气体辅助注塑成型技术与设备
气辅注塑加工工艺与一般注塑工艺
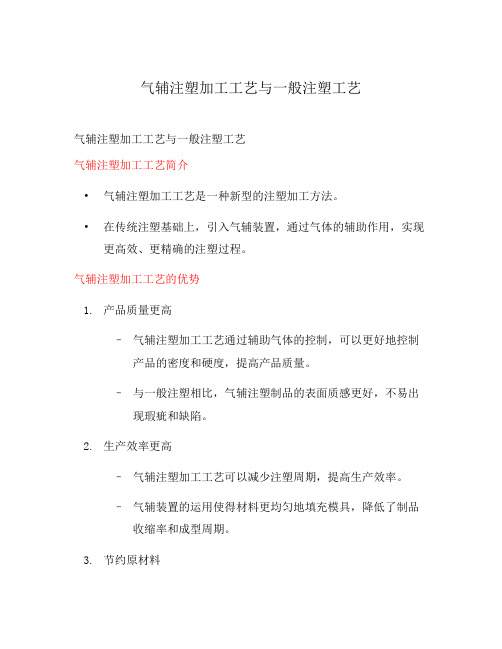
气辅注塑加工工艺与一般注塑工艺气辅注塑加工工艺与一般注塑工艺气辅注塑加工工艺简介•气辅注塑加工工艺是一种新型的注塑加工方法。
•在传统注塑基础上,引入气辅装置,通过气体的辅助作用,实现更高效、更精确的注塑过程。
气辅注塑加工工艺的优势1.产品质量更高–气辅注塑加工工艺通过辅助气体的控制,可以更好地控制产品的密度和硬度,提高产品质量。
–与一般注塑相比,气辅注塑制品的表面质感更好,不易出现瑕疵和缺陷。
2.生产效率更高–气辅注塑加工工艺可以减少注塑周期,提高生产效率。
–气辅装置的运用使得材料更均匀地填充模具,降低了制品收缩率和成型周期。
3.节约原材料–气辅注塑加工工艺由于材料分布更均匀,减少了材料的浪费。
–相比较于一般注塑,气辅注塑制品在制造时所需的原材料用量更少。
4.环保节能–气辅注塑加工工艺不需要额外的加热或冷却设备,节约了能源。
–通过优化制程,减少了废品率,降低了对环境的负面影响。
气辅注塑加工工艺的应用领域•电子产品:手机壳、电池壳、硬盘壳等。
•汽车配件:车灯壳、仪表板、车门把手等。
•家居用品:儿童玩具、家具配件、文具等。
一般注塑工艺的特点与局限性•一般注塑工艺在制品的表面平整度和精度方面有一定的局限性。
•一般注塑制造过程中,因为材料无法完全填充到模具中的每个角落,易产生瑕疵和缺陷。
结语气辅注塑加工工艺相对于一般注塑工艺具有众多优势,无论是产品质量、生产效率还是原材料的节约都占有明显的优势。
在如今注塑加工行业日益竞争激烈的背景下,气辅注塑加工工艺的应用前景非常广阔。
希望本文能对读者对气辅注塑加工工艺与一般注塑工艺有更深入的了解。
气辅注塑加工工艺的工作原理1.注塑过程中,将塑料颗粒加热融化。
2.融化的塑料通过注塑机的螺杆被注入模具腔中。
3.气辅装置通过喷嘴向注入的塑料中喷入压缩空气。
4.压缩空气通过气门控制,辅助塑料充填模具,使得塑料更加均匀地填充到模具的每个角落。
5.注塑机冷却塑料,然后开模取出制品。
气辅设备改善
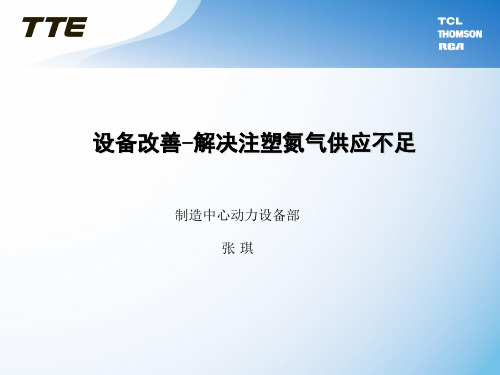
二、注塑气辅设备的现状与问题分析 3、 氮气发生器运行状况与问题分析 A、因进口设备配件缺乏,有2台氮气发生器长期故障停机; B、实际总制氮气量低,只占总标称产气量的65%;并且气辅设备故 障率高,约占注塑总修机工时的33~40%(不含长期停机), C、因产气量不足,无法进行设备正常停机保养,部分设备带病运行; D、各车间产气量配置差异大,注塑二厂二车间氮气辅助注塑比率只 有81%,而注塑一厂二车间气辅注塑比率达到145%(详见附表); E、大多数车间拥有2~3种品牌的气辅设备,由于不同品牌设备混合 使用,存在维修与配件管理困难的情况。
使用部门 一厂一车间 一厂二车间 二厂一车间 二厂二车间 现产气量 (NL/mim) 1550 1600 1550 1350 调整方案 维持不变 调出1台新普雷斯 用1台新普雷斯换1台中拓 从一车间调入1台中拓 调整后制氮量 供注塑机 现注塑机 气辅注塑 制氮气辅 (NL/min) 数量(台) 数量(台) 数量(台) 比率 1550 1350 1350 1800 15 13 13 18 16 12 18 20 11 11 10 16 136% 118% 130% 113%
三、提高与平衡氮气供应量的实施方案 1、修复故障停机的设备,如大修理2#宝尔氮气发生器,使达到新设 备的产气量、氮气纯度等性能指标,具体方案如下: A、更换疲劳断裂的增压机曲轴与连杆; B、更换拉毛的一级缸、活塞与活塞环; C、更换磨损的二级浮动缸与活塞(超过原配合间隙0.01毫米两倍) ; D、检修一、二级进、排气阀,要求阀芯行程1~1.25MM; E、更换失效的低压空气三级过滤芯与高压高效过滤芯等易耗品; F、更换空压机堵塞的进口过滤芯、油过滤器、油气分离器等; G、检查制氮膜组、电控系统与高压安全阀的性能; H、预算大修理总费用约¥86000元,约占设备原值的11%。
气辅注塑成型工艺

气辅注塑成型工艺这种成型工艺,对于很多工程师来说很陌生,因为平时大家接触的产品很少会用到这种成型工艺,包括我本人也是一样,直到我接触到一款产品,才慢慢了解,就是以下这个锅体。
锅体的把手部分,除了2个螺丝塞,整个把手是一个完整的塑胶件,且外观并没有缩水等缺陷,看下侧面和背面图。
咋一看,以为内部是实心的,实际上并不是,而是空心的,是利用了气体辅助注塑成型技术。
01气辅成型的原理气体辅助注塑系统,是把惰性气体(通常用氮气)经由分段压力控制系统直接注射入模腔内的塑化塑料里,使塑件内部膨胀而造成中空,但仍然保持产品表面的外形完整无缺。
气辅注塑成型可被认为是中空吹塑成型的变型,其过程是先向模具腔中注入经过准确计量的占模腔一定比例的塑胶熔体,这一过程称为“欠料注塑”,再直接往熔融塑胶中注入一定体积和压力的高压氮气,气体在塑胶熔体的包围下沿着阻力最小的方向扩散前进。
由于靠模壁部分的塑胶温度低,表面粘度高,而製作较厚部分中心塑胶熔体的温度高,粘度低,所以气体容易对中心塑胶熔体进行穿透和排空,在制件的厚部形成中空气道,而被气体所排空的熔融塑胶又被气体压力推向模具末端直至充满模具型腔,在冷却阶段压缩气体对塑胶熔体进行保压补缩。
待制品冷却凝固后再卸气,然后开模顶出。
以上气辅成型过程实际上分为四个阶段:熔体短射、气体注射、气体保压、气体排出和制件顶出。
02气辅成型的方法除了常规的欠料注塑成型法,还有:1.副腔成型法(也叫满料注塑法)2.型芯成型法3.熔体回流成型法上面的锅体的把手猜测是采用了副腔成型法(也叫满料注塑法):具体细节可参考下图:03气辅注塑成型与普通注塑成型的区别主要区别在于多了一套气辅设备:(1)普通注塑机(计料精度稍高些为好)。
(2)氮气控制系统,包括自封闭式气辅喷嘴。
(3)高压氮气发生器。
(4)工业氮气钢瓶以及提供增压动力的空气压缩机。
(5)为气体辅助注射设计制造的模具。
(6)气辅注塑气辅喷嘴喷嘴进气方式,即使用专用的自封闭式气辅喷嘴,在塑料注射结束后,将高压气体依靠喷嘴直接进入塑料内部,按气道形成一个延展的封闭空间—气腔并保持一定压力,直至冷却,在模具打开之前,通过座台后退使喷嘴与制品料道强行分离,使气体排出制品。
气辅注塑工艺的应用和工艺过程
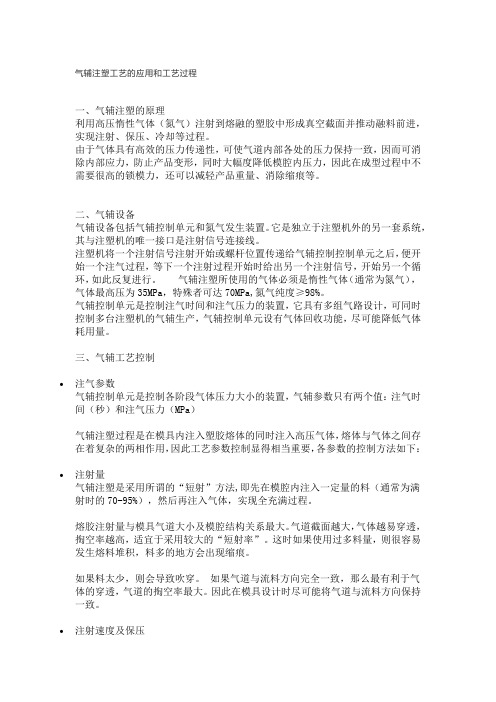
气辅注塑工艺的应用和工艺过程一、气辅注塑的原理利用高压惰性气体(氮气)注射到熔融的塑胶中形成真空截面并推动融料前进,实现注射、保压、冷却等过程。
由于气体具有高效的压力传递性,可使气道内部各处的压力保持一致,因而可消除内部应力,防止产品变形,同时大幅度降低模腔内压力,因此在成型过程中不需要很高的锁模力,还可以减轻产品重量、消除缩痕等。
二、气辅设备气辅设备包括气辅控制单元和氮气发生装置。
它是独立于注塑机外的另一套系统,其与注塑机的唯一接口是注射信号连接线。
注塑机将一个注射信号注射开始或螺杆位置传递给气辅控制控制单元之后,便开始一个注气过程,等下一个注射过程开始时给出另一个注射信号,开始另一个循环,如此反复进行。
气辅注塑所使用的气体必须是惰性气体(通常为氮气),气体最高压为35MPa,特殊者可达70MPa,氮气纯度≥98%。
气辅控制单元是控制注气时间和注气压力的装置,它具有多组气路设计,可同时控制多台注塑机的气辅生产,气辅控制单元设有气体回收功能,尽可能降低气体耗用量。
三、气辅工艺控制•注气参数气辅控制单元是控制各阶段气体压力大小的装置,气辅参数只有两个值:注气时间(秒)和注气压力(MPa)气辅注塑过程是在模具内注入塑胶熔体的同时注入高压气体,熔体与气体之间存在着复杂的两相作用,因此工艺参数控制显得相当重要,各参数的控制方法如下:•注射量气辅注塑是采用所谓的“短射”方法,即先在模腔内注入一定量的料(通常为满射时的70-95%),然后再注入气体,实现全充满过程。
熔胶注射量与模具气道大小及模腔结构关系最大。
气道截面越大,气体越易穿透,掏空率越高,适宜于采用较大的“短射率”。
这时如果使用过多料量,则很容易发生熔料堆积,料多的地方会出现缩痕。
如果料太少,则会导致吹穿。
如果气道与流料方向完全一致,那么最有利于气体的穿透,气道的掏空率最大。
因此在模具设计时尽可能将气道与流料方向保持一致。
•注射速度及保压在保证制品表现不出现缺陷的情况下,尽可能使用较高的注射速度,使熔料尽快充填模腔,这时熔料温度仍保持较高,有利于气体的穿透及充模。
气体辅助成型技术
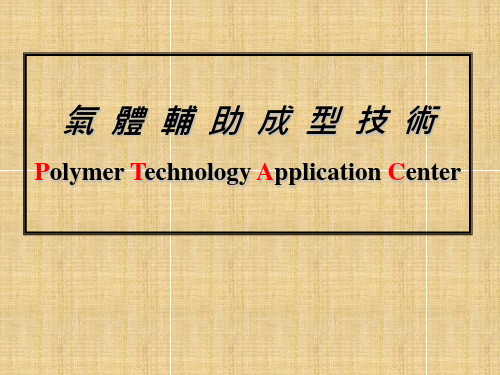
三.進氣嘴
1.根據進氣位置的不同可分為兩類: (1) 一類是特殊結構的注塑機噴嘴,氣體與熔體都通過
這個噴嘴進行注射. (2) 另一類是有獨特氣體通道的專用氣嘴.
2.進氣嘴結構
進氣嘴結構可分為彈簧復位型和間隙出氣型兩類.
5. 技術關鍵
1. 模具及制品設計
* 氣體入口位置及氣道設計是氣輔注射成型模具和制品設計的關鍵. 入口位置設計時應注意:入口位置應盡可能靠近澆口部位,不能形成 氣體環流狀態;注氣口注入氣體流動方向應與樹脂流動方向一致.
(2) 轉換時間 當注射結束時,合理選擇氣體的轉換時間,可以避免流動前沿停止流 動和在制件表面出現可見的滯留痕或形不成氣道.因為注入氣體過 早,熔體外表無充分冷卻,氣體易穿破熔體;過晚,熔體冷卻,氣體不 能形成氣道或在制件表面形成滯流痕.
(3) 氣體壓力 注氣開始時較高的壓力和以后稍低的壓力為氣體通道成型和定型所需.
1.壓力生成設備. 它必須保證注氣系統可得到高壓氣體.一般使用氮氣,氮氣提供方式 有三種:瓶裝氮氣,液體氮氣和氮氣發生器.氣體壓力一般為5~32MPa, 最高可達100MPa.
2.氣體注射控制單元 新工藝參數:氣體起射時間,氣體注射延遲時間,氣體注射壓力或流 量,氣體射入時間. 其中氣體起射時間由螺杆位置觸發. 所有工藝參數中,氣體充填,保壓過程中氣體壓力控制的精度對產品 質量的影響最大.
* 連續壓力產生法 利用專門壓縮裝置來產生高壓氣體,包括壓縮機和儲壓罐,壓縮機的運 轉保證了儲壓罐的壓力恆定,壓力一般為30MPa .
優點: 1. 壓力分布可以用壓力控制裝置來自由選擇. 2. 具有不同壓力需求的幾個註射點或幾台氣體輔助注 射成型機可用同一套注氣系統.
二.注氣系統
注氣系統包括壓力生成設備用氣體注射控制單元.
气体辅助注塑工艺简介

气体辅助注塑工艺简介1.气体辅助注塑目前所指的气体辅助注塑:是指将氮气注射入产品内,使产品内部形成中空。
模具打开前,控制器会将塑胶工件内的氮气释放回大气中。
2.气辅注塑成形工艺的优势1)低射胶、低锁模力;2)压力分布均匀、收缩均匀、残余应力低、不易翘曲,尺寸稳定;3)消除凹陷,型面再现性高;4)省塑料,可用强度及价格更低的塑料;5)可用强度和价格更低的模具金属;6)厚薄件一体成型,减少模具及装配线数目;7)可用较厚的筋,角板等补强件,提高制品刚性,使得制件公称厚度得以变薄。
8)增强设计自由度。
3.气辅射胶控制工艺1)短射工艺,即胶料未完全充满型腔时,继之以氮气注射;2)满射工艺,塑胶熔体充满型腔之后,停止注射,继之以氮气注射。
短射工艺的特点:在气辅注塑中,塑胶注射取决于胶件形状及胶料性能,在以下条件才可进行短射。
1)胶件必须有独立完整的气体通道,即气流在穿透胶件时,无分支气道可走。
2)气体通道中多余胶料有足够的溢流空间。
3)胶料流动性优良,粘度不可太低,尽量避免使用含破坏高分子键的填充物的胶料。
4)胶料导热度较低,有可较长时间保持熔融状态的能力。
满射工艺特点:胶件射胶完成,通过气体代替啤机,防止胶件收缩。
其优点在于,啤机保压是以射胶量及压力来防止胶件收缩,气辅保压,则以气体穿透塑胶收缩后的空间,防止胶件表层埸陷。
4.气辅压力分析:现我们看以下气辅压力与啤机压力的对比:1)气辅压力a)低气压800psi=56.34kg/cm2b)中气压1500psi=105.63 kg/cm2c)高气压2500psi=176.06kg/cm22)啤机压力a)100 TON注塑最大压力188Mpa=1917 kg/cm2b)280 TON注塑最大压力150Mpa=1530 kg/cm2c)650TON注塑最大压力153Mpa=1560 kg/cm2从以上压力对比可知,氮气压力只相当于普通啤机注塑压力的十分之一,甚至更少。
气辅注塑

1)封闭式气体注射(SEALED INJECTION GAS)方法: * 是把气体直接注入模腔内,使塑料成品中空的方法。无需采用活阀,只是 通过简单模具加工,把气辅气嘴装在模具中。 * 在同一模具上,可有单一或多个注入气体的地方,这视乎同产品的需要, 慕求令产品有良好效果和提供产品设计有较大的灵活性。
太小会使气体流动失去控制 7.冷却要尽量均匀,内外壁温差要尽量小
8.在流道上放置合理流道半径的截流块,辅助注塑设备按工艺需求大致应有以下几类: 1、氮气机:主要用于氮气的制造 2、氮气增压器:主要是将氮气的气压加大,以便于氮气的注入 3、气辅控制器:主要用于控制氮气注入量、气压、时间及排气的控制,是
• 降低生产成本
– 由于减少了壁厚,因此降低了零件成品的总重量. – 由于壁厚较小,因此缩短了冷却时间和循环时间. – 由于降低了锁模力和注塑保压压力,能源消耗成本降低. – 由于零件的集成化,从而降低了装配成本.
• 降低投资成本
– 由于注射压力较低,因此可以降低注塑机的锁模压力,可使用吨位较小的注塑 机.
整个气辅设备的控制中心 4、气辅配件:主要有气针、气管及各种接头等,用于气辅设备与模具的连
接
因各种设备加在一起,占用的空间较大,现有很大一部分已采用一体化的气 辅系统。
END
同传统注射成型工艺相比.应用气体辅助注塑技术,有以下优点:
• 自由设计
– 综合功能较为复杂的塑胶零件可以整装为单一的组件. – 可以在同一零件上结合厚壁和薄壁部分. – 使用空心的"加强筋"部分可以提高其强度.
• 提高零件质量
– 由于减小了微收缩,因此扭曲和变形就减少了. – 消除缩痕. – 由于注射点的数量减少,所以波纹和熔接线也相应减少.
气体辅助注射成型
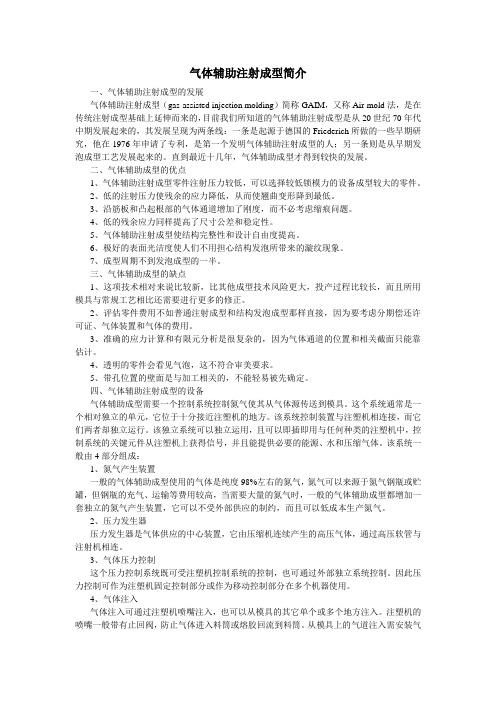
气体辅助注射成型简介一、气体辅助注射成型的发展气体辅助注射成型(gas-assisted injection molding)简称GAIM,又称Air-mold法,是在传统注射成型基础上延伸而来的,目前我们所知道的气体辅助注射成型是从20世纪70年代中期发展起来的,其发展呈现为两条线:一条是起源于德国的Friederich所做的一些早期研究,他在1976年申请了专利,是第一个发明气体辅助注射成型的人;另一条则是从早期发泡成型工艺发展起来的。
直到最近十几年,气体辅助成型才得到较快的发展。
二、气体辅助成型的优点1、气体辅助注射成型零件注射压力较低,可以选择较低锁模力的设备成型较大的零件。
2、低的注射压力使残余的应力降低,从而使翘曲变形降到最低。
3、沿筋板和凸起根部的气体通道增加了刚度,而不必考虑缩痕问题。
4、低的残余应力同样提高了尺寸公差和稳定性。
5、气体辅助注射成型使结构完整性和设计自由度提高。
6、极好的表面光洁度使人们不用担心结构发泡所带来的漩纹现象。
7、成型周期不到发泡成型的一半。
三、气体辅助成型的缺点1、这项技术相对来说比较新,比其他成型技术风险更大,投产过程比较长,而且所用模具与常规工艺相比还需要进行更多的修正。
2、评估零件费用不如普通注射成型和结构发泡成型那样直接,因为要考虑分期偿还许可证、气体装置和气体的费用。
3、准确的应力计算和有限元分析是很复杂的,因为气体通道的位置和相关截面只能靠估计。
4、透明的零件会看见气泡,这不符合审美要求。
5、带孔位置的壁面是与加工相关的,不能轻易被先确定。
四、气体辅助注射成型的设备气体辅助成型需要一个控制系统控制氮气使其从气体源传送到模具。
这个系统通常是一个相对独立的单元,它位于十分接近注塑机的地方。
该系统控制装置与注塑机相连接,而它们两者却独立运行。
该独立系统可以独立运用,且可以即插即用与任何种类的注塑机中,控制系统的关键元件从注塑机上获得信号,并且能提供必要的能源、水和压缩气体。
气辅注塑成型技术

气辅注塑成型技术气辅注塑工艺是国外八十年代研究成功,九十年代才得到实际应用的一项实用型注塑新工艺,其原理是利用高压隋性气体注射到熔融的塑料中形成真空截面并推动熔料前进,实现注射、保压、冷却等过程,使产品形成真空。
气辅设备包括气辅控制单元和氮气发生装置;氮气发生装置主要包括氮气发生器,氮气压缩机,氮气储气瓶。
它是独立于注塑机外的另一套系统,其与注塑机的唯一接口是注射信号连接线。
注塑机将一个注射信号注射开始或螺杆位置传递给气辅控制单元之后,便开始一个注气过程,等下一个注射过程开始时给出另一个注射信号,开始另一个循环,如此反复进行。
气体辅助注塑过程可分为注塑期,充气期,气体保压期和脱模期。
1.注塑期:所需塑料注塑量要通过实验找出来,以保证在充气期间,气体不会把成品表面冲破及能有一个理想的充气体积,通常注满产品的70%-95%。
注入熔体2.充气期:可以在注射中或后的不同时间注入气体,气体注入的压力必需大于注塑压力,以达到产品成中空状态。
注入氮气3.气保压期:当成品内部被气体填充后,气体在成品中空部分的压力就成为保压压力,可大大减低成品的缩水及变形率。
保压成型4.脱模期:随冷却周期完成,防止产品暴裂,自动排出气体,模具内压力降至大气压力,成品由模腔内顶出。
排出气体和产品出模气体辅助注塑成型进气方式有两种:一种由射嘴进入成品;二种由模具进入成品,这两种各有各的优点和缺点。
一从射嘴进气优点:1)修改现在有旧模具即可使用。
2)流道形成中空状,减少塑料使用。
3)成品无气针所留下之气口痕迹。
缺点:1)所有气体通道必须相通连接。
2)气体通道必须对称且平衡。
3)不能用于热流道模具上使用。
4)注塑机射嘴更换且费用较高。
二从模具进气优点:1)可以多处进气,气体通道不需完全相通连接。
2)气体与塑料可同时射入。
3)可允许使用热流道模具。
4)可使用于非对称模穴之产品成型。
缺点:1)模具须重新开发设计。
2)气针会留下气口痕迹。
塑料制品成型应用气体辅助成型技术,有以下优点:1)节省塑胶原料,节省可高达50%。
注塑成型中的气体辅助技术应用
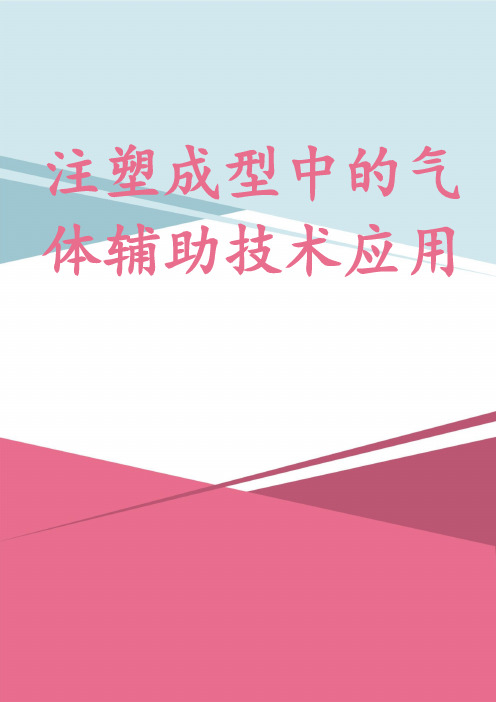
注塑成型中的气体辅助技术应用注塑成型中的气体辅助技术应用注塑成型是一种常用的塑料加工方法,通过将熔化的塑料注入模具中,经过冷却固化后得到所需的塑料制品。
然而,在注塑成型过程中,常常会出现一些问题,如缺陷、翘曲等。
为了解决这些问题,气体辅助技术在注塑成型中得到了广泛的应用。
气体辅助技术是指在注塑成型过程中,通过向模具中注入气体,利用气体的性质对塑料进行辅助成型的一种方法。
在注塑成型过程中,通过在模具中注入气体,可以改善产品表面质量,减少翘曲和缩水等缺陷,提高产品的整体性能。
首先,气体辅助技术可以改善产品的表面质量。
在注塑成型中,由于塑料的热胀冷缩和浇注冷却的不均匀性,常常会出现产品表面的缺陷,如气泡、痕迹等。
通过在模具中注入气体,可以使塑料在充填过程中更加均匀,减少气泡的产生,从而改善产品的表面质量,使其更加光滑。
其次,气体辅助技术可以减少产品的翘曲和缩水。
在注塑成型中,由于塑料的收缩性质,产品往往会出现翘曲和缩水等问题。
通过在模具中注入气体,可以产生一定的气压,使塑料在冷却固化过程中更加均匀,减少翘曲和缩水的可能性,从而提高产品的几何稳定性和尺寸精度。
最后,气体辅助技术可以改善产品的整体性能。
在注塑成型中,由于塑料的结晶性质,产品往往会出现内部应力集中的问题,从而影响产品的强度和韧性。
通过在模具中注入气体,可以使塑料在充填过程中形成空腔结构,减少内部应力的集中,提高产品的整体性能,使其更加坚固耐用。
综上所述,气体辅助技术在注塑成型中的应用可以改善产品的表面质量,减少翘曲和缩水,提高产品的整体性能。
随着技术的不断发展,气体辅助技术在注塑成型中的应用前景更加广阔,将为塑料制品的生产提供更多的可能性。
注塑气辅技术指南

气体辅助注塑成型是从传统的注射成型发展而来的。它的工作原理是将高压氮气通过注塑喷嘴或气针射至模腔内。射入的气体会产生气泡,这个气泡将推动熔体塑料进入模具的末端从而产生中空截面。
气辅成型有很多工艺和设计特点,这些工艺和设计特点有助于满足应用要求。一些潜在的特性和优点如下:
Extend Design Guidelines
Troubleshooting
过程控制
厚壁形成
厚壁的控制
速度对厚壁的影响
零件的连贯性
厚壁和气体渗入的相互作用
发现并修理故障
About Gas Assist Injection Molding
Gas assist injection molding is a variation of conventional injection molding that can be easily retrofitted to an existing injection press by the addition of an auxiliary gas unit. The usual injection of molten plastic is assisted by the introduction of pressurized gas (usually nitrogen) into the mold. The gas produces a bubble which pushes the plasticinto the extremities of the mold creating hollow sections as the bubble propagates.
-增加结构件的强度/坚固度对质量的比值,
- Molding large cross-sections (parts consolidation)
气体辅助注射成型技术原理及应用.

气体辅助注射成型技术原理及应用气体辅助注射成型(Gas-Assisted Injection Molding, GAIM)技术最早可追溯到20世纪70年代,该技术在20世纪80年代末得到了完善并实现了商品化。
从20世纪90年代开始,作为一项成功的技术,气体辅助注射成型技术在美、日、欧等发达国家和地区得到了广泛应用。
目前该技术主要被应用在家电、汽车、家具、日常用品、办公用品等加工领域中。
气体辅助注射成型技术的工艺过程气体辅助注射成型技术的工艺过程是:先向模具型腔中注入塑料熔体,再向塑料熔体中注入压缩气体。
借助气体的作用,推动塑料熔体充填到模具型腔的各个部分,使塑件最后形成中空断面而保持完整外形。
在成型后的制品中,由气体形成的中空部分被称为气道。
由于具有廉价、易得且不与塑料熔体发生反应的优点,因此一般所使用的压缩气体为氮气。
气体辅助注塑成型周期可分为以下六个阶段。
(1)塑料充模阶段这一阶段与普通注塑成型基本相同,只是普通注塑成型时塑料熔体是充满整个型腔,而气体辅助注塑成型时塑料熔体只充满局部型腔,其余部分要靠气体补充。
(2)切换延迟阶段这一阶段是塑料熔体注射结束到气体注射开始时的时间,这一阶段非常短暂。
(3)气体注射阶段此阶段是从气体开始注射至整个型腔被充满的时间,这一阶段也比较短,但对制品质量的影响极为重要,如控制不好,会产生空穴、吹穿、注射不足和气体向较薄的部分渗透等缺陷。
(4)保压阶段熔体内气体压力保持不变或略有上升使气体在塑料内部继续穿透,以补偿塑料冷却引起的收缩(5)气体释放阶段使气体入口压力降到零。
(6)冷却开模阶段将制品冷却到具有一定刚度和强度后开模取出制品。
根据具体工艺过程的不同,气体辅助注射成型可分为标准成型法、副腔成型法、熔体回流法和活动型芯法四种。
1、标准成型法标准成型法是先向模具型腔中注入经准确计量的塑料熔体(如图1a所示),再通过浇口和流道注入压缩气体。
气体在型腔中塑料熔体的包围下沿阻力最小的方向扩散前进,对塑料熔体进行穿透和排空(如图1b所示),最后推动塑料熔体充满整个模具型腔并进行保压冷却(如图1c所示),待塑料制品冷却到具有一定刚度和强度后,开模将其顶出(如图1d所示)。
气体辅助注塑成型技术

气体辅助注塑成型技术嘿,朋友们!今天咱来聊聊气体辅助注塑成型技术,这可真是个了不起的玩意儿啊!你看啊,普通注塑成型就像是盖房子只用砖头,而气体辅助注塑成型呢,就好比在盖房子的时候加了根钢梁,那效果可就大不一样啦!它能让制品变得更轻巧、更坚固,还能节省材料呢!这就好像咱做饭,同样的食材,有的人就能做出美味佳肴,有的人就只能做出勉强能吃的东西,这气体辅助注塑成型技术就是那个能把注塑变得超级棒的“魔法调料”呀!它是怎么做到的呢?简单来说,就是在注塑过程中注入气体。
这气体就像个小精灵,在模具里跑来跑去,把塑料推到该去的地方,让制品内部形成中空的结构。
这有啥好处呢?哎呀,好处可多啦!比如说,可以减少塑料的用量,降低成本啊。
你想想,同样的一个东西,用更少的塑料就能做出来,那不是省钱嘛!而且啊,这样做出来的制品还不容易变形,质量杠杠的!咱再打个比方,这就好比是吹气球,气体进去了,把气球撑起来了,可气球还是那个气球,但它变得更饱满、更有型了。
这气体辅助注塑成型技术不就是这样嘛,让塑料制品变得更完美!你说这技术神奇不神奇?它能让那些复杂形状的制品变得轻而易举就能制造出来。
以前那些很难做出来的东西,现在有了它,都不是事儿啦!就好像原本要翻山越岭才能到达的地方,现在有条高速公路直接通到那儿了,多方便呀!还有啊,这技术对环境也有好处呢!用的塑料少了,不就减少了对资源的浪费嘛,也减少了垃圾的产生。
这不是一举多得嘛!不过呢,要想用好比这个技术,可得下点功夫。
就像学骑自行车,得掌握好平衡,不然就会摔倒。
咱得了解它的脾气,知道怎么去调整参数,让它乖乖听话,给咱做出最好的制品。
这可不是随便谁都能做到的哦,得有经验,得有技术!咱中国现在在这方面发展得也很不错呢!越来越多的企业开始用上了这神奇的技术,生产出了好多高质量的产品。
这说明啥?说明咱中国人聪明啊,啥技术都能掌握,啥难题都能解决!总之呢,气体辅助注塑成型技术就是注塑领域的一颗闪亮明星,给我们带来了好多惊喜和好处。
气辅技术

一、什么是气辅注塑
它是利用高压惰性气体在注塑件内部产生中空截面,并推动 熔体完成充填过程的一项技术。原理是当氮气注入熔胶后, 沿着阻力最小的路径形成中空的连续通道,包括了3个方面:
1、氮气容易进入产品的厚截面处; 2、氮气从高压处向低压处推动熔胶;
3、氮气推动熔胶充填模腔最后的位置。
二、气辅注塑的分类及应用
11 多型腔多气道成形产品,是否一条气道由一路气来控制成形。
6 气道周边气道白印
气道边缘材料在气道内部气压作用下受挤压而造成边缘一 条白色痕迹。此白印因气辅局部气体保压造成完全消除比较困 难,从工艺角度可减轻。
1 降低气辅成形压力,此白印会减轻。
(包括前面提到解决产品串气在模具上作的改进方法也适用)
2 模具气道边缘皮纹长时间受侧向积压,轻微变形,模具喷砂处理 后白印会减轻。
3 产品皮纹深度深,会掩盖此缺陷。表面白印不会很明显。
(深皮纹对气辅成形有利:A 可掩盖缩瘪,白印缺陷。B 深皮纹产 品同模具表面接触面积大,散热快可提高气道外壁同内部熔融料 的温差,有利于气辅成形。)
4 材料颜色 :浅色材料产品此缺陷不明显 ,黑色材料产品此缺陷 明显。
1 产品气道表面缩瘪
A 整条气道缩瘪 1 产品是否吹气, 气道不吹通产品表面肯定缩瘪 2 吹气压力是否偏低?吹气保压压力低无法抵御材 料收缩引起表面缩瘪。 3 溢料井是否完整?溢料井不完整,吹气压力在溢料井 处被卸压,气道内实际压力低于显示压力。 4 溢料口及溢料冷流道偏小。溢料口和溢料冷流道偏小,气道 内废料不能在短时间内吹出,引起气道表面缩瘪。
b气道未被完全吹通,溢料井未被填满,吹气压力低或发生气针堵塞导 致废料无法完全吹出引起表面缩瘪。调整吹气压力和检查气路是否通 畅。
气体辅助注塑成型技术简介
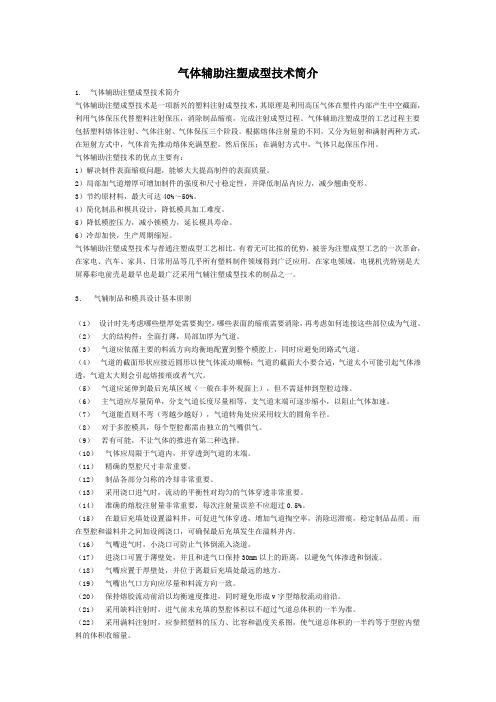
气体辅助注塑成型技术简介1. 气体辅助注塑成型技术简介气体辅助注塑成型技术是一项新兴的塑料注射成型技术,其原理是利用高压气体在塑件内部产生中空截面,利用气体保压代替塑料注射保压,消除制品缩痕,完成注射成型过程。
气体辅助注塑成型的工艺过程主要包括塑料熔体注射、气体注射、气体保压三个阶段。
根据熔体注射量的不同,又分为短射和满射两种方式,在短射方式中,气体首先推动熔体充满型腔,然后保压;在满射方式中,气体只起保压作用。
气体辅助注塑技术的优点主要有:1)解决制件表面缩痕问题,能够大大提高制件的表面质量。
2)局部加气道增厚可增加制件的强度和尺寸稳定性,并降低制品内应力,减少翘曲变形。
3)节约原材料,最大可达40%~50%。
4)简化制品和模具设计,降低模具加工难度。
5)降低模腔压力,减小锁模力,延长模具寿命。
6)冷却加快,生产周期缩短。
气体辅助注塑成型技术与普通注塑成型工艺相比,有着无可比拟的优势,被誉为注塑成型工艺的一次革命,在家电、汽车、家具、日常用品等几乎所有塑料制件领域得到广泛应用。
在家电领域,电视机壳特别是大屏幕彩电前壳是最早也是最广泛采用气辅注塑成型技术的制品之一。
3.气辅制品和模具设计基本原则(1)设计时先考虑哪些壁厚处需要掏空,哪些表面的缩痕需要消除,再考虑如何连接这些部位成为气道。
(2)大的结构件:全面打薄,局部加厚为气道。
(3)气道应依循主要的料流方向均衡地配置到整个模腔上,同时应避免闭路式气道。
(4)气道的截面形状应接近圆形以使气体流动顺畅;气道的截面大小要合适,气道太小可能引起气体渗透,气道太大则会引起熔接痕或者气穴。
(5)气道应延伸到最后充填区域(一般在非外观面上),但不需延伸到型腔边缘。
(6)主气道应尽量简单,分支气道长度尽量相等,支气道末端可逐步缩小,以阻止气体加速。
(7)气道能直则不弯(弯越少越好),气道转角处应采用较大的圆角半径。
(8)对于多腔模具,每个型腔都需由独立的气嘴供气。