气体辅助注塑成型技术简介
气体辅助注塑成型技术

气体辅助注塑成型技术第一章: 气体辅助注塑成型简介1、气体辅助注塑成型的发明及发展概述: 多年来,人们一直在研究中空塑料制品的成型加工技术及对塑料产品的质量改善作出研究。
1944年,Opavsky将气体或液体通过注射器注入到树脂中以达到改善产品质量为目的,但未获成功,这是最早的气辅概念研究。
我们今天所知道的气体辅助注塑成型技术是从20世纪70年代中期发展起来的,德国人Ernst Friederich是第一个发明气体辅助注塑成型工艺的人(1975年)(他的原理是将已加压的气体通过喷嘴注射到熔融物料当中,使熔融物料与模具内壁表面充分接触)。
由于当时的技术存在相当的局限性,并没有得到一定的重视。
直到80年代中期,该项技术才开始得到真正的发展及运用。
后来在欧洲出现了包括: Cinpress, Battenfeld, Ferromatik, Stork, Engel 及Johnson Controls 一批设备生产商,并在不断地改良这种技术。
到了90年代后期,气体辅助注塑成型技术得到飞速的发展及运用。
2、气体辅助注塑成型制品的两个主要类型:●封闭式气道(SINGEL GAS CHANNEL) ●开放式气道(GAS CHANNEL) 封闭式气道制品主要由一个厚壁截面和气体穿行的通道组成,如门把手、扶手、管状把手等都属于这种结构。
因为气体的扩散有一条设定好的路线(即胶料较厚,温度较高,流动性较好的部分,亦即是气体流动的方向),制品能达到最佳的节省材料的目的,而且由于制品中空结构使刚性加强而不用增加质量。
开放式气道制品主要是薄壁制品(壁厚不能少于2MM),类似于传统的加强筋结构制品。
气体会从较厚的加强筋向前扩散(及气体流动的方向:胶料相对较厚的部分,形成气道GAS CHANNEL),但气体可能会穿透制品的薄壁部分(有时会出现指形扩散:指纹效应FINGERING),即高压气体往较厚胶料或密度较低的部分渗入。
3、气体辅助注塑成型方法的优点:●制品残余应力降低●翘曲变形较小●减少/消除缩痕●简化模具设计●制品综合性能提高●缩短成型周期●合模力吨位要求降低●射胶压力降低4、气体辅助注塑成型适用材料: ABS、ABS/PC、HIPS、PA、PBT、PC、PS、PVC、PET、PP、PPE等第二章: 气体辅助注塑成型的方法及原理 1、气体辅助注塑成型的原理:通过管道与模具连接,把高压气体(氮气)注入到模腔的塑料熔体中,形成局部的中空,加速产品冷却成型。
气体辅助注射成型技术原理及应用

气体辅助注射成型技术原理及应用
气体辅助注射成型技术的应用
● 管状和棒状零件,如门把手、转椅支座、吊 钩、扶手、导轨、衣架等。这是因为,管状结 构设计使现存的厚截面适于产生气体管道,利 用气体的穿透作用形成中空,从而可消除表面 成型缺陷,节省材料并缩短成型周期。
气体辅助注射成型技术原理及应用
在进行模具设计之前,利用MoldFlow MPI 5.0对设计方案进行了模拟。 分析模型如图8所示,在该分析模型中确定了浇口及进气口位置。在模拟中, 设定预注射量为70%,熔体温度为230℃,注射时间为3s,延迟时间为1.5s, 气体压力为20MPa。
气体辅助注射成型技术原理及应用
● 可通过气体的穿透减轻制品重量,节省原材料 用量,并缩短成型周期,提高生产率。
● 该技术可适用于热塑性塑料、一般工程塑料及 其合金以及其他用于注射成型的材料。
气体辅助注射成型技术原理及应用
气体辅助注射成型技术的缺点是:
●需要增加供气和回收装置及气体压力控制单元, 从而增加了设备投资;对注射机的注射量和注射 压力的精度要求有所提高;制品中接触气体的表 面与贴紧模壁的表面会产生不同的光泽;制品质 量对工艺参数更加敏感,增加了对工艺控制的精 度要求。
气体辅助注射成型CAE分析的主要作用是:
1.分析产品的成型工艺性 2.评价模具的设计是否合理 3.优化成型工艺参数 4.预测制品可能出现的缺陷
气体辅助注射成型技术原理及应用
下面以成型把手为例,介绍气体辅助注射成型 CAE分析的过程。
如图7所示的把手材料为ABS,手柄位置壁厚为14mm。由于是外观件,对 其成型要求很高。
9气体辅助注塑成型

气体辅助注射成型
可能的问题-内部起泡
原因是气体进入了熔体里.
气体辅助注射成型
可能的问题-内部起泡
解决方案:
增加气体保压时间 缓慢地释放气体 增加延迟时间 降低气体压力 保持材料干燥 降低熔体温度 改变塑料材料
气体辅助注射成型
可能的问题-手指效应
气体辅助注射成型
可能的问题-手指效应
解决方案:
增加熔体注入量 增加气体注入时间 增加气体延迟时间 降低气体压力 增加气道高度尺寸
进气位臵
通过模具型腔进气
气体辅助注射成型
制品形状-加强筋
普通塑件加强筋的厚度应比塑件主体壁厚薄 ( 约为其一半 ) ,即使这样也免不了在加强筋所 在壁的对面产生凹陷,因此应尽量少采用。在 气辅注塑中加强筋可设计得比塑件主体壁厚大 得多,作为气体通路,不但可避免产生凹陷, 而且可大大地增加塑件的刚度,粗大的加强筋 通常不会增加制品总重,因为平板部分可减薄, 在筋中的大量气体也可减轻重量。
气体辅助注射成型
翘曲和变形
气辅成型能消除制品 的翘曲和变形吗?
气体辅助注射成型
翘曲和变形
气体辅助注射成型
剩余壁厚-注入树脂量
太少
太多
气体辅助注射成型
剩余壁厚-注入树脂量
气体辅助注射成型
剩余壁厚-模温
以PC(Makrolon® 2458)为例子,模温变化大于 30°C而 制品的壁厚基本上不变,平均壁厚的改变量仅 0.02mm.
气体辅助注射成型
适宜成型的制品
例子:电视机前框改为气辅注塑成型,制件经重新设 计后,重量减轻了26%,零件数减少了54%。
气体辅助注射成型
适宜成型的制品
例子:马自达汽车保险杠。用气辅成型克服了表面凹陷,
气体辅助注射成型【范本模板】
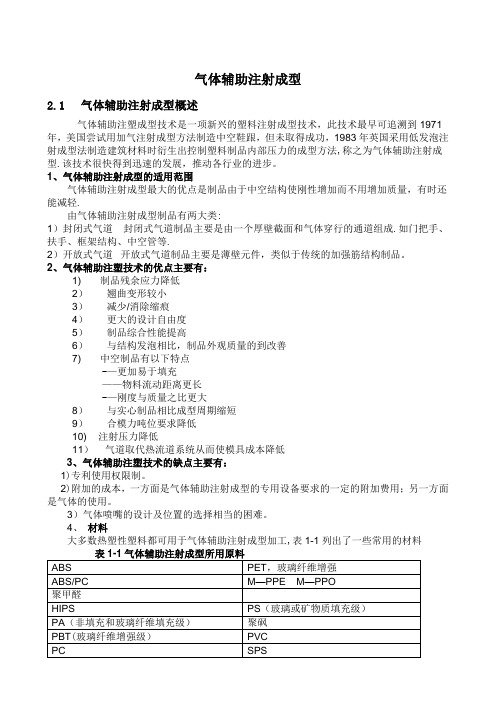
气体辅助注射成型2.1气体辅助注射成型概述气体辅助注塑成型技术是一项新兴的塑料注射成型技术,此技术最早可追溯到1971年,美国尝试用加气注射成型方法制造中空鞋跟,但未取得成功,1983年英国采用低发泡注射成型法制造建筑材料时衍生出控制塑料制品内部压力的成型方法,称之为气体辅助注射成型.该技术很快得到迅速的发展,推动各行业的进步。
1、气体辅助注射成型的适用范围气体辅助注射成型最大的优点是制品由于中空结构使刚性增加而不用增加质量,有时还能减轻.由气体辅助注射成型制品有两大类:1)封闭式气道封闭式气道制品主要是由一个厚壁截面和气体穿行的通道组成.如门把手、扶手、框架结构、中空管等.2)开放式气道开放式气道制品主要是薄壁元件,类似于传统的加强筋结构制品。
2、气体辅助注塑技术的优点主要有:1)制品残余应力降低2)翘曲变形较小3)减少/消除缩痕4)更大的设计自由度5)制品综合性能提高6)与结构发泡相比,制品外观质量的到改善7)中空制品有以下特点-—更加易于填充——物料流动距离更长-—刚度与质量之比更大8)与实心制品相比成型周期缩短9)合模力吨位要求降低10)注射压力降低11)气道取代热流道系统从而使模具成本降低3、气体辅助注塑技术的缺点主要有:1)专利使用权限制。
2)附加的成本,一方面是气体辅助注射成型的专用设备要求的一定的附加费用;另一方面是气体的使用。
3)气体喷嘴的设计及位置的选择相当的困难。
4、材料大多数热塑性塑料都可用于气体辅助注射成型加工,表1-1列出了一些常用的材料聚醚酰亚胺HDPE5、设计注意事项:气体辅助注射成型制品的优化设计需要注意以下三点:1)气道布局的优化2)气道尺寸与制品相关3)平衡物料填充方式气道在模腔内的布局既包括气体喷嘴的定位,也包括气道进入模具位置的选择,气体会沿着阻力最小的方向向前流动。
在物料进入模具之后,模腔中压力最小的地方必须靠近气道的末端,这个压力差会促使气流沿着预期流道前进,从而推动物料充满整个型腔。
气体辅助注塑成型技术简介.
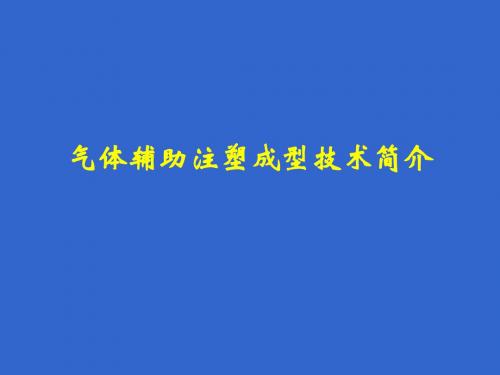
一、气体辅助注塑原理:
气体辅助注塑原理是把高压氮气经气辅 主控制器(分段压力控制系统)直接注射入 模腔内塑化塑料里,使塑件内部膨胀而造成 真空,但仍然保持产品表面的外形完整无缺, 减小产品表面的收缩、产品变形和翘曲,从 而达到提高产品的质量,降低成本的目的。
二、采用气体辅助注塑技术的优点:
应用气辅技术的国内公司:康佳、长虹、创维、科龙、 美的、海信等等;上海延锋伟世通、浙江远翅、上海龙贤汽 配、余姚塑料四厂、宁波国雅汽车内饰件厂以及各类注塑厂 都应用了气辅技术。
四、气体辅助注塑整系统的原理图:
A、整套系统
氮气 发生 器
低压 贮气缸
电动 高压 增压机
高压 贮气缸
气辅 主控 制器
单相电源 压缩空气 三相电源
六、气道形式:
• C、全部中空
七、我厂第一副气辅产品-前门拉手 (LZ111-6402101)
八、前门拉手采用气辅方案:
八、前门拉手采用气辅方案:
谢谢!
——END——
B、简易系统
氮气 缸瓶
气动 高压 增压机
压缩空气
单相电源
高压 贮气缸
气辅 主控 制器
单相——以定量塑化塑料充填入模腔内。所需塑料 份量要通过试验找出来,以保证在充氮期间,气体不 会把成品表面冲破及能有一理想的充氮体积。
2、充气期——注塑期中或后,不同时间注入气体,气体 注入的压力必需大于注塑压力,以达至产品成中空状 态。
模具的工作寿命; 7、降低注塑机的锁模压力,可高达50%; 8、提高注塑机的工作寿命和降低耗电量。
三、气体辅助注塑技术的应用:
基本上所有用于注塑的热塑性塑料及一般的工程材料 (如PS、HIPS、PP、ABS…)都适用于气辅技术。
气体辅助注塑成型技术
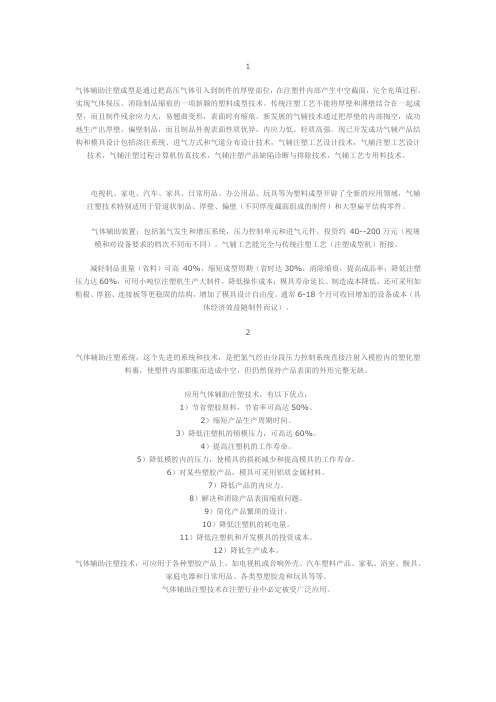
1气体辅助注塑成型是通过把高压气体引入到制件的厚壁部位,在注塑件内部产生中空截面,完全充填过程、实现气体保压、消除制品缩痕的一项新颖的塑料成型技术。
传统注塑工艺不能将厚壁和薄壁结合在一起成型,而且制件残余应力大,易翘曲变形,表面时有缩痕。
新发展的气辅技术通过把厚壁的内部掏空,成功地生产出厚壁、偏壁制品,而且制品外观表面性质优异,内应力低。
轻质高强。
现已开发成功气辅产品结构和模具设计包括浇注系统、进气方式和气道分布设计技术,气辅注塑工艺设计技术,气辅注塑工艺设计技术,气辅注塑过程计算机仿真技术,气辅注塑产品缺陷诊断与排除技术,气辅工艺专用料技术。
电视机、家电、汽车、家具、日常用品、办公用品、玩具等为塑料成型开辟了全新的应用领域,气辅注塑技术特别适用于管道状制品、厚壁、偏壁(不同厚度截面组成的制件)和大型扁平结构零件。
气体辅助装置:包括氮气发生和增压系统,压力控制单元和进气元件。
投资约40--200万元(视规模和对设备要求的档次不同而不同)。
气辅工艺能完全与传统注塑工艺(注塑成型机)衔接。
减轻制品重量(省料)可高40%,缩短成型周期(省时达30%,消除缩痕,提高成品率;降低注塑压力达60%,可用小吨位注塑机生产大制件,降低操作成本;模具寿命延长、制造成本降低,还可采用如粗根、厚筋、连接板等更稳固的结构,增加了模具设计自由度。
通常6-18个月可收回增加的设备成本(具体经济效益随制件而议)。
2气体辅助注塑系统,这个先进的系统和技术,是把氮气经由分段压力控制系统直接注射入模腔内的塑化塑料裹,使塑件内部膨胀而造成中空,但仍然保持产品表面的外形完整无缺。
应用气体辅助注塑技术,有以下优点:1)节省塑胶原料,节省率可高达50%。
2)缩短产品生产周期时间。
3)降低注塑机的锁模压力,可高达60%。
4)提高注塑机的工作寿命。
5)降低模腔内的压力,使模具的损耗减少和提高模具的工作寿命。
6)对某些塑胶产品,模具可采用铝质金属材料。
气体辅助成型综述

注射成型产品及模具设计综述引言:人们很早就开始研究如何彻底消除裂痕而又能节省材料的有效方法。
曾经研究过的方法有低压注塑、气体补压注塑、混合注塑、气体发泡成型等,但效果都不很理想。
气体辅助注塑工艺是将气体直接注入熔胶中,气体内的压力抵消了塑料在冷却过程中的体积收缩。
用这种方式注塑出来的制品,不仅没有裂痕,而且还有许多其他的优越性。
气体辅助注射成型技术(简称:气辅成型)是20世纪80年代在结构发泡成型工艺基础上发展起来的一项新兴的塑料注射成型技术,是塑料注射成型工艺技术中的一项革命。
气辅成型应用在最近一、二年来有强劲的增长趋势,它具有多种优点,但因为经验不足和气体不易控制,增加了气辅成型产品开发上的困难。
简要介绍:气辅注射模塑,又称气体注射模塑是一种创新的注射成型工艺。
它是自住复式螺杆注射机问世以来.注射成型工业上最重要的发展之一,它能用于生产无内应力、表面光滑且无凹陷的大型制件.在生产较厚的制件时,气辅注射模塑还可以通过减少所需的夹紧吨位、用材量和循环时间来降低制件成本.气辅注射模塑的工艺过程如图1所示。
首先把部分熔融的塑料注射到模具中.我们称此为“欠料注射”。
紧接着再注入一定体积或一定压力的惰性气体(通常为氮气)到熔融塑料流中。
由于靠近模具表面部分的塑料温度低、表面张力高.而处在制件较厚部分中心的塑料熔融体的温度高、粘度低,致使气体易于在制件较厚的部位(如加强筋)形成空腔.而被气体所取代的熔融塑料被推向模具的末端,形成所要成型的制件。
在气辅注射模塑中.由于气体的压力始终使塑料紧贴着模具的表面.制件较厚部分的外表面不能形成“凹陷”.大大提高了制件的质量。
此工艺不但简化了模具设计,降低了模具成本.还增加了制件设计的灵活性。
在合理的设计下,可使制件的重量比传统注射模塑减少10--50%,且使制件得到较高的强度与重量比。
另外。
氮气充满制件的气体压力与传统注射模塑所需的压力柑比要小得多.因此所需的模具夹紧力也较小。
气体辅助注塑工艺简介

气体辅助注塑工艺简介1.气体辅助注塑目前所指的气体辅助注塑:是指将氮气注射入产品内,使产品内部形成中空。
模具打开前,控制器会将塑胶工件内的氮气释放回大气中。
2.气辅注塑成形工艺的优势1)低射胶、低锁模力;2)压力分布均匀、收缩均匀、残余应力低、不易翘曲,尺寸稳定;3)消除凹陷,型面再现性高;4)省塑料,可用强度及价格更低的塑料;5)可用强度和价格更低的模具金属;6)厚薄件一体成型,减少模具及装配线数目;7)可用较厚的筋,角板等补强件,提高制品刚性,使得制件公称厚度得以变薄。
8)增强设计自由度。
3.气辅射胶控制工艺1)短射工艺,即胶料未完全充满型腔时,继之以氮气注射;2)满射工艺,塑胶熔体充满型腔之后,停止注射,继之以氮气注射。
短射工艺的特点:在气辅注塑中,塑胶注射取决于胶件形状及胶料性能,在以下条件才可进行短射。
1)胶件必须有独立完整的气体通道,即气流在穿透胶件时,无分支气道可走。
2)气体通道中多余胶料有足够的溢流空间。
3)胶料流动性优良,粘度不可太低,尽量避免使用含破坏高分子键的填充物的胶料。
4)胶料导热度较低,有可较长时间保持熔融状态的能力。
满射工艺特点:胶件射胶完成,通过气体代替啤机,防止胶件收缩。
其优点在于,啤机保压是以射胶量及压力来防止胶件收缩,气辅保压,则以气体穿透塑胶收缩后的空间,防止胶件表层埸陷。
4.气辅压力分析:现我们看以下气辅压力与啤机压力的对比:1)气辅压力a)低气压800psi=56.34kg/cm2b)中气压1500psi=105.63 kg/cm2c)高气压2500psi=176.06kg/cm22)啤机压力a)100 TON注塑最大压力188Mpa=1917 kg/cm2b)280 TON注塑最大压力150Mpa=1530 kg/cm2c)650TON注塑最大压力153Mpa=1560 kg/cm2从以上压力对比可知,氮气压力只相当于普通啤机注塑压力的十分之一,甚至更少。
气辅注塑

1)封闭式气体注射(SEALED INJECTION GAS)方法: * 是把气体直接注入模腔内,使塑料成品中空的方法。无需采用活阀,只是 通过简单模具加工,把气辅气嘴装在模具中。 * 在同一模具上,可有单一或多个注入气体的地方,这视乎同产品的需要, 慕求令产品有良好效果和提供产品设计有较大的灵活性。
太小会使气体流动失去控制 7.冷却要尽量均匀,内外壁温差要尽量小
8.在流道上放置合理流道半径的截流块,辅助注塑设备按工艺需求大致应有以下几类: 1、氮气机:主要用于氮气的制造 2、氮气增压器:主要是将氮气的气压加大,以便于氮气的注入 3、气辅控制器:主要用于控制氮气注入量、气压、时间及排气的控制,是
• 降低生产成本
– 由于减少了壁厚,因此降低了零件成品的总重量. – 由于壁厚较小,因此缩短了冷却时间和循环时间. – 由于降低了锁模力和注塑保压压力,能源消耗成本降低. – 由于零件的集成化,从而降低了装配成本.
• 降低投资成本
– 由于注射压力较低,因此可以降低注塑机的锁模压力,可使用吨位较小的注塑 机.
整个气辅设备的控制中心 4、气辅配件:主要有气针、气管及各种接头等,用于气辅设备与模具的连
接
因各种设备加在一起,占用的空间较大,现有很大一部分已采用一体化的气 辅系统。
END
同传统注射成型工艺相比.应用气体辅助注塑技术,有以下优点:
• 自由设计
– 综合功能较为复杂的塑胶零件可以整装为单一的组件. – 可以在同一零件上结合厚壁和薄壁部分. – 使用空心的"加强筋"部分可以提高其强度.
• 提高零件质量
– 由于减小了微收缩,因此扭曲和变形就减少了. – 消除缩痕. – 由于注射点的数量减少,所以波纹和熔接线也相应减少.
注塑成型过程中气体辅助成型技术的应用前景探讨
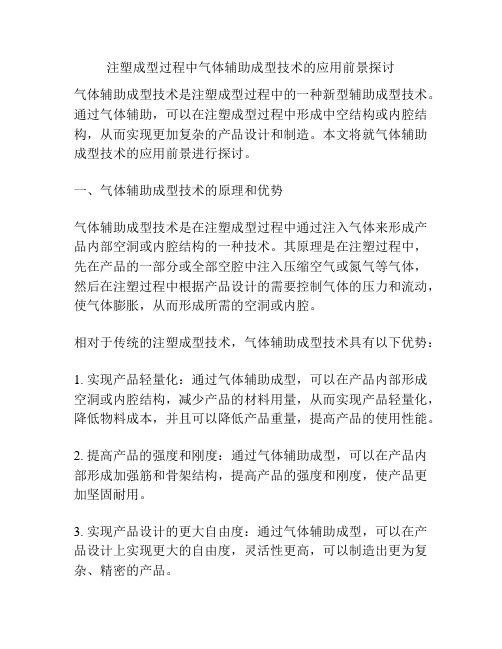
注塑成型过程中气体辅助成型技术的应用前景探讨气体辅助成型技术是注塑成型过程中的一种新型辅助成型技术。
通过气体辅助,可以在注塑成型过程中形成中空结构或内腔结构,从而实现更加复杂的产品设计和制造。
本文将就气体辅助成型技术的应用前景进行探讨。
一、气体辅助成型技术的原理和优势气体辅助成型技术是在注塑成型过程中通过注入气体来形成产品内部空洞或内腔结构的一种技术。
其原理是在注塑过程中,先在产品的一部分或全部空腔中注入压缩空气或氮气等气体,然后在注塑过程中根据产品设计的需要控制气体的压力和流动,使气体膨胀,从而形成所需的空洞或内腔。
相对于传统的注塑成型技术,气体辅助成型技术具有以下优势:1. 实现产品轻量化:通过气体辅助成型,可以在产品内部形成空洞或内腔结构,减少产品的材料用量,从而实现产品轻量化,降低物料成本,并且可以降低产品重量,提高产品的使用性能。
2. 提高产品的强度和刚度:通过气体辅助成型,可以在产品内部形成加强筋和骨架结构,提高产品的强度和刚度,使产品更加坚固耐用。
3. 实现产品设计的更大自由度:通过气体辅助成型,可以在产品设计上实现更大的自由度,灵活性更高,可以制造出更为复杂、精密的产品。
4. 提高生产效率:由于气体辅助成型可以一次性实现多个镶嵌件的成型,因此可以提高生产效率,降低生产成本。
5. 减少废品率:气体辅助成型能够减少由于变形、翘曲等问题导致的废品率,提高产品的成形质量。
二、气体辅助成型技术的应用前景随着工业自动化水平的提高和人们对产品质量和性能要求的提高,气体辅助成型技术在注塑成型中的应用前景越来越广阔。
以下是其应用前景的具体探讨:1. 制造电子产品组件在电子产品制造过程中,一些组件需要在内部形成空洞或内腔结构,以容纳电路板和电子元器件。
传统注塑成型很难实现这种内部空洞的制造,而气体辅助成型技术能够轻松地实现这种需求。
因此,气体辅助成型技术在制造电子产品组件方面有着广阔的应用前景。
2. 制造汽车零部件汽车行业是注塑成型的重要应用领域之一,而气体辅助成型技术正好满足了汽车零部件制造上的一些需求。
气辅注塑成型技术

气辅注塑成型技术气辅注塑工艺是国外八十年代研究成功,九十年代才得到实际应用的一项实用型注塑新工艺,其原理是利用高压隋性气体注射到熔融的塑料中形成真空截面并推动熔料前进,实现注射、保压、冷却等过程,使产品形成真空。
气辅设备包括气辅控制单元和氮气发生装置;氮气发生装置主要包括氮气发生器,氮气压缩机,氮气储气瓶。
它是独立于注塑机外的另一套系统,其与注塑机的唯一接口是注射信号连接线。
注塑机将一个注射信号注射开始或螺杆位置传递给气辅控制单元之后,便开始一个注气过程,等下一个注射过程开始时给出另一个注射信号,开始另一个循环,如此反复进行。
气体辅助注塑过程可分为注塑期,充气期,气体保压期和脱模期。
1.注塑期:所需塑料注塑量要通过实验找出来,以保证在充气期间,气体不会把成品表面冲破及能有一个理想的充气体积,通常注满产品的70%-95%。
注入熔体2.充气期:可以在注射中或后的不同时间注入气体,气体注入的压力必需大于注塑压力,以达到产品成中空状态。
注入氮气3.气保压期:当成品内部被气体填充后,气体在成品中空部分的压力就成为保压压力,可大大减低成品的缩水及变形率。
保压成型4.脱模期:随冷却周期完成,防止产品暴裂,自动排出气体,模具内压力降至大气压力,成品由模腔内顶出。
排出气体和产品出模气体辅助注塑成型进气方式有两种:一种由射嘴进入成品;二种由模具进入成品,这两种各有各的优点和缺点。
一从射嘴进气优点:1)修改现在有旧模具即可使用。
2)流道形成中空状,减少塑料使用。
3)成品无气针所留下之气口痕迹。
缺点:1)所有气体通道必须相通连接。
2)气体通道必须对称且平衡。
3)不能用于热流道模具上使用。
4)注塑机射嘴更换且费用较高。
二从模具进气优点:1)可以多处进气,气体通道不需完全相通连接。
2)气体与塑料可同时射入。
3)可允许使用热流道模具。
4)可使用于非对称模穴之产品成型。
缺点:1)模具须重新开发设计。
2)气针会留下气口痕迹。
塑料制品成型应用气体辅助成型技术,有以下优点:1)节省塑胶原料,节省可高达50%。
注塑成型中的气体辅助技术应用
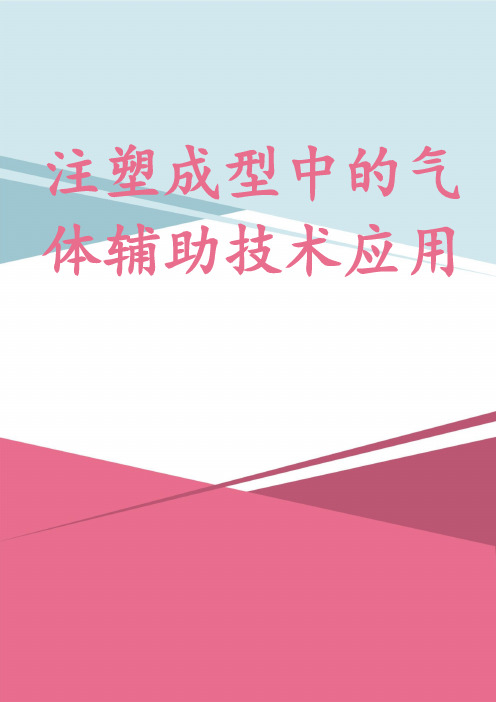
注塑成型中的气体辅助技术应用注塑成型中的气体辅助技术应用注塑成型是一种常用的塑料加工方法,通过将熔化的塑料注入模具中,经过冷却固化后得到所需的塑料制品。
然而,在注塑成型过程中,常常会出现一些问题,如缺陷、翘曲等。
为了解决这些问题,气体辅助技术在注塑成型中得到了广泛的应用。
气体辅助技术是指在注塑成型过程中,通过向模具中注入气体,利用气体的性质对塑料进行辅助成型的一种方法。
在注塑成型过程中,通过在模具中注入气体,可以改善产品表面质量,减少翘曲和缩水等缺陷,提高产品的整体性能。
首先,气体辅助技术可以改善产品的表面质量。
在注塑成型中,由于塑料的热胀冷缩和浇注冷却的不均匀性,常常会出现产品表面的缺陷,如气泡、痕迹等。
通过在模具中注入气体,可以使塑料在充填过程中更加均匀,减少气泡的产生,从而改善产品的表面质量,使其更加光滑。
其次,气体辅助技术可以减少产品的翘曲和缩水。
在注塑成型中,由于塑料的收缩性质,产品往往会出现翘曲和缩水等问题。
通过在模具中注入气体,可以产生一定的气压,使塑料在冷却固化过程中更加均匀,减少翘曲和缩水的可能性,从而提高产品的几何稳定性和尺寸精度。
最后,气体辅助技术可以改善产品的整体性能。
在注塑成型中,由于塑料的结晶性质,产品往往会出现内部应力集中的问题,从而影响产品的强度和韧性。
通过在模具中注入气体,可以使塑料在充填过程中形成空腔结构,减少内部应力的集中,提高产品的整体性能,使其更加坚固耐用。
综上所述,气体辅助技术在注塑成型中的应用可以改善产品的表面质量,减少翘曲和缩水,提高产品的整体性能。
随着技术的不断发展,气体辅助技术在注塑成型中的应用前景更加广阔,将为塑料制品的生产提供更多的可能性。
气辅技术简介
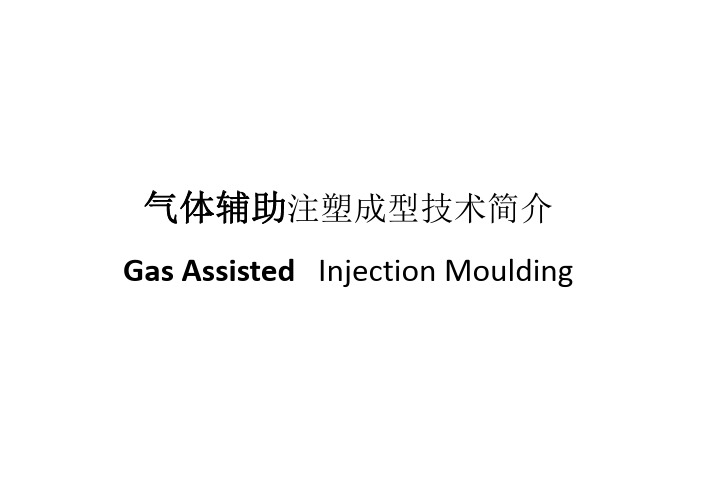
A 高压氮气源设备包含氮气机或氮气发生器,隔膜式压缩机。
气辅设备系统方案
B、高压氮气管网说明: 根据标准的注塑成型车间设计,推荐用户选用标准耐高压管网来输送高压氮气,同时将具 备生产条件的注塑机周边都安装高压氮气出口,从而保证有多台注塑机具备气辅工艺使用条 件;
• 缩短成型时间,提高生产效率,减轻制品重量; • 延长模具使用寿命,降低模具制造成本; • 降低锁模力,射胶力合注塑机耗电量;
气辅设备系统方案
气辅设备简要说明:
由于气辅注塑的技术特点,高压气体必须在塑料成型过程中注入产品内 部,因此必须使用惰性气体才能避免塑料发生氧化反应,而氮气是工业领 域中最经济安全的惰性气体。
气辅压力控制器
B
注塑成 型机
氮气机
A
压缩机
气辅机 C
谢 谢! Thanks!
气辅成型技术
• 气体辅助注塑成型是一种新型的塑料加工技术, 该技术充分利用了气体能均匀,有效地传递压力的 特点,使气辅GIT技术具有一系列传统注塑成型无 法比拟的优越性。
气辅工艺原理
气体辅助注塑技术优势
• 消除产品表面缩痕和表面凝斑,改善产品表面质量,使制 品表面光滑、饱满、美观;
• 降低产品出模后残余内应力,减轻翘曲变形,提高新产品 强度;
气体辅助注塑成型技术简介
Gas Assisted Injection Moulding
• 气辅成型技术
气辅成型是通过在气辅模具型腔中预先通入由氮气流峰的流动状态,从而使熔体对模具表面有更好的复制效果; 同时气辅GIT技术也可以通过在熔体内部建立保压通道,解决厚 壁胶位外观容易出现缩痕的问题。
气辅成型技术

气辅成型技术在注塑业中又称气体辅助住宿和中空成型,在近10年来发展起来的革新成型技术,也可说是注塑技术的第二次革命。
目前该技术主要用于汽车、大型家电等大件注塑行业。
其主要原理是:先注入一定量的熔融塑胶(通常为90%-98%,以产品的总胶量而言)可通过分析计算+经验。
然后再在熔融塑胶内注入高压氮气,高压氮气在熔融的塑胶内沿预设的路径形成气道(最好是和流向一致当然有特殊具体情况你决定)。
使不到100%的熔融塑胶充满整个模腔,此后进入保压阶段,同时冷却,最后排气、脱模。
高压氮气进入塑料后自然会穿越粘度低(温度高)和低压的部位,并中在冷却过程中利用气体高压来保压而紧贴模具壁成型。
此项技术除需传统注塑设备外,还需所体辅助注塑控制系统(新科益有MDI控制器)。
与传统的注塑成型相比,气体辅助注塑成型有下列优点:1.减少内部的残留应力,从而减弱甚至完全消除翘曲变形状况,同时增加其机械强度和刚性。
2.成品壁厚部分的中央是中空的,可以减少原料,特别是短射和中空型的模具,塑料最多可以节约达30%。
3.减少或消除加强筋造成的表现收缩凹陷现象。
4.降低制品的收缩不均,提高制品的精密度。
5.设备耗减,大量减少锁模力,可以用小吨位的注塑机替代大吨位的注塑机。
6.利用气道来形成加强结构,提高成品的强度。
7.减少射入点。
8.缩短成期。
9.厚薄比大的制品也能通过气辅一次成型。
10。
改变传统成品设计观念,能使用一体化设计来减少附属的零组件。
缺点:1.由于所体具有压缩特征因而不容易作精确控制,加上对周围操作环境敏感,因此工艺的重复性与稳定性比传统工艺差。
2.国内技术和经验问题导致资源较浪费(废品率高)。
目前用于的产品有:汽车门把手、座椅、保险杠、门板、电视机外客、空调、冰箱、马桶........你说呢曾做过:汽车门把手、门板、雪上摩托前罩三类7款。
气体辅助注塑成型的预注塑部分与普通注塑成型一样,主要增加了一个氮气注射和回收系统。
根据注气压力产生方式的不同,目前,常用的气体注射装置有以下两种:(1)不连续压力产生法即体积控制法,如Cinpres公司的设备,它首先往汽缸中注入一定体积的气体(通常是氮气),然后采用液压装置压缩,使气体压力达到设定值时才进行注射充填。
气体辅助注塑成型技术研究

气体辅助注塑成型技术研究气体辅助注塑成型技术通过在熔体注塑过程中引入高压气体,获得高表面质量、高尺寸精度的塑料制件,从而克服了常规注射成型工艺难以一次成型壁厚差异大、结构复杂的注塑件的局限性,目前已经在国内外家电、汽车等众多行业获得推广应用。
本文介绍了气体辅助注射成型技术原理、特点、优势、适用范围及发展前景,分析了气辅成型制品的典型气道截面形状以及常见的工艺缺陷问题,并以保险杠、把手等汽车零部件为例阐述了气体辅助注塑成型工艺在汽车行业应用的技术优势。
标签:气辅注塑成型;汽车注塑件;设计原则;工艺1 气体辅助注塑成型技术概述1.1 气体辅助注塑成型的技术原理与技术特点气体辅助注塑成型技术是20世纪90年代初兴起于欧洲的一种创新性的塑料成型技术。
该技术的主要成型原理为:在塑料熔体填充成型模具的过程中,利用可控制的高压气体(通常为氮气)注入到塑料熔体内部,从而推动塑料熔体充填全部模具型腔,并通过高压气体在熔体内部形成的中空气道对塑料熔体施加保压压力,从而可以实现一次性生产壁厚差异大、结构复杂的注塑制件。
由于气体注入的位置及压力可以灵活设置,大大提高了汽车、家电、日用品等众多行业注塑制件的设计自由度,被称为注塑成型行业继螺杆注塑机以来的又一项革命性技术[1]。
气体辅助注塑成型技术的优势:(1)节省材料10%~50%;(2)锁模力降低30%~70%;(3)提高生产效率20%~40%;(4)消除制品的缩痕、翘曲等缺陷。
1.2 气体辅助注塑成型技术的应用范围由于高压气体注入注塑制件内部后形成中空气道,因此气辅注塑成型技术对于杆类或棒状制件具有显著的节省原材料效果,例如冰箱/电器把手件、座椅扶手等厚壁实心类注塑制件。
采用气体辅助注塑成型技术,不仅可以节省原材料高达20%-40%,而且由于高压气体由内向外的保压作用,还可以取得优异的表面质量。
此外,气体辅助注塑成型技术还可以有效地提升大型平板类制件的成型尺寸精度,抑制或消除平板类制件常见的翘曲变形缺陷,例如車门板、冰箱托盘、汽车内外饰件等平板类制件采用气体辅助注塑成型工艺,可以通过合理设计和利用制件的加强筋结构,在加强筋根部开设气体通道,从而有效减小或消除平板件因截面壁厚差异产生的内应力,达到降低或消除翘曲变形的目的。
气体辅助注塑成型技术简介.
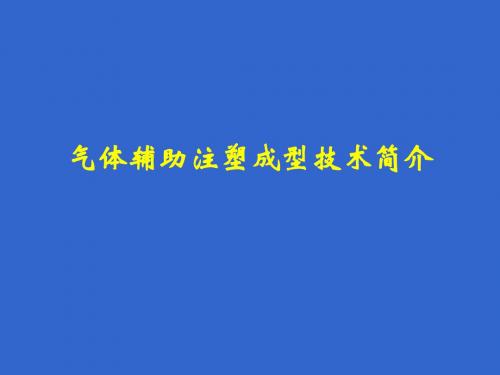
四、气体辅助注塑整系统的原理图:
A、整套系统
氮气 发生 器
低压 贮气缸
电动 高压 增压机
高压 贮气缸
气辅 主控 制器
单相电源 压缩空气 三相电源
模具的工作寿命; 7、降低注塑机的锁模压力,可高达50%; 8、提高注塑机的工作寿命和降低耗电量。
三、气体辅助注塑技术的应用:
基本上所有用于注塑的热塑性塑料及一般的工程材料 (如PS、HIPS、PP、ABS…)都适用于气辅技术。
目前气辅技术广泛应用于各类塑胶产品上,例如:电视 机、电冰箱、空调或音响外壳、汽车塑料产品、家电、日用 品、玩具等。
B、简易系统
氮气 缸瓶
气动 高压 增压机
压缩空气
单相电源
高压 贮气缸
气辅 主控 制器
单相电源
模具 模具
五、气体辅助注塑周期简介:
1、注塑期——以定量塑化塑料充填入模腔内。所需塑料 份量要通过试验找出来,以保证在充氮期间,气体不 会把成品表面冲破及能有一理想的充氮体积。
2、充气期——注塑期中或后,不同时间注入气体,气体 注入的压力必需大于注塑压力,以达至产品成中空状 态。
气体辅助注塑成型技术简介
一、气体辅助注塑原理:
气体辅助注塑原理是把高压氮气经气辅 主控制器(分段压力控制系统)直接注射入 模腔内塑化塑料里,使塑件内部膨胀而造成 真空,但仍然保持产品表面的外形完整无缺, 减小产品表面的收缩、产品变形和翘曲,从 而达到提高产品的质量,降低成本的目的。
二、采用气体辅助注塑技术的优点:
气体_助注塑成型技__介
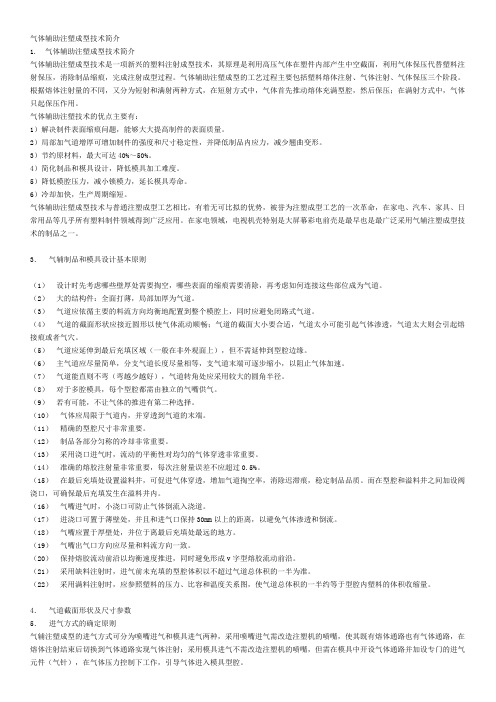
气体辅助注塑成型技术简介1. 气体辅助注塑成型技术简介气体辅助注塑成型技术是一项新兴的塑料注射成型技术,其原理是利用高压气体在塑件内部产生中空截面,利用气体保压代替塑料注射保压,消除制品缩痕,完成注射成型过程。
气体辅助注塑成型的工艺过程主要包括塑料熔体注射、气体注射、气体保压三个阶段。
根据熔体注射量的不同,又分为短射和满射两种方式,在短射方式中,气体首先推动熔体充满型腔,然后保压;在满射方式中,气体只起保压作用。
气体辅助注塑技术的优点主要有:1)解决制件表面缩痕问题,能够大大提高制件的表面质量。
2)局部加气道增厚可增加制件的强度和尺寸稳定性,并降低制品内应力,减少翘曲变形。
3)节约原材料,最大可达40%~50%。
4)简化制品和模具设计,降低模具加工难度。
5)降低模腔压力,减小锁模力,延长模具寿命。
6)冷却加快,生产周期缩短。
气体辅助注塑成型技术与普通注塑成型工艺相比,有着无可比拟的优势,被誉为注塑成型工艺的一次革命,在家电、汽车、家具、日常用品等几乎所有塑料制件领域得到广泛应用。
在家电领域,电视机壳特别是大屏幕彩电前壳是最早也是最广泛采用气辅注塑成型技术的制品之一。
3.气辅制品和模具设计基本原则(1)设计时先考虑哪些壁厚处需要掏空,哪些表面的缩痕需要消除,再考虑如何连接这些部位成为气道。
(2)大的结构件:全面打薄,局部加厚为气道。
(3)气道应依循主要的料流方向均衡地配置到整个模腔上,同时应避免闭路式气道。
(4)气道的截面形状应接近圆形以使气体流动顺畅;气道的截面大小要合适,气道太小可能引起气体渗透,气道太大则会引起熔接痕或者气穴。
(5)气道应延伸到最后充填区域(一般在非外观面上),但不需延伸到型腔边缘。
(6)主气道应尽量简单,分支气道长度尽量相等,支气道末端可逐步缩小,以阻止气体加速。
(7)气道能直则不弯(弯越少越好),气道转角处应采用较大的圆角半径。
(8)对于多腔模具,每个型腔都需由独立的气嘴供气。
气体辅助注塑成型技术研究

气体辅助注塑成型技术研究气体辅助注塑成型技术是近年来发展起来的一项新型注塑成型技术。
与传统注塑成型技术相比,其最大的优点是可以在注塑过程中控制气体压力,从而在塑料制件中形成中空区域或类似泡沫的结构,改善制件的物理性能和外观质量。
气体辅助注塑成型技术的基本原理是在注塑射出过程中,通过向塑料中注入惰性气体(如氮气、空气)来改变塑料的结构和性质。
在注塑成型过程中,首先将塑料材料加热至熔融状态,然后将熔融塑料通过射出装置注入模具中形成塑料制件。
在这个过程中,通过向塑料中注入气体来影响塑料的形态和性质,从而得到具有更好物理性能和外观质量的塑料制件。
具体来说,气体辅助注塑成型技术主要分为两种形式:一种是在注塑成型过程中向塑料中注入惰性气体,如氮气、空气等,以形成中空区域或类似泡沫的结构;另一种是在注塑成型过程中通过向模腔中加压气体来控制塑料的形态和性质。
气体辅助注塑成型技术的应用范围非常广泛,其中最典型的应用就是制造汽车零部件。
比如,汽车中的仪表盘、门板、车顶、挡风玻璃支架等都可以通过气体辅助注塑成型技术来制造。
此外,气体辅助注塑成型技术还可以应用于家具、电子产品、医疗器械等领域。
气体辅助注塑成型技术相对于传统注塑成型技术的优点主要有以下几个方面:首先,可以大大降低制造成本。
在传统注塑成型过程中,由于塑料结构设计的限制,往往需要采用更大的注塑机和更多的材料,从而带来更高的制造成本。
而在气体辅助注塑成型技术中,通过控制气体压力,可以有效减小制品的体积和重量,降低成本。
其次,可以提高制品的质量。
在气体辅助注塑成型过程中,通过向塑料中注入惰性气体可以形成中空区域或类似泡沫的结构,从而使得制品具有更好的物理性能和外观质量。
比如,汽车零部件可以通过气体辅助注塑成型技术来制造,可以使得这些零部件更轻、更坚固,有效提高车辆整体性能。
最后,气体辅助注塑成型技术还可以提高生产效率。
由于气体辅助注塑成型技术可以使得制品更容易脱模,同时生产过程也更加稳定,从而大大提高生产效率和制品质量。
塑料注塑气辅成型原理

塑料注塑气辅成型原理塑料注塑气辅成型是一种常见的塑料成型方法,它结合了注塑成型和气辅成型两种工艺,使得产品的成型效果更加精确和高效。
本文将从原理、工艺流程、优点和应用等方面介绍塑料注塑气辅成型。
一、原理塑料注塑气辅成型是指在注塑成型的过程中,通过加入气体辅助来实现产品的成型。
其原理是在注塑成型时,通过注射机将熔化的塑料注入模具中,然后在注塑过程中加入一定的气体,使得塑料在模具中充分膨胀,从而得到所需的产品形状。
注塑气辅成型可以有效地解决一些注塑过程中容易产生缺陷的问题,如翘曲、收缩等。
二、工艺流程塑料注塑气辅成型的工艺流程主要包括以下几个步骤:1. 原料准备:选用适合注塑成型的塑料原料,并进行预处理,如干燥、混合等。
2. 模具设计:根据产品的需求设计模具,并制作成型模具。
3. 注塑成型:将预处理好的塑料原料放入注塑机的料斗中,经过加热、熔化后,通过注射机将熔化的塑料注入模具中。
4. 气辅成型:在注塑过程中,通过气体辅助装置向模具中注入一定的气体,使得塑料在模具中膨胀成型。
5. 冷却固化:待塑料在模具中冷却固化后,将成型产品从模具中取出。
6. 后处理:对成型产品进行修整、去除余料、清洁等处理。
三、优点塑料注塑气辅成型相比传统的注塑成型有以下几个优点:1. 产品质量好:通过气辅成型可以减少或避免一些常见的缺陷,如翘曲、收缩等,提高产品的质量。
2. 成型效率高:气辅成型可以在注塑过程中快速膨胀,提高成型效率,缩短生产周期。
3. 成本低:相比其他成型工艺,注塑气辅成型的设备和工艺要求相对简单,成本较低。
4. 适用范围广:注塑气辅成型适用于各种塑料材料,适用于各种形状的产品,具有很大的灵活性。
四、应用塑料注塑气辅成型在各个领域都有广泛的应用,特别是对于一些形状复杂、尺寸精确的产品,更加适用。
以下是一些常见的应用领域:1. 汽车零部件:如汽车灯罩、仪表盘等。
2. 家电产品:如电视外壳、空调面板等。
3. 医疗器械:如注射器、输液器等。
- 1、下载文档前请自行甄别文档内容的完整性,平台不提供额外的编辑、内容补充、找答案等附加服务。
- 2、"仅部分预览"的文档,不可在线预览部分如存在完整性等问题,可反馈申请退款(可完整预览的文档不适用该条件!)。
- 3、如文档侵犯您的权益,请联系客服反馈,我们会尽快为您处理(人工客服工作时间:9:00-18:30)。
气体辅助注塑成型技术简介
气体辅助注塑成型技术简介类型:气体辅助注塑成型是欧美近期发展出来的一种先进的注塑工艺,它的工作流程是首先向模腔内进行树脂的欠料注射,然后利用精确的自动化控制系统,把经过高压压缩的氮气导入熔融物料当中,使塑件内部膨胀而造成中空,气体沿着阻力{TodayHot}最小方向流向制品的低压和高温区域。
当气体在制品中流动时,它通过置换熔融物料而掏空厚壁截面,这些置换出来的物料充填制品的其余部分。
当填充过程完成以后,由气体继续提供保压压力,解决物料冷却过程中体积收缩的问题。
气体辅助注塑成型优点为什么人们对于气体辅助注射成型的兴趣如此之大呢?其主要的原因在于这种方法出现时所许诺的种种优点。
成型者希望以低制造成本生产高质量的产品。
在不降低质量的前提下用现代注塑机和成型技术可以缩短生产周期。
通过使用气体辅助注射成型的方法,制品质量得到提高,而且降低了模具的成本。
使用气体辅助注射成型技术时,它的优点和费用的节约是非常显着的。
1、减少产品变形:低的注射压力使内应力降低,使翘曲变形降到最低;
2、减少锁模压力:低的注射压力使合模力降
低,可以使用小吨位机台;
3、提高产品精度:低的残余应力同样提高了尺寸公差和产品的稳定性;
4、减少塑胶原料:成品的肉厚部分是中空的,减少塑料最多可达40%;
5、缩短成型周期:与实心制品相比成型周期缩短,不到发泡成型一半;
6、提高设计自由:气体辅助注射成型使结构完整性和设计自由度提高;
7、厚薄一次成型:对一些壁厚差异大的制品通过气辅技术可一次成型;
8、提高模具寿命:降低模腔内压力,使模具损耗减少,提高工作寿命;
9、降低模具成本:减少射入点,气道取代热流道从而使模具成本降低;
10、消除凹陷缩水:沿筋板和根部气道增加了刚度,不必考虑缩痕问题。
第一阶段:按照一般的注塑成型工艺把一定量的熔融塑胶注射入模穴;
第二阶段:在熔融塑胶尚未充满模腔之前,将高压氮气射入模穴的中央;
第三阶段:高压气体推动制品中央尚未冷却的熔融塑胶,一直到模穴末端,最后{HotTag}填满模腔;
第四阶段:塑胶件的中空部分继续保持高压,压力迫使塑料向外紧贴模具,直到冷却下来;
第五阶段:塑料制品冷却定型后,排除制品内部的高压气体,然后开模取出制品。
气体辅助注塑成型系统由四个部分组成
A.氮气来源部分B.氮气增压部分C.氮气控制部
分D.氮气注入部分
↓↓
↓↓
① 氮气产生机① 气驱式增压机①简易式控制台① 模具气针进气
② 购瓶装氮气② 电动式增压机② 箱柜式控制台② 氮气射咀进气气体辅助注射成型配置
⑴气驱式增压机 + 气辅控制台
这种配置比较经济,(如一台120NL/Min气动增压机配上一台手提式控制台)使用这种配置,操作方便,接上外购的瓶装氮气即可增压并控制气体的输出。
但其输出的高压氮气流量较小,较难满足耗氮气量大且注塑周期很短的产品生产。
⑵电动高压压缩机 + 气辅控制台
这种配置也可用外购的瓶装氮气为气源(如瓶装氮气经电动高压压缩机,再配上手提式控制台),通常电动高压压缩机可提供较
大的高压氮气流量,可以同时供给几个控制台输出气量,控制多副模具生产。
但要经常更换氮气瓶。
⑶氮气产生机 + 电动高压压缩机 + 气辅控制台
这是一种整套制氮机经高压压缩机增压后配上气辅控制器的配置。
这是较理想的配置,有高压氮气发生器为控制器的氮气来源,不需另外购买瓶装氮气,而且一部高压氮气发生器可作为多台气辅控制台的氮气来源,可同时控制多副模具生产。
但这种配置的投资成本较高。
气辅注塑成型使用的气体
气体辅助注塑成型使用的主要是氮气。
氮气作为空气中含量最丰富的气体,取之不竭,用之不尽。
它无色、无味,透明,属于亚惰性气体,不维持生命。
不会发生化学反应,氮气的另一个优点是无毒、难燃、成本低。
高纯氮气常作为保护性气体,用于隔绝氧气或空气的场所。
氮气(N2)在空气中的含量为78.084%(空气中各种气体的容积组分为N2: 78.084%、O2:20.9476%、氩气: 0.9364%、CO2:0.0314%、其它还有H2、CH4、N2O、O3、SO2、NO2等,但含量极少),分子量为28,沸点:-195.8℃,冷凝点:-210℃。
压缩空气由于不洁净(主要是氧气),在高温、高压情况下发生化学反应而导致材料降解或腐蚀,所以不适用。
采用气辅注塑成型的状况当零件设计中出现下列一个或几个情
况时,应考虑采用气体辅助注塑成型工艺:
1、零件很大;
2、外观很重要;
3、零件有很多内部结构,可能引起塌陷;
4、零件必须很平,而且需要较小残余应力;
5、零件很复杂,而且结构需要;
6、产品数量可以补偿制模方面的投资;
7、美观需要,厚壁不可避免;
8、二次加工量要求最小;
以下列出了部分采用气体辅助注射成型产品的名称
—器具手柄—加油器管路—吸尘器储灰箱—垃圾箱
—机动车—乘客辅助手柄—高尔夫球棒杆—坐便器座—ATM盖子—轮椅车轮—传真机机座—卡车保险杠端帽
—加速器踏板臂—移动式档案架—厨房用具手柄—卡车外装饰物
—气体过滤器机架—篮球篮板—草地和花园设备—卡车滤油器外罩
—制动器踏板臂—瓶箱—原料搬运用设备—卡车空气过滤器外罩
—缓冲器仪表盘—光驱托盘—电视机外壳—医疗分析仪器外壳
—车门把手—椅子座—医院病床护栏—电脑外壳
—车门模板—椅子扶手—LCD显示器支架—复印机纸张输入辊
—电子布线系统—婴儿车座提手—功率放大器机架—鼠标外壳
—外装饰物—复印机面板—打印机提手—实用的货棚板
—文具柜面板—饮水机外罩板—打印机硒鼓—洗衣机搅拌器—挡泥板外延—计算机仪表盖—打印机控制面板—自动贩卖机外壳
—仪器面板组—键盘包覆物—淋浴器基座—凉水机仪表盘—内装饰物—电吉他外壳—淋浴器喷头—服务器机箱面板—汽车保险杠—洗碗机仪表板—遮阳板框架—窗框
—汽车车牌座—电工工具手柄—通用手推车—电视柜
—汽车侧镜安装座—油漆刷手柄—音箱外壳—电冰箱门把手气辅注塑成型基本守则
1、在气体射入点,气体的压力大于塑胶压力时,气体才会射入塑料中。
2、气体射入后,必须防止由射入点溢出,可用密封的(SEALING)壁免。
3、气体进入塑胶后,会延着最小阻力的方向前进。
如:较厚的截面。
4、在塑胶内的气体会由高压区流向低压区。
5、塑胶在冷却及成形时,其压力是由气体控制,而非注塑机。
6、在一个连续的气道内,气体的压力在入口及末端是一样的。
(等压)
7、塑胶内的气体必须有开模前被排放到大气中或经回收循环使用。
8、塑胶冷却时体积收缩的现象,可由气体的膨胀来补偿。
9、在成形过程中,气体控制传送系统和注塑机必须尽可能的配合。
10、避免注塑机螺杆移动到最末端,防止塑胶回流到螺杆前端的空隙中。
11、若没有单向射咀,则尽可能将料管储料的时间延后,以避免气体回流。