重熔用铝锭铸造中的质量控制管理
铸造生产过程的质量控制
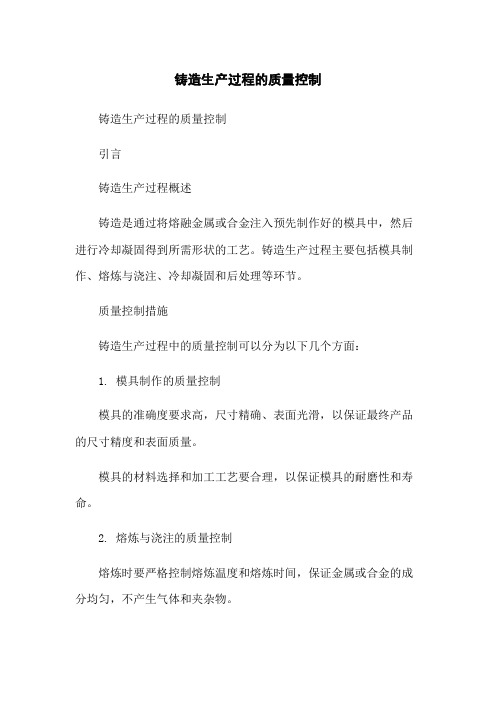
铸造生产过程的质量控制铸造生产过程的质量控制引言铸造生产过程概述铸造是通过将熔融金属或合金注入预先制作好的模具中,然后进行冷却凝固得到所需形状的工艺。
铸造生产过程主要包括模具制作、熔炼与浇注、冷却凝固和后处理等环节。
质量控制措施铸造生产过程中的质量控制可以分为以下几个方面:1. 模具制作的质量控制模具的准确度要求高,尺寸精确、表面光滑,以保证最终产品的尺寸精度和表面质量。
模具的材料选择和加工工艺要合理,以保证模具的耐磨性和寿命。
2. 熔炼与浇注的质量控制熔炼时要严格控制熔炼温度和熔炼时间,保证金属或合金的成分均匀,不产生气体和夹杂物。
浇注时要控制浇注温度和速度,避免产生气孔、夹渣和缩松等缺陷。
3. 冷却凝固的质量控制控制冷却速度和冷却方式,以避免产生组织缺陷,如晶粒过大、晶界不清晰等。
控制凝固过程中的温度变化,以避免产生应力和变形。
4. 后处理的质量控制清理杂质和缺陷,如夹渣、气孔等。
进行热处理、表面处理或机械加工,以改善产品的性能和表面质量。
质量控制方法为了有效控制铸造生产过程中的质量,可以采取以下几种方法:1. 设计质量控制在产品设计阶段,就应考虑产品的铸造性,合理设计产品的几何形状和壁厚,减少可能出现的缺陷和变形。
2. 工艺参数控制对每个工艺环节中的关键参数进行严格控制,如熔炼温度、浇注温度和速度等。
在铸造过程中,通过实时监测温度、压力和流速等参数,进行及时调整和控制。
3. 检测和检验使用各种检测设备和仪器,如X射线探伤仪、超声波检测仪等,对产品进行无损检测,以发现和排除可能存在的缺陷。
进行物理和化学性能的检验,如拉伸试验、硬度测试和成分分析等。
4. 信息化管理建立完善的质量管理体系,进行全过程的质量记录和数据分析,发现问题并采取措施进行改进。
运用信息化技术,实现数据的实时监控和追溯,提高生产过程的透明度和可控性。
结论铸造生产过程的质量控制是确保最终产品质量的重要环节。
通过合理的质量控制措施和方法,可以有效避免铸造过程中可能出现的缺陷和变形,提高产品的质量和性能。
重熔用铝锭质量控制水平
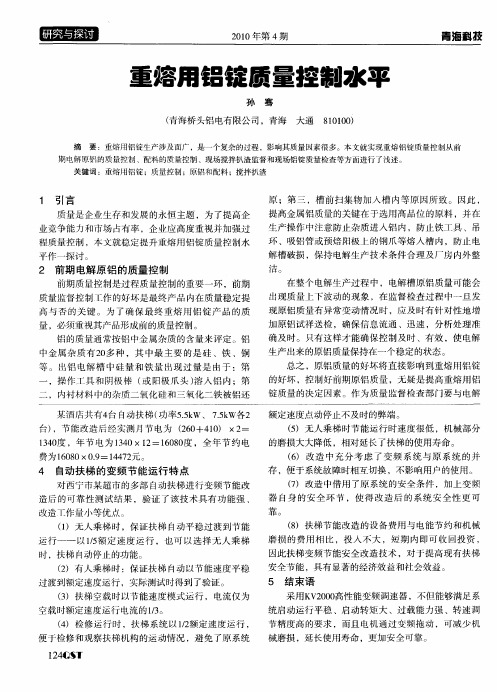
生产 出来 的原铝 质量 保持在 一个 稳定 的状态 。 总之 ,原 铝质 量 的好坏 将 直接 影 响到 重熔 用 铝锭 的好坏 ,控 制好前 期 原铝 质量 ,无疑 是提 高 重熔 用 铝
5 结 束 语
采用K 20 高性 能变 频调速 器 ,不但 能够满 足 系 V 00 统启 动运行 平 稳 、启 动转矩 大 、过 载 能力 强 、转速 调
节精 度高 的要 求 ,而且 电机 通 过 变频拖 动 ,可减 少机 械磨损 ,延 长使用 寿命 ,更 加安 全可靠 。
() 扶梯 空载 时 以节 能速度 模 式运 行 ,电流仅 为 3
4 自动 扶 梯 的 变 频 节 能运 行 特 点
对 西宁市 某超 市 的多 部 自动扶 梯进 行 变频 节能 改 造 后 的 可靠 性测 试 结 果 ,验 证 了该技 术 具 有 功 能强 、 改造 T作 量小 等优点 。
存, 便于系统故障时相互切换 ,不影响用户的使用。 () 改造 中借 用 了原 系统 的 安全 条件 ,加上 变 频 7
配人 的铝 量 = 一 / C ) W ( B)( x C 配入 铝杂 质含 量 ; 为 铝液 重量 。 为 ()液 体铝 和 固体 铝配 料计算 公 式 2
器 自身 的安 全 环 节 ,使 得 改 造 后 的 系 统 安 全 性 更 可 靠。
()无 人 乘梯 时 ,保证 扶梯 自动平 稳过 渡 到节 能 1 运 行 一一 以 1 额 定 速 度 运行 ,也 可 以选 择 无 人乘 梯 / 5 时 ,扶梯 自动停 止 的功能 。 ()有 人乘 梯 时 :保证 扶梯 自动 以节能 速度 平 稳 2
铸造生产过程质量控制点

铸造生产过程质量控制点铸造生产过程质量控制点铸造生产过程质量控制点是指在铸造生产过程中,通过采取一系列控制措施,以确保铸件质量达到设计要求的关键环节和要点。
铸造生产过程质量控制点的正确选择和实施,对于提高铸造生产过程质量、减少废品率具有重要意义。
以下是铸造生产过程中一些常见的质量控制点。
1.原材料控制原材料是影响铸件质量的关键因素之一。
在铸造生产过程中,需要对原材料进行严格的控制,包括熔炼炉料及加入剂的选择、原材料配比的控制等。
只有选择合适的原材料并正确使用,才能保证铸造产品质量的稳定性和一致性。
2.熔炼控制熔炼过程是铸造生产中最关键的环节之一。
在熔炼过程中,需要控制炉温、炉料的投入速度、炉内压力等参数,以确保金属液的质量稳定。
对于特殊材料的熔炼过程,还需要控制熔炼环境的气氛、熔炼时间等因素。
3.浇注控制浇注过程是将熔融金属注入到型腔中的过程。
在浇注过程中,需要控制浇注速度、浇注温度、浇注方式等因素,以保证浇注质量和铸件的致密性。
还需要控制浇注过程中金属液的气体排出情况,避免气孔的产生。
4.型腔控制型腔是铸造中形成铸件形状和尺寸的关键部位,对铸件质量有着重要影响。
型腔控制包括型腔设计、制造和维护等环节。
必须确保型腔的准确尺寸和光洁度,避免型腔表面的破损和变形,以确保铸件的形状精度和表面质量。
5.冷却控制冷却过程是铸件从熔融状态到固态过程中的一个关键环节。
在冷却过程中,需要控制冷却速度、冷却介质、冷却时间等因素,以保证铸件组织的均匀性和致密性。
还需要控制冷却过程中的温度梯度,避免铸件产生应力和变形。
6.热处理控制对于某些特殊材料或要求较高的铸件,还需要进行热处理过程。
热处理过程包括加热、保温和冷却等环节。
在热处理过程中,需要控制温度、保温时间、冷却速度等参数,以确保铸件组织的改善和性能的提升。
7.表面处理控制铸件的表面处理是为了提高铸件的表面质量和耐腐蚀性。
表面处理包括喷砂、抛光、电镀等工艺。
在表面处理过程中,需要控制处理剂的使用和浸溶时间,以保证铸件表面的光洁度和处理效果。
提高重熔用铝锭质量的措施
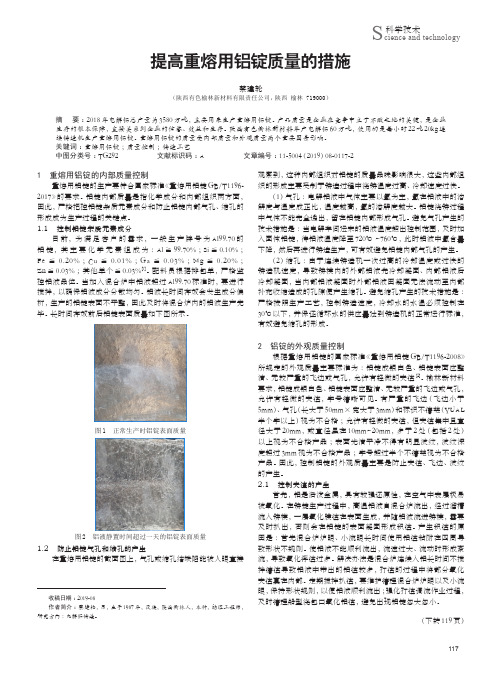
提高重熔用铝锭质量的措施蔡建轮(陕西有色榆林新材料有限责任公司,陕西 榆林 719000)摘 要:2018年电解铝总产量为3580万吨,主要用来生产重熔用铝锭。
产品质量是企业在竞争中立于不败之地的关键,是企业生存的根本保障,直接关系到企业的信誉、效益和生存。
陕西有色榆林新材料年产电解铝60万吨,使用的是每小时22吨20kg 连续铸造机生产重熔用铝锭。
重熔用铝锭的质量受内部质量和外观质量两个重要因素影响。
关键词:重熔用铝锭;质量控制;铸造工艺中图分类号:TG292 文献标识码:A 文章编号:11-5004(2019)08-0117-2 收稿日期:2019-08作者简介:蔡建轮,男,生于1987年,汉族,陕西榆林人,本科,助理工程师,研究方向:电解铝铸造。
1 重熔用铝锭的内部质量控制重熔用铝锭的生产要符合国家标准《重熔用铝锭GB/T1196-2017》的要求。
铝锭内部质量是指化学成分和内部组织两方面,因此,严格把控铝锭杂质元素成分和防止铝锭内部气孔、缩孔的形成成为生产过程的关键点。
1.1 控制铝锭杂质元素成分目前,为满足客户的需求,一般生产牌号为Al99.70的铝锭,其主要化学元素组成为:Al ≧99.70%;Si ≦0.10%;Fe ≦0.20%;Cu ≦0.01%;Ga ≦0.03%;Mg ≦0.20%;Zn ≦0.03%;其他单个≦0.03%[1]。
配料员根据排包单,严格监控铝液品位。
当加入混合炉中铝液超过Al99.70标准时,要进行搅拌,以确保铝液成分分散均匀。
铝液长时间存放会发生成分偏析,生产的铝锭表面不平整,因此及时将混合炉内的铝液生产完毕。
长时间存放前后铝锭表面质量如下图所示。
图1 正常生产时铝锭表面质量图2 铝液静置时间超过一天的铝锭表面质量1.2 防止铝锭气孔和缩孔的产生在重熔用铝锭的截面图上,气孔或缩孔结缺陷能被人眼直接观察到,这种内部组织对铝锭的质量品味影响很大,这些内部组织的形成主要受制于铸造过程中浇铸温度过高、冷却速度过快。
降低重熔用铝锭烧损的措施
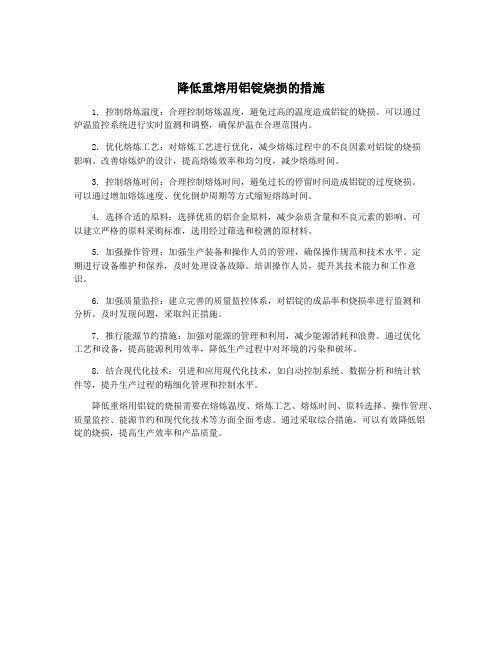
降低重熔用铝锭烧损的措施
1. 控制熔炼温度:合理控制熔炼温度,避免过高的温度造成铝锭的烧损。
可以通过
炉温监控系统进行实时监测和调整,确保炉温在合理范围内。
2. 优化熔炼工艺:对熔炼工艺进行优化,减少熔炼过程中的不良因素对铝锭的烧损
影响。
改善熔炼炉的设计,提高熔炼效率和均匀度,减少熔炼时间。
3. 控制熔炼时间:合理控制熔炼时间,避免过长的停留时间造成铝锭的过度烧损。
可以通过增加熔炼速度、优化倒炉周期等方式缩短熔炼时间。
4. 选择合适的原料:选择优质的铝合金原料,减少杂质含量和不良元素的影响。
可
以建立严格的原料采购标准,选用经过筛选和检测的原材料。
5. 加强操作管理:加强生产装备和操作人员的管理,确保操作规范和技术水平。
定
期进行设备维护和保养,及时处理设备故障。
培训操作人员,提升其技术能力和工作意
识。
6. 加强质量监控:建立完善的质量监控体系,对铝锭的成品率和烧损率进行监测和
分析。
及时发现问题,采取纠正措施。
7. 推行能源节约措施:加强对能源的管理和利用,减少能源消耗和浪费。
通过优化
工艺和设备,提高能源利用效率,降低生产过程中对环境的污染和破坏。
8. 结合现代化技术:引进和应用现代化技术,如自动控制系统、数据分析和统计软
件等,提升生产过程的精细化管理和控制水平。
降低重熔用铝锭的烧损需要在熔炼温度、熔炼工艺、熔炼时间、原料选择、操作管理、质量监控、能源节约和现代化技术等方面全面考虑。
通过采取综合措施,可以有效降低铝
锭的烧损,提高生产效率和产品质量。
提高重熔用精铝锭质量的措施
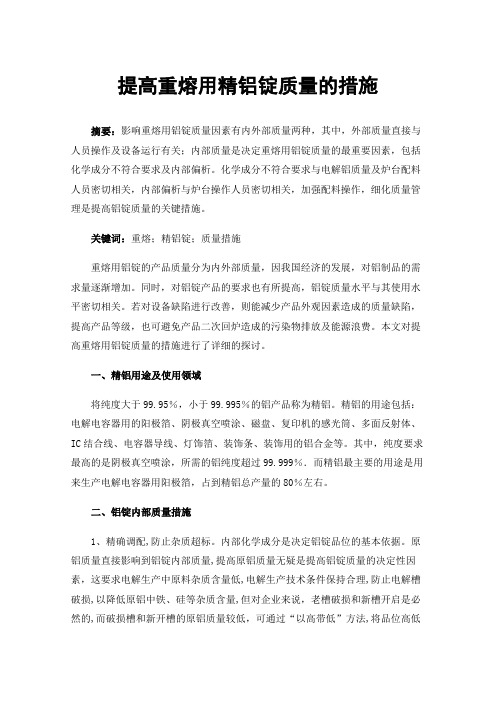
提高重熔用精铝锭质量的措施摘要:影响重熔用铝锭质量因素有内外部质量两种,其中,外部质量直接与人员操作及设备运行有关;内部质量是决定重熔用铝锭质量的最重要因素,包括化学成分不符合要求及内部偏析。
化学成分不符合要求与电解铝质量及炉台配料人员密切相关,内部偏析与炉台操作人员密切相关,加强配料操作,细化质量管理是提高铝锭质量的关键措施。
关键词:重熔;精铝锭;质量措施重熔用铝锭的产品质量分为内外部质量,因我国经济的发展,对铝制品的需求量逐渐增加。
同时,对铝锭产品的要求也有所提高,铝锭质量水平与其使用水平密切相关。
若对设备缺陷进行改善,则能减少产品外观因素造成的质量缺陷,提高产品等级,也可避免产品二次回炉造成的污染物排放及能源浪费。
本文对提高重熔用铝锭质量的措施进行了详细的探讨。
一、精铝用途及使用领域将纯度大于99.95%,小于99.995%的铝产品称为精铝。
精铝的用途包括:电解电容器用的阳极箔、阴极真空喷涂、磁盘、复印机的感光筒、多面反射体、IC结合线、电容器导线、灯饰箔、装饰条、装饰用的铝合金等。
其中,纯度要求最高的是阴极真空喷涂,所需的铝纯度超过99.999%.而精铝最主要的用途是用来生产电解电容器用阳极箔,占到精铝总产量的80%左右。
二、铝锭内部质量措施1、精确调配,防止杂质超标。
内部化学成分是决定铝锭品位的基本依据。
原铝质量直接影响到铝锭内部质量,提高原铝质量无疑是提高铝锭质量的决定性因素,这要求电解生产中原料杂质含量低,电解生产技术条件保持合理,防止电解槽破损,以降低原铝中铁、硅等杂质含量,但对企业来说,老槽破损和新槽开启是必然的,而破损槽和新开槽的原铝质量较低,可通过“以高带低”方法,将品位高低不同的铝液在铸造车间混合炉内混合(整炉),得到符合质量要求的产品。
通过这种方法既能消化破损槽或新开槽生产的等外品,又可控制铝液中各种杂质含量,使之符合国家或企业标准要求。
在配料前先要检查各电解槽原铝质量是否有质量上下波动的槽子,若发现原铝质量有变动,必须在配料时考虑质量变动情况。
铸造质量控制

铸造质量控制铸造质量控制是指在铸造过程中,通过一系列的控制措施和检测手段,确保铸件的质量符合设计要求和客户需求的过程。
本文将详细介绍铸造质量控制的标准格式,包括质量控制的目标、方法、流程和关键要点。
一、质量控制的目标铸造质量控制的目标是确保铸件的尺寸精度、组织结构、力学性能等质量指标符合设计要求和客户需求,同时降低废品率,提高生产效率。
二、质量控制的方法1. 原材料控制:选择合格的原材料,包括金属合金、砂型、熔炼剂等。
对原材料进行化学成分分析、物理性能测试等,确保原材料的质量稳定。
2. 工艺控制:制定合理的铸造工艺,包括砂型制备、熔炼、浇注、冷却等环节。
严格控制砂型的湿度、砂型的硬度、浇注温度、浇注速度等参数,确保铸件的凝固过程稳定。
3. 设备控制:对铸造设备进行定期维护和检修,确保设备的正常运行。
同时,配备先进的铸造设备,如自动浇注机、温度控制系统等,提高铸造的稳定性和一致性。
4. 检测控制:采用合适的检测手段,对铸件进行全面的检测。
包括尺寸测量、金相组织观察、力学性能测试等,确保铸件的质量指标符合要求。
常用的检测方法包括X射线检测、超声波检测、磁粉检测等。
三、质量控制的流程1. 原材料检验:对原材料进行化学成分分析、物理性能测试等,确保原材料的质量稳定。
2. 工艺参数设定:根据铸件的要求,制定合理的铸造工艺参数,包括砂型制备、熔炼、浇注、冷却等环节。
3. 设备调试:对铸造设备进行调试,确保设备的正常运行。
4. 首件检验:对首件进行全面的检测,包括尺寸测量、金相组织观察、力学性能测试等,确保首件质量符合要求。
5. 在线检验:在铸造过程中,对铸件进行抽检,确保铸件的质量稳定。
6. 最终检验:对最终产品进行全面的检测,确保产品的质量指标符合要求。
四、质量控制的关键要点1. 制定严格的质量控制标准和工艺规范,确保每个环节都有明确的要求和控制措施。
2. 建立完善的质量管理体系,包括质量责任制、质量培训、质量记录等,确保质量控制的有效实施。
重熔用铝锭铸造过程中的质量管控

重熔用铝锭铸造过程中的质量管控摘要:对现阶段重熔用铝锭的整个铸造过程进行深入分析,我们则可发现,其铸造过程在本质上是一个具有多点控制特征的生产过程,其主要涉及着配铝、化验以及铸造等生产环节。
结合实际情况来看,重熔用铝锭铸造过程总的质量管控关键点以及标准值的明确,通常为行业长期生产经验的积累,此外,相关行业还需进一步强化设备维护工作开展的力度,以此来有效的确保铝锭产品生产的品位与外观质量都能够满足国家相关质量标准。
基于此,本文对现阶段重熔用铝锭铸造过程中的质量管控进行深入分析,望能够对相关工作的开展起到一定的帮助。
关键词:重熔用铝锭;铸造过程;质量控制在当前社会,现代化铝工业原铝生产活动在实际开展时,通常采用的生产方法为冰晶石-氧化铝融盐电解法。
其生产出的液态状的铝液会以真空抬包的方式输送到铝锭铸造车间,在通过混合炉调价溶剂等操作对其进行精炼、扒渣等,最后在对铝液的实际成分开展必要的化验分析工作,待其满足相关足量标准后,方可开展铸造生产活动。
1.铝锭的品位控制1.铝液配比结合实际情况来看,入铝配比作为铝锭铸造生产活动开展的重要工序之一,其配比的科学性以及合理性将会对后期铸造生产活动开展的质量造成十分直接的影响,为此,在进行入铝配比工作时,相关工作人员必须要以原铝检测报告为基础,对其进行科学的合包配比,这时,电解系统出铝环节的相关工作人员需根据合包单中的内容对应槽号进行出铝[1]。
其次,在铝液经过抬包后到达铸造系统时,入铝环节的相关工作人员需根据混合炉内铝液的实际品位为基础来进一步确定这类铝液应入哪种型号的混合炉。
此外,如若在电解车间某一电解槽的实际状况相对较差时,相关工作人员需严格的以槽内铝液的实际品位为基础,对其开展混合炉内配比工作。
这时,如若出现无法配比等负面现象时,相关工作人员可结合自身铸造车间运转的实际情况,合理的空出一台混合炉用来专门铸造生产纯度在百分之九十九点七以下的铝锭,这类实际纯度相对较低的铝锭可作为回炉冷料来与炉内的铝原液进行再次配比,从而有效的降低资源浪费等负面现象出现的概率。
刍议重熔用铝锭铸造工艺的控制
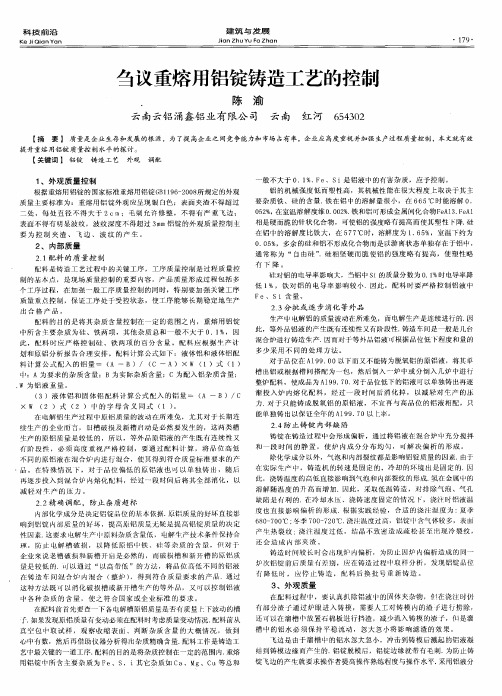
提 升 重 熔 用铝 锭 质 量控 制 水 平 的 探 讨 。
【 关键词 l 铝锭
1 、外 观 质 量 控 制
根据重熔用铝锭 的国家标准重熔用铝锭G 1 9 — 0 8 B 1 6 2 0 所规定的外观
质 量 主 要 标 准 为 : 重熔 用 铝 锭 外 观 应 呈 现 银 白色 ;表 面 夹 渣 不 得 超 过
科 技 前 沿
Ke Q i n Y a I Ji 0
建 筑 与 发 展
Jal Z i l hUY o Zh l U F ar ・1 79・
刍议重熔用铝锭铸造工艺的控制
.
陈
渝
640 5 32
云 南云铝 涌鑫铝 业有限公 司 云南 红河
【 摘
要 】 质量是企 业生存 和发展 的根 源,为 了提 高企 业之 间竞争能力和 市场 占有 率,企业应高度重视并加强生产过程质量控制 ,本文就有效 铸造 工艺 外观 调配
24防 止 铸 锭 内部 缺 陷 . 铸锭在铸造 过程 】 }会形成偏析 ,通过将铝液在 混合炉 中充 分搅拌 和 一段 时 问的 静 置 ,使炉 内成 分分 布均 匀 , 解 决偏 析 的形成 。
除化 学 成 分 以 外 , 气 泡 和 内部 裂 纹 都 是 影 响 铝 锭 质 量 的 因 素.由于 在 实 际 生 产 中 ,铸 造 机 的转 速 是 固 定 的 ,冷 却 的 环 境 出是 固 定 的.因
0 2 ,在室温溶 解度维0 0 2 . 5% . 0% 铁和铝可形成金属问化合物F A 3 F A e 1.e 1 相是硬而脆 的针状化合物 ,町使铝的强度略有提高而 使其 塑性 卜降. 硅 在铝 中的溶解度 比铁大 ,在 5 ℃时,溶解度为 1 6 %,室温 F 7 7 . 5 约为 0 0 %,多余 的硅 和铝不形成化合 物而是以游 离状态单独存 在于铝中, .5 通 常称为 “自由硅 ” .硅 相坚硬 而脆 使铝的强 度略 有提 高 ,使 塑性略
铸造生产过程的质量控制

铸造生产过程的质量控制铸造生产过程的质量控制1. 原材料的质量控制铸造过程中使用的原材料主要包括金属合金和砂型材料。
为了保证产品的质量,必须对原材料进行质量控制。
具体控制措施包括:选择高质量的原材料供应商,并建立稳定的供应链。
对原材料进行严格的检验和筛选,确保其符合产品的要求。
对原材料进行化学成分分析和物理性能测试,以确保其质量符合标准。
2. 模具制造过程的质量控制模具是铸造过程中的重要工具,其质量直接影响到产品的精度和表面质量。
为了保证模具的质量,必须对模具制造过程进行质量控制。
具体控制措施包括:制定模具制造工艺和工作指导书,确保每个环节都符合标准要求。
对模具材料进行质量检查和测试,以确保其质量达到要求。
对模具零部件进行尺寸检验和装配检验,确保模具的准确性和稳定性。
3. 铸造工艺参数的质量控制铸造工艺参数是影响产品质量的重要因素,必须进行严格的质量控制。
具体控制措施包括:确定合理的铸造温度和压力,以确保产品的致密性和机械性能。
控制铸造过程中的冷却速率和凝固时间,以确保产品的表面质量和内部组织结构。
对铸造过程中的熔炼和浇注过程进行监控和调整,以确保产品的成分和收缩率符合要求。
4. 产品质量的检验和测试铸造产品的质量必须进行全面的检验和测试,以确保其质量达到要求。
具体控制措施包括:对产品外观进行目测和尺寸测量,以检查产品的表面质量和尺寸精度。
对产品进行物理性能测试,包括硬度、拉伸强度等指标。
对产品进行化学成分分析,以确保其成分符合标准要求。
对产品进行无损检测,如X射线检测、超声波检测等,以检查产品的内部质量。
5. 不良品的处理和纠正措施在质量控制过程中,可能会出现一些不合格的产品或过程。
为了保证产品质量,必须及时进行处理和纠正措施。
具体控制措施包括:对不良品进行分类和评估,确定其影响范围和原因。
采取相应的纠正措施,如返工、修复、补救等。
对纠正措施进行跟踪和评估,以确保问题得到彻底解决。
以上就是铸造生产过程中常用的质量控制方法和措施。
铝熔铸 管理制度
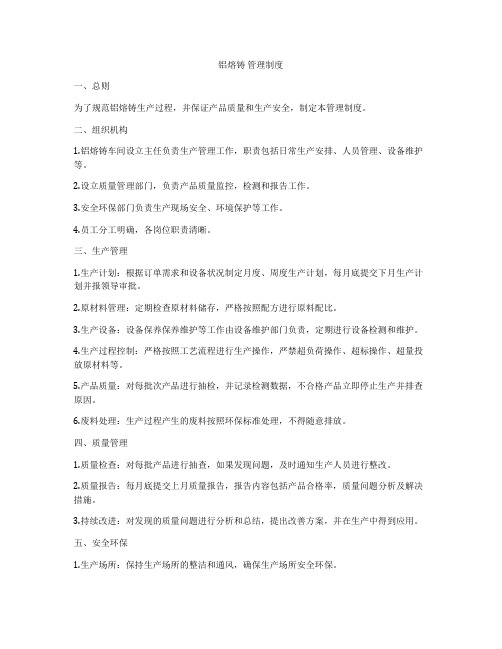
铝熔铸管理制度一、总则为了规范铝熔铸生产过程,并保证产品质量和生产安全,制定本管理制度。
二、组织机构1.铝熔铸车间设立主任负责生产管理工作,职责包括日常生产安排、人员管理、设备维护等。
2.设立质量管理部门,负责产品质量监控,检测和报告工作。
3.安全环保部门负责生产现场安全、环境保护等工作。
4.员工分工明确,各岗位职责清晰。
三、生产管理1.生产计划:根据订单需求和设备状况制定月度、周度生产计划,每月底提交下月生产计划并报领导审批。
2.原材料管理:定期检查原材料储存,严格按照配方进行原料配比。
3.生产设备:设备保养保养维护等工作由设备维护部门负责,定期进行设备检测和维护。
4.生产过程控制:严格按照工艺流程进行生产操作,严禁超负荷操作、超标操作、超量投放原材料等。
5.产品质量:对每批次产品进行抽检,并记录检测数据,不合格产品立即停止生产并排查原因。
6.废料处理:生产过程产生的废料按照环保标准处理,不得随意排放。
四、质量管理1.质量检查:对每批产品进行抽查,如果发现问题,及时通知生产人员进行整改。
2.质量报告:每月底提交上月质量报告,报告内容包括产品合格率,质量问题分析及解决措施。
3.持续改进:对发现的质量问题进行分析和总结,提出改善方案,并在生产中得到应用。
五、安全环保1.生产场所:保持生产场所的整洁和通风,确保生产场所安全环保。
2.操作规程:严格执行操作规程,不得使用不符合安全标准的工具,不得穿戴适宜的劳动防护用品。
3.事故处理:发生事故时,立即通知相关部门处理,并进行事故原因分析和处理。
4.环保措施:生产过程中产生的废气、废水、废渣等要按照环保要求处理。
六、员工管理1.员工培训:对新员工进行岗位培训,不定期对老员工进行技术、安全等方面的培训。
2.员工奖惩:对员工的工作表现进行奖惩,对优秀员工进行表彰,对违反规定行为进行处理。
3.员工福利:提供良好的工作环境和福利待遇,关心员工的生活及身体健康。
七、监督检查1.内部检查:定期组织内部质量检查,发现问题及时整改。
重熔用铝锭质量现状分析
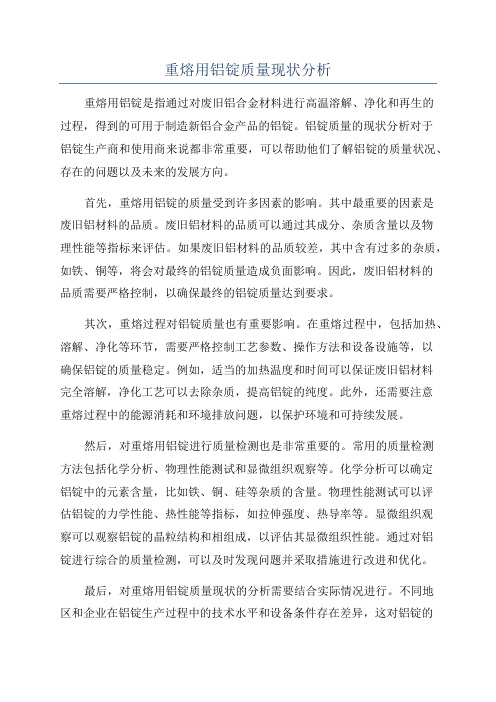
重熔用铝锭质量现状分析重熔用铝锭是指通过对废旧铝合金材料进行高温溶解、净化和再生的过程,得到的可用于制造新铝合金产品的铝锭。
铝锭质量的现状分析对于铝锭生产商和使用商来说都非常重要,可以帮助他们了解铝锭的质量状况、存在的问题以及未来的发展方向。
首先,重熔用铝锭的质量受到许多因素的影响。
其中最重要的因素是废旧铝材料的品质。
废旧铝材料的品质可以通过其成分、杂质含量以及物理性能等指标来评估。
如果废旧铝材料的品质较差,其中含有过多的杂质,如铁、铜等,将会对最终的铝锭质量造成负面影响。
因此,废旧铝材料的品质需要严格控制,以确保最终的铝锭质量达到要求。
其次,重熔过程对铝锭质量也有重要影响。
在重熔过程中,包括加热、溶解、净化等环节,需要严格控制工艺参数、操作方法和设备设施等,以确保铝锭的质量稳定。
例如,适当的加热温度和时间可以保证废旧铝材料完全溶解,净化工艺可以去除杂质,提高铝锭的纯度。
此外,还需要注意重熔过程中的能源消耗和环境排放问题,以保护环境和可持续发展。
然后,对重熔用铝锭进行质量检测也是非常重要的。
常用的质量检测方法包括化学分析、物理性能测试和显微组织观察等。
化学分析可以确定铝锭中的元素含量,比如铁、铜、硅等杂质的含量。
物理性能测试可以评估铝锭的力学性能、热性能等指标,如拉伸强度、热导率等。
显微组织观察可以观察铝锭的晶粒结构和相组成,以评估其显微组织性能。
通过对铝锭进行综合的质量检测,可以及时发现问题并采取措施进行改进和优化。
最后,对重熔用铝锭质量现状的分析需要结合实际情况进行。
不同地区和企业在铝锭生产过程中的技术水平和设备条件存在差异,这对铝锭的质量状况有一定的影响。
通过调查和采集数据,可以了解不同地区和企业的铝锭质量现状,有助于发现问题和寻求解决方案。
总之,重熔用铝锭质量现状分析对于铝工业的可持续发展具有重要意义。
通过深入研究和探索,可以不断改进铝锭生产工艺和质量控制方法,提高铝锭的质量和降低成本,促进铝工业的健康发展。
重熔用铝锭铸造质量控制
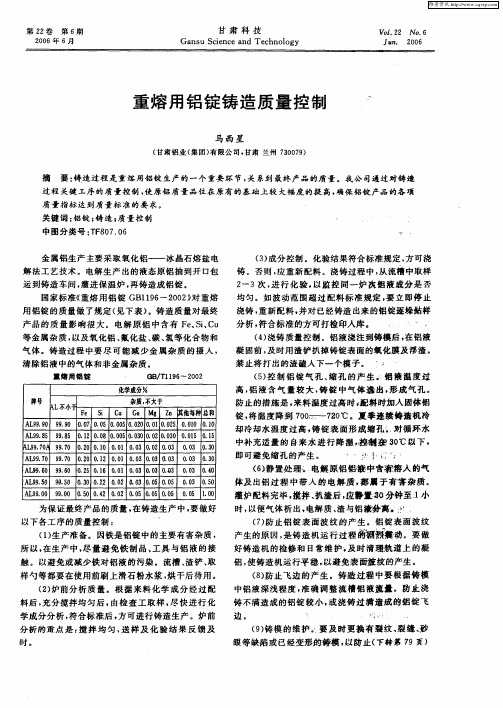
第2卷 2
第 6期
甘 肃 科 技
Ga u Sce e a c o o ns inc nd Te hn l gy
V . 2 Nl 6 2 0 .
20 0 6年 6月
J n 2 0 u. 06
重熔 用铝 锭 铸造 质 量 控 制
质 量指标达 到质量 标 准的要 求。
关键 词 : 铝锭 ; 铸造 ; 质量控 制
中 图分 类 号 :F 0 . 6 T 8 7 0
,
.
金 属铝生 产主要采 取氧化 铝—— 冰 晶石 熔盐 电 解法 工艺 技术 。电解 生 产 出的液态原铝 抽到 开 口包
() 3 成分控制 。化验 结果符合 标准规定 , 方可浇 铸 。否则 , 重新 配料 。浇铸过程 中 , 应 从流槽 中取样
运到 铸造车 间 , 灌进 保温炉 , 铸造成铝 锭 。 再
国家标准 《 重熔 用 铝 锭 G 1 9 —2 0 》 重 熔 B 16 0 2 对 用对最 终 产 品 的质 量影 响 很 大 。电解 原 铝 中 含有 F 、 iC eS、 u 等 金属 杂质 , 以及氧化 铝 、 氟化 盐 、 、 碳 氢等化 合物 和 气 体 。铸 造过程 中要 尽 可 能减 少金 属杂 质 的摄 人 , 清 除铝液 中的气体 和非 金属杂质 。
() 6 静置处理 电艉原铝铝 中含有 溶人 的气 漆
体及 出铝过 程 中带 人 的 电 解 质 , 都属 于 有 害 杂 质 。 灌炉配料完毕 , 搅拌、 扒渣后 , 应静置 暑 分钟至 .小 0 1 时, 以便气 体 析出 , 电解 质 、 与铝渍分离一 渣 .: () 7 防止 铝 锭 表面 波 纹 的产 生 。铝锭 表 面波 纹
降低重熔用铝锭烧损的措施
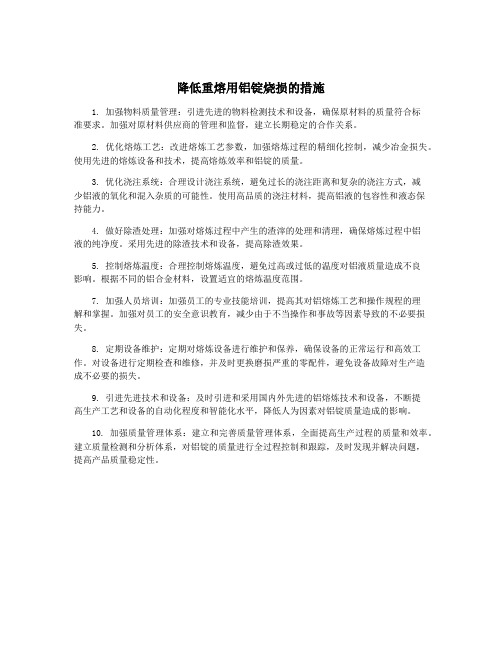
降低重熔用铝锭烧损的措施1. 加强物料质量管理:引进先进的物料检测技术和设备,确保原材料的质量符合标准要求。
加强对原材料供应商的管理和监督,建立长期稳定的合作关系。
2. 优化熔炼工艺:改进熔炼工艺参数,加强熔炼过程的精细化控制,减少冶金损失。
使用先进的熔炼设备和技术,提高熔炼效率和铝锭的质量。
3. 优化浇注系统:合理设计浇注系统,避免过长的浇注距离和复杂的浇注方式,减少铝液的氧化和混入杂质的可能性。
使用高品质的浇注材料,提高铝液的包容性和液态保持能力。
4. 做好除渣处理:加强对熔炼过程中产生的渣滓的处理和清理,确保熔炼过程中铝液的纯净度。
采用先进的除渣技术和设备,提高除渣效果。
5. 控制熔炼温度:合理控制熔炼温度,避免过高或过低的温度对铝液质量造成不良影响。
根据不同的铝合金材料,设置适宜的熔炼温度范围。
7. 加强人员培训:加强员工的专业技能培训,提高其对铝熔炼工艺和操作规程的理解和掌握。
加强对员工的安全意识教育,减少由于不当操作和事故等因素导致的不必要损失。
8. 定期设备维护:定期对熔炼设备进行维护和保养,确保设备的正常运行和高效工作。
对设备进行定期检查和维修,并及时更换磨损严重的零配件,避免设备故障对生产造成不必要的损失。
9. 引进先进技术和设备:及时引进和采用国内外先进的铝熔炼技术和设备,不断提高生产工艺和设备的自动化程度和智能化水平,降低人为因素对铝锭质量造成的影响。
10. 加强质量管理体系:建立和完善质量管理体系,全面提高生产过程的质量和效率。
建立质量检测和分析体系,对铝锭的质量进行全过程控制和跟踪,及时发现并解决问题,提高产品质量稳定性。
浅析提高重熔用铝锭质量的方法和措施
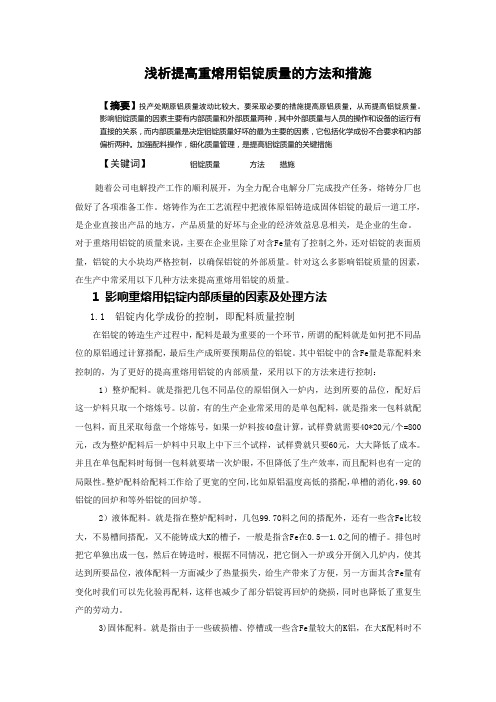
浅析提高重熔用铝锭质量的方法和措施【摘要】投产处期原铝质量波动比较大,要采取必要的措施提高原铝质量,从而提高铝锭质量。
影响铝锭质量的因素主要有内部质量和外部质量两种,其中外部质量与人员的操作和设备的运行有直接的关系,而内部质量是决定铝锭质量好坏的最为主要的因素,它包括化学成份不合要求和内部偏析两种。
加强配料操作,细化质量管理,是提高铝锭质量的关键措施【关键词】铝锭质量方法措施随着公司电解投产工作的顺利展开,为全力配合电解分厂完成投产任务,熔铸分厂也做好了各项准备工作。
熔铸作为在工艺流程中把液体原铝铸造成固体铝锭的最后一道工序,是企业直接出产品的地方,产品质量的好坏与企业的经济效益息息相关,是企业的生命。
对于重熔用铝锭的质量来说,主要在企业里除了对含Fe量有了控制之外,还对铝锭的表面质量,铝锭的大小块均严格控制,以确保铝锭的外部质量。
针对这么多影响铝锭质量的因素,在生产中常采用以下几种方法来提高重熔用铝锭的质量。
1 影响重熔用铝锭内部质量的因素及处理方法1.1 铝锭内化学成份的控制,即配料质量控制在铝锭的铸造生产过程中,配料是最为重要的一个环节,所谓的配料就是如何把不同品位的原铝通过计算搭配,最后生产成所要预期品位的铝锭。
其中铝锭中的含Fe量是靠配料来控制的,为了更好的提高重熔用铝锭的内部质量,采用以下的方法来进行控制:1)整炉配料。
就是指把几包不同品位的原铝倒入一炉内,达到所要的品位,配好后这一炉料只取一个熔炼号。
以前,有的生产企业常采用的是单包配料,就是指来一包料就配一包料,而且采取每盘一个熔炼号,如果一炉料按40盘计算,试样费就需要40*20元/个=800元,改为整炉配料后一炉料中只取上中下三个试样,试样费就只要60元,大大降低了成本。
并且在单包配料时每倒一包料就要堵一次炉眼,不但降低了生产效率,而且配料也有一定的局限性。
整炉配料给配料工作给了更宽的空间,比如原铝温度高低的搭配,单槽的消化,99.60铝锭的回炉和等外铝锭的回炉等。
铸造生产过程的质量控制
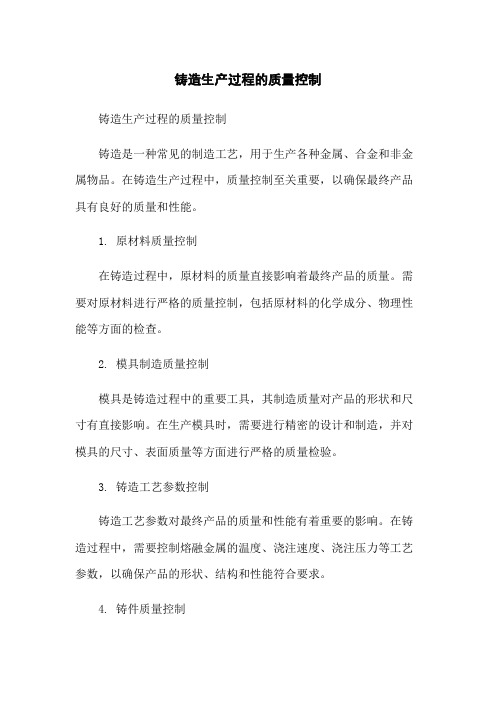
铸造生产过程的质量控制
铸造生产过程的质量控制
铸造是一种常见的制造工艺,用于生产各种金属、合金和非金属物品。
在铸造生产过程中,质量控制至关重要,以确保最终产品具有良好的质量和性能。
1. 原材料质量控制
在铸造过程中,原材料的质量直接影响着最终产品的质量。
需要对原材料进行严格的质量控制,包括原材料的化学成分、物理性能等方面的检查。
2. 模具制造质量控制
模具是铸造过程中的重要工具,其制造质量对产品的形状和尺寸有直接影响。
在生产模具时,需要进行精密的设计和制造,并对模具的尺寸、表面质量等方面进行严格的质量检验。
3. 铸造工艺参数控制
铸造工艺参数对最终产品的质量和性能有着重要的影响。
在铸造过程中,需要控制熔融金属的温度、浇注速度、浇注压力等工艺参数,以确保产品的形状、结构和性能符合要求。
4. 铸件质量控制
铸件质量是衡量铸造过程成功与否的重要指标。
在铸造过程中,需要对铸件的尺寸、表面质量、内部缺陷等进行严格的质量检验,
以确保产品的质量符合要求。
5. 产品性能检验
最终产品的性能是铸造过程成功与否的重要标志。
在铸造完成后,需要对产品的力学性能、化学性能、表面硬度等进行全面的检验,以确保产品的性能符合要求。
,铸造生产过程的质量控制是确保最终产品质量的关键环节。
通过对原材料质量、模具制造质量、铸造工艺参数、铸件质量和产
品性能的严格控制,可以提高产品的质量和性能,满足客户的需求。
降低重熔用铝锭烧损的措施
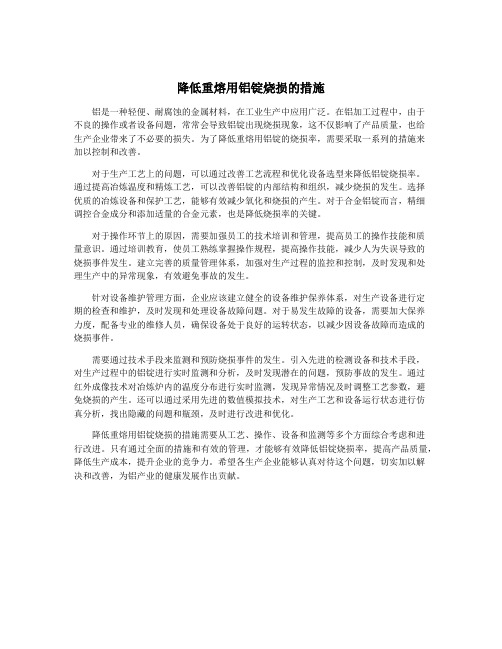
降低重熔用铝锭烧损的措施铝是一种轻便、耐腐蚀的金属材料,在工业生产中应用广泛。
在铝加工过程中,由于不良的操作或者设备问题,常常会导致铝锭出现烧损现象,这不仅影响了产品质量,也给生产企业带来了不必要的损失。
为了降低重熔用铝锭的烧损率,需要采取一系列的措施来加以控制和改善。
对于生产工艺上的问题,可以通过改善工艺流程和优化设备选型来降低铝锭烧损率。
通过提高冶炼温度和精炼工艺,可以改善铝锭的内部结构和组织,减少烧损的发生。
选择优质的冶炼设备和保护工艺,能够有效减少氧化和烧损的产生。
对于合金铝锭而言,精细调控合金成分和添加适量的合金元素,也是降低烧损率的关键。
对于操作环节上的原因,需要加强员工的技术培训和管理,提高员工的操作技能和质量意识。
通过培训教育,使员工熟练掌握操作规程,提高操作技能,减少人为失误导致的烧损事件发生。
建立完善的质量管理体系,加强对生产过程的监控和控制,及时发现和处理生产中的异常现象,有效避免事故的发生。
针对设备维护管理方面,企业应该建立健全的设备维护保养体系,对生产设备进行定期的检查和维护,及时发现和处理设备故障问题。
对于易发生故障的设备,需要加大保养力度,配备专业的维修人员,确保设备处于良好的运转状态,以减少因设备故障而造成的烧损事件。
需要通过技术手段来监测和预防烧损事件的发生。
引入先进的检测设备和技术手段,对生产过程中的铝锭进行实时监测和分析,及时发现潜在的问题,预防事故的发生。
通过红外成像技术对冶炼炉内的温度分布进行实时监测,发现异常情况及时调整工艺参数,避免烧损的产生。
还可以通过采用先进的数值模拟技术,对生产工艺和设备运行状态进行仿真分析,找出隐藏的问题和瓶颈,及时进行改进和优化。
降低重熔用铝锭烧损的措施需要从工艺、操作、设备和监测等多个方面综合考虑和进行改进。
只有通过全面的措施和有效的管理,才能够有效降低铝锭烧损率,提高产品质量,降低生产成本,提升企业的竞争力。
希望各生产企业能够认真对待这个问题,切实加以解决和改善,为铝产业的健康发展作出贡献。
铝合金熔铸过程质量的控制
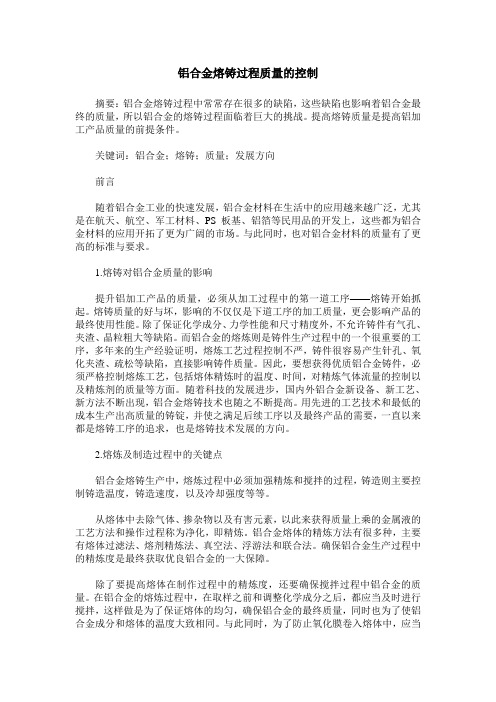
铝合金熔铸过程质量的控制摘要:铝合金熔铸过程中常常存在很多的缺陷,这些缺陷也影响着铝合金最终的质量,所以铝合金的熔铸过程面临着巨大的挑战。
提高熔铸质量是提高铝加工产品质量的前提条件。
关键词:铝合金;熔铸;质量;发展方向前言随着铝合金工业的快速发展,铝合金材料在生活中的应用越来越广泛,尤其是在航天、航空、军工材料、PS板基、铝箔等民用品的开发上,这些都为铝合金材料的应用开拓了更为广阔的市场。
与此同时,也对铝合金材料的质量有了更高的标准与要求。
1.熔铸对铝合金质量的影响提升铝加工产品的质量,必须从加工过程中的第一道工序——熔铸开始抓起。
熔铸质量的好与坏,影响的不仅仅是下道工序的加工质量,更会影响产品的最终使用性能。
除了保证化学成分、力学性能和尺寸精度外,不允许铸件有气孔、夹渣、晶粒粗大等缺陷。
而铝合金的熔炼则是铸件生产过程中的一个很重要的工序,多年来的生产经验证明,熔炼工艺过程控制不严,铸件很容易产生针孔、氧化夹渣、疏松等缺陷,直接影响铸件质量。
因此,要想获得优质铝合金铸件,必须严格控制熔炼工艺,包括熔体精炼时的温度、时间,对精炼气体流量的控制以及精炼剂的质量等方面。
随着科技的发展进步,国内外铝合金新设备、新工艺、新方法不断出现,铝合金熔铸技术也随之不断提高。
用先进的工艺技术和最低的成本生产出高质量的铸锭,并使之满足后续工序以及最终产品的需要,一直以来都是熔铸工序的追求,也是熔铸技术发展的方向。
2.熔炼及制造过程中的关键点铝合金熔铸生产中,熔炼过程中必须加强精炼和搅拌的过程,铸造则主要控制铸造温度,铸造速度,以及冷却强度等等。
从熔体中去除气体、掺杂物以及有害元素,以此来获得质量上乘的金属液的工艺方法和操作过程称为净化,即精炼。
铝合金熔体的精炼方法有很多种,主要有熔体过滤法、熔剂精炼法、真空法、浮游法和联合法。
确保铝合金生产过程中的精炼度是最终获取优良铝合金的一大保障。
除了要提高熔体在制作过程中的精炼度,还要确保搅拌过程中铝合金的质量。
铸造生产过程的质量控制

铸造生产过程的质量控制质量控制是铸造生产过程中非常重要的一环,能够确保产品符合质量标准和客户要求。
本文档将详细介绍铸造生产过程中的质量控制措施和标准,以供参考。
1.质量控制概述1.1 目的和范围本章节介绍质量控制的目的和范围,明确质量控制对产品质量的重要性,以及在整个铸造生产过程中需要实施的质量控制措施。
1.2 质量控制流程本章节详细描述铸造生产过程中的质量控制流程,包括材料准备、模具制备、熔炼浇注、冷却和清理等环节中的质量控制措施和标准。
2.材料准备质量控制2.1 材料选择本章节介绍材料选择的原则和标准,包括原材料的物理性质和化学成分等要求。
2.2 材料检验本章节详述材料检验的方法和标准,包括外观检验、尺寸检验、化学成分分析等。
3.模具制备质量控制3.1 模具设计本章节介绍模具设计的原则和要求,包括模具结构、内腔形状等方面的质量控制。
3.2 模具加工本章节详细描述模具加工的质量控制要求,包括模具尺寸精度、表面光洁度等方面。
4.熔炼浇注质量控制4.1 熔炼操作本章节介绍熔炼操作的要求,包括熔炼温度、保持时间、熔炼材料配比等方面的质量控制。
4.2 浇注操作本章节详述浇注操作的质量控制措施,包括铸型预热、浇注速度、浇注温度等方面的要求。
5.冷却和清理质量控制5.1 冷却过程质量控制本章节介绍冷却过程中的质量控制措施,包括冷却时间、冷却速率等方面的要求。
5.2 清理过程质量控制本章节详细描述清理过程中的质量控制要求,包括清理方法、清理剂的选择等方面。
附件:法律名词及注释:1.法律名词:的解释说明。
2.YYY法律名词:YYY的解释说明。
- 1、下载文档前请自行甄别文档内容的完整性,平台不提供额外的编辑、内容补充、找答案等附加服务。
- 2、"仅部分预览"的文档,不可在线预览部分如存在完整性等问题,可反馈申请退款(可完整预览的文档不适用该条件!)。
- 3、如文档侵犯您的权益,请联系客服反馈,我们会尽快为您处理(人工客服工作时间:9:00-18:30)。
天山铝业重熔用铝锭制程质量管理制度针对质量控制目标,结合我厂的生产特点,制定了明确、具体的工艺质量管理措施,并建立了打渣——倒包——定点取样化验——铸锭——堆垛5个工序质量控制点,从技术措施上指导和保证质量目标的实现。
1 确保铝锭品位和化学成分均匀一致
⑴流槽、小渣铲等铁制工具在使用前刷上滑石粉水浆,烘干后使用,以避免或减少铁等杂质对铝液的污染。
⑵每包中的铝液必须倒尽,同一熔炼号的铝锭为一垛,严禁混放,并对个别品位偏低的电解槽配置专用抬包和流槽,避免质量混杂。
⑶取样由专责检测员在浇铸时从抬包中取每一熔炼号的化学成分试样。
2 符合铝锭的外观质量和锭重、锭型要求
⑴浇铸时在铝液凝固前,及时用小渣铲扒除铸锭表面的氧化膜渣,禁止将扒出的浮渣磕入下模中。
⑵浇铸时控制好流槽中流液稳定,防止因铝液冲击过猛,或扒渣时渣铲速度太快,使铝液涌出铸模而凝固形成飞边。
⑶铝液温度过高时,铝液的含气量大,要采取降温措施,避免在铸锭凝固过程中大量气体溢出形成气孔,或因冷却强度不够,铸锭尚未完全凝固就磕落下来,未凝固的铝液流出,是铸锭上表面形成空槽。
⑷及时更换有裂纹、裂缝、砂眼等缺陷或已变形的铸模,防止铝锭带飞翅或因铸模缺陷中夹带有水分形成气孔,或锭形不规则。
⑸加强铸造机日常维护保养和检修工作,及时清理铸造机轨道上的凝铝,使铸造机运转平稳,以避免严重波纹的产生。
⑹铸锭中根据铸模中铝液深浅程度,准确调整液流量,防止铝锭浇铸过满或不足,使铝锭重量超出了偏差范围,造成重量不符。
(7)外观检验由工人自检和品质检验员相结合,并由品质检验员在合格铝锭表面打上“检”字方可入库。
3、定点取样化验
根据取样的要示配制专用的取样工具,做到所取的铝样能真实代表所生产的铝锭,严禁不按操作规程取样,做到每生产二捆铝锭取一试样。
另外,为实现质量控制管理,我们在组织上建立车间——班组——个人岗位质量责任制,明确规定各自在质量管理中的作用、任务和责任,并把质量与个人效益结合起来进行考核,使大家在工作中各司其职、相互配合,为达到提高产品质量,提高经济效益的目的而共同努力。
同时,在实际工作中,我们不仅认真检查和指导工艺质量管理措施的执行,落实岗位质量责任制,还组织工人对常见的几类质量事故原因进行分析,研究排除和解决方法,积累经验,初步完善工艺质量管理措施,不断的把质量控制管理工作推向深入。
铝锭质量检验评定标准
适用范围
本制度适用于铸造车间重熔用铝锭生产全过程。
本制度规定了铝锭内部质量、外观质量、包装等工序的质量控制方法。
本制度规定了对产品质量的检查与考核。
目的
本制度的目的在于能够更好的控制重熔用铝锭的各项质量标准,保证公司产品质量始终处于合格状态。
一、化学成分控制及外观定级标准按照表一执行:
表一、重熔用铝锭质量标准(GB/T1196-2008)
二、标志
1、每块铝锭上应浇铸或打印生产厂标志。
6.7 包装后对每捆铝锭用红色漆进行编号,编号要正确,写在统一的位置上(最上层铝锭的第二块上,且一定要写在打包带里面)书写时字体要统一工整(为时间字体),字迹要清晰。
化验室将铝品位的化验结果写在如图产位置,仓库要将所称重量写在铝锭编号的左侧(最上层铝锭的第二块上)如图示 如图示:
60 表示为铝锭的品位,化验室用红色漆笔填写。
2、各牌号铝锭应有不易脱落的鲜明标志,其标志规定应符合表二的要求。
3、各牌号铝锭的标示应在单块铝锭的统一位置(铝锭耳槽内)。
表二
三、包装
1、铝锭打捆包装,形式采用“井”字形。
2、铝锭打捆采用钢带或其他材料,但应保证铝锭不散捆。
3、打捆钢带表面应进行防锈处理,抗拉强度不小于490MPa,伸长率不小于5%,尺寸应符合表3的要求,其他要求应符合YB/T025的有关规定。
4、铝锭每捆11层,底层4块,其他每层5块,共54块。
(如图一)
5、铝锭堆垛要整齐,要求锭耳内沿对齐,长短一致,上下一线。
每层铝锭块
块相扣,层层平稳,整捆铝锭四角等高,高差不大于1cm。
6、钢带应打在铝锭耳槽内,侧面两根钢带打在正面两根钢带下面(图二),
四、质量证明书
每批产品应附有质量证明书,其上注明: 1、 供方名称、地址; 2、 产品名称和牌号; 3、 注册商标; 4、 批号; 5、 净重和件数;
6、 分析检验结果和供方质量部门印记;
7、 本标准编号;
8、 出厂日期; 五、检查和验收;
1、重熔用铝锭由供方质量部门进行检验,保证产品质量符合本标准的规定并
填写质量证明书。
2、需方应对收到的产品按本标准的规定进行复检。
如复验结果与本标准或者合同规定的不符合时,应在收到产品两个月内向供方提出,由供需双方协商解决。
如需仲裁,仲裁取样在需方共同进行。
3、铝锭应按批过磅计量。
六、化学成分仲裁取样的和制样:
1、从该批铝锭任一捆上、中、下部各取一块铝锭。
当铝锭散开,分不清上、中、下时,则随机取样不少于三块。
2、采用钻孔法取样。
用直径15mm~20mm的钻头取样,用乙醇作润滑剂。
3、在铝锭的大面,沿其对角线钻孔三处,一处在中心,另两处各距角顶红100mm,各钻孔钻进的深度不小于原厚度的三分之二。
在钻取试样前,必须先清除表面氧化层,其厚度不少于0.5mm。
4、钻取的铝屑应混匀,以磁铁处理后,用四分法缩分,重量不少于100g,作为分析化学成分的试样。
七、仲裁结果处理:
1、化学成分仲裁分析结果与原牌号规定不符合时,按仲裁分析结果定牌号。
2、外观不合格时,按块处理。