工艺点检表
工艺参数点检表

月份:
日期
x 公
司
编号:xx-xx-xx
点检表
26
序号项 目 A01 A02 A03 A04 A05 A06 A07 A08 A09 包装 A10 A11 A12 A13 A14 A15 A16 A17
标准 检验项目 是否齐全 检验标志 是否画线 检验工具 成 检 有铅无铅 是否混用
27
28
29
30
31
1
2
3ห้องสมุดไป่ตู้
4
5
6
7
8
9
10
11
12
13
14
15
16
17
18
19
20
21
22
23
24
25
不合 格次 数
检验方法 是否正确 烘箱温度 125±5℃ 检验工具 标签 合格证 外观 是否完好 有效 是否正确 是否正确 是否平整
每叠数量 是否正确 包装温度 90-120℃
ZG-22-2009《成 品检验记录一览 表》 ZG-26-2009《特 许放行申请单》 ZG-21-2009《产 品出货检验报告 》 ZZ-02-2010《出 库单》 ZG-37-2009《返 工记录表》 印制板生产制作 指示 如实填写 、记录清 晰 如实填写 、记录清 晰 如实填写 、记录清 晰 如实填写 、记录清 晰 如实填写 、记录清 晰 如实填写 、记录清 晰
不 合 格 项 数
点检人/监督人
备注:1、检查有数据的,必须填写数据。没有数据的,合格划“√”表示,不合格用红色笔“×”(主管每日点检2次,每班点检1次,工艺部门每日点检1次,工艺部负责人每周点检一次。在点检过程中出现不合格时按MT/ZG7-2011《操作现场NG反馈处理流程》执行。
生产工艺品质监查表

插灯 3.检查的灯管类别、极性、位号有无出现异常不良? 14 检查
2.是否按照检查的作业标准进行检查?
14
插灯 检查 4.出现异常不良后有无及时进行反馈?
5.有无按照点检表的要求进行记录? 1.PCB板是否平稳地放在承放工装上?
1 2 1 2 1 1 1 3 3 2 2 1 2 1 1 2 1 1 1 2 1 3 3 2 2 2 2 1 1 1 2 1 3
监查结果记录
判定 备注
电源 6.使用烙铁的焊接工艺是否正确? 17 插座 装配 7.是否使用专用的焊锡丝(FLUX1.8 DIA 1.2M/M)及烙铁头?
8.使用工具是否齐全?(海绵、烙铁架、焊丝架、锡渣盒、烙铁承放盒)
3 2 2 2 1 3 2 2 1 1 3 2 1 2 2
印刷 7.是否标识开封日期?解冻时间? 2 锡膏
8.印刷过程中的力度、速度、角度是否符合作业指导书的要求? 9.打开钢网的速度是否合适(3秒钟以上)? 10.印刷好的PCB贴片量是否控制在15分钟内? 11.锡膏的印刷位置锡量等是否正确?《参照锡膏印刷检查指导书》。 12.刮刀是否按规定标识?是否有损坏? 13.钢网是否按规定要求清洗? 1.有无按照《设备日常、定期点检保养记录表》的内容进行保养? 2.贴片机是否按照正常的程序开机关机?
灯板 过波 8 峰焊 3.每次生产前有无按照指导书的要求进行高度和角度的测量?测量 后的 检查 结果是否记录在《灯管高度测量记录表》和《灯管角度抽查表》上 。 4.检查结果有无出现异常的不良?若有及时反馈到组长.
1.盖印的位置、方向、日期及序号是否正确?
2 2 3 1 1 2 2 2 2 2 3 2 2 1 1 2 B-043-A
生产工艺品质监查表
《工艺纪律检查表》
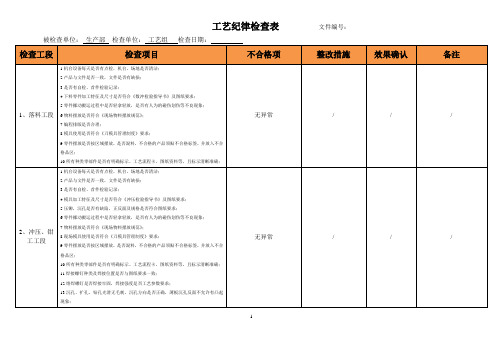
被检查单位:生产部检查单位:工艺组检查日期:
检查工段
检查项目
不合格项
整改措施
效果确认
备注
1、落料工段
1.机台设备每天是否有点检,机台、场地是否清洁;
2.产品与文件是否一致,文件是否有缺损;
3.是否有自检、首件检验记录;
4.下料零件加工特征及尺寸是否符合《数冲检验指导书》及图纸要求;
5.零件挪动搬运过程中是否轻拿轻放,是否有人为的碰伤划伤等不良现象;
6.物料摆放是否符合《现场物料摆放规范》;
7.编程排版是否合理;
8.模具使用是否符合《刀模具管理制度》要求;
9.零件摆放是否按区域摆放,是否混料,不合格的产品须贴不合格标签,并放入不合格品区;
10.所有种类零部件是否有明确标示、工艺流程卡、图纸资料等,且标示清晰准确;
7.物料摆放是否符合《现场物料摆放规范》;
8.现场模具使用是否符合《刀模具管理制度》要求;
9.零件摆放是否按区域摆放,是否混料,不合格的产品须贴不合格标签,并放入不合格品区;
10.所有种类零部件是否有明确标示、工艺流程卡、图纸资料等,且标示清晰准确;
11.焊接螺钉种类及焊接位置是否与图纸要求一致;
12.熔焊螺钉是否焊接牢固,焊接强度是否工艺参数要求;
无异常
/
/
/
6、装配工段
1.流水线设备及工具每天是否有点检,机台、场地是否清洁。
2.生产产品与文件是否一致,文件是否有缺损,且技术资料是否为最新版本。
3.是否有自检、首件检验记录。
4.是否有区域规划,零件摆放是否按区域摆放,零件是否有保护,物料摆放是否有标识,标识是否准确。
5.电镀产品是否戴手套操作。
工艺日常点检表

日期:
班次:□白班□夜班点检事项
频率各镍槽pH值检查并调整
每班两次镍、锡槽弱电解是否开启
每班一次根据当天要生产的产品按照安培小时数添加添加剂每班一次各线脱脂是否需要更换
每班一次各线酸洗是否需要更换
每班一次各镍槽、锡槽阳极是否需要添加
每班一次各线镍槽液位调整(补水)
每班四次各线分析结果检查并添加
每天一次金槽波美度、pH检查并调整
每班一次是否有滤芯需要更换
每班一次是否有阳极袋需要更换
每班一次□其它:
*执行后记下执行的时间产线生产状况:
*当班使用的通道打“√”
审核:执行人:工艺日常点检表
执行时间备注。
ESI结构工艺评审点检表(checklist)[空白模板]
![ESI结构工艺评审点检表(checklist)[空白模板]](https://img.taocdn.com/s3/m/c3ac82dfb90d6c85ed3ac6a9.png)
序号类型点检项目点检人不符合项原因分析建议措施责任单位/责任人跟进反馈关闭状态改善完成时间复查情况1客户信息、项目简况、评审时间是否明确。
23D图档、CMF、工艺标准等资料客户是否提供。
3产品材质、胚料重量是否确定。
4客户特殊加工要求是否明确,是否满足我司技术能力。
5整体工艺方案和加工顺序是否合理,夹数是否过多,部分夹位能否合并。
6材料余量预留是否合理,能否进一步减少。
7定位基准是否合理可靠,尽可能避免多次转换基准,夹持方式是否牢固。
8刀具选型是否合理,有无特殊要求,刀具加工参数和寿命评估是否合理。
9工序3D有无接刀问题,如何避免接刀风险,同一夹台阶光刀尽可能用一 把刀完成。
10产品变形风险评估,如何有效解决产品加工变形导致的尺寸不稳问题。
11定位孔是否已考虑防呆,定位孔直径公差及深度是否合理,有没有考虑加倒角,加工方式是否合理,大批量生产是否可靠。
12有无放大偏位特征,如何避免。
13加工冷却方式有无特殊要求。
14外观有无特殊要求,外观面不允许出现接刀,外观刀材质选择是否合理。
15容易出现毛刺的特征如何解决毛刺问题,有没有加专门去毛刺刀具刀路。
16进刀位和退刀位是否合理,有无撞刀风险。
17是否需要断刀检测,探头,探点位选择是否合理,探点数量是否合理,变量选择是否正确。
18是否需要记版本号和机台号。
19每次飞面厚度0.30mm,飞面光刀后,接刀纹要控制在0.02以内。
20裙边宽度定义D6销钉+4mm+7mm为准,外侧壁优先考虑分夹加工;外侧壁合夹加工的裙边留料定义D6销钉+4mm+外侧壁刀具过刀直径+1.0mm。
21宽度方向以注塑前半成品尺寸(铝挤面)单边+0.5mm,长度方向以注塑前半成品尺寸(锯切面)单边+1.0mm。
22CNC1飞面,并加工一组定位孔只给CNC2使用,定位孔直径D5,方便后工序二次使用时扩孔。
23CNC2或CNC3加工内腔的工序需同时在产品内腔及外裙边加工两组定位孔作为后工序直至外侧壁工序的定位。
PCB点检表(增加工艺审查)

PCB点检表设计规范的附录A兀器件种类及名称文字符号兀器件种类及名称文字符号变压器T 接触器KM测试点(焊盘) TP 晶体振荡器、谐振器Y插头、插座J 开关S电池GB 滤波器Z电感器、磁珠L 模块电源MP电容器 C 熔断器FU电阻器R 三极管Q电位器RP 二极管、稳压二极管 D排阻RR 发光二极管DL热敏电阻RT 指示灯HL压敏电阻RV 继电器K蜂鸣器VD 集成电路、三端稳压块U光耦ISO TVS管TVS跳线器、拨码开关JUMP 数码管LVDS电流互感器CT 电压互感器PT设计规范的附录B器件间距要求PLCG QFR SOP各自之间和相互之间间隙》2.5mm( 100mil )。
PLCC QFP SOP与 Chip、SOT之间间隙 >1.5mm (60mil )回流焊:Chip、SOT各自之间和相互之间的间隙可以小至0.3mm(12mil)。
波峰焊:Chip、SOT相互之间的间隙 R8mm(32mil )和 1.2mm (47mil ),钽电容在前面时,间隙应 >2.5mm (100mil )。
见下图:BGA外形与其他元器件的间隙 >5mm(200mil )PLCC表面贴转接插座与其他元器件的间隙>3mrm( 120mil )。
表面贴片连接器与连接器之间应该确保能够检查和返修。
一般连接器引线侧应该留有比连接器高度大的空间。
元件到喷锡铜带(屏蔽罩焊接用)应该 2mm(80mil)以上。
元件到拼板分离边需大于1mm(40mil)以上。
如果B面(焊接面)上贴片元件很多、很密、很小,而插件焊点又不多,建议插件引脚离开贴片元件焊盘 5mm 以上,以便可以采用掩模夹具进行局部波峰焊。
注:其中间隙一般指不同元器件焊盘间的间隙,器件体大于焊盘时,指器件体的间隙)设计规范的附录C丝印字符大小参考值)设计规范的附录F 器件封装制作要求器件封装制作要求:。
工艺纪律检查点检表模板

序号单位 检查内容 加工现场有图纸料单 及工艺流程卡片填写 完整 测量工具精准合格 收集计划、图纸完善 下转自检工艺卡片上 面签名 图纸与模具对应 材料不许有锈蚀、沙 土、脚印、划伤、波 浪、水迹 零件摆放、转运符合 工艺要求 后工序需电镀件应用 防护材料进行分隔 备料是否按料单工艺 要求 刀具与料厚间隙相配 合 毛刺修磨是否符合要 1 下料 求(操作、工件毛 刺) 现场模具摆放不能摞 放、裸放于地 模具上不许有锈迹、 水、铁屑、异物等 弯曲刀槽与料厚相符 模具对接口无产生弯 曲接刀的塌角不良 弯曲后零件无明显的 拼角、角度、变形不 良 回头弯内及打死边内 的保护膜按要求进行 去除 对电镀件、不锈钢、 敷铝锌板、镀锌板、 耐指纹板进行隔离防 护 劳动防护用品穿戴齐 全
月
日工艺纪律检;不符合的填写现场状况 责任人及 冲床 剪板 折弯 九折 区域 考核金额
PCB点检表(增加工艺审查)
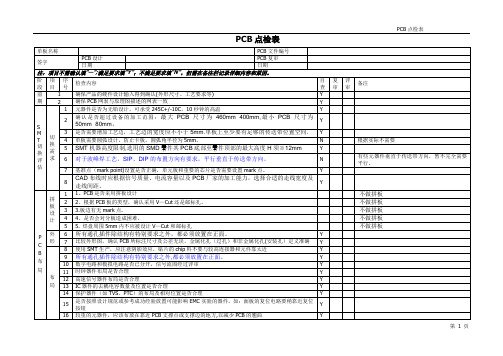
PCB点检表
设计规范的附录A
公司对元器件文字符号(REFDES)的统一规定
器件间距要求
设计规范的附录C
内外层线路及铜箔到板边、非金属化孔壁的尺寸要求单位:mm(mil)
PCB布线最小间距
丝印字符大小(参考值)
器件封装制作要求
器件封装制作要求:
a。
器件在极限尺寸时,应该还能保证:尺寸a(toesolderfillet)=0。
4~0。
6mm且大于1/3引脚厚度H.器件引脚中心距<=0.5mm时,取0。
4mm.
b.器件在极限尺寸时,应该还能保证:尺寸b(heelsolderfillet)=0。
4~0.6mm.器件引脚中心距<=0.5mm时,取0。
4mm。
c.器件在极限尺寸时,应该还能保证:尺寸c(sidesolderfillet)=0~0。
2mm。
设计规范的附录G
通孔制作要求
一般通孔直接大于管脚直径0。
2~0.5mm,考虑公差适当增加,确保透锡量好.
PCB点检表设计规范的附录H
SMD贴片元件工艺要求。
点检表模板
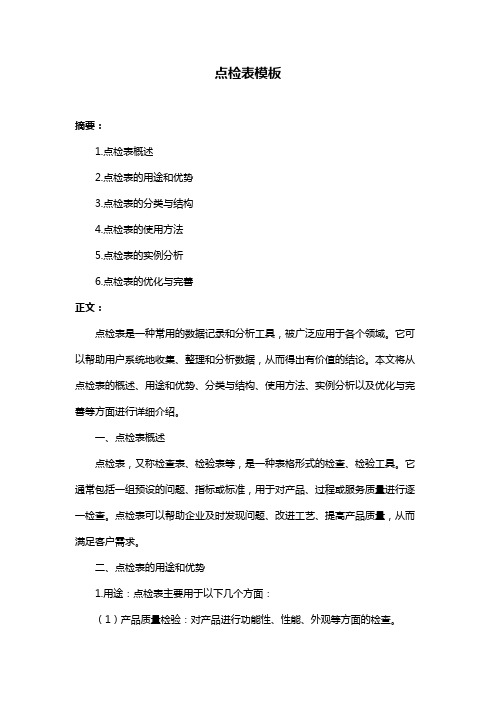
点检表模板摘要:1.点检表概述2.点检表的用途和优势3.点检表的分类与结构4.点检表的使用方法5.点检表的实例分析6.点检表的优化与完善正文:点检表是一种常用的数据记录和分析工具,被广泛应用于各个领域。
它可以帮助用户系统地收集、整理和分析数据,从而得出有价值的结论。
本文将从点检表的概述、用途和优势、分类与结构、使用方法、实例分析以及优化与完善等方面进行详细介绍。
一、点检表概述点检表,又称检查表、检验表等,是一种表格形式的检查、检验工具。
它通常包括一组预设的问题、指标或标准,用于对产品、过程或服务质量进行逐一检查。
点检表可以帮助企业及时发现问题、改进工艺、提高产品质量,从而满足客户需求。
二、点检表的用途和优势1.用途:点检表主要用于以下几个方面:(1)产品质量检验:对产品进行功能性、性能、外观等方面的检查。
(2)生产过程控制:对生产过程中的关键环节进行监控,确保生产质量。
(3)设备运行检查:对设备运行状态、保养情况等进行检查,预防设备故障。
(4)安全与环境检查:对生产环境、安全设施、环保措施等进行检查。
(5)管理体系审核:对管理体系进行内部审核,评估体系运行的有效性和适宜性。
2.优势:(1)结构清晰:点检表采用表格形式,使检查内容条理清晰,便于填写和分析。
(2)标准化:预设的问题和标准具有普遍性,可确保检查的客观性和一致性。
(3)易于执行:点检表内容简洁,操作方便,可快速完成检查。
(4)及时反馈:点检表可及时发现问题,为改进提供依据。
三、点检表的分类与结构1.分类:(1)按检查内容分:产品质量检查表、生产过程检查表、设备检查表等。
(2)按检查方式分:手工检查表、仪器检查表、现场检查表等。
2.结构:(1)表头:包括检查项目、检查部位、检查人员等。
(2)检查内容:包括问题、指标、标准等,可根据实际情况进行增减。
(3)检查结果:填写检查过程中发现的问题、异常情况等。
(4)验收标准:对检查结果进行评价,判断是否符合要求。
10-事故隐患排查工艺专项检查表

混合时的不良后果,混合后是否发生反应;
e)对于泄漏化学品的处置方法。 a) 工艺流程简图;
b) 工艺化学原理资料;
c) 设计的物料最大存储量;
d) 安全操作范围(温度、压力、流量、液位或
组分等);
e) 偏离正常工况后果的评估及纠正,包括对员
2
工艺(操作)规 工的安全和健康的影响
程
f)修订信息
g)初始开车、正常操作、临时操作、应急操作
、正常停车、紧急停车等各个阶段的操作步骤
h)安全、健康和环境相关事项。如危险化学品
的特性与危害、防止暴露的必要措施、发生身体
接触或暴露后的处理措施、安全系统及其功能管理程序;
3
培训
b)培训记录;
c)培训计划、培训方式。
4
变更管理
a)变更管理程序; b)工艺变更报告。
危险化学品企业事故隐患工艺排查表
排查对象:
NO.
专项
排查内容
a) 毒性;
b) 物理参数,如沸点、蒸气压、密度、溶解度
、闪点、爆炸极限;
1
化学品安全技术 c)腐蚀性数据,腐蚀性以及材质的不相容性; 说明书(MSDS) d)热稳定性和化学稳定性,如受热是否分解、
暴露于空气中或被撞击时是否稳定;与其它物质
现场排查
亮点
排查日期:
建议
编制部门: 安全管理部
审核:
审批:
a)操作室配置工艺卡片、工艺卡片信息齐全;
5
工艺卡片 b)工艺卡片变更记录、修订记录;
c)工艺卡片执行情况。
a)员工遵守操作规程、按照工艺参数要求操
作;
6
岗位现场工艺管 b)定时巡回检查,有检查记录;
理
灌胶点检表

QM-HK-750-06
灌胶点检表
日期 班次 操作员点检 工艺点检 点检时间 首件成功 循环清零 备注 点检人
()当日开线()长时间待机 ()添加胶 ()机器故障 ()更换夹具 ()当日开线()长时间待机 ()添加胶 ()机器故障 ()更换夹具 ()当日开线()长时间待机 ()添加胶 ()机器故障 ()更换夹具 ()当日开线()长时间待机 ()添加胶 ()机器故障 ()更换夹具 ()当日开线()长时间待机 ()添加胶 ()机器故障 ()更换夹具 ()当日开线()长时间待机 ()添加胶 ()机器故障 ()更换夹具 ()当日开线()长时间待机 ()添加胶 ()机器故障 ()更换夹具 ()当日开线()长时间待机 ()添加胶 ()机器故障 ()更换夹具 ()当日开线()长时间待机 ()添加胶 ()机器故障 ()更换夹具 ()当日开线()长时间待机 ()添加胶 ()机器故障 ()更换夹具 ()当日开线()长时间待机 ()添加胶 ()机器故障 ()更换夹具 ()当日开线()长时间待机 ()添加胶 ()机器故障 ()更换夹具 ()当日开线()长时间待机 ()添加胶 ()机器故障 ()更换夹具 ()当日开线()长时间待机 ()添加胶 ()机器故障 ()更换夹具 ()当日开线()长时间待机 ()添加胶 ()机器故障 ()更换夹具 ()当日开线()长时间待机 ()添加胶 ()机器故障 ()更换夹具 ()当日开线()长时间待机 ()添加胶 ()机器故障 ()更换夹具 ()当日开线()长时间待机 ()添加胶 ()机器故障 ()更换夹具 ()当日开线()长时间待机 ()添加胶 ()机器故障 ()更换夹具 ()当日开线()长时间待机 ()添加胶 ()机器故障 ()更换夹具 ()当日开线()长时间待机 ()添加胶 ()机器故障 ()更换夹具 ()当日开线()长时间待机 ()添加胶 ()机器故障 ()更换夹具 ()当日开线()长时间待机 ()添加胶 ()机器故障 ()更换夹具 ()当日开线()长时间待机 ()添加胶 ()机器故障 ()更换ቤተ መጻሕፍቲ ባይዱ具 ()当日开线()长时间待机 ()添加胶 ()机器故障 ()更换夹具 ()当日开线()长时间待机 ()添加胶 ()机器故障 ()更换夹具 ()当日开线()长时间待机 ()添加胶 ()机器故障 ()更换夹具 ()当日开线()长时间待机 ()添加胶 ()机器故障 ()更换夹具 ()当日开线()长时间待机 ()添加胶 ()机器故障 ()更换夹具 ()当日开线()长时间待机 ()添加胶 ()机器故障 ()更换夹具 ()当日开线()长时间待机 ()添加胶 ()机器故障 ()更换夹具 备注:(1)每次灌满整筒胶后机器上循环必须清零 (3)为避免胶量不足,I3系列每次点500个,ID系列点440个需重新添满胶
注塑模具试模验收点检表A0
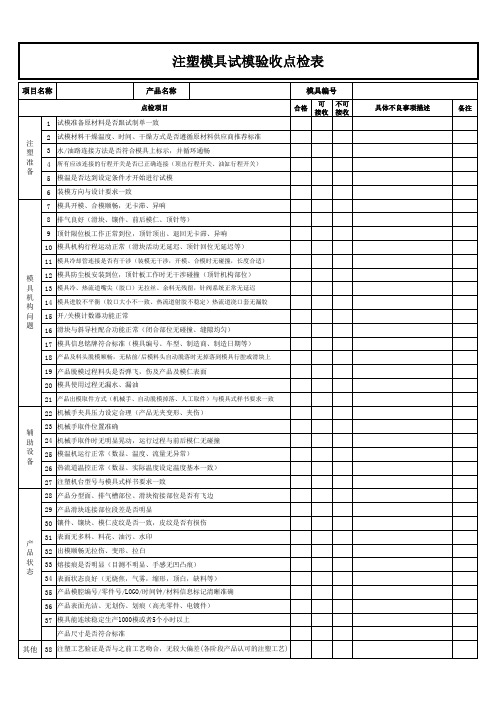
合格
可 接收
不可 接收
其他 38 注塑工艺验证是否与之前工艺吻合,无较大偏差(各阶段产品认可的注塑工艺)
具体不良事项描述
备注
注塑模具试模验收点检表
项目名称
产品名称
点检项目
1 试模准备原材料是否跟试制单一致
2 试模材料干燥温度、时间、干燥方式是否遵循原材料供应商推荐标准 注 塑 3 水/油路连接方法是否符合模具上标示,并循环通畅 准 4 所有应该连接的行程开关是否已正确连接(顶出行程开关、油缸行程开关) 备
5 模温是否达到设定条件才开始进行试模
设 25 模温机运行正常(数显、温度、流量无异常) 备
26 热流道温控正常(数显、实际温度设定温度基本一致)
27 注塑机台型号与模具式样书要求一致
28 产品分型面、排气槽部位、滑块衔接部位是否有飞边
29 产品滑块连接部位段差是否明显
30 镶件、镶块、模仁皮纹是否一致,皮纹是否有损伤
31 表面无多料、料花、油污、水印 产 品 32 出模顺畅无拉伤、变形、拉白
状 33 熔接痕是否明显(目测不明显、手感无凹凸痕) 态
34 表面状态良好(无烧焦,气雾,缩形,顶白,缺料等)
35 产品模腔编号/零件号/LOGO/时间钟/材料信息标记清晰准确
36 产品表面光洁、无划伤、划痕(高光零件、电镀件)
37 模具能连续稳定生产1000模或者5个小时以上
产品尺寸是否符合标准
模具编号
具 13 模具冷、热流道嘴尖(胶口)无拉丝、余料无残留,针阀系统大小不一致、热流道射胶不稳定)热流道浇口套无漏胶
问 15 开/关模计数器功能正常
题 16 滑块与斜导柱配合功能正常(闭合部位无碰撞、缝隙均匀)
17 模具信息铭牌符合标准(模具编号、车型、制造商、制造日期等)
水刺工段日常点检以及保养登记表

项目
水刺工段日常点检及保养记录
点检及保养周期
班组:
保养记录
过滤袋
1、每2小时点检1次; 2、压力达到2.0时必须更换; 3、每班每组必须换3个 4、金属过滤网每24小时必须清洗一遍
警察过滤滤芯
1、每日停机后至少更换1个; 2、每周需要一套全部更换; 3、压差达到10bar以上,必须清洗更换
水针板清洗 每次停机时清洗
保养时间 保养人
金属过滤器
1、每日停机后至少更换1个; 2、每周需要一套全部更换; 3、金属过滤器更换同时必须 更换警察过滤滤芯; 4、压差达到10bar以上,必须清洗更换
气浮及地下水池
1、气浮水池正常情况10天更பைடு நூலகம்1次 2、地下水池正常情况15天更换1次
加药
1、杀菌剂更换水后第一次加200KG; 2、杀菌剂在第二次开始每次加15KG-20KG/天 3、聚合氯化铝每隔24小时加1袋
工艺纪律检查项目及评价表
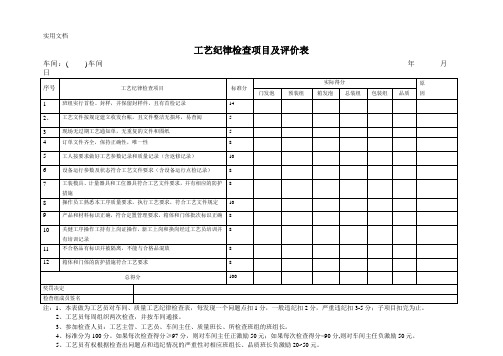
工艺纪律检查项目及评价表
车间:( )车间年月
注:1、本表做为工艺员对车间、质量工艺纪律检查表,每发现一个问题点扣1分,一般违纪扣2分,严重违纪扣3-5分;子项目扣完为止。
2、工艺员每周组织两次检查,并按车间通报。
3、参加检查人员:工艺主管、工艺员、车间主任、质量班长、所检查班组的班组长。
4、标准分为100分。
如果每次检查得分≥97分,则对车间主任正激励50元;如果每次检查得分<90分,则对车间主任负激励50元。
5、工艺员有权根据检查出问题点和违纪情况的严重性对相应班组长、品质班长负激励20~50元。
工艺纪律检查项目及评价表
部门:年月
注:1、本表做为部门对车间、质量工艺纪律检查表,每发现一个问题点扣1分,一般违纪扣2分,严重违纪扣3-5分;子项目扣完为止。
2、工艺部每周组织一次检查,并按车间通报。
3、参加检查人员:总经理、工艺部长、质量部长、技术部长、生产部长、设备部长所检查班组的车间主任、班组长。
4、标准分为100分。
如果每次检查得分≥90分,则对车间主任激励50元;如果每次检查得分<90分,则对车间车间主任负激励50元。
组装工艺评审点检表v10.xls

4
5
六
FPC/同轴 线/天线
6六Fຫໍສະໝຸດ C/同轴 线/天线78 9 1 2
3 4 5
6
7
喇叭、听
七
筒、马达 、mic、
8
摄像头
9 10
11
12
XXX项目组装工艺评审点检表
检查内容 按键组件、侧按键应有明显的手感,是否有干涉、连动、行程不足、各按键手感不一致、 触点偏位、按键间隙大、是否会与镜片、壳边、装饰件有干涉的可能,按键是否便于装配 和定位等。对于主板上按键设计为微动开关的,试产要特别注意开关贴片和手感情况。
设计点胶路径时优先考虑CPU球密度小的方向做为点胶口,便于胶水流动
邮票孔位置最好不要放在壳与主板卡合位置,以免分板毛边,导致主板难装到位。
T卡、SIM卡、小卡卡托等卡座须考量卡插拔是否顺畅;卡是否与壳体有干涉、卡座弹片是 否与壳体干涉,是否有相应的方向和卡座顺序标识,sim卡顺序和软件是否对应,双模机应 该有对卡位信息标识;卡座开孔处反面设计应该避开CPU和FLASH,避免点胶渗透粘死卡座 装SIM卡后,SIM卡应无起翘、前后左右方向应定位可靠,要求支撑SIM的面是平面,壳体或 电池盖上要求做相对应的防滑动设计.侧面小卡卡托需确认间隙是否OK,有无突出、下陷、 色差不良。卡托如有镭雕丝印,需确认其是丝印否正确,是否容易磨花。
TP FPC IC位置与面壳必须预留0.8mm 的间隙,以免IC部位点胶过厚导致TP被顶起起翘。
TP背胶的有效黏贴宽度建议至少在1.5mm以上,以免TP起翘。且面壳的平面度要求在0.3mm 以内。
TP字符透光性,均匀度,功能机的按键透光性和均匀度检查是否OK。
TP外保护膜上听筒和感应孔位置必须做开孔避空处理。
点检表

备注:
JBJH-MA—O-F0013-1.1
点
生产线名称 缝纫线B008
日期: 产品:
检
表
——————————
时
间
2012年 2月
D
设备名称 / 编号
工序描述
组装螺栓组件,包装
1.操作者经考核合格;已熟练掌握操作技能 2.以前生产的合格与不合格零组件已清理 3.操作指导书,检验指导书齐全有效 4.工人自检-互检表齐全 5.待装零件已备齐、且与待生产产品及工艺相适应 6. 工作场地整洁,设备/工装/工位器具准确且无灰尘/异物 7.首件检验合格: 外观或各单项数值依据相对应产品的《检验 指导书》
备注:
JBJH-MA—O-F0013-1.1
点
生产线名称 缝纫线B008
日期: 产品: 1.操作者经考核合格;已熟练掌握操作技能 2.设备工作参数:气压0.50±0.10MPa 3.设备无漏气/电现象,运转正常,添加机油 4.用废织带试机,图案符合工艺要求 5.以前生产的合格与不合格零组件已清理 6.操作指导书,检验指导书齐全有效 7.工人自检-互检表齐全 8.待装零件已备齐、且与待生产产品及工艺相适应 9. 工作场地整洁,设备/工装/工位器具准确且无灰尘/异物 10.首件检验合格: 外观或各单项数值依据相对应产品的《检验 指导书》 11.末件检验合格:外观或各单项数值依据相对应产品的《检验 指导书》 点检状态 操作者签名 现场工程师签字 班长签名 质检员抽检结果 质检员签名
备注:
填 表 说 明
JBJH-MA—O-F0013-1.1
点
生产线名称 缝纫线B008
日期: 产品:
检
表
——————————
时
间