可行性分析报告案例
工程项目可行性研究报告案例5篇
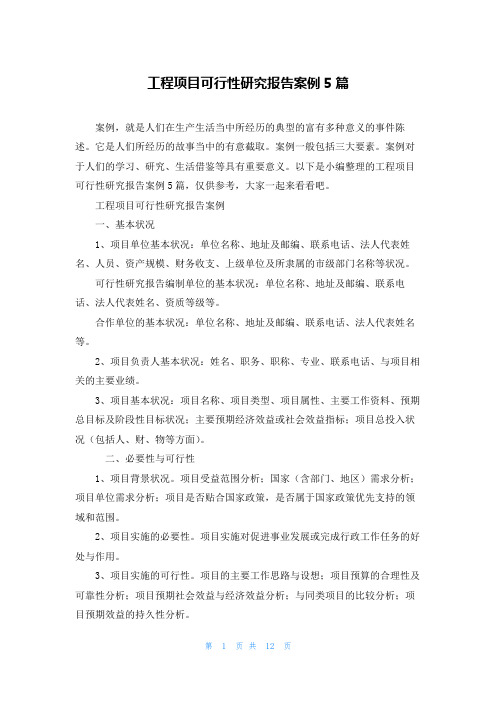
工程项目可行性研究报告案例5篇案例,就是人们在生产生活当中所经历的典型的富有多种意义的事件陈述。
它是人们所经历的故事当中的有意截取。
案例一般包括三大要素。
案例对于人们的学习、研究、生活借鉴等具有重要意义。
以下是小编整理的工程项目可行性研究报告案例5篇,仅供参考,大家一起来看看吧。
工程项目可行性研究报告案例一、基本状况1、项目单位基本状况:单位名称、地址及邮编、联系电话、法人代表姓名、人员、资产规模、财务收支、上级单位及所隶属的市级部门名称等状况。
可行性研究报告编制单位的基本状况:单位名称、地址及邮编、联系电话、法人代表姓名、资质等级等。
合作单位的基本状况:单位名称、地址及邮编、联系电话、法人代表姓名等。
2、项目负责人基本状况:姓名、职务、职称、专业、联系电话、与项目相关的主要业绩。
3、项目基本状况:项目名称、项目类型、项目属性、主要工作资料、预期总目标及阶段性目标状况;主要预期经济效益或社会效益指标;项目总投入状况(包括人、财、物等方面)。
二、必要性与可行性1、项目背景状况。
项目受益范围分析;国家(含部门、地区)需求分析;项目单位需求分析;项目是否贴合国家政策,是否属于国家政策优先支持的领域和范围。
2、项目实施的必要性。
项目实施对促进事业发展或完成行政工作任务的好处与作用。
3、项目实施的可行性。
项目的主要工作思路与设想;项目预算的合理性及可靠性分析;项目预期社会效益与经济效益分析;与同类项目的比较分析;项目预期效益的持久性分析。
4、项目风险与不确定性。
项目实施存在的主要风险与不确定分析;对风险的应对措施分析。
三、实施条件1、人员条件。
项目负责人的组织管理潜力;项目主要参加人员的姓名、职务、职称、专业、对项目的熟悉状况。
2、资金条件。
项目资金投入总额及投入计划;对财政预算资金的需求额;其他渠道资金的来源及其落实状况。
3、基础条件。
项目单位及合作单位完成项目已经具备的基础条件(重点说明项目单位及合作单位具备的设施条件,需要增加的关键设施)。
可行性分析报告范文(精选15篇)
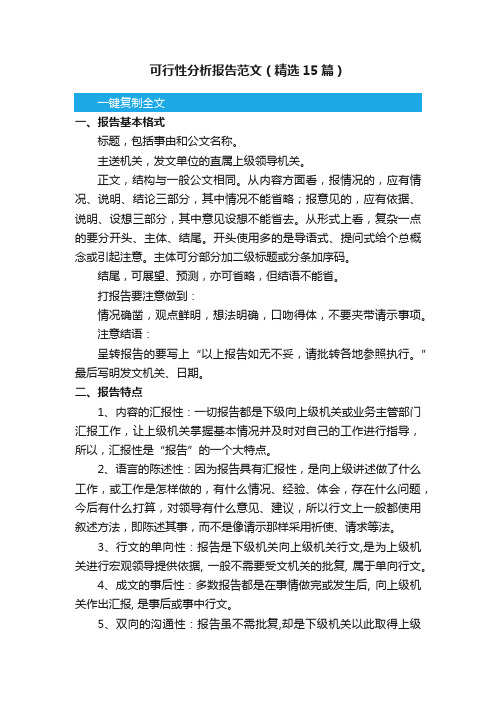
可行性分析报告范文(精选15篇)一、报告基本格式标题,包括事由和公文名称。
主送机关,发文单位的直属上级领导机关。
正文,结构与一般公文相同。
从内容方面看,报情况的,应有情况、说明、结论三部分,其中情况不能省略;报意见的,应有依据、说明、设想三部分,其中意见设想不能省去。
从形式上看,复杂一点的要分开头、主体、结尾。
开头使用多的是导语式、提问式给个总概念或引起注意。
主体可分部分加二级标题或分条加序码。
结尾,可展望、预测,亦可省略,但结语不能省。
打报告要注意做到:情况确凿,观点鲜明,想法明确,口吻得体,不要夹带请示事项。
注意结语:呈转报告的要写上“以上报告如无不妥,请批转各地参照执行。
”最后写明发文机关、日期。
二、报告特点1、内容的汇报性:一切报告都是下级向上级机关或业务主管部门汇报工作,让上级机关掌握基本情况并及时对自己的工作进行指导,所以,汇报性是“报告”的一个大特点。
2、语言的陈述性:因为报告具有汇报性,是向上级讲述做了什么工作,或工作是怎样做的,有什么情况、经验、体会,存在什么问题,今后有什么打算,对领导有什么意见、建议,所以行文上一般都使用叙述方法,即陈述其事,而不是像请示那样采用祈使、请求等法。
3、行文的单向性:报告是下级机关向上级机关行文,是为上级机关进行宏观领导提供依据, 一般不需要受文机关的批复, 属于单向行文。
4、成文的事后性:多数报告都是在事情做完或发生后, 向上级机关作出汇报, 是事后或事中行文。
5、双向的沟通性:报告虽不需批复,却是下级机关以此取得上级机关的支持指导的桥梁;同时上级机关也能通过报告获得信息, 了解下情, 报告成为上级机关决策指导和协调工作的依据。
三、可行性分析报告范文(精选15篇)在经济发展迅速的今天,报告的使用频率呈上升趋势,其在写作上有一定的技巧。
我敢肯定,大部分人都对写报告很是头疼的,以下是小编为大家整理的可行性分析报告范文(精选15篇),欢迎大家借鉴与参考,希望对大家有所帮助。
最新建设工程可行性研究报告案例(精选3篇)
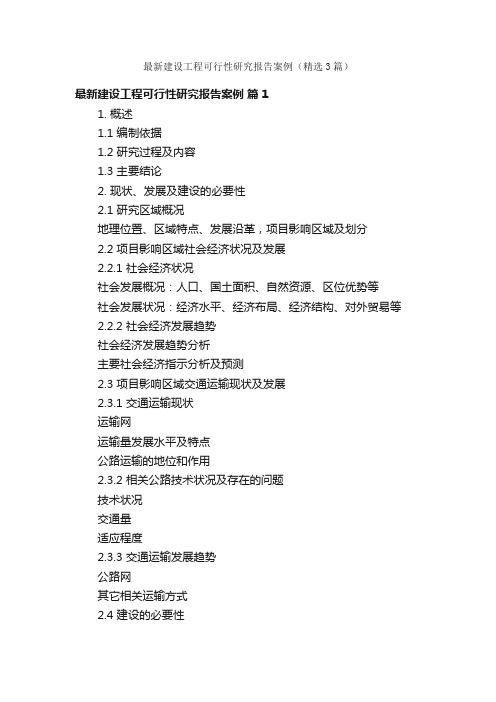
最新建设工程可行性研究报告案例(精选3篇)最新建设工程可行性研究报告案例篇11. 概述1.1 编制依据1.2 研究过程及内容1.3 主要结论2. 现状、发展及建设的必要性2.1 研究区域概况地理位置、区域特点、发展沿革,项目影响区域及划分2.2 项目影响区域社会经济状况及发展2.2.1 社会经济状况社会发展概况:人口、国土面积、自然资源、区位优势等社会发展状况:经济水平、经济布局、经济结构、对外贸易等2.2.2 社会经济发展趋势社会经济发展趋势分析主要社会经济指示分析及预测2.3 项目影响区域交通运输现状及发展2.3.1 交通运输现状运输网运输量发展水平及特点公路运输的地位和作用2.3.2 相关公路技术状况及存在的问题技术状况交通量适应程度2.3.3 交通运输发展趋势公路网其它相关运输方式2.4 建设的必要性3. 交通分析及预测3.1 公路交通调查及分析3.1.1 调查综述公路交通调查内容、方法、范围3.1.2 调查资料分析相关公路的交通量构成、分布特点交通运行特征运输效率及主要运输货类等3.2 其它运输方式相关线路的调查与分析3.2.1 调查概述3.2.2 资料分析3.3 预测思路与方法3.3.1 交通量预测的总体思路3.3.2 交通量预测方法及步骤概述3.4 交通量预测3.4.1 特征年路网范围路段参数3.4.2 交通生成模型标定未来交通增长3.4.3 交通分布模型标定未来交通量分布3.4.4 诱增交通需求及其他运输方式转移量的初步估计3.4.5 交通分配分配方法分配方案分配结果及分析4.建设条件、技术标准、初步方案及建设规模4.1 建设条件4.1.1 地形、地质、水文等条件4.1.2 筑路材料及运输条件4.1.3 社会环境4.1.4 拟建项目与其他交通衔接情况4.2 工程环境影响4.3 技术标准4.4 建设方案4.4.1 建设项目起讫点论证4.4.2 方案主要控制因素及可能的路线方案4.4.3 建设方案比较4.4.4 推荐方案工程概况和建设规模4.4.5 建设项目实施意见最新建设工程可行性研究报告案例篇2由XX市东胜区发展和改革局主持,在XX市召开了《富兴花园三期工程建设项目可行性研究报告》专家咨询评估会议。
项目可行性分析报告范文三篇

项目可行性分析报告范文三篇篇一:旅游在线预订系统可行性分析报告一、项目背景随着旅游业的发展,越来越多的人开始选择出行,因此旅游在线预订系统已成为各大旅游企业必备的工具之一。
现阶段市面上已有众多的旅游在线预订系统,但大多数存在运营费用高、对后期维护要求高等问题,因此对于一些小型旅游企业而言,想要拥有一套成本低、高效率的旅游在线预订系统,具有很大的市场需求。
二、项目概述该项目旨在开发一套旅游在线预订系统,该系统能为旅游企业提供基本的预订、支付、订单查询、用户评价等功能。
并且,我们将尽力降低系统的运营成本,使其适应大多数小型旅游企业的需要。
三、市场分析1、适用于多种旅游企业旅游在线预订系统适用于各种不同类型的旅游企业,如酒店、旅行社等。
2、更加发达的旅游市场近年来,我国旅游市场持续发展,预计未来还会有较大的发展空间。
3、更加方便的客户体验旅游在线预订系统可以提供更加方便快捷的客户体验,让用户更加愿意选择在线预订。
四、竞争分析目前市场上已经有大量的旅游在线预订系统,如携程、去哪儿等,这些系统都已经走向成熟,具有很高的用户黏性和品牌知名度。
但与之相比,我们的系统具有运营成本低、开发周期短等优势。
五、技术选择我们将采用Java EE技术,使用MySQL数据库进行数据存储,前端部分采用Vue.js进行开发。
六、项目可行性1、市场可行性:旅游市场处于持续发展中,旅游在线预订系统具有很大的市场需求。
2、经济可行性:在较低的开发成本下,项目可为旅游企业带来稳定收益。
3、技术可行性:开发所需的技术已经十分成熟,能够保证该项目的开发进程。
七、项目风险1、市场风险:由于市场竞争激烈,项目可能会受到同类竞争对手的压力。
2、技术风险:如果团队成员技术能力不足,可能会导致开发周期延长。
3、资金风险:如果项目资金不足,开发可能会受到一定的限制。
八、总结在目前激烈的竞争市场中,我们所开发的旅游在线预订系统具有很大的市场需求和经济意义。
产品可行性分析报告

产品可行性分析报告产品可行性分析报告是一种针对新产品进行商业评估的报告。
该报告涉及的内容包括市场调研、成本分析、竞争分析、销售预测等。
通过对这些数据的分析,可以确定产品是否有市场潜力,以及是否具有商业可行性和利润空间。
以下将分别以三个案例来说明产品可行性分析报告的重要性。
案例一:智能马桶盖智能马桶盖是一种可以自动开启、保温、照明、加湿等功能的马桶盖。
公司开发该产品的初衷是提升用户的生活质量。
在进行产品可行性分析报告之前,公司进行了市场调研,得出了以下数据:1)目前市场上的智能马桶盖品牌较少,但需求量逐渐增加;2)该产品价格偏高,但用户对品质要求较高;3)该产品目标用户群体为高收入人群和老年人群。
基于这些数据,公司进行了成本分析,初步测算出生产成本、销售价格和利润空间。
基于以上数据的综合分析,公司决定推出智能马桶盖产品,市场反应显著,该产品在市场上获得了成功。
案例二:创意T恤创意T恤是一种以创意为主题的T恤。
通过设计独特的图案、标语或图案,以吸引年轻人群体的目光。
在进行产品可行性分析报告之前,公司进行了市场调研,得出了以下数据:1)年轻人群体愿意购买创新、时尚的产品;2)近年来,创意T恤市场需求量逐渐增加;3)创意T恤的价格较普通T恤高出一些。
基于这些数据,公司进行了成本分析,初步测算出生产成本、销售价格和利润空间。
基于以上数据的综合分析,公司决定开发和生产创意T恤,市场反应一般。
案例三:跨境电商平台跨境电商平台是一种可以让国内用户购买海外商品的在线平台。
在进行产品可行性分析报告之前,公司进行了市场调研,得出了以下数据:1)国内用户购买海外商品的需求量逐渐增加;2)跨境电商平台品牌市场较少,但存在较大的市场空间;3)该产品主要面向中高收入人群。
基于这些数据,公司进行了成本分析,初步测算出生产成本、销售价格和利润空间。
基于以上数据的综合分析,公司决定开发和生产跨境电商平台,市场反应良好。
综上所述,产品可行性分析报告是一种对新产品进行商业评估的重要工具,通过对市场调研、成本分析、竞争分析、销售预测等数据进行综合分析,可以准确把握市场需求,确保产品的商业可行性和稳定的利润空间。
可行性财务分析报告范文(3篇)

第1篇一、项目概述项目名称:XX智能制造业生产基地建设项目项目地点:XX省XX市XX区项目业主:XX科技有限公司项目投资估算:人民币XX亿元项目投资资金来源:自筹资金、银行贷款项目预计建设周期:XX个月项目预计投产时间:XX年XX月二、项目背景及必要性随着我国经济的快速发展和产业结构的不断优化升级,智能制造业已成为国家战略新兴产业的重要组成部分。
为响应国家号召,推动地区经济发展,XX科技有限公司拟在XX市XX区建设一座智能制造业生产基地。
该项目旨在提高我国智能制造业的自主创新能力,降低生产成本,提升产品竞争力。
通过建设现代化生产基地,公司可以实现生产规模的扩大、生产效率的提升以及产品质量的保证,从而在激烈的市场竞争中占据有利地位。
三、市场分析1. 市场需求分析根据XX省及全国智能制造业的发展趋势,预计未来几年我国智能制造业市场规模将保持高速增长。
随着5G、物联网、大数据等新技术的应用,智能制造业将迎来更加广阔的市场空间。
2. 竞争分析目前,我国智能制造业市场竞争激烈,国内外知名企业纷纷加大研发投入,抢占市场份额。
本项目将通过引进先进技术和设备,提高产品技术含量,降低生产成本,以应对激烈的市场竞争。
3. 风险分析(1)市场需求风险:若市场需求不及预期,可能导致项目产品滞销,影响投资回报。
(2)技术风险:随着技术更新换代速度加快,项目所采用的技术可能面临被淘汰的风险。
(3)政策风险:国家产业政策调整可能对项目产生不利影响。
四、项目实施方案1. 建设规模项目总占地面积XX万平方米,建设内容包括生产车间、研发中心、办公楼、仓储物流中心等。
2. 生产工艺采用国际先进的生产工艺,确保产品质量和生产效率。
3. 设备选型引进国内外知名品牌的先进设备,提高生产自动化程度。
4. 人员配置根据生产需求,招聘各类专业技术人才和管理人员。
五、财务分析1. 投资估算(1)固定资产投资:人民币XX亿元(2)流动资金:人民币XX亿元(3)建设期利息:人民币XX亿元(4)其他费用:人民币XX亿元总计:人民币XX亿元2. 资金筹措(1)自筹资金:人民币XX亿元(2)银行贷款:人民币XX亿元3. 财务指标(1)投资回收期:XX年(2)内部收益率:XX%(3)净现值:XX亿元4. 盈利能力分析(1)销售收入:预计XX亿元(2)成本费用:预计XX亿元(3)利润总额:预计XX亿元(4)净利润:预计XX亿元六、风险防范措施1. 市场风险防范加强市场调研,密切关注市场动态,调整产品结构,提高产品竞争力。
可行性分析报告范文
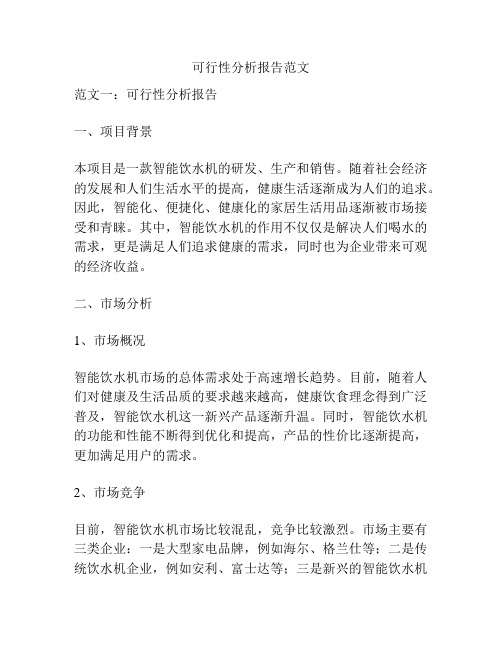
可行性分析报告范文范文一:可行性分析报告一、项目背景本项目是一款智能饮水机的研发、生产和销售。
随着社会经济的发展和人们生活水平的提高,健康生活逐渐成为人们的追求。
因此,智能化、便捷化、健康化的家居生活用品逐渐被市场接受和青睐。
其中,智能饮水机的作用不仅仅是解决人们喝水的需求,更是满足人们追求健康的需求,同时也为企业带来可观的经济收益。
二、市场分析1、市场概况智能饮水机市场的总体需求处于高速增长趋势。
目前,随着人们对健康及生活品质的要求越来越高,健康饮食理念得到广泛普及,智能饮水机这一新兴产品逐渐升温。
同时,智能饮水机的功能和性能不断得到优化和提高,产品的性价比逐渐提高,更加满足用户的需求。
2、市场竞争目前,智能饮水机市场比较混乱,竞争比较激烈。
市场主要有三类企业:一是大型家电品牌,例如海尔、格兰仕等;二是传统饮水机企业,例如安利、富士达等;三是新兴的智能饮水机企业,例如华为、小米等。
这些企业的竞争优势不同,例如大型家电品牌有雄厚的资金和品牌优势,传统饮水机企业有丰富的经验和销售渠道,而新兴智能饮水机企业则有技术创新和品牌价值等优势。
3、市场前景随着我国健康市场的发展和人们健康意识的提高,智能饮水机市场有望保持高速增长,预计未来三年市场规模将增长30%以上。
同时,智能饮水机将朝着更加智能、便捷、健康的方向发展,未来具有广阔的发展空间。
三、技术可行性智能饮水机采用多种技术实现,主要包括:物联网、传感器、高效过滤技术、蓝牙连接等。
这些技术均已成熟,可以保证产品的稳定性和可靠性。
同时,随着科技的不断发展,新的技术将不断涌现,为产品的创新和升级提供新的技术支持和技术保证。
四、资金可行性本项目需要投入的资金主要包括:研发费用、生产成本、销售费用和市场推广费用等。
根据市场调查和分析,预计本项目的总投资将达到500万元。
同时,根据市场分析,预计未来三年的市场销售额将达到8000万元以上,具有良好的收益情况。
五、市场策略本项目的市场策略主要包括以下几个方面:一是要提高产品质量和性价比,保证顾客的满意度;二是要加强品牌力度,提高市场占有率;三是要拓展销售渠道,增加销售额;四是要注重售后服务,提升品牌口碑和用户体验。
可行性分析报告范文(通用5篇)

可行性分析报告范文(通用5篇)第一条为了加强饮用水水源保护,保障饮用水安全,维护公众健康,推进生态文明建设,促进经济社会与环境协调发展,根据《中华人民共和国环境保护法》《中华人民共和国水法》《中华人民共和国水污染防治法》《饮用水水源保护区污染防治管理规定》和国家有关规定,结合本市实际,制定本办法。
第二条本市行政区域内集中式供水的饮用水水源保护区环境保护管理,适用本办法。
第三条本市实行饮用水水源保护区制度。
饮用水水源保护区,分为一级保护区、二级保护区、准保护区。
第四条饮用水水源保护区环境保护管理,坚持政府主导、公众参与、预防为主、防治结合、属地监管、综合治理原则。
第五条市、县区人民政府领导本行政区域内饮用水水源保护区环境保护管理工作,对饮用水水源保护区环境质量负责。
市、县区生态环境部门对本行政区域内饮用水水源保护区环境保护工作实施统一监督管理。
市、县区水务、住建、卫生健康、畜牧兽医、农业农村、林草、自然资源、交通运输等部门,在各自职责范围内,依照有关法律、法规、规章规定对本行政区域内饮用水水源保护区资源保护和污染防治等环境保护工作实施监督管理。
乡镇人民政府依法履行乡镇饮用水水源保护区环境保护管理职责,配合有关部门做好辖区内饮用水水源保护区环境保护管理工作。
第六条市、县区人民政府建立饮用水水源保护区环境保护协调联动工作机制,实行信息资源共享和重大事项会商制度。
第七条饮用水水源保护区环境保护管理工作,应当纳入市、县区国民经济和社会发展规划,所需经费列入同级财政预算。
第八条市、县区人民政府应当综合平衡饮用水水源使用、保护等各方利益,建立饮用水水源保护区水环境生态保护补偿机制。
第九条市、县区饮用水水源保护区环境保护管理相关部门、乡镇人民政府,应当加强饮用水水源保护区环境保护法律、法规、规章宣传,提高公众环境保护意识,鼓励、引导公众积极参与饮用水水源保护区环境保护。
第十条任何组织和个人有义务保护饮用水水源保护区环境,有权利对污染和破坏饮用水水源保护区环境的行为进行监督和举报。
可行性研究报告分析案例范文

可行性研究报告分析案例范文一、项目概述随着社会经济的快速发展和科技进步,人们的生活水平不断提高,对于居住环境的要求也越来越高。
在这个大背景下,我公司决定开发一种智能家居系统,旨在为用户提供更便捷、舒适的居住体验,同时提升生活质量。
该系统将针对家庭、办公室、商业场所等不同场景,具有远程控制、自动化调节、安全监控等多种功能,能够智能化管理和优化居住环境。
二、市场分析1. 行业现状:目前,智能家居系统已经成为一个热门的发展趋势,得到了广泛的应用。
许多公司和企业已经推出了各种智能家居产品,包括智能灯具、智能门锁、智能安防系统等。
消费者对于智能家居产品的需求也在逐渐增加,市场前景广阔。
2. 竞争分析:在智能家居领域,竞争对手众多,主要包括国内外知名企业,如小米、华为、亚马逊等。
这些企业在产品研发、市场推广等方面都具有较大优势。
但是,我们相信通过自身的技术实力和服务质量,能够在激烈的市场竞争中取得一席之地。
3. 潜在用户:智能家居系统的用户群体主要包括有一定的消费能力、追求生活品质的家庭、企业和商业场所。
根据市场调研数据显示,目前国内智能家居市场规模巨大,潜在用户数量庞大,具有良好的发展潜力。
三、项目可行性分析1. 技术可行性:作为一个新兴的行业,智能家居系统的技术发展空间广阔。
我公司已经拥有一支技术实力雄厚的研发团队,具有丰富的研发经验和创新能力。
我们能够应用先进的科技,研发出高性能、稳定可靠的智能家居系统。
2. 市场可行性:通过对市场的深入调研和分析,我们发现智能家居系统的市场需求量大,市场潜力巨大。
消费者对于智能家居产品的认知度逐渐增加,对于产品的功能和质量要求也更加追求。
因此,我们相信在市场上具有良好的发展前景。
3. 经济可行性:项目的投资成本主要包括研发成本、生产成本和市场推广成本等。
通过对投资回报率的测算和分析,我们认为项目的经济收益将会高于投资成本,具有一定的盈利空间。
同时,我们也将采取有效的成本控制和管理措施,确保项目的经济效益。
可行性研究报告案例
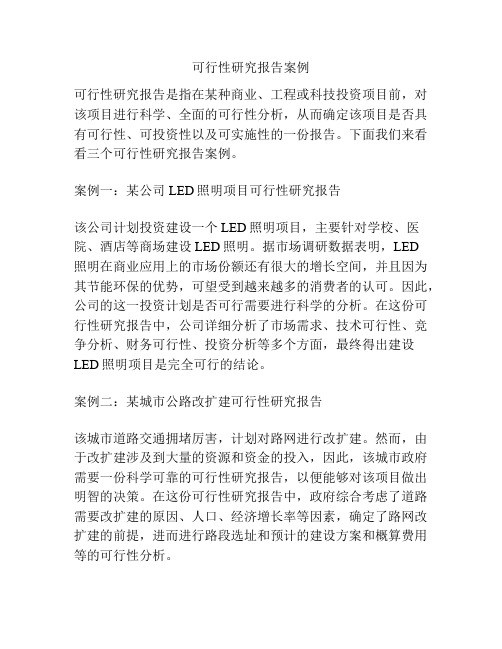
可行性研究报告案例可行性研究报告是指在某种商业、工程或科技投资项目前,对该项目进行科学、全面的可行性分析,从而确定该项目是否具有可行性、可投资性以及可实施性的一份报告。
下面我们来看看三个可行性研究报告案例。
案例一:某公司LED照明项目可行性研究报告该公司计划投资建设一个LED照明项目,主要针对学校、医院、酒店等商场建设LED照明。
据市场调研数据表明,LED照明在商业应用上的市场份额还有很大的增长空间,并且因为其节能环保的优势,可望受到越来越多的消费者的认可。
因此,公司的这一投资计划是否可行需要进行科学的分析。
在这份可行性研究报告中,公司详细分析了市场需求、技术可行性、竞争分析、财务可行性、投资分析等多个方面,最终得出建设LED照明项目是完全可行的结论。
案例二:某城市公路改扩建可行性研究报告该城市道路交通拥堵厉害,计划对路网进行改扩建。
然而,由于改扩建涉及到大量的资源和资金的投入,因此,该城市政府需要一份科学可靠的可行性研究报告,以便能够对该项目做出明智的决策。
在这份可行性研究报告中,政府综合考虑了道路需要改扩建的原因、人口、经济增长率等因素,确定了路网改扩建的前提,进而进行路段选址和预计的建设方案和概算费用等的可行性分析。
案例三:某新型能源设备可行性研究报告某公司开发了一种新型能源设备,可以将光能、风能等清洁能源转化为电力。
为了确定该新型能源设备的市场前景和商业价值,公司委托一家专业的研究机构进行可行性研究。
在这份可行性研究报告中,研究机构详细分析了新型能源设备的市场需求、技术可行性、竞争分析、财务可行性、投资分析等因素,根据分析结果得出了该新型能源设备的可行性结论,并给出了进一步开发的建议。
总之,可行性研究报告在项目决策中起到了至关重要的作用,能够帮助企业和政府明确目标和方向,为决策提供有力的依据。
通过这三个案例,我们可以看出可行性研究报告是一个全面、科学的可行性分析,不仅仅是对市场需求、技术可行性、竞争分析、财务可行性、投资分析等单一方面进行研究,还需要研究这些因素的相互关系和对项目的影响。
项目可行性分析报告范文(三篇)

项目可行性分析报告范文(三篇)项目可行性分析报告范本一、一、项目背景本项目旨在分析并评估项目的可行性,以确定这个项目能否在技术、市场、财务和管理等方面达到预期的目标。
二、项目概述项目是一个,主要目标是。
项目计划在地区进行,预计实施周期为。
三、技术可行性分析1、技术方案评估:分析现有技术方案是否能够达到项目目标,并评估其可行性和可靠性。
2、技术实施能力:评估实施团队的技术能力和资源配备是否满足项目需求。
3、技术风险评估:识别可能存在的技术风险,并制定相应的风险应对措施。
四、市场可行性分析1、市场需求评估:分析目标市场的需求情况,确定项目的市场容量和潜在用户规模。
2、竞争分析:评估竞争对手的实力和市场份额,并确定项目在市场上的竞争优势。
3、市场推广策略:制定项目的市场推广策略,包括市场定位、销售渠道等方面的考虑。
五、财务可行性分析1、投资评估:评估项目投资规模和资金需求,并对项目的收益进行预测和分析。
2、资金筹措:提出项目资金筹措的途径和方式,并进行风险评估。
3、财务指标分析:分析项目的投资回报率、财务风险等财务指标,以评估项目的可行性。
六、管理可行性分析1、组织架构设计:设计项目的组织架构,并明确各岗位职责和权限。
2、人力资源管理:评估项目所需的人力资源和培训需求,并制定相应的人力资源管理策略。
3、项目管理计划:制定项目的详细工作计划和进度安排,包括项目启动、执行、控制和收尾等各个阶段的管理。
七、法律法规及注释1、法律名词:- 注释:2、法律名词:- 注释:(以此类推,列出本文所涉及的法律名词及注释)附件:1、附件一、2、附件二、3、附件三、(列出涉及的附件)----------------------------------------------------------------------------------项目可行性分析报告范本二、一、项目背景本项目旨在分析并评估项目的可行性,以确定这个项目能否在技术、市场、财务和管理等方面达到预期的目标。
可行性研究报告案例
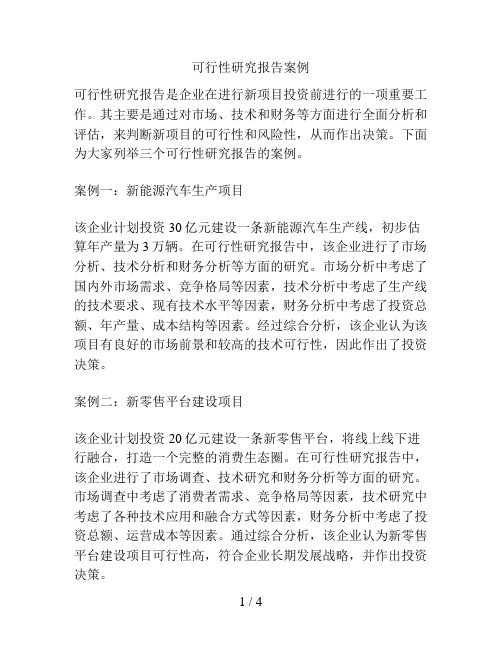
可行性研究报告案例可行性研究报告是企业在进行新项目投资前进行的一项重要工作。
其主要是通过对市场、技术和财务等方面进行全面分析和评估,来判断新项目的可行性和风险性,从而作出决策。
下面为大家列举三个可行性研究报告的案例。
案例一:新能源汽车生产项目该企业计划投资30亿元建设一条新能源汽车生产线,初步估算年产量为3万辆。
在可行性研究报告中,该企业进行了市场分析、技术分析和财务分析等方面的研究。
市场分析中考虑了国内外市场需求、竞争格局等因素,技术分析中考虑了生产线的技术要求、现有技术水平等因素,财务分析中考虑了投资总额、年产量、成本结构等因素。
经过综合分析,该企业认为该项目有良好的市场前景和较高的技术可行性,因此作出了投资决策。
案例二:新零售平台建设项目该企业计划投资20亿元建设一条新零售平台,将线上线下进行融合,打造一个完整的消费生态圈。
在可行性研究报告中,该企业进行了市场调查、技术研究和财务分析等方面的研究。
市场调查中考虑了消费者需求、竞争格局等因素,技术研究中考虑了各种技术应用和融合方式等因素,财务分析中考虑了投资总额、运营成本等因素。
通过综合分析,该企业认为新零售平台建设项目可行性高,符合企业长期发展战略,并作出投资决策。
案例三:物流中心建设项目该企业计划在国内主要城市投资30亿元建设多个物流中心,实现快速、高效的物流配送。
在可行性研究报告中,该企业进行了市场调查、技术研究和财务分析等方面的研究。
市场调查中考虑了物流需求情况、物流市场状况等因素,技术研究中考虑了物流中心的建设方式、技术设计等因素,财务分析中考虑了投资总额、成本结构等因素。
通过综合分析,该企业认为物流中心建设项目有较高的市场需求和技术可行性,并作出投资决策。
综上可得,可行性研究报告是企业决策的重要依据,具有重要的指导和决策价值,对企业的发展和利润增长具有重要的推动作用。
同时,在进行可行性研究报告时,需要注意以下几点:1. 全面的市场调查,包括行业状况、市场趋势、竞争格局等方面的内容。
可行性研究报告案例

可行性研究报告案例可行性研究报告案例一、项目背景某市政府希望建设一个人工智能产业园区,促进本地人工智能产业的发展。
该园区将提供办公、研发、生产等基础设施,并吸引人工智能企业入驻。
现委托我公司对该项目进行可行性研究,评估其是否具备实施条件。
二、项目概述1. 项目目标:建设一个专门服务人工智能企业的产业园区。
2. 项目规模:占地面积约500亩,包括办公楼、实验室、生产车间、住宅区等功能区。
3. 项目内容:提供办公、研发、生产等基础设施,并提供相关服务支持,如人才引进、技术培训等。
三、市场分析1. 行业发展:人工智能产业近年来快速发展,市场需求旺盛。
2. 竞争现状:其他地区已有不少人工智能产业园区,但本地尚无。
3. 人才储备:本地拥有一定的人工智能相关人才储备。
四、技术分析1. 技术实力:本地拥有多家人工智能企业,具备自主研发能力。
2. 技术合作:可与高校、科研机构合作,共享资源,提高技术水平。
3. 技术保障:既有的基础设施完善程度较高,有利于人工智能技术的应用和发展。
五、投资分析1. 建设投资:初步估计建设投资约10亿元,包括土地购置、基础设施建设、相关设备采购等。
2. 运营后收入:根据入驻企业数量和租金收入预测,预计年收入约为3000万元。
3. 成本分析:预计年运营成本约为2000万元,包括基础设施维护费用、人力成本等。
六、可行性分析1. 市场可行性:由于市场需求旺盛,且本地尚无人工智能产业园区,因此项目具备较好的市场潜力。
2. 技术可行性:本地拥有一定的人工智能人才储备,并具备较好的技术保障条件,因此项目具备较好的技术支持。
3. 经济可行性:建设投资较大,但通过租金收入和经营管理,项目可望实现盈利。
七、风险评估1. 政策风险:政策调整可能对项目运营产生影响。
2. 竞争风险:其他地区已有不少人工智能产业园区,竞争激烈。
3. 经济风险:经济不稳定可能导致企业逆周期调整。
八、推进建议1. 相关政府部门要加大政策支持力度,为项目提供良好的政策环境。
项目可行性研究报告案例范文(通用5篇)
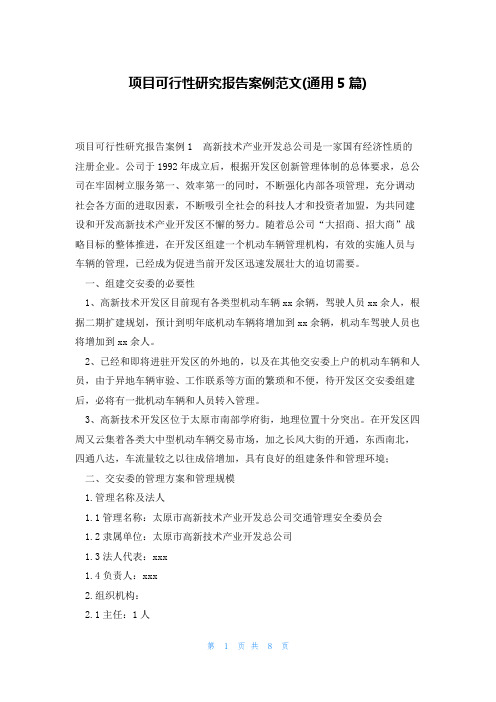
项目可行性研究报告案例范文(通用5篇)项目可行性研究报告案例1 高新技术产业开发总公司是一家国有经济性质的注册企业。
公司于1992年成立后,根据开发区创新管理体制的总体要求,总公司在牢固树立服务第一、效率第一的同时,不断强化内部各项管理,充分调动社会各方面的进取因素,不断吸引全社会的科技人才和投资者加盟,为共同建设和开发高新技术产业开发区不懈的努力。
随着总公司“大招商、招大商”战略目标的整体推进,在开发区组建一个机动车辆管理机构,有效的实施人员与车辆的管理,已经成为促进当前开发区迅速发展壮大的迫切需要。
一、组建交安委的必要性1、高新技术开发区目前现有各类型机动车辆xx余辆,驾驶人员xx余人,根据二期扩建规划,预计到明年底机动车辆将增加到xx余辆,机动车驾驶人员也将增加到xx余人。
2、已经和即将进驻开发区的外地的,以及在其他交安委上户的机动车辆和人员,由于异地车辆审验、工作联系等方面的繁琐和不便,待开发区交安委组建后,必将有一批机动车辆和人员转入管理。
3、高新技术开发区位于太原市南部学府街,地理位置十分突出。
在开发区四周又云集着各类大中型机动车辆交易市场,加之长风大街的开通,东西南北,四通八达,车流量较之以往成倍增加,具有良好的组建条件和管理环境;二、交安委的管理方案和管理规模1.管理名称及法人1.1管理名称:太原市高新技术产业开发总公司交通管理安全委员会1.2隶属单位:太原市高新技术产业开发总公司1.3法人代表:xxx1.4负责人:xxx2.组织机构:2.1主任:1人2.2内勤:1人(负责车辆和驾驶人员的档案管理〕2.3车管员:2人2.4安全管理:1人3.管理办法3.1主任由总公司选派一名具有多年交通管理实际经验的技术人员担任。
3.2其他所需人员全部面向社会实行公开招聘。
择优录用。
3.3制定岗位实施细则,严格各项管理规定。
3.4实行年度测评、奖优罚劣、竞争上岗,采取末位淘汰的新机制。
4.办公地址:鉴于高新技术开发区的极佳投资环境,场址选择在高新开发区管委会大楼为最优方案。
可行性研究分析报告(精选10篇)

可行性研究分析报告(精选10篇)可行性研究分析报告随着社会的不断发展,越来越多的项目需要进行可行性研究分析,以确定其是否值得投资和实施。
本文将介绍10篇精选的可行性研究分析报告,以帮助读者更好地了解这一领域的研究方法和实践。
1.《某高速公路建设项目可行性研究报告》该报告对某高速公路建设项目进行了全面的可行性研究分析,包括市场需求、技术可行性、经济效益等方面。
通过对各项指标的评估和分析,得出该项目具有较高的可行性和投资价值。
2.《某新能源汽车生产项目可行性研究报告》该报告对某新能源汽车生产项目进行了可行性研究分析,包括市场前景、技术可行性、经济效益等方面。
通过对各项指标的评估和分析,得出该项目具有较高的可行性和投资价值。
3.《某旅游度假区开发项目可行性研究报告》该报告对某旅游度假区开发项目进行了可行性研究分析,包括市场需求、技术可行性、经济效益等方面。
通过对各项指标的评估和分析,得出该项目具有较高的可行性和投资价值。
4.《某新型医疗器械研发项目可行性研究报告》场前景、技术可行性、经济效益等方面。
通过对各项指标的评估和分析,得出该项目具有较高的可行性和投资价值。
5.《某新型材料生产项目可行性研究报告》该报告对某新型材料生产项目进行了可行性研究分析,包括市场前景、技术可行性、经济效益等方面。
通过对各项指标的评估和分析,得出该项目具有较高的可行性和投资价值。
6.《某新型能源开发项目可行性研究报告》该报告对某新型能源开发项目进行了可行性研究分析,包括市场前景、技术可行性、经济效益等方面。
通过对各项指标的评估和分析,得出该项目具有较高的可行性和投资价值。
7.《某新型农业生产项目可行性研究报告》该报告对某新型农业生产项目进行了可行性研究分析,包括市场前景、技术可行性、经济效益等方面。
通过对各项指标的评估和分析,得出该项目具有较高的可行性和投资价值。
8.《某新型环保技术研发项目可行性研究报告》该报告对某新型环保技术研发项目进行了可行性研究分析,包括市场前景、技术可行性、经济效益等方面。
建筑项目的可行性研究报告案例
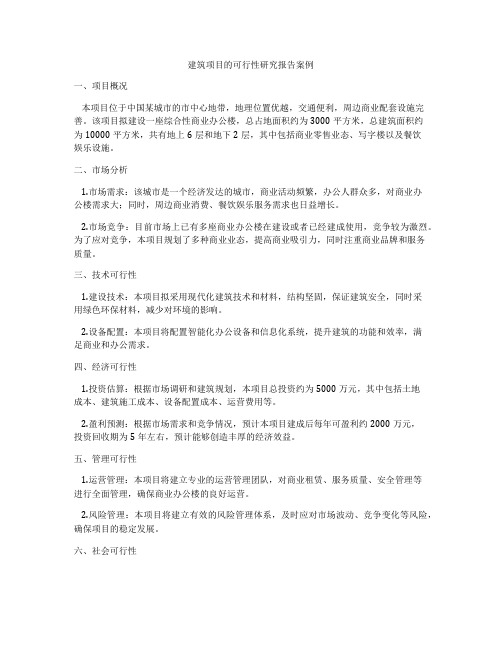
建筑项目的可行性研究报告案例一、项目概况本项目位于中国某城市的市中心地带,地理位置优越,交通便利,周边商业配套设施完善。
该项目拟建设一座综合性商业办公楼,总占地面积约为3000平方米,总建筑面积约为10000平方米,共有地上6层和地下2层,其中包括商业零售业态、写字楼以及餐饮娱乐设施。
二、市场分析1.市场需求:该城市是一个经济发达的城市,商业活动频繁,办公人群众多,对商业办公楼需求大;同时,周边商业消费、餐饮娱乐服务需求也日益增长。
2.市场竞争:目前市场上已有多座商业办公楼在建设或者已经建成使用,竞争较为激烈。
为了应对竞争,本项目规划了多种商业业态,提高商业吸引力,同时注重商业品牌和服务质量。
三、技术可行性1.建设技术:本项目拟采用现代化建筑技术和材料,结构坚固,保证建筑安全,同时采用绿色环保材料,减少对环境的影响。
2.设备配置:本项目将配置智能化办公设备和信息化系统,提升建筑的功能和效率,满足商业和办公需求。
四、经济可行性1.投资估算:根据市场调研和建筑规划,本项目总投资约为5000万元,其中包括土地成本、建筑施工成本、设备配置成本、运营费用等。
2.盈利预测:根据市场需求和竞争情况,预计本项目建成后每年可盈利约2000万元,投资回收期为5年左右,预计能够创造丰厚的经济效益。
五、管理可行性1.运营管理:本项目将建立专业的运营管理团队,对商业租赁、服务质量、安全管理等进行全面管理,确保商业办公楼的良好运营。
2.风险管理:本项目将建立有效的风险管理体系,及时应对市场波动、竞争变化等风险,确保项目的稳定发展。
六、社会可行性1.对就业的促进:本项目建成后将为周边地区提供大量的就业机会,促进当地经济的发展。
2.对城市形象的提升:本项目将提升周边城市商业环境和商业设施,提高城市的吸引力和竞争力。
综上所述,本项目的可行性较高,具备良好的市场潜力和经济效益,同时也对当地就业、城市形象等方面具有积极的社会影响。
希望相关部门能够给予支持和指导,共同推动该项目的顺利实施。
可行性分析报告(通用17篇)

可行性分析报告可行性分析报告(通用17篇)随着人们自身素质提升,需要使用报告的情况越来越多,报告根据用途的不同也有着不同的类型。
在写之前,可以先参考范文,以下是小编精心整理的可行性分析报告,仅供参考,希望能够帮助到大家。
可行性分析报告篇1一.背景1.宏观背景国际经济学家预测未来五年最具前途的九大行业,快餐业和休闲业占据二个席位;休闲餐饮是21世纪餐饮业的发展方向,其市场前景,行业利润远远超过传统餐饮;“民以食为天,百业餐饮为王!”餐饮业是一个永远充满活力的行业。
西式快餐将是21世纪最热门的行业之一。
西式快餐中最为火爆的还是奶茶店,在境外餐饮业中占据的比例是:美国35% 、欧洲30% 、日本20% 、香港10% ,而在中国,即使在广州、深圳、上海这一比例也仅为5% ,所以奶茶市场还有很大的开发潜力2.微观背景新的社会环境下,大学生就业形势已日渐严峻,为此,国家为鼓励大学生创业出台了一系列的优惠政策,大大减小了投资风险。
奶茶店行业投入少,见效快,收入稳定,风险小,无技术难读。
对于刚踏入社会创业的大学生来说,这是一个很好的选择。
二.项目研究1.样本此次研究采用的是在神农城与湖南工业大学附近邀请路人填写调查问卷的方法选取样本。
调查于20xx年11月2号在神农城,3号4号在湖南工业大学进行。
调查对象是路人,采用的原则是随机抽样法,方法如下:在选取了第一个之后,每隔二十个在调查一个,如果其中一个拒绝了,则选择下一个,以此类推。
在这三天的调查中,我们一共发放了300份问卷,其中回收了212份有效问卷。
这就是我们研究的重要依据。
2.问卷:本次问卷共有9个问题,其中有单选有多选。
将这212份问卷制成如下表格:样本购买情况人口统计特征购买行为分析通过上面的数据分析,我们可以作如下分析:1.目标群体:从调查的报告分析我们可以看出年轻人购买奶茶的概率更大,所以我们的目标更偏向于年轻人2.购买行为:从上表可以看出光顾新店多为开店活动所吸引,当然传单的作用也是显而易见的。
可行性研究报告案例
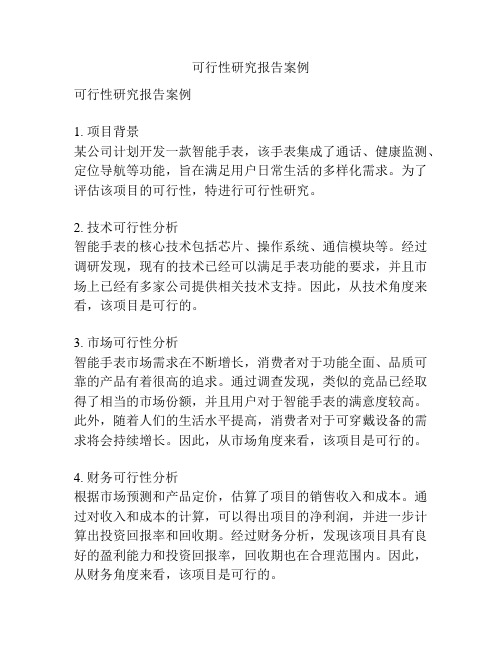
可行性研究报告案例可行性研究报告案例1. 项目背景某公司计划开发一款智能手表,该手表集成了通话、健康监测、定位导航等功能,旨在满足用户日常生活的多样化需求。
为了评估该项目的可行性,特进行可行性研究。
2. 技术可行性分析智能手表的核心技术包括芯片、操作系统、通信模块等。
经过调研发现,现有的技术已经可以满足手表功能的要求,并且市场上已经有多家公司提供相关技术支持。
因此,从技术角度来看,该项目是可行的。
3. 市场可行性分析智能手表市场需求在不断增长,消费者对于功能全面、品质可靠的产品有着很高的追求。
通过调查发现,类似的竞品已经取得了相当的市场份额,并且用户对于智能手表的满意度较高。
此外,随着人们的生活水平提高,消费者对于可穿戴设备的需求将会持续增长。
因此,从市场角度来看,该项目是可行的。
4. 财务可行性分析根据市场预测和产品定价,估算了项目的销售收入和成本。
通过对收入和成本的计算,可以得出项目的净利润,并进一步计算出投资回报率和回收期。
经过财务分析,发现该项目具有良好的盈利能力和投资回报率,回收期也在合理范围内。
因此,从财务角度来看,该项目是可行的。
5. 管理可行性分析项目开发需要有一定的技术人员和管理团队支持。
通过企业内部的资源分析和组织结构调整,可以合理配置项目所需的人力资源,并确保开发进展顺利。
此外,项目管理团队需要具备丰富的项目管理经验和良好的沟通协调能力。
经过分析,认为公司有能力有效管理该项目。
因此,从管理角度来看,该项目是可行的。
综上所述,该智能手表项目在技术、市场、财务和管理等多个方面都具备可行性。
建议公司进一步开展项目开发,并在市场上推出该产品。
可行性分析研究报告(精选5篇)

可⾏性分析研究报告(精选5篇)可⾏性分析研究报告(精选5篇) 在⼈们素养不断提⾼的今天,越来越多⼈会去使⽤报告,报告具有成⽂事后性的特点。
你所见过的报告是什么样的呢?下⾯是⼩编为⼤家整理的可⾏性分析研究报告(精选5篇),仅供参考,希望能够帮助到⼤家。
可⾏性分析研究报告1 通过对场地现状分析,以营造乡野⽓息浓郁的⽥园风光为规划⽬标,将场地划分为科技⽰范园区、农事体验园,花艺游赏园区三个园区。
结合每个区的主题,在区内布臵安排景点,建设休闲娱乐、风景游览、观光采摘、会议度假、品种展⽰、农业⽣产、科普教育等多功能于⼀体的现代农业⾼新技术和⽣态观光庄园。
⼀、项⽬背景 该项⽬是以依托万亩果园农业观光基地并充分利⽤⾝处龙泉⼭脉得天独厚的⾃然⽣态环境,采⽤现代化的农业⽣产运作模式进⾏经营管理,辅以旅游设施和服务,经过精⼼规划设计和施⼯,将农业的⽣产、⽣态与⽣活三者结合,形成⼀⽚富有⽥园情趣和地⽅特⾊的现代化农业科技⽣态观光园。
⼆、规划范围 本农庄位于xx镇,规划占地⾯积约1000亩。
基地三⾯环⼭,形成天然屏障,植被丰富,⼩⽓候环境条件优越;⼀⾯靠近主路,交通便捷,主路另⼀侧为村庄,从丘陵到⽥地,再到村庄,呈现三级梯度式变化。
基地被连绵的⼭丘⾃然划分为⼏个条状地块。
三、规划原则 3.1⽣态性原则 ⽣态性是创造园区安静、适宜、⾃然的⽣产⽣活环境的基本原则,是提⾼园区景观环境质量的基本依据。
在保护利⽤的基础上,结合地⽅风格,正确开发现有资源,充分发挥⽣态作⽤,创造良好的⽣态环境。
3.2参与性原则 应因地制宜营造良好的⽣境,开展⼀系列的可参与性的游赏活动,吸引游客⼴泛参与到园区⽣产、⽣活的⽅⽅⾯⾯,让游客更多层⾯地体验农村⽣活,欣赏农业景观,,使游客陶醉于原汁原味的乡村⽂化氛围。
3.3⽂化性原则 深⼊挖掘本地地⽅⽂化塑造农业观光园独特的⽂化内涵,并阐释原始农业⽂明、传统农业⽂明和现代农业⽂明的不同内涵,在旅游规划中发掘和培育农业观园的⽂化意义,提升其⽂化价值。
可行性报告9篇范文

可行性报告9篇范文一、殖项目内容1、养殖优质快大三黄鸡;2、占地面积1100m2;3、建设二间砖木结构的养鸡舍,每间长50m,宽110m,计1100m2;4、建设一间工人宿舍、储备饲料库,长16m,宽6m,计96m2;5、养量10000羽快大三黄,养殖时间每批鸡60—70天可以出拦。
二、投入预算;建设养鸡舍鸡、储备室1、设养鸡舍鸡、储备室共需78000.00元;2、基础设施建设50000元,饮水用电设施28000元。
三、购置鸡种和启动鸡饲料的投入1、10000只鸡种×1.5元=15000元;2、运费及采购费元;3、鸡饲料42吨×3500=147000元;4、工人工资4000元5、电费3000元以上合计171000元。
四、效益分析(按鸡养殖分析)(一)生产规模;饲养量10000羽快大三黄每批鸡60—70天可以出拦,年可以出栏4—5批鸡,出栏量50000羽。
(二)销售收入1、成鸡毛收入10000羽×3.6斤×平均价5元=180000元;2、鸡粪收入4000元3、两项毛收入合计184000元;4、每年纯收入184000元-171000元=9000元×5(批)=45000元。
五、社会效益养鸡,每年能增加全乡农民45000元的收入。
六、区政协扶贫摸式是采取养殖合作社+入股分红的方式确保农户利益。
1、把所需资金由养殖合作社来经营,合作社确保农户股金分红。
2、每年按实际出栏批数分红,一年不能少于4批。
3、养殖合作社有生产经营经验。
4、实际亏损风险由养殖合作社承担,可以保证农户利益不受损害。
项目可行性研究报告篇二该园区位于×市东北部,距市中心12公里,邻近机场、港口、火车站及丹大、沈丹高速公路起点,三维交通十分便利。
园区距鸭绿江断桥12公里,距虎山长城10公里,距河口度假区50公里,能增加丹东沿江旅游的景点,园区内青山绿水,山水相映,既有日俄战争遗址,日本碑和俄国坟,又有远销俄罗斯、黑龙江等国家和地区的无公害水果,燕红桃和寒富苹果;可以说,独特的地理位置,优越的'自然、人文景观,发展迅猛的无公害水果、蔬菜、花卉、水产品,为发展农业生态旅游观光奠定了坚定基础。
- 1、下载文档前请自行甄别文档内容的完整性,平台不提供额外的编辑、内容补充、找答案等附加服务。
- 2、"仅部分预览"的文档,不可在线预览部分如存在完整性等问题,可反馈申请退款(可完整预览的文档不适用该条件!)。
- 3、如文档侵犯您的权益,请联系客服反馈,我们会尽快为您处理(人工客服工作时间:9:00-18:30)。
第五章可行性分析可行性分析是企业进行清洁生产审核工作的第五个阶段。
本阶段的目的是对筛选出来的中/高费方案进行分析和评估,以选择最佳的、可实施的清洁生产方案。
本阶段工作重点是:在结合市场调查和收集一定资料的基础上,进行方案的技术、环境、经济的可行性分析和比较,从中选择和推荐最佳的可行方案。
5.1矿粉矾渣综合利用方案可行性分析5.1.1方案简介公司原有生产工艺是孰料、石灰粉、炉渣、粉煤灰和脱硫石膏混合,经粉磨后选粉进入包装车间。
考虑到水泥中加入矿粉矾渣可以节约原料,公司决定实施该方案。
在粉磨车间,在粉磨车间粉磨工段后配置2个300吨储罐,矿粉矾渣加入储罐后,由提升机提升至水泥输送线,将矿渣和矾渣掺入到水泥成品,再混匀。
该方案主要设备如下:斗提提升机NE50×17m 2台螺旋闸门500×500 2台电动三通分料器400×400 2台300吨矿粉、矾渣储罐 2套机械吊装 2只绞刀、转子秤及配套产品 2台方案工艺流程图如下图:图5-1 矿粉矾渣综合利用方案工艺流程图5.1.2技术可行性评估矾渣是一种灰白色的粒状物,有时亦呈粉红色。
其主要成份为硅、铝的化合物及少量铁、硫、钙、碱的化合物。
由于矾渣中含有一定数量的可溶性铝,在石膏存在的条件下,有可能形成钙矾石,起着良好的增强作用。
目前国家支持水泥行业利用工业废渣在制造复合水泥,《国家重点行业清洁生产技术导向目录》(第二批)中指出,采用此技术可以减少粉尘产生量,水泥生产成本大大降低,同时使工业废渣得到综合利用。
通过本方案实施,每年可提高混合材配料比,降低熟料使用量,通过核算,混合材配料比为31.2%,熟料配料比为68.8%,优化了配料结构,减少熟料使用量。
因此本方案符合国家有关的技术政策和能源政策。
本方案采用的设备为行业通用设备,自动化程度高,易于操作,安全可靠。
因此本方案在技术上是可行的。
5.1.3环境可行性评估矿渣、矾渣是工业废物,目前还没有有效的处理方法,对环境的影响也较大。
该项目实施后,不但可以解决工业废渣处理问题,年收纳矿粉、矾渣各22500t,将其很好利用,解决了矾渣堆积对环境的影响,同时提高了企业的废渣利用率,并节约了熟料4万t。
矾渣、矿粉均采用罐车运输至厂区,分别直接打入新建的储罐中,由储罐底部卸料口直接加入水泥成品输送线,整个进料和卸料过程全部密封,减少了原料装卸及输送过程产生的粉尘,经核算每年可减少粉尘1t,对环境有所贡献。
5.1.4经济可行性评估经企业对本装置各项目做的经济效益估算,矾渣和矿粉技术改造项目投入后,年收益共由2部分组成,即低价格购入矾渣和矿粉与高价格水泥产品差价增加效益,及矾渣和矿粉添加到水泥产品过程中均化需耗电费用,该方案向水泥成品加入矿粉、矾渣各22500t/a,消耗电量1.5kWh/t,则每年可节约生产45000t 水泥成品所需电耗,单位水泥成品粉磨及原辅料输送等工序电耗约33.8kWh/t,节约电耗为:45000t×(33.8kWh/t-7.5kWh/t)=1183500kWh,约343.2吨标煤,降低了生产单位水泥所需的电耗(按12年89.66万吨产量计算)1.3kWh/t。
水泥中掺加矾渣、转炉渣和粉煤灰等各种混合材,可降低水泥成本,改善水泥性能,从而降低水泥综合电耗。
1、投资成本估算2、年节约费用(P)原有水泥原料的成本是266元/t,矿粉的成本是258元/t,矾渣成本是254元/t,加入矿粉矾渣可以代替一部分生产原料,降低了生产成本,获得效益=(原料成本-矿粉/矾渣成本)×矿粉/矾渣加入量。
每年加入矾渣、矿渣各22500吨,每吨所用电费0.59元。
表5-2 矿粉矾渣综合利用方案收益情况一览表3、净现值(NPV)和部收益率(IRR)如上表可知,该方案的部收益率IRR为131.9%,大于银行贷款10%,且项目投资偿还期较短为0.76年,因此该方案从经济角度考虑是可行的。
5.2 HFCG160-140型辊压机预粉磨系统方案可行性分析5.2.1方案简介目前润德水泥1#和2#水泥粉磨系统采用Ф4.2×13m球磨机闭路粉磨系统,台时产量均为110t/h左右,单位产品水泥粉磨工段耗电量为34kwh/t。
本次对1#球磨机进行改造,在1#球磨机前增加一套HFCG160-140辊压机预粉磨系统,采用目前最先进的水泥挤压联合粉磨系统,同时将目前1#球磨机闭路粉磨系统改为开路系统。
开路系统的特点是成品颗粒分布宽,水泥的早期强度好,需水量小,电耗指标相对更先进,操作维护系统简单。
闭路系统改为开路系统后,水泥成品的温度会有所提高;新增辊压选粉系统利用气流分级机和动态选粉机的高效选粉,使入水泥磨物料比表面积达到160m2/kg以上,减少磨机粉磨做功比例,大幅提高产量的同时起到降低出磨水泥温度的作用。
熟料及混合材(粉煤灰、脱硫石膏等粉状料直接入球磨机)等按一定比例配好的混合料通过除铁设备除铁后由皮带机和提升机送入稳流称重仓,经辊压机挤压后的物料由料饼提升机提升至气流分级机分选,分选出大于0.5mm的粗颗粒(未挤好的料和边缘漏料)返回辊压机重新挤压,分选出小于0.5mm的细颗粒由旋风筒收集后通过空气输送斜槽送到球磨机进一步研磨,出球磨机物料即为成品,由提升机、空气输送斜槽等送至原有的水泥储库及散装系统。
出旋风筒的含尘风大部分回到气流分级机循环使用,少部分风送入原磨系统收尘器。
原水泥磨房中的设备改造如下:1、对原水泥磨房中Ospea选粉机进行改造,拆除其部转子和电机,保留壳体部分,在必要时用于出磨成品降温;2、将原水泥磨系统的成品收尘器后排风机进行改造,保留原有风机机壳,更换风轮及变频电机,作为磨机系统通风收尘使用;原出磨斗提提升能力可以满足改造后输送成品水泥需要,在提升机出口增加阀门和溜子,成品水泥可通过溜子直接溜入到水泥库斜槽;当成品水泥温度较高时,也可通过现有斜槽入“选粉机”,通过引入冷风降温。
新增辊压机系统采用HFCG160-140辊压机+HFV4000气流分级机的配置,辊压机与气流分级机形成闭路,原有1#球磨机系统由闭路改为开路,同时球磨机部进行高效筛分磨改造,以充分发挥球磨机的研磨特长。
辊压机产生的大量细粉被充分选出,并有效控制入磨半成品粒度在~0.5mm以下,比表面积可达到160m2/kg以上。
同样系统产量下,配套的磨机规格更小、磨机平均球径可更小,其运行成本及电耗更低。
改造后,台时产量可增加80%~90%,1#磨机台时产量可达到205t/h,粉磨工段单位水泥耗电量可降低为28.4kwh/t,每年可提高产量40万吨。
5.2.2技术可行性分析在水泥磨前增加大型辊压机预粉磨系统主要是对原有的水泥粉磨系统进行节能技术改造,采用目前国产最先进的水泥挤压联合粉磨系统,不仅投资省,在污染物排放、系统运行噪音、系统运转率、产品电耗等指标上可达到国先进水平。
同时大大降低企业能耗指标和生产成本,提高对市场需求波动的适应能力。
新建辊压机预粉磨框架占地面积约322m2,放置在原水泥磨车间与配料库之间,不影响原生产线。
图5-2 改造后系统工艺流程图采用这种改造方案是基于大辊压机、小球磨的原则,即尽量减少球磨机在粉磨系统中所占的电耗比例,增加辊压机的做功比例,从而减少系统电耗。
表5-4 新增主要设备一览表序号设备名称型号规格装机功率(KW)单位数量该方案为国际最先进的挤压联合粉磨系统,技术成熟,可靠性高。
技术上完全可行。
通过进行装机功率核算,技改后预计粉磨工段单位产品水泥电耗约28.4kwh/t,同时减少研磨体损耗,每年可提高产能40万吨。
5.2.3环境可行性分析改造后系统产能约205t/h,粉磨工段单位水泥电耗约28.4kWh/t,比2012年粉磨工段单位水泥电耗34kwh/t下降5.6kwh/t,按照2012年产量90万吨计,每年可直接减少用电约504万kWh,相当于每年节约标煤约1461.6吨,减少CO2排放3800.2t/a,SO2排放23.4t/a,减少NOx排放10.8t/a。
由于入磨物料粒度大幅下降,球磨机的平均球径也更加减少,不仅进一步降低了研磨体消耗,其产生的噪声强度也远小于传统系统。
因此,该方案从环境方面分析是可行的。
5.2.4经济可行性分析1、投资成本估算表5-5 辊压机预粉磨系统方案投资情况一览表拟对现有水泥粉磨系统以及配套设施进行技术改造,且倡导节能减排,降低电耗、减少成本,每年既节约水泥粉磨系统电耗504万度,又避峰降低电价,节约电耗成本;同时每年水泥产量增加40万吨。
表5-6 原有90万吨粉磨系统改造前生产运行情况表5-7 原有90万吨粉磨系统改造后生产运行情况注:以上价格为不含税价格。
2、年节约费用(P)改造后系统产能约205t/h,增加产能约95t/h。
原单位水泥粉磨工段电耗约34kWh/t,系统改造后粉磨工段单位产品水泥电耗降为约28.4kWh/t,吨水泥节约用电 5.6kWh,年节约用电900000×5.6kWh=5040000 kWh,节约电费5040000 kWh×0.59=2973600元。
同时减少研磨体消耗,每年可节省费用72万元。
则每年可节约成本297.36+72=369.36万元。
3、净现值(NPV)和部收益率(IRR)表5-8 辊压机预粉磨系统方案经济分析情况表由上表可以看出,该方案的部收益率IRR为13.79%,大于我们确定的基准利率10%;项目投资偿还期为5.26年,小于高费方案的定额偿还期10年;方案的净现值为828.35万元,大于零,所以本方案从经济角度考虑是可行的。
5.3推荐可实施方案由以上可行性分析可以得出:公司两个中/高费方案都是可行的,具有节能、降耗、减污、增效的环境效益,综合上面的技术环境、经济评估结果以及方案的投资和收益情况,公司决定全部实施上述方案。
5 可行性分析本阶段是对筛选出来的清洁生产备选中/高费方案进行综合分析,包括技术评估、环境评估和经济评估。
通过方案的分析比较,以选择技术上可行又获得经济和环境最佳效益的方案供企业领导和技术人员进行科学决策,以得到最后实施方案。
5.1 调查市场需求经过方案筛选,初步可行的4个中/高费方案分别为:F9“1线变频节能改造方案”、F18“1线低氮分级燃烧技术改造方案”、F19“1线、2线、3线烟气脱硝方案”和F20“废气余热供暖改造方案”。
本轮清洁生产审核过程无新产品产生,所采用工艺均为国较为成熟的工艺,因此不再需要进行全面的市场需求调查。
5.2 中/高费方案可行性分析5.2.1 1线变频节能改造方案1、技术可行性分析海昌分公司1线窑三代篦冷机的15307、15308、25321、25322、25323、25331、25332、25333八台风机控制方式为传统的入口阀门控制方式,风机耗电较大,因此,对1线窑三代篦冷机风机的控制方式进行变频节能改造是非常必要的。