尼龙注塑常见缺陷和解决方法
尼龙注塑工艺容易产生的14种不良现象及对应解决方案大全

尼龙注塑工艺容易产生的14种不良现象及对应解决方案大全尼龙塑料制品尺寸精确,适用于大量生产与形状复杂产品等成型加工领域。
注塑工艺简单易操作,但也存在很多因人工操作,或者注塑设备,原料等因素导致的问题。
对于尼龙注塑工艺容易产生的一些不良现象,我们应当如何解决呢?以下是14种易产生的不良现象及对应的解决方案。
1. 尼龙塑料制品打不满原因分析:1.模具温度低2.注入给料筒温度过低3.给料量不够4.尼龙塑料制品质量超过注塑机的最大注塑量5.注入压力太小,注入速度比较慢6.喷嘴温度低,物料在出料口冷凝(干尖)7.柱塞或螺杆退回太早,注入时间不够8.浇口太小、太薄或太长9.模具没有排气孔或位置不当等原因解决方案:1.提升给料筒温度2.减少模具冷却水,提升模温3.增加给料量4.选择适合尼龙塑料制品成型注入量的设备5.适当提升注入压力6.提升喷嘴温度7.保证合适的注入时间和保压时间8.加大模具浇口9.模具需合理设计排气装置2. 溢流或出现飞边原因分析:1.注入压力太大2.锁模机构磨损,锁模力太小3.料温太高4.模具的接触面不平,模具磨损变形5.模具接触平面落入异物1.降低注入压力2.修理设备,提升锁模力3.降低给料筒温度4.修理模具5.及时清理模具中的异物3. 有凹痕(由于收缩率大造成塌坑)原因分析:1.浇口及料道太小2.料温太高3.模具温度太高4.给料量不足5.注入及保压时间不够6.注塑尼龙制品太厚或薄厚悬殊解决方案:1.扩大浇口2.降低给料筒温度3.有效冷却模具4.调整给料量5.加长保压时间6.合理设计模具,壁厚应尽量均匀一致尼龙毛刷条4. 有熔接痕(合料线)原因分析:1.料温太低2.注入压力太低,注入速度太慢3.模具温度太低4.浇口较多5.尼龙塑料制品壁厚不均6.脱模剂用量较多7.模腔排气不佳解决方案:1.提升给料筒温度2.提升注入压力及速度3.提升模具温度4.适当减少浇口数量5.提升模具制作精度6.减少脱模剂用量7.增强排气5. 尼龙塑料制品表面有波纹原因分析:1.料温太低、树脂黏度大,流动性差2.注入压力小,速度太慢3.模具温度低4.模具浇口太小解决方案:1.提升给料筒温度2.提升注入压力3.提升模具温度4.加大浇口6. 有气泡和真空泡原因分析:1.原料中含有水分、溶剂或其他的挥发物2.料温太高,受热时间长3.注入压力太小4.尼龙塑料制品太厚,表里冷却速度不同,内部产生真空泡.5.模具温度太低.6.注入时间太短.解决方案:1.成型前先将原料进行干燥2.降低给料筒温度3.提升注入压力4.加大流道及浇口尺寸5.适当提升模具温度6.延长注入时间7. 有黑点及条纹原因分析:1.塑料分解出现黑色斑点2.模具没有排气孔或排气位置不当3.柱塞与给料筒间隙太大,粒料在间隙中受热时间过长分解而黑,或是由于坚硬颗粒使螺杆磨损而出现黑点.解决方案:1.合理控制工艺温度,避免塑料过热分解2.合理开设排气孔3.及时维修机器,增加料缸冷却尼龙拉链8.有银丝及斑纹原因分析:1.物料分解后的产物进入模腔,以致出现斑纹2.原料中含水分过高,水汽混在料中产生银丝3.原料中含有易挥发物解决方案:1.降低给料筒温度2.原料使用前进行预热干燥3.成型前对原料进行干燥、预热9.变色原因分析:1.料温过高,颜色分解而致变色2.塑料在给料筒中停留时间过长,受热分解3.润滑剂涂得过多解决方案:1.选择耐高温的颜色粉2.减少物料在给料筒中的停留时间3.减少润滑剂的用量10.变形、翘曲原因分析:1.冷却时间短,尼龙塑料制品未完全定型2.尼龙塑料制品厚薄不均,冷却时收缩不均3.注入两次,注入压力太大4.尼龙塑料制品顶杆位置不当,顶出时受力不均5.物料温度低或塑化温度不均解决方案:1.延长冷却时间或降低模型温度2.尼龙塑料制品设计力求合理3.降低第二注入压力,缩短保压时间4.合理布置顶杆位置5.提升给料筒温度11.尼龙塑料制品出现裂纹原因分析:1.模具太冷2.尼龙塑料制品在模具内冷却时间过长,塑料和金属嵌件收缩不同所致3.尼龙塑料制品顶出装置倾斜或不平衡4.顶出杆截面积太小或数量太少,分布不当5.尼龙塑料制品斜度不够,脱模困难解决方案:1.提升模具温度2.适当减少冷却时间,或对金属嵌件进行预热3.调整顶出位置4.正确设计定出位置5.尼龙塑料制品设计合理,要有一定斜度尼龙滑轮12.黏模(脱模困难)原因分析:1.模腔表面光洁度不够2.模具斜度不够(特别是形状较深尼龙塑料制品)3.注入压力较大,物料进入模具镶块边的缝隙4.模具温度高低和冷却时间长短不适当5.模具磨损划伤造成尼龙塑料制品飞边,脱模困难6.模具排气不当7.原料本身就黏模解决方案:1.提升模腔光洁度,最好表面镀铬2.增加模具倾斜度3.修理模具4.型芯面难脱模时可提升模具温度、缩短冷却时间,型腔中央难脱模时可降低模具温度、增加冷却时间。
注塑缺陷原因分析与解决方案
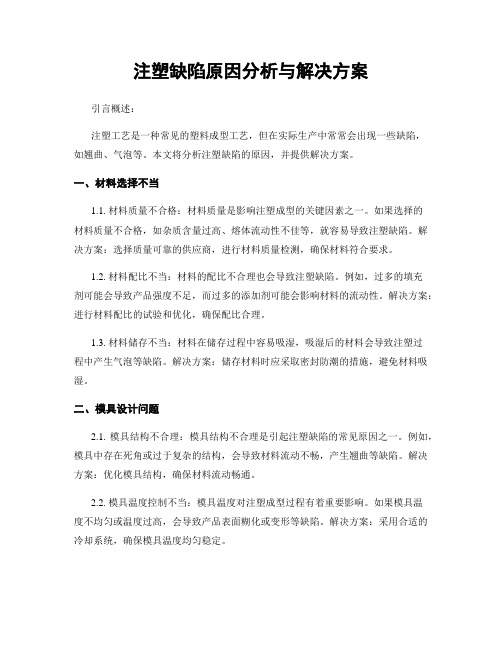
注塑缺陷原因分析与解决方案引言概述:注塑工艺是一种常见的塑料成型工艺,但在实际生产中常常会出现一些缺陷,如翘曲、气泡等。
本文将分析注塑缺陷的原因,并提供解决方案。
一、材料选择不当1.1. 材料质量不合格:材料质量是影响注塑成型的关键因素之一。
如果选择的材料质量不合格,如杂质含量过高、熔体流动性不佳等,就容易导致注塑缺陷。
解决方案:选择质量可靠的供应商,进行材料质量检测,确保材料符合要求。
1.2. 材料配比不当:材料的配比不合理也会导致注塑缺陷。
例如,过多的填充剂可能会导致产品强度不足,而过多的添加剂可能会影响材料的流动性。
解决方案:进行材料配比的试验和优化,确保配比合理。
1.3. 材料储存不当:材料在储存过程中容易吸湿,吸湿后的材料会导致注塑过程中产生气泡等缺陷。
解决方案:储存材料时应采取密封防潮的措施,避免材料吸湿。
二、模具设计问题2.1. 模具结构不合理:模具结构不合理是引起注塑缺陷的常见原因之一。
例如,模具中存在死角或过于复杂的结构,会导致材料流动不畅,产生翘曲等缺陷。
解决方案:优化模具结构,确保材料流动畅通。
2.2. 模具温度控制不当:模具温度对注塑成型过程有着重要影响。
如果模具温度不均匀或温度过高,会导致产品表面糊化或变形等缺陷。
解决方案:采用合适的冷却系统,确保模具温度均匀稳定。
2.3. 模具磨损严重:模具长时间使用后会出现磨损,磨损严重的模具会导致产品尺寸不准确或表面粗糙等缺陷。
解决方案:定期检查和维护模具,及时更换磨损严重的模具部件。
三、注塑工艺参数设置不当3.1. 注射压力过高或过低:注射压力是影响注塑成型的关键参数之一。
如果注射压力过高,会导致产品变形或开裂,而注射压力过低则会导致产品表面光洁度不高。
解决方案:根据产品要求和材料特性,合理设置注射压力。
3.2. 注射速度不合理:注射速度对产品的充填和冷却过程有着重要影响。
如果注射速度过快,会导致产品内部产生气泡或短射,而注射速度过慢则会导致产品表面瑕疵。
注塑产品缺陷产生原因及处理方法(五篇模版)

注塑产品缺陷产生原因及处理方法(五篇模版)第一篇:注塑产品缺陷产生原因及处理方法注塑产品缺陷产生原因及处理方法在注塑成型加工过程中可能由于原料处理不好、制品或模具设计不合理、操作工没有掌握合适的工艺操作条件,或者因机械方面的原因,常常使制品产生注不满、凹陷、飞边、气泡、裂纹、翘曲变形、尺寸变化等缺陷。
对塑料制品的评价主要有三个方面,第一是外观质量,包括完整性、颜色、光泽等;第二是尺寸和相对位置间的准确性;第三是与用途相应的机械性能、化学性能、电性能等。
这些质量要求又根据制品使用场合的不同,要求的尺度也不同。
生产实践证明,制品的缺陷主要在于模具的设计、制造精度和磨损程度等方面。
但事实上,塑料加工厂的技术人员往往苦于面对用工艺手段来弥补模具缺陷带来的问题而成效不大的困难局面。
生产过程中工艺的调节是提高制品质量和产量的必要途径。
由于注塑周期本身很短,如果工艺条件掌握不好,废品就会源源不绝。
在调整工艺时最好一次只改变一个条件,多观察几回,如果压力、温度、时间统统一起调的话,很易造成混乱和误解,出了问题也不知道是何道理。
调整工艺的措施、手段是多方面的。
例如:解决制品注不满的问题就有十多个可能的解决途径,要选择出解决问题症结的一、二个主要方案,才能真正解决问题。
此外,还应注意解决方案中的辨证关系。
比如:制品出现了凹陷,有时要提高料温,有时要降低料温;有时要增加料量,有时要减少料量。
要承认逆向措施的解决问题的可行性。
1.6.1 塑料成型不完整这是一个经常遇到的问题,但也比较容易解决。
当用工艺手段确实解决不了时,可从模具设计制造上考虑进行改进,一般是可以解决的。
一、设备方面:(1)注塑机塑化容量小。
当制品质量超过注塑机实际最大注射质量时,显然地供料量是入不敷出的。
若制品质量接近注塑机实际注射质量时,就有一个塑化不够充分的问题,料在机筒内受热时间不足,结果不能及时地向模具提供适当的熔料。
这种情况只有更换容量大的注塑机才能解决问题。
注塑成型常见不良现象及处理措施

注塑成型常见不良现象及处理措施注塑成型常见的不良现象有以下几种:
1. 短射:指注塑料进模型中未充满模腔,导致产品缺陷。
处理措施:增加注射
压力、延长注射时间、增加料缸温度、增加模具温度、增加模具出料口直径等。
2. 气泡:指产品表面或者内部浮现气泡,影响产品质量。
处理措施:增加注射
压力、延长注射时间、增加模具温度、增加料缸温度、增加模具出料口直径、增加模具排气孔等。
3. 热熔线:指产品表面浮现细小的线状缺陷,通常是由于注射速度过快导致的。
处理措施:减小注射速度、增加模具温度、增加模具出料口直径等。
4. 毛刺:指产品表面浮现细小的凸起,通常是由于模具设计不合理或者模具磨
损导致的。
处理措施:修复模具、修改模具设计、增加模具温度、增加模具出料口直径等。
5. 缩水:指产品尺寸缩小,通常是由于注射压力不足或者冷却时间不足导致的。
处理措施:增加注射压力、延长冷却时间、增加模具温度等。
6. 毛洞:指产品表面或者内部浮现凹陷,通常是由于注射速度过快或者模具设
计不合理导致的。
处理措施:减小注射速度、修改模具设计、增加模具温度等。
处理不良现象的关键是找到问题的根源,然后针对性地采取相应的处理措施。
同时,注塑成型过程中的参数控制和模具维护也是关键的因素,需要进行定期检查和调整。
注塑产品常见缺陷

注塑产品常见缺陷注塑产品常见缺陷及其原因分析注塑产品在生产过程中可能会遇到各种缺陷,这些缺陷可能源于产品设计、模具制造、材料选择、注塑工艺等多个因素。
以下是一些常见的注塑产品缺陷及可能的原因分析:1.填充不足(缺料)这可能是由于注塑压力不足、注射时间过短、模具排气不良、浇口设计不合理等原因造成的。
解决这个问题的方法包括增加注塑压力、延长注射时间、优化模具排气设计、改进浇口位置等。
2.溢料(毛边)溢料通常是由于注射压力过高、浇口设计不当、模具磨损等原因造成的。
解决溢料问题的方法包括降低注塑压力、优化浇口设计、修复模具磨损等。
3.气泡(气孔)气泡可能是由于塑料在模具中未完全填满、气体未完全排出、注射速度过快等原因造成的。
解决气泡问题的方法包括降低注射速度、增加冷却时间、优化模具设计等。
4.变形变形可能是由于产品结构不合理、冷却不均匀、模具温度波动等原因造成的。
解决变形问题的方法包括优化产品结构设计、改善冷却条件、稳定模具温度等。
5.银纹(流纹)银纹可能是由于塑料流动不均匀、模具温度过低、注射速度过快等原因造成的。
解决银纹问题的方法包括优化注射条件、提高模具温度、降低注射速度等。
6.裂纹(龟裂)裂纹可能是由于产品结构设计不合理、材料韧性不足、注射压力过高等原因造成的。
解决裂纹问题的方法包括优化产品结构设计、更换韧性更好的材料、降低注射压力等。
7.翘曲(扭曲)翘曲可能是由于产品结构设计不合理、模具温度不均匀、注射压力过低等原因造成的。
解决翘曲问题的方法包括优化产品结构设计、改善冷却条件、提高注射压力等。
8.冷块(冷凝物)冷块可能是由于塑料在冷却过程中速度过快、模具温度过低等原因造成的。
解决冷块问题的方法包括降低冷却速度、提高模具温度等。
9.喷射痕迹(蛇形纹)喷射痕迹可能是由于注射速度过快、浇口设计不当等原因造成的。
解决喷射痕迹问题的方法包括降低注射速度、优化浇口设计等。
10.颜色分布不均(色差)颜色分布不均可能是由于材料混合不均匀、注塑条件不稳定等原因造成的。
注塑缺陷原因分析与解决方案
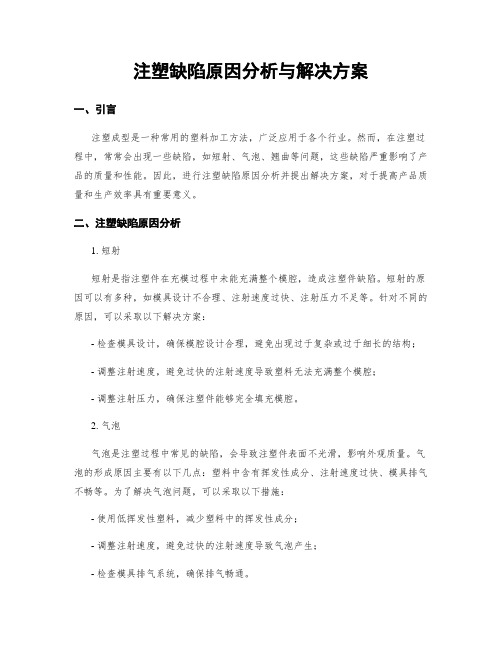
注塑缺陷原因分析与解决方案一、引言注塑成型是一种常用的塑料加工方法,广泛应用于各个行业。
然而,在注塑过程中,常常会出现一些缺陷,如短射、气泡、翘曲等问题,这些缺陷严重影响了产品的质量和性能。
因此,进行注塑缺陷原因分析并提出解决方案,对于提高产品质量和生产效率具有重要意义。
二、注塑缺陷原因分析1. 短射短射是指注塑件在充模过程中未能充满整个模腔,造成注塑件缺陷。
短射的原因可以有多种,如模具设计不合理、注射速度过快、注射压力不足等。
针对不同的原因,可以采取以下解决方案:- 检查模具设计,确保模腔设计合理,避免出现过于复杂或过于细长的结构;- 调整注射速度,避免过快的注射速度导致塑料无法充满整个模腔;- 调整注射压力,确保注塑件能够完全填充模腔。
2. 气泡气泡是注塑过程中常见的缺陷,会导致注塑件表面不光滑,影响外观质量。
气泡的形成原因主要有以下几点:塑料中含有挥发性成分、注射速度过快、模具排气不畅等。
为了解决气泡问题,可以采取以下措施:- 使用低挥发性塑料,减少塑料中的挥发性成分;- 调整注射速度,避免过快的注射速度导致气泡产生;- 检查模具排气系统,确保排气畅通。
3. 翘曲翘曲是指注塑件在冷却过程中由于内外表面温度差异引起的变形现象。
翘曲的原因主要有材料收缩率不一致、模具温度控制不当等。
为了解决翘曲问题,可以采取以下方法:- 选择具有一致收缩率的塑料材料,减少翘曲的可能性;- 控制模具温度,确保注塑件冷却均匀,避免温度差异导致翘曲。
三、解决方案的实施和效果评估在实施解决方案之前,需要进行充分的实验和测试,以验证方案的可行性和有效性。
在实施过程中,需要注意以下几点:1. 确保操作人员熟悉解决方案的具体步骤和操作要点;2. 根据实际情况,对解决方案进行适当的调整和优化;3. 对解决方案的实施效果进行评估,包括产品质量改善程度、生产效率提升等方面的指标。
通过实施解决方案,可以有效地解决注塑缺陷问题,提高产品质量和生产效率。
注塑缺陷原因分析与解决方案

注塑缺陷原因分析与解决方案一、引言注塑是一种常用的塑料加工方法,广泛应用于各个行业。
然而,在注塑过程中,可能会出现一些缺陷,例如短斑、气泡、翘曲等问题,这些缺陷会影响产品质量和使用寿命。
因此,对注塑缺陷的原因进行分析,并提出相应的解决方案,对于提高产品质量具有重要意义。
二、注塑缺陷原因分析1. 温度控制不当:注塑过程中,温度是一个关键因素。
如果温度过高或过低,都会导致注塑缺陷。
例如,温度过高会导致熔融物流动性增加,易产生短斑;温度过低会导致熔融物流动性降低,易产生翘曲。
2. 压力控制不当:注塑过程中,压力也是一个重要因素。
如果压力过高或过低,都会导致注塑缺陷。
例如,压力过高会导致短斑、气泡等缺陷;压力过低会导致产品密度不足,易产生翘曲。
3. 注塑模具设计问题:注塑模具的设计也会影响产品质量。
如果模具设计不合理,例如流道设计不良、冷却系统不完善等,都会导致注塑缺陷的产生。
4. 塑料材料选择不当:不同的塑料材料具有不同的熔点、流动性等特性。
如果选择的塑料材料与产品要求不匹配,也会导致注塑缺陷。
例如,选择的塑料材料熔点过高,容易产生短斑;选择的塑料材料流动性不足,容易产生翘曲。
5. 操作人员技术水平不高:注塑过程需要操作人员具备一定的技术水平。
如果操作人员技术水平不高,不了解注塑工艺的要点,也会导致注塑缺陷的产生。
三、注塑缺陷解决方案1. 温度控制方案:合理控制注塑过程中的温度,根据塑料材料的特性和产品要求,调整熔融温度和模具温度。
可以通过使用温度传感器和温度控制器来实时监测和调整温度,确保温度在合适的范围内。
2. 压力控制方案:合理控制注塑过程中的压力,根据塑料材料的特性和产品要求,调整注射压力和保压压力。
可以通过使用压力传感器和压力控制器来实时监测和调整压力,确保压力在合适的范围内。
3. 注塑模具设计方案:优化注塑模具的设计,确保流道设计合理、冷却系统完善。
可以通过使用CAD软件进行模具设计和模拟分析,优化模具结构,减少缺陷的产生。
尼龙注塑加工工艺及其问题

尼龙注塑加工工艺及其问题PA—聚酰胺、也称尼龙,是一大类酰胺型聚合物的统称。
最常见的有 PA6 、 PA66 、 PA1010 。
最近,随着 I T 业的发展,一种新型的聚酰胺—PA46 的使用量剧增,它用于代替 LCP (液晶聚合物)生产电脑上的插件。
由于 PA 具有良好的机械性能,韧性好、抗冲击、耐磨、自润滑、阻燃、绝缘等特点,所以被广泛用于汽车、机械、电子、仪表、化工等多个领域,如齿轮、滑轮、轴承、叶轮、衬套、容器、刷子、拉链等。
PA6 、 PA66 、 PA46 都属脂肪族聚酰胺,是线性聚合物,其分子结构中有极强极性的酰胺基,所以具有高度的结晶能力。
PA 制品的性能依赖于其结晶形态及结晶度。
而加工条件对结晶形态和结晶度有影响,加工条件不同, PA 制品的结晶变化可达 40% ,制品冷却慢,结晶度高,且形成较大尺寸的结晶形态。
吸水性对其结晶度也有影响。
另外, PA 在加工过程中由于流动、剪切作用会产生一定程度的取向,导致制品性能的各向异性,沿取向方向的强度优于非取向方向,取向也有利于结晶过程的进行,在模具设计时要考虑这个因素。
• PA 的性能•物理性能无※、无味、不霉烂、外观为半透明或透明,乳白色或淡黄色,密度 1.04-1.36 ,燃烧时放出特殊的蛋白味,火焰为蓝色上端呈黄色。
•机械性能刚韧性好,耐反复冲击震动,使用温度为– 40-100 ℃,耐摩擦、耐磨耗、自润滑,但抗蠕变性差,尺寸稳定性较差,可以通过加入玻璃纤维增强或与其他材料共混来克服此缺点。
•耐化学品性能及耐候性PA 的有机溶剂很少,乃化学性能良好, PA 的有机溶剂是甲酸、酚类化合物。
不同浓度的无机酸、碱、盐均可导致 PA 溶胀、溶解或水解。
在不受阳光照射的条件下,其耐老化性能良好,但在热作用、光照、辐射条件下老化快、制品变色、性能下降。
•加工性能•易吸湿,成型前必须进行干燥。
•熔点高,熔限窄,熔点分别为: PA6 : 215 ℃, PA66:255℃, PA46:290℃。
- 1、下载文档前请自行甄别文档内容的完整性,平台不提供额外的编辑、内容补充、找答案等附加服务。
- 2、"仅部分预览"的文档,不可在线预览部分如存在完整性等问题,可反馈申请退款(可完整预览的文档不适用该条件!)。
- 3、如文档侵犯您的权益,请联系客服反馈,我们会尽快为您处理(人工客服工作时间:9:00-18:30)。
1 、模具的脱模锥度不足,表面光洁 10 、脱 度不足 模困难 、 顶出 2、 脱模顶针的位置不当或直径过小 破裂 • 机筒温度设置不当 11 、下 • 机筒下料口处冷却不足 料困难或 • 螺杆、机筒设计不当 不下料
料困难或 不下料 • 法 1 、提高注射压力 2 、提高注射速度 3 、提高机筒温度 , 4 、在未填满的部位加排气孔 5 、扩大浇口尺寸或缩短浇口流道的距离 6 、检查过胶圈的磨损程度,更换 1 、增加熔胶量,提高注射压力 2 、提高机筒温度,提高注射速度 3 、提高模具温度 4 、充分排气 • 降低机筒温度、螺杆转速、背压 • 降低注射速度和注射压力 • 扩大浇口尺寸 • 开设或增加排气孔、槽 • 加强干燥,加长干燥时间或采用真空干燥 • 降低机筒温度、螺杆转速 • 降低注射速度和注射压力 • 检查材料中有无杂质 1 、提高注射压力 、 速度 、 机筒温度 、 模具温度 2 、更改浇口位置,使熔合纹出现在不受负荷或不显著的部位; 开设冷料井,使熔合纹处的冷料排出 1 、调整模具的温度控制,使其冷却均匀 2 、产品的设计尽量使其壁厚均匀 3 、降低注射压力和保压压力 4 、降低注射速度 1 、增加熔胶量,提高注射压力,延长注射时间 2 、充分干燥材料 3 、制品厚度不要超过 7—10MM 4 、降低机筒温度及模具温度 1 、提高模具温度,制品取出后浸入热水或放入烘箱中缓慢冷却 2 、降低注射速度,提高模具温度 1 、增加排气孔 2 、降低机筒温度 、 注射速度 3 、加大浇口 1 、加大脱模锥度,模具表面抛光 2 、增加顶针数量或加大顶针直径 3 、延长冷却时间,降低机筒温度 、 模具温度 适当提高机筒中段温度、降低后段温度 • 检查冷却水管有无堵塞 • 螺杆的加料段较长、螺槽较深、该处机筒拉槽
尼龙注塑常见缺陷和解决方法 缺陷 原因 1 、注射压力不足 2 、注射速度慢 1 、填充 3 、熔料温度低 不足 4 、排气不良 5 、浇口过小 6 、过胶圈磨损 1 、制品密度不足 2 、表面 2 、填充速度慢 无光泽 3 、模具温度低 4 、排气不良 • 熔料温度过高 3 、变色 • 注射速度过快 • 浇口过小 • 模具排气不良 干燥不足 • 熔料温度过高 • 注射速度过快 • 材料中有杂质 1 、熔料充模后冷却快引起
• 检查材料中有无尺寸较长的再生料、再生料的使用比例过大。
4 、银纹
5 、熔合 纹 2 、浇口位置开设不当 1 、制品冷却不均匀 6 、翘曲 2 、制品壁厚不均匀 3 、填充过度 4 、注射速度过快 • 制品密度不足 7 、收缩 • 熔料含有气体 、 凹陷 • 制品壁厚过厚 • 热收缩大 8 、内部 1 、制品冷却过快 裂纹 2 、残余应力 1 、排气不良 9 、烧焦 2 、熔料温度过高