车削加工实训报告
金工实习报告车削加工

金工实习报告车削加工篇一:金工实习之车工普通车床操作实训指导书烟台南山学院机械工程训练中心金工教研室实训一车床基本操作一. 实训目的:1.了解普通车床的安全操作规程2.掌握普通车床的基本操作及步骤3.对操作者的有关要求4.掌握车削加工中的基本操作技能5.培养良好的职业道德二. 实训内容:1.安全技术2.熟悉普通车床的结构组成及功用3.熟悉普通车床的基本操作①车床的启动和停止②车床转速、进给量、进给方向、光丝杠转换③车床手动进给控制三. 实训设备:C616-1D 车床18台四. 实训步骤:(一)熟悉车工基本概念及其加工范围车工是在车床上利用工件的旋转运动和刀具的移动来改变毛坯形状和尺寸,将其加工成所需零件的一种切削加工方法。
其中工件的旋转为主运动,刀具的移动为进给运动(图1-1)。
图1-1 车削运动车床主要用于加工回转体表面(图1-2),加工的尺寸公差等级为IT11~IT6,表面粗糙度Ra值为12.5~0.8μm。
车床种类很多,其中卧式车床应用最为广泛。
图1-2 普通车床所能加工的典型表面a)车外园b)车端面C)车锥面d)切槽、切断e)切内槽f)钻中心孔g)钻孔h)镗孔i)铰孔j)车成形面k)车外螺纹l)滚花(二)学习卧式车床型号及结构组成Ⅰ、机床的型号主参数代号(最大车削直径的1/10,即320mm)机床型别代号(普通车床型)机床组别代号(普通车床组)机床类别代号(车床类)主参数的1/10,即车床主轴轴线到导轨面的尺寸为160mm,(其车削工件最大直径为320mm)。
组别(普通车床)类别(车床类)Ⅱ、卧式车床的结构1.卧式车床的型号卧式车床用C61333来表示,其中C 为机床分类号,表示车床类机床;61为组系代号,表示卧式。
其它表示车床的有关参数和改进号。
2.卧式车床各部分的名称和用途C6132普通车床的外形如图1-3所示。
图1-3 C6132普通车床1-床头箱;2-进给箱;3-变速箱;4-前床脚;5-溜板箱;6-刀架;7 -尾架;8-丝杠;9-光杠;10-床身;11-后床脚;12-中刀架;13-方刀架;14-转盘;15-小刀架;16-大刀架1.主轴箱又称床头箱,内装主轴和变速机构。
车工实习报告范文七篇

车工实习报告范文七篇车工实习报告篇1在技能上,我们对车工有了一些基础,我们相信我们将来走上社会工作岗位一定有所帮助。
在对待人生,我们从中有了启发,可想当初我们投着极高的兴趣和非常认真的态度去车间实习,正因为我们初始的态度决定了我们在车工实习操作的动力,似的我们在车工实习时认真得去寻找我们心中好奇的答案。
车床的相关知识1、车削的基本定义:工件在旋转运动和刀具的进给运动的作用下,改变工件毛坯尺寸及形状的一种冷加工切削方法。
2、主运动:工件的旋转运动。
3、辅助运动:刀具的进给运动。
4、车床的型号标注说明:5、车床的加工范围:车外圆、车端面、切槽、切断、特型面。
6、主轴变速箱:又名床头箱。
通过箱外手柄的调整来改变箱内齿轮的传动比,使主轴获得不同的转速。
7、走刀箱:又名进给箱。
通过箱外手柄来调节刀具进给量。
8、拖板箱:又名溜板箱。
把丝杆或光杆的旋转运动转换为拖板的纵向或横向的直线进给运动。
9、挂轮箱:传递动力。
调换齿轮的齿数改变比并与走刀箱配合,使刀具得到不同的进给速度,可加工不同螺距的螺纹。
10、刀架:安装和固定刀具。
11、尾座:安装刀具和顶尖,支顶工件。
12、拖板:分为大、中、小三种。
大拖板纵向运动,中拖板横向运动,小拖板也是纵向运动,主要用于车锥面。
13、三杆:丝杆主要用于车削螺纹时使用,光杆用于车削内外圆柱面时的自动进刀,操纵杆用于操纵控制车床。
14、床身:支撑车床各主要部件,并按一定的技术要求组合成车床。
15、中心架、跟刀架、花盘、拨盘、冷却咀、照明灯、电动机、盛液盘。
16、车床的保养及维护:润滑:上班时加注润滑油。
检查:检查各机构是否完好正常。
空运转:观察运转是否正常,有无异常。
防砸:不允许在机床上敲打和堆放工件、量具、工具等杂物。
停车变速:改变主轴转动速时,必须先停车后变速,以免打坏齿轮。
安全操作规程1、穿戴合适的工作服,女生长头发要压入工作帽中,佩带首饰不得悬露,不得带手套操作。
2、俩人公用一台机床时,只能一人操作,并注意他人安全。
大学生车工实训报告五篇
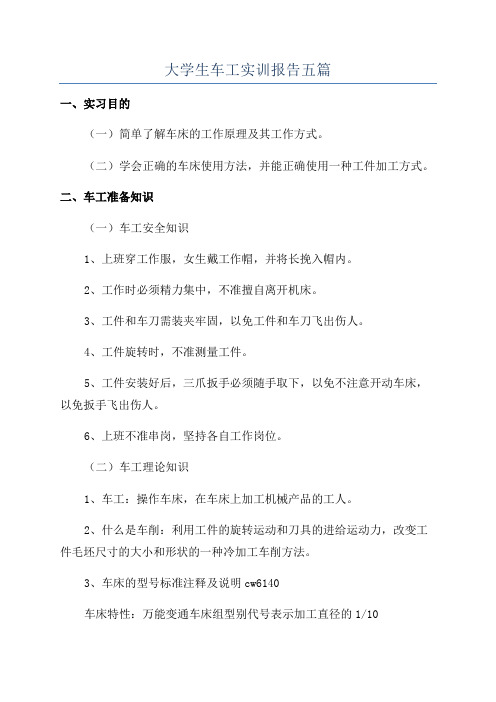
大学生车工实训报告五篇一、实习目的(一)简单了解车床的工作原理及其工作方式。
(二)学会正确的车床使用方法,并能正确使用一种工件加工方式。
二、车工准备知识(一)车工安全知识1、上班穿工作服,女生戴工作帽,并将长挽入帽内。
2、工作时必须精力集中,不准擅自离开机床。
3、工件和车刀需装夹牢固,以免工件和车刀飞出伤人。
4、工件旋转时,不准测量工件。
5、工件安装好后,三爪扳手必须随手取下,以免不注意开动车床,以免扳手飞出伤人。
6、上班不准串岗,坚持各自工作岗位。
(二)车工理论知识1、车工:操作车床,在车床上加工机械产品的工人。
2、什么是车削:利用工件的旋转运动和刀具的进给运动力,改变工件毛坯尺寸的大小和形状的一种冷加工车削方法。
3、车床的型号标准注释及说明cw6140车床特性:万能变通车床组型别代号表示加工直径的1/104、车床的组成部分:主轴箱、挂轮箱、走入箱、拖板箱、刀架、尾架、拖板三杆、床身、附件。
5、车床的维护和保养①润滑油②检查机床是否完好③防砸④打扫卫生⑤关闭电源。
(三)工件名称加工内容工具:1、车外圆车φ30±0、590度的外圆车刀游标卡尺。
2、车台阶(画线定位)车φ22和φ1790度外圆车刀游标卡尺。
4、整形用锉刀整形锉刀、砂布。
(四)车床通用规定工作中认真作到:1、找正工件时只准用手板动卡盘或开最低速找正,不准开高速找正。
2、加工棒料时,棒料不得太长,一般以不超出主轴孔后端300毫米为宜并用木片在主轴孔内卡紧。
如超过300毫米以上,应用支架支承,确认安全后方可加工,但不准开高速度。
3、加工偏重工件时,配重要加得恰当,紧固牢靠,用手转动卡盘检查无障碍后,再低速回转,确认配重符合要求,方可加工。
4、用尾座顶针顶持工件时,尾座套筒的伸出量不准超过套筒直径的二倍,同时注意锁紧。
5、用尾座装钻头钻孔时,不准用杠杆转动手轮进刀。
6、装卸较重的工件时,要在床面上垫块木板,防止发生意外。
7、装卸卡盘时,只准用手转动三角皮带代动主轴回转进行,绝对禁止直接开动机床强制松开或拧紧,同时要在床面上垫块木板,防止发生意外。
车削实训报告
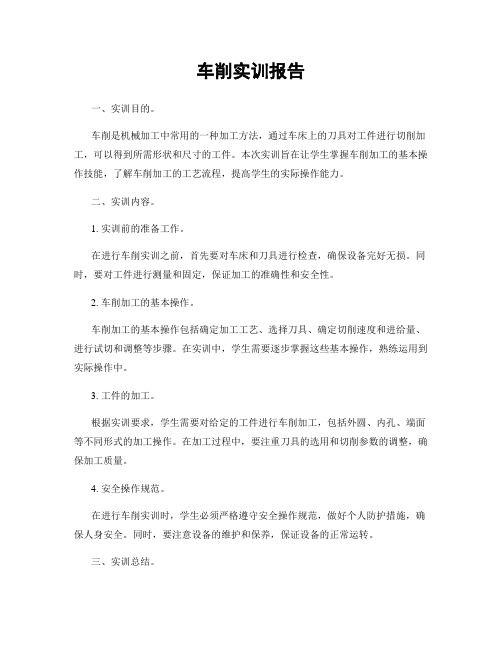
车削实训报告一、实训目的。
车削是机械加工中常用的一种加工方法,通过车床上的刀具对工件进行切削加工,可以得到所需形状和尺寸的工件。
本次实训旨在让学生掌握车削加工的基本操作技能,了解车削加工的工艺流程,提高学生的实际操作能力。
二、实训内容。
1. 实训前的准备工作。
在进行车削实训之前,首先要对车床和刀具进行检查,确保设备完好无损。
同时,要对工件进行测量和固定,保证加工的准确性和安全性。
2. 车削加工的基本操作。
车削加工的基本操作包括确定加工工艺、选择刀具、确定切削速度和进给量、进行试切和调整等步骤。
在实训中,学生需要逐步掌握这些基本操作,熟练运用到实际操作中。
3. 工件的加工。
根据实训要求,学生需要对给定的工件进行车削加工,包括外圆、内孔、端面等不同形式的加工操作。
在加工过程中,要注重刀具的选用和切削参数的调整,确保加工质量。
4. 安全操作规范。
在进行车削实训时,学生必须严格遵守安全操作规范,做好个人防护措施,确保人身安全。
同时,要注意设备的维护和保养,保证设备的正常运转。
三、实训总结。
通过本次车削实训,学生们对车削加工的基本原理和操作流程有了更深入的理解,掌握了一定的实际操作技能。
但在实训过程中也暴露出一些问题,比如对刀具的选择和切削参数的调整还不够熟练,需要进一步加强练习。
希望通过今后的实训课程和实际操作中的练习,能够更好地掌握车削加工的技术要领,为将来的工作做好充分准备。
四、实训感想。
在本次车削实训中,我深刻体会到了实际操作的重要性。
只有通过实际操作,才能更好地理解理论知识,并且掌握操作技能。
在实训中,我遇到了许多问题,但通过不断的实践和摸索,我逐渐克服了这些问题,取得了一定的进步。
我相信,只要坚持不懈地努力,我一定能够成为一名优秀的车削工。
五、实训展望。
通过本次实训,我对车削加工有了更深入的了解,也意识到了自己在实际操作中的不足之处。
我将继续加强对车削加工技术的学习,不断提高自己的实际操作能力,争取在以后的实训和工作中取得更好的成绩。
车削实验报告

一、实验目的1. 了解车削加工的基本原理和方法,掌握车削加工的基本操作步骤。
2. 熟悉车床的结构和性能,学会使用车床进行简单零件的加工。
3. 培养实际操作技能,提高动手能力和工程实践能力。
二、实验设备1. 车床:C6150型卧式车床一台。
2. 刀具:车刀、内孔刀、外圆刀、螺纹刀等。
3. 工件:钢棒、铝棒、铜棒等。
4. 测量工具:卡尺、千分尺、量角器等。
三、实验内容1. 车削加工的基本原理车削加工是利用车床将工件旋转,刀具在工件上作旋转运动,从而完成切削加工的一种方法。
车削加工主要包括外圆车削、内孔车削、端面车削、螺纹车削等。
2. 车床的基本操作(1)开机前准备1)检查车床各部位是否完好,润滑系统是否正常。
2)安装工件:将工件安装在卡盘上,调整卡盘与工件的位置,确保工件夹紧牢固。
3)安装刀具:根据加工要求,选择合适的刀具,将刀具安装在刀架上,确保刀具安装牢固。
(2)开机运行1)打开机床电源,启动主轴电机,使主轴旋转。
2)调整切削参数:根据工件材料、加工要求,调整切削速度、进给量、切削深度等。
3)试切:进行试切,观察工件加工情况,调整切削参数。
(3)加工过程1)外圆车削:将刀具对准工件外圆,开始切削。
切削过程中,保持刀具与工件外圆的距离,避免刀具划伤工件。
2)内孔车削:将刀具对准工件内孔,开始切削。
切削过程中,保持刀具与工件内孔的距离,避免刀具划伤工件。
3)端面车削:将刀具对准工件端面,开始切削。
切削过程中,保持刀具与工件端面的距离,避免刀具划伤工件。
4)螺纹车削:将刀具对准工件螺纹,开始切削。
切削过程中,保持刀具与工件螺纹的距离,避免刀具划伤工件。
3. 车削加工质量分析(1)尺寸精度:通过测量工件尺寸,判断加工精度是否符合要求。
(2)表面粗糙度:通过测量工件表面粗糙度,判断加工表面质量是否符合要求。
(3)形状误差:通过测量工件形状误差,判断加工形状是否符合要求。
四、实验结果与分析1. 实验结果(1)外圆车削:加工出的工件外圆尺寸符合要求,表面粗糙度达到Ra1.6。
车削台阶轴加工实训报告

一、实训目的通过本次实训,使学生掌握车削台阶轴的基本加工工艺,熟悉车床操作和刀具使用,提高学生的实际操作能力和工程意识。
二、实训内容1. 台阶轴加工工艺分析(1)材料:45号钢(2)加工要求:外圆、内孔、端面、台阶、键槽等(3)加工步骤:毛坯加工、粗车、半精车、精车、孔加工、倒角、去毛刺等2. 车床操作及刀具使用(1)车床操作:熟悉车床的基本结构、操作规程、安全注意事项等(2)刀具使用:了解各种刀具的用途、结构、选用原则等三、实训过程1. 毛坯加工(1)将毛坯放入车床卡盘,调整卡爪位置,使毛坯中心线与车床主轴中心线对齐(2)使用砂轮修整毛坯端面,使端面与主轴中心线垂直(3)使用外圆车刀粗车外圆,保证外圆尺寸和形状符合要求2. 粗车(1)使用内孔车刀粗车内孔,保证内孔尺寸和形状符合要求(2)使用端面车刀粗车端面,保证端面与外圆中心线垂直(3)使用台阶车刀粗车台阶,保证台阶尺寸和形状符合要求3. 半精车(1)使用外圆精车刀精车外圆,保证外圆尺寸和形状符合要求(2)使用内孔精车刀精车内孔,保证内孔尺寸和形状符合要求(3)使用端面精车刀精车端面,保证端面与外圆中心线垂直(4)使用台阶精车刀精车台阶,保证台阶尺寸和形状符合要求4. 孔加工(1)使用钻头钻孔,保证孔的位置、尺寸和形状符合要求(2)使用扩孔钻扩孔,保证孔的尺寸和形状符合要求(3)使用铰刀铰孔,保证孔的尺寸和形状符合要求5. 倒角、去毛刺(1)使用倒角刀倒角,保证倒角尺寸和形状符合要求(2)使用去毛刺工具去除毛刺,保证工件表面光滑四、实训结果与分析1. 实训结果本次实训中,我完成了台阶轴的加工,达到了加工要求,工件表面光滑,尺寸和形状符合要求。
2. 实训分析(1)在加工过程中,要注意刀具的选择和切削参数的调整,以保证加工质量(2)在操作过程中,要严格按照操作规程进行,确保加工安全(3)在加工过程中,要注意观察工件的变化,及时调整刀具和切削参数,以保证加工质量五、实训总结通过本次实训,我掌握了车削台阶轴的基本加工工艺,熟悉了车床操作和刀具使用,提高了实际操作能力和工程意识。
车削加工实训报告(最新版)

车削加工实训报告车削加工实训报告。
车削加工实训报告篇一《数控车削加工实训报告》数控车削加工实训报专业:数控技术班级:11009班姓名:石禹忠学号:32 号指导老师:姜天根赵传彬裘敏浩日期:2016年11月27日一.实训的目的和要求:知识目标:加深学生对数控机床结构和数控原理液压理论知识的理解,培养学生思考解决问题的能力和良好的工作素质。
使学生掌握从事数控车床操作编程和加工所必须的专业知识方法和专业技能。
同时,通过本次实训课程,提高学生的全面素质,培养学生的综合职业能力创新精神和良好的职业道德,提高学生运用所学理论知识分析和解决实际工程问题的能力。
为学生从事本专业工作和适应职业岗位的变化以及学习新的生产科学技术打下基础。
能力目标:1.熟悉数控车床组成结构及工作原理。
2.熟练掌握待加工零件的装夹定位加工路线设置及加工参数调校实际操作工艺。
3.掌握数控车综合操作技能;迅速独立编制练习件的加工程序。
4.养成独立的工作能力和安全文明生产的习惯。
5.能熟练使用常用的精密量具进行尺寸测量。
6.能分析判断并解决加工程序中所出现的错误,学会排除编程及机械方面的一般性故障。
二.实训任务: 1. 实训课题: 2.数控车削零件操作加工图:见附件(图一、图二) 3.实训任务:(1).全班学生根据教师给定的实训进程完成每天的工作内容。
(2).各组人员按给定的零件图,在规定的时间内独立完成零件的数控加工。
(3).实训结束,每人交付实训零件 2个,个人交付实训报告一份,作为成绩评定的依据。
图一图二四.零件工艺分析 1.图一工艺分析:①该零件由外圆柱、圆锥、螺纹等表面组成零件尺寸标注完整,表面粗糙度要求不高。
②采用三角定心抓盘加紧,伸出100mm ③确定切削用量零件切削用量④确定加工路线:a.用90º外圆车刀粗精加工外圆b.切槽刀(宽4mm)4×2槽 c.普通螺纹刀加工螺纹。
⑤数值计算:a. 螺纹加工计算实际车削的外圆锥面直径d=分度圆直径-0.13×2 螺纹大径小端为φ29.73,大端为φ37.73,螺纹实际牙型高度h=0.65×2=1.3(mm)。
普通车削加工实训报告
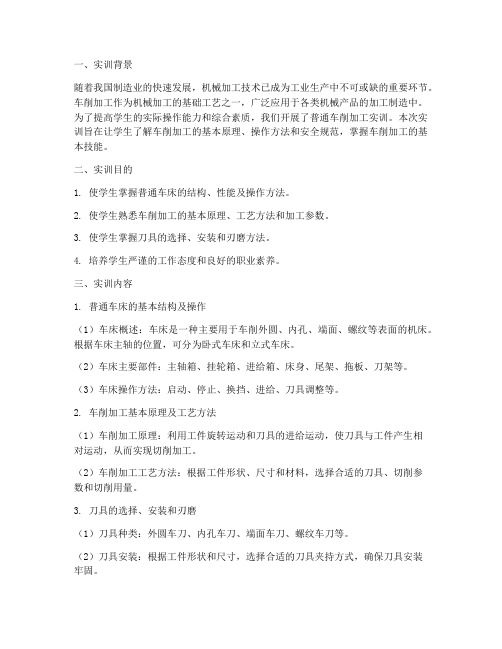
一、实训背景随着我国制造业的快速发展,机械加工技术已成为工业生产中不可或缺的重要环节。
车削加工作为机械加工的基础工艺之一,广泛应用于各类机械产品的加工制造中。
为了提高学生的实际操作能力和综合素质,我们开展了普通车削加工实训。
本次实训旨在让学生了解车削加工的基本原理、操作方法和安全规范,掌握车削加工的基本技能。
二、实训目的1. 使学生掌握普通车床的结构、性能及操作方法。
2. 使学生熟悉车削加工的基本原理、工艺方法和加工参数。
3. 使学生掌握刀具的选择、安装和刃磨方法。
4. 培养学生严谨的工作态度和良好的职业素养。
三、实训内容1. 普通车床的基本结构及操作(1)车床概述:车床是一种主要用于车削外圆、内孔、端面、螺纹等表面的机床。
根据车床主轴的位置,可分为卧式车床和立式车床。
(2)车床主要部件:主轴箱、挂轮箱、进给箱、床身、尾架、拖板、刀架等。
(3)车床操作方法:启动、停止、换挡、进给、刀具调整等。
2. 车削加工基本原理及工艺方法(1)车削加工原理:利用工件旋转运动和刀具的进给运动,使刀具与工件产生相对运动,从而实现切削加工。
(2)车削加工工艺方法:根据工件形状、尺寸和材料,选择合适的刀具、切削参数和切削用量。
3. 刀具的选择、安装和刃磨(1)刀具种类:外圆车刀、内孔车刀、端面车刀、螺纹车刀等。
(2)刀具安装:根据工件形状和尺寸,选择合适的刀具夹持方式,确保刀具安装牢固。
(3)刀具刃磨:掌握刀具刃磨的基本方法和技巧,提高刀具使用寿命。
4. 车削加工参数及切削用量(1)切削速度:根据工件材料、刀具材料和切削深度等因素确定。
(2)进给量:根据工件材料、刀具材料和切削深度等因素确定。
(3)切削深度:根据工件加工精度和加工余量确定。
四、实训过程1. 实训前准备(1)熟悉实训场地和设备,了解车床操作规程。
(2)了解实训内容和要求,明确实训目标。
(3)准备实训所需的刀具、量具和工件。
2. 实训过程(1)按照实训指导书的要求,进行工件装夹、刀具安装和切削参数设置。
车削实训报告

车削实训报告
目录
1. 准备工作
1.1 机床操作
1.2 刀具准备
2. 车削操作
2.1 设定加工参数
2.2 工件夹持
2.3 车削加工
3. 常见问题与解决
3.1 刀具磨损
3.2 加工精度问题
3.3 机床故障
准备工作
机床操作
在进行车削实训前,首先要熟悉机床的操作,包括如何打开电源,怎样调整操作台的高度,如何操作各个按钮等等。
刀具准备
选取适合加工工件的刀具是非常重要的,根据工件的材质和形状,选择合适的刀具,并进行正确的安装与调整。
车削操作
设定加工参数
在开始车削操作前,需要根据工件的要求,设定好加工参数,如车削速度、进给速度、切削深度等。
工件夹持
正确的工件夹持是保证加工精度的关键,需要根据工件形状和材质选择合适的夹具,并确保夹持牢固。
车削加工
根据设定的加工参数,开始进行车削加工,注意实时检查加工质量,及时调整参数以保证加工效果。
常见问题与解决
刀具磨损
刀具在车削过程中会有磨损,需要定期检查并更换刀具,避免因为磨损导致加工质量下降。
加工精度问题
如果出现加工精度问题,可以先检查加工参数是否设定正确,刀具是否磨损严重,及时调整参数或更换刀具来解决。
机床故障
在车削实训过程中,可能会遇到机床故障,如电源故障或机床运行不稳定等,应及时通知相关人员进行维修处理。
车削工件实训报告

一、实训背景随着我国制造业的快速发展,车削加工作为机械制造中最基本、最常用的加工方法之一,在各个行业中都发挥着至关重要的作用。
为了提高学生的实践操作能力和专业素养,我们开展了为期两周的车削工件实训。
本次实训旨在使学生了解车削加工的基本原理、操作方法和注意事项,并能够熟练运用车削加工技术完成简单零件的加工。
二、实训目的1. 理解车削加工的基本原理和操作方法。
2. 掌握车床的构造、性能和使用方法。
3. 学会正确选用刀具、切削用量和装夹工件。
4. 培养学生的动手操作能力和安全意识。
三、实训内容1. 车床认识与操作首先,我们学习了车床的基本构造、工作原理和性能。
通过实物观察和教师讲解,了解了车床的各个部件及其功能,如主轴、刀架、进给箱、溜板箱等。
在熟悉车床的基础上,我们进行了实际操作。
在教师的指导下,学会了如何启动和停止车床,如何调整主轴转速、进给速度和切削深度,以及如何进行手动进给和自动进给。
2. 刀具选用与刃磨刀具是车削加工中的关键工具,选用合适的刀具对加工质量和效率有很大影响。
我们学习了不同种类刀具的用途、特点和使用范围,并学会了如何根据工件材料、形状和加工要求选择合适的刀具。
此外,我们还学习了刀具的刃磨方法。
刃磨刀具是保证加工质量的重要环节,我们学会了如何使用砂轮、磨刀机等工具对刀具进行刃磨。
3. 装夹工件工件装夹是车削加工的前提和基础。
我们学习了不同类型工件的装夹方法,如三爪自定心卡盘、四爪卡盘、心轴等,并学会了如何调整工件的定位和夹紧。
4. 车削加工在掌握了以上基础知识后,我们开始了实际的车削加工。
本次实训选择了简单轴类零件作为加工对象,包括外圆、内孔、端面、台阶等。
在操作过程中,我们遵循以下原则:(1)合理选择切削用量:根据工件材料、刀具和车床性能,选择合适的切削速度、进给量和切削深度。
(2)正确选用刀具:根据工件形状、加工要求和使用范围,选择合适的刀具。
(3)正确装夹工件:确保工件定位准确、夹紧牢固。
车削实训报告总结

一、实训背景为了提高学生的实际操作能力和专业技能,增强学生对机械加工工艺的认识,我参加了为期一个月的车削实训。
本次实训由学校组织,在机械加工实习基地进行。
通过本次实训,我深入了解了车削加工的基本原理、操作方法和工艺流程,提高了自己的动手能力和实践技能。
二、实训目的1. 掌握车削加工的基本原理、操作方法和工艺流程;2. 熟悉车床的结构、性能和操作方法;3. 培养学生的动手能力和实践技能;4. 提高学生的团队协作能力和沟通能力。
三、实训内容1. 车削加工基本原理及操作方法在实训过程中,我学习了车削加工的基本原理和操作方法。
车削加工是利用车床和刀具对工件进行旋转切削,使其达到所需的形状、尺寸和表面质量。
我了解了车削加工的切削力、切削速度、进给量等参数对加工质量的影响,并掌握了车削加工的基本操作步骤。
2. 车床的结构、性能和操作方法实训期间,我熟悉了车床的结构、性能和操作方法。
车床主要由床身、主轴箱、进给箱、刀架、尾座等部分组成。
我了解了各部分的功能和作用,掌握了车床的操作方法,如装夹工件、调整刀具、设置切削参数等。
3. 工艺流程在实训过程中,我了解了车削加工的工艺流程。
首先,根据零件图纸和工艺要求,确定加工方案;然后,进行工件装夹、刀具调整、切削参数设置等准备工作;接着,进行切削加工,完成零件的加工;最后,对加工完成的零件进行检验,确保其尺寸和表面质量符合要求。
4. 实训项目实训期间,我完成了以下实训项目:(1)加工外圆、内孔、端面、螺纹等基本形状的零件;(2)加工复杂形状的零件,如轴类、盘类、套类等;(3)进行刀具刃磨和保养。
四、实训成果1. 理论知识方面:通过本次实训,我对车削加工的基本原理、操作方法和工艺流程有了更深入的了解,为今后的学习和工作打下了坚实的基础。
2. 实践技能方面:通过实际操作,我掌握了车削加工的基本技能,如装夹工件、调整刀具、设置切削参数等,提高了自己的动手能力。
3. 团队协作和沟通能力:在实训过程中,我与同学们相互协作、共同解决问题,提高了自己的团队协作和沟通能力。
金工实习车削实训报告范文(通用10篇)

金工实习车削实训报告范文(通用10篇)金工实习车削实训报告 1一、实训目的掌握钳工操作技能,加工工艺;按图纸要求完成加工手锤工件加工任务;提高学生动手操作能力,为就业奠定基础。
二、实训内容1、钳工加工的特点(1)手工操作(2)冷加工(3)加工灵活、操作方便2、钳工的基本操作方法划线:划线的目的,所用的工具和量具,划线前的准备,基准选择,平面和立体零件的划线方法。
锯削:手锯的应用范围及使用方法,锯条的安装,锯切的正确姿势与操作方法。
锉削:应用范围,锉刀种类,选择及锉削方法,锉削的正确姿势与操作方法,零件尺寸与形状的检验(用钢尺、卡尺、角尺等)钻孔:钻孔的方法,所用的钻床的组成、运动和用途,工具和夹具,掌握常用钻头的刃磨方法。
三、实训设备材料;钳工工作台、台虎钳、手锤、钢锯、锉刀、錾子、针、直尺、游标卡尺、游标高度尺,万能角度尺1、划线的特点。
根据图样或实物的尺寸要求,用划线工具在毛坯或半成品工件上划出待加工部位的轮廓线或作为基准的点、线的操作。
这些点和线标明了工件某部分的形状、尺寸或特征,并确定了加工的尺寸界限。
2、锯割的特点。
用手锯对材料或工件进行切断或切槽等的加工方法称为锯削。
它具有操作方便、简单、灵活的特点,不需任何辅助设备,不消耗动力,在临时工地,以及切削异形工件、修理等场合,应用很广。
3、手锯的种类及构造。
手锯由锯弓和锯条两部分组成。
锯弓用于安装和张紧锯条,有固定式和可调式两种。
固定式只能安装一种长度的锯条,可调式通过调整可以安装几种长度的锯条。
4、锯割方法(示范讲授)5、工件的夹持(1)工件应夹在台虎钳的左面,以便操作;(2)工件不应伸出钳口过长,锯缝距钳口侧面约20ΜΜ左右,防止产生振动;(3)锯缝线要与钳口侧面保持平行,便于控制锯缝不偏离划线线条;(4)紧要牢靠,同时要避免将工件夹变形和夹坏已加工面。
6、锯条安装。
安装锯条时,锯齿要朝前,不能反装。
锯条安装松紧要适当,太松或太紧在锯割过种中锯条都容易折断,太松还会在锯割时锯缝容易歪斜,一般松紧程度以两个手指的力旋紧为止。
车削加工实训报告答案
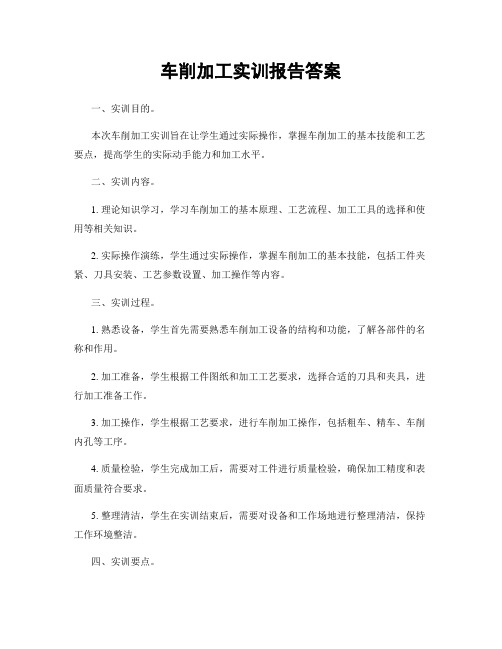
车削加工实训报告答案一、实训目的。
本次车削加工实训旨在让学生通过实际操作,掌握车削加工的基本技能和工艺要点,提高学生的实际动手能力和加工水平。
二、实训内容。
1. 理论知识学习,学习车削加工的基本原理、工艺流程、加工工具的选择和使用等相关知识。
2. 实际操作演练,学生通过实际操作,掌握车削加工的基本技能,包括工件夹紧、刀具安装、工艺参数设置、加工操作等内容。
三、实训过程。
1. 熟悉设备,学生首先需要熟悉车削加工设备的结构和功能,了解各部件的名称和作用。
2. 加工准备,学生根据工件图纸和加工工艺要求,选择合适的刀具和夹具,进行加工准备工作。
3. 加工操作,学生根据工艺要求,进行车削加工操作,包括粗车、精车、车削内孔等工序。
4. 质量检验,学生完成加工后,需要对工件进行质量检验,确保加工精度和表面质量符合要求。
5. 整理清洁,学生在实训结束后,需要对设备和工作场地进行整理清洁,保持工作环境整洁。
四、实训要点。
1. 安全第一,学生在实训过程中,必须严格遵守操作规程,正确佩戴防护用具,确保人身和设备安全。
2. 精益求精,学生在实际操作中,要注重加工精度和表面质量的控制,做到精益求精,不断提高加工水平。
3. 团队合作,学生在实训中要加强团队合作意识,互相协助,共同完成加工任务,培养团队精神。
五、实训效果。
通过本次车削加工实训,学生不仅掌握了车削加工的基本技能和工艺要点,还提高了实际动手能力和加工水平,为将来的工程实践打下了坚实的基础。
六、总结。
车削加工作为机械加工中常见的一种加工方式,对学生的实际操作能力和加工水平有着重要的影响。
通过本次实训,学生深刻理解了车削加工的原理和要点,掌握了基本的操作技能,为日后的学习和工作打下了坚实的基础。
希望学生能够在今后的学习和工作中,不断提升自己的技能,为祖国的机械制造事业做出更大的贡献。
金工实习车削实训报告范文

金工实习车削实训报告范文金工实习车削实训报告范文精选篇11、钳工实习因为此次的实习成果是做团队做一个实验室的大铁桌,而以往的学长们则做的是一个锤子,或许这两个物件的工艺流程也不一样吧,指导老师对我们的讲解格外详细,最重要的是在安全方面的知识。
第一天老师首先把实习期间的安全问题以及操作注意事项给我们说了一下,接着把钳工实习所涉及的所有理论知识告诉了我们。
最后,我们就进行了简单的工具使用练习。
钳工实习所要用的工具有:大锉刀、中锉刀、小锉刀、手锯、钢尺、游标卡尺、垂直度测量仪。
由于在理论知识讲解过程中老师就详细的给我们讲了锉刀如何使用,手如何放置,身体如何站立,包括与工作台的距离、角度等,还有手锯的如何使用,左右手放在什么位置,如何用力等知识,所以我们操作起来就觉得很省力、很自在。
在钳工工作中,涉及到英制单位及于公制单位的换算:1英寸约等于25.4毫米,1英尺为12英寸,1英寸为8英分,1英分为4角。
2、车工实习车加工所用的机器就是车床,所以,讲的理论主要内容就是车床各部分的使用。
由于是机器操作,所以,效率较高,工件加工需要时间很短。
所以,老师将大部分时间都放在了理论知识的讲解上。
车床由床身、床头箱、挂轮架、进给箱、光杠、丝杠、溜板箱、方刀架、卡盘、尾座、中心架、跟刀架等组成。
在讲到车刀时,老师将所有的车刀形状和名称告诉了我们。
车削加工刀具一般选用高速工具钢和硬质合金钢,以下列举了几种不同的刀具,分别为45°刀,90°刀,尖刀,方刀,内孔刀,根据加工工件的要求不同对刀具的使用不同。
不同刀具的主视图如下:3、铣工实习铣床的种类很多,有卧式铣床、立式铣床、工具铣床、龙门铣床、数控铣床,铣床的特点是刀具进行旋转运动,工件作水平或垂直直线运动。
铣床主要部件及附件的名称有床身、主轴、拉刀杆、横向工作台、纵向工作台、升降台、分度头、圆转盘、平口虎钳。
根据所加工零件要求不一,铣刀可分为立铣刀、三面刃铣刀、端铣刀、片铣刀、模数铣刀、和异型铣刀。
车削的实训报告

一、实训目的本次车削实训的主要目的是让学生了解和掌握车削加工的基本原理、操作方法和工艺要求,培养实际操作技能,提高对机械加工工艺的认识,为今后从事相关领域的工作打下基础。
二、实训内容1. 车削加工原理车削加工是利用车刀对工件进行切削,使其产生所需形状和尺寸的加工方法。
车削加工主要应用于加工轴类、盘类、套类等旋转表面和内外表面。
2. 车削加工设备实训过程中,我们主要使用的是C6132型卧式车床。
该机床具有以下特点:(1)结构简单,操作方便;(2)主轴转速范围广,可满足不同加工要求;(3)床身刚性好,稳定性好;(4)切削力大,加工精度高。
3. 车削加工工艺(1)加工前的准备工作1)检查机床各部件是否完好,润滑系统是否正常;2)安装刀具,调整刀具位置;3)装夹工件,调整工件位置;4)检查工件尺寸,确保加工精度。
(2)车削加工过程1)根据工件材料、形状和加工要求选择合适的刀具;2)调整刀具的切削深度、切削速度和进给量;3)启动机床,进行车削加工;4)观察加工过程,及时调整刀具位置和加工参数;5)加工完成后,检查工件尺寸和形状,确保加工精度。
4. 车削加工注意事项(1)安全操作:严格遵守机床操作规程,确保人身和设备安全;(2)刀具选用:根据工件材料、形状和加工要求选择合适的刀具;(3)加工参数:根据工件材料、形状和加工要求调整切削深度、切削速度和进给量;(4)装夹工件:确保工件装夹牢固,防止工件在加工过程中移动或变形;(5)观察加工过程:及时调整刀具位置和加工参数,确保加工精度。
三、实训过程1. 实训前,我们对机床的结构、操作规程和车削加工原理进行了学习和了解;2. 实训过程中,我们按照实训指导书的要求,进行了工件装夹、刀具安装、加工参数调整和车削加工等操作;3. 在实训过程中,我们遇到了一些问题,如刀具磨损、工件变形等,通过查阅资料和请教老师,我们解决了这些问题;4. 实训结束后,我们对加工的工件进行了检查,确保加工精度和形状符合要求。
车削加工螺纹零件实训报告

一、实训目的本次实训旨在使学生了解和掌握螺纹车削加工的基本原理、工艺方法及操作技能,培养学生的实际操作能力和工程实践能力。
通过实训,使学生能够熟练操作车床,完成螺纹零件的加工,并掌握螺纹加工的检验方法。
二、实训内容1.螺纹车削加工基本原理螺纹是圆柱或圆锥表面上的螺旋线,具有一定的螺旋升角和螺距。
螺纹车削加工是利用车刀在工件上旋转的同时,沿轴向进给,使刀具与工件产生相对运动,从而在工件上形成螺纹。
2.螺纹车削加工工艺方法(1)直进法:适用于中、小螺距的螺纹加工。
操作时,刀具以一定的切削深度和进给量切削工件,直至达到螺纹长度。
(2)左右切削法:适用于大螺距的螺纹加工。
操作时,刀具先向左切削,然后向右切削,直至达到螺纹长度。
(3)斜向切削法:适用于大螺距的螺纹加工。
操作时,刀具以一定的切削深度和进给量切削工件,同时使刀具与工件产生一定的倾斜角度,从而在工件上形成螺纹。
3.螺纹车削加工操作技能(1)安装刀具:根据螺纹规格选择合适的螺纹车刀,安装刀具时,使刀尖与工件旋转中心等高,刀尖角的平分线与工件轴线垂直。
(2)调整机床:根据工件螺距的大小,查找车床标牌,选定进给箱手柄位置,脱开光杆进给机构,改由丝杆传动。
选取较低的主轴转速,以便切削顺利,并有充分时间退刀。
(3)装夹工件:工件必须装夹牢固,以防加工过程中发生松动。
(4)操作方法:螺纹中径是靠控制多次进刀的总切深量来保证的。
车螺纹时每次切深量要小,而总切深量可根据计算的螺纹工作牙高(工作牙高0.54工件的螺距,单位为毫米),由中滑板刻度盘大致控制,并借助于螺纹量规来测量。
4.螺纹加工检验方法(1)螺纹中径:用螺纹千分尺或螺纹量规测量螺纹中径,应符合图纸要求。
(2)螺纹牙型:用螺纹量规或样板检查螺纹牙型,应符合图纸要求。
(3)螺纹螺距:用螺纹千分尺或螺纹量规测量螺纹螺距,应符合图纸要求。
(4)螺纹表面质量:观察螺纹表面,应无划痕、毛刺、裂纹等缺陷。
三、实训过程1.预习教材,了解螺纹车削加工的基本原理、工艺方法及操作技能。
车削实训报告步骤

一、实训准备1. 实训目的:通过车削实训,掌握车削加工的基本原理、操作方法和安全注意事项,提高动手能力和实际操作技能。
2. 实训要求:(1)熟悉车床的结构、性能和操作规程;(2)掌握车刀的种类、选用和使用方法;(3)了解工件装夹、定位和加工工艺;(4)学会使用常用量具进行尺寸测量。
3. 实训工具及材料:(1)车床:C6132型卧式车床;(2)工件:材料为45号钢;(3)刀具:外圆车刀、内孔车刀、切断刀、螺纹车刀等;(4)量具:卡尺、千分尺、角度尺等;(5)其他:夹具、扳手、油石等。
二、实训步骤1. 熟悉车床结构(1)观察车床外观,了解各部分名称及作用;(2)熟悉车床的操作面板,了解各按钮、开关、手柄的功能;(3)检查车床各部件是否完好,如有异常及时报告。
2. 工件装夹与定位(1)根据工件形状和加工要求选择合适的夹具;(2)按照夹具安装步骤将工件装夹在车床上;(3)调整工件位置,使其满足加工要求;(4)锁紧工件,确保加工过程中工件不会移动。
3. 刀具选用与安装(1)根据加工工件材料、形状和加工要求选择合适的刀具;(2)检查刀具质量,如有损坏及时更换;(3)按照刀具安装步骤将刀具安装在刀架上;(4)调整刀具位置,确保刀具与工件加工表面接触良好。
4. 车削加工(1)启动车床,调整主轴转速、进给速度和切削深度;(2)根据加工要求,选择合适的切削方式(如顺车、逆车等);(3)观察工件加工过程,确保加工质量;(4)根据加工情况进行刀具调整和工件位置调整。
5. 加工后检查(1)使用量具对加工后的工件进行尺寸测量;(2)检查工件加工质量,如表面粗糙度、形状精度等;(3)如有质量问题,分析原因并采取相应措施进行改进。
6. 清理与保养(1)清理加工后的工件,去除毛刺、切屑等;(2)清洗车床、刀具和量具,保持设备清洁;(3)检查设备磨损情况,及时更换磨损部件;(4)关闭车床电源,确保安全。
三、实训总结1. 通过本次实训,掌握了车削加工的基本原理、操作方法和安全注意事项;2. 提高了动手能力和实际操作技能,为今后的生产实践奠定了基础;3. 发现自身不足,如刀具选用、加工参数调整等方面,需要在今后的学习中加以改进。
工训实训报告车削

一、前言随着科技的不断进步和工业生产的日益发展,机械加工技术已成为我国制造业的核心竞争力之一。
车削作为机械加工中的一种基本加工方法,具有操作简便、加工精度高、生产效率高等优点,广泛应用于各种机械制造领域。
为了提高自己的动手能力和实际操作技能,我参加了本次工训实训,对车削加工进行了深入学习和实践。
二、实训目的1. 熟悉车削加工的基本原理和操作方法;2. 掌握车削加工中的刀具选择、切削参数的确定和工件装夹等技术要求;3. 培养良好的安全意识和团队协作精神;4. 提高自己的动手能力和实际操作技能。
三、实训内容1. 车削加工的基本原理车削加工是利用车床上的刀具对工件进行旋转切削,使其表面产生一定形状和尺寸的加工方法。
在车削过程中,刀具与工件之间的相对运动主要包括以下几种:(1)纵向进给运动:刀具沿工件轴向移动,实现切削;(2)横向进给运动:刀具沿工件径向移动,实现切削;(3)刀具旋转运动:刀具绕工件轴线旋转,实现切削。
2. 刀具选择与切削参数的确定(1)刀具选择:根据工件的材料、加工要求、车削精度和表面粗糙度等因素,选择合适的刀具。
常用的刀具包括:外圆车刀、端面车刀、螺纹车刀、内孔车刀等。
(2)切削参数的确定:切削参数主要包括切削深度、切削宽度、切削速度和进给量等。
切削参数的确定应遵循以下原则:①切削深度:切削深度应尽量减小,以降低切削力,提高加工质量;②切削宽度:切削宽度应适中,以保证加工表面质量;③切削速度:切削速度应适中,以保证加工效率和加工质量;④进给量:进给量应适中,以保证加工表面质量和刀具寿命。
3. 工件装夹工件装夹是车削加工的重要环节,直接影响到加工精度和表面质量。
工件装夹方法主要有以下几种:(1)三爪自定心卡盘装夹;(2)四爪卡盘装夹;(3)心轴装夹;(4)顶尖装夹。
4. 安全操作在车削加工过程中,应注意以下安全事项:(1)操作前,应熟悉车床的结构、性能和操作规程;(2)操作时,应穿戴好个人防护用品,如安全帽、工作服、手套等;(3)操作过程中,严禁将手、脚伸入机床工作区域;(4)操作结束后,应关闭机床电源,清理现场。
- 1、下载文档前请自行甄别文档内容的完整性,平台不提供额外的编辑、内容补充、找答案等附加服务。
- 2、"仅部分预览"的文档,不可在线预览部分如存在完整性等问题,可反馈申请退款(可完整预览的文档不适用该条件!)。
- 3、如文档侵犯您的权益,请联系客服反馈,我们会尽快为您处理(人工客服工作时间:9:00-18:30)。
本页面为作品封面,下载文档后可自由编辑删除! 实习报告 • • •
• • • 位 名 间 单
二.实验目的
1、了解数控车床的编程特点,掌握数控车床车削加工编程步骤。
2、掌握G92设定工件坐标系的方法。
3、熟练掌握车削加工零件的数控程序编制方法。
三.实验设备
1、C K400Q型数控车床一台;
2、车刀一把;
3、铝棒工件一根;
4、毛刷一把。
四•实验步骤
1、了解CK-400Q型数控车床的主要结构布置
(1)工件安装
工件安装:利用三爪卡盘钥匙拧开卡盘,送入工件的部分,留出适当的长度,再用钥匙拧紧卡盘,卡住工件,必要时可采用加力杆进行加力拧紧。
取出工件,同样也是如此操作,按照上面的方法,可以将工件夹紧,完成工件的安装。
(2)刀具安装
刀具安装:数控车床的刀具安装跟普通车床的刀具安装类似,都是利用螺钉将刀具压紧在四方刀架上,卡住数控车床车刀至少要用两个螺钉,并轮流逐个拧紧,拧紧力量要适当。
(3)对刀操作
对刀操作:通过刀具试触切削工件样品棒料边缘,读入相应位置坐标,可以得出相应的X、Z轴的对刀零点,载入相应数据到控制面板,完成机床的工件坐标零点设置。
2、数控系统操作面板的熟悉及操作。
(1)机床MDI操作
MDI操作是可以简单输入编程指令,运行机床,试看机床对刀或者检测编程的正确安全性。
(2)主轴转速调节
主轴转速可以通过右边的旋钮调节对应转速。
(3)机床坐标移动的正确操作方法。
可以通过转动手轮或者使用数控面板上X/Z按键。
3、编写零件加工程序
在车床控制面板中新建一个程序名,将需要加工的零件程序编写到控制面板内。
T0101 M03 S400
G00X38.0Z1.0
G71U1.0R0.5
G71P10Q20U0.4W0.2F0.1
N10G01X0.0
G01Z0.0
G03X28.0Z14.0R14.0
G01Z30.0
G01X30.0
Z- 51.0
G01X34.0
乙55.0N20G01X38.0
G00X100.0Z100.0
S450F0.05
G00X38.0Z1.0
G70P10Q20
G00X150.0
G00Z100.0
4、程序检测
可以通过程序自带的模拟仿真软件,检测程序运行的安全性。
或者运用单段点动试运行程序,测试刀具与工件或床体是否干涉。
5、执行程序
进行程序检测,确定无误后,将刀具移动到安全位置,即可点击程序运行按钮,运行程序。
6加工结束后的清理工作
程序结束后,机床停止运动,完成零件加工。
零件加工完成后,应将切屑废料打扫倒回垃圾回收处,并使用气枪与毛刷进行机床的清理工作,以备下次机床的使用。
7、实验训练结果
通过以上实验步骤,我们组进项
了数控车床的车削操作实验。
实验训练的实验样品实物图如
下图所示。
车笊榄丽仿黛图车削UZL黑籾
图
车削产品
五•实验总结
通过此次数控车床加工实验操作训练,我初步了解了CK400Q型数控车床的
基本组成与操作,在老师悉心的指导下,我们学会了数控车床的基本操作,还巩固了编程,最关键的是学会了怎样对刀。
将课堂学习的数控车床加工零件编程程序与实际数控车床加工操作结合训练,对G指令、M指令、T指令、S指令的含义和基本应用更加熟练,更加清晰的认识了数控车床。
对于数控技术这门课程也有了更加清晰的认识。
在训练操作的过程中,我发现细心和耐心对于数控加工很重要,如果稍有不慎,加工工件的时候就会产生撞车,崩刀断刀,工件报废,重则人员受伤。
所以实验是对我们的耐心和细心的考验,也是增加我们经验的最重要的时刻。
安全确是第一位。
实验教学时老师讲得最多的还是安全操作。
这要求我们对每一步都十分的了解,才能做到万无一失。
细心并不表示要我们畏首畏尾,机床操作过程中需要我们在安全的前提下,大胆操作,只有反复的多次练习,才能真的学会数控机床的操作。