Moldflow在气体辅助注塑成型中的应用分析
Moldflow在注塑成型模拟分析中的应用
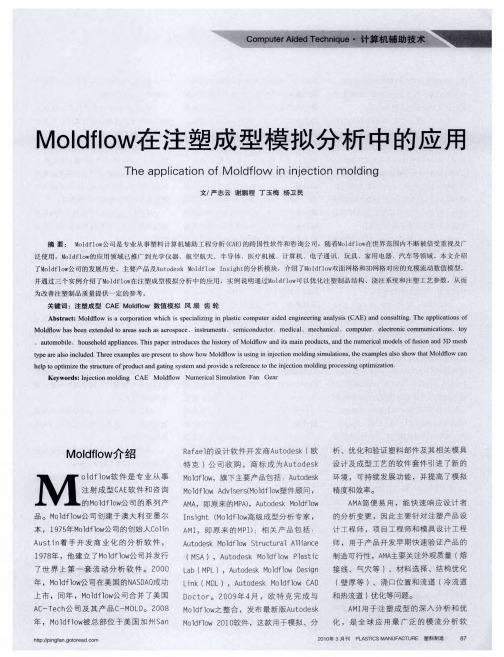
( MS A )
La b Li
n c
Au t
,
o
de
o
s
k
Mo l d f l o w
Pla s t i c
制造 可 行性
A MA 主 要 关 注 外 观 质 量 (
、
熔
( MP L )
Au t
,
d e s k Mo l d f l o w
o
De s i g n CAD
接线
、
气穴等 )
、
材料选 择
m e
d ic
m a
l
、
m e c
ha
ic
,
l
、
p
u te r
、
le
c tr o n
c o m m u n
ic a t i o
an
n s
、
to y
a u to m o
b ile ls
o
ho
c
u s e
h o ld
.
p p lia
e
n c e s
.
T h is p a p e
r
in tr o d u
s
o
s
ho
th a t M o
o w
c a n
h e lp t o
K
p t im
o r
e
tru
c
tu
r e
o
f pr o du
d g m in g
M
o
s
y
te m
d pr o
ic
a
v
a
fe
n
r e n c e
MoldFlow软件在特殊注塑成型中的应用

MoldFlow软件在特殊注塑成型中的应用MoldFlow软件在特殊注塑成型中的应用作者:文劲松麻向军来源:PT现代塑料一前言MPI3.1除了能对传统的注塑成型进行模拟分析外,还能对一些特殊的注塑成型过程进行模拟分析,如共注塑成型(Co-injection Molding)、压注成型(Injection-Compression Molding)、反应注塑成型(Reaction Injection Molding)、微芯片封装(Microchip Encapsulation)、气体辅助注塑成型(Gas-Assisted Injection Molding),其中,气体辅助注塑成型将有专门的文章进行介绍,下面讨论其它的注塑成型模拟分析。
二共注塑成型模拟分析共注塑成型是指用两个或两个以上注塑单元的注塑成型机,将不同的品种或不同色泽的塑料,同时或先后注入模具内的成型方法,可生产多种色彩或多种塑料的复合制品。
MPI/Co-Injection可以模拟先后注射成型过程。
一般用于共注塑的注塑机有两个料筒和一个公用的喷嘴。
制品表面的塑料首先注射,由于喷泉效应,塑料熔体喷射到模腔壁,模壁的温度远低于熔体的凝固温度,熔体迅速凝固,形成绝缘层,新的熔体沿着模壁流动,直到覆盖整个模腔表面。
随后注射制品内部的塑料,最后再次注射表面塑料。
在共注塑过程中,有两个很难控制的工艺参数:1)两种塑料的最优混合比例。
理论上,制品内部塑料最大可占到制品体积的百分之六十七,但实际上很难到达,尤其是复杂制品,工程上内部塑料可达到制品体积的百分之三十。
2)两种塑料注射转换的时间控制点。
由于模具设计不合理或者两种塑料比例不合适,有可能使内部塑料露出表面,尤其是最后填充的地方。
MPI/Co-Injection根据两种注射塑料的特性,预测它们在模腔中的分布,并给出两种塑料的最佳混合比例以及注射时间控制点,分析结果包括:1)两种塑料在填充过程中,模腔中任一点在任一时间的体积百分比。
技术分享Moldflow在困气问题上的应用-死角困气

技术分享Moldflow在困气问题上的应用-死角困气
一、概述
注塑成型工艺中,困气问题是最常见的问题之一,它可能会引起烧焦、短射、气痕等缺陷。
我们一般将困气分为三种类型:分型面排气不良、包风困气、还有深筋处的死角困气。
Moldflow在解决困气问题上有着重要的指导作用,这一期小编给大家分享一个死角困气案列。
二、案例分享
•项目资料:
材料信息:PP (红色)不含填充物
产品信息:化妆品行业产品直径18mm 高度12mm 见下图:
工艺信息:模温55℃ 料温235℃ 注塑机:海天
试模问题点:前模外观面有气痕(见下图)调整模温、料温、速
度、压力均不能解决。
•原因分析
从Moldflow分析结果上没有能看到直接的结果,其实这里需要工程师做一番推理:
首先:产品厚度不同导致走胶快慢不一致。
其次:从模具设计上看,这里形成了死角困气的问题。
第三:死角困气位置并不是对应外观缺陷位置,两者之间有没有什么关系?我们可以做个一这样的假设(见下图):
难道死角处气体被挤压吹到表面塑胶里去了?完全有可能!
•实际论证
前边的原因分析也只是我们的推理,这里推理或者是对的,也有可能是错的,那么有没有什么简易的方法可以快速验证一下?
答案是有的!
简单跑了这个删筋方案后,我们就可以现场这样验证:
这样就可以充分证明我们前面的推理是正确的!
•此项目后续就完全可以通过调整局部厚度、浇口等来解决这个死角困气。
•有可能我们遇到的产品问题表面上看不出跟困气有直接关系,但是我们可以从Moldflow工程师专业的角度剖析问题并做出合理的推理,再通过一定的实际论证来验证我们的推理和寻找解决方案,此方法屡试不爽!。
气体辅助注射成型技术原理及应用

气体辅助注射成型技术原理及应用
气体辅助注射成型技术的应用
● 管状和棒状零件,如门把手、转椅支座、吊 钩、扶手、导轨、衣架等。这是因为,管状结 构设计使现存的厚截面适于产生气体管道,利 用气体的穿透作用形成中空,从而可消除表面 成型缺陷,节省材料并缩短成型周期。
气体辅助注射成型技术原理及应用
在进行模具设计之前,利用MoldFlow MPI 5.0对设计方案进行了模拟。 分析模型如图8所示,在该分析模型中确定了浇口及进气口位置。在模拟中, 设定预注射量为70%,熔体温度为230℃,注射时间为3s,延迟时间为1.5s, 气体压力为20MPa。
气体辅助注射成型技术原理及应用
● 可通过气体的穿透减轻制品重量,节省原材料 用量,并缩短成型周期,提高生产率。
● 该技术可适用于热塑性塑料、一般工程塑料及 其合金以及其他用于注射成型的材料。
气体辅助注射成型技术原理及应用
气体辅助注射成型技术的缺点是:
●需要增加供气和回收装置及气体压力控制单元, 从而增加了设备投资;对注射机的注射量和注射 压力的精度要求有所提高;制品中接触气体的表 面与贴紧模壁的表面会产生不同的光泽;制品质 量对工艺参数更加敏感,增加了对工艺控制的精 度要求。
气体辅助注射成型CAE分析的主要作用是:
1.分析产品的成型工艺性 2.评价模具的设计是否合理 3.优化成型工艺参数 4.预测制品可能出现的缺陷
气体辅助注射成型技术原理及应用
下面以成型把手为例,介绍气体辅助注射成型 CAE分析的过程。
如图7所示的把手材料为ABS,手柄位置壁厚为14mm。由于是外观件,对 其成型要求很高。
Pro/E与Moldflow技术在气体辅助注射成型分析中的应用

文件将实体模型 网格化 , 再分割成层 , 以层层堆栈出实体的形状 , 故选择 C D模型文件格式为 S L比 A T 较 口 好 】 。
2 气 辅注射成型分析
21 划 分 网格 与设 置成型 工艺参数 .
将保存好 的气辅成型制件 S L T 文件导入 M l of P 模块 中, o fwM I d l 模型尺寸为 8 Ⅱ X 0 m 0 啪 。网格划 6m 分采用 中面网格模型 , 平均长度为 6 q , E 合并公差为 0 / l / I S nn G . n, 1 n生成网格后 , 对原始网格进行纵横 比、 交叉单元 、 自由边等修正 , 最后获得理想 网格文件 。有 限元网格划分结果 的数据如下 , 三角单元个数为 22节 点数为 16最小 纵横 比为 1 6 , 6, 5, . 7 最大纵 横 比为 405 1 . 。网格划 分结果 如 图 2所示 。 8
程师 在开发 过程 的每一 个 阶段 都能控制 最终产 品 的质量 、 能和成本 效益 。 功 气辅 成型 制件 的 C D原 始模 型 的建 立主要 采用 Po A rE实 体建 模技术 实 现 , 立 的模 型 如 图 1 示 , / 建 所 最后 以 S L或 IE T G S文 件格 式保 存 。 IE G S文件 常 常有破 面 或很 多失 真 的 面 , 分 网格 很麻 烦 ; S L 划 而 T
图 1 原 始模 型
图 2 网格 划 分
本文选择由 ASh la M H塑料公司生产的P 塑料 , u n B c m G P 牌号为 Plo 12 — 。其推荐的基本 o f t P 39 1 yr P N
成型参数为 : 模具表面温度为 5  ̄ 模具温度范围为 2 8  ̄ 塑料熔体温度范 围为 20 20C, 0 C, 0 0C, 0 ~ 8  ̄ 顶出
219402680_基于Moldflow软件的短射法气辅成型数值分析及优化

加工设备与应用CHINA SYNTHETIC RESIN AND PLASTICS合 成 树 脂 及 塑 料 , 2023, 40(3): 54气体辅助注射成型技术(GAIM)具有无缩痕、内应力低、质量轻、刚度高、机台能耗低等优点[1],可减小产品壁厚,防止产品表面缩水,同时节约原料。
按照充气时间点划分,气辅成型可以分为短射法和满射法。
短射法是在塑料短射状态充入压缩氮气,将气体充满型腔;满射法是在塑料满射状态充入压缩氮气,被气体替换的塑料熔体排出型腔至溢料井。
一般说来,短射法模具结构简单,工艺复杂;满射法增加了余料排出机构,模DOI:10.19825/j.issn.1002-1396.2023.03.13具结构相对复杂,而工艺较为简单。
为了节约模具成本,本工作采用短射法,在模具设计之前,运用Moldflow软件对气辅成型过程进行仿真分析,找到合适的进气点和最佳的工艺参数设置,以提升基于Moldflow软件的短射法气辅成型数值分析及优化谭安平,骆 静,谭 平(成都理工大学 工程技术学院,四川 乐山 614000)摘要:使用数值成型对短射法气辅成型进行分析及优化。
依据经验设计,对塑料扶手设计了3种进气方案,仿真结果表明:设置进气点位于浇口位置附近(方案3),气体虽未能充满所有部位熔体内部,但气道质量最佳。
以方案3为基础,优化工艺参数,得到最佳方案为熔体注射量40%,气体延迟时间2.5 s,此时气体充满熔体内部,熔体壁厚减小且壁厚均匀,气道质量较好。
以翘曲变形量为考察对象,运用正交试验法继续优化其他工艺参数,得到了最佳工艺方案为:熔体温度240 ℃,模具温度60 ℃,保压压力3 MPa,保压时间10 s。
关键词:塑料扶手 短射法 气辅成型 进气点 工艺优化中图分类号:TQ 320.66文章标志码: B 文章编号:1002-1396(2023)03-0054-05Numerical analysis and optimization of short shot gas assistedmolding based on MoldflowTan Anping,Luo Jing,Tan Ping(The Engineering & Technical College of Chengdu University of Technology,Leshan 614000,China)Abstract:Numerical molding was used for analysis and optimization of short shot gas assisted molding. Three air inlet schemes were designed for the plastic handrail according to the experience design. The simulation results show that though the air through the inlet that is near the gate position in scheme 3 doesn’t fill the whole melt,the air inlet quality is the best. Based on scheme 3,the process parameters were optimized,and the best scheme is that the melt injection volume is 40%,and the gas delay time is 2.5 s. At this time,the gas fills the whole interior of the melt,reducing the wall thickness and keeping the uniform thickness of the melt,so the air inlet quality is good. The warpage deformation was used as the object of investigation to optimize other process parameters by the orthogonal experimental method and the optimal process scheme is obtained as follows:melt temperature is 240 ℃,mold temperature is 60 ℃,gas holding pressure is 3 MPa,and gas holding time is 10 s.Keywords:plastic handrail; short shot method; gas assisted molding; inlet point; process optimization收稿日期:2022-12-27;修回日期:2023-02-26。
Moldflow在塑料注塑成型中的应用

Moldflow在塑料注塑成型中的应用摘要:本文简单介绍了注塑成型的背景及国内外的发展状况,并对注塑成型的工艺、影响因素及常见的缺陷进行了了解。
最后对注塑成型分析软件Moldflow 进行了一定的介绍。
关键字:注塑成型,塑料,Moldflow1.1引言在现代工业生产中,60%~90%的工业产品需要使用模具,模具工业已经成为工业发展的基础[1]。
早期的注塑成型方法主要用于热塑性塑料制品。
随着塑料工业的迅速发展以及塑料制品应用范围的不断扩大,注塑成型已经推广应用到热固性塑料和一些塑料复合材料制品的生产中。
传统的注射模设计和制造很大程度上依赖于设计者的经验和制造工人的技巧,设计的正确性只有通过试模才能知道,制造的缺陷主要依靠修模来纠正,有时还可能导致整套模具的报废,特别是对复杂的中高档模具,问题则为突出[2]。
随着计算机技术的发展和人们对计算力学、流体力、聚合物加工流变学、传热学等学科的深入,成型模拟(CAE)技术与注塑成型技术相结合,为改变这种状况提供了新的手段。
CAE技术通过建立高聚物成型的物理和数学模型,构造有效的数值计算方法,借助于计算机仿真模拟确定加工条件的变化规律、预测制品的结构和性能、确定高聚物制品和模具设计参数及工艺条件的最佳方案,使高聚物成型加工和模具设计建立在科学分析基础上,为优化模具设计和控制产品成型过程以获得理想的最终“定构”提供科学依据和设计分析手段,指导高分子模型,提高高分子材料使用水平。
成型模拟技术使高聚物成型加工过程在流场、力场、热场等作用下出现的各种物理现象和化学变化的描述更加数学化和定量化,从而使加工成型从一项使用技术变为一门应用科学。
掌握成型CAE技术对缩短产品的开发周期、提高塑料制品的质量、降低生产成本具有很重要的意义[3]。
注塑成型是一种主要的塑料制品成型方法,能够一次成型复杂外形的塑件,同时所生产的塑件尺寸精度高,是一种高效率,能大批量生产的加工方法。
长期以来,我国的注塑模具在设计过程中主要依赖设计员的直觉和经验,而产品结构、模具设计以及成型工艺参数的合理性都无法预知,因此一套模具生产出来的产品是否满足客户的需求,往往是在不断的试模与修模中进行改善的,这加大了模具的设计制造周期,延长了交付日期,同时也加大了模具制造成本,这在激烈的市场经济竞争中使得企业出于一个被动的位置,加大了企业的生存风险[3,4]。
MoldFlow在注塑成型中的应用

MoldFlow在注塑成型中的应用作者:广西大学机械工程学院汤宏群苏广才摘要:利用MoldFlow对星型注塑件不同浇口位置进行流动模拟分析,预测可能存在的气泡位置和熔接痕位置,确定最佳浇口位置和数目。
以此为例说明MoldFlow在注塑成型中应用的好处。
关键词:MoldFlow;模拟分析;最佳浇口位置中传统的注射模设计主要依靠设计人员的直觉和经验,模具设计加工完后往往需要经过反复地调试与修正才能正式投入生产,发现问题后,不仅要重新调整工艺参数,甚至要修改塑料制品和模具,这种生产方式降低了新产品的开发速度。
而利用Moldflow软件在模具加工之前,在计算机上对整个注塑成形进行模拟分析,可以进行填充、保压、冷却、翘曲、纤维取向、结构应力、收缩以及气辅成形等分析,找出可能出现的缺陷,提高一次试模的成功率,降低生产成本,缩短生产周期。
本文主要介绍使用MOLD-FLOW模拟分析软件对星型注塑件不同浇口位置进行流动模拟分析,预测可能存在的气泡位置和预测熔接痕的位置,确定最佳浇口位置和数目。
为模具设计人员进行模具设计提供依据。
1模拟分析过程1.1分析模型的建立图图1为该零件的三维实体模型,由实体模型建立的该注塑件的有限元分析模型如图2所示,在分析中采用中性面网格,有限元分析模型数据为:面单元数-1547,节点数-821。
1.2浇口位置的确定及流动分析本文分别采用一个浇口和两个浇口进行分析比较:方案1一个浇口居中(如图3所示),方案2两个浇口居左右两侧(如图4所示),塑件所用材料为DUPONT,相关参数为:塑料熔融温度-215.00℃;模具温度-90.00℃。
2. 流动模拟分析结果比较2. 1不同浇口位置产生的气泡在塑料熔体注射充填过程中,模腔内除了原有空气外,还有塑料含有的水分在注射温度下蒸发而成的水蒸气,塑料局部过热分解产生的低分子挥发性气体等。
这些气体若不能通过排气系统顺利排出模腔,将会影响制品成型以及脱模后的质量。
MoldFlow在注塑模具中的模流分析及应用(修改)

MoldFlow在注塑模具中的模流分析及应⽤(修改)MoldFlow在注塑模具中的模流分析及应⽤新疆天业集团模具中⼼朱财 832000摘要:⽂章通过介绍MoldFlow在热塑性注塑件的制品设计、模具设计、成型⼯艺⽅⾯的作⽤的阐述,以及对模流分析步骤和对內镶式滴头模流分析的典型结果,提出了在设计阶段采⽤简易模流分析软件来模拟注塑成型过程和成型后的制件缺陷形式,从⽽缩短产品设计全过程周期(特别是模具制造周期),降低模具的费⽤,提⾼企业在市场上的产品竞争⼒.关键词:MoldFlow 注塑模具模流分析MoldFlow in the injection mold-flow analysis and applicationXinjiang Tianye (Group) Ltd. Mould Center Zhu Cai 832000Abstract:The article through introduced that MoldFlow in the thermosplastic injection molding's product design, the mold design, the formation craft aspect's function's elaboration, as well as and inlays the type drop mold class analysis internally to the mold class analysis step the typical result, proposed after the design stage uses the simple mold class analysis software to simulate the injection molding process and the formation workpiece flaw form, thus the reduction product design entire process cycle (is specially die making cycle), reduces mold's expense, enhances the enterprise in the market product competitive power.Key word:MoldFlow Injection mold Mold class analysis引⾔对于任何注塑成型来说,最重要的是控制塑料在模具中的流动⽅式。
基于MOLDFLOW的塑料件注射成型方案分析

熔接痕的影响[J]. 轻工机械,2007,25( 1) : 24 - 27. [4]郑建,胡治流,何娟. moldf low 在注塑模在设计中的
应用[J ]. 装备制造技术,2006,( 4) : 44 - 54.
74
江西化工
2011 年第 4 期
基于 MOLDFLOW 的塑料件注射成型方案分析
郑志刚 余筱勤 钟 勤
( 江西陶瓷工艺美术职业技术学院材料工程系,江西 景德镇 333000)
摘 要:借助计算机辅助工程( CAE) 软件 moldflow 的模流分析功能,对鼠标外壳件塑 件进行了填充、流动前沿温度、压力、熔接痕及表层取向、螺杆行程等模拟分析。确定了最 优设计方案,并且结合模拟结果,介绍了注塑模 CAE 技术对塑件模具优化设计的重要作 用: CAE 技术可以有效地简化设计过程,提高设计效率,降低模具的报废率。
两点进胶,在产品的中部会产生一条细长的熔接痕,但 熔接时溶体温度较高,熔接质量较好,不会影响产品强 度,但熔接痕迹还是会有,由图 7 结合模拟表层取向结 果显示不影响产品外观[3]。
图 7 表层取向
图 8 流动前沿温度
( 4) 流动前沿温度 图 8 为流动前沿温度模拟结果。从图中可以看 出,此模型的模温分布比较均匀,说明熔体在流动过程 中温度下降 缓 慢,利 于 填 充,且 该 产 品 温 度 降 幅 较 小, 这意味着该塑件的表面质量将会得到保证。由图 8 分
关键词:moldflow 模流分析 注塑模 CAE 优化设计
1 前言 Moldflow 技术无论在提高生产率、保证产品质量,
Moldflow在注塑模具毕业设计中的应用

Moldflow在注塑模具毕业设计中的应用近年来,随着我国计算机辅助设计技术以及相应制造技术的不断发展,其在注塑模具中的应用越来越频繁。
如今,计算机辅助工程(CAE)技术已经开始广泛应用到塑料产品生产以及注塑模具设计过程中。
而Moldflow就是一种专业化的CAE软件,在注塑模具毕业设计中的应用价值较大。
标签:Moldflow;注塑模具;毕业设计0 引言注塑模具是进行相关产品生产的主要装备,我国现代化注塑模具设计行业发展速度越来越快,塑胶产品在各个工业部门的应用价值越来越大。
针对塑料产品来说,对模具要求是比较严格的,继续采取传统模具设计模式是不可行的。
本文主要研究Moldflow在注塑模具毕业设计中的应用。
1 moldflow软件的基本介绍及优势Autodesk Moldflow Products主要应用在模具设计过程中,可以起到优化制件的作用,进而完善设计方案和解决方案。
Autodesk Moldflow Products内容主要有三个,第一个是Autodesk Mold-flow Advisers,能够完成实体文件注塑成型研究工作;第二个是Autodesk Moldflow Insight(AMI),能够完成塑料流动、产品收缩情况研究工作;第三个是Autodesk Mold-flow Communicator[1]。
moldflow软件在注塑模具毕业设计中的应用优势较大,主要包括五大优势:第一,该软件操作相对来说比较简单;第二,该软件具备计算机辅助设计操作工具和构件,且功能强大;第三,该软件拥有相对完整的塑料数据库和信息库,可以为用户提供精确而完整的信息和数据,利于设计者评估材料性能;第四,该软件分析功能是比较强的,仿真系统比较完善,利用该系统,设计者可以提前预知相关设计问题并及时解决;第五,该软件后期处理功能是比较强的,后处理工具完善,利于用户进行数据共享。
2 注塑模具设计的基本步骤要想完成注塑模具设计,需要完成以下设计流程:掌握注塑塑件情况,明确塑件设计标准化要求、生产批量、体积以及质量等参数;结合注塑塑件情况科学选用注塑机,确定模具设计所需的结构和型号,全面掌握注塑模具设计的相关信息和参数;计算注塑模具设计中涉及的相关数据,不仅有模具零件工作尺寸、模具地板厚度,还有型腔壁厚度,另外还要确定冷却系统;进行模具结构合理化设计,设计塑件分型面、型腔排列、模具零件、抽芯机构、顶出机构,确定模具腔数、浇口位置、模具腔数等;确定模具整体尺寸,选购合适的模架;加强注塑机相关参数的校对;模具图表绘制;投产制造情况总结和审核[2]。
Moldflow在注塑成型中的应用

一 36 17 en 2 7.7 1t n e
图 5 填充过程 及计算 结果
图 1 注 塑 件 三 维 实 体 模 型
0■
方案一 图 3 单 元定 义厚度
方 案 二
图 2 有限 元网格划分 图
方案三
=
F l A 1 l n毫 y s l ∞ i e t O re u m n1 c i n p s _ s
方 案 四 三 四
3; £
9
3 72
3 鲁 6
.
Ti a t e 0  ̄ l me t he nd £ i li H iu l mmC f rc 一 抽 o e B l k ∞ D r盘 u e — mi m. 1 t l e tr ni B l t r ra  ̄ u k  ̄ pe tt — m i o re m Wa 1 he l s s re s — n l t § l
H l i p a e r s l s s ma g : l M h s e u t u r
1mml ilci p esr 4 i l net ̄ rsue a+ g
Edo i n h s eut ll 9 n F f ni  ̄p a e r s l s smur
(t 2M9s a . '=
2 4 1 22e∞3 7● 27 0 27 《 027 7
1 ∞ 2 28 + 3 ]e o0 1 5 9 25 嘻 0 6 .1 3
2 81 I . 2. 6e O 3 2 + O 2 9e 0 3 1 + 0 13 7 12 9 2 0, 25 4 0. 8 15 0 18 5
工 业 技
术
SI C &TC L0 C NE E 0O Y E
moldflow 注塑成型分析 模流分析报告

1. 熔体密度 2.实体密度 3.顶出温度 4.推荐模具温度 5.推荐熔料温度 6.材料失效温度
0.88 g/cu.cm 1.06 g/cu.cm
119 deg.C 45 deg.C 225 deg.C 290 deg.C
7. 熔料温度下限 8. 熔料温度上限 9. 模具温度上限 10.模具温度下限 11.最大剪切速率 12.最大剪切应力
Page 8
体积收缩
体积收缩结果用来判断产 品各处的体积收缩情况,收 缩不均匀会造成翘曲变形, 收缩较大则造成缩痕。 由图可见产品内部收缩较小, 且比较均匀。出现缩痕风险 小。
Page 9
困气位置
1
Air traps可提供模具的困气位 置。air traps产生在填充末端包 括高rib和boss柱位置、结合线、 流动包封位置。故而在这些位置 一般需要开设排入槽或排气入子。 另外在熔体温降较大处也应增加 排气,提高流动性。
pagepage1919尾部分子剪切作用较高故而分子取向度高并且分子结晶度高取向诱导结晶在取向方向上收缩较大故而收缩应力导致产品尾部收拉力而张开变形
Moldflow注塑成型分析
For
滨海
Reporter : 孟栋梁 sduan@
2010-07-16
分析描述
▪ 产品描述 此是汽车用产品,使用热浇道系统注射成型。
200.0 deg.C 250.0 deg.C 30.0 deg.C 60.0 deg.C 100000.0 1/s
0.25 Mpa
PVT Plow材料数据库
Page 3
工艺条件
注塑机设定:
最大锁模力:
未限定
最大注塑压力:
未限定
最大注射速度:
结合线
气辅注塑模具设计中的CAE(moldflow)技术

信 息 技 术10科技资讯 SC I EN C E & TE C HN O LO G Y I NF O R MA T IO N传统的注塑模设计中,一般先由设计人员凭经验和设计手册设计出模具图纸并制定相应的生产工艺,然后进行模具加工,装配试模,一旦试模出现问题,就需要重新设定工艺参数,乃至修改塑料制品的形状和模具结构,如此反复,这势必增加了成本,延长了产品开发周期,给生产和经营带来不必要的损失。
利用C AE 技术可以在模具加工前,用计算机对整个注塑成型过程进行模拟分析,正确预测熔体的填充、保压、冷却等方面的情况,从而能使设计者尽早发现问题,并能快捷地修改设计方案,这样有效地降低了成本且缩断了生产周期。
该文以美国的moldflow公司的分析软件为工具进行注塑成型分析研究。
1 椅子背框CAE 技术在注塑成型中的作用首先,应根据塑料产品的尺寸和形状,利用CA D完成其三维的造型(该文使用的是UG NX 3.0),然后将其以STL的格式存储,再用m o l d f l o w 来分析计算。
同时,moldflow作为成功的注塑产品成型仿真及分析软件,利用的基本思想也是工作领域中最为常用的有限元方法,因此精确地划分“网格”(mesh)是moldflow分析的前提,现以两款产品椅子背框后视镜为例来说明其应用步骤。
椅子背框是一副气辅模具,它的材料是PA6+40%GF(DUPONT的zytel 73G45),重量是2430g克,它的材料特性可以在软件的菜单中相对应地找出,并根据设计手册所提供的资料初步定出工艺参数。
(1)熔融温度270℃,(Range:260~290℃);(2)温度分布:区域1:285℃;区域2:280℃;区域3:275℃;区域4:270℃;射嘴:270℃;(3)最大螺杆转速:0.3×60000./.(screw diameter×3.14)rpm;(4)模具温度:85℃(Range:65~110℃);(5)保压压力:85±15Mpa;(6)保压时间:3s/mm (7)注射速度:300mm/s;1.1预测浇口的位置与浇口的数量浇口是连接流道和型腔之间的一段细短通道,是浇注系统的关键部位,其形状、尺寸、位置和数量对塑料制品的质量影响很大。
moldflow在《塑料成型与模具设计》课程教学中的应用

moldflow在《塑料成型与模具设计》课程教学中的应用MoldFlow是一种塑料成型与模具设计方面的软件,主要用于模具分析和塑料件设计预测。
它能够帮助工程师和设计师们有效地将设计的想法转换到塑料制品上,并能够预测制品的最终性能和外观。
Moldflow的应用可以帮助工程师更好地管理塑料成型过程中的流程,提高工作效率,并且能够让塑料制品拥有更佳的性能和外观。
本文分别从介绍MoldFlow,描述MoldFlow在塑料成型及模具设计教学中的应用,探讨MoldFlow在模具设计及塑料成型实验中的应用这三个方面,探讨MoldFlow在教学和实际应用中的重要作用,以及MoldFlow 的未来发展等内容,具体进行阐述。
【MoldFlow介绍】MoldFlow是一款由Autodesk公司开发的计算机辅助工程软件,主要用于模具分析和塑料件预测。
该软件采用了多种几何学模型,并可以进行热流体模拟,模具汽包分析和零件塑性变形分析等。
它可以用于分析模具汽包的分布、模具的散热性能和模型的收缩率以及塑料件上的塑性变形等。
MoldFlow的应用广泛,包括模具设计、塑料成型、汽车塑料件的设计以及模具制造行业等。
【MoldFlow在塑料成型及模具设计教学中的应用】MoldFlow在塑料成型及模具设计教学中容易操作,可以显著提高教学效果。
首先,MoldFlow可以帮助教师更好地指导学生利用有限元分析软件对塑料元件进行分析。
其次,MoldFlow可以帮助教师指导学生实现模具参数的优化,从而更好地控制成型过程中的温度和塑性变形,并最终得到更高质量的塑料件。
此外,MoldFlow还可以帮助学生更好地理解模具空气和液体的流动规律,从而更加准确地设计出合理的模具型腔。
【MoldFlow在模具设计及塑料成型实验中的应用】MoldFlow的应用还可以帮助工程师更好地管理模具设计及塑料成型实验过程,提高工作效率,并且能够让塑料制品拥有更佳的性能和外观。
MoldFlow软件在气体辅助成型中的应用

MoldFlow软件在气体辅助成型中的应用作者:麻向军文劲松前言气体辅助成型技术作为新的注射成型工艺,是自往复式螺杆注射技术问世以来,注射成型工业最重要的发展之一,被业界誉为塑料注射工艺的第二次革命。
与传统的注射成型相比,气体辅助注射成型技术有许多优点,如提高产品强度、刚度、精度,可消除缩痕从而提高制品表面质量,简化浇注系统和模具设计,减小产品成型应力和翘曲,节省塑料材料,解决大尺寸和壁厚差别较大产品的变形问题,降低注射压力和成型压力等。
但是,影响气体辅助注射成型工艺的因素多,如注射温度、注射时间、熔体预注射量、充气工艺与位置、材料种类等。
MPI/Gas通过对气辅成型过程进行模拟计算,帮助工艺人员确定合理的工艺条件,大大降低了产品的试模次数。
一、MPI/Gas简介与普通注射成型相比,气体辅助注射成型的工艺难度大,要求严格。
由于气体的注入,使得塑料熔体在模腔中的成型行为发生显著变化,气体注入对塑料熔体的填充形式、模具冷却、制品的收缩和翘曲及最终的使用性能产生很大影响。
MPI/Gas能够充分考虑注入气体对制品的填充、保压、冷却、翘曲、应力的影响。
气体辅助注射成型技术中,选择合适的气体注入位置、延迟时间及压力是保证制品质量的关键因素。
MPI/Gas能够对制品和浇注系统中设置单个或多个气体注入位置的情况进行分析,当通过多个位置注入气体时,可以设定相同或不同的延迟时间。
对于气体注入的控制方法,MPI/Gas提供了压力控制和体积控制两种方法供用户选择。
MPI/Gas通过对气辅成型过程进行模拟计算,能够确定合适的注射量以避免吹穿,同时,确定避免短射、熔体前沿粘滞所需气体压力。
考虑气体注入前的延迟时间以便使薄壁凝固,确定合适的气道尺寸,以优化填充工艺和气体注入工艺,并确定最佳的气道布局及控制气室长度。
可以确定气体注入不良时的气室长度或其他与气体注入有关的质量问题。
在此基础上,进一步确定气体穿透后制品最终的壁厚及制品最终的重量。
MoldFlow软件在注塑模具设计中的应用

MoldFlow软件在注塑模具设计中的应用The application of MoldFlow in Injection Mold Design文劲松麻向军(华南理工大学聚合物新型成型装备国家工程中心SCUT—MoldFlow高级技术应用培训中心)一前言塑料产品从设计到成型生产是一个十分复杂的过程,它包括塑料制品设计、模具结构设计、模具加工制造和模塑生产等几个主要方面,它需要产品设计师、模具设计师、模具加工工艺师及熟练操作工人协同努力来完成,它是一个设计、修改、再设计的反复迭代、不断优化的过程。
传统的手工设计、制造已越来越难以满足市场激烈竞争的需要。
计算机技术的运用,正在各方面取代传统的手工设计方式,并取得了显著的经济效益.计算机技术在注塑模中的应用主要表现在以下几方面.1、塑料制品及模具结构设计商品化三维CAD造型软件如Pro/Engineer、UG、CATIA等为设计师提供了方便的设计平台,其强大的曲面造型和编辑修改功能以及逼真的显示效果使设计者可以运用自如地表现自己的设计意图,真正做到所想即所得,而且制品的质量、体积等各种物理参数一并计算保存,为后续的模具设计和分析打下良好的基础.同时,这些软件都有专门的注塑模具设计模块,提供方便的模具分型面定义工具,使得复杂的成型零件都能自动生成,而且标准模架库、典型结构及标准零件库品种齐全,调用简单,添加方便,这些功能大大缩短了模具设计时间。
同时,还提供模具开合模运动仿真功能,这样就保证了模具结构设计的合理性.2、注塑过程数值分析运用CAE软件如MoldFlow模拟塑料熔体在模具模腔中的流动、保压、冷却过程,对制品可能发生的翘曲进行预测等,其结果对优化模具结构和注塑工艺参数有着重要的指导意义,可提高一次试模的成功率。
在下面的章节中将详细讨论。
3、数控加工利用数控编程软件可模拟刀具在三维曲面上的实时加工过程并显示有关曲面的形状数据,以保证加工过程的可靠性,同时还可自动生成数控线切割指令、曲面的三轴、五轴数控铣削刀具轨迹等。
- 1、下载文档前请自行甄别文档内容的完整性,平台不提供额外的编辑、内容补充、找答案等附加服务。
- 2、"仅部分预览"的文档,不可在线预览部分如存在完整性等问题,可反馈申请退款(可完整预览的文档不适用该条件!)。
- 3、如文档侵犯您的权益,请联系客服反馈,我们会尽快为您处理(人工客服工作时间:9:00-18:30)。
Moldflow在气体辅助注塑成型中的应用一.引言气体辅助注塑成型(简称气辅成型)是塑料加工领域的一种新方法,80年代开始用于生产实际,气体辅助注射成型比传统注射成型多一个气体注射阶段,由气体推动塑料熔体充满模具型腔,因此在气辅成型制品设计和模具设计时必须提供明确的气道来引导气体的走向。
气道几何尺寸的大小、截面形状的确定和位置的布置都会影响到气体的穿透和气体对熔体流动的干涉,从而最终影响到成型制品的质量。
根据气辅成型时射入型腔的熔融塑料的体积不同,气辅成型工艺大致可分为3种方式:a、中空成型,即熔体射入型腔充填到型腔体积的60-70%时,停止注射熔体,开始注入气体,直至保压冷却定型。
这种工艺主要适用于类似把手、手柄之类的大壁厚塑料制品,应用效果最理想。
b、短射,即熔体充填到型腔体积的90-98%时,开始进气。
该方法主要用于较大平面的厚壁或偏壁制品。
c、满射,即熔体充填至完全充满型腔时才注入气体,由气体填充因熔体体积收缩而产生的空间,并将气体保压和熔体保压配合使用,使制品翘曲变形大大降低,用于较大平面的薄壁制品成型,其工艺控制较复杂。
前两种方法也称为缺料气辅注射法,后者称为满料气辅注射法。
气辅工艺原理第一阶段:塑料注射:熔体进入型腔遇到温度低的模壁,形成一个较薄的凝固层。
第二阶段:气体注射:惰性气体进入熔融的塑料,推动中心未凝固的塑料进入尚未充满的型腔。
第三阶段:气体入射结束:气体继续推动塑料熔体流动直到熔体充满整个型腔。
第四阶段:气体保压结束:在保压状态下,气道中的气体压缩熔体,进行补料确保制件的外观。
二.气辅注射成型技术的特性(1)可保证壁厚差异较大制品的成型质量采用气辅技术可将制品壁厚处“挖空”设计成气道,从而保证壁厚差异较大制品的成型质量。
可简化制品的形状,可将原来因壁厚差异较大需分成几个零件成型然后组合的制品,实现一体成型。
如图1所示。
(2)注射压力低所需注射压力为普通注射成型注射压力的10%~75%,相应成型同样投影面积制品的锁模力也只需普通注射成型锁模力的10%~75%,图2为普通注射与气辅技术成型过程中熔融树脂的压力行为。
(3)可消除缩痕,提高制品表面质量从制品整体收缩的情况分析,普通注射成型采用树脂保压,保压压力较高,直到浇口封闭之前都不断向型腔内补充树脂,因而树脂密度增大,收缩减小,但浇口封闭以后其收缩部分得不到补偿,而无法保证制品表面形体完全与模具型腔表面一致。
采用气辅技术气体保压压力较小,虽然树脂自身的收缩较大,但其收缩可由气体从内部膨胀予以补偿,使制件不会出现凹痕,因而可使制品表面重现模具型腔表面质量。
另外,制品筋肋部分表面出现缩痕是由于制品的壁厚差异造成的,对于这种情况,采用气辅技术后,可将筋肋与表面相交处“挖空”减小甚至消除缩痕,如图3所示。
(4)可减小制品成型应力和翘曲采用普通注射成型需要很高的注射压力,才能使树脂填满整个型腔,并因从浇口处至填充末端的压力梯度很大而产生应力,树脂在凝结固化的过程中,应力就会“冻结”、“残留”,成为成型中的一种“记忆”,待制品脱落型腔后,可能会马上发生翘曲变形,或在使用过程中逐步变形,尤其是在喷漆、电镀等二次加工或装饰时,这种现象会更明显。
采用气辅技术后,所需注射压力较低,而且内部填充的气压处于均等,因此可显著降低制品内部应力,又使制品在冷却时,内部气压保持恒定,可进一步减低制品的扭曲变形趋势。
(5)可提高制品的强度与刚度采用气辅技术可使壁厚差异较大制品实现均匀充填,避免了普通注射成型产生较大内应力缺陷,并可在不增加制品重量下,通过气道设计增加制品截面的二次惯性矩。
综上所述,采用气辅技术后,可简化模句结构、减轻制品重量、大大节省材料(20%~30%)、降低锁模力、缩短成型周期,达到降低制品成本及提高制品质量的目的,因而气辅技术得到各行业的广泛关注。
三.气体辅助注射成型工艺过程气辅成型一般包括熔融树脂注射、气体注射、气体保压、气体回收、制件顶出等几个主要步骤。
首先由浇口向模具型腔内注入熔融的树脂后,再注入一定压力的惰性气体(氮气),借助气体压力的作用推动树脂充实到模具型腔的各个部位,使塑件最后形成中孔断面而保持完整外形,并从树脂内部进行保压,此时气体压力就变为保压压力。
由于靠近模具表面部分塑料的温度低,表面张力高,而处于模具型腔中心部位的熔体温度高,粘度低,致使气体易于在塑件较厚的部位(如加强筋)形成空腔,而被气体所取代的熔融塑料被推向模具的末端,形成所需要成型的制件。
气体可回收,其回收过程发生在冷却结束,开模之前。
与传统注塑成型相比,多了一个气体辅助充填阶段,且保压阶段是靠气压进行保压的,保压压力低,可降低制品内应力,防止制品翘曲变形。
由于气体能有效传递所施加的压力,可保证制件内表面上压力分布均匀一致,即可补偿熔体冷却时的体积收缩,也避免了制件顶出时的变形。
采用气辅成型是通过控制注入型腔内的塑料量来控制制品的中空率及气道的形状,气辅成型有压力控制法与体积控制法两种。
气辅成型循环周期(A)充填阶段1:循环开始1-2:注入树脂2:完成树脂填充2-3:注入气体前树脂膨胀时间3:开始注入气体3-4:注入气体4:型腔填充完毕(B)保压阶段4-5:气体保压5:气体泄压(抽回气体或派出气体)6:开始脱模(C)脱模阶段注射成型循环周期内压力与时间的关系如图6所示。
普通注射成型,其注射压力与时间大关系曲线表明,在时间间隔t1内,型腔的大部分被充满,从t1~t2之间型腔充填时,注射压力急剧增大,t2时刻的压力为充满型腔所需的最大的注射压力,这压力值也决定了所需的锁模力。
在t2~t3阶段,型腔内树脂压力随冷却而下降,在t3之后开模。
对气辅成型而言,t1时刻内为缺料注射,t1~t2这一段时间为注入气体之前,注入型腔内的熔融树脂膨胀时间。
这个时间很重要,是一个重要的工艺参数,根据不同情况可设定为零到几秒之间。
这时间需精确控制。
在t2~t3时间内注入气体,有气体将熔融树脂填充到型腔各表面,在t3~t4时间内树脂冷却,气体保持恒定压力,在t4时刻开始回收气体至t5时刻开模取出制品。
四.气辅成型制品设计的基本原则能否采用气辅技术成型制品,首先在于制品设计是否成功。
在构思及设计制品时,就必须考虑树脂的浇口位置,气体的入口位置,气道的形状及布置,制造的可行性。
根据不同制品的形状及工艺方法,气体的入口位置可与树脂浇口是同一位置,也可以在型腔及分模线的某一部位设置,可以设置一个或多个。
气体的入口位置及气道设计是制品设计的关键,气道的作用除了引导气体之外,另一个作用是便于树脂流动。
在注入树脂阶段,气道成为树脂的流道,因截面面积较大,可降低注射压力。
在气道设计时应注意:(1)气道相对浇口的布置应是对称或单一的;(2)气道必须是连续的,但不应自己形成回路;(3)一般情况下气道体积应小于制品整个体积的10%。
利用气辅成型的制品根据结构形状不同,大致分为三类:棒类制品,类似把手之类的大壁厚制件板类制品,容易产生翘曲变形和局部熔体聚积的大平面制件特殊制件,由传统注射成型技术难以一次成型的特殊结构的制件棒类制品气辅成型技术在棒类制品的成型中显示出明显的优势,一般采用中空注射的气辅工艺,即气体穿过整个制件的壁厚部位形成气道。
因此,制件的设计即是气道的设计应考虑以下方面:制品截面最好是接近圆形。
因为气体在气道中穿透形成的中空部分截面趋向于圆形,这样制品接近圆形可避免因熔体的不均匀分布而造成壁厚不均匀。
当制品因使用或结构要求不允许采用圆形截面时,应遵循以下原则:外形尽量接近圆形; 避免尖角,采用大的圆角过渡;避免熔体在角部产生堆积;保证整个制品壁厚均匀。
采用矩形截面时,气道通常为椭圆形。
为保证气体穿透的均匀性,应满足b≤(3~5)h制件长度应大于制件截面高度h的5倍,保证沿制件长度方向气体尽量穿透,以得到均匀的壁厚。
气道转弯处制件应有足够大的圆角半径,避免内外转角处的壁厚差异。
气道截面尺寸变化应平缓过渡,以免引起收缩不均。
气道入口位置不应设置在外观面或制件承受机械外力处。
进气口位置应接近浇口,以保证气体与熔体流动方向一致,但两者距离应在30mm以上,以避免气体反灌入浇口。
熔体和气体的注射入口应尽量布置在制件中间,熔体流动和制品设计应保证平衡结构,才能确保气道的均匀穿透。
板类制品气辅成型技术的主要应用之一就是板类制件的成型。
气辅成型技术能有效克服传统注塑成型中板类制件的一些困难,显著降低缩模力,减小制件翘曲变形,提高制件的刚强度,避免局部的表面凹陷。
因为气体总是沿着阻力最小的方向前进,容易在较厚的部位进行穿透,因此设计板类制件时常将加强筋或肋板等较厚部位作为气道,一般设在制品的边缘或壁的转角处。
对制品的设计也就是对加强筋和肋板的设计,即气道的设计。
特殊制品由于结构和使用的要求,一些复杂的塑料制品不能采用传统方法一次注射成型,往往需要多个部件装配而成。
如图所示的汽车支架零件,凸缘的壁厚远大于侧壁的壁厚,采用传统的注射成型会在凸缘形成明显的凹陷,影响表观质量和使用性能。
该类制品采用气辅成型后,均能很好地保证制件的表面质量,并且大大地节省材料,缩短冷却时间五.气体辅助注射成型技术设备气体辅助注射成型是通过在普通的注塑机上安装一套附加的气体注射装置来完成的,气体注射成型装置有注塑机、气辅装置及特种进气嘴三部分组成。
(1)注塑机由于气辅成型采用压力控制与体积控制法控制制品的中空率及气道形态,以对注射熔融树脂量及注射压力的精度误差有一定的要求。
要求注射量的精度控制在±0.5%,注射压力波动相对稳定,只要能满足上述要求的注塑机在控制系统上能与气体单元相匹配,均可用于气辅成型。
(2)气辅装置有氮气发生器、控制单元及氮气回收装置组成。
其功能是从氮气发生器中获取低压氮气后,将其增压为高压气体,储于高压气缸内。
(2)特种气嘴(3)进气嘴根据气辅方式大致分为两类:一类是主流道式进气嘴,这种气嘴是利用注射机喷嘴注射树脂的通路,实现对型腔注入气体也就是待喷嘴完成熔融树脂注射后,切换成气体通道。
另一类是独立的气体通路专用气嘴,根据要求及分析结果可在塑件的任何位置设置。
六.利用阀式浇口控制溢料井这个例子将讨论如何模拟有溢料井的制件在成型过程中利用阀浇口来控制气体的穿透情况,利用该特征,必需在工艺参数设置模板上设置其参数,在有限元网格文件中相关的阀浇口的开关时间也必需指定。
对于某些气辅成型例子来说,溢料井可连接在气道的末端,以便获得理想的气体穿透效果。
在树脂注射阶段,树脂填充型腔的其它区域,而到溢料井的通道是关闭的,如图上部所示,在树脂注射结束后,可设定一个延迟时间,让树脂松弛、薄壁区域树脂固化。
在注气之前必须立即打开溢料井,创建多余的一部分体积,与被注入的气体代替的树脂相当。