冲压模具组模程序
模具制造技术 冲压模具装配实例

(2)复合冲裁模的装配过程及步骤 复合冲裁模主要工作零件的加工
01 备料(材料CrWMn,棒料,备料时要考虑锻造时的烧损) 备料(材料CrWMn,棒料,备料时要考虑锻造时的烧损) 02 锻造(锻成146 ㎜×l26 ㎜×31 ㎜的坯料) 锻造(锻成146 ㎜×l26 ㎜×31 03 热处理(退火) 04 铣(刨)削 (铣或刨削六面成141㎜×l21 ㎜×26㎜) (铣或刨削六面成141㎜×l21 ㎜×26㎜ 05 磨削(磨削上、下两端面及相邻两侧基面,用90角尺测量相邻两面 磨削(磨削上、下两端面及相邻两侧基面,用90角尺测量相邻两面 的垂直度) 06 钳工加工(用平板和划线盘按图划线,并打洋冲眼,用φ8.5的钻头 钳工加工(用平板和划线盘按图划线,并打洋冲眼,用φ8.5的钻头 钻4-M10的螺纹预孔;用φ9.7mm的钻头钻2-φ100+0.015mm圆柱销孔的 M10的螺纹预孔;用φ9.7mm的钻头钻2 φ100+0.015mm圆柱销孔的 预孔;用φ9mm的钻头钻3 φ9mm×35mm的挡料销让位孔;用φ3mm的 预孔;用φ9mm的钻头钻3-φ9mm×35mm的挡料销让位孔;用φ3mm的 钻头在R9.820 +0.08mm中心处钻穿丝孔φ3mm;正、反面孔口倒角; 钻头在R9.820 +0.08mm中心处钻穿丝孔φ3mm;正、反面孔口倒角; 攻螺纹4 M10;铰孔2 φ100+0.015mm。) 攻螺纹4-M10;铰孔2-φ100+0.015mm。) 07 铣削(平口钳装夹工件;用φ10mm的立铣刀铣削20 mm×70 mm的 铣削(平口钳装夹工件;用φ10mm的立铣刀铣削20 mm× mm的 型孔至尺寸,保证深度为13.2mm.) 型孔至尺寸,保证深度为13.2mm.) 08 热处理 (工件淬硬至HRC60~64HRC) (工件淬硬至HRC60~64HRC) 09 平磨(磨上、下两端面及相邻两侧基面,用90°角尺测量相邻两面 平磨(磨上、下两端面及相邻两侧基面,用90° 的垂直度;退磁) 10 线切割(按图编制线切割程序,切割凹模型孔形状,留单面研磨余 量0.005mm) 0.005mm) 11 钳工加工(研光线切割面) 12 检验
冲压模具开发验收移交程序(含表格)

冲压模具开发验收移交程序(IATF16949:2016/ISO9001-2015)1.0目的规范模具开发、验收、移交流程,定义各自的职责。
使模具能够满足公司持续稳定生产,缩短模具交期,提升公司效益。
2.0适用范围适用于本公司所需正常生产的所有模具。
3.0定义3.1模具分类定义3.1.1新项目所需制作模具:指根据客户新产品需求所制作的模具。
3.1.2生产所需制作备用模具:指目前已生产中的模具,由于模具寿命、模具缺陷或内部改进等方面原因提出的需求。
3.1.3客户或客户指定第三方移管模具:指根据客户要求,从客户处或客户指定的第三方供应商移交给公司生产的模具。
4.0权责4.1技术部(主要负责新项目模具及客户移管模具)4.1.1负责新项目产品开发的技术规格书及与供应商技术澄清及确定,模具申购及开发。
4.1.2负责产品内部技术的讨论及模具技术要求的制定。
4.1.3负责与模具供应商的技术沟通及设计方案的审核。
4.1.4负责模具开发制作过程的跟踪及监督(模具进度计划表)。
4.1.5参与组织确定合作模具供应商(依据供应商选择评分表)4.1.5负责组织模具的预验收、终验收、移交。
4.1.6负责内部试模及试生产工作的组织和协调。
4.1.7负责新模具图纸及所需备件的整理发行及移交。
4.1.8主导供应商培训内部模具维修人员模具维修保养工作,且填写培训记录表。
4.1.9负责模具的试生产评估并制定试生产报告依据制定模具生产产品作业操作指导书。
4.1.10参与备用模具开发的技术讨论及方案评估。
4.2采购部(负责所有外发模具的采购)4.2.1负责根据技术或生产部门提供的采购申请及技术要求,根据分类的合格供应商名录及技术部或运营部门的建议,联系供应商报价,并提供方案。
4.2.2负责组织确定合作供应商。
4.2.3负责模具价格、交期的最终确认以及合同的签订和订单的释放。
4.2.4负责商务、合同进度方面的沟通和跟踪。
4.3运营部(负责所有的模具的保管以及备用模具申请,主要负责备用模具)4.3.1负责备用模具的申请和开发。
冲压模具课程设计说明书 2
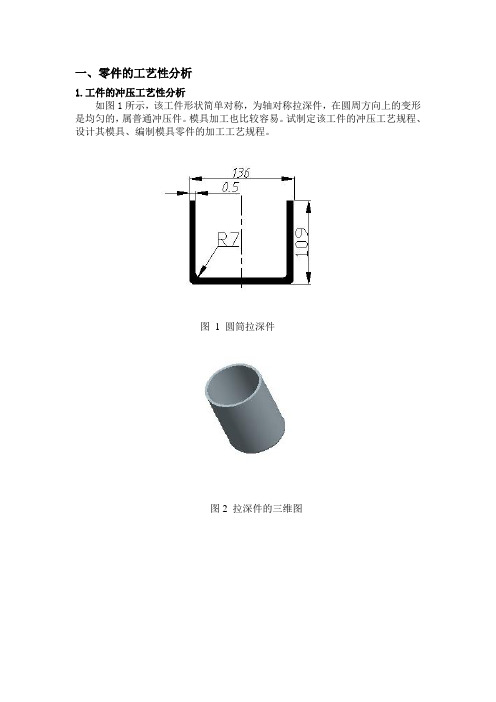
一、零件的工艺性分析1.工件的冲压工艺性分析如图1所示,该工件形状简单对称,为轴对称拉深件,在圆周方向上的变形是均匀的,属普通冲压件。
模具加工也比较容易。
试制定该工件的冲压工艺规程、设计其模具、编制模具零件的加工工艺规程。
图1 圆筒拉深件图2 拉深件的三维图2.工件材料化学成分和机械性能分析(1)材料分析工件的材料为08钢,属于优质碳素结构钢,优质沸腾钢,强度、硬度低,冷变形塑性很好,可深冲压加工,焊接性好。
成分偏析倾向大,时效敏感性大,故冷加工时应采用消除应力热处理或水韧处理,防止冷加工断裂。
08钢的主要机械性能如下:σ(兆帕) 280-390抗拉强度bσ(兆帕) 180屈服强度s抗剪强度(兆帕) 220-310延伸率δ 32%(2)结构分析工件为一窄凸缘筒形件,结构简单,圆角半径为r=7,厚度为t=0.5mm,满足筒形拉深件底部圆角半径大于一倍料厚的要求,因此,零件具有良好的结构工艺性。
(3)精度分析工件上尺寸均为未注公差尺寸,普通拉深即可达到零件的精度要求。
经上述分析,产品的材料性能符合冷冲压加工要求。
在零件工艺性分析的基础上制定其工艺路线如下:零件的生产包括落料、拉深(需计算确定拉深次数)、修边(采用机械加工)等工序,为了提高生产效率,可以考虑工序的复合,经比较决定采用落料与第一次拉深复合。
二、工件的拉深工艺分析及计算1.毛坯尺寸计算(1)计算原则相似原则:拉深前坯料的形状与拉深件断面形状相似;等面积原则:拉深前坯料面积与拉深件面积相等。
(2)计算方法由以上原则可知,旋转体拉深件采用圆形毛坯,其直径按面积相等的原则计算。
计算坯料尺寸时,先将拉深件划分为若干便于计算的简单几何体,分别求出其面积后相加,得拉深件总面积A。
图3 拉深件的坯料计算如图3所示,筒形件坯料尺寸,将圆筒件分成三个部分,每个部分面积分别为:(3)确定零件修边余量由于板料的各向异性和模具间隙不均等因素的影响,拉深后零件的边缘不整齐,甚至出现耳子,需在拉伸后进行修边。
冲压作业指导书

冲压作业指导书一、冲压工序作业流程1.材料受入2.上料(立式、卧式)3.过校平机(选用)4.模具的安装与调试5.入模6.试冲7.自检8.专检9.冲制10.入库名称冲压作业指导书编号YH-ZY-001-02 改定3/13二、原材料1.原材料的分类与废料的收集(1)原材料的分类:a.194#铜带:含铁量较高,冲裁废料可用吸铁石吸上,IC 系列产品使用;b.KFC#铜带:含铁量较低,冲裁废料无法用吸铁石吸上,TO —92,TO —126产品的使用;c.C1220#材料:可分为两种,一种是白板,一种是覆镍材料,TO —220系列,TO —3PH 产品的使用;d.42#铁镍合金材料:部分IC 产品及SOT —23B 、C 使用;e.黄铜带;TO —126、TO —92模具使用;(2)废料的收集:分类收集,不得相混,交原材料二级库称重收集。
2.原材料的搬运、安装:(1)搬运:为防止人员受伤及原材料受损,搬运原材料时要求两人以上,并采用叉车进行搬运。
搬动材料时手、脚不要置于材料下方,以免砸伤。
搬运材料时要小心轻放,着力点及叉车臂上要垫伤软性材料,以免发生材料受损,材料在搬运时要一人拉车,另一人需扶住材料以防材料脱落。
(2)安装:a.立式开卷:拆下开卷机承料盘前挡,将料撑直径缩至小于材料内径,呈倒三角行放置,料撑上要包上软材料,以免材料受损,用单臂叉车将材料小心放下,小心转动轮盘,使材料贴住承料盘后档,然后使料撑呈正三角形,转动调节杆,使料撑张开将材料撑住,加上前挡并锁紧。
b.卧式开卷:将材料用用双臂叉车平放叉出,拉至开卷平台,将材料一头小心搭在平台上,叉车略降,搬运者将材料小心搬至平台上,摆正位置;3.原材料的校平:先将较平机较平调节旋钮完全松开,剪一段待冲材料(1米左右),穿入较平机,调整校平调节旋钮,同时将材料沿进给垂直方向拖动,感觉材料状况,要求校平辊轮均匀压在材料上,校平后的材料以略向下卷为宜,其后可在生产中根据具体情况微调;4.原材料的领用、结转、退库:(1)原材料领用:原材料领用时,操作者必须进行核查称重,在与仓管员双方确认后领出。
冲压模具组模流程

冲压模具组模流程下面是更口语化的冲压模具组模流程:第一步:准备妥当模具选对:看你要冲的材料、尺寸、厚度,还有产量要求,挑个合适的冲床。
记得看看模具高不高,能不能塞进冲床的工作台下面。
清理干净:冲床上下台面擦得亮堂堂的,不要有脏东西。
模具底下的下模座也得平平整整,没有杂物。
第二步:开始拼装滑块抬高:先把冲床滑块升起来,然后慢慢降到最低点,用那个“一毫米一毫米降”的模式。
模柄对准:模具带模柄的话,对准模柄孔,降到最低点,让模柄紧紧卡在模座上。
没模柄的装法:没有模柄的模具,找个合适的位置放下,注意有废料孔的模具,千万不能堵住孔。
第三步:装组件脱料板装好:把脱料板里面的零件,比如脱料板入子、脱料板成形工件、引导针什么的,一一装进模板,用螺丝把脱料背板固定好。
下模板拼起来:把冲裁入子、成形入子、导料板等塞进模仁固定板,注意冲裁入子的刀口朝上,活动的零件(比如浮料销)要能灵活动,废料要能顺利出去,脱料板和下模板要贴得严实。
上模板拼上:把冲子固定板入子、冲子装到上模板,用压板压紧。
记住,冲子的高度不能超过模面。
第四步:合模检查没弹簧先试试:先把上下模贴在一起,看看冲子和剥料板的位置对不对,下模板和成形冲子会不会打架,主导柱有没有冒出来。
看看平行不:通过模板间的缝隙,判断上下模是不是平行。
如果需要,用AB胶或者快干胶把主导柱粘牢,让它比上模座低个几毫米。
第五步:装剥料板零件归位:把剥料板入子、导向销、剥料板成形工件、剥料套(推料杆)等装进剥料板。
注意剥料板入子不能太高,剥料板背板要能挡住入子、成形工件往后跑。
第六步:胶水加固下模涂胶:用定位销把下模板和下模座对准,用螺丝拧紧,然后在它们之间的灌胶PIN 上涂上680胶,粘得牢牢的。
上模也涂胶:通过付导柱把上模板和下模板对准,保持平行,用螺丝拧紧,再涂上680胶,粘住上模板和上模座。
第七步:最后检查与调试全面复查:再看看所有的零件都装好了吗,螺丝都拧紧了吗,活动的部分能不能自由活动。
冲压模具装配工艺

第五章模具装配工艺第一节装配尺寸链一、装配尺寸链的概念装配的精度要求,与影响该精度的尺寸构成的尺寸链,称为装配尺寸链。
如图5-1a所示,为落料冲模的工作部分,装配时,要求保证凸、凹模冲裁间隙。
Z/2 一-*工门a)图5-1凸、凹模的冲裁间隙根据相关尺寸绘出尺寸链图,如图5-1b所示。
二、用极值法解装配尺寸链与工艺尺寸链的极值解法相类似。
以图5-1所示落料冲模为例。
解:A1为增环,A2为减环计算封闭的基本尺寸m _ n -1 .A、= Z = A i-為A i二29.74「29 .64 二0.10 (mm )i =1 i +计算封闭环的上、下偏差m _ n」-ESA ESA i - ' El Aj = 0.024 -(-0.016 )= 0.04 (mm )i 亠i h +n」二ESA =0i h ""1求出冲裁间隙的尺寸及偏差为0.10 o"40mm,能满足Z min 二0.10mm , Z max =0.14 mm。
第二节装配方法及其应用范围一、互换装配法1•完全互换法(1)在装配时各配合零件不经修理、选择和调整即可达到装配的精度要求。
n」T\ T2 匚丄=、T ii 二(2)特点装配简单,对工人技术要求不高,装配质量稳定,易于流水作业,生产率高,产品维修方便;但其零件加工困难。
试用范围广。
2•不完全互换法按Tv二..'、T2确定装配尺寸链中各组成零件的尺寸公差,可使尺寸\ 7链政治中个组成环的公差增大,使产品加工容易和经济,但将有0.27%的零件不合格。
适用于成批和大量生产二、分组装配法1 •在成批和大量生产中,将产品各配合副的零件按实测尺寸分组,装配时按组进行呼唤装配以达到装配精度的方法。
先将零件的制造公差扩大数倍,按经济精度进行加工,然后将加工出来的零件按扩大前的公差大小分组进行装配。
2 .特点1)每组配合尺寸的公差要相等,以保证分组后各组的配合精度和配合性质都能达到原来的设计要求。
《冲压工艺与模具设计》课程标准
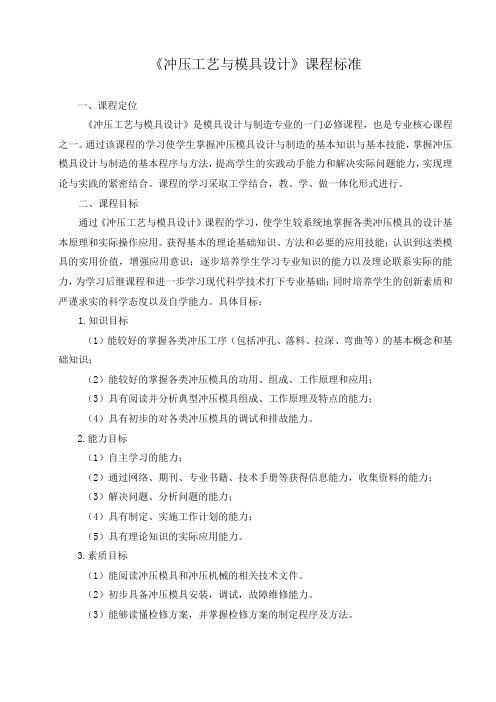
《冲压工艺与模具设计》课程标准一、课程定位《冲压工艺与模具设计》是模具设计与制造专业的一门必修课程,也是专业核心课程之一。
通过该课程的学习使学生掌握冲压模具设计与制造的基本知识与基本技能,掌握冲压模具设计与制造的基本程序与方法,提高学生的实践动手能力和解决实际问题能力,实现理论与实践的紧密结合。
课程的学习采取工学结合,教、学、做一体化形式进行。
二、课程目标通过《冲压工艺与模具设计》课程的学习,使学生较系统地掌握各类冲压模具的设计基本原理和实际操作应用。
获得基本的理论基础知识、方法和必要的应用技能;认识到这类模具的实用价值,增强应用意识;逐步培养学生学习专业知识的能力以及理论联系实际的能力,为学习后继课程和进一步学习现代科学技术打下专业基础;同时培养学生的创新素质和严谨求实的科学态度以及自学能力。
具体目标:1.知识目标(1)能较好的掌握各类冲压工序(包括冲孔、落料、拉深、弯曲等)的基本概念和基础知识;(2)能较好的掌握各类冲压模具的功用、组成、工作原理和应用;(3)具有阅读并分析典型冲压模具组成、工作原理及特点的能力;(4)具有初步的对各类冲压模具的调试和排故能力。
2.能力目标(1)自主学习的能力;(2)通过网络、期刊、专业书籍、技术手册等获得信息能力,收集资料的能力;(3)解决问题、分析问题的能力;(4)具有制定、实施工作计划的能力;(5)具有理论知识的实际应用能力。
3.素质目标(1)能阅读冲压模具和冲压机械的相关技术文件。
(2)初步具备冲压模具安装,调试,故障维修能力。
(3)能够读懂检修方案,并掌握检修方案的制定程序及方法。
(4)根据典型冲压模具装配的训练,掌握零件装配的基本方法及技巧。
(5)持续学习,不断更新科学知识,提高技术水平。
(6)培养学生勤于思考、认真工作的良好作风。
三、课程设计1.设计思想(1)坚持以高职教育培养目标为依据,基于本课程在化机类专业知识、能力构筑中的位置及这门技术的特点,突出应用能力和综合素质培养,充分注意“教、学、做”三结合。
冲压模具组立步骤
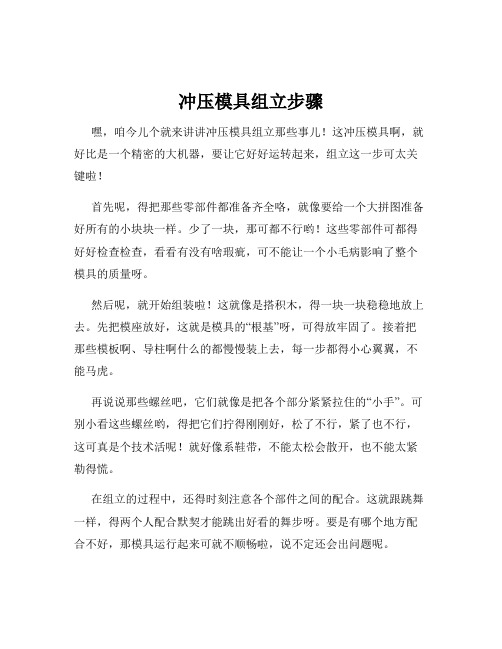
冲压模具组立步骤嘿,咱今儿个就来讲讲冲压模具组立那些事儿!这冲压模具啊,就好比是一个精密的大机器,要让它好好运转起来,组立这一步可太关键啦!首先呢,得把那些零部件都准备齐全咯,就像要给一个大拼图准备好所有的小块块一样。
少了一块,那可都不行哟!这些零部件可都得好好检查检查,看看有没有啥瑕疵,可不能让一个小毛病影响了整个模具的质量呀。
然后呢,就开始组装啦!这就像是搭积木,得一块一块稳稳地放上去。
先把模座放好,这就是模具的“根基”呀,可得放牢固了。
接着把那些模板啊、导柱啊什么的都慢慢装上去,每一步都得小心翼翼,不能马虎。
再说说那些螺丝吧,它们就像是把各个部分紧紧拉住的“小手”。
可别小看这些螺丝哟,得把它们拧得刚刚好,松了不行,紧了也不行,这可真是个技术活呢!就好像系鞋带,不能太松会散开,也不能太紧勒得慌。
在组立的过程中,还得时刻注意各个部件之间的配合。
这就跟跳舞一样,得两个人配合默契才能跳出好看的舞步呀。
要是有哪个地方配合不好,那模具运行起来可就不顺畅啦,说不定还会出问题呢。
还有啊,组立的时候得有耐心,不能着急。
就像绣花一样,得一针一线慢慢地来。
要是着急忙慌的,很可能就会出错,那可就得不偿失啦。
等模具组立得差不多了,还得再仔细检查检查。
这就像是考试完了要检查一遍试卷一样,看看有没有遗漏的地方,有没有没装好的地方。
只有经过这样认真的检查,才能保证模具能正常工作呀。
你想想,要是模具没组立好,那生产出来的东西能合格吗?那肯定不行呀!所以说呀,冲压模具组立这事儿可太重要啦,绝对不能马虎对待哟!咱可得把这个大机器组装得稳稳当当的,让它为我们好好工作,生产出高质量的产品来!这就是冲压模具组立的步骤,你记住了吗?。
模具制造过程管理程序

模具制造过程管理程序1.目的为了使本公司所有模具能有计划,按秩序的进行,确保模具质量与客户交期,特制定此制度.2.适用范围公司内部所有模具制造过程:包括采购、加工、组立、试模和品管检测计划进度管控。
3.定义3.1各部门以接受到设计图纸,工艺卡开始为制造过程。
3.2 模具制造过程包括:采购购料,制造一部加工,制造二部组装调试,品质检查,PMC进度管理。
4.职责与权限4。
1 PMC职责PMC按照《冲压模具制作确认传达书》《生产指令书》《冲压件需求单》安排各相关部门进行检讨,制定出时间然后根据检讨时间制定出公司《冲压模具制作计划排程》并下发到各个部门,开始设计。
客户确认后根据实际情况(客户还是自己延误)重新制定制造排程计划,各部门按照此计划开始运行,PMC负责监督汇报各部门计划达成状况。
遇到未达成计划PMC有权力召集各部门检讨及提出处罚。
对于严重延误直接上报总经理。
(此流程也使用与产品设变)4。
2生产计划实施4。
2。
1设计部依据《冲压模具制作计划排程、制作确认传达书》中所拟定的工作进度,进行模具设计作业,内部结构确认后第一时间先排出《海益五金模具物料清单》时间给采购部,优先购料。
4.2.2采购计划的实施采购按照设计部排出的《五金模具物料清单》和零、配件加工图并依据《模具制作计划排程生产指令表》进行采购作业。
采购必须与供应商确认交期满足《模具制作计划排程生产指令表》上规定的时间。
遇到未达成或达成不了情况,召集汇报公司总经办商讨,重新制定解决方案来确保纳期。
4.2。
3加工部门加工计划实施4。
2。
3。
1 CNC加工:按照工件流程(图纸上附有工艺说明)4.2。
3。
1。
1 CNC加工部接到制二部加工物料及盖有生管章加工工艺图纸转到制一部CNC加工区.4.2。
3。
1。
2制一部CNC编程员按照工件工艺图纸,从设计部共用文件夹tooling里调取与图纸日期相同模号,相同编码进行编制,按照《编程标准文件》进行操作。
4.2。
冲压模具管理程序(含表格)

冲压模具管理程序(IATF16949-2016/ISO9001-2015)1.0目的冲压模具是汽车车身生产中不可缺少的特殊工装,模具的合理使用、维护、保养与管理对延长模具使用寿命、降低冲压件成本、提高制件质量、改善模具的技术状态至关重要,是保证冲压正常生产的一项重要工作。
2.0适用范围本文件适用于冲压厂所有模具。
3.0术语及定义无4.0职责4.1装备动力部工装科是模具的归口管理部门4.2冲压工艺科负责拟定《模具调整卡》。
4.3冲压工艺科负责模具的改进涉及到产品设计更改,由冲压工艺科提出设计更改申请,报研发部评审确认后进行相关产品设计文件的更改。
4.4负责本厂无能力维修的模具异常问题,由冲压厂技质科上报冲压工艺科,冲压工艺科及时制定维修方案并组织外协维修。
4.5模具保全负责组织已交付使用模具的维修,并填写《模具维修记录》,每月制模具维修计划,模具维修人员依据模具维修计划对模具进行改动和主动维修。
4.6模具保全负责组织已交付使用模具的保养,严格按照《模具保养计划》执行,保养模具过程中发现问题及时维修,并填写《模具维修记录》。
4.7模具保全负责模具易损件库存量的管理,采购模具标准件及外协维修制件质量的检验,包括材质、尺寸规格、表面硬度、表面粗糙度等技术指标的检验;临时加工件由维修人员协助按相应技术标准进行验收。
4.8模具保全负责监督对模具使用部门的正确使用的管理权,对违规使用情况给予警告纠正或通报处罚。
4.9各生产班组负责执行《模具调整卡》要求,确保模具正常使用。
4.10各生产班组负责模具使用前、使用中、使用后的点检,并如实填写《模具点检表》,发现异常及时联系模具维修人员,异常处置完毕后方可正常生产。
4.11各生产班组负责模具使用后的存储管理,清理模具上下表面料豆油污,清理模具尘土杂物,确保模具放置区卫生。
5.0工作程序5.1冲压模具管理规定工作流程图:见附件。
5.2模具的使用依据《模具调整卡》设定相关参数执行。
冲压模具制造流程

冲压模具制造流程冲压模具,是在冷冲压加工中,将材料(金属或非金属)加工成零件(或半成品)的一种特殊工艺装备,称为冷冲压模具(俗称冷冲模)。
冲压模具的制造流程是什么。
以下是店铺为大家整理的关于冲压模具制造流程,给大家作为参考,欢迎阅读!冲压模具制造流程l 、升图和制造工艺模型:根据零件图对其各部尺寸按锌合金线收缩系数定向放缩尺,并设计浇冒口和冷铁。
所以绘制出模型工艺图,根据此图加工制造工艺模型。
2、凸模模形制造:按照模型工艺图提供的各项尺寸,选用优质木材制作凸模模型。
模型的尺寸精度要求达到木模二级精度。
木模表面涂刷漆片使表面粗糙度Rz值小于10μm 。
拔模斜度取士1 °。
3 、凹模模型制造:凹模制造是在凸模工作表面上贴上一层与产品零件厚度相等的铅皮,以制出凸、四之间的间隙。
应对凸模铅皮表面进行喷漆,以使铸后的凹模型面的粗糙度数值小。
凹模模型采用熟石膏制造。
为了凸、凹模模型在浇铸石膏时便于分开,应在分模面上喷涂一层脱模剂(如聚苯乙烯的甲苯溶液)。
浇铸后,应将石膏凹模模型进行千燥,之后再,进行脱模。
应对型腔表面及分模面进行喷漆。
4、造型。
选用强度高、颗粒较细的型砂作为造型材料。
因为锌合金浇铸温度比较低,对型砂的耐火性和透气性要求不高。
对凸模和凹模分别进行造型,可以选用砂箱造型或地坑造型等造型方法。
按模具的要求,浇铸系统采用底注式或敞开式。
由于锌合金收缩系数较大,应设补缩冒口。
5 、锌合金熔化6 、浇铸:对于中、小型模具可以采用干型浇铸,也可以.采用涅型浇铸。
涅型浇铸的排气孔应多些。
浇铸锌合金时,应使合金液流缓慢而平稳地注入型腔。
对于大型模具,为了防止或减少模具型腔变形,浇铸时可以在型腔周围设置冷却水管或加冷铁,保证液态合金的顺序凝固。
7 、锌合金模具铸件的冷却、清理和修饰:浇铸后的模具铸件一般采用自然冷却,但对形状简单的小型模具铸件也可以采用水冷的方法进行冷却,这样有利于合金机械性能的提高。
冲压模具设计与制造规范

冲压模具设计与制造规范一.目的:统一公司模具设计规范,更好地配合加工单位,适应快速作业的需要。
二.范围:适用于本公司所有部门之作业。
三.权责:由各个部门编写文件之人员负责执行此规范。
四.内容:1.开模前相关作业程序:1-1 程序说明:新项目提出开模时,模具工程师必须先向业务或此项目负责人确认此项目预估的量能会有多少,之后再依照此量能特性加以分析,以最快速、经济、合理之要求达成最佳化冲压模具状态,以确保后续之量产能力。
模具开发前期制作冲压模具工程设计制作分析,此分析用意在于预见模具开发可能产生之问题点,将其整理以及早发现及早修正的形态为目的,其次安排各工程图面的合理性(包含单工程模具工程图面以及连续模料带图面)、考虑模具结构设计的安全以及正确性……等,另外依照评估后模具形式决定模具材质以及热处理特性,再规范定义各配件的使用时机,明确规划出最佳化模具的形式。
在模具制作期间,模具开发进度的掌控往往是造成一个新的项目是否有办法如期成行的一个重要症结点。
试模时实际的状况记录于试模检讨记录中,藉由实际的问题记录以及改善确认方式此套新开发的模具运行无误有量产能力,最后确认每个单件皆符合RD所设计的规范要求后,签认模具移交单以做模具验收的标准,而针对以上叙述以下用流程图加以说明:冲压模具级数及作业分类原则Design For Manufacture Report工程图以带图面确定工程模:各工程工序图连续模:料带图模具确定各工程模具结构图模具开发进度掌控模具开发进度表试模检讨改善记录FAI Report & Cpk Report模具确认模具验收办法2. 冲压模具级数、寿命定义及模具组织架构:2-1 冲压模具级数定义:各类冲压模具依照不同程度产能之要求,定义出三种级数冲压模具结构尺寸以及相关规定之设计形态,分别为每个月产能在50K以下少量产能型态的模具(定义为一般产能模具)50K~100K之间中产能型态之模具(定义为中产能模具)以及每个月100K以上产量之模具(定义为高产能模具),定义各级数产能模具如下表所示:由于模具在冲压过程中有一定的磨损、变形,为了保证产品的质量,冲压一定次数后就必须有一次模具保养,根据本厂内多年的现场统计,总结模具保养规律如下:2-3 冲压模具结构分类:冲压类模具可分为下料形式、冲孔形式、折弯形式、连续模具等,其模具结构、板材尺寸、模具材质规范如以下所示。
如何利用Proe设计冲压模具
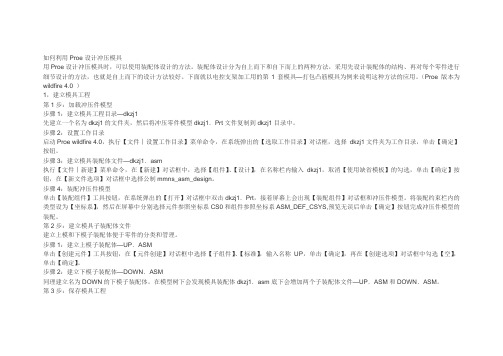
如何利用Proe设计冲压模具用Proe设计冲压模具时,可以使用装配体设计的方法。
装配体设计分为自上而下和自下而上的两种方法,采用先设计装配体的结构、再对每个零件进行细节设计的方法,也就是自上而下的设计方法较好。
下面就以电控支架加工用的第1套模具—打包凸筋模具为例来说明这种方法的应用。
(Proe 版本为wildfire 4.0 )1,建立模具工程第1步:加载冲压件模型步骤1:建立模具工程目录—dkzj1先建立一个名为dkzj1的文件夹,然后将冲压零件模型dkzj1.Prt文件复制到dkzj1目录中。
步骤2:设置工作目录启动Proe wildfire 4.0,执行【文件︱设置工作目录】菜单命令,在系统弹出的【选取工作目录】对话框,选择dkzj1文件夹为工作目录,单击【确定】按钮。
步骤3:建立模具装配体文件—dkzj1.asm执行【文件︱新建】菜单命令,在【新建】对话框中,选择【组件】、【设计】,在名称栏内输入dkzj1,取消【使用缺省模板】的勾选,单击【确定】按钮,在【新文件选项】对话框中选择公制mmns_asm_design。
步骤4:装配冲压件模型单击【装配组件】工具按钮,在系统弹出的【打开】对话框中双击dkzj1.Prt,接着屏幕上会出现【装配组件】对话框和冲压件模型。
将装配约束栏内的类型设为【坐标系】,然后在屏幕中分别选择元件参照坐标系CS0和组件参照坐标系ASM_DEF_CSYS,预览无误后单击【确定】按钮完成冲压件模型的装配。
第2步:建立模具子装配体文件建立上模和下模子装配体便于零件的分类和管理。
步骤1:建立上模子装配体—UP.ASM单击【创建元件】工具按钮,在【元件创建】对话框中选择【子组件】、【标准】,输入名称UP,单击【确定】,再在【创建选项】对话框中勾选【空】,单击【确定】。
步骤2:建立下模子装配体—DOWN.ASM同理建立名为DOWN的下模子装配体。
在模型树下会发现模具装配体dkzj1.asm底下会增加两个子装配体文件—UP.ASM和DOWN.ASM。
模具组立作业指导书

6.2.5安装主导柱(针对外购模座以外)
6.2.5.1将下模座单独平放于钳工桌面的垫布上
6.2.5.2主导柱配合孔内壁,涂上润滑脂,将冷冻的主导柱(提前24H进行冷冻,主导柱和副导柱分别以布包上,防止结霜)取一支且擦拭干净,注意手用布拿据持区,勿摸配合区以免导柱热膨胀,先用手将主导柱压入配合孔,调整与下模座模面垂直。
6.2.5.3用铜棒垂直敲入至台肩距模面约8MM处
6.2.5.4手握抬模螺栓,空起下模座模板底部对应主导柱孔上安装锁紧垫圈及螺栓,将主导柱拉至台肩与模面紧密接触,其余以同样方法安装
6.2.6安装副导柱
6.2.6.1将脱料板/夹板用垫块垫起,反面/反面朝上,垫块间距不要太大,以免敲击导柱模板变形。
6.2.6.2副导柱配合的孔以清洁布擦拭干净后,在内壁涂上牛油,取冷冻的副导柱一支擦干净,用布包手副导柱压入配合孔,调整垂直度,用铜棒敲入,不可高出模板正面,其余安装方法相同,装好扣用M6螺丝锁紧
6.2.2.3螺纹孔实配,牙孔有无锁不顺畅的。
6.2.2.4是否有漏加工
6.2.2.5如以上检查有品质异常,第一点因加工造成要及时联络加工单位返修,并填写品质异常联络单;第二点因图面错误造成,则及时通知设计修改图面,返修或重制。以上问题点记录于《组模报告》中。
6.2.3模板和工件钳工作业
6.2.3.1将所有工件模板进行去磁
6.2.3.2将所有工件进行选择性倒角、抛光
A.模板
a:作业之前,应先将干净的布铺于钳工桌上,以防止模板遭铁屑\铜屑刮伤
b:模板周边棱角倒角为C2.5且去掉毛刺,抛光压平触摸感觉光滑
c:脱背板正面和镶件正面要用合金笔头进行倒角
冲压模具结构基础知识
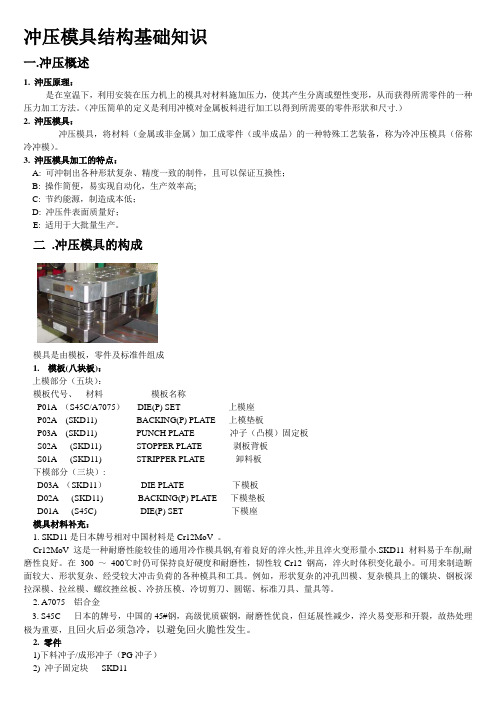
五.模具中最基本数值常识
1.冲子(凸模)长度L = P03A+S02A+S01A+1.0
P03A?
P01A=50.0 / 55 .0 mm
P02A=13.000 mm
P03A=18.000mm
S02A=10.950 mm
S01A=20.000mm
D03A=20.000 mm
S01A (SKD11) STRIPPER PLATE卸料板
下模部分(三块):
D03A(SKD11)DIE PLATE下模板
D02A (SKD11) BACKING(P) PLATE下模垫板
D01A (S45C)DIE(P) SET下模座
模具材料补充:
1. SKD11是日本牌号相对中国材料是Cr12MoV。
5.方便修模设计
方便移位修正尺寸
三、折弯工站设计技巧
1.折弯零件强度的合理性(折弯凸凹模)
先压料后成形
2.考量零件的加工性能(折弯凸凹模):设计的零件便于加工,能用磨床研磨的就不要线割,磨床研磨加工比线切割或电火花放电加工效率高的多
3.方便修模设计:研磨后仍可保证不影响折弯成形
4.保持折弯稳定性
尽可能在料带连接强度好的情况下折弯成形,保证有足够的压料
利用千分表量测,將手壓在模板另一端,運用變形支點原理,觀察另一端千分錶刻度是否有變化来量测模板有否翘曲,正反面以及四个对角点均要量测,模板的變形及翘曲量一般不超过0.003mm
7-3模板累計誤差测量:
将模板組合在一起用千分表测量模板翘曲及平行度,并将六組以上的数据計录下来,理輪上要求變形量不超过0.016 mm(提示:测量时整个面不能低于六点)
冲压模具生产工艺流程

冲压模具生产工艺流程冲压模具,是在冷冲压加工中,将材料(金属或非金属)加工成零件(或半成品)的一种特殊工艺装备,称为冷冲压模具(俗称冷冲模)。
小编给大家整理了关于冲压模具生产工艺流程,希望你们喜欢!冲压模具生产工艺流程五金冲压模具制作流程一.毛胚材料加工:1.铣六面对角尺(垂直度误差不大于0.1/300),同一付模具材料长宽尺寸一致即可,厚度留0.2mm磨量(需淬火件留0.5mm磨量);棱边倒角。
2.磨上下两平面,(需淬火工件留0.3mm)二.机加工:1.根据图纸分别钻、攻各螺钉牙孔及过孔以及穿丝孔等;2.铣各漏料孔或成形部分;3.热处理后,工件需磨上下两平面及基准边;4.车加工各回转件,公差按图要求。
☆☆所有销钉孔都不能先加工:需热处理的钻穿丝孔,其余都在装配是配钻、铰三.线割:按图纸规定的配合要求线割各个成型部分。
导柱、导套与模架紧配合;冲头与固定板过渡配合;销钉与各孔均为过渡配合。
四.装配:1.先按图装配模架,确保导柱、导套与模架垂直并运动顺畅;2.在模架上先固定凹模,按图纸给定间隙将相应厚度的铜皮均匀地放在凹模周边,再装入凸模,试冲纸片确定四周毛刺均匀后,紧固凸、凹模并配打销钉。
(如果是复合模,还需对好冲头间隙再固定凸、凹模)。
3.之后再装好卸料及顶出机构五.模具整体加工顺序:1.优先加工需要热处理的工件2.其次加工.需要线切割的工件3.然后加工模架部件即上托和底座4.再后加工其它部件。
5.装配、试模五金冲压模具的分类按完成工序的性质分类,包括冲裁模、弯曲模、拉深模等;按工序的组合程度分类,包括单工序模、级进模、复合模等;按自动化程度分类,包括全自动模、半自动模、手动模;按模具材料分类,包括聚氨酯橡胶模、钢模等;看你从哪个角度说。
如果是按第一种分类,具体包括冲孔模、落料模、切边摸、切断模、剖切模、整修模、切舌模、弯曲模、拉弯模、拉伸模、卷圆模、胀形模、翻边模、翻孔模、缩口模、扩口模、整形模、校平模、精冲模等。
冲压模具管理的讲义

3-1-1功能----衝切、彎曲成形、引伸,調整
3-1-2固定方式
沖子背 板
a.帶肩沖頭
b.填隙固定式
c.螺絲固定式 d.樹脂固定式
壓
入
a
沖子固定板
b
c
d
e.定位銷固定式
f.沖小孔沖頭固定式
e
f
g. A-type結構最常見的沖子固定方式 (重點學習)
5.000mm
剝料板入子孔
定位針孔0.003-0.005/side﹐ 作用﹕加工過程中﹐ 使料條定位(時間﹕約 1/1000秒)﹐然后加工。
S01A主要功能為﹕壓料﹐將料條自沖頭的周邊剝離,不使其黏附於沖頭 隨之升起,及緊密地導引著細小的沖頭以防止其被折斷﹐導正衝子。
上下模的模攤運動:
• 2.衝壓模各模板精度
模具工程分析
一 .客 戶 的 指 定 1 .產 量 的 考 慮 。 2 .單 工 程 。 3 .R O B O T 生 產 。 4 .連 續 模 。
二 .廠 內 的 考 量 1 .機 台 噸 數 。 2 .生 產 線 的 安 排 。 3 .人 數 的 需 求 。 4 .每 一 工 程 C y c le T im e
是否平均。
三 .分 析 工 程 的 原 則 1. 先 下 料 外 形 。 2. 沖 內 孔 。 3. 再 折 彎 , 後 成 型 。 4. 折 彎 是 由 外 向 內 折 曲 。 5. 同 一 方 向 可 同 時 折 彎 。
四 .影 響 分 析 之 原 因 1 . 孔 與 孔 的 間 距 是 否 太 近 (模 具 強 度 ) 。 2 . 孔 離 折 彎 邊 是 否 太 近 (易 造 成 拉 料 ) 。 3 . 沖 壓 的 穩 定 性 (折 單 邊 易 產 生 拉 力 不 均 ) 。 4 . 脫 料 是 否 困 難 (沒 空 間 放 彈 簧 ) 。 5 . 如 抽 引 會 造 成 外 形 拉 料 (就 需 考 慮 先 引 伸 再 下 外 形 ) 。
冲压模具组立试模流程
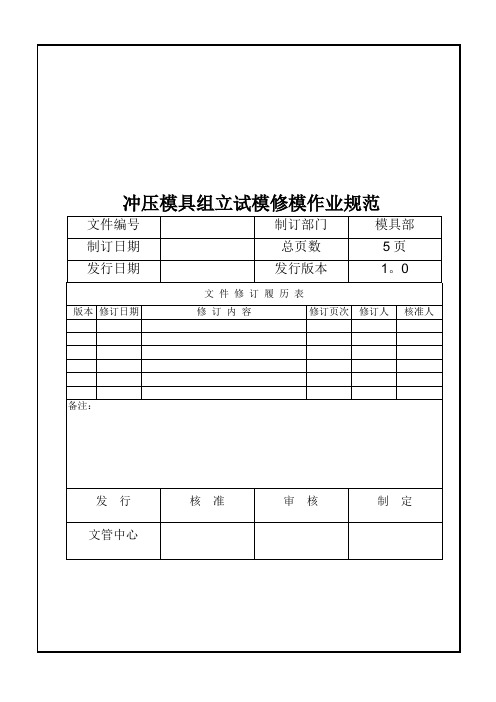
5.4. 样品生产与量测
5。4。1. 样品生产:手工送料或自动送料生产出所需数量的尺寸,外观,功能,装配性均
OK 的样品;
5.4.2. 样品量测:依据产品蓝图量测样品尺寸和功能参数,并填写自主检验记录。
最后,将样品,自主检验记录,组立试模报告,修正后的模具图面一并交设计工程 师。
5.5.总结。
每次每套新模组立试模完毕后,由责任模具组立工程师,根据记录之《试模组立试模报告》 及修正图面。
5。1。3)模具零件的查检,包括模板﹑工件的形状﹑尺寸﹑材质硬度是否与图面一致。
5。1.4) 标准件领用:标准冲子﹑主导柱整组,付导柱整组,灌胶,等高套筒,压板,弹簧,
定位销,引导针,合销,垫片,螺丝等。
5。1.5) 打磨并清理模板,去除模板表面以及框口内的铁屑和杂物,测量模板厚度尺寸, 使用风磨机将尺寸刻在模板侧面。
2、范围:适用于公司所有冲压新模具.
3、定义:无
4、职责:设计工程师:提供新模之产品图、模具零件图,并提供技术指导。
模具师傅:按照规范高精度,高质量的完成模具组立及试模。
5、作业流程:
5.1。准备工作
5。1.1)设计工程师切入:提供产品图 ﹑模具零件图,并提供技朮指导。
5.1。2)模具零件的整理与清点,根据模具零件清单,责任模具组立人员进行模具零件清 点。模具零件清点时,注意保护零件刀口不受碰撞受损。
6、附表:
6。1.附表 1:新模组立试模报告
5。3。1.2. 将模具各调整滑块调至最外面,以免打坏模具;
5.3.1。3。 试模机台的选用:考虑参数为吨位,精度,行程,工作面大小,落料孔大小,架
模高度,调机难易等.
5。3。2。模具试模
5。3.2.1. 架模:确保冲床工作台面和模座面上无废屑等杂物;模具应处于工作台面中心 并平行于工作台面;模具与冲床工作台面和上滑块紧固应该牢靠;同时将闭合 高度调间隙 0~0.05mm。
- 1、下载文档前请自行甄别文档内容的完整性,平台不提供额外的编辑、内容补充、找答案等附加服务。
- 2、"仅部分预览"的文档,不可在线预览部分如存在完整性等问题,可反馈申请退款(可完整预览的文档不适用该条件!)。
- 3、如文档侵犯您的权益,请联系客服反馈,我们会尽快为您处理(人工客服工作时间:9:00-18:30)。
冲压模具组模程序
一依图纸清理零件
1.清查零件,防止零件与图纸不符合。
2.线割件与标准件须研磨加工,用零件盒区分。
3.细小工件与大型工件分开装,防止损坏。
4.将清点好的零件进行合理倒角
二依图纸清理模板
1.测量模板厚度是否在图纸尺寸范围之内。
2.测量模板平行度,分别测量各板前后左右6个点是否在±0.002以内。
3.模板垂直度检验,千分表测量其上下偏听偏差是否在±0.002内。
4. 将模板上(定位销孔.过孔.导料板让位处.副导套孔.弹簧过孔.零件敲击孔)进行圆滑倒角(先用砂轮打磨头倒角.再用牛皮打磨头抛光)
5. 模板表面用800-1000号砂纸推平(将号砂包在指丁的模板推块上)
6. 模板表面推平后再用纤维油石将框口内线割氧化层去除.
7. 用去污油把模板清洗干净(最好用纸将清洗过的模板表面轻轻抹一遍.再用气枪吹去纸屑或布屑).试配合销间隙.
三导柱,导套组装
1.清洁导柱,导套,加油试配,如较紧,则检查是否偏心。
2.清洁模板导套,将外沿涂上润滑油(或机油),对准孔沿,轻轻装入。
3.导套装好后,用辅助导柱插入导套是否滑配。
4.夹板反转,正面向上,清洁干净内孔,导柱螺牙端涂上机,轻轻装入夹板。
5.用千分表检查导柱的垂直度。
6.将夹板,脱料板,下模板脱磁后三块叠合在一起,拉动导柱,是否顺畅。
四零件组装
(一)下模
1.研磨后的工件用分厘卡检查,将入块外围分别试配,可以插入则把入块外
沿用600#以上油石倒圆滑。
2.清理干净入块内孔,将模板反转,底面朝上,入块脱磁后,刀口方向朝下,
对应装入模板。
3.用细红铜棒轻轻敲入,发现较紧,退出检查原因。
4.入块两端或一端高出模板时,应检查入块,还是模板孔的垂直度是否偏差。
5.成型入块应抛光后装入。
6.没有防呆方向的入块应对照图纸进行确认检查。
7.浮升梢在模板内是否顺畅,如太紧,则检查浮升梢,还是浮升梢孔的尺寸
不符。
(二)夹板
1.依下模板类似方法,入块可以正,反面装入。
2.冲子压板在压着冲头的同时,应留有0.02-0.05mm的松动。
3.冲子压板的螺丝以M4*10L为宜。
4.成型冲头和下料冲头应核查好长度。
(下料冲头总长为基本冲高加3个冲
材厚小冲子加2个冲材厚)
(三)脱料板
1.入块从上往下装入。
2.脱料板入块,挂台应比图纸尺寸小0.01-0.05mm,避免入块装入时不平。
3.引导针装入时,切勿太松或太紧,太松易造成定位不准.太紧会造成引导
针变形.
4.入块底面与脱料板料槽底平齐。
五模板组配
1.先将三块主板按顺序叠放在一起.打入合销.试配所有下料冲及成型冲是否顺畅.
2.若试配OK后.再将所有镶件取出.以免影响导套灌胶时受力不均.
3.将冰好的内导柱敲入脱料板对应孔内.(注意敲入前要在导柱孔内加机油或黄油).再将其它两块主板依次放整齐敲入合销.用0.01厚的间隔隙片检测模板间是否间隙过大(0.01垫片感觉有阻力即为合格状态).
4.将剪好的纸圈放入要灌胶的槽内,然后将打粗糙的导套与滚珠视套以最合理的高度配入导套孔内。
确认OK后将导套旋转提起约即将脱离模板为宜滴入680胶水均匀旋转导套使胶水充分进入。
5.灌完一面约过5分钟可将模板反过一面以同理灌胶(最后用黄油将灌胶处密封)再用“C”型夹将模板两头均匀夹紧待胶水凝固10-12小时后方可拆掉“C”型夹
(一)下模座组立
用600#油石清理下模座,将定位好的下模板和下垫板装入下模座,用M8的螺丝固定。
六模座组立
(二)上模座组立
1.将脱料板,脱背板与夹板,下垫板组合在一起,检查四块板之间有无空隙
和阻碍。
2.将四块板装在下模座上,检查6块板有无间隙和阻碍后,把上模座盖上,
用M8的螺丝锁紧。
3.合模,闭模均顺畅后,装上等高套筒,锁上脱料板固定螺丝,
4.上模座固定螺丝核好弹簧压缩量后,装入φ22绿色(或棕色)弹簧,锁
好上盖板,检查闭合情况。
(三)查所有板的也是位配合是否正常。
倒角:倒角包括:
1.模板处围。
2.导料板进退之入口。
3.脱料板冲子入口。
4.固定销孔入口。
5.浮升销,所倒角面须光滑平整。
六合模
1.拆出所有弹簧。
2.检查所有模板,零件,用去渍油清洁干净。
3.将所有导柱,导套,刀口与冲子抹上机油。
4.装好所有模板,零件,顶料梢,浮升梢。
检查各梢是否顺畅。
5.合好上下模,等待试模。