现场6S管理制度
生产现场6S管理规定(5篇)

生产现场6S管理规定1.0目的:为了提升产品品质,降低不良品的发生,减少浪费,降低成本,工厂环境清洁有序,得到客户认可,特制定本管理规定。
2.0适用范围:本规定适用于生产现场管理,凡生产现场物品物料及环境卫生等按照本规定要求执行3.0管理职责:3.0.1生产部负责本规定的制定,修改,并监督实施;3.0.2车间各班组负责按照规定内容做好各自的现场6S管理工作;3.0.3总经理负责本规定的发布之批准工作。
4.0工作程序推行现场6S,内容包括:整理、整顿、清扫、清洁、素养、安全4.1整理:将作业现场有用的东西和没有用的东西进行区分,把没有用的东西清理作业现场,使之保持干净整齐。
4.2要求:4.2.1车间各班组下班后将搬运工具有序地按指定区域放置,合格品、不合格品、半成品、待检品、待加工品及工装夹具、工艺卡片有序地放置。
4.2.2工作台及设备电控箱上无破布、手套、废品工件。
4.2.3所有不动物品每周六进行彻底清扫,除去表面灰尘,及时将废品垃圾送到指定地点。
4.3整顿:把有用的东西按照规定位置进行合理的摆放整齐,明确地标识,以便于拿取方便。
4.4要求:____周转架、箱、车内工件摆放有序,车间周转架摆放高度应低于3层,做到周转架、箱、车摆放整齐有序,左右成行,原则为平行。
生产线附近只能放置真正需要的物品,不超过所规定的范围。
4.4.2各班组及维修班将维修工具集中放置。
车间工具箱内工具(如螺丝刀、钳子、油枪及上油工具、量具等)摆放整齐有序。
4.4.3车间各工序的工件严格按区域划分,进行存放(因场地窄应及时通知有关领导作临时处理)。
4.4.4车间半成品零部件等按《半成品、零部件管理规定》执行4.4.5车间所有清扫工具放在各班组指定位置。
4.4.6工件搬运时应轻拿轻放,任何操作者不允许以工件作支撑点操作,以防止磕碰疤现象的发生。
4.5清扫:清除现场内的脏污,并防止污染的发生。
4.6要求:每周六对全厂所有设备、车间地面、卫生间进行卫生检查,标准为无死角垃圾,设备无明显油污。
6s管理制度范文范本6S管理细则(五篇)
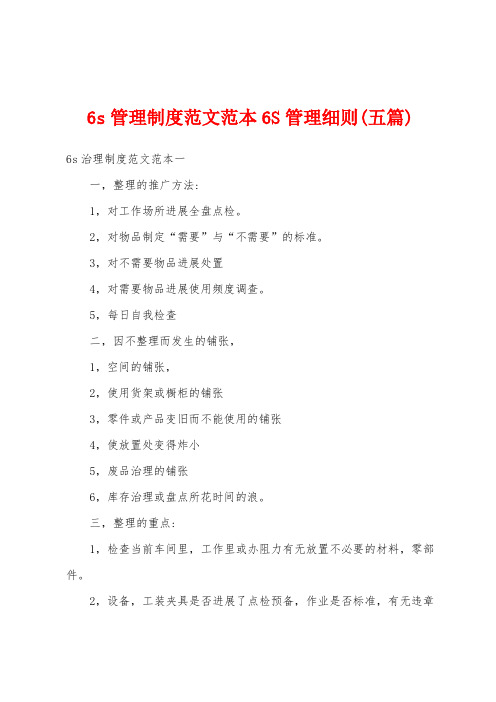
6s管理制度范文范本6S管理细则(五篇) 6s治理制度范文范本一一,整理的推广方法:1,对工作场所进展全盘点检。
2,对物品制定“需要”与“不需要”的标准。
3,对不需要物品进展处置4,对需要物品进展使用频度调查。
5,每日自我检查二,因不整理而发生的铺张,1,空间的铺张,2,使用货架或橱柜的铺张3,零件或产品变旧而不能使用的铺张4,使放置处变得炸小5,废品治理的铺张6,库存治理或盘点所花时间的浪。
三,整理的重点:1,检查当前车间里,工作里或办阻力有无放置不必要的材料,零部件。
2,设备,工装夹具是否进展了点检预备,作业是否标准,有无违章作业。
3,操作规程是否张贴在规定的位置,各种警示牌是否齐全。
整顿:将需要品根据规定的定位、定量等方式进展摆放整齐,并对其做标识,使查找需要品的时间削减为零。
整顿的目的:腾出空间,发挥更大的价值,太高效率,创立清爽,政界的环境,提升企业形象。
一,整顿的推广方法:1、落实整理工作。
2、对需要的物品明确其放置场所。
3、储存场所要实行地面画线定位。
4、对场所、物品进展标记、标识。
5、制订废弃物处理方法。
二,整顿的重点:1、现场必要的物品、元器位和工装夹是否散乱存放。
2、存放的物品、元器件和存放地点有无标识。
3、当你需要取用物品时,是否能快速地拿到,并且不会拿错。
半成品、存放柜、托盘、手推车等存放是否整齐、有序。
清扫:将办公场所和现场的工作环境清扫洁净,使其保持在无垃圾、无灰尘、无脏污、洁净干净的状态,并防止污染的发生。
清扫的目的:消退脏污,保持现场洁净、光明,提高设备的性能,提高作业质量,提高产品质量削减安全隐患。
清扫活动的重点:就是必需根据如下步骤实施方能真正起到效果。
清洁:将整理、整顿、清扫的实施做法进展究竟,且维持其正果,并对其事实做法予以标准化、制度化。
清洁的目的:维持前面“3s”的成果。
清洁的推车方法:1、落实前“3s”工作。
2、设法养成干净的习惯。
3、制订目视治理的标准。
施工现场6s管理制度
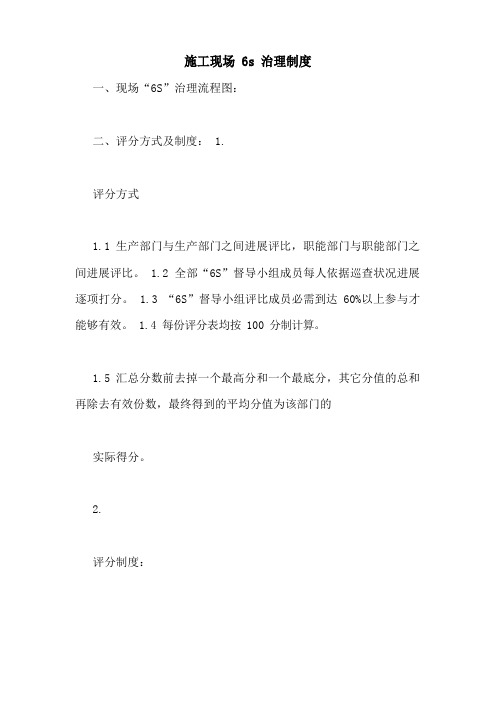
施工现场 6s 治理制度一、现场“6S”治理流程图:二、评分方式及制度: 1.评分方式1.1 生产部门与生产部门之间进展评比,职能部门与职能部门之间进展评比。
1.2 全部“6S”督导小组成员每人依据巡查状况进展逐项打分。
1.3 “6S”督导小组评比成员必需到达 60%以上参与才能够有效。
1.4 每份评分表均按 100 分制计算。
1.5 汇总分数前去掉一个最高分和一个最底分,其它分值的总和再除去有效份数,最终得到的平均分值为该部门的实际得分。
2.评分制度:2.1 全部参与评分的人员,在每份评比表上均签上实名制。
2.2 评分后不得任凭修改。
2.3评分过程中不得交头接耳,不得询问或打听他人评分状况。
2.4其它扣分工程必需注明扣分事由及内容。
2.5汇总均由督查办汇总,全部评分原始资料均存档。
2.6巡检评分每周一次,周例会定为每周星期五下午 16:00 钟,准时到峻海会议室集中。
三、“6S”督导小组治理制度: 1.出勤制度:1.1 周例会无故缺勤扣当事人 20 元/次。
1.2 周例会迟到扣当事人5 元/次。
1.3 周例会无故提前离开的扣当事人 10 元/次。
2.日常治理制度:2.1 未按要求制作本部门整改打算,惩罚 10 元/次。
2.2 对本部门“6S”督导不力,惩罚 2 元/项。
2.3 对巡查过程中只走过程,弄虚作假,惩罚30 元/次。
2.4 消灭全安事故未准时上报,惩罚 10 元/次。
2.5 未按要求填写各类对策表,惩罚 5 元/次。
2.6 “6S”相关会议未准时传达及汇报给本部门,消灭问题均直接扣当事人。
3.嘉奖条例:3.1被公司评分第一名者,对该部门发一面“6S”先进部门流淌红旗。
如连续三次被评为第一,对该部门的“6S”督导员直接嘉奖 50 元。
3.2年终评先进部门或先进个人此项该作为评比的主要条件之一。
3.3对“6S”工作做出突出奉献的嘉奖 100—200 元。
3.4被公司连续三次评为最终一名者,对该部门惩罚 50 元。
6S管理制度完整版

6S管理制度一、目的为了规范公司的生产现场管理,提高生产效率和质量,降低生产成本,特制定本制度。
二、适用范围本制度适用于公司所有生产现场的管理。
三、职责1. 生产部负责6S管理的实施和监督。
2. 各部门负责本部门6S管理的执行和实施。
四、管理要求1. 整理(Seiri)1.1 生产现场要保持整洁,无杂物堆积。
1.2 生产设备、工具、物料等要摆放整齐,标识清晰。
1.3 生产现场要定期进行清理,保持清洁。
2. 整顿(Seiton)2.1 生产现场的各种设备、工具、物料等要分类存放,标识明确。
2.2 生产现场要设置专门的存放区域,并标识清楚。
2.3 生产现场要定期进行整理,保持有序。
3. 清扫(Seiso)3.1 生产现场要定期进行清扫,保持清洁。
3.2 生产现场要设置专门的清扫区域,并标识清楚。
3.3 生产现场要定期进行清理,保持整洁。
4. 清洁(Seiketsu)4.1 生产现场要制定清洁标准,并严格执行。
4.2 生产现场要定期进行清洁,保持清洁。
4.3 生产现场要设置专门的清洁区域,并标识清楚。
5. 素养(Shitsuke)5.1 生产现场要制定素养标准,并严格执行。
5.2 生产现场要定期进行素养培训,提高员工的素养水平。
5.3 生产现场要设置专门的素养区域,并标识清楚。
6. 安全(Safety)6.1 生产现场要制定安全标准,并严格执行。
6.2 生产现场要定期进行安全检查,确保生产安全。
6.3 生产现场要设置专门的安全区域,并标识清楚。
五、检查与考核7.1 生产部负责对生产现场的6S管理进行检查和考核。
7.2 对未按规定执行6S管理的部门和个人,将给予相应的处罚。
六、附则8.1 本制度自发布之日起实施。
8.2 本制度由生产部负责解释和修订。
6s管理实施办法6篇

6s管理实施办法6篇6s管理实施办法 (1)一、整理:将车间现场内需要和不需要的东西分类,丢弃或处理不需要的东西,管理需要的东西。
目的:腾出空间,空间活用,防止误用、误送,塑造清爽的工作场所。
内容:1、车间内废品、边角料当天产生当天处理,入库或从现场清除。
2、班组产生的返修品及时返修,在班组内存放不得超过二天,避免与合格品混淆。
3、用户返回的产品应及时处理,如暂时无时间处理,应存放在临时库,不得堆放在生产现场。
4、外来产品包装物及时去除,货品堆放整齐。
工作现场不能堆放过多(带包装)外购产品。
5、合格部件、产品经检查人员确认后及时入库,不得在班组存放超过一天。
6、报废的工夹具、量具、机器设备撤离现场存放到指定的地点。
7、领料不得领取超过二天用量的部件材料,车间内不允许存放不需要的材料、部件。
8、工作垃圾(废包装盒、废包装箱、废塑料袋)及生活垃圾及时清理到卫生间。
9、窗台、设备、工作台、周转箱内个人生活用品(食品、餐饮具、包、化妆品、毛巾、卫生用品、书报、衣物、鞋)清离现场。
二、整顿:对整理之后留在现场的必要的物品分门别类放置,排列整齐。
物品的保管要定点、定容、定量,有效标识,以便用最快的速度取得所需之物。
目的:工作场所一目了然,消除找寻物品的时间内容:1、车间绘制现场<定置图管理图>。
2、车间对各类设备,工装,器具进行分类编号。
3、废品、废料应存放于指定废品区、废料区地点。
4、不合格品、待检品、返修品要与合格品区分开,周转箱内有清晰明显标识。
5、周转箱应放在货架上或周转车上,设备上不得放置周转箱、零件。
6、操作者所加工的零部件、半成品及成品的容器内,必须有明显的标识(交检单,转序卡),注明品名,数量,操作者,生产日期。
7、搬运周转工具(吊车、拖车、升降车、周转车)应存放于指定地点,不得占用通道。
8、工具(钳子、螺丝刀、电烙铁、通路仪)、工位器具(周转箱、周转车、零件盒)、抹布、拖布、包装盒、酒精等使用后要及时放回到原位。
6s管理制度(通用5篇)

6s管理制度(通用5篇)6s管理制度篇1第一章总则一、目的:为了营造一个干净、整洁、舒适、合理、安全的工作场所和空间环境;强化公司基础管理,提升经营形象和员工综合素质,特制定本制度。
二、适用范围:本规定适用于公司全体员工。
三、推行方法:6S推行以PDCA循环管理模式为方法。
第二章 6S 的定义、目的一、总目的强化基础管理、提升员工素质及企业形象、加强企业竞争力;营造出整洁、舒适的工作环境;使得设备保持清洁、员工文明进取、企业健康发展。
二、6S 的定义、目的1、整理1.1定义:将工作场所中任何物品区分为必要的与不必要的,必要的留下来,不必要的彻底清除,腾出空间。
1.2目的:(1)腾出空间; (2)防止误用、误送; (3)塑造清爽的工作场所;2、整顿2.1定义:必要的东西分类按规定的位置摆放整齐,加以标识,以便在需要时立即找到。
2.2 目的:(1)清除“寻找”的浪费; (2)工作场所清除明了;(3)整齐的工作环境; (4)清除过多的积压物品;3、清扫3.1定义:清除工作场所的脏污,并防止脏污的发生,保持工作环境的干净明丽。
3.2 目的:(1)保持令人心情愉快的干净环境;(2)减少脏污对品质的影响; (3)减少工业伤害事故;4、清洁4.1 定义:将以上3S实施的做法制度化、规范化,并贯彻执行及维持。
4.2 目的:维持上面的3S成果;5、素养5.1 定义:人人养成好习惯,依规定行事、培养积极进取精神。
5.2 目的:培养具有良好习惯,遵守规则的员工,营造团队精神。
6、安全6.1 定义:养成良好的安全防范意识,减少和杜绝安全事故和人身伤亡事件。
6.2 目的:确保生产现场处于安全状态,设备运转正常。
第三章“6S” 推进组织、职责与权限一、6S 推进委员会组织结构图二、明确组织职责和权限1、实行责任制1.1 推行小组对委员会负责。
1.2 推行小组应依据委员会颁布的目标计划,制定详细的适合本小组实情的目标计划上交委员会,接受委员会的监督考核。
6S管理制度完整版
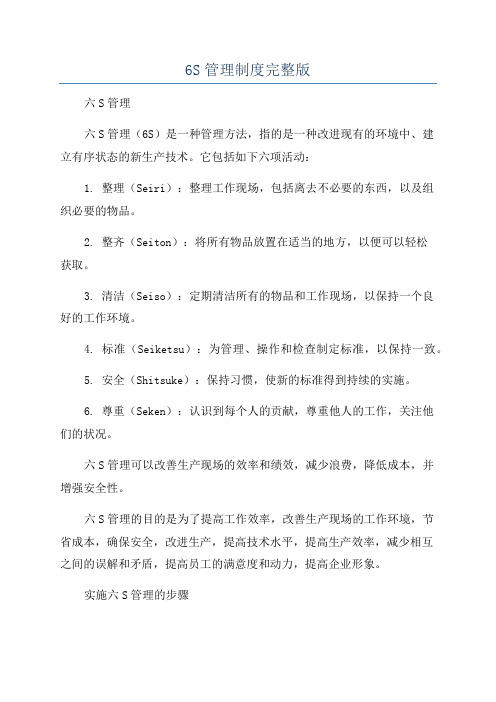
6S管理制度完整版
六S管理
六S管理(6S)是一种管理方法,指的是一种改进现有的环境中、建
立有序状态的新生产技术。
它包括如下六项活动:
1. 整理(Seiri):整理工作现场,包括离去不必要的东西,以及组
织必要的物品。
2. 整齐(Seiton):将所有物品放置在适当的地方,以便可以轻松
获取。
3. 清洁(Seiso):定期清洁所有的物品和工作现场,以保持一个良
好的工作环境。
4. 标准(Seiketsu):为管理、操作和检查制定标准,以保持一致。
5. 安全(Shitsuke):保持习惯,使新的标准得到持续的实施。
6. 尊重(Seken):认识到每个人的贡献,尊重他人的工作,关注他
们的状况。
六S管理可以改善生产现场的效率和绩效,减少浪费,降低成本,并
增强安全性。
六S管理的目的是为了提高工作效率,改善生产现场的工作环境,节
省成本,确保安全,改进生产,提高技术水平,提高生产效率,减少相互
之间的误解和矛盾,提高员工的满意度和动力,提高企业形象。
实施六S管理的步骤
1.立即组织一个六S管理团队:为了确保实施六S管理,必须首先组织一个6S管理小组。
6s管理制度(通用6篇)

6s管理制度6s管理制度篇1一、目的为了更有效的实行和推动6S活动、体现全员参与共同推进和提升。
二、范围公司全体职员三、权责6S推行小组:负责6S的策划、制定、修改、监督执行。
各车间主任:协助6S推行小组组织各车间具体实施执行。
公司全体职员:学习和执行6S精要、体现全员参与。
四、6S诠释4.16S管理之概念6S管理即指整理、整顿、清扫、清洁、修养和安全。
由于前五个词组日文的罗马拼写和第六个词组英文的字母拼写中,第一个字母均为“S”,故简称为“6S”。
6S管理起源于日本,现已成为企业现场管理的经典之作。
4.26S管理之内容⑴整理:首先,对工作现场物品进行分类处理,区分为必要物品和非必要物品、常用物品和非常用物品、一般物品和贵重物品等;⑵整顿:对非必要物品果断丢弃,对必要物品要妥善保存,使工作现场秩序昂然、井井有条;并能经常保持良好状态。
这样才能做到想要什么,即刻便能拿到,有效地消除寻找物品的时间浪费和手忙脚乱;⑶清扫:对各自岗位周围、办公设施进行彻底清扫、清洁,保持无垃圾、无脏污、保证美好的工作环境;⑷清洁:维护清扫后的整洁状态、建立相应的'规章制度;⑸修养:持之以恒,从而养成良好的工作和生活习惯;⑹安全:按章操作,确保人身和公司财产安全,一切主旨均遵循《安全第一、预防为主》的原则。
五、考核5.1平时由6S推行小组实施日常监督和考核。
5.2每周一次由6S推行小组组织各部门车间主任共同参与考核,并提出需整改地方和意见。
5.3每月一次由6S推行小组组织一次公司中层干部共同参与考核,并提出需整改地方和意见。
5.4每半年一次由6S推行小组组织公司高层领导共同参与考核,并提出需整改地方和意见。
5.56S考核最终纳入班组和个人绩效考核。
六、附则6.1具体考核标准参照《6S检查表》。
6.2本规定未尽事宜以6S管理细则或其它相关规定为准。
6.3本规定的解释、修订及废止权归6S推行小组。
6.4本规定自颁发之日起开始生效。
6S管理制度完美版
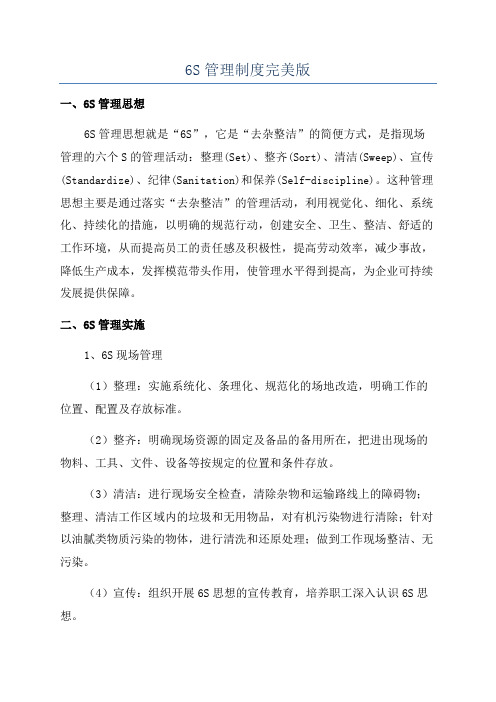
6S管理制度完美版
一、6S管理思想
6S管理思想就是“6S”,它是“去杂整洁”的简便方式,是指现场管理的六个S的管理活动:整理(Set)、整齐(Sort)、清洁(Sweep)、宣传(Standardize)、纪律(Sanitation)和保养(Self-discipline)。
这种管理思想主要是通过落实“去杂整洁”的管理活动,利用视觉化、细化、系统化、持续化的措施,以明确的规范行动,创建安全、卫生、整洁、舒适的工作环境,从而提高员工的责任感及积极性,提高劳动效率,减少事故,降低生产成本,发挥模范带头作用,使管理水平得到提高,为企业可持续发展提供保障。
二、6S管理实施
1、6S现场管理
(1)整理:实施系统化、条理化、规范化的场地改造,明确工作的位置、配置及存放标准。
(2)整齐:明确现场资源的固定及备品的备用所在,把进出现场的物料、工具、文件、设备等按规定的位置和条件存放。
(3)清洁:进行现场安全检查,清除杂物和运输路线上的障碍物;整理、清洁工作区域内的垃圾和无用物品,对有机污染物进行清除;针对以油腻类物质污染的物体,进行清洗和还原处理;做到工作现场整洁、无污染。
(4)宣传:组织开展6S思想的宣传教育,培养职工深入认识6S思想。
6S管理6s管理制度

6S管理6s管理制度6S管理6s管理制度一、6s管理的概念1、6s管理:即指“整理、整顿、清扫、清洁、素养、安全”;2、6s词语由来:由于前五个词组日文的罗马拼写和第六个词组英文的字母拼写中,第一个字母均为“s”,故简称为“6s”;3、6s管理起源:6s管理起源于日本,现已成为国际上许多大中型企业现场管理的经典之作。
二、6s管理之内容1、整理:首先,对工作现场物品进行分类处理,区分为必要物品和非必要物品、常用物品和非常用物品、一般物品和贵重物品等;2、整顿:对非必要物品果断丢弃,对必要物品要妥善保存,使工作现场秩序昂然、井井有条;并能经常保持良好状态。
这样才能做到想要什么,即刻便能拿到,有效地消除寻找物品的时间浪费和手忙脚乱;3、清扫:对各自岗位周围、办公设施进行彻底清扫、清洗,保持无垃圾、无脏污;4、清洁:维护清扫后的整洁状态;5、素养:将上述四项内容切实执行、持之以恒的贯彻执行下去,从而养成一种良好习惯;6、安全:上述一切活动,始终贯彻一个宗旨:围绕其工作环境改善,实现“安全第一,预防为主”。
三、6s管理的意义及好处(一)对个人的意义及好处1、工作态度的改变;2、增加荣誉感;3、增加责任感;4、改善沟通能力;5、改善管理能力;6、改变工作习惯;7得到好的工作环境;改变心态,改善管理沟通能力,改变工作习惯,得到个人能力整体提升。
(二)对企业的意义及好处1、工作态度;2、改善流程;3、改进管理;4、增加放权授能;5、提高效率;6、提升形象;7、合理利用场地;8、提高竞争力;9、改善沟通与信息流通渠道;顾客满意、管理流程改善、提高效率、节约成本、提高竞争力、业绩成长。
四、如何推动6s管理(一)责任部门1、行政部统一管理公司6s的推动工作,负责组建一个由各部门指定人员参加的6s管理小组,该小组有权对各部门6s开展情况进行指导、监督、检查、评比、奖罚和发布;2、各部门组建本部门6s管理小组,定期参加公司6s管理进行指导、监督、检查、评比、奖罚和发布工作。
6S管理制度中的现场管理和持续改进机制

6S管理制度中的现场管理和持续改进机制引言:在现代企业管理中,提高效率和质量是每个企业追求的目标。
为了实现这一目标,许多企业采用了6S管理制度,其中的现场管理和持续改进机制是关键要素。
本文将探讨6S管理制度中的现场管理和持续改进机制,以及它们对企业运营的重要性。
一、6S管理制度的概述6S管理制度是一种基于日本的管理理念,旨在通过整理、整顿、清扫、清洁、素养和自律六个步骤,提高工作环境和工作效率。
这种管理制度强调现场管理和持续改进,以实现高效率和高质量的生产。
二、现场管理在6S管理制度中的作用1. 现场管理的定义现场管理是指对生产现场进行全面管理的过程,包括人员管理、设备管理、物料管理等。
在6S管理制度中,现场管理是实施6S的基础,通过对现场进行规范化管理,提高生产效率和质量。
2. 现场管理的重要性现场管理对企业的运营至关重要。
通过规范现场管理,可以减少生产中的浪费和错误,提高工作效率。
同时,现场管理还可以提高员工的工作积极性和责任感,增强团队协作能力。
三、持续改进机制在6S管理制度中的作用1. 持续改进机制的定义持续改进机制是指通过不断的改进和创新,提高工作流程和产品质量的过程。
在6S管理制度中,持续改进机制是实现6S目标的关键,通过持续改进,可以不断提高生产效率和质量水平。
2. 持续改进机制的重要性持续改进机制对企业的发展至关重要。
通过持续改进,企业可以不断优化工作流程,减少浪费和错误,提高产品质量和客户满意度。
同时,持续改进还可以激发员工的创新能力,促进企业的可持续发展。
四、现场管理和持续改进机制的关系1. 现场管理为持续改进提供基础现场管理是持续改进的基础,只有通过规范的现场管理,才能发现问题和改进的机会。
通过6S的整理、整顿、清扫、清洁等步骤,可以创造一个良好的工作环境,为持续改进提供条件。
2. 持续改进促进现场管理的升级持续改进是现场管理的推动力,只有通过持续改进,才能不断提高现场管理的水平。
生产车间现场6S管理制度(4篇)

生产车间现场6S管理制度第一章总则第一条为了改善生产现场的管理水平,提高工作效率和品质水平,制定本管理制度。
第二条本制度适用于生产车间现场,包括生产设备、工作场所、物料存放等环节。
第三条本制度的要求是:整理(Sorting)、整顿(Set in order)、清扫(Shine)、清洁(Standardize)、素养(Sustain)、安全(Safety)。
第四条全体员工都应遵守本制度,并积极配合执行。
第五条为保障生产车间6S管理制度的执行,将定期组织审核,并根据实际情况进行修订完善。
第二章整理第六条整理是指将工作现场、工作台面、仓库等场所的物品进行分类整理,划分为必要物品、常用物品和不必要物品。
第七条每个工作岗位的员工必须对工作台面、设备周围进行整理,并确保物品摆放合理、标识明确。
第八条不必要的物品应及时清理,可以进行捐赠、报废或处理。
第九条定期检查和整理工作场所的物品,保持整洁有序。
第十条整理工作需要员工的共同努力,各部门之间要加强沟通和协作,确保整理工作的顺利进行。
第三章整顿第十一条整顿是指对工作现场、工作台面、仓库等场所进行布局规划,提高工作效率和人员作业舒适度。
第十二条根据工作需要调整工作现场的布局,确保物品摆放合理、人员通行顺畅。
第十三条保持工作现场的清洁整齐,维护设备和工作台面的整洁。
第十四条提供适当的工作工具和设备,提高工作效率。
第十五条定期检查工作现场的整顿情况,及时进行整改和改进。
第四章清扫第十六条清扫是指对工作现场进行定期清洁,保持整洁有序。
第十七条员工每天上班前和下班后要对工作台面、设备周围进行清扫。
第十八条清扫除灰尘、垃圾等杂物,保持工作现场的清洁。
第十九条定期进行大扫除,对工作场所进行整体的清洁。
第二十条配备必要的清洁工具和设备,保证清洁的进行。
第五章清洁第二十一条清洁是指对工作现场进行定期的清洁和维护,保持工作现场的整洁美观。
第二十二条定期对设备、工作台面、工作区域等进行清洁,确保设备正常运行和工作台面的清洁整洁。
车间6S管理制度17篇

车间6S管理制度篇1一、整理1、通道畅通、整洁。
2、工作场所的设备、物料堆放整齐,不放置不必要的东西。
3、办公桌上、抽屉内办公物品归类放置整齐。
4、料架的'物品摆放整齐。
二、整顿1、机器设备定期保养并有设备保养卡,摆放整齐,处于最佳状态。
2、工具定位放置,定期保养。
3、零部件定位摆放,有统一标识,一目了然。
4、工具、模具明确定位,标识明确,取用方便。
5、车间各区域有6S责任区及责任人。
三、清扫1、保持通道干净、作业场所东西存放整齐,地面无任何杂物3、办公桌、工作台面以及四周环境整洁。
4、窗、墙壁、天花板干净整洁。
5、工具、机械、机台随时清理。
四、清洁1、通道作业台划分清楚,通道顺畅。
2、每天上下班前5分钟做“6S”工作。
3、对不符合的情况及时纠正。
4、保持整理、整顿、清扫成果并改进。
五、素养1、员工戴厂牌。
2、穿厂服且清洁得体,仪容整齐大方。
3、员工言谈举止文明有礼,对人热情大方。
4、员工工作精神饱满。
5、员工有团队精神,互帮互助,积极参加“6S”活动,时间观念强。
六、安全1、重点危险区域有安全警示牌。
2、遵守安全操作规程,保障生产正常进行,不损坏公物。
3、班前不酗酒,不在禁烟区内吸烟车间6S管理制度篇2为保持维修车间现场卫生的清洁,使卫生清理有章可循,特订本规定如下:一、本规定要求卫生清理的范围涵盖了车间设备、车间地板、工作间(总成修理间、工具房、员工休息室和更衣室)、车间内外墙(主要指车间门窗玻璃、各种外露水管和气管等)以及车间用卫生间与地沟等五大部分,本规定对各部分均作了不同的要求。
二、车间设备卫生清理要求1、每台设备空闲时都有其相对固定的位置。
设备空闲时不允许随意挪动,使用完毕后使用人须及时将设备归位。
2、设备使用过程中使用人要养成“随手清洁”的习惯,使用中也尽量保持设备清洁;使用完毕后对设备进行全面清洁后方可将设备归位。
3、车间配件架须按所贴标签要求存放对象,严禁混放;同时摆放要整齐。
6s管理实施制度(精选12篇)

6s管理实施制度(精选12篇)(经典版)编制人:__________________审核人:__________________审批人:__________________编制单位:__________________编制时间:____年____月____日序言下载提示:该文档是本店铺精心编制而成的,希望大家下载后,能够帮助大家解决实际问题。
文档下载后可定制修改,请根据实际需要进行调整和使用,谢谢!并且,本店铺为大家提供各种类型的经典范文,如总结计划、报告材料、策划方案、条据文书、演讲致辞、合同协议、党团资料、教案资料、作文大全、其他范文等等,想了解不同范文格式和写法,敬请关注!Download tips: This document is carefully compiled by this editor. I hope that after you download it, it can help you solve practical problems. The document can be customized and modified after downloading, please adjust and use it according to actual needs, thank you!Moreover, our store provides various types of classic sample essays for everyone, such as summary plans, report materials, planning plans, doctrinal documents, speeches, contract agreements, party and youth organization materials, lesson plan materials, essay encyclopedias, and other sample essays. If you want to learn about different formats and writing methods of sample essays, please stay tuned!6s管理实施制度(精选12篇)6s管理实施制度(精选12篇)6s管理实施制度篇1当场梳理但凡当场没有用的废料、滞销品物品,闲置工作服、设施等都属不必物。
现场6s管理制度
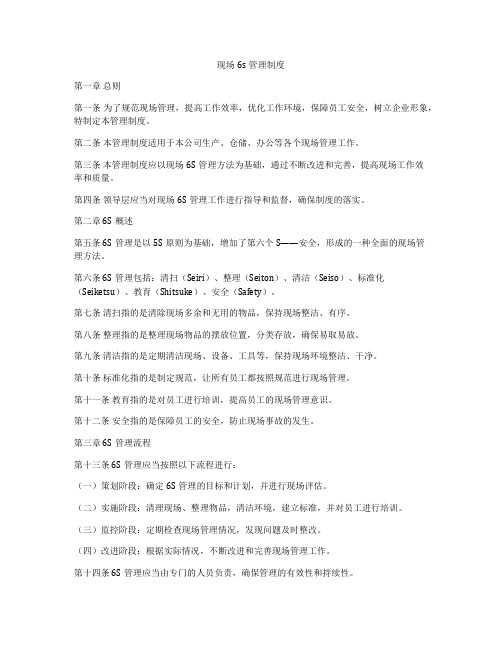
现场6s管理制度第一章总则第一条为了规范现场管理,提高工作效率,优化工作环境,保障员工安全,树立企业形象,特制定本管理制度。
第二条本管理制度适用于本公司生产、仓储、办公等各个现场管理工作。
第三条本管理制度应以现场6S管理方法为基础,通过不断改进和完善,提高现场工作效率和质量。
第四条领导层应当对现场6S管理工作进行指导和监督,确保制度的落实。
第二章 6S概述第五条 6S管理是以5S原则为基础,增加了第六个S——安全,形成的一种全面的现场管理方法。
第六条 6S管理包括:清扫(Seiri)、整理(Seiton)、清洁(Seiso)、标准化(Seiketsu)、教育(Shitsuke)、安全(Safety)。
第七条清扫指的是清除现场多余和无用的物品,保持现场整洁、有序。
第八条整理指的是整理现场物品的摆放位置,分类存放,确保易取易放。
第九条清洁指的是定期清洁现场、设备、工具等,保持现场环境整洁、干净。
第十条标准化指的是制定规范,让所有员工都按照规范进行现场管理。
第十一条教育指的是对员工进行培训,提高员工的现场管理意识。
第十二条安全指的是保障员工的安全,防止现场事故的发生。
第三章 6S管理流程第十三条 6S管理应当按照以下流程进行:(一)策划阶段:确定6S管理的目标和计划,并进行现场评估。
(二)实施阶段:清理现场、整理物品,清洁环境,建立标准,并对员工进行培训。
(三)监控阶段:定期检查现场管理情况,发现问题及时整改。
(四)改进阶段:根据实际情况,不断改进和完善现场管理工作。
第十四条 6S管理应当由专门的人员负责,确保管理的有效性和持续性。
第十五条 6S管理应当制定具体的管理制度和规范,明确工作责任和要求。
第四章 6S管理要求第十六条现场工作人员应当认真执行6S管理制度,做到以下要求:(一)保持现场整洁、有序,避免随意堆放物品。
(二)按照规范存放和使用工具、设备,保持现场整洁。
(三)保持设备、工具的清洁,定期进行维护和保养。
6s施工管理制度

6s施工管理制度一、前言为了规范施工现场的管理,提高施工质量和安全,降低施工事故发生的概率,我们对施工现场进行了6S管理制度的制定,以确保施工现场的整洁、有序和安全。
二、施工现场的6S意义1、提高工作效率2、改善工作环境3、加强安全管理4、降低生产成本5、提高员工工作积极性6、推动企业持续改进三、6S施工管理制度的内容(一)分类整理(Seiri)1、组织专业人员对施工现场设施、工具和材料等进行分类整理,清点库存并制定管理清单。
2、对不需要的设备、材料、工具等进行清理,打包处理或交给相关部门负责人处理。
3、定期对施工现场进行清点,确保设施、工具和材料的分类整理有效。
(二)整顿整理(Seiton)1、对施工现场的工具、设备和材料进行整顿整理,确定合理的存放位置,并进行标示。
2、建立标准化的堆放和存放方式,确保每一件设备、工具和材料都有固定的存放位置。
3、定期维护和清洁存放的设施、工具和材料,保持存放环境的整洁和有序。
(三)清扫清洁(Seiso)1、组织专业人员进行日常清扫清洁,对施工现场的地面、墙面和设施进行彻底清洁。
2、建立清扫清洁的工作标准和频次,确保施工现场的整洁和卫生。
3、加强卫生巡查和监督,发现卫生死角及时整改,确保施工现场的清洁。
(四)清新清爽(Seiketsu)1、组织专业人员对施工现场的环境进行清新清爽,保持施工现场的空气清新和无异味。
2、加强施工现场的通风和消毒工作,确保施工现场的环境卫生和安全。
3、定期进行环境检测,确保施工现场环境的符合标准。
(五)素质教育(Shitsuke)1、加强施工人员的培训和教育,提高员工的素质和意识。
2、建立健全的施工管理制度和工作规范,规范员工的工作行为和工作态度。
3、定期进行员工素质教育和培训,不断提升员工的专业技能和意识。
(六)安全管理(Safety)1、制定施工现场的安全管理制度,并加强管理和督促执行。
2、加强对施工人员的安全教育和培训,确保施工人员的安全意识。
6s现场管理制度
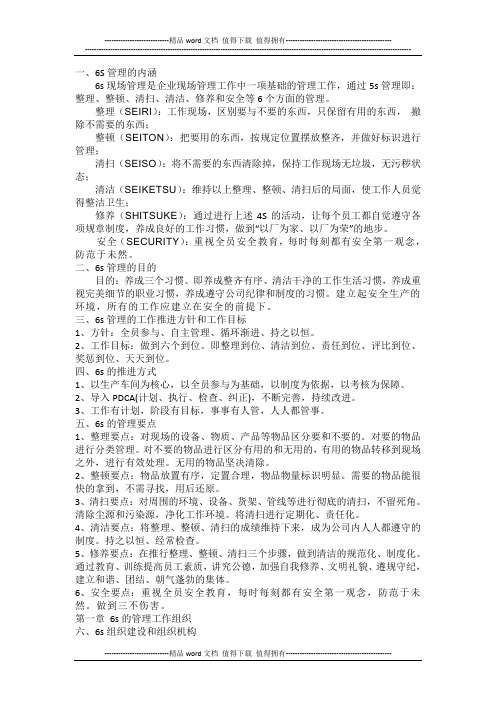
一、6S管理的内涵6s现场管理是企业现场管理工作中一项基础的管理工作,通过5s管理即:整理、整顿、清扫、清洁、修养和安全等6个方面的管理。
整理(SEIRI):工作现场,区别要与不要的东西,只保留有用的东西,撤除不需要的东西;整顿(SEITON):把要用的东西,按规定位置摆放整齐,并做好标识进行管理;清扫(SEISO):将不需要的东西清除掉,保持工作现场无垃圾,无污秽状态;清洁(SEIKETSU):维持以上整理、整顿、清扫后的局面,使工作人员觉得整洁卫生;修养(SHITSUKE):通过进行上述4S的活动,让每个员工都自觉遵守各项规章制度,养成良好的工作习惯,做到“以厂为家、以厂为荣”的地步。
安全(SECURITY):重视全员安全教育,每时每刻都有安全第一观念,防范于未然。
二、6s管理的目的目的:养成三个习惯。
即养成整齐有序、清洁干净的工作生活习惯,养成重视完美细节的职业习惯,养成遵守公司纪律和制度的习惯。
建立起安全生产的环境,所有的工作应建立在安全的前提下。
三、6s管理的工作推进方针和工作目标1、方针:全员参与、自主管理、循环渐进、持之以恒。
2、工作目标:做到六个到位。
即整理到位、清洁到位、责任到位、评比到位、奖惩到位、天天到位。
四、6s的推进方式1、以生产车间为核心,以全员参与为基础,以制度为依据,以考核为保障。
2、导入PDCA(计划、执行、检查、纠正),不断完善,持续改进。
3、工作有计划,阶段有目标,事事有人管,人人都管事。
五、6s的管理要点1、整理要点:对现场的设备、物质、产品等物品区分要和不要的。
对要的物品进行分类管理。
对不要的物品进行区分有用的和无用的,有用的物品转移到现场之外,进行有效处理。
无用的物品坚决清除。
2、整顿要点:物品放置有序,定置合理,物品物量标识明显。
需要的物品能很快的拿到,不需寻找,用后还原。
3、清扫要点:对周围的环境、设备、货架、管线等进行彻底的清扫,不留死角。
清除尘源和污染源,净化工作环境。
车间6S现场管理制度

车间6S现场管理制度一、引言为了提高车间的生产效率和工作环境,确保安全和品质,促进员工工作积极性,制定了车间6S现场管理制度,以规范车间现场的管理工作。
二、目的1.提高车间的整体管理水平,提高生产效率和质量;2.创建整洁有序的工作环境,提高员工的工作积极性和幸福感;3.降低事故和质量问题发生的概率,保障安全和品质;4.强化现场管理的规范性,提升车间形象。
三、管理原则1.环境整洁:保持工作区域的整洁,无杂物、无灰尘、无垃圾;2.整顿有序:将工作工具和物料归位妥善,保证一切准备就绪;3.清洁干燥:工作台面、设备器具、地面保持干净、清洁,无油污、无水渍;4.保持安全:消除安全隐患,确保员工安全;5.培养团队合作意识,共同推进管理工作;6.持续改进,提高管理水平。
四、具体规定1.参与者:全体车间员工及相关工作人员。
2.责任分工:车间主管负责制定执行计划,班组长负责具体组织实施,员工配合执行。
3.每天上班前进行清扫,包括地面、设备、器具、工作台面等;下班后将工作区域内的垃圾清理干净,归位工具和物料。
4.周末进行周清洁,对车间所有区域进行全面的清洁,包括角落、墙壁、天花板等。
5.及时整改异常现象:如发现有杂物、油渍、水渍、设备故障等问题,应及时通知相关责任人进行处理。
6.质量问题的处理:如发现生产过程中的质量问题,应立即停止作业,并进行分析和整改。
7.安全隐患问题的处理:如发现安全隐患问题,应立即上报,并采取相应的措施进行处理。
8.车间标识牌的规范使用:车间内应设置符合规范的安全标识、警示标识,以提醒员工注意安全、防止事故的发生。
9.文件归档:车间管理相关文件、记录应按时归档,确保有效性和可查性。
10.定期检查和评估:车间主管应定期检查和评估6S现场管理的执行情况,对发现的问题及时进行整改。
五、奖惩措施1.凡是积极参与和遵守现场管理规定的员工,将予以表扬和奖励;2.凡是违反和不遵守现场管理规定的员工,将受到批评或相应的惩罚;3.对于多次违反现场管理规定的员工,将视情节严重程度进行相应的处罚。
6s管理制度

6s管理制度6s管理制度(精选11篇)在现实社会中,制度对人们来说越来越重要,制度泛指以规则或运作模式,规范个体行动的一种社会结构。
这些规则蕴含着社会的价值,其运行表彰着一个社会的秩序。
想学习拟定制度却不知道该请教谁?下面是小编收集整理的6s管理制度,希望能够帮助到大家。
6s管理制度篇11、目的为了塑造一个舒适、整洁的工作环境,提升工作效率,节能、清洁、安全生产,把不良因素扼制于萌芽状态,特制订此制度。
2、范围2.1本制度规定了公司在清洁生产工作中对“6S”绩效的奖励和处罚标准;2.2本制度适用于XXXX食品厂各部门(包括办公楼各办公室)、生产车间及其全体人员。
3、6S术语详见附件一《6S管理术语》。
4、组织架构“6S”现场管理检查小组成员:组长:副组长:组员:5、职责5.1公司6S执行小组是公司6S管理的主导部门,负责对公司各部门、生产车间在6S工作中的绩效进行考核。
5.2公司6S执行小组根据本制度相关规定,提出奖惩明细,报6S 负责人审核同意,下达奖惩考核决定。
5.3人力资源部负责对相应的奖惩给予核对。
5.4财务部依据奖惩考核,负责执行。
5.5各部门本着“谁主管、谁负责”的原则,根据本制度负责对部门各班组、在岗员工在6S生产工作中的绩效进行考核。
5.6公司6S执行小组负责对公司部门(车间)、在全年6S生产工作中的绩效进行考核。
6、检查及奖惩6.1检查方法6.1.1公司6S检查共分为集中检查及日常巡查,其中集中检查为3-4次/月、日常巡查视工作开展需要进行,无明确次数;6.1.2检查范围包括但不限于附件二《6S检查范围及执行标准》。
6.2考核6.2.1每月6S执行小组根据设备部A、B区的设备一级保养专项检查、安委会对消防与安全生产(含工伤预防)的专项检查和“6S执行小组”在日常巡查的三项检查结果,综合评比出前三名和后四名(月度评比),按当月6S检查得分综合评比产生,按照相应比例给予奖励和惩罚;6.2.2相关部门管辖范围内的生产现场不符合要求时,在日常巡查发现的,及时通知并督促该部门(车间)主管进行整顿;对于第一次检查不合格的,内网公布其检查结果,并要求作出立即整改;三日后复查如还未整改且又无充分理由的,按执行标准扣罚相应车间主管、责任线主管(技术员),(重大责任事故另行处理);内网公布复查结果;6.2.3对非本部门在本部门管辖范围内的场地施工、作业造成本部门场地脏、乱的,本责任部门有权督促其及时清洁、处理;如未及时作出处理的,一经查出,由本责任部门主管、责任线主管(技术员)全权负责承担;6.2.4月度集中检查采取评分制,即每个区域以100分为基准,每发现一项扣取相应的分数(每项一分/该区域的加权系数),得出每个区域的相应分数;日常巡查采取首次发现不合格项给予整改,第二次复查同类不合格项根据“附件二”的标准予以罚款,第三次在第二次罚款的标准上予以翻番罚款,依次类推;6.2.5公司各部门(车间)可实行内部自检,其奖惩标准不能高于本文件的执行标准。
生产车间现场6S管理制度(3篇)

生产车间现场6S管理制度第一章总则第一条为确保生产秩序,保证各项生产正常运作,持续营造良好的工作环境,促进本公司的发展,结合本公司的实际情况特制订本制度。
第二条本规定适用于本公司生产全体员工。
第二章员工管理第三条工作时间内所有员工倡导普通话,在工作及管理活动中严禁有地方观念或省籍区分。
第四条全体员工须按要求佩戴厂牌(应正面向上佩戴于胸前),穿厂服。
不得穿拖鞋进入车间。
第五条晚上如加班依生产需要临时通知。
若晚上需加班,在下午16:30前填写加班人员申请表,报工程部长并送人事部门作考勤依据。
第六条按时上、下班(员工参加早会须提前____分钟到岗),不迟到,不早退,不旷工(如遇赶货,上、下班时间按照车间安排执行),有事要请假,上、下班须排队依次打卡。
严禁代打卡及无上班、加班打卡。
违者依《考勤管理制度》处理。
第七条工作时间内,质检员和其它管理人员因工作关系在车间走动,其他人员不得离开工作岗位相互窜岗,若因事需离开工作岗位须向生产部长申请方能离岗。
第八条上班后半小时内任何人不得因私事而提出离岗,如有私事要求离岗者,须事先向生产部长申请,经批准方可离岗。
第九条员工在车间内遇上厂方客人或厂部高层领导参观巡察时,组长以上干部应起立适当问候或有必要的陪同,作业员照常工作,不得东张西望。
集体进入车间要相互礼让,特别是遇上客人时,不能争道抢行。
第十条禁止在车间吃饭、吸烟、聊天、嬉戏打闹,吵嘴打架,私自离岗,窜岗等行为(注:脱岗:指打卡后脱离工作岗位或办私事;窜岗:指上班时间窜至他人岗位做与工作无关的事),吸烟要到公司指定的地方或大门外。
违者依《行政管理制度》处理。
第十一条作业时间谢绝探访及接听私人电话.禁止带小孩或厂外人士在生产车间玩耍或滥动车床,由此而造成的事故自行承担。
第十二条未经厂办允许或与公事无关,员工一般不得进入办公室。
第十三条任何人不得携带易燃易爆、易腐烂、毒品、浓气味等违禁物品,危险品或与生产无关之物品进入车间;不得将产品(或废品)和私人用品放在操作台或流水线上,违者《行政管理制度》处理。
- 1、下载文档前请自行甄别文档内容的完整性,平台不提供额外的编辑、内容补充、找答案等附加服务。
- 2、"仅部分预览"的文档,不可在线预览部分如存在完整性等问题,可反馈申请退款(可完整预览的文档不适用该条件!)。
- 3、如文档侵犯您的权益,请联系客服反馈,我们会尽快为您处理(人工客服工作时间:9:00-18:30)。
现场6S管理制度
一、目的
1、对工作现场进行整理、整顿,保持现场处于清洁、整齐、有序的状态;
2、以提高工作效率、降低生产成本、保障生产安全;
3、达到标准化工作、程序化办事、目视化管理、全员自主管理。
二、范围
适用于车间办公场所、生产车间、库房区域等所有区域。
三、名词解释
1、6S:指的是由6S的日文SEIRI(整理)、SEITON(整顿)、SEISO(清扫)、SEIK ETSU(清洁)、SHITSUKE(素养)和英文SAFETY(安全)这六个单词,由于这六个单词前面的发音都是“S”,所以简称为“6S”。
2、整理:将办公场所和工作现场中的物品、设备、工器具清楚的区分为需要品和不需要品,对需要品进行妥善保管,对不需要品则进行处理、报废或移出。
3、整顿:将需要品依据所规定的定位、定量等方式进行摆放整齐,并明确地对其予以标识或划线,使寻找需要品的时间减少为零,同时现场管理更透明。
4、清扫:将办公场所和现场的工作环境打扫干净,使其保持在无垃圾、无灰尘、无脏污、干净整洁的状态,并防止其污染的发生。
5、清洁:将整理、整顿、清扫的实施做法进行到底,且维持其成果,并对其实施做法予以标准化、制度化。
6、素养:以“人性”为出发点,透过整理、整顿、清扫、清洁等合理化的改善活动,培养上下一体的共同管理语言,使全体人员养成守标准、守规定的良好习惯,进而促进全面管理水平的提升。
7、安全:指企业在产品的生产过程中,能够在工作状态、行为、设备及管理等一系列活动中给员工带来即安全又舒适的工作环境。
四、职责:
1、车间主任、主管、辅管全面负责生产现场、车间区域、办公区域等工作环境执行指导、监督检查;
2、班组长、质检员、主操等负责各岗位的现场执行、维持和管理;
五、现场6S管理内容
1、现场管理原则:现场一切物品都有区(位);一切区域都有标识;一切设施的用途
和状态都明确;一切不安全因素都要排除。
2、工作环境区域划分:根据实际的工作区域使用情况划分工作环境责任区域,明确工作环境责任区域的负责人,责任到人,体系管理。
3、6S执行小组定期检查:每周一次对车间内所有的生产现场、办公区域、库房等工作环境区域按6S检查项目进行检查,针对检查问题讨论合理优化方案。
4、目视化管理:利用形象直观、色彩适宜的各种视觉感知信息来组织现场管理,就是指“无论谁见到管理的对象,都能立刻对其正常、异常状态作出正确的判断、并且清楚异常处置方法的管理。
也叫“看得见的管理”或“一目了然的管理”。
从简单有效处入手,从模仿到创造,循序渐进,逐步完善。
目视化管理可用于现场管理、库存管理、安全管理、设备管理、品质管理及办公室管理等。
六、执行方案
1、建立6S执行小组:车间主任、主管、辅管、全场质检员、班组长、主操;
2、建立现场6S责任区域清单,责任到人,系统管理;
3、逐步推进计划
七、附表
附表1 基准表
附表2 要与不要物品清单附表3 清扫责任基准表附表4 现场定置管理图
.
附表1 基准表
附表2 现场整理——要与不要物品清单岗位:
附表3 清扫基准表。