圆形支座铸造工艺设计
圆筒铸造方案

圆筒铸造方案1. 引言本文档旨在提供一个圆筒铸造方案的详细描述,方便相关人员了解铸造过程的步骤和要求。
圆筒铸造是一种常见的铸造工艺,适用于制造各种圆筒形状的零部件。
本文将从铸模设计、原材料准备、熔炼操作、铸造工艺流程等多个方面进行介绍。
2. 铸模设计铸模设计是圆筒铸造的第一步,合理的铸模设计能够保证铸件的质量和尺寸精度。
下面是一些铸模设计的要点:•圆筒模具形状:圆筒模具应根据所需铸件形状进行设计,包括底部和顶部的开孔,以方便砂芯的设置和取出。
•砂芯设计:根据铸件的中空结构,需要在铸模中设置砂芯。
砂芯应具有足够的强度和耐高温性能。
•铸道和浇口设计:铸道和浇口的设计要考虑到金属液的流动和进入铸件的均匀性。
合理的铸道和浇口设计能够避免缺陷的产生。
3. 原材料准备在铸造前,需要准备好以下原材料:•铸造材料:常用的铸造材料包括铝合金、铜合金、铁合金等。
根据铸件的要求选择合适的材料。
•砂料:铸模中常用的砂料有石英砂、粘土等。
根据铸模的要求选择合适的砂料。
•砂芯材料:制作砂芯需要砂芯材料,通常使用粘土砂芯材料。
•熔炼材料:根据所选的铸造材料,需要准备相应的熔炼材料,例如铝合金需要准备铝锭。
4. 熔炼操作熔炼是将原材料熔化成金属液的过程,下面是熔炼操作的步骤:1.准备熔炉:根据所选的熔炼材料和熔炼方式,选择合适的熔炉。
确保熔炉干净,并根据需要预热。
2.称量和加入原材料:按比例称重所需的原材料,在炉内加入熔炼材料。
3.加热和熔化:启动熔炉,根据所选熔炼方式和材料的特性,进行适当的加热和熔化过程。
4.熔炼温度控制:根据所选材料的熔点和熔炼要求,控制熔炉温度。
5.除渣和净化:在熔炉中可能会产生杂质和渣滓,需要进行除渣和净化操作。
5. 铸造工艺流程铸造工艺流程是指从准备铸模到铸件冷却出模的整个铸造过程。
下面是圆筒铸造的典型工艺流程:1.铸模准备:根据前面的铸模设计,制作好铸模和砂芯,确保其完整和质量。
2.浸涂剂处理:在铸模和砂芯表面涂上一层浸涂剂,以增加其表面光滑度和耐高温性能。
铸造工艺设计说明书

铸造⼯艺设计说明书铸造⼯艺设计说明书课程设计:机械⼯艺课程设计设计题⽬:底座铸造⼯艺设计班级:机⾃1103设计⼈:学号:指导教师:张锁梅、贾志新前⾔学⽣通过设计能获得综合运⽤过去所学过的全部课程进⾏机械制造⼯艺及结构设计的基本能⼒,为以后做好毕业设计、⾛上⼯作岗位进⾏⼀次综合训练和准备。
它要求学⽣全⾯地综合运⽤本课程及有关选修课程的理论和实践知识,进⾏零件加⼯⼯艺规程的设计和机床夹具的设计。
其⽬的是:(1)培养学⽣综合运⽤机械制造⼯程原理课程及专业课程的理论知识,结合⾦⼯实习、⽣产实习中学到的实践知识,独⽴地分析和解决机械加⼯⼯艺问题,初步具备设计中等复杂程度零件⼯艺规程的能⼒。
(2)培养学⽣能根据被加⼯零件的技术要求,运⽤夹具设计的基本原理和⽅法,学会拟订夹具设计⽅案,完成夹具结构设计,进⼀步提⾼结构设计能⼒。
(3)培养学⽣熟悉并运⽤有关⼿册、图表、规范等有关技术资料的能⼒。
(4)进⼀步培养学⽣识图、制图、运算和编写技术⽂件的基本技能。
(5)培养学⽣独⽴思考和独⽴⼯作的能⼒,为毕业后⾛向社会从事相关技术⼯作打下良好的基础。
⽬录⼀、⼯艺审核 (1)1.数量与材料 (1)2.图样 (1)3.零件的结构性 (1)⼆、成形⼯艺设计 (1)1.确定⼯艺⽅案 (1)(1)浇注位置的选择 (2)(2)分型⾯的选择 (2)2.确定铸造⼯艺参数 (4)(1)机械加⼯余量和铸出孔 (4)(2)浇注位置的选择 (5)(3)拔模斜度 (5)(4)铸造收缩率 (6)3.砂芯设计 (6)4.浇注系统的设计 (6)5. 冷铁的设置 (6)三、⼼得体会 (7)⼀、⼯艺审核1、数量与材料由零件图可知,该零件结构⽐较简单,但是形状不是很规则,⼯作条件⼀般以承受压⼒为主,故要求该零件有良好的刚性和强度。
另外,根据零件图的要求,该底座零件为单件⼩批量⽣产,另外材料选⽤灰铸铁HT200,流动性较好,适于铸造。
2、图样该零件图给出了主视图、左视图、俯视图3个视图。
支座铸造工艺设计

支座铸造工艺设计1. 引言支座是一种常见的结构零件,广泛应用于桥梁、建筑物和机械设备等领域。
支座的质量和性能对于保证结构的稳定性和安全性至关重要。
支座的制造过程中的铸造工艺设计是确保支座质量的重要环节之一。
本文将就支座铸造工艺设计进行详细介绍,并探讨其关键步骤。
2. 材料选型支座通常是由钢铁材料铸造而成。
选择合适的材料对于支座的性能和寿命具有重要影响。
常用的支座材料有碳钢、合金钢和不锈钢等。
在材料选型上,需要考虑支座的使用环境、承载能力和使用寿命等因素。
材料的选用需要满足相关标准和规范的要求。
3. 铸造工艺设计铸造工艺设计是支座制造过程中至关重要的一环,它直接影响支座的质量和性能。
铸造工艺设计包括模具设计、熔炼、浇注、冷却和清理等多个步骤。
3.1 模具设计模具设计是支座铸造工艺设计的第一步。
模具的设计应满足支座形状和尺寸的要求,同时要考虑到铸造过程中的收缩和变形。
模具的设计需要考虑到易于制造和使用,并能保证支座的精度和表面质量。
常用的模具材料有铁、铝和砂等。
3.2 熔炼熔炼是将所选材料加热至熔点,使其转化为液态的关键过程。
在支座铸造工艺中,通常采用电炉或高频感应炉进行熔炼。
熔炼过程中需要控制炉温、保持合适的熔化时间,并添加合适的熔剂和熔化助剂,以提高铸件的熔化质量和纯度。
3.3 浇注浇注是将熔融金属倒入模具中的步骤。
在支座铸造过程中,浇注需要控制浇注速度和温度,以避免产生气孔和夹渣等缺陷。
浇注过程中需要确保熔融金属能够充分填满模具腔体,并尽量避免产生温度梯度,以减少应力和变形。
3.4 冷却铸造完成后,支座需要进行冷却过程。
冷却速度的控制对于支座的组织结构和性能具有重要影响。
较快的冷却速度可能导致铸件硬化过深,影响其力学性能;而较慢的冷却速度可能会产生过大的晶粒,导致铸件的强度下降。
因此,需要通过合理控制冷却速度来获得理想的支座性能。
3.5 清理清理是支座铸造工艺中的最后一个步骤。
在清理过程中,需要将模具和浇注系统中的残留物清除,以及对铸件的表面进行抛光和清洗。
支座铸造工艺毕业论文

支座铸造工艺毕业论文本文介绍了支座铸造工艺的相关背景和应用,详细阐述了支座铸造工艺流程和方法,探讨了支座铸造工艺中的材料选择和质量控制。
最后,提出了支座铸造工艺存在的问题和改进措施。
一、背景介绍支座是一种常见的机械零件,用于支撑设备或组件。
支座广泛应用于化工、制药、食品等行业,该领域的发展为支座铸造工艺的提升和创新提供了机会。
支座铸造工艺是通过铸造技术来生产该零件,其生产成本低、生产效率高,具有广泛的应用前景。
二、支座铸造工艺流程1.模具制备支座铸造的第一步是模具制备。
选择具有合适形状和尺寸的铸造模具,并将其涂抹上脱模剂,以便后续的模具脱模。
2.熔炼原材料将铸造材料,如铸铁、铸钢、铜、铝等材料,加入熔炉中进行熔炼,并添加合适的合金元素,以达到所需的材料化学成分。
3.铸造过程将熔融的金属注入模具中,然后静置,直到铸造材料凝固成型。
在铸造过程中,必须控制合金的温度、流动速度和氧化状态,以保证铸造质量。
4.去毛刺将成型支座从模具中取出,并进行去毛刺和砂型清洗。
5.表面处理进行表面处理,包括砂喷、抛光和涂漆等过程。
6.质量检验进行质量检验,以确保支座强度、硬度和尺寸精度符合设计要求。
三、材料选择和质量控制1.材料选择支座铸造工艺的材料选择将影响产品的性能和成本。
常见的支座材料有灰铸铁、球墨铸铁、铸钢、红铜和铝合金等。
根据具体应用场景,选择合适的支座材料,满足强度要求的同时尽可能降低成本。
2.质量控制支座铸造工艺的质量控制是确保支座产品性能和外观质量的关键。
对铸造温度、流速、浇注位置和氧化情况等参数进行严格控制,以确保产品成型质量。
此外,对于成型后的支座产品,进行温度处理、去毛刺和表面处理等工艺,以确保最终产品质量。
四、存在问题及改进措施1.存在问题支座铸造工艺存在生产效率低、产量不稳定、质量难以保证等问题。
2.改进措施为了缓解上述问题,可以采取以下改进措施:(1)优化生产流程,确保生产效率。
(2)引入智能化设备,提高产量稳定性。
支座铸造工艺设计
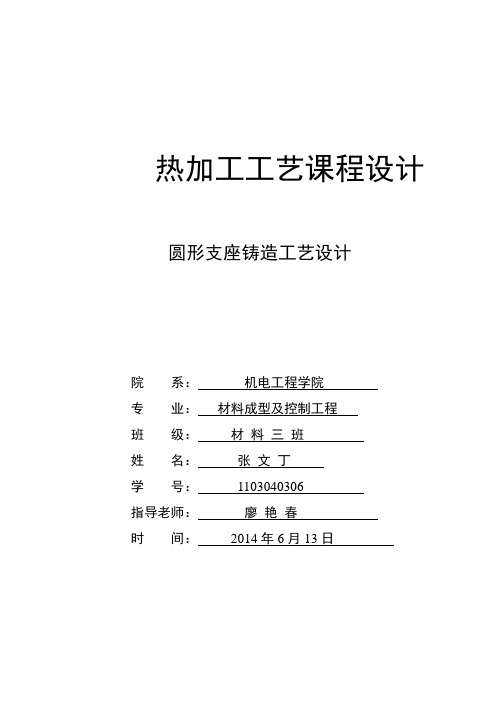
热加工工艺课程设计圆形支座铸造工艺设计院系:机电工程学院专业:材料成型及控制工程班级:材料三班姓名:张文丁学号:1103040306指导老师:廖艳春时间:2014年6月13日摘要热加工技术是机械类个专业一门重要的综合性技术学科。
在机械制造过程中,由于加工过程十分复杂,加工工序繁多,工艺过程不仅有铸造成型,锻压成形,焊接成形,还有非金属的模压成形,挤压成形等。
因此选着合适的工艺是保证产品质量的重要依据。
本次课程设计,将进行铸造工艺的总结和学习。
铸造主要是将液态金属或合金浇注到与零件尺寸、形状相适应的铸型型腔里,待其冷却凝固后获得毛坯或零件的方法,是机械类零件和毛坯成型的主要工艺方法,尤其适合于制造内腔和外形复杂的毛坯或零件。
本文主要分析了支座的结构并根据其结构特点确定了它的铸造工艺,支座是支撑零部件的载体其主要承受了轴向的压缩作用的机械零件。
在日常生产中对支座的选用异常广泛,因为它具有经济型良好、结构稳定性好、结构简单美观实用等特点,所以在机器零件的设计,加工过程中支座都起着不可代替的作用。
确定支座的铸造工艺过程主要包括:1)铸型及方法选择、2)分型面选择、3)浇注位置的确定、4)工艺参数的确定、5)浇注系统的设计、7)绘制铸造工艺图、8)绘制铸件图型面,型芯的数量、形状、尺寸及固定方法,加工余量,收缩率,浇注系统,起模斜度,冒口和冷铁的尺寸和位置等。
目录绪论 (1)一、零件的简介 (2)1.1 零件的介绍 (2)1.2确定零件的材料及牌号 (2)二、铸造工艺方案的确定 (3)2.1铸件的结构特点 (3)2.2铸件的工艺分析 (4)2.3分型面选择 (4)2.4 确定出最佳浇注位置 (6)三、工艺参数确定 (8)3.1工艺参数的确定 (8)3.1.1铸件尺寸公差 (9)3.1.2 机械加工余量 (9)3.1.3铸造收缩率 (9)3.1.4起模斜度 (10)3.1.5铸造圆角 (10)3.1.6反变形量 (10)3.2 砂芯设计 (10)3.2.1 芯头的设计 (10)3.2.2 砂头的定位结构 (11)3.2.3 芯座 (11)四、浇注系统及冒口、冷铁、出气孔等设计 (11)4.1 浇注系统的设计 (11)4.1.1选择浇注系统类型 (12)4.1.2横浇道及内浇道 (12)4.2 冒口的设计 (12)4.3 冷铁的设计 (13)4.4 出气孔的设计 (13)五、铸造工艺图绘制 (14)六、铸件图的绘制 (15)七、支座铸造工艺卡 (16)总结 (17)致谢 (18)参考文献: (19)绪论热加工成型技术也叫材料成型技术,是机械制造生产过程的重要组成部分。
支座压铸模具毕业设计
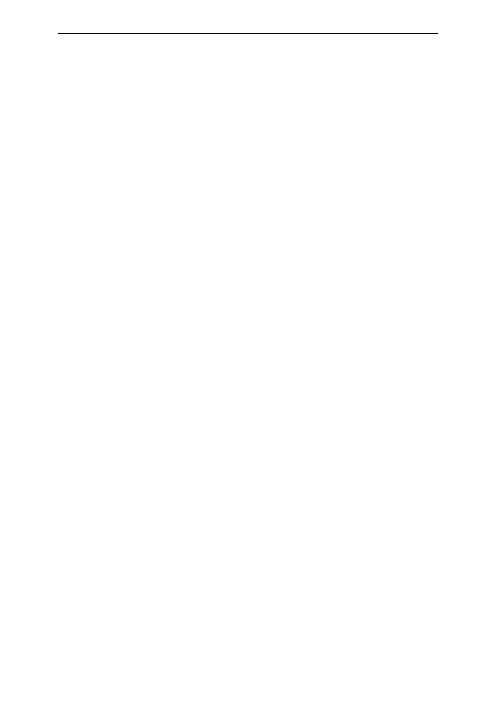
压力铸造是目前成型有色金属铸件的重要成型工艺方法,压铸的工艺特点是铸件的强度和精度较高,形状较为复杂且铸件壁较薄,而且生产力极高。
压铸模具是压力铸造的生产关键,压铸模具的质量决定着压铸件的质量和精度,而且模具设计直接影响着模具的质量和寿命。
因此,模具设计是模具技术进步关键,也是模具发展的重要因素。
根据零件的结构和尺寸设计了完整的模具。
设计内容主要包括:浇注系统设计,成型零件设计,抽芯机构设计,推出机构设计及模体结构设计。
根据铸件的形状特点,零件尺寸及精度,选定了合适是我压铸机,通过准确的计算并查阅设计手册,确定了成型零件以及模体是我尺寸及精度,在材料的选取及热处理要求上也做了详细说明,并在结合理论的基础上,借助于计算机辅助软件绘制了各部分零件及装配体的立体图和工程图,以保障模具的加工制造。
关键词:压力铸造,压铸模具,模具设计前言 (1)摘要 (I)目录 (I)1、压铸件的工艺分析 (1)1.1对压铸件的结构分析 (3)1.2压铸件材料的分析 (3)2、设备型号及其相关参数 (3)3、分析模具结构 (4)3.1浇注系统的设计 (4)3.2溢流槽和排气槽的设计 (4)3.3分型面的设计 (4)3.4型腔和型芯尺寸的确定 (4)3.5导柱与导套 (5)3.6推杆的结构设计 (5)3.7模具的冷却 (5)4、压铸工艺参数的选择 (5)4.1压射比压 (5)4.2压铸温度 (5)4.3压铸模温度 (5)4.4保压时间 (6)4.5留模时间 (6)4.6压射速度 (6)5、涂料的种类 (7)5.1压铸涂料 (7)6、型芯与型腔的选材 (7)7、校核 (7)8、零件图和装配图 (7)致谢 (11)参考文献 (12)结论 (13)前言国内外模具发展现状现代模具工业有“不衰亡工业”之称。
世界模具市场总体上供不应求,市场需求量维持在600亿至650亿美元,同时,我国的模具产业也迎来了新一轮的发展机遇。
近几年,我国模具产业总产值保持13%的年增长率中国模具行业发展现状:目前,中国17000多个模具生产厂点,从业人数约50多万。
ht250支座铸造及热处理复合工艺设计,毕设论文 ht热处理工艺

ht250支座铸造及热处理复合工艺设计,毕设论文 ht热处理工艺工艺课程设计课程设计 L 砂型类别 D 或≦25 >40~63 S h S h >100~160 湿型 0.2 20~25 ≦100 湿型 0.3 25~30 4.2 砂箱中铸件数量的确定由于该件小批量生产,机器湿砂造型,为了便于操作和保证质量,每箱放置一件铸件。
4.3 砂芯数量的确定根据铸件结构和已选定的分型面,使用一个芯子。
5 浇注系统设计浇注系统是指砂型中引导金属液流入行腔的通道,一般由浇口杯、直浇杯、横通道等组成。
浇口杯承接金属液,并进入横浇道,再分配给内浇道流入型腔,因此各浇道形状及截面均影响铸件质量。
5.1 浇注系统类型的选择浇注系统分为封闭式浇注系统,开放式浇注系统,半封闭式浇注系统和封闭-开放式浇注系统。
因为封闭式浇注系统控流截面积在内浇道,浇注开始后,金属液容易充满浇注系统,呈有压流动状态。
挡渣能力强,但充型速度快,冲刷力大,易产生喷溅,金属液易氧化。
适用于湿型铸件小件。
而支座就是采用湿型的铸件小件,所以选择封闭式浇注系统。
图3 HT250支座的中间注入式浇注系统 5.2确定内浇道在铸件上的位置、数目、金属引入方向支座结构较为简单且是小型件,铸造时采取一箱四件,故每个铸件上只用一个内浇道。
为了方便造型,内浇道开设在分型面上。
因为铸件采用底座朝上且铸件全部位于下箱的方式进行铸造,这样铸件凝固顺序为由下至上凝固,这样有利于支座的重要部分先凝固并得到补缩,如此内浇道则设置在底部侧面引入金属液,如图4所示。
图4 内浇道位置示意图 5.3决定直浇道的位置和高度实践证明,直浇道过低使充型及液态补缩压力不足,容易出现铸件棱角和轮廓不清晰、浇不到上表面缩凹等缺陷。
初步设计直浇道高度等于上砂箱高度200mm。
但应检验该高度是否足够。
检验依据为,剩余压力头应满足压力角的要求,如下式所列:式中 HM——最小剩余压力头 L——直浇道中心到铸件最高且最远点的水平投影距离 a——压力角由《铸造工艺学》查表3-4-11得:а为9~10 取10 因为铸件全部位于下箱,所以剩余压力头HM等于上箱高度200mm 经过验证剩余压力头满足压力角的要求。
支座铸造设

河南机电高等专科学校毕业论文毕业论文题目:支座铸造工艺设计系部:材料工程系专业: 材料成形于控制技术班级:材料成形于控制技术121班学生姓名:***学号:*********指导教师:***2015年4 月 10日支座铸造工艺设计摘要:本支座为一小型铸件,铸件材质 HT200,结构简单,无复杂的型腔和阻碍起模的凸起。
铸件的外形尺寸为 200mm× 110mm× 120mm,主要壁厚为 15m m,壁厚均匀。
支座采用 HT200 是一种较高强度铸铁,基体为珠光体,强度、耐磨性、耐热性均较好,减振性也良好,铸造性能较好。
从支座的整体结构特点出发,进行铸造工艺设计分析,确定铸造方案,并进行铸造工艺参数和砂芯的设计,在此基础上再根据铸件的材质重量和浇注系统性能设计补缩系统。
采用粘土砂手工造型、制芯、金属摸样和半封闭加注系统,设计时应综合考虑各方面因素,浇注系统不是简单地金属液流动通道,用 proe 三维造型后,采用华铸 CAE 软件对设计方案进行浇注、凝固模拟计算。
结果显示,浇注系统设计合理,但凝固时铸件上表面有明显的缩孔缩松,经仔细观察此缩孔在铸件刚开始凝固时都已经产生,分析原因是因为铸件为湿型,开始凝固时吸收较多的热量,使上表面先凝固下沉,产生凹坑阻碍金属液补缩,为了避免此缺陷的产生减少热量散失浇筑前铸件进行预热,改进工艺后再次运用华铸 CAE 模拟铸件无明显缺陷。
由于铸件模数较小 M=1.5cm,HT200 凝固时伴随着石墨的析出与膨胀,铸件以层状-糊状方式凝固,其共晶膨胀压力小,加之石墨片尖端伸向铁液的生长方式,使其有很好的“自补”能力,需要的补缩金属液较少,件工艺出品率为 75%。
关键词:支座;工艺设计;华铸 CAESupport casting process designAbstract: This bearing is a small-sized castings, casting material HT200, structure is simple, no complicated cavity and hinder the draw. The shape of the casting size for 200 mmx110mmx120mm, main wall thickness is 15 mm, wall thickness uniformity. Bearing adopts HT200 is a kind of high strength cast iron, for pearlite matrix, and the strength, abrasion resistance and heat resistance are good, vibration is also good; Casting performance is good. Starting from the overall structure of the bearing characteristics, analysis of casting process design, casting solution is determined, and the casting process parameters and the design of sand core, on this basis, according to the material weight of casting and pouring system and feeding system design performance. Using clay sand handmade molding and core making, metal touch kind and semi-closed charging system, gating system design should be considered when factors not simply metal fluid flow channels, after using proe 3 d modelling, the China casting CAE software is adopted to design plans for pouring and solidification simulation. , according to the results of gating system design is reasonable, but the casting surface has obvious shrinkage on the shrinkage, carefully observe the shrinkage in casting solidification have been produced at first, analysis the reason is because the casting for wet and solidifies when absorbs more heat, making the surface solidification down first, the pits producing metal liquid feeding, in order to avoid the defect of reduce the heat lost preheated before pouring casting, improve the process after casting CAE simulation casting again using China has no obvious defects. Due to casting modulus of 1.5 cm, smaller HT200 with graphite precipitation and solidification of casting, solidification in layered - paste way, its eutectic expansion pressure is small, and flake graphite tip to the growth of iron liquid, so that it is a very good ability to "repair", and need less feeding metal, pieces of craft production rate was 75%.Key words: Support; process planning; Hua Zhu CAE目录毕业论文 (1)1 绪论 (5)1.1国内铸造现状及发展趋势 (5)1.1.1国内铸造的现状 (5)2设计任务 (7)2.1 铸造方案的确定 (8)2.2支座结构的铸造工艺性分析 (8)2.3造型造芯方法的选择 (10)2.4浇注位置的选择 (10)2.5支座分型面的选择 (11)2.6砂箱中铸件数目的确定 (14)3 铸造工艺参数的确定 (15)3.1 铸件的尺寸公差 (15)3.2 机械加工余量 (15)3.3 铸件收缩率 (15)3.4 起模斜度 (15)3.5 最小铸出的孔和槽 (16)3.6 工艺补正量 (16)3.7 浇注温度和铸件在铸型中的冷却时间 (16)4 砂芯的设计 (17)4.1 芯头的设计 (17)4.2 砂芯的定位结构 (17)4.3 压环、防压环和集砂槽的尺寸 (18)4.4 芯骨 (18)4.5 芯撑 (18)4.6 砂芯的排气 (18)5 浇注系统及冒口、冷铁、出气孔的设计 (19)5.1 浇注系统类型的选择 (19)5.2 浇注时间的计算 (19)5.3 阻流元截面积的计算及各阻流原件的比例关系的确定 (20)5.4.确定内浇道的截面积 (20)5.5 确定横浇道截面积 (21)5.6 确定直浇道的截面积 (21)5.7直浇道窝的设计 (22)5.8 浇口杯的设计 (22)5.9 冒口的设计 (23)5.10 冷铁的设计 (23)5.11 出气孔的设计 (23)6 支座浇注、凝固过程模拟分析 (24)6.1 华铸 CAE 简介 (24)6.2 华铸 CAE 模拟分析的步骤 (24)6.3 华铸 CAE 模拟支座浇注、凝固过程分析报告 (24)7 铸造工艺装备的设计 (27)7.1 模板的设计 (27)7.2 芯盒的设计 (27)8 总结 (28)8.1 铸造工艺图 (28)8.2 铸造工艺卡 (28)9 结论 (29)10 致谢 (30)参考文献 (31)1 绪论铸造行业是制造也的重要组成本部分,对国民经济发展起着重要的作用。
HT250支座铸造及热处理复合工艺设计
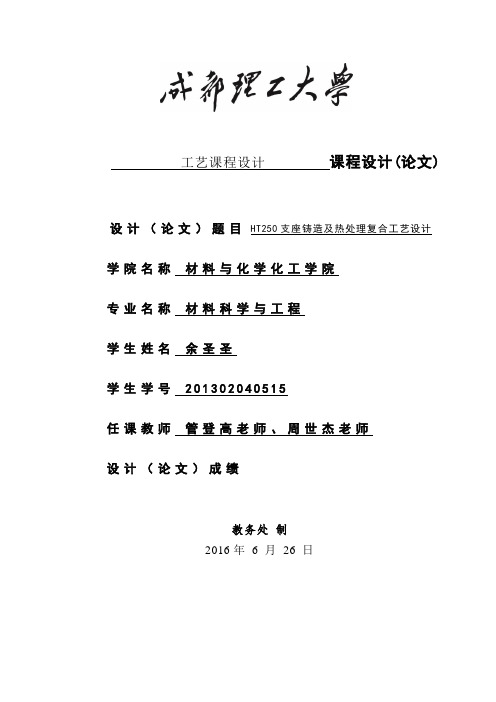
工艺课程设计课程设计(论文) 设计(论文)题目HT250支座铸造及热处理复合工艺设计学院名称材料与化学化工学院专业名称材料科学与工程学生姓名余圣圣学生学号201302040515任课教师管登高老师、周世杰老师设计(论文)成绩教务处制2016年 6 月26 日目录前言 (5)HT250支座铸造及热处理复合工艺设计任务书 (6)1 HT250支座工艺分析 (7)1.1 支座零件图 (7)1.2 工艺分析 (7)2 铸造工艺方案的确定 (8)2.1 铸造方法的选择 (8)2.2 造型、造芯方法的选择 (9)2.3 凝固原则、浇注位置的确定 (9)2.4 分型面的选择 (11) (12) (12) (13)3 铸造工艺参数的确定 (13)3.1 铸件尺寸公差 (13)3.2 机械加工余量 (13)3.3 最小铸出孔和槽 (14)3.4 起模斜度 (14)3.5 铸造收缩率 (14)4 砂芯设计 (15)4.1 芯头的设计 (15)4.2 砂箱中铸件数量的确定 (15)4.3 砂芯数量的确定 (15)5 浇注系统设计 (16)5.1 浇注系统类型的选择 (16) (17)5.4 浇注系统的设计与计算 (18)5.4.1 铸件重量 (18)5.4.2 金属液总质量 G (19)5.4.3 浇注时间t的确定 (19)5.4.4 流量因数 u (19)5.4.5 平均静压头 Hp (20)5.4.6 铸铁件在浇注系统最小截面积 (20) (20) (21) (21) (22)5.4.11 浇口杯的设计 (23)5.4.12 工艺出品率校核 (23)6 冒口的设计 (24)6.1 铸铁件无冒口工艺设计的条件 (24)6.2 冒口的计算方法 (24)6.3 冒口及尺寸确定 (24)7 排气的设计 (24)7.1 砂型的排气 (24)7.2 砂芯的排气 (25)8 铸造工艺图和铸件图的绘制 (25)9 铸造质量控制 (26)9.1 铸造缺陷分析及防止措施 (26)9.2 铸件质量检查 (27)10 铸造工艺卡的拟定 (28)11 铸铁件热处理种类 (29)11.1 常见热处理 (29)11.2 本次设计的热处理方式 (32)11.3 铸铁件时效处理工艺曲线 (33)11.4 热处理后的组织及其性能 (33)12 热处理后的检验工作 (34)12.1 质量检验 (34)12.2 化学成分检验 (35)13 误差分析及预防措施 (36)13.1 淬火、回火缺陷分析及防止补救措施 (36)14 总结 (38)15参考文献 (39)前言本设计是对支座零件进行铸造毛坯工艺设计。
(完整word版)铸造工艺课程设计说明书

铸造工艺课程设计说明书目录1 前言 (4)1。
1本设计的意义 (4)1.1.1 本设计的目的 (4)1.1。
2 本设计的意义 (5)1.2本设计的技术要求 (5)1。
3本课题的发展现状 (5)1.4本领域存在的问题 (6)1.5本设计的指导思想 (6)1。
6本设计拟解决的关键问题 (7)2 设计方案 (7)2。
1零件的材质分析 (8)2.2支座工艺设计的内容和要求 (9)2.3造型造芯方法的选择 (11)2。
4浇注位置的选择与分型面的选择 (12)2。
4.1 浇注位置的选择 (12)2.4.2 分型面的确定 (14)2.4.3 砂箱中铸件数目的确定 (15)3 设计说明 (17)3。
1工艺设计参数确定 (17)3。
1.1 最小铸出的孔和槽 (17)3.1.2 铸件的尺寸公差 (18)3。
1.3 机械加工余量 (19)3。
2铸造收缩率 (19)3。
2。
1 起模斜度 (20)3.2。
2 浇注温度和冷却时间 (21)3。
3砂芯设计 (22)3.3。
1 芯头的设计 (22)3。
3。
2 砂芯的定位结构 (23)3。
3.3 芯骨设计 (23)3.3.4 砂芯的排气 (23)3。
4浇注系统及冒口,冷铁,出气孔的设计 (24)3。
4.1 浇注系统的类型和应用范围 (24)3。
4。
2 确定内浇道在铸件上的位置、数目、金属引入方向 (24)3.5决定直浇道的位置和高度 (25)3.5.1 计算内浇道截面积 (25)3.5.2 计算横浇道截面积 (26)3。
5。
3 计算直浇道截面积 (27)3。
5.4 冒口的设计 (27)4 铸造工艺装备设计 (28)4。
1模样的设计 (28)4。
1.1 模样材料的选用 (28)4.1。
2 金属模样尺寸的确定 (29)4。
1。
3 壁厚与加强筋的设计 (29)4。
1。
4 金属模样的技术要求 (29)4.1。
5 金属模样的生产方法 (29)4.2模板的设计 (30)4。
2。
1 模底板材料的选用 (30)4.2。
圆筒铸造方案

圆筒铸造方案在工业制造领域,圆筒铸造是一种常见的技术,广泛应用于制造各种类型的圆筒状零件。
本文将介绍圆筒铸造的方案,并探讨其具体步骤和技术要点。
一、方案概述圆筒铸造方案旨在通过铸造工艺制造圆筒状零件,以满足特定的设计要求和功能需求。
铸造过程中,通过选择合适的材料、设计模具以及控制工艺参数等因素,确保最终产品的质量和性能。
二、材料选择在圆筒铸造中,常用的材料包括铸铁、钢铁和铝合金等。
材料的选择应基于零件的使用要求、耐久性要求、成本因素以及制造工艺的可行性等考虑因素。
铸铁适用于一些对耐磨性和强度有较高要求的场景,而铝合金则常用于追求轻量化和导热性能的应用。
三、模具设计模具设计是圆筒铸造的重要环节,它决定了最终产品的形状和尺寸。
在设计模具时,需要考虑材料的流动性、凝固收缩率以及避免出现砂眼等缺陷。
此外,还需要确定合适的浇口和浇注系统,以确保熔融金属在整个铸造过程中能够均匀流动并充满整个型腔。
四、工艺参数控制在铸造过程中,合理的工艺参数控制对于最终产品的质量至关重要。
首先是熔炼温度和时间的控制,以保证金属合金能够达到适当的流动性和凝固性。
其次是浇注速度和压力的控制,以避免气孔和夹杂等缺陷的产生。
此外,还需要合理控制铸造中的冷却速度,以实现理想的组织和性能。
五、质量检验与处理在完成圆筒铸造后,需要进行质量检验和处理,以保证产品的合格率和品质。
具体的检验方法包括尺寸测量、无损检测、磁粉检测等。
对于出现缺陷的产品,需要及时进行修复或重新铸造,以满足设计要求。
六、技术创新随着科技的发展和工艺的不断创新,圆筒铸造技术也在不断演进和改进。
目前,一些先进的技术如数值模拟、快速凝固等被引入到圆筒铸造中,以提高产品的质量和制造效率。
此外,还可以结合其他工艺如粉末冶金、复合材料等,开发新的材料和工艺组合,满足更高级别的要求。
总结:圆筒铸造方案是一种重要的工艺,用于制造圆筒状零件。
通过选择合适的材料、设计模具以及控制工艺参数等因素,可以实现产品的高质量制造。
圆形支座铸造工艺设计
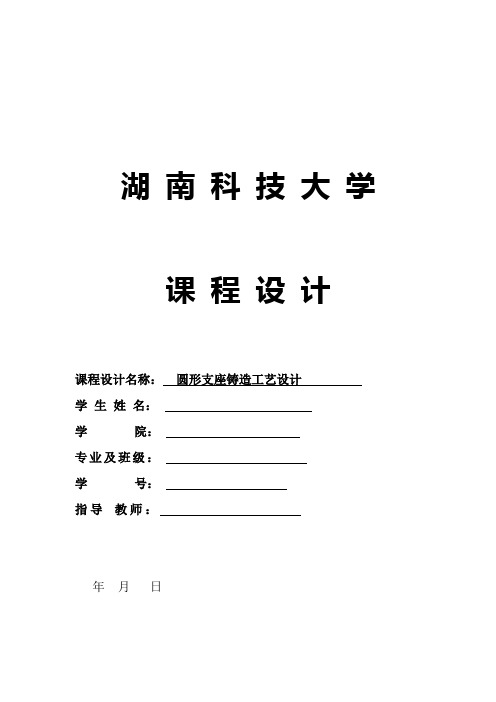
湖南科技大学课程设计课程设计名称:圆形支座铸造工艺设计学生姓名:学院:专业及班级:学号:指导教师:年月日铸造工艺课程设计任务书一、任务与要求1.完成产品零件图、铸件铸造工艺图各一张,铸造工艺图需要三维建模(完成3D图)。
2.完成芯盒装配图一张。
3.完成铸型装配图一张。
4. 编写设计说明书一份(15~20页),并将任务书及任务图放置首页。
二、设计内容为2周1. 绘制产品零件图、铸造工艺图及工艺图的3D图(2天)。
2. 铸造工艺方案设计:确定浇注位置及分型面,确定加工余量、起模斜度、铸造圆角、收缩率,确定型芯、芯头间隙尺寸。
(1天)。
3. 绘制芯盒装配图(1天)。
4. 绘制铸型装配图、即合箱图(包括流道计算共2天)。
5. 编制设计说明书(4天)。
三、主要参考资料1. 张亮峰,材料成形技术基础[M],高等教育出版社,2011.2. 丁根宝,铸造工艺学上册[M] ,机械工业出版社,1985.3. 铸造手册编委会,铸造手册:第五卷[M] ,机械工业出版社,1996.4. 沈其文, 材料成形工艺基础(第三版)[M],华中科技大学出版社,2003.摘要支座是支撑零部件的载体其主要承受了轴向的压缩作用的机械零件。
在日常生产中对支座的选用异常广泛,因为它具有经济型良好、结构稳定性好、结构简单美观实用等特点。
本文主要分析了支座的结构,并根据其结构特点确定了铸造工艺,确定了支座的铸造工艺过程,绘制了芯盒装配图,铸造装配图等。
关键词:圆形支座;砂型铸造;铸造工艺设计;装配图目录一、造型材料选择1. 铸造合金的选用 (1)2. 造型和造芯材料 (1)二、浇注位置及分型面的确定 (2)三、铸造工艺参数设计1.加工余量的选择 (5)2.铸件孔是否铸出的确定 (5)3.起模斜度的确定 (5)4.铸造圆角的确定 (6)5. 铸造收缩率的确定 (7)6.反变形量 (8)四、造型方法的设计 (8)五、木模的设计 (10)六、浇注系统的设计1.浇口杯 (12)2.浇注系统的尺寸 (12)七、冒口的设计 (14)八、铸型装配图设计 (15)心得体会 (17)参考文献 (18)一、造型材料选择1. 铸造合金的选用灰铸铁的力学性能与基体的组织和石墨的形态有关。
支座压铸工艺设计(简介)

支座压铸工艺设计摘要压力铸造是目前成型有色金属铸件的重要成型工艺方法。
压铸的工艺特点是铸件的强度和硬度较高,形状较为复杂且铸件壁较薄,而且生产率极高。
压铸模具是压力铸造生产的关键,压铸模具的质量决定着压铸件的质量和精度,而模具设计直接影响着压铸模具的质量和寿命。
因此,模具设计是模具技术进步的关键,也是模具发展的重要因素。
根据零件的结构和尺寸设计了完整的模具。
设计内容主要包括:浇注系统设计、成型零件设计、抽芯机构设计、推出机构设计以及模体结构设计。
根据铸件的形状特点、零件尺寸及精度,选定了合适的压铸机,通过准确的计算并查阅设计手册,确定了成型零件以及模体的尺寸及精度,在材料的选取及热处理要求上也作出了详细说明,并在结合理论知识的基础上,借助于计算机辅助软件绘制了各部分零件及装配体的立体图和工程图,以保障模具的加工制造。
关键词:压力铸造;压铸模具;铝硅合金铸件;支座绪论 (1)1.1铸造技术简介 (1)1.2压铸模具设计的意义 (2)第二章零件结构工艺分析 (3)2.1支座的生产条件、结构及技术要求 (3)2.2支座结构的压铸技术分析 (4)第三章.铸造工艺方案的拟定 (6)3.1铸造方法的选择 (6)3.2分型面方案的选择 (6)3.2砂芯的选择 (7)第四章.浇注系统的确定 (9)4.1内浇口设计 (11)4.2直浇道设计 (11)4.3切向浇道入口处设计 (12)4.4切向浇道末端设计 (13)4.5主横浇道尺寸设计 (13)4.6缓冲包尺寸设计 (13)4.7计算金属液流向角 (13)4.8计算半三角区尺寸 (13)第五章压铸机的选用 (14)5.1 根据产品的特点选择压铸机类型 (14)5.2计算主胀型力F (15)5.3计算分胀型力F (15)5.4计算锁模力 (15)5.5 校核锁模力 (16)5.6 压室容量校核 (16)第六章压铸件成形尺寸计算 (17)6.1型腔尺寸计算 (17)6.2型芯尺寸计算 (18)6.3 中心距,位置尺寸计算 (20)6.4 螺纹型环尺寸计算 (21)6.5螺纹型芯尺寸计算....................................................... 错误!未定义书签。
铸造工艺学课程设计说明书
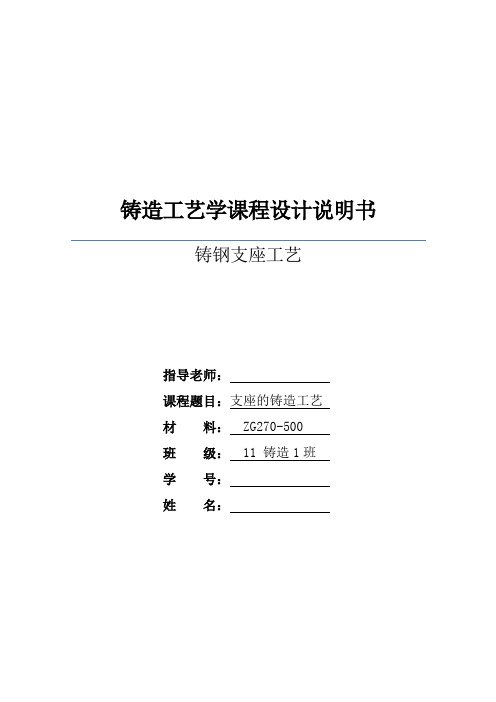
铸造工艺学课程设计-铸钢支座工艺
设计要求: 1 用 CAD 绘制符合国家制图标准的铸件零件二维三视图,经过指导老师检 查合格打印出图,图纸采用 A0 图幅; 2 在 A0 铸件图样上用红蓝铅笔做铸造工艺设计,包括分型面、加工余量、 分型(芯)负数、拔模斜度、铸造体(线)收缩率、补正量、冷铁,浇注系统设 计、冒口设计、砂芯设计、工艺说明等;必须设计 3 种分型方案,从中选取一种 合适的方案做铸造工艺设计, 设计中冒口及浇注系统等设计须有详细的计算过程 和计算依据; 3 铸造工艺图设计完成后,根据铸造工艺图设计金属模板装配图、金属芯盒 装配图(中等难度砂芯) ,用 A2 图幅打印出图;
表22铸件质量公差数值323机械加工余量铸造工艺学课程设计铸钢支座工艺420铸件为保证其加工面尺寸和零件精度应有加工余量即在铸件工艺设计时预先增加的而后在机械加工时又被加工去的金属层厚度称为机械加工余量简称加工余量
铸造工艺学课程设计说明书
铸钢支座工艺
指导老师: 课程题目:铸钢支座的铸造工艺 课程题目:支座的铸造工艺 材 料: 材 料: ZG270-500 班 学 姓 级: 号: 名: 11 铸造 1 班
图 1.1 零件图
1 / 20
铸造工艺学课程设计-铸钢支座工艺
1 零件分析 1.1 零件结构分析 零件为支座,其零件结构如图 1.1 所示。该件结构复杂,壁厚较为均匀,长、 宽和高相差大,结构上的铸造工艺性能较为合理。 1.2 零件化学成分分析 零件为支座,其零件结构如图 1.1 所示。材料为 ZG270-500,对材料的化学 成分和机械性能要求见下表 1.1 和表 1.2。 表 1.1 ZG270-500 化学成分(%) 元素 C≤ 0.40 Si≤ 0.50 Mn≤ 0.90 S≤ 0.04 P≤ 0.04 Ni 0.30 残余元素≤ Cr Cu Mo 0.30 0.30 0.25 V 0.05
支座铸造工艺课程设计

支座铸造工艺课程设计-2(总21页)--本页仅作为文档封面,使用时请直接删除即可----内页可以根据需求调整合适字体及大小--热加工工艺课程设计支座铸造工艺设计院系:工学院机械系专业:机械设计制造及其自动化班级:姓名:学号:指导老师:时间:黄河科技学院课程设计任务书工学院机械系机械设计制造及其自动化专业 2011级 1班学号姓名指导教师设计题目: 支座铸造工艺设计课程名称:热加工工艺课程设计课程设计时间:5 月 22 日至 6 月 6 日共 2 周课程设计工作内容与基本要求(已知技术参数、设计要求、设计任务、工作计划、所需相关资料)(纸张不够可加页)1、已知技术参数图1 支座零件图2、设计任务与要求1)设计任务1 选择零件的铸型种类,并选择零件的材料牌号。
2 分析零件的结构,找出几种分型方案,并分别用符号标出。
3 从保证质量和简化工艺两方面进行分析比较,选出最佳分型方案,标出浇注位置和造型方法。
4 画出零件的铸造工艺图(图上标出最佳浇注位置与分型面位置、画出机加工余量、起模斜度、铸造圆角、型芯及型芯头,图下注明收缩量)5 绘制出铸件图。
2)设计要求1设计图样一律按工程制图要求,采用手绘或机绘完成,并用三号图纸出图。
2 按所设计内容及相应顺序要求,认真编写说明书(不少于3000字)。
3、工作计划熟悉设计题目,查阅资料,做准备工作 1天确定铸造工艺方案 1天工艺设计和工艺计算 2天绘制铸件铸造工艺图 1天确定铸件铸造工艺步骤 2天编写设计说明书 3天答辩 1天4.主要参考资料《热加工工艺基础》、《金属成形工艺设计》、《机械设计手册》系主任审批意见:审批人签名:时间:2013年月日支座铸造工艺设计摘要铸造是指将液态金属或合金浇注到与零件尺寸、形状相适应的铸型型腔里,待其冷却凝固后获得毛坯或零件的方法。
铸造成形是机械类零件和毛坯成形的重要工艺方法之一,尤以适合于制造内腔和外形复杂的毛坯或零件。
本文主要分析了支座的结构,并根据其结构特点确定了它的砂型铸造工艺。
圆形支座铸造工艺设计

热加工工艺课程设计圆形支座铸造工艺设计院系:机电工程学院专业:材料成型及控制工程班级:姓名:学号:指导老师:时间:摘要热加工技术是机械类个专业一门重要的综合性技术学科。
在机械制造过程中,由于加工过程十分复杂,加工工序繁多,工艺过程不仅有铸造成型,锻压成形,焊接成形,还有非金属的模压成形,挤压成形等。
因此选着合适的工艺是保证产品质量的重要依据。
本次课程设计,将进行铸造工艺的总结和学习。
铸造主要是将液态金属或合金浇注到与零件尺寸、形状相适应的铸型型腔里,待其冷却凝固后获得毛坯或零件的方法,是机械类零件和毛坯成型的主要工艺方法,尤其适合于制造内腔和外形复杂的毛坯或零件。
本文主要分析了支座的结构并根据其结构特点确定了它的铸造工艺,支座是支撑零部件的载体其主要承受了轴向的压缩作用的机械零件。
在日常生产中对支座的选用异常广泛,因为它具有经济型良好、结构稳定性好、结构简单美观实用等特点,所以在机器零件的设计,加工过程中支座都起着不可代替的作用。
确定支座的铸造工艺过程主要包括:1)铸型及方法选择、2)分型面选择、3)浇注位置的确定、4)工艺参数的确定、5)浇注系统的设计、7)绘制铸造工艺图、8)绘制铸件图型面,型芯的数量、形状、尺寸及固定方法,加工余量,收缩率,浇注系统,起模斜度,冒口和冷铁的尺寸和位置等。
目录绪论 (1)一、零件的简介 (2)1.1 零件的介绍 (2)1.2确定零件的材料及牌号 (2)二、铸造工艺方案的确定 (3)2.1铸件的结构特点 (3)2.2铸件的工艺分析 (4)2.3分型面选择 (4)2.4 确定出最佳浇注位置 (6)三、工艺参数确定 (8)3.1工艺参数的确定 (8)3.1.1铸件尺寸公差 (9)3.1.2 机械加工余量 (9)3.1.3铸造收缩率 (9)3.1.4起模斜度 (10)3.1.5铸造圆角 (10)3.1.6反变形量 (10)3.2 砂芯设计 (10)3.2.1 芯头的设计 (10)3.2.2 砂头的定位结构 (11)3.2.3 芯座 (11)四、浇注系统及冒口、冷铁、出气孔等设计 (11)4.1 浇注系统的设计 (11)4.1.1选择浇注系统类型 (12)4.1.2横浇道及内浇道 (12)4.2 冒口的设计 (12)4.3 冷铁的设计 (13)4.4 出气孔的设计 (13)五、铸造工艺图绘制 (14)六、铸件图的绘制 (15)七、支座铸造工艺卡 (16)总结 (17)致谢 (18)参考文献: (19)绪论热加工成型技术也叫材料成型技术,是机械制造生产过程的重要组成部分。
支座铸造工艺设计

一、零件铸造工艺要求及结构1.1 支座的生产条件、结构及技术要求●产品生产性质——大批量生产●零件材质——RuT300●零件的外型示意图如图2.1所示,支座的零件图如图2.2所示,支座的外形轮廓尺寸为160mm*135mm*100mm,主要壁厚18mm,最大壁厚20mm,为一小型铸件;铸件除满足几何尺寸精度及材质方面的要求外,无其他特殊技术要求。
图2.1 支座外型示意图图2.2 支座零件图1.2 支座结构的铸造工艺性零件结构的铸造工艺性是指零件的结构应符合铸造生产的要求,易于保证铸件品质,简化铸件工艺过程和降低成本。
审查、分析应考虑如下几个方面:1.铸件应有合适的壁厚,为了避免浇不到、冷隔等缺陷,铸件不应太薄。
2.铸件结构不应造成严重的收缩阻碍,注意薄壁过渡和圆角铸件薄厚壁的相接拐弯等厚度的壁与壁的各种交接,都应采取逐渐过渡和转变的形式,并应使用较大的圆角相连接,避免因应力集中导致裂纹缺陷。
3.铸件内壁应薄于外壁铸件的内壁和肋等,散热条件较差,应薄于外壁,以使内、外壁能均匀地冷却,减轻内应力和防止裂纹。
4.壁厚力求均匀,减少肥厚部分,防止形成热节。
5.利于补缩和实现顺序凝固。
6.防止铸件翘曲变形。
7.避免浇注位置上有水平的大平面结构。
对于支座的铸造工艺性审查、分析如下:支座的轮廓尺寸为160mm*135mm*100mm。
砂型铸造条件下该轮廓尺寸允许的最小壁厚查《铸造工艺学》表3-2-1得:最小允许壁厚为3~4 mm。
而设计支座的最小壁厚为10mm。
符合要求。
支座设计壁厚较为均匀,两壁相连初采用了加强肋,可以有效构成热节,不易产生热烈。
二、铸造工艺方案的确定2.1 造型,造芯方法的选择支座的轮廓尺寸为160mm*135mm*100mm,铸件尺寸较小,属于中小型零件且要大批量生产。
采用湿型粘土砂造型灵活性大,生产率高,生产周期短,便于组织流水生产,易于实现机械化和自动化,材料成本低,节省烘干设备、燃料、电力等,还可延长砂箱使用寿命。
- 1、下载文档前请自行甄别文档内容的完整性,平台不提供额外的编辑、内容补充、找答案等附加服务。
- 2、"仅部分预览"的文档,不可在线预览部分如存在完整性等问题,可反馈申请退款(可完整预览的文档不适用该条件!)。
- 3、如文档侵犯您的权益,请联系客服反馈,我们会尽快为您处理(人工客服工作时间:9:00-18:30)。
湖南科技大学课程设计课程设计名称:圆形支座铸造工艺设计学生姓名:学院:专业及班级:学号:指导教师:铸造工艺课程设计任务书一、任务与要求1.完成产品零件图、铸件铸造工艺图各一张,铸造工艺图需要三维建模(完成3D 图)。
2.完成芯盒装配图一张。
3.完成铸型装配图一张。
4. 编写设计说明书一份(15~20 页),并将任务书及任务图放置首页。
二、设计内容为2 周1.绘制产品零件图、铸造工艺图及工艺图的3D图(2 天)。
2.铸造工艺方案设计:确定浇注位置及分型面,确定加工余量、起模斜度、铸造圆角、收缩率,确定型芯、芯头间隙尺寸。
(1 天)。
3.绘制芯盒装配图(1 天)。
4.绘制铸型装配图、即合箱图(包括流道计算共2 天)。
5. 编制设计说明书(4 天)。
三、主要参考资料1.张亮峰,材料成形技术基础[M],高等教育出版社,2011.2.丁根宝,铸造工艺学上册[M],机械工业出版社,1985.3.铸造手册编委会,铸造手册:第五卷[M],机械工业出版社,1996.4.沈其文, 材料成形工艺基础(第三版)[M],华中科技大学出版社,2003.摘要支座是支撑零部件的载体其主要承受了轴向的压缩作用的机械零件。
在日常生产中对支座的选用异常广泛,因为它具有经济型良好、结构稳定性好、结构简单美观实用等特点。
本文主要分析了支座的结构,并根据其结构特点确定了铸造工艺,确定了支座的铸造工艺过程,绘制了芯盒装配图,铸造装配图等。
关键词:圆形支座;砂型铸造;铸造工艺设计;装配图目录一、造型材料选择1.铸造合金的选用 (1)2.造型和造芯材料·····················································1 二、浇注位置及分型面的确定············································2 三、铸造工艺参数设计1.加工余量的选择 (5)2.铸件孔是否铸出的确定 (5)3.起模斜度的确定 (5)4.铸造圆角的确定 (6)5.铸造收缩率的确定 (7)6.反变形量···························································8 四、造型方法的设计·····················································8 五、木模的设计·························································10 六、浇注系统的设计1.浇口杯 (12)2.浇注系统的尺寸....................................................12 七、冒口的设计.........................................................14 八、铸型装配图设计....................................................15 心得体会................................................................17 参考文献. (18)一、造型材料选择1.铸造合金的选用灰铸铁的力学性能与基体的组织和石墨的形态有关。
灰铸铁中的片状石墨对基体的割裂严重,在石墨尖角处易造成应力集中,使灰铸铁的抗拉强度、塑性和韧性远低于钢,但抗压强度与钢相当,也是常用铸铁件中力学性能最差的铸铁。
同时,基体组织对灰铸铁的力学性能也有一定的影响,铁素体基体灰铸铁的石墨片粗大,强度和硬度最低,故应用较少;珠光体基体灰铸铁的石墨片细小,有较高的强度和硬度,主要用来制造较重要铸件;铁素体一珠光体基体灰铸铁的石墨片较珠光体灰铸铁稍粗大,性能不如珠光体灰铸铁。
故工业上较多使用的是珠光体基体的灰铸铁。
灰铸铁具有良好的铸造性能、良好的减振性、良好的耐磨性能、良好的切削加工性能、在铸造过程中,应选用的金属材料种类是灰铸铁,因为此铸件结构基本为左右对称,最大截面为地面,因此可以采用整体造型进行铸造。
灰铸铁的流动性好,易浇注,且收缩率最小。
并随含碳量的增加而减少,使铸件易于切削加工。
铸铁材料还可以减少噪音。
在浇注时,浇注温度为 1200-1380℃。
采用砂型铸造方法,操作简便,工艺性好,提高了工作效率。
灰铸铁材料抗压能力强,保证了铸件的使用性能。
因为支座是指用以支承容器或设备的重量,并使其固定于一定位置的支承部件。
还要承受操作时的振动与地震载荷,而且此铸件为290×120mm 的灰铸铁,其型号应为 HT250。
2.造型和造芯材料由于本次课程设计的铸件是中等批量生产,所以造型和造芯的方法应采用灵活多样,适应性强的手工造型。
但它有生产率低,劳动强度大,铸件质量不易稳定的缺点。
造型方法可选用砂箱造型,其操作方便,无论是大、中、小型铸件,还是大量、成批和单件生产均可采用。
型砂选择:铸铁用的型砂和泥心砂,其主要的组成部分是石英砂和耐火粘土。
作为造型材料的沙子性质,由砂粒形状和大小,氧化硅的含量,以及沙子中存在的各种混合物来确定。
该铸件型砂选用瘦沙(粘土含量 2-10%)来代替石英砂。
在湿模造型时,小型和中小型铸铁件泥心砂可以采用小颗粒的半肥沙(粘土含量 10-20%)作为附加物加入石英砂中。
加入的耐火粘土,其工艺试样的抗压强度应为 0.5-0.6kg/mm2。
耐火粘土应该是白色或者淡灰色的,不应有可被肉眼看出的混杂物,如砂子、矿石、石灰等。
碎粘土所含水分不应超过 2%。
(铸件材料是铸铁时,制造湿砂型的粘土砂所用粘土为膨润土,湿抗压强度一般为 80-120kPa。
含水量为 4.5-5.5%,透气性为 60-100,型砂配比 70/140 目占 33,100/200 目占 17%,红砂占 50%。
芯砂选择油砂或水玻璃砂。
)造芯的方法可采用芯盒造芯和刮板造芯,前者用于造各种形状、尺寸和批量的砂芯,后者用于造单件小批量生产,形状简单或回转体砂芯。
二、浇注位置及分型面的确定分型面是指上、下砂型的接触面或铸造模样的分合面,分型面的选择应在保证质量前提下,尽量简化工艺过程,节省人力物力。
对于零件质量要求不高、外形复杂且批量不大的支撑台铸件,为简化工艺操作,可优先考虑分型面,并找出零件的可分型方案。
选择分型面时应注意一下原则:1)应使铸件全部或大部分置于同一半型内2)应尽量减少分型面的数目3)分型面应尽量选用平面4)便于下芯、合箱和检测5)不使砂箱过高6)受力件的分型面的选择不应削弱铸件结构强度7)注意减轻铸件清理和机械加工量该零件可能的分型方案有三种。
a)以支架的底面为分型面(如图 2-1所示)图 2-1b)以凸台为分型面(如图 2-2所示)图 2-2c)以对称中心线为分型面(如图2-3 所示)图 2-3分析比较各方案的特点并确定方案1)以支架的底面为分型面这种分型方法只需外加一活块造型,其分型面数量不仅少而且铸件全部放在下型,既便于型芯安放和检验,又可以使上型高度减低而便于合箱和检验壁厚,还有利于起模及翻箱操作。
而且底面可以向下放,以保证其表面粗糙度,分型面为底面时便于起模。
2 )以凸台为分型面不利于起模及翻箱操作。
3 )以对称中心线为分型面需采用两箱造型造型复杂,容易造成错箱,从而影响铸件精度。
三、铸造工艺参数设计确定铸造工艺参数必须以零件尺寸为依据,零件的详细尺寸如图3-1 所示。