扩散工艺-半导体制造
半导体八大工艺顺序

半导体八大工艺顺序半导体八大工艺顺序,是指半导体制造过程中的八个主要工艺步骤。
这些工艺步骤包括晶圆清洗、光刻、沉积、刻蚀、扩散、离子注入、退火和包封。
下面将逐一介绍这些工艺步骤的顺序及其作用。
1. 晶圆清洗晶圆清洗是半导体制造过程中的第一步。
在这一步骤中,晶圆将被放入化学溶液中进行清洗,以去除表面的杂质和污染物。
这样可以确保后续工艺步骤的顺利进行,同时也可以提高器件的质量和性能。
2. 光刻光刻是半导体制造中的关键工艺步骤之一。
在这一步骤中,将使用光刻胶覆盖在晶圆表面上,并通过光刻机将图形投射到光刻胶上。
然后,利用化学溶液将未曝光的光刻胶去除,从而形成所需的图形。
3. 沉积沉积是指在晶圆表面上沉积一层薄膜的工艺步骤。
这一层薄膜可以用于改变晶圆表面的性质,增加其导电性或绝缘性。
常用的沉积方法包括化学气相沉积和物理气相沉积。
4. 刻蚀刻蚀是将多余的材料从晶圆表面去除的工艺步骤。
在这一步骤中,利用化学溶液或等离子刻蚀机将不需要的材料去除,从而形成所需的图形和结构。
5. 扩散扩散是将杂质或掺杂物diffused 到晶圆中的工艺步骤。
这一步骤可以改变晶圆的电学性质,并形成PN 结等器件结构。
常用的扩散方法包括固体扩散和液相扩散。
6. 离子注入离子注入是将离子注入到晶圆中的工艺步骤。
这可以改变晶圆的导电性和掺杂浓度,从而形成电子器件的结构。
离子注入通常在扩散之前进行。
7. 退火退火是将晶圆加热至一定温度并保持一段时间的工艺步骤。
这可以帮助晶圆中的杂质扩散和掺杂物活化,从而提高器件的性能和稳定性。
8. 包封包封是将晶圆封装在外部保护材料中的工艺步骤。
这可以保护晶圆不受外部环境的影响,同时也可以方便晶圆的安装和使用。
半导体制造过程中的八大工艺顺序是一个复杂而精密的过程。
每个工艺步骤都起着至关重要的作用,只有严格按照顺序进行,才能生产出高质量的半导体器件。
希望通过本文的介绍,读者对半导体制造过程有了更深入的了解。
半导体不同扩散工艺的特点

半导体不同扩散工艺的特点
半导体的扩散技术是将特定种类的杂质原子在半导体晶体中扩散,并改变半导体材料的导电性质。
半导体扩散工艺主要分为以下几种:
1. 扩散氧化法:将硅片加热至高温,使气体中的氧气(O2)分解,产生的氧分子与硅片表面反应,生成二氧化硅(SiO2),从而控制扩散层的深度和宽度。
该工艺的特点是扩散面积大,扩散层深度均匀,但是扩散速度较慢,适用于生产较高质量要求的器件。
2. 氧化掩蔽扩散法(LOCOS):利用化学气相沉积或物理气相沉积在硅片表面沉积一层硅氧化物光刻膜(LOCOS法)或硅酸盐膜(LOCAT法),通过扩散杂质(如磷、硼等)和高温处理,使膜下方的硅衬底发生晶格变形和氧化,形成带孔的氧化硅层,从而形成了扩散区域。
该工艺特点是可制造出复杂的器件结构,但是对于大尺寸芯片来说,芯片表面会过度弯曲,造成拉应力,最终导致母片变形,影响器件性能和可靠性。
3. 氧化铝扩散法:在扩散前利用化学气相沉积在硅片表面沉积一层氧化铝膜,再在这层氧化铝膜上打一个小口(缺口),通过缺口在晶体下面扩散,形成扩散区。
该工艺特点是可保护芯片表面,避免造成晶片变形,但是扩散层较浅,仅适用于制造器件的浅扩散层。
4. 离子注入法:利用离子加速器将杂质离子注入到硅晶体中,形成扩散区。
该
种方法的特点是扩散速度快,扩散深度大,适用于生产器件的深扩散层,但是也存在与晶片表面反应的问题,同时也会导致结果分布不均匀的问题。
总之,选择适当的扩散工艺需要根据所需器件的性质和质量要求来确定。
半导体制造工艺之扩散原理概括

预淀积+退火。预淀积:气固相预淀积
1、掺杂工艺一般分为 哪两步?结深?薄层电 阻?固溶度?
扩散或离子注入。Rs:表面为正方形的 半导体薄层(结深),在平行电流方向
所呈现的电阻,单位为 /,反映扩散
入硅内部的净杂质总量。固溶度:在平
衡条件下,杂质能溶解在硅中而不发生
2、两种特殊条件下的费 反应形成分凝相的最大浓度。
3、氧化增强/抑制扩散(oxidation enhanced / retarded diffusion)OED/ORD
对于B,P来说,在氧化过程中,其扩散系数增加。
对Sb来说,扩散系数减小。
双扩散机制: 杂质可以通过空位和间隙两种方式扩散
1 )OED:对于原子B或P来说,其在硅中的扩散可以 通过间隙硅原子进行。氧化时由于体积膨胀,造成大 量Si间隙原子注入,增加了B和P的扩散系数
DA ef fD0DnpiDnpi
n型掺杂 p型掺杂
1000 C下,非本征扩散系数:
D A s1.6 6 11 04 c2 m /sec
箱型
非本征掺杂扩散系数比本征掺
杂扩散系数高一个数量级!!
由于非本征掺杂的扩散系数在 掺杂边缘迅速衰减,因而出现 边缘陡峭的“箱型”分布。
n
由
np
n
2 i
并假定杂质全部离化,有
C NA ND
n C24ni2 C 2
场助扩散方程: FhDCx
其中h为扩散系数的电场增强因子: h1
C C2 4ni2
当掺杂浓度远大于本征载流子浓度时,h 接近 2。
电场效应对于低浓度本体杂质分布影响更大
2、扩散系数与杂质浓度的关系
离子注入 +
扩散工艺-半导体制造

扩散工艺前言:扩散部按车间划分主要由扩散区域及注入区域组成,其中扩散区域又分扩散老区和扩散新区。
扩散区域按工艺分,主要有热氧化、扩散、LPCVD、合金、清洗、沾污测试等六大工艺。
本文主要介绍热氧化、扩散及合金工艺。
目录第一章:扩散区域设备简介……………………………………第二章:氧化工艺第三章:扩散工艺第四章:合金工艺第一章:扩散部扩散区域工艺设备简介炉管设备外观:扩散区域的工艺、设备主要可以分为:类别主要包括按工艺分类热氧化一氧、二痒、场氧、Post氧化扩散推阱、退火/磷掺杂LPCVD TEOS、SI3N4、POL Y清洗进炉前清洗、漂洗合金合金按设备分类卧式炉A、B、C、D、F、H、I六台立式炉VTR-1、VTR-2、VTR-3 清洗机FSI-1、FSI-2炉管:负责高温作业,可分为以下几个部分:组成部分功能控制柜→对设备的运行进行统一控制;装舟台:→园片放置的区域,由控制柜控制运行炉体:→对园片进行高温作业的区域,由控制柜控制升降温源柜:→供应源、气的区域,由控制柜控制气体阀门的开关。
FSI:负责炉前清洗。
第二章:热氧化工艺热氧化法是在高温下(900℃-1200℃)使硅片表面形成二氧化硅膜的方法。
热氧化的目的是在硅片上制作出一定质量要求的二氧化硅膜,对硅片或器件起保护、钝化、绝缘、缓冲介质等作用。
硅片氧化前的清洗、热氧化的环境及过程是制备高质量二氧化硅膜的重要环节。
2. 1氧化层的作用2.1.1用于杂质选择扩散的掩蔽膜常用杂质(硼,磷,砷等)在氧化层中的扩散系数远小于在硅中的扩散系数,因此氧化层具有阻挡杂质向半导体中扩散的能力。
利用这一性质,在硅上的二氧化硅层上刻出选择扩散窗口,则在窗口区就可以向硅中扩散杂质,其它区域被二氧化硅屏蔽,没有杂质进入,实现对硅的选择性扩散。
1960年二氧化硅就已被用作晶体管选择扩散的掩蔽膜,从而导致了硅平面工艺的诞生,开创了半导体制造技术的新阶段。
同时二氧化硅也可在注入工艺中,作为选择注入的掩蔽膜。
扩散片生产工艺
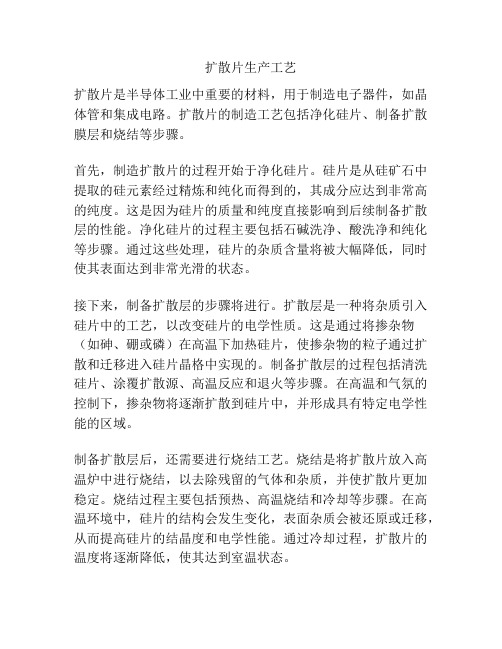
扩散片生产工艺扩散片是半导体工业中重要的材料,用于制造电子器件,如晶体管和集成电路。
扩散片的制造工艺包括净化硅片、制备扩散膜层和烧结等步骤。
首先,制造扩散片的过程开始于净化硅片。
硅片是从硅矿石中提取的硅元素经过精炼和纯化而得到的,其成分应达到非常高的纯度。
这是因为硅片的质量和纯度直接影响到后续制备扩散层的性能。
净化硅片的过程主要包括石碱洗净、酸洗净和纯化等步骤。
通过这些处理,硅片的杂质含量将被大幅降低,同时使其表面达到非常光滑的状态。
接下来,制备扩散层的步骤将进行。
扩散层是一种将杂质引入硅片中的工艺,以改变硅片的电学性质。
这是通过将掺杂物(如砷、硼或磷)在高温下加热硅片,使掺杂物的粒子通过扩散和迁移进入硅片晶格中实现的。
制备扩散层的过程包括清洗硅片、涂覆扩散源、高温反应和退火等步骤。
在高温和气氛的控制下,掺杂物将逐渐扩散到硅片中,并形成具有特定电学性能的区域。
制备扩散层后,还需要进行烧结工艺。
烧结是将扩散片放入高温炉中进行烧结,以去除残留的气体和杂质,并使扩散片更加稳定。
烧结过程主要包括预热、高温烧结和冷却等步骤。
在高温环境中,硅片的结构会发生变化,表面杂质会被还原或迁移,从而提高硅片的结晶度和电学性能。
通过冷却过程,扩散片的温度将逐渐降低,使其达到室温状态。
最后,对扩散片进行测试和封装。
在测试过程中,根据扩散片的设计和制造要求,对其进行性能、电学和功能测试,以确保其质量合格。
通过封装工艺,将扩散片连接到器件的引脚上,并加上绝缘材料和外壳,以保护扩散片不受外界环境的损害。
总结起来,扩散片的制造工艺包括净化硅片、制备扩散膜层和烧结等步骤。
通过这些工艺步骤,硅片的纯度和电学性能得到改善,扩散层的材料和结构也得到了优化。
这些工艺的控制和优化对于确保扩散片的质量和可靠性非常重要,同时也对半导体器件的性能和功能发挥起着至关重要的作用。
半导体制造工艺之扩散原理

01
半导体制造工艺简介
半导体材料的基本特性
半导体材料的导电性
半导体材料的光电特性
半导体材料的热稳定性
• 半导体材料的导电性介于导体和绝
• 半导体材料具有光电效应
• 半导体材料具有较高的热稳定性
缘体之间
• 半导体材料的光电效应可用于光电
• 半导体材料的热稳定性可用于高温
• 随着温度的升高,半导体材料的导
扩散掩膜与阻挡层材料
扩散掩膜材料
• 扩散掩膜材料可分为光刻胶、金属薄膜、氧化膜等
• 扩散掩膜材料的选择应根据扩散工艺的要求和半导体材料的性质进行
• 扩散掩膜材料的选择应考虑掩膜材料的耐腐蚀性、抗氧化性、光刻性能等
阻挡层材料
• 阻挡层材料可分为氧化物、氮化物、碳化物等
• 阻挡层材料的选择应根据扩散工艺的要求和半导体材料的性质进行
扩散源的选择
扩散源的制备
• 扩散源可分为气体扩散源、液体扩散源、固体扩散源等
• 气体扩散源的制备方法包括蒸发法、溅射法、化学气相
• 扩散源的选择应根据扩散工艺的要求和半导体材料的性
沉积法等
质进行
• 液体扩散源的制备方法包括溶液法、溶胶-凝胶法等
• 扩散源的选择应考虑扩散源的纯度和可控性
• 固体扩散源的制备方法包括烧结法、热压法等
• 扩散工艺的可持续发展应考虑工艺的创新性和竞争力
扩散工艺的环境保护
• 扩散工艺的环境保护应考虑工艺的废弃物处理、污染物排放、环境风险等
• 扩散工艺的环境保护应考虑工艺对半导体器件性能的影响和生产成本
• 扩散工艺的环境保护应考虑工艺的环保政策和法规要求
谢谢观看
Tencent Docs
半导体扩散工艺

半导体扩散工艺
半导体扩散工艺是半导体工艺中最重要的一种工艺,用它来在半导体器件中制造出电子元件和晶体管。
它是通过将一种特定的元素,如铜、硼、钒或钴等,以电子成分形式沉积在半导体片上,从而制造电子元件和晶体管的工艺。
这种工艺在模拟和数字电路装配等各个领域得到了广泛应用,特别是用来制造微电子装置。
半导体扩散工艺的原理是将一种元素的电子沉积在半导体片上,通过一种物理热力学过程,当此元素熔合在半导体基体上时,会产生少量的电子,少量的电子会与基体后固态化,将此元素完全沉积在半导体基体上。
半导体器件制造多种元件都需要用到它。
此工艺需要温度控制非常精确,才能溶解和形成适当的电子活动,而且沉积的能电子活动也是同样重要的。
现代的半导体技术允许使用半导体扩散工艺制造出更小和更复杂的电子元件。
因为它可以创造出超微的三维结构,使设计的电路变得更容易,更小型,更有效。
精密的技术也更容易缩小特性阻抗不一致,减少无效噪音。
所以,半导体扩散工艺已经成为制造超灵敏和超高速半导体电路的必要技术之一。
半导体扩散工艺需要使用多种物质,如硼、砷、铝、铜、砒霜、钿等,以使沉积的材料能够形成特定的三维结构。
其中硫化铝和砒霜是扩散工艺所必须的物质,因为硫化铝能加速活性碳和真空的反应,砒霜能与半导体材料形成强化膜,加快固溶因子的游离度。
此外,扩散工艺还需要使用真空熔体装置,保持环境的干净和污染,因为氧的迹及其它杂质会影响到最终产品的质量和性能。
八个基本半导体工艺

八个基本半导体工艺随着科技的不断进步,半导体技术在各个领域得到了广泛的应用。
半导体工艺是半导体器件制造过程中的关键环节,也是半导体产业发展的基础。
本文将介绍八个基本的半导体工艺,分别是氧化、扩散、沉积、光刻、蚀刻、离子注入、热处理和封装。
一、氧化工艺氧化工艺是指在半导体晶片表面形成氧化层的过程。
氧化层可以增强晶片的绝缘性能,并且可以作为蚀刻掩膜、电介质、层间绝缘等多种用途。
常见的氧化工艺有湿法氧化和干法氧化两种。
湿法氧化是在高温高湿的环境中,通过将晶片浸泡在氧化液中使其表面氧化。
干法氧化则是利用高温下的氧化气体与晶片表面反应来形成氧化层。
二、扩散工艺扩散工艺是指将掺杂物质(如硼、磷等)通过高温处理,使其在晶片中扩散,从而改变晶片的导电性能。
扩散工艺可以用于形成PN结、调整电阻、形成源、漏极等。
扩散工艺的关键是控制扩散温度、时间和掺杂浓度,以确保所需的电性能。
三、沉积工艺沉积工艺是将材料沉积在半导体晶片表面的过程。
常见的沉积工艺有化学气相沉积(CVD)和物理气相沉积(PVD)两种。
CVD是利用化学反应在晶片表面沉积薄膜,可以实现高纯度、均匀性好的沉积。
而PVD则是通过蒸发、溅射等物理过程,在晶片表面形成薄膜。
四、光刻工艺光刻工艺是将光敏胶涂覆在晶片表面,然后通过光刻曝光、显影等步骤,将光敏胶图案转移到晶片上的过程。
光刻工艺是制造半导体器件的核心工艺之一,可以实现微米级甚至纳米级的图案制作。
五、蚀刻工艺蚀刻工艺是通过化学反应或物理过程将晶片表面的材料去除的过程。
蚀刻工艺可以用于制作电路的开关、互连线等。
常见的蚀刻方法有湿法蚀刻和干法蚀刻两种。
湿法蚀刻是利用化学溶液对晶片表面进行腐蚀,而干法蚀刻则是通过等离子体或离子束对晶片表面进行刻蚀。
六、离子注入工艺离子注入工艺是将掺杂离子注入晶片中的过程。
离子注入可以改变晶片的导电性能和材料特性,常用于形成源漏极、调整电阻等。
离子注入工艺需要控制注入能量、剂量和深度,以确保所需的掺杂效果。
2、半导体工艺原理-扩散

薄层电阻Rs(方块电阻) 表面浓度:扩散层表面的杂质浓度。
扩散层质量参数
方块电阻
方块电阻是标志扩散层质量的另一个重要参数, 一般用R□或Rs表示,单位是Ω/□ 。
2、恒定杂质总量扩散
扩散开始时,表面放入一定量的杂质源,而在以后的扩散
过程中不再有杂质加入。假定扩散开始时硅片表面极薄一层内
单位面积的杂质总量为 QT ,杂质的扩散长度远大于该层厚度,
则杂质的初始分布可取为 函数,扩散方程的初始条件和边界
条件为
0 N (x, t)dx QT
N (,t) 0
2 NS1
D1t1 D2t2
exp
x
2 j
4 D2t2
NB
即可解得
xj 2
D2t2
ln
2 NS1
NB
1
D1t1 D2t2
2
A
D2t2
掺杂分布控制:
3.3 简单理论的修正
前面得出的扩散后的杂质分布是采用理想化假设的结果, 而实际分布与理论分布之间存在着一定的差异,主要有:
1、二维扩散(横向扩散) 实际扩散中,杂质在通过窗口垂直向硅中扩散的同时,也 将在窗口边缘沿表面进行横向扩散。考虑到横向扩散后,要得 到实际的杂质分布,必须求解二维或三维扩散方程。横向扩散 的距离约为纵向扩散距离的 75% ~ 80% 。由于横向扩散的存在, 实际扩散区域大于由掩模版决定的尺寸,此效应将直接影响到 VLSI 的集成度。
2、杂质浓度对扩散系数的影响
前面的讨论假定扩散系数与杂质浓度无关。实际上只有当 杂质浓度比扩散温度下的本征载流子浓度 ni(T) 低时,才可认 为扩散系数与掺杂浓度无关。在高掺杂浓度下各种空位增多, 扩散系数应为各种电荷态空位的扩散系数的总和。
半导体制造工艺扩散上

半导体制造工艺扩散上半导体制造工艺中的扩散技术是一种基础性的工艺技术,它具有极高的重要性。
扩散技术主要用于控制半导体材料中杂质浓度及其分布,以及基本材料参数(例如,导电性、PN结绝缘等等),这对于制造优质半导体芯片来说是不可或缺的。
扩散技术的原理“扩散”一词意为“分散”或“分布”。
在半导体领域中,“扩散”指的是杂质(或原子)从一个区域逐渐分散到另一个区域的的过程。
扩散过程主要是基于热力学原理发生的,其发生的基本原理是高浓度区域向低浓度区域传输,这种传输是一种自然趋势。
扩散过程需要满足Fick’s定律,即杂质或原子的扩散迁移率与它在材料中的浓度梯度成正比,与温度和材料阻力成反比。
扩散技术在半导体材料制备过程中的应用扩散技术是半导体制造中最为基础并且也是最为普遍应用的技术之一。
它可以应用于制备许多不同种类的器件,例如:1.PN结制备扩散技术在PN结制备中是不可或缺的。
通过对半导体硅晶片进行扩散掺杂,可以在硅晶片表面形成浓度梯度,从而在P型区域和N型区域形成硅晶片的PN结。
2.表面功能化和通道控制在面向晶圆的制造工艺中,扩散技术通常用于表面功能化和通道控制。
通过半导体材料表面的扩散工艺,可以轻松地在晶圆表面形成氧化物层、硅类材料层等功能性层,还可以通过扩散工艺控制通道的形状和尺寸。
3.金属接触制备扩散技术通常可以与金属联系在一起,制备金属与半导体之间的接触点。
在该过程中,原子从金属的表面逐渐进入半导体材料,并将金属与半导体之间形成硬接结,这是许多器件的耐久性和稳定性的基础。
扩散技术的技术调优当人们在制造半导体器件时,对于扩散技术的选择,需要根据具体细节和设备要求进行调优。
以下是扩散技术的技术调优方法:1.涂覆层厚度和材料的选择在很多情况下,使用涂覆材料可以帮助控制扩散过程。
经典的例子是硅胶片,它在半导体晶体片制造过程中通常用作覆盖层。
通过合理地选择涂覆层的厚度和材料,制造人员以期望的方式控制扩散过程,从而缩小半导体器件的尺寸并控制制造纯度。
半导体制造工艺之扩散原理概述

半导体制造工艺之扩散原理概述引言半导体器件是现代电子化工程的重要组成部分,而半导体制造工艺中的扩散过程是其中的核心步骤之一。
扩散是指将外部杂质或原子通过加热和蒸发的方式引入半导体晶体内部,从而改变其导电性能的过程。
本文将概述半导体制造工艺中的扩散原理,包括扩散的定义、分类、扩散过程的主要步骤以及应用。
扩散的定义和分类扩散在半导体制造加工中是用于改变材料电学特性和形成器件结构的重要工艺。
它通过在半导体材料中掺杂外部杂质或原子,改变其禁带宽度、导电性能和晶格结构,从而实现对器件特性的控制。
根据掺杂的原子种类和结构变化,扩散可以分为以下几类:1.硼扩散(Boron diffusion):将硼原子引入到半导体材料中,可以增加材料的p型掺杂浓度。
2.磷扩散(Phosphorus diffusion):将磷原子引入到半导体材料中,可以增加材料的n型掺杂浓度。
3.氮扩散(Nitrogen diffusion):将氮原子引入到半导体材料中,可以改变半导体材料的特性,如降低材料的电阻率和增加材料的硬度。
4.氢扩散(Hydrogen diffusion):将氢原子引入到半导体材料中,可以提高材料的电阻率。
5.金属扩散(Metal diffusion):在半导体材料中引入金属原子,可以改变材料的特性,如增强导电性能或改变器件结构。
扩散过程的主要步骤扩散过程是一个涉及多个步骤的复杂过程,主要包括以下几个步骤:清洗在扩散之前,半导体晶体需要进行清洗,以去除表面的污染物和杂质,保证扩散过程的准确性和稳定性。
清洗步骤可以使用化学清洗方法或物理清洗方法,如溶剂洗涤、超声波清洗等。
预处理预处理步骤是为了提高扩散效果和降低生产成本而进行的一系列处理。
包括表面氧化、蚀刻、离子注入等工艺,以提高扩散层的质量和一致性。
掺杂掺杂是扩散过程中的核心步骤,通过向半导体晶体中注入外部杂质,改变材料的导电性能。
掺杂过程中需要控制掺杂浓度和深度,以满足器件设计要求。
半导体制造工艺流程
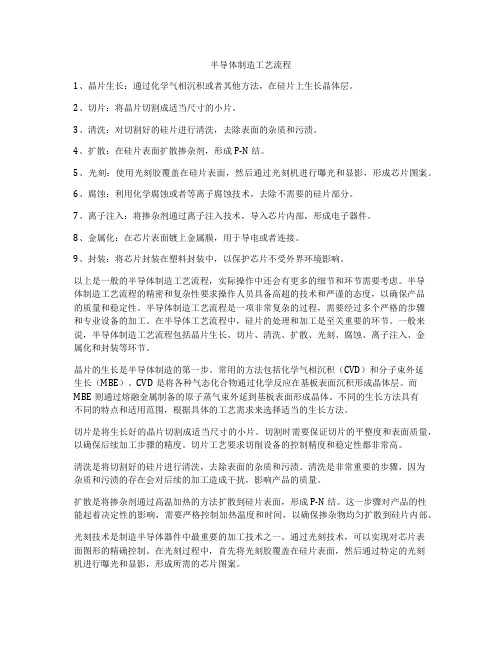
半导体制造工艺流程1、晶片生长:通过化学气相沉积或者其他方法,在硅片上生长晶体层。
2、切片:将晶片切割成适当尺寸的小片。
3、清洗:对切割好的硅片进行清洗,去除表面的杂质和污渍。
4、扩散:在硅片表面扩散掺杂剂,形成P-N结。
5、光刻:使用光刻胶覆盖在硅片表面,然后通过光刻机进行曝光和显影,形成芯片图案。
6、腐蚀:利用化学腐蚀或者等离子腐蚀技术,去除不需要的硅片部分。
7、离子注入:将掺杂剂通过离子注入技术,导入芯片内部,形成电子器件。
8、金属化:在芯片表面镀上金属膜,用于导电或者连接。
9、封装:将芯片封装在塑料封装中,以保护芯片不受外界环境影响。
以上是一般的半导体制造工艺流程,实际操作中还会有更多的细节和环节需要考虑。
半导体制造工艺流程的精密和复杂性要求操作人员具备高超的技术和严谨的态度,以确保产品的质量和稳定性。
半导体制造工艺流程是一项非常复杂的过程,需要经过多个严格的步骤和专业设备的加工。
在半导体工艺流程中,硅片的处理和加工是至关重要的环节。
一般来说,半导体制造工艺流程包括晶片生长、切片、清洗、扩散、光刻、腐蚀、离子注入、金属化和封装等环节。
晶片的生长是半导体制造的第一步。
常用的方法包括化学气相沉积(CVD)和分子束外延生长(MBE)。
CVD是将各种气态化合物通过化学反应在基板表面沉积形成晶体层。
而MBE则通过熔融金属制备的原子蒸气束外延到基板表面形成晶体。
不同的生长方法具有不同的特点和适用范围,根据具体的工艺需求来选择适当的生长方法。
切片是将生长好的晶片切割成适当尺寸的小片。
切割时需要保证切片的平整度和表面质量,以确保后续加工步骤的精度。
切片工艺要求切削设备的控制精度和稳定性都非常高。
清洗是将切割好的硅片进行清洗,去除表面的杂质和污渍。
清洗是非常重要的步骤,因为杂质和污渍的存在会对后续的加工造成干扰,影响产品的质量。
扩散是将掺杂剂通过高温加热的方法扩散到硅片表面,形成P-N结。
这一步骤对产品的性能起着决定性的影响,需要严格控制加热温度和时间,以确保掺杂物均匀扩散到硅片内部。
半导体制造工艺基础之扩散工艺培训课件
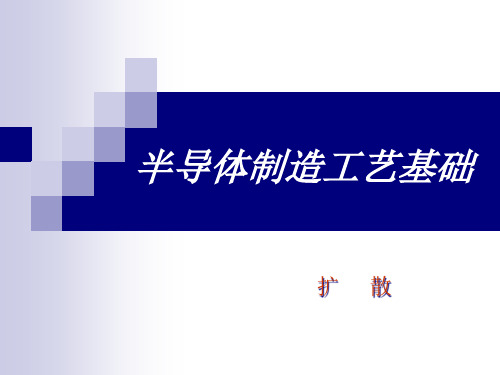
掺杂区
掺杂区的类型:相同或相反 结深:硅片中p型杂质与n型杂质相遇的深度,用
Xj表示,深度等于结深的地方,电子与空穴的浓 度相等。
6.1 基本扩散工艺
掺入方式有:气相源;固相源;液相源,其中液态 源最常用。 使用液相源的磷扩散的化学反应如下:
4POCl3 3O2 2P2O5 6Cl2
(1)替代式扩散
替位原子的运动必须以其近邻处有空位存在为前提。
移动速度较慢的杂质,如半导体掺杂常用的砷、磷,通常 利用替代运动填充晶格中的空位。
(2)填隙式扩散
F D C x
扩散流密度F--单位时间内通过单位面积的杂质原子数; C--单位体积的杂质浓度; D--扩散系数或扩散率; 扩散驱动力是浓度梯度,杂质原子从高浓度区流向低浓度 区。
热扩散中的横向扩散通常是纵向结深的75%-85%。
6.1.3 扩散层测量
扩散工艺的结构可由三种测量方式来评价:扩散层的结深、 薄层电阻与杂质分布。下图是在半导体内磨以凹槽并用溶液 腐蚀去除表面,溶液会使P区颜色暗,因而描绘出结深。
用磨槽和染色法测量结深
若R0是磨槽所用工具的半径,则可得结深:
x j R02 b2 R02 a2
扩散和离子注入是半导体掺杂的两种主要方式。 高温扩散:杂质原子通过气相源或掺杂过的氧化物扩散到硅 片的表面,这些杂质浓度将从表面到体内单调下降,而杂质 分布主要是由高温与扩散时间来决定。
形成深结
扩散工艺的优越性:
(1)可以通过对温度、时间等工艺条件的准确调节,来控 制PN结面的深度和晶体管的基区宽度,并能获得均匀平坦 的结面。
杂质移动
杂质只有在成为硅晶格结构的一部分(即被 激活)后,才可以作为施主和受主。如果杂 质占据间隙位置,它就没有被激活,不会起 到杂质的作用。
半导体制造工艺之扩散原理
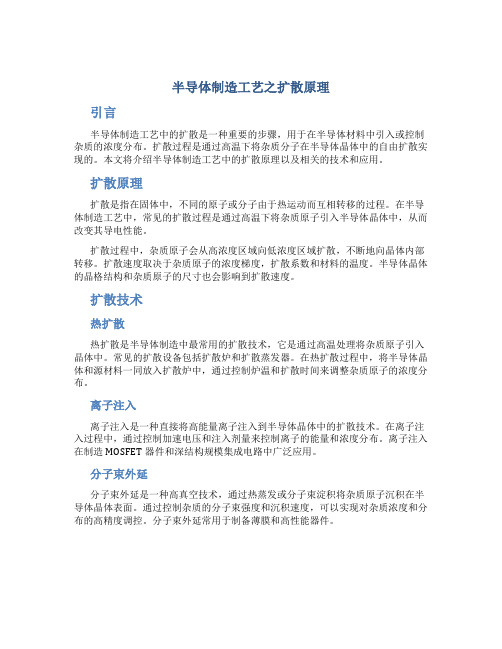
半导体制造工艺之扩散原理引言半导体制造工艺中的扩散是一种重要的步骤,用于在半导体材料中引入或控制杂质的浓度分布。
扩散过程是通过高温下将杂质分子在半导体晶体中的自由扩散实现的。
本文将介绍半导体制造工艺中的扩散原理以及相关的技术和应用。
扩散原理扩散是指在固体中,不同的原子或分子由于热运动而互相转移的过程。
在半导体制造工艺中,常见的扩散过程是通过高温下将杂质原子引入半导体晶体中,从而改变其导电性能。
扩散过程中,杂质原子会从高浓度区域向低浓度区域扩散,不断地向晶体内部转移。
扩散速度取决于杂质原子的浓度梯度,扩散系数和材料的温度。
半导体晶体的晶格结构和杂质原子的尺寸也会影响到扩散速度。
扩散技术热扩散热扩散是半导体制造中最常用的扩散技术,它是通过高温处理将杂质原子引入晶体中。
常见的扩散设备包括扩散炉和扩散蒸发器。
在热扩散过程中,将半导体晶体和源材料一同放入扩散炉中,通过控制炉温和扩散时间来调整杂质原子的浓度分布。
离子注入离子注入是一种直接将高能量离子注入到半导体晶体中的扩散技术。
在离子注入过程中,通过控制加速电压和注入剂量来控制离子的能量和浓度分布。
离子注入在制造MOSFET器件和深结构规模集成电路中广泛应用。
分子束外延分子束外延是一种高真空技术,通过热蒸发或分子束淀积将杂质原子沉积在半导体晶体表面。
通过控制杂质的分子束强度和沉积速度,可以实现对杂质浓度和分布的高精度调控。
分子束外延常用于制备薄膜和高性能器件。
扩散应用掺杂形成PN结在半导体器件中,通过控制杂质的扩散可以形成PN结,这是半导体器件中常见的结构。
PN结具有整流特性,在半导体器件中起到了关键作用。
控制扩散过程可以调整PN结的深度和浓度分布,从而优化器件的性能。
温度传感器扩散过程中的温度影响着扩散速度,因此扩散过程可以用于制造温度传感器。
通过测量扩散速度,可以间接得到环境的温度信息。
晶体管制造扩散过程在晶体管制造中也扮演着重要的角色。
通过控制杂质原子的扩散,可以形成晶体管的掺杂区域,从而实现对晶体管性能的调控。
半导体扩散区主要工艺

半导体扩散区主要工艺
半导体扩散区主要工艺是半导体制造过程中的重要环节之一。
扩散区是指在半导体晶体中,掺杂了掺杂剂的区域。
掺杂剂可以改变半导体的电学性质,从而使其具有导电或者绝缘的特性。
半导体扩散区主要工艺包括以下几个方面:
1. 掺杂:掺杂是指将掺杂剂引入半导体晶体中的过程。
掺杂剂可以是五价元素(如磷、砷)或三价元素(如硼、铝)。
掺杂的目的是改变半导体的电学性质,从而使其具有导电或者绝缘的特性。
2. 扩散:扩散是指将掺杂剂在半导体晶体中的扩散过程。
扩散可以通过高温处理或者化学反应来实现。
扩散的目的是使掺杂剂分布均匀,从而形成扩散区。
3. 掩膜:掩膜是指在半导体晶体表面涂覆一层光阻,然后通过光刻技术将需要形成扩散区的部分暴露出来。
掩膜的目的是保护未被暴露的部分,防止其被扩散。
4. 退火:退火是指在高温下对半导体晶体进行加热处理,以促进扩散过程。
退火可以使扩散区更加均匀,提高半导体器件的性能。
5. 清洗:清洗是指将半导体晶体表面的污染物清除干净。
清洗可以通过化学反应或者机械清洗来实现。
清洗的目的是保证半导体器件的质量和稳定性。
以上就是半导体扩散区主要工艺的介绍。
半导体扩散区的制备是半导体器件制造过程中至关重要的一步,对于半导体器件的性能和稳定性有着重要的影响。
在实际制备过程中,还需要根据具体情况进行调整和优化,以达到最佳效果。
半导体制造工艺基础之扩散工艺培训
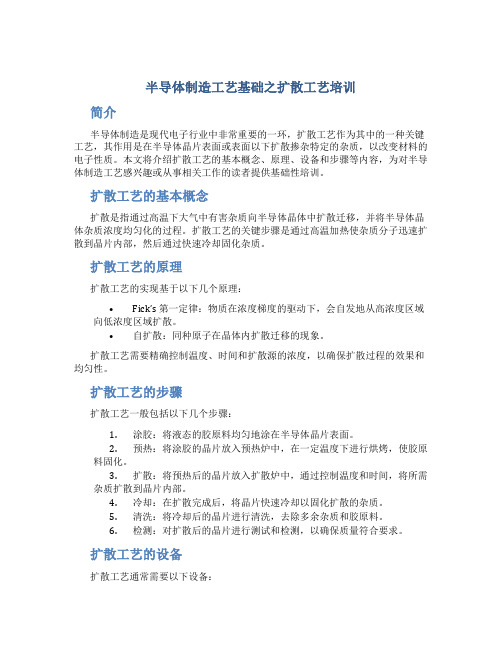
半导体制造工艺基础之扩散工艺培训简介半导体制造是现代电子行业中非常重要的一环,扩散工艺作为其中的一种关键工艺,其作用是在半导体晶片表面或表面以下扩散掺杂特定的杂质,以改变材料的电子性质。
本文将介绍扩散工艺的基本概念、原理、设备和步骤等内容,为对半导体制造工艺感兴趣或从事相关工作的读者提供基础性培训。
扩散工艺的基本概念扩散是指通过高温下大气中有害杂质向半导体晶体中扩散迁移,并将半导体晶体杂质浓度均匀化的过程。
扩散工艺的关键步骤是通过高温加热使杂质分子迅速扩散到晶片内部,然后通过快速冷却固化杂质。
扩散工艺的原理扩散工艺的实现基于以下几个原理:•Fick’s 第一定律:物质在浓度梯度的驱动下,会自发地从高浓度区域向低浓度区域扩散。
•自扩散:同种原子在晶体内扩散迁移的现象。
扩散工艺需要精确控制温度、时间和扩散源的浓度,以确保扩散过程的效果和均匀性。
扩散工艺的步骤扩散工艺一般包括以下几个步骤:1.涂胶:将液态的胶原料均匀地涂在半导体晶片表面。
2.预热:将涂胶的晶片放入预热炉中,在一定温度下进行烘烤,使胶原料固化。
3.扩散:将预热后的晶片放入扩散炉中,通过控制温度和时间,将所需杂质扩散到晶片内部。
4.冷却:在扩散完成后,将晶片快速冷却以固化扩散的杂质。
5.清洗:将冷却后的晶片进行清洗,去除多余杂质和胶原料。
6.检测:对扩散后的晶片进行测试和检测,以确保质量符合要求。
扩散工艺的设备扩散工艺通常需要以下设备:•扩散炉:用于控制温度和时间进行扩散过程。
•预热炉:用于将涂胶的晶片进行烘烤,以固化胶原料。
•清洗设备:用于清洗扩散后的晶片,去除多余的杂质。
•检测设备:对扩散后的晶片进行测试和检测,以确保质量符合要求。
扩散工艺的应用扩散工艺在半导体制造中有广泛的应用,主要用于掺杂制造PN结、MOS结构以及形成超浅和深层掺杂等。
常见的扩散工艺包括硼扩散、砷扩散、硅扩散等。
结束语扩散工艺是半导体制造过程中不可或缺的一环,它的实施对于半导体器件的性能和质量具有重要影响。
半导体制作工艺----掺杂解析
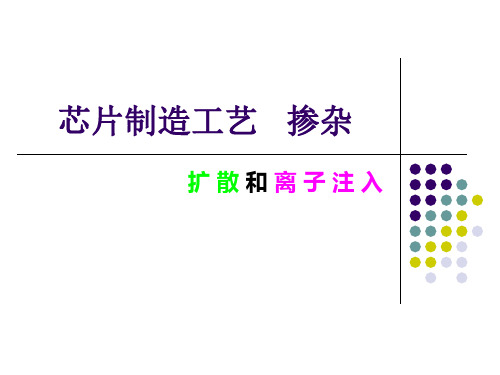
33
锡
50
锑
51
5.2 扩散
扩散是微电子工艺中最基本的工艺之一,是在约 1000℃的高温、p型或n型杂质气氛中,使杂质向衬 底硅片的确定区域内扩散,达到一定浓度,实现半 导体定域、定量掺杂的一种工艺方法,也称为热扩 散。
在集成电路发展初期是半导体器件生产的主要技术 之一。但随着离子注入的出现,扩散工艺在制备浅 结、低浓度掺杂和控制精度等方面的巨大劣势日益 突出,在制造技术中的使用已大大降低。
扩散机理
掺杂剂在半导体中的扩散可以看成是:
杂质原子在晶格中以空位或间隙原子形式进行 的原子运动。
杂质原子的扩散方式有以下几种:
①交换式:两相邻原子由于有足够高的能 量,互相交换位置③填隙式:在空隙中的原子挤开晶格原子 后占据其位,被挤出的原子再去挤出其他原 子。
间隙扩散杂质:O, Fe,Cu,Zn,Mg
B,P,一般作为替代式扩 散杂质,实际情况更复杂, 包含了硅自间隙原子的作 用,称填隙式或推填式扩 替位扩散杂质:散As, Al,Ga, Sb,Ge。 替位原子的运动一般是以近邻 处有空位为前提
5.2.3 扩散系数与扩散方程
1、 菲克第一定律
1855年,菲克(Fick),提出描述物质扩散的第一定律。 菲克第一定律:如果在一个有限的基体中杂质浓度C(x, t)存在梯 度分布,则杂质将会产生扩散运动,杂质的扩散流密度 J 正比 于杂质浓度梯度C/ x ,比例系数D定义为杂质在基体中的扩 散系数。
掺杂是指将需要的杂质原子掺入到特定的半导 体区域中,用于对衬底基片进行局部掺杂。以 达到改变半导体电学性质,形成PN结、电阻、 欧姆接触的目的。
扩散和离子注入
ⅢA族受主掺质(P型)
元素
原子量
精选半导体制造工艺07扩散上

二步扩散
第一步 为恒定表面浓度的扩散(Pre-deposition) (称为预沉积或预扩散) 控制掺入的杂质总量
第二步 为有限源的扩散(Drive-in),往往同时氧化 (称为主扩散或再分布) 控制扩散深度和表面浓度
因为
当 时,最后的杂质浓度分布为
余误差函数分布(erfc)
表面浓度恒定杂质总量增加扩散深度增加
关键参数 Cs(表面浓度) xj (结深) Rs(薄层电阻)
本节课主要内容
1、掺杂工艺一般分为哪两步?结深?薄层电阻?固溶度?
对于x>>1
1)掺杂总量为
A和Cs/CB有关D与温度T是指数关系,因此T对结深的影响要较t大许多
2)扩散结深为xj ,则
3)杂质浓度梯度
梯度受到Cs、t 和D(即T)的影响。改变其中的某个量,可以改变梯度,如增加Cs(As)。
在p-n结处
CB和Cs一定时,xj 越深,结处的梯度越小。
余误差函数分布
预淀积扩散
扩散时间越长,杂质扩散距离越深,进入衬底的杂质总量越多。恒定表面源的扩散,其表面杂质浓度Cs 基本由杂质在扩散温度(900-1200 C)下的固溶度决定,而固溶度随温度变化不大。
t1 t2 t3
t1<t2<t3
3、有限源扩散:杂质总量恒定为QT
2、两种特殊条件下的费克第二定律的解及其特点?特征扩散长度?
预淀积+退火。预淀积:气固相预淀积扩散或离子注入。Rs:表面为正方形的半导体薄层(结深),在电流方向所呈现的电阻。单位为 /。反映扩散入硅内部的净杂质总量。固溶度:在平衡条件下,杂质能溶解在硅中而不发生反应形成分凝相的最大浓度。
感谢您的下载观看
3、杂质固溶度(dopant solid solubility)
- 1、下载文档前请自行甄别文档内容的完整性,平台不提供额外的编辑、内容补充、找答案等附加服务。
- 2、"仅部分预览"的文档,不可在线预览部分如存在完整性等问题,可反馈申请退款(可完整预览的文档不适用该条件!)。
- 3、如文档侵犯您的权益,请联系客服反馈,我们会尽快为您处理(人工客服工作时间:9:00-18:30)。
扩散工艺前言:扩散部按车间划分主要由扩散区域及注入区域组成,其中扩散区域又分扩散老区和扩散新区。
扩散区域按工艺分,主要有热氧化、扩散、LPCVD、合金、清洗、沾污测试等六大工艺。
本文主要介绍热氧化、扩散及合金工艺。
目录第一章:扩散区域设备简介……………………………………第二章:氧化工艺第三章:扩散工艺第四章:合金工艺第一章:扩散部扩散区域工艺设备简介炉管设备外观:扩散区域的工艺、设备主要可以分为:类别主要包括按工艺分类热氧化一氧、二痒、场氧、Post氧化扩散推阱、退火/磷掺杂LPCVD TEOS、SI3N4、POL Y清洗进炉前清洗、漂洗合金合金按设备分类卧式炉A、B、C、D、F、H、I六台立式炉VTR-1、VTR-2、VTR-3 清洗机FSI-1、FSI-2炉管:负责高温作业,可分为以下几个部分:组成部分功能控制柜→对设备的运行进行统一控制;装舟台:→园片放置的区域,由控制柜控制运行炉体:→对园片进行高温作业的区域,由控制柜控制升降温源柜:→供应源、气的区域,由控制柜控制气体阀门的开关。
FSI:负责炉前清洗。
第二章:热氧化工艺热氧化法是在高温下(900℃-1200℃)使硅片表面形成二氧化硅膜的方法。
热氧化的目的是在硅片上制作出一定质量要求的二氧化硅膜,对硅片或器件起保护、钝化、绝缘、缓冲介质等作用。
硅片氧化前的清洗、热氧化的环境及过程是制备高质量二氧化硅膜的重要环节。
2. 1氧化层的作用2.1.1用于杂质选择扩散的掩蔽膜常用杂质(硼,磷,砷等)在氧化层中的扩散系数远小于在硅中的扩散系数,因此氧化层具有阻挡杂质向半导体中扩散的能力。
利用这一性质,在硅上的二氧化硅层上刻出选择扩散窗口,则在窗口区就可以向硅中扩散杂质,其它区域被二氧化硅屏蔽,没有杂质进入,实现对硅的选择性扩散。
1960年二氧化硅就已被用作晶体管选择扩散的掩蔽膜,从而导致了硅平面工艺的诞生,开创了半导体制造技术的新阶段。
同时二氧化硅也可在注入工艺中,作为选择注入的掩蔽膜。
作为掩蔽膜时,一定要保证足够厚的厚度,杂质在二氧化硅中的扩散或穿透深度必须要小于二氧化硅的厚度,并有一定的余量,以防止可能出现的工艺波动影响掩蔽效果。
2.1. 2缓冲介质层其一:硅与氮化硅的应力较大,因此在两层之间生长一层氧化层,以缓冲两者之间的应力,如二次氧化;其二:也可作为注入缓冲介质,以减少注入对器件表面的损伤。
2.1.3电容的介质材料电容的计算公式:C=ε0*εr *S/dε0:真空介质常数 εr :相对介电常数S :电容区面积 D :介质层厚度二氧化硅的相对介电常数为3-4。
二氧化硅的耐击穿能力强,温度系数小,是制作电容介质的常用材料。
在电容的制作过程中,电容的面积和光刻、腐蚀有较大的关系,而厚度则由二氧化硅的厚度决定。
2.1.4 集成电路的隔离介质P-Well SiO 2 Si 3N 4二氧化硅的隔离效果比PN结的隔离效果好,漏电流小,耐击穿能力强,隔离区和衬底之间的寄生电容小,不受外界偏压的影响,使器件有较高的开关速度。
如工艺中常用的场氧化就是生长较厚的二氧化硅膜,达到器件隔离的目的。
2.1.5 MOS场效应晶体管的绝缘栅材料二氧化硅的厚度和质量直接决定着MOS场效应晶体管的多个电参数,因此在栅氧化的工艺控制中,要求特别严格。
2.2 热氧化方法介绍2.2.1 干氧氧化干氧氧化化学反应式:Si+O2 == SiO2氧分子以扩散的方式通过氧化层到达二氧化硅-硅表面,与硅发生反应,生成一定厚度的二氧化硅层。
干氧化制作的SiO2结构致密,均匀性、重复性好,掩蔽能力强,对光刻胶的粘附性较好,但生长速率较慢;一般用于高质量的氧化,如栅氧等;厚层氧化时用作起始和终止氧化;薄层缓冲氧化也使用此法。
2.2.2 水汽氧化水汽氧化化学反应式:2H2O+Si == SiO2+2H2水汽氧化生长速率快,但结构疏松,掩蔽能力差,有较多缺陷。
对光刻胶的粘附性较差,我们公司不采用此方法。
2.2.3 湿氧氧化湿氧氧化反应气体中包括O2 和H2O ,实际上是两种氧化的结合使用。
湿氧氧化化学反应式:H2+O2==H2ON-WellSiO22H2O+Si == SiO2+2H2Si+O2 == SiO2湿氧氧化的生长速率介于干氧氧化和水汽氧化之间;在今天的工艺中H2O的形成通常是由H2和O2的反应得到;因此通过H2和O2的流量比例来调节O2和H2O的分压比例,从而调节氧化速率,但为了安全,H 2/O2比例不可超过1.88。
湿氧氧化的氧化层对杂质掩蔽能力以及均匀性均能满足工艺要求,并且氧化速率比干氧氧化有明显提高,因此在厚层氧化中得到了较为广泛的应用,如场氧化等。
2.2.4 掺氯氧化氧化气体中掺入HCL或DCE(C2H2Cl2)后,氧化速率及氧化层质量都有提高。
人们从两个方面来解释速率变化的原因,其一:掺氯氧化时反应产物有H2O,加速氧化;其二:氯积累在Si-SiO2界面附近,氯与硅反应生成氯硅化物,氯硅化物稳定性差,在有氧的情况下易转变成SiO2,因此,氯起了氧与硅反应的催化剂的作用。
并且氧化层的质量也大有改善,同时能消除钠离子的沾污,提高器件的电性能和可靠性。
热氧化过程中掺入氯会使氧化层中含有一定量的氯原子,从而可以减少钠离子沾污,钝化SiO2中钠离子的活性,抑制或消除热氧化缺陷,改善击穿特性,提高半导体器件的可靠性和稳定性。
我们公司大多数干氧氧化都含有掺氯氧化。
2. 3热氧化过程中的硅片表面位置的变化如果热生长的二氧化硅厚度是X0(um),所消耗的硅厚度为X1,则:a=X1/X=0.46即生长1um的SiO2,要消耗掉0.46um的Si。
但不同热氧化生长的SiO2的密度不同,a值会略有差异。
2.4 影响氧化速率的因素2.4.1 热氧化模型简介硅片的热氧化过程是氧化剂穿透二氧化硅层向二氧化硅和硅界面运动并与硅进行反应。
Deal-Grove方程具体描述了这种热氧化过程。
Deal-Grove膜厚方程式:X2+AX=B(t+ )式中:A=2D0*(1/KS+1/h)B=2D*N*/n=(XI 2+A*XI)/BD:氧化剂在二氧化硅中的有效扩散系数; h:气相输运常数KS:界面反应速率常数;N*:氧化剂在氧化层中的平衡浓度XI:初始氧化层厚度; n:形成单位体积二氧化硅所需的氧分子数极限情况1:短时间氧化时X=(B/A)*t B/A:线性氧化速率常数极限情况2:长时间氧化时X2=Bt B:抛物线速率常数这两个速率常数都与工艺方法、氧化温度、氧化剂的分压、晶向有关系。
2.4.2 氧化温度的影响温度越高,氧化速率越快。
2.4.4 硅片晶向的影响线性速率常数与晶向有较大的关系,各种晶向的园片其氧化速率为:(110)>POLY>(111)>(100)2.4.5 掺杂杂质浓度的影响当掺杂杂质的浓度相当高时,会产生增强氧化,使氧化速率发生较大变化。
如 LVMG 产品N+退火氧化:在未掺杂区的氧化厚度:670A在N+掺杂区氧化厚度:1700A2.4.6 氯化物的影响2.4.7 氧化剂分压的影响在前面介绍的湿氧氧化中,如果改变H2或O2的流量,就会使水汽和氧气的分压比降低,使氧化速率变化。
2.4 CSMC-HJ扩散课的工艺状况2.4.1 氧化质量控制2.4.1.1 拉恒温区控制温度定期拉恒温区以得到好的温度控制2.4.1.2 DCE(C2H2Cl2)吹扫炉管2.4.1.3 BT 测量BT项目可以检测到可动离子数目,使我们及时掌握炉管的沾污情况,防止炉管受到可动电荷粘污,使大批园片受损。
2.4.1.4 片内均匀性保证硅片中每个芯片的重复性良好2.4.1.5 片间均匀性保证每个硅片的重复性良好2.4.1.6定期清洗炉管清洗炉管,可以减少重金属离子、碱金属离子的沾污同时也能减少颗粒,保证氧化层质量。
2.4.1.7 定期检测系统颗粒2.5.常见问题及处理I 膜厚异常,但均匀性良好对策:首先,检查测量结果是否准确、仪器工作状态是否正常,然后1 检查气体流量、工艺温度是否正常;2 检查炉管的气体接口是否正常;3 如使用控制片,检查控制片是否用对;4 和动力部门确认,工艺时气体供应有无出现异常;5 对于外点火的炉管,请检查点火装置的各处连接正常,然后进行TORCH点火实验。
Ⅱ部分园片或部分测试点膜厚正常,但整体均匀性差对策:1 如使用控制片,检查控制片;2 检查排风正常3检查炉门正常第三章扩散工艺扩散技术目的在于控制半导体中特定区域内杂质的类型、浓度、深度和PN结。
在集成电路发展初期是半导体器件生产的主要技术之一。
但随着离子注入的出现,扩散工艺在制备浅结、低浓度掺杂和控制精度等方面的巨大劣势日益突出,在制造技术中的使用已大大降低。
3.1 扩散机构3.1.1 替位式扩散机构这种杂质原子或离子大小与Si原子大小差别不大,它沿着硅晶体内晶格空位跳跃前进扩散,杂质原子扩散时占据晶格格点的正常位置,不改变原来硅材料的晶体结构。
硼、磷、砷等是此种方式。
3.1.2 填隙式扩散机构这种杂质原子大小与Si原子大小差别较大,杂质原子进入硅晶体后,不占据晶格格点的正常位置,而是从一个硅原子间隙到另一个硅原子间隙逐次跳跃前进。
镍、铁等重金属元素等是此种方式。
3.2 扩散方程∂N / ∂t = D*2N / ∂x2N=N(x,t)杂质的浓度分布函数,单位是cm-3D:扩散系数,单位是cm2/s加入边界条件和初始条件,对上述方程进行求解,结果如下面两小节所诉。
3.2.1 恒定表面浓度扩散保持不变整个扩散过程中,硅片表面浓度NSerfc(x/(2*(Dt)1/2))N(x,t)=NS式中erfc称作余误差函数,因此恒定表面浓度扩散分布符合余误差分布。
3.2.2.限定源扩散杂质源限定在硅片表面薄的一层,杂质总量Q是常数。
N(x,t)=(Q/(πDt)1/2)*exp(-X2/4Dt)exp(-X2/4Dt)是高斯函数,因此限定源扩散时的杂质分布是高斯函数分布。
由以上的求解公式,可以看出扩散系数D以及表面浓度对恒定表面扩散的影响相当大3.2.3 扩散系数扩散系数是描述杂质在硅中扩散快慢的一个参数,用字母D表示。
D大,扩散速率快。
D与扩散、扩散气氛、衬底晶向、缺陷等因素有关。
温度T、杂质浓度N、衬底浓度NBexp(-E/kT)D=DT:绝对温度;K:波尔兹曼常数;E:扩散激活能:频率因子D3.2.4 杂质在硅中的固溶度杂质扩散进入硅中后,与硅形成固溶体。
在一定的温度下,杂质在硅中有一个最大的溶解度,其对应的杂质浓度,称该温度下杂质在硅中的固溶度。
固溶度在一定程度上决定了硅片的表面浓度。
3.3 CSMC-HJ扩散课的扩散工艺状况扩散工艺按照作用可以分为推阱、退火、磷掺杂,不同工艺的作业炉管在配置上稍有不同。