焦炉烘炉问题的探讨
干熄焦装置烘炉管理的改进及探讨
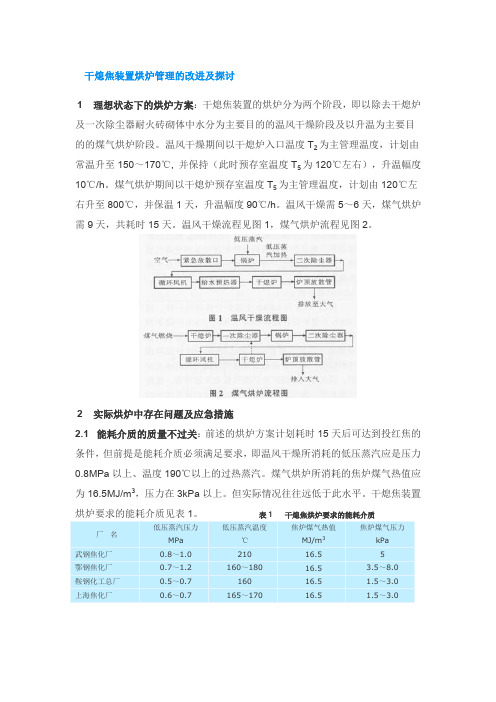
干熄焦装置烘炉管理的改进及探讨1 理想状态下的烘炉方案:干熄焦装置的烘炉分为两个阶段,即以除去干熄炉及一次除尘器耐火砖砌体中水分为主要目的的温风干燥阶段及以升温为主要目的的煤气烘炉阶段。
温风干燥期间以干熄炉入口温度T2为主管理温度,计划由常温升至150~170℃, 并保持(此时预存室温度T5为120℃左右),升温幅度10℃/h。
煤气烘炉期间以干熄炉预存室温度T5为主管理温度,计划由120℃左右升至800℃,并保温1天,升温幅度90℃/h。
温风干燥需5~6天,煤气烘炉需9天,共耗时15天。
温风干燥流程见图1,煤气烘炉流程见图2。
2 实际烘炉中存在问题及应急措施2.1 能耗介质的质量不过关:前述的烘炉方案计划耗时15天后可达到投红焦的条件,但前提是能耗介质必须满足要求,即温风干燥所消耗的低压蒸汽应是压力0.8MPa以上、温度190℃以上的过热蒸汽。
煤气烘炉所消耗的焦炉煤气热值应为16.5MJ/m3,压力在3kPa以上。
但实际情况往往远低于此水平。
干熄焦装置(1) 低压蒸汽。
低压蒸汽压力低造成的直接后果是随着锅炉汽包压力的升高,通入汽包的蒸汽量将越来越少,干熄炉方面升温幅度将随之减慢,甚至不升反降。
而低压蒸汽的温度低将限制系统温升的最高值,如果低压蒸汽温度仅为160℃,由于锅炉换热效率及热量损失等原因,锅炉出口循环气体温度仅为140℃,再经过二次除尘器、循环风机及给水预热器等设备的损耗,干熄炉入口气体温度将为110℃左右,达不到烘炉方案中150~170℃的要求。
遇到这种情况时,应将中压蒸汽串接入低压蒸汽管网,以提高低压蒸汽的温度和压力。
如果客观条件不允许,应采取应急措施,即在T5温度无法升至120℃的情况下,仍将煤气点火,进入煤气烘炉阶段。
例如在鞍钢干熄焦装置烘炉时,T5升至77℃后就进行了煤气烘炉的点火。
而上海焦化厂的T5仅升至56℃就进入煤气烘炉阶段了。
提前煤气点火造成的直接后果是干熄炉耐火材料砌体中的水分得不到很好的去除,鞍钢在干熄焦烘炉的中期,即T5升温至500℃时,干熄炉内仍有大量水蒸汽逸出,水蒸汽从耐火砖砌体内逸出的过程中会冲刷砌体的灰缝,造成灰缝火泥的脱落。
炼焦炉的烘炉
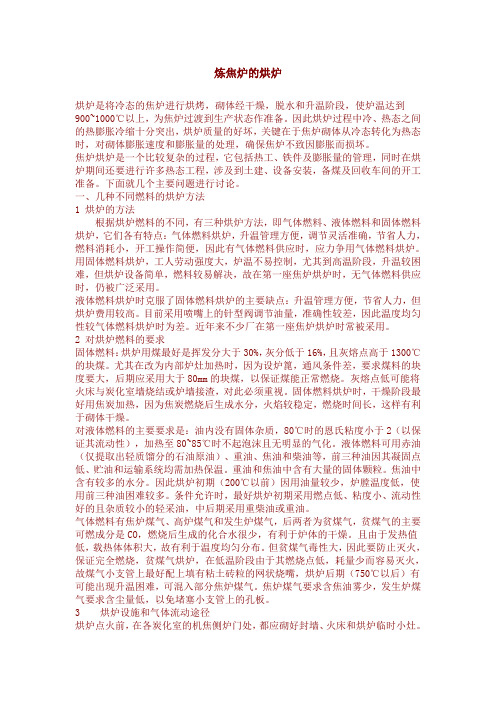
炼焦炉的烘炉烘炉是将冷态的焦炉进行烘烤,砌体经干燥,脱水和升温阶段,使炉温达到900~1000℃以上,为焦炉过渡到生产状态作准备。
因此烘炉过程中冷、热态之间的热膨胀冷缩十分突出,烘炉质量的好坏,关键在于焦炉砌体从冷态转化为热态时,对砌体膨胀速度和膨胀量的处理,确保焦炉不致因膨胀而损坏。
焦炉烘炉是一个比较复杂的过程,它包括热工、铁件及膨胀量的管理,同时在烘炉期间还要进行许多热态工程,涉及到土建、设备安装,备煤及回收车间的开工准备。
下面就几个主要问题进行讨论。
一、几种不同燃料的烘炉方法1 烘炉的方法根据烘炉燃料的不同,有三种烘炉方法,即气体燃料、液体燃料和固体燃料烘炉,它们各有特点:气体燃料烘炉,升温管理方便,调节灵活准确,节省人力,燃料消耗小,开工操作简便,因此有气体燃料供应时,应力争用气体燃料烘炉。
用固体燃料烘炉,工人劳动强度大,炉温不易控制,尤其到高温阶段,升温较困难,但烘炉设备简单,燃料较易解决,故在第一座焦炉烘炉时,无气体燃料供应时,仍被广泛采用。
液体燃料烘炉时克服了固体燃料烘炉的主要缺点:升温管理方便,节省人力,但烘炉费用较高。
目前采用喷嘴上的针型阀调节油量,准确性较差,因此温度均匀性较气体燃料烘炉时为差。
近年来不少厂在第一座焦炉烘炉时常被采用。
2 对烘炉燃料的要求固体燃料:烘炉用煤最好是挥发分大于30%,灰分低于16%,且灰熔点高于1300℃的块煤。
尤其在改为内部炉灶加热时,因为设炉篦,通风条件差,要求煤料的块度要大,后期应采用大于80mm的块煤,以保证煤能正常燃烧。
灰熔点低可能将火床与炭化室墙烧结或炉墙接渣,对此必须重视。
固体燃料烘炉时,干燥阶段最好用焦炭加热,因为焦炭燃烧后生成水分,火焰较稳定,燃烧时间长,这样有利于砌体干燥。
对液体燃料的主要要求是:油内没有固体杂质,80℃时的恩氏粘度小于2(以保证其流动性),加热至80~85℃时不起泡沫且无明显的气化。
液体燃料可用赤油(仅提取出轻质馏分的石油原油)、重油、焦油和柴油等,前三种油因其凝固点低、贮油和运输系统均需加热保温。
6m焦炉的烘炉及优化措施

在冷态 安装好 炉 门 , 炉时不 需要砌封 墙 , 烘 热 态工程 时不需 要扒 封 墙 , 约大 量 耐火 材 料及 减 节
2 在烘炉过程 中烟道 的吸力应保持相对稳 ) 定, 并视炉温分布稍做调整, 正确控制炉体上下部
的温度分 配 比例 , 确保烘 炉质量 。 3 烘炉 低 温 阶段 , 了 防 止 升 温速 度 太 快 , ) 为 通 过增加 吸力 、 风 门开度 , 调节 确保 空气 过剩系数
6 在 烘 炉煤 气 的机 焦 侧 支 管 安装 自动调 节 ) 装置, 以稳 定烘 炉煤气 压力 , 减少 总管压力 波动对
・
6・
梅 山科技
4 优化措 施
4 1 带炉 门烘炉 .
21 0 0年第 1 期
炉温 的影响 。 2 2 烘 炉压 力控制方 案 . 1 加强 全 炉 吸力 测 量 是 保 证 全 炉 温 度 一 致 ) 的重要 手段 , 全炉炉顶 火道吸 力每班测 1 。 次
轻 了热 态 工 程 劳 动 强 度 , 短 了 焦炉 开 工 时 间 。 缩
1 1 烘 炉计 划编排 .
为适 应焦 炉硅 砖 膨胀 的特 性 , 确定 升 温 期 最 大 日平 均膨胀采 用 0 0 % , 硅 砖在 主要 膨 胀期 .3 使 做 到缓慢 、 匀膨 胀 。烘 炉 干燥 阶段 的基 本 原则 均 是 要在保 障灰缝严 密性 和砌体 完整性 的前 提下有 效 的排 出水分 , 干燥 期 (0 10℃前 ) 根据 梅 山 的气
确定是 根据 各 区域 砖样在 不 同温度下 的膨胀 率计 算 而得 。根 据 以上数 据 编 排烘 炉 计 划 , 制定 升 温
曲线 。 12 烘 炉温度 与膨胀 测量 点的选 择 .
谈焦炉烘炉升温速度
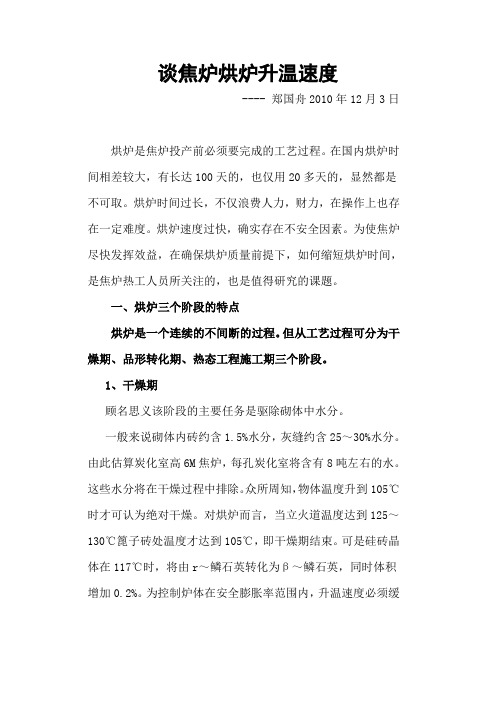
谈焦炉烘炉升温速度---- 郑国舟2010年12月3日烘炉是焦炉投产前必须要完成的工艺过程。
在国内烘炉时间相差较大,有长达100天的,也仅用20多天的,显然都是不可取。
烘炉时间过长,不仅浪费人力,财力,在操作上也存在一定难度。
烘炉速度过快,确实存在不安全因素。
为使焦炉尽快发挥效益,在确保烘炉质量前提下,如何缩短烘炉时间,是焦炉热工人员所关注的,也是值得研究的课题。
一、烘炉三个阶段的特点烘炉是一个连续的不间断的过程。
但从工艺过程可分为干燥期、品形转化期、热态工程施工期三个阶段。
1、干燥期顾名思义该阶段的主要任务是驱除砌体中水分。
一般来说砌体内砖约含1.5%水分,灰缝约含25~30%水分。
由此估算炭化室高6M焦炉,每孔炭化室将含有8吨左右的水。
这些水分将在干燥过程中排除。
众所周知,物体温度升到105℃时才可认为绝对干燥。
对烘炉而言,当立火道温度达到125~130℃篦子砖处温度才达到105℃,即干燥期结束。
可是硅砖晶体在117℃时,将由r~鳞石英转化为β~鳞石英,同时体积增加0.2%。
为控制炉体在安全膨胀率范围内,升温速度必须缓慢,所以在实际操作中将立火道温度达到100℃时作为干燥期结束,显然这是假设的。
2、晶形转化期硅砖在117℃、163℃、180~270℃以及573℃时发生晶形转化,体积迅速膨胀。
将晶形转化点密集的温度段100~600℃称为晶形转化期。
炉温达到600℃时砌体膨胀量占总膨胀为92%(1.229/1.336=92%),可视为炉体在烘炉时膨胀基木结束。
在100℃~600℃范围内不仅砌体总膨胀量大,其相对膨胀也是最大的,炉温每升高1℃砌体相对膨胀为1.229-0.118/600-100=0.222%,比600℃~1000℃温度段砖体相对膨胀1.336-1.229/1000-600=0.0268%大8.3倍。
比常温至100℃时相对膨胀0.118/100-25=0.157%大1.4倍。
尤其在300℃前砌体膨胀量占总膨胀0.992/1.336=74.3%。
JN50_02型焦炉烘炉应注意的问题
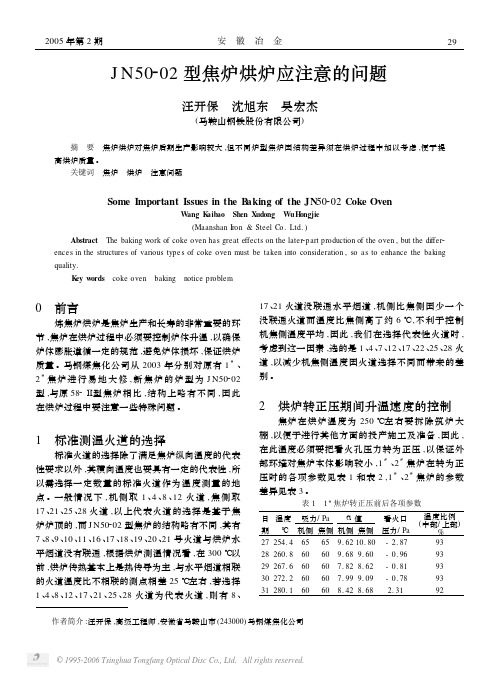
93
30 272. 2 60 60 7. 99 9. 09 - 0. 78
93
31 280. 1 60 60 8. 42 8. 68 2. 31
92
作者简介 :汪开保 ,高级工程师 ,安徽省马鞍山市 (243000) 马钢煤焦化公司
© 1995-2006 Tsinghua Tongfang Optical Disc Co., Ltd. All rights reserved.
(收稿日期 2005 - 03 - 18)
(上接第 6 页)
(3) T3 、T4 同一层面各点温差不大 ,较为均匀 ,
T3 低于排焦温度设计值 ,如表 3 所示 。
表 3 改进后 T3 、T4
℃
T4
T3
TR - 102A
174
TR - 103A
137
TR - 102B
166
TR - 103B
给 。一般认为 ,煤气供给调节量为 50 Pa/ 次 ,1 # 焦炉
采用此调 节 幅 度 , 而 2 # 焦 炉 采 用 调 节 量 为 20 ~
30 Pa/ 次 ,两座焦炉烘炉日膨胀的统计见下表 4 。
表 4 1 # 、2 # 焦炉烘炉日膨胀量
烘炉天数 日均膨胀量 日均膨胀
1 # 焦炉 2 # 焦炉
℃ 1 # 焦炉 5. 6 2 # 焦炉 7. 1
mm 2. 28 2. 92
% 0. 0215 0. 0291
偏差 1. 270 0. 449
从表 1 和表 2 可知 ,2 # 焦炉比 1 # 焦炉转正压时 间少 1 天 ,而温度比例约高出 2 个百分点 ,从转正压 期间的炉体膨胀来看 ,在 250~270 ℃期间 ,膨胀均 匀性 2 # 炉比 1 # 炉平稳 ,其膨胀量标准偏差相差较 大 ,分别为 1. 270 和 0. 449 ,由此可知 ,转正压期间 , 在能够满足最大膨胀量的前提下 ,提高日升温度数 , 减少了因外部烘炉大棚拆除环境对焦炉的影响 ,有 利于炉温的稳定和缩短转正压的时间 ,保证了焦炉 砌体的晶型平稳转化 。
6m焦炉采用天然气直接烘炉的实践与探讨
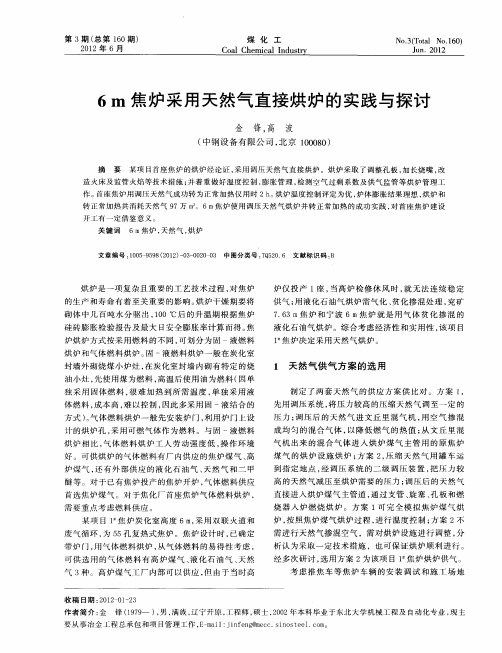
收 稿 日期 :0 2 O 3 2 1 卜2
作者 简介 : 金
锋 (9 9 ) 男 , 1 7一 , 满族 , 宁开原 , 程师 , 辽 工 硕士 ,0 2年本科 毕业于东 北大 学机械 工程及 自动化专 业 , 主 20 现
要从事 冶金 上程总 承包和项 目管理工 作 ,- a 1 j n eg m c . i o te . o 。 Em i : if n @ e c sn s e ] cm
醚等 。对于 已有焦 炉投产 的焦炉 开炉 , 气体燃 料供应 首选 焦炉煤气 。对 于焦 化厂首座焦炉 气体燃料 烘炉 ,
需要 重点考虑燃料供应 。
直接进 入烘炉煤气 主管道 , 通过支管 、 旋塞 、 板 和燃 孔 烧 器入 炉燃烧 烘 炉 。方 案 1 完全 模拟 焦炉 煤气 烘 可
炉烘 炉 方 式 按 采 用 燃 料 的 不 同 , 划 分 为 固 一液 燃 料 可
炉仅 投产 1 , 座 当高 炉检修 休风 时 , 就无法 连续 稳定 供气 ; 用液化石油气烘 炉需气化 、 贫化 掺混处理 , 兖矿
7 6 炉 和 宁 波 6m焦 炉 就 是 用 气 体 贫 化 掺 混 的 . 3m焦
计 的 烘 炉 孔 , 用 可燃 气 体 作 为燃 料 。与 固 一液 燃 料 采
烘 炉相 比 , 气体燃 料烘 炉工 人劳 动强度 低 , 作 环境 操
好 。 可 供 烘 炉 的气 体 燃 料 有 厂 内供 应 的 焦 炉 煤 气 、 高 炉 煤 气 , 有 外 部 供 应 的液 化 石 油 气 、 然 气 和 二 甲 还 天
煤 气 的 烘 炉 设 施 烘 炉 ; 案 2 压 缩 天 然 气 用 罐 车 运 方 , 到 指 定 地 点 , 调 压 系 统 的 二 级 调 压 装 置 , 压 力 较 经 把 高 的 天 然 气 减 压 至烘 炉 需 要 的压 力 ; 压 后 的 天 然 气 调
6m焦炉烘炉吸力制度的探讨

温的需要 ,但仔 细分 析全过程 ,发现 4焦炉实 际
烘 炉在 以下 3个 方 面 比 3焦 炉做 得更 好 。
维普资讯
20 0 6年 5月
第3 7卷 第 3期
燃 料 与 化 工 Fo& Ce l l r es ul h,t o s s n ̄ P c e a
2 7
外因有足嚣焦炭参与反应 ,故这少部分的水几乎全
部参加了水煤气反应 ,因而在风机底部 、锅炉底部
水夹套漏水,则应首先浸入下灰管中的焦粉中,然
应用 性 。
4 结论
通过千熄焦系统循环气体中可燃成分升高的规 律判断可燃成分升高的原因,再用排出法判断余热
锅炉泄漏。这一方法的实施可以成功的解决 了干熄 焦系统余热锅炉泄漏难以判断的难题 ,有利于余热 锅炉的维护及保养;可防止循环气体中可燃成分持 续升高等对干熄焦系统安全性造成的威胁 ,对干熄 焦的安全顺行有着十分重要的意义。
炉 ,目前 ,2 座焦炉相继投产 。由于 2 座焦炉所用
的耐火 材料 相 同 ,因此 从 2座焦 炉烘 炉 制订 的吸 力 制 度看 ,还 有一些 地方 值得 探讨 。
控制吸力的大小来实现。
2 控 制吸力的选择
为了保证焦炉各部位的相应膨胀 ,使相对位移 达到最小 ,不致使砌体因内应力造成拉裂或产生不 合理的位移 ,在干燥期又能有效地将砌体内在水分 排除 ,因而在烘炉过程中,焦炉各部位温度要控制
较快速均匀。
() 5 保证烘炉大棚拆除时,看火孑压力转 为正 L
压:
() 2 小烟道与开闭器没出现凝结水。由于刚开
() 6 保证热态工程与开工需要 。
下面重点对焦炉烘炉过程中焦炉管理火道 ( 燃 烧室 ) 、蓄顶 ( 斜道 ) 、篦子砖 ( 蓄热室 ) 点温度控 3 制进行分析。焦炉烘 炉过程中相关数据见表 1 、表 2 。从 表 中数 据 看 ,2座 焦 炉都 保 证 了焦 炉 烘 炉 升
焦炉烘炉安全技术
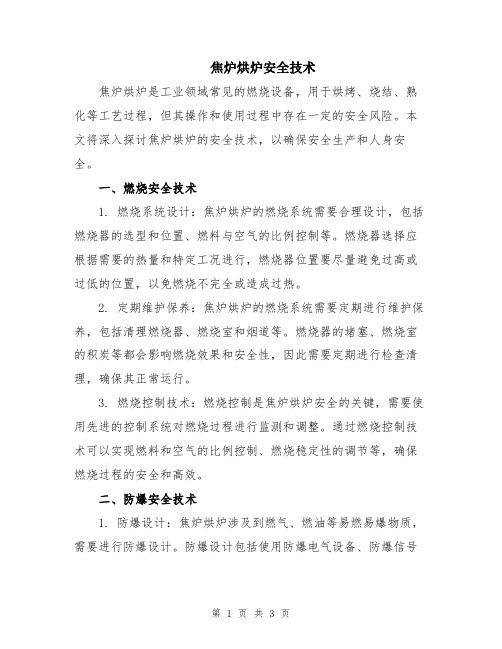
焦炉烘炉安全技术焦炉烘炉是工业领域常见的燃烧设备,用于烘烤、烧结、熟化等工艺过程,但其操作和使用过程中存在一定的安全风险。
本文将深入探讨焦炉烘炉的安全技术,以确保安全生产和人身安全。
一、燃烧安全技术1. 燃烧系统设计:焦炉烘炉的燃烧系统需要合理设计,包括燃烧器的选型和位置、燃料与空气的比例控制等。
燃烧器选择应根据需要的热量和特定工况进行,燃烧器位置要尽量避免过高或过低的位置,以免燃烧不完全或造成过热。
2. 定期维护保养:焦炉烘炉的燃烧系统需要定期进行维护保养,包括清理燃烧器、燃烧室和烟道等。
燃烧器的堵塞、燃烧室的积炭等都会影响燃烧效果和安全性,因此需要定期进行检查清理,确保其正常运行。
3. 燃烧控制技术:燃烧控制是焦炉烘炉安全的关键,需要使用先进的控制系统对燃烧过程进行监测和调整。
通过燃烧控制技术可以实现燃料和空气的比例控制、燃烧稳定性的调节等,确保燃烧过程的安全和高效。
二、防爆安全技术1. 防爆设计:焦炉烘炉涉及到燃气、燃油等易燃易爆物质,需要进行防爆设计。
防爆设计包括使用防爆电气设备、防爆信号传输装置、防爆管路和防爆仪表等,确保设备在爆炸环境中工作时不引发爆炸。
2. 气体检测技术:焦炉烘炉使用燃气燃料,需要使用气体检测技术来监测燃气的浓度和泄漏情况。
气体检测仪器可以及时发现燃气泄漏,避免爆炸事故的发生。
3. 通风系统:焦炉烘炉的通风系统需要合理设计和维护,确保室内的有害气体及时排出。
通风系统可以采用机械通风和自然通风相结合的方式,保持室内空气流通和清新。
三、热安全技术1. 绝热设计:焦炉烘炉的绝热设计要考虑设备壁体的保温效果和热损失问题。
采用合适的绝热材料和技术,减少热能的散失,提高设备的热效率。
2. 温度控制:焦炉烘炉操作中需要对炉内的温度进行监测和控制,使其在安全范围内保持稳定。
可以采用温度传感器和温度调节器进行监测和控制,及时发现和处理异常情况。
3. 热辐射防护:焦炉烘炉在工作时会产生大量热辐射,需要采取相应的防护措施,防止人员被灼伤。
焦炉砌筑、烘炉、开工安全技术

焦炉砌筑、烘炉、开工安全技术焦炉是炼焦的重要设备,对炼焦质量和产量有着直接的影响。
因此,焦炉的砌筑、烘炉和开工过程中的安全技术十分关键。
一、焦炉砌筑技术1. 焦炉砌筑前的筹备工作焦炉砌筑前需要进行充分的筹备工作,包括制定砌筑方案、准备砌筑材料、组织人员和设备等。
砌筑方案应根据实际情况进行科学、合理的设计,确保焦炉的结构牢固、安全可靠。
砌筑材料的选用要符合规定的技术要求,确保材料的质量稳定。
2. 焦炉砌筑过程的安全措施焦炉砌筑过程中,需要采取一系列的安全措施,确保施工人员的安全。
首先,要对施工人员进行必要的安全教育和培训,提高他们的安全意识。
其次,要配备必要的防护装备,如安全帽、防护服、安全鞋等。
另外,要定期对施工现场进行安全检查,发现问题及时处理。
最后,要建立完善的应急预案,做好应急救援工作。
3. 焦炉砌筑质量的控制焦炉砌筑质量是确保焦炉长期稳定运行的重要保证。
为了控制砌筑质量,首先要对砌筑工艺进行合理安排,确保每个砌筑环节的顺利进行。
其次,要对砌筑过程中的关键环节进行严格的质量检查,发现问题及时处理。
最后,要对焦炉的砌筑质量进行全面评估,确保焦炉的质量达到预期要求。
二、焦炉烘炉技术1. 烘炉前的准备工作焦炉砌筑完成后,需要进行适当的烘炉工作,以保证焦炉内的砌筑材料能够充分干燥。
烘炉前的准备工作主要包括加热设备的准备、烘炉次数的确定以及适当的通风控制。
加热设备的选择要符合烘炉的要求,确保砌筑材料能够均匀加热。
烘炉次数的确定要科学合理,根据实际情况进行综合考虑。
通风控制要根据焦炉内的温度和湿度情况进行调整,确保烘炉效果良好。
2. 焦炉烘炉过程的安全技术焦炉烘炉过程中,要注重安全技术的应用,确保工作人员的安全。
首先,要确保烘炉设备的安全运行,定期进行设备巡检和维护,发现问题及时处理。
其次,要加强对烘炉操作人员的培训,提高其对安全事故的防范和处置能力。
最后,要建立健全的烘炉安全管理制度,加强对烘炉过程中的安全风险的防控。
浅谈焦炉冒烟、烟囱冒烟的原因与治理
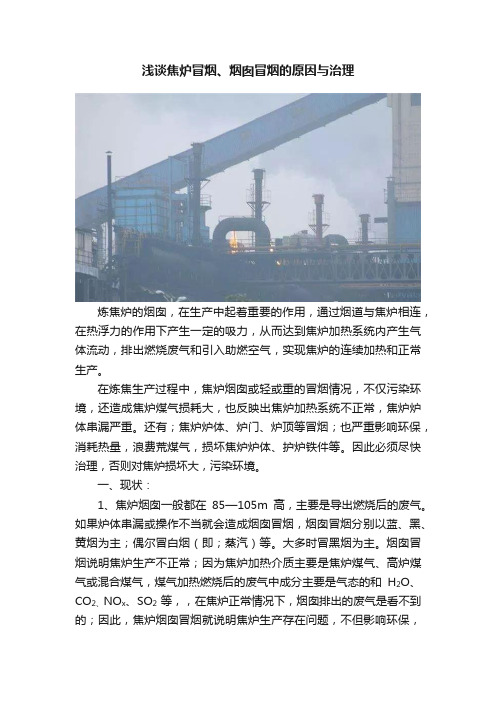
浅谈焦炉冒烟、烟囱冒烟的原因与治理炼焦炉的烟囱,在生产中起着重要的作用,通过烟道与焦炉相连,在热浮力的作用下产生一定的吸力,从而达到焦炉加热系统内产生气体流动,排出燃烧废气和引入助燃空气,实现焦炉的连续加热和正常生产。
在炼焦生产过程中,焦炉烟囱或轻或重的冒烟情况,不仅污染环境,还造成焦炉煤气损耗大,也反映出焦炉加热系统不正常,焦炉炉体串漏严重。
还有;焦炉炉体、炉门、炉顶等冒烟;也严重影响环保,消耗热量,浪费荒煤气,损坏焦炉炉体、护炉铁件等。
因此必须尽快治理,否则对焦炉损坏大,污染环境。
一、现状:1、焦炉烟囱一般都在85—105m高,主要是导出燃烧后的废气。
如果炉体串漏或操作不当就会造成烟囱冒烟,烟囱冒烟分别以蓝、黑、黄烟为主;偶尔冒白烟(即;蒸汽)等。
大多时冒黑烟为主。
烟囱冒烟说明焦炉生产不正常;因为焦炉加热介质主要是焦炉煤气、高炉煤气或混合煤气,煤气加热燃烧后的废气中成分主要是气态的和H2O、CO2、NO x、SO2等,,在焦炉正常情况下,烟囱排出的废气是看不到的;因此,焦炉烟囱冒烟就说明焦炉生产存在问题,不但影响环保,还影响焦炭产量、质量,同时焦炉煤气消耗也大,所以说烟囱冒烟是百害而无一益的事。
治理烟囱冒烟是迫在眉睫的事,一定要重视。
2、焦炉炉体冒烟、炉门冒烟、上升管根部冒烟、上升管翻板轴处冒烟等,造成焦炉黄烟一片,现场气味气味呛人,这说明焦炉墙体串漏,护炉铁件没及时测量调节,操作不规范,炉温不均匀,炉门、炉框、上升管、桥管、集气管等清理不及时造成炉体冒烟。
二、焦炉、烟囱冒烟分析:(一)烟囱冒烟分析:焦炉烟囱排出废气分别是;60万吨年生产能力,排出废气量约为150000m³/h,110万吨年生产能力,排出废气量约为275000m³/h,其中含有颗粒物量37—74mg/m³,能看到明显冒烟,说明排放的废气中含有未完全燃烧的煤气以及在高温下裂解形成的含炭微粒,引起烟囱冒烟原因很多,主要原因还是焦炉炉体的串漏和燃烧不合理造成。
焦炉烘炉安全技术(2篇)
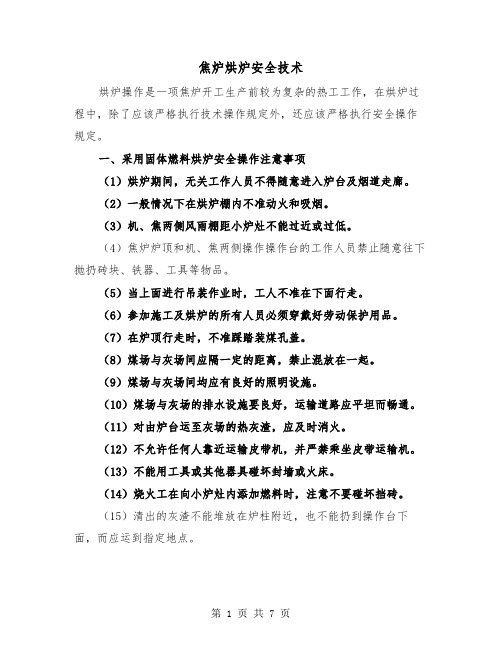
焦炉烘炉安全技术烘炉操作是一项焦炉开工生产前较为复杂的热工工作,在烘炉过程中,除了应该严格执行技术操作规定外,还应该严格执行安全操作规定。
一、采用固体燃料烘炉安全操作注意事项(1)烘炉期间,无关工作人员不得随意进入炉台及烟道走廊。
(2)一般情况下在烘炉棚内不准动火和吸烟。
(3)机、焦两侧风雨棚距小炉灶不能过近或过低。
(4)焦炉炉顶和机、焦两侧操作操作台的工作人员禁止随意往下抛扔砖块、铁器、工具等物品。
(5)当上面进行吊装作业时,工人不准在下面行走。
(6)参加施工及烘炉的所有人员必须穿戴好劳动保护用品。
(7)在炉顶行走时,不准踩踏装煤孔盖。
(8)煤场与灰场间应隔一定的距离,禁止混放在一起。
(9)煤场与灰场间均应有良好的照明设施。
(10)煤场与灰场的排水设施要良好,运输道路应平坦而畅通。
(11)对由炉台运至灰场的热灰渣,应及时消火。
(12)不允许任何人靠近运输皮带机,并严禁乘坐皮带运输机。
(13)不能用工具或其他器具碰坏封墙或火床。
(14)烧火工在向小炉灶内添加燃料时,注意不要碰坏挡砖。
(15)清出的灰渣不能堆放在炉柱附近,也不能扔到操作台下面,而应运到指定地点。
(16)测温或取样扒管时要戴好石棉手套,防止高温铁管烫伤身体。
(17)测温时要防止灰渣等杂物落入立火道中。
(18)打开看火孔盖时,应站在上风侧,防止热气流烧伤面部。
(19)打开看火孔盖测温时应使用安全火钩,不得使用其他不安全的工具,防止金属杂物掉入立火道内。
(20)用热电偶测温时,要经常检查套管丝扣的松紧程度,防止其掉入立火道内。
(21)热修瓦工在各部位工作时,要注意防止耐火泥浆溅入眼睛。
(22)在给炭化室封墙或蓄热室封墙刷浆时,应使用安全梯子进行操作,禁止踏在烘炉小灶或交换开闭器上操作。
(23)各个工种的各种操作工具应整齐放置,操作时严禁碰到照明线上。
二、采用气体燃料烘炉安全操作注意事项(1)煤气管道及其配件,应按照焦炉加热用管道及配件的安装、试压技术条件进行检查和验收,保证管路系统的严密性。
焦炉常见问题(窑炉知识)

焦炉常见问题(窑炉知识)焦炉交换时,经常听到的放炮声是怎样产生的?“放炮”是由于焦炉煤气和空气在砖煤气道中混合着火和回火而产生的。
一般“放炮”是在交换后10~20s左右发生。
多数发生在上升气流改下降气流的砖煤气道中。
常见的原因有:(1) 安装交换旋塞顶丝过松,产生漏气。
(2) 地下室横管和立管漏气。
(3) 换孔板时,没有在加减旋塞关闭15~20s后,拧紧发兰螺丝,造成吸入空气,产生“放炮”(4) 交换旋塞开、关不正,旋塞转动角度不够或已转90°但仍未全关,以至造成漏气和除碳口进空气。
(5) 交换旋塞芯和外壳研磨不好,受到腐蚀或润滑不好,以至全关时仍漏气。
(6) 违反压力制度,炭化室石墨保护层被烧掉,荒煤气串漏。
(7) 砖煤气道漏气。
地下室煤气管道着大火的应急处理?管径在100mm以上,逐渐关闭煤气来源阀门,压力降到500Pa 左右时,用蒸汽泡沫灭火器灭火,通入氮气、蒸汽切断煤气,以达到灭火。
管径在100mm以下,关闭煤气来源,通氮气、蒸汽灭火;地下室煤气管道着小火的应急处理?戴好放毒面具,用黄泥、湿麻袋或灭火器将火扑灭。
废气的行走途径产生的废气经跨越孔到下降火道,再经过斜道、下降气流蓄热室、小烟道、分烟道到烟囱根部,被烟囱抽走排往大气。
废气盘的作用控制进入焦炉加热系统的空气量和高炉煤气的煤气量,同时还控制排出加热系统产生的废气。
焦炉的加热设备有哪些煤气管道、废气盘、煤气预热器、煤气混合器、加减旋塞、交换旋塞、水封槽、交换机、流量孔板、测温和测压管等。
焦炉煤气为什么不经过蓄热室焦炉煤气中含有大量的甲烷等碳氢化合物,这些物质在高温下分解,产生游离碳或石墨沉渍容易将格子砖或斜道等处堵塞。
另外,焦炉煤气热值较高,不需预热到象高炉煤气那样高的温度。
焦炉煤气为什么要预热到45℃因为焦炉煤气里含有一些未被回收的焦油和萘等物质,这些物质在温度低的情况下冷凝下来,往往在煤气道旋塞、孔板或管径较小的地方堵塞管道,这样会严重影响炼焦炉均匀加热。
焦化厂捣鼓焦炉推焦困难原因分析及措施

焦化厂(煤化工)捣鼓焦炉推焦困难原因分析及措施捣固炼焦可大幅度提高入炉煤料的堆比重,并可明显提高焦炭的冷、热强度,因而可以配入2/3的弱粘煤而不降低焦炭质量,根据国内现有的煤价情况,可以降低入炉煤成本50〜100元/吨,经济效益十分显著,因而日益受到重视。
但是,应用捣固炼焦,由于其炉体自身因素或其他配煤等因素,一旦考虑不周,就可能造成推焦困难。
焦炉炼焦是一个复杂的工艺过程,煤料在炭化室内隔绝空气加热(即高温干镭),经过干燥、热解、熔融、粘结、固化和收缩等阶段,最终成为焦炭。
炭化室内的结焦过程有两个基木特点:一是层结焦,即焦炭总是在靠近炉墙处首先形成,而后逐渐向炭化室中心推移,二是结焦过程中的传热性能随炉料状态和温度而变化。
因此,炭化室内各部位焦炭质量与特性有所差异,一般以结焦终了时炭化室中心温度作为整个炭化室焦炭成熟的标志。
由于焦炉炭化室的定期装煤、出焦和加热系统气流的定期换向,使得炭化室内的煤-焦状态、加热火道内的气流以及焦炉各处温度场均产生周期性变化。
结焦末期,由于焦饼收缩,焦饼与炭化室墙面之间产生缝隙。
如果缝隙很小或者没有缝隙,则推焦时焦饼将推焦杆的推力传给炭化室墙。
这时推焦杆的推力不仅对炭化室底上产生摩擦力,而且对炭化室墙而也产生很大的摩擦力,因而电动机需要消耗较大的推焦电力,即消耗较大的电流量,用安培作单位,简称推焦电流。
推焦电流的大小能表示推动焦饼的难易程度。
在推焦过程中,电流量的大小并不固定,一般接触焦饼时电流量最大,然后下降。
推焦电流大时,显然有某些阻力阻止焦饼移动,一般表现为焦饼移动困难、很费力,或者根本推不动,这就叫焦饼难推。
焦饼难推是很危险的,甚至能造成炭化室炉墙损坏。
因此,分析推焦困难的原因并采取适当的解决措施,对延长炉体寿命,减少设备事故,提高焦炭质量和产量,有很大的意义。
1、推焦困难原因分析:1.1捣固焦炉自身原因:1. 1. 1 一般捣固焦炉设计机焦侧锥度较小,仅lOmmo1. 1.2捣固焦炉煤饼密度较大,为顶装煤的1.5倍左右,膨胀量加大,会增加炉墙的膨胀压力。
7.63m焦炉存在的问题及解决办法

7.63m焦炉存在的问题及解决办法1 提高单孔炭化室装煤量7.63m焦炉投产初期,装煤量不足,炉顶空间高度达800mm,导致炉顶空间温度高达987℃,由此引发下列问题。
(1) 装煤孔和上升管内的石墨生长速度很快,影响装煤操作,延误了出焦。
(2) 上升管因长石墨而造成内径缩小,导致炭化室内的压力增加,使机焦侧炉门和装煤孔冒烟。
(3) 3号装煤孔堵死,4个装煤孔的煤线高度不均匀,没有达到设计要求。
(4) 装煤车的装煤螺旋加料机产生大电流,甚至堵死螺旋加料出口,无法正常生产。
1.1 提高单孔炭化室装煤量的措施为解决装煤量不足带来的一系列问题,我们采取以下措施:(1) 装煤称重仓单斗装煤量调试优化;(2) 装煤车称重系统校正、提高稳定性,保证装煤量的稳定;(3) 培训提高工人的作业水平,稳定装煤操作环节;(4) 修改不同炉号、不同炉孔的加煤控制时间及装煤各导套的延迟时间,测试出较准确的配置方案。
原设计的加煤总时间为82s,因煤的粒度、水分、配煤等差异,加煤后期,会因炉顶空间压力过大而造成装煤孔冒烟着火现象,环保方面达不到要求。
由于加煤速度在短时间内变化过快,会影响装煤螺旋机构的正常运转,经常发生螺旋电流大、螺旋拧死、堵塞装煤孔等问题。
针对以上情况,连续测量了加煤过程中4个装煤孔的压力变化,从加煤总时间和4个煤斗分别延迟加煤等方面进行试验,最终测算出加煤时间为85s比较合理,且4个煤斗加煤部分采用延迟时间控制在5s、3s、 1s和0s。
有利于炉顶空间压力的流畅,确保了装煤过程中不冒烟,达到了环保要求。
(5) 为解决装煤末期炉顶空间压力波动大,装煤孔冒烟,环保不达标的难题,测试出装煤车二次加煤及推焦机二次平煤的协调控制方式。
原设计的不足之处是平煤时炉顶空间压力过大,焦侧炉门冒烟情况居多,平煤杆带出的余煤大。
我们将4.3m焦炉采用过的2次加煤及2次平煤的操作经验应用到7.63m焦炉上。
装煤车第1次加煤后暂时停止装煤,推焦机进行第1次平煤,使炭化室内的煤峰得到初步拉平,然后装煤车再继续加煤,推焦机进行2次平煤。
炼焦的问题及解决方法
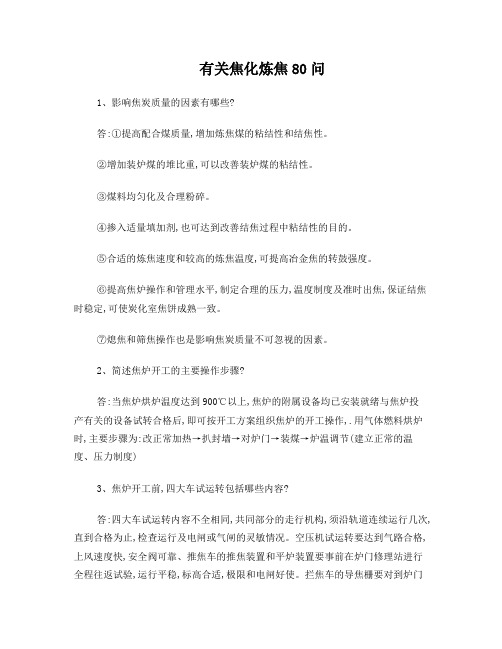
有关焦化炼焦80问1、影响焦炭质量的因素有哪些?答:①提高配合煤质量,增加炼焦煤的粘结性和结焦性。
②增加装炉煤的堆比重,可以改善装炉煤的粘结性。
③煤料均匀化及合理粉碎。
④掺入适量填加剂,也可达到改善结焦过程中粘结性的目的。
⑤合适的炼焦速度和较高的炼焦温度,可提高冶金焦的转鼓强度。
⑥提高焦炉操作和管理水平,制定合理的压力,温度制度及准时出焦,保证结焦时稳定,可使炭化室焦饼成熟一致。
⑦熄焦和筛焦操作也是影响焦炭质量不可忽视的因素。
2、简述焦炉开工的主要操作步骤?答:当焦炉烘炉温度达到900℃以上,焦炉的附属设备均已安装就绪与焦炉投产有关的设备试转合格后,即可按开工方案组织焦炉的开工操作,.用气体燃料烘炉时,主要步骤为:改正常加热→扒封墙→对炉门→装煤→炉温调节(建立正常的温度、压力制度)3、焦炉开工前,四大车试运转包括哪些内容?答:四大车试运转内容不全相同,共同部分的走行机构,须沿轨道连续运行几次,直到合格为止,检查运行及电闸或气闸的灵敏情况。
空压机试运转要达到气路合格,上风速度快,安全阀可靠、推焦车的推焦装置和平炉装置要事前在炉门修理站进行全程往返试验,运行平稳,标高合适,极限和电闸好使。
拦焦车的导焦栅要对到炉门框中,检查运行和吻合情况、煤塔内要清扫干净,煤塔漏嘴手动合格,磨电道调整好,煤斗闸套上下、闸板进出灵活好使。
熄焦车开关门灵活,开度够用等等。
4、坚持检修人员检修后,司机试车,验收,取回操作牌的意义?答:司机最了解本岗位车辆的使用性能。
在检修和试车过程中,可提出不同意见和建议,以达到提高检修质量,满足操作要求的目的。
从安全角度考虑,从检修人员手中取回操作牌,表明检修结束,可以操作车辆,以保证检修人员和设备的安全。
5、干法熄焦的优点?答:①可回收焦炭中大量热量,是焦化厂最大的节能设备,回收的热量于用来发电,采暖及供给其它用汽设备。
目前世界上有三十多套干熄焦在运行。
②可提高焦炭的转鼓强度,有利炼铁生产。
新焦炉烘炉操作要点及注意事项

新焦炉烘炉操作要点及注意事项焦炉的烘炉,是焦炉开工生产前的必要阶段,是焦炉特殊生产的重要组成部分,正常的烘炉与开工是冷态焦炉转为热态焦炉的基本手段,烘炉与开工质量的好坏直接影响到焦炉炉体的质量。
因此,认真抓好冷态焦炉烘炉与热态炉的开工是十分重要的。
一、温度比例及其范围的确定为了保持焦炉砌体各部位相应地膨胀,不使焦炉砌体彼此间产生拉裂现象,焦炉烘炉规定:烘炉初期,要求蓄热室温度为燃烧室温度的90%以上,烘炉末期85%以上;小烟道温度为燃烧室温度的80%以上,烘炉结束前为60%以上。
这不但能使焦炉在各向保持足够的严密性,而且可防止因砌体上下温差大,砖缝裂开及出现裂缝,使砌体的完整性不会遭到损坏。
这项规定,指明了各种类型的焦炉,在烘炉期间为保持砌体的严密性、完整性,砌体不同部位的温度比例安全界限。
各种类型的焦炉砌体不同部位的温度比例,只有控制在安全界限之内,焦炉的烘炉才是安全可靠的。
在焦炉烘炉规定中,烘炉初期这个概念的温度界限界定范围比较模糊。
如果按鞍山焦耐院热工站的烘炉规定,烘炉初期蓄热室温度为燃烧室温度的95%以上来推断,烘炉初期的最后温度界限为燃烧室砌体温度为100℃,这比国外燃烧室温度达125-135℃作为干燥终点与烘炉开始的界限提前了许多,且温度范围较窄。
100℃前烘炉天数的确定,并不是完全按昼夜膨胀定额来确定的,而是在昼夜膨胀定额的基础上,根据以往其它焦炉的烘炉经验,确定烘炉天数。
在100℃后,才严格按照焦炉烘炉的日膨胀定额进行升温管理,从这个意义上讲,把立火道砌体温度100作为烘炉开始的温度界限与国外立火道温度达125-135℃作为干燥终点与烘炉开始的温度界限就比较接近,如此则100℃后的一段时间应为烘炉初期。
从硅砖的晶形转化范围及300前炉体膨胀来看,把300℃作为烘炉初期的最后期限是比较合理的。
这样烘炉初期这个概念的温度界限范围也较宽。
在编制烘炉图表时300℃前,蓄热室温度比例、小烟道温度比例分别按大于95%、大于80%取值,更有利于砌体严密性和完整性的充分保证。
6m焦炉烘炉吸力制度的探讨
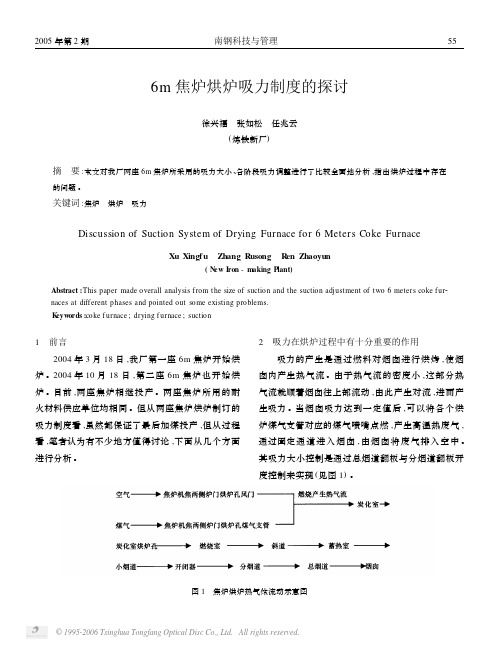
2 吸力在烘炉过程中有十分重要的作用 吸力的产生是通过燃料对烟囱进行烘烤 ,使烟
囱内产生热气流 。由于热气流的密度小 ,这部分热 气流就顺着烟囱往上部流动 ,由此产生对流 ,进而产 生吸力 。当烟囱吸力达到一定值后 ,可以将各个烘 炉煤气支管对应的煤气喷嘴点燃 ,产生高温热废气 , 通过固定通道进入烟囱 , 由烟囱将废气排入空中 。 其吸力大小控制是通过总烟道翻板与分烟道翻板开 度控制来实现 (见图 1) 。
19 466 466. 91 455. 77 457. 19 396. 25 395. 74 224. 23 215. 3 180. 5 166. 17 1 0. 85 0. 47 8. 2 84 82 130 56 20 580 580. 13 569. 29 568. 85 486. 47 488. 73 255. 28 246. 88 207. 17 200. 5 1 0. 84 0. 43 12. 4 88 88 130 59
13 218 218. 45 213. 01 215. 43 199. 66 198. 81 147. 12 142. 9 133. 75 120. 83 1 0. 91 0. 66 - 15. 2 66 64 100 35 14 250 249. 9 246. 3 245. 99 218. 78 222. 03 153. 18 151. 83 132. 67 123 1 0. 88 0. 61 2. 5 66 62 90 40
15 271 271. 22 267. 41 268. 56 235. 67 235. 59 160. 74 156. 3 142. 42 131. 17 1 0. 87 0. 58 4. 4 66 62 100 43 16 300 300. 5 298. 6 299. 57 257. 73 258. 09 168. 28 166. 33 137. 5 126. 67 1 0. 86 0. 56 4. 8 72 68 150 47