加工工艺点检表
工艺纪律检查表

5
3.工装夹具是否定期保养?是否按工艺文件对其进行检查清理?
1.没有定期保养记录
2.没有检查清理记录
5
4.量具、检具、仪表等是否有校验标识?是否超期使用?
现场没有量具
3
生产
51是否按要ຫໍສະໝຸດ 进行自检,检验方法是否正确?有自检(没有核对自检记录)
5
2.是否进行了首检?
有首检(没有核对首检记录)
5
3.出现不合格时的流程是否熟悉?
熟悉不合格品流程
5
4.操作员工是否按照工艺文件操作,操作是否规范?
实际使用自动装夹设备,但文件描述使用旧工装手动装夹
4
物流
5
1.物料是否有标识?是否填写产品流转卡?产品区域是否清楚不易混料?
1物料有标识;
2没有产品流转卡
3.产品区域清楚
5
2.产品区域是否清楚并不易混料?
5
3.工艺文件是否符合现场加工?是否有指导性?
实际使用自幼装夹设备,但文件描述使用旧工装手动装夹
5
4.作业流程是否清楚?
清楚
5
5.生产记录单是否记录规范、正确?
没有生产记录单
2
备装具设工检
5
1.设备是否按规定进行定期维护和点检?是否每日点检和记录?
没有每日点检记录,没有其他记录
5
2.设备是否悬挂操作规程?
工艺纪律检查表
被检查班组:被检查工位:检查人:检查时间:
序号
检查项目
标准分
检查内容
检查结果
被检查人
实得分
1
文件资料
5
1.是否悬挂有效工艺文件或图纸?是否完好清晰?是否理解和被执行?
生产工装管理要求点检表(TS16949要求))
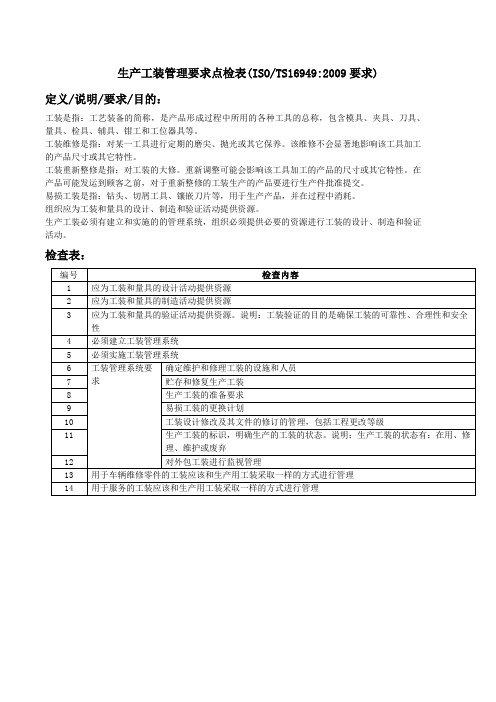
生产工装管理要求点检表(ISO/TS16949:2009要求)
定义/说明/要求/目的:
工装是指:工艺装备的简称,是产品形成过程中所用的各种工具的总称,包含模具、夹具、刀具、量具、检具、辅具、钳工和工位器具等。
工装维修是指:对某一工具进行定期的磨尖、抛光或其它保养。
该维修不会显著地影响该工具加工的产品尺寸或其它特性。
工装重新整修是指:对工装的大修。
重新调整可能会影响该工具加工的产品的尺寸或其它特性。
在产品可能发运到顾客之前,对于重新整修的工装生产的产品要进行生产件批准提交。
易损工装是指:钻头、切屑工具、镶嵌刀片等,用于生产产品,并在过程中消耗。
组织应为工装和量具的设计、制造和验证活动提供资源。
生产工装必须有建立和实施的的管理系统,组织必须提供必要的资源进行工装的设计、制造和验证活动。
检查表:。
《工艺纪律检查表》
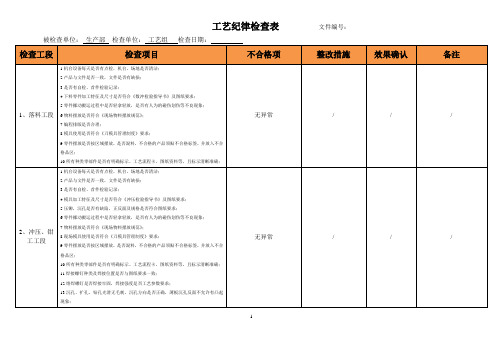
被检查单位:生产部检查单位:工艺组检查日期:
检查工段
检查项目
不合格项
整改措施
效果确认
备注
1、落料工段
1.机台设备每天是否有点检,机台、场地是否清洁;
2.产品与文件是否一致,文件是否有缺损;
3.是否有自检、首件检验记录;
4.下料零件加工特征及尺寸是否符合《数冲检验指导书》及图纸要求;
5.零件挪动搬运过程中是否轻拿轻放,是否有人为的碰伤划伤等不良现象;
6.物料摆放是否符合《现场物料摆放规范》;
7.编程排版是否合理;
8.模具使用是否符合《刀模具管理制度》要求;
9.零件摆放是否按区域摆放,是否混料,不合格的产品须贴不合格标签,并放入不合格品区;
10.所有种类零部件是否有明确标示、工艺流程卡、图纸资料等,且标示清晰准确;
7.物料摆放是否符合《现场物料摆放规范》;
8.现场模具使用是否符合《刀模具管理制度》要求;
9.零件摆放是否按区域摆放,是否混料,不合格的产品须贴不合格标签,并放入不合格品区;
10.所有种类零部件是否有明确标示、工艺流程卡、图纸资料等,且标示清晰准确;
11.焊接螺钉种类及焊接位置是否与图纸要求一致;
12.熔焊螺钉是否焊接牢固,焊接强度是否工艺参数要求;
无异常
/
/
/
6、装配工段
1.流水线设备及工具每天是否有点检,机台、场地是否清洁。
2.生产产品与文件是否一致,文件是否有缺损,且技术资料是否为最新版本。
3.是否有自检、首件检验记录。
4.是否有区域规划,零件摆放是否按区域摆放,零件是否有保护,物料摆放是否有标识,标识是否准确。
5.电镀产品是否戴手套操作。
工序检查表

标段工程师 :
年月日
工程项目名称:
模板安装工程质量检查验收表
施工单位:
验收部位:施工ຫໍສະໝຸດ 量检查项目检 查 内 容检查情况
检查人
1
模板支承体系必须按照相关技术要求设置
2
出现高支模情况,必须按所报高支模方案实施
3
模板和支架完好,清理干净,起皮和变形模板不得使用
4
模板拼装顺序:后拆的先支,先拆的后支
14
高压水枪试水
30~45min
监理(建设)单位验收结论
标段工程师 :
年月日
工程项目名称:
模板分项工程复线、测量检查验收表
施工单位:
检查部位:
检查项目
检 查 内 容
检查情况
检查人
1
轴线位置
2
底模上表面标高
3
截面内部尺寸
柱、梁、墙
4
层高垂直度
不大于
5M
大于5M
5
相邻两表板
表面高低差
6
表面平整度
7
每五层检查层高及垂直度
吊模、边模加固及顺直
14
结构施工图中的反梁和飘窗模板平面位置及标高检查
监理(建设)单位
验收结论
标段工程师:
年月日
5
模板拼缝是否符合相关技术
要求
6
避免隔离剂沾污
7
检查柱模垂直度、梁侧模垂直度符合相关技术要求
8
检查梁、板底模标高 是否符合相关技术要求
9
检查梁、墙柱轴线定位是否符合相关技术要求
10
柱模的拉紧螺栓、木方箍等设置间距是否符合相关技术
11
柱模根处是否设置清扫口是否订压脚板
工厂过程工艺检查表
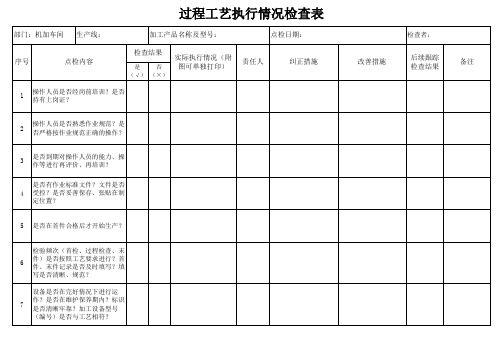
3
是否到期对操作人员的能力、操 作等进行再评价、再培训? 是否有作业标准文件?文件是否 受控?是否妥善保存、张贴在制 定位置?
4
5
是否在首件合格后才开始生产?
6
检验频次(首检、过程检查、末 件)是否按照工艺要求进行?首 件、末件记录是否及时填写?填 写是否清晰、规范? 设备是否在完好情况下进行运 作?是否在维护保养期内?标识 是否清晰牢靠?加工设备型号 (编号)是否与工艺相符?
过程工艺执行情况检查表
部门:机加车间 生产线: 加工产品名称及型号: 检查结果 序号 点检内容
是 否 (√) (×)
点检日期:
检查者:
实际执行情况(附 图可单独打印)
责任人
纠正措施
改善措施
后续跟踪 检查结果
备注
1
操作人员是否经岗前培训?是否 持有上岗证?
2
操作人员是否熟悉作业规范?是 否严格按作业规范正确的操作?
7
8
工具是否摆放至指定位置?
9
在线产品是否定置、定量管理? 待、已加工产品是否摆放至指定 位置?产品是否采取防护措施? 废弃物、废料是否放在指定位 置?是否及时处理?
10
11
不合格品(不良品)标识是否明 确?是否及时处理? 在线量具、检具是否完好、齐 全?是否在合格期内使用?是否 放在指定位置? 卡盘夹持力是否与工艺要求相 符?
12
13
14
工装夹具是否与工艺要求相பைடு நூலகம்?
15
走刀路线、走刀次数、进给量是 否与工艺要求相符?
16
刀体、刀片型号是否与工艺要求 相符?
17
刀具更换频次是否与工艺要求相 符?是否及时记录?
备注:1、每周现场技术员、质量工程师车间主任对机加现场工艺执行情况进行检查,每周一次;2、点检不符合内容传责任单位限期整改。
机器加工分层审核检查清单表格模板(可修改)
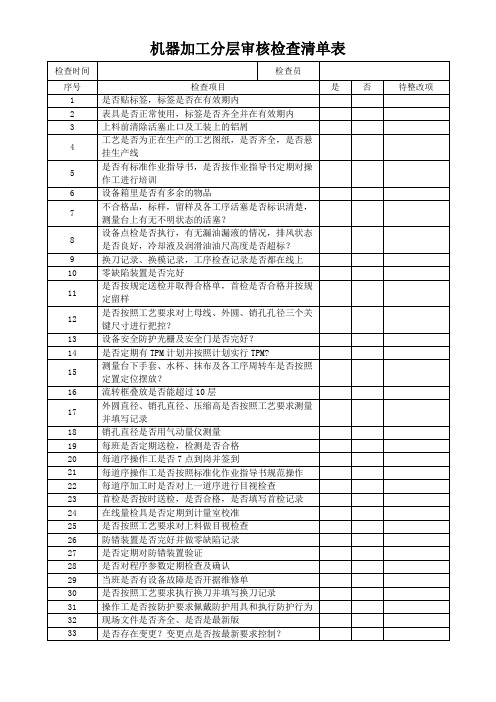
检查时间
检查员
序号
检查项目
是
否
待整改项
1
是否贴标签,标签是否在有效期内
2
表具是否正常使用,标签是否齐全并在有效期内
3
上料前清除活塞止口及工装上的铝屑
4
工艺是否为正在生产的工艺图纸,是否齐全,是否悬挂生产线
5
是否有标准作业指导书,是否按作业指导书定期对操作工进行培训
6
设备箱里是否有多余的物品
20
每道序操作工是否7点到岗并签到
21
每道序操作工是否按照标准化作业指导书规范操作
22
每道序加工时是否对上一道序进行目视检查
23
首检是否按时送检,是否合格,是否填写首检记录
24
在线量检具是否定期到计量室校准
25
是否按照工艺要求对上料做目视检查
26
防错装置是否完好并做零缺陷记录
27
是否定期对防错装置验证
13
设备安全防护光栅及安全门是否完好?
14
是否定期有TPM计划并按照计划实行TPM?
15
测量台下手套、水杯、抹布及各工序周Leabharlann 车是否按照定置定位摆放?16
流转框叠放是否能超过10层
17
外圆直径、销孔直径、压缩高是否按照工艺要求测量并填写记录
18
销孔直径是否用气动量仪测量
19
每班是否定期送检,检测是否合格
7
不合格品,标样,留样及各工序活塞是否标识清楚,测量台上有无不明状态的活塞?
8
设备点检是否执行,有无漏油漏液的情况,排风状态是否良好,冷却液及润滑油油尺高度是否超标?
9
换刀记录、换模记录,工序检查记录是否都在线上
模具验收点检表
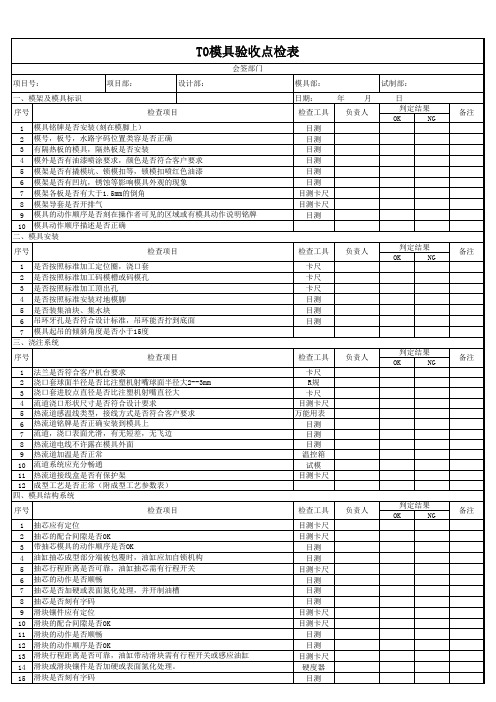
八、液压、电子、控制
T0模具验收点检表
会签部门 项目号: 一、模架及模具标识 序号 检查项目 项目部: 设计部: 模具部: 日期: 检查工具 目测 目测 目测 目测 目测 目测 目测卡尺 目测卡尺 目测 年 月 负责人 试制部: 日 判定结果 OK NG
备注
1 模具铭牌是否安装(刻在模脚上) 2 模号,板号,水路字码位置类容是否正确 3 有隔热板的模具,隔热板是否安装 4 模外是否有油漆喷涂要求,颜色是否符合客户要求 5 模架是否有撬模坑、锁模扣等,锁模扣喷红色油漆 6 模架是否有凹坑,锈蚀等影响模具外观的现象 7 模架各板是否有大于1.5mm的倒角 8 模架导套是否开排气 9 模具的动作顺序是否刻在操作者可见的区域或有模具动作说明铭牌 10 模具动作顺序描述是否正确 二、模具安装 序号 检查项目
检查工具 目测卡尺 目测卡尺 目测 目测 目测卡尺 目测 目测 目测 目测卡尺 目测卡尺 目测 目测 目测卡尺 硬度器 目测
负责人
判定结果 OK NG
备注
16 斜顶配合间隙是否OK 17 斜顶胶位面应抛光,斜顶顶面低于型芯面 18 斜顶的动作是否顺畅 19 斜顶是否刻有字码 20 模具镶件的配合间隙是否OK 21 模具镶件是否需要加硬或表面氮化处理 22 顶块配合间隙是否OK 23 顶块是否需要加硬或表面氮化处理 24 顶块是否刻有字码 25 各活动部件压条、耐磨片是否加硬处理并开制油槽 26 各导向块、导向座是否加硬或表面氮化处理 27 各装配零部件是否有字码,周边非成型边倒C角 28 所有螺牙长度是否有1.5倍螺丝直径 29 大滑块,镶件,抽芯是否有吊装螺孔 五、顶出系统 序号 1 2 3 4 5 6 7 8 检查项目 顶针与滑块是否干涉,有干涉的是否有先复位机构,是否安装行程开关 顶出时应顺畅、无卡滞、无异常声响。 顶出距离应用限位块进行限位。 所有顶杆、顶块应有止转定位,每个顶杆、顶块都应进行编号,顶杆, 顶块不应上下串动 顶杆上加倒钩,倒钩的方向应保持一致,倒钩易于从制品上去除 顶杆孔与杆的配合间隙,封胶段长度,顶杆孔的表面粗糙度应符合客户要求 制品顶出时易跟着斜顶走,顶杆上应加槽或蚀纹 固定在顶杆上的顶块,应牢固可靠,四周非成型部分应加工3-5°的斜面, 下底部周边倒角
PCB点检表(增加工艺审查)

PCB点检表设计规范的附录A兀器件种类及名称文字符号兀器件种类及名称文字符号变压器T 接触器KM测试点(焊盘) TP 晶体振荡器、谐振器Y插头、插座J 开关S电池GB 滤波器Z电感器、磁珠L 模块电源MP电容器 C 熔断器FU电阻器R 三极管Q电位器RP 二极管、稳压二极管 D排阻RR 发光二极管DL热敏电阻RT 指示灯HL压敏电阻RV 继电器K蜂鸣器VD 集成电路、三端稳压块U光耦ISO TVS管TVS跳线器、拨码开关JUMP 数码管LVDS电流互感器CT 电压互感器PT设计规范的附录B器件间距要求PLCG QFR SOP各自之间和相互之间间隙》2.5mm( 100mil )。
PLCC QFP SOP与 Chip、SOT之间间隙 >1.5mm (60mil )回流焊:Chip、SOT各自之间和相互之间的间隙可以小至0.3mm(12mil)。
波峰焊:Chip、SOT相互之间的间隙 R8mm(32mil )和 1.2mm (47mil ),钽电容在前面时,间隙应 >2.5mm (100mil )。
见下图:BGA外形与其他元器件的间隙 >5mm(200mil )PLCC表面贴转接插座与其他元器件的间隙>3mrm( 120mil )。
表面贴片连接器与连接器之间应该确保能够检查和返修。
一般连接器引线侧应该留有比连接器高度大的空间。
元件到喷锡铜带(屏蔽罩焊接用)应该 2mm(80mil)以上。
元件到拼板分离边需大于1mm(40mil)以上。
如果B面(焊接面)上贴片元件很多、很密、很小,而插件焊点又不多,建议插件引脚离开贴片元件焊盘 5mm 以上,以便可以采用掩模夹具进行局部波峰焊。
注:其中间隙一般指不同元器件焊盘间的间隙,器件体大于焊盘时,指器件体的间隙)设计规范的附录C丝印字符大小参考值)设计规范的附录F 器件封装制作要求器件封装制作要求:。
沃得冲床点检表
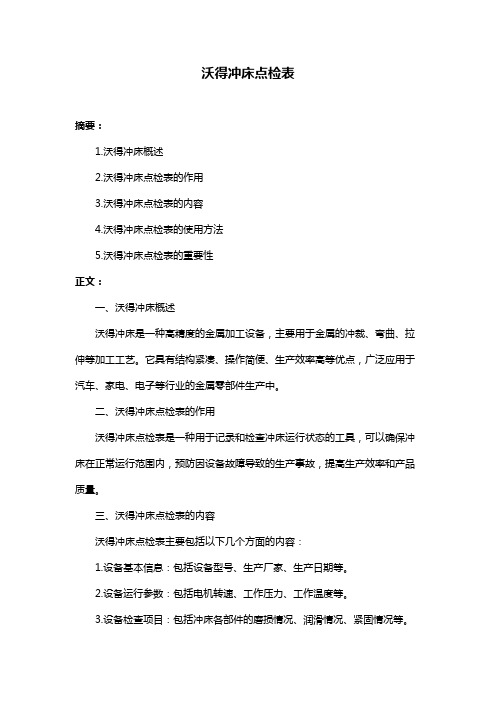
沃得冲床点检表
摘要:
1.沃得冲床概述
2.沃得冲床点检表的作用
3.沃得冲床点检表的内容
4.沃得冲床点检表的使用方法
5.沃得冲床点检表的重要性
正文:
一、沃得冲床概述
沃得冲床是一种高精度的金属加工设备,主要用于金属的冲裁、弯曲、拉伸等加工工艺。
它具有结构紧凑、操作简便、生产效率高等优点,广泛应用于汽车、家电、电子等行业的金属零部件生产中。
二、沃得冲床点检表的作用
沃得冲床点检表是一种用于记录和检查冲床运行状态的工具,可以确保冲床在正常运行范围内,预防因设备故障导致的生产事故,提高生产效率和产品质量。
三、沃得冲床点检表的内容
沃得冲床点检表主要包括以下几个方面的内容:
1.设备基本信息:包括设备型号、生产厂家、生产日期等。
2.设备运行参数:包括电机转速、工作压力、工作温度等。
3.设备检查项目:包括冲床各部件的磨损情况、润滑情况、紧固情况等。
4.设备维护记录:包括上次维护时间、维护内容、维护人员等。
四、沃得冲床点检表的使用方法
1.定期检查:按照规定周期进行设备检查,如每天、每周、每月等。
2.详细记录:对于检查中发现的问题,应详细记录在点检表上,并及时进行处理。
3.分析总结:定期对点检表中的数据进行分析,总结设备的运行状况,预测设备的使用寿命,为设备的维护和管理提供依据。
五、沃得冲床点检表的重要性
沃得冲床点检表对于保证设备的正常运行、提高生产效率、降低维修成本、确保产品质量具有重要意义。
工艺纪律检查表

检查 项目 检查日期: 检查人: 插件 插件 补焊 补焊 加工 波峰 组装 组装 老化 检查明细 分数 A拉 B拉 A拉 B拉 台 焊 A拉 B拉 物料 新进员工有无岗前培训记录 2分 有无定刚定位分布图 5分 有无按定岗定全图定岗定员 5分 员工厂牌是否挂在拉上 2分 员工坐姿是否端正、有无工 5分 作懒散状况 员工离岗时是否带有离岗证 2分 员工未配带静电环 2分 员工是否有聊天/嘻笑情况 2分 设备仪器是否有故障,未及 时修理,导致影响产品质量 3分 或产量 静电环、电烙铁未有点检记 2分 录 波峰焊温度是否及时测量、 2分 记录 仪器设备是否按保养计划保 5分 养、点检 仪器是否有校验标识卡 2分 外箱是否有合格标签 2分 对于特采物料是否有对应的 5分 外理方法 物料摆放是否整齐 2分 是否有严重堆机现象 3分 物料、产品区域标识是否清 2分 楚 物料、产品是否按区域摆放 2分 物料是否有混用现象 5分 半成品是否有混料现象 5分 组装拉用半成品是否有IPQC 5分 抽查签字 生产现场是否挂有与生产产 3分 品对应的SOP 生产排拉是否按照SOP来排 3分 作业员的作业方法是否与 2分 SOP一致 现场生产的产品是否符合工 2分 艺要求 现场生产的产品测试方法是 3分 否符合测试要求 产品摆放的方法是否正确 3分 QC位的报表记录是否及时、 3分 准确 半成品测试是否有做记号 2分 不良品是否有标识、隔离、 3分 装在红色不良盒内 生产现场是否干净整洁 3分 区域划分是否明确、产品摆 3分 放区域是否正确 合计: 100分
人
机
料
法
环
备注:上述各项,如到即得满分,如未做到即行0分。
备注
CNC编程和制造评审点检表
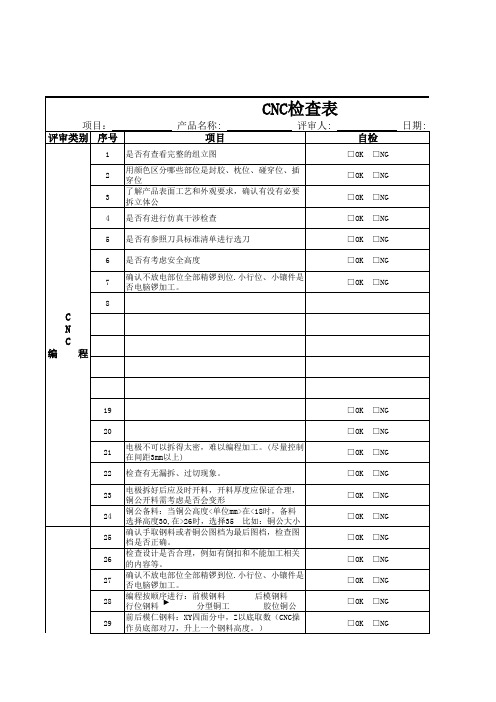
□OK □NG
6 是否有考虑安全高度
7
确认不放电部位全部精锣到位.小行位、小镶件是 否电脑锣加工。
8
C N C 编程
□OK □NG □OK □NG
年月日
19
20
21
电极不可以拆得太密,难以编程加工。(尽量控制 在间距3mm以上)
22 检查有无漏拆、过切现象。
23
电极拆好后应及时开料,开料厚度应保证合理, 铜公开料需考虑是否会变形
57 检查模拟刀路路径是否适当、是否安全。
58 检查工件预留量是否适当。
59 检查切削S、F参数是否适当。
60 检查程序单图的X、Y、 Z轴方向是否标示清楚。
61 修改过的程式单是否有跟编程人员确认?
62 修(改)模件程序单是否有更新
63
钢料在装夹前是否已将工件毛刺去除干净和消 磁?
64
钢料装夹时应将工件的基准角按程式单的标示方 向进行装夹
C
操 机作
业
70 71
钢料工件放置后,是否有用百分表校正工件的XY 、YZ、XZ平面? 钢料,铜料分中后是否有检查一次工件是否分 错?
72
将工件坐标输入对应的工件坐标系,抄入后检查 是否抄错。
73 装刀前检查刀具的刀尖刃口是否完整。
74
装刀时应先用干净的布碎将刀具、锁咀、刀头、 主轴锥孔擦干净。
75
50
部 外小 观骨 电位 极加 火工 花而 间影 隙响 是整 否个有组适合量电加极大的,火保花证间模隙仁单 边留铁用来抛光或喷涂。
51
字体过小时是否有单独做刻字电极,然后再用整 体精公电极加工?
52
铜公程序做完以后,是否有检查加工工艺是否合 理,加工部位是否有漏,参数是否设置正确。火
加工工序过程审核检查表

2分 作业指导书
查有温度记录
2
2 生产/仓库环境是否能满足需要
2分 温湿度,接地防护等
满足
2
环 3 达不到环境要求时是如何应对
2分 作业指导书
产线知会工艺工程师 2
4 人员是否了解环境对生产的影响
2分 询问
了解
2
5 是否有应急计划
2分 应急管理计划
是
2
1 是否配备了足够的测量仪器
2分 测量仪器清单\作业指导书
加工工序过程审核检查表ຫໍສະໝຸດ 检查项目序号 审核内容
生产阶段 作业工序
玻壳/绕丝/定型/套钼套
需提供资料
审核结果
得分
1 是否有明确岗位设置
2分 人员登记矩阵图表
岗位明确,有上岗证 2
2 是否清楚岗位职责 人 3 是否经过培训具备能力
4 是否有激励机制
2分 岗位说明书
有岗位说明书
2
2分
查培训要求、增训实施、培训记 录
2分 不合格品控制程序 70分
实际得分:95.71
纠正措施有记录 合计
评价结论
2 67
符合
审核员:
陪同人员:
受审部门确认:
备注:1、有文件,文件与操作一致,得2分 2、有文件,文件不符合操作,得1分 3、无文件,无操作指引,得0分
是否符合 符合 符合 符合 符合 符合 符合 符合 符合 符合 符合 符合 符合 符合 符合 符合 符合 符合 符合 符合 符合 符合 符合 符合 符合 符合 符合 符合 符合 符合
需提供资料
审核结果
得分
1 是否对过程进行监控
2 是否恰当使用统计过程
改 进
3 过程能力是否足够
工艺纪律检查点检表模板

序号单位 检查内容 加工现场有图纸料单 及工艺流程卡片填写 完整 测量工具精准合格 收集计划、图纸完善 下转自检工艺卡片上 面签名 图纸与模具对应 材料不许有锈蚀、沙 土、脚印、划伤、波 浪、水迹 零件摆放、转运符合 工艺要求 后工序需电镀件应用 防护材料进行分隔 备料是否按料单工艺 要求 刀具与料厚间隙相配 合 毛刺修磨是否符合要 1 下料 求(操作、工件毛 刺) 现场模具摆放不能摞 放、裸放于地 模具上不许有锈迹、 水、铁屑、异物等 弯曲刀槽与料厚相符 模具对接口无产生弯 曲接刀的塌角不良 弯曲后零件无明显的 拼角、角度、变形不 良 回头弯内及打死边内 的保护膜按要求进行 去除 对电镀件、不锈钢、 敷铝锌板、镀锌板、 耐指纹板进行隔离防 护 劳动防护用品穿戴齐 全
月
日工艺纪律检;不符合的填写现场状况 责任人及 冲床 剪板 折弯 九折 区域 考核金额
机加工审核检查表

21 管理层
与最高管理层交流,了解组织对内外环境的分析,相关方对企业的期望或 要求,为完成质量环境安全方针、目标采取的措施,以及在持续改进方面 所做的工作,管理评审
GB/T19001-2016 5.2.2,7.3 7.4 5.3 7.2,7.1.2
7.1.3 7.1.4
对应条款 GB/T24001-2016
11
现场观察操作人员是否按规定进行首检、互检与专检,并做好检验记录 (记住本批产品及原材料)
12
现场观察操作人员是否按规定做好产品的防护、以及合格品、不合格品、 废的消防器材是否按期进行检查,讯问操作人员如何使用消防器 材?是否进行培训,并根据需要查询记录
根据操作人员使用的原材料,到仓库检查此原材料是否贯彻了先入先出的 14 原则?并同时现场观察物料的管理水平,如帐卡物是否一致?物料标示、
18 根据销售合同,查研发设计部的研发设计条款及设计变更,并查看是否考 研发部 虑了从生命周期的不同阶段考虑了环境、安全因素
19 质量部
根据操作者及使用的测量工具,到质量部查工具台帐及检测报告及周期内 的质量绩效情况(是否有改进),产品放行情况,让步接受情况(降 低),并同时检查环境、安全因素,内部质量审核
7.2,8.1,8.2 6.1,8.5.2,8.5.3,8.5.4
8.4,9.1.3
8.1
8.2,8.3,8.5.4,8.5.5 9.1.2,9.1.3
8.1
8.3,8.5.6
8.1
7.1.5,8.6,8.7 9.1.1,9.1.3,9.2,10.2,10.3
8.1
4.4.2,4.4.6,4.4.7 4.4.6 4.4.6 4.4.6 4.4.6
20 到操作工为例,人事部门查岗位职责、年度培训的编制情况,人员能力的 人事部 确认情况,培训效果的验证情况,关键岗位人员的流失情况
生产过程5M1E检查表
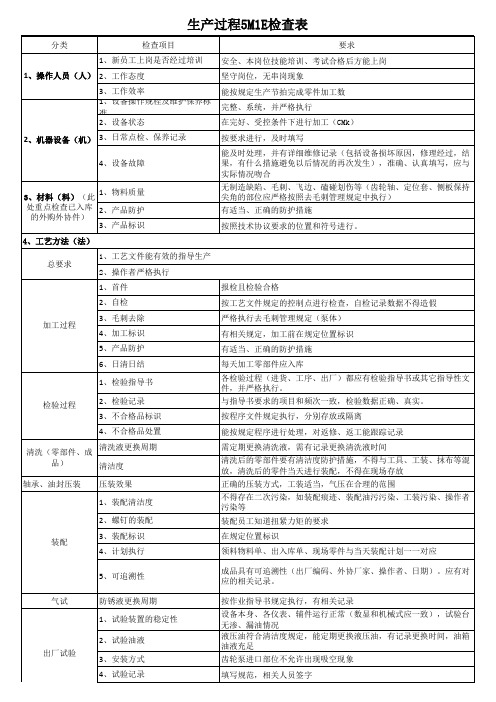
4、工艺方法(法)
总要求
1、工艺文件能有效的指导生产 2、操作者严格执行
1、首件
报检且检验合格
2、自检
按工艺文件规定的控制点进行检查,自检记录数据不得造假
加工过程
3、毛刺去除 4、加工标识
严格执行去毛刺管理规定(泵体) 有相关规定,加工前在规定位置标识
检验过程
5、产品防护 6、日清日结 1、检验指导书 2、检验记录 3、不合格品标识
按作业指导书规定执行,有相关记录 设备本身、各仪表、辅件运行正常(数显和机械式应一致),试验台 无渗、漏油情况 液压油符合清洁度规定,能定期更换液压油,有记录更换时间,油箱 油液充足 齿轮泵进口部位不允许出现吸空现象
填写规范,相关人员签字
5、不合格产品的处置
1、外观
喷漆包装 产品标识
2、外联接 3、标识位置
4、出厂编码
5、生产环境(环) 生产现场
6、测量(测) 检验设备、计量器具
分开存放,原因清楚,后续处理到位 非加工表面无磕碰、划伤现象。无掉漆、漏喷现象,无毛刺、锈迹、 铸件表面无凸起 符合技术协议或联接尺寸图
按指导书、标识规定、产品图纸要求执行
具有唯一性、对应性、正确性
符合5S标准(按具体的5S推进计划和要求进行检查)
2、机器设备(机) 3、日常点检、保养记录 4、设备故障
3、材料(料)(此 1、物料质量 处重点检查已入库 2、产品防护 的外购外协件)
3、产品标识
按要求进行,及时填写
能及时处理,并有详细维修记录(包括设备损坏原因,修理经过,结 果,有什么措施避免以后情况的再次发生),准确、认真填写,应与 实际情况吻合 无制造缺陷、毛刺、飞边、磕碰划伤等(齿轮轴、定位套、侧板保持 尖角的部位应严格按照去毛刺管理规定中执行) 有适当、正确的防护措施
铸造工序工艺纪律检查表

工位
序号检查内容
配分扣分得分
扣分原因
1铸件检验是否执行铸件检验规程52
检验现场铸件状态、标识是否清楚53标识牌填写是否正确,齐全54不同状态的铸件是否分类摆放55是否按规定填写合格单、废品单56是否按规定进行设备点检
57保管好检具,没有损坏丢失情况发生51入厂原材料是否符合进行检查52
需要存储的样块是否按规定时间存储53需要存储的样块是否标识清楚54电炉浇注监控是否正常使用
55检查报告和质保书是否及时符合工艺要求56试样模的准备及时,没有影响发货情况57试样加工符合图纸要求51
生产现场工艺文件齐全62工艺文件有无损坏、缺页和丢失63操作人员是否经过培训,有无培训记录64有无违反操作规程野蛮操作现象65
生产过程记录是否符合规定
6100
检查人员:
组长:
检验工序工艺纪律检查评分表
合计
铸件检验35分
材料检验35分
培训文件30分
B-JS-30-A
检查日期:年
月
日。
现场工艺纪律检查表 -
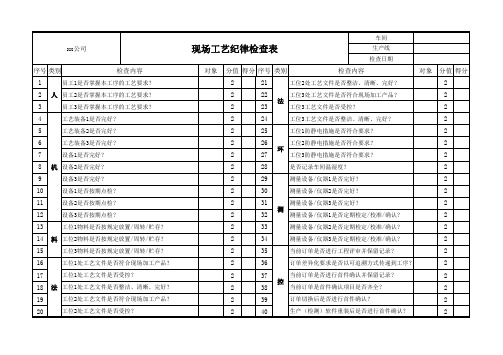
12
设备3是否按期点检?
13
工位1物料是否按规定放置/周转/贮存?
14 料 工位2物料是否按规定放置/周转/贮存?
15
工位3物料是否按规定放置/周转/贮存?
16
工位1处工艺文件是否符合现场加工产品?
17
工位1处工艺文件是否受控?
18 法 工位1处工艺文件是否整洁、清晰、完好?
19
工位2处工艺文件是否符合现场加工产品?
2
2
34
测量设备/仪器3是否定期检定/校准/确认?
2
2
35
当前订单是否进行工程评审并保留记录?
2
2
36
订单差异化要求是否以可追溯方式传递到工序?
2
2
37
当前订单是否进行首件确认并保留记录?
2
控
2
38
当前订单是首件确认项目是否齐全?
2
2
39
ቤተ መጻሕፍቲ ባይዱ
订单切换后是否进行首件确认?
2
2
40
生产(检测)软件重装后是否进行首件确认?
2
2
26
工位2防静电措施是否符合要求?
2
环
2
27
工位3防静电措施是否符合要求?
2
2
28
是否记录车间温湿度?
2
2
29
测量设备/仪器1是否完好?
2
2
30
测量设备/仪器2是否完好?
2
2
31
测量设备/仪器3是否完好?
2
测
2
32
测量设备/仪器1是否定期检定/校准/确认?
2
2
33
测量设备/仪器2是否定期检定/校准/确认?
金属切削机床铣削加工安全检查表范本(2篇)
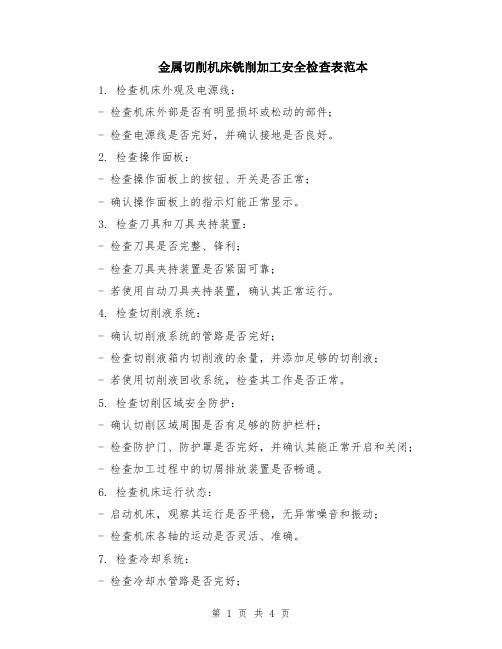
金属切削机床铣削加工安全检查表范本1. 检查机床外观及电源线:- 检查机床外部是否有明显损坏或松动的部件;- 检查电源线是否完好,并确认接地是否良好。
2. 检查操作面板:- 检查操作面板上的按钮、开关是否正常;- 确认操作面板上的指示灯能正常显示。
3. 检查刀具和刀具夹持装置:- 检查刀具是否完整、锋利;- 检查刀具夹持装置是否紧固可靠;- 若使用自动刀具夹持装置,确认其正常运行。
4. 检查切削液系统:- 确认切削液系统的管路是否完好;- 检查切削液箱内切削液的余量,并添加足够的切削液;- 若使用切削液回收系统,检查其工作是否正常。
5. 检查切削区域安全防护:- 确认切削区域周围是否有足够的防护栏杆;- 检查防护门、防护罩是否完好,并确认其能正常开启和关闭;- 检查加工过程中的切屑排放装置是否畅通。
6. 检查机床运行状态:- 启动机床,观察其运行是否平稳,无异常噪音和振动;- 检查机床各轴的运动是否灵活、准确。
7. 检查冷却系统:- 检查冷却水管路是否完好;- 检查冷却液箱内冷却液的余量,并添加足够的冷却液;- 检查冷却系统的温度和压力是否在正常范围内。
8. 检查机床润滑系统:- 确认润滑油箱内润滑油的余量,并添加足够的润滑油;- 检查润滑系统管路是否完好;- 检查润滑系统的工作是否正常,无异常的润滑点。
9. 检查电气系统:- 检查电气线路是否完好,无短路或接触不良;- 检查电气设备的接地是否良好;- 若使用变频器进行控制,检查其工作是否正常。
10. 检查运输锁定装置:- 检查运输锁定装置是否已全部解除。
11. 检查紧固件:- 检查机床上的紧固件是否全部紧固可靠。
12. 检查安全标识:- 检查机床上的安全标识是否清晰可见;- 确认操作人员是否了解并遵守相应的安全规范。
以上为金属切削机床铣削加工安全检查表范本,详细检查内容,请根据具体机床的型号和使用情况进行相应的调整和补充。
请在使用任何机床之前,先进行安全检查,确保操作人员的安全。
工艺纪律检查(装配、包装组)
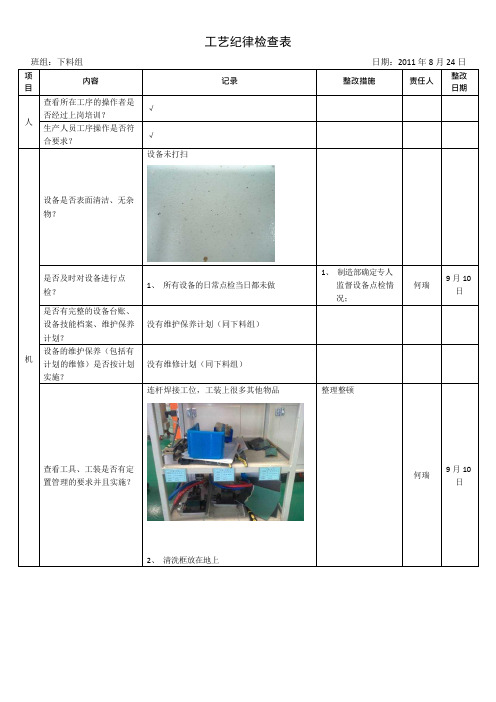
无标识的产品?
日
产品放置是否定置整齐存
放?
√
产品是否按规定的标识并
区分放置?
√
测
是否进行首末件检测?
√
产品首件是否标识并单独
存放?
/
是否按要求填写检验记
录?
√
是否对产品进行了性能检查(强度试验、撕裂试
验)?
/
对待检品、返修品、废品是否有醒目标识,并隔离
存放?
/
注:检测的内容覆盖所有的班组。
工艺纪律检查表
班组:下料组日期:2011年8月24日
项
目
内容
记录
整改措施
责任人
整改
日期
人
查看所在工序的操作者是
否经过上岗培训?
√
生产人员工序操作是否符
合要求?
√
机
设备是否表面清洁、无杂物?
设备未打扫
是否及时对设备进行点检?
1、 所有设备的日常点检当日都未做
1、 制造部确定专人监督设备点检情
况;
何瑞
9月10
√
料
库房的零件是否经检验合
格后入库?
同下料组(库房项目)
库房零件是否有明确的存
放规则?
同下料组(库房项目)
库房零件是否有明确标
识?
√
转入本工序的原料或半成品,是否进行了明确的标
识?
√
所加工出的半成品、成品
是否有明确的标识?
√
生产物料信息管理有效,
质量问题可追溯。
√
法
查看现场作业文件(图纸、工艺、参数卡)是否齐全
日
是否有完整的设备台账、设备技能档案、维护保养
计划?