最终检验规定(标准范本)
公司产品最终检验规定

公司产品最终检验规定1. 引言本文档旨在规范公司产品的最终检验流程,确保产品质量和符合客户需求。
最终检验是产品生产过程中的关键环节,通过对产品进行全面检查和测试,以确保产品的性能、安全性和符合规定的标准。
2. 检验准备在进行最终检验之前,必须进行充分的检验准备工作,包括但不限于以下内容:•确定检验点:根据产品特点和客户需求,明确最终检验的关键点和检验标准。
•确定检验设备:根据产品特性和检验要求,选择合适的检验设备和工具。
•确定检验环境:确保最终检验环境符合产品的使用条件和要求。
•准备检验记录表格:为每个产品建立检验记录表格,记录检验结果和相关信息。
•培训检验人员:确保所有参与最终检验的人员都接受过专业培训,了解检验流程和要求。
3. 最终检验流程最终检验流程包括以下步骤:3.1 接收产品接收产品时,必须进行以下检查和记录:•外观检查:检查产品外观是否完好,无损坏、划痕或其他质量问题。
•配件检查:确认产品配件齐全,包括使用说明书、电源适配器等。
•标签检查:检查产品标签是否齐全、清晰可读,包括型号、批次号等信息。
•记录数据:将接收产品的信息登记在检验记录表格中。
3.2 功能测试功能测试是确保产品性能符合要求的关键步骤。
根据产品的不同特点,进行相应的功能测试,包括但不限于以下方面:•电气性能测试:对产品的电气性能进行检测,如电压、电流、功耗等。
•功能特性测试:针对产品的特殊功能进行测试,如产品的各项功能是否正常。
•效能测试:对产品的性能进行全面测试,如产品的工作温度、速度等参数。
•压力测试:对产品进行压力测试,确保产品在正常工作环境下的可靠性。
•安全性测试:检查产品是否符合相关安全标准,确保使用时不会对用户造成伤害。
•记录数据:将功能测试的结果和相关信息记录在检验记录表格中。
3.3 标准检查标准检查是针对产品是否符合相关标准的环节。
根据产品的不同类型和行业要求,进行相应的标准检查,包括但不限于以下内容:•材料检查:检查产品所用材料是否符合国家相关标准,如环保标准、可降解材料等。
产品最终检验规范

产品最终检验规范文件QD-T-02-003文件名称:产品最终检验规范版本号:A编制:审核:批准:制定日期:2017-8-20实施日期:2017-8-25版本号修订次数日期说明文件审批编号A0首次发布新文件1首次修订分发部门研发部、技术部、生产部、品保部、销售部(份数)1目的为了进一步明确产品出厂检验标准和检测方法,提升产品品质控制手段。
2适用范围适用于腾亚环境所有产品。
3引用标准GB/T13914-2013 冲压件尺寸公差GB/T 13915-2013 冲压件角度公差GB/T 14295-2008 空气过滤器GB/T 15055-2007 冲压件未注公差尺寸极限偏差GB/T 18801-2008 空气净化器GB/T 1804-2008 一般公差未注公差的线性和角度尺寸的公差GB/T 21087-2007 空气-空气能量回收装置JG/T 22-1999 一般通风用空气过滤器性能试验方法GB/T 2408-2008 塑料燃烧性能的测定水平法和垂直法GB/T 2423.8-1995 电工电子产品环境试验第2部分:试验方法试验Ed:自由落体GB/T 2518-2008 连续热镀锌钢板及钢带GB/T 2828.1-2012 计数抽样检验程序JG/T 294-2010 空气净化器污染物净化性能测定GB 3096-2008 声环境质量标准GB/T 4706.1-2005 家用和类似用途电器的安全第一部分通用要求GB/T 4706.45-2005 家用和类似用途电器的安全空气净化器的特殊要求4矛盾处理4.1本制度与上级制度有矛盾时,以上级制度为准。
4.2与原出厂检验规范冲突部分按本制度执行。
4.3未提及部分按原检验规范执行。
5质量符合性检验5.1产品质量检查内容产品外观检验a)外观要求机组外表面无明显划伤、桔纹、流痕等缺陷机组一级表面单面颗粒Ф≤0.4mm,数量≤2个;颗粒Ф≤0.2mm,数量≤4个,点距应大于50mm机组一级表面单面细划伤0.2×10mm,数量≤2个;0.2×5mm,,数量≤4个,线距应大于50mm机组一级表面色差ΔE≤1.0,三级表面色差≤1.6机组一级表面光泽度:50度≤Gu≤70度b)测试方法●采用目测法检验产品外观是否满足5.1.1a)的要求c)合格判据满足5.1.1a)的要求即为合格,并将检验结果记入记录表。
鞋业行业标准之鞋类产品出厂前的最终检验标准(完整版)
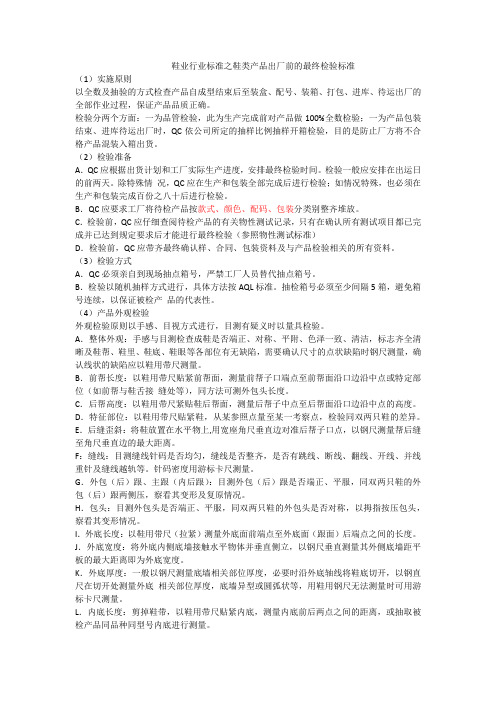
鞋业行业标准之鞋类产品出厂前的最终检验标准(1)实施原则以全数及抽验的方式检查产品自成型结束后至装盒、配号、装箱、打包、进库、待运出厂的全部作业过程,保证产品品质正确。
检验分两个方面:一为品管检验,此为生产完成前对产品做100%全数检验;一为产品包装结束、进库待运出厂时,QC依公司所定的抽样比例抽样开箱检验,目的是防止厂方将不合格产品混装入箱出货。
(2)检验准备A.QC应根据出货计划和工厂实际生产进度,安排最终检验时间。
检验一般应安排在出运日的前两天。
除特殊情况,QC应在生产和包装全部完成后进行检验;如情况特殊,也必须在生产和包装完成百份之八十后进行检验。
B.QC应要求工厂将待检产品按款式、颜色、配码、包装分类别整齐堆放。
C.检验前,QC应仔细查阅待检产品的有关物性测试记录,只有在确认所有测试项目都已完成并已达到规定要求后才能进行最终检验(参照物性测试标准)D.检验前,QC应带齐最终确认样、合同、包装资料及与产品检验相关的所有资料。
(3)检验方式A.QC必须亲自到现场抽点箱号,严禁工厂人员替代抽点箱号。
B.检验以随机抽样方式进行,具体方法按AQL标准。
抽检箱号必须至少间隔5箱,避免箱号连续,以保证被检产品的代表性。
(4)产品外观检验外观检验原则以手感、目视方式进行,目测有疑义时以量具检验。
A.整体外观:手感与目测检查成鞋是否端正、对称、平附、色泽一致、清洁,标志齐全清晰及鞋帮、鞋里、鞋底、鞋眼等各部位有无缺陷,需要确认尺寸的点状缺陷时钢尺测量,确认线状的缺陷应以鞋用带尺测量。
B.前帮长度:以鞋用带尺贴紧前帮面,测量前帮子口端点至前帮面沿口边沿中点或特定部位(如前帮与鞋舌接缝处等),同方法可测外包头长度。
C.后帮高度:以鞋用带尺紧贴鞋后帮面,测量后帮子中点至后帮面沿口边沿中点的高度。
D.特征部位:以鞋用带尺贴紧鞋,从某参照点量至某一考察点,检验同双两只鞋的差异。
E.后缝歪斜:将鞋放置在水平物上,用宽座角尺垂直边对准后帮子口点,以钢尺测量帮后缝至角尺垂直边的最大距离。
最终检验规范

编号:-5CT-08
第0次修订
标题:最终检验规范
修订日期:2008年3月
实施日期:2008年3月
版号:A
页码:1/2
1目的
确保产品整体性能符合标准规定,兑现向顾客的承诺。
2范围
适用于套管、接箍和短节的最终检验和试验。
3检验要求
最终检验和试验包括:产品性能检验(压力试验)、磷化和成品入库前检验和产品交付检验。
2)内外表面上任何方向,深度大于表3所示数值的任何缺陷。所有加厚产品的内加厚轮廓上都不应有尖角或截面突变。
3)淬火裂纹
3)长度检查:每捆油、套管之差值小于20mm
4)油漆:色彩均匀、光亮,不得有皱皮、流痕、露底、杂物等缺陷,颜色符合API 5CT规范要求
3.3.2接箍
1)表面检查:在磷化之前进行内眼检查,不应有内眼可见的发裂、裂纹和气体,不应有破坏螺纹连续性的缺欠,若有夹痕、点坑、圆底或尖底凿槽及类似缺欠,只要这些缺欠不超过下表的深度,仍认为合格。
3.1产品压力试验
3.1.1试验机应配备各种装置,以保证满足规定的试验压力和时间间隔要求。在每次试验前4个月内,试验压力测量装置应用固定静载压力试验机或同类设备进行校准。校准和验证记录应保存5年。
3.1.2压力试验按《压力试验规范》的规定执行。
3.2磷化
3.2.1由外协单位进行,为公司合格供方名单中的合格供方。
5.3经检验不合格品由检验员开出《不合格品评审报告》(FY/JLQ058),执行《不合格品控制程序》。
编制:陶阳
审核:
批准:
公司套管厂技术文件
编号:-5CT-08
第0次修订
标题:最终检验规范
修订日期:
实施日期:2008年3月
气瓶安装质量最终检验管理制度范文

气瓶安装质量最终检验管理制度范文一、概述本制度旨在规范气瓶安装质量最终检验工作,确保气瓶安装质量符合相关标准和要求,提高工作效率和质量水平。
本制度适用于所有涉及气瓶安装最终检验的岗位和人员。
二、工作职责1. 气瓶安装质量最终检验人员应严格按照相关标准和要求进行检验,确保气瓶安装质量符合规定;2. 气瓶安装质量最终检验人员应对涉及到的气瓶、管道、阀门等安装设备进行全面检查,确保设备完好无损;3. 气瓶安装质量最终检验人员应准确记录检验结果,并及时上报相关部门;4. 气瓶安装质量最终检验人员应做好检验数据的保存和归档工作,以备后续查阅。
三、工作流程1. 准备工作:(1)收集相关检验标准和要求,做好预检准备;(2)收集所需检验工具和设备,确保检验工作的顺利进行;2. 开展检验工作:(1)对气瓶、管道、阀门等安装设备进行全面检查,包括外观、尺寸、材料、紧固件等方面;(2)对气瓶安装过程中的焊缝、密封、连接等关键部位进行仔细检查,确保符合相关标准和要求;(3)检查气瓶安装过程中是否存在质量问题,如松动、变形、损坏等;3. 处理检验结果:(1)对于符合要求的气瓶安装,填写相应的检验单据,并及时上报相关部门;(2)对于不符合要求的气瓶安装,及时通知相关责任人,要求其进行整改;(3)记录检验结果和处理情况,做好数据保存和归档工作。
四、质量保证措施1. 加强培训:对气瓶安装质量最终检验人员进行定期培训,提高其专业素质和技能水平;2. 配备检验工具和设备:保证检验工作所需的工具和设备齐全,并进行定期维护和检修;3. 审核制度:建立对气瓶安装质量最终检验工作的审核制度,确保检验结果的准确性和可靠性;4. 检查制度:建立定期检查机制,对气瓶安装质量最终检验工作进行抽查,发现问题及时整改;5. 反馈机制:对气瓶安装质量最终检验中发现的问题,及时向相关部门和责任人反馈,确保问题及时解决。
五、责任追究对于违反本制度的行为,将按照公司相关管理制度进行追究责任,包括但不限于警告、处罚、降职甚至开除。
API6A最终检验规范

1目的
确保产品整体性能符合标准规定,兑现向顾客的承诺。
2范围
适用于本公司产品的最终检验。
3职责
3.1、生产部负责产品的装配、试验、油漆等作业。
3.2、质量部负责检验和记录。
4程序
4.1最终检验包括:产品性能检验、成品入库前检验和产品交付检验。
4.2 产品性能检验。
试验过程中所有检测设备都要完好无损,必须满足产品性能试验的要求,所有压力表及计量器具都要在有效的检定周期内,压力表的量程应根据额定工作压力确定并符合有关要求,压力表及计量器具的准确度和精确度要满足产品性能试验的要求。
产品性能试验前必须检查检测设备是否完好。
4.2.1装配连接性代号
a)PSL 1无要求
b)PSL2-4阀、井口装置、三通、四通、油管头异径接头、悬挂器、节流阀和流体取样器要求系列化。
4.2.2 跟踪性记录
a)PSL1-2无要求
b)PSL3-4应编写鉴定部装设备本体、盖、阀杆、端部和出口连接与阀孔密封机构的报告,以实现装配跟踪。
最小保持压力时间为3min。
在各稳压周期之间,应将压力降到零。
闸板或旋塞的每一侧,至少试两次。
b)验收准则
在稳压期间,无可见渗漏。
4.2.4 PSL2试验
4.2.4.1通径试验- 全孔阀 与PSL1要求相同。
4.2.4.2通径试验- 采油树 与PSL1要求相同。
4.2.4.3本体静水压试验- 单独设备 与PSL1要求相同。
(3)具有入口连接比出口连接有较高压力额定值的节流阀,从入口连接至可更换阀座(或节流油嘴)的阀体 – 油嘴密封点阀体,应按入口连接的相应压力作静水压试验,从密封点下游的阀体其余部分,应按出口连接相应的压力试验。可采用临时阀座密封,以便于试验。
三级检验制度(最终)

QB 中铁十一局集团第三工程有限公司蒲城制梁场企业标准PC/CR11LC01.02-2009预制后张法预应力混凝土铁路桥简支T梁三级检验制度编制:审核:批准:受控编号:发放编号:2009-1-10发布2009-1-10实施中铁十一局集团第三工程有限公司蒲城制梁场发布三级检验制度1 范围本标准规定了桥梁生产过程中从原材料投入到成品验收入库各工序的质量检验要求。
本标准适用于包西铁路蒲城制梁场桥梁生产的各项工序的检验。
2 术语2.1 自检:就是“自我把关”。
操作者对自己加工的产品或完成的工作进行自我检验,主要起到自我监督的作用。
确认合格后,才能流入下道工序。
对自检未达到标准的产品或半成品,及时修复,未经修复不得流入下道工序。
互检:就是操作者之间对加工的产品、半成品和完成的工作进行相互检验,起到相互监督的作用。
互检中对发现问题应作记录,及时向质检人员进行信息反馈并通知上道工序进行纠正,本班组工序在互检中发现未达到质量标准时,及时修复使之达到标准再流入下道工序。
专检:就是专职检验员对产品质量进行检验,负责产品的主要工序的工艺检查,发现有不执行操作规程时,立即制止并进行说服教育,对屡次违章操作者及时向技术主管反映,如影响产品质量时立即制止并加以纠正后方可流入下道工序。
3 总则3.1 产品质量是企业各项管理工作的综合反映,是全面质量管理的重要组成部分,生产中,要树立精品意识,实行自检,互检和专检相结合的三级检验,正确处理质量与数量的关系,确保出厂产品质量达到标准规定的要求,实现顾客满意的愿望。
产品质量检验工作贯彻“预防为主”的原则,实行三级质量检验制度。
做到层层把关,确保不合格的产品不出厂。
4 原材料、工装、配件、外协件及工序三级检验制度4.1原材料和配件、外协件在进场要执行三级检验制度。
原材料和外协件进场后,首先是物资设备部检查厂家的出场材质证明书、生产日期、出场日期、批号、数量、外观等。
4.2按照《原材料检验制度》上要求对材料检验项目进行委托试验室或者质检员进行试验和检验。
最终检验规范
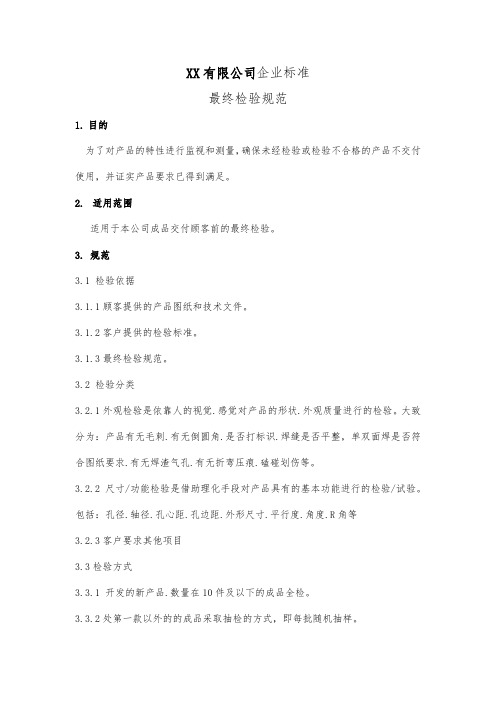
XX有限公司企业标准最终检验规范1.目的为了对产品的特性进行监视和测量,确保未经检验或检验不合格的产品不交付使用,并证实产品要求已得到满足。
2.适用范围适用于本公司成品交付顾客前的最终检验。
3. 规范3.1 检验依据3.1.1顾客提供的产品图纸和技术文件。
3.1.2客户提供的检验标准。
3.1.3最终检验规范。
3.2 检验分类3.2.1外观检验是依靠人的视觉.感觉对产品的形状.外观质量进行的检验。
大致分为:产品有无毛刺.有无倒圆角.是否打标识.焊缝是否平整,单双面焊是否符合图纸要求.有无焊渣气孔.有无折弯压痕.磕碰划伤等。
3.2.2尺寸/功能检验是借助理化手段对产品具有的基本功能进行的检验/试验。
包括:孔径.轴径.孔心距.孔边距.外形尺寸.平行度.角度.R角等3.2.3客户要求其他项目3.3检验方式3.3.1 开发的新产品.数量在10件及以下的成品全检。
3.3.2处第一款以外的的成品采取抽检的方式,即每批随机抽样。
4. 检验实施4.1检验员接到完工的最后工序通知后,确定该产品所规定的检验都已经完成,且结果满足规定要求后方能进行最终检验。
4.2检验员按检验依据和检验分类中的项目对产品进行检验。
这里特别注意的是:顾客图纸中有的尺寸和形位位置没有标注公差,但在技术要求中规定:***未注公差按***标准执行,这里的标注不是没有公差而是未注公差。
例如:图纸技术要求中未注线性公差和角度公差按QC/T268执行,几何公差按GB/T13916-m执行。
这就是给出了未注公差,检验按技术要求中的未注公差执行。
4.3检验员按检验方式规定的抽样数抽样,检验合格的在《工艺流程卡》上签字予以确认。
检验员确定合格后,由操作者运至成品库与保管员进行交接。
检验员应将检验结果记录在《终检记录》中。
4.4检验员按检验方式规定的抽样数量进行抽样检验,发现有不合格品时应在原抽样的基础上加倍抽样数量。
通过再抽样检验没有发现不合格品时应按4.3执行。
气瓶安装质量最终检验管理制度模版
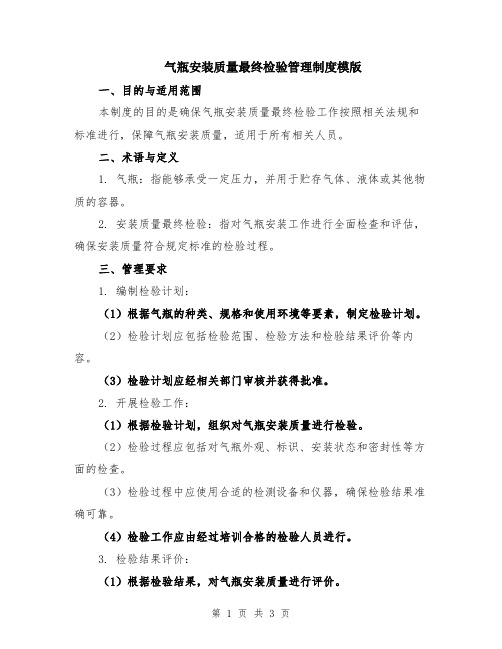
气瓶安装质量最终检验管理制度模版一、目的与适用范围本制度的目的是确保气瓶安装质量最终检验工作按照相关法规和标准进行,保障气瓶安装质量,适用于所有相关人员。
二、术语与定义1. 气瓶:指能够承受一定压力,并用于贮存气体、液体或其他物质的容器。
2. 安装质量最终检验:指对气瓶安装工作进行全面检查和评估,确保安装质量符合规定标准的检验过程。
三、管理要求1. 编制检验计划:(1)根据气瓶的种类、规格和使用环境等要素,制定检验计划。
(2)检验计划应包括检验范围、检验方法和检验结果评价等内容。
(3)检验计划应经相关部门审核并获得批准。
2. 开展检验工作:(1)根据检验计划,组织对气瓶安装质量进行检验。
(2)检验过程应包括对气瓶外观、标识、安装状态和密封性等方面的检查。
(3)检验过程中应使用合适的检测设备和仪器,确保检验结果准确可靠。
(4)检验工作应由经过培训合格的检验人员进行。
3. 检验结果评价:(1)根据检验结果,对气瓶安装质量进行评价。
(2)评价结果应分为合格和不合格两种情况,并进行相应记录和处理。
(3)对于不合格的气瓶安装质量,应制定整改措施,并进行追踪到位。
4. 记录与归档:(1)对气瓶安装质量最终检验的相关信息,应进行记录和归档。
(2)记录内容应包括气瓶的种类、规格、安装单位、检验人员、检验时间和评价结果等。
(3)归档材料应妥善保管,便于随时查阅。
四、责任与权限1. 检验人员应根据相关规定和标准,进行检验工作并提出评价结果。
2. 检验计划的编制和审核由专业技术人员负责。
3. 检验结果的评价和整改措施的制定,由专业技术人员和管理人员共同参与。
五、培训与考核1. 对从事气瓶安装质量最终检验的人员进行培训,确保其具备必要的专业技能和知识。
2. 培训内容应包括相关法规、标准、检验方法和评价要求等。
3. 定期对检验人员进行考核,确保其工作质量和技术能力。
六、附则1. 本制度的修改和废止,由相关部门负责,并进行相应的通知和培训。
最终检验规范(出货检验规范)

最终检验作业规范版次A2 成品页次1/25一﹑目的:为保障公司成品质量可靠度,增加市场竟争能力,保障客户权益,提高本公司信誉特制定本检验规范.二﹑适用范围:本公司交运至客户之成品(含自制品及外发产品)皆适用之.三﹑抽样标准:3.1 除非客户契约特要求,本公司一概采用,MIL-STD-105E 一般检验水平II(见附表-附表一)之单次抽样计划.3.2 转换准则:3.2.1 正常→加严﹑减量:当某生产线送检批连续10批允收时,抽样程序由正常转换为减量检验;当连续5批中有2批判退时,抽样程序由正常转换加严检验.3.2.2 加严→正常:当某生产线送检批连续5批加严检验均正常时即由加严转换为正常;3.2.3 减量→正常:当某生产线在减量检验过程中有1批判退时,即由减量转为正常;3.2.4新线投单开始一个月一概采用加严检验;客诉/客户退货重检之产品采用加严检验;3.2.5 QA根据各线成品检验状况(见统计资料)施行转换程序;3.2.6首批生产之新机种及新客户首批出货之机种一概采用加严检验;3.2.7加严检验与减量检验方法,即送检数之相对应之抽检数加严至下一个和上一个及减量一个栏位,以决定实际抽检数量.3.2.8 E125型以下200PCS以下全检,E125型以上100PCS以下全检;开关电源类产品100pcs以下全检.3.3 抽样方式:第一步:根据送检单所覆盖的总箱数决定抽样箱数,方法为将总箱数开算术平方根,若所得值为非整数,则采用进尾法在整数基楚上多抽一箱.第二步:在所抽取的箱内按抽样计划要求的数量随机抽取样本;若依该步骤所抽之箱数在变压器总数未达样本数要求,则需继续抽样,直至满足样本要求为止.3.4 除非客户契约特别要求,本公司将不合格分二大类:主要缺点&次要缺点.3.5除非客户契约特别要求,本公司规定允收质量水平及抽样水平为;3.5.1 允收品管水平:3.5.1.1 严重缺点:(CR):AQL=03.5.1.2主要缺点(MAJ):AQL=0.4%3.5.1.3 次要缺点(MIN):AQL=1.5%3.5.1.4 本厂所有功能电气特性及安规类验收水准规定为0收,1退.3.6抽样方案:根据样本大小字码和允收质量水平索抽方案.3.6.1样本大小字码:从提交检查批量所在据行和规定的检查水平所在列相交处读出样本大小字码;使用方法:由3.6.1得到样本大小字码,水平向右在样本大小栏内读出样本大小再从样本大小字码所在行和规定的合格质量水平所在列相交处读出判定数组(AC﹑RE);若在相交处是箭头,则沿着箭头的方向读出箭头所指的第一个定数组(AC﹑RE),然后,由此定数组(AC﹑RE)所在行向左在样本大小等于或大于批量时,将该批量作样本大小,抽样方案的下数组保持不变.3.7除非客户契约特别要求,本公司一概采用缺陷数法检索正常检验方案使用记录不符合数量. 日期:确认:审核:制表:最終檢驗作業規範版次A2 成品頁次2/25四﹑產品檢驗條件:4.1檢驗環境條件:4.1.1在正常的太陽光線下,40W日光燈下檢驗,而對品質較高者以高於150W燈光之光度檢驗仍屬許可;4.1.2檢驗者的視力須在1.0以上,檢驗時檢驗距離在20-30cm,檢驗時間2秒;4.1.3不可將零件故意放置在造成反射之角度下,以強調顯示出表面缺點(即不可以單燈照明以折射反映表面缺點);4.1.4一般正常檢驗外觀檢視不可以使用放大鏡.4.2檢驗方式:4.2.1外觀:目視;4.2.2測試選定經校驗儀器進行.4.3名詞定義:4.3.1 A面(主要面):指客戶使用上之外觀正面及主要標簽粘貼位置;4.3.2 B面(次要面):指客戶使用上之外觀側﹑背面:4.3.3 C面(客戶使用)上之外觀底面;4.3.4 嚴重缺點:在特定使用條件下會導致生命財產有危險或不安全之缺點.主要缺點:直接影響產品功能與使用的缺點.4.3.5次要缺點:不直接影響產品功能與使用﹑但對產品的潛在價值及有效使用有不良影響的缺點;4.3.6明顯刮傷:正常光亮度及肉眼下刮傷顯而易見,或用手觸摸有明顯感覺;4.3.7 錦林常規產品簡述:低頻類:Adaptor: 傳統化組裝CASE,AC PIN或AC CORD INPUT,& PLUG OUTPUT;PIN針類:插針型;線圈用絕緣膠帶包覆並帶有絕緣膠套, 鐵芯四周包覆絕緣膠帶或凡立水. PIN針INPUT/OUPUT;引線型:線圈用絕緣膠帶包覆,鐵芯四周涂凡立水,腳架,螺絲固定或有上鐵帶固定,初級引線次級引線帶端子和HOUSING;高頻及磁環類,磁棒.電感類:高頻鐵芯為鐵氧體磁芯(FERRITE CORE),結構為EE,EI,UU,EP型組合;磁環線圈鐵芯為環形鐵芯,線圈環繞於鐵芯上;磁棒.電感類:鐵芯為鐵氧体的棒狀,DR型等.線圈繞于鐵芯.音頻類:鐵芯為鎳鋼片,結構為EE 型組合.開關電源: 大範圍輸入,穩定電壓輸出,以高頻變壓器取代工頻變壓器來進行電壓轉換和電網隔離,采用脈衝調製技術的變換穩壓電源.信息類: 適用於ISDN,ADSL等信息產業類產品,有LINE,MODEM,PHONE,等多端分頻端口.4.4說明:4.4.1附表二﹑三﹑四﹑五﹑六﹑七為錦林常規產品之常規檢驗部份,加*號為非常規項目,在客戶有指定要求時方執行之.或者依客戶SPEC執行;日期:確認:審核:制表:最終檢驗作業規範版次A2 成品頁次3/254.4.2若此標準之內容興相關資料發生沖突時,則檢驗標準以客戶檢驗規範﹑工程規格資料表,工程變更,最終檢驗規範之先后順序執行;4.4.3若此標準之內容未能完全涵蓋部份,得由品管會同相關單位予以補正.4.5 成品分類:4.5.1 開關電源類産品(見附件二);4.5.2 引線型,PIN針類產品(見附件三);4.5.3 高頻及磁環線圈類,磁棒.電感類產品(見附件四);4.5.4 音頻類產品(見附件五);4.5.5 信息網絡產品類(見附件六) ;4.5.6 排線類産品(見附件七);4.6 表單記錄與中止檢驗:4.6.1 品管員需將檢驗結果如實記錄於(測試報告),《成品檢驗記錄表》僅記錄前10個樣本的完整特性數據及外觀狀況,其余之樣本數(若樣本數多於10個)不予完整記錄(但QA 須執行同前10個一樣的完整檢驗動作),產品尺寸檢驗每批限定僅抽10PCS進行實際量測與記錄.4.7 不良制定與處理;4.7.1不良品制定:當樣本被發現與工程資料,麥頭資料及客戶特別要求有一項不符合者該樣本即被視為不良品,不良品經品管員挑出後,應貼附相應不良標簽並呈QA主管確認;4.7.2 當缺陷數超過允收標準時,該送檢批即為不良批,不良批須由QA主管將不良品會生產課共同確認批退該受檢批,批退后交相關部門妥善處置(重工,重修,重檢或者報廢);4.7.3 QA驗完貨,不良品被取出後,應向生產單位取合格品補入才能送出產品,若生產單位尚未有產品可供補入,則QA不得判定合格,不得送出所有報告及貼合格檢簽,補樣由生產課領班交QA主管確認,再由主管補入.4.8 工程樣品檢驗標準:4.8.1工程樣品檢驗之依據為業務委作資料及客戶所提供,當設計依據之資料和圖面和客人提供之資料和圖面僅供設計參考,則依據樣品承認書作為檢驗依據.4.8.2 QA在檢驗樣品完畢後,需對此(樣品承認書)與業務委作單,客人資料之一致性,不一致的填寫聯絡單回饋工程;4.8.3當工程樣品驗收失敗時,提出異常回饋意見於樣品送檢單上,由工程部提出原因分析及改善對策並追蹤改善,若重新檢驗時則需附上此單,在不符合項糾正完畢後由工程部,品管部,業務部分別存檔備案,若屬可以立即解決之輕微缺陷,不填此單,只在樣品檢驗記錄表中注明即可;4.8.4除上術三項外,樣品檢驗標準與產品保持一致.4.9 外購﹑委外加工產品:一個外購廠商完全視同本公司一條生產線,執行與本公司完全相同之檢驗標準.五﹑出貨檢驗標準:5.1任何成品離廠前必須接受出貨品管員的檢驗.5.2檢驗項目包括數量﹑機種﹑包裝方式﹑是否貼追控標簽,是否貼有環保標示,搬運狀況等. 日期:確認:審核:制表:檢驗和試驗抽樣作業規範(MIL-STD-105E)文件編號WI-Q-033 版次A2頁次4/25樣本代字批量樣本數AQL0 0.4 1.5A 2-8 2 AC RE AC RE AC REB 9-15 3 0 1 0 1 0 1C 16-25 5 0 1 0 1 0 1D 26-50 8 0 1 0 1 0 1E 51-90 13 0 1 0 1 0 1F 91-150 20 0 1 0 1 1 2G 151-280 32 0 1 0 1 1 2H 281-500 50 0 1 0 1 2 3I 501-1200 80 0 1 1 2 3 4J 1201-3200 125 0 1 1 2 5 6 K 3201-10000 200 0 1 2 3 7 8 L 10001-35000 315 0 1 3 4 10 11 M 35001-150000 500 0 1 5 6 14 15 N 150001-500000 800 0 1 7 8 21 22 O 500001-OVER 1250 0 1 10 11 21 22 如樣本大小等於或超過批量時則用100%檢驗AC=允收數RE=拒收數AQL值規定為:CR=0 MAJ=0.4 MIN=1.5附件二開關電源類一.功能特性類:序號檢驗項目檢驗工具/方法檢驗數量缺陷描述缺陷等級備注CR MAJ MIN1輸入輸出特性測試Input/OutputtesATE6000/3610A樣本數輸出空載電壓偏離規格✓依<<工程規格書>>;<<客戶承認書>>輸出負載電壓偏離規格✓漣波電壓高於規格✓效率低於規格✓2*Dynamic test 動態特性測試ATE6000/3610A樣本數輸出空載電壓偏離規格✓輸出負載電壓偏離規格✓漣波電壓高於規格✓Dv偏離規格✓產品模似使用工作中不穩定或不動作✓3Load tegulationtest 負載效應測試ATE6000/3610A樣本數輸出空載電壓偏離規格✓輸出負載電壓偏離規格✓漣波電壓高於規格✓輸出電壓不穩定或不工作或負載調整率低✓4Line regulationtest電源效應測試ATE6000/3610A樣本數輸出空載電壓偏離規格✓輸出負載電壓偏離規格✓漣波電壓高於規格✓輸出電壓不穩定或不工作或負載調整率低✓5*Combine regulationtest 混合效應測試ATE6000/3610A樣本數輸出空載電壓偏離規格✓輸出負載電壓偏離規格✓當輸入某電壓時,產品某項不良或多項不良✓當帶載於某電流值時,產品某項不良或多項不良✓效率低於規格✓漣波電壓高於規格✓6Turn on&sequencetest開機測試ATE6000/3610A樣本數不啟動無輸出✓7 Horn on&Sequencetest關機測試ATE6000/3610A樣本數不符合要求,達不到産品斷電✓關機時所要求的各項設計參數✓8*Over loadprotecton test 過載保護測試ATE6000/3610A樣本數電流過載時,電壓仍有輸出✓9*Over loadprotection test 過載保護測試ATE6000/3610A樣本數電流過載時,電壓仍有輸出✓10 Short circutt tset短路測試ATE6000/3610A樣本數短路測試時輸出電壓不為零✓短路測試過後輸出電壓偏離規格✓短路測試過後無電壓輸出或輸出不穩定✓11 *Orp/uvp test 過電壓/低電壓保護測試ATE6000/3610A樣本數過電/壓低電壓保護測試,仍有電壓輸出✓12TOTAL*REGULATION TEST總效應測試ATE6000/3610A樣本數Dv偏離規格✓輸出空載電壓偏離規格✓輸出負載電壓偏離規格✓漣波電壓高於規格✓低電壓輸入時初級電流高於規格✓效率低/其它項不良✓13 *VIN RAMP TEST 輸入電壓极限測試ATE6000/3610A樣本數輸出電壓偏離規格✓14 交流輸出電壓電子負載樣本數電壓偏離規格✓二﹑安規類:序號檢驗項目檢驗工具/方法檢驗數量缺陷描述缺陷等級備注CR MAJ MIN1HI-POTTEST 耐壓測試耐壓机樣本數高壓擊穿✓依<<客戶承認書>> <<工程規格書>>2 *AC PIN 與外殼縫隙耐壓測試耐壓机10PCS/批高壓擊穿✓3 *電磁干擾電子干擾測試儀樣品數超過規定值✓三.信賴試驗序號檢驗項目檢驗工具/方法檢驗數量缺陷描述缺陷等級備注CR MAJ MIN1 DROP TEST 落地實驗*整箱落地(1米任意方向自由落體)1箱/LOT1.紙箱字損壞嚴重,已無法辨認2.紙箱開裂露出小白盒✓單体3英尺3面3次或依客人要求2PC/批外殼有裂紋及開裂✓四﹑尺寸類:序號檢驗項目檢驗工具/方法檢驗項目缺陷描述缺陷等級備注MAJ MIN1 成品長/寬/高度等CASE各尺寸卡尺10PCS/LOT 偏離規格✓依<<工程規格書>><<工程圖面>2 AC PIN長/PIN距/傾斜度卡尺/目視/量角器10PCS/LOTPIN歪傾斜度:工程樣品>3°,其它產品>5°✓偏離規格✓偏離規格但不影響客戶使用/兩PIN長之差距<0.3mm✓3 AC PIN寬/厚度卡尺10PCS/LOT 偏離規格✓4 輸出線長度卷尺/直尺10PCS/LOT 小於規格✓依<<工程規格書>>《工程圖面》大于規格✓5輸出線端子頭內徑/外徑/長度卡尺10PCS/LOT 偏離規格✓6 其它尺寸各種量具10PCS/LOT偏離規格且直接影響產品使用✓偏離規格且不直接影響產品使用✓五﹑外觀類:序號檢驗項目檢驗工具/方法檢驗數量缺陷描述缺陷等級備注1 CASE 目視/塞規/卡尺樣本數A面注塑嚴重不良短射,流紋,有明顯結合線✓依<<工程規格書>> 25mm²>塑料射出縮水/毛邊≧10mm2✓塑料射出縮水/毛邊 25mm²✓有針孔/B.C面變形或內陷 1cm²✓斷裂缺損/錯模/死料(凸點凹點)/注塑口凸出及凹陷.✓B C面有雜色.污點不可擦除直徑>0.5mm✓雜色.污點在20-30㎝內40W燈光下,2秒內目視明顯✓燙傷/刮傷程度用手角摸有尖刺感覺者或露出底材.✓外殼刮傷長度:A面<2.5㎜,B面<3㎜,C面<3.5㎜.深度<0.15mm且同一面只有一條.✓外殼燙傷,破損✓A面有雜色,污點✓B,C面有雜色或污點2點距離在40mm.以上.✓表面有異物或雜色可以擦試干凈(面積<1 mm²)✓外殼縫隙大于0.3 mm. ✓毛邊>0.3mm. ✓錯位:41型(含)以下>0.3mm; 41型(不含)以上>0.5mm.✓影響銘板平整. ✓內有异物,響動,晃動✓組裝後上下蓋顏色有落差現象. ✓2 捺印/銘版/標簽目視樣本數顏色,規格,內容錯誤,內容模糊不清,斷字,位置貼錯✓依<<工程規格書>><<工程圖面>>臟污可擦試✓有雜色點/气泡<0.9 mm²✓划傷<4mm.深度<0.1 mm ✓臟污不可擦試✓重影20-30 mm目視2S有重影✓歪斜>5度. ✓歪斜<5度. ✓起皺貼翹或標簽翹>1/5其寬度✓漏貼(印)或貼(印)反或脫落✓字體大小不符✓3AC/DC/CORD及引線目視樣本數破皮﹑露銅﹑無印字﹑規格不符﹑印字不清﹑無法辨認﹑有不可擦試之污染.✓壓痕/綁束帶綁後鬆開/刮傷長度在10mm內或圓周<1/3R✓應綁束帶而未綁漏綁/刮傷長度在10mm以上或圓周 1/3r✓4 PLUG頭目視樣本數氧化/刮傷/變形/破損/測試時測試冶具不良造成错误!未找到引用源。
涂层产品最终检测标准

一、目的:对生产出来的涂层板进行检验,防止不合格品的产出。
二、范围:涂层车间三、涂层板定义:以光铝为底材,经系列工艺,在其表面施加装饰性或保护性涂层。
四、产品分类:按产品用途分:面涂、底涂。
按油漆种类分:聚酯树脂型(PE)和丙烯酸树脂型(AC)1、面涂(面漆):是铝塑复合板正面铝箔上的涂层,起到装饰、保护功能、要求有较好的性能指标。
2、背涂(背漆):是铝塑复合板反面铝箔上的涂层,起到保护背面铝箔不受潮、不氧化的作用。
五、铝基板预处理要求:所用铝基板应经过多级清洗和预处理,以去除铝基板表面油污、脏物和自然形成的松散和氧化层,并形成一层紧密的化学转化膜,以利于涂层的牢固粘结。
六、铝基板要求:1、铝卷外包装应附有厂名、合金牌号、合金状态、批号、规格、生产日期、重量;2、卷材应卷紧、卷齐,无凹陷、碰伤,背涂卷材允许有轻微印痕,轻度不平整、压痕、划伤及小量锈斑,不明显波浪,鼓包,允许存明显横竖色差条纹。
七、涂层彩卷要求:1、涂层彩卷外观应整洁、整齐,不得有油污、凹陷、跑偏和碰伤;2、涂层彩卷外观质量的检测应在自然光条件下进行,将1200×1000(mm)的铝箔固定在平板上,板与水平面夹角为70°,距板心3M处目测,对目测到的缺陷用精度为1mm的直尺测量其最大尺寸,最大尺寸不得超过表一中缺陷规定的上限,检查需两人进行,抽取和铺放试样者不参加检验。
3、(表一)第24页八、涂层物理力学性能的检测1、试样的制备:每次取3块小样,取样时距离不少于50mm;2、涂层厚度:试验方法:用测厚仪测量,要注意调零和校准,在板面色差符合规定的情况下,测10次取平均值,测量点要距板边10mm以上。
3、光泽度偏差:光泽度根据客户要求量定。
用光泽仪测量,当光泽度小于70时,测量极限误差≤10,光泽度大于70时,测量极限误差≤5。
4、铝笔硬度:漆膜铅笔硬度的最低要求≥HB。
试验可用手划,将铅笔垂直在砂纸上磨平,铅笔与试样表面成45º角,以1kg的压力匀速向前推进5mm。
制袋制程及最终检验标准
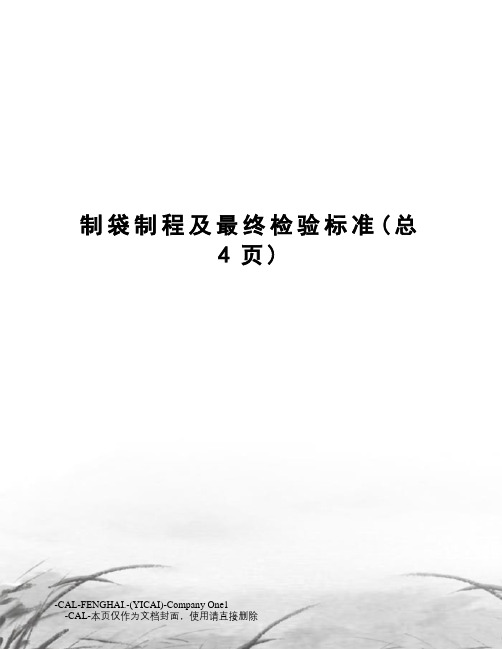
制袋制程及最终检验标准(总4页)-CAL-FENGHAI.-(YICAI)-Company One1-CAL-本页仅作为文档封面,使用请直接删除适用范围:本标准适用于制袋工序生产过程中生产人员对所生产产品的自检、质量控制及品管人员对制袋产品的制程检验和制袋成品包装缴库时的完工检验和出货前的出厂检验。
标准内容:1.抽取样本1.1依制袋机生产顺序,确定检验对象,在已确定的品种被制袋成型为成品状态的产品中随机抽样。
生产人员每一百只自检一次,制程检验人员每两小时抽查一次。
1.3成品包装缴库前进行完工检验。
产品出货前作出厂检验。
完工检验和出厂检验的抽样规格及数量执行以下标准:以产品个数抽样的抽样标准以产品包装件数抽样的抽样标准3.1上述指标全部合格则判定为合格;上述指标有一项不合格,则判定为不合格。
3.2首检合格才允许正式生产,制程检验发现不合格及时通知生产人员调整,必要时停机处理。
生产过程中意外停机或生产人员调整后须重复首件检验直至合格。
3.3制程检验发现的不合格品和出厂检验发现的不合格品,如果可以筛选或修复的由当班生产人员负责筛选或修复,无法筛选或修复的不合格品要开出《不合格产成品报告处理单》进行相应处理。
3.4 生产成品缴库前须由品管人员按计划缴库数量抽样作完工检验,完工检验不合格的产品不可缴库;库存产品出厂前须由仓库人员通知品管按照出货量进行抽检,作出厂检验。
4.记录与区分4.1分切和制袋制程检验及判定结果,分别填入《分切/制袋制程检验记录》,生产人员自检不做记录。
4.2产品缴库前的完工检验由品管记录检验数据和判定结果于《完工检验报告》上作为缴库依据;产品出厂前由品管人员作出厂检验,将出厂检验的数据和判定结果记录于《出厂检验报告》上,作为出厂放行的依据。
4.3对所有已检、未检产品作出明确、固定的标识,区分摆放。
已检合格的成品放入待包装区域。
4.4已检不合格产品可返工,重修的退还生产部门返工,若不合格又不能返工利用的,放入待处理品区域,同时填写《不合格产成品报告处理单》呈报公司批示后处理。
出货检验标准【范本模板】

一、目的为保证本公司的最终产品品质,加强对出货产品的检验,确保检验合格后的产品才能包装、入库、发货.二、范围适用于本公司最终产品的出货检验。
三、职能1、品质科负责成品的检验、包装、及检验规定的制定和培训。
2、采购员负责成品的发货工作。
3、需入库的产品,由仓库管理员进行防护、标识、分类保管。
四、标准内容1、成品的定义:已完成全部生产过程,经检验合格后就可以交货的产品。
2、检验方式:检验人员根据”检验日单”对需检验的产品进行3文件核对无误后,将流转盒中的产品整齐的摆放在检验工作台上,需对该批次产品一一检验,杜绝偷工减料(不检验或者抽检),并及时的记录在检验报告单上,不合格处以记号笔标识在产品上。
3、最终产品的判定a)不合格品,需报废或返工的。
b)不合格品,可特采接收的.c)合格产品,需入库的。
4、检验项目3。
1外观的检测a)产品不得有磕碰、划伤、毛刺等现象b)产品不得有材料缺陷。
c)产品不得有裂纹、气孔、浃渣、焊接缺肉等现象。
d)经过氮化的产品,观察氮化颜色:应该为均匀黑色或灰色,若出现金属色,则为不合格品。
e)对于特殊工序加工的,如抛光等,必要时需借助专门测量仪器观测。
d)观察产品是否有按客户要求刻印的代号(刻印的位置、内容无误),如发现没有,则核对清楚后在规定位置刻印上代号。
3。
2结构、尺寸的检测a)根据客户图纸对产品进行一一检验,不得有漏检项。
3.3性能的检测:一般指材料的硬度要求、氮化质量、对产品特性影响较大的,需着重注意。
3。
4附件检验人员应核对清楚是否有客户特别要求的指示,如提供的检测报告材料等.3.5包装检测:检验人员检查产品的包装形态,确认产品的名称、规格、数量、包装要求、标识、邮寄地址是否符合要求,不符合要求则按包装文件重新包装、标识.5、产品经检验判定后的处理4.1对于检验不合格的成品按照《不合格品控制程序文件》的相关内容进行处理。
4.2检验合格的产品品质科在检验报告单上盖上”合格”以示受控状态,根据成品入库的的程序通知管理科办理入库程序,并做好入库记录。
最终检验规范

修订5 修订5.2.2/5.4检验标准内容 组织架构变更
会 会签单位 ■工程部 ■营业部 ■财务部 ■人力资源部 ■品控部 ■制造部 ■物流部 ■体系办 会签姓名
签
记
录 会 签 意 见
同意 同意 同意 同意 同意 同意 同意 同意
核准
审核
制定
集团体系办
制作单位
发
行
章
品控部
文件编号: 文件编号: HLSG3-Q00040
◎ ◎ ◎ ◎ ◎
4
包装 检验
产品标签 环保标示 包装标示
文件编号: 文件编号: HLSG3-Q00040
最终检验规范
5.4.2素材端子类检验标准: 素材端子类检验标准: 项 次
版本/ 版本/次: 页 日 次: 次: 期: 期:
A/3 4 OF 12 20100327
不良判定 检验项目 检验依据 检验方式 样本数/ 样本数/频率 CR 严重压伤/ 严重压伤/刮 伤 轻微压伤/ 轻微压伤/刮 伤 变形、 变形、歪斜 毛边、 毛边、缺损 缺损 绕盘方向 样品 样品 样品 样品 样品、 样品、工程图 包装规范 用尖嘴钳/ 用尖嘴钳/治具夹 住预断点折弯, 住预断点折弯, 依工程图要求检 验 端子PIN无针部位 端子PIN无针部位 PIN 不可有毛边/ 不可有毛边/毛刺 不良 工程图 样品、 样品、工程图 样品、 样品、工程图 QIP 组配无不良 依包装规范要求 依包装规范要求 依包装规范要求 料号/数量/日期/ 料号/数量/日期/ 合格章等 目视 目视 目视 1.ANSI/ASQC Standard Z1.4-Ⅱ级水 目视 准 批量在10 2.批量在10 目视 卷以下产品 全检,10卷 全检,10卷 尖嘴钳/ 尖嘴钳/治具 以上抽检需 在原基础上 /投影仪 加抽30 30% 加抽30%,每 卷至少需拉 开 500 投影仪/ 投影仪/ 1000 mm 长 显微镜 度 投影仪 目视、 目视、钢尺 投影仪 目视 投影仪& 投影仪&卡尺 目视 目视 目视 目视 目视 5PCS/ 每批 5PCS/ 每批 每批 每批 每批 每批 ◎ ◎ ◎ ◎ ◎ ◎ ◎ ◎ ◎ MA ◎ ◎ MI
出厂检验规程【范本模板】

出厂检验规程
1. 目的:
保证出厂产品进行了规定的检验和试验,达到有关技术标准和用户规定的要求.
2。
范围:
适用于指导公司生产的带式给料机成品的最终检验工作。
3.职责:
3.1 质检部是成品最终检验的归口管理部门,负责最终检验和试验工作的实施和管理工作。
3.2 质检部负责产品最终检验技术标准的制定。
3。
3 各工段、仓库负责产品最终检验的协助工作。
4.检验项目、技术要求及检验方法:
给料机检验完毕后,出具检验报告书.
5.合格品的处理
给料机检验合格后,由质检部发放合格证。
6.不合格品的处理
6.1 成品检验判定为不合格,可以通过返工、返检达到验收要求的,由检验员作出处理。
产品经返工、反检后重新交检.
6.2 当成品的不合格项不可能通过返工、返检达到合格接受条件时,按《不合格品控制程序》执行。
山东省华斯达工贸有限公司。
产品最终检验规程
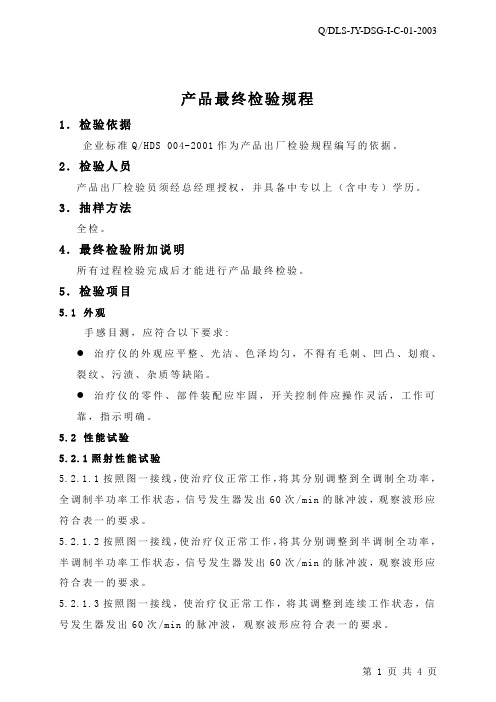
产品最终检验规程1.检验依据企业标准Q/HDS 004-2001作为产品出厂检验规程编写的依据。
2.检验人员产品出厂检验员须经总经理授权,并具备中专以上(含中专)学历。
3.抽样方法全检。
4.最终检验附加说明所有过程检验完成后才能进行产品最终检验。
5.检验项目5.1 外观手感目测,应符合以下要求:●治疗仪的外观应平整、光洁、色泽均匀,不得有毛刺、凹凸、划痕、裂纹、污渍、杂质等缺陷。
●治疗仪的零件、部件装配应牢固,开关控制件应操作灵活,工作可靠,指示明确。
5.2 性能试验5.2.1照射性能试验5.2.1.1按照图一接线,使治疗仪正常工作,将其分别调整到全调制全功率,全调制半功率工作状态,信号发生器发出60次/min的脉冲波,观察波形应符合表一的要求。
5.2.1.2按照图一接线,使治疗仪正常工作,将其分别调整到半调制全功率,半调制半功率工作状态,信号发生器发出60次/min的脉冲波,观察波形应符合表一的要求。
5.2.1.3按照图一接线,使治疗仪正常工作,将其调整到连续工作状态,信号发生器发出60次/min的脉冲波,观察波形应符合表一的要求。
治疗仪治疗灯信号发生器双踪示波器图一5.3 辐射强度试验使治疗仪正常工作,将热释功率计置于治疗仪20cm处,使治疗仪的灯正对热释功率计的探头,约5min后待热释功率计的指针稳定后,读取数字,连续照射方式下辐射强度大于0.07W/cm2。
5.4 定时设置试验使治疗仪正常工作,将定时设置在30min,即用秒表计时,当治疗仪停止工作时,观察秒表其结果应与治疗仪定时设置符合。
治疗仪的定时设置为5min~90min,允差为±5%。
5.5 安全性能试验5.5.1保护接地阻抗5.5.1.1要求治疗仪电源输入插口的设备,在插口中的保护接地点与已保护接地的可触及金属部件阻抗,不得超过0.1Ω。
5.5.1.2试验方法用医用设备保护接地阻抗测量仪在端子或接地点或接地脚与金属部件之间进行测量。
模具检验验证规范【范本模板】

模具检验验证规范NJSC/GL11—2014编制:审核:批准:日期:2014年3月31日南京XXXX有限公司一、目的对来自于外部的物料、内部加工的部品以及总成后的模具按要求进行检验,以确保投入使用的物料、部品和模具满足预期的要求。
二、范围适用于所有组成模具的部品及模具,包括采购的物料、委外和内部加工的部品、以及电极类间接用的部品。
三、定义3。
1来料检验:采购的物料、外购件和委外加工部品的检验.3.2过程检验:内部加工的模具零部件、电极类部品等的半成品和成品检验.3.3最终检验:3.3。
1模具零部件的成品最终检验,包括零部件的尺寸公差、形位公差、光洁度的检验。
3。
3.2模具总成后的检验,包括模具外观、可成形性、成形产品等的检验。
四、职责4。
1 技术部负责相关检验要求数据的提供。
4.2 质量部负责对物料、部品以及模具实施来料检验、过程检验和最终检验。
4。
3 采购部对采购物资质量负责,并配合质量部做好来料检验工作。
4。
4 生产部协助做好过程检验,并确保未经检验或检验不合格的物资不投入使用。
五、检验验证流程5。
1来料检验5.1。
1 作业流程图5。
1.2 作业流程5.1.2.1 仓管员在接收到外来的物料时,对物料种类、供应商、数量等信息进行确认,确认无误后将物料存放在暂放区域,并以“待检品”予以标识同时通知质检.5。
1。
2.2 质量部接到报检信息后在二个工作日内对物料名称、规格、供应商、包装、标识等与相应的采购文件进行核对,无误后进行抽样或全数检查,并将检验结果填入《进货检验记录》。
如遇到特殊情况,生产急需使用物料,质量部应在半个工作日内完成检查工作。
5。
1。
2。
3 检验合格的物料贴上“合格”标签,仓管人员办理入库手续。
5。
1.2.4 检验不合格的物料,填写《不合格品处置单》,质量部会同技术部相关人员进行检讨,可接受的以“特别采用”进行标识,无法采用的贴上“不合格”标签并予以隔离.5.1。
2.5 项目部将不合格物料的信息反馈给供应商,无法采用的物品予以退回.5.1.2。
最终检验及出货检验管理规定
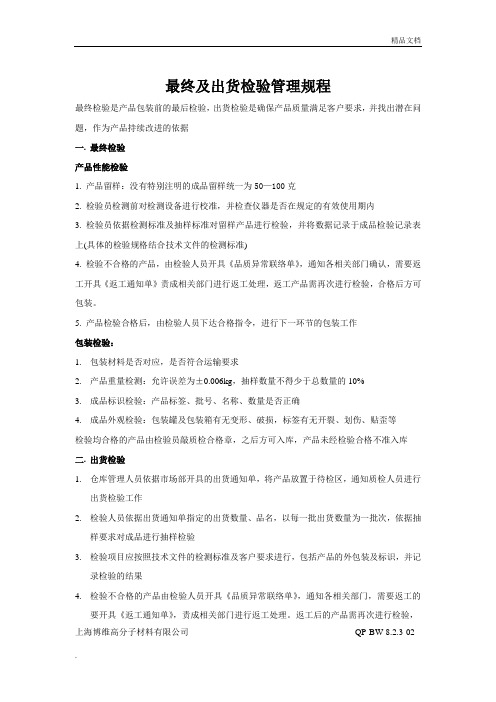
最终及出货检验管理规程最终检验是产品包装前的最后检验,出货检验是确保产品质量满足客户要求,并找出潜在问题,作为产品持续改进的依据一.最终检验产品性能检验1. 产品留样:没有特别注明的成品留样统一为50—100克2. 检验员检测前对检测设备进行校准,并检查仪器是否在规定的有效使用期内3. 检验员依据检测标准及抽样标准对留样产品进行检验,并将数据记录于成品检验记录表上(具体的检验规格结合技术文件的检测标准)4. 检验不合格的产品,由检验人员开具《品质异常联络单》,通知各相关部门确认,需要返工开具《返工通知单》责成相关部门进行返工处理,返工产品需再次进行检验,合格后方可包装。
5. 产品检验合格后,由检验人员下达合格指令,进行下一环节的包装工作包装检验:1.包装材料是否对应,是否符合运输要求2.产品重量检测:允许误差为±0.006kg,抽样数量不得少于总数量的10%3.成品标识检验:产品标签、批号、名称、数量是否正确4.成品外观检验:包装罐及包装箱有无变形、破损,标签有无开裂、划伤、贴歪等检验均合格的产品由检验员敲质检合格章,之后方可入库,产品未经检验合格不准入库二.出货检验1.仓库管理人员依据市场部开具的出货通知单,将产品放置于待检区,通知质检人员进行出货检验工作2.检验人员依据出货通知单指定的出货数量、品名,以每一批出货数量为一批次,依据抽样要求对成品进行抽样检验3.检验项目应按照技术文件的检测标准及客户要求进行,包括产品的外包装及标识,并记录检验的结果4.检验不合格的产品由检验人员开具《品质异常联络单》,通知各相关部门,需要返工的要开具《返工通知单》,责成相关部门进行返工处理。
返工后的产品需再次进行检验,上海博维高分子材料有限公司QP-BW-8.2.3-02合格后方可出库5.对于存放超过规定期限的产品,在出库前应重新进行开箱检验6.检验合格的产品,由出货检验员在外箱敲检验合格章后,方可出库7.出货检验报告应详细记录顾客厂家名称、抽样检验时间、抽样箱数及数量、出货总箱数、抽样检验时发现的不合格项目、不合格品处理结果及检验员签名等。
API6A最终检验规范

4.2.3.1通径试验 – 全孔阀
a)方法 用表1所述的通径规贯通阀孔。
b)验收规则 通径规应完全贯通阀孔。
4.2.3.2通径试验 – 采油树
a)方法 用表1所述的通径规采油树总成的主孔。
b)验收准则 通径规应完全贯通采油树孔。
4.2.3.3本体静水压试验 – 单独设备
a)方法 总装的设备应在制造商的工厂装运前,经受本体静水压试验。本体静水压试验应是最先进行的压力试验。试验压力不是阀关闭机构两端的压力差,水或带添加剂的可用作试验液,试验应在涂漆前完成。
(3)具有入口连接比出口连接有较高压力额定值的节流阀,从入口连接至可更换阀座(或节流油嘴)的阀体 – 油嘴密封点阀体,应按入口连接的相应压力作静水压试验,从密封点下游的阀体其余部分,应按出口连接相应的压力试验。可采用临时阀座密封,以便于试验。
(4)阀和节流阀在试验期间应处于局部开启位置。
(5)多孔设备的每一孔径应单独试验。
除节流阀外,试验后,阀应在满压差下开启。
上述两步试验应重复试验。
然后在闸板或旋塞一侧进行三次施压。稳压后,监视至少三分钟。
双向阀在闸板或旋塞另一侧,使用上述相同程序再次试验。对开式闸板可同时作两次阀座试验。
b)验收准则- 阀座试验
在任一稳压期间,阀不应有可见的渗漏。
4.2.5 PSL3试验
4.2.5.1通径试验 – 全孔阀 与PSL1要求相同。
c)验收准则
设备在试验压力下,不应有可见的渗漏,当与螺纹式装置连接时,厂内静水压试验期间超过螺纹工作压力时的螺纹渗漏是允许的。
4.2.3.4本体静水压试验-阀
a)方法 双向阀应以额定工作压力施加于闸板或旋塞的每一侧,另一段通大气,进行阀座静水压试验。
最终检验规定准则
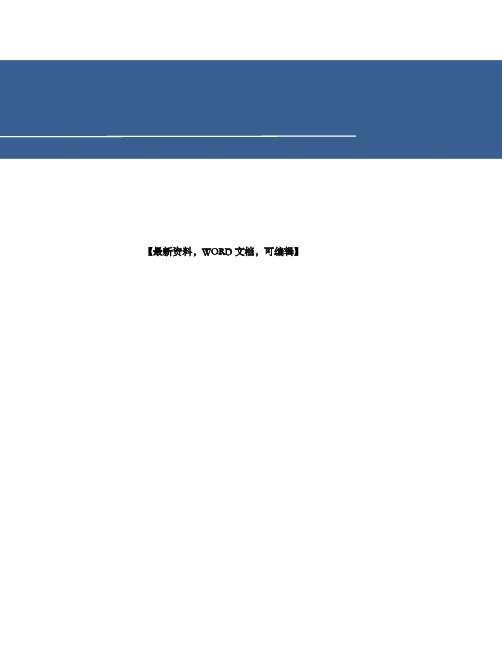
【最新资料,WORD文档,可编辑】最终检验规定1.总则1.1.制定目的本公司为加强产品品质管制,确保各工程间品质稳定,特制定本规定。
1.2.适用范围本公司产品加工过程中,各工程完工后之制品或成品需入库时,适用本规定。
1.3.权责单位1)品管部负责本规定制定、修改、废止之起草工作。
2)总经理负责本规定制定、修改、废止之核准。
2.检验规定2.1.抽样计划依据GB2828(等同MIL-STD-105D)单次抽样计划。
2.2.品质特性品质特性分为一般特性与特殊特性。
2.2.1.一般特性符合下列条件之一者,属一般特性。
1)检验工作容易者,如外观特性。
2)品质特性对产品品质有直接而重要之影响者,如电气性能。
3)品质特性变异大者。
2.2.2.特殊特性符合下列条件之一者,属特殊特性:1)检验工作复杂、费时,或费用高者。
2)品质特性可由其他特性之检验参考判断者。
3)品质特性变异小者。
4)破坏性之试验。
2.3.检验水准1)一般特性采用GB2828正常单次抽样一般II级水准。
2)特殊特性采用GB2828用正常单次抽样特殊S-2水准。
2.4.缺陷等级抽样检验中发现之不符合品质标准之瑕疵,称为缺陷,其等级有下列三种:1)致命缺陷(CR)能或可能危害制品的使用者、携带者的生命或财产安全之缺陷,称为致命缺陷,又称严重缺陷,用CR表示。
2)主要缺陷(MA)不能达成制品的使用目的之缺陷,称为主要缺陷或重缺陷,用MA表示。
3)次要缺陷(MI)并不影响制品使用目的之缺陷,称为次要缺陷,或轻微缺陷,用MI表示。
2.5.允收水准本公司对最终检验缺陷等级允收水准规定如下:1)CR缺陷,AQL=0。
2)MA缺陷,AQL=1.0%。
3)MI缺陷,AQL=2.5%。
2.6.检验依据依据下列一项或多项:1)技术文件。
2)有关检验规范。
3)国际、国家标准。
4)行业标准或协会标准(如TUV、UL、CCEE等)。
5)客户要求。
6)品质历史档案。
7)比照样品。
- 1、下载文档前请自行甄别文档内容的完整性,平台不提供额外的编辑、内容补充、找答案等附加服务。
- 2、"仅部分预览"的文档,不可在线预览部分如存在完整性等问题,可反馈申请退款(可完整预览的文档不适用该条件!)。
- 3、如文档侵犯您的权益,请联系客服反馈,我们会尽快为您处理(人工客服工作时间:9:00-18:30)。
绩效考核绩效管理企业建设企业管理招聘配置薪酬待遇薪酬管理培训开发培训与开发员工关系人事管理行政后勤行政管理制度规范招聘与配置实用表格规章制度管理制度建设方案方案书员工培训培训计划入职培训团队建设考核方法员工考核工资待遇工作计划工作计划表签到表考勤表工资表考核表申请表登记表检查表计划表报告表通知单日报表记录表审批表报销单绩效考核企业管理招聘配置薪酬待遇培训开发员工关系行政后勤实用表格行政表格办公常用人事报表财务报表
最终检验规定
(2019-2020年版)
最终检验规定
1.总则
1.1.制定目的
本公司为加强产品品质管制,确保各工程间品质稳定,特制定本规定。
1.2.适用范围
本公司产品加工过程中,各工程完工后之制品或成品需入库时,适用本规定。
1.3.权责单位
1)品管部负责本规定制定、修改、废止之起草工作。
2)总经理负责本规定制定、修改、废止之核准。
2.检验规定
2.1.抽样计划
依据GB2828(等同MIL-STD-105D)单次抽样计划。
2.2.品质特性
品质特性分为一般特性与特殊特性。
2.2.1.一般特性
符合下列条件之一者,属一般特性。
1)检验工作容易者,如外观特性。
2)品质特性对产品品质有直接而重要之影响者,如电气性能。
3)品质特性变异大者。
2.2.2.特殊特性
符合下列条件之一者,属特殊特性:
1)检验工作复杂、费时,或费用高者。
2)品质特性可由其他特性之检验参考判断者。
3)品质特性变异小者。
4)破坏性之试验。
2.3.检验水准
1)一般特性采用GB2828正常单次抽样一般II级水准。
2)特殊特性采用GB2828用正常单次抽样特殊S-2水准。
2.4.缺陷等级
抽样检验中发现之不符合品质标准之瑕疵,称为缺陷,其等级有下列三种:
1)致命缺陷(CR)
能或可能危害制品的使用者、携带者的生命或财产安全之缺陷,称为致命缺陷,又称严重缺陷,用CR表示。
2)主要缺陷(MA)
不能达成制品的使用目的之缺陷,称为主要缺陷或重缺陷,用MA表示。
3)次要缺陷(MI)
并不影响制品使用目的之缺陷,称为次要缺陷,或轻微缺陷,用MI表示。
2.5.允收水准
本公司对最终检验缺陷等级允收水准规定如下:
1)CR缺陷,AQL=0。
2)MA缺陷,AQL=1.0%。
3)MI缺陷,AQL=2.5%。
2.6.检验依据
依据下列一项或多项:
1)技术文件。
2)有关检验规范。
3)国际、国家标准。
4)行业标准或协会标准(如TUV、UL、CCEE等)。
5)客户要求。
6)品质历史档案。
7)比照样品。
8)其他技术、品质文件。
3.作业规定
3.1.生产批送验
1)制造单位在制造加工中,每累积一定数量之制品(半成品、成品)时,应将其
作为一个交验批(如一栈板)送品管部FQC检验。
2)品管部FQC(Final Quality Control)人员,依据抽样规定进行抽样检验,并填
写《入库检验记录》。
3.2.接收入库
1)FQC判定合格(允收)之制品(半成品、成品),在其外包装之标签上加盖“合
格”章,并签名。
2)制造单位物料人员填写《入库单》经品管人员签名后,将合格物料送往相应之
仓库办理入库手续。
3.3.拒收重流
1)FQC判定不合格(拒收)之制品,填写《不合格通知单》呈品管主管审核。
2)经品管主管审核为不合格之制品,由FQC在其外包装之标签上加盖“不合格”
章或“拒收”章,并签名。
3)《不合格通知单》一联由FQC保存,作为复检依据,一联转制造单位,安排
制品重流(或称重检)。
4)不合格制品由制造单位根据不合格原因安排重流作业,进行挑选、加工、返修
作业。
5)重流完成后,制造单位重新交验该批制品,FQC进行复检。
6)重新送验时,制造单位应将重流数量、重流发现之不良数量、改善对策等填入
《不合格通知单》,并将该单随物料送检。
3.4.特采入库
1)FQC判不合格(拒收)之制品,制造或生管单位因下列情形可申请特采:
A)缺陷轻微对品质特性妨碍极小。
B)下工程或出货急需该批制品。
C)经下工程简单挑选或修复后可使用。
D)其他特殊状况。
2)经品管部经理得核,可以维持不合格判或改判特采(让步接收)。
3)特采后,制品依合格品流程入库,但由FQC在标签上注明特采及特采原因。
4)特采物料之后续处理方式:
A)让步接受予以使用。
B)经挑选后使用。
C)经加工修复后使用。