铣刀的热处理生产设计
硬质合金焊接铣刀的热处理技术改进

法。这种制作方法 对刀 体强 度要求 不高 的铣 刀是 可行
的 ,但对于切削速度高 ,切削力大 ,尤其是刀体截面 积 较小的刀具就不能取得满意的效果。 我厂生产 的 B 29机床 ,用户 订货时要求我厂提供 7 配套的专用刀具如 : 72 、R75槽铣刀 ( 图 1 ;l .5 . 见 )
图 8 试验 刀体淬火后的金相组织 ( 0 ) ×50
卫
图 6 试验铣刀
对试验 刀体先进行 淬火 ,工 艺为 80 3 %加 热 3 m n 0i 油冷却 ,2 0 回火 9 m n 0% 0 i,其热处 理工艺 曲线 见 图 7 。 试验刀体经淬火 后 的金 相组织 为 马 氏体 +少量 铁素 体 ( 见图 8 ,对其测试硬度为 5 5 H C ( ) 2 4 R 见表 1 。在淬 )
火刀体上高频 焊接硬质 合金 刀头 后 ,对距焊 口 1 m处 m
的刀体进行金相化验 ,金相组织为索 氏体型珠光 体 +碎 块状 铁 素 体 ( 图 9 ,靠 近 刀 头 处 的 硬 度 为 2 见 ) 0~ 2H C( 4 R 见表 1 。由金相组织和所测 的硬度可知 ,刀体 )
图 9 焊接刀头后 ,靠近焊 1 的刀体金相组织 3 处
WWW. c n st c r . n ma hi i . o n c
维普资讯
r 口 me n e t ,
以前我厂从未采用过 ,人们 担心在淬火 的加热 和冷却过 程 中会使硬质合金刀头性能变坏,甚 至在加热 过程 中焊 口发生变化造成刀头脱落等。为此,我们就硬 质合金刀 头在各种不同的热处理工艺下的性能变化 ( 包括硬 度和
表 1 试 验 铣 刀 刀体 淬火 后 和 焊 接 刀头 后 的硬 度
刀体淬火后的 刀体焊接刀头后 的硬度 HR C
刀具热处理
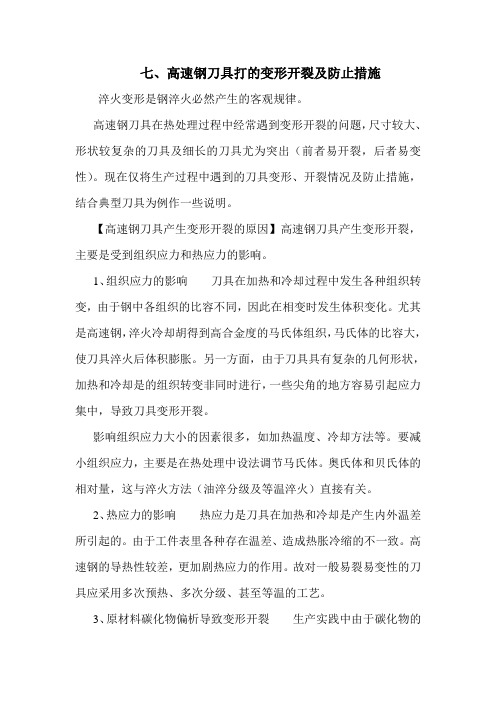
七、高速钢刀具打的变形开裂及防止措施淬火变形是钢淬火必然产生的客观规律。
高速钢刀具在热处理过程中经常遇到变形开裂的问题,尺寸较大、形状较复杂的刀具及细长的刀具尤为突出(前者易开裂,后者易变性)。
现在仅将生产过程中遇到的刀具变形、开裂情况及防止措施,结合典型刀具为例作一些说明。
【高速钢刀具产生变形开裂的原因】高速钢刀具产生变形开裂,主要是受到组织应力和热应力的影响。
1、组织应力的影响刀具在加热和冷却过程中发生各种组织转变,由于钢中各组织的比容不同,因此在相变时发生体积变化。
尤其是高速钢,淬火冷却胡得到高合金度的马氏体组织,马氏体的比容大,使刀具淬火后体积膨胀。
另一方面,由于刀具具有复杂的几何形状,加热和冷却是的组织转变非同时进行,一些尖角的地方容易引起应力集中,导致刀具变形开裂。
影响组织应力大小的因素很多,如加热温度、冷却方法等。
要减小组织应力,主要是在热处理中设法调节马氏体。
奥氏体和贝氏体的相对量,这与淬火方法(油淬分级及等温淬火)直接有关。
2、热应力的影响热应力是刀具在加热和冷却是产生内外温差所引起的。
由于工件表里各种存在温差、造成热胀冷缩的不一致。
高速钢的导热性较差,更加剧热应力的作用。
故对一般易裂易变性的刀具应采用多次预热、多次分级、甚至等温的工艺。
3、原材料碳化物偏析导致变形开裂生产实践中由于碳化物的不均匀性,是工具沿碳化物集中处开裂。
例如铣刀、剃齿刀等刀具的内孔开裂,多数是上述原因所导致的。
4、淬火前刀具内部存在较大的应力在处理过程中易引起变形开裂。
例如薄形锯片铣刀在处理前先消除应力,处理后能减少变形。
5、淬火温度过高使钢材强度大大下降,因此在加热和冷却过程中容易发生变形与开裂。
实践经验证明,凡刀具有过热、过烧现象,则刀具变形就大(如车刀、钻头之类),容易引起开裂(如铣刀、滚刀之类)。
6、冷却过快在热应力和组织应力的复杂作用下,易引起变形开裂。
同样,加热过快也易引起变形开裂。
高速钢具有极好的淬透性,只有在600℃以后缓慢的冷却都不妨碍刀具的硬度和其他切削性能。
硬质合金铣刀钝化处理工艺

硬质合金铣刀钝化处理工艺一、引言硬质合金铣刀作为一种重要的切削工具,在机械加工行业中得到了广泛的应用。
然而,由于长时间使用或者不当使用,铣刀刃面容易出现磨损、断裂等问题,影响其切削性能和使用寿命。
为了解决这个问题,钝化处理工艺被广泛应用于硬质合金铣刀的表面处理中,以增强其耐磨性和延长使用寿命。
二、钝化处理工艺的原理钝化处理是通过表面化学反应,形成一层致密的、均匀的、无机的氧化物膜,以提高硬质合金铣刀的表面硬度和耐磨性。
常用的钝化处理方法有化学氧化法、化学沉积法和热处理法等。
三、化学氧化法化学氧化法是将硬质合金铣刀浸泡在含有氧化剂和助剂的酸性溶液中,通过在溶液中发生氧化反应,使铣刀表面形成一层致密的氧化膜。
常用的氧化剂有硝酸、硫酸和硝酸铵等,助剂可以提高氧化速度和膜层质量。
在氧化过程中,要控制好温度、浸泡时间和溶液浓度等参数,以确保获得均匀、致密的氧化膜。
四、化学沉积法化学沉积法是通过在硬质合金铣刀表面沉积一层金属或合金膜,以提高其表面硬度和耐磨性。
常用的沉积方法有电化学沉积、热浸镀和化学气相沉积等。
其中,电化学沉积是利用电解池中的金属离子在铣刀表面还原沉积,形成金属膜;热浸镀是将硬质合金铣刀浸泡在金属溶液中,通过金属离子的扩散,在铣刀表面形成金属膜;化学气相沉积是通过在高温环境中将金属或者合金气体分解,使金属原子在铣刀表面沉积形成金属膜。
五、热处理法热处理法是通过在一定温度下对硬质合金铣刀进行加热处理,以改变其组织结构和性能。
常用的热处理方法有退火、淬火和回火等。
退火是将硬质合金铣刀加热至一定温度,保持一定时间后,缓慢冷却,以消除内部应力和改善刀具的硬度和韧性;淬火是将加热至临界温度以上的硬质合金铣刀迅速冷却,使其获得高硬度和耐磨性;回火是在淬火后将硬质合金铣刀加热至低于临界温度的一定温度,保温一定时间后,再冷却,以提高硬质合金铣刀的韧性和耐磨性。
六、钝化处理工艺的优势钝化处理工艺可以提高硬质合金铣刀的表面硬度和耐磨性,延长其使用寿命;钝化处理过程简单、操作方便,适应性强,可以应用于不同类型和规格的硬质合金铣刀;钝化处理工艺不会改变硬质合金铣刀的整体性能,不会影响切削性能和加工精度。
立铣刀的发展趋势
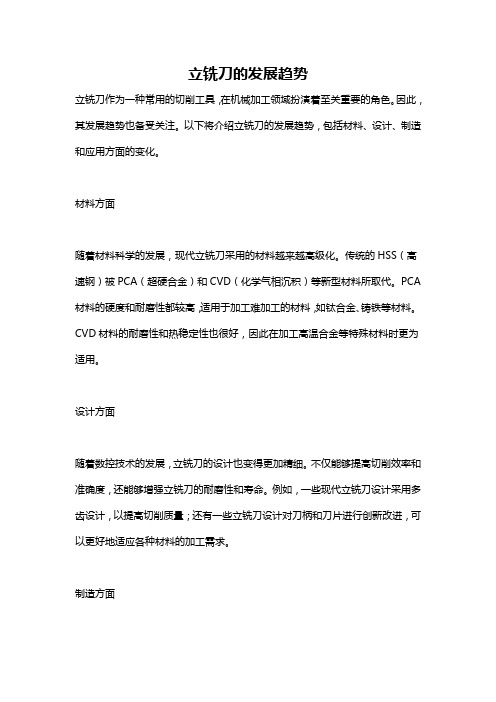
立铣刀的发展趋势
立铣刀作为一种常用的切削工具,在机械加工领域扮演着至关重要的角色。
因此,其发展趋势也备受关注。
以下将介绍立铣刀的发展趋势,包括材料、设计、制造和应用方面的变化。
材料方面
随着材料科学的发展,现代立铣刀采用的材料越来越高级化。
传统的HSS(高速钢)被PCA(超硬合金)和CVD(化学气相沉积)等新型材料所取代。
PCA 材料的硬度和耐磨性都较高,适用于加工难加工的材料,如钛合金、铸铁等材料。
CVD材料的耐磨性和热稳定性也很好,因此在加工高温合金等特殊材料时更为适用。
设计方面
随着数控技术的发展,立铣刀的设计也变得更加精细。
不仅能够提高切削效率和准确度,还能够增强立铣刀的耐磨性和寿命。
例如,一些现代立铣刀设计采用多齿设计,以提高切削质量;还有一些立铣刀设计对刀柄和刀片进行创新改进,可以更好地适应各种材料的加工需求。
制造方面
随着制造技术的不断提高,立铣刀制造方式也不断改进。
除了传统的热处理等工艺外,还出现了一些新型制造方式。
例如,采用激光熔覆技术制造立铣刀,可以根据需要制造出各种复杂形状的立铣刀,提高了立铣刀的加工精度和可靠性。
应用方面
立铣刀的应用范围也不断扩大。
除了通用的金属加工外,立铣刀还扩展到了一些特殊领域。
例如,在医疗领域,立铣刀已广泛应用于人工关节手术中;在汽车工业中,立铣刀则扮演着重要的制造角色,加工各种车身零部件和钣金件。
总之,随着科技的不断发展,立铣刀的材料、设计、制造和应用等方面都在不断变化,以适应不同领域的加工需求。
cnc刀具制作知识点总结

cnc刀具制作知识点总结一、CNC刀具的种类及结构1. 铣刀铣刀是一种用于切削金属和其他材料的刀具。
常见的铣刀类型包括球头铣、平头铣、立铣刀、T型铣刀等。
铣刀的结构包括刀头、刀杆和刀柄,刀头的设计和材质决定了铣刀的切削性能。
2. 钻头钻头是用于钻孔的刀具,主要用于加工金属和非金属材料。
根据其结构和用途,钻头可以分为中心钻头、扩孔钻头、深孔钻头、钻孔刀等。
3. 铣削刀铣削刀主要用于金属材料的铣削加工,通常包括铣刀头、铣刀柄和铣刀杆。
铣削刀的结构设计和材料选择直接影响了铣削加工的质量和效率。
4. 镗刀镗刀是用于加工精密孔的刀具,常见的镗刀类型包括扩孔刀、精密镗孔刀等。
镗刀的结构设计和刀具材料选择对孔的精度和表面质量有很大影响。
5. 刨刀刨刀是用于平面加工的刀具,通常包括刨刀头和刨刀柄。
刨刀的结构设计和刀具材料选择对平面加工的表面光洁度和精度有重要影响。
二、CNC刀具的制作工艺1. 材料选择CNC刀具的制作材料一般为高速钢、硬质合金、陶瓷等。
根据刀具的用途和要求,选择合适的刀具材料是制作过程中的第一步。
2. 制作工艺CNC刀具的制作工艺包括锻造、热处理、切削、表面处理等多个工序。
其中,热处理是非常关键的工艺环节,可以使刀具获得良好的硬度和耐磨性。
3. 制作设备CNC刀具的制作需要使用各种刀具加工设备,如数控磨床、数控铣床、电火花机等。
这些设备的使用需要技术娴熟的操作者和精准的加工工艺。
4. 制作质量检测CNC刀具的制作质量需要经过严格的检测,包括尺寸测量、硬度测试、表面质量检查等。
只有通过质量检测的刀具才能投入使用。
三、CNC刀具的使用与维护1. 使用注意事项在使用CNC刀具时,需要注意正确的切削参数,如切削速度、进给量、切削深度等。
同时,需要根据不同的材料和加工要求选择合适的刀具,并进行正确的夹持和安装。
2. 刀具维护CNC刀具的维护包括清洁、润滑、修磨等多个方面。
定期对刀具进行检查和维护,可以延长刀具的使用寿命并保持良好的加工质量。
刀具热处理技术的应用
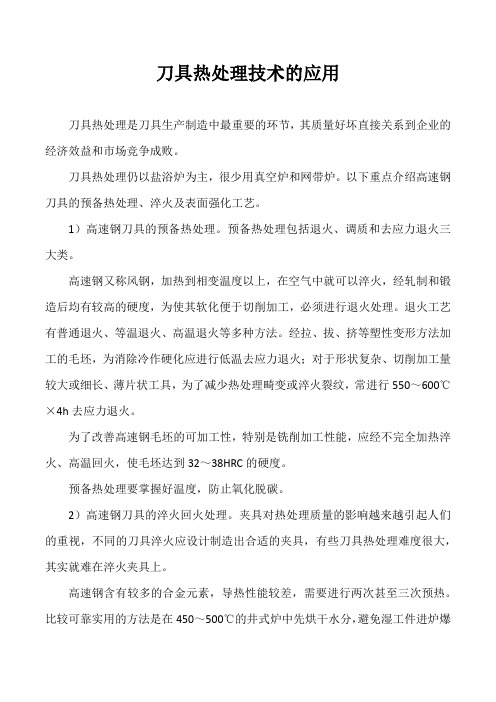
刀具热处理技术的应用刀具热处理是刀具生产制造中最重要的环节,其质量好坏直接关系到企业的经济效益和市场竞争成败。
刀具热处理仍以盐浴炉为主,很少用真空炉和网带炉。
以下重点介绍高速钢刀具的预备热处理、淬火及表面强化工艺。
1)高速钢刀具的预备热处理。
预备热处理包括退火、调质和去应力退火三大类。
高速钢又称风钢,加热到相变温度以上,在空气中就可以淬火,经轧制和锻造后均有较高的硬度,为使其软化便于切削加工,必须进行退火处理。
退火工艺有普通退火、等温退火、高温退火等多种方法。
经拉、拔、挤等塑性变形方法加工的毛坯,为消除冷作硬化应进行低温去应力退火;对于形状复杂、切削加工量较大或细长、薄片状工具,为了减少热处理畸变或淬火裂纹,常进行550~600℃×4h去应力退火。
为了改善高速钢毛坯的可加工性,特别是铣削加工性能,应经不完全加热淬火、高温回火,使毛坯达到32~38HRC的硬度。
预备热处理要掌握好温度,防止氧化脱碳。
2)高速钢刀具的淬火回火处理。
夹具对热处理质量的影响越来越引起人们的重视,不同的刀具淬火应设计制造出合适的夹具,有些刀具热处理难度很大,其实就难在淬火夹具上。
高速钢含有较多的合金元素,导热性能较差,需要进行两次甚至三次预热。
比较可靠实用的方法是在450~500℃的井式炉中先烘干水分,避免湿工件进炉爆炸,飞液溅出伤人。
预热温度一般为850~870℃,预热时间为加热时间的两倍。
盐浴配方(质量分数)为70%BaCl2+30%NaCl。
高速钢刀具高温加热是非常重要又非常难的环节,盐浴成分为100%BaCl2。
从增加碳化物溶入量,提高奥氏体合金化程度的角度考虑,奥氏体化温度越高越好,以便提高钢的耐磨性和热硬性;但从细化晶粒,提高韧性的角度考虑,加热温度不宜太高。
不同牌号有不同的加热温度,同一牌号钢制作不同刀具,加热温度相差也很大,也就是说,制订热处理工艺应该个性化。
不管何种刀具,在制订热处理工艺时,必须了解刀具加工的对象,在满足韧性的前提下,温度高比温度低优越。
模具加工方法与热处理

1.模具加工方法:平面加工:龙门刨床刨刀牛头刨床刨刀对模具坯料进行六面加工龙门铣床断面铣刀车削加工:车床车刀数控车床车刀各种模具零件的回转面和平面立式车床车刀钻孔加工:钻床钻头、铰刀横臂钻床钻头、铰刀铣床: 钻头、铰刀数控铣床钻头、铰刀加工模具的各种孔加工中心钻头、铰刀深孔钻:深孔钻头镗孔加工:加工中心镗刀卧室镗床镗刀镗削模具中的各种孔铣床镗刀坐标镗床镗刀铣削加工:铣床立铣刀、断面铣刀数控铣床立铣刀、球头铣刀铣削各种模具平面和曲面加工中心立铣刀、球头铣刀仿形加工球头铣刀雕刻机小直径立铣刀磨削加工:平面磨床砂轮成型磨床砂轮数控磨床砂轮磨削模具精密孔光学曲线磨床砂轮坐标磨床砂轮内外圆磨床砂轮万能磨床砂轮电加工:型腔电加工电极电蚀切削难以加工的线切割加工线电极部位精密轮廓加工电解加工电极型腔和平面加工切削加工:抛光加工抛光机砂轮、锉刀、砂纸、油石和抛光剂。
去除铣削痕迹,对模具零件进行抛光非切削加工:挤压加工压力机挤压凸模难以切削加工的型腔铸造加工铍铜压力铸造精密铸造铸造设备、石膏模型铸造设备铸造注塑模型腔电铸加工电铸设备电铸母型精密注塑模型腔表面装饰纹加工蚀刻装置蚀刻纹样板在注塑模型腔表面2模具零件的热处理工序1退火:将钢件加热到临界温度以上‘保温一定时间后随炉温或在土灰、石英砂中缓慢冷却的操作过程。
目的:消除模具的铸、锻件或冷压件的内应力,改善组织,降低硬度,提高塑性,以利于切削加工。
分类:扩散退火、完全退火、球化退火等。
扩散退火目的:适用于合金钢锭,消除合金钢锭中的成分不均匀性,故又称为均匀化退火。
完全退火目的:主要用于含碳量在0.77%以下的亚共析钢,降低硬度,细化晶粒,消除冷热加工应力。
球化退火目的:主要用于含碳量≥0.77%的钢,使碳化铁成球状,降低硬度,改善切削性能,为淬火做准备。
不完全退火目的:主要用于含碳量高于0.77%的高碳钢,降低硬度,消除内应力。
等温退火目的:改善金相组织,降低硬度,改善切削加工性能。
硬质合金铣刀钝化处理工艺

硬质合金铣刀钝化处理工艺硬质合金铣刀钝化处理工艺是一项重要的加工工艺,它能够提高铣刀的使用寿命和性能稳定性,减少生产成本,提高加工效率。
下面将为大家详细介绍硬质合金铣刀钝化处理工艺的相关内容。
首先,钝化处理是指通过一系列的化学物质或物理方法对硬质合金铣刀进行表面处理,形成一层保护膜,从而减少与工件的摩擦、磨损和氧化腐蚀,延长铣刀的使用寿命。
常用的钝化处理方法有化学氧化、热处理和涂层处理等。
在进行硬质合金铣刀钝化处理之前,我们首先需要对铣刀进行预处理。
这包括清洗、脱脂和除锈等步骤,确保铣刀表面干净且无杂质。
接下来,我们可以根据具体情况选择合适的钝化处理方法。
化学氧化是一种常见的钝化处理方法。
它通过将硬质合金铣刀浸泡在含有氧化剂的酸性溶液中,使铣刀表面与溶液中的氧发生氧化反应,从而形成一层致密的氧化膜。
氧化膜的形成可以增强铣刀表面的硬度和耐磨性,减少与工件的摩擦和磨损。
同时,氧化膜还能起到一定的防腐蚀作用,延长铣刀的使用寿命。
热处理是另一种常用的钝化处理方法。
它通过将硬质合金铣刀加热至一定温度,保持一定时间,然后冷却至室温。
热处理可以改变铣刀的晶格结构和组织性能,提高硬质合金铣刀的硬度和耐磨性。
此外,热处理还可以消除铣刀内部的应力,提高其强度和韧性,降低断裂风险。
涂层处理是一种比较先进的钝化处理方法。
它通过在硬质合金铣刀表面涂覆一层特殊的材料,例如氮化物、碳化物等,形成一种硬度较高、润滑性好的涂层。
这种涂层不仅可以减少与工件的摩擦和磨损,还能增强铣刀的耐高温性能和抗化学腐蚀能力。
涂层处理不仅可以提高硬质合金铣刀的使用寿命,还可以提高加工效率和产品质量。
在进行硬质合金铣刀钝化处理时,我们还需要注意一些操作细节。
首先,根据具体的处理要求选择合适的处理方法和处理参数,确保处理效果。
其次,进行钝化处理时,需要使用专用的设备和工艺,遵循安全规范,防止事故发生。
此外,钝化处理后的硬质合金铣刀还需要进行质量检验和保养,以保证其正常运行和使用寿命。
三面刃铣刀的热处理工艺

( 齐齐哈尔 ! "#"$%& ) ! 赵振霞
( + ) 加热时间的确定! 应保证工作部分烧透及碳化 物达到相对于该温度下较充分的溶解,加热时间按 %- . %12 " 33 确定。 ( / ) 分级冷却! 一次分级,工件在 %+:- . %+&-0 保 温足够时间后直接转入 1&- . ,+-0 分级盐浴炉 ( /%4 =6’7+ 8 )&4 ’6’7+ 8 +%4 56’7 ) 中,保持一段时间 ( 保 温时间与高温加热时间相同) 。实践证明,在此温度下 保持十几分钟,不会影响淬火硬度及红硬性,却能使刀 具内外温度接近均匀,较之油冷可显著减少热应力与组 织应力,从而减少刀具的变形与开裂,因此刀具均可采 用一次分级代替油冷。紧接着转入 +1- . +&-0 箱式电炉 中进行二次分级,保温时间约为一次分级的 %# 1 . + 倍, 出炉空冷,空冷至 :-0 为宜 ( 即不带手套可短时间抓住 工件) ,然后及时装炉回火。二次分级能进一步减少热 应力与组织应力,减少变形和开裂倾向,特别适用于形 状复杂、材料质量差的大型刀具。
淬火高温加热应保证适当碳化物பைடு நூலகம்解,使奥氏体有 足够的含碳量与合金元素含量,使刀具淬火后能得到要 求的红硬性,同时还留有一定数量的未熔碳化物。这样 一方面增加刀具耐磨性;另一方面阻止晶粒长大,防止 过热过烧。由于三面刃铣刀截面变化大,有尖角,易开 裂,同时钢坯一般都存在严重的碳化物的不均匀,宜采 用较低的淬火温度 %+:- . %+&-0 ,取较长的加热时间; 淬火温度实际温度控制要根据试块加热冷透后观察断口 晶粒度来确定,在同一根原料上切取试块,能准确地反 映出实际晶粒度的情况。
铣刀的热处理生产设计..

铣刀的选材及热处理生产线设计1.设计原则1.1本次课程设计任务要求根据铣刀论的服役条件、失效形式和性能要求,在此基础上进行材料设计和选材,制定工件的加工工艺流程,制定详细的热处理工艺规范,选择热处理设备,绘制热处理车间的平面布置图。
具体要求:1)每人选择一个课题,但同一课题选择不能超过5人,选择同一课题的同学组成一个小组,共同讨论,但须独立撰写完成;2)确定工件的尺寸为45°Φ12*28*75、形状和年时基数;3)详细讨论选材的依据,合金元素作用、组织与性能之间的关系;提出不少于三种的备选方案,并进行分析比较,确定一种最佳方案;4)确定工件的加工工艺流程,制定热处理工艺规范,并加以论述其依据;5)根据热处理工艺选择适当的热处理设备,对主要热处理设备的炉体结构、炉膛尺寸、功率进行计算论证,年产量4万件,分4个批次生产,即每批生产1万件,确定所需炉子的台数;6)合理设计工件的热处理生产线,画出设备在车间内的平面布置图(要求用计算机绘图,图中设备用参考图例绘出,其他按照国家标准画出)。
1.2热处理零件结构形状设计需要热处理的工件,在设计时,除了应考虑服役条件、承受载荷的大小和机械加工工艺外,还要要考虑热处理的变形、开裂所造成的产品报废。
因此,对热处理件结构形状有一定的设计要求。
1)结构形状设计应避免应力集中截面急剧变化的工件,淬火时易引起过量变形或开裂,一般应采用平滑过渡或圆弧过渡;外形的尖锐棱边,尖角和凹腔角处会产生应力集中,因此,也常用圆弧代替尖角,为防止工件上的孔或模具型腔成为裂纹的策源地,孔与孔之间应有一定的距离,冲模型腔与模边之间的距离也应足够大。
2)结构形状设计应尽量简单、均衡、规则、对称结构件的形状应尽量使工件各部位的质量均匀分布,以减少淬火时可能引起的过量变形和开裂。
理想的结构形状可遵循以下的基本原则:a.球形优于立方体,更优于长方体;b.圆柱体优于圆锥体;c.圆形截面优于椭圆形截面,方形截面优于矩形截面;d.在可能的条件下,应尽量使功能孔的尺寸与位置均衡、对称、分布,也可以通过加开工艺孔或工艺槽来解决质量均衡问题;e.辅助孔应位于交叉刃口的延长线上,尤其不能靠近小锐角,以免成为裂纹的策源地。
热处理车间课程设计
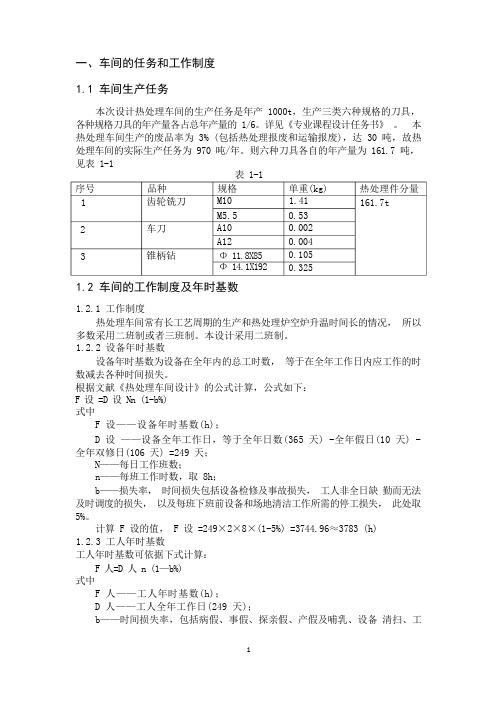
一、车间的任务和工作制度1.1 车间生产任务本次设计热处理车间的生产任务是年产 1000t ,生产三类六种规格的刀具, 各种规格刀具的年产量各占总年产量的 1/6。
详见《专业课程设计任务书》 。
本 热处理车间生产的废品率为 3% (包括热处理报废和运输报废),达 30 吨,故热 处理车间的实际生产任务为 970 吨/年。
则六种刀具各自的年产量为 161.7 吨, 见表 1-1表 1-1 1.2 车间的工作制度及年时基数1.2.1 工作制度热处理车间常有长工艺周期的生产和热处理炉空炉升温时间长的情况, 所以 多数采用二班制或者三班制。
本设计采用二班制。
1.2.2 设备年时基数设备年时基数为设备在全年内的总工时数, 等于在全年工作日内应工作的时 数减去各种时间损失。
根据文献《热处理车间设计》的公式计算,公式如下: F 设 =D 设 Nn (1-b%) 式中F 设——设备年时基数(h);D 设 ——设备全年工作日,等于全年日数(365 天) -全年假日(10 天) - 全年双修日(106 天) =249 天;N ——每日工作班数;n ——每班工作时数,取 8h ;b ——损失率, 时间损失包括设备检修及事故损失, 工人非全日缺 勤而无法 及时调度的损失, 以及每班下班前设备和场地清洁工作所需的停工损失, 此处取 5%。
计算 F 设的值, F 设 =249×2×8×(1-5%) =3744.96≈3783 (h) 1.2.3 工人年时基数工人年时基数可依据下式计算:F 人=D 人 n (1—b%) 式中F 人——工人年时基数(h);D 人——工人全年工作日(249 天);b ——时间损失率,包括病假、事假、探亲假、产假及哺乳、设备 清扫、工序号 品种 规格单重(kg) 热处理件分量 1齿轮铣刀 M10 M5.5 1.41 0.53161.7t 2 车刀 A10 A12 0.0020.0043 锥柄钻 Φ 11.8X85 Φ 14.1X192 0.1050.325间歇息等工时损失,本设计取 4%。
三面刃铣刀
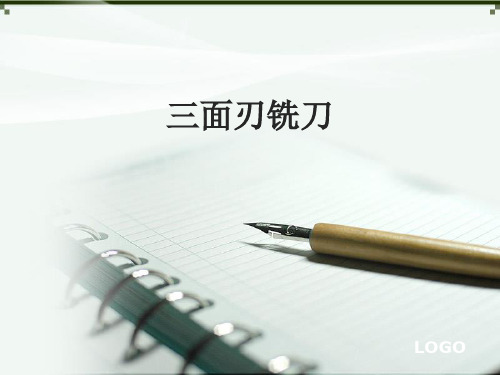
三,代替花键铣刀铣花键 对于大批量的花键轴,成形铣刀一次铣出花健 槽(图7),和单刀或组合铣刀铣花键相比, 成形铣刀铣花键生产效率高、操作简单等优点, 一般工厂多数使用铲齿成形铣刀,对于一些没有 条件制造铲齿铣刀的工厂或应急时,也 可用三面刃铣刀改制成尖齿成形铣刀.
谢谢
1 刃磨烧伤对切削的影响
刀具刃磨时出现磨糊烧伤现象,是工具制造行 业中普遍存在的问题,大多数工具厂只是采用 检测观察手段来控制刃磨烧伤,这样就会出现 下,粗磨时发生磨削烧伤后,精磨又将表面烧 伤痕迹蹭掉。虽然从刀具刃磨表面上来看.似 乎没有产生磨削烧伤,但实际上,刀具粗磨时 产生的磨削烧伤已经引起刃磨表面的金相组织 发生了变化。
一、代替直角面铣刀铣端面和台阶面 在立铣或卧铣上加工端面时,一般都要采用主 偏角为75°或60°的端面铣刀;而加工图1所示 带有直角台阶面的工件,则应该采用主偏角为 90°的直角面铣刀,当缺乏这种铣刀时,可用三 面刃铣刀来代替。
二、代替单角铣刀铣铰刀齿和棘轮
有些铰刀或棘轮的槽形角为80°或 85°,当工厂没有相应角度的单角铣刀 时,可把三面刃铣刀稍加修磨就成为一 把专用的单角度铣刀。。
2,加热时间的确定,应保证碳化物充分的溶解,加热 时间按10~15min确定.
3分级冷却一次分级,工件在1270~1280度保温 足够时间后直接转入580~620度分级盐浴炉中, 保持一段时间(保温时间与高温加热时间相同).这 样温度下保持十几分钟,不会影响淬火硬度及硬性 ,能使刀具内外温度接近均匀,油冷可显著减少热 应力与组织应力,
1,淬火温度 高碳钢中20% ~25%碳化物,合金元素Cr、 C大量 集中在碳化物内,见下表
相的组成4)
碳化物类型
铁素体
碳化物
40Cr铣刀杆的热处理工艺改进

40Cr铣刀杆的热处理工艺改进王江红;肖软生;张政伟;张素芳【摘要】The sub-temperature quenching process of 40Cr cutter bar was studied. The results show that: The microstructure is ferrite + tempered martensite and mechanical properties meet technical requirements of the milling cutter bar.The improvement technology saves electric energy, shortens the quenching time, reduces the pollution to the environment, and has obvious economic benefit and promotion value.%对40Cr铣刀杆的亚温淬火工艺进行了研究,结果表明:其显微组织是铁素体+回火索氏体,且力学性能指标满足铣刀杆的相关技术要求。
该工艺节省了电能,缩短了淬火冷却时间,降低了对环境的污染,具有明显的经济效益和推广价值。
【期刊名称】《安阳工学院学报》【年(卷),期】2016(015)006【总页数】3页(P1-2,6)【关键词】40Cr钢;亚温淬火;铣刀杆;热处理工艺【作者】王江红;肖软生;张政伟;张素芳【作者单位】中国联合装备有限公司安阳机械厂;安阳鑫盛机床股份有限公司,河南安阳455000;中国联合装备有限公司安阳机械厂;中国联合装备有限公司安阳机械厂【正文语种】中文【中图分类】TG156.3D01∶10.19329/ ki.1673-2928.2016.06.00140Cr是一种比较常见的中碳合金钢,在机械制造业中具有较为广泛的应用;40Cr 钢经过调质处理后具有良好的综合力学性能,良好的低温冲击韧性和低的缺口敏感性,常用于制造承受中等速度和中等负荷的机械零件,如汽车半轴,转向节以及普通机床上的齿轮、蜗杆、花键轴等。
合金工具钢的热处理工艺分析_机械论文
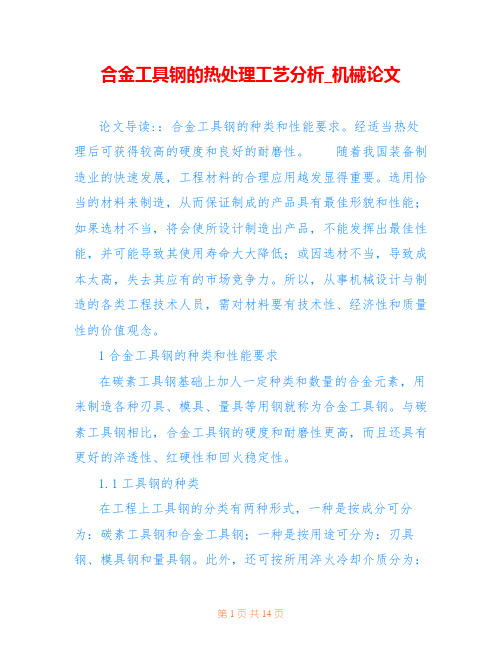
合金工具钢的热处理工艺分析_机械论文论文导读::合金工具钢的种类和性能要求。
经适当热处理后可获得较高的硬度和良好的耐磨性。
随着我国装备制造业的快速发展,工程材料的合理应用越发显得重要。
选用恰当的材料来制造,从而保证制成的产品具有最佳形貌和性能;如果选材不当,将会使所设计制造出产品,不能发挥出最佳性能,并可能导致其使用寿命大大降低;或因选材不当,导致成本太高,失去其应有的市场竞争力。
所以,从事机械设计与制造的各类工程技术人员,需对材料要有技术性、经济性和质量性的价值观念。
1合金工具钢的种类和性能要求在碳素工具钢基础上加人一定种类和数量的合金元素,用来制造各种刃具、模具、量具等用钢就称为合金工具钢。
与碳素工具钢相比,合金工具钢的硬度和耐磨性更高,而且还具有更好的淬透性、红硬性和回火稳定性。
1.1工具钢的种类在工程上工具钢的分类有两种形式,一种是按成分可分为:碳素工具钢和合金工具钢;一种是按用途可分为:刃具钢、模具钢和量具钢。
此外,还可按所用淬火冷却介质分为:水淬钢、油淬钢和空硬钢三类。
工具钢分类方法很多,其中按用途分类是常用的。
1.2工作条件和性能要求1.2.1低合金刃具钢对于某些低速而且走刀量较小的机用工具机械论文,以及要求不太高的刃具,如丝锥、板牙等刃具可用碳素工具钢T7、T8、T10、T12来制作。
碳素工具钢价格低廉,加工性能好,经适当热处理后可获得较高的硬度和良好的耐磨性。
但是其淬透性差,回火稳定性和红硬性不高,不能用作对性能有较高要求的刀具。
为了克服碳素工具钢的不足之处,在其基础上加(3%~5%)Me的合金元素就形成了低合金刃具钢。
1.2.2高速工具钢高速钢是一种高合金工具钢,含钨、钼、铬、钒等合金元素,总量超过10%Me。
高速钢优于其他工具钢的主要之处是其具有良好的红硬性,在切削零件刃部温度高达600℃时,硬度仍不会明显降低。
高速钢的碳平均质量分数较高,一般为(0.70%~1.50%)C核心期刊。
各类钢制铣刀的热处理工艺
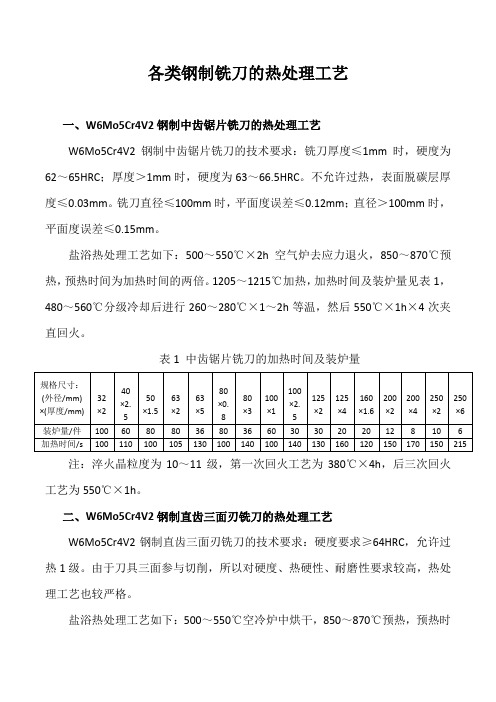
各类钢制铣刀的热处理工艺一、W6Mo5Cr4V2钢制中齿锯片铣刀的热处理工艺W6Mo5Cr4V2钢制中齿锯片铣刀的技术要求:铣刀厚度≤1mm时,硬度为62~65HRC;厚度>1mm时,硬度为63~66.5HRC。
不允许过热,表面脱碳层厚度≤0.03mm。
铣刀直径≤100mm时,平面度误差≤0.12mm;直径>100mm时,平面度误差≤0.15mm。
盐浴热处理工艺如下:500~550℃×2h空气炉去应力退火,850~870℃预热,预热时间为加热时间的两倍。
1205~1215℃加热,加热时间及装炉量见表1,480~560℃分级冷却后进行260~280℃×1~2h等温,然后550℃×1h×4次夹直回火。
表1 中齿锯片铣刀的加热时间及装炉量注:淬火晶粒度为10~11级,第一次回火工艺为380℃×4h,后三次回火工艺为550℃×1h。
二、W6Mo5Cr4V2钢制直齿三面刃铣刀的热处理工艺W6Mo5Cr4V2钢制直齿三面刃铣刀的技术要求:硬度要求≥64HRC,允许过热1级。
由于刀具三面参与切削,所以对硬度、热硬性、耐磨性要求较高,热处理工艺也较严格。
盐浴热处理工艺如下:500~550℃空冷炉中烘干,850~870℃预热,预热时间为加热时间的两倍。
1220~1230℃加热,加热时间及装炉量见表2,480~560℃分级冷却后空冷,然后进行550℃×1h×3次回火。
表2 直齿三面刃铣刀的加热时间及装炉量注:晶粒度为9.5~10.5级,为保证热处理后高硬度,应选用碳含量较高的钢制作。
三、W6Mo5Cr4V2Al钢制立铣刀的热处理工艺立铣刀有直柄立铣刀、削平型直柄立铣刀、莫氏锥柄立铣刀、短莫氏锥柄立铣刀、7:24锥柄立铣刀。
立铣刀用于以相应的夹头装夹于立式铣床或镗铣加工中心机床上进行平面铣削加工。
立铣刀加工时以周刃切削为主。
用W6Mo5Cr4V2Al 钢制作的立铣刀,使用寿命超过W2Mo9Cr4VCo8钢铣刀。
合金铣刀生产工艺流程

合金铣刀生产工艺流程英文回答:The production process of alloy milling cutters involves several steps. First, the raw materials, such as steel and other alloying elements, are collected and prepared. These materials are then melted in a furnace to form a molten alloy. Once the alloy has reached the desired composition and temperature, it is poured into a mold to create the desired shape of the milling cutter. The mold is then cooled, and the solidified alloy is removed.Next, the rough milling cutter is formed by removing excess material from the solidified alloy using a milling machine. This process involves cutting, shaping, and smoothing the alloy to achieve the desired dimensions and surface finish. Various cutting tools and techniques may be used during this step, such as end mills, face mills, and ball mills.After the rough milling process, the milling cutter undergoes heat treatment to improve its hardness and strength. This involves heating the cutter to a specific temperature and then cooling it rapidly to create a hardened surface layer. The heat treatment process may also include tempering to relieve internal stresses and improve toughness.Once the heat treatment is complete, the milling cutter is subjected to further finishing operations. This includes grinding, polishing, and coating the cutter to enhance its performance and durability. Grinding helps to achieve a precise shape and size, while polishing improves the surface finish. Coating the cutter with a protective layer, such as titanium nitride or diamond-like carbon, can reduce friction and extend its lifespan.Finally, the finished milling cutters are inspected for quality assurance. This involves checking the dimensions, surface finish, and hardness of the cutters to ensure they meet the required specifications. Any defective or non-conforming cutters are identified and either repaired ordiscarded.In summary, the production process of alloy milling cutters involves collecting and preparing raw materials, melting and molding the alloy, rough milling, heat treatment, finishing operations, and quality inspection. Each step contributes to the overall quality and performance of the final product.中文回答:合金铣刀的生产工艺流程包括几个步骤。
高速钢半圆键槽铣刀的热处理工艺

高速钢半圆键槽铣刀的热处理工艺
高速钢半圆键槽铣刀用于加工GB/T1098—2003《半圆键键槽的剖面尺寸》中规定的轴上半圆键槽,键宽为1~10mm。
这类铣刀由于直径比较小,故都做成直柄的而且以焊柄居多。
对于不同直径的铣刀,规定了Ⅰ、Ⅱ、Ⅲ型三种结构,这里只介绍整体高速钢第Ⅱ型半圆键槽铣刀热处理工艺。
半圆键槽铣刀如图1所示。
图1 半圆键槽铣刀
半圆键铣刀的硬度要求:铣刀工作部分的外径≤7mm时,硬度为63~65HRC,外径>7mm时,硬度为64~66.5HRC;铣刀柄部的硬度为30~50HRC。
金相要求:奥氏体晶粒度控制在10.5~10级,回火程度≤2级,过热程度≤1级。
(1)预热
选用合适的淬火夹具,按规定装夹,装炉量见表1。
首先于450~500℃的井式炉中烘干,然后在850~870℃的中温盐浴中预热,预热时间为加热时间的2倍。
为确保柄部硬度,预热时柄部全浸入浴中(如采用高频感应淬火,预热时应将柄部提出液面)。
(2)加热
高温加热时将柄部提出液面,W18Cr4V、W6Mo5Cr4V2、W9Mo3Cr4V钢的加热温度分别为1250~1270℃、1215~1225℃、1220~1230℃,加热时间见表1。
表1 半圆键槽铣刀的装炉量和加热时间
(3)冷却
用480~560℃中性盐浴冷却,冷却时间同高温加热时间。
(4)回火
用540~560℃×1h×3次常规回火。
(5)检验
重点检查硬度、金相组织,表面质量(如裂纹、碰伤、崩齿、腐蚀等)也应检查。
奥氏体晶粒度控制在10~10.5级,外径d≤10mm的以10.5级为好。
- 1、下载文档前请自行甄别文档内容的完整性,平台不提供额外的编辑、内容补充、找答案等附加服务。
- 2、"仅部分预览"的文档,不可在线预览部分如存在完整性等问题,可反馈申请退款(可完整预览的文档不适用该条件!)。
- 3、如文档侵犯您的权益,请联系客服反馈,我们会尽快为您处理(人工客服工作时间:9:00-18:30)。
铣刀的选材及热处理生产线设计1.设计原则1.1本次课程设计任务要求根据铣刀论的服役条件、失效形式和性能要求,在此基础上进行材料设计和选材,制定工件的加工工艺流程,制定详细的热处理工艺规范,选择热处理设备,绘制热处理车间的平面布置图。
具体要求:1)每人选择一个课题,但同一课题选择不能超过5人,选择同一课题的同学组成一个小组,共同讨论,但须独立撰写完成;2)确定工件的尺寸为45°Φ12*28*75、形状和年时基数;3)详细讨论选材的依据,合金元素作用、组织与性能之间的关系;提出不少于三种的备选方案,并进行分析比较,确定一种最佳方案;4)确定工件的加工工艺流程,制定热处理工艺规范,并加以论述其依据; 5)根据热处理工艺选择适当的热处理设备,对主要热处理设备的炉体结构、炉膛尺寸、功率进行计算论证,年产量4万件,分4个批次生产,即每批生产1万件,确定所需炉子的台数;6)合理设计工件的热处理生产线,画出设备在车间内的平面布置图(要求用计算机绘图,图中设备用参考图例绘出,其他按照国家标准画出)。
1.2热处理零件结构形状设计需要热处理的工件,在设计时,除了应考虑服役条件、承受载荷的大小和机械加工工艺外,还要要考虑热处理的变形、开裂所造成的产品报废。
因此,对热处理件结构形状有一定的设计要求。
1)结构形状设计应避免应力集中截面急剧变化的工件,淬火时易引起过量变形或开裂,一般应采用平滑过渡或圆弧过渡;外形的尖锐棱边,尖角和凹腔角处会产生应力集中,因此,也常用圆弧代替尖角,为防止工件上的孔或模具型腔成为裂纹的策源地,孔与孔之间应有一定的距离,冲模型腔与模边之间的距离也应足够大。
2)结构形状设计应尽量简单、均衡、规则、对称结构件的形状应尽量使工件各部位的质量均匀分布,以减少淬火时可能引起的过量变形和开裂。
理想的结构形状可遵循以下的基本原则:a.球形优于立方体,更优于长方体;b.圆柱体优于圆锥体;c.圆形截面优于椭圆形截面,方形截面优于矩形截面;d.在可能的条件下,应尽量使功能孔的尺寸与位置均衡、对称、分布,也可以通过加开工艺孔或工艺槽来解决质量均衡问题;e.辅助孔应位于交叉刃口的延长线上,尤其不能靠近小锐角,以免成为裂纹的策源地。
3)设计中实际措施机械构件中工作的轮廓、形状和尺寸是各式各样的,往往不能遵循上述设计原则,对此可根据实际情况采取措施加以补救。
a.设计成合理形状,淬火后再磨去不必要的部分;b.开切必要的孔槽使质量均衡;c.一个不平衡的工件,为了平衡质量、改善散热条件,可加开工艺孔;d.大型复杂工件可采用拼镶结构,以解决加工和热处理的困难;e.刻字、印痕的位置应远离应力集中程度高的孔。
为减少损失,避免事故,充分估计各种因素的影响,可采用设计、热加工和热处理几方面共同商讨,协同设计,避免因设计不当造成加工、热处理和使用上的题。
图1.1铣刀零件图1.3热处理工艺设计1.3.1工艺分析的基本原则热处理工艺设计是热处理车间设计的中心环节,是设备选择的主要依据。
所确定的热处理工艺必须先进、可靠、经济合理,并与车间生产规模相适应。
常规工艺应力求工艺路线简化,运输量最小,工序较小,节省能源及劳动量。
采用先进工艺应经过技术经济论证或实验研究,取得可信的试用效果。
1.3.2 工艺路线产品零件从毛坯生产到完成成品,生产路线是确定热处理车间任务的基础,具体如下:(1)铸铁,铸钢,有色金属一般铸件的预备热处理与铸造之后进行,包括正火、扩散退火、等温退火、球化退火、可锻化退火、再结晶退火、消除应力退火、人工时效(稳化处理)等。
(2)硬度要求在285HB(30HRC)以下的一般铸件,可在机械加工前热处理到要求硬度,包括正火、调质(淬火及高温回火)。
加工余量大的锻件,为保证其热处理效果,应在粗加工后进行热处理。
(3)表面硬化,化学热处理零件,硬度要求大于285HB(30HRC)的零件,应在机械加工后进行。
一些精度要求高的零件,可使用特殊加工刀具的零件,也可在加工前进行热处理。
(4)局部化学热处理零件,生产批量大时,非处理部分应镀层保护,批量小时可采用机械保护,防渗涂层以及车去渗层等方法。
(5)绕制弹簧、冷镦、冷挤成形零件、应进行去应力退火、再结晶退火、正火等工序。
(6)形变热处理可简化工艺路线,减少工序,节约能源。
有些铸、锻件,特别是锻件,可充分利用锻造余热进行淬火、调质等处理,使锻造加工与热处理结合起来。
1.3.3 工艺方法的选定(1)常规热处理工艺热处理零件的常规热处理工艺,包括毛坯的预备热处理和零件的最终热处理,如退火、正火、去应力退火、调质(淬火及高温回火)、时效及固溶处理等。
从提高热处理质量考虑,如不许在加热过程中发生氧化、脱碳,应采用保护气氛下加热。
(2)化学热处理化学热处理包括奥氏体状态下渗碳、碳氮共渗,铁素体状态下的渗氮和氮碳共渗,以及渗硼、渗硅、渗铝及各种渗金属和多元共渗工艺。
化学热处理可以在气态、固态或液态介质中完成,确定化学热处理的工艺选用。
有化学热处理后需要淬火的,应根据可能尽量采取渗后直接淬火工艺。
(3)调质热处理调质热处理技术的发展主要有以下几个方面。
①炉型。
由于振底炉长期使用中存在振底板变形零件在炉内布料、加热不均淬火质量散差大同时振动噪声大、环境差,振底炉已逐渐退出生产线,网带炉、铸链炉得到普遍应用。
②碳势控制技术的应用。
碳势控制技术在保护气氛调质生产线得到普遍应用。
有效的控制炉内碳势控制精度,保证了零件淬火后的表面质量。
③计算机技术的应用。
通过应用计算机能够按照工艺设定自动完成工件的生产全过程记录、保存工件生产中的各种工艺参数具有完善的故障诊断、安全警示及连锁功能。
④快速淬火油和水基淬火介质的应用。
快速淬火油的应用保证了高强度螺栓件的热处理内在质量。
水基淬火介质的应用解决了零件淬油不硬、淬水开裂及零件淬火变形的质量问题。
(4)感应加热淬火感应加热可使用高频、中频、工频、超音频,以及双频及脉冲加热工艺,根据零件钢种、尺寸特点、要求硬化层深度、零件批量等确定工艺。
感应加热淬火后可根据可能采用自然回火。
(5)火焰表面淬火火焰表面淬火技术的发展,如采用先进温度检测技术与自动化控制与操作,淬火质量可保证。
在单件小批量生产中部分采用火焰淬火工艺,生产灵活实用。
(6)高密度能量表面处理高密度能量表面处理包括激光表面处理,电子束表面处理和物理及化学气相沉积。
一般适用某些特定的零件,选用这种工艺必须先进行工艺实验,试生产使用,用从热处理质量和经济效益考虑。
2立铣刀材料设计2.1工件服役条件和失效形式分析2.1.1 立铣刀的服役条件由于立铣刀是一种用来对金属材料进行铣孔的刀具其结构如上图油刃部和柄部组成,铣刀工作时刃部深入金属内部进行铣削,被金属包围散热困难,升温快,尤其是切削速度很高刃部温度很快达到600℃左右。
因此要求刃部要有高的硬度、耐磨性和红硬性要高。
由于铣刀在很大的轴向压力下钻削,受大的压应力和扭转应力。
因此要求具有一定的韧性和高的强度,由于刃部不断磨损,为了使铣刀能长久的使用,要求刃部应淬透。
对于柄部来说,它不承担切削工作过程中挤压扭转。
要求具有一定的韧度、强度和一定的硬度来保证铣刀良好的铣削要求立铣刀应有良好的几何形状。
立铣刀的切削受力分析:在切削金属材料时,立铣刀要受到阻止刀具切除切屑的阻力(即铣削力) 。
在不同的加工条件下,铣削力的变化范围较大。
分析认为,铣刀切削时,工件材料将发生部分弹性变形和塑性变形,并对刀具产生抗力;同时,刀具与切屑、刀具与工件之间要产生摩擦力,铣削力就是二者的合力。
图2.1 立铣刀受力与变形示2.1.2主要失效形式1刀具的磨粒磨损:磨粒磨损是因为工件材料磨擦划过刀具的主后刀面而造成的。
2月牙洼磨损:月牙洼磨损是由钢制工件与铣刀之间的化学作用(即刀具前刀面渗出的碳溶入切屑中)引起的。
不过,月牙洼磨损也有可能是由高速切削铸铁时切屑划过刀具前刀面的磨蚀作用所引起。
3沟槽磨损:刀具产生沟槽磨损的原因通常是在全切深情况下被加工工件表面某处的切削条件与其余部分相比发生恶化造成的。
导致工件表面切削条件出现差异的原因可能与工件表面剥落有关;也可能由冷作应力或加工硬化所引起;还有可能与某些似乎无关紧要的因素——例如油漆——有关,工件表面的油漆有可能对切入工件不太深的切削刃起到一种淬火作用。
4变形:刀具的变形是指刀片在切削热和切削压力的作用下发生软化和扭曲变形。
5崩刃和碎裂:因为切削刃的脆性过大,难以承受切削冲击而发生碎片崩裂。
6热裂纹与冷却液有关当倾注到切削刃上的冷却液不均匀时,切削刃的温度就会发生波动,引起刀片膨胀和收缩,从而导致切削刃出现裂纹。
磨损热裂纹变形崩刃2.2材料设计方案及优化比较2.2.1 铣刀材料的基本要求及设计方案1)高硬度和耐磨性:在常温下,切削部分材料必须具备足够的硬度才能切入工件;具有高的耐磨性,刀具才不磨损,延长使用寿命。
2)好的耐热性:刀具在切削过程中会产生大量的热量,尤其是在切削速度较高时,温度会很高,因此,刀具材料应具备好的耐热性,既在高温下仍能保持较高的硬度,有能继续进行切削的性能,这种具有高温硬度的性质,又称为热硬性或红硬性。
3)高的强度和好的韧性:在切削过程中,刀具要承受很大的冲击力,所以刀具材料要具有较高的强度,否则易断裂和损坏。
由于铣刀会受到冲击和振动,因此,铣刀材料还应具备好的韧性,才不易崩刃,碎裂等特点,故设计以下方案。
方案一 W18Cr4VW18Cr4V为钨系高速钢,具有高的硬度、红硬性及高温硬度。
其热处理范围较宽淬火不易过热,热处理过程不易氧化脱碳,磨削加工性能较好。
该钢在500℃及600℃时硬度分别保持在HRC57~58及HRC52~53,对于大量的、一般的被加工材料具有良好的切削性能。
加工流程:铸型→锻造→球化淬火→退火→回火→成品①用途:形状复杂的小型刀具②成分含量: 含碳量0.7--0.8%,含钨量17.5--19%,含铬量3.80--4.4%,含钒量1.0--1.4%,含硅量小于0.4%,含锰量小于0.4%,含钼量小于0.3%。
③成分特点:在钢中,碳主要与铬、钨、钼和钒(碳化物的形成元素)等形成碳化物,以提高硬度、耐磨性及红硬性。
钨是提高红硬性的主要元素,它在钢中形成碳化物。
加热时,一部分碳化物溶入奥氏体,淬火后形成含有大量钨及其他合金元素、有很高回火稳定性的马氏体。
在回火时,一部分钨以碳化物的形式弥散析出,造成二次硬化。
在加热时,未溶的碳化物则起到阻止奥氏体晶粒长大的作用.钒能显著地提高高速钢的红硬性、硬度及耐磨性。
钒形成的碳化物在加热时,部分溶入奥氏体,回火时以细小的质点弥散析出,造成二次硬化而提高钢的红硬性。
铬在高速钢中主要是增加其淬透性,同时还能提高钢的抗氧化脱碳和抗腐蚀能力。