锻造工艺质量控制规范
锻造厂质量管理制度范本

第一章总则第一条为确保锻造产品质量,规范生产过程,提高企业核心竞争力,特制定本制度。
第二条本制度适用于本厂所有锻造生产活动,包括原材料采购、生产过程、成品检验、售后服务等各个环节。
第三条本制度遵循“预防为主、质量第一”的原则,强化全员质量意识,落实质量责任。
第二章组织机构与职责第四条成立锻造厂质量管理部门,负责全厂质量管理工作的组织、协调、监督和考核。
第五条质量管理部门的主要职责:1. 制定和修订质量管理制度,并组织实施;2. 组织质量教育培训,提高员工质量意识;3. 监督检查生产过程,确保产品质量;4. 组织质量事故调查和处理;5. 负责产品质量认证和售后服务。
第六条各部门质量职责:1. 生产部门:负责按照工艺规程进行生产,确保生产过程符合质量要求;2. 技术部门:负责编制和修订工艺规程,确保工艺技术先进、合理;3. 采购部门:负责原材料采购,确保原材料质量符合要求;4. 设备部门:负责设备维护保养,确保设备正常运行;5. 售后服务部门:负责客户投诉处理,确保客户满意度。
第三章质量管理要求第七条原材料采购:1. 采购原材料应选用合格供应商,确保原材料质量;2. 采购合同中应明确质量要求,确保原材料质量符合规定;3. 收到原材料后,应进行入库检验,合格后方可入库。
第八条生产过程:1. 严格执行工艺规程,确保生产过程符合质量要求;2. 加强生产过程监控,及时发现和纠正质量问题;3. 对关键工序进行重点控制,确保产品质量稳定。
第九条成品检验:1. 按照国家标准和行业标准进行成品检验;2. 检验员应具备相应的检验技能和知识;3. 检验不合格的产品,不得出厂。
第十条质量事故处理:1. 对发生的质量事故,应及时进行调查和处理;2. 分析事故原因,制定预防措施,防止类似事故再次发生;3. 对事故责任人进行严肃处理。
第四章培训与考核第十一条定期组织员工进行质量教育培训,提高员工质量意识;第十二条建立质量考核制度,将质量指标纳入绩效考核,奖优罚劣。
锻造工艺要求

锻造工艺要求
锻造是一种金属加工工艺,通过对金属坯料进行加热、锤击或压力加工,使其形成所需的形状和尺寸。
锻造工艺要求包括以下几个方面:
1. 材料要求:锻造工艺需要使用适合的金属材料,通常包括低碳钢、合金钢、铝合金等。
这些材料具有较好的可锻性和可塑性,能够在锻造过程中形成所需的形状和尺寸。
2. 坯料要求:锻造工艺需要准备适当的坯料,通常采用圆钢、板材、棒材等。
坯料的尺寸和形状需要符合锻造工艺的要求,以便在锻造过程中形成所需的形状和尺寸。
3. 加热要求:锻造工艺需要将坯料加热到适当的温度,以便使其具有良好的可塑性。
加热温度的选择需要考虑材料的性质和锻造工艺的要求,通常需要在金属材料的相变温度范围内进行加热。
4. 锻造要求:锻造工艺需要使用适当的锻造设备和工具,如锻造机、锤击机等。
锻造工艺需要按照规定的锻造程序进行操作,以确保锻造出的零件具有所需的形状、尺寸和力学性能。
5. 后处理要求:锻造工艺需要进行后处理,如去毛刺、切割、热处理等,以确保锻造出的零件符合要求。
后处理的方法和工艺需要根据具体的锻造零件的要求进行选择和调
整。
总之,锻造工艺需要综合考虑材料、坯料、加热、锻造和后处理等多个方面的要求,以确保锻造出的零件具有所需的形状、尺寸和力学性能。
s31254 锻件标准

s31254 锻件标准S31254锻件标准属于钢材标准的一部分,用于指导S31254材料的锻造工艺和质量要求。
本文将对S31254锻件的标准进行详细介绍。
一、材料要求S31254是一种超级奥氏体不锈钢,具有优异的耐腐蚀性能。
在锻造过程中,材料的化学成分和机械性能需满足以下要求:1. 化学成分:C≤0.02%,Si≤0.8%,Mn≤1.0%,P≤0.03%,S≤0.01%,Cr 19.5~20.5%,Ni 17.5~18.5%,Mo 6.0~6.5%,Cu 0.50~1.00%,N0.20~0.30%,Fe余量。
2. 机械性能:抗拉强度σb≥650MPa,屈服强度σ0.2≥300MPa,延伸率δ≥35%,断面收缩率ψ≥45%,冲击功AKV≥100J。
二、工艺规范1. 热处理:S31254锻件在锻造前需要进行固溶退火处理,温度范围为1100~1200℃,保温时间不少于1小时。
锻件完成锻造后需要进行快速冷却处理。
2. 锻造温度:S31254锻件的加热温度一般为1150~1250℃,保温时间根据锻件的大小和形状而定。
3. 锻件形状:S31254锻件的最大厚度不宜超过360mm,最大宽度不应超过500mm。
对于较大尺寸的锻件,可以采用多次锻造的方式进行。
4. 锻造比例:锻件的尺寸比例应控制在1:4以内,超出比例范围将导致不均匀的应力分布和变形。
三、质量要求1. 外观质量:锻件表面应光滑、无裂纹、气泡等缺陷。
2. 化学成分和机械性能:锻件应符合上述材料要求中的化学成分和机械性能指标。
3. 结构一致性:锻件的组织应均匀一致,不应出现太大的晶粒和过多的夹杂物。
4. 尺寸精度:锻件的尺寸公差应符合技术要求,在许用偏差范围内。
5. 出厂检验:锻件出厂前应进行严格的检验,包括化学成分分析、机械性能测试、外观检查和尺寸测量等。
四、应用领域S31254锻件广泛应用于海洋石油、化工、海水淡化等领域,尤其适用于具有高腐蚀介质和高温高压条件下的工作环境。
锻造工艺质量控制规范

锻造工艺质量控制规范1 主题内容与适用范围本标准规定了对锻造工艺进行全过程质量控制的通用原则和要求。
本标准适用于锻造车间的锻造工艺质量控制。
2 引用标准GB 12361 钢质模锻件通用技术条件GB 12362 钢质模锻件公差及机械加工余量GB 13318 锻造车间安全生产通则GB/T 12363 锻件功能分类JB 4249 锤上钢质自由锻件机械加工余量与公差JB 4385 锤上钢质自由锻件通用技术条件JB/T 6052 钢质自由锻件加热通用技术要求JB/T 6055 锻造车间环境保护导则3 锻件分类本标准质量控制所涉及的锻件分类按GB/T 12363 执行。
4 环境的控制锻造厂的工作环境包括厂房地面、天窗、温度、通风、照明、噪声、通道、管道以及坯料、锻件和工夹模具的存放等均应按GB 13318 第3 章和JB/T 6055 第3、4 章的要求和国家的有关法规、法律制订本企业的具体实施要求。
5 设备、仪表与工装的控制5. 1 设备、仪表5. 1. 1 各类设备必须完好,并有操作规程和维修、检定制度。
5. 1. 2 各类在用主要设备必须挂有完好设备标牌,并有检验有效期及下次检定日期。
不合格设备及超过检定合格有效期的设备必须挂“停用”标牌。
5. 1. 3 设备的控制系统及检测显示仪表应定期检查,确保仪表和其精度的显示数值准确。
5. 1. 4 加热设备的温度显示及测点布置应正确反应加热区炉温及炉温均匀性。
5. 1. 5 所用设备都必须建立档案,其具体内容包括:a. 设备使用说明书;b.台时记录;c.故障记录d.修理记录e. 历年检定报告及检定合格证。
5. 2 模具及其他工装5. 2. 1 新模具应按模具图的要求制造,检验合格后进行试模,确认达到设计、制造要求后方可投入生产。
5. 2. 2 在每批锻件生产结束时,应将锻造的尾件上打标记并经检验尺寸合格后,模具方可返库继续使用。
5. 2. 3 锻造所用工具,必须按工艺文件的规定选用,并经检查完好方可使用。
锻件质量控制范本

锻件质量控制锻件质量控制1. 引言2. 材料选用2.1 原材料选择在进行锻件生产之前,需要选择合适的原材料。
原材料的选择要考虑到锻件的使用环境和要求,包括强度、耐磨性、耐腐蚀性等。
常用的锻件材料包括碳钢、合金钢、铝合金等。
根据不同的使用要求,可以选择不同的材料。
2.2 材料质量控制在材料进厂之后,需要进行质量控制。
这包括对材料的化学成分、力学性能和物理性能等进行检测。
常用的检测方法包括化学分析、金相分析、拉伸试验和硬度等。
只有经过严格的质量控制,才能确保原材料的质量符合要求。
3. 工艺控制3.1 锻造工艺锻件的质量与锻造工艺密切相关。
在锻造过程中,需要控制锻件的温度、冷却速度和变形程度等参数。
这些参数的选择与锻件的形状和尺寸有关。
合理的工艺控制可以保证锻件具有良好的内部组织和力学性能。
3.2 热处理工艺在锻造后,锻件需要进行热处理,以消除内部应力和改善材料的性能。
热处理工艺包括退火、正火、淬火等。
不同的工艺对锻件的性能影响不同,需要根据锻件的要求选择合适的热处理工艺。
3.3 表面处理工艺锻件的表面处理对于保护锻件和延长使用寿命至关重要。
常见的表面处理方法包括镀锌、热喷涂和涂装等。
这些方法可以提高锻件的耐腐蚀性和耐磨性,也可以增加锻件的美观度。
4. 质量检测4.1 金相检测金相检测是一种常见的锻件质量检测方法。
通过对锻件的金相组织进行观察和分析,可以判断锻件的质量是否达到要求。
金相检测可以检测锻件的晶粒尺寸、组织均匀性和缺陷等。
4.2 声波检测声波检测是一种无损检测方法,可以用来检测锻件的内部缺陷和裂纹等。
声波检测可以通过对锻件表面传播的声波信号进行分析,判断锻件的质量是否符合标准要求。
4.3 硬度硬度是一种常用的锻件硬度检测方法。
通过在锻件表面施加一定的压力,测量压痕的深度或周长,可以推断锻件的硬度。
硬度可以用来评估锻件的耐磨性和强度。
5. 结论锻件质量控制是确保锻件质量的重要手段。
通过对材料选用、工艺控制和质量检测等方面的控制,可以确保锻件具有良好的性能和质量。
铝合金锻造工艺技术要求

铝合金锻造工艺技术要求铝合金锻造工艺技术要求铝合金锻造工艺是一种将铝合金材料加热至一定温度后在压力作用下使其发生塑性变形的工艺方法。
下面将介绍铝合金锻造工艺技术的要求。
一、温度控制:铝合金锻造过程中,材料的温度控制至关重要。
高温有利于材料的塑性变形,但温度过高会导致材料的烧损、氧化以及晶粒长大,降低材料的性能,因此需要控制加热温度,一般在材料的熔点以下适当加热。
而在锻造过程中,温度的控制也很重要,锻造温度过低会使材料难以塑性变形,而温度过高则易导致过度变形、裂纹等缺陷。
因此,需要根据材料的特性和实际情况,在适宜的温度范围内进行锻造。
二、锻造压力控制:铝合金的锻造过程中,锻造压力的大小直接影响到材料的塑性变形。
合理的锻造压力能够使材料得到良好的塑性变形,但过大的锻造压力会使得材料过度变形,甚至出现裂纹等缺陷。
因此,在锻造过程中需要合理控制锻造压力,根据材料的特性和锻造要求进行调整。
三、锻造速度控制:锻造速度是指在铝合金锻造过程中,锤击或压力的速度。
良好的锻造速度有利于材料的塑性变形,但过快的锻造速度则会使得材料塑性变形不充分,甚至出现裂纹等缺陷。
因此,在铝合金锻造过程中,需要合理控制锻造速度,使其保持在适宜范围内,以确保材料得到良好的塑性变形。
四、模具设计和加工精度:模具设计和加工精度直接影响到铝合金锻造件的尺寸和形状。
模具设计应合理,保证锻造件的尺寸和形状满足要求。
而模具的加工精度对于铝合金锻造件的质量也有重要影响,因此,需要严格按照设计要求进行模具的加工。
五、表面处理:铝合金锻造后的产品通常需要进行表面处理,以去除表面氧化层、油污等杂质,提高表面质量。
表面处理的方法可以包括酸洗、抛光等。
表面处理的质量直接影响到产品的外观和性能,因此,需要严格控制表面处理的质量。
综上所述,铝合金锻造工艺技术要求包括温度控制、锻造压力控制、锻造速度控制、模具设计和加工精度以及表面处理等多个方面。
只有通过合理控制这些要求,才能保证铝合金锻造过程中材料的塑性变形和锻造件的质量。
一-、锻造过程质量控制

一、锻造过程质量控制锻造是制造行业中重要的成型工艺之一,主要应用于金属制品的生产。
正确的质量控制可以提高锻造的成功率,减少不合格品率,降低生产成本,提高生产效率。
本文将介绍锻造过程中的质量控制方法和技巧。
1. 原材料控制1.1. 原材料材质和尺寸的选择不同的材质和尺寸的原材料会对后续锻造工艺的成功与否产生重大影响。
选择正确的原材料是保证锻造成功的重要因素。
原材料应符合国家标准和行业规范,并经过严格的质量检测和审核。
1.2. 原材料储存原材料的储存应该在防潮、防震、防污染的情况下进行,确保原材料的质量不会受到影响。
在储存过程中要注意分类、标识、清点,并对储存环境定期进行检查。
2. 模具的质量控制2.1. 模具的制造模具的制造质量直接影响到成品的质量。
模具的制造过程应该符合相关技术规范和标准,以确保模具具备耐用性、精度和稳定性等特性。
2.2. 模具的维护模具使用过程中需要进行适当的维护,如要及时清理、润滑,做好防锈工作等。
维护模具可延长其使用寿命,节约生产成本,保证成品的质量。
3. 锻造的工艺控制3.1. 锻造温度和时间的控制锻造温度是影响锻造质量的重要因素,打开锻模前应根据锻造材料确定合适的合金锻造温度。
锻造过程中应根据材料性能来调控温度和工序。
打制物件、加工装备、锻造工艺的不同都会影响锻造时间的选择。
3.2. 锻造的过程控制锻造过程中需要严格控制上、下件之间的高度和位置,防止成品的形状变形或出现缺陷。
在锻造过程中要避免热裂和表面缺陷、孔洞的出现。
在锻造的过程中要根据锻造材料的物性,将锻造力度控制在合理的范围内,以确保成品质量。
4. 成品的质量控制4.1. 成品尺寸控制成品的尺寸控制是保证产品质量的关键。
需使用量具对产品进行尺寸测量,并根据测量的数据进行修正。
成品严重尺寸超标将直接影响产品的质量和外观。
4.2. 成品外观和表面处理成品外观质量是保证产品销售的关键因素之一。
成品表面的处理需要做到光滑、美观、符合质量要求。
锻件质量检验规范
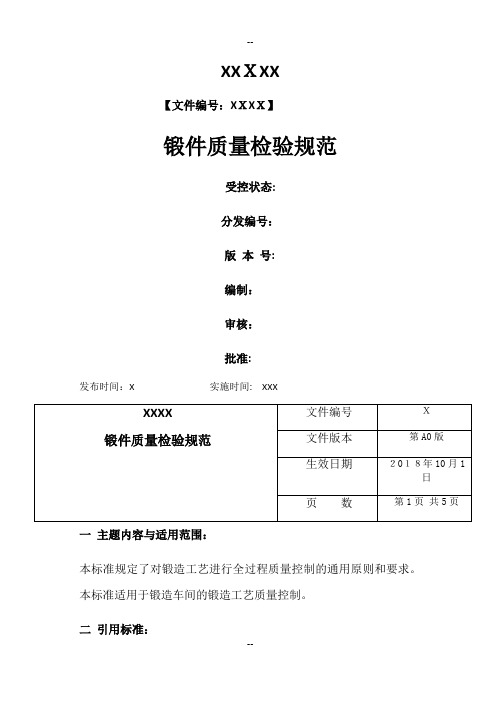
XXXXX【文件编号:XXXX】锻件质量检验规范受控状态:分发编号:版本号:编制:审核:批准:发布时间:X 实施时间: XXX一主题内容与适用范围:本标准规定了对锻造工艺进行全过程质量控制的通用原则和要求。
本标准适用于锻造车间的锻造工艺质量控制。
二引用标准:GB 12361-2016 钢质模锻件通用技术条件GB 12362-2016 钢质模锻件公差及机械加工余量GB 13318锻造车间安全生产通则GB/T12363-2005 锻件功能分类JB 4249 锤上钢质自由锻件机械加工余量与公差JB4385锤上钢质自由锻件通用技术条件JB/T 6052钢质自由锻件加热通用技术要求JB/T 6055 锻造车间环境保护导则GB/T7232金属热处理工艺GB/T231-2009金属材料布氏硬度GB/T13320-2007钢制模锻件金相组织评定图及评定方法三.锻件分类本标准质量控制所涉及的锻件分类按GB/T 12363 执行。
四环境的控制:锻造厂的工作环境包括厂房地面、天窗、温度、通风、照明、噪声、通道、管道以及坯料、锻件和工夹模具的存放等均应按GB 13318第3 章和JB/T 6055 第3、4章的要求和国家的有关法规、法律制订本企业的具体实施要求。
五设备、仪表与工装的控制:5. 1设备、仪表5. 1.1各类设备必须完好,并有操作规程和维修、检定制度。
5.1. 2 各类在用主要设备必须挂有完好设备标牌,并有检验有效期及下次检定日期。
不合格设备及超过检定合格有效期的设备必须挂“停用”标牌。
5. 1.3设备的控制系统及检测显示仪表应定期检查,确保仪表和其精度的显示数值准确。
5. 1.4 加热设备的温度显示及测点布置应正确反应加热区炉温及炉温均匀性。
5. 1.5 所用设备都必须建立档案,其具体内容包括:a.设备使用说明书b.台时记录c.故障记录d.修理记录e. 历年检定报告及检定合格证。
5. 2 模具及其他工装5. 2. 1新模具应按模具图的要求制造,检验合格后进行试模,确认达到设计、制造要求后方可投入生产。
锻件生产中质量控制的节点及问题修复(二)

锻件生产中质量控制的节点及问题修复(二)引言概述:锻件生产中的质量控制对于确保产品质量和客户满意度至关重要。
本文将在前一篇文章的基础上继续探讨锻件生产中的质量控制的节点和问题修复。
通过对质量控制节点的认识和解决问题的方法,可以提高锻件生产的质量,降低质量风险,增加企业竞争力。
正文:一、原材料质量控制1. 严格选择合格的锻造原材料供应商2. 对原材料进行质量检测,包括化学成分、机械性能等3. 建立合理的原材料进货检验标准4. 定期对原材料供应商进行评估和管理二、锻件成型质量控制1. 控制锻造温度和时间,确保锻造工艺参数符合要求2. 检查锻件表面质量,确保无裂纹、麻花、气孔等缺陷3. 进行锻件尺寸测量,保障尺寸精度符合设计要求4. 对锻件进行硬度测试,评估材料的力学性能5. 利用无损检测技术对锻件进行质检,发现隐蔽缺陷三、热处理质量控制1. 控制热处理温度和时间,保持合适的工艺参数2. 定期对热处理设备和工艺进行校准和维护3. 检查热处理后的锻件组织和性能,确保满足要求4. 严禁出现过热、过淬和组织不均匀等质量问题5. 对热处理过程进行记录和跟踪,便于问题溯源和控制四、机械加工质量控制1. 选择合适的加工工艺和工装,确保加工质量2. 进行加工参数的精确控制,包括切削速度、进给量等3. 定期检查和保养加工设备,确保设备的正常运行4. 对加工后的锻件进行尺寸检测,确保精度符合要求5. 建立合理的加工过程记录和质量跟踪机制,用于分析和改进五、最终产品质量控制1. 对锻件进行总体质量检查,确保无缺陷和问题2. 进行性能测试,包括强度、硬度、韧性等方面3. 进行外观检测,包括表面光洁度、形状等方面4. 进行功能验证,确保锻件能满足设计要求5. 建立合理的产品质量追溯体系,便于问题修复和质量管理总结:锻件生产中质量控制的节点及问题修复是确保产品质量的关键。
通过对原材料、成型、热处理、机械加工和最终产品的质量控制,可以降低质量风险,提高产品质量和客户满意度。
硬铝锻造标准最新规范

硬铝锻造标准最新规范硬铝锻造是一种金属加工技术,它涉及到将硬铝材料加热至一定温度后进行锻造以改善其物理性能和加工特性。
以下是硬铝锻造的最新标准规范:1. 材料选择与准备:- 硬铝材料应符合ASTM B221或相应的国际标准。
- 材料在锻造前应进行彻底的清洁和检查,以确保无杂质和缺陷。
2. 加热温度:- 硬铝的加热温度应控制在450°C至500°C之间,以确保材料的可塑性。
3. 锻造工艺:- 锻造应在加热后的硬铝材料处于热塑性状态下进行。
- 锻造过程中应控制锻造速度,避免过快或过慢导致材料性能下降。
4. 锻造设备:- 使用的锻造设备应定期进行维护和校准,确保其精度和可靠性。
5. 锻造后处理:- 锻造完成后,材料应进行适当的冷却处理,以稳定其微观结构。
- 冷却后的材料应进行硬度测试和微观结构分析,确保符合性能要求。
6. 质量控制:- 锻造过程中应实施严格的质量控制措施,包括但不限于尺寸精度、表面光洁度和内部缺陷检测。
7. 安全与环保:- 锻造操作应遵守相关的安全标准,确保操作人员的安全。
- 锻造过程中产生的废气、废液等应进行妥善处理,符合环保要求。
8. 记录与追溯:- 所有锻造过程的参数和结果都应详细记录,以便追溯和分析。
9. 产品标识:- 完成锻造的产品应有清晰的标识,包括材料类型、锻造日期、批次号等信息。
10. 后续加工:- 对于需要进一步加工的硬铝锻造件,应按照特定的加工标准进行操作。
结束语:硬铝锻造标准的最新规范旨在确保产品质量的同时,提高生产效率和安全性。
随着技术的发展和行业标准的更新,这些规范可能会有所变化,因此制造商和操作人员应持续关注最新的行业动态和技术进步。
锻件质量控制

锻件质量控制一、引言锻件作为一种重要的金属加工方式,广泛应用于航空航天、汽车制造、机械制造等领域。
为了确保锻件的质量,提高产品的性能和可靠性,需要进行严格的质量控制。
本文将详细介绍锻件质量控制的标准格式文本,包括锻件质量控制的目的、原则、方法和步骤等内容。
二、质量控制目的锻件质量控制的目的是确保锻件的尺寸精度、力学性能和表面质量达到设计要求,以满足产品的功能和使用要求。
通过质量控制,可以提高产品的可靠性和使用寿命,降低生产成本,增强企业的竞争力。
三、质量控制原则1. 完善的质量管理体系:建立健全的质量管理体系,包括质量目标、质量标准、质量检测方法和质量管理流程等,以确保质量控制的全面性和系统性。
2. 严格的工艺控制:对于每个锻件工艺环节,要制定详细的工艺规程和操作规范,确保每个环节的工艺参数和操作要求得到严格执行。
3. 精细的设备管理:对于锻造设备,要进行定期的维护和保养,确保设备的正常运行和精度稳定。
4. 严格的原材料控制:对于锻件所使用的原材料,要进行严格的质量检验和控制,确保原材料的质量符合要求。
5. 全员参与的质量意识:通过培训和教育,提高员工的质量意识和责任心,使每个员工都能够积极参与到质量控制中来。
四、质量控制方法1. 尺寸控制:通过测量和检验,对锻件的尺寸进行控制。
可以使用传统的测量工具如卡尺、游标卡尺等,也可以使用先进的三坐标测量仪等设备进行精确测量。
2. 力学性能控制:通过对锻件进行拉伸、硬度、冲击等力学性能测试,对锻件的力学性能进行控制。
3. 表面质量控制:通过对锻件的表面进行观察和检验,对锻件的表面质量进行控制。
可以使用目视检查、放大镜观察、显微镜观察等方法进行表面质量检验。
4. 非破坏性检测:通过超声波检测、磁粉检测、涡流检测等非破坏性检测方法,对锻件进行缺陷检测,以确保锻件的无损性。
五、质量控制步骤1. 制定质量控制计划:根据产品的要求和生产工艺,制定质量控制计划,明确质量控制的目标、方法和步骤。
锻压工艺规范

1.3 墩粗工序的操作要点和规则墩粗是使坯料高度减小而横截面积增大的锻造工序。
它主要用于锻造齿轮坯、凸缘和圆盘等类锻件,也作为提高拔长锻造比和冲孔前的预备工序。
操作中应注意:1)坯料在墩粗前应加热到材料所允许的最高加热温度,并进行适当的保温,以便坯料内外温度均匀一致,降低其变形抗力,防止墩粗时坯料中心出现偏移,造成钢锭偏析区移向一边,从而使墩件质量变坏。
2)合金钢和重量大于8~12t的碳素钢钢锭,墩粗前必须倒棱,以锻合其皮下缺陷,使墩粗表面不致产生裂纹,同时去除钢锭棱边和锥度,可保证锭身平直,避免不均匀性墩粗。
3)为了防止坯料墩粗时产生纵向弯曲,坯料墩粗前的高度H与直径D 之比不应超过3,最好将H/D控制在2~2.5之间。
对于正六面体锻坯的墩粗,其高度和最小基边之比应小于3.5~4。
4)檄粗前的坯料两端面必须平整,且应与坯料的轴心线垂直。
在坯料的侧表面上,不应有凹坑、划痕和裂纹等缺陷,以防在墩粗过程中进一步扩大。
5)钢坯墩粗时,为了防止出现墩粗裂纹和不均匀变形,应不断地绕着坯料的轴心线转动,每次墩粗的压下量不应超过该材料所允许的极限值。
墩后再拔时其高度应满足拔长要求。
6)锤上墩粗时,坯料的高度应与锤头的行程空间尺寸相适应,即应使H-h0>0.25H式中H—锤头的最大行程(mm);h0——坯料的原始高度(mm)。
7)水压机上墩粗时,其锭身高度、上墩粗板高度和下墩粗盘高度之和,应小于水压机的最大净空距,即应使H n≥H u+H i+H b+(100~200)式中H n——水压机的最大净空距(mm);H u——上墩粗板高度(mm);H i——锭身高度(mm));H b——下墩粗盘高度(mm)。
8)为了使墩粗坯料组织均匀和不出现过大的侧面鼓肚,应视情况采取相应的改善措施,这些可行的措施有:①预热墩粗工具,以防坯料过快冷却。
一般均应预热到200—300℃。
②对于低塑性材料的墩粗,应在上、下端面使用玻璃粉、玻璃棉和石墨粉等润滑剂,以提高变形均匀性。
锻件质量控制的工作内容(二)
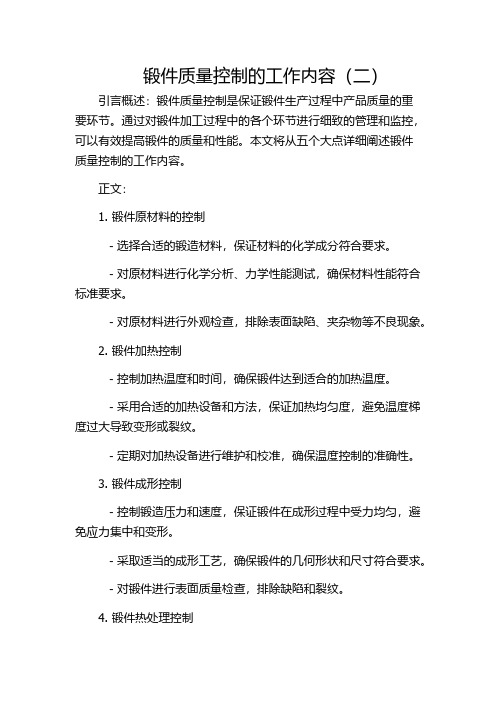
锻件质量控制的工作内容(二)引言概述:锻件质量控制是保证锻件生产过程中产品质量的重要环节。
通过对锻件加工过程中的各个环节进行细致的管理和监控,可以有效提高锻件的质量和性能。
本文将从五个大点详细阐述锻件质量控制的工作内容。
正文:1. 锻件原材料的控制- 选择合适的锻造材料,保证材料的化学成分符合要求。
- 对原材料进行化学分析、力学性能测试,确保材料性能符合标准要求。
- 对原材料进行外观检查,排除表面缺陷、夹杂物等不良现象。
2. 锻件加热控制- 控制加热温度和时间,确保锻件达到适合的加热温度。
- 采用合适的加热设备和方法,保证加热均匀度,避免温度梯度过大导致变形或裂纹。
- 定期对加热设备进行维护和校准,确保温度控制的准确性。
3. 锻件成形控制- 控制锻造压力和速度,保证锻件在成形过程中受力均匀,避免应力集中和变形。
- 采取适当的成形工艺,确保锻件的几何形状和尺寸符合要求。
- 对锻件进行表面质量检查,排除缺陷和裂纹。
4. 锻件热处理控制- 选择合适的热处理工艺,根据锻件的材料和性能要求进行退火、正火、淬火等处理。
- 控制热处理温度和时间,确保锻件达到所需的组织结构和硬度。
- 对热处理设备进行定期检查和维护,保证热处理过程的稳定性和可靠性。
5. 锻件检测与检验- 采用合适的检测方法,如超声波检测、射线检测、磁粉检测等,检查锻件的内部和外部缺陷。
- 进行硬度测试、拉伸试验、冲击试验等力学性能测试,确保锻件的力学性能符合标准。
- 进行尺寸测量和形状检查,检验锻件的几何尺寸和外观质量。
总结:锻件质量控制的工作内容包括锻件原材料的控制、锻件加热控制、锻件成形控制、锻件热处理控制以及锻件检测与检验。
通过严格管理和监控每个环节,可以保证锻件的质量和性能达到设计要求,提高产品的可靠性和安全性。
锻件质量控制的方法与要点(二)
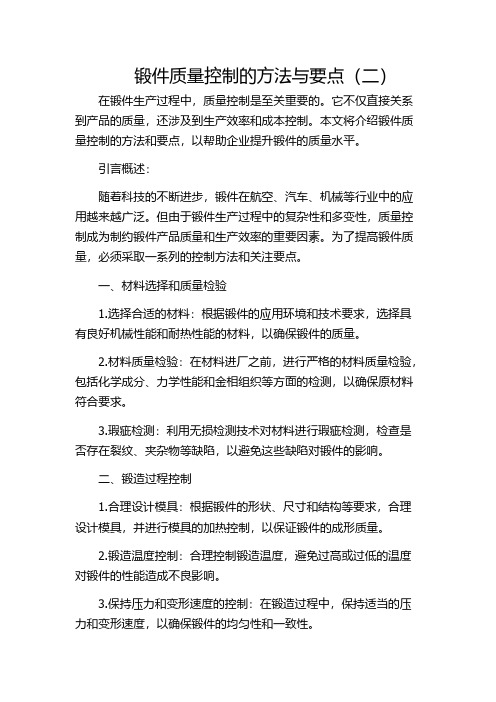
锻件质量控制的方法与要点(二)在锻件生产过程中,质量控制是至关重要的。
它不仅直接关系到产品的质量,还涉及到生产效率和成本控制。
本文将介绍锻件质量控制的方法和要点,以帮助企业提升锻件的质量水平。
引言概述:随着科技的不断进步,锻件在航空、汽车、机械等行业中的应用越来越广泛。
但由于锻件生产过程中的复杂性和多变性,质量控制成为制约锻件产品质量和生产效率的重要因素。
为了提高锻件质量,必须采取一系列的控制方法和关注要点。
一、材料选择和质量检验1.选择合适的材料:根据锻件的应用环境和技术要求,选择具有良好机械性能和耐热性能的材料,以确保锻件的质量。
2.材料质量检验:在材料进厂之前,进行严格的材料质量检验,包括化学成分、力学性能和金相组织等方面的检测,以确保原材料符合要求。
3.瑕疵检测:利用无损检测技术对材料进行瑕疵检测,检查是否存在裂纹、夹杂物等缺陷,以避免这些缺陷对锻件的影响。
二、锻造过程控制1.合理设计模具:根据锻件的形状、尺寸和结构等要求,合理设计模具,并进行模具的加热控制,以保证锻件的成形质量。
2.锻造温度控制:合理控制锻造温度,避免过高或过低的温度对锻件的性能造成不良影响。
3.保持压力和变形速度的控制:在锻造过程中,保持适当的压力和变形速度,以确保锻件的均匀性和一致性。
4.锻件冷却控制:在锻件完成后,进行合理的冷却处理,以消除内部应力,提高锻件的强度和韧性。
5.锻件尺寸和形状控制:通过更细致的模具设计和更精确的锻造工艺控制,实现锻件尺寸和形状的精确控制。
三、热处理和表面处理1.热处理工艺的选择:根据锻件的材料和要求,选择合适的热处理工艺,以改善锻件的组织结构和性能。
2.热处理温度和时间的控制:在热处理过程中,控制温度和时间,确保锻件的热处理效果符合要求。
3.表面处理的选择:根据锻件的应用要求,选择合适的表面处理方式,如表面涂层、镀层等,以提高锻件的耐腐蚀性和装饰性。
四、非破坏性检测和尺寸检验1.非破坏性检测方法的选择:根据锻件的形状和结构,选择合适的非破坏性检测方法,如超声波检测、磁粉检测等,以检测锻件的内部缺陷。
锻造操作规程

锻造操作规程一、概述锻造是一种重要的金属加工方式,它通过施加力量将金属坯料加热至一定温度后进行塑性变形,从而获得所需形状和尺寸的金属工件。
为了确保锻造操作的安全性、高效性和质量,制定一套科学合理的锻造操作规程至关重要。
二、设备与工具1. 锻造设备:包括锻造机床、锻模、锻锤等,必须经过定期维护和检查,确保设备的正常运行和安全性。
2. 工具:包括测量工具(千分尺、卡尺等)、夹具、润滑剂等,必须保持干净整洁,并按要求进行保养和更换。
三、操作流程1. 准备工作:- 检查设备和工具的状态,确保其良好运行。
- 清理待锻造的金属坯料,确保其表面无杂质,材质符合要求。
- 准确测量和标记金属坯料的尺寸和形状,以便后续操作。
2. 加热:- 将金属坯料放置在锻造炉中进行加热,加热温度应根据材料种类、形状和尺寸等因素进行合理控制。
- 确保金属坯料均匀受热,避免局部过热或过冷。
3. 锻造操作:- 对加热至适宜温度的金属坯料,根据工艺要求选择合适的锻造设备和锻模。
- 将金属坯料放置在锻造设备上,根据工艺要求施加适当的压力进行变形。
- 控制锤击频率和力度,确保锻造过程稳定,避免金属坯料的损坏或变形超过允许范围。
4. 后处理:- 将锻造好的金属工件进行修整和清洁,确保尺寸和形状的精确度和表面质量。
- 根据需要进行热处理、表面处理等工艺,以增强金属工件的性能和使用寿命。
四、操作安全1. 操作人员必须经过专业培训,并持证上岗,严禁未经许可进行锻造操作。
2. 操作人员必须佩戴符合要求的劳动保护用具,如安全帽、防护眼镜、防护手套等。
3. 在进行加热和锻造操作时,应保持工作区域整洁,禁止存放易燃易爆物品,并确保通风良好。
4. 定期对锻造设备进行维护保养,如润滑、清洁和检查电气线路,确保设备的正常运行和安全性。
5. 如发现设备故障、异常或事故,应立即停止操作并报告相关负责人,采取相应措施进行处理。
五、质量控制1. 对加热温度、锻造压力和时间等关键参数进行监控和记录,以确保工件质量符合要求。
锻件质量控制

锻件质量控制一、引言锻件是一种常见的金属加工工艺,广泛应用于各个行业,如汽车创造、航空航天、能源等。
为了确保锻件的质量,保证产品的性能和可靠性,需要进行严格的质量控制。
本文将详细介绍锻件质量控制的标准格式文本。
二、质量控制目标1. 提高锻件的机械性能:包括强度、韧性、硬度等指标。
2. 保证锻件的尺寸精度:确保锻件的几何形状和尺寸符合设计要求。
3. 消除锻件的缺陷:如气孔、夹杂、裂纹等缺陷,提高锻件的无损检测合格率。
4. 提高锻件的表面质量:确保锻件表面光洁度、无明显的划痕和氧化。
三、质量控制步骤1. 原材料检验:对用于锻件的原材料进行严格的检验,包括化学成份、物理性能等指标的检测,确保原材料符合要求。
2. 锻造工艺控制:根据产品的要求,制定合理的锻造工艺参数,包括锻压力、锻后温度等,确保锻件的内部组织和力学性能达到要求。
3. 热处理控制:根据锻件的材料和要求,选择合适的热处理工艺,如淬火、回火等,对锻件进行热处理,提高其硬度和强度。
4. 机械性能测试:对锻件进行拉伸、冲击、硬度等机械性能测试,确保锻件的性能符合要求。
5. 尺寸检测:使用合适的测量工具,对锻件的尺寸进行检测,确保其几何形状和尺寸精度符合要求。
6. 无损检测:使用超声波、射线等无损检测方法,对锻件进行探伤,检测是否存在缺陷,如气孔、夹杂、裂纹等。
7. 表面质量检查:对锻件的表面进行检查,确保表面光洁度、无划痕和氧化等缺陷。
四、质量控制措施1. 制定详细的工艺文件:包括原材料要求、锻造工艺参数、热处理工艺等,确保每一道工艺环节都有明确的要求和标准。
2. 建立质量控制体系:制定相关的质量控制标准和流程,明确各个环节的责任和要求,确保质量控制的全面性和连续性。
3. 培训操作人员:对参预锻件质量控制的操作人员进行培训,提高其技术水平和质量意识,确保操作的准确性和一致性。
4. 使用先进的设备和工艺:选择先进的锻造设备和工艺,提高锻件的质量和生产效率。
锻件质量控制范文精简版

锻件质量控制锻件质量控制引言锻造是一种常见的金属加工工艺,通过在高温下施加压力,将金属材料塑造成所需形状的工艺。
锻件作为一种重要的机械零部件,广泛应用于航空航天、汽车制造、能源和重工业等领域。
由于锻造过程中存在很多因素会影响锻件质量,需要进行严格的质量控制,以保证锻件的稳定性和可靠性。
锻件质量控制的重要性锻件质量直接影响到产品的使用寿命和性能。
对于航空航天领域来说,质量控制尤为关键,一旦因为锻件质量问题导致事故发生,可能造成巨大的损失甚至人员伤亡。
锻件质量控制是提高产品质量、确保安全生产的重要环节。
锻件质量控制方法1. 原材料的质量控制原材料的质量直接关系到最终锻件的质量。
在选择原材料时,需要对其进行严格的检测,包括化学成分、物理性能等方面。
以确保原材料满足设计要求,并且能够在高温高压下具备足够的韧性和强度。
2. 设计和模具的质量控制设计和模具是决定锻件形状和尺寸的重要因素。
设计应该考虑到锻件的形变特性和金属流动情况,以确保锻件能够在锻造过程中均匀受力,避免产生裂纹、缺陷等问题。
模具的质量和精度直接影响到锻件的成型质量,需要进行定期的维修和检测。
3. 锻造过程中的控制锻造过程中,应根据锻件的具体形状和要求,控制适当的温度、压力和速度,以确保金属流动顺畅、成型完整。
需要对锻件进行定期检测和测量,以及及时调整和纠正工艺参数,以防止质量问题的产生。
4. 热处理和表面处理的控制热处理和表面处理是锻件质量控制的重要环节。
通过合理的热处理工艺,可以改善锻件的组织结构和性能。
表面处理则可以提高锻件的抗腐蚀性能和装配性能。
对于关键部位的锻件,还需要进行无损检测和特殊处理。
5. 锻件的检验与锻件的质量检验与是确保质量控制的重要手段。
常用的方法包括外观检查、尺寸测量、硬度、力学性能等。
还需要进行金相显微镜检测、超声波检测等非破坏性检测,以及金属log检测等特殊的质量检验。
锻件质量控制是保证产品质量和安全的重要环节。
锻件质量控制

锻件质量控制锻件质量控制锻件是一种常见的金属成形工艺,通过对金属料坯施加压力,使其发生塑性变形并填充模具的凹槽,从而得到所需形状和尺寸的零件。
锻件广泛应用于航空、航天、汽车、机械等行业,对其质量控制显得尤为重要。
本文将介绍几种常用的锻件质量控制方法。
1. 材料选择在进行锻造之前,首先需要选择适合的锻材。
材料的选择直接影响锻件的质量和性能。
一般来说,优质钢材是较为理想的锻造材料,因其具有良好的塑性和变形能力,可以更好地满足锻造过程中的工艺要求。
此外,还需要根据锻件的具体要求选择合适的材料牌号,确保锻件的强度、韧性和耐磨性等性能指标达到设计要求。
2. 温度控制锻造过程中的温度控制非常重要,直接影响着锻件的质量。
在热锻过程中,材料的变形能力随着温度的提高而增强,因此需要控制锻造温度以保证材料具有足够的塑性。
另外,温度过高也会导致锻件表面氧化,影响锻件的质量。
因此,需要在合适的温度范围内进行锻造,同时注意锻件与空气的隔离,防止氧化。
3. 成形控制成形控制是锻件质量控制的关键环节之一。
在锻造过程中,应根据锻件的形状和尺寸要求,采用合适的成形方式和工艺参数。
对于复杂形状的锻件,可以采用多次工艺锤击或采用多个模具进行多次成形,以保证锻件的准确性和质量。
此外,还应注意锻造的过程控制,确保锻件表面没有裂纹、疵点和缺陷。
4. 热处理控制热处理是锻件质量控制中的重要环节。
通过热处理,可以改善锻件的组织结构和性能,提高其强度和韧性。
常见的热处理方式包括淬火、调质和回火等。
在进行热处理时,需要严格控制时间、温度和冷却速度等参数,确保锻件获得理想的组织和性能。
5. 检测与检验为了保证锻件的质量,需要进行全面的检测与检验。
常用的检测方法包括磁粉探伤、超声波探伤、射线探伤等,可以有效地检测锻件的内部缺陷和表面裂纹。
此外,还需要对锻件的尺寸、形状和性能进行严格的检验,确保锻件符合设计要求。
通过准确的检测和检验,可以及时发现并排除存在的问题,提高锻件的质量。
锻件的工艺及质量控制要点

锻件的工艺及质量控制要点锻件是通过将金属材料加热至一定温度后进行锻造加工得到的零件。
它具有高强度、高硬度、高耐磨性、高抗冲击性等优点,被广泛应用于航空航天、汽车、机械制造等领域。
下面将从工艺和质量控制两个方面来介绍锻件的要点。
一、锻件的工艺要点:1. 材料选择:选择适合锻造的金属材料,并通过分析材料的化学成分、机械性能等指标来确保选择的材料符合要求。
2. 热处理工艺:锻件在锻造过程中需要经历加热、锻造、冷却等工艺过程。
合理的热处理工艺可以确保锻件具有良好的力学性能和组织结构。
3. 锻造温度控制:选择合适的锻造温度可以降低金属材料的变形阻力,提高锻造质量。
在锻造过程中,需要根据不同材料的熔点和热膨胀系数,合理控制锻件的温度,避免发生过热或过冷的情况。
4. 锻造润滑剂选择:在锻造过程中,适量的润滑剂可以减小摩擦阻力,减少热应力和表面氧化,提高锻造质量。
同时,润滑剂的选择也应考虑到对环境的影响。
5. 锻造设备和工装设计:选择合适的锻造设备和工装可以提高锻造效率和质量。
设备的能力和稳定性、工装的精度和可靠性都需要考虑。
6. 锻造过程控制:锻造过程中需要控制好加热温度、锻造力度、锻后尺寸、冷却速度等参数,以保证锻件的内部结构均匀、尺寸精确。
二、锻件的质量控制要点:1. 检验方法和标准:根据锻件的设计要求,制定相应的检验方法和标准。
常用的检验方法包括X射线探伤、超声波探伤、金相分析等,标准可以包括尺寸、力学性能、化学成分等方面。
2. 组织结构控制:通过适当的热处理工艺和锻造参数的控制,调控锻件的组织结构,以获得符合要求的晶粒尺寸、晶粒形状和显微组织等。
3. 尺寸控制:使用精密测量仪器对锻件的尺寸进行测量,确保其符合设计要求。
可以采用三坐标测量机、投影仪等设备进行尺寸测量。
4. 表面质量控制:对锻件表面的缺陷、氧化层、划痕等进行检查和控制,可以采用目视检查、触摸检查或辅助检测设备对表面质量进行评估。
5. 力学性能控制:对锻件的强度、硬度、韧性等力学性能进行测试和评价,并与设计要求进行比较。
hb锻造工艺标准

hb锻造工艺标准
HB锻造工艺标准是针对金属材料锻造过程的一种规范,旨在确保锻件的质量和性能。
以下是一般的HB锻造工艺标准:
1.准备阶段:确定锻造材料和锻造温度范围。
对原材料进行检验,
确保其符合要求。
准备锻造设备和工具,并对它们进行检查和维护。
2.下料:将原材料切割成适当大小的块或条。
下料方式可根据锻造
要求和设备能力选择,如剪切、切割或锯切等。
3.加热:将块或条放入加热炉中加热至锻造温度。
加热时间、温度
和气氛应严格按照规定操作,以确保材料具有合适的塑性和组织。
4.锻造:将加热后的材料放入锻造设备中进行锻打。
根据产品形状
和要求,选择合适的模具和工艺参数。
在锻造过程中,应控制变形量和速度,以避免产生裂纹和其他缺陷。
5.冷却:将锻件迅速冷却至室温,以防止热处理过程中可能产生的
裂纹。
6.热处理:根据需要,对锻件进行热处理以调整其机械性能和硬度。
热处理工艺应根据材料类型和要求选择,包括加热温度、时间、冷却速度等参数。
7.表面处理:对锻件进行必要的表面处理,如清理、打磨、防锈等。
8.检验:对锻件进行质量检验,包括尺寸、外观、无损检测等。
确
保锻件符合设计要求和技术标准。
9.包装:将合格锻件包装好,以便运输和存储。
需要注意的是,HB锻造工艺标准不是唯一的锻造工艺规范,具体标准可能因材料类型、设备条件和产品要求而有所不同。
在实际操作中,应根据具体情况选择合适的工艺流程和参数。
- 1、下载文档前请自行甄别文档内容的完整性,平台不提供额外的编辑、内容补充、找答案等附加服务。
- 2、"仅部分预览"的文档,不可在线预览部分如存在完整性等问题,可反馈申请退款(可完整预览的文档不适用该条件!)。
- 3、如文档侵犯您的权益,请联系客服反馈,我们会尽快为您处理(人工客服工作时间:9:00-18:30)。
衡阳振洋汽车配件有限公司锻造工艺质量控制规范一主题内容与适用范围:本标准规定了对锻造工艺进行全过程质量控制的通用原则和要求。
本标准适用于衡阳振洋汽车配件有限公司锻造车间的锻造工艺质量控制。
二引用标准:GB 12361钢质模锻件通用技术条件 GB 12362钢质模锻件公差及机械加工余量 GB 13318锻造车间安全生产通则 GB/T 12363锻件功能分类JB 4249锤上钢质自由锻件机械加工余量与公差JB 4385锤上钢质自由锻件通用技术条件JB/T 6052钢质自由锻件加热通用技术要求JB/T 6055锻造车间环境保护导则三.锻件分类本标准质量控制所涉及的锻件分类按GB/T 12363执行。
四环境的控制:锻造厂的工作环境包括厂房地面、天窗、温度、通风、照明、噪声、通道、管道以及坯料、锻件和工夹模具的存放等均应按GB 13318第3章和JB/T 6055第3、4章的要求和国家的有关法规、法律制订本企业的具体实施要求。
五设备、仪表与工装的控制:5. 1设备、仪表5. 1. 1各类设备必须完好,并有操作规程和维修、检定制度。
5. 1.2各类在用主要设备必须挂有完好设备标牌,并有检验有效期及下次检定日期。
不合格设备及超过检定合格有效期的设备必须挂“停用”标牌。
5. 1.3设备的控制系统及检测显示仪表应定期检查,确保仪表和其精度的显示数值准确。
5. 1. 4加热设备的温度显示及测点布置应正确反应加热区炉温及炉温均匀性。
5. 1.5所用设备都必须建立档案,其具体内容包括:a. 设备使用说明书b. 台时记录c. 故障记录d. 修理记录e. 历年检定报告及检定合格证5. 2 模具及其他工装5. 2. 1 新模具应按模具图的要求制造 ,检验合格后进行试模 , 确认达到设计、制造要求后方可投入生产。
5. 2. 2 在每批锻件生产结束时 ,应将锻造的尾件上打标记并经检验尺寸合格后 , 模具方可返库继续使用。
5. 2. 3 锻造所用工具 ,必须按工艺文件的规定选用 ,并经检查完好方可使用。
5. 2. 4 每套模具(含预锻模、切边模等)必须建立“模具履历表” , 并建立严格的模具管理制度。
六原材料的控制:6. 1 锻件用原材料(含钢锭)应有质量证明书,并符合工艺文件规定的材料牌号、尺寸规格、性能要求。
6. 2 原材料和坯料进厂后需经材料检验部门复验 , 锻造用的棒材及锻坯 , 都必须有复验合格报告单, 复验合格的原材料应有复验印记 , 不合格料应做出明显的标记。
6. 3 合格料、待检料、不合格料应有明显标记 ,且应分区存放 ,严禁混料。
6. 4 合格料的入库、出库必须严格遵守公司的管理制度。
七文件与资料的控制:7. 1 必备的技术文件锻件生产应具有零件图、锻件图、工序图、模具图、技术标准、生产说明书、工艺规程等技术文件。
7. 2 技术文件要求:7. 2. 1 技术文件内容的表达要准确、简明、通俗易懂且有逻辑性 ,并应符合标准化的要求 , 各种技术文件必须统一、完整。
7. 2. 2 所有的技术文件均应按规定的程序审批签字后 ,方能生效。
技术文件如有更改 ,其审批程序与原文件的审批程序相同。
7. 2. 3 所有技术文件均应分类存档7. 3 原始记录所涉及的所有原始记录、工艺参数和检测报告等技术资料均应归档 , 其保存期视锻件的重要程度而定 , 一般在 1-10 年内。
八生产工艺的控制:8. 1 下料8. 1. 1 下料前应根据工艺规程和工序卡核实材料牌号、规格、数量、熔炼炉(批)号。
并检查表面质量 , 有特殊要求时 ,还应检查头尾部标记。
8. 1. 2 下料必须按照锻件号、材料牌号、规格和熔炼炉(批)号分批进行 , 并在工序卡上注明下料个数,以防止有异料混入。
如遇材料代用, 必须严格按材料代用制度的规定办理代用手续后, 方可下料。
8. 1. 3 下料时, 应严格执行“首件三检” (自检、互检和专检)制度。
检验合格并作出明显标记后方可投入生产。
8. 1. 4 坯料的重量、尺寸公差、表面及端面质量 ,按工艺规程要求。
8. 1. 5 下料工在下料过程中 ,如发现坯料有肉眼可见的缺陷时 , 应及时报告检验人员或工艺人员, 待处理后方可继续工作。
8. 1. 6 下料场地应保持整洁。
应按材料牌号、熔炼炉(批)号、规格尺寸分别放置 , 下好的坯料经检验员检查确认合格并做好标记后 ,应装箱管理 ,不得混料。
8. 1. 7 剩余料应标明材料牌号和熔炼炉(批)号及时退库 ,严格分类管理。
8. 2 加热:8. 2. 1 坯料加热前应检查材料牌号、熔炼炉(批)号、尺寸规格、数量是否与工序卡相符。
8. 2. 2 坯料装炉前必须清除炉膛内的杂物。
在电炉中加热的坯料表面不得沾染油污。
8. 2. 3 坯料入炉时 ,应放在工作区内 , 为保证坯料加热均匀 ,大型坯料应加垫块 , 坯料之间应有一定的间距 , 必要时, 应有序排放。
8. 2. 4 冷锭加热应按相应的“锻件加热通用技术要求” 规定加热。
8. 2. 5 敞焰炉加热时 ,不允许火焰直接喷射在坯料表面。
8. 2. 6 电炉加热时 ,坯料应与发热元件保持一定距离 , 或采取屏蔽措施防止金属过烧。
8. 2. 7对于精锻件坯料的加热,应采用无氧化或少氧化加热方法。
8. 2. 8坯料加热温度及加热时间,应按相应锻件的工艺规程要求进行。
坯料加热的全过程应做好加热记录,以便归档备查。
8. 2. 9坯料加热时氧化皮的厚度、脱碳层深度应符合锻件工艺要求坯料加热不允许产生过热、过烧和内部裂纹等现象坯料因故不能按时锻造可采取降温或出炉等方法处理但必须符合工艺规程的要求。
8. 2. 10相同加热规范的不同坯料同炉加热时在炉内必须分区放置严禁混料。
8. 2. 11不同加热规范的材料原则上不得同炉加热若确需同炉加热则必须选择加热规范相近的装入一炉加热但需采取技术保证措施。
8. 2. 12加热不同类型合金的注意事项a. 加热过铜合金的设备应先进行除铜清理后方可对钢坯及其他合金进行加热b. 加热铝合金坯料时炉内气氛不允许含硫和含水蒸气c. 加热钛合金坯料时炉内不允许有还原性气氛。
8. 2. 13坯料加热时的料温应用测温仪器检测并做好加热记录归档备查。
8. 3锻造:8. 3. 1根据锻件的材料、形状、尺寸及工艺要求选择相应的锻造设备。
锻件必须在工艺文件指定的设备上进行锻造。
8. 3. 2锻造前操作人员应熟悉锻件图及工艺文件。
8. 3. 3锻造前所用工、模具必须采用正确的方法预热至规定的温度。
8. 3. 4根据锻件复杂程度、材料和工艺要求选用合适的润滑剂。
8. 3. 5坯料在锻造前和锻造过程中应注意去除氧化皮。
8. 3. 6锻造时必须严格控制始锻温度、终锻温度、变形程度和变形速度。
8. 3. 7锻造操作过程中必须严格按照工艺规程和工序卡进行。
并随时注意坯料变形是否正常如发现折摺、裂纹等缺陷必须立即采用适当方法加以清除在不影响锻件质量情况下方可继续锻造。
8. 3. 9锻后热处理应按有关工艺文件进行。
可以按生产厂的工艺规程进行8. 3. 10 I、H类锻件必要时应提出专用工艺说明书并应进行初始生产工艺、工装的试验验证合格后方可投入生产。
I、H 类锻件应按锻件图号建立质量档案。
8. 3. 11锻件的切边、冲孔、校正温度应根据锻件工艺规程的有关规定进行。
8. 3. 12锻件表面应按如下的要求进行清理a. 表面清理应按工艺要求选用喷砂、抛丸、滚筒、酸洗或其他方法。
清理后的锻件表面质量应符合工艺技术文件要求b. 锻件表面缺陷允许清理清理深度及深宽比按相应锻件技术标准规定c. 采用酸洗清理时酸洗溶液应按相应的技术文件进行定期化验和更换。
锻件不允许酸洗过度。
8. 4锻件检验8. 4. 1工序检验8. 4. 1. 1每批锻件必须进行“首件三检”制度,由试模员试模检验合格后方可正式投产。
生产中严格执行自检、互检和专检。
8. 4. 1. 2车间主管应对生产现场进行巡回检查对锻件加热炉温度的控制、锻造操作情况进行监控并定期抽检锻件的外形尺寸及表面质量。
8. 4. 1. 3锻件或坯料经检验合格后检验员应在工序卡或记录卡上签字后方可转入下道工序。
8. 4. 2锻件终检8. 4. 2. 1模锻件终检应按锻件图及 GB 12361 GB 12362和公司等有关规定进行。
8. 4. 2. 2 自由锻锻件终检应按锻件图及J B 4249 JB 4385 ZB J32 003.1 003.8、ZB J32 001 或公司的有关规定进行。
8. 4. 2. 3在规定的锻件部位上打检验印记(或挂标签)或其他标记均可。
8. 4. 3合格证合格证应由检验部门按有关技术标准或合同要求填写和签发锻件合格证。
8. 4. 4不合格品经检验部门检验,确认为不合格的锻件,应隔离存放,并交质保体系的不合格品处理单位进行处理。
九锻件质量及信息反馈处理:9. 1 生产过程中 , 发现质量问题 , 应立即停止生产并及时组织分析 , 找出原因并提出处理办法或改进措施 , 并经生产验证确认产品合格后 , 方可恢复生产。
9. 2 定期进行用户(或下道工序)的查访工作 , 对查访中用户提出的意见及反馈的信息要及时研究处理。
十人员素质控制:10. 1 锻造生产各类岗位的操作人员和质量控制管理人员 , 应具有一定的专业理论知识和生产实践经验。
10. 2 锻造操作人员、仪表员、检验员等必须进行相应专业的技术培训和考核 , 取得操作许可证后 , 方可上岗操作。
10. 3 对各类操作工人的技术要求按“机械工业工人技术等级中锻压的应知应会” 进行培训和考核。
培训和考核按有关规定执行。