钣金折弯成型最小折边
钣金最小折弯高度

钣金最小折弯高度1. 引言钣金加工是一种常见的金属材料加工方式,通过对金属板材进行切割、冲孔、折弯等工艺,将其加工成所需的形状和尺寸。
在钣金加工中,折弯是一项重要的工艺操作,它可以使平面的金属板材变成具有三维形状的构件。
钣金折弯过程中,折弯高度是一个关键参数。
合理设置折弯高度可以保证零件的尺寸精度和形状质量,同时还可以避免因过大或过小的折弯高度导致零件变形、开裂等问题。
因此,确定钣金最小折弯高度对于保证加工质量和提高生产效率具有重要意义。
本文将从以下几个方面对钣金最小折弯高度进行详细讨论:1.折弯过程及影响因素2.确定最小折弯高度的方法3.最小折弯高度对零件质量的影响4.如何优化最小折弯高度2. 折弯过程及影响因素在钣金加工中,折弯是通过将金属板材放置在折弯模具上,并施加力量使其发生弯曲变形的过程。
折弯过程中,受力部位会发生拉伸和压缩,而非受力部位则会发生弹性回复。
折弯高度是指在折弯过程中,板材在模具上的最大变形高度。
它受到以下几个因素的影响:2.1 板材性质不同材料的板材具有不同的力学性能和变形特点。
例如,软质金属如铝合金通常具有较好的可塑性,可以实现较小的最小折弯高度;而硬质金属如不锈钢则较难实现较小的最小折弯高度。
2.2 板厚板厚是影响最小折弯高度的重要因素之一。
一般来说,板厚越薄,其可塑性越好,能够实现较小的最小折弯高度。
2.3 模具几何参数模具几何参数包括模具角度、半径等。
合理设置模具几何参数可以使得板材在折弯过程中分布均匀的应力,从而实现较小的最小折弯高度。
2.4 折弯工艺参数折弯工艺参数包括折弯力、折弯速度等。
合理设置折弯工艺参数可以使得板材在折弯过程中受到适当的力量和速度作用,从而实现较小的最小折弯高度。
3. 确定最小折弯高度的方法确定最小折弯高度是为了保证零件的尺寸精度和形状质量。
常用的方法包括经验法、试验法和数值模拟法。
3.1 经验法经验法是根据经验总结得出的一种确定最小折弯高度的方法。
钣金设计一定要考虑这些折弯问题

钣金设计一定要考虑这些折弯问题设计需要考虑,究竟哪些是成型前加工,究竟哪些是成型后加工。
考虑工作制作工艺过程中,必须先折弯,后加工部分孔的情况有:距离折弯边很近的圆孔,方孔,腰圆孔,螺纹等,下料时都需要做处理,如果直接按展开下料,在后续的加工中就没法完成,腰圆在折弯时会拉孔,螺纹孔用常用丝锥无法攻丝。
设计需要考虑,哪些是可以钣金成型的,哪些是不可钣金成型的。
要考虑最小折弯高度:(如下图)要考虑最小折弯半径:最小折弯钣金取决于钣金材料的折弯半径,下表中是常用钣金材料的最小折弯半径。
要考虑能不能直接使用机床定位,如果不能就预留两个小方块留做定位用,折弯后去除。
考虑钣金折弯方向问题:特别是有色金属,比如铝板,还有铜板折弯。
要看材料轧制的纹理方向,要垂直于纹理方向折弯,不要平行于轧制纹理方向,那样很容易有折弯裂缝。
要预留折弯避让间隙:钣金折弯包边钣金件时,两个折弯面有包边与被包边的关系。
要在做展开图时,画出折弯避让间隙。
因为折弯到90度时,钣金有折弯回弹,为了避免回弹后不到90度,就需要折弯大于90度,以抵消回弹。
所以,要预留间隙做折弯回弹避位用。
钣金多重折弯累计误差问题:钣金折弯精度不是很高,一般控制在0.2毫米之内。
折弯高度越大,折弯精度越低。
在折弯面有安装孔,螺纹孔,压铆螺钉,压铆螺母时,要充分考虑累计加工误差。
采用安装过孔增大或安装孔设计为腰型孔等,避免安装误差。
方便后续安装。
要考虑钣金压铆螺钉或压铆螺母,孔距离折弯边太小的问题:折弯时,有弯曲变形和拉伸变形同时存在。
有孔、缺口离折弯边过小,会造成孔、缺口拉伸变形。
一般离开折弯边为4.5倍材料厚度时,就不会有折弯变形问题。
以上就是钣金设计需要考虑钣金折弯的问题,钣金设计需要充分考虑折弯工艺,了解折弯工艺,设计是为了能够加工成产品。
不能忽略钣金折弯工艺的限制。
钣金折弯边距标准

一、折弯件上的孔边距
二、材料弯曲时,其圆角区上,外层收到拉伸,内层则受到压缩。
当材料厚度一定时,内r越小,材
料的拉伸和压缩就越严重;当外层圆角的拉伸应力超过材料的极限强度时,就会产生裂缝和折断,因此,弯曲零件的结构设计,应避免过小的弯曲圆角半径。
公司常用材料的最小弯曲半径见下表。
弯曲半径是指弯曲件的内侧半径,t是材料的壁厚。
t为材料壁厚,M为退火状态,Y为硬状态,Y2为1/2硬状态。
常用金属材料最小折弯半径列表
小,材
产生裂缝和折断,弯曲半径见下表。
钣金折弯常见成形方式与折弯步骤规范( 参考)

钣金折弯常见成形方式与折弯步骤规范1.折弯机《板材折弯压力表》意义说明:S:为加工板材厚度,一般设计指订,不允许更改(一般我们通常用“t”表示板厚);V:下模槽宽度(开口最大尺寸),一般根据板材厚度S和最小折弯宽度b决定选择,保证常规折弯成形成功必须是b>V/2;模具的槽口V尺寸的选择依据折弯工件的材质、板厚以及成形角度来确定。
b:最小折弯宽度,图表中所给数据是指该板材板厚情况下,采用图示折弯可以成功成型的最小宽度。
一般设计时应大于此数值。
r:图表中的r值是指折弯内圆角,是板材折弯部位弹性变形失效的最大曲率半径。
折弯刀的刃圆角一般不大于此值。
如果此r过大,折弯将无法折弯到位,且有涨裂下模的危险;r过小会在折弯角内圆上压出凹坑(质软的板材更明显),在折弯角外圆上出现拉裂(在拉伸变形率小的板材上更容易出现)。
实际折弯使用中,对于折弯刀来讲,其刃圆角r一般是固定的,其值应不大于图表中的数值。
2.折弯定位(靠位)工件在折弯机上折弯时,将以工件外形定位,在折弯机上的靠位一般有三种靠位定位方式:1)后靠位,即靠位在折弯刀后方,操作者与靠位在折弯刀两侧,一般数控折弯机采用较多,属主定位。
2)前靠位,即靠位在折弯刀前方,操作者与靠位在折弯刀同侧,一般普通折弯机或大深度工件采用较多,属主定位。
3)侧靠位,即靠位在工件的左或右方,主要目的是精确定折弯刀与工件的左右下刀位置或更好的保证有垂直(或精角度)要求的工件,属辅助定位(非必要定位)。
4)不管是前靠位还是后靠位,一般都应设计成可后拉或前退的结构方式,因为工件在折弯成形过程中是上翘变化的。
死靠位可能会造成工件变形。
在设计上一般采用翻转定位方式来满足后拉前退要求(数控折弯机可能有后拉这个动作,但普通折弯机本身没有这个功能,在设计靠位时应考虑此动作)。
5)靠位一般应设置两个,两个靠位间距应尽量大,同时应考虑方便工件定位的地方,并以折弯机压力中心(折弯刀、工件也应以折弯机压力中心作为布置参考)成对称布置。
钣金折弯成型最小折边[优质参考]
![钣金折弯成型最小折边[优质参考]](https://img.taocdn.com/s3/m/a3ab315f7e21af45b207a826.png)
成型最小折边一、L折。
1.决定最小L折的因素。
V槽中间距离为悬空段,成型时,折边必须超过此悬空段,具体搭边尺寸各公司有小小区别,(下V槽因使用时间长,R角变大,搭边距离将会随之变大,否则会“滑位”)。
2.换算公式(经验式):6*T/2+0.5+(1.8*T/2)3.如下图,T=1,K=1.8*1, 最小L折:3+0.5+0.9=4.4特注:⑴因每个公司的下V槽并一定都齐全,故需要灵活使用公式。
⑵特别情况下,需用更小V槽时,原则上相对V槽减小不能超过2.0MM.⑶附表。
说明:尽量采用黑粗线最小折边尺寸。
一、U折。
1.U折的种类A. 常规折弯刀成型。
B. 垫片反折压平。
(先折至30°,中间放一块合适垫板后压平。
)2.决定最小U折的因素。
A .上模具的形状。
(如下图)从常规刀具来看,小U折最佳刀具为“弯刀”。
(弯刀有很多种型号,具体要依公司现有尺寸)C. 折边尺寸。
(见下小图)两尺寸的梯增关系:A愈长则B愈长。
3.换算公式:(大弯刀经验型)◆0.5MM板:最小U折A尺寸=7.67。
B尺寸=0.5板最小L折3.0。
梯增值:A尺寸每梯增1MM,B尺寸对应梯增1.87,公式:已知A尺寸,求B尺寸=(A-7.67)/T*梯增值+该板厚最小L折如:A=15时,B=(15-7.67)/0.5*1.87+ 3.0=30.4已知B尺寸,求A尺寸=(B-该板厚最小L折)/梯增值*T+7.67. 如:B=30.4时,A=(30.4-3)/1.87*0.5+7. 67=15◆0.8MM板最小U折A尺寸=8.5,B尺寸=0.8最小L折4.2。
梯增值:1.87/0.5*0.8=2.99◆ 1.0MM板最小U折A尺寸=8.94,B尺寸=1.0最小L折4.5梯增值:1.87/0.5*1.0=3.7◆ 1.2MM板最小U折A尺寸=9.3,B尺寸=1.2最小L折4.5梯增值:1.87/0.5*1.2=4.5◆ 1.5MM板最小U折A尺寸=10.3,B尺寸=1.5最小L折6.2梯增值:1.87/0.5*1.5=5.5◆ 2.0MM板最小U折A尺寸=12.7,B尺寸=2.0最小L折12.0梯增值:1.87/0.5*2=7.4特注:1. A尺寸超过85.0MM及B尺寸超过60.0MM的不按此公式计算。
钣金最小折弯半径

钣金最小折弯半径
1 钣金折弯最小半径
钣金折弯是在金属制品加工过程中必不可少的一步操作,其最小折弯半径也是衡量一个好的钣金产品的重要指标。
钣金折弯最小半径受到多种因素影响,尤其是金属材料质量、折弯工艺两个因素。
首先,金属材料的质量对最小折弯半径起着至关重要的作用。
折弯机械加工的塑性变形能力与金属的硬度密切相关,而金属的硬度又受到温度和退火处理程度的影响,所以好的金属材料能够保证机械加工塑性变形,折弯最小半径才能达到客户要求。
其次,折弯工艺也影响着钣金折弯最小半径。
折弯工艺的优劣不但决定着折弯几何精度,而且也影响最小折弯半径的大小。
对于边角材来说,折弯工艺的优劣会直接影响最小折弯半径,折弯工艺有不同的方法,采用折弯机、热弯、冷弯的不同方式,可以实现不同的最小折弯半径。
此外,还需要注意金属材料的厚度、宽度、机械性质等因素,可以帮助折弯工艺工程师准确掌握钣金折弯最小半径。
2 总结
在金属制品加工中,折弯是不可或缺的操作,钣金折弯最小半径是衡量一个好的钣金产品的重要指标。
最小折弯半径完全受到金属材
料质量以及折弯工艺的影响,正确掌握好金属材料和折弯工艺,可以实现折弯最小半径的要求。
02. 板材一次折弯的最小折弯边的计算
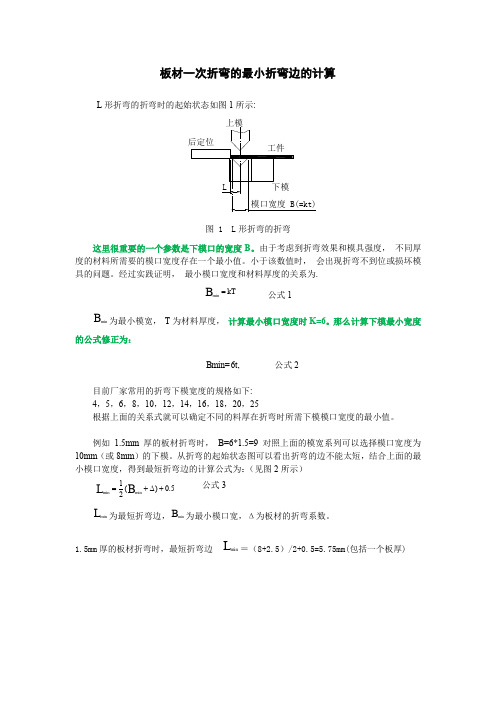
板材一次折弯的最小折弯边的计算
L
不同厚度的材料所需要的模口宽度存在一个最小值。
小于该数值时, 会出现折弯不到位或损坏模具的问题。
经过实践证明, 最小模口宽度和材料厚度的关系为.
kT
B
=min
公式1
B
min
为最小模宽, T 为材料厚度, 计算最小模口宽度时K=6。
那么计算下模最小宽度
的公式修正为:
Bmin=6t, 公式2
目前厂家常用的折弯下模宽度的规格如下: 4,5,6,8,10,12,14,16,18,20,25
根据上面的关系式就可以确定不同的料厚在折弯时所需下模模口宽度的最小值。
例如 1.5mm 厚的板材折弯时, B=6*1.5=9 对照上面的模宽系列可以选择模口宽度为10mm (或8mm )的下模。
从折弯的起始状态图可以看出折弯的边不能太短,结合上面的最小模口宽度,得到最短折弯边的计算公式为:(见图2所示)
5.0)(21
min
min
+∆+=
B L 公式3 L
min
为最短折弯边,B min 为最小模口宽,Δ为板材的折弯系数。
1.5mm 厚的板材折弯时,最短折弯边 L min =(8+
2.5)/2+0.5=5.75mm(包括一个板厚)
注:1、最小折弯高度包含一个料厚。
2、当V形折弯是折弯锐角时,最短折弯边需加大0.5。
3、当零件材料为铝板和不锈钢板时,最小折弯高度会有较小的变化,铝板会变小一点,不锈钢会大一点,参考上表即可。
钣金u型折弯最小尺寸

钣金u型折弯最小尺寸
钣金u型折弯最小尺寸是指在进行u型折弯加工时,最小可以折出的内径尺寸。
在钣金加工中,u型折弯是一种常用的加工方式,通过将钣金经过弯曲加工,可以制作出各种形状的零部件,具有广泛的应用领域。
但是在进行u型折弯时,需要注意最小尺寸,以避免出现弯曲过度或者折裂等问题。
一般来说,钣金u型折弯最小尺寸取决于材料的厚度、硬度、弯曲半径等因素,需要根据具体情况进行计算和调整。
在实际加工中,可以采用数控折弯机等设备进行精确的加工,以确保制作出的零部件符合要求的尺寸和质量标准。
- 1 -。
钣金最窄折边计算
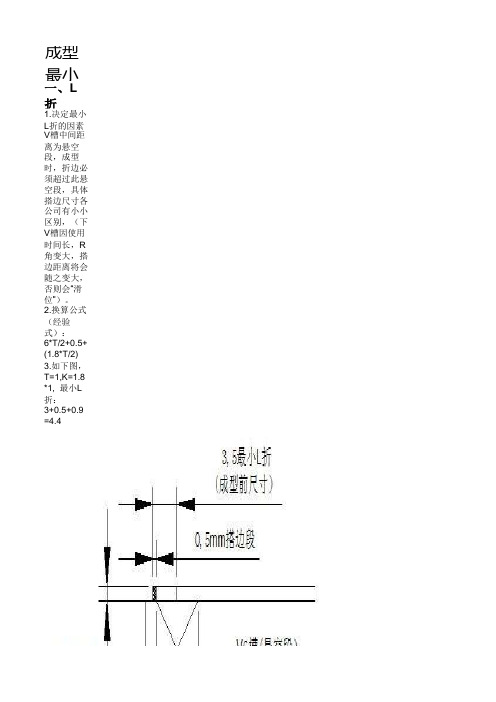
成型最小折边一、L 折1.决定最小L 折的因素。
V 槽中间距离为悬空段,成型时,折边必须超过此悬空段,具体搭边尺寸各公司有小小区别,(下V 槽因使用时间长,R2.换算公式(经验式):6*T/2+0.5+(1.8*T/2)3.如下图,T=1,K=1.8*1, 最小L 折:3+0.5+0.9=4.4特注:⑴ 因每个公司的下V 槽并一定都齐全,故需要灵活使用公式。
⑵ 特别情况下,需用更小V 槽时,原则上相对V 槽减小不能超过2.0MM.⑶ 附表。
说明:尽量采用黑粗线最小折边尺寸。
V 槽板厚0.52.530.83.2 3.74.213.544.555.51.23.544.555.51.54.85.2 5.86.2 6.827.5341516519202224262830板厚:6mm 最小折边:23.9mm二、U 折1.U 折的种类A. 常规折弯刀成型。
B. 垫片反折压平。
(先折至30°,中间放一块合适垫板后压平。
)2.决定最小U 折的因素。
A. 上模具的形状。
(如下图)从常规刀具来看,小U 折最佳刀具为“弯刀”。
(弯刀有很多种型号,具体要依公司现有尺寸)B. 折边尺寸。
(见下小图)两尺寸的梯增关系:A 愈长则B 愈长。
9108345673.换算公式:(大弯刀经验型)◆ 0.5MM板:最小U折A尺寸=7.67。
B尺寸=0.5板最小L折3.0。
梯增值:A尺寸每梯增1MM,B尺寸对应梯增1.87,公式:已知A尺寸,求B尺寸=(A-7.67)/T*梯增值+该板厚最小L折如:A=15时,B=(15-7.67)/0.5*1.87+3.0=30.4已知B尺寸,求A尺寸=(B-该板厚最小L折)/梯增值*T+7.67. 如:B=30.4时,A=(30.4-3)/1.87*0.5+7.67=15◆ 0.8MM板最小U折A尺寸=8.5,B尺寸=0.8最小L折4.2。
梯增值:1.87/0.5*0.8=2.99◆ 1.0MM板最小U折A尺寸=8.94,B尺寸=1.0最小L折4.5梯增值:1.87/0.5*1.0=3.7◆ 1.2MM板最小U折A尺寸=9.3,B尺寸=1.2最小L折4.5梯增值:1.87/0.5*1.2=4.5◆ 1.5MM板最小U折A尺寸=10.3,B尺寸=1.5最小L折6.2梯增值:1.87/0.5*1.5=5.5◆ 2.0MM板最小U折A尺寸=12.7,B尺寸=2.0最小L折12.0梯增值:1.87/0.5*2=7.4特注:1. A尺寸超过85.0MM及B尺寸超过60.0MM的不按此公式计算。
最小折弯边与板厚的表格
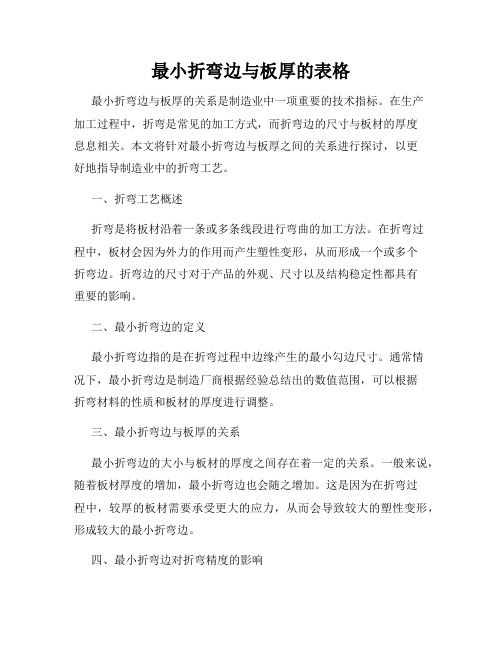
最小折弯边与板厚的表格最小折弯边与板厚的关系是制造业中一项重要的技术指标。
在生产加工过程中,折弯是常见的加工方式,而折弯边的尺寸与板材的厚度息息相关。
本文将针对最小折弯边与板厚之间的关系进行探讨,以更好地指导制造业中的折弯工艺。
一、折弯工艺概述折弯是将板材沿着一条或多条线段进行弯曲的加工方法。
在折弯过程中,板材会因为外力的作用而产生塑性变形,从而形成一个或多个折弯边。
折弯边的尺寸对于产品的外观、尺寸以及结构稳定性都具有重要的影响。
二、最小折弯边的定义最小折弯边指的是在折弯过程中边缘产生的最小勾边尺寸。
通常情况下,最小折弯边是制造厂商根据经验总结出的数值范围,可以根据折弯材料的性质和板材的厚度进行调整。
三、最小折弯边与板厚的关系最小折弯边的大小与板材的厚度之间存在着一定的关系。
一般来说,随着板材厚度的增加,最小折弯边也会随之增加。
这是因为在折弯过程中,较厚的板材需要承受更大的应力,从而会导致较大的塑性变形,形成较大的最小折弯边。
四、最小折弯边对折弯精度的影响最小折弯边的大小直接影响着折弯工艺的精度。
当最小折弯边过大时,可能导致产品的尺寸偏差增加,外观质量下降,甚至无法满足设计要求。
因此,在实际生产中,需要根据具体的产品要求和板材厚度来确定合理的最小折弯边。
五、如何控制最小折弯边1. 板材选择:选择合适的板材厚度可以在一定程度上控制最小折弯边的大小。
较薄的板材更容易产生较小的最小折弯边,而较厚的板材则可能产生较大的最小折弯边。
2. 折弯工艺参数:在折弯加工中,合理的工艺参数设定也是控制最小折弯边的关键。
包括折弯角度、折弯力度、模具的选择等。
3. 模具设计:合理设计模具的形状和尺寸,可以有效地控制最小折弯边的大小。
通过模具的正确配合,可以减小折弯过程中的应力集中,降低最小折弯边的尺寸。
六、最小折弯边的应用领域最小折弯边的概念常见于金属加工行业,尤其是钣金加工和机械制造领域。
在这些领域中,制造商需要根据产品的要求和板材的特性来选择合适的最小折弯边,以确保产品的外观和质量。
折弯边最小尺寸算法

钣金结构件可加工性设计规范一.冲裁冲裁有两种方法:数控冲床冲裁和模具冲裁,数控冲床冲裁:单量不大,精度一般为±0.1,与加工的尺寸大小没有太大的关系。
模具冲裁:公差尺寸采用GB/T1804-m。
冲裁件的工艺性要求:A:冲裁件的外形及内孔应避免尖角。
R>=0.5t。
B:冲裁件尽量避免过长的悬臂和狭槽,悬臂和狭槽的宽度不宜过小。
对合金钢或不锈钢A≥2t对一般钢A≥1.5t对黄铜、铝A≥1.2t(A为宽度)C:冲孔优先选用圆孔,冲孔时,孔径不宜过小。
二.折弯1.在折弯有撕裂的地方,需要留撕裂槽。
撕裂槽的宽度一般不小于1.5t,且≥1.5,撕裂槽的长度和宽度与壁厚的关系如下图b,c所示。
或者是折弯线让开阶梯线如下图a所示。
2.折弯件的直边高度不宜过小,否则不易形成足够的弯矩,很难得到形状准确的零件。
其弯曲值h≥R+2t,且h≥3方可。
如果设计需要,应加大弯边高度,弯好后再加工到需要尺寸,或者在弯曲变形区内加工浅槽后,再拆弯。
3.折弯件的孔边距离:先冲孔后折弯的零件,当t<2mm时,L≥t;当t≥2mm时,L≥2t。
先折弯再冲孔的零件,L≥0.5t。
4.压死边最小长度L≥R +3.5t,R为压死边前道工序的最小内折弯半径,一般为0.65.折弯件不得对多个折弯边同时要求较严的尺寸公差。
6.在U形弯曲件上,两弯曲边最好等长,以免弯曲时产生向一边移位。
如不允许,可设一工艺定位孔,如下图7.为了防止零件弯曲后,直角的两侧平面产生褶皱,应设计预留切口,如下图8.为了防止冲孔后再弯曲的零件,在孔边产生裂纹,建议增加切口9.防止弯曲时,一边向内产生收缩。
可设计工艺定位孔,或两边同时折弯,还可用增加幅宽的办法来解决收缩问题。
10. 弯曲的零件,在弯曲区压制加强筋,不仅可以提高工件的刚度,也有利于抑制回弹。
常用筋的结构尺寸推荐如下三.拉伸拉深件的尺寸精度不宜要求过高,形状应尽量简单、对称。
1. 防止拉深时产生扭曲变形,A、B宽度应相等(对称)即A=B2. 拉深件的圆角半径要合适,圆角半径尽量取大些,以利于成型和减少拉深次数3. 翻孔攻丝四.铆接涨铆螺母,压铆螺母,拉铆,翻孔攻丝的比较AutoCAD的快捷方式:ADCENTER:管理内容ADC ALIGN:在二维和三维空间中将某对象与其他对象对齐AL APPL OAD:加载或卸载应用程序并指定启动时要加载的应用程序AP ARC:创建圆弧A AREA:计算对象或指定区域的面积和周长AA ARRAY:创建按指定方式排列的多重对象副本AR ATTD EF:创建属性定义ATT ATTEDIT:改变属性信息ATE ATTEXT:提取属性数据DDATTEXT B BHATCH:使用图案填充封闭区域或选定对象H、BH BLOCK:根据选定对象创建块定义BBOUNDARY:从封闭区域创建面域或多段线BO BREAK:部分删除对象或把对象分解为两部分BR C CHAMFER:给对象的边加倒角CHA CHANGE:修改现有对象的特性-CH CIRCL E:创建圆形C COLOR:定义新对象的颜色COL COPY:复制对象CO、CP D DBCONN ECT:为外部数据库表提供AutoCAD 接口AAD、AEX、ALI、ASQ、ARO、ASE、DBC DDEDIT:编辑文字和属性定义ED DDVPOINT:设置三维观察方向VP DIMALIGNED:创建对齐线性标注DAL DIMANGULAR:创建角度标注DAN DIMBASELINE:从上一个或选定标注的基线处创建线性、角度或坐标标注DBA DIMCENTER:创建圆和圆弧的圆心标记或中心线DCE DIMC ONTINUE:从上一个或选定标注的第二尺寸界线处创建线性、角度或坐标标注DCO DIMDIAMETE R:创建圆和圆弧的直径标注DDI DIMEDIT:编辑标注DED DIMLINEAR:创建线性尺寸标注DLI DIMORDINATE:创建坐标点标注DOR DIMOVERRIDE:替代标注系统变量DOV D IMRADIUS:创建圆和圆弧的半径标注DRA DIMSTYLE:创建或修改标注样式D DIMTEDIT:移动和旋转标注文字DIMTED DIST:测量两点之间的距离和角度DI DIVIDE:将点对象或块沿对象的长度或周长等间隔排列DIV DONUT:绘制填充的圆和环DO DRAWORDER:修改图像和其他对象的显示顺序DR DSETTINGS:指定捕捉模式、栅格、极坐标和对象捕捉追踪的设置DS、RM、SE DSVIEWER:打开“鸟瞰视图”窗口AV DVIEW:定义平行投影或透视视图DV E ELLIPSE:创建椭圆或椭圆弧EL ERASE:从图形中删除对象E EXPLODE:将组合对象分解为对象组件X EXPORT:以其他文件格式保存对象EXP EXTEND:延伸对象到另一对象EX EXTRUDE:通过拉伸现有二维对象来创建三维原型EXT F FILLET:给对象的边加圆角 F F ILTER:创建可重复使用的过滤器以便根据特性选择对象FI G GROUP:创建对象的命名选择集G H HATCH:用图案填充一块指定边界的区域-H HATCHEDIT:修改现有的图案填充对象HEHIDE:重生成三维模型时不显示隐藏线HI I IMAGE:管理图像IM IMAGEADJUST:控制选定图像的亮度、对比度和褪色度IAD IMAGEATTACH:向当前图形中附着新的图像对象IAT IMAGECLIP:为图像对象创建新剪裁边界ICL IMPORT:向AutoCAD 输入文件IMP INS ERT:将命名块或图形插入到当前图形中I INTERFERE:用两个或多个三维实体的公用部分创建三维复合实体INF INTERSECT:用两个或多个实体或面域的交集创建复合实体或面域并删除交集以外的部分IN INSERTOBJ:插入链接或嵌入对象IO L LAYER:管理图层和图层特性LA -LA YOUT:创建新布局,重命名、复制、保存或删除现有布局LO LEADER:创建一条引线将注释与一个几何特征相连LEAD LENGTHEN:拉长对象LEN LINE:创建直线段L LINETYPE:创建、加载和设置线型LT LIST:显示选定对象的数据库信息LI、LS LTSCALE:设置线型比例因子LTS LWEIGHT:LW M MATCHPROP:设置当前线宽、线宽显示选项和线宽单位MA MEASURE:将点对象或块按指定的间距放置ME MIRROR:创建对象的镜像副本MI MLI NE:创建多重平行线ML MOVE:在指定方向上按指定距离移动对象M MSPACE:从图纸空间切换到模型空间视口MS MTEXT:创建多行文字T、MT MVIEW:创建浮动视口和打开现有的浮动视口MV O OFFSET:创建同心圆、平行线和平行曲线O OPTIONS:自定义AutoCAD 设置GR、OP、PR OSNAP:设置对象捕捉模式OS P PAN:移动当前视口中显示的图形P PASTESPEC:插入剪贴板数据并控制数据格式PA PEDIT:编辑多段线和三维多边形网格PE PLINE:创建二维多段线PL PRINT :将图形打印到打印设备或文件PLOT POINT:创建点对象PO POLYGON:创建闭合的等边多段线POL PREVIEW:显示打印图形的效果PRE PROPERTIES:控制现有对象的特性CH、MO PROPERTIESCLOSE:关闭“特性”窗口PRCLOSE PSPACE:从模型空间视口切换到图纸空间PS PURGE:删除图形数据库中没有使用的命名对象,例如块或图层PU Q QLEADER:快速创建引线和引线注释LE QUIT:退出AutoCAD EXIT R RECTANG:绘制矩形多段线REC REDRAW:刷新显示当前视口R REDRAWALL:刷新显示所有视口RA REGEN:重生成图形并刷新显示当前视口RE REGENALL:重新生成图形并刷新所有视口REA REGION:从现有对象的选择集中创建面域对象REG RENAME:修改对象名REN RENDER:创建三维线框或实体模型的具有真实感的渲染图像RR REVOLVE:绕轴旋转二维对象以创建实体REV RPREF:设置渲染系统配置RPR ROTATE:绕基点移动对象RO S SCALE:在X、Y 和Z 方向等比例放大或缩小对象SC SCRIPT:用脚本文件执行一系列命令SCR SECTION:用剖切平面和实体截交创建面域SEC SETVAR:列出系统变量并修改变量值SET SLICE:用平面剖切一组实体SL SNAP:规定光标按指定的间距移动SN SOLID:创建二维填充多边形SO SPELL:检查图形中文字的拼写SP SPLINE:创建二次或三次(NURB S) 样条曲线SPL SPLINEDIT:编辑样条曲线对象SPE STRETCH:移动或拉伸对象S ST YLE:创建或修改已命名的文字样式以及设置图形中文字的当前样式ST SUBTRACT:用差集创建组合面域或实体SU T TABLET:校准、配置、打开和关闭已安装的数字化仪TA THICKNESS:设置当前三维实体的厚度TH TILEMODE:使“模型”选项卡或最后一个布局选项卡当前化TI、TM TOLERANCE:创建形位公差标注TOL TOOLBAR:显示、隐藏和自定义工具栏TO TOR US:创建圆环形实体TOR TRIM:用其他对象定义的剪切边修剪对象TR U UNION:通过并运算创建组合面域或实体UNI UNITS:设置坐标和角度的显示格式和精度UN V VIEW:保存和恢复已命名的视图V VPOINT:设置图形的三维直观图的查看方向-VP W WBLOCK:将块对象写入新图形文件W WEDGE:创建三维实体使其倾斜面尖端沿X 轴正向WE X XATTACH:将外部参照附着到当前图形中XA XBIND:将外部参照依赖符号绑定到图形中XB XCLIP:定义外部参照或块剪裁边界,并且设置前剪裁面和后剪裁面XC XLINE:创建无限长的直线(即参照线)XL XREF:控制图形中的外部参照XR Z ZOOM:放大或缩小当前视口对象的外观尺寸Z。
0.5mm钣金折弯半径

0.5mm钣金折弯半径
0.5mm钣金折弯半径是指在钣金加工中,对于0.5mm厚度的
钣金,在进行折弯加工时所需要的最小弯曲半径。
这个数值对于钣金加工来说非常重要,因为它决定了钣金加工的精度和质量。
在进行钣金折弯时,如果弯曲半径过小,就会导致钣金变形、破裂等问题,从而影响加工的质量和精度。
因此,在进行钣金折弯时,需要根据不同的厚度和材质来确定合适的折弯半径。
对于0.5mm厚度的钣金来说,其折弯半径一般不少于1.5倍钣金厚度,即0.75mm。
这个数值是经过实践和经验总结得出的,可以保证钣金加工的质量和精度。
当然,具体的折弯半径还需要根据具体的加工要求和材料来确定。
在进行钣金加工时,需要根据不同的厚度、材质、形状等因素来选择合适的折弯半径,以确保加工出来的钣金零件符合要求。
总之,0.5mm钣金折弯半径是钣金加工中一个非常重要的参数,需要根据实际情况来确定合适的数值。
在进行钣金加工时,需要注意选择合适的折弯半径,并严格控制加工过程中的各项参数,以确保加工出来的钣金零件质量和精度符合要求。
基于Solidworks钣金折弯计算分析(原创)
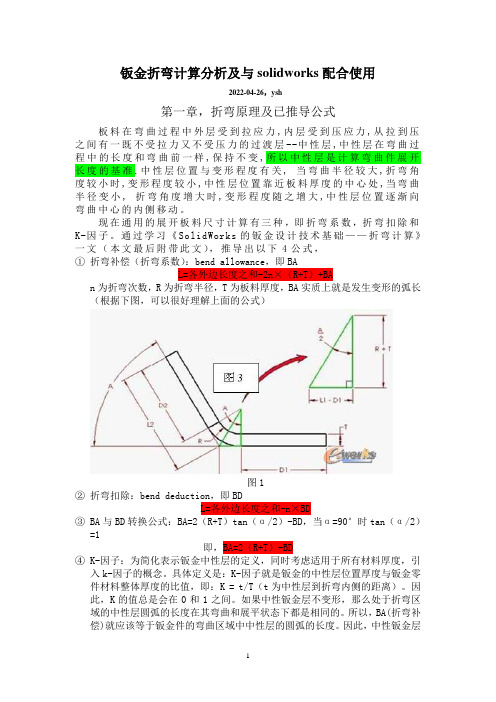
钣金折弯计算分析及与solidworks配合使用2022-04-26,ysh第一章,折弯原理及已推导公式板料在弯曲过程中外层受到拉应力,内层受到压应力,从拉到压之间有一既不受拉力又不受压力的过渡层--中性层,中性层在弯曲过程中的长度和弯曲前一样,保持不变,所以中性层是计算弯曲件展开长度的基准.中性层位置与变形程度有关, 当弯曲半径较大,折弯角度较小时,变形程度较小,中性层位置靠近板料厚度的中心处,当弯曲半径变小, 折弯角度增大时,变形程度随之增大,中性层位置逐渐向弯曲中心的内侧移动。
现在通用的展开板料尺寸计算有三种,即折弯系数,折弯扣除和K-因子。
通过学习《SolidWorks的钣金设计技术基础——折弯计算》一文(本文最后附带此文),推导出以下4公式,①折弯补偿(折弯系数):bend allowance,即BAL=各外边长度之和-2n×(R+T)+BAn为折弯次数,R为折弯半径,T为板料厚度,BA实质上就是发生变形的弧长(根据下图,可以很好理解上面的公式)图1②折弯扣除:bend deduction,即BDL=各外边长度之和-n×BD③BA与BD转换公式:BA=2(R+T)tan(α/2)-BD,当α=90°时tan(α/2)=1即,BA=2(R+T)-BD④K-因子:为简化表示钣金中性层的定义,同时考虑适用于所有材料厚度,引入k-因子的概念。
具体定义是:K-因子就是钣金的中性层位置厚度与钣金零件材料整体厚度的比值,即:K = t/T(t为中性层到折弯内侧的距离)。
因此,K的值总是会在0和1之间。
如果中性钣金层不变形,那么处于折弯区域的中性层圆弧的长度在其弯曲和展平状态下都是相同的。
所以,BA(折弯补偿)就应该等于钣金件的弯曲区域中中性层的圆弧的长度。
因此,中性钣金层圆弧的半径可以表示为(R+t).利用这个表达式和折弯角度,中性层圆弧的长度(BA)就可以表示为:BA = π(R+t)α/180°=π(R+KT)α/180°K-因子与BA的转换公式:BA=π(R+KT)×α/180°,当α=90°时,即BA=π(R+KT)/2solidworks系统也是采用上面的公式进行计算。
2mm钣金最小折弯高度

2mm钣金最小折弯高度2mm钣金最小折弯高度是指在钣金加工过程中,将2mm厚的钣金折弯成一定角度时,所需的最小内半径或V型槽深度。
这个数值对于钣金加工来说非常重要,因为它决定了能否成功完成折弯,以及折弯后零件的质量和精度。
在实际生产中,2mm钣金最小折弯高度通常取决于材料的硬度、厚度、弹性模量和表面状态等因素。
一般来说,硬度越大、厚度越大、表面状态越差的材料,其最小折弯高度也就越大。
而弹性模量则是影响最小折弯高度的关键因素之一。
在进行2mm钣金折弯时,如果内半径或V型槽深度太小,则会导致材料过分拉伸和变形,甚至出现断裂和裂纹等缺陷。
如果内半径或V型槽深度太大,则会导致零件尺寸不准确、角度不精确等问题。
为了确定2mm钣金的最小折弯高度,在实际生产中需要进行试验和计算。
一般来说,可以采用下面几种方法:1.经验公式法:根据经验公式计算最小内半径或V型槽深度。
这种方法简单易行,但精度较低,只适用于一些简单的折弯工艺。
2.试验法:通过试验来确定最小内半径或V型槽深度。
这种方法比较准确,但需要进行大量试验才能得到可靠的数据。
3.数值模拟法:采用有限元分析等数值模拟方法来计算最小内半径或V 型槽深度。
这种方法精度较高,但需要专业的软件和技术支持。
无论采用哪种方法,都需要考虑到材料的硬度、厚度、弹性模量和表面状态等因素,并结合实际生产情况进行综合分析和确定。
总之,2mm钣金最小折弯高度是一个重要的技术参数,在钣金加工中具有重要的作用。
正确地确定最小折弯高度可以保证零件质量和精度,提高生产效率和经济效益。
“最小”折弯概念及计算方式

“最小”折弯概念及计算方式最小折弯边所指的是一次折弯的最小折边。
在这我们不考虑模具强度,只讨论V槽与最小折弯边的联系。
为什么折弯会有最小折弯边呢?原因是折弯成型时,假如折边悬空,折弯会打滑,折弯将达不到你想要的尺度。
所以研讨最小折弯边是为了处理折弯打滑的问题。
如下图所示是1.0板厚的最小折边的靠位尺度。
核算最小折弯边有个大略的经历公式:L=V/2+1.8T+.5(.5是搭边段),而更为准确的是中兴折弯公式:L=V/2+K/2+.5(K为外补偿量),不过条件是要知道外补偿量。
经过下图咱们来加深对最小折弯边知道,理论公式为:L=V/2+K/2+X=V/2+K/2+tan(90-a)/2*R。
当a=90时,L=V/2+K/2+0.414*R。
(X为最小搭边)当R=1.2时,最小搭边量即为0.5,所以上面提到的经历公式与中兴公式都只合适较小板厚(t<>在实践生产中,因为每个公司选用模具不同,R角磨损不同,最小折边不尽相同。
R角磨损越大,最小折边就越大。
下面供给相应V槽相应板厚的最小折边(用经历公式算)V槽 / 板厚0.5(4v) 3.00.8(4v/5v) 3.2/3.71.0(6v) 4.41.2(6v/8v) 4.5/5.51.5(8v/10v) 5.8/6.82.0(12v) 8.32.5(14v/16v) 9.7/10.73.0(16v/18v) 11.1/12.14.0(25v) 16.5注:1、最小折弯高度包括一个料厚。
2、当V形折弯是折弯锐角时,最短折弯边需加大0.5。
3、当零件材料为铝板和不锈钢板时,最小折弯高度会有较小的变化,铝板会变小一点,不锈钢会大一点。
-------------------------------------------------------------------------。
钣金件的折弯

钣金件的折弯钣金的折弯,是指改变板材或板件角度的加工。
如将板材弯成V形,U形等。
一般情况下,钣金折弯有两种方法:一种方法是模具折弯,用于结构比较复杂,体积较小、大批量加工的钣金结构;另一种是折弯机折弯,用于加工结构尺寸比较大的或产量不是太大的钣金结构。
目前公司产品的折弯主要采用折弯机加工。
这两种折弯方式有各自的原理,特点以及适用性。
模具折弯:对于年加工量在5000件以上,零件尺寸不是太大的结构件(一般情况为300X300),加工厂家一般考虑开冲压模具加工。
该在(0折弯机折弯折弯机分普通折弯机和数控折弯机两种。
由于精度要求较高,折弯形状不规则,通信设备的钣金折弯一般用数控折弯机折弯,其基本原理就是利用折弯机的折弯刀(上模)、V形槽4)折弯半径钣金折弯时,在折弯处需有折弯半径,折弯半径不宜过大或过小,应适当选择。
折弯半径太小容易造成折弯处开裂,折弯半径太大又使折弯易反弹。
各种材料不同厚度的优选折弯半径(折弯内半径)见下表1-9最小弯曲半径数值 (mm)注:表中t为板料厚度。
上表中的数据为优选的数据,仅供参考之用。
实际上,厂家的折弯刀的圆角通常都是0.3,少量的折弯刀的圆角为0.5,所以,我们的钣金件的折弯内圆角基本上都是0.2。
对于普通的低碳钢钢板、防锈铝板、黄铜板、紫铜板等,内圆角0.2 都是没有问题的,但对于一些高碳钢、硬铝、超硬铝,这种折弯圆角就会导致折弯断裂,或者外圆角开裂。
折弯回弹1)回弹角Δα=b-a式中 ba2) 回弹角的大小单角90 o3)影响回弹的因素和减少回弹的措施。
1,材料的力学性能回弹角的大小与材料的的屈服点成正比,与弹性模量E成反比。
对于精度要求较高的钣金件,为了减少回弹,材料应该尽可能选择低碳钢,不选择高碳钢和不锈钢等。
2,相对弯曲半径r/t 越大,则表示变形程度越小,回弹角Δα就越大。
这是一个比较重要的概念,钣金折弯的圆角,在材料性能允许的情况下,应该尽可能选择小的弯曲半径,有利于提高精度。
钣金折弯加工能力工艺技术规范

1 适用范围适用于XXX公司折弯机钣金件的折弯加工2 目的1.完善钣金折弯机加工能力要求、明确钣金折弯的工艺参数;2.指导研发设计、车间生产;3.降低因设计不合理造成的返工、返修几率。
3 内容3.1 折边处属于板材变形,其周围的孔易受影响变形,折弯件的孔到折弯边的最小距离应按照以下要求:3.1.1当孔为圆孔和垂直于弯曲方向的长圆孔时,圆孔边与折弯线要求大于最小孔边距X≥2t+R(2.5mm板厚(含)以下,R值为0.5)、X≥3t+R(2.5mm板厚以上,R值为1);t圆孔距折弯边最小距离板料厚度0.6~0.8 1 1.2 1.5 2 2.5 3 5最小距离X 2 2.5 3 3.5 4.5 5.5 10 16当孔为方孔和平行于弯曲方向的长圆孔时,长圆孔距折弯边最小距离3.2折弯加工工艺3.2.1说明:厂内所拥有的折床以及折弯模具可达到的折弯加工尺寸范围:最大可折出500mm 折边(如是盒形,另两边不可大于150mm ,如大于150,则需要在设计时进行结构拆分),最小可折出5mm 折边(T0.4~1.0mm )。
在设计的时候要注意所绘的尺寸必须在以下图表的尺寸范围内,否则会造成折弯交涉,导致加工变形或难以加工。
盒形结构3.2.2 厂内折弯极限尺寸表:3.2.2.1弯第一边的最小极限尺寸决定于下模V 槽宽中心至外边的最小尺寸及弯第一边的弯边圆角R 。
弯边最小极限尺寸表:L <26 26~50 >50 最小距离X2t+R2.5t+R3t+R材料厚度t(mm)0.5~1 1.2 1.5 2.0 2.5 3.0 5第一折边最小极限尺寸amin (mm)5(推荐取6)8 10 12 14 18 283.2.2.2(Z形)弯第一边等同于3.2.2.1的情况,弯第二边最小极限尺寸决定于下模V槽宽中心至外边的最小尺寸d、弯第一边的弯边圆角R及材料厚度t。
弯边最小极限尺寸表:材料厚度t(mm)0.5~0.8 1 1.2 1.5 2 2.5 3.0 5.0第二折边最小极限尺寸bmin (mm) 6 7 9.5 12 15 16 20 353.2.2.3(U形)弯第一边等同于3.2.2.1的情况,弯第二边,其极限尺寸决定于凸模的几何形状、凹模槽宽V和第二边的弯边尺寸。
- 1、下载文档前请自行甄别文档内容的完整性,平台不提供额外的编辑、内容补充、找答案等附加服务。
- 2、"仅部分预览"的文档,不可在线预览部分如存在完整性等问题,可反馈申请退款(可完整预览的文档不适用该条件!)。
- 3、如文档侵犯您的权益,请联系客服反馈,我们会尽快为您处理(人工客服工作时间:9:00-18:30)。
成型最小折边
一、L折。
1.决定最小L折的因素。
V槽中间距离为悬空段,成型时,折边必须超过此悬空段,具体搭边尺寸各公司有小小区别,(下V槽因使用时间长,R角变大,搭边距离将会随之变大,否则会“滑位”)。
2.换算公式(经验式):6*T/2+0.5+(1.8*T/2)
3.如下图,T=1,K=1.8*1, 最小L折:3+0.5+0.9=
4.4
特注:
⑴因每个公司的下V槽并一定都齐全,故需要灵活使用公式。
⑵特别情况下,需用更小V槽时,原则上相对V槽减小不能超过2.0MM.
⑶附表。
说明:尽量采用黑粗线最小折边尺寸。
一、U折。
1.U折的种类
A. 常规折弯刀成型。
B. 垫片反折压平。
(先折至30°,中间放一块合适垫板后压平。
)
2.决定最小U折的因素。
A .上模具的形状。
(如下图)从常规刀具来看,小U折最佳刀具为“弯刀”。
(弯刀有很多种型号,具体要依公司现有尺寸)
C. 折边尺寸。
(见下小图)两尺寸的梯增关系:
A愈长则B愈长。
3.换算公式:(大弯刀经验型)
◆0.5MM板:
最小U折A尺寸=7.67。
B尺寸=0.5板最小L折3.0。
梯增值:A尺寸每梯增1MM,B尺寸对应梯增1.87,
公式:已知A尺寸,求B尺寸=(A-7.67)/T*梯增值+该板厚最小L折如:A=15时,B=(15-7.67)/0.5*1.87+ 3.0=30.4
已知B尺寸,求A尺寸=(B-该板厚最小L折)/梯增值*T+7.67. 如:B=30.4时,A=(30.4-3)/1.87*0.5+7. 67=15
◆0.8MM板
最小U折A尺寸=8.5,B尺寸=0.8最小L折4.2。
梯增值:1.87/0.5*0.8=2.99
◆ 1.0MM板
最小U折A尺寸=8.94,B尺寸=1.0最小L折4.5
梯增值:1.87/0.5*1.0=3.7
◆ 1.2MM板
最小U折A尺寸=9.3,B尺寸=1.2最小L折4.5
梯增值:1.87/0.5*1.2=4.5
◆ 1.5MM板
最小U折A尺寸=10.3,B尺寸=1.5最小L折6.2
梯增值:1.87/0.5*1.5=5.5
◆ 2.0MM板
最小U折A尺寸=12.7,B尺寸=2.0最小L折12.0
梯增值:1.87/0.5*2=7.4
特注:
1. A尺寸超过85.0MM及B尺寸超过60.0MM的不按此公式计算。
2. 附表:A=测试值,B=该板最小L折。
K=测试值
一、Z折。
1.Z折的种类。
A. H大于或等于5T时,按2个90度折弯计算。
B. H小于5T时,一次成型(即:压台阶,不列入最小计算范围)
2. 影响最小Z折的因素主要为下V槽的V幅宽及V槽的到边距离。
3.计算公式:6*T/2+V槽边距+(1.8*T/2)+T(附上右图):1.0板用V6下V槽,到边距=1.5,最小Z折H=6*1/2+1.5+(1.8*1/2)+1=6.
4.。