中,我们使用毛刺厚度来表示毛刺尺寸。
毛刺如果不去除,极有可能会导致零件无法正常运作。
至于外观方面,毛刺也会划伤其他产品,组装过程中也会出现测量问题,以及操作者安全问题。
02毛刺的大小和方向毛刺的大小和方向取决于工艺。
例如在金属加工工艺中,表面的外围会产生水平毛刺。
在这种情况下,刀具入口侧的毛刺尺寸与刀具的另一侧不同:在入口侧,毛刺往往较小;在出口侧,毛刺往往较大。
入口侧产生的毛刺称为初始毛刺,末端产生的毛刺称为翻边毛刺。
这种机制在钻孔过程中也是一样,在钻孔过程中,入口侧产生垂直毛刺,产生小的初始毛刺,在外面产生大的翻边毛刺。
03如何测量毛刺的尺寸测量毛刺尺寸的一些常用方法是使用千分尺和卡尺或数码显微镜。
使用表面粗糙度测试仪测量毛刺尺寸的方式与测量表面粗糙度相同,但这种方法只能测量非常小的毛刺。
选择合适的测量工具很重要,有很多方法可以测量毛刺大小或边缘状况,因此在选择工具之前,最好先决定如何评估毛刺或形状。
04如何检查已去除的毛刺2018年开始,我们对300多家加工企业进行的一项调查显示:61%的加工企业会通过手指触摸或使用放大镜目视检查的方式进行检查;此外还调查了询问操作员如何量化“去除所有毛刺”,其中34%表示低于10-50μm的毛刺是可以接受的,26%表示介于50μm-0.1mm之间。
05如何最小化毛刺尺寸如何控制毛刺方向最小化毛刺尺寸很重要,因为毛刺越大,需要去除它们的刀具就越少。
毛刺大小是由边缘的角度引起的,角度对毛刺大小至关重要。
大多数情况下,刃角为90度且锋利时,毛刺越大;反之,刃角越小,毛刺越小。
如果刃角精确到150度,则不会产生毛刺。
有时可能会遇到非常大的毛刺,这时建议改变切削刀具的刃角以减小毛刺尺寸。
至于边角毛刺差异,有时改变模具的形状并不容易,可以通过在切削条件上做一些改变来尝试。
关于铝合金材料的螺纹加工的毛刺及铝屑的原理及解决方案

关于铝合金材料的内螺纹加工的方法及产生毛刺及铝屑的解决方案内螺纹加工有车削螺纹、攻丝、挤压、铣削,车削、攻丝加工是传统加工工艺,挤压螺纹、铣削螺纹是现代制造业中的先进技术。
挤压内螺纹主要适用延伸率大于10%钢材的薄板及铝合金材料,钢材薄板厚度一般在3mm。
铣削螺纹是用螺纹销在数控机床通过圆弧插补加工成形的螺纹。
由于铣削螺纹是通过刀具的侧刃铣削,刀具会受到侧向力作用,如果材料较硬,会产生让刀现象,导致螺纹上下大小不一。
所以小直径(直径20以内)的螺纹铣削一般不适用钢材,一般适用于铝合金材料。
挤压螺纹时原理是通过材料塑性变形形成的螺纹,用挤压丝锥挤压螺纹时,不会产生切削,也就是说没有把材料切除,所以不会切削物产生。
而切削丝锥加攻螺纹是通过吧材料切除,形成螺纹,所以会产生切削物。
挤压螺纹的加工预钻孔直径和切削丝锥不一样,切削丝锥的加工螺纹时的预钻孔直径就是螺纹的小径,挤压丝锥的预钻孔直径要比螺纹的小径大,具体公式是:预钻孔直径=D-0.2P-0.00403Pf1+0.0127n ,D:标准大径,P:螺距,f1:螺纹接触高度比(%),n:RH(OSG标准,此标准能与国标对应)的精度号,例如:M10×1.5RH7P2级内螺纹,螺纹接触高度比为90%,预钻孔直径=10-0.2×1.5-0.00403×1.5×90+0.0127×7=9.24铣削螺纹的预钻孔是和切削丝锥的螺纹预钻孔直径一样,其原理螺纹铣刀在数控机床走一个圆弧插补,刀具的进一个螺距的深度。
切削丝锥的切削齿是按照螺距螺旋的,在丝锥的每个截面圆上是按照一个螺距在上升的。
螺纹铣刀的切削齿刃不是按照螺距螺旋的,每个齿形在刀具的一个截面圆上的。
金属切削时,由于材料有延伸性,所以被切削材料容易在被切处的棱边、孔等的相交线处形成毛刺。
铝合金材料的延伸性好,所以在加工铝合金材料是更容易产生毛刺,特别是在加工铝合金材料的内螺纹时,会在螺纹的牙尖形成毛刺和铝屑。
金属加工中的毛刺问题

金属切削加工中的毛刺问题王春梅[摘要]毛刺是金属切削加工中产生的必然现象,它直接影响产品的质量,应从产品结构设计、工艺设计、刀具设计和生产管理等方面对毛刺加以控制。
关键词:金属切削加工毛刺解决措施1.引言长期以来,毛刺现象没有引起人们足够的重视,以至毛刺悄然影响着产品的质量。
如在进行挖掘机液压系统某个零件的设计时,在技术要求中写上“去除各孔交、贯处毛刺”的字样,但有人却以加工难度大、检测不方便、增加加工成本等为由提出质疑。
工人们也常常嫌麻烦忽视去毛刺工序,部分设计人员对此也不太重视,在图样上漏写“去毛刺”或“棱边倒钝”等。
其实,去毛刺是一个非常重要的工序,在液压系统中,零件上的毛刺一旦脱落进入元件时就会卡死滑阀,损伤零件表面,割破软管或堵塞出液口等从而影响主机性能,甚至停机。
毛刺如果掉在定位基准面上会影响加工精度;毛刺还会容易划伤工人造成不安全因素影响装配质量以及零件寿命,如何看待和控制金属切削加工中的毛刺问题,这将直接关系到产品的质量,这里就此发表一点看法。
2.对毛刺问题的重新认识毛刺,是指在金属(包括热加工和冷加工)切割加工过程中在切削力作用下,产生晶粒剪切滑移、塑性变形使材料挤压撕裂,导致工件表面过渡处出现各种尖角、毛边等不规则的金属部分。
这里主要指的是在冷加工,即金属切削加工中的毛刺问题。
毛刺是金属切削加工中产生的普遍现象之一,也是金属切削理论研究中迄今为止尚未解决好的两大难题(毛刺的生成与控制,切屑的处理与控制)之一。
大家都知道金属切削加工是指从工件上切除多于金属材料的加工方法。
不同的切削方法选用的刀具不同(常用的刀具有车刀、刨刀、钻头、齿轮刀具等,常见的切削加工方法有车削、刨削、钻削、磨削、铣削、齿轮加工等),切削加工虽有多种不同的方式但在很多方面(如切削时的运动、切削刀具以及切削过程的实质等)度有着共同的规律,采用不同的切削手段,毛刺的形成机理也不仅相同,毛刺的形状也不同。
所以毛刺对工件质量的影响程度也不同,毛刺直接影响被加工工件的尺寸精度、形位精度和表面粗糙度。
铝管旋槽缺陷与解决方案

铝管旋槽缺陷与解决方案一、铝管旋槽常见缺陷。
1. 槽深不均匀。
这槽深不均匀可就像人脸上的麻子,这儿深那儿浅的。
有时候是因为旋槽刀具在加工的时候磨损得不均匀。
就好比你拿个不太锋利的铅笔写字,有的笔画粗有的笔画细。
还有可能是铝管在旋槽的时候固定得不好,它在那儿晃悠呢,刀具就没法均匀地切出槽来。
2. 槽壁粗糙度大。
这槽壁粗糙得就像没打磨过的石头表面。
一个原因呢,是刀具的转速不合适。
转速太快或者太慢都不行,就像你扫地,扫帚挥动的速度得刚刚好才能扫得干净。
如果太快,就像一阵狂风乱扫,扫不干净还把灰尘扬得到处都是;太慢呢,就像小蚂蚁慢慢爬,根本扫不动。
另外,刀具的切削刃如果不够锋利,那切出来的槽壁肯定是毛毛糙糙的。
3. 槽形不规整。
槽形不规整就像你画个圆,结果画成了个歪歪扭扭的椭圆。
这可能是由于旋槽设备的精度不够。
比如说设备的导轨有点歪,那刀具沿着歪的导轨走,切出来的槽肯定也是歪的。
而且如果在旋槽过程中受到了额外的振动干扰,就像有人在旁边敲锣打鼓一样,那槽形也会变得乱七八糟的。
4. 槽内有毛刺。
槽内有毛刺就像衣服上沾了刺儿球,特别讨厌。
这主要是因为刀具在切削完之后,没有一个合适的去毛刺工序。
还有可能是刀具在切削的时候,它的排屑不畅,切下来的铝屑就像堵车一样堵在那儿,然后就形成了毛刺。
二、解决方案。
1. 针对槽深不均匀。
首先得定期检查和更换刀具,让刀具一直保持锋利而且磨损均匀。
就像我们要定期换牙刷一样,牙刷用久了就刷不干净牙了。
然后呢,要把铝管固定得稳稳当当的。
可以使用专门的夹具,把铝管紧紧夹住,就像给它戴上了一副紧箍咒,让它在旋槽的时候不能乱动。
2. 针对槽壁粗糙度大。
调整刀具的转速,这个要根据铝管的材质和旋槽的要求来确定。
可以多做几次试验,就像厨师做菜试味道一样,找到最合适的转速。
还有就是要保证刀具的切削刃锋利,可以使用磨刀石之类的工具来磨刀。
而且在旋槽的时候,适当加一些切削液,这样就像给刀具和铝管之间加了润滑油,切起来更顺滑,槽壁也就更光滑了。
铝合金切削加工过程中毛刺形成机理与控制

上海交通大学硕士学位论文铝合金切削加工过程中毛刺形成机理与控制姓名:董洪艳申请学位级别:硕士专业:机械工程指导教师:邵华;张其然20080601BURR FORMATION MECHANISM AND CONTROLIN MILLING OF 2A12 ALUMINUM ALLOYABSTRACTBurr formed during metal cutting process,is harmful to both function and quality of mechanical components. In this thesis, based on FEM analysis and cutting experiment in milling of 2A12(LY12) aluminum-alloy,burr formation mechanism and the impact of cutting parameters on burr dimensions were explored. FEM analysisⅠdemonstrated that when cutting 2A12(LY12) aluminum-alloy ,the type burr was formed in cutting out direction due to chip bending at theⅡend of the work piece and the burr is big ;The type burr is formedⅠdue to the breakage of type burr with further plastic bending at the endof the work piece and the burr is relatively small. FEM analysis and cutting experiment showed that the bigger the depth of cut is,the larger the formed burr is; the increase the cutting velocity decreases the burr dimensions,and the impact of feed rate on burr dimension depends on the machining system. The orthogonal experiments of the two machining system indicated that the optimized cutting conditions of the first machining system are : depth of cut 0.1mm,feed per tooth 0.05mm/z,spindle speed 250m/min and corresponding burr height was about 0.02mm;the optimization cutting conditions of the second machiningsystem are :depth of cut 0.2mm,feed per tooth 0.2mm/z,spindle speed 4000r/min, and corresponding burr height was around 0.01mm. In this thesis machinability of 2A12(LY12) aluminum alloy was further explored. The work is of some practical value to the machining of the material.KEY WORDS:2A12(LY12) aluminum alloy,milling,burr,metal cutting,machinability, FEA上海交通大学学位论文原创性声明本人郑重声明:所呈交的学位论文,是本人在导师的指导下,独立进行研究工作所取得的成果。
制一部(丝攻专案(毛刺改善))

5 追踪确认改善对策效果
6
第3次会议:确认改善对策之可 行性,并针对性检讨再次改进
7 再次改善实施
8
追踪确认再次改善对策实施效 果
计划进度 实际进度
2/252/28
2/283/5
3/53/10
工作分配 全员参与
全员参与
全员参与
全员参与
全员参与Βιβλιοθήκη 全员参与全员参与全员参与
五.原因分析
环
法
人
抽芽底孔孔径太小 攻牙油油品粘度不足
制一部/赵课 制二部/范课
9
由QE和IE负责统计收集100PCS验证产品之攻 牙孔毛刺,依各位置点类分之毛刺现象及比率.
品保部/ 生技部/
下阶段待续-----
需求完成 预计完成 实际完成
2月23日
2/23
2月23日
2/25
2月23日
2/25
无(依现况)
2月3日
2/2
2/2
待定
2月26日
待定 待定 待定
一.专案问题点
各牙孔攻牙后90%毛刺
攻牙前固定孔位80%毛刺
一 .专案问题点
日期 班别 材质 1月3日 B AL 1月22日 A AL 1月23日 B AL 1月13日 A AL
产品 类型 背板类
背板类
背板类
背板类
客户 机种/品名
不良现象
广东 亚一
广东 亚一
广东 亚一
广东 亚一
LED-26 COVER LED-26 COVER LED-26 COVER LED-37 COVER
负责推动设备治具面对策方案措施的执行展开. 负责专案推动之前后制程在在线执行效果与专案 进度执行措施确认,对改善状况作汇总并提交. 负责模具面与设计面对策方案措施的执行展开. 负责专案推动之产品功能及客户标准认定. 负责专案涉及产品制程管制重点的在效执行.
关于铝型材毛刺问题的解决

关于铝型材毛刺问题的解决郑光为(广东兴发集团有限公司,广东佛山528219)毛刺的产生是由于型材出口处的强度小于型材表面与模具定径带的摩擦力而造成局部的撕裂。
要解决此问题主要从提高出口处型材的强度降低型材与模具之间的摩擦力着手。
1 提高出口处型材的强度在同一合金情况下,合金的温度越高,强度越低。
所以降低出口温度可以提高型材出口的强度,可通过以下方式:1.1 降低棒温尽量用较低的棒温挤压.1.2 提高铝棒的塑性,即挤压性能铝棒的塑性越好,挤压的变形力越少,挤压过程的温升越少。
铝棒的塑性主要受合金成份,含渣,含气量,均匀化状态影响,同一条件下,成份越低越好挤,工艺一 定的情况下,含渣含气量主要受原材料的影响,废料越多越差,尤其是氧化皮越多的废料,杂质含量也会使铝棒的塑性降低,有些特别难挤压的模具用全部铝锭做的 棒较好。
1.3 降低挤压速度降低挤压速度是减少毛刺最有效的方法,但会影响产量,最好根据每个型号模具制定合理的速度范围,有些模具要加速以提高产量,有些模具要减速以保证表面质量。
1.4 提高模具的加工精度,合理设计减少铝棒通过模孔的阻力,减少温升,另外同样的型材,采用小一级的棒径的模挤压,降低挤压比(比如:1800T转880T挤压),对减少毛刺相当有效。
2 减少型材与定径带之间的摩擦力(1)提高定径带的表面光洁度。
(2)采用先进的氮化工艺及设备,提高氮化层的硬度和耐磨性。
(3)建立完善的保养制度,每个模挤压到—定数量要重新氮化。
(4)有条件可采用模具通氮冷却。
纵上所述,解决毛刺是一个系统问题,只有熔铸、挤压、模具水平的不断提高,才能逐步减少毛刺的发生。
- 1、下载文档前请自行甄别文档内容的完整性,平台不提供额外的编辑、内容补充、找答案等附加服务。
- 2、"仅部分预览"的文档,不可在线预览部分如存在完整性等问题,可反馈申请退款(可完整预览的文档不适用该条件!)。
- 3、如文档侵犯您的权益,请联系客服反馈,我们会尽快为您处理(人工客服工作时间:9:00-18:30)。
关于铝合金材料的内螺纹加工的方法及产生毛刺及铝屑的解决方案内螺纹加工有车削螺纹、攻丝、挤压、铣削,车削、攻丝加工是传统加工工艺,挤压螺纹、铣削螺纹是现代制造业中的先进技术。
挤压内螺纹主要适用延伸率大于10%钢材的薄板及铝合金材料,钢材薄板厚度一般在3mm。
铣削螺纹是用螺纹销在数控机床通过圆弧插补加工成形的螺纹。
由于铣削螺纹是通过刀具的侧刃铣削,刀具会受到侧向力作用,如果材料较硬,会产生让刀现象,导致螺纹上下大小不一。
所以小直径(直径20以内)的螺纹铣削一般不适用钢材,一般适用于铝合金材料。
挤压螺纹时原理是通过材料塑性变形形成的螺纹,用挤压丝锥挤压螺纹时,不会产生切削,也就是说没有把材料切除,所以不会切削物产生。
而切削丝锥加攻螺纹是通过吧材料切除,形成螺纹,所以会产生切削物。
挤压螺纹的加工预钻孔直径和切削丝锥不一样,切削丝锥的加工螺纹时的预钻孔直径就是螺纹的小径,挤压丝锥的预钻孔直径要比螺纹的小径大,具体公式是:预钻孔直径=D-0.2P-0.00403Pf1+0.0127n ,D:标准大径,P:螺距,f1:螺纹接触高度比(%),n:RH(OSG标准,此标准能与国标对应)的精度号,例如:M10×1.5RH7P2级内螺纹,螺纹接触高度比为90%,预钻孔直径=10-0.2×1.5-0.00403×1.5×90+0.0127×7=9.24
铣削螺纹的预钻孔是和切削丝锥的螺纹预钻孔直径一样,其原理螺纹铣刀在数控机床走一个圆弧插补,刀具的进一个螺距的深度。
切削丝锥的切削齿是按照螺距螺旋的,在丝锥的每个截面圆上是按照一个螺距在上升的。
螺纹铣刀的切削齿刃不是按照螺距螺旋的,每个齿形在刀具的一个截面圆上的。
金属切削时,由于材料有延伸性,所以被切削材料容易在被切处的棱边、孔等的相交线处形成毛刺。
铝合金材料的延伸性好,所以在加工铝合金材料是更容易产生毛刺,特别是在加工铝合金材料的内螺纹时,会在螺纹的牙尖形成毛刺和铝屑。
产生这些毛刺的和铝屑的根本原因是螺纹刀具没有和铝合金材料完全贴合。
由于铝合金内螺纹可以用挤压丝锥加工,挤压螺纹是无切削加工,所以不会产生毛刺和铝屑问题。
有的铝合金螺纹必须要用切削丝锥加工时,当刀具寿命到一定程度是就会产生毛刺,但是刀具还可以使用,要是刀具报废浪费大,制造成本高。
为了解决这种毛刺问题,必须有这样要求:1.由于丝锥制造时小径是砂轮修磨的,小径一般都会比预钻孔直径小,所以会产生毛刺,所以加工铝合金内螺纹要是用切削丝锥时,丝锥必须定做非标,要求丝锥小径按照螺纹精度制造。
2.然后预钻孔小径要和丝锥小径一致。
螺纹铣刀加工螺纹时,要求螺纹铣刀的小径必须与螺纹小径的表面贴合,这样才不会产生毛刺。