SMT线体介绍
FPC及SMT介绍

FPC及SMT介绍目录Index§电路板常见名词§FPC种类§FPC设计基本原则§FPC流程简介§SMT基本知识§考虑FPC工艺等要求,研发在设计中应注意的问题(11/01补充)Manufacturing Types of FPCFPC的种类FPC(Flexible Printed Circuit)即柔性印刷线路板具有轻、薄、易折曲等特点广泛应用于激光头、随身听、电子表、摄像机、打印机、传真机、手机等电子领域按结构分为:§单面板§双面板§多层板§软硬复合板无胶系材料特征§耐热性:无胶软板基材由于没有耐热差的接着剂,所以耐热性相当优异,且长期使用温度可达300以上§难燃性:无卤素添加可通过UL94V-O规格,符合无卤环保需求§轻量性:厚度降低,减少重量,达到薄型化目的§电气特性:减少离子迁移效应(Ion Migration),减少线路间短路现象§耐药品性:减少接着剂受化学药品之侵蚀,而提高铜箔与基材间的抗撕强度§尺寸安全性:无胶软板基材尺寸变化尺寸变化受温度影响相当小,即使高温(300下)尺寸变化率仍在0。
1%之内§高密度化:Fine line 高密度线路设计趋动2 layer 材料大量化使用§耐屈折高:耐屈挠之表现可适应高度动态屈挠设计之需求FPC设计基本原则FPC设计基准书.xls裁剪Cutting/shearing§一般软板材料多为卷状方式制造,为了符合产品不同尺寸要求,必需依不同产品尺寸规划设计最佳的利用率,而依规划结果将材料分裁成需要的尺寸。
§规划限制:单面板:作业长度250~350mm较佳单一铜箔:作业长度320mm较佳双面板:作业长度250~350mm较佳多层板:作业长度180~300mm较佳钻孔CNC Drilling§一般电路板为符合客户设计要求及制程需求,都会在材料(单/双面板)上以机械钻孔方式钻出定位孔、测试孔、零件孔等。
smt生产线
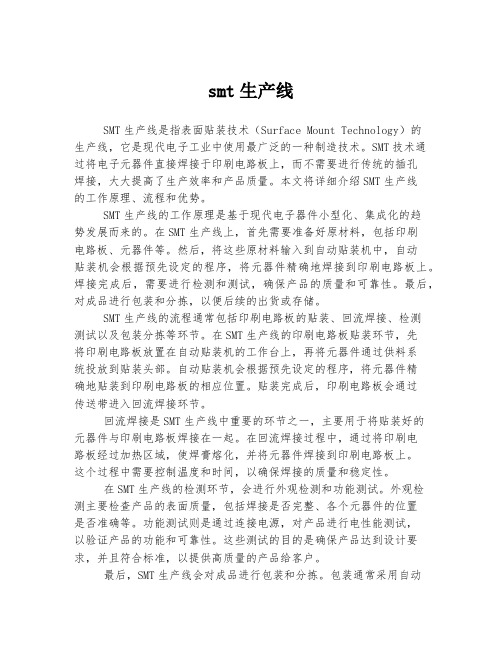
smt生产线SMT生产线是指表面贴装技术(Surface Mount Technology)的生产线,它是现代电子工业中使用最广泛的一种制造技术。
SMT技术通过将电子元器件直接焊接于印刷电路板上,而不需要进行传统的插孔焊接,大大提高了生产效率和产品质量。
本文将详细介绍SMT生产线的工作原理、流程和优势。
SMT生产线的工作原理是基于现代电子器件小型化、集成化的趋势发展而来的。
在SMT生产线上,首先需要准备好原材料,包括印刷电路板、元器件等。
然后,将这些原材料输入到自动贴装机中,自动贴装机会根据预先设定的程序,将元器件精确地焊接到印刷电路板上。
焊接完成后,需要进行检测和测试,确保产品的质量和可靠性。
最后,对成品进行包装和分拣,以便后续的出货或存储。
SMT生产线的流程通常包括印刷电路板的贴装、回流焊接、检测测试以及包装分拣等环节。
在SMT生产线的印刷电路板贴装环节,先将印刷电路板放置在自动贴装机的工作台上,再将元器件通过供料系统投放到贴装头部。
自动贴装机会根据预先设定的程序,将元器件精确地贴装到印刷电路板的相应位置。
贴装完成后,印刷电路板会通过传送带进入回流焊接环节。
回流焊接是SMT生产线中重要的环节之一,主要用于将贴装好的元器件与印刷电路板焊接在一起。
在回流焊接过程中,通过将印刷电路板经过加热区域,使焊膏熔化,并将元器件焊接到印刷电路板上。
这个过程中需要控制温度和时间,以确保焊接的质量和稳定性。
在SMT生产线的检测环节,会进行外观检测和功能测试。
外观检测主要检查产品的表面质量,包括焊接是否完整、各个元器件的位置是否准确等。
功能测试则是通过连接电源,对产品进行电性能测试,以验证产品的功能和可靠性。
这些测试的目的是确保产品达到设计要求,并且符合标准,以提供高质量的产品给客户。
最后,SMT生产线会对成品进行包装和分拣。
包装通常采用自动化方式进行,将成品放入适当的包装盒或袋中,并进行标识。
分拣则是将成品按照订单或目的地进行分类和整理,以便后续的出货或存储。
SMT线体组建项目方案
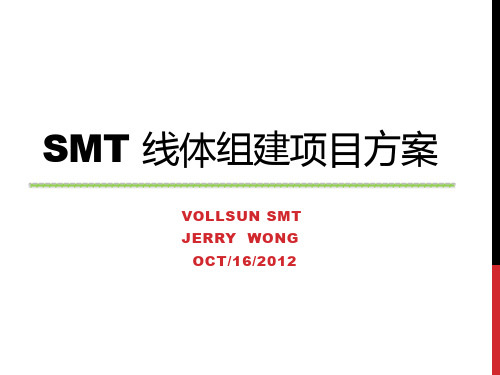
materials counter( 物料计数器) power flat socket(电源排插)
plier(镊子) antistatic brush(静电刷) antistatic box (静电导电盒) antistatic coat,caps,lipper( 静电衣帽鞋) ESD wrist strap( 静电环) ESD test equipment(静电测试仪)
Magnifying glass(放大镜) microscope(显微镜)
Visual inspection table(目检工作台) QA Visual inspection table(QA工作台)
table(工作台) Visual inspection board (看板)
solder iron(烙铁) magazine(上板架) ESD trolley(静电箱) hand trolley(拖车)
Caliper(游标卡尺)
zebra crossing(斑马胶线)
vacuum cleaner(吸尘器) air gun(气枪)
SMT repair tools(SMT ME 维修工具)
Application description
Q'TY
Unit Price
Total Amount
air supply (供应气源)
DEK,GKG,MPM
接驳台 贴片机1 接驳台 贴片机2 接驳台
自动运输PCB至第1台贴片机 机器小型元件自动贴片
自动运输PCB至第2台贴片机 机器异型元件自动贴片 自动运输PCB至回流炉
Fuji, Siemens,assembleon
表面组装技术(SMT工艺)
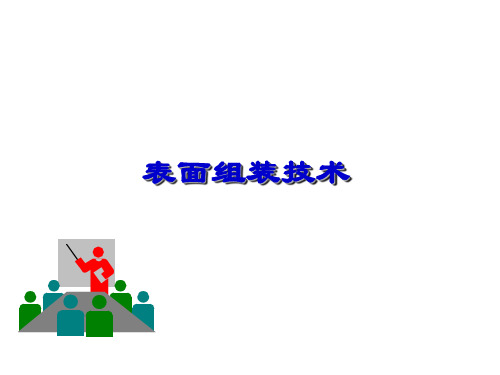
5、与PCB表面非常接近,间隙小,清洗困难。
二、分类: 1、按功能分为三大类(两类:SMC、SMD) 无源元件(SMC):片式电阻、电容、电感等 有源元件(SMD):SOT、SOP、PLCC、QFP、LCCC等
机电元件:异型元件,如继电器、开关、变压器等
2、按结构形状分:薄片矩形、圆柱形、扁平异型
A B
A面回流焊 清洗
B面胶水固化
翻板
B面波峰焊
检测
3.单面混合组装工艺流程
⑴ 先贴法 来料检测 B面点胶
A B
B面贴装元器件
A面插装元器件
B面波峰焊
翻板
检测
B面胶水固化
清洗
3.单面混合组装工艺流程
A B
⑵ 后贴法
来料检测 B面胶水固化 翻板 A面插装元器件 B面贴装元器件 B面波峰焊 检测 翻板 B面点胶 清洗
★ 环境温度
最佳: 23±3 ℃
一般:17~28℃
极限:15~35℃
★ 环境湿度 45%~70%RH
SMT发展趋势
一、绿色化生产 1、无铅焊料,无铅焊接 2、PCB制造过程中不再使用阻燃剂 3、使用无VOC助焊剂
二、元器件的发展 1、无源元件(小型化) 1812 1210 1206 0805 0603 0402 0201 01005 2、有源器件 SOT SOP PLCC QFP BGA CSP FC COB MCM
A
A B A B
4、双面混合组装
① ②
A B A B
二、基本工艺流程(两条
) ※ 先在印制电路板焊盘上印刷适量的焊膏,再将 片式元器件贴放到印制板规定位置上,最后将贴装 好元器件的印制板通过回流炉完成焊接过程。
※ 焊膏-回流焊工艺(表贴元器件)
第一章SMT介绍

第一章SMT介绍第一章 SMT 介绍SMT就是表面组装技术(Surface Mounted Technology)的缩写,是目前电子组装行业里最流行的一种技术和工艺。
表面组装技术是一种无需在印制板上钻插装孔,直接将表面组装元器件贴﹑焊到印制电路板表面规定位置上的电路装联技术。
具体的说,表面组装技术就是一定的工具将表面组装元器件引脚对准预先涂覆了了粘剂接剂和焊膏的焊盘图形上,把表面组装组件贴装元器件贴装到未钻安装孔的PCB表面上,然后经过波峰焊或再流焊使表面组装元器件和电路之间建立可靠的机械和电气连接。
一、SMT的特点:1. 组装密度高、电子产品体积小、重量轻,贴片元件的体积和重量只有传统插装元件的1/10左右,一般采用SMT之后,电子产品体积缩小40%~60%,重量减轻60%~80%。
2. 可靠性高、抗振能力强。
焊点缺陷率低。
3. 高频特性好。
减少了电磁和射频干扰。
4. 易于实现自动化,提高生产效率。
5. 降低成本达30%~50%。
节省材料、能源、设备、人力、时间等。
二、为什么要用表面贴装技术(SMT)?1. 电子产品追求小型化,以前使用的穿孔插件元件已无法缩小。
2. 电子产品功能更完整,所采用的集成电路(IC)已无穿孔元件,特别是大规模、高集成IC,不得不采用表面贴片元件。
3. 产品批量化,生产自动化,厂方要以低成本高产量,出产优质产品以迎合顾客需求及加强市场竞争力。
4. 电子元件的发展,集成电路(IC)的开发,半导体材料的多元应用。
5. 电子科技革命势在必行,追逐国际潮流。
三、SMT工艺流程及作用1.单面板生产流程供板印刷红胶(或锡浆) 贴装SMT元器件回流固化(或焊接) 检查测试包装2.双面板生产流程(1) 一面锡浆﹑一面红胶之双面板生产流程:供板丝印锡浆贴装SMT元器件回流焊接检查供板(翻面) 丝印红胶贴装SMT元器件回流固化波峰焊接检查包装(2) 双面锡浆板生产流程供板第一面(集成电路少,重量大的元器件少) 丝印锡浆贴装SMT元器件回流焊接检查供板第二面(集成电路多﹑重量大的元器件多) 丝印锡浆贴装SMT元器件回流焊接检查包装丝印:其作用是将焊膏或贴片胶漏印到PCB的焊盘上,为元器件的焊接做准备。
SMT基础知识介绍
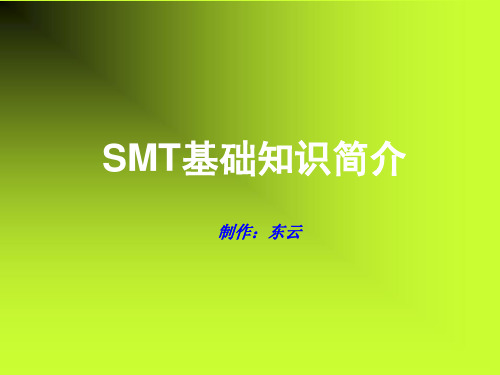
制作:东云
SMT基础知识简介
课程目录
一. SMT技术简介与特点 二. SMT生产线流程介绍 三. SMT生产线各工站作业简介 四. SMT的部门组织构架以及工作执掌
一. SMT技术简介与特点
1. SMT技术简介
SMT是英文Surface Mount Technology的缩写,
一. SMT技术简介与特点
2.SMT技术的优点:
1>零件组装密度高------一般来说,采用SMT可使电 子产品体积缩小40%~60%,重量减轻60%~85%. 2>可靠性高------SMT元件小而轻,抗震能力强.
3>高频特性好------SMT元件贴装牢固,通常为无引 脚或短引脚零件,降低了寄生电感和寄生电容的影 响,提高了电路的高频特性.
三. SMT生产线各工站作业简介
第五站:泛用机贴片作业 该工站的主要作业内容是,在PCB上装贴体积较大 形状不规则的材料(包含异型材料).例如包括BGA在内的各 种封装的IC,各锺连接器等.置放零件的速度为 2~10秒/颗不等. 泛用机的生产作业过程相对比较复杂.在将零件置 放到PCB上之前,先要对零件进行光学影像处理,检查零件 外型是否与数据库数据相符.对于特别重要零件,还要做光 学影像校正后才做零件摆放,就是用摄像头检视零件脚与
4>便于自动化生产------减少人力作业.稳定产品质量. 节省材料,缩短生产周期等.
一. SMT技术简介与特点
3.SMT技术的缺点:
1>生产设备投入成本较高------一条SMT生产线机 器设备的购买成本非常高.日常的设备维修成本也 是一比不小的开支.再加上设备的更新换代越来越
快.这些都是一家企业进入SMT行业的门槛.
smt线体实施方案
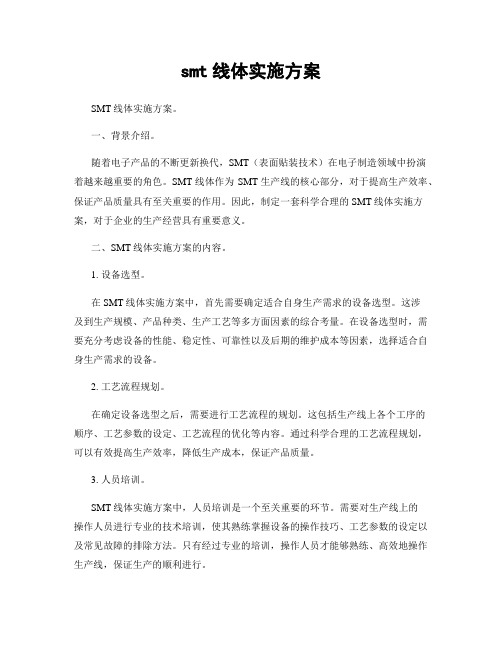
smt线体实施方案SMT线体实施方案。
一、背景介绍。
随着电子产品的不断更新换代,SMT(表面贴装技术)在电子制造领域中扮演着越来越重要的角色。
SMT线体作为SMT生产线的核心部分,对于提高生产效率、保证产品质量具有至关重要的作用。
因此,制定一套科学合理的SMT线体实施方案,对于企业的生产经营具有重要意义。
二、SMT线体实施方案的内容。
1. 设备选型。
在SMT线体实施方案中,首先需要确定适合自身生产需求的设备选型。
这涉及到生产规模、产品种类、生产工艺等多方面因素的综合考量。
在设备选型时,需要充分考虑设备的性能、稳定性、可靠性以及后期的维护成本等因素,选择适合自身生产需求的设备。
2. 工艺流程规划。
在确定设备选型之后,需要进行工艺流程的规划。
这包括生产线上各个工序的顺序、工艺参数的设定、工艺流程的优化等内容。
通过科学合理的工艺流程规划,可以有效提高生产效率,降低生产成本,保证产品质量。
3. 人员培训。
SMT线体实施方案中,人员培训是一个至关重要的环节。
需要对生产线上的操作人员进行专业的技术培训,使其熟练掌握设备的操作技巧、工艺参数的设定以及常见故障的排除方法。
只有经过专业的培训,操作人员才能够熟练、高效地操作生产线,保证生产的顺利进行。
4. 质量控制。
质量控制是SMT线体实施方案中的一个重要环节。
需要建立科学合理的质量控制体系,包括原材料的检验、生产过程中的质量监控以及成品的检测等环节。
只有通过严格的质量控制,才能够保证产品的质量稳定可靠。
5. 设备维护。
设备的维护保养是SMT线体实施方案中不可忽视的一环。
需要建立健全的设备维护保养体系,包括定期的设备维护保养计划、设备故障的及时处理等内容。
只有通过科学的设备维护保养,才能够保证设备的长期稳定运行。
三、总结。
SMT线体实施方案的制定需要全面考虑设备选型、工艺流程规划、人员培训、质量控制以及设备维护等多个方面的内容。
只有通过科学合理的实施方案,才能够提高生产效率、保证产品质量,从而赢得市场竞争的优势。
SMT贴片生产线的设计资料
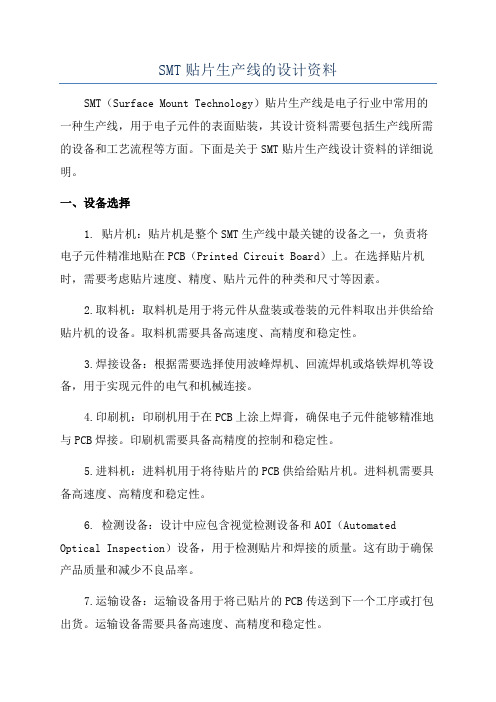
SMT贴片生产线的设计资料SMT(Surface Mount Technology)贴片生产线是电子行业中常用的一种生产线,用于电子元件的表面贴装,其设计资料需要包括生产线所需的设备和工艺流程等方面。
下面是关于SMT贴片生产线设计资料的详细说明。
一、设备选择1. 贴片机:贴片机是整个SMT生产线中最关键的设备之一,负责将电子元件精准地贴在PCB(Printed Circuit Board)上。
在选择贴片机时,需要考虑贴片速度、精度、贴片元件的种类和尺寸等因素。
2.取料机:取料机是用于将元件从盘装或卷装的元件料取出并供给给贴片机的设备。
取料机需要具备高速度、高精度和稳定性。
3.焊接设备:根据需要选择使用波峰焊机、回流焊机或烙铁焊机等设备,用于实现元件的电气和机械连接。
4.印刷机:印刷机用于在PCB上涂上焊膏,确保电子元件能够精准地与PCB焊接。
印刷机需要具备高精度的控制和稳定性。
5.进料机:进料机用于将待贴片的PCB供给给贴片机。
进料机需要具备高速度、高精度和稳定性。
6. 检测设备:设计中应包含视觉检测设备和AOI(Automated Optical Inspection)设备,用于检测贴片和焊接的质量。
这有助于确保产品质量和减少不良品率。
7.运输设备:运输设备用于将已贴片的PCB传送到下一个工序或打包出货。
运输设备需要具备高速度、高精度和稳定性。
二、工艺流程1.PCB准备:首先将PCB从仓库中取出,并进行清洁和检查。
确保PCB符合要求,并清除表面的污垢和杂质。
2.印刷焊膏:使用印刷机将焊膏均匀地涂在PCB上。
确保焊膏的厚度和精度符合要求。
3.进料和贴片:将准备好的PCB送入进料机,通过贴片机将电子元件精确地贴在PCB上。
贴片机按照预定的规则和程序,自动将各种电子元件贴在正确的位置。
4.焊接:通过波峰焊机、回流焊机或烙铁焊机等设备,将贴片后的PCB进行焊接,保证电子元件能够电气和机械连接。
5.检测:通过视觉检测设备和AOI设备检测贴片和焊接的质量。
SMT线体介绍
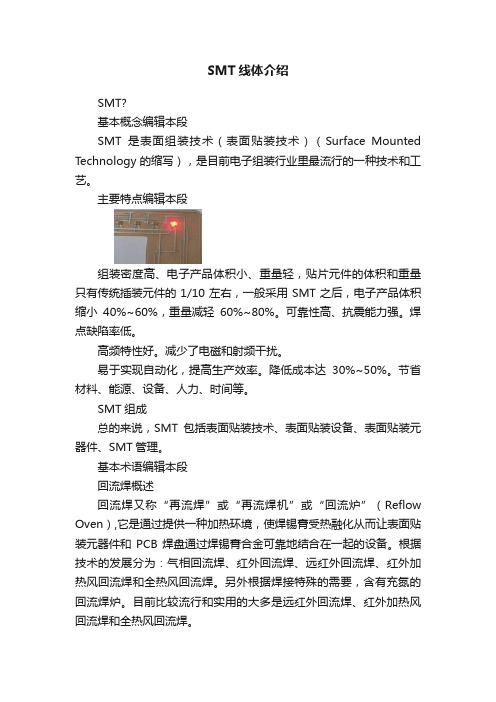
SMT线体介绍SMT?基本概念编辑本段SMT是表面组装技术(表面贴装技术)(Surface Mounted Technology的缩写),是目前电子组装行业里最流行的一种技术和工艺。
主要特点编辑本段组装密度高、电子产品体积小、重量轻,贴片元件的体积和重量只有传统插装元件的1/10左右,一般采用SMT之后,电子产品体积缩小40%~60%,重量减轻60%~80%。
可靠性高、抗震能力强。
焊点缺陷率低。
高频特性好。
减少了电磁和射频干扰。
易于实现自动化,提高生产效率。
降低成本达30%~50%。
节省材料、能源、设备、人力、时间等。
SMT组成总的来说,SMT包括表面贴装技术、表面贴装设备、表面贴装元器件、SMT管理。
基本术语编辑本段回流焊概述回流焊又称“再流焊”或“再流焊机”或“回流炉”(Reflow Oven),它是通过提供一种加热环境,使焊锡膏受热融化从而让表面贴装元器件和PCB焊盘通过焊锡膏合金可靠地结合在一起的设备。
根据技术的发展分为:气相回流焊、红外回流焊、远红外回流焊、红外加热风回流焊和全热风回流焊。
另外根据焊接特殊的需要,含有充氮的回流焊炉。
目前比较流行和实用的大多是远红外回流焊、红外加热风回流焊和全热风回流焊。
红外再流焊(1)第一代-热板式再流焊炉(2)第二代-红外再流焊炉热能中有80%的能量是以电磁波的形式――红外线向外发射的。
其波长在可见光之上限~ 到1mm 之间,~ 为近红外;~ 为中红外;~1000um 为远红外,微波则在远红外之上。
升温的机理:当红外波长的振动频率与被辐射物体分子间的振动频率一致时,就会产生共振,分子的激烈振动意味着物体的升温。
波长为1~8um第四区温度设置最高,它可以导致焊区温度快速上升,提高泣湿力。
优点:使助焊剂以及有机酸和卤化物迅速水利化从而提高润湿能力;红外加热的辐射波长与吸收波长相近似,因此基板升温快、温差小;温度曲线控制方便,弹性好;红外加热器效率高,成本低。
SMT简介

2.1PTH------(Plate through hole),是人工插件,
然后再人工浸锡(现在用波峰焊代替)。 2.2 Ai ------(Auto insert),机器自动插件,再过
波峰。
SMT 发展与未来
3.由于在80年代末兴起一些片式电容,电阻,电
极体,QFP(Quad Flat Package),BGA(Ball Grid Array)等电子元件,PTH/AI已经不能满足电子元
Pop (packge of packge),flip chip(到装芯片)
SMT 机器展示
锡膏印刷机
DEK 英国
MPM 美国
GKG 中国
SMT 机器展示
一流贴片机
Siemens 德国 hs20-,27,50,60,d,x
Fuji nxt 日本 Cp3,4,6,7,8,nxt1,2
panasonic npm 日本 MV2C,F,B, CM88,CM402,602
SMT 机器展示 二流贴片机
Yamaha 日本
Philip 荷兰 介于一流与二流 之间
JUKI
日本
universal
美国
SMT 机器展示
三流贴片机
sony
samsung
Casio
I pulse
SMT 机器展示 回流炉
炉温曲线
HELLER,BTU SPLINE---美国, JT,SUNESAT等---中国
Jerry wong Oct 22 2012
SMT发展与未来发展 SMT机器 SMT模块 SMT流程 SMT上、下游 SMT工厂评判 SMT线体(Vollsun)
SMT 发展与未来
有电子组装的地方就有SMT,SMT是现在电子制 造组装最流行的一种技术。 SMT(surface mount technology)发展史: 1.始于80年代末,90年代初,盛行于90-20年代; 2.以前仅限:
SMT概述
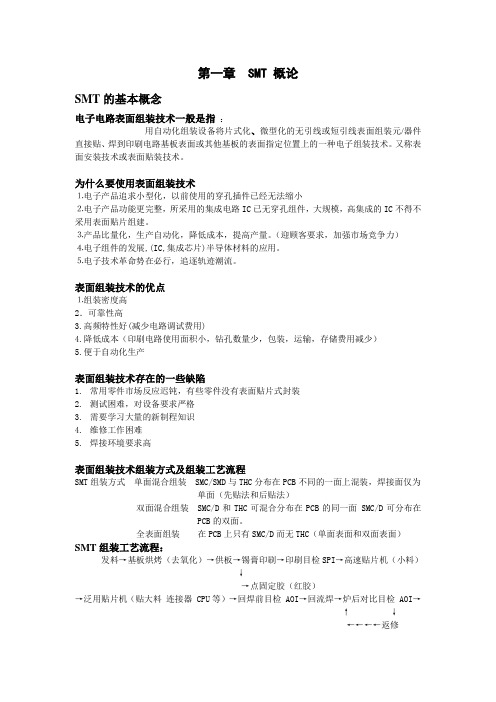
第一章 SMT 概论SMT的基本概念电子电路表面组装技术一般是指:用自动化组装设备将片式化、微型化的无引线或短引线表面组装元/器件直接贴、焊到印刷电路基板表面或其他基板的表面指定位置上的一种电子组装技术。
又称表面安装技术或表面贴装技术。
为什么要使用表面组装技术⒈电子产品追求小型化,以前使用的穿孔插件已经无法缩小⒉电子产品功能更完整,所采用的集成电路IC已无穿孔组件,大规模,高集成的IC不得不采用表面贴片组建。
⒊产品比量化,生产自动化,降低成本,提高产量。
(迎顾客要求,加强市场竞争力)⒋电子组件的发展,(IC,集成芯片)半导体材料的应用。
⒌电子技术革命势在必行,追逐轨迹潮流。
表面组装技术的优点⒈组装密度高2.可靠性高3.高频特性好(减少电路调试费用)4.降低成本(印刷电路使用面积小,钻孔数量少,包装,运输,存储费用减少)5.便于自动化生产表面组装技术存在的一些缺陷1.常用零件市场反应迟钝,有些零件没有表面贴片式封装2.测试困难,对设备要求严格3.需要学习大量的新制程知识4.维修工作困难5.焊接环境要求高表面组装技术组装方式及组装工艺流程SMT组装方式单面混合组装 SMC/SMD与THC分布在PCB不同的一面上混装,焊接面仅为单面(先贴法和后贴法)双面混合组装 SMC/D和THC可混合分布在PCB的同一面 SMC/D可分布在PCB的双面。
全表面组装在PCB上只有SMC/D而无THC(单面表面和双面表面)SMT组装工艺流程:发料→基板烘烤(去氧化)→供板→锡膏印刷→印刷目检SPI→高速贴片机(小料)↓→点固定胶(红胶)→泛用贴片机(贴大料连接器 CPU等)→回焊前目检 AOI→回流焊→炉后对比目检 AOI→↑↓←←←←返修插件→波峰焊→ICT/FCT测试→装配/目检→品检→入库→市场↑↓↑↓←←←返修←返修1英尺(Feet)=12英寸 1英寸(inch)=25.4MM0201——0603 0402——1005 0603——1608 0805——2012 1206——3216 1210——3225 1812——4592 2010——5032第二章表面组装元件表面组装元器件俗称无引脚或段引脚元器件SMC 无源元件如片式电阻、电容、电感。
SMT基础知识介绍

三、SMT工艺技术 SMT工艺技术
2.5 波峰焊接炉
回流焊工程目的: 回流焊工程目的:
熔融的液态焊料﹐借助与泵的作用﹐ 熔融的液态焊料﹐借助与泵的作用﹐在焊料槽液面形成特定形状的焊 料波﹐插装了元器件的PCB置与传送链上﹐ 料波﹐插装了元器件的PCB置与传送链上﹐经过某一特定的角度以及一 PCB置与传送链上 定的浸入深度穿过焊料波峰而实现焊点焊接. 定的浸入深度穿过焊料波峰而实现焊点焊接.
四、SMT工艺与DFX SMT工艺与DFX 工艺与
DFM&DFR对SMT的影响实例 3.2 DFM&DFR对SMT的影响实例
单面组装
双面组装
三、SMT工艺技术 SMT工艺技术
单面组装
双面组装
三、SMT工艺技术 SMT工艺技术
SMT线体机台配置简介 2、外协厂SMT线体机台配置简介(深圳沙井优斯特为例) 外协厂SMT线体机台配置简介(深圳沙井优斯特为例)
对所有外协厂车间温湿度要求:摄氏24+/ 度以内, 24+/2.1 对所有外协厂车间温湿度要求:摄氏24+/-3度以内,湿度控
贴片机主要组成:供料系统、传输系统、感应系统、 贴片机主要组成:供料系统、传输系统、感应系统、
贴装系统、识别校正系统. 贴装系统、识别校正系统.
贴片机主要参数:贴装精度、相机分辨率、 贴片机主要参数:贴装精度、相机分辨率、重复精
度、8mm带宽料站数、气缸压力 8mm带宽料站数、 带宽料站数
三、SMT工艺技术 SMT工艺技术
三、SMT工艺技术 SMT工艺技术
贴片机(FUJI XP-143E,高速机贴装精度:0.05mm; 2.3 贴片机(FUJI XP-143E,高速机贴装精度:0.05mm; 泛用机贴片精度:0.04mm) 泛用机贴片精度:0.04mm) 贴片机工程目的:从轨道传入机器内的PCB PCB板 贴片机工程目的:从轨道传入机器内的PCB板,感应
SMT生产线规划图纸

上板机 上板机
移载机
SPI锡膏检测机
接驳台
贴片机
接驳台
AOI
接驳台
上板机 上板机
印刷机 印刷机
移载机
SPI锡膏检测机
接驳台
贴片机
AOI
接驳台
接驳台
SMT生产线体规划图
移载机
接驳台 (双轨)
氮气回流焊(双规)
AOI
移载机
接驳台
检验台
检验台
AOI 接驳台
接驳台
接驳台
接驳台
AOI
贴片机
SPI锡膏检测机
1
上板机 4台
10 回流焊 1台
氮气/双轨
2
印刷机 4台
11 检验台 2张
3 短移载机 2台
印刷位
4
SPI
2台
5
接驳台 8台
单轨
6
贴片机 2台
7
AOI
4台
炉前/后
8 长移载机 2台
合/分
9
接驳台 1台
双轨
印刷机 印刷机
印刷机 印刷机
移载机
SPI锡膏检测机
接驳台
贴片机
接驳台
AOI
接驳台
上板机 上板机
印刷机 印刷机
印刷机 印刷机
移载机
上板机 上板机
印刷机 印刷机
移载机
SPI锡膏检测机
接驳台
贴片机
AOI 接驳台
接驳台
移载机
接驳台 (双轨)
氮气回流焊(双规)
AOI
移载机
接驳台
检验台
AOI 接驳台
检验台
两条SMT生产线使用设备配置说明
SMT线体介绍
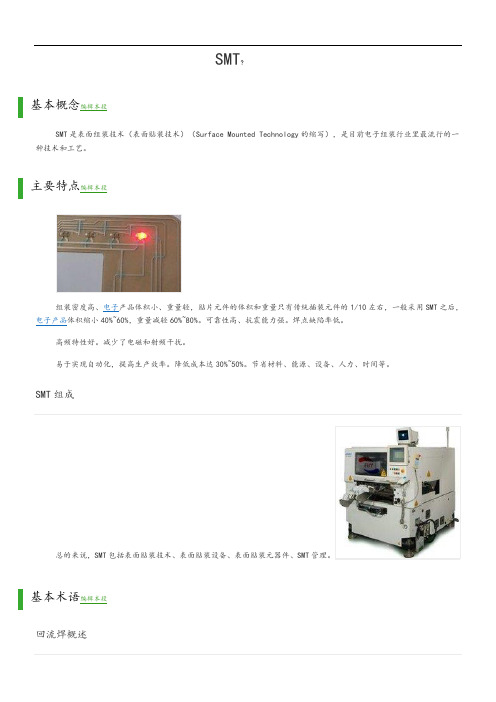
SMT?基本概念编辑本段SMT是表面组装技术(表面贴装技术)(Surface Mounted Technology的缩写),是目前电子组装行业里最流行的一种技术和工艺。
主要特点编辑本段组装密度高、电子产品体积小、重量轻,贴片元件的体积和重量只有传统插装元件的1/10左右,一般采用SMT之后,电子产品体积缩小40%~60%,重量减轻60%~80%。
可靠性高、抗震能力强。
焊点缺陷率低。
高频特性好。
减少了电磁和射频干扰。
易于实现自动化,提高生产效率。
降低成本达30%~50%。
节省材料、能源、设备、人力、时间等。
SMT组成总的来说,SMT包括表面贴装技术、表面贴装设备、表面贴装元器件、SMT管理。
基本术语编辑本段回流焊概述回流焊又称“再流焊”或“再流焊机”或“回流炉”(Reflow Oven),它是通过提供一种加热环境,使焊锡膏受热融化从而让表面贴装元器件和PCB焊盘通过焊锡膏合金可靠地结合在一起的设备。
根据技术的发展分为:气相回流焊、红外回流焊、远红外回流焊、红外加热风回流焊和全热风回流焊。
另外根据焊接特殊的需要,含有充氮的回流焊炉。
目前比较流行和实用的大多是远红外回流焊、红外加热风回流焊和全热风回流焊。
红外再流焊(1)第一代-热板式再流焊炉(2)第二代-红外再流焊炉热能中有 80%的能量是以电磁波的形式――红外线向外发射的。
其波长在可见光之上限~ 到1mm 之间,~ 为近红外;~ 为中红外;~1000um 为远红外,微波则在远红外之上。
升温的机理:当红外波长的振动频率与被辐射物体分子间的振动频率一致时,就会产生共振,分子的激烈振动意味着物体的升温。
波长为1~8um第四区温度设置最高,它可以导致焊区温度快速上升,提高泣湿力。
优点:使助焊剂以及有机酸和卤化物迅速水利化从而提高润湿能力;红外加热的辐射波长与吸收波长相近似,因此基板升温快、温差小;温度曲线控制方便,弹性好;红外加热器效率高,成本低。
缺点:穿透性差,有阴影效应――热不均匀。
SMT自动化生产线方案

SMT自动化生产线方案一、背景介绍SMT(Surface Mount Technology)自动化生产线是一种先进的电子元器件表面贴装技术,它通过将电子元器件直接焊接在印刷电路板(PCB)表面,实现电子产品的高效生产。
为了提高生产效率和质量,许多电子创造企业正在积极引入SMT 自动化生产线。
本文将详细介绍SMT自动化生产线的方案。
二、SMT自动化生产线方案概述SMT自动化生产线方案包括以下几个关键环节:物料管理、贴装机、回流焊接、质检和包装。
下面将详细介绍每一个环节的方案。
1. 物料管理物料管理是SMT自动化生产线的基础,它包括物料采购、入库、库存管理和出库等环节。
为了实现高效的物料管理,可以采用以下方案:- 建立完善的供应商管理体系,与优质供应商建立长期合作关系,确保物料的质量和供应的稳定性。
- 引入物料管理系统,实现对物料的自动化管理,包括物料的采购计划、库存监控和出库跟踪等功能。
2. 贴装机贴装机是SMT自动化生产线的核心设备,它负责将电子元器件精确地贴装在PCB上。
为了实现高效的贴装,可以采用以下方案:- 选择适合生产规模的贴装机,考虑生产线的产能和贴装精度要求,选择具有高速度和高精度的贴装机。
- 配备自动上料系统,实现对电子元器件的自动供料,提高生产效率。
- 引入视觉识别系统,实现对电子元器件的自动定位和校正,提高贴装精度。
3. 回流焊接回流焊接是将贴装好的电子元器件与PCB焊接在一起的过程。
为了实现高质量的焊接,可以采用以下方案:- 选择适合生产规模的回流焊接设备,考虑生产线的产能和焊接质量要求,选择具有稳定性和可靠性的设备。
- 控制回流焊接的温度曲线,确保焊接过程中的温度均匀分布,避免焊接缺陷的产生。
- 引入可视化检测系统,实时监控焊接质量,及时发现并修复焊接缺陷。
4. 质检质检是SMT自动化生产线中不可或者缺的环节,它负责对贴装好的PCB进行检测,以确保产品质量。
为了实现高效的质检,可以采用以下方案:- 引入自动光学检测系统,实现对PCB的自动检测,包括焊接质量、元器件位置和PCB电气性能等方面的检测。
SMT详细解读

SMT详细解读一、SMT是什么意思?SMT(Surface Mount Technology表面贴装技术)是利用锡膏印刷机、贴片机、回流焊等专业自动组装设备将表面组装元件(类型包括电阻、电容、电感等)直接贴、焊到电路板表面的一种电子接装技术,是目前电子组装行业里最流行的一种技术和工艺。
SMT生产线SMT生产线的主要组成部分为:由表面组装元件、电路基板、组装设计、组装工艺;主要生产设备包括上板机、印刷机、送板机、点胶机、贴装机、再流焊炉和波峰焊机。
辅助设备有检测设备、返修设备、清洗设备、干燥设备和物料存储设备等。
二、SMT工艺优化表面贴装元件(SMD)生产的成本和质量,必须着眼于整体的生产方法。
只有在把生产线和供应链(从供应商到顾客)作为一个整体来考虑时才能够在这方面取得进展。
工艺工程师的工作和专用工具的使用一天天变得更重要。
1.成本质量工艺工艺工程师的主要工作仍然是准备、执行和监视生产过程,但是,有了更高的要求。
今天,工艺工程师必须在执行之前,能够准确地界定或者预测工艺上的这些改变会给重要的性能指标带来什么结果。
为了顺利地完成这些任务,作为工艺工程师,他的必须取得最高级的资格。
他们热心于作出改进,他们还需要有明确的方向,开放,善于合作;作为工艺工程师,他要管理质量,要主动地编制计划,需要有很强的分析能力以及统计工艺管理(SPC)技术的知识。
对于工艺的要求提高了,同时,可以使用的工具也在改进。
对于数据的记录和收集,过去需要许多时间,现在可以由最新的机器和工具自动完成。
稳步改进程序和提高效用,可以帮助你分析大量的数据、自动监测最重要的工艺参数。
当工艺改变时,这些工具能够在数秒钟内计算出这种改变对整个工艺的影响。
因此,工程师可以用数据模型和场景技术,在生产线以外对新工艺进行模拟,不必在生产线上进行反复试验。
2.用于产品生命期所有阶段的工具产品的设计阶段。
现在的一些新型贴片机有许多软件模块和系统解决办法,工艺工程师可以用来设计、控制和监测许多条生产线的SMT 工艺过程。
SMT简介(精)
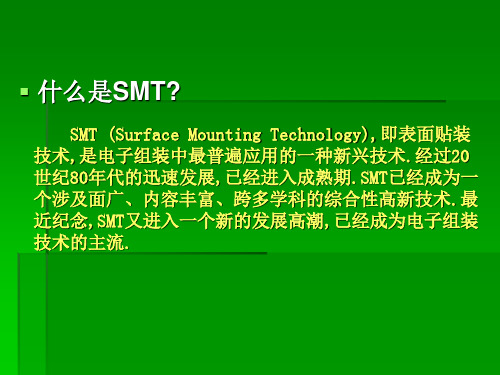
迴焊前目檢
Visual Insp.b/f Reflow
迴流焊
Reflow Soldering
爐后比對目檢
測試
修理
Rework/Repair
插件
M.I / A.I
波峰焊
Wave Soldering
裝配/目檢 Assembly/VI
品檢
入庫 Stock
修理
Rework/Repair
高速貼片機(MV2VB) -反射及透射識別系統 -12個旋轉工作頭, 5種Nozzle -最快貼片速度: 0.1 Sec/Comp -貼片零件種類: 0402mm Chip~32*32mmQFP<6.5mmHeight. 相關制程條件: ---貼片參數 ---Program ---Feeder &Nozzle ---來料
1.1SMT简介
1.THT与SMT
技术缩写
表1.1.1是THT与SMT区别
年代 代表元器件 安装基板 安装方法 焊接技术
单、双面 PCB 手工/半手 工插装 手工浸焊
通 空 安 装 表 面 安 装
20世纪 晶体管,轴向引 60~70年代 线元件
THT
70~80年代
单、双列直插 IC,轴向引线 元器件编带
SMT概述
SMT是无需对印制板钻插装孔,直接将片式元器件或 适合与表面组装的微型元件器件贴、焊到印制板基板表面 规定位置上的装联技术. 由于各种片式元器件的几何尺寸和占空间体积比查装 元器件小得多,这种组装形式具有组装形式具有结构紧凑、 体积小、耐振动、抗冲击、高频特性和生产效率高等优点. 采用双面贴装时密度是插件组装的1/5左右,从面使印制板 面积节约了60%-70%,重量减轻80%以上. SMT是电子装联技术的发展方向,已成为世界电子整 机组装技术的主流.我国SMT的应用起步于80年代初期,最 初从美、日等国成套引进了SMT生产线用于彩电调谐器 生产,随后用于录像机、摄像机及袖珍式高档多波段收音 机、随身听等生产中.近几年在计算机、通信设备、航空 航天电子产品中也逐渐得到应用.
- 1、下载文档前请自行甄别文档内容的完整性,平台不提供额外的编辑、内容补充、找答案等附加服务。
- 2、"仅部分预览"的文档,不可在线预览部分如存在完整性等问题,可反馈申请退款(可完整预览的文档不适用该条件!)。
- 3、如文档侵犯您的权益,请联系客服反馈,我们会尽快为您处理(人工客服工作时间:9:00-18:30)。
SMT基本概念编辑本段SMT是表面组装技术(表面贴装技术)(Surface Mounted Technology的缩写),是目前电子组装行业里最流行的一种技术和工艺。
主要特点编辑本段组装密度高、电子产品体积小、重量轻,贴片元件的体积和重量只有传统插装元件的1/10左右,一般采用SMT之后,电子产品体积缩小40%~60%,重量减轻60%~80%。
可靠性高、抗震能力强。
焊点缺陷率低。
高频特性好。
减少了电磁和射频干扰。
易于实现自动化,提高生产效率。
降低成本达30%~50%。
节省材料、能源、设备、人力、时间等。
SMT组成总的来说,SMT包括表面贴装技术、表面贴装设备、表面贴装元器件、SMT管理。
基本术语编辑本段回流焊概述回流焊又称“再流焊”或“再流焊机”或“回流炉”(Reflow Oven),它是通过提供一种加热环境,使焊锡膏受热融化从而让表面贴装元器件和PCB焊盘通过焊锡膏合金可靠地结合在一起的设备。
根据技术的发展分为:气相回流焊、红外回流焊、远红外回流焊、红外加热风回流焊和全热风回流焊。
另外根据焊接特殊的需要,含有充氮的回流焊炉。
目前比较流行和实用的大多是远红外回流焊、红外加热风回流焊和全热风回流焊。
红外再流焊(1)第一代-热板式再流焊炉(2)第二代-红外再流焊炉热能中有 80%的能量是以电磁波的形式――红外线向外发射的。
其波长在可见光之上限~ 到1mm 之间,~ 为近红外;~ 为中红外;~1000um 为远红外,微波则在远红外之上。
升温的机理:当红外波长的振动频率与被辐射物体分子间的振动频率一致时,就会产生共振,分子的激烈振动意味着物体的升温。
波长为1~8um第四区温度设置最高,它可以导致焊区温度快速上升,提高泣湿力。
优点:使助焊剂以及有机酸和卤化物迅速水利化从而提高润湿能力;红外加热的辐射波长与吸收波长相近似,因此基板升温快、温差小;温度曲线控制方便,弹性好;红外加热器效率高,成本低。
缺点:穿透性差,有阴影效应――热不均匀。
对策:在再流焊中增加了热风循环。
(3)第三代-红外热风式再流焊。
对流传热的快慢取决于风速,但过大的风速会造成元件移位并助长焊点的氧化,风速控制在~s。
热风的产生有两种形式:轴向风扇产生(易形成层流,其运动造成各温区分界不清)和切向风扇(风扇安装在加热器外侧,产生面板涡流而使得各温区可精确控制)。
基本结构与温度曲线的调整:1. 加热器:管式加热器、板式加热器铝板或不锈钢板1. 单面板:(1) 在贴装与插件焊盘同时印锡膏;(2) 贴放 SMC/SMD;(3) 插装 TMC/TMD;(4) 再流焊2. 双面板(1) 锡膏-再流焊工艺,完成双面片式元件的焊接;(2) 然后在 B 面的通孔元件焊盘上涂覆锡膏;(3) 反转 PCB 并插入通孔元件;(4) 第三次再流焊。
1. 与SMB 的相容性,包括焊盘的润湿性和SMB 的耐热性;2. 焊点的质量和焊点的抗张强度;3. 焊接工作曲线:预热区:升温率为~ 度/s,温度在90~100s 内升至150 度保温区:温度为 150~180 度,时间40~60s再流区:从180到最高温度250 度需要10~15s,回到保温区约30s快速冷却无铅焊接温度(锡银铜)217度4、 Flip Chip 再流焊技术汽相再流焊又称汽相焊(Vapor Phase Soldering,VPS),美国最初用于厚膜集成电路的焊接,具有升温速度快和温度均匀恒定的优点,但传热介质FC-70 价格昂贵,且需FC-113,又是臭氧层损耗物质优点:1. 汽相潜热释放对SMA 的物理结构和几何形状不敏感,使组件均匀加热到焊接温度2. 焊接温度保持一定,无需采用温控手段,满足不同温度焊接的需要3. VPS 的汽相场中是饱和蒸气,含氧量低4. 热转化率高。
激光再流焊1. 原理和特点:利用激光束直接照射焊接部位,2. 焊点吸收光能转变成热能,加热焊接部位,使焊料熔化。
3. 种类:固体YAG(乙铝石榴石)激光器。
SMT组装工艺SMT组装工艺与焊接前的每一工艺步骤密切相关,其中包括资金投入、PCB设计、元件可焊性、组装操作、焊剂选择、温度/时间的控制、焊料及晶体结构等。
1 、焊料目前,波峰焊接最常用的焊料是共晶锡铅合金:锡63%;铅37%,应时刻掌握焊锡锅中的焊料温度,其温度应高于合金液体温度183℃,并使温度均匀。
过去,250℃的焊锡锅温度被视为“标准”。
随着焊剂技术的革新,整个焊锡锅中的焊料温度的均匀性得到了控制,并增设了预热器,发展趋势是使用温度较低的焊锡锅。
在230-240℃的范围内设置焊锡锅温度是很普遍的。
通常,组件没有均匀的热质量,要保证所有的焊点达到足够的温度,以便形成合格的焊点是必要的。
重要的问题是要提供足够的热量,提高所有引线和焊盘的温度,从而确保焊料的流动性,湿润焊点的两面。
焊料的温度较低就会降低对元件和基板的热冲击,有助于减少浮渣的形成,在较低的强度下,进行焊剂涂覆操作和焊剂化合物的共同作用下,可使波峰出口具有足够的焊剂,这样就可减少毛刺和焊球的产生。
焊锡锅中的焊料成份与时间有密切关系,即随着时间而变化,这样就导致了浮渣的形成,这就是要从焊接的组件上去除残余物和其它金属杂质的原因及在焊接工艺中锡损耗的原因。
以上这些因素可降低焊料的流动性。
在采购中,要规定的金属微量浮渣和焊料的锡含量的最高极限,在各个标准中,(如象IPC/J-STD-006都有明确的规定)。
在焊接过程中,对焊料纯度的要求在ANSI/J-STD-001B标准中也有规定。
除了对浮渣的限制外,对63%锡;37%铅合金中规定锡含量最低不得低于%。
波峰焊接组件上的金和有机泳层铜浓度聚集比过去更快。
这种聚集,加上明显的锡损耗,可使焊料丧失流动性,并产生焊接问题。
外表粗糙、呈颗粒状的焊点常常是由于焊料中的浮渣所致。
由于焊锡锅中的集聚的浮渣或组件自身固有的残余物暗淡、粗糙的粒状焊点也可能是锡含量低的征兆,不是局部的特种焊点,就是锡锅中锡损耗的结果。
这种外观也可能是在凝固过程中,由于振动或冲击所造成的。
焊点的外观就能直接体现出工艺问题或材料问题。
为保持焊料“满锅”状态和按照工艺控制方案对检查焊锡锅分析是很重要的。
由于焊锡锅中有浮渣而“倒掉”焊锡锅中的焊剂,通常来说是不必要的,由于在常规的应用中要求往锡锅中添加焊料,使锡锅中的焊料始终是满的。
在损耗锡的情况下,添加纯锡有助于保持所需的浓度。
为了监控锡锅中的化合物,应进行常规分析。
如果添加了锡,就应采样分析,以确保焊料成份比例正确。
浮渣过多又是一个令人棘手的问题。
毫无疑问,焊锡锅中始终有浮渣存在,在大气中进行焊接时尤其是这样。
使用“芯片波峰”这对焊接高密度组件很有帮助,由于暴露于大气的焊料表面太大,而使焊料氧化,所以会产生更多的浮渣。
焊锡锅中焊料表面有了浮渣层的覆盖,氧化速度就放慢了。
在焊接中,由于锡锅中波峰的湍流和流动而会产生更多的浮渣。
推荐使用的常规方法是将浮渣撇去,要是经常进行撇削的话,就会产生更多的浮渣,而且耗用的焊料更多。
浮渣还可能夹杂于波峰中,导致波峰的不稳定或湍流,因此要求对焊锡锅中的液体成份给予更多的维护。
如果允许减少锡锅中焊料量的话,焊料表面的浮渣会进入泵中,这种现象很可能发生。
有时,颗粒状焊点会夹杂浮渣。
最初发现的浮渣,可能是由粗糙波峰所致,而且有可能堵塞泵。
锡锅上应配备可调节的低容量焊料传感器和报警装置。
2 波峰在波峰焊接工艺中,波峰是核心。
可将预热的、涂有焊剂、无污物的金属通过传送带送到焊接工作站,接触具有一定温度的焊料,而后加热,这样焊剂就会产生化学反应,焊料合金通过波峰动力形成互连,这是最关键的一步。
目前,常用的对称波峰被称为主波峰,设定泵速度、波峰高度、浸润深度、传送角度及传送速度,为达到良好的焊接特性提供全方位的条件。
应该对数据进行适当的调整,在离开波峰的后面(出口端)就应使焊料运行降速,并慢慢地停止运行。
PCB随着波峰运行最终要将焊料推至出口。
在最挂的情况下,焊料的表面张力和最佳化的板的波峰运行,在组件和出口端的波峰之间可实现零相对运动。
这一脱壳区域就是实现了去除板上的焊料。
应提供充分的倾角,不产生桥接、毛刺、拉丝和焊球等缺陷。
有时,波峰出口需具有热风流,以确保排除可能形成的桥接。
在板的底部装上表面贴装元件后,有时,补偿焊剂或在后面形成的“苛刻的波峰”区域的气泡,而进行的波峰整平之前,使用湍流芯片波峰。
湍流波峰的高竖直速度有助于保证焊料与引线或焊盘的接触。
在整平的层流波峰后面的振动部分也可用来消除气泡,保证焊料实现满意的接触组件。
焊接工作站基本上应做到:高纯度焊料(按标准)、波峰温度(230~250℃)、接触波峰的总时间(3~5秒钟)、印制板浸入波峰中的深度(50~80%),实现平行的传送轨道和在波峰与轨道平行状态下锡锅中焊剂含量。
3 波峰焊接后的冷却通常在波峰焊机的尾部增设冷却工作站。
为的是限制铜锡金属间化合物形成焊点的趋势,另一个原因是加速组件的冷却,在焊料没有完全固化时,避免板子移位。
快速冷却组件,以限制敏感元件暴露于高温下。
然而,应考虑到侵蚀性冷却系统对元件和焊点的热冲击的危害性。
一个控制良好的“柔和稳定的”、强制气体冷却系统应不会损坏多数组件。
使用这个系统的原因有两个:能够快速处理板,而不用手夹持,并且可保证组件温度比清洗溶液的温度低。
人们所关心的是后一个原因,其可能是造成某些焊剂残渣起泡的原因。
另一种现象是有时会出现与某些焊剂浮渣产生反应的现象,这样,使得残余物“清洗不掉”。
在保证焊接工作站设置的数据满足所有的机器、所有的设计、采用的所有材料及工艺材料条件和要求方面没有哪个定式能够达到这些要求。
必须了解整个工艺过程中的每一步操作。
4 结论总之,要获得最佳的焊接质量,满足用户的需求,必须控制焊接前、焊接中的每一工艺步骤,因为SMT的整个组装工艺的每一步骤都互相关联、互相作用,任一步有问题都会影内到整体的可靠性和质量。
焊接操作也是如此,所以应严格控制所有的参数、时间/温度、焊料量、焊剂成分及传送速度等等。
对焊接中产生的缺陷,应及早查明起因,进行分析,采取相应的措施,将影响质量的各种缺陷消灭在萌芽状态之中。
这样,才能保证生产出的产品.其他资料编辑本段印刷(红胶/锡膏)--> 检测(可选AOI全自动或者目视检测)-->贴装(先贴小器件后贴大器件:分高速贴片及集成电路贴装)-->检测(可选AOI 光学/目视检测)--> 焊接(采用热风回流焊进行焊接)--> 检测(可分AOI 光学检测外观及功能性测试检测)--> 维修(使用工具:焊台及热风拆焊台等)--> 分板(手工或者分板机进行切板)工艺流程简化为:印刷-------贴片-------焊接-------检修(每道工艺中均可加入检测环节以控制质量)其作用是将锡膏呈45度角用刮刀漏印到PCB的焊盘上,为元器件的焊接做准备。