作图技术要求大全
工程制图图样上的技术要求

过盈配合 用于零件间只依托结合面之间旳过盈来实现传动旳场合(无键、 销、
螺钉等紧固件),过盈配合旳零件不可拆卸
过渡配合 用于零件间定位精确、无相对运动,要求能拆卸旳场合。
17
二、配合
2. 配合旳基准制
2、配合旳基准制 1)基孔制
2)基轴制
1)基孔制 基本偏差为一定旳孔旳公差带,与不同基本偏差旳轴旳公
4
第一节 极限与配合
一、尺寸公差
2. 极限偏差 尺寸公差
极限偏差:极限尺寸减基本尺寸所得代数差
(代数差,能够是正值、负值或零)
上偏差=最大极限尺寸﹣基本尺寸 下偏差=最小极限尺寸﹣基本尺寸
孔
上偏差代号为ES 下偏差代号为EI
ES = +0.021
EI = 0
公差=0.021
轴 上偏差代号为es
下偏差代号为ei
ቤተ መጻሕፍቲ ባይዱ
2)过盈配合
3)过渡配合
1)间隙配合
间隙
• 确保具有间隙旳配合,孔公差带完全在轴公差带之上,任 取其中一对孔和轴相配,都成为具有间隙旳配合(涉及最小 间隙为零)
15
二、配合
1、配合旳种类
1、配合种类 1)间隙配合
2)过盈配合 3)过渡配合
过盈配合
• 确保具有过盈旳配合。孔公差带完全在轴公差带之下,任
标注上、下偏差旳措施
P.200
上、下偏差数值 相同步旳标注措13 施
二、配合
1、配合旳种类
基本尺寸相同旳,相互结合旳孔和轴公差带之间旳关系称为配合
根据使用要求旳不同, 孔和轴之间旳配合有 松有紧
三种配合种类
• 间隙配合 • 过盈配合 • 过渡配合
14
CAD图纸技术要求

一般技术要求:1、零件去除氧化皮。
2、零件加工表面上不应有划痕、擦伤等损伤零件表面的缺陷。
3、去除毛刺。
热处理要求:1、经调质处理,HRC50~55。
2、零件进行高频淬火,350~370℃回火,HRC40~45。
3、渗碳深度0.3mm。
4、进行高温时效处理。
公差要求:1、未注形状公差应符合GB1184-80的要求。
2、未注长度尺寸允许偏差±0.5mm。
3、铸件公差带对称于毛坯铸件基本尺寸配置。
零件棱角:1、未注圆角半径R5。
2、未注倒角均为C2。
3、锐角倒钝。
装配要求:1、各密封件装配前必须浸透油。
2、装配滚动轴承允许采用机油加热进行热装,油的温度不得超过100℃。
3、齿轮箱装配后应设计和工艺规定进行空载试验。
试验时不应有冲击、噪声,温升和渗漏不得超过有关标准规定。
4、齿轮装配后,齿面的接触斑点和侧隙应符合GB10095和GB11365的规定。
5、装配液压系统时允许使用密封填料或密封胶,但应防止进入系统中。
6、进入装配的零件及部件(包括外购件、外协件),均必须具有检验部门的合格证方能进行装配。
7、零件在装配前必须清理和清洗干净,不得有毛刺、飞边、氧化皮、锈蚀、切屑、油污、着色剂和灰尘等。
8、装配前应对零、部件的主要配合尺寸,特别是过盈配合尺寸及相关精度进行复查。
9、装配过程中零件不允许磕、碰、划伤和锈蚀。
10、螺钉、螺栓和螺母紧固时,严禁打击或使用不合适的旋具和扳手。
紧固后螺钉槽、螺母和螺钉、螺栓头部不得损坏。
11、规定拧紧力矩要求的紧固件,必须采用力矩扳手,并按规定的拧紧力矩紧固。
12、同一零件用多件螺钉(螺栓)紧固时,各螺钉(螺栓)需交叉、对称、逐步、均匀拧紧。
13、圆锥销装配时应与孔应进行涂色检查,其接触率不应小于配合长度的60%,并应均匀分布。
14、平键与轴上键槽两侧面应均匀接触,其配合面不得有间隙。
15、花键装配同时接触的齿面数不少于2/3,接触率在键齿的长度和高度方向不得低于50%。
机械人必备的图纸技术要求大全,建议收藏

机械人必备的图纸技术要求大全,建议收藏引领机械前沿、机械视频,汽车、加工技术、3D打印、自动化、机器人、生产工艺、轴承、模具、机床、钣金等行业前沿在这里等你机械图纸技术要求汇总,机械人必备资料,记得收藏!▌一般技术要求1. 零件去除氧化皮。
2. 零件加工表面上,不应有划痕、擦伤等损伤零件表面的缺陷。
3. 去除毛刺飞边。
▌热处理要求1. 经调质处理,HRC50~55。
2. 零件进行高频淬火,350~370℃回火,HRC40~45。
3. 渗碳深度0.3mm。
4. 进行高温时效处理。
▌公差要求1. 未注形状公差应符合GB1184-80的要求。
2. 未注长度尺寸允许偏差±0.5mm。
3. 铸件公差带对称于毛坯铸件基本尺寸配置。
▌零件棱角1. 未注圆角半径R5。
2. 未注倒角均为2×45°。
3. 锐角/尖角/锐边倒钝。
▌装配要求1. 各密封件装配前必须浸透油。
2. 装配滚动轴承允许采用机油加热进行热装,油的温度不得超过100℃。
3. 齿轮装配后,齿面的接触斑点和侧隙应符合GB10095和GB11365的规定。
4. 装配液压系统时允许使用密封填料或密封胶,但应防止进入系统中。
5. 进入装配的零件及部件(包括外购件、外协件),均必须具有检验部门的合格证方能进行装配。
6. 零件在装配前必须清理和清洗干净,不得有毛刺、飞边、氧化皮、锈蚀、切屑、油污、着色剂和灰尘等。
7. 装配前应对零、部件的主要配合尺寸,特别是过盈配合尺寸及相关精度进行复查。
8. 装配过程中零件不允许磕、碰、划伤和锈蚀。
9. 螺钉、螺栓和螺母紧固时,严禁打击或使用不合适的旋具和扳手。
紧固后螺钉槽、螺母和螺钉、螺栓头部不得损坏。
10. 规定拧紧力矩要求的紧固件,必须采用力矩扳手,并按规定的拧紧力矩紧固。
11. 同一零件用多件螺钉(螺栓)紧固时,各螺钉(螺栓)需交叉、对称、逐步、均匀拧紧。
12. 圆锥销装配时应与孔应进行涂色检查,其接触率不应小于配合长度的60%,并应均匀分布。
图纸上的技术要求汇总
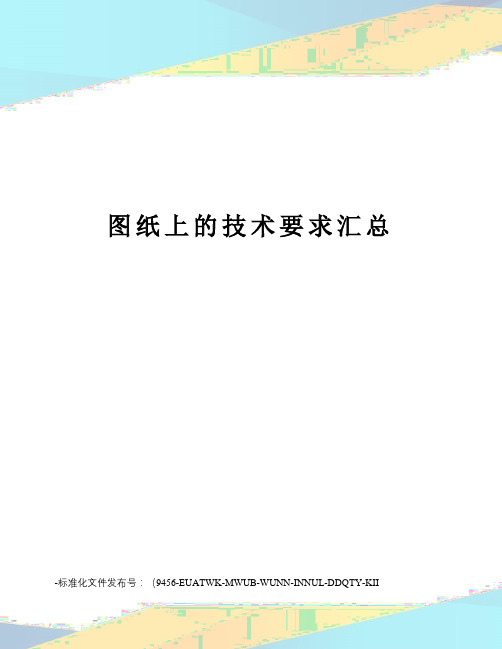
图纸上的技术要求汇总-标准化文件发布号:(9456-EUATWK-MWUB-WUNN-INNUL-DDQTY-KII图纸技术要求一、一般技术要求制件去除表面氧化皮;制件不得有划痕、擦伤等损伤零件表面的缺陷;去除毛刺飞边;锐角倒钝;未注倒角均为0.5×45%%d;未注越程槽均为1.2×0.3;表面平整无毛刺;二、未注公差技术要求(金属件)未注公差尺寸的极限偏差按GB/T 1804-m;未注形位公差按GB/T 1184-K;未注长度尺寸允许偏差±0.5;三、表面处理技术要求表面镀白(黑)锌处理;表面喷漆(喷塑)处理;表面发黑处理;表面电泳处理;表面镀铬处理;表面抛光处理;表面滚花,直纹(网纹)m=0.4 GB/T 6403.3;四、热处理技术要求制件氮化450-480HV;制件毛坯须调质处理220-260HB;制件调质处理30-35HRC;制件高频淬火45~50HRC;制件渗碳处理,深度>0.1;制件进行高温回火处理;制件整体淬火40-45HRC;五、铸件技术要求1、压铸件技术要求未注公差尺寸的极限偏差按GB/T 1804-m;未注形位公差按GB/T 1184-K;未注倒角均为0.5×45%%d;未注壁厚2.5;未注筋板1.5~2;未注过渡圆角R0.5-R2;未注脱模斜度≤1%%d;制件饱满光洁、无气孔、缩松、裂纹、夹渣、缺料等缺陷;各脱模顶料推杆压痕均应低于该制件表面0.2;制件要求符合GB/T 15114《铝合金压铸件》标准规定;表面喷漆(喷塑)处理,不得污染到已加工表面;加工表面在表面处理后加工,加工后涂油保护;未注尺寸参照三维造型;制件表面处理及其它要求按客户定;2、砂型铸造技术要求未注铸造圆角R5-10;铸件应彻底清砂,浇冒口应清除平整;铸件需人工时效;铸件不得有砂眼、气孔、缩松、裂纹等缺陷;粗加工后应再次进行人工时效;不加工表面涂底漆;六、冲压件技术要求制件未注公差尺寸的极限偏差按GB/T 15055-m;制件未注形位公差按GB/T 13916-2级;制件不得有裂纹或缺损;制件表面平整,不得有沟痕、碰伤等损坏表面,降低强度及寿命的缺陷;去除边角毛刺;表面处理:七、塑料件技术要求未注公差尺寸的极限偏差按GB/T 14486-MT6级;制件应饱满光整、色泽均匀;无缩痕、裂纹、银丝等缺陷;浇口、溢边修剪后飞边≤0.3,且不得伤及本体;未注壁厚3;未注筋板1.5~2;表面打光(喷砂)处理;未注过渡圆角取R0.3~R1,脱模斜度≤0.3%%d;各脱模顶料推杆压痕均应低于该制件表面0.2;与对应装配结合面外形配合错位≤0.5;制件应进行时效处理;制件机械强度须符合GB 3883.1标准规定;制件内腔表面打上材料标记和回收标志;未注尺寸参照三维造型;制件表面处理及其它要求由客户定;八、焊接件技术要求未注公差线性及角度尺寸的极限偏差均按GB/T 19804-B级;未注形位公差按GB/T 19804-F级;焊缝应均匀平整,焊渣清理干净;焊缝应焊透,不得烧穿及产生裂纹等影响机械性能的缺陷;九、各类零、部件技术要求1、齿轮(齿轴)技术要求未注公差尺寸的极限偏差按GB/T 1804-m;未注形位公差按GB/T 1184-K;制件毛坯须调质220~260HB;制件材料的化学成分和力学性能应符合GB/T 3077的规定;齿面接触斑点:按齿高不小于40%,按齿长不小于50%;齿面高频淬火回火至49-52HRC;制件表面不应有锈迹、裂纹、灼伤等影响使用寿命的伤痕及缺陷;最终工序热处理表面不得有氧化皮;2、一般轴芯(无铣齿)技术要求未注公差尺寸的极限偏差按GB/T 1804-m;未注形位公差按GB/T 1184-K;未注倒角均为0.5×45%%d;未注越程槽均为1.2×0.3;制件毛坯须调质220~260HB;尺寸%%c 档车正反两条螺旋槽,螺距10,深0.4;螺纹表面不允许有磕碰、乱扣、毛刺等缺陷;热处理:表面处理:3、包轴毛坯(一次成型)技术要求未注公差尺寸的极限偏差按GB/T 1804-m;未注形位公差按GB/T 1184-K;绝缘层应饱满光洁,无裂纹、气孔、缺料、杂质等缺陷;包轴毛坯:绝缘层%%c 档(注:指冲片配合档)与轴芯间应能承受50Hz,实际正弦波电压2500V历时1min不击穿,其余绝缘层档3750V历时1min不击穿;一次成型:铁芯与轴芯间应能承受50Hz,实际正弦波电压2500V历时1min不击穿,其余绝缘层档3750V历时1min不击穿;4、包轴(加工)技术要求未注公差尺寸的极限偏差按GB/T 1804-m;未注形位公差按GB/T 1184-K;塑层应饱满光洁,无裂纹、气孔、缺料、杂质等缺陷;塑层%%c 档(注:指冲片配合档)与轴芯间应能承受50Hz,实际正弦波电压2500V历时1min不击穿,其余塑层档3750V历时1min不击穿;制件磨加工后应烘干除水处理;5、转子技术要求未注公差尺寸的极限偏差按GB/T 1804-m;未注形位公差按GB/T 1184-K;绕组接线按转子绕线原理图;绕组绝缘漆应均匀充满绕组并充分固化,漆膜应均匀无气泡或裂痕;云母槽开深0.8~1,槽宽0.6,槽内不得残留云母片;绕组冷态绝缘电阻不低于50MΩ;装风叶后校动平衡,其精度应不低于G6.3级;去重不允许有冲片铣穿、残缺现象;铁芯外圆不加工,绝缘漆不得高出铁芯外圆,并不得有明显积瘤;铁芯与轴芯间应能承受50Hz,实际正弦波电压2500V,1min不击穿;绕组与铁芯间应能承受50Hz,实际正弦波电压1250V,1min不击穿;匝间绝缘应能承受1000Hz,峰值为2100V,历时3s不击穿;换向器与轴芯间应能承受50Hz,实际正弦波电压3750V,1min不击穿;应去除铁屑、铜粉、油污等杂质;铁芯外圆应涂透明淡金水防锈处理;6、定子技术要求绕组绕制整齐无松散;引线接头应牢固可靠且充分绝缘;绕组与铁芯间应能承受50Hz,实际正弦波电压1250V历时1min不击穿;匝间绝缘应能承受1000Hz,峰值为2100V,历时3s不击穿;绕组绝缘漆应均匀充满绕组并充分固化,漆膜应均匀无气泡或积瘤;铁芯表面不得有明显绝缘漆;7、定、转子铁芯技术要求未注公差尺寸的极限偏差按GB/T 1804-m;未注形位公差按GB/T 1184-K;冲片叠装应紧密可靠,片间无夹杂,表面及槽内无污物和油渍;冲片按同一冲制方向压装;冲片齿槽口整齐与转轴平行,误差不大于0.5;铁芯两端弹开度不大于0.5;8、定、转子冲片技术要求制件未注公差尺寸的极限偏差按GB/T 15055-m;制件未注形位公差按GB/T 13916-2级;制件应表面平整,完整无缺料;尖角处允许用R0.3过渡;制件毛刺不大于0.05(注:高速冲时不大于0.02);制件应不含油脂,剪切油不能用机油;9、绝缘纸技术要求表面不得有划痕、折痕;裁边不起毛;10、换向器技术要求未注公差尺寸的极限偏差按GB/T 1804-m;未注形位公差按GB/T 1184-K;外观完整,表面光滑,应无裂纹、毛刺、锈蚀、气孔、夹杂等缺陷;绝缘电阻:室温下内孔与换向片之间大于50MΩ;云母片厚度取0.5;换向片对换向器轴线偏斜度不大于云母片厚度的1/3;介电强度:片间承受频率50Hz,泄露电流为0.1mA,实际正弦波电压600V历时1s不击穿;换向片与内孔轴芯间承受频率50Hz,泄露电流为0.25mA,实际正弦波电压3750V历时1min不击穿;试验与检验应符合JB/T 10107《电动工具换向器》标准要求;11、电缆线技术要求电缆线长度尺寸指工具电缆出口至插头的导线部分,不包括插头和插脚;软电缆应符合GB/T 5013《额定电压450V/750V及以下橡皮绝缘电缆》标准要求;聚氯乙烯电缆应符合GB/T 5023《额定电压450V/750V及以下聚氯乙烯绝缘电缆》标准要求;插脚与可触及插头表面的绝缘应能承受50Hz,实际正弦波电压3750V历时1min不击穿;制件还应符合GB 1002《家用和类似用途单相插头插座型式、基本参数和尺寸》和GB 2099《家用和类似用途插头插座》标准要求;12、开关技术要求未注公差尺寸的极限偏差按SJ/T 10628-7级;除本图要求的外形尺寸、功能、图形、文字外,试验和检验均应符合GB/T 22692《电动工具开关》标准要求;开关的使用性能应保证5万次无故障正常使用;13、电缆护套技术要求未注公差尺寸的极限偏差按GB/T 3672.1-2级;未注形位公差按GB/T 3672.2-M级;制件不得有缺料、破裂等缺陷。
图纸技术要求大全
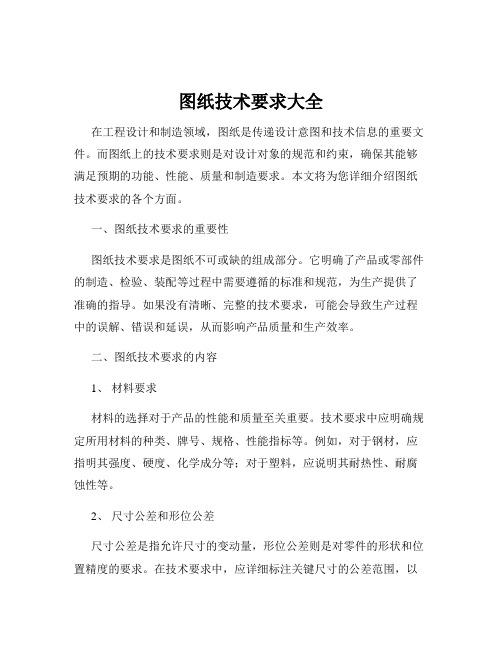
图纸技术要求大全在工程设计和制造领域,图纸是传递设计意图和技术信息的重要文件。
而图纸上的技术要求则是对设计对象的规范和约束,确保其能够满足预期的功能、性能、质量和制造要求。
本文将为您详细介绍图纸技术要求的各个方面。
一、图纸技术要求的重要性图纸技术要求是图纸不可或缺的组成部分。
它明确了产品或零部件的制造、检验、装配等过程中需要遵循的标准和规范,为生产提供了准确的指导。
如果没有清晰、完整的技术要求,可能会导致生产过程中的误解、错误和延误,从而影响产品质量和生产效率。
二、图纸技术要求的内容1、材料要求材料的选择对于产品的性能和质量至关重要。
技术要求中应明确规定所用材料的种类、牌号、规格、性能指标等。
例如,对于钢材,应指明其强度、硬度、化学成分等;对于塑料,应说明其耐热性、耐腐蚀性等。
2、尺寸公差和形位公差尺寸公差是指允许尺寸的变动量,形位公差则是对零件的形状和位置精度的要求。
在技术要求中,应详细标注关键尺寸的公差范围,以及形状(如平面度、圆度)和位置(如平行度、垂直度)的公差要求。
这有助于保证零件之间的配合精度和装配质量。
3、表面质量要求表面质量直接影响产品的外观、耐磨性和耐腐蚀性等。
技术要求中应规定表面粗糙度、表面处理方式(如电镀、喷漆)以及表面缺陷的允许程度。
4、热处理要求对于需要进行热处理的零件,应明确热处理的类型(如淬火、回火、退火)、工艺参数(如温度、时间)以及处理后的性能指标。
5、加工工艺要求这包括加工方法(如车削、铣削、磨削)、加工顺序、切削参数等。
此外,对于一些特殊的加工工艺,如焊接、铸造、锻造等,也应给出相应的技术要求。
6、装配要求如果是装配图,应规定零部件的装配顺序、配合要求、紧固力矩等,以确保装配的正确性和可靠性。
7、检验要求明确检验的方法、量具、检验项目和验收标准。
这有助于保证产品在生产过程中的质量控制。
8、包装和标识要求说明产品的包装方式、防护措施以及标识内容(如产品名称、型号、批次、生产日期等),以便于产品的储存、运输和识别。
图纸技术要求大全

图纸技术要求大全在工程和制造领域,图纸是至关重要的沟通工具,它能够清晰地传达设计意图和规范,确保产品或项目的顺利实施。
而图纸上的技术要求则是对设计的进一步补充和说明,为生产、加工、检验等环节提供了明确的指导。
下面我们就来详细了解一下图纸技术要求的方方面面。
一、尺寸与公差要求尺寸是图纸中最基本的元素之一,它准确地描述了零件或结构的大小和形状。
在标注尺寸时,需要遵循一定的标准和规范,确保尺寸的清晰、准确和完整。
同时,为了保证零件在制造过程中的互换性和功能性,还需要规定公差。
公差是允许尺寸的变动量,分为尺寸公差和形位公差。
尺寸公差控制零件的尺寸精度,形位公差则控制零件的形状和位置精度。
例如,对于一个圆柱形零件,不仅要规定其直径的尺寸和公差,还要规定圆柱度、同轴度等形位公差要求。
二、材料要求材料的选择直接影响到产品的性能、质量和成本。
在图纸技术要求中,需要明确指定所使用的材料种类、牌号、规格等信息。
例如,对于机械零件,可以指定使用 45 号钢、铝合金等材料,并注明其热处理要求,如淬火、回火等。
对于建筑结构,可能会指定使用混凝土的强度等级、钢材的型号等。
此外,还需要考虑材料的供应情况和成本,选择合适的替代材料方案。
三、表面处理要求表面处理可以提高零件的耐腐蚀性、耐磨性、美观度等性能。
常见的表面处理方法包括电镀、喷涂、氧化等。
在图纸技术要求中,需要明确表面处理的种类、工艺要求和质量标准。
例如,对于需要防锈的零件,可以要求进行镀锌处理,并规定镀层的厚度和质量要求。
对于外观要求较高的零件,可以进行喷漆处理,并指定漆的颜色、光泽度等要求。
四、加工工艺要求加工工艺是将原材料转化为成品的过程,它直接影响到产品的质量和生产效率。
在图纸技术要求中,需要根据零件的结构和功能,规定合理的加工工艺方法和顺序。
例如,对于一个复杂的零件,可能需要先进行铸造或锻造,然后再进行机械加工。
对于有精度要求的孔和轴,可能需要采用磨削加工工艺。
工程制图技术要求

技术要求•用一些规定的符号、数字以及文字注解等表示出零件制造后在技术指标上所应达到的要求。
主要包括:•表面粗糙度•公差与配合•形和位置公差(简称形位公差)。
•零件的表面处理、热处理、检验要求等。
4、标题栏•说明零件的名称、材料、数量、图的编号、比例以及描绘、审核人员签字等。
一、表面粗糙度的概念零件表面经加工后,看起来很光滑,见下图a,若用放大镜观察、则会看到表面有明显高低不平的粗糙痕迹,见下图b。
这种零件加工表面上所存在的较小间距的峰谷组成的微观几何特性称为表面粗糙度。
表面粗糙度反映了零件表面的质量,它对零件的装配、工作精度、疲劳强度、耐磨、抗蚀和外观等都有影响。
零件的表面粗糙度应根据零件的作用恰当地选择。
表面粗糙度的主要参数评定表面粗糙度的参数有三项,即:轮廓算术平均偏差Ra;轮廓算术平均偏差轮廓算术平均偏差是指在取样长度L(用于判别具有表面粗糙度特征的一段基准线长度)内,轮廓偏距y(表面轮廓上点至基准线的距离)绝对值的算术平均值,用Ra表示,轮廓算术平均偏差Ra的标准数值及对应的取样长度和评定长度见下表。
微观不平度十点高度Rz;轮廓最大高度Ry。
表面粗糙度符号、代号表面粗糙度代号及意义见下表。
表面粗糙度符号的画法见下图。
表面粗糙度数值及其有关规定详见GB/T131一93,在符号中注写的位置见下图。
表面粗糙度代(符)号在图样上的标注方法表面粗糙度代号中数字及符号的方向必须按下图a的规定标注。
带有横线的表面粗糙度符号应按下图b的规定标注。
在图样上,当空间狭小或不便标注时可以引出标注,见下图。
当零件所有表面具有相同的表面粗糙度要求时,可统一标注在图样的右上角,见下图。
零件上连续表面(下图)、重复要素(如孔、齿、槽等)的表面和用细实线连接不连续的同一表面,其表面粗糙度代(符)号只注一次。
同一表面上有不同的表面粗糙度要求时,应用细实线画出其分界线,并注出相应的表面粗糙度代号和尺寸,见下图。
齿轮、螺纹等工作表面没有画出齿(牙)形时,其表面粗糙度代(符)号注法见下图。
制图技术要求大全

技术要求大全一、一般技术要求:1.零件去除氧化皮.2.零件加工表面上,不应有划痕、擦伤等损伤零件表面的缺陷。
3.去除毛刺飞边。
二、热处理要求:1.经调质处理,HRC50~55。
2.零件进行高频淬火,350~370℃回火,HRC40~45。
3.渗碳深度0.3mm。
三、公差要求:1.未注形状公差应符合GB1184-80的要求。
2.未注长度尺寸允许偏差±0.5mm。
.铸件公差带对称于毛坯铸件基本尺寸配置。
四、零件棱角:1.未注圆角半径R5。
2.未注倒角均为2×45°。
3.锐角倒钝。
五、铸件要求:1.铸件表面上不允许有冷隔、裂纹、缩孔和穿透性缺陷及严重的残缺类缺陷(如欠铸、机械损伤等)。
2.铸件应清理干净,不得有毛刺、飞边,非加工表明上的浇冒口应清理与铸件表面齐平。
3.铸件非加工表面上的铸字和标志应清晰可辨,位置和字体应符合图样要求。
铸件非加工表面的粗糙度,砂型铸造R,不大于50μm。
4.铸件应清除浇冒口、飞刺等。
非加工表面上的浇冒口残留量要铲平、磨光,达到表面质量要求。
5.铸件上的型砂、芯砂和芯骨应清除干净。
6.铸件有倾斜的部位、其尺寸公差带应沿倾斜面对称配置。
7.铸件上的型砂、芯砂、芯骨、多肉、粘沙等应铲磨平整,清理干净。
8.对错型、凸台铸偏等应予以修正,达到圆滑过渡,一保证外观质量。
9.铸件非加工表面的皱褶,深度小于2mm,间距应大于100mm。
10.机器产品铸件的非加工表面均需喷丸处理或滚筒处理,达到清洁度Sa2 1/2级的要求。
11.铸件必须进行水韧处理。
12.铸件表面应平整,浇口、毛刺、粘砂等应清除干净。
13.铸件不允许存在有损于使用的冷隔、裂纹、孔洞等铸造缺陷。
六、锻件要求:1.每个钢锭的水口、冒口应有足够的切除量,一以保证锻件无缩孔和严重的偏折。
2.锻件应在有足够能力的锻压机上锻造成形,以保证锻件内部充分锻透。
3.锻件不允许有肉眼可见的裂纹、折叠和其他影响使用的外观缺陷。
CAD图纸技术要求
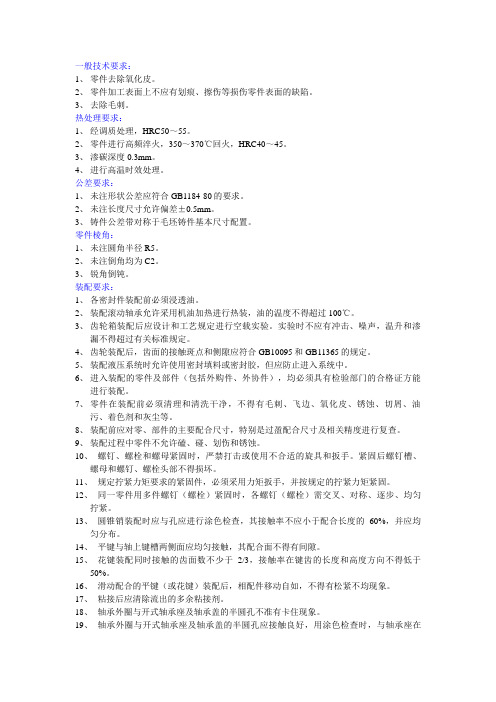
一般技术要求:1、零件去除氧化皮。
2、零件加工表面上不应有划痕、擦伤等损伤零件表面的缺陷。
3、去除毛刺。
热处理要求:1、经调质处理,HRC50~55。
2、零件进行高频淬火,350~370℃回火,HRC40~45。
3、渗碳深度0.3mm。
4、进行高温时效处理。
公差要求:1、未注形状公差应符合GB1184-80的要求。
2、未注长度尺寸允许偏差±0.5mm。
3、铸件公差带对称于毛坯铸件基本尺寸配置。
零件棱角:1、未注圆角半径R5。
2、未注倒角均为C2。
3、锐角倒钝。
装配要求:1、各密封件装配前必须浸透油。
2、装配滚动轴承允许采用机油加热进行热装,油的温度不得超过100℃。
3、齿轮箱装配后应设计和工艺规定进行空载实验。
实验时不应有冲击、噪声,温升和渗漏不得超过有关标准规定。
4、齿轮装配后,齿面的接触斑点和侧隙应符合GB10095和GB11365的规定。
5、装配液压系统时允许使用密封填料或密封胶,但应防止进入系统中。
6、进入装配的零件及部件(包括外购件、外协件),均必须具有检验部门的合格证方能进行装配。
7、零件在装配前必须清理和清洗干净,不得有毛刺、飞边、氧化皮、锈蚀、切屑、油污、着色剂和灰尘等。
8、装配前应对零、部件的主要配合尺寸,特别是过盈配合尺寸及相关精度进行复查。
9、装配过程中零件不允许磕、碰、划伤和锈蚀。
10、螺钉、螺栓和螺母紧固时,严禁打击或使用不合适的旋具和扳手。
紧固后螺钉槽、螺母和螺钉、螺栓头部不得损坏。
11、规定拧紧力矩要求的紧固件,必须采用力矩扳手,并按规定的拧紧力矩紧固。
12、同一零件用多件螺钉(螺栓)紧固时,各螺钉(螺栓)需交叉、对称、逐步、均匀拧紧。
13、圆锥销装配时应与孔应进行涂色检查,其接触率不应小于配合长度的60%,并应均匀分布。
14、平键与轴上键槽两侧面应均匀接触,其配合面不得有间隙。
15、花键装配同时接触的齿面数不少于2/3,接触率在键齿的长度和高度方向不得低于50%。
图纸上的技术要求汇总

图纸技术要求一、一般技术要求制件去除表面氧化皮;制件不得有划痕、擦伤等损伤零件表面的缺陷;去除毛刺飞边;锐角倒钝;未注倒角均为0.5×45%%d;未注越程槽均为1.2×0.3;表面平整无毛刺;二、未注公差技术要求(金属件)未注公差尺寸的极限偏差按GB/T 1804-m;未注形位公差按GB/T 1184-K;未注长度尺寸允许偏差±0.5;三、表面处理技术要求表面镀白(黑)锌处理;表面喷漆(喷塑)处理;表面发黑处理;表面电泳处理;表面镀铬处理;表面抛光处理;表面滚花,直纹(网纹)m=0.4 GB/T 6403.3;四、热处理技术要求制件氮化450-480HV;制件毛坯须调质处理220-260HB;制件调质处理30-35HRC;制件高频淬火45~50HRC;制件渗碳处理,深度>0.1;制件进行高温回火处理;制件整体淬火40-45HRC;五、铸件技术要求1、压铸件技术要求未注公差尺寸的极限偏差按GB/T 1804-m;未注形位公差按GB/T 1184-K;未注倒角均为0.5×45%%d;未注壁厚2.5;未注筋板1.5~2;未注过渡圆角R0.5-R2;未注脱模斜度≤1%%d;制件饱满光洁、无气孔、缩松、裂纹、夹渣、缺料等缺陷;各脱模顶料推杆压痕均应低于该制件表面0.2;制件要求符合GB/T 15114《铝合金压铸件》标准规定;表面喷漆(喷塑)处理,不得污染到已加工表面;加工表面在表面处理后加工,加工后涂油保护;未注尺寸参照三维造型;制件表面处理及其它要求按客户定;2、砂型铸造技术要求未注铸造圆角R5-10;铸件应彻底清砂,浇冒口应清除平整;铸件需人工时效;铸件不得有砂眼、气孔、缩松、裂纹等缺陷;粗加工后应再次进行人工时效;不加工表面涂底漆;六、冲压件技术要求制件未注公差尺寸的极限偏差按GB/T 15055-m;制件未注形位公差按GB/T 13916-2级;制件不得有裂纹或缺损;制件表面平整,不得有沟痕、碰伤等损坏表面,降低强度及寿命的缺陷;去除边角毛刺;表面处理:七、塑料件技术要求未注公差尺寸的极限偏差按GB/T 14486-MT6级;制件应饱满光整、色泽均匀;无缩痕、裂纹、银丝等缺陷;浇口、溢边修剪后飞边≤0.3,且不得伤及本体;未注壁厚3;未注筋板1.5~2;表面打光(喷砂)处理;未注过渡圆角取R0.3~R1,脱模斜度≤0.3%%d;各脱模顶料推杆压痕均应低于该制件表面0.2;与对应装配结合面外形配合错位≤0.5;制件应进行时效处理;制件机械强度须符合GB 3883.1标准规定;制件内腔表面打上材料标记和回收标志;未注尺寸参照三维造型;制件表面处理及其它要求由客户定;八、焊接件技术要求未注公差线性及角度尺寸的极限偏差均按GB/T 19804-B级;未注形位公差按GB/T 19804-F级;焊缝应均匀平整,焊渣清理干净;焊缝应焊透,不得烧穿及产生裂纹等影响机械性能的缺陷;九、各类零、部件技术要求1、齿轮(齿轴)技术要求未注公差尺寸的极限偏差按GB/T 1804-m;未注形位公差按GB/T 1184-K;制件毛坯须调质220~260HB;制件材料的化学成分和力学性能应符合GB/T 3077的规定;齿面接触斑点:按齿高不小于40%,按齿长不小于50%;齿面高频淬火回火至49-52HRC;制件表面不应有锈迹、裂纹、灼伤等影响使用寿命的伤痕及缺陷;最终工序热处理表面不得有氧化皮;2、一般轴芯(无铣齿)技术要求未注公差尺寸的极限偏差按GB/T 1804-m;未注形位公差按GB/T 1184-K;未注倒角均为0.5×45%%d;未注越程槽均为1.2×0.3;制件毛坯须调质220~260HB;尺寸%%c 档车正反两条螺旋槽,螺距10,深0.4;螺纹表面不允许有磕碰、乱扣、毛刺等缺陷;热处理:表面处理:3、包轴毛坯(一次成型)技术要求未注公差尺寸的极限偏差按GB/T 1804-m;未注形位公差按GB/T 1184-K;绝缘层应饱满光洁,无裂纹、气孔、缺料、杂质等缺陷;包轴毛坯:绝缘层%%c 档(注:指冲片配合档)与轴芯间应能承受50Hz,实际正弦波电压2500V历时1min不击穿,其余绝缘层档3750V历时1min不击穿;一次成型:铁芯与轴芯间应能承受50Hz,实际正弦波电压2500V历时1min不击穿,其余绝缘层档3750V历时1min不击穿;4、包轴(加工)技术要求未注公差尺寸的极限偏差按GB/T 1804-m;未注形位公差按GB/T 1184-K;塑层应饱满光洁,无裂纹、气孔、缺料、杂质等缺陷;塑层%%c 档(注:指冲片配合档)与轴芯间应能承受50Hz,实际正弦波电压2500V历时1min不击穿,其余塑层档3750V历时1min不击穿;制件磨加工后应烘干除水处理;5、转子技术要求未注公差尺寸的极限偏差按GB/T 1804-m;未注形位公差按GB/T 1184-K;绕组接线按转子绕线原理图;绕组绝缘漆应均匀充满绕组并充分固化,漆膜应均匀无气泡或裂痕;云母槽开深0.8~1,槽宽0.6,槽内不得残留云母片;绕组冷态绝缘电阻不低于50MΩ;装风叶后校动平衡,其精度应不低于G6.3级;去重不允许有冲片铣穿、残缺现象;铁芯外圆不加工,绝缘漆不得高出铁芯外圆,并不得有明显积瘤;铁芯与轴芯间应能承受50Hz,实际正弦波电压2500V,1min不击穿;绕组与铁芯间应能承受50Hz,实际正弦波电压1250V,1min不击穿;匝间绝缘应能承受1000Hz,峰值为2100V,历时3s不击穿;换向器与轴芯间应能承受50Hz,实际正弦波电压3750V,1min不击穿;应去除铁屑、铜粉、油污等杂质;铁芯外圆应涂透明淡金水防锈处理;6、定子技术要求绕组绕制整齐无松散;引线接头应牢固可靠且充分绝缘;绕组与铁芯间应能承受50Hz,实际正弦波电压1250V历时1min不击穿;匝间绝缘应能承受1000Hz,峰值为2100V,历时3s不击穿;绕组绝缘漆应均匀充满绕组并充分固化,漆膜应均匀无气泡或积瘤;铁芯表面不得有明显绝缘漆;7、定、转子铁芯技术要求未注公差尺寸的极限偏差按GB/T 1804-m;未注形位公差按GB/T 1184-K;冲片叠装应紧密可靠,片间无夹杂,表面及槽内无污物和油渍;冲片按同一冲制方向压装;冲片齿槽口整齐与转轴平行,误差不大于0.5;铁芯两端弹开度不大于0.5;8、定、转子冲片技术要求制件未注公差尺寸的极限偏差按GB/T 15055-m;制件未注形位公差按GB/T 13916-2级;制件应表面平整,完整无缺料;尖角处允许用R0.3过渡;制件毛刺不大于0.05(注:高速冲时不大于0.02);制件应不含油脂,剪切油不能用机油;9、绝缘纸技术要求表面不得有划痕、折痕;裁边不起毛;10、换向器技术要求未注公差尺寸的极限偏差按GB/T 1804-m;未注形位公差按GB/T 1184-K;外观完整,表面光滑,应无裂纹、毛刺、锈蚀、气孔、夹杂等缺陷;绝缘电阻:室温下内孔与换向片之间大于50MΩ;云母片厚度取0.5;换向片对换向器轴线偏斜度不大于云母片厚度的1/3;介电强度:片间承受频率50Hz,泄露电流为0.1mA,实际正弦波电压600V历时1s不击穿;换向片与内孔轴芯间承受频率50Hz,泄露电流为0.25mA,实际正弦波电压3750V历时1min不击穿;试验与检验应符合JB/T 10107《电动工具换向器》标准要求;11、电缆线技术要求电缆线长度尺寸指工具电缆出口至插头的导线部分,不包括插头和插脚;软电缆应符合GB/T 5013《额定电压450V/750V及以下橡皮绝缘电缆》标准要求;聚氯乙烯电缆应符合GB/T 5023《额定电压450V/750V及以下聚氯乙烯绝缘电缆》标准要求;插脚与可触及插头表面的绝缘应能承受50Hz,实际正弦波电压3750V历时1min不击穿;制件还应符合GB 1002《家用和类似用途单相插头插座型式、基本参数和尺寸》和GB 2099《家用和类似用途插头插座》标准要求;12、开关技术要求未注公差尺寸的极限偏差按SJ/T 10628-7级;除本图要求的外形尺寸、功能、图形、文字外,试验和检验均应符合GB/T22692《电动工具开关》标准要求;开关的使用性能应保证5万次无故障正常使用;13、电缆护套技术要求未注公差尺寸的极限偏差按GB/T 3672.1-2级;未注形位公差按GB/T 3672.2-M级;制件不得有缺料、破裂等缺陷。
CAD制图中零件图的技术要求大全

CAD制图中零件图的技术要求大全 CAD制图中零件图的技术要求大全一般在设计机械零件时都会碰到各种问题,今日YJBYS我跟大家共享的是零件图的技术要求,零件上常见的工艺结构!一、铸件铸件转折处应有圆角,铸件设计应有拔模斜度,铸件的设计要有利于起模,铸件的设计应合理简化,铸件的壁厚要均匀或慢慢过渡。
二、金属切削加工1.倒角、倒圆便于装配和使用安全。
2.退刀槽、越程槽在零件的台肩处,为爱惜加工刀具和刀具方便退出,以及装配时两零件外表能紧密接触,一般在零件上要加工出退刀槽或越程槽。
3.零件上孔的设计应有利于加工与测量。
4.避开零件的加工面在内壁上。
5.零件结构应尽量削减加工面。
零件图的技术要求一、外表粗糙度1.外表粗糙度的概念及参数(1)轮廓算术平均偏差Ra轮廓算术平均偏差 Ra是指取样长度l(用于判别具有外表粗糙度特征的一段长度)内,轮廓偏差y(外表轮廓上点至基准线的距离)确定值的算术平均值。
(2)微观不平十点高度Rz在取样长度内 5个最大轮廓峰高的平均值和5个最大轮廓谷深的平均值之和。
(3)轮廓最大高度Ry在取样长度内,轮廓峰顶线和轮廓谷底线之间的距离即为 Ry。
2.外表粗糙度符号、及其意义3.外表粗糙度的标注标注原则(1)同一图样上,每个外表一般只标注一次外表粗糙度符号、,并应注在可见轮廓线、尺寸界线、引出线或它们的延长线上。
(2)符号的尖端必需从材料的外部指向零件外表。
(3)在图样上,外表粗糙度中数字的大小和方向必需与图中尺寸数字的大小和方向一致。
二、极限与协作1.互换性概念在相同规格的一批零件中,不用选择,不经修配就能装在机器上,到达规定的性能要求,零件的这种性质就称为互换性。
2.尺寸与尺寸公差(1)基本尺寸:由设计确定的尺寸。
(2)实际尺寸:通过测量获得的尺寸。
(3)极限尺寸:允许零件尺寸转变的两个界限值称为极限尺寸。
分最大极限尺寸和最小极限尺寸。
(4)尺寸偏差:某一尺寸减其基本尺寸所得的代数差称为尺寸偏差,简称偏差。
常用图纸技术要求
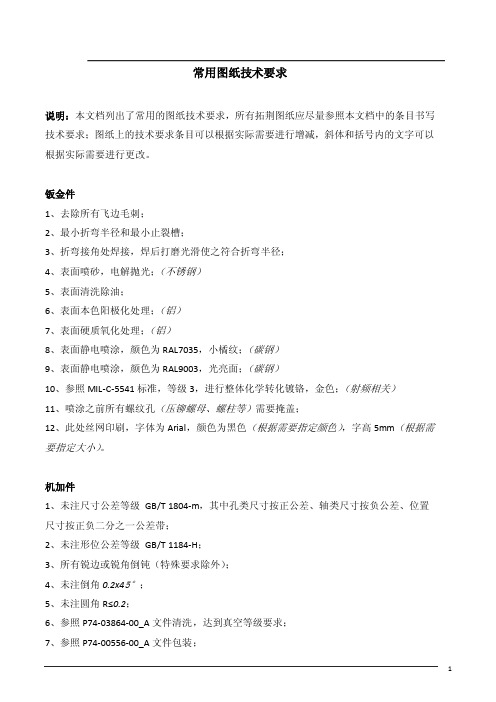
常用图纸技术要求说明:本文档列出了常用的图纸技术要求,所有拓荆图纸应尽量参照本文档中的条目书写技术要求;图纸上的技术要求条目可以根据实际需要进行增减,斜体和括号内的文字可以根据实际需要进行更改。
钣金件1、去除所有飞边毛刺;2、最小折弯半径和最小止裂槽;3、折弯接角处焊接,焊后打磨光滑使之符合折弯半径;4、表面喷砂,电解抛光;(不锈钢)5、表面清洗除油;6、表面本色阳极化处理;(铝)7、表面硬质氧化处理;(铝)8、表面静电喷涂,颜色为RAL7035,小橘纹;(碳钢)9、表面静电喷涂,颜色为RAL9003,光亮面;(碳钢)10、参照MIL-C-5541标准,等级3,进行整体化学转化镀铬,金色;(射频相关)11、喷涂之前所有螺纹孔(压铆螺母、螺柱等)需要掩盖;12、此处丝网印刷,字体为Arial,颜色为黑色(根据需要指定颜色),字高5mm(根据需要指定大小)。
机加件1、未注尺寸公差等级GB/T 1804-m,其中孔类尺寸按正公差、轴类尺寸按负公差、位置尺寸按正负二分之一公差带;2、未注形位公差等级GB/T 1184-H;3、所有锐边或锐角倒钝(特殊要求除外);4、未注倒角0.2x45°;5、未注圆角R≤0.2;6、参照P74-03864-00_A文件清洗,达到真空等级要求;7、参照P74-00556-00_A文件包装;8、此处激光刻字:P15-00154-00_AXXXX-YYMM-SSS其中XXXX为四位供应商编码,YYMM为四位出厂日期码,YY为年编码,MM为月编码,SSS为此零件在此月内的序列号,从001开始计数,字体为Arial,字高5mm,行间距3mm;9、材料热处理方法:正火、调质、淬火,热处理后表面应达到的硬度;(根据需要)10、注明表面处理要求(渗碳、氰化、淡化、喷丸等)、表面涂层或镀层(油漆、发兰、镀铬、镀镍等)以及表面修饰(去毛刺、清砂)等(根据需要),可参考钣金表面处理。
图纸技术要求
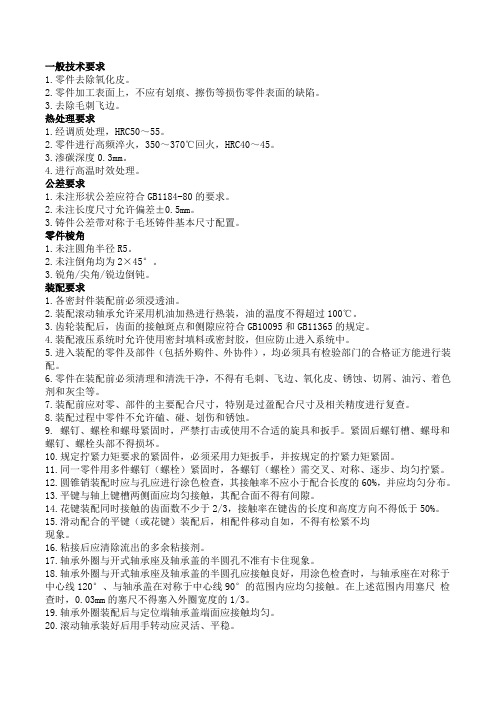
一般技术要求1.零件去除氧化皮。
2.零件加工表面上,不应有划痕、擦伤等损伤零件表面的缺陷。
3.去除毛刺飞边。
热处理要求1.经调质处理,HRC50~55。
2.零件进行高频淬火,350~370℃回火,HRC40~45。
3.渗碳深度0.3mm。
4.进行高温时效处理。
公差要求1.未注形状公差应符合GB1184-80的要求。
2.未注长度尺寸允许偏差±0.5mm。
3.铸件公差带对称于毛坯铸件基本尺寸配置。
零件棱角1.未注圆角半径R5。
2.未注倒角均为2×45°。
3.锐角/尖角/锐边倒钝。
装配要求1.各密封件装配前必须浸透油。
2.装配滚动轴承允许采用机油加热进行热装,油的温度不得超过100℃。
3.齿轮装配后,齿面的接触斑点和侧隙应符合GB10095和GB11365的规定。
4.装配液压系统时允许使用密封填料或密封胶,但应防止进入系统中。
5.进入装配的零件及部件(包括外购件、外协件),均必须具有检验部门的合格证方能进行装配。
6.零件在装配前必须清理和清洗干净,不得有毛刺、飞边、氧化皮、锈蚀、切屑、油污、着色剂和灰尘等。
7.装配前应对零、部件的主要配合尺寸,特别是过盈配合尺寸及相关精度进行复查。
8.装配过程中零件不允许磕、碰、划伤和锈蚀。
9. 螺钉、螺栓和螺母紧固时,严禁打击或使用不合适的旋具和扳手。
紧固后螺钉槽、螺母和螺钉、螺栓头部不得损坏。
10.规定拧紧力矩要求的紧固件,必须采用力矩扳手,并按规定的拧紧力矩紧固。
11.同一零件用多件螺钉(螺栓)紧固时,各螺钉(螺栓)需交叉、对称、逐步、均匀拧紧。
12.圆锥销装配时应与孔应进行涂色检查,其接触率不应小于配合长度的60%,并应均匀分布。
13.平键与轴上键槽两侧面应均匀接触,其配合面不得有间隙。
14.花键装配同时接触的齿面数不少于2/3,接触率在键齿的长度和高度方向不得低于50%。
15.滑动配合的平键(或花键)装配后,相配件移动自如,不得有松紧不均现象。
制图的技术要求

机械制图常用技术要求技术要求(冲压件) 1.锐边去毛刺,冲压切口粗糙度6.3. 2.冲件表面氧化处理:H.Y.或(表面镀锌钝彩.Zn8.DC.). 3.未注公差尺寸的极限偏差按GB/T 1804-92 m级. 技术要求(铸件) 1.铸件不得有气孔、夹渣、裂纹等缺陷. 2.未注明铸造斜度为1~2.5%%d. 3.铸造公差按GB6414-86 CT6. 4.未注明铸造圆角为R1~R2.5. 5.未注公差尺寸的极限偏差按GB/T 1804-92 m级. 6.未注形位公差按GB/T1184-96 H级. 7.去毛刺,未注倒角0.5x45%%D. 技术要求(锻件) 1.未注锻造圆角半径为R1~R2.2.未注锻造斜度为1~1.5%%D,锻造公差为IT15级.3.锻件组织应致密,不得有折叠、裂纹等缺陷,并去飞边. 4.去锐边毛刺,直角处倒钝. 5.未注公差尺寸的极限偏差按GB/T 1804-92 m级. 6.未注形位公差按GB/T1184-96 H级. 技术要求(活塞件) 1.未注公差尺寸的极限偏差按GB/T 1804-92 m级. 2.未注形位公差按GB/T1184-96 H级. 3.去毛刺,未注倒角0.5x45%%D. 4.表面磷化处理. 技术要求(橡胶件) 1.零件表面应光洁.(模具表面粗糙度应在Ra0.4以上) 且不允许有气泡.杂技级凸凹等缺陷. 2.合模缝不允许错位,合模飞边的凸起级厚度不得大于0.02mm. 3.邵氏A型硬度65%%P5. 4.去净飞边. 技术要求(塑料件) 1.成形前材料应预热干燥. 2.成形后制件应光整不得有扭曲变形现象.3.未注圆角为R0.5.4.外表面应光滑,其粗糙度不大于Ra0.4. 且不得有划伤,刻痕等缺陷.5.未注尺寸公差按GB/T 1804-92 m级. 技术要求(弹簧件) 1.旋向:左旋. 2.总圈数:no=12 3.工作圈数:no=10 4.钢丝硬度:HRC42~48. 5.表面氧化处理:H.Y.(俗称发黑) 6.单端并紧磨平.再如:ν如果是整机安装后的技术要求还应该增加:整机的的性能指标,最后的喷漆要求。
图纸一般技术要求
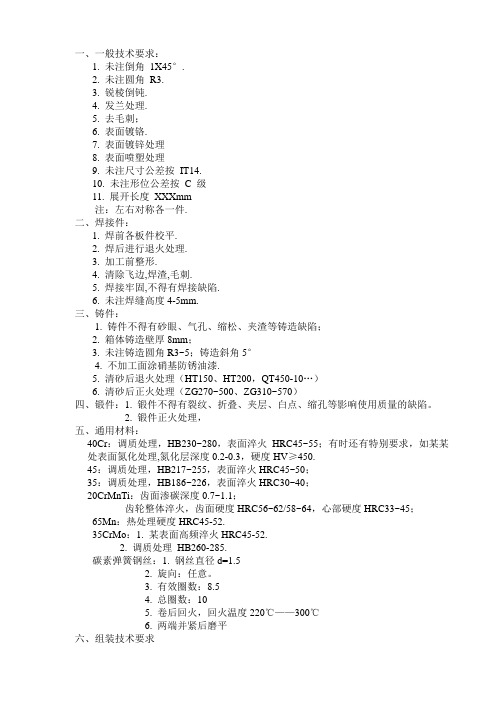
一、一般技术要求:1. 未注倒角1X45°.2. 未注圆角R3.3. 锐棱倒钝.4. 发兰处理.5. 去毛刺;6. 表面镀铬.7. 表面镀锌处理8. 表面喷塑处理9. 未注尺寸公差按IT14.10. 未注形位公差按C 级11. 展开长度XXXmm注:左右对称各一件.二、焊接件:1. 焊前各板件校平.2. 焊后进行退火处理.3. 加工前整形.4. 清除飞边,焊渣,毛刺.5. 焊接牢固,不得有焊接缺陷.6. 未注焊缝高度4-5mm.三、铸件:1. 铸件不得有砂眼、气孔、缩松、夹渣等铸造缺陷;2. 箱体铸造壁厚8mm;3. 未注铸造圆角R3~5;铸造斜角5°4. 不加工面涂硝基防锈油漆.5. 清砂后退火处理(HT150、HT200,QT450-10…)6. 清砂后正火处理(ZG270~500、ZG310~570)四、锻件:1. 锻件不得有裂纹、折叠、夹层、白点、缩孔等影响使用质量的缺陷。
2. 锻件正火处理,五、通用材料:40Cr:调质处理,HB230~280,表面淬火HRC45~55;有时还有特别要求,如某某处表面氮化处理,氮化层深度0.2-0.3,硬度HV≥450.45:调质处理,HB217~255,表面淬火HRC45~50;35:调质处理,HB186~226,表面淬火HRC30~40;20CrMnTi:齿面渗碳深度0.7~1.1;齿轮整体淬火,齿面硬度HRC56~62/58~64,心部硬度HRC33~45;65Mn:热处理硬度HRC45-52.35CrMo:1. 某表面高频淬火HRC45-52.2. 调质处理HB260-285.碳素弹簧钢丝:1. 钢丝直径d=1.52. 旋向:任意。
3. 有效圈数:8.54. 总圈数:105. 卷后回火,回火温度220℃——300℃6. 两端并紧后磨平六、组装技术要求1. 组装前将箱体、各零件清洗干净.2. 组装端盖前应在端盖根部均匀涂抹密封胶;/各密封接合面及纸垫应保持清洁无油,涂密封铰,钻通的螺孔,其螺栓应粘附厌氧胶后拧紧,确保无渗油3. 组装完成后注入升油.4. 组装后应检查图示装配尺寸XX、XX、XX、XX,合格后方可进行总装.5. 轴转动灵活无卡阻,操作手柄准确无误七、焊接箱体技术要求:1. 未注焊缝均为角焊缝K=5-7mm2. 焊缝应密封可靠;3. 组焊后整形并退火处理;4. 焊后焊缝应打磨光滑;5. 全部棱角到角2X45%°;6. 组装前箱内应除锈清渣,并涂耐油防锈漆;7. 螺孔不得钻穿,以免漏油。
手工制图考核要求及标准
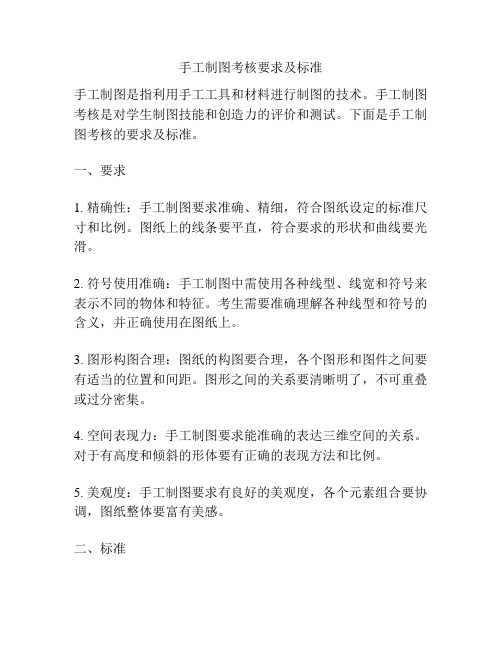
手工制图考核要求及标准手工制图是指利用手工工具和材料进行制图的技术。
手工制图考核是对学生制图技能和创造力的评价和测试。
下面是手工制图考核的要求及标准。
一、要求1. 精确性:手工制图要求准确、精细,符合图纸设定的标准尺寸和比例。
图纸上的线条要平直,符合要求的形状和曲线要光滑。
2. 符号使用准确:手工制图中需使用各种线型、线宽和符号来表示不同的物体和特征。
考生需要准确理解各种线型和符号的含义,并正确使用在图纸上。
3. 图形构图合理:图纸的构图要合理,各个图形和图件之间要有适当的位置和间距。
图形之间的关系要清晰明了,不可重叠或过分密集。
4. 空间表现力:手工制图要求能准确的表达三维空间的关系。
对于有高度和倾斜的形体要有正确的表现方法和比例。
5. 美观度:手工制图要求有良好的美观度,各个元素组合要协调,图纸整体要富有美感。
二、标准1. 尺寸准确性:图纸尺寸相对准确,与设计要求相符。
误差在±1mm范围内。
2. 线条精确性:图纸上的线条要直,符合要求的形状和曲线要光滑。
线条宽度和线型符合要求。
3. 符号使用准确:各种线型和符号的使用准确,能正确表达图纸上所需要的信息。
4. 构图合理性:图纸的构图合理,各个图形和图件之间位置和间距适当。
图纸整体布局美观、清晰。
5. 空间表现力:对于有高度和倾斜的形体,能正确表达其三维空间的关系。
形体在图纸上比例合适,没有拉伸和压缩的现象。
6. 美观度:手工制图整体美观度高,图纸布局协调、平衡。
线条流畅、清晰,使用的材料干净整齐,没有瑕疵。
除了上述要求和标准之外,还需要考虑考生在制图过程中的专业技能和操作流程是否正确和流畅。
考生需要准确理解设计要求,并能合理应用各种手工工具和材料进行制图。
此外,考核过程中也会评估考生的创造力和创新能力,看是否能在手工制图的基础上进行展示和表达。
总的来说,手工制图考核旨在评估考生的制图技能和创造力。
要求考生能准确、精细、合理地表达设计要求,满足标准尺寸和比例,并能展现出美观度和空间表现力。
CAD绘图零件图的技术要求
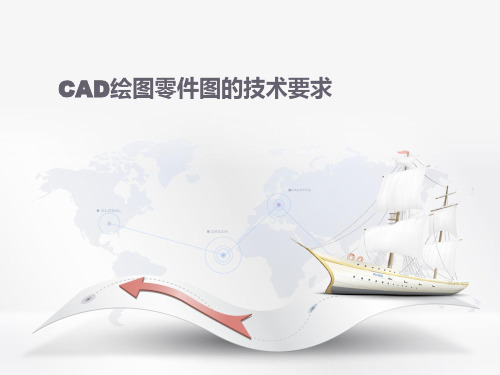
(2)微观不平十点高度Rz 在取样长度内 5个最大轮廓峰高的平均值和5个最大轮廓谷深的平均值 之和。
(3)轮廓最大高度Ry 在取样长度内,轮廓峰顶线和轮廓谷底线之间的距离即为 Ry。
2.表面粗糙度符号、代号及其意义
3.表面粗糙度的标注 标注原则 ( 1 )同一图样上,每个表面一般只标注一次表面粗糙度符号、代号, 并应注在可见轮廓线、尺寸界线、引出线或它们的延长线上。
3.零件上孔的设计应有利于加工与测量。 4.避免零件的加工面在内壁上。 5.零件结构应尽量减少加工面。
零件图的技术要求
一、表面粗糙度
1.表面粗糙度的概念及参数
(1)轮廓算术平均偏差Ra 轮廓算术平均偏差 Ra是指取样长度l(用于判别具有表面粗糙度特征 的一段长度)内,轮廓偏差y(表面轮廓上点至基准线的距离)绝对值 的算术平均值。
(2)符号的尖端必须从材料的外部指向零件表面。
( 3 )在图样上,表面粗糙度代号中数字的大小和方向必须与图中尺 寸数字的大小和方向一致。
1.互换性概念 在相同规格的一批零件中,不用选择,不经修配就能装在机器上,达 到规定的性能要求,零件的这种性质就称为互换性。
2.尺寸与尺寸公差
(1)基本尺寸:由设计确定的尺寸。
CAD绘图零件图的技术要求
一、铸件 铸件转折处应有圆角,铸件设计应有拔模斜度,铸件的设计要有 利于起模,铸件的设计应合理简化,铸件的壁厚要均匀或逐渐过渡。
二、金属切削加工
1.倒角、倒圆 便于装配和使用安全。
2.退刀槽、越程槽 在零件的台肩处,为保护加工刀具和刀具方 便退出,以及装配时两零件表面能紧密接触,一般在零件上要加工出 退刀槽或越程槽。
1.图纸绘制要求

绘图要求:一、图框要求对图纸1的任意一个柱脚进行深化,(深化时钢柱取2米高,2m 以上的钢柱内容不用深化)。
图框:A3,比例1:10。
二、图线1.图纸中图线的线宽按不同颜色区别开,图线颜色不宜过多。
2.零件序号的圆圈、尺寸线、引出线、标高符号、索引符号、不可见图线、定位轴线、对称线、中心线、折断线、波浪线等宜用细线表示,线宽宜取0.18mm。
3.图中各种构件的轮廓线、文字等宜用中线表示,线宽宜取0.30mm。
4.下标下横线、详图符号的圆圈、剖切符号等宜用粗线表示,线宽宜取0.60mm。
注意:此处线宽是指打印时的线宽,绘图时用acad默认的线宽。
三、字体1.图中零件序号字体、焊缝序号字体、尺寸标注字体、一般注释文字字体、说明栏字体、材料表字体宜取2.5mm字高,FJK文字样式。
2.图中标高字体、剖切序号字体、构件截面字体、轴号字体宜取3.5mm字高,FJK文字样式。
3.图中各种下标(包括构件名称、剖面图名称、零件详图名称、焊缝详图名称等)字体、图框中图名、工程名称及项目一栏字体,宜取5.0mm字高,FJK文字样式。
4.FJK文字样式应为:SHX字体取Simplex.shx,使用大字体,大字体取Fjktxt.shx,高度取0.0000,宽度比例取0.65。
五、符号1. 图中所有剖切符号都统一用剖切位置线表示,长度宜取6mm。
剖切符号的编号数字的字高宜取3.5mm,剖切符号宜按顺序由左至右、由下至上连续编排。
2.零件编号应由直径为5mm的圆和阿拉伯数字(字高2.5mm)组成。
先编重要零件(如柱子腹板、翼缘、柱底板,梁腹板、翼缘),其余宜按由左至右、由下至上连续编排。
3.焊缝索引符号应由边长为5mm的正方形和大写拉丁字母(字高2.5mm)组成。
编排顺序按先重要后次要的原则,其余宜按由左至右、由下至上连续编排。
4.详图符号、索引符号圆直径宜取10mm,定位轴线的圆直径宜取8mm,焊缝详图正方形边长宜取10mm。
- 1、下载文档前请自行甄别文档内容的完整性,平台不提供额外的编辑、内容补充、找答案等附加服务。
- 2、"仅部分预览"的文档,不可在线预览部分如存在完整性等问题,可反馈申请退款(可完整预览的文档不适用该条件!)。
- 3、如文档侵犯您的权益,请联系客服反馈,我们会尽快为您处理(人工客服工作时间:9:00-18:30)。
技术要求大全1.零件去除氧化皮。
2.零件加工表面上,不应有划痕、擦伤等损伤零件表面的缺陷。
3.去除毛刺飞边。
4.经调质处理,28HRC~32HRC。
5.零件进行高频淬火,350~370℃回火,40HRC~45HRC。
6.渗碳深度0.3mm。
7.进行高温时效处理。
8.未注形状公差应符合GB1184-2000.9.未标注尺寸公差应该按照GB/T1804-M10.铸件公差带对称于毛坯铸件基本尺寸配置。
11.未注圆角半径R5。
12.未注倒角均为2×45°。
13.锐角倒钝。
14.各密封件装配前必须浸透油。
15.装配滚动轴承允许采用机油加热进行热装,油的温度不得超过100℃。
20.齿轮装配后,齿面的接触斑点和侧隙应符合GB10095和GB11365的规定。
21.装配液压系统时允许使用密封填料或密封胶,但应防止进入系统中。
22.进入装配的零件及部件(包括外购件、外协件),均必须具有检验部门的合格证方能进行装配。
23.零件在装配前必须清理和清洗干净,不得有毛刺、飞边、氧化皮、锈蚀、切屑、油污、着色剂和灰尘等。
24.装配前应对零、部件的主要配合尺寸,特别是过盈配合尺寸及相关精度进行复查。
25.装配过程中零件不允许磕、碰、划伤和锈蚀。
26.螺钉、螺栓和螺母紧固时,严禁打击或使用不合适的旋具和扳手。
紧固后螺钉槽、螺母和螺钉、螺栓头部不得损坏。
27.规定拧紧力矩要求的紧固件,必须采用力矩扳手,并按规定的拧紧力矩紧固。
28.同一零件用多件螺钉(螺栓)紧固时,各螺钉(螺栓)需交叉、对称、逐步、均匀拧紧。
29.圆锥销装配时应与孔应进行涂色检查,其接触率不应小于配合长度的60%,并应均匀分布。
30.平键与轴上键槽两侧面应均匀接触,其配合面不得有间隙。
31.花键装配同时接触的齿面数不少于2/3,接触率在键齿的长度和高度方向不得低于50%。
32.滑动配合的平键(或花键)装配后,相配件移动自如,不得有松紧不均现象。
33.粘接后应清除流出的多余粘接剂。
34.轴承外圈与开式轴承座及轴承盖的半圆孔不准有卡住现象。
35.轴承外圈与开式轴承座及轴承盖的半圆孔应接触良好,用涂色检查时,与轴承座在对称于中心线120°、与轴承盖在对称于中心线90°的范围内应均匀接触。
在上述范围内用塞尺检查时,0.03mm的塞尺不得塞入外圈宽度的1/3。
36.轴承外圈装配后与定位端轴承盖端面应接触均匀。
37.滚动轴承装好后用手转动应灵活、平稳。
38.上下轴瓦的结合面要紧密贴和,用0.05mm塞尺检查不入。
39.用定位销固定轴瓦时,应在保证瓦口面和端面与相关轴承孔的开合面和端面包持平齐状态下钻铰、配销。
销打入后不得松动。
40.球面轴承的轴承体与轴承座应均匀接触,用涂色法检查,其接触不应小于70%。
41.合金轴承衬表面成黄色时不准使用,在规定的接触角内不准有离核现象,在接触角外的离核面积不得大于非接触区总面积的10%。
42.齿轮(蜗轮)基准端面与轴肩(或定位套端面)应贴合,用0.05mm塞尺检查不入。
并应保证齿轮基准端面与轴线的垂直度要求。
43.齿轮箱与盖的结合面应接触良好。
44.组装前严格检查并清除零件加工时残留的锐角、毛刺和异物。
保证密封件装入时不被擦伤。
45.铸件表面上不允许有冷隔、裂纹、缩孔和穿透性缺陷及严重的残缺类缺陷(如欠铸、机械损伤等)。
46.铸件应清理干净,不得有毛刺、飞边,非加工表明上的浇冒口应清理与铸件表面齐平。
47.铸件非加工表面上的铸字和标志应清晰可辨,位置和字体应符合图样要求。
48.铸件非加工表面的粗糙度,砂型铸造R,不大于50μm。
49.铸件应清除浇冒口、飞刺等。
非加工表面上的浇冒口残留量要铲平、磨光,达到表面质量要求。
50.铸件上的型砂、芯砂和芯骨应清除干净。
51.铸件有倾斜的部位、其尺寸公差带应沿倾斜面对称配置。
52.铸件上的型砂、芯砂、芯骨、多肉、粘沙等应铲磨平整,清理干净。
53.对错型、凸台铸偏等应予以修正,达到圆滑过渡,一保证外观质量。
54.铸件非加工表面的皱褶,深度小于2mm,间距应大于100mm。
55.机器产品铸件的非加工表面均需喷丸处理或滚筒处理,达到清洁度Sa21/2级的要求。
56.铸件必须进行水韧处理。
57.铸件表面应平整,浇口、毛刺、粘砂等应清除干净。
58.铸件不允许存在有损于使用的冷隔、裂纹、孔洞等铸造缺陷。
59.所有需要进行涂装的钢铁制件表面在涂漆前,必须将铁锈、氧化皮、油脂、灰尘、泥土、盐和污物等除去。
60.除锈前,先用有机溶剂、碱液、乳化剂、蒸汽等除去钢铁制件表面的油脂、污垢。
61.经喷丸或手工除锈的待涂表面与涂底漆的时间间隔不得多于6h。
62.铆接件相互接触的表面,在连接前必须涂厚度为30~40μm防锈漆。
搭接边缘应用油漆、腻子或粘接剂封闭。
由于加工或焊接损坏的底漆,要重新涂装。
63.装配前所有的管子应去除管端飞边、毛刺并倒角。
用压缩空气或其他方法清楚管子内壁附着的杂物和浮锈。
64.装配前,所有钢管(包括预制成型管路)都要进行脱脂、酸洗、中和、水洗及防锈处理。
65.装配时,对管夹、支座、法兰及接头等用螺纹连接固定的部位要拧紧,防止松动。
66.预制完成的管子焊接部位都要进行耐压试验。
67.配管接替或转运时,必须将管路分离口用胶布或塑料管堵封口,防止任何杂物进入,并拴标签。
68.补焊前必须将缺陷彻底清除,坡口面应修的平整圆滑,不得有尖角存在。
69.根据铸钢件缺陷情况,对补焊区缺陷可采用铲挖、磨削,炭弧气刨、气割或机械加工等方法清除。
70.补焊区及坡口周围20mm以内的粘砂、油、水、锈等脏物必须彻底清理。
71.在补焊的全过程中,铸钢件预热区的温度不得低于350°C。
72.在条件允许的情况下,尽可能在水平位置施焊。
73.补焊时,焊条不应做过大的横向摆动。
74.铸钢件表面堆焊接时,焊道间的重叠量不得小于焊道宽度的1/3。
75.每个钢锭的水口、冒口应有足够的切除量,一以保证锻件无缩孔和严重的偏折。
76.锻件应在有足够能力的锻压机上锻造成形,以保证锻件内部充分锻透。
77.锻件不允许有肉眼可见的裂纹、折叠和其他影响使用的外观缺陷。
局部缺陷可以清除,但清理深度不得超过加工余量的75%,锻件非加工表面上的缺陷应清理干净并圆滑过渡。
78.锻件不允许存在白点、内部裂纹和残余缩孔。
81.精加工后的零件摆放时不得直接放在地面上,应采取必要的支撑、保护措施。
加工面不允许有锈蛀和影响性能、寿命或外观的磕碰、划伤等缺陷。
82.滚压精加工的表面,滚压后不得有脱皮现象。
83.最终工序热处理后的零件,表面不应有氧化皮。
经过精加工的配合面、齿面不应有退火84.加工的螺纹表面不允许有黑皮、磕碰、乱扣和毛刺等缺陷。
85、发蓝、变色的现象。
谢谢clutch_2006提供1装配滚动轴承允许采用机油加热进行热装,油的温度不得超过100℃。
2.齿轮箱装配后应设计和工艺规定进行空载试验。
试验时不应有冲击、噪声,温升和渗漏不得超过有关标准规定。
3.齿轮装配后,齿面的接触斑点和侧隙应符合GB10095和GB11365的规定。
4.装配液压系统时允许使用密封填料或密封胶,但应防止进入系统中。
5.进入装配的零件及部件(包括外购件、外协件),均必须具有检验部门的合格证方能进行装配。
6.零件在装配前必须清理和清洗干净,不得有毛刺、飞边、氧化皮、锈蚀、切屑、油污、着色剂和灰尘等。
7.装配前应对零、部件的主要配合尺寸,特别是过盈配合尺寸及相关精度进行复查。
8.圆锥销装配时应与孔应进行涂色检查,其接触率不应小于配合长度的60%,并应均匀分布。
9.轴承外圈与开式轴承座及轴承盖的半圆孔应接触良好,用涂色检查时,与轴承座在对称于中心线120°、与轴承盖在对称于中心线90°的范围内应均匀接触。
在上述范围内用塞尺检查时,0.03mm的塞尺不得塞入外圈宽度的1/3。
10.轴承外圈装配后与定位端轴承盖端面应接触均匀。
转自:[url=/?fromuid=0]验货员论坛[/url] /viewthread.php?tid=55017&fromuid=0某厂钣金检验标准1目的本标准定义维盛冲压件产品外观品质的基本要求,并确立允收/拒收之准则。
2适用范围本标准适用于维盛生产的所有冲压件产品。
3相关文件《**产品外观检验标准》。
4定义A级面:客户经常看到的面,如面板,机箱的上表面、正面,出给客户的零件,马口铁生产的产品等。
B级面:不移动的情况下,客户偶尔能看到的面,如机箱的后面、侧面等。
C级面:产品在移动或被打开时才能看到的面,如机箱的底面,内部零件的表面等。
5检测条件5.1所有检验均应在正常照明,并模拟最终使用条件下进行。
检测过程中不使用放大镜,所检验表面和人眼呈45°角。
A级面在检测时应转动,以获得最大反光效果。
B级面和C级面在检测期间不必转动。
光源=40W荧光灯零件表面人眼距离500毫米A级面停留10秒,B级面停留5秒,C级面停留3秒。
6薄板金属件外观检验标准6.1允收总则6.1.1可接受的缺陷不能影响该零件的装配和功能,否则,将被拒收。
6.1.2缺陷允收定义了1250平方毫米的区域内各类缺陷的最大允收数量。
对于较大的零件表面,可允收数量和该表面所含1250平方毫米区域数量成正比,但是,两个或两个以上缺陷不能相连。
6.2缺陷定义6.2.1彩虹效应:镀锌有可能造成变色或“彩虹”效应。
6.2.2生锈/氧化:暴露在空气中的金属表面发生的化学反应。
6.2.3变色:底色或预期的颜色发生改变,或零件表面的颜色不一致。
6.2.4刮伤:零件表面的呈条状的浅沟。
6.2.5压痕:由尖锐物件在零件表面造成的沟痕,指甲能够感受到。
6.2.6镀痕/流痕:由于镀层厚度不均匀造成零件表面上波纹状或条状异常的区域。
6.2.7痕迹:指基体材料的小坑、折弯痕或其他痕迹,涂装后仍无法消除。
6.2.8灰尘或油脂:在制造过程中产生并留在零件表面上的赃污(未清洗)。
6.2.9斑点/沙粒/绒线:涂装面或零件表面任何非预期的异物。
6.2.10凹坑:零件表面弹坑状的缺陷。
6.2.11模压痕:因成形模具在零件表面造成的工艺痕,所有零件的模压痕的位置和大小都一样,均匀分布于成形/折弯区域。
6.3缺陷允收表(薄板冲压件)每个面的缺陷数量不能超过允收的界限,如下表所示:薄板金属件缺陷允收表缺陷类型A级面B级面C级面彩虹效应(镀锌面)不允收允收允收生锈/氧化不允收不允收切断面允收,表面最大缺陷直径不超过1毫米变色不允收允收允收刮伤/压痕刮伤在6.5毫米长0.4毫米宽的范围内允收状况表面积(平方毫米)可接受的缺陷数量250—500501—12501251—50005001+01刮伤在13毫米长0.2毫米宽的范围内允收状况表面积(平方毫米)可接受的缺陷数量250—500501—12501251—50005001+01刮伤在6.5毫米长0.4毫米宽的范围内允收状况表面积(平方毫米)可接受的缺陷数量250—500501—12501251—50005001+361020刮伤在13毫米长0.2毫米宽的范围内允收状况表面积(平方毫米)可接受的缺陷数量250—500501—12501251—50005001+1237累积刮伤长度不超过62.5毫米/5000平方毫米可允收缺陷个数为:1个。