宝钢股份高炉生产工艺与设备-yj
高炉炼铁炼钢工艺

本次将高炉炼铁工艺流程分为以下几部分:一、高炉炼铁工艺流程详解二、高炉炼铁原理三、高炉冶炼主要工艺设备简介四、高炉炼铁用的原料附:高炉炉本体主要组成部分介绍以及高炉操作知识工艺设备相见文库文档:一、高炉炼铁工艺流程详解高炉炼铁工艺流程详图如下图所示:二、高炉炼铁原理炼铁过程实质上是将铁从其自然形态——矿石等含铁化合物中还原出来的过程。
炼铁方法主要有高炉法、直接还原法、熔融还原法等,其原理是矿石在特定的气氛中(还原物质CO、H2、C;适宜温度等)通过物化反应获取还原后的生铁。
生铁除了少部分用于铸造外,绝大部分是作为炼钢原料。
高炉炼铁是现代炼铁的主要方法,钢铁生产中的重要环节。
这种方法是由古代竖炉炼铁发展、改进而成的。
尽管世界各国研究发展了很多新的炼铁法,但由于高炉炼铁技术经济指标良好,工艺简单,生产量大,劳动生产率高,能耗低,这种方法生产的铁仍占世界铁总产量的95%以上。
炼铁工艺是是将含铁原料(烧结矿、球团矿或铁矿)、燃料(焦炭、煤粉等)及其它辅助原料(石灰石、白云石、锰矿等)按一定比例自高炉炉顶装入高炉,并由热风炉在高炉下部沿炉周的风口向高炉内鼓入热风助焦炭燃烧(有的高炉也喷吹煤粉、重油、天然气等辅助燃料),在高温下焦炭中的碳同鼓入空气中的氧燃烧生成的一氧化碳和氢气。
原料、燃料随着炉内熔炼等过程的进行而下降,在炉料下降和上升的煤气相遇,先后发生传热、还原、熔化、脱炭作用而生成生铁,铁矿石原料中的杂质与加入炉内的熔剂相结合而成渣,炉底铁水间断地放出装入铁水罐,送往炼钢厂。
同时产生高炉煤气,炉渣两种副产品,高炉渣铁主要矿石中不还原的杂质和石灰石等熔剂结合生成,自渣口排出后,经水淬处理后全部作为水泥生产原料;产生的煤气从炉顶导出,经除尘后,作为热风炉、加热炉、焦炉、锅炉等的燃料。
炼铁工艺流程和主要排污节点见上图。
三、高炉冶炼主要工艺设备简介高护炼铁设备组成有:①高炉本体;②供料设备;③送风设备;④喷吹设备;⑤煤气处理设备;⑥渣铁处理设备。
宝钢生产工艺流程
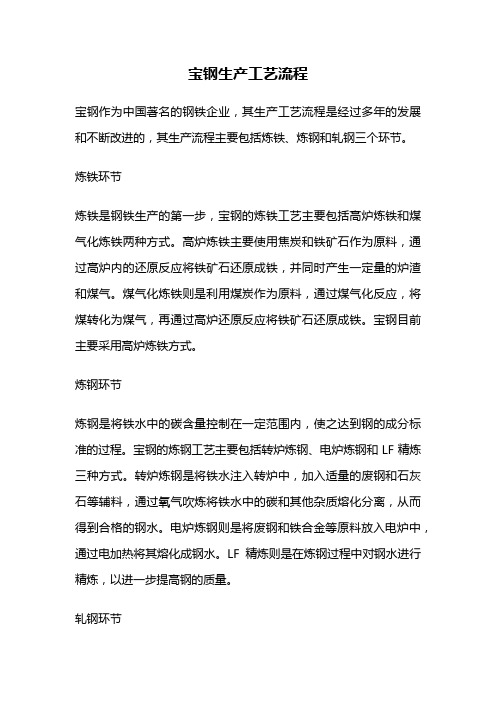
宝钢生产工艺流程
宝钢作为中国著名的钢铁企业,其生产工艺流程是经过多年的发展和不断改进的,其生产流程主要包括炼铁、炼钢和轧钢三个环节。
炼铁环节
炼铁是钢铁生产的第一步,宝钢的炼铁工艺主要包括高炉炼铁和煤气化炼铁两种方式。
高炉炼铁主要使用焦炭和铁矿石作为原料,通过高炉内的还原反应将铁矿石还原成铁,并同时产生一定量的炉渣和煤气。
煤气化炼铁则是利用煤炭作为原料,通过煤气化反应,将煤转化为煤气,再通过高炉还原反应将铁矿石还原成铁。
宝钢目前主要采用高炉炼铁方式。
炼钢环节
炼钢是将铁水中的碳含量控制在一定范围内,使之达到钢的成分标准的过程。
宝钢的炼钢工艺主要包括转炉炼钢、电炉炼钢和LF精炼三种方式。
转炉炼钢是将铁水注入转炉中,加入适量的废钢和石灰石等辅料,通过氧气吹炼将铁水中的碳和其他杂质熔化分离,从而得到合格的钢水。
电炉炼钢则是将废钢和铁合金等原料放入电炉中,通过电加热将其熔化成钢水。
LF精炼则是在炼钢过程中对钢水进行精炼,以进一步提高钢的质量。
轧钢环节
轧钢是将钢坯或钢材经过加热、调质等工序后,通过轧机压制成不同形状和规格的钢材的过程。
宝钢的轧钢工艺主要包括热轧和冷轧两种方式。
热轧是将加热后的钢坯通过轧机加工成各种规格的钢材,主要用于制造大型构件和钢板等。
冷轧则是将冷却后的钢坯通过轧机加工成一定规格的冷轧板、冷轧带钢等,主要用于制造汽车、电器等产品。
总结
宝钢的生产工艺流程是一个完整的系统,每个环节都至关重要。
通过不断创新和改进,宝钢不断提高生产效率和产品质量,为国家的工业发展做出了重要贡献。
宝钢工艺流程分析
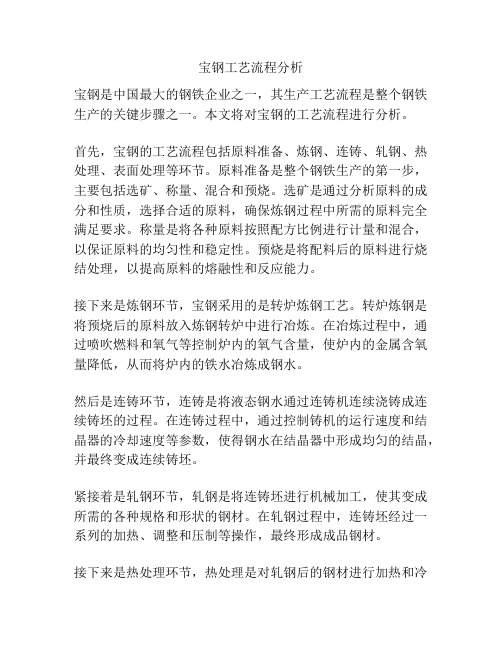
宝钢工艺流程分析宝钢是中国最大的钢铁企业之一,其生产工艺流程是整个钢铁生产的关键步骤之一。
本文将对宝钢的工艺流程进行分析。
首先,宝钢的工艺流程包括原料准备、炼钢、连铸、轧钢、热处理、表面处理等环节。
原料准备是整个钢铁生产的第一步,主要包括选矿、称量、混合和预烧。
选矿是通过分析原料的成分和性质,选择合适的原料,确保炼钢过程中所需的原料完全满足要求。
称量是将各种原料按照配方比例进行计量和混合,以保证原料的均匀性和稳定性。
预烧是将配料后的原料进行烧结处理,以提高原料的熔融性和反应能力。
接下来是炼钢环节,宝钢采用的是转炉炼钢工艺。
转炉炼钢是将预烧后的原料放入炼钢转炉中进行冶炼。
在冶炼过程中,通过喷吹燃料和氧气等控制炉内的氧气含量,使炉内的金属含氧量降低,从而将炉内的铁水冶炼成钢水。
然后是连铸环节,连铸是将液态钢水通过连铸机连续浇铸成连续铸坯的过程。
在连铸过程中,通过控制铸机的运行速度和结晶器的冷却速度等参数,使得钢水在结晶器中形成均匀的结晶,并最终变成连续铸坯。
紧接着是轧钢环节,轧钢是将连铸坯进行机械加工,使其变成所需的各种规格和形状的钢材。
在轧钢过程中,连铸坯经过一系列的加热、调整和压制等操作,最终形成成品钢材。
接下来是热处理环节,热处理是对轧钢后的钢材进行加热和冷却处理,以改变钢材的组织结构和性能。
热处理的具体方式包括淬火、回火、正火等等,根据不同的钢材和要求进行选择。
最后是表面处理环节,表面处理主要是对钢材的表面进行清洁和涂层处理。
清洁是通过酸洗等方式去除钢材表面的氧化物和杂质,以提高钢材表面的光洁度和质量。
涂层是将防锈漆、润滑油等涂覆在钢材表面,以保护钢材的表面不被氧化和腐蚀。
综上所述,宝钢的工艺流程包括原料准备、炼钢、连铸、轧钢、热处理、表面处理等环节,每个环节都有严格的控制和操作要求,以确保生产出高质量的钢材。
宝钢凭借其强大的技术实力和丰富的生产经验,在国内钢铁产业中处于领先地位。
宝钢三高炉II系设备工艺
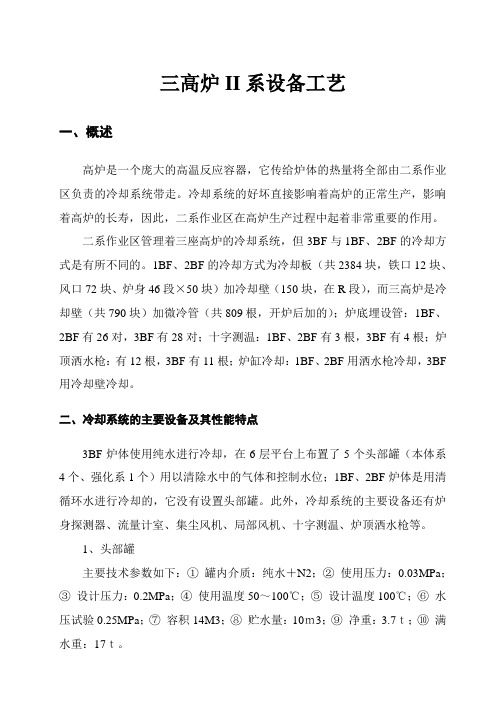
三高炉II系设备工艺一、概述高炉是一个庞大的高温反应容器,它传给炉体的热量将全部由二系作业区负责的冷却系统带走。
冷却系统的好坏直接影响着高炉的正常生产,影响着高炉的长寿,因此,二系作业区在高炉生产过程中起着非常重要的作用。
二系作业区管理着三座高炉的冷却系统,但3BF与1BF、2BF的冷却方式是有所不同的。
1BF、2BF的冷却方式为冷却板(共2384块,铁口12块、风口72块、炉身46段×50块)加冷却壁(150块,在R段),而三高炉是冷却壁(共790块)加微冷管(共809根,开炉后加的);炉底埋设管:1BF、2BF有26对,3BF有28对;十字测温:1BF、2BF有3根,3BF有4根;炉顶洒水枪:有12根,3BF有11根;炉缸冷却:1BF、2BF用洒水枪冷却,3BF 用冷却壁冷却。
二、冷却系统的主要设备及其性能特点3BF炉体使用纯水进行冷却,在6层平台上布置了5个头部罐(本体系4个、强化系1个)用以清除水中的气体和控制水位;1BF、2BF炉体是用清循环水进行冷却的,它没有设置头部罐。
此外,冷却系统的主要设备还有炉身探测器、流量计室、集尘风机、局部风机、十字测温、炉顶洒水枪等。
1、头部罐主要技术参数如下:①罐内介质:纯水+N2;②使用压力:0.03MPa;③设计压力:0.2MPa;④使用温度50~100℃;⑤设计温度100℃;⑥水压试验0.25MPa;⑦容积14M3;⑧贮水量:10m3;⑨净重:3.7t;⑩满水重:17t。
冷却系统补水标准:当头部罐水位低于-300mm时开始补水,当头部罐水位高于300mm时停止补水。
强化系一天补水3~4次,每隔7、8个小时补一次水。
2、炉身探测器①工艺技术条件②主要技术规格3、流量计室每个高炉各有4个流量计室,分别位于4根柱子旁。
3BF各流量计室内控制的风口为:1#流量计室:35#~38#,1#~6#;2#流量计室:7#~15#;3#流量计室:16#~25#;4#流量计室:26#~34#。
宝钢5000立方米高炉主沟通铁量300~350万吨的实践
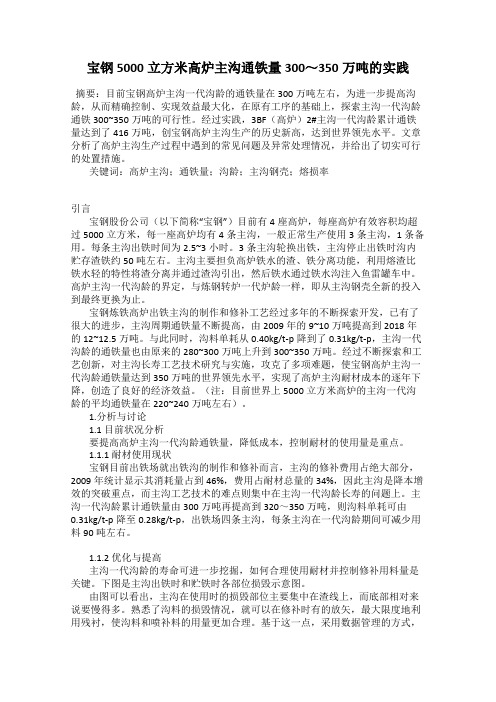
宝钢5000立方米高炉主沟通铁量300~350万吨的实践摘要:目前宝钢高炉主沟一代沟龄的通铁量在300万吨左右,为进一步提高沟龄,从而精确控制、实现效益最大化,在原有工序的基础上,探索主沟一代沟龄通铁300~350万吨的可行性。
经过实践,3BF(高炉)2#主沟一代沟龄累计通铁量达到了416万吨,创宝钢高炉主沟生产的历史新高,达到世界领先水平。
文章分析了高炉主沟生产过程中遇到的常见问题及异常处理情况,并给出了切实可行的处置措施。
关键词:高炉主沟;通铁量;沟龄;主沟钢壳;熔损率引言宝钢股份公司(以下简称“宝钢”)目前有4座高炉,每座高炉有效容积均超过5000立方米,每一座高炉均有4条主沟,一般正常生产使用3条主沟,1条备用。
每条主沟出铁时间为2.5~3小时。
3条主沟轮换出铁,主沟停止出铁时沟内贮存渣铁约50吨左右。
主沟主要担负高炉铁水的渣、铁分离功能,利用熔渣比铁水轻的特性将渣分离并通过渣沟引出,然后铁水通过铁水沟注入鱼雷罐车中。
高炉主沟一代沟龄的界定,与炼钢转炉一代炉龄一样,即从主沟钢壳全新的投入到最终更换为止。
宝钢炼铁高炉出铁主沟的制作和修补工艺经过多年的不断探索开发,已有了很大的进步,主沟周期通铁量不断提高,由2009年的9~10万吨提高到2018年的12~12.5万吨。
与此同时,沟料单耗从0.40kg/t-p降到了0.31kg/t-p,主沟一代沟龄的通铁量也由原来的280~300万吨上升到300~350万吨。
经过不断探索和工艺创新,对主沟长寿工艺技术研究与实施,攻克了多项难题,使宝钢高炉主沟一代沟龄通铁量达到350万吨的世界领先水平,实现了高炉主沟耐材成本的逐年下降,创造了良好的经济效益。
(注:目前世界上5000立方米高炉的主沟一代沟龄的平均通铁量在220~240万吨左右)。
1.分析与讨论1.1 目前状况分析要提高高炉主沟一代沟龄通铁量,降低成本,控制耐材的使用量是重点。
1.1.1 耐材使用现状宝钢目前出铁场就出铁沟的制作和修补而言,主沟的修补费用占绝大部分,2009年统计显示其消耗量占到46%,费用占耐材总量的34%,因此主沟是降本增效的突破重点,而主沟工艺技术的难点则集中在主沟一代沟龄长寿的问题上。
高炉炼铁生产工艺流程简介
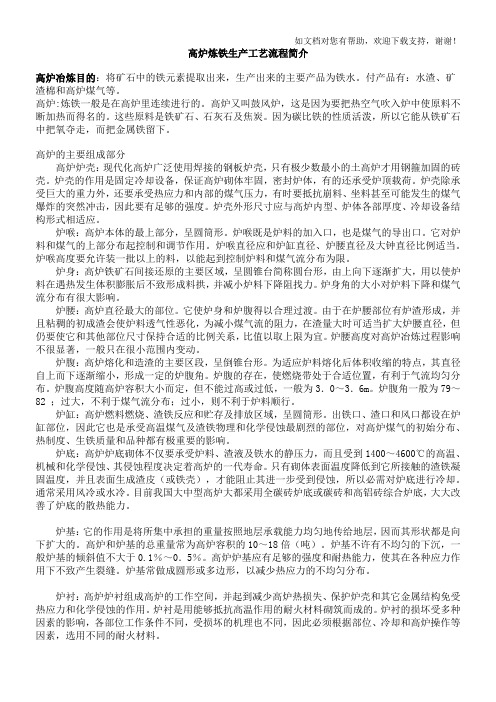
高炉炼铁生产工艺流程简介高炉冶炼目的:将矿石中的铁元素提取出来,生产出来的主要产品为铁水。
付产品有:水渣、矿渣棉和高炉煤气等。
高炉:炼铁一般是在高炉里连续进行的。
高炉又叫鼓风炉,这是因为要把热空气吹入炉中使原料不断加热而得名的。
这些原料是铁矿石、石灰石及焦炭。
因为碳比铁的性质活泼,所以它能从铁矿石中把氧夺走,而把金属铁留下。
高炉的主要组成部分高炉炉壳:现代化高炉广泛使用焊接的钢板炉壳,只有极少数最小的土高炉才用钢箍加固的砖壳。
炉壳的作用是固定冷却设备,保证高炉砌体牢固,密封炉体,有的还承受炉顶载荷。
炉壳除承受巨大的重力外,还要承受热应力和内部的煤气压力,有时要抵抗崩料、坐料甚至可能发生的煤气爆炸的突然冲击,因此要有足够的强度。
炉壳外形尺寸应与高炉内型、炉体各部厚度、冷却设备结构形式相适应。
炉喉:高炉本体的最上部分,呈圆筒形。
炉喉既是炉料的加入口,也是煤气的导出口。
它对炉料和煤气的上部分布起控制和调节作用。
炉喉直径应和炉缸直径、炉腰直径及大钟直径比例适当。
炉喉高度要允许装一批以上的料,以能起到控制炉料和煤气流分布为限。
炉身:高炉铁矿石间接还原的主要区域,呈圆锥台简称圆台形,由上向下逐渐扩大,用以使炉料在遇热发生体积膨胀后不致形成料拱,并减小炉料下降阻找力。
炉身角的大小对炉料下降和煤气流分布有很大影响。
炉腰:高炉直径最大的部位。
它使炉身和炉腹得以合理过渡。
由于在炉腰部位有炉渣形成,并且粘稠的初成渣会使炉料透气性恶化,为减小煤气流的阻力,在渣量大时可适当扩大炉腰直径,但仍要使它和其他部位尺寸保持合适的比例关系,比值以取上限为宜。
炉腰高度对高炉冶炼过程影响不很显著,一般只在很小范围内变动。
炉腹:高炉熔化和造渣的主要区段,呈倒锥台形。
为适应炉料熔化后体积收缩的特点,其直径自上而下逐渐缩小,形成一定的炉腹角。
炉腹的存在,使燃烧带处于合适位置,有利于气流均匀分布。
炉腹高度随高炉容积大小而定,但不能过高或过低,一般为3.0~3.6m。
宝钢高炉操作指南
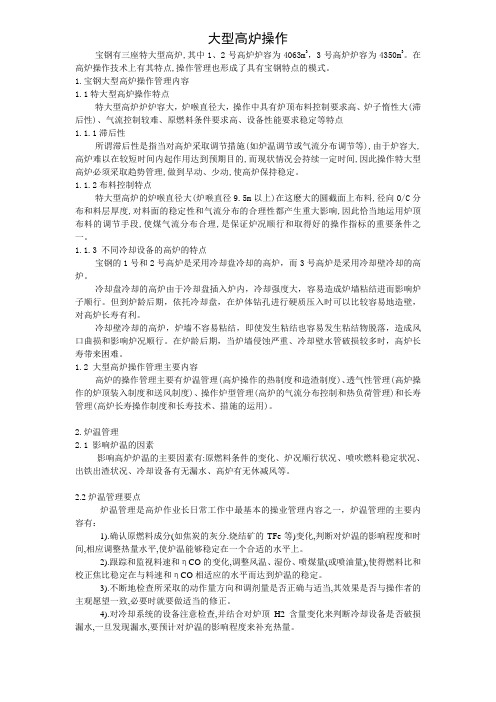
大型高炉操作宝钢有三座特大型高炉,其中1、2号高炉炉容为4063m3,3号高炉炉容为4350m3。
在高炉操作技术上有其特点,操作管理也形成了具有宝钢特点的模式。
1.宝钢大型高炉操作管理内容1.1特大型高炉操作特点特大型高炉炉炉容大,炉喉直径大,操作中具有炉顶布料控制要求高、炉子惰性大(滞后性)、气流控制较难、原燃料条件要求高、设备性能要求稳定等特点1.1.1滞后性所谓滞后性是指当对高炉采取调节措施(如炉温调节或气流分布调节等),由于炉容大,高炉难以在较短时间内起作用达到预期目的,而现状情况会持续一定时间,因此操作特大型高炉必须采取趋势管理,做到早动、少动,使高炉保持稳定。
1.1.2布料控制特点特大型高炉的炉喉直径大(炉喉直径9.5m以上)在这麽大的圆截面上布料,径向O/C分布和料层厚度,对料面的稳定性和气流分布的合理性都产生重大影响,因此恰当地运用炉顶布料的调节手段,使煤气流分布合理,是保证炉况顺行和取得好的操作指标的重要条件之一。
1.1.3 不同冷却设备的高炉的特点宝钢的1号和2号高炉是采用冷却盘冷却的高炉,而3号高炉是采用冷却壁冷却的高炉。
冷却盘冷却的高炉由于冷却盘插入炉内,冷却强度大,容易造成炉墙粘结进而影响炉子顺行。
但到炉龄后期,依托冷却盘,在炉体钻孔进行硬质压入时可以比较容易地造壁,对高炉长寿有利。
冷却壁冷却的高炉,炉墙不容易粘结,即使发生粘结也容易发生粘结物脱落,造成风口曲损和影响炉况顺行。
在炉龄后期,当炉墙侵蚀严重、冷却壁水管破损较多时,高炉长寿带来困难。
1.2 大型高炉操作管理主要内容高炉的操作管理主要有炉温管理(高炉操作的热制度和造渣制度)、透气性管理(高炉操作的炉顶装入制度和送风制度)、操作炉型管理(高炉的气流分布控制和热负荷管理)和长寿管理(高炉长寿操作制度和长寿技术、措施的运用)。
2.炉温管理2.1 影响炉温的因素影响高炉炉温的主要因素有:原燃料条件的变化、炉况顺行状况、喷吹燃料稳定状况、出铁出渣状况、冷却设备有无漏水、高炉有无休减风等。
宝钢高炉炉前脱硅技改工程简介1
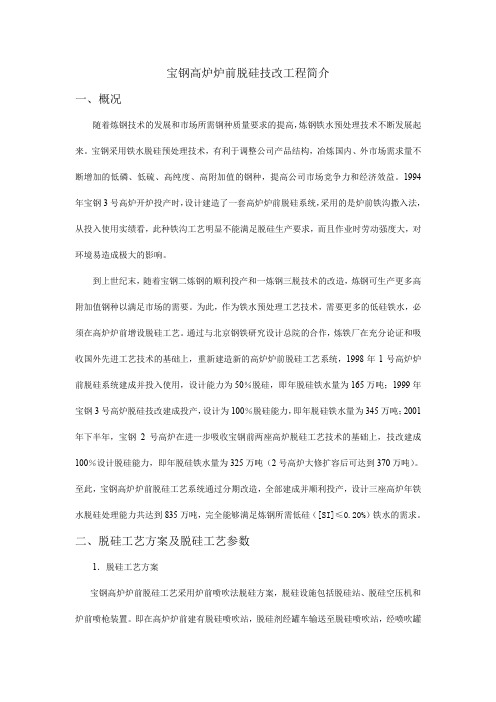
宝钢高炉炉前脱硅技改工程简介一、概况随着炼钢技术的发展和市场所需钢种质量要求的提高,炼钢铁水预处理技术不断发展起来。
宝钢采用铁水脱硅预处理技术,有利于调整公司产品结构,冶炼国内、外市场需求量不断增加的低磷、低硫、高纯度、高附加值的钢种,提高公司市场竞争力和经济效益。
1994年宝钢3号高炉开炉投产时,设计建造了一套高炉炉前脱硅系统,采用的是炉前铁沟撒入法,从投入使用实绩看,此种铁沟工艺明显不能满足脱硅生产要求,而且作业时劳动强度大,对环境易造成极大的影响。
到上世纪末,随着宝钢二炼钢的顺利投产和一炼钢三脱技术的改造,炼钢可生产更多高附加值钢种以满足市场的需要。
为此,作为铁水预处理工艺技术,需要更多的低硅铁水,必须在高炉炉前增设脱硅工艺。
通过与北京钢铁研究设计总院的合作,炼铁厂在充分论证和吸收国外先进工艺技术的基础上,重新建造新的高炉炉前脱硅工艺系统,1998年1号高炉炉前脱硅系统建成并投入使用,设计能力为50%脱硅,即年脱硅铁水量为165万吨;1999年宝钢3号高炉脱硅技改建成投产,设计为100%脱硅能力,即年脱硅铁水量为345万吨;2001年下半年,宝钢2号高炉在进一步吸收宝钢前两座高炉脱硅工艺技术的基础上,技改建成100%设计脱硅能力,即年脱硅铁水量为325万吨(2号高炉大修扩容后可达到370万吨)。
至此,宝钢高炉炉前脱硅工艺系统通过分期改造,全部建成并顺利投产,设计三座高炉年铁水脱硅处理能力共达到835万吨,完全能够满足炼钢所需低硅([SI]≤0.20%)铁水的需求。
二、脱硅工艺方案及脱硅工艺参数1.脱硅工艺方案宝钢高炉炉前脱硅工艺采用炉前喷吹法脱硅方案,脱硅设施包括脱硅站、脱硅空压机和炉前喷枪装置。
即在高炉炉前建有脱硅喷吹站,脱硅剂经罐车输送至脱硅喷吹站,经喷吹罐加压、流化后,通过喷吹管线,从脱硅喷枪喷入出铁中的摆动流咀中,脱硅剂(主要是烧结矿除尘粉,含较高的FeO)与铁水一起进入鱼雷罐中,脱硅剂与铁水中的[SI]发生剧烈反应,形成SiO2进入渣中,从而达到铁水脱[SI]的目的。
宝钢三高炉设备概况

三高炉冶炼设备表面一、概述:宝钢股份公司三号高炉是目前海内最大的高炉,其有效容积达4350M 3,日产优质、及格铁水达万吨以上,作为炼钢铁水的主要供给者,其自己就是一个集高新技能于一身的设计难度高、工艺庞大、制造要求高的庞大的设备系统。
三高炉冶炼设备按作业区分别主要包罗运转系统、炉前出铁系统、炉前II 系系统、煤粉系统和水渣系统等五大系统,各系统间相对独立但又部门影响,在宁静、高效地配合作用下包管了高炉的稳产、高产。
炉腰:15.2M炉缸:14M炉吼:10.1m1VS2VSDCTRTSV焦炭OREC O C OOCOKEHS HS HS HS焦槽450m3*8烧结矿槽650m3*8块矿槽220m3*6小块焦槽600m3*2副原料槽:220m3*4焦碳中间料斗80m3*2矿石中间料斗60m3*2上料主皮带:宽:2.2M 长:347M速度:120M/MIN 矿石:3500T/H 焦碳:1300T/H旋转料罐80m3称量料罐:80m3溜槽:长:4.5M转速:8R/MIN 倾动:11档,内容积:4350m3铁口*4风口*384座新日铁式外燃式热风炉,最高风温:1310度余压发电高压伐组制粉喷吹设备:二台碗式中速磨煤机,串罐下喷式,分A 、B 、C 三个系统,从38个风口喷入煤粉。
煤气清洗系统分:重力除尘,1文氏,2文氏300吨混铁车INBA 法水渣铁口风口二、运转系统:运转作业区所辖设备包罗原料系统、炉顶装入系统、热风炉系统、煤气清洗系统和余压发电系统(TRT),其日常事情任务是对五大系统进行操纵、监督、点检和维护,该作业区统领着高炉约莫75%的设备,其特点是区域广、工艺庞大、技能要求高。
运转作业区卖力将矿石、焦炭、热风等高炉生产必须的原料和介质三高炉工艺流程总图适时适量的送入高炉内,包管高炉的生产能连续进行。
因此,运转作业区的日常事情对高炉的正常生产起着至关重要的作用。
㈠、原料系统:1、主要设备的规格及作用原料系统主要由两大部门组成:矿石系统和焦炭系统,其主要设备有皮带、矿槽、焦槽、称量漏斗、中间漏斗、转换溜槽、振动筛等。
宝钢炼钢工艺和设备详细

宝钢炼钢工艺和设备详细宝钢集团有限公司是中国最大的钢铁企业之一,拥有先进的炼钢工艺和设备。
炼钢是将生铁或废钢通过冶炼和精炼等工艺,制成合格的钢材的过程。
宝钢炼钢工艺和设备的先进性,直接影响到钢材的质量和生产效率。
下面我们来详细了解一下宝钢的炼钢工艺和设备。
首先是炼钢工艺。
宝钢采用了先进的转炉炼钢工艺,主要包括废钢预处理、炼钢冶炼、精炼和连铸等环节。
在废钢预处理环节,宝钢采用了先进的废钢分选技术,将不同种类的废钢进行分类处理,以保证炼钢过程中的原料质量。
在炼钢冶炼环节,宝钢主要采用转炉冶炼工艺,通过高温燃烧和氧气吹炼,将生铁或废钢中的杂质和不良元素去除,得到高质量的熔铁。
在精炼环节,宝钢采用了LF精炼炉和VD真空脱气设备,通过精确控制温度和气氛,进一步提高钢材的纯度和均匀性。
最后,在连铸环节,宝钢采用了连铸机组,将熔化的钢水连续浇铸成坯料,为后续的轧制和成品加工提供原料。
其次是炼钢设备。
宝钢拥有一批先进的炼钢设备,包括转炉、精炼炉、连铸机组等。
其中,转炉是炼钢的核心设备,宝钢拥有多台不同规格的转炉,能够满足不同种类钢材的生产需求。
精炼炉是提高钢材质量的关键设备,宝钢引进了国际先进的LF和VD设备,通过真空脱气和精确的合金添加,提高了钢材的纯度和均匀性。
连铸机组是将熔化的钢水浇铸成坯料的设备,宝钢的连铸机组采用了先进的直接结晶技术,能够生产高质量的连铸坯料。
除了上述的主要工艺和设备外,宝钢还在炼钢过程中引入了先进的自动化控制系统和在线检测设备,以确保生产过程的稳定性和钢材质量的可控性。
同时,宝钢还注重节能减排,采用了高效的热能回收设备和环保设施,实现了炼钢过程的清洁生产。
总的来说,宝钢的炼钢工艺和设备处于国际领先水平,能够满足不同种类钢材的生产需求,保证钢材质量和生产效率。
未来,宝钢还将继续引进先进的炼钢技术和设备,不断提升自身的竞争力和可持续发展能力。
宝钢300吨转炉生产工艺介绍
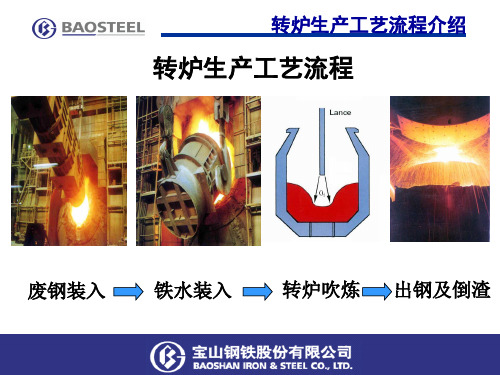
转炉生产工艺流程
废钢装入
铁水装入
转炉吹炼 出钢及倒渣
生产工艺流程介绍—装入制度
宝钢的装入制度: 宝钢采用的是定量装入制度,装入量有严格的规定。
装入量的确定 1.装入量计算:
装入量(吨)=目标出钢量(吨)/出钢收得率(%) 铁水量(吨)=装入量×铁水比(%) 冷铁量(吨)=装入量×冷铁比(%) 废钢量(吨)=装入量-铁水量-冷铁量 2.目标出钢量计算 目标出钢量=目标锭或坯量(吨)+补正量(吨)
装入的最大、最小量 根据操作、设备的限制,规定主原料装入量的最大、最小量。 ①操作上的制约 铁水:最大100%~最小73%;废钢:最小0%~最大27%;冷铁: 最小0%~最大5% ②设备的制约 铁水:最大量315吨/炉次;废钢:最大量95吨/炉次
生产工艺流程介绍—装入制度
宝钢废钢、生铁的入炉标准
废钢铁应按规定分类供应,不允许有成套的机器、设备及结构件;低合 金废钢铁应与普通废钢分别管理;废钢铁中不准有二端封闭的管状物及封闭 器皿、易燃、易爆物及毒品等。对其性质和尺寸规定如下:
注:各修正参数可参考技术规程。
二、300t转炉过程温度的控制计算方法 根据炉内反应理论以及炉内O2平衡、热平衡 ,引入冷却能的概念, 计算出每炉钢所需冷却剂量或发热剂量和吹氧量,进而对转炉过程 温度进行控制。具体计算方法可参见技术规程。
生产工艺流程介绍—复吹工艺
宝钢300t氧气顶吹转炉于1990年6月进行了复吹改造,底部喷吹惰性气体的弱搅拌 型复吹工艺,以改善钢水纯净度,提高经济效益,充分发挥大型氧气转炉炼钢的优势。 宝钢转炉的复吹方式采用新日铁的LD-CB顶底复吹技术,主要底吹N2和Ar气,供气强度 0.022~0.11Nm3/min.t,N2总管压力1.5~1.7MPa,Ar气总管压力2.4~2.6MPa。目前底 部供气风口有6孔、6孔、10孔等方式,其中1#炉、3#炉均为二路控制,2#炉经2002年 10月份进行BRP脱磷改造以后变为五路单独可调控制。风口的透气砖有2种型式,一种 是日本黑崎窑业圆形Φ4×39,即由39根精制的细不锈钢管组成,每根管内径4mm;另 一种是奥镁方形Φ2.5×96,即由96根内径2.5mm的不锈钢管组成。风口的透气砖长度 为900mm,但2#炉因BRP改造现采用1200mm长度的透气砖。 复吹工艺的优点:
宝钢的生产管理系统介绍(完整版)
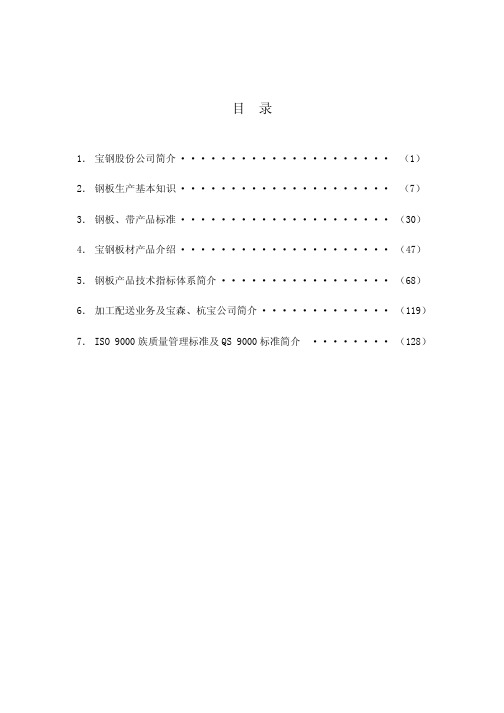
宝钢的质量管理与质量保证体系于 1994 年通过了由 BSI-QA(英国标准协 会质量保证部)进行的 ISO 9001-1994 认证,成为中国领先获得 ISO 9000 系 列标准认证的大型钢铁联合企业之一。1999 年又通过了美国三大汽车公司(通 用、福特、克莱斯勒)的 QS 9000 标准认证,进一步提升了宝钢的质量保证体 系层次。
电镀锌机组从奥地利引进,采用鲁斯纳重力法,钝化采用辊涂,这样锌层 及钝化层更均勾。机组电镀槽后采用全封闭保证了电镀锌卷表面的清洁,可生 产适于作汽车零件的厚镀层电镀锌及锌镍合金化产品,卷宽可达 1830mm。
热镀锌机组从德国西马克引进,可生产无铅零锌花及锌铁合金化产品,先 进的镀层厚度闭环自动控制系统保证了镀锌层重量均匀,入口段设置高级强化
2030 冷轧主体设备分别从德国、日本和美国成套引进,包括酸洗机组、 2030mm 五机架全连续冷轧机组、罩式退火炉、单机架四辊式平整机组、六段立 式连续退火机组(CAPL)、横切、纵切及重卷机组、连续热镀锌机组、连续电镀 锌机组、彩色涂层机组等。
先进的生产技术有:采用了盐酸浅槽酸洗,可有效地清除热轧来料表面氧 化铁皮;生产过程采用计算机控制;装有厚度自动控制 AGC 系统,确保轧后厚 度精度;轧机装有最新的板型检测调节装置和 CVC 轧辊凸度连续可变的调节技 术,保证了板型平直;计算机控制的罩式退火炉可按不同钢种及堆垛方式分别 采用不同的退火曲线;CAPL 连续退火机组可一次完成脱脂、再结晶退火和平整 工艺,使冷轧板(卷)获得良好的力学性能。
宝钢炼钢技术资料

≤ 0 .1 2 ≤ 0 .1 2 ≤ 0 .1 2 ≤ 0 .0 3 ~ 0 .0 1
35 174 79 35
≥ 0 .3 0 ≤ 0 .0 0 5 ≤ 0 .3 0 ≤ 0 .0 1 ~ 0 .0 0 5
-
10
二炼钢铁水预处理
2
宝钢一炼钢RH脱气处理计划
单位:万吨/年(基本设计审查后)
类 品 油 井 管 条 钢 钢 锅 炉 钢 管 高 压 锅 炉 管 普 通 钢 管 外 供 钢 管 坯 计 焊 条 钢 钢 轨 钢 低 合 金 钢 普 通 碳 素 钢 计 热 轧 普 通 钢 深 冲 用 钢 低 合 金 钢 螺 旋 焊 管 钢 计 钢 锭 用 钢 水 合 计 普 碳 钢 R ib a n d 钢 A L- K 钢 低 合 金 钢 造 船 用 碳 素 钢 低 合 金 钢 螺 旋 焊 管 钢 计 合 计 月 生 产 能 力 t/月 RH 处 理 量 3 8 .2 6 .3 3 .3 4 .6 2 .5 5 4 .9 3 .4 1 0 .3 1 3 .7 6 .1 6 .1 3 .7 1 5 .9 8 4 .5 5 4 .7 6 8 .7 2 5 .3 5 .3 1 3 .5 1 6 7 .2 252 21
6
一炼钢主要原材料及辅助材料 主要原材料 铁水化学成分
C 4 ~ 4 .5 Si 0 .4 ~ 0 .8 M n > 0 .4 S < 0 .0 4 P ≤ 0 .1 2 Cu ≤ 0 .0 6 ∑ A* ≤ 0 .3
*∑ A = C u = N i+ C r+ A s + S n + T i+ V + P b + C o + Z n + S b + B i+ A l+ M o + M g 铁 水 温 度 在 高 炉 炉 前 挡 渣 堰 处 1500℃ 以 上 。
宝钢生产工艺流程

宝钢生产工艺流程工艺流程是指在宝钢生产过程中,原料的处理、各个环节的加工、成品的制造等一系列步骤和方法。
下面将详细介绍宝钢的生产工艺流程。
1. 原料准备宝钢的主要原料是铁矿石、焦炭和石灰石。
首先,铁矿石经过破碎和磨矿的处理,使其粒度合适;焦炭则通过破碎、筛分和烘干等步骤进行处理,以保证其质量;石灰石经过破碎、筛分和烘干等工序,以满足生产需要。
2. 炼铁在宝钢的炼铁工艺中,采用高炉法。
首先,将铁矿石、焦炭和石灰石按一定比例混合,并送入高炉中。
高炉内部通过高温和还原剂的作用,使铁矿石中的铁氧化物被还原成金属铁,并与石灰石反应生成炉渣。
炉渣和铁水分离后,得到生铁。
3. 精炼生铁中含有杂质,需要进行精炼处理。
宝钢采用转炉法进行精炼。
将生铁装入转炉中,通过吹氧和加入石灰石等辅助剂的方式,使杂质被氧化、还原或结合,从而得到低含碳的钢水。
4. 连铸将精炼后的钢水倒入连铸机中,通过结晶器的作用,使钢水逐渐冷却凝固,形成连续的坯料。
坯料经过切割后,得到符合要求的铸坯。
5. 热轧铸坯经过预热后,送入热轧机中。
热轧机通过辊道的作用,将铸坯进行多道次的轧制,使其逐渐变薄,并得到带有一定形状的热轧板卷。
6. 酸洗热轧板卷中含有氧化铁皮和锈蚀层等杂质,需要进行酸洗处理。
将热轧板卷浸入酸洗槽中,通过酸洗液的作用,使杂质被溶解掉,从而得到干净的钢板。
7. 冷轧经过酸洗的钢板送入冷轧机中。
冷轧机通过辊道的作用,将钢板进行多道次的轧制,使其进一步变薄,并得到带有更高表面质量的冷轧板卷。
8. 退火冷轧板卷中存在一定的残余应力,需要进行退火处理。
将冷轧板卷送入退火炉中,通过加热和冷却的方式,使钢板的晶粒重新排列,消除残余应力,从而提高钢板的强度和韧性。
9. 镀锌或涂层根据不同需求,一部分钢板需要进行镀锌或涂层处理。
镀锌是将钢板浸入熔融的锌液中,形成一层锌层;涂层是将涂料涂覆在钢板表面,形成一层保护膜。
这样可以提高钢板的耐腐蚀性能和美观度。
宝钢高炉炉型特点及其对操作的影响
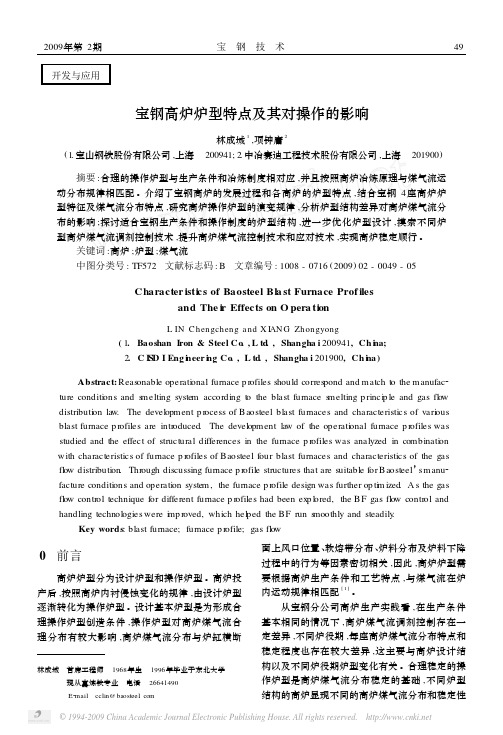
2009年第2期宝 钢 技 术开发与应用宝钢高炉炉型特点及其对操作的影响林成城1,项钟庸2(1.宝山钢铁股份有限公司,上海 200941;2.中冶赛迪工程技术股份有限公司,上海 201900) 摘要:合理的操作炉型与生产条件和冶炼制度相对应,并且按照高炉冶炼原理与煤气流运动分布规律相匹配。
介绍了宝钢高炉的发展过程和各高炉的炉型特点,结合宝钢4座高炉炉型特征及煤气流分布特点,研究高炉操作炉型的演变规律,分析炉型结构差异对高炉煤气流分布的影响;探讨适合宝钢生产条件和操作制度的炉型结构,进一步优化炉型设计,摸索不同炉型高炉煤气流调剂控制技术,提升高炉煤气流控制技术和应对技术,实现高炉稳定顺行。
关键词:高炉;炉型;煤气流中图分类号:TF572 文献标志码:B 文章编号:1008-0716(2009)02-0049-05Character isti cs of Baosteel Bl a st Furnace Prof ilesand The i r Effects on O pera ti onL IN C hengcheng and X I AN G Zhongyong(1.Baoshan I ron&Steel Co.,L td.,Shangha i200941,Ch i n a;2.C I S D I Eng i n eer i n g Co.,L td.,Shangha i201900,Ch i n a) Abstract:Reas onable operati onal furnace p r ofiles should corres pond and match t o the manufac2 ture conditi ons and s melting syste m according t o the blast furnace s melting p rinci p le and gas fl ow distributi on la w.The devel opment p r ocess of Baosteel blast furnaces and characteristics of vari ous blast furnace p r ofiles are intr oduced.The devel opment la w of the operati onal furnace p r ofiles was studied and the effect of structural differences in the furnace p r ofiles was analyzed in combinati on with characteristics of furnace p r ofiles of Baosteel f our blast furnaces and characteristics of the gas fl ow distributi on.Thr ough discussing furnace p r ofile structures that are suitable f or Baosteel’smanu2 facture conditi ons and operati on syste m,the furnace p r ofile design was further op ti m ized.A s the gas fl ow contr ol technique f or different furnace p r ofiles had been ex p l ored,the BF gas fl ow contr ol and handling technol ogies were i m p r oved,which hel ped the BF run s moothly and steadily.Key words:blast furnace;furnace p r ofile;gas fl ow0 前言高炉炉型分为设计炉型和操作炉型。
宝钢高炉炼铁工艺介绍ppt课件
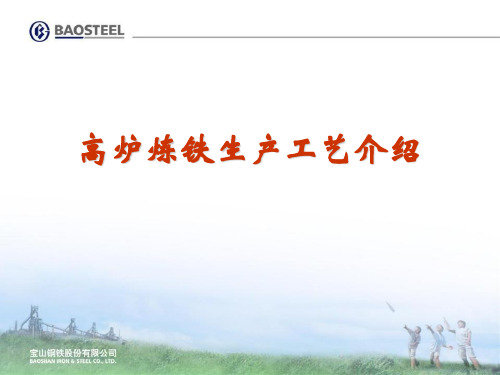
1 2 0 m /m i n
CC OO O
炉顶装料
BF
喷煤系统
重力 除尘器
热风
1VS 2VS
TRT
调压阀组
消音器
水封装置
冷风
HS HS
HS
HS
最高风温
1310℃
最高拱顶温度 1450℃
最高废气温度
350℃
混铁车
高炉脱硅装 置
2、高炉工艺流程介绍
高炉冶炼物流流程
原燃料 鼓风机
矿石 焦炭 辅料 煤粉
高温鼓风
1、行车、悬臂吊车等起重设备; 2、泥炮; 3、开口机; 4、移盖机; 5、摆动流嘴; 6、残铁开口机; 7、主沟、渣铁沟; 8、液压系统。
2.6高炉炉前工艺流程
2、高炉工艺流程介绍
2.7高炉炉渣处理流程
2、高炉工艺流程介绍
渣处理方式
水渣:熔渣经过冷却水急冷,产生细碎颗粒状水渣,用于制作水泥。 干渣:熔渣放入坑中,洒水冷却,冷却后挖掘清运出厂,用于铺路。
水渣处理工艺
LASA法:粗粒分离槽与脱水槽脱水;电消耗大,管道易磨损,占地大 。 INBA法:转鼓与成品槽脱水,水电消耗少,管道阀门寿命长,占地少。 新INBA法:较INBA法增加了蒸汽冷却装置,环保,耗电增多。
2.7高炉炉渣处理流程
压缩空气
烟囱
2、高炉工艺流程介绍
风扇
冷却 塔
炉渣
渣水槽
渣水沟
冲渣水
P 事故水
渣皮带
输送皮带
渣槽
转鼓
P
集水槽 温水槽
P
水渣
P
P
2.7高炉炉渣处理流程
2、高炉工艺流程介绍
2.8高炉除尘系统
- 1、下载文档前请自行甄别文档内容的完整性,平台不提供额外的编辑、内容补充、找答案等附加服务。
- 2、"仅部分预览"的文档,不可在线预览部分如存在完整性等问题,可反馈申请退款(可完整预览的文档不适用该条件!)。
- 3、如文档侵犯您的权益,请联系客服反馈,我们会尽快为您处理(人工客服工作时间:9:00-18:30)。
焦槽,B侧矿槽为球团矿槽、块矿槽和副原料槽。
矿槽槽下设有给料
机、振动筛、称量料斗 及皮带机等设备;
焦槽下设有振动筛
及皮带机等设备。
高炉炉顶装料流程
项 目 上部漏斗 下料罐 溜槽长度 大钟直径 炉顶压力 探尺数量 单位 m3 m3 mm mm MPa 把 1BF 40 80 2BF 3BF 80 80 80 80 4500 4500
Z-101BC
Z-301BC UHG US
闸阀
No 1 No 2 No 3 No 4
7300 0.25 0.25 0.25 4 3 3
No 1 No 2 No 3
No 4
密封阀
FCG LSV
小钟
溜槽
探尺 导料板
大钟 探尺
串罐式炉顶装料流程
一次排压阀 二次排压阀 消音器 一均 上部密封阀 二均
GAS
高炉生产工艺与设备
宝钢股份炼铁厂
高炉技术组 2014.10
提
一、炼铁厂概况
纲
二、高炉生产工艺流程介绍
三、高炉本体结构及冶炼特点 四、高炉操作基本知识简介
第一部分
炼铁厂概况
宝钢股份炼铁厂生产组织结构
炼铁厂 Iron Making Plant
高炉分厂 Blast Furnace Branch 炼焦分厂 Coking Branch 铁焦设备车间 Blast Furnace & Coking Equipment Workshop
意义:高炉喷煤是现代高炉炼铁技术革命性的重大措施。
(1)以煤粉代焦,高炉吨铁焦比降低,生铁成本下降; (2)调剂高炉热制度的有效手段; (3)可改善高炉炉缸工作状态,使高炉稳定顺行; (4)降低理论燃烧温度,为高炉使用高风温和富氧鼓风创造了条件; (5)煤粉释放出更多的氢气,提高了煤气的还原能力和穿透扩散能力 ,利于矿石还原和高炉操作指标的改善; (6)喷吹煤粉替代部分冶金焦炭减少了炼焦设施投资; (7)降低了炼焦生产对环境的污染。
贫煤 无烟煤
辅料
硅石
石灰石
白云石 锰矿
钛矿
高炉原料输送流程
焦槽
Y-301BC Y-302BC
焦炭称量漏斗
C C
Z-301BC
矿槽
Y-307BC
矿石称量漏斗
X-301BC
X-302BC
矿石中间漏斗 O O
X-303BC
Z-301BC
原料称量系统分矿石和焦炭两个部分。 矿槽为双排料槽布置,A侧矿槽为烧结矿、块矿和小块
煤气清洗流程一
项 目 处理煤气量 (m3/h)
3
DC 700000 13.5 5000
1VS 700000 5 100
2VS 700000 0.1 <10
进口粉尘浓度 (g/m ) 出口粉尘浓度 (mg/m3)
BF
重力 除尘器
TRT 1VS 2VS
消音器 调压阀 组
水封装置
煤气清洗流程二
煤 气 总 网
“以高炉为中心”
炼钢
烧结
高炉
炼焦
原料
原料分厂简介
原料工序是我国钢铁企业第一个现代化的大型原料处理厂,对全公司的 原燃料进行集中管理,以精料为宗旨向全公司各用户供料。具有以下特点: 大型化:料场占地面积1.02平方公里;年作业总量1亿吨。 现代化:计算机、PLC高效率集中分级控制,并实现三电一体化。 先进性:装备良好的环境保护设备;混匀矿堆积采用先进的数模智能控制。
高炉分厂简介
高 炉 分 厂
现有四座5000m³级大型高炉, 年产铁达到1500万吨以上。
宝钢高炉发展阶段
85年~91年
单高炉生产
91年~97年
发展时期
97年~至今
创新时期
No1 BF
85.9.15
96.4-97.5 91.6.29 94.9.20
2008.9-2009.2.15 2006.9-2006.12.7 2013.9-2013.11.16
热风炉基本工作原理 热风炉主要有三种工作状态:燃烧状态、送风状态和 换炉过程。热风炉处于燃烧状态时,向热风炉送入高炉 煤气和助燃空气,燃料燃烧产生热量使热风炉蓄热;热 风炉处于送风状态时,向燃烧结束的热风炉送入冷风, 经热风炉加热后送入高炉。上述二种状态间的转换定义 为换炉过程。
高炉煤气清洗系统 高炉煤气清洗系统介绍
行车、悬臂吊车等起重设备; 泥炮; 开口机; 移盖机; 摆动流嘴; 残铁开口机; 主沟、渣铁沟; 液压系统;
出铁场主要功能
1、及时安全排放高炉产生渣铁; 2、将铁口排放的渣铁进行分离; 3、运输存储高炉生产检修等资材; 4、清除高炉产生粉尘;
出渣铁管理内容
1. 2. 3. 4. 5. 6. 7. 8. 见渣时间; 出渣率; 铁口深度; 打泥量; 出铁次数; 出铁速度; 出渣速度; 设备点检;
直吹管
高炉喷煤系统流程图
热风炉废 气烟囱
原煤仓
旋风分离器
再循环废气 布袋除尘器
给煤机 Distributer
振动筛
热风炉废 气引风机
主排风机
×18支 管 分配器
仓顶除尘器
磨煤 流化气
煤粉仓
排气系统
×2
Air
BFG
干燥炉
喷吹罐 1# 2# 3#
输送压缩 空气 混合器
高 炉
COG N2 加压、流化气
高炉炉渣处理系统
原料分厂 Raw Material Branch 烧结分厂 Sintering Branch 原烧设备车间 Raw Material & Sintering Equipment Workshop
高炉大修项目组 Blast Furnace Overhaul Project Team 生产技术室 Production Technology Division 设备技术室 Equipment Management Division 办公室 Administrative Office
炼焦分厂简介
炼焦分厂原有国内6米大容积焦炉12座计600孔,一、二 、三期焦炉设计生产能力分别为年产171万吨。 一、二、三期首座焦炉的投产日期分别为:85年8月、91年5 月和97年12月。 配备有煤处理、成型煤、炼焦炉、干熄焦和焦处理系统 ;其中一二期焦炉共用一套煤处理及成型煤系统。 目前,正在对现有三期焦炉进行扩容改造,改建成7米大 容积焦炉,更适合当前炼铁及公司未来发展需要。
炉顶装料 矿石 TRT
Z101BC X102BC 1600mm 1800mm 120m/min O RE 3500t/h
重力 除尘器
1VS 2VS 消音器 调压阀组
焦炭 焦炭
120m/min
BF
水封装置
冷风
C C O O O HS HS HS HS
最高风温 1310 ℃ 最高拱顶温度 最高废气温度
热风
环缝洗涤塔:粉尘与水滴碰撞凝聚,同时,蒸汽促使粉尘集 合。 干法除尘:通过滤袋将煤气中的粉尘除去并收集起来,具有 除尘效率高,节约水的优点,同时能提高TRT发电量。
高炉喷煤系统 高炉喷煤系统介绍 原理:高炉喷煤就是把原煤(无烟煤、烟煤)经过烘干、磨细,用压缩
空气(或氮气)输送,通过喷煤枪从高炉风口直接喷入炉缸的生产工艺。
高炉内型 高炉有效容积 各部位直径 有效高度 高径比(矮胖、瘦长型) 风口、铁口 死铁层厚度
高炉用冷却器
高炉用冷却器主要包括二大类:
冷却板、冷却壁(铜冷却壁、铸铁冷却壁铸钢冷 却壁)。
另外,还有一类是作为维修用的微型冷却器。
冷却板实物及解剖图
冷 却 壁 图 片
光面冷却壁
镶砖冷却壁
微型冷却器实物及解剖图
烧结分厂简介
烧结分厂原有三台鲁奇式烧结机。三台烧结机的有效烧结面积为分别 为490m2、490m2、490m2,投产日期分别为85年8月、91年6月和 98年4月。在2003年10月、2004年9月和2005年3月分别于进行了扩 容改造,改造后的有效烧结面积为分别为495m2、495 m2、495m2 。目前正在实施改造,改造后的三台烧结机面积为650m² 。
渣处理方式
水渣: 熔渣经过冷却水急冷,产生细碎颗粒状 水渣,用于制作水泥。
干渣: 熔渣放入坑中,洒水冷却,冷却后挖掘 清运出厂,用于铺路。
水渣处理方法 LASA法:粗粒分离槽与脱水槽脱水; INBA法:转鼓与成品槽脱水; 新INBA法:转鼓与成品槽脱水,增加了蒸汽 冷却装置。
三种水渣处理方式比较
采用贮铁式主沟
鱼雷罐受铁
高炉除尘系统
高炉除尘系统
原料区域,包括矿石除尘与焦炭除尘;
1.出铁场除尘;
2.一次除尘,主沟、渣铁沟、撇渣器、摆动流嘴、炉顶 ; 3.二次除尘,散发到出铁场的粉尘再收集; 4.铸铁除尘;
5.碾泥除尘;
第三部分
高炉本体结构及冶炼特点
高炉本体结构
高炉五段式结构
高炉本体组成主要包括: 1、炉皮 2、冷却器 3、耐火材料 4、炉基 5、框架
LASA法:电消耗大,管道易磨损,占地大; INBA法:水电消耗少,管道阀门寿命长,占地少; 新INBA法:环保,耗电增多。
风扇
压缩空气 烟囱 冷却 塔
炉渣
渣水槽
渣水沟 渣皮带
输送皮带 渣槽
冲渣水
转鼓
P
集水槽
P 事故水
温水槽
P
水渣
P P
高炉炉前工艺流程
出铁场主要设备
1. 2. 3. 4. 5. 6. 7. 8.
No2 BF
No3 BF
No4 BF
2005.4.27
2014.9-
宝钢高炉炉容实绩
炉号
1BF 2BF 3BF 4BF
炉容(m³)
1代